«Технологии, научно-техническое и информационное обеспечение в образовании, экономике и производстве региона»
Вид материала | Документы |
TPROG- Программный задатчик температуры (технологическая карта); ОУ КСУ- каскадная система управления; ПИ Проблемы применения источников малой |
- V международная научно-техническая конференция «Информационные технологии в науке,, 63.57kb.
- V международная научно-практическая конференциЯ «информационные и коммуникационные, 290.79kb.
- Vii всероссийская научно-практическая конференция «Информационное обеспечение реализации, 50.33kb.
- Лекция 4 Обеспечивающие подсистемы асу. Математическое, программное, лингвистическое,, 59.3kb.
- Техническое задание на оказание услуг по теме Научно техническое обеспечение исследований, 126.7kb.
- Лекция: Информационное обеспечение ис: Информационное обеспечение ис. Внемашинное информационное, 314.22kb.
- Первая студенческая региональная научно-практическая конференция «Компьютерные технологии, 32.52kb.
- Информационное письмо, 38.62kb.
- Участие в выставке-презентации программных продуктов с предоставлением рекламного описания, 73.4kb.
- Iii международная научно-практическая конференция «коммуникация в социально-гуманитарном, 46.7kb.
В пакете VisSim можно моделировать различные системы: линейные и нелинейные; непрерывные и дискретные. В одной модели можно одновременно задавать и определять как непрерывные, так и дискретные передаточные функции; для дискретной части модели возможно многочастотное квантование.
Вышеописанные достоинства и возможности ППП VisSim могут успешно применяться в качестве средства моделирования и разработки различных автоматизированных систем при решении широкого круга научных и инженерных задач.
В данной работе для примера приводится имитационная модель тепловлажностной обработки железобетонных изделий.
Известно, что процесс твердения бетона значительно превышает по длительности все остальные операции по изготовлению бетонных и железобетонных изделий. Тепловая обработка, позволяющая во много раз ускорить процесс твердения бетона, является, как правило, необходимым условием заводского производства бетонных и железобетонных изделий; включение тепловой обработки в технологический процесс изготовления изделий дает возможность значительно увеличить оборачиваемость форм, повысить коэффициент использования производственных площадей цеха и сократить длительность общего цикла производства.
В заводской практике применяются следующие виды тепловой обработки бетонных и железобетонных изделий и конструкций:
- пропаривание в камерах при нормальном атмосферном давлении пара или паровоздушной смеси и температуре среды от 60 до 1000С;
- запаривание в автоклавах, в среде насыщенного водяного пара повышенного давления- обычно 0,9-1,3 Па и при температуре соответственно 174,5-191°С;
- нагрев в закрытых формах с контактно передачей тепла бетону от различных источников через ограждающие поверхности формы;
- электропрогрев пропуском электрического тока непосредственно через бетон изделия;
- периферийный прогрев бетона со стороны открытых поверхностей изделия в форме с помощью наружных источников тепла, преимущественно электронагревателей;
- прогрев бетона индукционными токами в электромагнитном поле.
К методам тепловой обработки может быть также отнесен предварительный нагрев паром или электрическим током бетонной смеси непосредственно перед укладкой в формы, с последующим выдерживанием сформованных изделий в течение нескольких часов в термосных условиях. Возможна также комбинация предварительного нагрева бетонной смеси с последующей короткой тепловой обработкой бетона в сформованных изделиях.
Оптимальное сочетание этих средств с эффективными методами тепловой обработки позволяет в настоящее время сократить ее сроки до 8-6 ч.
Эффективность тепловой обработки оценивается по двум показателям: по прочности, достигнутой к концу тепловой обработки, выражаемой в процентах от прочности такого же бетона в 28-суточно возрасте нормального твердения, - показатель ускорения твердения; по сравнительной прочности в 28-суточном возрасте бетона, прошедшего тепловую обработку и в последующем нормально твердевшего, и такого же бетона, не подвергавшегося тепловой обработке, - показатель относительной прочности бетона после тепловой обработки.
