Процессы и технологии синтеза алмазных поликристаллических композиционных материалов на основе разработанных сплавов-катализаторов Ni-X(Mo, Cr, Ti, B)
Вид материала | Автореферат диссертации |
- 6-я Московская Международная конференция «Теория и практика технологии производства, 64.17kb.
- Комплексная инновационная программа повышения квалификации и профессиональной переподготовки, 22.24kb.
- Ознакомление с основными марками цветных сплавов и композиционных материалов, их свойствами, 385.05kb.
- Жаропрочность платины, палладия и их сплавов, 427.22kb.
- Совершенствование технологии производства композиционных материалов на основе древесных, 644.07kb.
- Программы: подготовка специалистов в области техники и технологии, 305.23kb.
- Разработка состава и технологии спекания дисперсно-упрочнённых композиционных материалов, 481.56kb.
- Рассматриваются вопросы изучения свойств наноалмазов детонационного синтеза, 1738.6kb.
- 150100. 62 Металлургия металлургия, 183.45kb.
- Пояснительная записка к курсовому проекту по курсу: «Процессы и аппараты химической, 52.08kb.
На правах рукописи
Лаптев Александр Иванович
Процессы и технологии синтеза алмазных
поликристаллических композиционных
материалов на основе разработанных
сплавов-катализаторов Ni–X(Mo, Cr, Ti, B)
Специальность 05.16.06 - Порошковая
металлургия и композиционные материалы
Автореферат диссертации на соискание
ученой степени доктора технических наук
Москва 2009
Работа выполнена в Федеральном государственном образовательном учреждении высшего профессионального образования "Национальный исследовательский технологический университет "МИСиС"
Официальные оппоненты:
доктор технических наук
профессор
член корреспондент РАН, Костиков Валерий Иванович
доктор физико-математических наук,
профессор Бланк Владимир Давыдович
доктор химических наук,
профессор Спицин Борис Владимирович
Ведущая организация: Открытое акционерное общество "Московское производственное объединение по выпуску алмазного инструмента" (ОАО "МПО по ВАИ")
Защита диссертации состоится 09 декабря 2009 г. В 14 30 в аудитории К-541 на заседании диссертационного совета Д 212.132.05 при Федеральном государственном образовательном учреждении высшего профессионального образования "Национальный исследовательский технологический университет "МИСиС" по адресу: 119049, Москва, Крымский вал, д.3.
С диссертацией можно ознакомиться в библиотеке Федерального государственного образовательного учреждения высшего профессионального образования "Национальный исследовательский технологический университет "МИСиС"
Автореферат разослан ‘’ ‘’___________2009г.
Справки по телефону: 638-44-64
Ученый секретарь
диссертационного совета Т.А. Лобова
ОБЩАЯ ХАРАКТЕРИСТИКА РАБОТЫ
Актуальность работы.
Развитие современной промышленности невозможно без использования сверхтвердых материалов, в частности, поликристаллических алмазов в различных областях: машиностроении, строительстве, геологоразведке. Одним из перспективных направлений получения поликристаллических алмазов является их синтез из углеграфитовых материалов. Приоритет синтеза поликристаллических алмазов принадлежит отечественной физике высоких давлений. Впервые в мире поликристаллы типа карбонадо были синтезированы коллективом ученых Института физики высоких давлений РАН под руководством академика Л.Ф. Верещагина. Эти поликристаллы обладают уникальной твердостью. Однако для получения высококачественных поликристаллов требуются экстремально высокие параметры синтеза (давления выше 10 ГПа при температурах выше 2000К). Достижение таких условий в настоящее время является трудной технической задачей. Твердосплавная технологическая оснастка под действием огромных нагрузок быстро разрушается, что приводит к повышенному расходу твердого сплава и из-за изменения режимов синтеза поликристаллы получаются нестабильного качества. Поэтому требуется применение дорогостоящего контроля механических свойств каждого синтезированного образца, что приводит к значительному увеличению себестоимости. Кроме этого, невысокая термостойкость поликристаллических алмазов из-за большого содержания сплавов-катализаторов сдерживает широкое их использование в алмазном инструменте. Механизмы образования поликристаллических алмазов, формирования их структуры и влияния на нее условий синтеза, состава и свойств сплава-катализатора, свойств исходного углеродного материала и других факторов до настоящего времени остаются дискуссионными. Поэтому разработка эффективных процессов синтеза алмазных поликристаллических композиционных материалов (АПКМ) для применения в различном алмазном инструменте несомненно является актуальной.
Цель работы.
Изучение механизма и кинетики формирования алмазных поликристаллических композиционных материалов при использовании сплавов-катализаторов системы Ni-X(Mo, Cr, Ti, B) и на этой основе разработка технологий и организация серийного производства АПКМ повышенной прочности широкой области применения.
