Методические указания к выполнению лабораторной работы №12 для студентов очной и заочной форм обучения всех специальностей
Вид материала | Методические указания |
- Методические указания к выполнению курсовой работы для студентов эфф, автф всех специальностей, 1176.51kb.
- Методические указания к выполнению лабораторной работы №9 для студентов очной и заочной, 251.35kb.
- Методические указания к выполнению лабораторной работы №6 для студентов всех форм обучения, 197.64kb.
- Методические указания к выполнению лабораторной работы №10 для студентов очной формы, 240.19kb.
- Методические указания к выполнению лабораторной работы №21 по физике для студентов, 119.29kb.
- Методические указания по выполнению лабораторной работы №6 для студентов 1-го курса, 124.2kb.
- Методические указания по написанию курсовой работы для студентов очной, заочной и очно-заочной, 318.34kb.
- Методические указания по выполнению рефератов и контрольных работ по курсу «экология», 187.76kb.
- Методические указания к выполнению лабораторной работы №23 по физике для студентов, 142.34kb.
- Методические указания по выполнению курсовой работы для студентов очной и заочной форм, 364.03kb.

Утверждаю
Ректор университета
__________________А.В.Лагерев
«____»____________2008 г.
МАТЕРИАЛОВЕДЕНИЕ, МАТЕРИАЛОВЕДЕНИЕ
И ТЕХНОЛОГИЯ конструкционных МЕТАЛЛОВ
ИЗУЧЕНИЕ МИКРОСТРУКТУРЫ СТАЛЕЙ ПОСЛЕ
ПОВЕРХНОСТНЫХ МЕТОДОВ УПРОЧНЕНИЯ
(ЗАКАЛКИ ТВЧ, ЦЕМЕНТАЦИИ, АЗОТИРОВАНИЯ)
Методические указания
к выполнению лабораторной работы № 12 для студентов
очной и заочной форм обучения
всех специальностей
2-е изд., перераб. и доп.
Брянск 2008
УКД 669.01
Материаловедение, материаловедение и технология конструкционных материалов. Изучение микроструктуры сталей после поверхностного упрочнения (закалка ТВЧ, цементация, азотирование): методические указания к выполнению лабораторной работы № 12 для студентов очной и заочной форм обучения всех специальностей –
2-е изд., перераб. и доп. - Брянск: БГТУ, 2008. – 18 с.
Разработали:
В.П.Мельников
канд. техн. наук, доц.,
С.В.Давыдов
д-р. техн. наук, проф.
Рекомендовано кафедрой «Технология металлов и металловедение» БГТУ (протокол № 6 от 30.10.07 г.)
Печатается по изданию: Материаловедение, материаловедение и технология конструкционных материалов. Изучение микроструктуры сталей после поверхностного упрочнения (закалка ТВЧ, цементация, азотирование): методические указания к лабораторной работе № 12 для студентов дневной и заочной форм обучения всех специальностей. – Брянск: БИТМ, 1990. – 13 с.
ЦЕЛЬ И ЗАДАЧИ РАБОТЫ
Цель работы – ознакомиться с методами поверхностного упрочнения и их влиянием на надежность и долговечность работы деталей.
Задачи работы - изучить микроструктуру и твердость поверхностных слоев и сердцевины стальных деталей после закалки ТВЧ, цементации и азотирования. Ознакомиться с методами определения глубины слоя закалки, цементации и азотирования.
Продолжительность работы – 4 часа.
Необходимое оборудование и материалы
1. Металлографический микроскоп для изучения микроструктуры и измерения глубины слоя.
2. Макротемплеты и микрошлифы от деталей, подвергнутых:
- закалке ТВЧ (обр.№1 и №2);
- цементации, закалке и низкотемпературному отпуску (обр. № 3...6);
- закалке, высокотемпературному отпуску и азотированию (обр. № 7…8);
3. Образцы с указанием марки стали.
ЗАДАНИЕ И ПОРЯДОК РАБОТЫ
1. Провести макро- и микроанализ шлифов коллекции образцов от деталей, подвергнутых закалке ТВЧ, цементации и азотированию. Изучить и зарисовать микроструктуру.