Конечная эффективность тепловой обработки, суммирующая влияние положительных и отрицательных факторов, зависит от выбора исходных материалов и состава бетона, подвергаемого тепловой обработке, от принятого режима этой обработки. Хотя достижение в наиболее короткие сроки возможно более высокой прочности бетона и является основной задачей всякой тепловой обработки, сроки и режимы ее следует выбирать таким образом, чтобы снижение показателей физико-механических свойств бетона при его тепловой обработке было бы минимальным.
Пропаривание при атмосферном давлении является наиболее распространенным способом тепловой обработки бетонных и железобетонных изделий. При пропаривании сформованные изделия выдерживаются в камере в среде насыщенного пара или паровоздушной смеси до достижения бетоном заданной прочности. В пропарочной камере создаются не только благоприятная температура для ускоренного твердения (в пределах 60-100оС), но и оптимальная влажность среды, способствующая сохранению влаги в бетоне для его дальнейшего твердения и после окончания пропаривания. Это дает основание считать пропаривание эффективной тепловлажностной обработкой бетона.
Основными параметрами режима пропаривания бетона являются:
- принятая максимальная температура среды, при которой осуществляется изотермический прогрев и его продолжительность;
- длительность и характер подъема температуры в камере от исходной до принятой наивысшей (скорость подъема температуры в камере);
- скорость понижения температуры среды (интенсивность остывания бетона в камере после тепловой обработки);
- относительная влажность среды твердения, а так же срок предварительного выдерживания сформованных изделий до начала тепловой обработки.
Изотермический прогрев. Температуру в камере пропаривания на стадии изотермического прогрева следует принимать для бетонов на рядовых портландцементах (с умеренным содержанием трехкальцевого алюмината - С3А), равной 80-85° С. При более низкой температуре длительность изотермического прогрева существенно увеличивается, что нежелательно из-за снижения оборачиваемости камер, форм для изделий и пр. Однако, если используемый портландцемент содержит С3А более 10-12%, температуру изотермического прогрева приходится уменьшать до 65-70°С с тем, чтобы уменьшить возможный недобор прочности при последующем твердении бетона по сравнению с бетоном, твердевшим в нормальных температурно-влажностных условиях.
Подъем температуры бетона (или среды в камере) является наиболее ответственным этапом тепловой обработки, так как возможные нарушения в структуре бетона протекают именно на этой стадии тепловой обработки. Величина и характер структурных нарушений зависят от достигнутой бетоном к началу тепловой обработки прочности, от скорости подъема температуры среды в камере и ряда других факторов, способствующих или препятствующих развитию деструктивных процессов.
Предварительное выдерживание сформованных изделий перед тепловой обработкой имеет целью обеспечить бетону ту минимально необходимую начальную (критическую) прочность бетона, при которой он может воспринимать тепловое воздействие при принятом режиме без нарушения его структуры. Оптимальное время выдерживания зависит от вида и марки (активности) цемента, начального водосодержания бетонной смеси (В/Ц), температуры среды и применения химических ускорителей твердения; оно должно составлять в среднем 2- 4 ч., в отдельных случаях и более, но не менее 1-2 ч.
Выбирая в зависимости от марки и вида применяемого цемента, температуры изотермического прогрева и водоцементного отношения ту или иную кривую, можно определить необходимую продолжительность прогрева (подъем температуры + изотермический прогрев), а также рекомендуемую скорость подъема температуры в камере для получения требуемой прочности бетона в процентах от марочной.
Математическая модель объекта управления (пропарочной камеры) и системы программного управления тепловлажностной обработки ЖБИ разработана в среде моделирования VisSim и представлена на рис.1.
