Вступ
Вид материала | Документы |
- Вступ, 323.48kb.
- Програма дисципліни кредитний модуль " основи радіоелектроніки" (для груп фф) Вступ, 153.44kb.
- Питания з Програми з курсу «Механіка», що виноситься на зм 1 вступ, 86.8kb.
- Робоча навчальна програма здисципліни: Принципи І методи аналізу художнього твору Спеціальність, 222.75kb.
- План, вступ, викладення змісту теми (як правило, 2 глави), висновок, а також список, 24.79kb.
- Вступ України до Світової огранізації торгівлі. Законодавчі зміни. Галузеві стратегії”, 72.41kb.
- Робоча навчальна програма Модуля Вступ до спеціальності Для студентів спеціальності, 404.17kb.
- Вступ до історії україни 5-й клас (35 годин), 86.86kb.
- Вступ до історії україни 5-й клас (35 годин), 104.36kb.
- М. В. Ломоносов; [вступ ст., сост., примеч. А. А. Морозова]. Ленинград : Сов писатель,, 249.18kb.
5.5. Роль порошкової металургії в утилізації відходів машинобудування.
Порошкова металургія (або металокераміка) - галузь науки і техніки про отримання виробів з порохоподібних матеріалів - металів, сплавів, а також неметалів шляхом одночасної дії на суміш цих компонентів високим тиском і температурою спікання з отриманням готових деталей і виробів.
Ця галузь називається ще металокерамікою тому, що дозволяє отримувати деталі і вироби з металів та неметалів типу кераміки.
Вперше порошкову металургію застосував інженер П.Г.Соболевський (1782-1841). Порошкова металургія складається з трьох етапів; одержання порошків, їх пресування і спікання виробів з цих порошків.
Металеві порошки для цієї технології отримують механічним, фізико-механічним і хімічним методами.
До перших і других методів відносяться дроблення і помел, розпилення, грануляція. До других - хімічне відновлення оксидів металів. Інших сполук воднем, конвертовним природним газом, вуглецем, коксом або активними металами - натрієм, кальцієм і іншими.
Відновлення оксиду заліза або інших оксидів до металу проходить по А. А Байкову, в три стадії при температурі 572°С (для заліза): адсорбції відновника на поверхні оксиду, поверхневої реакції молекул відновника з киснем оксиду металу і десорбції продукту реакції з поверхні речовини.
Для відновлення воднем застосовують прохідні муфельні печі або безперервно діючі конвеєрні печі з більш високою температурою, ніж 572°С.
Більше 25 років тому був розроблений і втілений новий спосіб відмовлення оксидів, який одержав назву "відновлення в киплячій кулі" або так званий "ПЖ-ПРОЦЕС".
Цим способом залізний порошок отримують 9 марок в залежності хімічного складу. ПЖО, ПЖ1, ПЖ2 ... ПЖ8, з яких для порошкової металургії застосовують тільки п'ять перших. Порошок "ПЖО" містить, %: заліза вуглецю 0,1; кремнію 2,0; марганцю 0,15; фосфору 0,015 і кисню 0,2.
Підготовка порошків до пресування складається з їх обпалу (для більшої пластичності), класифікації (тобто розділення за розмірами за допомогою повітряного сепаратора) і виготовлення суміші за рецептурой вироблення тих чи інших деталей.
Пресування виробів проходить в сталевій формі. Спочатку порошки дозують після розрахунків їх наважки і засипають в матрицю пресформи Наважка порошку розраховується за формулою:
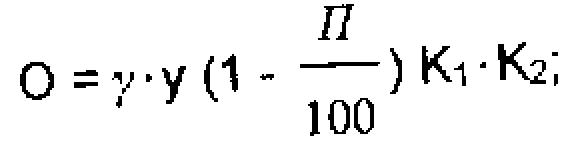
де О - наважка порошку, кг; - густина матеріалу, г/см3; - об'єм виробу після спікання, см3; П - фактична пористість спеченого виробу, %; К1 -, коефіцієнт, який враховує витрату порошку при пресуванні і який залежить від точності виготовлення пресформи, він дорівнює 1,005-1,01; К2 - коефіцієнт, що враховує витрати маси при спіканні в результаті відновлення оксидів і відділення домішок, втому числі і мастил, К2 = 1,01-1,03.
При пресуванні суміші різних компонентів їх густину визначають за правилом адитивності, г/см3 за формулою:

В наступний час порошкова металургія одержала великий розвиток для виробництва різних деталей із відходів. Загальний об'єм виробництва продукції цим методом сягає 6000 тис. т на рік.