Для достижения поставленной цели в работе решали следующие задачи:
- исследование закономерностей синтеза АПКМ и механизмов инфильтрации расплавов-катализаторов в зависимости от условий синтеза;
- изучение физических, химических и механических свойств, особенностей структуры АПКМ в зависимости от условий их получения и состава;
- разработка новых составов катализаторов, позволяющих повысить прочность, износостойкость и термостойкость АПКМ.
- исследование влияния генезиса искусственных графитов на синтез АПКМ и разработка критерия их выбора для синтеза высококачественных алмазных композитов;
- создание и внедрение в производство технологии изготовления легированных катализаторов методами порошковой металлургии и последующего синтеза АКПМ с изготовлением алмазного инструмента повышенной износостойкости различного назначения.
Методики исследования.
Работа выполнена с применением современной аппаратуры высокого давления (до 12 ГПа), привлечением современных физико-химических методов анализа: химического, спектрального и микрорентгеноспектрального, рентгенофазового и рентгеноструктурного, электронно-оптического, металлографического, фрактографического, дифференциально-термического; с использованием современных методов определения механических свойств и абразивной стойкости алмазных поликристаллов. Определение технологических параметров разработанного алмазного инструмента проводилось на современных стендах и серийном оборудовании. В работе также использовалась вычислительная техника для расчета рентгенограмм и профилограмм, а также обработки полученных экспериментальных зависимостей.
Научная новизна.
1. Предложен механизм формирования алмазного поликристаллического композиционного материала, основанный на том, что в процессе плавления сплава-катализатора при высоком давлении формирование фронта кристаллизации алмаза происходит за счет градиента давлений, возникающих из-за объемного эффекта полиморфного превращения графита в алмаз, что приводит к инфильтрации расплава по внутренним межкристаллитным каналам и по поверхности растущего композита, значимость вклада каждого из которых определяется давлением синтеза.
2. Обнаружено образование промежуточных фаз (лонсдейлита) при синтезе алмазного поликристаллического композиционного материала в области термодинамической стабильности алмаза при полиморфном превращении графита в алмаз, которое протекает как в жидкой, так и твердой фазах и определяется структурными свойствами графита.
3. Установлены закономерности изменения структуры алмазного поликристаллического композиционного материала в процессе синтеза, выражающиеся в снижении упорядочения алмазных кристаллитов в направлении роста [110] с увеличением давления синтеза от 6,0 ГПа до 10-12 ГПа, что позволяет управлять свойствами получаемых композитов.
4. Установлена связь между химическим составом сплавов-катализаторов и механическими свойствами синтезируемых алмазных поликристаллических композиционных материалов, выражающаяся в том, что с повышением прочности сплава-катализатора наблюдается упрочнение металлической связки АПКМ, а также алмазного композита в целом.
5. Выявлена связь между стойкостью к окислению алмазного поликристаллического композиционного материала и химическим составом его металлической связки, заключающаяся в том, что стойкость АПКМ к окислению возрастает с увеличением содержания боридов в связке из-за формирования защитных оксидных слоев на поверхности алмазных композитов при их нагреве.
Практическая ценность.
1. Разработаны составы сплавов-катализаторов, применение которых позволяет синтезировать алмазные поликристаллические композиционные материалы с повышенной прочностью и износостойкостью; повысить температуру начала окисления поликристаллических алмазов с 910 до 1040 К и замедлить скорость их окисления при более высоких температурах за счет образования поверхностных оксидных пленок; увеличить температуру начала разупрочнения АПКМ с 970 до 1220 К за счет снижения термонапряжений, возникающих в них при нагреве. Разработанные методы получения и составы сплавов-катализаторов, защищены авторскими свидетельствами на изобретения.
2. Разработаны критерии оценки прочностных свойств синтезируемых алмазных поликристаллических композиционных материалов по их структурным и магнитным свойствам. В первом случае пригодность для изготовления ответственного однокристального инструмента оценивается по полюсной плотности и параметру рассеяния текстуры алмазного композиционного материала, во втором – по магнитным свойствам. Для определения магнитных свойств рекомендован к использованию широкодиапазонный измеритель "Магнит 704", предназначенный для определения количества ферромагнитных включений в абразивных материалах. Данный метод применим для оценки пригодности АПКМ как в однокристальном, так многокристальном инструменте.
3. Установлено влияние давления синтеза алмазных поликристаллических композиционных материалов на их прочность. Определено оптимальное давление синтеза, позволяющее синтезировать алмазные высокопрочные композиты при умеренных давлениях, что позволяет более чем в 2 раза уменьшить расход твердого сплава.
4. Разработаны технологии синтеза высокопрочных и термостойких АПКМ с использованием сплавов катализаторов сложного химического состава для применения в алмазном инструменте расширенной области применения.
