Вопрос Катализаторы как инструмент экологической безопасности переработки горючих ископаемых (безотходные технологии, экологическое топливо, переработка отходов)
Вид материала | Документы |
- Актуальные вопросы рециклинга, переработки отходов и чистых технологий, 141.62kb.
- Безотходные технологические процессы и охрана окружающей среды в химической технологии, 340.8kb.
- Программа дисциплины по кафедре «Строительные и дорожные машины» Обогащение полезных, 211.66kb.
- Vii переработка химических продуктов термической переработки твердых горючих ископаемых, 256.07kb.
- Экологическое право гусейнов, 16.05kb.
- Программа спецкурса «Геология каустобиолитов» Для специальностей «геология», «геохимия»,, 110.58kb.
- Рабочая программа по дисциплине ен. В. 02. 02 «Малоотходные и безотходные технологии, 151.8kb.
- Положение Об организации утилизации и переработки бытовых и промышленных отходов, 89.39kb.
- Рекомендации межрегионального семинара-совещания и выставки «Оборудование и технологии, 126.8kb.
- 1 отделение профилактической медицины, 432.97kb.
Водород – это топливо будущего, потому что в долгосрочной перспективе человечество будет вынуждено перейти на возобновляемые источники энергии. Водород - самое экологически чистое топливо. Продуктом горения водорода является вода, что видно из простого уравнения этой химической реакции 2H2 +O2=2H2O. Принято считать, что экологически чистым водородное топливо является лишь в том случае, если для его производства была использована экологически чистая электроэнергия. Основное преимущество водорода как топлива в том, что транспорт работает почти бесшумно, а из выхлопной трубы вместо двуокиси углерода и прочих веществ, загрязняющих окружающую среду, выходит водяной пар без всяких примесей. Другое, не менее важное преимущество этого вида топлива - его безопасность
Топливный элемент— электрохимическое (преобразует химическую энергию в электрическую) устройство, подобное гальваническому элементу, но отличающееся от него тем, что вещества для электрохимической реакции подаются в него извне— в отличие от ограниченного количества энергии, запасенного в гальваническом элементе или аккумуляторе. Топливный элемент – это элемент, в котором окислительно-восстановительная реакция поддерживается непрерывной подачей реагентов (топлива, напр. водорода, и окислителя, напр. кислорода) из специальных резервуаров. Важнейшая составная часть электрохимического генератора, обеспечивающая прямое преобразование химической энергии в электрическую. В метанольных топливных элементах топливом является метанол или раствор метанола. В результате сгорания топлива образуется электроэнергия с КПД = 50..95% в зависимости от температуры, чем ниже, тем выше КПД.
Обычно в низкотемпературных топливных элементах используются: водород (метанол) со стороны анода и кислород на стороне катода (водородный элемент). В топливном элементе реагенты втекают, продукты реакции вытекают, и реакция может протекать так долго, как поступают в нее реагенты и сохраняется работоспособность самого элемента.
Первая батарея в промышленности — 1953 год, 1970 — запуск Шатла с генератором из ТЭ (КПД примерно 70%, носитель — метанол).
Топливные элементы не могут хранить электрическую энергию, как гальванические или аккумуляторные батареи.
СH3OH + H2O ↔ CO2 + 6H+ +4e-
Т
ипы топливных элементов:
- Твердооксидный топливный элемент
- Топливный элемент с протонообменной мембраной
- Обратимый топливный элемент
- Прямой метанольный топливный элемент
- Расплавной карбонатный топливный элемент
- Фосфорнокислый топливный элемент
- Щелочной топливный элемент
18. Получение уксусной и других органических кислот из метанола и синтез-газа.
Уксусная кислота - важнейший химический продукт, который широко используется в промышленности для получения сложных эфиров, мономеров (винилацетат), в пищевой промышленности и т.д. Мировое производство ее достигает 10 млн тонн в год. Получение уксусной кислоты до недавнего времени базировалось на нефтехимическом сырье. В Уокер-процессе этилен в мягких условиях окисляют кислородом воздуха до ацетальдегида в присутствии каталитической системы PdCl2 и CuCl2 . Далее ацетальдегид окисляется до уксусной кислоты:
CH2=CH2 + 1/2 O2→CH3CHO→CH3COOH
По другому методу уксусную кислоту получают при окислении н-бутана при температуре 200 ºC и давлении 50 атм в присутствии кобальтового катализатора.