В чому ж полягає значення металокераміки або порошкової металургії!? По-перше, в якості сировини використовуються відходи і без залишку; по-друге дозволяє отримувати вироби із металів і неметалів з особливими властивостями, яких не знає природа; по-третє, економить теплову енергію за рахунок використання тиску; по-четверте, економить працю робітників за рахунок скорочення кількості операцій; по-п'яте, дає більш дешеві вироби і, по-шосте, дає можливість отримувати матеріали з особливими властивостями - пористі, антифрикційні, фрикційні, фільтруючі, електротехнічні магнітні, контактні, високотемпературні, тугоплавкі, волоконні, жаростійкі, надтверді і інші.
5.6. Регенерація мастильно-охолоджуючих рідин (МОР).
МОР в процесі роботи при механічній обробці виробів поступово забруднюються частинками абразиву, тирсою, стружкою і іншими металевими включеннями, волокнами.
Методи очищення МОР полягають в їх відстоюванні, відділенні мастил і нейтралізації звільненої від мастил води. Очищення МОР від механічних домішок проводиться у відстійниках з попередньою магнітною сепарацією відпрацьованої емульсії.
Забруднена МОР проходить в клиновидну зону між поступово обертальним магнітним барабаном і корпусом сепаратора. Металеві залишки притягуються до барабана і очищуються з нього гумовою щіткою. Потім намагнічена емульсія попадає в бак-відстійник, де частинки шламу коагулюють в більш крупні агрегати і випадають в осад. Він відфільтровується і та ж МОР повертається в обіг.
5.7. Азотнозалізисті добрива з відходів травильних розчинів.
Технологічний процес отримання азотнозалізистих добрив з травильних розчинів складається з обробітку аміаком відпрацьованих травильних розчинів металооброблюючих підприємств.
Травильні розчини застосовуються для відділення іржі тобто гідроксиду заліза (111)з виробів, які підлягають нанесенню покриття для захисту їх від корозії. В залежності від складу травильних відпрацьованих розчинів азотнозалізисті добрива містять гідроксид окису заліза, сульфат амонію (або хлорид амонію, якщо травильний розчин мав соляну кислоту); аміачну селітру, фосфати амонію, аміачну воду і в невеликій кількості солі молібдену, нікелю, хрому, марганцю і деяких інших елементів.
Ці добрива можуть застосовуватися самостійно або в суміш з іншими туками.
Досліди про застосування азотнозалізистих добрив, одержаних з травильних відпрацьованих розчинів, під плодово-ягідні культури, картоплю, капусту і інші, показали їх високу ефективність, особливо на вапнякових і карбонатних грунтах. Відомо, що на цих грунтах рослини часто хворіють на хлороз через відсутність заліза, яке служить каталізатором процесу утворення хлорофілу. Застосування ж цього добрива особливо на солонцевих грунтах приводить до покращання структури грунтів і до підвищення врожаїв рослин.
Азотнозалізисті добрива можуть застосовуватись і для позакореневого підгодовування рослин, при цьому добрива діють як інсектофунгіциди.
Експерименти, які проводились в проблемній лабораторії Дніпропетровського сільськогосподарського інституту, підтвердили високу ефективність азотнозалізистих добрив. Внесення в грунт 50 кг на 1 га посівів вага рослин томатів збільшується на 25% в порівнянні з внесенням тієї ж кількості добрив у вигляді сульфату амонію.
Досліди, які були проведені інститутом ґрунтознавства АН Казахської РСР азотнозалізистих добрив на культурі рису на луково-болотних грунтах Кзил-Ординської області, виявили, що при внесенні цих добрив врожай рису збільшився приблизно в два рази а з добавкою суперфосфату навіть більше, ніж у два рази.
5. Технології переробки та використання основних BMP промисловості основної хімії
5.1. Економічна ефективність безвідходних виробництв в промисловості основної хімії.
Основа безвідходних виробництв - комплексне використання сировини. оскільки відходи виробництва - це з тих, чи інших причин є не використана або недовикористана частина сировини. Це обумовлено тим, що затрати на сировину і матеріали в хімічній промисловості в собівартості продукції складають 70-80%, а то й більше. Тому комплексне і раціональне використання сировини в хімічній промисловості є важливим народногосподарським завданням, як і в інших галузях.
Необхідність повного використання природних ресурсів і сировини "Обумовлено також зростаючими темпами росту промислових відходів, які утворюються при їх переробці, а також тим, що вони забруднюють довкілля-грунт, повітря, воду. І, найголовніше, запаси мінеральної сировини на землі обмежені, а ціни на них і затрати на їх відтворення безперервно достають.
Технологія безвідходного виробництва включає мінімальну кількість операцій, технологічних стадій і переходів, а також включає їх суміщення з тим, щоб менше утворювалось відходів і менше втрачалось вихідної сировини.