2. Определить глубину поверхностных слоев (после цементации и азотирования по микроструктуре; после закалки ТВЧ по микроструктуре и микротвердости по Виккерсу).
За глубину слоя цементации принимают расстояние от поверхности до полуперлитной зоны (50 % перлита + 50 % феррита). В этой зоне концентрация углерода ~ 0,4 %.
Глубина закаленного при ТВЧ слоя определяется либо по макро-структуре, либо измерением твердости по Виккерсу (или микротведости). Во втором случае за глубину закаленного слоя принимают расстояние от поверхности до полумартенситной структуры (50 % мартенсита + 50 % троостита).
3. Замерить твёрдость поверхностных слоев и сердцевины (после закалки ТВЧ и цементации на приборе Роквела, после азотирования на приборе Виккерса).
Составить отчет, в котором:
-описать особенности каждого способа, излагая кратко, четко и по существу изучаемого вопроса.
-привести данные результатов измерений твёрдости и глубин слоев (табл.1);
Таблица 1
Технологические параметры упрочненной поверхности
№ образца | Вид поверхностной обработки | Марка стали | Глубина слоя, мм | Твердость | |||
Поверхности | Сердцевины | ||||||
HB | HRC (HV) | HB | HRC (HV) | ||||
| | | | |
- сопоставить твердость поверхностных слоев и сердцевин и дать сравнительный анализ;
- изучить, зарисовать и описать микроструктуру поверхностных слоев и сердцевин;
- привести данные о рекомендуемых глубинах закалки ТВЧ, цементации, азотирования, концентрациях: насыщения углеродом при цементации в практике;
- объяснить, за счет чего увеличивается надежность и долговечность работы деталей в каждом случае;
- указать условия целесообразности применения того или иного вида обработки, марки применяемых сталей.
Техника безопасности
При выполнении лабораторной работы студенты проходят инструктаж по технике безопасности, который проводит преподаватель, ведущий учебное занятие, с соответствующей записью в журнале по технике безопасности.
КРАТКИЕ СВЕДЕНИЯ О ЗАКАЛКЕ ТВЧ,
ЦЕМЕНТАЦИИ, АЗОТИРОВАНИИ
Общая часть
в практике рабочая поверхность многих контактирующих в работе друг с другом деталей истирается (изнашивается), либо работает с большими контактными нагрузками1 (рис.1). В ряде случаев между контактирующими поверхностями деталей (сопряженными парами) кроме истирания возможно адгезионное схватывание (сваривание), что приводит к образованию задиров (вырывов металла) на рабочей поверхности.
