Процессы и технологии синтеза алмазных поликристаллических композиционных материалов на основе разработанных сплавов-катализаторов Ni-X(Mo, Cr, Ti, B)
Вид материала | Автореферат диссертации |
Содержание6 Физические свойства АПКМ 7. Механизм и кинетика образования АПКМ 8 Механические, технологические, эксплуатационные свойства АПКМ и инструмента из них, реализация работы Св 15бу (вниитс) |
- 6-я Московская Международная конференция «Теория и практика технологии производства, 64.17kb.
- Комплексная инновационная программа повышения квалификации и профессиональной переподготовки, 22.24kb.
- Ознакомление с основными марками цветных сплавов и композиционных материалов, их свойствами, 385.05kb.
- Жаропрочность платины, палладия и их сплавов, 427.22kb.
- Совершенствование технологии производства композиционных материалов на основе древесных, 644.07kb.
- Программы: подготовка специалистов в области техники и технологии, 305.23kb.
- Разработка состава и технологии спекания дисперсно-упрочнённых композиционных материалов, 481.56kb.
- Рассматриваются вопросы изучения свойств наноалмазов детонационного синтеза, 1738.6kb.
- 150100. 62 Металлургия металлургия, 183.45kb.
- Пояснительная записка к курсовому проекту по курсу: «Процессы и аппараты химической, 52.08kb.
6 Физические свойства АПКМ
Состав металлической фазы, её количество, форма вхождения и распределение зависят от используемого сплава-катализатора и условий получения конкретного АПКМ. Установление зависимости электрических и магнитных свойств композитов от условий синтеза необходимо как для понимания механизма их образования, так и для разработки методики классификации и неразрушающего метода контроля АПКМ по качественным характеристикам.
Электрические характеристики поликристаллических алмазов сравнительно мало исследованы. При сравнении электрических сопротивлений необработанных и обработанных шлифованием целых заготовок "карбнадо" было установлено, что при шлифовании электрическое сопротивление увеличивается в 102–104 раз, т.е. определяющим является поверхностное электросопротивление. Также установлено, что химическая обработка резко (в 105 раз) уменьшает электропроводность "карбонадо", что связано с растворением металлической связки. При изучении магнитных свойств было отмечено, что синтез "балласов" с применением немагнитного катализатора Х20Н80 приводит к образованию магнитных композитов. В настоящей работе для синтеза АПКМ "карбонадо" в качестве катализатора применяли чистый никель и сплав Х20Н80, различающиеся по своим магнитным свойствам, а также железо, кобальт и сплав никель-марганец.
Изучение магнитных свойств АПКМ проводили на широкодиапазонном измерителе "Магнит 704", предназначенном для определения количества ферромагнитных включений в абразивных материалах. Измерение магнитных характеристик проводили в условных единицах. Поскольку абсолютное их значение зависит от массы анализируемого материала, то сравнение значений магнитных характеристик проводили в относительных единицах, приведенных к массе анализируемой пробы (у.е./г). Результаты экспериментов для образцов АПКМ, синтезированных в системах Х20Н80 - углерод и никель - углерод представлены в таблице 11.
Таблица 11 – Магнитные характеристики АПКМ
№ | Условия получения АПКМ | Магнитные свойства, у.е./г | ||||
Давление, ГПа | Температура, К | Время, с | Катализатор | Масса алмаза, г | ||
1 | 7,0 | 2000 | 10 | Х20Н80 | 0,10 | 0,32 |
2 | 8,0 | 2000 | 10 | Х20Н80 | 0,12 | 0,155 |
3 | 9,0 | 2000 | 10 | Х20Н80 | 0,12 | 0,123 |
4 | 10,4 | 2000 | 10 | Х20Н80 | 0,12 | 0,11 |
5 | 9,0 | 2000 | 3 | Х20Н80 | 0,02 | 0,07 |
6 | 9,0 | 2000 | 6 | Х20Н80 | 0,25 | 0,11 |
7 | 9,0 | 2000 | 10 | Х20Н80 | 0,32 | 0,95 |
8 | 9,0 | 2000 | 10 | Fe | 0,16 | 8,6 |
9 | 6,8 | 2000 | 10 | Ni | 0,10 | 5,1 |
10 | 8,5 | 2000 | 10 | Ni | 0,12 | 4,4 |
11 | 10,0 | 2000 | 10 | Ni | 0,12 | 4,0 |
12 | 12,0 | 2000 | 10 | Ni | 0,12 | 4,3 |
13 | 9,0 | 2000 | 10 | Ni | 0,12 | 4,3 |
14 | 9,0 | 2000 | 10 | Ni | 0,24 | 3,0 |
Примечания. 1. №№ 1-4, 8-13 – режим "АСПК-2"; №№ 5-7, 14 – режим "АСПК-9". 2. В графе "масса алмаза" указана средняя масса алмаза АПКМ.