Безвідходне виробництво - це виробництво, в якому вся вихідна сировина повністю перетворюється в ту чи іншу продукцію.
Абсолютна економічна ефективність безвідходних виробництв визначається за формулою:
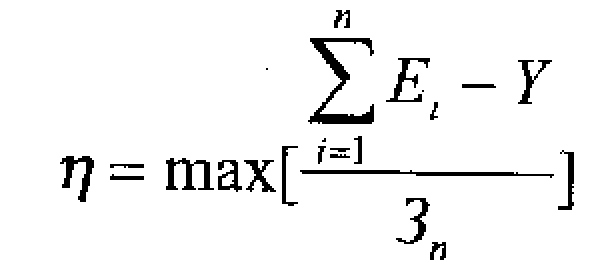
де,
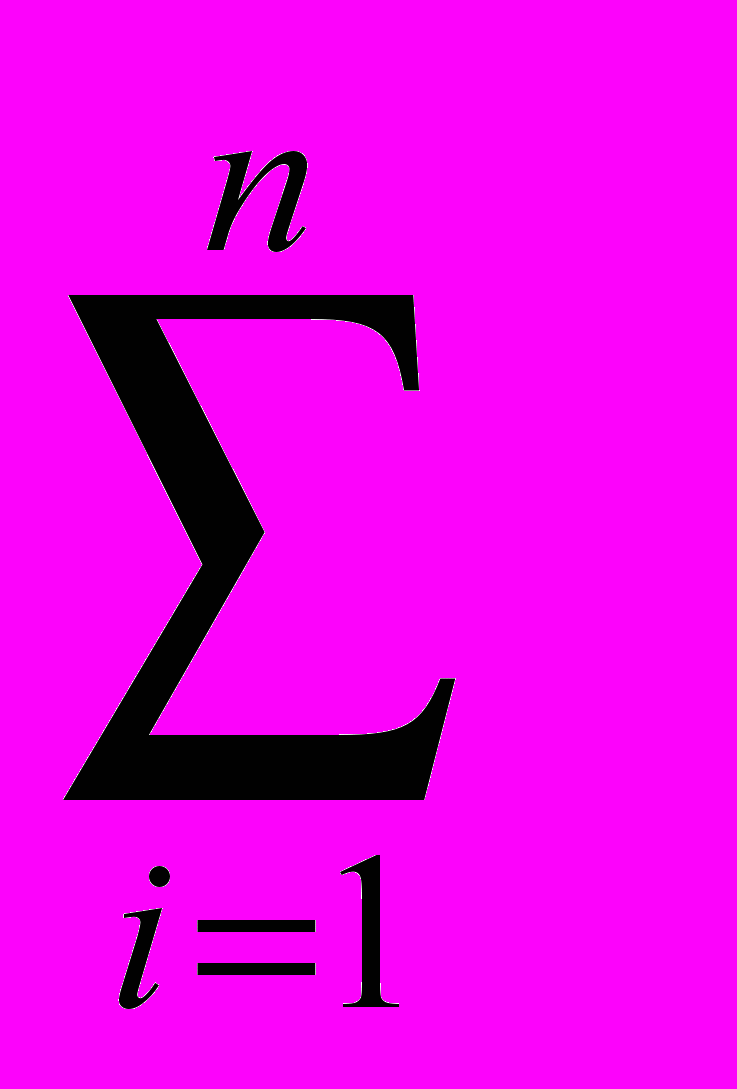
При наявності кількох варіантів безвідходних технологій вибирають варіант з максимальним коефіцієнтом абсолютної економічної ефективності при рівних народногосподарських витратах.
М.І.Києвський, В.Н.Євстратов і А.Г.Ватманов наводять і розглядають чотири варіанти ефективних капітальних вкладень у безвідходне виробництво (див. таблицю 15).
Таблиця 15 Порівняння варіантів безвідходних технологій
Показники | Варіанти Bapis 2 4 | |||
1 | 2 | 3 | 4 | |
Коефіцієнт використання сировини Витрати на одержання товарної продукції, крб/рік; поточні одночасні Вихід готової продукції, % Вихід токсичних речовин у довкілля% Втрата товарної продукції, крб/рік Ефект споживання додатково одержаної товарної продукції, крб/рік Ефект скорочення витрат на видобуток сировини, крб/рік Коефіцієнт ефективності капвкладень Коефіцієнт ефективності по народному господарству | 0,8 0,8 0,75 100 100 0,15 - - 0,27 0,066 | 0,85 0,82 0,90 105 70 0,09 0,05 0,01 0,21 0,105 | 0,9 0,84 1,10 110 40 0,06 0,07 0,02 0,16 0,109 | 0,95 0,87 1,30 117 25 0,03 0,08 0,08 0,10 0,104 |
Об'єм вихідних продуктів і сировини у всіх варіантах однаковий. Коефіцієнт використання-відношення готового продукту до маси сире вини і вихідних матеріалів-підвищується від 0,8 до 0,95 в четвертому варіанті. Питомі витрати у всіх варіантах на отримання продукції зростають незначно. Але капітальні витрати зростають аж на 75%. Автори вважають, що фактичні витрати на ліквідацію промислових забруднень складають на багатьох підприємствах 10-20% від усього об'єму капітальних вкладень в хімічній промисловості.