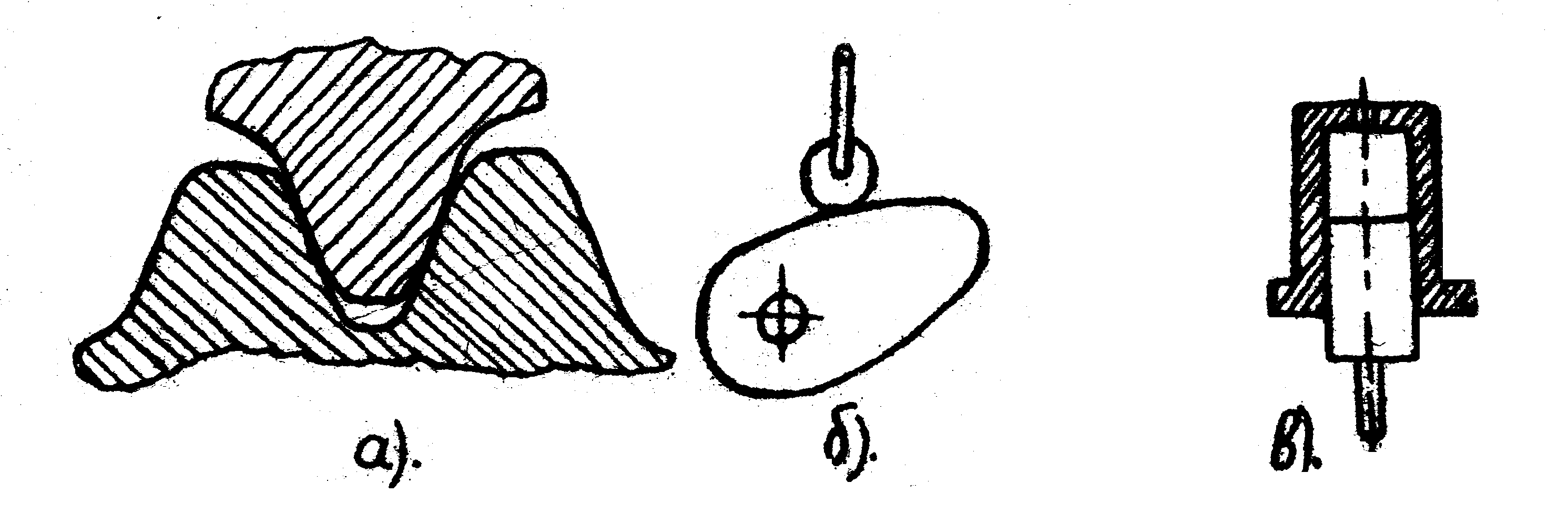
Рис.1. Примеры условий работы контактирующих деталей:
а - истирание (износ) поверхностей и изгиб зубьев шестерен;
б - работа с контактными нагрузками (обкатка ролика по кулачной шайбе);
в - истирание (износ) и адгезионное схватывание взаимнотрущихся
поверхностей плунжерной пары
Это ведет к нарушению (ухудшению) условий работы деталей пар (рис.1в). Одновременно с этим сердцевина2 деталей может воспринимать циклические, переменные и ударные нагрузки, а в некоторых случаях работать еще и на срез1.
Для обеспечения нормальной (надежной) работы деталей сопряженных пар такого типа, кроме высокой твердости, износостойкости контактной прочности или задиростойкости2 поверхностных слоев, необходимо, чтобы сердцевина деталей во многих случаях обладала пластичностью и особенно ударной вязкостью. В таких условиях обычно работают поршневые пальцы, всевозможные шестерни, втулки и ролики приводных цепей, распредвалы и др.
К обработкам, позволяющим существенно изменять свойства поверхностных слоев, сохраняя пластичной и вязкой сердцевину деталей, относятся различные виды химико-термических обработок (цементация, азотирование и др.) и поверхностных закалок (например, закалка ТВЧ).
Поверхностная закалка ТВЧ3
Поверхностная закалка при нагревании токами высокой частоты осуществляется на специальных установках ТВЧ. При этом способе металлическая деталь 1 (рис.2) помещается в концентрированное переменное электромагнитное поле, создаваемое индуктором 2, вследствие чего в поверхностном слое детали возбуждаются (индуктируются) высокой плотности вихревые токи4, тепловая энергия которых почти вся выделяется в этом же слое и вызывает его нагрев.
Изменяя силу тока, можно получить любую скорость нагрева, температуру и глубину прогрева. После нагрева поверхностного слоя деталь 1 перемещается в спрейер 3 (душирующее устройство) для интенсивного охлаждения5.
Рекомендуемые глубины закаленных слоев:
- 1,5...3 мм - детали, работающие на истирание (износ), усталость;
- 4...5 мм - детали, работающие в условиях смятия (продавливающих нагрузок), а в ряде случаев еще и с последующей перешлифовкой;
- 10...15 мм - детали, работающие с большими контактными нагрузками.
На рис.3 дан пример макроструктуры стальной детали с поверхностно закаленным слоем.