Разработанные технологии изготовления легированных катализаторов, синтеза АПКМ с их использованием, были внедрены на ЭМЗ г. Лермонтов, лаборатории НИЛ ВТМ МИСиС. На ЭМЗ было синтезировано более 8 млн. карат алмазных композитов с повышенной абразивной способностью, что позволило выпустить более 38 тыс. алмазных буровых коронок типа КСК и 47 тыс. шлифовальных головок типа ШГК, что подтверждено соответствующими актами.
5. Разработаны технологии производства широкой номенклатуры высокоэффективного алмазного инструмента. Режущий, выглаживающий, конструкционный и сопловой инструменты с использованием модифицированных АПКМ используются в военной области, геологоразведке, машиностроении и стройиндустрии.
Разработанные технологии изготовления резцов, выглаживателей, контактных опор, наконечников активного контроля, сопел с использованием высокопрочных АПКМ применяются в лаборатории НИЛ ВТМ МИСиС и на Томилинском заводе алмазного инструмента (ТЗАИ). Алмазные шлифпорошки, полученные из разработанных АПКМ, используются при изготовлении буровых коронок и шлифовального инструмента на опытном производстве ИФВД РАН.
Разработка технологии и освоение опытно-промышленного выпуска АПКМ и инструмента из них в условиях лаборатории ВТМ МИСиС позволило с 2000 года и по настоящее время выполнить хозяйственных договоров по поставке НТП более чем на 10 млн. рублей. Разработка технологии алмазных формообразующих сопел для газо- и жидкостно-абразивной резки различных материалов из опытных АПКМ была отмечена дипломом Министерства науки и технологий РФ.
Основные положения, выносимые на защиту:
- установленные закономерности и механизм формирования алмазного поликристаллического композиционного материала;
- результаты исследований структурных особенностей АПКМ и влияние на них условий синтеза;
- результаты исследований по влиянию происхождения и свойств графита на процесс синтеза и свойства поликристаллических алмазов, установленный критерий выбора графита для синтеза алмазов, закономерности образования АПКМ из пирографита;
- закономерности влияния составов сплавов-катализаторов на процесс синтеза, состав АПКМ, его прочностные свойства и термостойкость;
- результаты исследований процесса окисления АПКМ и влиянию на него состава металлической связки;
- закономерности изменения магнитных свойств АПКМ в зависимости от состава сплава-катализатора и условий синтеза;
- методики определения механических свойств АПКМ и их абразивной стойкости;
- конструкции алмазных инструментов и технологии их изготовления;
- результаты испытаний алмазных инструментов в машиностроении, геологоразведке и строительной промышленности и рекомендации по их применению.
В совокупности перечисленные положения составляют новые научные представления о механизме процесса синтеза алмазных поликристаллических композиционных материалов и влиянию на этот процесс различных факторов (свойств сплава-катализатора, исходного углеродного материала, условий синтеза).
Личный вклад автора.
Автор непосредственно принимал участие во всех этапах выполнения работы по исследованию процесса образования алмазных поликристаллических композиционных материалов, изучению их структурных, механических, физических, химических, эксплуатационных свойств и термостойкости; созданию метода получения катализаторов сложного химического состава; разработке конструкций алмазного инструмента на основе полученных АПКМ и проведению его стендовых испытаний.
При непосредственном участии автора созданы опытные и промышленные технологии изготовления алмазных поликристаллических композиционных материалов и инструмента на их основе. Автор участвовал во внедрении разработанных технологий и проведении их производственных испытаний на промышленных предприятиях.
Автор осуществляет постоянный контроль над внедренными технологиями и оказывает научно-техническую помощь производителям инструмента.
Апробация работы. Основные положения результатов работы докладывались на Уральской региональной конференции по порошковой металлургии и композиционным материалам (Пермь, 1985); XV Всесоюзной научно-технической конференции (Киев, 1985); Российской научно-технической конференции "Композиционные, керамические, порошковые материалы и покрытия" (М.: МГАТУ, 1995), 50-й ежегодном конгрессе Бразильской Ассоциации Металлургии и Материалов (Бразилия, Сан-Педро, 1995), XXXVIII European High Pressure Research Group Meeting 2000 (Germany, Kroster Banz, 2000), V Всероссийской конференции (М.: МИФИ, 2000), International Science and Technology Conference (Киев, ИСМ, 2001); XXXIX European High Pressure Research Group Meeting (Santander, Spain, 2001); научно-технической конференции по современным проблемам производства и эксплуатации углеродной продукции (Челябинск, 2000); EVRO PM 2002 European Conference on Hard Materials and Diamond Tools (Lausanne, Switzerland, 2002); V (2002), VI (2003), VII (2004), VIII (2005), IX (2006), Х (2007), XI (2008), XII (2009) международных конференциях "Породоразрушающий и металлообрабатывающий инструмент- техника и технология его изготовления и применения" ИСМ им. В.Н. Бакуля НАН Украины; III (2004), IV (2005) и V (2006) Международных конференциях “Углерод: фундаментальные проблемы науки, материаловедение, технология” М.: МГУ им. М.В. Ломоносова.