Изящный Уокер-процесс - один из символов развития нефтехимии - постепенно замещается новыми методами, основанными на использовании угольного сырья. Разработаны способы получения уксусной кислоты из метанола:
CH3OH + CO →CH3COOH
Эта реакция, имеющая большое промышленное значение, является прекрасным примером, иллюстрирующим успехи гомогенного катализа. Поскольку оба компонента реакции - СН3ОН и СО - могут быть получены из угля, процесс карбонилирования должен стать более экономичным по мере роста цен на нефть. Существуют два промышленных процесса карбонилирования метанола. В более старом методе, разработанном на фирме BASF, использовали кобальтовый катализатор (СoI2+CoAl), условия реакции были жесткими: температура 250 °С и давление 300-500 атм. Реакция карбонилирования метанола была открыта учеными фирмы BASF в 1913 году. В 1960 году эта компания запустила первый завод, производящий уксусную кислоту этим методом Чистота получаемого продукта составляет 99,8%. В другом процессе, освоенном фирмой "Monsanto", реакцию проводили при более низких температурах (150-200 °С) и давлении (1-40 атм).
Это гомогенный процесс, в котором используются соли родия в качестве катализаторов, а также йодид-ионы в качестве промоторов. Важной особенностью метода является большая скорость, а также высокая селективность (99% по метанолу и 90% по CO). Этим способом получают чуть более 50% всей промышленной уксусной кислоты.
В процессе фирмы BP в качестве катализаторов используются соединения иридия.
Муравьина кислота( «безопасный консервант», E236).
О

Немецкие ученые доказали возможность получения из CO2. CO2 (г) +H2O(г) → НСООН.
Пропионовая кислота - бесцветная едкая жидкость с резким запахом. В природе пропионовая кислота найдена в нефти, образуется при брожении углеводов. В промышленности её получаю карбонилированием этилена по реакции Реппе: CH2=CH2 + CO2 → CH3CH2COOH. Применяется в производстве гербицидов, лекарственных средств, душистых веществ, пластмасс, ПАВ. Препятствует росту плесени и некоторых бактерий, консервант.
19. Изонианаты. Бесфосгенное производство
Изоцианаты — органические соединения, содержащие функциональную группу —N=C=O.
Наиболее распространённый метод синтеза изоцианатов - реакция аминов с фосгеном (фосгенирование аминов), реакция идёт в среде инертного растворителя через промежуточное образование карбамоилхлоридов:
RNH2 + COCl2 → RNHCOCl + HCl
RNHCOCl → RNCO + HСl. Этот метод является и основным промышленным методом синтеза изоцианатов.
Другой метод синтеза изоцианатов, использующийся в промышленности - термическое разложение карбаматов:
R'NHCOOR → R'NCO + ROH
Карбаматы, в свою очередь, могут быть получены реакцией соответствующего амина с мочевиной и спиртом:
R'NH2+ NH2CONH2+ ROH → R'NHCOOR + 2NH3
Такой «бесфосгенный» метод в промышленности используется для синтеза алифатических изоцианатов, в частности, гексаметилендиизоцианата.
Изоцианаты, гидролизующиеся in situ до аминов, также образуются в качестве промежуточных продуктов в перегруппировках Гофмана, Курциуса и Лоссена и могут быть выделены при проведении реакции в инертных растворителях:
RCONH2 + Hal → RCONHCl → RCNO + HHal (Реакция Гофмана)
RCOCl + NaN → RCN3 → RCNO + N2 (Реакция Курциуса)
RCONHOR' + OH¯ → R'CNO + RCOO ̄(Реакция Лоссена)
Изоцианаты входят в состав ряда промышленных материалов , известных под названием полиуретанов. К наиболее применяемым в настоящее время изоцианатам относятся 2,4-толуоловый диизоцианат, толуол 2,6-диизоцианат и дифенилметан 4,4'-диизоцианат. Реже используются гексаметиленовый диизоцианат и 1,5-нафтилен диизоцианат .
Изоцианаты самопроизвольно вступают в реакцию с соединениями, содержащими активные атомы водорода, которые мигрируют к азоту . Соединения, в состав которых входят гидроксильные группы, самопроизвольно образуют сложные эфиры замещенной диоксида углерода или уретаны.
