Vii улавливание и получение сырого бензола
Вид материала | Лекция |
- X. переработка сырого бензола, 321.46kb.
- Vii переработка химических продуктов термической переработки твердых горючих ископаемых, 256.07kb.
- Viii. Переработка фракций сырого бензола, 431.56kb.
- Ароматические углеводороды. Бензол представитель аренов. Строение молекулы и физические, 54.51kb.
- Анализа состояния конкуренции на рынке сырого молока. I. Общие положения Анализ проводился, 348.46kb.
- Термохимия растворения ccl 4, бензола и его производных в индивидуальных и смешанных, 298.7kb.
- Выбросы и улавливание загрязняющих атмосферу веществ, отходящих от стационарных источников, 20.65kb.
- Приказ 04. 04. 2011 n 151 Об итогах VII районной научно практической конференции проектных, 439.61kb.
- Лекция 4, 220.93kb.
- Зао «Куйбышевазот» Строительство производства бензола с сырьевым складом, 1760.62kb.
7.3. Конечное охлаждение коксового газа
Бензольные углеводороды улавливают из коксового газа, прошедшего сульфатное отделение. Температура газа после сульфатного отделения не бывает ниже 52–55°С, а иногда достигает 60–70°С. Газ содержит значительное количество нафталина (1,0–1,2 г/м3) и водяных паров. Для успешного выделения бензольных углеводородов коксовый газ должен быть охлажден до 25–30°С, очищен от нафталина и освобожден от некоторой части содержащихся в нем водяных паров. Это охлаждение газа называют конечным, т.к. после этого газ больше не охлаждается. Холодильники, в которых происходит охлаждение газа, называются конечными. Эти холодильники располагаются по газовой трассе цеха улавливания перед бензольными скрубберами. На коксохимических заводах страны существует два способа конечного охлаждения газа: с нафталиновым отстойником и с экстрагированием нафталина из воды смолой. В настоящее время широкое применение получил второй способ как более эффективный.
На рис. 12 приведена схема конечного охлаждения коксового газа с применением горячей смолы для вымывания нафталина из воды. Верхняя газовая часть конечного холодильника оборудована полками и служит для охлаждения газа. В полках имеется значительное количество отверстий диаметром 10 мм. Нижняя часть холодильника служит промывателем и поэтому оборудована восемью полками с отверстиями 3 мм.
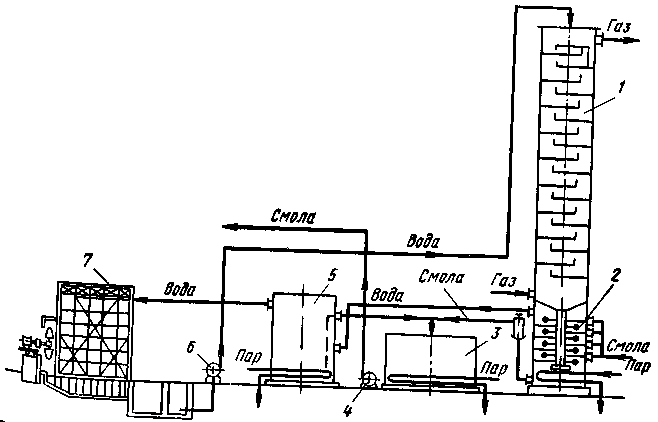
Рис. 12. Схема конечного охлаждения газа с экстрагированием нафталина из воды смолой:
1 – верхняя газовая часть холодильник; 2 – нижняя часть холодильника (промыватель); 3 – сборник; 4, 6 – насосы; 5 – отстойник; 7 – градирня
Коксовый газ с температурой 52–60°С поступает в газовую часть холодильника 1, поднимаясь вверх, охлаждается технической водой до 25–30°С и направляется в бензольные скрубберы. Охлаждение газа производится оборотной технической водой, находящейся в замкнутом цикле холодильник–отстойник–градирня–насос–холодильник.
Охлажденная в градирне 7 техническая вода с температурой 20–25°С насосом 6 подается на верхнюю газовую часть холодильника 1 и охлаждает идущий противотоком коксовый газ. При охлаждении газа из него одновременно с конденсацией содержащихся в нем водяных паров вымываются кристаллы нафталина. Выделяемый из газа нафталин вместе с водой стекает по центральной трубе (или боковой) в нижнюю часть холодильника 2, служащую промывателем.
