Безотходные технологические процессы и охрана окружающей среды в химической технологии твердых горючих ископаемых
Вид материала | Лекция |
- Вопрос Катализаторы как инструмент экологической безопасности переработки горючих ископаемых, 707.41kb.
- Программа спецкурса «Геология каустобиолитов» Для специальностей «геология», «геохимия»,, 110.58kb.
- Тема : «Загрязнение и охрана окружающей среды», 38.66kb.
- Резюме Ищу работу инженера-химика-эколога Ткач Яна Михайловна, 15.95kb.
- Рабочая программа по дисциплине Ф. 13 «Системный анализ процессов химической технологии», 148.25kb.
- В. Н. Масляев охрана окружающей среды учебное пособие, 1544.73kb.
- Практикум по экологическому мониторингу окружающей среды Учебное пособие, 949.79kb.
- Рабочая программа элективного курса «Химия и охрана окружающей среды», 82.96kb.
- Рабочая программа дисциплины компьютерные моделирующие системы в химической технологии, 239.63kb.
- Программа породненных университетов и кафедр юнеско кафедра юнеско, 207.32kb.
ЛЕКЦИЯ 2
БЕЗОТХОДНЫЕ ТЕХНОЛОГИЧЕСКИЕ ПРОЦЕССЫ
И ОХРАНА ОКРУЖАЮЩЕЙ СРЕДЫ В ХИМИЧЕСКОЙ ТЕХНОЛОГИИ ТВЕРДЫХ ГОРЮЧИХ ИСКОПАЕМЫХ
1.3. Охрана окружающей среды в коксохимическом производстве
В существующих технологических процессах подготовки и коксования угля, улавливания и переработки химических продуктов образуются отходы, количество которых составляет (в % от массы сухой угольной шихты): выбросы в атмосферу (пыль, углеводороды, оксиды углерода, серы и азота и т.п.) – 0,7–0,8; фенолсодержащие сточные воды – 30–40; отходы химических цехов (фусы, кислые смолки, кубовые остатки, полимеры) – 0,25–0,28. Кроме того, как уже отмечалось, на углефабриках образуются отходы углеобогащения в количестве до 35–50% от массы готовой шихты.
1.3.1. Пути сокращения количества сточных вод и их очистка
Количество сточных вод на большинстве коксохимических заводов страны составляет 0,35–0,4 м3/т сухой шихты, или 0,45– 0,53 м3/г кокса. На рисунке 1 показана схема формирования сточных вод на коксохимическом предприятии. Как видно из схемы, большую часть стоков составляет надсмольная вода после аммиачных колонн (более 60%). Важно также и то, что общее количество воды в 3–4 раза превышает количество образующейся при коксовании избыточной воды (влага шихты + пирогенная вода). Это свидетельствует о том, что большие количества воды подаются в систему дополнительно в результате применения соответствующих технических решений, а также из-за отсутствия в отрасли безводных технологий, поэтому существуют резервы сокращения количества сточных вод.
Представление о составе сточных вод различных цехов дают данные таблицы 1.
Таким образом, фенольные сточные воды являются самыми загрязненными и нуждаются в тщательной очистке. Наибольшее внимание уделяется очистке сточных вод от фенолов, что обусловлено их токсичностью, а также способностью образовывать при хлорировании воды хлорфенолы, обладающие повышенной токсичностью и резким неприятным запахом даже при низких концентрациях. Кроме того, коксохимические фенолы (точнее, метилфенолы – крезолы, которые до недавнего времени производились только на коксохимических предприятиях) представляют собой ценное сырье. Фенолы сточных вод коксохимических предприятий имеют следующий состав (в %): собственно фенол – 60–65, крезолы – 30–35, ксиленолы – 5.
Сточные воды, получаемые при полукоксовании или энерготехнологической переработке углей, отличаются следующим составом: общее содержание фенолов значительно выше– 2,6 г/дм3, в том числе 60–70% фенола и его гомологов и 30–40% двухатомных фенолов: пирокатехина, резорцина и их гомологов. В связи с тем, что двухатомные фенолы используются в качестве сырья для специальных, особенно ценных, синтетических смол (эпоксидные, полиакрилатные, поликарбонатные, некоторые виды фенолоформальдегидных смол), а также для изготовления синтетических дубителей и лекарственных веществ, выделению их из этих вод уделяется особое внимание.
Для извлечения фенолов из сточных вод используют в основном два метода: перегонку с паром и экстракцию селективными растворителями.
Принципиальная схема установки пароциркуляционного обесфеноливания представлена на рисунке 2.
Таблица 1. Состав сточных вод различные цехов химического производства
Содержание, г/дм3 | Источники воды | ПДК для водоемов, мг/дм3 | |||||
после аммиачной колонны | из цикла конечного охлаждения | сепараторная бензольного отделения | цех ректификации | разгонка смол | общий сток фенольных вод | ||