Публикации. По теме диссертации опубликованы 67 научных трудов, из них 27 статей в журналах, рекомендованных ВАК, 11 авторских свидетельств и 2 патента РФ.
Структура и объем работы. Диссертация состоит из введения, 8 глав, общих выводов, списка литературы и 11 приложений. Материалы диссертации изложены на 360 листах, включают 130 рисунков, 105 таблиц и список литературы из 484 наименований.
В первой главе рассмотрено современное состояние методов получения углеродных материалов, их термодинамические и структурные свойства, термодинамические основы синтеза алмазных материалов (порошков и поликристаллов), сформулированы требования к камерам высокого давления для синтеза алмазных поликристаллических композиционных материалов.
Во второй главе рассмотрены состав и свойства природных и синтетических поликристаллических алмазов, методы синтеза алмазных поликристаллов. Проведено изучение состава сплава-катализатора на условия получения и состав АПКМ. Описаны методы и результаты изучения структурных свойств и текстуры АПКМ в зависимости от условий их синтеза.
Третья глава содержит результаты исследований по влиянию структуры и химического состава исходных углеродных материалов на процесс алмазообразования. Описаны результаты работы по синтезу порошков и поликристаллов алмаза из различных природных и искусственных графитов, показана взаимосвязь между этими процессами синтеза, разработан критерий выбора углеродного материала для различных процессов синтеза, изучен механизм образования поликристаллического алмаза из пирографита.
Четвертая глава содержит результаты исследований по влиянию термодинамических условий синтеза и химического состава катализатора на свойства АПКМ, результаты изучения адгезионных свойств сплавов-катализаторов и их влияние на процесс образования алмазного композита. Проведено изучение синтеза АПКМ в различных металлических системах и сформулированы требования к свойствам исходных сплавов-катализаторов.
Пятая глава содержит результаты исследований по изучению процесса окисления АПКМ. Показано, что процесс окисления является многостадийным процессом, его интенсивность зависит от используемого сплава-катализатора. Нагрев АПКМ, как в вакууме, так и в окислительной атмосфере приводит к снижению его прочности. Введение бора в катализатор приводит к образованию боридов и повышению термостойкости алмазных композитов. Термостойкость АПКМ может быть повышена при использовании высоких давлений при их нагреве, например при изготовлении инструмента.
Шестая глава содержит результаты исследований магнитных свойств АПКМ и влиянию на них условий синтеза и состава сплава-катализатора. Показано, что количество ферромагнитных включений снижается с повышением давления синтеза.
Седьмая глава содержит результаты исследований по кинетике и механизму формирования алмазных поликристаллических композиционных материалов. Установлена линейная зависимость размера композита от времени синтеза. Давление синтеза определяет скорость образования АПКМ.
Восьмая глава содержит результаты исследований по механическим, технологическим и эксплуатационным свойствам АПКМ и инструмента, изготовленного с их применением. Сформулированы представления о применяемых режимах изготовления и эксплуатации разработанного алмазного инструмента. Показана перспективность и эффективность серийного применения разработанной технологии для изготовления широкого класса алмазных инструментов.
Содержание работы
1 Методы получения, состав и строение поликристаллических алмазов
Основой классификации природных поликристаллических алмазов являются разновидности их структуры. Структура поликристалла зависит от условий его роста и определяет физические, механические и эксплуатационные его свойства, поэтому в литературе изучению структуры алмазных поликристаллов уделяется большое внимание. Природный карбонадо впервые был обнаружен в Бразилии в 1843 г. Характерный размер карбонадо из Бразилии: 3-5 мм вдоль длинной оси, весом 0,6 каратов, хотя встречаются и крупные карбонадо весом в сотни каратов. Рентгеновская дифракция показывает наличие беспорядочно ориентированных алмазных зерен, присутствие четко очерченного ореола от аморфного углерода, наличие интенсивного фона, полученного от присутствия графитизации зерен.
Второй промышленно применяемой разновидностью природных поликристаллических алмазов является баллас. Баллас представляет собой поликристаллический алмаз круглой формы с радиально-лучистым строением кристаллитов. Размер кристаллитов 10-200 мкм, среднее значение – 30-40 мкм. Отличие балласов – это многократное двойниковое срастание кристаллитов.