В промыватель на одну из верхних полок (или на каждую) непрерывно подается смола с температурой 70–80°С. Смола, соприкасаясь с водой, растворяет содержащийся в ней нафталин.
Промыватель снабжен паровым подогревателем для подогрева стекающей смолы. Объем этой части промывателя позволяет производить отстой смолы от воды за 5–8 ч. Отстоявшаяся смола из промывателя при температуре 50–60°С выводится через смолоотводчик в сборник 3, а затем в хранилище отделения конденсации. Вода из верхней части промывателя перетекает в отстойник 5, где окончательно освобождается от незначительного количества уносимой ею смолы и поступает на охлаждение в градирню 7. Охлажденная вода снова поступает в холодильник для охлаждения газа.
Извлечение нафталина в промывателе достигает 95–100%. Для извлечения нафталина в промыватель подается товарная смола отделения конденсации, которая дополнительно обогащается нафталином и фенолами, и облагораживается в результате уменьшения содержания солей хлора, которые вымываются водой. Расход смолы на извлечение нафталина из воды составляет 2,0–2,5% от количества подаваемой в холодильник охлаждающей воды. Опыт эксплуатации нафталиновых промывателей показал высокую их эффективность.
Для конечного охлаждения коксового газа применяют газовые холодильники непосредственного действия с нафталиновым промывателем (либо без промывателя) диаметром 4,5–6,0 м, высотой 37,4–46,0 м. Изготавливаются холодильники из стали. В газовой части предусматривается 18 полок, в промывателе 8 полок. Дальнейшая интенсификация процесса конечного охлаждения коксового газа, с учетом больших потоков коксового газа, предполагает использование колонных аппаратов с регулярными пластинчатыми насадками из которых наиболее простой является плоскопараллельная. В таких аппаратах при скорости газового потока 3–5 м/с коэффициент теплопередачи увеличивается в 2 и более раз. Аппараты имеют малые габариты, что значительно сокращает капитальные затраты на их сооружение и улучшает технико-экономические показатели работы установок.
7.4. Основы улавливания бензольных углеводородов поглотительным маслом. Регенерация поглотительного масла
На большинстве отечественных коксохимических заводов в качестве поглотителя для улавливания бензольных углеводородов из коксового газа применяют каменноугольное масло и только на некоторых заводах соляровое масло. Хорошее поглотительное масло должно обладать следующими свойствами:
1) достаточная поглотительная способность по отношению ко всем компонентам сырого бензола при низких температурах и малая концентрация их в газе, а также хорошая способность легко выделять их при нагреве;
2) температура начала кипения поглотительного масла должна быть значительно выше температуры кипения компонентов сырого бензола, чтобы при отгонке сырого бензола в него попадало минимальное количество поглотителя;
3) достаточная физико-химическая стойкость, обеспечивающая стабильность поглотительных свойств масла при длительной работе;
4) оптимальная вязкость, при которой может быть достигнуто равномерное и свободное стекание масла по насадке скруббера;
5) минимальная теплоемкость, при которой расход тепла на нагрев масла при отгонке сырого бензола был бы невысоким;
6) масло должно не образовывать с водой эмульсий и легко отстаиваться от воды.
В качестве каменноугольного поглотительного масла применяют фракцию каменноугольной смолы, выкипающую в пределах 230–300°С. Для использования указанной фракции в качестве поглотителя сырого бензола она предварительно подвергается химической очистке для удаления фенолов и пиридиновых оснований.
Приведенным выше требованиям, предъявляемым к жидким поглотителям сырого бензола, полностью не отвечают ни каменноугольное, ни соляровое масло. Каждое из этих масел обладает достоинствами и недостатками.
Свежее каменноугольное масло должно отвечать следующим техническим условиям (масло не должно давать осадка при охлаждении до температуры 0°С):
-
Плотность, кг/м3
1040
Содержание воды, %, не более
0,5
Отгон до 230°С, %, не более
1
Отгон в интервале 230–300°С, %, не менее
95
Содержание фенолов, %, не более
0,7–0,8
Содержание нафталина, %, не более
8–13
Вязкость при 250°С, Э, не более
2
Молекулярная масса
170–180
Содержание фенолов в масле ограничивается потому, что они образуют с водой трудно разделяемые эмульсии и повышают вязкости масла.