Фенолы | 0,3–1,3 | 0,1 2,0 | 0,2–0,4 | 0,2–0,3 | 2–5 | 0,2–0,4 | 0,001 |
Аммиак летучий | 0,05–0,2 | 0,01–0,1 | 0,03–0,05 | 0,05–0,1 | 0,5 | 0,3 | 0,1 |
связанный | 0,1–0,5 | 0,1–0,2 | 0,1–0,2 | 0,02 | 0,2 | 0,6 | 0,1 |
Сероводород | 0,02–0,05 | 0,1 | 0,1 | 0,01 | 0,05 | 0,05 | 1 |
Тиоцианат-ион | 0,4–0,6 | 0,1–0,2 | 0,1 | Нет | 0,05 | 0,2–0,4 | 1500 |
Цианид-ион | 0,005–0,02 | 0,1 | 0,15 | Следы | 0,03 | 0,02–0,04 | 0,2 |
БПК, мг О2 на 1 дм3 | 1600 | 2000–3000 | 2000 | 1000 | 2500–7000 | 1000–3000 | Не более 2,0–6,0 |
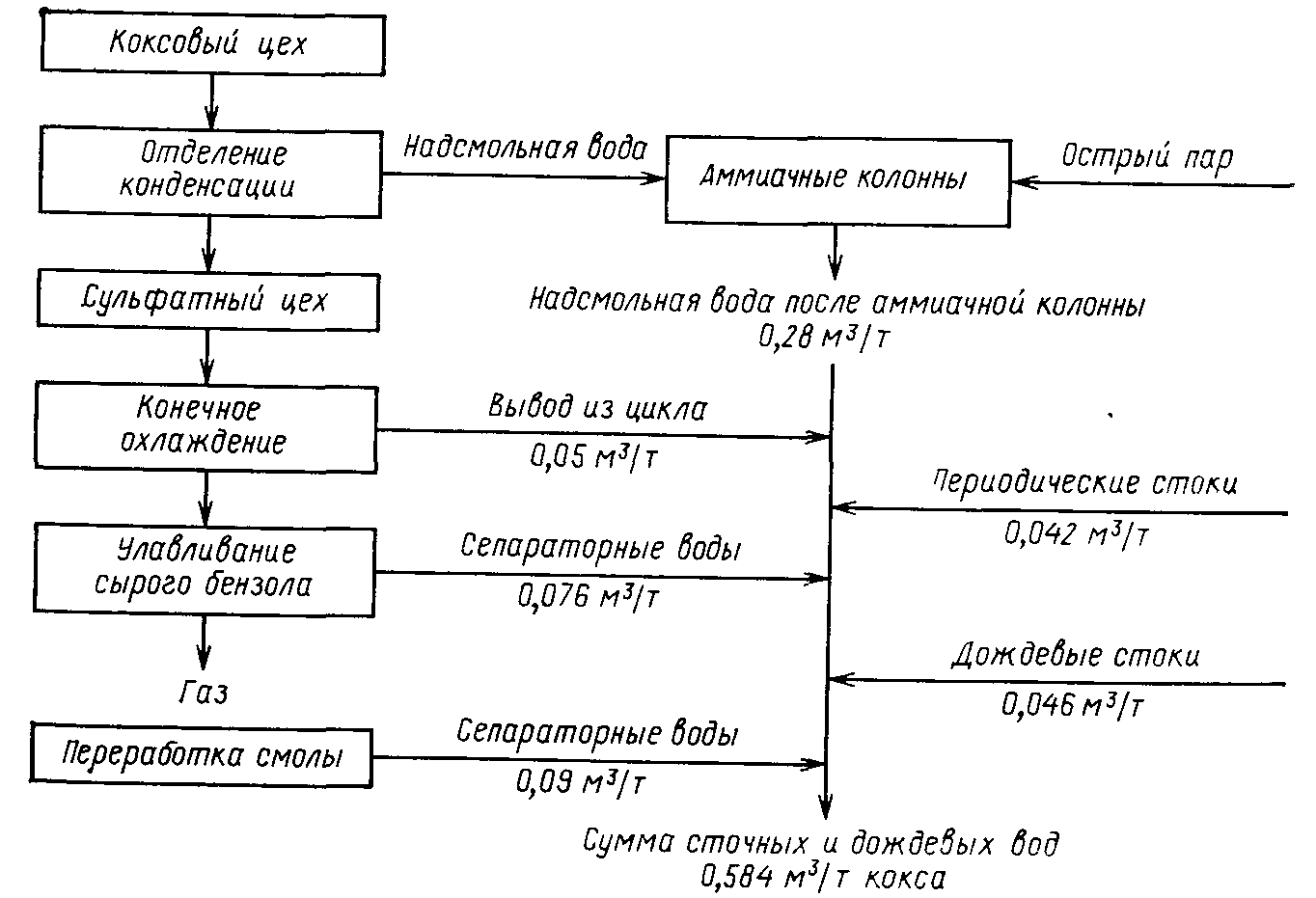
Рис. 1. Схема формирования сточных вод на коксохимическом производстве
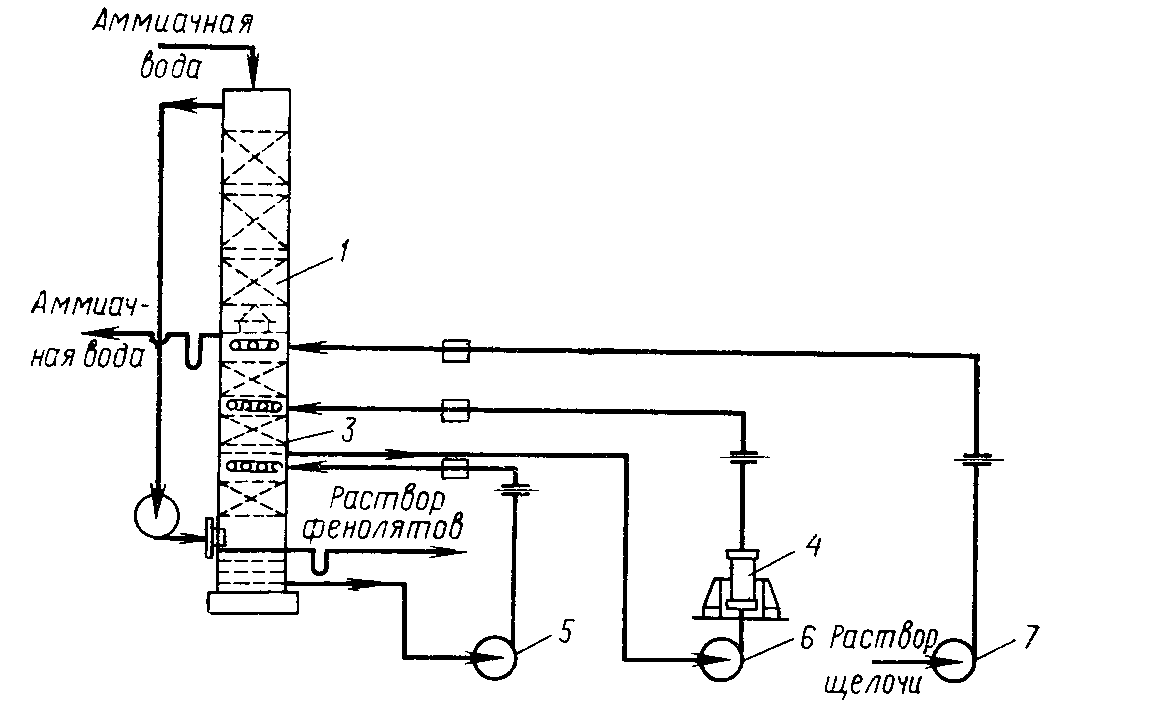
Рис. 2. Установка пароциркуляционного обесфеноливания сточных вод:
1 – верхняя секция скруббера; 2 – вентилятор; 3 – нижняя секция скруббера; 4 – подогреватель; 5–7 – насосы
Надсмольная вода после аммиачных колонн поступает на верхнюю секцию 1 обесфеноливающего скруббера, затем стекает по насадке и взаимодействует с циркулирующим в аппарате паром. При этом происходит десорбция фенолов. Пар с помощью циркуляционного вентилятора 2 нагнетается в нижнюю секцию 3 того же скруббера. Здесь пар промывается сначала циркулирующим раствором фенолятов натрия, а затем – раствором 8%-ного NaOH. При этом фенолы экстрагируются щелочью, а обесфеноленный пар отводится через паровой патрубок в верхнюю секцию, где он десорбирует фенолы из новой порции надсмольной воды. Циркулирующий в нижней части скруббера раствор фенолятов проходит подогреватель 4, с помощью которого в систему подводится тепло для компенсации тепловых потерь через стенки аппарата и паропровода.
Рассмотрим закономерности и особенности работы этой системы. При температуре 102°С коэффициент распределения фенолов между паровой и жидкой фазой К = Сп/Сж = 2, где Сп и Сж – концентрации фенолов в паровой и жидкой фазах, масс. %.
Минимальный расход сухого пара при очистке воды, содержащей 0,6–1,3 г/дм3 фенолов, составляет 1400 м3/м3 воды при 102°С. В связи с тем что поверхность насадки секции десорбера конечна, а в поступающем из нижней секции паре содержится некоторое количество фенолов, фактический расход. пара составляет 1500–2200 м3/м3 воды.
Таким образом, в аппарате циркулирует значительное количество пара – 60–80 тыс. м3 (при производительности аппарата по воде 30–40 м3/ч), поэтому диаметр скруббера должен составлять 4,5–5,5 м, а мощность привода вентилятора – превышать 100 кВт. Степень обесфеноливания в секции десорбции равна 70–96% и зависит от степени обесфеноливания пара в нижней секции аппарата. Использование традиционной насадочной нижней секции (см. рис. 9.2) обеспечивает обесфеноливание воды на 65–70% (до остаточного содержания фенолов 0,25–0,3 г/дм3).
Как следует из изложенного, эффективность очистки зависит от работы нижней секции обесфеноливающего скруббера, где для хемосорбции фенолов из пара применяют раствор NaOH. Образующаяся при этом соль слабой кислоты (константы диссоциации фенола и его гомологов при 25°С равны соответственно: для фенола – 1,15·10-10, о-крезола – 0,63·10–10, п-крезола – 0,98·10–10) и сильного основания будет подвергаться гидролизу. В соответствующих условиях работы обесфеноливающего скруббера (102–105°С) этот процесс усиливается (с. 325). Единственным средством увеличения полноты извлечения фенолов из пара и подавления гидролиза может быть применение избытка щелочи.
Таким образом, высокая эффективность пароциркуляционного обесфеноливания достигается только при непрерывной подаче свободного от фенолов раствора щелочи на верхний ярус насадки нижней секции скруббера.
При использовании насадочного аппарата непрерывная подача оказывается невозможной из-за несоответствия количества раствора щелочи, который нужно подавать на орошение, и условий эффективной работы насадочного, аппарата.
Для иллюстрации произведем расчет. Необходимо извлечь фенолы из сточной воды, содержащей 1,5 г/дм3 фенолов. Расход вод 30 м3/ч. Для извлечения содержащихся в этой воде фенолов (1,5·30 = 45 кг/ч) при двукратном избытке щелочи и применении 10%-ного раствора потребуется 45·(40·2/94)·10 = 382 кг/ч раствора.
В то же время для очистки 30 м3/ч воды требуется скруббер диаметром 4,5 м и сечением 15,8 м2. Насадочные аппараты работают эффективно при плотности орошения не менее 1,2 м3/м2 сечения насадки. Следовательно, для обеспечения нормальной работы аппарата необходимо подавать не менее. 20 м3 раствора щелочи, т.е. почти в 60 раз больше расчетного.