Впровадження маловідходного виробництва збільшує вихід готової продукції від 5% в другому варіанті до 17% в четвертому.
Викиди токсичних речовин скорочуються, як і економічний збиток від них. Додаткова продукція, яка зроблена за рахунок більш повного використання вихідної сировини, створює ефект споживання і ефект скорочення витрат на її добування.
Ефективність капітальних вкладень визначається за формулою:
Е=(Ц-С):К,
де Ц - вартість продукції; С - собівартість продукції (поточні витрати):
К - капітальні витрати за одним із варіантів, вказаних в таблиці 15,
З аналізу варіантів можна зробити висновок, що в міру підвищення вилучення цінних компонентів з вихідної сировини, зменшення викидів в довкілля, зниження збитку економічна ефективність поданих варіантів зменшується. Найкращим буде перший, який має найвищий коефіцієнт ефективності - 0,27. А з позицій народного господарства кращим буде інший.
Народногосподарську ефективність визначають за формулою:

де it - індекс об'єму виробництва по кожному варіанту. Тому найкращим з позиції народного господарства буде другий, потім третій і четвертий варіанти. А з них - третій варіант.
Річний економічний ефект безвідходного виробництва автори пропонують визначати за формулою:
Е = За + Зп + ΔУ;
де За - альтернативні витрати на досягнення економічного ефекту
Еколого-економічна оцінка проектів передбачає порівняння проектів з кращими базовими підприємствами за наступними показниками: об'ємом випускної продукції; наслідками забруднення навколишнього середовища; збитками, які додає народному господарству забруднення довкілля, не комплексним використанням природних ресурсів і відходів виробництва: застосуванням маловідходної або безвідходної технологій, замкнених систем водопостачання і інших прогресивних методів; очищенням відхідних газів, стічних вод і т.п.
Об'єм стічної води для конкретного об'єкта до і після впровадження безвідходної технології визначається за формулами:

де
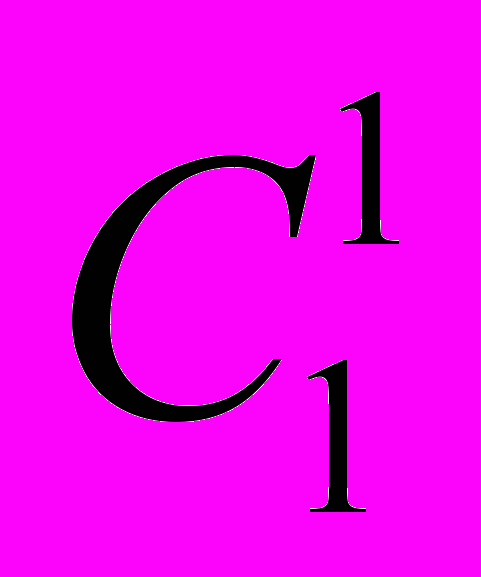
Ефект від здійснення водоохоронного заходу виражається зниженням об'єму забруднень, які викидають, у водойми, і визначається як різниця об'ємів стічних вод до і після виконання проекту.
Повний економічний ефект від водоохоронного заходу визначається за формулою;
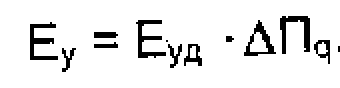
Еколого-економічна оптимальність проекту мало відходного або безвідходного виробництва визначається мінімумом витрат на його будівництво і експлуатацію з врахуванням оцінки компенсації споживних природних ресурсів і шкоди, яка б наносилась довкіллю.
Шкода, яка наноситься навколишньому середовищу, визначається за формулою;

де 3 - витрати на одиницю продукції; С - собівартість одиниці продукції; Ен - нормативний коефіцієнт економічної ефективності капітальних вкладень; К - капітальні вкладення; У - питомий еколого-економічний збиток.
Рішення про еколого-економічну доцільність проекту приймається на основі співставлення витрат на будівництво існуючого базового З1, і проектованого З2 підприємства.
Доцільність або ефект цей визначається за формулою:

де А - річний об'єм виробництва продукції на проектованому підприємстві в натуральних показниках.