Повышенное содержание низкокипящих погонов приводит к возрастанию в сыром бензоле балластных компонентов, т.к. при дистилляции насыщенного бензольными углеводородами масла они переходят в сырой бензол, увеличивая выход сольвент-нафты, кипящей, как правило, выше 180°С. Установление минимального отгона до 300°С обеспечивает малое содержание в масле высококипящих компонентов, обладающих повышенной вязкостью и склонных к образованию осадков. Выпадение кристаллических осадков на насадке скрубберов и в оросительных устройствах является одной из серьезных причин, приводящих к ухудшению работы абсорбционной аппаратуры и к значительному повышению расхода масла.
Потеря поглотительным маслом значительной части легких погонов с сырым бензолом повышает температуру кристаллизации масла, что вызывает необходимость повышения температуры улавливания даже в холодное время года. На практике это приводит к уменьшению степени улавливания бензольных углеводородов. Достоинством каменноугольного поглотительного масла является его большая по сравнению с соляровым поглотительная способность. Поэтому энергетические затраты, связанные с перекачкой оборотного масла, будут меньше, чем при работе на соляровом масле. Каменноугольное масло хорошо отделяется от воды, не образуя стойких эмульсий.
Недостатком каменноугольного поглотительного масла является его Недостаточная химическая стойкость. В процессе длительной работы увеличиваются плотность масла и его вязкость, а также повышается температура его кипения, снижается количество отгона до 300°С, увеличивается молекулярная масса (с 170–180 до 200–220).
Эти изменения качества масла связаны с отгонкой его легкокипящей составляющей при многократном нагревании, с уплотнением (полимеризацией) масла от воздействия на него компонентов коксового газа (кислорода, сероводорода и непредельных соединений). Образующиеся полимеры растворяются в каменноугольном масле, снижая его поглотительную способность. При накоплении в Поглотительном масле значительного количества полимеров они могут выпадать из него в виде осадков, которые забивают насадку скрубберов и ухудшают процесс улавливания бензольных углеводородов.
Свежее соляровое масло должно иметь следующую характеристику: плотность не более 890 кг/м3; содержание воды не более 0,2%; отгон до 350°С не менее 95%, молекулярная масса 230– 240, начало кипения не ниже 265°С.
Так как температура кипения солярового масла более высокая, его потери при улавливании и отгонке сырого бензола меньше, чем потери каменноугольного масла. Отгон сырого бензола до 180°С больше, чем при улавливании каменноугольным маслом. Соляровое масло обладает меньшей поглотительной способностью по сравнению с каменноугольным. Т.к. поглотительная способность масел обратно пропорциональна их молекулярным массам, то поглотительная способность солярового масла составляет 180 : 240 = 0,75 поглотительной способности каменноугольного масла. Значит для обеспечения одинаковой степени улавливания сырого бензола при работе с соляровым маслом его необходимо иметь в обороте в 1,32 раза больше, чем каменноугольного. Учитывая, однако, большую стойкость солярового поглотительного масла по сравнению с каменноугольным, а также то, что в процессе работы оно почти не изменяет своей поглотительной способности, указанная выше разница количества масла в обороте практически несколько ниже.
Соляровое масло в противоположность каменноугольному не изменяет в процессе работы вязкости и молекулярной массы. Следовательно, поглотительная способность его почти не изменяется и отличается высокой стабильностью. Однако и при работе на соляровом масле также образуются полимеры, которые в нем не растворяются, а выпадают, образуя так называемый шлам. Последний оседает на скрубберной насадке, увеличивая сопротивление газовому потоку, и в теплообменной и дистилляционной аппаратуре, приводит к серьезному нарушению технологического режима и понижению ее эффективности.
Наличие шлама в масле способствует образованию с водой весьма стойкой эмульсии, для разрушения которой требуются специальные аппараты деэмульсаторы, где происходит нагрев эмульсии до 70–80°С и отстаивание.