Из данных, представленных в таблице 11, следует, что увеличение давления синтеза для серии "АСПК-2", катализатор Х20Н80, или уменьшение времени синтеза - для серии "АСПК-9", катализатор Х20Н80, приводит к уменьшению значений магнитных свойств. При использовании никеля в качестве катализатора, значения магнитных свойств изменяются при изменении давления незначительно. Увеличение размера АПКМ, синтезированных с использованием никеля, приводит к снижению значений удельных магнитных свойств, связанному с уменьшением общего содержания металлической составляющей в АПКМ. Увеличение размера АПКМ, синтезированных с использованием неферромагнитного сплава Х20Н80, приводит к повышению значений удельных магнитных свойств, связанному с непропорциональным увеличением ферромагнитных областей в металлической составляющей АПКМ.
7. Механизм и кинетика образования АПКМ
Образование АПКМ характеризуется рядом особенностей. Например, при синтезе "балласов" с использованием различных сортов графита растущий композит наследует морфологические особенности углеродного материала. Образование и рост алмазных композитов происходит со скоростями, значительно превышающими скорости получения порошков и монокристаллов. Время образования АПКМ диаметром 6 мм составляет 15-30 секунд. При рассмотрении механизма синтеза также встает и вопрос транспорта металла-катализатора в зону превращения графит-алмаз, которая при синтезе АПКМ отделена предварительно синтезированным алмазом от исходного расположения катализатора на 2-4 мм.
Существуют две точки зрения на механизм проникновения металла в объем графитовой заготовки: инфильтрация расплава в объем графитовой заготовки связана с понижением давления в реакционной зоне из-за полиморфного перехода графит-алмаз, сопровождаемого заметным уменьшением объема и, вторая, процесс транспорта металла в объем графитовой заготовки определяется общим высоким давлением в КВД и наличием сквозной пористости в графитовой заготовке в условиях высоких давлений и температур. Упрощенное решение уравнения Навье-Стокса, описывающее течение вязкой несжимаемой жидкости при постоянной температуре может быть записано в виде:
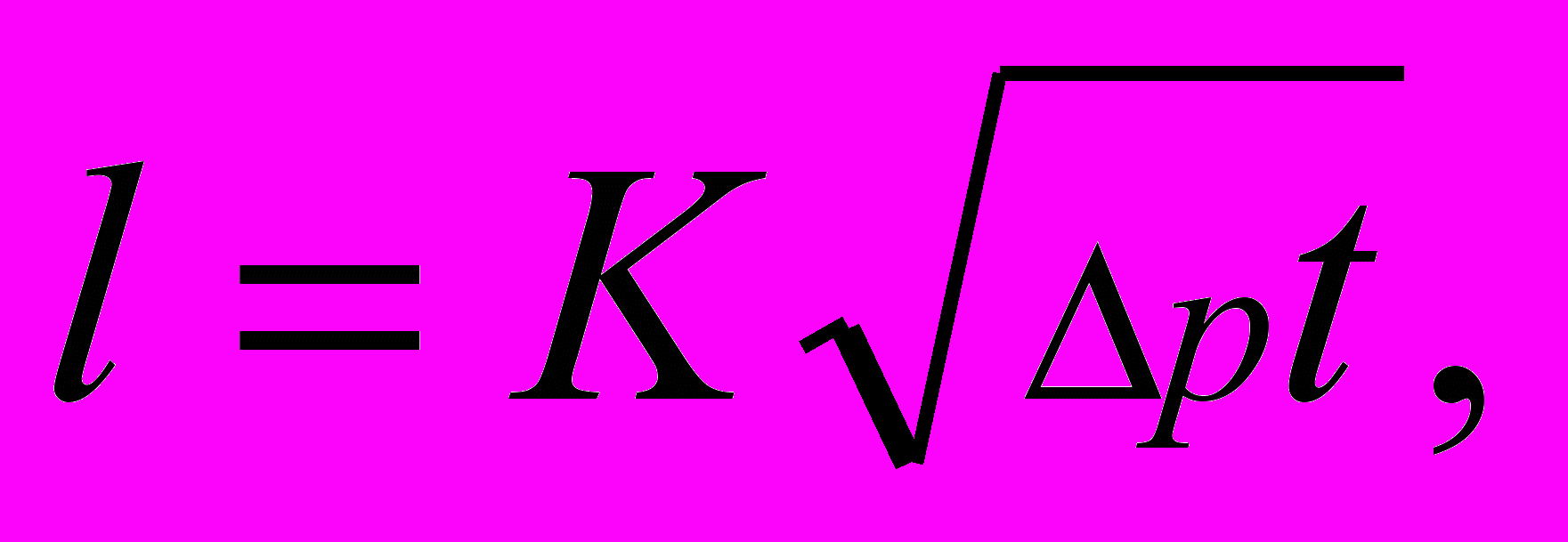
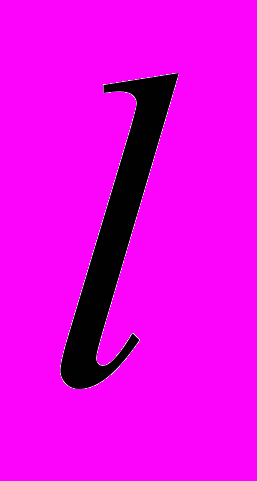
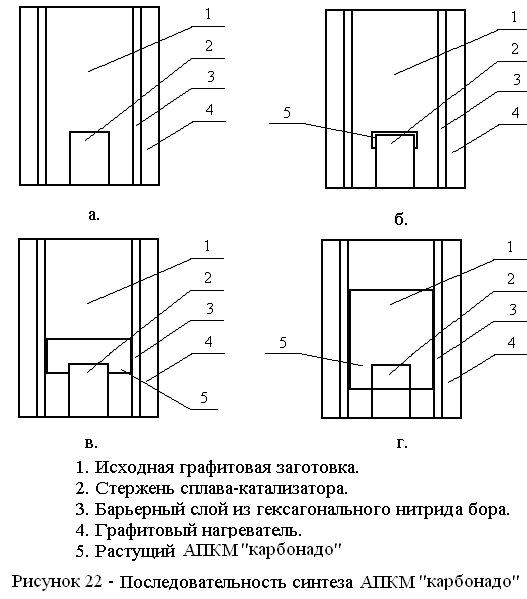
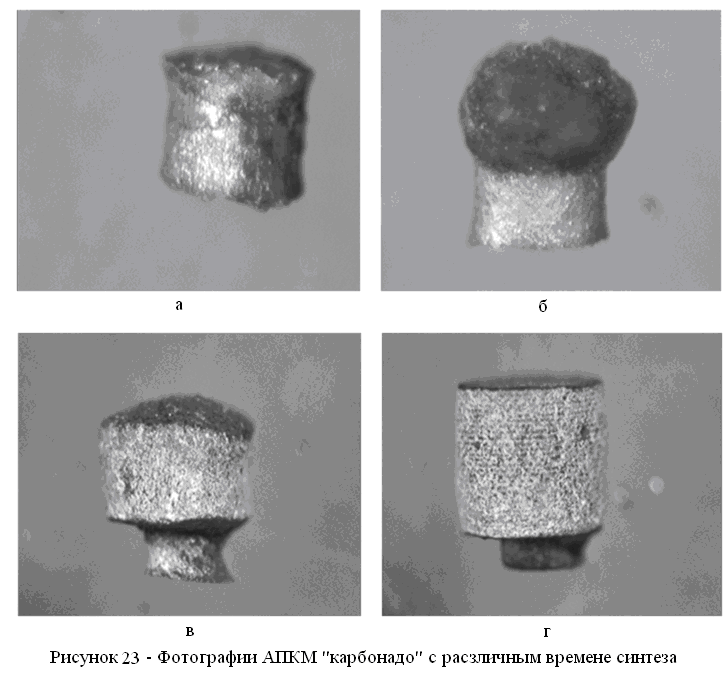
Нами было проведено исследование кинетики образования АПКМ. Начальное давление синтеза составляло 9,0 ГПа, в качестве сплава-катализатора применяли никель. Стадии образования композита по стандартной схеме представлены на рисунках 22-23, т.е. процесс синтеза идет с увеличением фронта кристаллизации, что затрудняет анализ данных по кинетике. Зависимости мощности нагрева от времени при синтезе АПКМ приведены на рисунке 24. Для изучения кинетики в работе применяли специально разработанную схему синтеза (рисунок 25) с плоским фронтом кристаллизации алмаза в процессе образования композита. Размер АПКМ оценивали по высоте, поскольку диаметр его довольно точно соответствовал диаметру исходной графитовой заготовки. Перед каждым опытом блок-матрицы выдерживались в термостате для установления определенной постоянной температуры. Результаты экспериментов представлены на рисунке 26. Кривая зависимости размера АПКМ хорошо описывается линейной зависимостью типа: l=Аt+В, где коэффициент А зависит от давления синтеза. Повышение давления приводит к ускорению процесса образования алмаза и увеличению А, уменьшение давления синтеза приводит к замедлению процесса образования алмаза и уменьшению А. Значение константы В зависит от мощности нагрева реакционной ячейки и связано с временем прогрева КВД до достижения температуры плавления никеля. Для нашего конкретного случая с учетом коэффициентов, подобранных методом наименьших квадратов, можно записать l=0,79t-1,45.
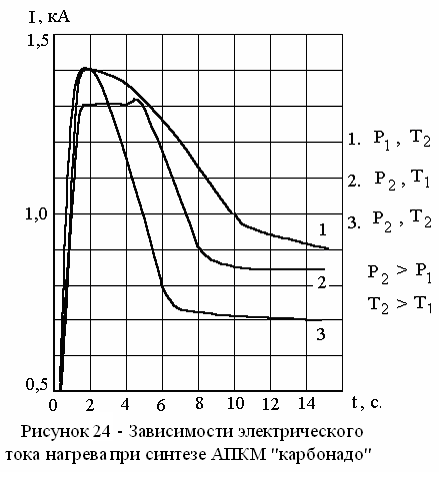
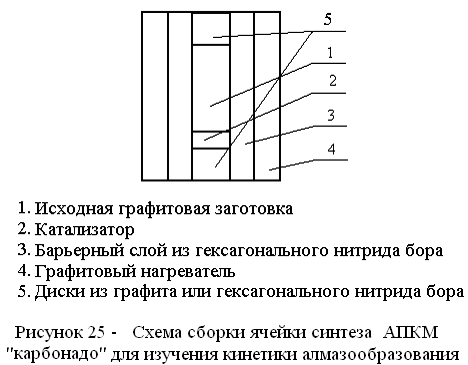
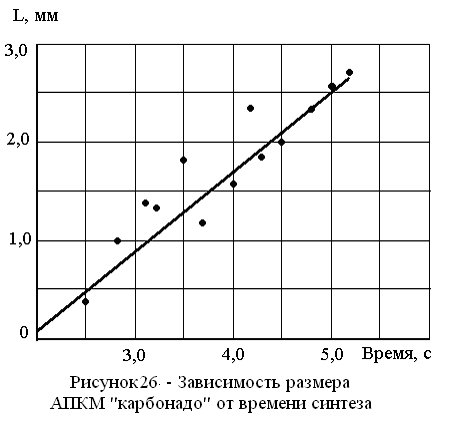
