Методические указания к выполнению лабораторной работы №6 для студентов всех форм обучения всех специальностей Брянск 2008
Вид материала | Методические указания |
- Методические указания по выполнению лабораторной работы №6 для студентов 1-го курса, 124.2kb.
- Методические указания к выполнению лабораторной работы №21 по физике для студентов, 119.29kb.
- Методические указания к выполнению лабораторной работы №12 для студентов очной и заочной, 222.24kb.
- Утверждаю Кафедра «Технология металлов и металловедение», 330.91kb.
- Методические указания к выполнению лабораторной работы №9 для студентов очной и заочной, 251.35kb.
- Методические указания к выполнению лабораторной работы №10 для студентов очной формы, 240.19kb.
- Методические указания к выполнению курсовой работы для студентов эфф, автф всех специальностей, 1176.51kb.
- Методические указания по выполнению контрольных работ по дисциплине «Страхование» для, 1588.5kb.
- Методические указания по выполнению курсовой работы для студентов специальностей 080507, 130.79kb.
- Методические указания к выполнению лабораторной работы №23 по физике для студентов, 142.34kb.


Утверждаю
Ректор университета
________________А.В.Лагерев
«____»___________2008 г.
Материаловедение. Материаловедение
и технология конструкционных материалов
Исследование влияния термической обработки
на микроструктуру и механические свойства
некоторых углеродистых конструкционных
и инструментальных сталей
Методические указания
к выполнению лабораторной работы № 6
для студентов всех форм обучения всех специальностей
Брянск 2008
УДК 669.01
Материаловедение. Материаловедение и технология конструкционных материалов и другие совмещенные дисциплины. Исследование влияния термической обработки на микроструктуру и механические свойства некоторых углеродистых конструкционных и инструментальных сталей: методические указания к выполнению лабораторной работы № 6 для студентов всех форм обучения всех специальностей. – Брянск: БГТУ, 2008 – 16 с.
Разработал: В.П. Мельников,
канд.техн.наук, доц.
Рекомендовано кафедрой «Технология металлов и металловедение» БГТУ (протокол № 3 от 04.04.08)
Цель и задачи работы
Цель работы – экспериментально показать, что оказанное температурное (тепловое) воздействие на металлические материалы может существенно изменять их строение и свойства.
Задача работы – изучить микроструктуру и твердость образцов после термических обработок, подвергнув образцы углеродистой конструкционной и инструментальной сталей отжигу, нормализации, закалке и отпуску; выполнить индивидуальное задание по назначению термической обработки для конкретного изделия.
Продолжительность работы – 4 часа.
- Краткие сведения из теории
Термическая обработка – самый распространенный в современной технике способ изменения свойств металлов и сплавов.
Термической обработкой называют совокупность операций нагрева, выдержки и последующего охлаждения изделий из металлов и сплавов. Задача термической обработки – путем нагрева и охлаждения вызвать требуемые изменения структуры и как следствие свойств*. Наиболее распространенными видами термической обработки являются отжиг, нормализация и закалка с отпуском.
Режимы термических обработок характеризуются следующими параметрами (рис. 1): временем (скоростью) нагрева τн до требуемой температуры tmp.н, временем выдержки τв и временем охлаждения τо (охлаждение с заданной скоростью снижения температуры).
Скорость нагревания зависит от химического состава стали исходного состояния и сложности конфигурации изделия. Требуемая температура нагрева в основном определяется на основании диаграммы состояния железоуглеродистых сплавов (рис.2). Выдержка при температуре нагрева должна обеспечивать полный прогрев изделия по всему объему для завершения фазовых превращений, растворения карбидов и выравнивания температуры и химического состава во всех сечениях. Условия (скорость) охлаждения при каждом виде термической обработки различны.
________________
* Термообработка имеет особое значение для изделий из сталей из-за полиморфизма железа. Для сплавов на базе других элементов она не дает такого эффекта по изменению свойств, как для сталей.