Загальна еколого-економічна оцінка нового об'єкта здійснюється за формулою:
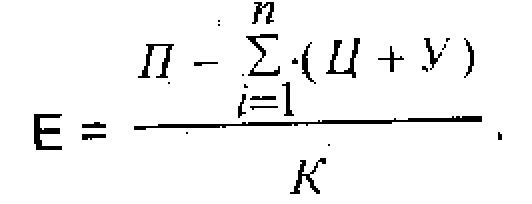
5.2. Переробка колчеданних недогарків, виробництво мідного купоросу, вилучення міді та видобування цинку.
Колчеданні недогарки отримуються як відходи у виробництві сірчаної кислоти із сірчаного колчедану або піриту (FeS2). Точніше приобпалі колчедану, який проходить згідно рівняння з виділенням сірчистого ангідриду:

В колчеданному недогарку, крім сірки, заліза, міститься багато інших речовин. Так, мідь міститься в недогарку у вигляді різних сполук - сульфату, карбонату, оксидів, а також сірчистих з'єднань Це утрудняє повне вилучення міді з недогарку одним простим методом.
Сульфат і сульфіт міді із недогарку легко вилуговуються водою, а оксиди - розведеною сірчаною кислотою.
Сульфіди міді, у яких знаходиться в недогарку до 20% міді, не розчиняються у воді і в розчинах сірчаної кислоти, але переходять в розчин після взаємодії при нагріванні з сульфатом або хлоридом тривалентного заліза згідно з рівняннями:

Цим же способом вилучають мідь з сульфідних мідних руд гідрохімічним методом, інтенсивність вилуговування збільшується при бактеріальному окисленню сульфатів.
Залізо з отриманого розчину вилучають піролюзитом або киснем повітря при наявності вапняку. Але спочатку солі двовалентного заліза переводять в солі тривалентного заліза:
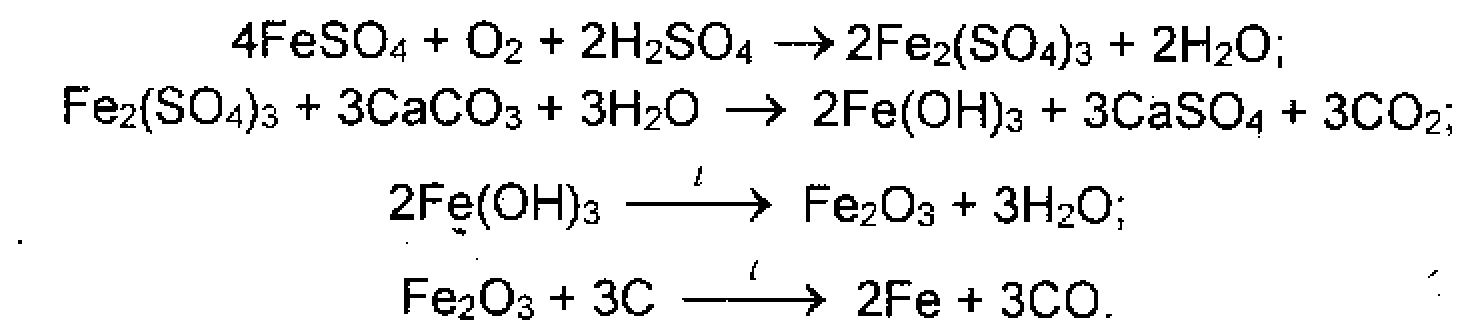
Халькопірит (CuFeS2), який також є в колчеданному недогарку, перетворюється в розчин хлоруванням:

Найбільш розробленим способом отримання сульфату міді або мідного купоросу з недогарків є воднокислотне вилуговування і хлоруючий обпал його при наявності хлористого натрію. Далі солі заліза і міді розділяють, користуючись різною розчинністю цих солей в залежності від температури. Процес закінчується фільтруванням після випаровування води, сушінням і фасуванням в тару.
Вилучення міді з колчеданних недогарків проводиться 1% розчином сірчаної кислоти при кімнатній температурі на протязі 1 г при співвідношенні рідкої і твердої фази, як 1:3. В розчин переходить від 60 до 80% мі/ яка є в недогарку. Внаслідок шестикратного вилуговування отримують розчин, який містить 15-18 г/л міді в формі сульфату. Ця сіль забруднена сполуками заліза 5-6 г/л. Ці сполуки видаляють окисленням розчину хлором або бертолетовою сіллю. Гідроксид заліза в розчині осаджують крейдою. Розчин сульфату міді, який очищений від заліза, випаровують для відділення надлишку води і кристалізують.
Іноді солі заліза і міді не розділяють, а розчин використовують як фунгіцид.