На основании приведенного экспериментального и литературного материала можно представить последовательность образования АПКМ "карбонадо" следующим образом. После приложения давления и включения тока нагрева происходит разогрев реакционной ячейки (рисунок 22). При достижении температуры плавления компактного сплава-катализатора в области максимальной температуры на границе его с графитом, за счет увеличения объема катализатора при плавлении происходит разрушение графита и образование в нем трещин, которые заполняются сплавом-катализатором. Трещины могут достигать 2 мм в глубь графитовой заготовки и распространяются, как правило, к центру реакционной ячейки. Далее происходит превращение графита в алмаз в зоне контакта расплав–графит, что приводит к уменьшению тока нагрева. Из-за возникающего перепада давления на границу образования композита впрыскивается новая порция расплава из центрального стержня, компенсируя расход расплава на образование межкристаллитных и внутрикристаллитных включений.
В работе проводили исследования по уточнению путей проникновения расплава в графитовую заготовку при образовании АПКМ. Его образование из графита сопровождается появлением несплошностей на фронте алмазообразования (трещины, поры), которые заполняются расплавом. Кроме того, внутри АПКМ образуются межкристаллитные каналы, заполненные расплавом катализатора и пронизывающие его в различных направлениях. Поэтому существуют два пути проникновения расплава в объем графитовой заготовки при образовании композита: по межзеренным каналам и по поверхности растущего композита. Причем скорость проникновения расплава по первому пути должна уменьшаться, а по второму пути увеличиваться с увеличением давления. Второй способ транспорта расплава катализатора реализуется преимущественно при высоких давлениях и приводит к повышению скорости роста АПКМ.
Таким образом, установленная линейная зависимость размера АПКМ от времени, существенная зависимость скорости его образования от общего давления в камере высокого давления, анализ литературных данных по инфильтрации расплавов в объем алмазной прессовки (характеристики контактного взаимодействия на границе расплав-графит и расплав-алмаз