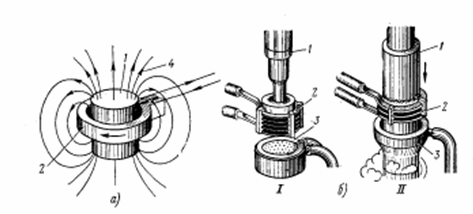
Рис.2. Индукционный нагрев: а - схема индукционного нагрева; б – закалка; I – закалка при одновременном нагреве всей поверхности; II – закалка при непрерывно-последовательном нагреве; 1 – деталь; 2 – индуктор; 3 – спрейер;
4 – силовые линии электромагнитного поля
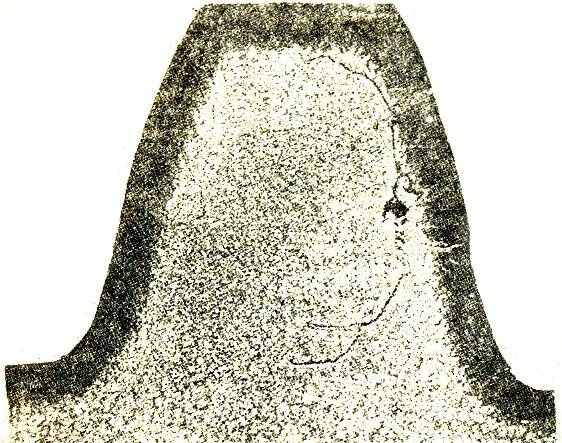
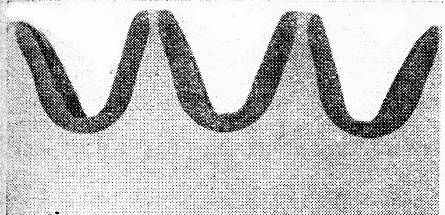


Рис.3. Макроструктура зуба шестерни (а) и зубьев звездочки (б) после ТВЧ-закалки. Темные участки - закаленный слой после травления
Детали, подвергаемые поверхностной закалке, чаще всего изготовляют из обычной среднеуглеродистой стали с содержанием углерода 0,4…0,5%. При меньшем содержании углерода трудно получить высокую твердость. При большой концентрации углерода стали склонны к образованию трещин и хрупкому разрушению в эксплуатации. При правильной конструкции закалочного устройства, обеспечивающего равномерное охлаждение, закалка ТВЧ позволяет закаливать стали с любым содержанием углерода (до 1,0…1,2%) без трещин. Поверхностный слой стали имеет структуру из очень мелкоигольчатого мартенсита (рис.4) и отличается твердостью на 2...4 HRC выше, чем после закалки с печного нагрева.
Твердость, близкую к максимально достижимой, можно получить уже при содержании углерода в стали около 0,6 %.

а
б
Рис.4. Микроструктура поверхностного слоя зуба шестерни после ТВЧ-закалки, х200, травление ниталем: а – мелкоигольчатый мартенсит;
б – троосто-сорбит
В табл.2 приведен пример поверхностной твердости некоторых сталей после закалки ТВЧ.
Таблица 2
Твердость сталей после закалки ТВЧ
Марка стали | НRC до отпуска | Марка стали | HRC до отпуска |
35 | 50... 55 | 35Г2 | 53... 58 |
45 | 55... 60 | 45Г2 | 56… 61 |
50 | 57. . .62 | 50Г | 57… 62 |
65Г | 59... 63 | 40ХНМ | 55... 60 |
У8 | 60. . .64 | ШХ15(~1%C) | 62... 64 |
45Х | 50... 61 | 40ХН | 55…60 |
Цементация
Цементация - процесс диффузионного насыщения углеродом при температуре 880. . .930 °С поверхности деталей из железа или малоуглеродистых (до 0,З5% С)1 сталей. Стали могут содержать и легирующие элементы (хром, никель, молибден, вольфрам, титан).
Производится цементация в специальных цементационных печах в среде углеродосодержащих газов. Глубина насыщения (слоя) для мелких деталей обычно составляет 0,1...0,3 мм, в остальных случаях - от 0,5 до 2,5 мм (наиболее часто 0,6...1,2мм).
На работоспособность цементируемой детали большое (часто решающее) влияние оказывает концентрация углерода в насыщенном слое; при 0,6...0,6% обеспечивается максимальное сопротивление хрупкому разрушению; усталостная прочность при изгибе достигает максимальных значений при 0,8...1,05%, а максимальные значения контактной выносливости получаются при содержании углерода в пределах 1,0...1,25%.