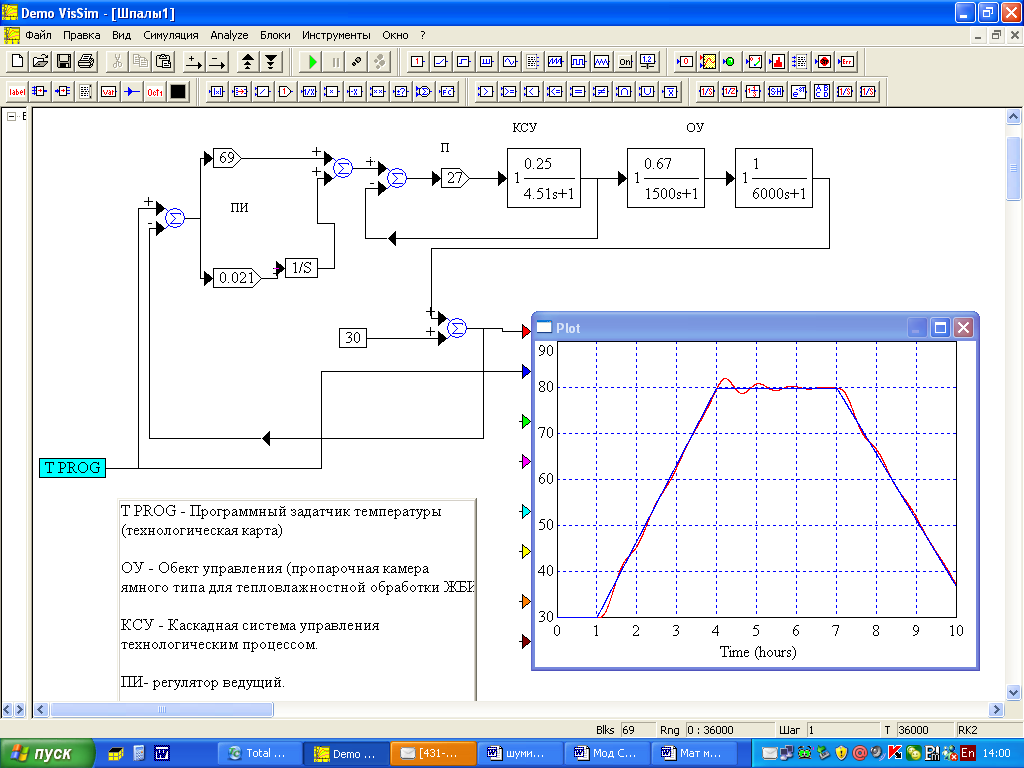
TPROG- Программный задатчик температуры (технологическая карта);
ОУ- Объект управления (пропарочная камера для тепловлажностной обработки ЖБИ);
КСУ- каскадная система управления;
ПИ- регулятор ведущий;
П- регулятор ведомый.
Рис. 1. Математическая модель каскадной системы управления тепловлажностной обработкой ЖБИ
Так как, процесс изменения температуры является медленным, в системе управления использован ПИ-регулятор. Настроечные параметры ПИ-регулятора получены в результате эксперимента. Для повышения качества управления к выходу ведущего ПИ-регулятора подключен ведомый П- регулятор. Таким образом, система управления является каскадной.
Модель изменения температуры в пропарочной камере по карте технологического процесс выделена в отдельный блок TPROG и в развернутом виде приводится на рис. 2.
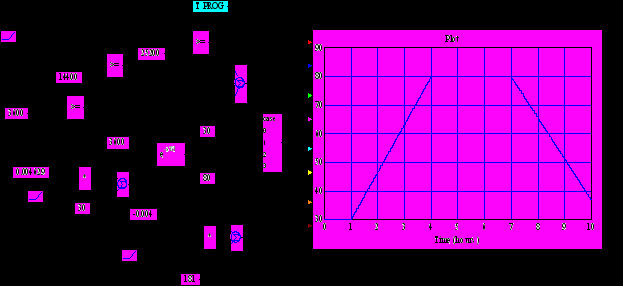
Рис. 2. Алгоритм изменения температуры в пропарочной камере по технологической карте. (Задатчик САУ)
Литература
- Шавров А. В., Коломиец А.П. Автоматика. – М.: «Колосс», 2003.
- Ротач В. Я. Теория автоматического управления. Учебник для вузов, 2-е издание. – М.: «МЭИ», 2004.