Видобування з колчеданного недогарка цинку проводять хлоруючим обпалом в тих випадках, коли недогарки мають значну кількість цинку. Після відпалу і наступного вилуговування водою цинк знаходиться в розчині вигляді суміші солей сульфатів і хлоридів. Розподіл цих солей пов'язаний зі значними труднощами, тому розчин використовують головним чином для виробництва білої фарби під назвою "літопон".
5.3. Розрахунок виходу недогарків з колчедану.
Вихід і склад недогарка, який утворюється при згорянні колчедану, залежить від хімічного складу сировини і ступеня вигорання з неї сірки. Вихід недогарка визначається за формулою:
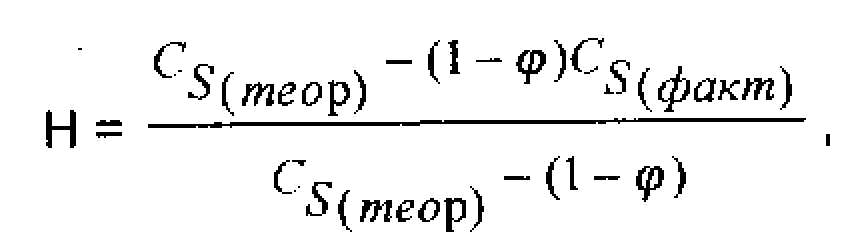
де Н - фактичний вихід недогарка, в долях одиниці від сухого колчедану, Cs(meop) - теоретичний вміст сірки в недогарку, %; φ - теоретичний вихід недогарка по реакції в долях одиниці; С(факт); - фактичний вміст сірки в недогарку, %. Вихід недогарка оцінюється з врахуванням пороху, який видноситься газом з печі. Значення Cs і φ для реакції відпалу різної сировини наведені нижче.
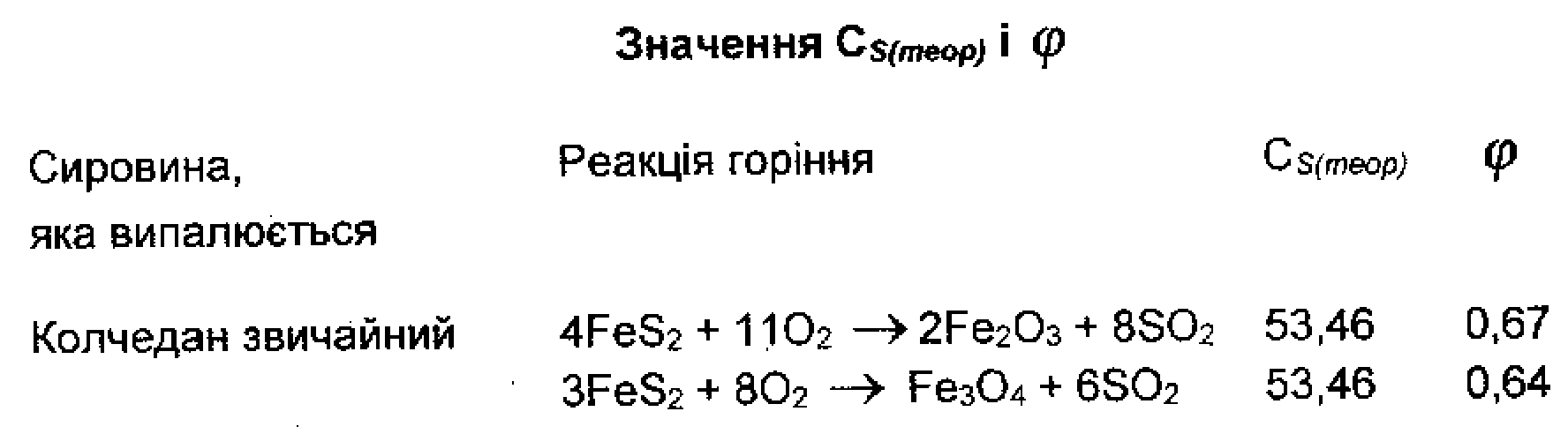

Витрати сірки з недогарком, % визначається за формулою:
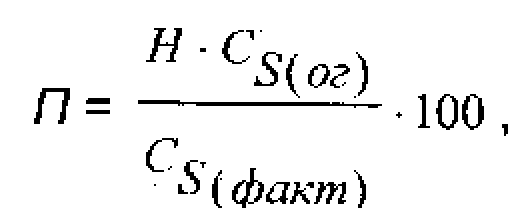
де П - витрати сірки з недогарком, % від кількості сірки, яка завантажена в піч; Cs(os) - вміст сірки в % недогарку.