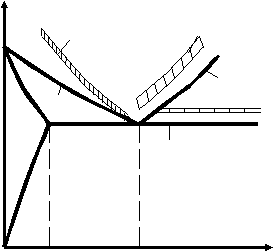
30…50o 50…70о
τн τв τо С Ay
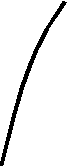

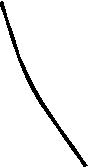








P


Время (τ) 0 0,02 0,8 С,%
Рис. 1. Режим термической Рис.2. Оптимальные интервалы
обработки температур нагрева для
термической обработки до-
и заэвтектоидных сталей
(АСз и АСсм – верхние кри-
тические температуры;
АС – нижняя критическая
температура)
Изделия несложных конфигураций из углеродистых и малолегированных сталей с низким углеродом можно нагревать относительно быстро: загружать изделия в предварительно нагретую до требуемой температуры печь. В этом случае общее время нагревания и выдержки при заданной температуре обычно исчисляют из расчета 1 минута на 1мм толщины в наибольшем сечении изделия из углеродистых сталей. Для малоуглеродистых легированных сталей в связи с их пониженной теплопроводностью* это время увеличивается на 25…40 % **.
Традиционными видами термической обработки изделий из конструкционных и инструментальных сталей являются отжиг, нормализация, закалка в сочетании с тем или иным вида отпуска.
________________
* Вследствие чего между внешними и внутренними слоями возникает большой перепад температур, приводящий к возникновению больших внутренних напряжений, а иногда и к возникновению трещин в процессе нагрева.
** Для изделий из среднелегированных и высоколегированных сталей время нагревания и время выдержки при температуре нагрева рассчитываются на основании известных эмпирических формул или определяются экспериментально в каждом конкретном случае.
- Отжиг*
Отжигом называют вид термической обработки, заключающейся в нагреве выше критических температур (рис.2) с последующим медленным охлаждением (обычно вместе с выключенной печью).
В зависимости от температуры нагрева отжиг подразделяют на полный (нагрев выше верхней критической температуры) и неполный (выше нижней критической температуры). Доэвтектоидные стали подвергают обычно только полному отжигу (нагрев на 30…50оС выше АС3)**, заэвтектоидные стали – неполному (нагрев на 50…70оС выше АС1)***.
- Нормализация
Нормализацией называют вид термической обработки, включающей нагрев выше верхних критических точек доэвтектоидных сталей на 30…50оС, заэвтектоидных – 50…70оС (рис.2) с последующим охлаждением на воздухе.
Микроструктура доэвтектоидных сталей перлитного класса после нормализации по фазовому составу получается такой же, как и после отжига, только более мелкозернистой вследствие ускоренного охлаждения на воздухе. Это способствует повышению твердости и прочности нормализованных сталей (по сравнению с отожженными) примерно на 10…15%.
- Закалка****
Закалкой называют вид термической обработки, заключающейся в нагреве сталей выше критических температур с последующим охлаждением со скоростями больше критических или критическими. При этом аустенит превращается в мартенсит, представляющий собой пересыщенный раствор углерода в тетрагональной α-решетке.
Указанные скорости охлаждения обеспечиваются применением соответствующих охлаждающих сред (см. приложение, табл.2).
_____________
* Речь идет об отжиге II-го рода (об отжиге для фазовой перекристаллизации).
** При неполном отжиге доэвтектоидных сталей феррит практически не претерпевает превращений, а потому в строении сталей не происходит заметных изменений.
*** При полном отжиге в заэвтектоидных сталях формируется цементитная сетка, резко снижающая механические свойства.
**** Речь идет о закалке с полиморфным превращением.
Закалку подразделяют на полную (нагрев на 30…50оС для доэвтектоидных и на 50…70оС для заэвтектоидных сталей выше верхних критических температур) и неполную (нагрев на 30…50оС или на 50…70оС соответственно выше нижней критической температуры АсI).
Закалка, вследствие больших остаточных напряжений в закаленных изделиях, высокой хрупкости мартенсита, не является окончательной термической обработкой. Поэтому закаленные изделия подвергают дополнительной термической обработке, называемой отпуском.
- Отпуск закаленных сталей
Отпуском называют вид термической обработки, заключающийся в нагреве закаленных сталей до температур, не превышающих АСI (рис.2).
По температуре нагрева отпуск подразделяют на:
- низкотемпературный (НТО) – до 200 (250) оС;
- среднетемпературный (СТО) – 350…450 (480) оС;
- высокотемпературный (ВТО) – 500…650 (680) оС.
Закалка с высокотемпературным отпуском называется термическим улучшением (или просто улучшением).
Температура, время выдержки и скорость охлаждения после отпуска выбирается в зависимости от характера и назначения изделия, химического состава стали и требований к свойствам.