Цементованный слой имеет переменную концентрацию углерода по своей толщине – она снижается от поверхности по направлению к сердцевине детали. В связи с этим изменяется по сечению цементованного слоя и микроструктура, как после медленного охлаждения с температуры цементации, так и после последующей термической обработки. На рис. 5 показано изменение микроструктуры по сечению цементованного слоя при насыщении его поверхностной зоны углеродом свыше 0,8%.
Микроструктура науглероженного слоя у поверхности соответствует строению заэвтектоидной стали (П+ЦII), в которой вторичный цементит наблюдается в виде сетки по границам перлитных колоний (рис.5, а). С понижением углерода до 0,8% микроструктура (рис.5, б) соответствует эвтектоидной стали (П). За эвтектоидной зоной следует доэвтектоидная структура, переходящая в структуру исходной стали, содержащей феррит и перлит (рис.5, в).
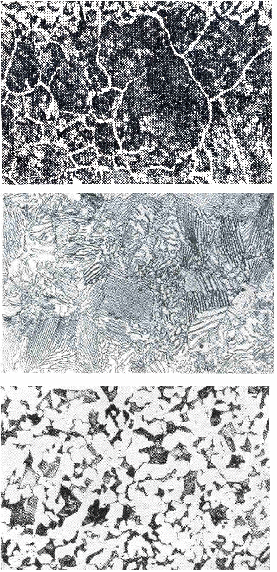
а)
б)
В) в)
Рис.5. Структура цементованного слоя углеродистой стали 15, х100,
травление ниталем: а – заэвтектоидная (П+ЦII); б – эвтектоидная (П);
в-доэвтектоидная (Ф+П)
Для получения в поверхностном слое высокой твердости (57... 63HRC) изделия после цементации подвергают закалке с низкотемпературным отпуском. На рис.6 показана микроструктура цементованного слоя после термической обработки.
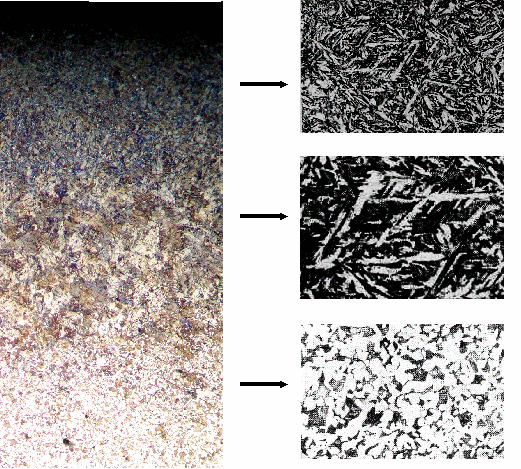
а)
б)
в)




Рис.6. Структура цементованного слоя после термообработки, х50, травление ниталем: а – мелкоигольчатый мартенсит (М+Аост), х500; б – крупноигольчатый мартенсит или троостомартенсит (М+Тр), х500;
в - основная структура (П+Ф), х500
В результате термической обработки поверхностный слой приобретает структуру мелкоигольчатого мартенсита (рис.6, а) с небольшими изолированными участками остаточного аустенита1. При содержании углерода свыше 0,8 % микроструктура содержит еще карбиды (цементит). Карбиды (цементит) в форме сетки по границам зерен резко увеличивают хрупкость. Недопустимы в значительном количестве и изолированные включения карбидов, так как они также снижают вязкость цементованной стали, особенно в углах и торцах деталей.
Под мелкоигольчатым мартенситом располагается зона троостомартенсита (рис.6, б), плавно переходящая в основную структуру, состоящую из феррита и перлита (рис.6, в). Для улучшения вязкости сердцевины деталей рекомендуется применять стали с мелким наследственным зерном (6…8 баллов).
Подобная микроструктура дает возможность судить о глубине цементирования, т.е. насколько далеко от поверхности простирается зона науглероженного металла. За эффективную толщину цементированного слоя принимают расстояние от поверхности детали до половины переходной зоны (зона Ф+П, на рис.6, в), где структура соответствует стали, содержащей 0,4…0,45%С, что соответствует твердости 50НRС.