На некоторых заводах используют периодическую подачу щелочи на верхний ярус насадки (насос включается каждые 15 мин и работает некоторое время). При этом кратковременно обеспечивается орошение насадки щелочью, но затем, когда подача щелочи прекращается, полнота улавливания фенолов резко ухудшается.
Единственным средством ликвидации существующего противоречия является применение аппаратов с тарелками в. нижней секции. Тарелки стабильно работают при небольшом орошении (особенно колпачковые и клапанные). Аппарат такого типа позволяет извлекать фенолы из сточных вод на 95–99% благодаря непрерывной подаче щелочи и созданию на верхних тарелках нижней секции аппарата многократного избытка щелочи.
На работу обесфеноливающего скруббера существенно» влияет степень десорбции аммиака в аммиачной колонне. Дело в том, что «летучий» аммиак в надсмольной воде находится в виде бикарбоната и гидросульфида аммония. При недостаточной полноте десорбции аммиака они также не полностью удаляются в аммиачной колонне. В результате происходит их десорбция в верхней части скруббера. Однако как угольная кислота, так и сероводород–более сильные кислоты (КIа соответственно 10–7 и 10–9), чем фенол. Поэтому они взаимодействуют со щелочью, образуя нелетучие гидрокарбонат и гидросульфид натрия. В результате увеличивается общий расход щелочи или уменьшается полнота десорбции фенолов из надсмольной воды. Для удовлетворительной работы обесфеноливающего скруббера нужно, чтобы содержание летучего аммиака в поступающей воде было не выше 0,1 г/дм3.
Пароциркуляционное обесфеноливание отличается простотой эксплуатации. Установка включает небольшое число аппаратов. Обесфеноливаемая вода не соприкасается с реагентами. Затраты на обесфеноливание сточных вод этим методом при хорошо налаженном технологическом режиме компенсируются стоимостью полученных фенолятов, если начальная концентрация фенолов в очищаемых водах не менее 1,8 г/дм3.
Недостаток пароциркуляционного обесфеноливания состоит в том, что в скруббер поступает надсмольная вода, из которой уже десорбирована часть фенолов. Эти фенолы отгоняются вместе с аммиаком в аммиачной колонне, и, попадая либо в пиридиновые основания, либо в коксовый газ, они не могут быть утилизированы.
Надсмольная вода после обесфеноливающего скруббера, как правило, передается на установку биохимического обесфеноливания. На ряде предприятий содержание фенолов в воде составляет менее 1 г/дм3, поэтому там не проводится пароциркуляционное обесфеноливание и надсмольная вода направляется после аммиачных колонн непосредственно на биохимические установки.
В промышленности полукоксования и отчасти в коксохимической пользуются экстракционным обесфеноливанием сточных вод. При этом важной задачей является выбор экстрагента. Последний должен быть дешевым, доступным, практически нерастворимым в воде, стабильным, относительно мало летучим и обладать высоким коэффициентом распределения. Как известно, общей особенностью процессов экстракции является стабильность коэффициента распределения, который численно равен (для обесфеноливания воды):
Красп = Cp/Cв
где Ср, Св – равновесные концентрации фенола в растворителе и воде.
Чем выше Красп, тем меньший объем растворителя необходим для контакта с водой, тем больше будет концентрация фенолов в экстракте и тем меньшими будут затраты на регенерацию растворителя и выделение фенолов.
Любые экстракционные схемы включают стадию регенерации растворителя. При этом для регенерации может быть использована либо отгонка растворителя от фенолов, либо экстракция фенолов из растворителя раствором щелочи. Первый прием можно применять только при высокой концентрации фенолов в растворителе (не менее 15–20%).
Выбор схемы регенерации оказывает решающее влияние на экономику процесса из-за высокой стоимости растворителей. В таблице 2 приводятся некоторые характеристики используемых растворителей.
Таблица 2. Характеристика растворителей для извлечения фенолов
Растворители | Красп | Содержание фенолов при насыщении*, % | Условия применения и ограничения |
Бензол | 2,2 | 1,1 | Коксохимия, регенерация щелочью |
Ацетаты | 36–50 | 18–25 | Очистка сточных вод, свободных от аммиака (из-за опасности гидролиза) |
Простые эфиры (диизопропиловый эфир и др.) | 18–25 | 9–13 | Любые сточные воды, регенерация щелочью |
Высшие спирты (С6–С15) | 15–20 | 7–10 | То же |
* Содержание фенолов в воде 5 г/л (максимальное).
Таким образом, для экстракции фенолов в коксохимической промышленности могут применяться бензол и другие углеводороды, простые эфиры и спирты. Применение сложных эфиров не может быть рекомендовано вследствие их гидролиза под действием аммиака или солей аммония и значительных потерь экстрагента. Регенерация с помощью ректификации применяется только при использовании сложных эфиров.
Применение сложных и простых эфиров приобретает особое значение при экстракции двухатомных фенолов, хорошо растворимых в воде. Коэффициенты распределения их между экстрагентом и водой много меньше, чем, например, у фенола.
На коксохимических предприятиях за рубежом преимущественно пользуются бензолом, хотя он обладает и многими недостатками (летучесть, частичная растворимость в воде), из-за его доступности. В последнее время вследствие токсичности бензола его заменяют гомологами бензола или высшими спиртами.
Как правило, экстрагенты подаются в больших количествах, чем это определяется условиями равновесия, и содержание фенолов в растворителе в 1,5–2 раза меньше максимально возможного. Экстракция–физический процесс, поэтому высокая полнота экстракции фенолов и необходимое насыщение растворителя достигается только при использовании многоступенчатых (5–8 теоретических ступеней) противоточных аппаратов или установок.
Для этой цели применяются аппараты различных типов, включая насадочные колонны, ротационно-дисковые экстракторы, колонны с перфорированными тарелками, инжекционные аппараты, пульсационные колонны с пульсацией жидкости и пульсацией сит.
Общим недостатком этих конструкций является сравнительно малая скорость встречных потоков, определяемая разностью плотностей и составляющая 0,02–0,05 м/с, что приводит к необходимости увеличения диаметра аппарата. По этой же причине в насадочных или тарельчатах аппаратах оказывается невысокой интенсивность массообмена. Пульсационные аппараты и аппараты с мешалками позволяют увеличить интенсивность массообмена, но при этом рост интенсивности ограничивается трудностью разделения образующихся эмульсий вода–растворитель. Это противоречие было разрешено при использовании центробежных противоточных экстракторов.
В центробежном поле интенсивность массообмена возрастает пропорционально фактору разделения, который в 100–500 раз превышает напряженность поля земного тяготения. Соответственно увеличивается и скорость встречного движения и расслоения фаз. Центробежные экстракторы отличаются компактностью. Так, для установки производительностью по воде 30 м3/ч требуются либо центробежные экстракторы с ротором диаметром 1250 мм и длиной 1000 мм, либо экстракционные колонны высотой 20 м и диаметром 2 м. Суммарное количество бензола либо другого растворителя в системе в первом случае составляет 4 м3, а во втором – около 200 м3. Поэтому при применении центробежных экстракторов значительно уменьшается первоначальная стоимость установки и сокращается ее пожароопасность. С помощью экстракторов содержание фенолов снижается от 2520 до 36 мг/дм3, или на 98,6%.
Стоимость центробежных и колонных экстракторов примерно одинакова из-за большей сложности изготовления первых, но расход металла ниже в 5–10 раз. При использовании центробежных экстракторов нужна тщательная предварительная очистка воды от твердых частиц и смолы. Потери растворителя составляют около 0,25 кг/м3 очищенной воды. Расход щелочи близок к теоретическому.
В экстракционных установках перерабатывается вода до поступления ее в аммиачную колонну, что позволяет использовать все растворенные в воде фенолы.
Стоимость извлечения фенолов бензолом из надмольной воды на 10–15% выше, чем при использовании пароциркуляционного метода.
На предприятиях полукоксования и гидрогенизации, где образуются воды с высоким содержанием фенолов (и особенно двухатомных), экстракционное обесфеноливание – единственный возможный процесс, позволяющий экономически рентабельно извлекать фенолы.