Основным применением изоцианатов является синтез полиуретанов в промышленных продуктах. Благодаря своей стойкости и прочности, 2,4-толуол диизоцианат используется в покрытиях самолетов, автоцистерн и автоприцепов. Метилен- бис -4-фенилизоцианат применяется для склеивания резины и вискозы или нейлона, а также для производства полиуретановых лаковых покрытий, которые могут использоваться в некоторых деталях автомобилей, и для производства лакированной кожи. 2,4-Толуоловый диизоцианат используется в полиуретановых покрытиях, в шпатлевке и отделочном материале для полов и деревянных изделий, в краске и бетонных заполнителях. Он также применяется для производства пенополиуретанов и полиуретановых эластомеров в уплотнениях для керамических труб и материалах с покрытием. Циклогексан представляет собой структурообразующее вещество при изготовлении зубоврачебных материалов, контактных линз и медицинских адсорбентов. Он также входит в состав автомобильной краски.
Изоцианаты вызывают раздражение кожи и слизистых оболочек, причем воздействие на кожу колеблется от местного зуда до достаточно широко распространенной экземы.
20 Переработка сопутствующего газа этан в этилен ( пропан в пропилен и бутан в бутелен). Олефлекс-процесс.
Попутный газ является побочным продуктом нефтедобычи (метан, этан, пропан, бутан). Нефтяной попутный газ – это смесь газов и парообразных углеводородных и не углеводородных компонентов, выделяющихся из нефтяных скважин и из пластовой нефти при её сепарации. Обычно нефтяной попутный газ рассматривается как источник cыpья для пpoизвoдcтва pяда xимичеcкиx продуктов, источник получения дешевой электрической и тепловой энергии. Переработка этан-бутановой фракции ПНГ и этилена первичного пиролиза проводится олигомеризацией, дегидроциклизацией.
Процесс «Олефлекс» представляет собой технологию дегидрирования легких парафинов, лицензированную фирмой UOP. В настоящее время восемь установок «Олефлекс» производят из пропана более 600 тыс. т/год пропилена для полимеризации и более 1,4 млн. т/год изобутилена из бутана. Продуктовый пропилен используется для производства полипропилена и акрилонитрила, а изобутилен — для производства более 2,2 млн. т/год метилтретбутилового эфира (МТБЭ). Процесс «Олефлекс» можно представить в виде трех отдельных блоков: реактор, отбор продукта и блок регенерации катализатора. В процессе UOP/Хайдро природный газ преобразуется в основном в этилен и пропилен. Это экономичный способ прямой конверсии метана в олефины для последующей полимеризации. При использовании технологической схемы не требуются дорогостоящие колонныразделения этилена/этана и пропилена/пропана, в процессе образуется ограниченное количество побочных продуктов по сравнению с паровым крекингом, что упрощает аппаратурное оформление секции отбора продуктов.
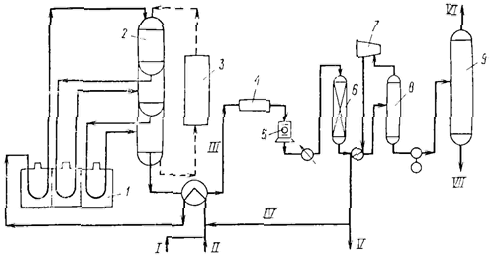
Схема процесса дегидрирования парафиновых углеводородов С3 - С4 (процесс олефлекс фирмы ЮOП):
1- печи для подогрева сырья; 2 - наборные реакторы; 3 - секция непрерывной регенерации катализатора; 4- воздушный холодильник: 5- компрессор; 6 - осушитель; 7 - турбоэкспандер; 8 - сепаратор; 9- отпарная колонна легких фракций; I - свежее сырье; II - возвратное сырье; III - контактный газ; IV - возвратный водород; V - газ. содержащим до 90% водорода; VI - легкие фракции; VII - целевые продукты на разделение.
21. Переработка легких углеводородов в бензин в ароматические углеводороды. Циклар — процесс Цеоформинг.
Процесс «Циклар» разработанный и реализованный компанией «British Petroleum» и предназначенный для переработки пропан-бутановой фракции. Процесс «Цеоформинг» разработанный фирмой «Цеосит» г. Новосибирск и реализованный фирмой «Лурги» предназначенный для переработки нафты в высокооктановый бензин. Следует отметить, что попытки осуществить промышленную реализацию реакции каталитической ароматизации низших парафинов, С2 - С4, сталкивались со значительными трудностями. Реакция протекает при достаточно высоких температурах 500 — 550 ºС, что приводило к быстрому закоксовыванию катализатора и, как следствие, потери им активности. Для поддержания высокой активности катализатора компания «British Petroleum» использовала в установке «Циклар» движущийся слой катализатора.