- УКАЗАНИЯ ПО ВЫПОЛНЕНИЮ РАБОТЫ
И СОДЕРЖАНИЮ ОТЧЕТА
- Необходимые материалы и оборудование
- По 6 шт. образцов одинаковых размеров и одного химического состава из сталей разного назначения.
- Термические печи для нагрева.
- Потенциометры для замера температур.
- Бачок с водой для охлаждения (закалки) образцов.
- Клещи для загрузки и выгрузки образцов из печей.
- Напильник, шлифовальная бумага с разной зернистостью абразива для предварительной механической обработки и подготовки образцов к полированию.
- Полировальный станок, суспензия порошка окиси хрома для полировки шлифов.
- Реактив ниталь (3…5% азотной кислоты в спирте) для травления и выявления микроструктуры изучаемых образцов; фильтровальная бумага для сушки шлифов после промывания в воде.
- Металлографический микроскоп для изучения микроструктур.
- Твердомеры для измерения твердости образцов после термических обработок.
- Техника безопасности
- Не разрешается касаться электропроводки руками, вскрывать защитный кожух терморегулятора на электропечах, находящихся под напряжением.
- Электропечи включать и выключать рубильниками.
- Образцы закладывать в печи и извлекать из них только клещами.
- Запрещается снимать защитный кожух полировального станка при вращении диска.
2.3. Последовательность выполнения работы
Работа выполняется за 2 занятия.
Первое занятие (2 часа):
- Получить образцы (№ 1-6 из стали одного химического состава и № 7-12 – другого), записать клейма.
- Назначить режимы отжига, нормализации, закалки и отпусков (прил. 1).
- Загрузить в предварительно нагретую печь обр. № 1 и 7 – на отжиг; обр. № 2 и 8 – на нормализацию; обр. № 3-6 и 9-12 – на закалку, выдержать в печи и охладить по режимам соответственно виду термической обработки.
- Образцы № 4 и 10 подвергнуть отпуску при температуре 200оС, образцы № 5 и 11 – при 400оС и образцы № 6 и 12 – при 600оС. Время выдержки не менее 50 минут, охлаждение после отпуска на воздухе.
- Начать предварительное оформление отчета.
Второе занятие (2 часа).
1. Зачистить на шлифовальной бумаге с грубым зерном торцы образцов и измерить твердость:
- образцов № 1,2,7,8 – на твердомере Бринелля;
- образцов № 3-6 и 9-12 – на твердомере Роквелла.
Результаты занести в отчет.
2. Провести предварительную шлифовку (вручную) образцов на шлифовальных бумагах различной зернистости и отполировать на полировальном станке поверхность шлифов.
3. Промыть и высушить фильтровальной бумагой шлифы после полировки.
4. Протравить шлифы в реактиве, повторно промыть и высушить.
5. Изучить и зарисовать в отчете микроструктуры образцов.
2.4. Содержание отчета
При составлении отчета необходимо:
- сформулировать цель и задачи работы;
- дать краткое изложение теории термической обработки и характеристику различных видов термообработок;
- перечислить необходимое оборудование и материалы, использованные при выполнении работы;
- кратко описать методику выполнения работы;
- привести результаты экспериментов в табл. 1 и 2 нижеприведенных форм;
- описать превращения, происходящие при отжиге, нормализации и отпуске сталей;
- привести рисунки микроструктур исследованных сталей после различных видов термической обработки; проанализировать микроструктуры и описать их различие;
- сравнить твердость сталей после отжига, нормализации, закалки и закалки с отпуском. Построить график зависимостей твердости закаленных сталей от температуры отпуска (рис. 3): для образцов № 3 и 9 температуру отпуска считать равной +20оС;
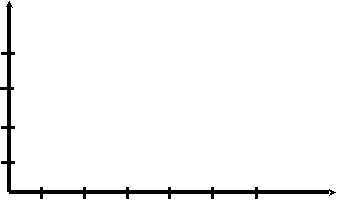
HRC
40
20
0 200 400 600 оС
Рис.3. Зависимость твердости закаленных сталей
от температуры отпуска
- отчет закончить выводами.
- Выполнение индивидуальных заданий
Задания выдаются преподавателем (тексты заданий приведены в работах [4] и [5].
Решение заданий привести в отчете по лабораторной работе.
- Защита лабораторной работы
Защита работы проводится в форме собеседования с преподавателем. Излагаемую информацию при необходимости иллюстрировать графиками и рисунками.