идентичны) и наших данных по инфильтрации в объем графитовой заготовки при синтезе композита, полученные данные по их структурным и магнитным свойствам позволяют следующим образом описать механизм формирования АПКМ в области стабильности алмаза. При плавлении сплава-катализатора в зоне контакта жидкого расплава с графитом происходит быстрая трансформация решетки графита в решетку алмаза, сопровождаемая локальным уменьшением давления и формированием фронта кристаллизации алмаза, который перемещается от межфазной поверхности сплава-катализатора и графита к периферии исходного графита. Возникающие градиенты давления являются движущей силой инфильтрации расплава в объем графитовой заготовки. При этом транспорт расплава катализатора в зону полиморфного перехода графит–алмаза в течение всего времени образования алмазного композиционного материала может протекать двумя способами: инфильтрацией по внутренним межкристаллитным каналам и течением по поверхности растущего композита. Образование новой межфазной поверхности расплав-графит приводит к дальнейшему образованию алмазной фазы. Одновременно с этим протекает процесс растворения углерода графита в прожилках расплава и рост образовавшихся алмазных зародышей. Образование алмазных зародышей и их рост являются одновременно протекающими процессами при образовании АПКМ. Повышение давления приводит к уменьшению критических размеров алмазного зародыша и увеличению скорости их образования. Рост алмазных кристаллитов может протекать также присоединением алмазных кластеров (критических и докритических зародышей алмаза) к растущему алмазу. Количество ферромагнитных зон, при использовании сплава Х20Н80, в АПКМ зависит от количества растворенного углерода в расплаве, т.е. от количества алмаза, образовавшегося по механизму перекристаллизации через плёнку металла. Повышение давления, и как следствие, количества центров кристаллизации способствует измельчению структуры АПКМ, снижение давления приводит к увеличению размера алмазных кристаллитов, слагающих АПКМ.