Глубина цементации – наиболее важная характеристика производственного процесса. Она определяется по излому, микроструктуре или путем химического анализа стружки, послойно снимаемой с упрочненной поверхности детали.
В тяжелонагруженных деталях1, работающих в сложных условиях весьма важное значение имеет и твердость сердцевины, для обеспечения наилучшей работоспособности и надежности. Твердость сердцевины таких деталей должна выдерживаться в пределах 29...43 HRC (такую твердость в сердцевине получают в легированных сталях) и иметь микроструктуру из низкоуглеродистого мартенсита или нижнего бейнита2.
В заключение приведена характеристика некоторых реально применяемых марок цементуемых сталей:
- при средних нагрузках - стали 20, 15Х,20Х,15ХР,18ХГН,20ХФ (среднепрочные с пределом прочности порядка 700 МПа; ударная вязкость свыше 60 Дж/см2);
- при повышенных нагрузках - стали 12Х2Н4А, 20ХН3А, 20Х2Н4А (с прочностью ~ 950…1150 МПа);
- при больших статических и ударных нагрузках - стали 18ХН4МА, 18Х2Н4ВА (высокий комплекс механических свойств: предел прочности 1000...1200 МПа, ударная вязкость больше 60 Дж/см2).
Азотирование
Азотирование (нитрирование) - диффузионное насыщение поверхности деталей азотом при температуре 500.. .520 °С.
Детали, подлежащие азотированию с указанными ранее целями, изготовляют обязательно из сталей, легированных: Cr-Ni, Cr-Mo, Cr-Ni-W, Cr-Ni-Mo,Cr-Mo-Al и др. легирующие элементы повышают твердость азотированного слоя (особенно алюминий). До азотирования детали еще в заготовках подвергают термическому улучшению: закалке и высокотемпературному отпуску на сорбит.
Азотирование проводят в специализированных печах в потоке аммиака NH3.После азотирования термическая обработка не требуется, так как высокая твердость поверхностного слоя обеспечивается непосредственно в процессе азотирования и последующего медленного охлаждения1. Твердость азотированного слоя в зависимости от марки стали колеблется в пределах 1000... 1300 НV2 (твердость поверхностного слоя после цементации 706... 830 НV). Глубина слоя - 0,25...0,45мм (в отдельных случаях до 0,8 мм). Микроструктура азотированного слоя (рис.7), если азотирование проводилось при температура ниже 591С, состоит из , и фаз3.
В процессе азотирования и последующем медленном охлаждении образуются еще зародыши нитридов, полностью когерентные с окружающей -фазой.
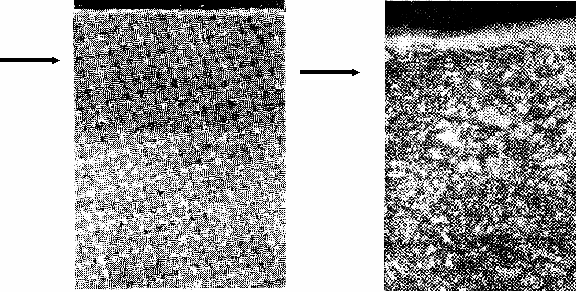
А
а б
Рис.7. Структура азотированного слоя (по стрелке А) с нитридной корочкой, х100 (а) и х250 (б)
Однако -фаза обладает чрезвычайно высокой (большой) хрупкостью. Поэтому в процессе азотирования стремятся не допускать образования -фазы.
Сопоставление рассмотренных способов
поверхностного упрочнения
При всех методах поверхностного упрочнения в поверхностных слоях создаются благоприятные остаточные напряжения сжатия1 (до 300...600 МПа, а в случае азотирования до 1000 МПа и более), которые существенно повышают усталостную прочность деталей2, уменьшают их чувствительность к концентраторам напряжений и увеличивают контактную прочность.
Детали после закалки ТВЧ обладают высокой статической и усталостной прочностью, высокой износостойкостью, контактной прочностью и малой чувствительностью к концентраторам напряжений. Но чаще всего закалку ТВЧ производят для увеличения износостойкости.