- Филипс Ч., Харбор Р. Системы управления с обратной связью. Пер. с англ. – М.: Лаборатории базовых знаний, 2001.
4. О. А. Гершберг Технология бетонных и железобетонных изделий. Издание третье, переработанное и дополненное. – М.: б.и., 2001.
Грыжов В. К., Русанов А. А.
Филиал ГОУ ВПО МГУТУ в г. Вязьме
г. Вязьма Смоленской обл.
ПРОБЛЕМЫ ПРИМЕНЕНИЯ ИСТОЧНИКОВ МАЛОЙ
ГИДРОЭНЕРГЕТИКИ
Данная публикация рассматривает проблемы малой гидроэнергетики. Среди главных факторов, тормозящих развитие малой гидроэнергетики в России, большинство экспертов называют неполную информированность потенциальных пользователей о преимуществах применения небольших гидроэнергетических объектов
This publication examines the problems of small hydroenergetics. Among main factors, braking development of small hydroenergetics in Russia, most experts name the incomplete being informed of potential users about advantages of application of small hydroenergetic objects.
В настоящее время гидроэнергетический потенциал практически полностью реализуется за счет больших и гигантских ГЭС. Вместе с тем, согласно имеющимся данным, в 1913 г. число действовавших в России ГЭС составляло 78 единиц, общей мощностью 8.4МВт. Крупнейшей из них была ГЭС на р. Мургаб, мощностью 1.35 МВт. Таким образом, согласно современной классификации, все действовавшие в то время ГЭС являлись малыми.
Менее чем через 30 лет — в 1941 г. в России работали 660 малых сельских ГЭС, общей мощностью 330 МВт. На 40-е и 50-е годы XX века пришелся пик строительства МГЭС, когда ежегодно в эксплуатацию вводились до 1000 объектов. Правда, уже в начале 50-х годов, в связи с переходом к строительству гигантских энергетических объектов и присоединением сельских потребителей к централизованному электроснабжению, это направление энергетики утратило государственную поддержку, что привело практически к полному разрушению и упадку созданной прежде инфраструктуры. Прекратилось проектирование, строительство, изготовление оборудования и запасных частей для малой гидроэнергетики.
В 1962 г. в СССР насчитывалось 2665 малых и микро-ГЭС. В 1980 г. их было около 100 с суммарной мощностью 25 МВт. А к моменту распада СССР в 1990 г. действовавших МГЭС оставалось всего 55. Согласно данным разных источников, в настоящее время по всей России действуют от нескольких десятков (60-70) до нескольких сотен (200-300) единиц.
В таблице 1 приводятся характеристики некоторых действующих в России МГЭС.
Таблица 1
Место расположения | Год создания | Тип | Установленная мощность (кВт) | Кол-во агрегатов | Общая мощность |
Кировская обл. | 1993 | микро-ГЭС-10 | 10 | 2 | 20 |
Адыгея | 1994 | микро-ГЭС-10 | 10 | 5 | 50 |
Адыгея | 1998 | ГА-2 | 200 | 1 | 200 |
Кабардино-Балкария | 1995 | ГА-8 | 550 | 2 | 1100 |
Республика Тыва | 1995 | микро-ГЭС-10 | 10 | 2 | 20 |
Продолжение табл. 1
Место расположения | Год создания | Тип | Установленная мощность (кВт) | Количество агрегатов | Общая мощность |
Республика Алтай, р. Кайру | 2002 | ГА-2М | 200 | 2 | 400 |
Краснодарский край, Краснодарская ТЭЦ | 2003 | ГА-1 | 350 | 7 | 2450 |
Республика Тыва, пос. Кызыл Хая, р. Мочен-Бурен | 2001 | микро-ГЭС-50ПР | 50 | 3 | 150 |
Карелия, р.Киви-Койву | 1995 | микро-ГЭС-50Д | 20 | 3 | 60 |
Карелия, Ланденпохский р-н | 1997 | микро-ГЭС-10 | 10 | 1 | 10 |
Ленинградская обл., Лужский завод | 1996 1999 | микро-ГЭС-50ПР, микро-ГЭС-10 | 50 10 | 1 1 | 50 10 |
Башкирия, Таналыкское водохранилище | 1997 | микро-ГЭС-50ПР | 50 | 1 | 50 |
Башкирия, пос. Табулды | 1997 | микро-ГЭС-10 | 10 | 1 | 10 |
Башкирия, зянское водохранилище | 1999 | микро-ГЭС-50ПР | 50 | 3 | 150 |
Башкирия, Соколки | 2003 | микро-ГЭС-50ПР | 50 | 3 | 150 |
Московская область, оз. Сенеж | 2004 | МГЭС | 10 и 60 | 2 | 70 |