Синтетические поликристаллические алмазы, синтезируемые из углеродных материалов в присутствии металлов-катализаторов, получили название "баллас" и "карбонадо" из-за сходства структуры с природными поликристаллическими алмазами. Синтез алмазных поликристаллов "баллас" и "карбонадо" проводят при статических давлениях в аппаратах высокого давления (АВД) типа "наковальня с углублениями". Давление в реакционной зоне создается в результате пластического истечения материала контейнера из полости углублений. Наиболее широко в отечественной промышленности представлены два типа этих АВД – "чечевица" и "тороид". АВД "чечевица" предназначена для создания давлений до 6,5 ГПа и применяется для синтеза поликристаллов "баллас" (АСБ). АВД "тороид" имеет дополнительное тороидальное кольцо, которое позволяет повысить давление до 11-12 ГПа, и применяется при синтезе поликристаллов "карбонадо" (АСПК). Как для получения АСБ, так и для получения АСПК характерна схема сборки камеры высокого давления, при которой металл-катализатор на основе металлов Fe, Ni, Co и их сплавов в виде стержня устанавливают в углеродсодержащем материале. Один из концов этого стержня имеет электрический контакт с охлаждаемыми участками АВД.
Условия образования алмаза определяются конструкцией используемой камеры, типом исходного углеродного материала, составом катализатора, давлением и температурой. Влияние каждого из перечисленных факторов весьма существенно. Проще всего влиять на условия образования алмаза изменением температуры процесса. Определению минимальной температуры алмазообразования для различных сплавов-катализаторов при синтезе монокристаллов и порошков уделено достаточно большое внимание. Это обусловлено требованием получения качественных монокристаллов алмаза, процесс образования которых продолжается длительное время, до нескольких суток. Для получения качественного монокристалла скорость переноса углерода к растущему алмазу должна быть сбалансирована со скоростью его роста. За минимальную температуру образования алмаза принимается температура образования жидкой фазы в системе расплав–углеродный материал при определенном давлении синтеза. Определение минимальной температуры образования алмазов важно как с научной, так и с практической точки зрения, поскольку температура контактного плавления при атмосферном давлении, например, в системе железо-углерод отличается от температуры плавления чистого железа почти на 400 градусов. Повышение температуры синтеза требует перехода на новую камеру, позволяющую создать значительно более высокие давления. Обычно ошибочно оценивают температуру образования алмазного поликристалла по температуре контактного плавления в системе сплав-графит.
В настоящей работе синтез алмазных поликристаллов проводили при давлениях 6,0-12,0 ГПа. Выбор сплавов-катализаторов проводили на основе анализа литературных данных по их химическим и механическим свойствам, влиянию на синтез алмаза. За основу были выбраны никелевые сплавы, легированные молибденом, хромом, титаном, танталом, кобальтом, углеродом и бором. Сплаву Х20Н80 было уделено повышенное внимание, т.к. он нашел наиболее широкое применение в промышленности. Но, поскольку обоснования по выбору этого сплава-катализатора в литературе представлено не было, то в настоящей работе проводили дополнительное изучение сплавов системы Ni-Cr с содержанием Cr до 50 %. Р, Т – области синтеза алмазных поликристаллов "АСБ" и "АСПК", установленные нами экспериментально, представлены на рисунке 1.
Определение минимальной температуры начала образования (Тн.обр.) АПКМ проводили при их синтезе из графита МГОСЧ при давлении 8,0 ГПа в камере типа "тороид" в присутствии различных сплавов-катализаторов. Тн.обр. определяли по началу уменьшения мощности, потребляемой КВД, вследствие превращения графита в алмаз. Для сплавов-катализаторов на основе систем никель-хром, никель-молибден различного состава и Х20Н80 с добавками углерода, бора, титана, молибдена и тантала установлено, что Тн.обр. АПКМ значительно превышает минимальную температуру алмазообразования. Например, при использовании в качестве катализатора никеля минимальная температура алмазообразования равна 1700К, а Тн.обр. АПКМ – 1850К, при использовании хрома -2400К и 2600К соответственно. При введении в сплав Х20Н80 углерода Тн.обр. АПКМ уменьшается до 1550 К при содержании углерода 3,5 %. Такое содержание углерода в сплаве Х20Н80 соответствует эвтектическому составу системы Ni-Cr-C с температурой плавления 1318 К. При сопоставлении экспериментальных данных с диаграммами состояния систем Ni-Cr, Ni-Mo, Ni-Cr-C, Ni-Cr-Ti, Ni-Cr-Ta, Ni-Cr-Mo можно сделать вывод, о том что Тн.обр. АПКМ определяется температурой плавления сплава-катализатора. Видимо, в процессе синтеза АПКМ значительного насыщения сплава-катализатора углеродом не происходит из-за скоротечности процесса. Об этом красноречиво свидетельствует уменьшение Тн.обр. АПКМ при введении углерода в сплав Х20Н80. Увеличение содержания углерода в сплаве Х20Н80-С до эвтектического состава приводит к уменьшению температуры его плавления, в то время как температура контактного плавления в системе Х20Н80–графит остается неизменной.