Процесс «Циклар» предназначен для переработ ки сжиженных газов непосредственно в жидкие ароматические углеводороды за один проход. Технология является срав нительно новой и позволяет расширить
использование сжиженных газов для производства ценных ароматических соединений (бензол, толуол и ксилол), используемых в нефтехимической про мышленности. При эксплуатации установки в режи ме низкого давления суммарный выход ароматических соединений возрастает с 61 % масс. для свежего сырья, состоящего
полностью из пропана, до 66 % масс. — для бутанового сырья, с соответствую щим снижением количества вырабаты ваемого топливного газа. Для сырья, со стоящего из смеси пропана и бутана, вы ходы продуктов могут быть рассчитаны с помощью линейной интерполяции. Из бутанового сырья получают продукт, ко торый содержит меньше бензола и боль ше ксилолов по сравнению с продуктом, полученным из пропана. Жидкий про
дукт, полученный как из пропанового, так и из бутанового сырья, содержит примерно 91 % бензола, толуола и ксилолов, 9 % тяжелых ароматических соединений.
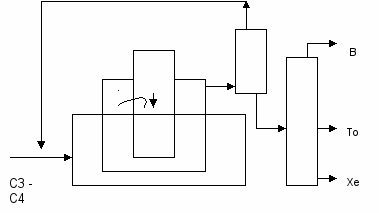
«Цеоформинг» - процесс каталитической переработки низкооктановых бензиновых фракций (прямогонные бензиновые фракции нефтей и газовых конденсатов, газовые бензины и другие фракции, выкипающие в интервале температур 35-200°С) в высокооктановые неэтилированные автобензины на цеолитсодержащих катализаторах.
В случае использования в качестве исходного сырья нефтей и газовых конденсатов переработка осуществляется на одной установке в две стадии:
- ректификация сырья с получением сортного дизельного топлива;
- производство высокооктановых бензинов с октановыми числами от 80 до 95 ИМ процессом «Цеоформинг».
«Цеоформинг» обеспечивает производство высокооктановых бензинов от АИ-80 до АИ-95, удовлетворяющих требованиям ГОСТ 2084-77 и ГОСТ Р 51105-97 по всем показателям без введения каких-либо добавок и дополнительного компаундирования. Выходы товарных бензинов из низкооктановых бензиновых фракций составляют 70-85%.
В случае применения на малотоннажных установках процесс «Цеоформинг» имеет ряд существенных преимуществ перед традиционными процессами:
- Катализаторы разработаны на основе экологически чистой системы, не содержащей дорогостоящих благородных и тяжелых металлов;
- Катализатор не чувствителен к повышенному содержанию серы, не требуется гидроочистки сырья от серы и азотсодержащих соединений;
- В результате протекающих реакций превращения сернистых соединений сырья, в том числе демеркаптанизации (процесс обессеривания сжиженных углеводородных газов и дезодорации высококипящих углеводородных бензиновых, керосиновых, дизельных фракций и нефтей), содержание общей серы в жидких продуктах не превышает 0.02-0.05%;
- Процесс «Цеоформинг» позволяет перерабатывать широкий спектр углеводородного сырья (Tк.к. = 120-250°С);
- В процессе «Цеоформинг» не используется водород и связанное с ним компрессорное оборудование;
- Процесс проводится при сравнительно низких температурах (340-450°С) и давлениях (0.5-1.5 МПа), что на 20-30% уменьшает его энергоемкость;
- Получаемые бензины более адаптированы к экологическим требованиям благодаря значительно меньшему содержанию ароматических углеводородов и низкому содержанию бензола, что отвечает современным стандартам;
- Получаемые бензины не требуют компаундирования;
- Процесс рентабелен при мощности установки от 5 000 т/год по сырью.
В результате указанных преимуществ капитальные затраты и эксплуатационные расходы значительно снижаются.
22.Переработка двуокиси углерода. Мочевина. Биологически разлагаемые полимеры.