Уничтожение фенолов и биохимическая очистка сточных вод. Как пароциркуляционное, так и экстракционное обесфеноливание не позволяют снизить содержание фенолов, в воде до санитарных норм или даже заметно приблизиться к ним. Поэтому остатки фенолов необходимо уничтожить. Наиболее рациональный путь – это окисление фенолов с получением СО2 и Н2О. Применяют различные методы окисления. На установках небольшой производительности для этой цели могут быть использованы озон, а также другие окисляющие агенты. Однако эти способы очистки сопряжены со значительным расходом энергии, озонирование связано с повышением рН до 12, значителен и расход озона (1,5–2 кг/м3 воды). Кроме того, образуются токсичные продукты окисления. Поэтому метод не применяется для очистки вод коксохимических предприятий.
Основным способом глубокой очистки сточных вод является биохимическое окисление, при использовании которого окисляются не только фенолы, но и тиоцианиды, и цианиды.
Для биохимической очистки используют либо активный ил, представляющий собой сложный конгломерат бактерий различных видов и других простейших, либо культуры специфических бактерий, предназначенных для разрушения определенных загрязняющих компонентов, например фенолов или тиоцианид-ионов (так называемый микробный метод). Фактически во втором случае также используется активный ил, но обогащенный специфическими микроорганизмами.
Оптимальные условия работы биохимической установки: температура 25–30°С, рН = 7,2–9,0; содержание летучего аммиака – не более 0,2 и общего – не более 2 г/дм3, содержание масел – не более 50 мг/дм3. Содержание фенолов, цианид-, сульфид-, тиоцианид-ионов и пиридиновых оснований в реальных условиях всегда ниже концентраций, при которых подавляется жизнедеятельность микроорганизмов. Типичный состав общего стока коксохимических заводов приведен в таблице 1.
Кроме того, в поступающих от разных цехов сточных водах содержатся механические примеси. Как видно из таблицы 1, велика концентрация смол и масел, а температура (36°С) также превышает оптимальную. Поэтому биологической очистке предшествует механическая очистка воды от примесей.
На рисунке 3 показана принципиальная схема одной из крупнейших установок очистки сточных вод коксохимического производства проектной производительностью 500 м3 сточной воды в час, введенной в строй в 19,80 г.
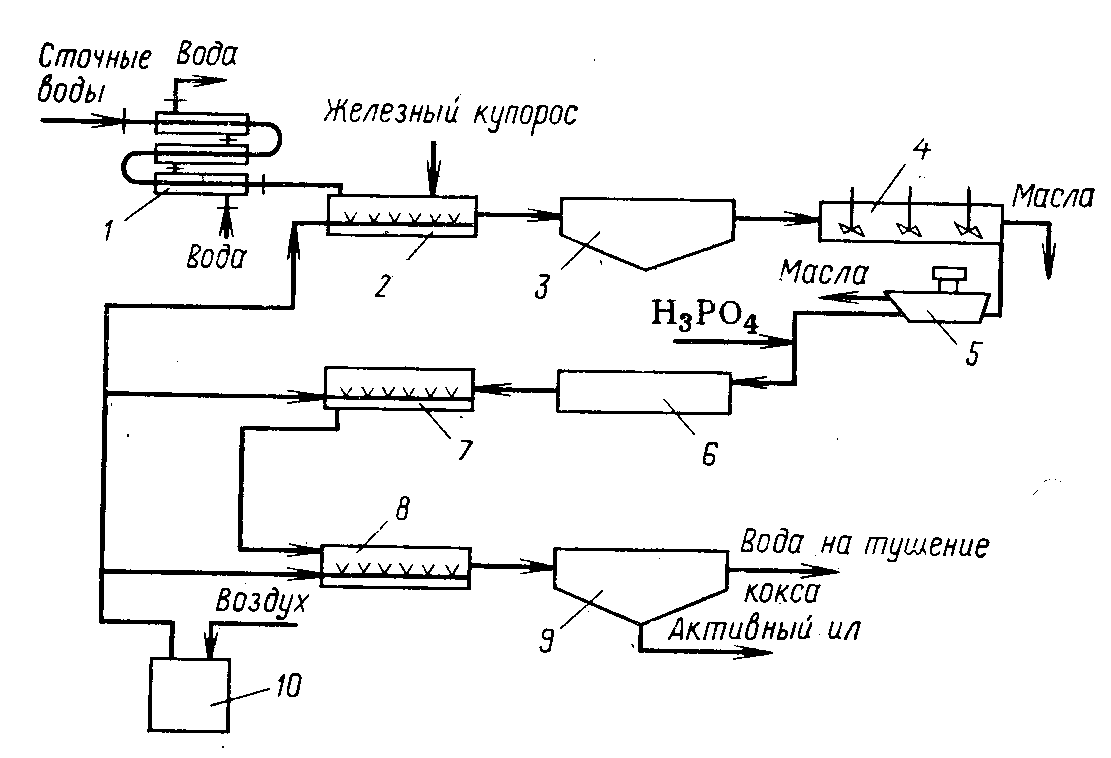
Рис. 3. Схема биохимической очистки сточных вод:
1 – холодильники «труба в трубе»; 2 – преаэратор; 3, 9 – соответственно первичный и вторичный отстойники; 4 – маслоотделитель; 5 – флотационная машина; 6 – усреднитсль; 7, 8 – аэротенки I и II ступеней; 10 – компрессор
Горячие надсмольные воды цехов улавливания (92°С) охлаждаются до 40–60°С в холодильниках типа «труба в трубе». Затем их смешивают с фенольными водами другого происхождения в преаэраторах 2, где они перемешиваются воздухом. Сюда же добавляют коагулянт – железный купорос, что позволяет значительно улучшить степень очистки воды от смол и масел.
Из преаэраторов (на рисунке показан один) вода последовательно проходит 12 первичных отстойников 3 радиального типа емкостью 220 м3 (показан один), 12-секционный импеллерный маслоотделитель 4 (емкостью около 130 м3) и далее три флотационных машины 5 суммарной вместимостью 200 м3. В токе воздуха происходит флотация смол и масел, токсичных для бактерий. Пленка снимается вместе с пеной и удаляется с поверхности воды. Содержание масел после механической очистки уменьшается с 600 (предельные значения от 100 до 1300) до 18 мг/дм3 (предельные значения от 15–30).
После завершения механической очистки к воде добавляют раствор ортофосфорной кислоты (источник фосфорного питания бактерий), и вода поступает в восьмисекционный усреднитель коридорного типа 6, используемый в качестве предаэротенка. С этой целью в него подают воздух. Из усреднителя 6 вода направляется на основную биохимическую очистку в аэротенки I и II ступеней 7 и 8 с рециркуляцией образующегося в них бактериального ила. В десяти аэротенках I ступени вода очищается от фенолов (суммарная емкость 800 м3), а в десяти аэротенках II ступени (суммарная емкость 1200 м3) – от тиоцианидов. Установлено, что очистка от тиоцианидов начинается при уменьшении содержания фенолов до 20–30 мг/дм3. В аэротенки интенсивно подается воздух, его расход составляет 180–240 м3/м3 очищаемой воды. Время пребывания воды в аэротенках I ступени 20 ч, а во II – 26 ч.
Из аэротенков II ступени вода поступает в четыре вторичных отстойника 9 (на рисунке показан один) суммарной вместимостью 220 м3 для отделения ила. Осветленная вода направляется на тушение кокса. Ниже приводятся сведения об эффективности биохимической очистки на указанной установке (усредненные данные):
| До очистки | После очистки |
рН | 8,8 | 8,3 |
ХПК, мг О2/дм3 | 1450 | 296 |
Содержание примесей, мг/дм3 фенолов | 263 | 4,2 |
тиоцианатов | 253 | 4,4 |
цианидов | 150 | 10,0 |
аммиака летучего | 265 | 240 |
аммиака общего | 610 | 610 |
масел | 13 | 9,6 |
Показатели очистки микробным методом аналогичны показателям биохимической очистки, но отличаются более высоким содержанием тиоцианатов (на 25–35%).
Таким образом, биохимическая очистка позволяет в варианте с активным илом удалить большую часть фенолов, тиоцианатов и цианидов и в 5 раз уменьшить ХПК вод. В то же время содержание масел снижается только на 30–40%, а количество аммиака остается неизменным.
Возможно одновременное глубокое окисление фенолов тиоцианатов в одном аэротенке с помощью активного ила до остаточной концентрации фенолов, тиоцианатов и цианидов не более 1 мг/дм3. При этом остаточная химическая потребность в кислороде уменьшается до 300 мг/дм3 и ниже.