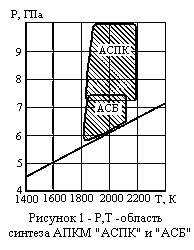
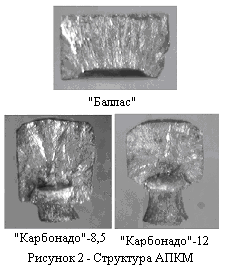
АПКМ, полученные при минимальных температурах синтеза, имеют небольшие размеры. Для получения их удовлетворительных размеров для инструментального применения необходимо увеличение температуры, превышающей минимальную на 100-200 градусов. Больший перегрев приводит не к дальнейшему увеличению размера АПКМ, а, главным образом, к ухудшению их качества из-за смещения области его образования к области стабильности графита.
Синтезируемые АПКМ состоят из алмазной и металлической фаз. Количество последней может достигать 20 %. В ряде работ отмечается сходство химических составов исходного сплава (сплава-катализатора), способствующего превращению графита в алмаз, и металлической фазы АПКМ. Нужно отметить, что, поскольку состав металлической фазы поликристалла существенно влияет на его прочностные свойства, необходимо знать влияние состава сплава-катализатора на количество и состав металлической фазы алмазного поликристалла. Анализ литературных данных по обсуждаемому вопросу затруднен тем обстоятельством, что часто названия "баллас" и "карбонадо" присваиваются поликристаллам не по их структурным свойствам, а по применяемым технологическим процессам. В этой связи необходимо уточнить, что условия получения поликристаллов оказывают определяющее влияние на его структуру и свойства.
Подробное изучение влияния состава исходного металла-катализатора на состав неалмазной фазы АПКМ проводилось нами при использовании в качестве катализаторов никеля, сплавов на основе систем никель-хром, никель-молибден. Содержание металлов в АПКМ определяли методом количественного спектрального анализа после механического удаления непрореагировавшей части стержня сплава-катализатора.
Данные количественного спектрального анализа алмазных композитов, синтезированных с использованием сплавов-катализаторов системы никель- хром и легированных бором, титаном, танталом и молибденом, показали, что состав металлической фазы при введении добавок до 10 % соответствует исходному сплаву-катализатору. Дальнейшее повышение содержания молибдена и тантала в катализаторе приводит к некоторому обеднению композитов данным легирующим элементом, возможно, из-за неполного проплавления металлического стержня во время образования АПКМ. Содержание молибдена и тантала, обнаруженное в алмазных композитах, соответствует их содержанию в жидкой фазе сплава-катализатора.
Результаты по изучению строения синтетических "балласов" и "карбонадо", полученные в различных работах, часто находятся в некотором противоречии. Также, в литературе имеются отдельные данные, которые свидетельствуют о существовании преимущественного направления роста кристаллитов при синтезе АПКМ. Однако каких либо систематизированных исследований по изучению влияния условий формирования алмазных композитов на их текстурное строение не проводилось. Поскольку направление роста кристаллитов влияет на механические свойства АПКМ и эксплуатационные характеристики инструментов, изготовленных из них, нами было проведено изучение структурных особенностей строения алмазных композитов и влияния на них условий синтеза. В качестве объекта исследования были выбраны АПКМ "баллас", синтезированные при давлении 5,5-6,5 ГПа; "карбонадо", синтезированные при давлении 8,5 ГПа ("карбонадо"-8,5) и при давлении 12 ГПа ("карбонадо"-12). В качестве катализатора использовали никель. Поликристаллы "баллас" представляли собой цилиндры диаметром 5,5 мм, высотой 3 мм; "карбонадо" - цилиндры диаметром 4 мм, высотой 4 мм.
Изучение сколов АПКМ (рисунок 2) показало, что "баллас" состоит из крупных столбчатых кристаллитов, расположенных перпендикулярно основанию цилиндра. Кристаллиты, слагающие "карбонадо"-8,5; также направлены ориентированно от катализатора к периферии АПКМ. Но их размер значительно меньше и они разориентированы в направлении роста. Еще более эта тенденция проявляется для "карбонадо"-12. Для некоторых образцов наблюдается слабо выраженная преимущественная ориентация кристаллитов, для других она отсутствует.