В сравнении со сквозной закалкой с печного нагрева при закалке ТВЧ отсутствуют явления окисления и обезуглероживания поверхности при нагреве. Закалка ТВЧ с успехом применяется вместо цементации, сквозной закалки с отпуском, так как позволяет снизить стоимость термической обработки, повысить производительность, получить значительную экономию легирующих элементов. Однако при закалке ТВЧ внешняя форма деталей имеет важнейшее значение. У многих деталей внешняя форма такова, что исключает возможность применить к ним такую закалку.
Назначение цементации деталей с последующей термической обработкой - придать их поверхностному слою высокую твердость и износостойкость, повысить предел контактной выносливости или предел выносливости (усталостной прочности) при изгибе и кручении. Однако себестоимость упрочнения цементацией примерно в 2,5…3 раза выше по сравнению с закалкой ТВЧ.
Азотирование следует использовать для деталей, испытывающих высокие циклические нагрузки при умеренных контактных напряжениях и работающих в условиях трения скольжения (или абразивного износа), а также в случаях, когда требуется низкая склонность к задирам.
Положительное влияние азотирования тем сильнее, чем меньше размеры поперечного сечения деталей и больше в ней концентраторов напряжений. Контактная усталостная прочность у азотированных сталей ниже, чем цементованных, но выше, чем у сталей после закалки ТВЧ. Толщина азотированного слоя деталей, работающих с контактными нагрузками, должна быть не менее 0,45...0,5 мм. Износостойкость азотированного слоя в 1,5…4 раза выше износостойкости закаленных высокоуглеродистых сталей, а также цементованного слоя.
При азотировании практически отсутствуют объемные изменения и коробление деталей.
Недостатки азотирования - высокая хрупкость и малая толщина слоя, необходимо изготавлять детали из легированных сталей, длительность процесса наибольшая.
КОНТРОЛЬНЫЕ ВОПРОСЫ
1. Назовите варианты возможных условий работы сопряженных пар деталей.
2. Какими свойствами должны обладать поверхностные слои и сердцевина деталей в каждом случае для обеспечения нормальной (надежной) работы?
3. Назовите виды обработки, позволяющие существенно изменять свойства поверхностных слоев.
4 . Как нагревается деталь при закалке ТВЧ?
5. Рекомендуемые глубины закаленных слоев в зависимости от условий работы деталей.
6. При каком содержании углерода в стали можно достичь твердости, близкой к максимальной?
7. Одинаковы ли твердость и микроструктура стали в поверхностном слое после закалки с печного нагрева и нагрева ТВЧ?
8. Какой процесс называют цементацией и какие конструкционные стали (указать содержание углерода) следует использовать для данного процесса?
9. Из каких соображений устанавливается величина концентрации углерода в насыщенном слое? Какова при этом микроструктура цементированного слоя после окончательной термической обработки?
10. В каких пределах может изменяться глубина слоя цементации?
11. Какой термической обработке подвергают цементирование детали, и с какой целью?
12. Каким образом можно улучшить вязкость сердцевины деталей?
13. Назовите рекомендуемые соотношения твердости поверхностного слоя и сердцевины в случае применения легированных сталей.
14. Какой процесс называют азотированием? Какие стали рекомендуется применять?
15. Назовите микроструктуру, уровень твердости и глубину азотированного слоя?
16. Какой термической обработке подвергают детали, назначаемые на азотирование?
17. За счет чего улучшается работоспособность деталей после закалки ТВЧ, цементации и азотирования?
18. Когда целесообразно применять закалку ТВЧ, цементацию и азотирование?
19. При какой обработке себестоимость упрочнения деталей ниже?
20. Какие достоинства и недостатки характерны для цементации и азотирования?
СПИСОК РЕКОМЕНДУЕМОЙ ЛИТЕРАТУРЫ
- Солнцев, Ю.П. Материаловедение: учеб. для вузов/ Ю.П.Солнцев, Е.И.Пряхин: под ред Ю.П.Солнцева. – 4-е изд. перераб. и доп. – СП.б.: Химиздат, 2007. – 784 с.