Активный ил обладает следующими преимуществами: повышенная концентрация микроорганизмов в аэротенке и одновременное окисление фенолов и тиоцианатов позволяют в несколько раз сократить объем очистных сооружений; хорошее отделение биологической массы активного ила от очищенной воды облегчает ее последующее использование.
Условием успешного перехода к использованию одноступенчатых биохимических установок является применение более эффективных аэраторов, позволяющих подавать в аэротенки в несколько раз большее количество воздуха на единицу объема аппаратов. В биохимических установках невозможно полностью удалить вредные примеси, т. е. очистить воду до санитарных норм; однако полнота очистки много выше, чем в установках с утилизацией фенолов.
Как видно из приведенных выше данных, установки биохимической очистки – громоздкие сооружения, строительство которых связано с большими капитальными затратами. В то же время эксплуатационные затраты незначительны и обслуживание их несложно.
Сточные воды после биохимической очистки ранее очищались на городских очистных сооружениях совместно с бытовыми сточными водами. Однако это приводило к перегрузке городских сооружений. В последнее время трудности усугубляются еще и тем, что для ряда веществ, идентифицированных в промышленных сточных водах, не установлены предельно допустимые концентрации в водоемах. Поэтому главной задачей становится полное прекращение сброса сточных вод за пределы предприятия и создание бессточного коксохимического предприятия.
Вопросы организации бессточного коксохимического производства. На многих предприятиях пока сохраняется стадия мокрого тушения кокса. При этом испаряется 0,5–0,6 м3 воды на 1 т кокса. Таким образом, при подаче очищенной воды на тушение кокса коксохимическое производство становится бессточным. При этом можно утилизовать также продувочные воды системы производственно-технического водоснабжения коксохимического предприятия (рис. 4).
Вывод продувочных вод из системы оборотного водоснабжения связан с необходимостью сокращения количества солей в оборотной воде, чтобы избежать образования накипей на поверхностях теплообмена.
Как известно, переход на сухое тушение кокса является одним из наиболее важных мероприятий, позволяющих рационально использовать энергетические и водные ресурсы, сократить выбросы в атмосферу и улучшить качество кокса. При сухом тушении кокса прекращается химическое и тепловое загрязнение окружающей среды, достигается большая экономия энергетического топлива (чтобы получить то количество пара, которое производится на установках сухого тушения кокса – УСТК, обслуживающей коксовую батарею производительностью 1 млн. т/год, надо израсходовать с учетом теплового к.п.д. парогенератора более 100 тыс. т условного топлива). Однако при полном переходе на сухое тушение кокса возникает новая проблема – утилизация сточных вод (в количестве 0,5 м3/т кокса). Наибольший интерес представляет использование этих вод после биологической очистки в цикле оборотного водоснабжения.
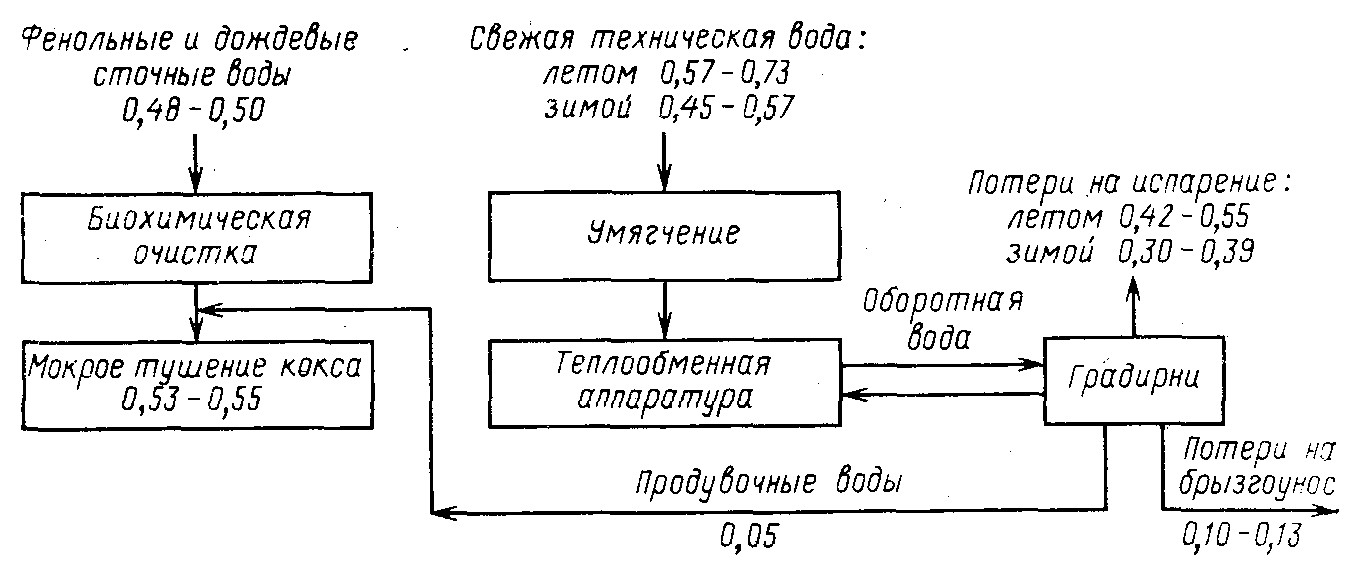
Рис. 4. Расход сточной и технической вод (в м3/т кокса) при мокром тушении кокса без использования сточных вод в оборотном водоснабжении
На охлаждение теплообменной аппаратуры и другие нужды на коксохимическом предприятии расходуется 19–25 м3 оборотной воды на 1 т кокса. Из этого количества испаряется на градирнях и безвозвратно теряются 0,30–0,39 м3 воды зимой и 0,42–0,55 м3 летом. Кроме того, 0,10–0,13 м3 воды выносится из градирен в виде мелких капель, брызг, тумана. И, наконец, 0,05 м3 – это упоминавшаяся выше продувочная вода, которая выводится из цикла с целью удаления накопившихся по мере испарения солей (в особенности солей жесткости). Таким образом, расход воды из цикла составляет от 0,45 до 0,8 м3/т кокса. Это количество может быть компенсировано за счет использования сточных вод.
Нормы содержания примесей в водооборотном цикле менее жесткие, чем при сбросе их в водоемы, и составляют (в мг/дм3):
-
Сброс в водоем
Повторное использование
CN–
0,1
200
H2S
Отсутствие
20
Фенол
0,001
25
При этом считают, что примеси разрушаются под действием кислорода воздуха и микроорганизмов и в системе оборотного водоснабжения.
Общим для сточных вод коксохимических заводов оказывается по сравнению с технической водой малое солесодержание (особенно на заводах Урала и Сибири, а также центра РСФСР) и малая жесткость. Поверхностно-активные вещества, содержащиеся в сточной воде, тормозят рост кристаллов карбоната и сульфата кальция. Скорость образования отложений в десятки раз меньше, чем при использовании технической воды. Возможно даже растворение образовавшегося ранее осадка в результате реакции:
СаСО3 + 2NH4C1 — CaCl2 + 2NН3 + СО2 + Н2О
Противоречивы данные о влиянии сточных вод на коррозию. Известны случаи, когда компоненты сточных вод могут проявлять себя как ингибиторы коррозии, в то же время хлорид и тиоцианид-ионы относятся к числу активаторов коррозии и могут быть причиной усиления коррозии.
Дождевые и талые воды также можно использовать для добавления в системы оборотного водоснабжения после очистки от взвешенных примесей. Естественно, что сточные воды следует подавать на оборотное водоснабжение после механической и биохимической очистки, причем содержание общего аммиака в них должно быть ограничено пределами 100–150 мг/дм3.
Таким образом, традиционный баланс воды на коксохимическом предприятии усложняет использование воздушного охлаждения. В этом случае на одну треть сокращается потребность в оборотной воде, а, следовательно, возникают трудности утилизации сточных вод. Выход заключается в совершенствовании технологии коксохимического производства и доведении объема сточных вод до 0,12–0,15 м3/т кокса в соответствии с материальным балансом коксования.
Рассмотрим некоторые пути сокращения количества фенольных сточных вод.