Для изучения текстуры алмазов были изготовлены шлифы на поверхности АПКМ в соответствии с рисунком 3. Применяли метод панорамного рентгеноструктурного анализа. Панорамную съемку проводили со стороны торцевой поверхности АПКМ (рисунок 3, вид А). В таблице 1 приведены результаты количественного фазового анализа АПКМ. Как следует из представленных в таблице 1 данных, текстура алмазных кристаллитов в АПКМ существенно изменяется при изменении условий синтеза от ярко выраженной [110] для "балласа" до слабой [110] или даже [111] для "карбонадо"-12. С целью определения распределения содержания никеля в поликристаллах проводили съемку АПКМ "карбонадо"-8,5 с торцевой поверхности после синтеза до изготовления шлифа и после изготовления шлифа. Количество никеля в поверхностной зоне нешлифованного "карбонадо"-8,5 составило 18,3 % против 11,1 % для шлифованного; размер ОКР –52,6 нм для нешлифованного против 34,3 нм для шлифованного. Полюсная плотность в направлении [110] составила 1,55; параметр рассеивания -20 для шлифованного; для нешлифованного "карбонадо"-8,5 текстуры обнаружено не было. Из этих данных следует, что текстура в направлении роста [110], четко выраженная для шлифованного АПКМ, для нешлифованного АПКМ не проявляется, т.е. поверхность АПКМ покрыта слоем нетекстурированных мелких кристаллитов алмаза. Кроме того, содержание никеля (по данным количественного рентгенофазового анализа) на поверхности растущего композита значительно превышает его содержание во внутренних областях.
При изучении структурного строения АПКМ применяли метод локального рентгеноструктурного анализа. Локальные исследования проводили с использованием специального коллиматора, создающего диаметр рентгеновского зонда ~ 1 мм. Точки локальной съемки обозначены цифрами (рисунок 3, вид А, вид Б). Интервал съемки 2 = 49-54 и 89-93, шаг съемки 0,2, экспозиция 30 секунд, излучение -СоК. Для "балласа", из-за его увеличенного диаметра, точка 2 (рисунок 3) была разбита на две точки 2' (ближе к центру) и 2" (ближе к краю). Обобщенные результаты рентгеновского анализа приведены в таблице 2.
Анализ данных, приведенных в таблице 1, позволяет заключить, что наиболее однородной по объему структурой обладают поликристаллы типа "баллас", получаемые при относительно низком давлении, с невысокими скоростями роста. Причем направление [110] параллельно направлению роста АПКМ и параллельно оси камеры высокого давления. Никель, присутствующий в композите, закономерно текстурирован (таблица 2) и распределен довольно равномерно по его объему. Текстура отдельных областей "карбонадо"-12 значительно слабее выражена и изменяется от [110] до [111]. Включения никеля распределены неоднородно и менее текстурированы, чем у "балласа". Для различных образцов "карбонадо"-12 текстура отдельных частей, даже центральных, меняется от [110] до [111]. Структура "карбонадо"-8,5 является промежуточной между "балласом" и "карбонадо"-12. Распределение никеля неравномерное. Центральная часть имеет текстуру [110]. На периферии композита встречаются области диаметром до 1мм с текстурой [110] и [111] в зависимости от выхода на поверхность композита центрального тела столбчатого кристаллита.
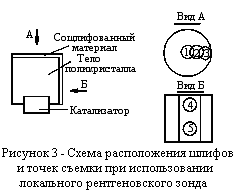

Строение АПКМ можно представить следующей схемой (рисунок 4). Цифрами обозначены алмазные столбчатые кристаллиты, растущие от области металла-катализатора. Столбчатые кристаллиты, центральные тела дендритов, состоят из закономерно ориентированных кристаллитов алмазов в направлении [110] параллельном направлению роста. Пространство между столбчатыми кристаллами зарастает кристаллитами алмаза закономерно к ним ориентированными. При снижении давления синтеза скорость роста алмазного композита замедляется и текстура становится более четко выраженной. При повышении давления происходит увеличение скорости роста алмазных композитов, измельчение алмазных кристаллитов, и при очень высоких давлениях (~12 ГПа) текстурных закономерностей в направлении роста алмазных кристаллитов не выявляется. Области неравномерности при этом сравнимы с размером рентгеновского зонда. В результате изучения структурных особенностей строения АПКМ установлено, что для измельчения размеров алмазных кристаллитов и снижения их текстурованности необходимо синтез АПКМ проводить при высоких давлениях и возможно более высоких скоростях роста, строение АПКМ необходимо учитывать при изготовлении их них алмазного инструмента.