Розрахунок кількості недогарка, який одержується при обпалі 1 т колчедану, можна провести за таким рівнянням:
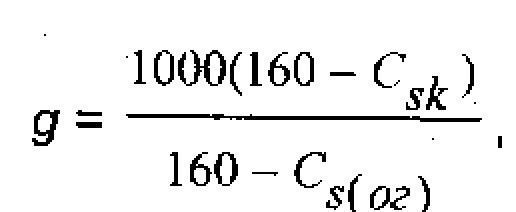
де g - кількість недогарка на 1 т спалюваного колчедану, кг: Csk -вміст cірки в колчедані, %; Cs(os). - вміст сірки в недогарку, %.
Наприклад, при вмісті сірки в колчедані 45%, а в недогарку 2%, вихід недогарка на 1 т колчедану складає:
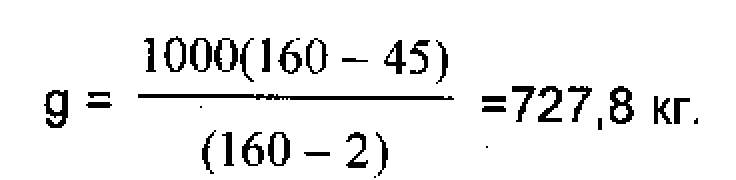
Недогарок в печі охолоджується водою до 70-80°С або проходить через нахилену холодил холодильно-транспортну трубу, яка обертається на роликах. Зовнішня поверхня труби зрошується водою до 120-140°С. Вивантаження недогарка проводиться скребковими транспортерами.
Значними перевагами володіють гідравлічні і пневматичні засоби вилучення недогарка з печі. В першому випадку недогарок змішується з водою і потрапляє в басейн-відстійник, де пульпа освітлюється. За другим методом недогарок висмоктується з бункера ежекцією стиснутого повітря, замість огарку в повітрі подається у відвали пневмотранспортером.
Приклади розрахунку виходу кількості недогарка.
Приклад 1. Розрахувати вихід колчеданного недогарка у виробництві сірчаної кислоти, якщо продуктивність печі киплячого шару по таких вихідних даних: продуктивність печі KШ (киплячого шару) т, сірчаної кислоти 1000/5; ступінь використання сірки, %, 88,5; витрати вихідного колчедану, який має 45% сірки, т/т сірчаної кислоти, 0,82; вміст сірки в колчедані, % 4Ї; вологи в колчедані, %, 6,0; сірки в недогарку, %, до 1,0; сірчистого газу в сухому випалювальному газі, %, 14,5; сірчаного газу в
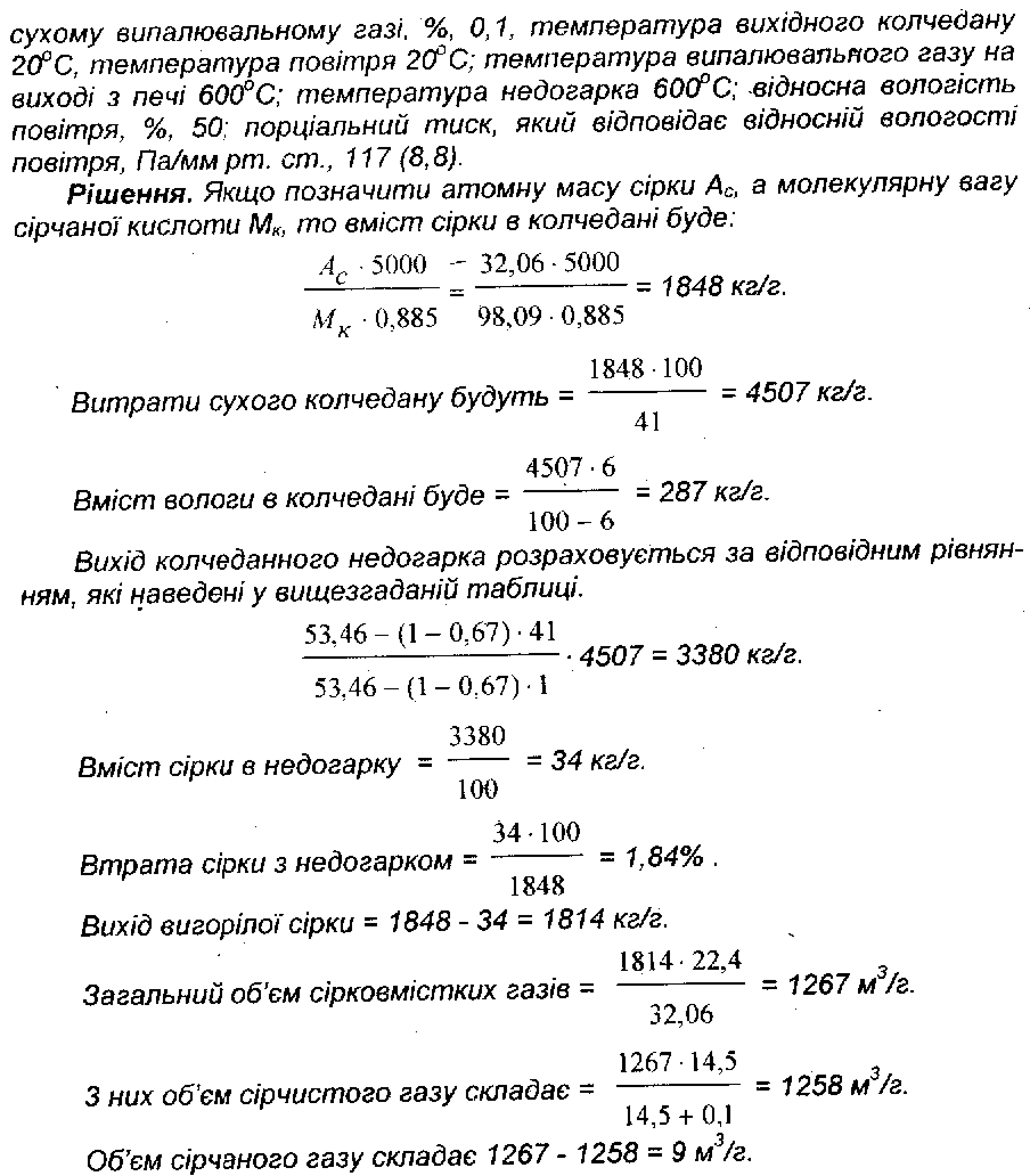
6.4. Використання колчеданних недогарків для отримання чавуну і сірчистого газу.
Колчеданний недогарок містить біля 50% оксиду заліза Fе20з. Тому він може служити цінною сировиною для отримання чавуну. Його треба підготувати. Недогарок являє собою дрібний порошок з домішками сірки і кольорових металів (особливо міді і цинку) в кількостях, які перевищують норми, встановлені для доменного процесу.
Підготовка недогарка полягає в тому, що його перемішують з розчином хлористого кальцію, отримують так звані "зелені гранули" і випалюють при 1200°С в обертальних печах. При цьому проходить сублімація (або перегін) кольорових металів і отримання більш міцних гранул, які б були придатні для завантаження в доменну піч.