1. Объем конденсата первичных газовых холодильников зависит от влажности исходного угля и количества пирогенетичсской влаги, на долю которой приходится менее 20% общего объема конденсата. При термоподготовке основная часть влаги угля удаляется при температурах 100–200°С, т.е. в условиях, исключающих разложение органической массы угля. Влага угля, выводимая из системы, практически свободна от токсичных веществ, т.е. на 0,06–0,07 м3/т шихты (или на 0,9–0,10 м3/т кокса) уменьшается балансовое количество загрязненных сточных вод.
2. Дополнительным источником сточных вод является принятая схема выделения аммиака из надсмольной воды при десорбции его острым паром. Расход пара на десорбцию аммиака составляет 20–25% объема перерабатываемой воды, или 40–45 т/т аммиака. Переход на обогрев аммиачных колонн глухим паром позволил бы уменьшить объем сточных вод на 0,03–0,07 м3/т кокса. Необходимо, чтобы коксохимическое предприятие возвращало на теплоэлектростанцию как можно больше конденсата глухого пара; в настоящее время значительная его часть поступает в сточные воды. Сокращение расхода острого пара и более полный возврат конденсата уменьшает не только объемы сточных вод, но и затраты на химическую водоочистку и водоподготовку в системе ТЭС.
3. Закрытие цикла конечного холодильника без улавливания в голове процесса несколько увеличивает объем сточных вод. В то же время переход к улавливанию цианистого водорода, сероводорода и аммиака в начале газового тракта делает ненужным узел конечного охлаждения и уменьшает объем сточных вод на 0,05 м3/т кокса.
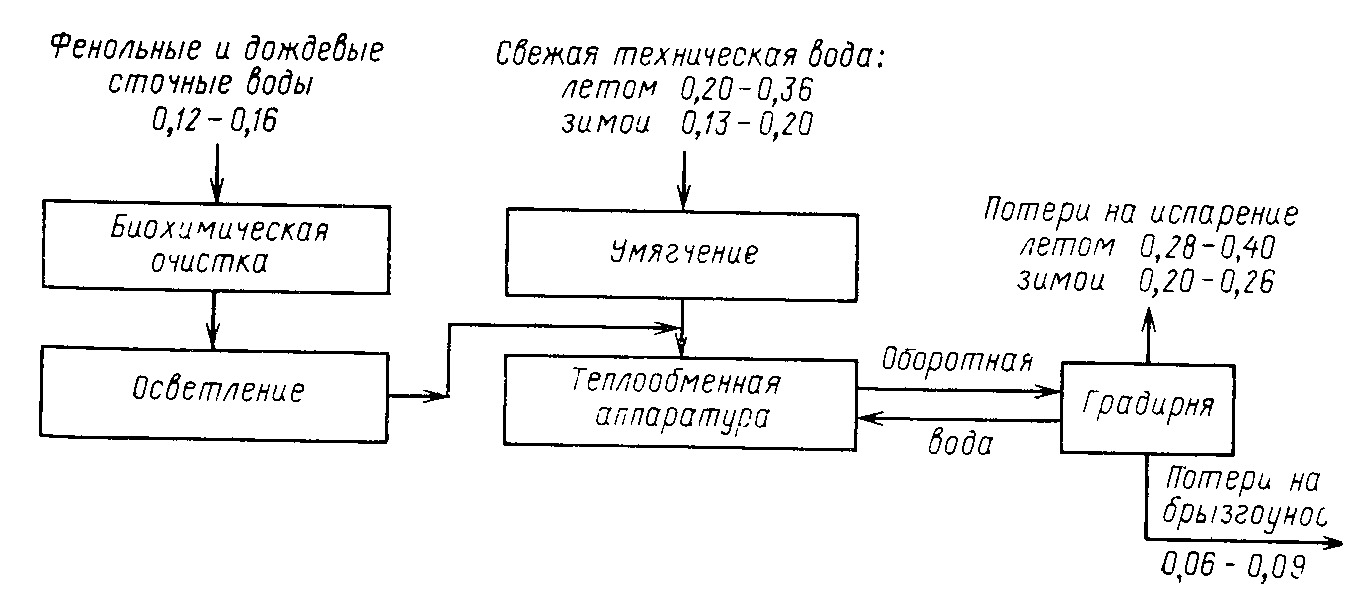
Рис. 5. Расход сточной и технической воды (в м3/т кокса) при 100%-ном сухом тушении
4. Улучшение технологии извлечения бензола из масла позволяет в 2–3 раза (т.е. на 0,03–0,05 м3/т кокса) уменьшить объем сепараторных вод бензольного отделения.
На рисунке 5 представлена схема очистки и утилизации сточных вод при условии, что в схему введена стадия термической подготовки угля и внесены необходимые усовершенствования в технологию коксохимического производства, включая применение воздушных холодильников. При этом предполагается сухое тушение всего получаемого кокса.
В ряде случаев очищенные сточные воды могут быть использованы и в смежных производствах, например для гранулирования доменного шлака или для пополнения водно-шламовых циклов углеобогащения (потребность в дополнительной воде 0,15 м3/т рядового угля, или 0,22 м3/т сухой шихты, или 0,27 м3/т кокса). Последний вариант можно использовать на предприятиях, имеющих в своем составе углеобогатительные фабрики.
1.3.2. Пути сокращения и утилизации газовых выбросов
Одной из наиболее серьезных задач является организация бездымной загрузки шихты в печные камеры. На ряде предприятий используют инжекцию парогазовой смеси, образующейся в момент загрузки в стояки и газосборник. Этот прием создает благоприятную санитарную обстановку на коксовых печах, но приводит к увеличению уноса пыли в смолу и повышает содержание кислорода в газе.
В РФ и за рубежом отрабатываются системы индивидуального отсоса газов загрузки и дожигания их в специальной установке, смонтированной на углезагрузочном вагоне.
Крупный источник выбросов в атмосферу – градирня конечного охлаждения коксового газа. Как уже было сказано ранее, закрытие цикла конечного охлаждения, очистка коксового газа от HCN в начале схемы улавливания позволяют исключить эти выбросы.
На ряде производств опасность представляют выбросы из воздушников. Отдельные виды выбросов попадают в коксовый газ. Так, на всасывающую линию нагнетателей подаются выбросы из воздушников пиридиновых установок. В этих выбросах содержатся токсичные цианистый водород и пиридиновые основания. В коксовый газ возвращают и легкую фракцию сырого бензола, которая не утилизируется на ряде предприятий. В пекококсовый газ подается отработанный газ после обработки пека воздухом.
Серьезную проблему представляли выбросы бензольных углеводородов из воздушников технологического оборудования и цехов ректификации сырого бензола. Потери составляли около 2% от массы сырого бензола. В настоящее время разработана двухступенчатая схема охлаждения парогазовой смеси с конденсацией продуктов и последующей абсорбцией бензольных углеводородов захоложенными сольвентами или ксилолами.
Существует несколько видов выбросов, содержащих пары ряда токсичных веществ, включая и полициклические ароматические углеводороды, которые не удается утилизировать. Возможным решением в этом случае является дожигание органических веществ, лучше – каталитическое. Для этой цели используют катализаторы – оксиды ванадия и меди, нанесенные на оксид алюминия. Температура каталитического процесса 400–500°С, объемная скорость 10–25 тыс. ч–1. Степень очистки составляет 97–100% при содержании углеводородов в исходной смеси 6–18 г/м3 (отбросные газы отделения пекоподготовки).
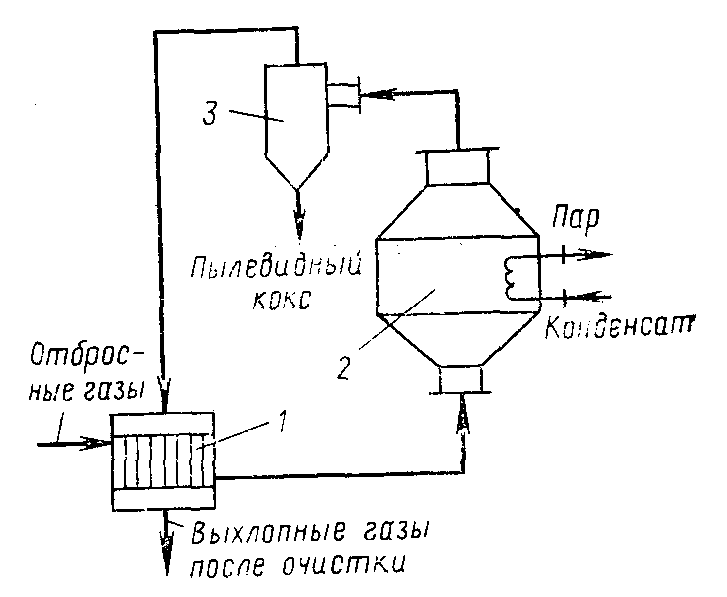
Рис. 6. Схема дожигания теплоносителя в производстве формованного кокса:
1 – теплообменник; 2 – контактный аппарат с кипящим слоем катализатора; 3 – циклон
Метод каталитического дожигания успешно используется и для очистки избыточного газа-теплоносителя установок формованного кокса. Особенностью такого газа является низкое содержание кислорода – 0,3–0,7%. В газе кроме углеводородов содержится 3–8 г/м3 угольной пыли, загрязненной смолистыми веществами, пары воды и сероводород.