8 Механические, технологические, эксплуатационные свойства АПКМ и инструмента из них, реализация работы
Особенностью строения АПКМ является наличие компактного остатка сплава-катализатора в его объеме. Поэтому приводимые значения прочности "карбонадо", полученные без учета этой особенности, значительно занижены. Например, прочность целых АПКМ "АСПК" в наших опытах при испытании на боковое сжатие составила 0,34 ГПа против 5-10 ГПа для поликристаллов типа СВ. Однако в соответствии с ГОСТ 9206-80 прочность алмазных шлифпорошков АРК4 и АРС4, получаемых из цельных заготовок АПКМ "АСПК" и "СВ-СП" соответственно, должна быть примерно одинакова.
Поэтому нами предпринята попытка измерить истинную прочность на сжатие АПКМ "АСПК". Для определения прочности на сжатие "АСПК" из надкатализаторной зоны композита были вырезаны образцы диаметром 1,6 и высотой 2,7 мм. Цилиндрический образец помещали между пластинами из дисков "АСПК" диаметром 4 мм, расположенных между твердосплавными пластинами. При таком методе измерения прочность на сжатие цилиндрических образцов "АСПК" составила 2,0–4,0 ГПа.
Основным свойством АПКМ "карбонадо" и "балласов", определяющим их применимость в конкретном виде алмазного инструмента, является уникально высокая абразивная стойкость. В связи с тем, что условия испытания на абразивную стойкость АПКМ в различных работах существенно различны, нами была разработана методика испытания АПКМ "АСПК" при режимах, соответствующих их работе в инструменте с учетом их невысокой термостойкости. Абразивную стойкость оценивали по отношению количества снятого абразива в см3 к уменьшению массы АПКМ в мг. Значения абразивной стойкости представлены в таблице 12. Для образцов "АСПК" значение абразивной стойкости составляет от 57 до 67 см3/мг при использовании абразивных кругов марки 24А и от 18 до 24 см3/мг – при использовании абразивных кругов 63(64)С, что значительно выше, чем у СВ-15 БУ (7,2), АТП (6,2) и СКМ (5,1). Значения абразивной стойкости "АСПК", полученные при испытаниях по данной методике, хорошо коррелируют с испытаниями на прочность (по ГОСТ 9206-80) для различных партий образцов "АСПК", изготовленных в различных условиях, что свидетельствует о корректности методики.
Таблица 12 – Значения абразивной стойкости (А) АПКМ различных марок
Условия испытания | Марка АПКМ | А, см3/мг | Диапазон значений А, см3/мг |
Абразивный круг: 24А 40 СМ2 35м/с 300х40х76 ГОСТ 2424-83 ЧАЗ. Режимы резания: (6-8) м/с (500об/мин); 0,1 мм/об; гл. 0,1мм; 40 проходов | "АСПК-2" | 57,5 | 48,1–69,6 |
"АСПК-3" | 67,2 | 45,3–89,1 | |
СКМ (ПЗИАиАИ) | 5,1 | 2,5–7,3 | |
Абразивный круг: 64С 25 СМ2 35м/с 300х40х76 ГОСТ 2424-83 ЧАЗ. Режимы резания: (6-8) м/с (500об/мин); 0,1 мм/об; гл. 0,1мм; 40 проходов | "АСПК-2" | 18,3 | 14,8–23,2 |
"АСПК-3" | 23,5 | 22,0–25,2 | |
АТП (ЛЗИАиАИ) | 6,2 | 5,0–7,3 | |
СВ 15БУ (ВНИИТС) | 7,2 | 5,3–9,1 |
В алмазном инструменте, применяемом в камнеобработке, применяются шлифпорошки из АПКМ марок АРК4 и АРВ1. Методика испытания их на статическую прочность описана в ГОСТ 9206-80. Испытание шлифпорошков АРК4 на динамическую прочность изучено гораздо меньше. Поэтому мы провели дополнительные исследования шлифпорошков АРК4 как на статическую, так и динамическую прочность в сравнении с другими алмазными шлифпорошками. Из данных, приведенных в таблице 13, следует, что алмазные материалы одной статической прочности (АРК 400/315; А6К80 400/315; АС80 400/315) имеют разную динамическую прочность, причем методом классификации по форме можно выделить поликристаллические алмазные порошки АРК с повышенными прочностными свойствами. Применение упрочняющего дробления с целью разрушения слабых зерен позволяет повысить в 1,5 раза прочность АРК4, что целесообразно при его использовании в дорогостоящем алмазном инструменте, например бурового назначения (таблица 14).