Гази, які виділяються при обпаленні "зелених гранул"; промиваються подою. Кольорові і благородні метали при цьому випадають в осад, який відфільтровують і вилучають ці метали. Надогарок агломерують: частина його йде на добування цементу або для отримання мінеральних пігментів сурику, мумії і охри. А другу частину надогарку змішують з паливом, іншими добавками і у вигляді шихти розмішують шарами визначеної височини і стрічці машини, яка завантажить її в піч. Горючі гази просочуються крізь шари шихти з повітрям, викликають окислення сірки до сірчистого газу, який вловлюється водою і перетворюється в сірчану кислоту. Оксид заліза, який залишився на стрічці, іде в доменну піч для одержання чавуну.
6.5. Отримання селену з сірчистого газу при виробництві сірчаної кислоти.
Ступінь вилучення селену з колчедану у виробництві сірчаної кислоти сягає від 30 до 60% і залежить від влаштування і режиму роботи печей, очисного відділення. 50% селену збирається з надогарками в сухих електрофільтрах.
Технологічний процес отримання селену при виробництві сірчаної кислоти складається з трьох стадій: поглинання селенистого ангідриду з випалювального газу сірчаною кислотою; відновлення селенистого ангідриду до елементарного селену і виділення селену з розчину сірчаної кислоти, Псі ці стадії проходять одночасно разом з очищенням випалювального газу згідно рівнянням:

Селен осаджується разом з частинами пороху і кислоти в промивних баштах у відстійниках, збірниках і холодильниках у вигляді шламу. Його називають "бідним селеновим шламом".
Селен, який утворюється при відновленні селенистого ангідриду в вигляді туману і осідає разом з залишками пороху в мокрих електрофільтрах, називають "багатим селеновим шламом". Перший в своєму складі містить до 5%, а другий " до 50% селену.
"Бідний селеновий шлам" після відстійників, збірників і холодильників кислоти промивних башт надходить в приймач, де він розводиться водою і нагрівається гострою парою. Розчин фільтрують, осад промивають водою і 0,5%-ним розчином соди, а потім висушують при 90-100°C.
"Багатий селеновий шлам" надходить у відстійники, розбавляється водою, фільтрується, а потім обробляється, як "бідний". Висушений шлам відправляється на підприємство по отриманню чистого селену.