Для очистки (рис. 6) используется аппарат с кипящим слоем катализатора 2. Избыточный теплоноситель разбавляется воздухом до концентрации кислорода 4 об. % и поступает в реактор. Здесь окисляются все органические вещества, включая и смолу, адсорбированную на поверхности частиц пыли. Мелкодисперсные частицы пыли проходят через слой катализатора. Теплоноситель охлаждается в теплообменнике 1, очищается от пылинок в циклоне 3 .или на металлокерамических фильтрах и выбрасывается в атмосферу.
1.3.3. Утилизация твердых и смолистых отходов
Наиболее крупная проблема–комплексное использование отходов углеобогащения и охрана окружающей среды при работе углеобогатительных фабрик. Масштабность этой проблемы характеризуется тем, что уже в 1980 г. углеобогатительные фабрики страны ежегодно перерабатывали 300 млн. т угля, получая 50 млн. т твердых отходов. На ряде предприятий их широко используют при сооружении дамб, для дорожных покрытий, в производстве строительных материалов. В Подмосковном угольном бассейне на разрезе «Кимовский» действует безотходная фабрика по комплексному обогащению высокосернистого бурого угля с получением обогащенного энергетического угля, серного колчедана – сырья для получения серной кислоты, глины для изготовления кирпича.
Представление о составе отходов дают характеристики промышленных отходов углеобогатительных фабрик Карагандинского угольного бассейна:
-
Зольность, %
68,5–70,5
Содержание серы, %
2,0–2,2
Теплота сгорания, МДж/кг
7,5–8,2
Состав, %
чистый уголь
31,33
сульфиды железа
1,3
глинистые материалы
62–64
карбонаты
1–3
Химический состав золы, масс.
-
SiO2
53–58
MgO
1,3-1,8
А12О3
25–28
TiO2
0,7–1,2
Fе2O3
5,5–6,5
SO3
1,4–2,2-
СаО
1,8–2,8
CO2
0,2–0,4
Достоинством отходов углеобогатительных фабрик является высокая степень готовности к переработке (стабильный состав минеральной части, однородный гранулометрический состав). В РФ разработана прогрессивная технология получения из, отходов углеобогащения искусственного пористого заполнителя (аглопорита) для легких бетонов.
В настоящее время отходы углеобогащения можно использовать в качестве следующих материалов:
1) сырье для производства аглопорита, стеновых керамических изделий, вяжущих материалов, дренажных труб, керамической плитки и других строительных материалов;
2) материалы для строительства дорог и земляных сооружений (строительный щебень, дорожные основания дамб, балластировка железных дорог);
3) сырье для сернокислотного производства–серный колчедан;
4) материалы для закладки выработанного пространства» шахт и планировки поверхности, нарушенной горными работами;
5) сырье для производства удобрений;
6) сырье для получения кремнеалюминиевых сплавов, материалов на основе карбида кремния, глинозема, сульфата алюминия и др.
Наибольшее значение имеют два первых направления.
Строительные материалы на основе отходов добычи и обогащения углей дешевле по сравнению с приготовленными из традиционного сырья: аглопорит – на 28%, кирпич – на 16%. При этом не полностью учтена экономия капитальных затрат на организацию добычи традиционного сырья.
Существуют, однако, организационные трудности, определяющиеся необходимостью сооружения самостоятельных производств строительных материалов, соответствующих по мощности углеобогатительным фабрикам. Трудной и не полностью решенной проблемой остаются переработка и утилизация отходов флотации углей, так как в этом случае необходимо не только тщательное механическое обезвоживание этих отходов,, но и уничтожение органических флотореагентов, уносимых вместе с углем.
Своеобразным твердым отходом становится сульфат аммония – низкосортное удобрение, на изготовление которого используют значительные количества дефицитной серной кислоты.
Крупным достижением коксохимической промышленности явилась утилизация смолистых отходов производства – фусов, кислых смолок сульфатных цехов и цехов по переработке сырого бензола и нафталина. Количество фусов составляет 0,15–0,18% от сухой шихты, кислой смолки цехов улавливания – 0,05%; столько же кислой смолки получают и при очистке сырого бензола.
Была разработана схема утилизации фусов, возвращаемых в угольную шихту, а также технология совместной утилизации кислых смолок, масел с очистных сооружений, кубовых остатков от ректификации бензола, полимеров, сильно загрязненных сточных вод, которая предполагает приготовление водно-масляной эмульсии из смеси отходов. Эту смесь затем дозируют в шихту. При этом эмульгаторами служат полимерные продукты, содержащиеся в отходах. В настоящее время эмульсионный способ утилизации практически всех образующихся химических отходов (кислых и щелочных, органических и неорганических) ' внедрен на большинстве коксохимических предприятий востока и центра РФ.
На заводах Украины кубовые остатки и кислые смолки в смеси с каменноугольной смолой используют в качестве связующего для дорожного строительства.
Охрана окружающей среды в коксохимической промышленности, как и в других отраслях, неразрывно связана с уровнем эксплуатации и общей культурой производства. Ряд производств может быть безотходным или малоотходным, если строго соблюдается технологический регламент. Нарушения режима, непродуманные изменения технологии не только ухудшают технико-экономические показатели процесса, но и приводят к образованию выбросов. Характерно в этом отношении производство пекового кокса, которое является безотходным на хорошо работающих предприятиях и оказывается источником опасных выбросов при плохой эксплуатации.
Стабильность состава сточных вод, рациональное использование локальных водооборотных циклов в отдельных цехах уменьшают нагрузку на очистные сооружения, делают их работу более стабильной и эффективной.
9.4. БЕЗОТХОДНЫЕ ТЕХНОЛОГИИ И ОХРАНА ОКРУЖАЮЩЕЙ СРЕДЫ
В ДРУГИХ ПОДОТРАСЛЯХ ХИМИЧЕСКОЙ ТЕХНОЛОГИИ
ТВЕРДЫХ ГОРЮЧИХ ИСКОПАЕМЫХ
Особенностью большинства других подотраслей (получение формованного и специальных видов кокса, полукоксование и энерготехнологическая переработка твердых горючих ископаемых, гидрогенизация и газификация) является то обстоятельство, что все они находятся в стадии опытных и опытно-промышленных разработок. В отличие от традиционной коксохимической промышленности, где существуют большие производственные мощности, где используются десятилетиями сложившиеся технологические решения и которую нереально быстро перевести на новую, совершенную технологию, в других подотраслях имеется возможность идти новыми путями и ориентироваться на создание производств, обладающих высокой степенью ннженерно-эколого-экономического совершенства. Существует также возможность в полной мере учесть опыт, накопленный в коксохимии, нефтепереработке и других отраслях промышленности.
Особенно важно создание оптимальной в инженерном и экологическом отношениях технологии производства жидких и газообразных топлив из угля.
Само по себе создание этой подотрасли имеет особое экологическое значение для России. Как в настоящее время, так и в перспективе основным районом потребления энергии будет европейская часть страны. В то же время запасы дешевого твердого топлива, способные на очень длительный период удовлетворить потребности в энергии, сконцентрированы в Сибири. Транспортирование углей на территорию европейской части России потребует создания новых железнодорожных магистралей и связано с очень большими затратами, включая и энергетические. Однако развитие угольной энергетики может усложнить существующую экологическую обстановку, так как, во-первых, зола, образующаяся при сгорании угля, потребует отчуждения больших территорий под зольные отвалы. Создание и эксплуатация отвалов сопряжены не только с большими затратами, но и с трудноустранимым воздействием отвалов на санитарную обстановку в регионе (пыль, просачивание токсичных веществ из отвалов в грунтовые воды и водоемы, вынос токсичных веществ с дымовыми газами). Во-вторых, при сжигании твердых топлив вся сера переходит в токсичный оксид серы (IV), а азот твердого топлива на 70% превращается в оксиды азота. Поэтому использование дополнительных количеств твердых горючих ископаемых в Европейской части России может усилить загрязнение атмосферы. Следовательно, с востока страны в европейскую ее часть должны передаваться безбалластное топливо и химическое сырье, приготовленное из дешевых углей, транспортирование которого осуществляется по трубопроводам.