Основными причинами, вызывающими образование шлама в соляровом масле и загустевания каменноугольного масла, являются:
1) наличие в коксовом газе смоляного тумана, т.е. несконденсировавшихся легкокипящих частей смолы, которые растворяются в масле;
2) содержание в газе сероводорода и кислорода, что способствует полимеризации непредельных соединений, находящихся в масле в результате поглощения их из газа;
3) наличие в газе аммиака, который, растворяясь в масле, способствует поглощению сероводорода и образованию сульфидов и элементарной серы, ускоряющих процесс полимеризации;
4) повторяемое многократное подогревание масла до температур, при которых происходит полимеризация непредельных соединений, находящихся в самом масле и поглощенных из газа.
Для стабилизации качества поглотительного масла, обеспечения чистоты аппаратуры и полного улавливания бензольных углеводородов из коксового газа применяют два метода регенерации (восстановления) поглотительного масла: паровой и в трубчатой печи. На регенерацию непрерывно отводится около 1% масла, находящегося в обороте.
Паровой метод осуществляется в паровом регенераторе путем подогрева масла до 170–175°С с последующей отгонкой масла от полимеров большим количеством острого пара. Подогрев масла в регенераторе производится глухим паром. При паровой регенерации не удается резко улучшить качество оборотного поглотительного масла, особенно каменноугольного.
Более эффективным методом является регенерация масла путем его подогрева в трубчатой печи до 300–310°С. Подогрев, масла до столь высокой температуры производится для ускорения полимеризации ненасыщенных соединений и перевода потенциальных смол в фактические. При этом температура нагрева масла должна быть выше максимальной температуры подогрева масла при дистилляции бензола, что позволяет предупредить забивание аппаратуры.
Для четкого разделения компонентов масла и полимеров установлена ректификационная тарельчатая колонна, орошаемая подогретым маслом. На рис. 13 приведена технологическая схема установки регенерации каменноугольного поглотительного масла. Регенерируемое масло после выделения сырого бензола насосом 1 прокачивается через конвекционную и радиантную секции трубчатой печи 2 и с температурой 300–310°С направляется в ректификационную колонну 3, куда вводится также перегретый водяной пар. Под действием острого пара большая часть масла переходит в парообразное состояние. На верхнюю тарелку подается орошение и происходит ректификация паров с выделением полимеров. Последние стекают в нижнюю часть колонны и через гидрозатвор 8 выводятся в сборник полимеров 9. Пары масла и воды из верхней части ректификационной колонны отводятся в конденсатор 4 и холодильник 5, охлаждаемые в противоточном направлении технической водой. В сепараторе 6 масло отстаивается от воды и возвращается в цикл улав-
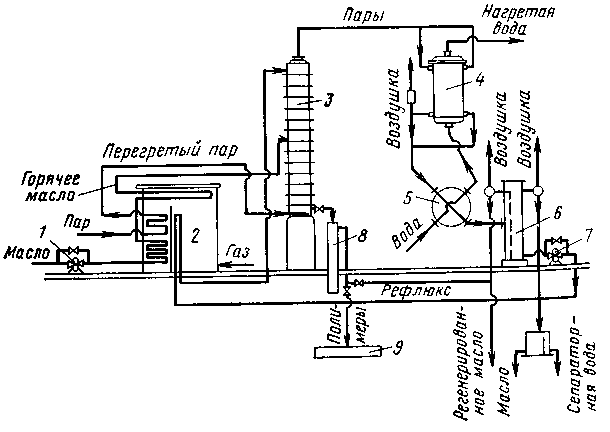
Рис. 13. Схема регенерации каменноугольного поглотительного масла с применением трубчатой печи:
1 – насос; 2 – трубчатая печь; 3 – ректификационная колонна; 4 – конденсатор; 5 – холодильник; 6 – сепаратор; 7 – рефлюксный насос; 8 – гидрозатвор; 9 – сборник полимеров
ливания. Часть масла рефлюксным насосом 7 прокачивается через расположенный в трубчатой печи нагревательный экран и в подогретом виде подается в качестве орошения на верхнюю тарелку ректификационной колонны. Через воздушники конденсатора 5 и сепаратора 6 непрерывно выводятся из оборотного масла соединения, вызывающие коррозию аппаратуры (H2S, HCN и др.).
Выход регенерированного масла зависит от качества оборотного масла и колеблется в пределах 80–90% от исходного масла.