Ярославская обл., р. Нерль-Волжская | 2003 | Восстановительная МГЭС | | | 160 |
Свердловская обл., г. Серов | 2004 | МГЭС | 200 | | 200 |
В течение последних 10 лет доля вырабатываемой на гидростанциях электроэнергии в общем энергетическом балансе России снижается. В 1995 г. она составляла 21%, в 1998 г. — 18%, в 2008 г. — 11%. Это связано как с устареванием и износом оборудования на гидроэнергетических гигантах прошлого, так и с увеличением в энергобалансе страны доли более удобного энергоресурса — природного газа.
Как и любой другой способ производства энергии, применение малых и мини-ГЭС имеет как преимущества, так и недостатки.
Среди экономических, экологических и социальных преимуществ объектов малой гидроэнергетики можно назвать следующие. Их создание повышает энергетическую безопасность региона, обеспечивает независимость от поставщиков топлива, находящихся в других регионах, экономит дефицитное органическое топливо. Сооружение подобного энергетического объекта не требует крупных капиталовложений, большого количества энергоемких строительных материалов и значительных трудозатрат, относительно быстро окупается. Кроме того, есть возможности для снижения себестоимости возведения за счет унификации и сертификации оборудования.
В процессе выработки электроэнергии ГЭС не производит парниковых газов и не загрязняет окружающую среду продуктами горения и токсичными отходами, что соответствует требованиям Киотского протокола. Подобные объекты не являются причиной наведенной сейсмичности и сравнительно безопасны при естественном возникновении землетрясений. Они не оказывают отрицательного воздействия на образ жизни населения, на животный мир и местные микроклиматические условия.


Среди факторов, тормозящих развитие малой гидроэнергетики в России, большинство экспертов называют неполную информированность потенциальных пользователей о преимуществах применения небольших гидроэнергетических объектов; недостаточную изученность гидрологического режима и объемов стока малых водотоков; низкое качество действующих методик, рекомендаций и СНиПов, что является причиной серьезных ошибок в расчетах; неразработанность методик оценки и прогнозирования возможного воздействия на окружающую среду и хозяйственную деятельность; слабую производственную и ремонтную базу предприятий, производящих гидроэнергетическое оборудование для МГЭС, а массовое строительство объектов малой гидроэнергетики возможно лишь в случае серийного производства оборудования, отказа от индивидуального проектирования и качественно нового подхода к надежности и стоимости оборудования — по сравнению со старыми объектами, выведенными из эксплуатации.
В целом можно сказать, что малая гидроэнергетика в своем развитии испытывает те же проблемы, что и энерготехнологии на остальных возобновляемых источниках энергии.
Московский государственный университет технологий и управления в рамках программы «Создание и развитие распределенного исследовательского университета для формирования пояса малых и средних инновационных предприятий в период с 2009 по 2018 г.» формирует базу инновационных проектов и предложений для создания технопарка на территории Вяземского района.
Одним из перспективных инновационных проектов, имеющих практическое развитие, является освоение и использование энергосберегающих технологий, малой и альтернативной энергетики.
Создание опытной площадки для испытания и внедрения этих технологий является на сегодня насущной проблемой.
Мы считаем, что создание такой площадки возможно в рамках генерального плана развития города Вязьмы, в части создания гидротехнического сооружения с формированием водного зеркала на реке Вязьме.
Этап 1. Строительство плотины и устройство водоема в центральной части города.