- Арзамасов, Б.М. Материаловедение: учеб. для вузов / Б.Н. Арзамасов, В.Н. Макарова, Г.Г. Мухин [и др.]: под общ. ред. Б.Н. Арзамасова, Г.Г. Мухина. – 5-е изд., стер. – М.: Изд-во МГТУ им. Н.Э. Баумана, 2003. – 648 с.
- Лахтин, Ю.М. Материаловедение / Ю.М.Лахтин. – М.: Машиностроение, 1990. - 528 с.
- Гуляев, А.П. Металловедение / А.П. Гуляев. – М.: Металлургия, 1986.- 544 с.
- Лахтин, Ю.Н. Металловедение и термическая обработка металлов / Ю.Н. Лахтин. – М.: Металлургия, 1984.- 321с.
- Термическая обработка в машиностроении: справочник / под ред. Ю.М.Лахтина, А.Г.Рахштадта. – М.: Машиностроение, 1980.- 783 с.
- Методика исследования микротвердости поверхностных слоев металла. – Брянск: БИТМ, 1984.-11 с.
Материаловедение, материаловедение и технология конструкционных материалов. Изучение микроструктуры сталей после поверхностного упрочнения (закалка ТВЧ, цементация, азотирование): методические указания к выполнению лабораторной работы № 12 для студентов очной и заочной форм обучения всех специальностей
Мельников Валентин Павлович
Давыдов Сергей Васильевич
Научный редактор С.В.Давыдов
Редактор издательства Л.И.Афонина
Компьютерный набор Д.А.Ковтуненко
Иллюстрации В.П.Мельников, С.В.Давыдов
Темплан 2008 г., п.98
Подписано в печать 01.11.07. Формат 60х84 1/16. Бумага офсетная. Офсетная печать. Усл. печ.л. 1,04. Уч.-изд.л. 1,04. Тираж 40 экз. Заказ . Бесплатно.
Брянский государственный технический университет.
241035, Брянск, бульвар 50-летия Октября, 7, БГТУ. 58-82-49.
Лаборатория оперативной полиграфии БГТУ, ул. Институтская, 16.
1 В этом случае условия работы нарушаются вследствие смятия, разрушения рабочей поверхности деталей.
2 Сердцевина - материал детали под упрочненным слоем, не затронутый ни химическим воздействием, ни закалкой.
1 При недостаточной пластичности и вязкости материала возможны поломки (разрушения) деталей.
2 Низким адгезионным схватыванием.
3 ТВЧ - токи высокой частоты.
4 Той же частоты, что и в индукторе.
5 Со скоростью большей критической скорости закалки стали
1 Надо помнить, что хрупкость цементованных деталей в целом, изготовленных из среднеуглеродистых сталей (0,3...0,35%), возрастает с уменьшением сечения деталей и усложнением конфигурации (особенно при отрицательных температурах).
1 Содержание остаточного аустенита в цементованном слое не должно превышать 15...20 %, так как значительно снижается прочность и др. эксплуатационные свойства цементованной детали.
1 Например зубчатые колеса и шестерни.
2 Недопустимы выделения структурно свободного феррита - резко снижается усталостная прочность, а также ударная вязкость.
1 Поэтому детали практически не имеют коробления и деформаций, что позволяет применять азотирование в точном машиностроении (например, при изготовлении шестерен с зацеплением сложной формы).
2 Твердость по Виккерсу.
3 -фаза – твердый раствор на базе нитрида Fe2-3N(4.55-11%N); -фаза – твердый раствор на базе нитрида Fe4N(5,3-5,7% N); -фаза - твердый раствор азота в -железе при 20оС – 0,004%N, при 590оС-0,11%N.
1 Напряжения 1 рода.
2 Прочность азотированного слоя составляет 0,1 прочности сердцевины. Увеличение предела выносливости (усталостной прочности) деталей в целом объясняют образованием в поверхностном (азотированном) слое остаточных напряжений сжатия, достигающих до уровня 1000 МПа, а в некоторых случаях и более.