CO2 +2NH3 → (NH2)2CO (мочевина)
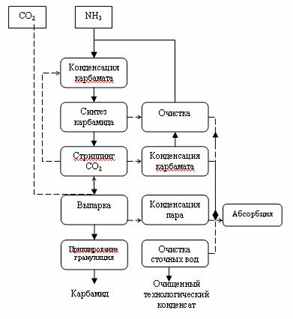
Аммиак и диоксид углерода превращаются в карбамид через карбамат аммония при давлении около 140 бар и температуре 180-185°C. Конверсия аммиака достигает 41%, углекислого газа – 60%. Непрореагировавшие аммиак и диоксид углерода поступают в стриппер, при этом СО2 выступает в роли стиппер-агента. После конденсации СО2 и NH3 идут на рецикл и возвращаются в процесс синтеза. Теплота конденсации используется для выработки пара, поступающего в компрессор СО2. |
В промышленности мочевина синтезируется по реакции Базарова из аммиака и углекислого газа,поэтому производства мочевины совмещают с аммиачными производствами.Мочевина является крупнотоннажным продуктом, используемым, в основном, как азотное удобрение (содержание азота 46 %) и выпускается в этом качестве в устойчивом к слеживанию гранулированном виде. Другим важным промышленным применением мочевины является синтез мочевино-альдегидных (в первую очередь мочевино-формальдегидных) смол, широко использующихся в качестве адгезивов в производстве древесно-волокнистых плит (ДВП) и мебельном производстве. Производные мочевины— эффективные гербициды.
Мочевина также применяется для очистки дымовых газов тепловых электростанций, котельных, мусоросжигательных заводов, двигателей внутреннего сгорания и т.п. от оксидов азота. Над дымовыми трубами некоторых химических предприятий можно увидеть рыжий «лисий хвост», он появляется в результате выбросов оксида азота NO, который окисляется кислородом воздуха до ярко окрашенного диоксида азота NO2:
NO + O2 = 2NO2. Этот оксид реагирует с водой с образованием сильной азотной кислоты HNO3, которая также может входить в состав кислотных дождей:
3NO2 + H2O = 2HNO3 + NO
(NH2)2CO + H2O → 2NH3 + CO2 (при повышенной температуре)
3NO + 2NH3 → N2 + 3H2O
Карбамид зарегистрирован в качестве пищевой добавки E927b. Используется, в частности, в производстве жевательной резинки.
Мочевина является пластификатором в биоразлагаемом топливе, относится к добавкам, легко усваиваемым микроорганизмами. Плистификаторы - вещества, которые вводят в состав полимерных материалов для придания (или повышения) эластичности и (или) пластичности при переработке и эксплуатации.
23. Моторное топливо из природовоспроизводимого сырья. Биоэтанол — как экологически чистая добавка в моторное топливо. Дизельное топливо из рапсового масла.
Биоэтанол— обычный этанол, получаемый в процессе переработки растительного сырья для использования в качестве биотоплива. Мировое производство биоэтанола в 2005 составило 36,3 млрд литров, из которых 45 % пришлось на Бразилию и 44,7 % — на США. Этанол в Бразилии производится преимущественно из сахарного тростника, а в США — из кукурузы. Производство этанола из тростника на сегодняшний день экономически более выгодно, чем из кукурузы. Сырьём для производства биоэтанола также могут быть различные с/х культуры с большим содержанием крахмала или сахара: маниок, картофель, сахарная свекла, батат, сорго, ячмень и т.д. Тростник у нас не растет, лучшим климатом для производства сахарного тростника обладает Перу, страны Карибского бассейна. Этанол можно производить в больших количествах из целлюлозы. Сырьём могут быть различные отходы сельского и лесного хозяйства: пшеничная солома, рисовая солома, багасса сахарного тростника, древесные опилки и т. д. Производство этанола из целлюлозы пока экономически не рентабельно.
Получение.
Получается спиртовым брожением под действием ферментов микроорганизмов(реакция довольно сложная):
С6H12O6 → 2C2H5OH + 2CO2
В результате брожения получается раствор, содержащий не более 15 % этанола, так как в более концентрированных растворах дрожжи обычно гибнут. Полученный таким образом этанол нуждается в очистке и концентрировании, обычно путем дистилляции.
Современная промышленная технология получения спирта этилового из пищевого сырья включает следующие стадии:
- подготовка и измельчение крахмалистого сырья — зерна (прежде всего — ржи, пшеницы), картофеля, кукурузы и т. п.;
- ферментация;
- брагоректификация. Осуществляется на разгонных колоннах.
Отходами бродильного производства являются барда и сивушные масла. Барда используется для производства кормов.
Этанол является менее «энергоплотным» источником энергии чем бензин, т.е. пробег машин, работающих на Е85 («E» - Ethanol; смесь 85% этанола и 15% бензина) составляет 75% от пробега стандартных машин. Обычные автомобильные ДВС не могут работать на Е85, хотя прекрасно работают на Е10. На «настоящем» этаноле могут работать только машины «Flex-Fuel» (автомобиль с многотопливным двигателем). Автозаправки в Бразилии предлагают на выбор либо Е20 (иногда Е25) под видом обычного бензина, либо «acool» Е100, азеотроп этанола (96 % С2Н5ОН и 4 % (по весу) воды). Этанол дешевле бензина.