Таблица 13 – Основные прочностные характеристики шлифпорошков АРК4
Характеристика алмазного шлифпорошка | Динамическая прочность, мг (по Фрайтестеру) | Статическая прочность, Н | Примечание |
АРК 630/500 (без классификации по форме) | 115 | 160 | Условия испытаний по Фрайтестеру: навеска 400мг., количество ударов- 900 |
А6К80 400/315 | 115 | 120 | |
АС80 400/315 | 140 | 128 | |
SDA 100 40/50 | 297 | - | |
АРК 400/315 к.ф. 1,34 | 160 | 88 | |
АРК 400/315 к.ф. 1,64 | 145 | 75 | |
АРК 400/315 к.ф. 2,0 | 105 | 68 |
Таблица 14 – Результаты упрочнения алмазных шлифпорошков АРК4.
Фракция | Статическая прочность по ГОСТ 9206-80; F, Н | После первичного дробления (общий выход фракций +400–87%) | После упрочняющего дробления (общий выход фракций +400–30%) | ||
Р, Н | Р/РГОСТ | Р, Н | Р/РГОСТ | ||
2000/1600 | 784 | 1612 | 2,06 | 2201 | 2,81 |
1600/1250 | 510 | 1007 | 1,97 | 1596 | 3,13 |
1250/1000 | 451 | 594 | 1,32 | 838 | 1,86 |
1000/800 | 367 | 405 | 1,1 | 615 | 1,68 |
В результате изучения механических свойств АПКМ установлено, что их отличает высокая твердость и износостойкость в сочетании с удовлетворительной прочностью и термостойкостью. Такое сочетание механических свойств АПКМ делает их перспективным для использования в широкой номенклатуре алмазных износостойких инструментов и позволило наладить выпуск конкурентоспособного алмазного инструмента для широкого круга использования.
В НИЛ ВТМ МИСиС налажено опытное производство АПКМ и различного алмазного инструмента (резцовых вставок, опор, выглаживателей). Разработаны технологии изготовления струеформирующих сопел из АПКМ с уникальным уровнем износостойкости, которые используются для газо- и жидкостноабразивной резки и обработки различных материалов (металлы, керамика, различные горные породы и пр.). С помощью подобных установок проводится резка различных материалов при заготовительных операциях, в особенности там, где огневая резка принципиально невозможна (резка органосодержащих композиционных материалов, например при утилизации военной техники), или там, где нагрев разрезаемого материала нежелателен из-за возможных изменений в структуре или прочностных характеристик; очистка внутренних поверхностей трубопроводов различных теплообменных систем от отложений, поскольку возможно использование длинномерных гибких питающих шлангов малого диаметра (катетеров). Возможно использование подобных устройств в двигателях коррекции орбиты в ракетной технике.
Наличие в институте современной лазерной установки позволило наладить выпуск сопел из собственного сырья. Разработка технологии алмазных формообразующих сопел для газо- и жидкостно-абразивной резки различных материалов из опытных АПКМ была отмечена дипломом Министерства науки и технологий РФ. Разработка технологии и освоение опытно-промышленного выпуска АПКМ и инструмента из них в условиях лаборатории ВТМ МИСиС позволило с 2000 года и по настоящее время выполнить хозяйственных договоров по поставке НТП более чем на 10 млн. рублей.