Таблица 1 – Данные количественного фазового анализа АПКМ (метод Ритвельда)
№ | Образец | Фаза | Количество | Параметры фазы | Описание текстуры алмаза | |||||
об. % | % | а, ![]() | ОКР | ,% | Направление | Полюсная плотность | Параметр рассеяния текстуры, град.3 | |||
1 | "Баллас" | Алмаз | 94,9 | 88 | 3,570 | 640 | 0,044 | 100 | 0,5 | 25 |
Никель | 5,1 | 12 | 3,547 | 270 | 0,099 | 110 | 3,2 | 15 | ||
| | | | | | 111 | 0,25 | 15 | ||
2 | "Карбонадо"-8,5 | Алмаз | 93,1 | 84,2 | 3,571 | 600 | 0,023 | 100 | 0,5 | 25 |
Никель | 6,9 | 15,8 | 3,548 | 250 | 0,123 | 110 | 2,7 | 15 | ||
| | | | | | 111 | 0,35 | 15 | ||
31 | "Карбонадо"-8,5 | Алмаз | 95,6 | 89,6 | 3,567 | 460 | 0,059 | 100 | 0,98 | - |
Никель | 4,4 | 10,4 | 3,539 | 280 | 0,126 | 110 | 1,85 | 12 | ||
| | | | | | 111 | 0,65 | 15 | ||
4 | "Карбонадо"-12 | Алмаз | 93,7 | 85,5 | 3,573 | 560 | 0,088 | 100 | 1,15 | 7 |
Никель | 6,3 | 14,5 | 3,558 | 220 | 0,134 | 110 | 0,95 | - | ||
| | | | | | 111 | 1,45 | 12 | ||
52 | "Карбонадо"-12 | Алмаз | 91,8 | 81,8 | 3,568 | 460 | 0,056 | 100 | 0,6 | 12 |
Никель | 8,2 | 18,2 | 3,551 | 270 | 0,155 | 110 | 1,15 | 15 | ||
| | | | | | 111 | 0,45 | 15 |
Примечание 1. №3 -"карбонадо"-8,5. Начальный период роста АПКМ, высота образца -2,5мм.
Примечание 2. №5 -"карбонадо"-12. Съемка поверхности без изготовления шлифа.
Примечание 3. Параметр рассеяния текстуры оценивали по углу , при котором полюсная плотность уменьшается в два раза.
Таблица 2 – Результаты локального рентгеноструктурного анализа
Точки съемки | Линия алмаза | ![]() | Линия никеля | ![]() | ![]() | ![]() | ||
I(111) | I(220) | I(111) | I(220) | |||||
№1 "Баллас" | ||||||||
1 | 0,4 | 44 | 110 | 4,8 | 38 | 7,9 | 0,084 | 1,16 |
2' | 0,46 | 411 | 893 | 2,1 | 111 | 53 | 0,22 | 3,7 |
2" | 0,8 | 180 | 225 | 2,2 | 145 | 66 | 0,36 | 1,24 |
3 | 0,3 | 217 | 723 | 1,3 | 215 | 165 | 0,23 | 1,0 |
4 | 23,8 | 1,6 | 0,067 | 5,4 | 9,8 | 0,18 | 0,44 | 0,164 |
5 | 6,1 | 0,4 | 0,065 | 20,5 | 4,5 | 0,22 | 0.3 | 0,087 |
№2 "Карбонадо"-8,5 | ||||||||
1 | 14,9 | 12,5 | 0,84 | 35,9 | 12,6 | 2,1 | 3,8 | 1,0 |
2 | 28,2 | 303 | 10,7 | 44 | 126 | 2,86 | 0,64 | 2,4 |
3 | 54,6 | 8,0 | 0,15 | 62,5 | 22,3 | 0,36 | 0,87 | 0,36 |
4 | 2,9 | 0,24 | 8,3 | 8,2 | 8,26 | 1,0 | 0,35 | 0,02 |
5 | 292 | 2,36 | 0,008 | 166 | 18,8 | 0,11 | 1,76 | 0,12 |
№3 "Карбонадо"-8,5 Начало синтеза. | ||||||||
1 | 14,3 | 20,3 | 1,4 | 13,9 | 18,8 | 1,35 | 1,03 | 1.08 |
2 | 1,9 | 1,2 | 0,63 | 0,5 | 3,.0 | 6,0 | 3,8 | 0.4 |
3 | 3,4 | 23,6 | 6.9 | 5,4 | 17,2 | 3,2 | 0,63 | 1,37 |
4 | 20,0 | 593 | 29,7 | 26,3 | 368 | 14,0 | 0,76 | 1,61 |
№4 "Карбонадо"-12 | ||||||||
1 | 256 | 21 | 0,082 | 82 | 8 | 3,12 | 3.12 | 2,6 |
2 | 16 | 5,6 | 0,35 | 21 | 2.8 | 0,76 | 0.76 | 2 |
3 | 421 | 3,9 | 0,009 | 133 | 108 | 3,16 | 3,17 | 0,036 |
4 | 15 | 502 | 33,5 | 22 | 120 | 0,68 | 0,68 | 4,2 |
5 | 651 | 558 | 0,86 | 106 | 118 | 6.14 | 6,1 | 4,7 |