Е5, Е7, Е10 — смеси с низким содержанием этанола (5, 7 и 10 весовых процентов, соответственно), наиболее распространённые в наши дни. В этих случаях добавка этанола не только экономит бензин путём его замещения, но и позволяет удалить вредную оксигенирирующую добавку МТБЭ.
Е100 — формально 100 % этанол, однако в силу того, что этанол гигроскопичен, получение и использование этанола без остаточной концентрации воды невыгодно. Поэтому в большинстве случаев под Е100 подразумевают стандартную азеотропную смесь этанола. Путём обычной дистилляции невозможно получить более высокую концентрацию этанола.
Биоэтанол как топливо нейтрален в качестве источника парниковых газов. Он обладает нулевым балансом диоксида углерода, поскольку при его производстве путём брожения и последующем сгорании выделяется столько же CO2, сколько до этого было связано из атмосферы использованными для его производства растениями. Содержащийся в этаноле кислород, позволяет более полно сжигать углеводороды топлива. 10 % содержание этанола в бензине позволяет сократить выхлопы аэрозольных частиц до 50 %, выбросы СО — на 30 %.
Биодизель — биотопливо на основе растительных или животных жиров (масел), а также продуктов их этерификации.
Растительное масло переэтерифицируется метанолом, реже или этанолом или изопропиловым спиртом (приблизительно в пропорции на 1 т масла 200 кг метанола +гидроксид калия или натрия) при температуре 60°С и нормальном давлении. Хранить более 3-х месяцев не рекомендуется, начинает разлагаться.
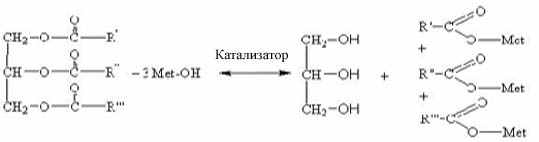
Применяется на автотранспорте в чистом виде и в виде различных смесей с дизельным топливом. В США смесь дизельного топлива с биодизелем обозначается буквой B; число после буквы означает процентное содержание биодизеля. В2 — 2 % биодизеля, 98 % дизельного топлива. В100 — 100 % биодизеля. Применение смесей не требует внесения изменений в двигатель.
Цетановое число:
-для минерального дизтоплива 42-45,
-для биодизеля не менее 51.
Сырьём для производства биодизеля служат жирные, реже — эфирные масла различных растений или водорослей. Также применяется отработанное растительное масло, животные жиры, рыбий жир и т. д.
80% европейского биодизеля производится из рапсового масла.
В России не существует единой государственной программы развития биодизельного топлива, но создаются региональные программы, например Алтайская краевая целевая программа «Рапс — биодизель». В Липецкой области создана Ассоциация Производителей Рапсового Масла. Планируется строительство заводов по производству биодизеля в: Липецкой области, Татарстане, Алтайском крае, Ростовской области, Волгоградской области, Орловской области,Краснодарском крае, Омской области.
ОАО «РЖД» в 2006—2007 годах провела испытания биодизеля из рапсового масла на тепловозах депо Воронеж-Курский Юго-Восточной железной дороги. Представители РЖД заявили о готовности использовать биодизель в промышленных масштабах на своих тепловозах. Разрешено 5% содержание в автомобильном топливе
Биодизель, как показали опыты, при попадании в воду не причиняет вреда растениям и животным. Кроме того, он подвергается практически полному биологическому распаду: в почве или в воде микроорганизмы за 28 дней перерабатывают 99 % биодизеля, что позволяет говорить о минимизации загрязнения рек и озёр. Сокращение выбросов СО2. При сгорании биодизеля выделяется ровно такое же количество углекислого газа, которое было потреблено из атмосферы растением, являющимся исходным сырьём для производства масла, за весь период его жизни. Биодизель в сравнении с обычным дизельным топливом почти не содержит серы.
У биодизеля высокая температура воспламенения. Точка воспламенения для биодизеля превышает 100 °С, что позволяет назвать биотопливо относительно безопасным веществом.
Еще один плюс -побочным продуктом производства биодезеля является глицерин.
Срок службы двигателя при работе на биодизеле увеличивается, т.к. тот имеет хорошие смазочные характеристики.