Особенность предприятий по производству жидких и газообразных топлив из угля заключается в том, что они должны иметь большую производительность. Так, завод, изготовляющий 15 млн. т жидкого топлива из угля в год, должен перерабатывать ежегодно 70–100 млн. т угля, т.е. в 10–15 раз больше, чем самое крупное современное коксохимическое предприятие. Более сложными и многооперационными оказываются и сами технологические процессы.
Для приготовления синтетических топлив используются молодые угли, отличающиеся высокой влажностью (влажность канско-ачинских углей 30–35%). Поэтому значительно возрастает и выход сточных вод. Кроме того, например, при гидрогенизации кислород угля полностью превращается в воду. Поэтому при любых методах приготовления жидких и газообразных топлив из угля основным технологическим процессам должно предшествовать обезвоживание угля, позволяющее значительно уменьшить объем загрязненных сточных вод.
При гидрогенизации азот и сера угля полностью переходят в аммиак и сероводород, которые необходимо извлекать из газов. При газификации до 50–70% азота исходного угля превращается в аммиак, а сера полностью переходит в сероводород и оксид серы (IV). При правильной организации этих процессов заметных количеств цианистого водорода не образуется. Это облегчает очистку газа и сточных вод, так как в них будут отсутствовать тиоцианаты.
Неизбежной проблемой любого предприятия получения жидких и газообразных топлив из угля будет утилизация золы, получаемой при газификации, или ее складирование.
Наиболее разнообразный ассортимент продуктов получают в различных вариантах полукоксования или скоростного пиролиза твердых горючих ископаемых. Твердый остаток, газ, два вида смол: легкая и тяжелая, загрязненная большим количеством угольной и полукоксовой пыли – все это создает трудности синхронного сбыта. Так, при выходе легкой смолы 5–10% на органическую массу угля необходимо обеспечить сбыт 8–10-кратного количества полукокса. Полукокс легко окисляется и самовозгорается. Поэтому его транспортирование и хранение целесообразны под слоем инертного газа. Это усложняет сбыт и транспортирование полукокса.
Сложной и нерешенной проблемой является переработка тяжелой смолы из-за ее высокой зольности и запыленности. Этих трудностей можно избежать, если горячий полукокс и тяжелая смола используются в качестве топлива на ТЭС. Легкая смола, как видно из разделов 5.1 и 6.2, не является готовым жидким топливом прежде всего из-за высокого содержания фенолов.
В любых технологиях полукоксования возникает необходимость гидрогенизации смол и очистки больших объемов сточных вод, содержащих одно- и многоатомные фенолы, сульфиды и карбонаты, азотистые основания, карбоновые кислоты и нейтральные масла.
Экологические проблемы, возникающие при развитии сланцеперерабатывающей промышленности, в основном подобны тем, которые существуют при развитии полукоксования и гидрогенизационных процессов. Существенной особенностью этой отрасли оказывается образование несравненно больших по сравнению с переработкой углей количеств зольных отходов, а также необходимость добычи значительно большего количества исходного материала.
В РФ накоплен опыт переработки минеральной части прибалтийских сланцев. Зола пылевидного сжигания сланцев полностью окислена, и в ней образуются клинкерные минералы, необходимые для создания вяжущих материалов. Она успешно применяется как известковое удобрение в сельском хозяйстве. В Эстонии ежегодно потребляется более 3 млн. т золы на общей площади 330 тыс. га, что дает чистую прибыль за счет прироста урожая около 6,5 млн. руб.
Сланцевая зола применяется также для производства уникальных высокомарочных цементов и автоклавных силикатобетонных изделий.
В условиях Прибалтики сланцевая зола представляет интерес также для монолитной закладки фосфоритных рудников и сланцевых шахт.
Гидрогенизация угля – многооперационный и весьма чувствительный к качеству исходного сырья способ приготовления жидких топлив. С инженерных позиций–это наиболее сложный способ получения указанных продуктов.
Самым неприятным отходом производства оказывается шлам после термического растворения или жидкофазной гидрогенизации. Высокая зольность и вязкость шлама, его большой выход усложняют переработку. Поэтому в состав любого гидрогенизационного производства входит либо полукоксование шлама с последующей газификацией полукокса, либо непосредственная газификация шлама. Многостадийность процесса гидрогенизации, высокие давления на основных его стадиях уменьшают надежность и усложняют управление технологией, что также делает процесс экологически неблагоприятным. При гидрогенизации неизбежно образование больших объемов сточных вод, содержащих фенолы, сульфид и карбонат аммония, различные нейтральные соединения.
Газификация угля – наиболее универсальный процесс, используемый самостоятельно и как важная составная часть (получение водорода) в других способах переработки.
Экологически разные варианты газификации неравноценны. Наиболее неблагоприятна слоевая газификация, так как при этом получают и сточные воды, и смолу, т.е. весь набор химических продуктов полукоксования. При газификации в псевдоожиженном слое и газификации пылевидного угля образуются газовые смеси, свободные от органических соединений, хотя в конденсирующейся воде обязательно будут присутствовать аммиак, сероводород и карбонаты. Недостатком газификации в псевдоожиженном слое оказывается получение твердого шлака, значительный остаток углерода в шлаке, большой пылеунос.
С экологических позиций наиболее заманчива безостаточная газификация с жидким шлакоудалением. Приготовление жидкого шлака расширяет возможный круг его использования (шлаковое литье, производство гранулированных материалов, искусственного гравия и т.п.). Парокислородная газификация на установках типа Колперс–Тотцек или Тексако позволяет получить водяной газ, свободный от органических веществ, и жидкий шлак.
Главной задачей в этих процессах являются улавливание пыли из газа и возвращение ее в цикл. Газификация может быть средством ликвидации и утилизации отходов производства. Любые сточные воды могут применяться в качестве сырья для производства в парогенераторах пара, используемого при газификации. Особенно перспективны в этом отношении схемы типа Тексако.
Таким образом, единственным в принципе безотходным способом приготовления газа из угля (даже в сочетании с иными процессами переработки угля) является газификация пылевидного топлива с применением парокислородного дутья при высоких температурах.
Создание инженерно и экологически совершенных технологий приготовления жидких и газообразных топлив из угля открывает перед специалистами простор для творческого поиска.
В промышленности углеграфитовых материалов, как отмечалось выше, существуют три вида отходов: засыпка из печей; отходы от механической переработки изделий; газы и смолистые вещества, выделяющиеся при обжиге изделий. Последние представляют собой особую опасность при применении углеграфитовых материалов в электролизерах и печах с самоспекающимися анодами (наиболее распространенный вариант производства алюминия), когда смолистые вещества, могут выделяться непосредственно в производственные помещения.
В традиционном производстве углеграфитовых материалов можно возвратить в цикл значительную часть отработанной засыпки. При этом, однако, требуется ее рассев и в некоторых случаях прокалка. Отходы от механической обработки представляют практически чистый углерод и могут использоваться как восстановители в ряде металлургических процессов и как наполнители при изготовлении некоторых видов углеграфитовых материалов. Утилизация или уничтожение смолистых веществ при существующих конструкциях печей–в полной мере нерешенный вопрос.
В новых технологических процессах можно избежать использования значительных количеств засыпки, применяя, например, обжиг в кассетах, печи высокочастотного обогрева. Эти же решения позволяют улавливать смолистые вещества. Принципиально важным может быть использование нефтяных связующих,. которые не только позволяют более гибко управлять качеством материалов, но и содержат на 1,5–2 порядка меньше канцерогенных веществ, чем обычно применяемые каменноугольные пеки. Это значительно улучшает условия труда и повышает степень экологической безопасности производств углеграфитовых материалов. С экологических же позиций необходимо отказаться от использования самоспекающихся электродов или, анодов и применять только обожженные электроды и аноды.