Перед защитой необходимо проработать теоретические положения по теме работы и быть готовыми к ответу на вопросы, приведенные ниже.
Таблица 1
Высокотемпературные виды термических обработок
№ образца | Исходная твердость, НВ | Вид термической обработки | Режимы | Твердость | Микроструктура | |||
Температура нагрева t,оС | Время нагрева и выдержки τ, мин | Охлаждающая среда | НВ | HRC | ||||
| | | | | | | | |
Таблица 2
Низкотемпературные обработки
№ образца | Вид отпуска | Режимы отпуска | Твердость, HRC | Микроструктура | ||
Температура t,оС | Время выдержки τ, мин | Охлаждающая среда | ||||
| | | | | | |
- Вопросы Для самоподготовки
к выполнению и защите лабораторной работы
Теория термической обработки
- Что понимают под термической обработкой?
- Распад переохлажденного аустенита в изотермических условиях и при непрерывном охлаждении с различными скоростями. В каких координатах строятся термокинетические диаграммы?
- В чем различие между перлитом, сорбитом, трооститом и бейнитом в строении и по свойствам? Что понимают под мартенситом? Каковы его свойства в сравнении с другими структурными составляющими, образующимися при распаде переохлажденного аустенита?
- В чем заключается влияние углерода на температуру начала и конца мартенситного превращения?
- Что понимают под критической скоростью закалки? От чего она зависит?
- Превращение мартенсита (закалки) и остаточного аустенита при нагреве закаленной стали. Чем отличается мартенсит отпуска от мартенсита закалки? В чем отличие строения сорбита и троостита отпуска от одноименных структур, образующихся при распаде переохлажденного аустенита?
Технология термической обработки стали
- Какие операции термических обработок называют отжигом, нормализацией, закалкой и отпуском? Каковы условия охлаждения при этом?
- Какие параметры характеризуют режим любой термической обработки? От каких факторов зависят? Как выбирается температура нагрева, время нагрева и выдержки для термической обработки?
- После какой термической обработки достигается наиболее высокая твердость?
- Закалка при непрерывном охлаждении, прерывистая, ступенчатая и изотермическая. Требования к охлаждающим средам. Охлаждающие среды.
- Что такое закаливаемость и прокаливаемость сталей? Перечислите основные факторы, оказывающие наибольшее влияние на эти характеристики. Какова связь между прокаливаемостью и критической скоростью закалки?
- Назовите виды отпуска закаленных сталей.
Дополнительные вопросы к защите лабораторной работы
- Перечислите возможные продукты распада переохлажденного аустенита при охлаждении со скоростями меньше и больше критической.
- В каких случаях изделия подвергаются отжигу, нормализации или закалке?
- Какими структурными дефектами сопровождается нагрев изделий значительно выше верхних критических температур? При какой температуре начинается интенсивный рост аустенитного зерна наследственно мелкозернистой стали?
- Как отражается перегрев сталей на свойствах термообработанных изделий?
- Почему полный отжиг не применяется для заэвтектоидных сталей?
- Для изделий из каких сталей отжиг можно заменить нормализацией? Почему?
- Какими характеристиками оцениваются результаты закалки сталей?
- Почему закалка не может быть окончательной термической обработкой?
- Почему доэвтектоидные стали рекомендуют подвергать полной закалке, а заэвтектоидные – неполной?
- Чем определяется выбор охлаждающей среды при закалке?
- Какой способ закалки позволяет иметь в изделиях наименьшие внутренние остаточные напряжения и величину деформации?
- Какую микроструктуру принимают за закаленную? Как регулируется глубина закаленного слоя в реальных изделиях?
- От чего зависит количество остаточного аустенита в закаленных сталях? Будет ли в структуре закаленной углеродистой стали с 0,5% углерода остаточный аустенит? Почему?
- С какой целью производится тот или иной вид отпуска закаленных сталей? Как изменяется твердость закаленной стали в зависимости от температуры отпуска?
- Что понимают под термическим улучшением? Когда оно применяется? Какова микроструктура стали? Какие свойства стали приобретают оптимальные значения?
- Какая микроструктура обеспечивает наибольшую твердость стали?
- Какие термические обработки обеспечивают наиболее высокую пластичность?
- Какой термической обработкой можно повысить предел упругости стали?
- Какая термическая обработка обеспечивает высокую износостойкость, а какая – предел выносливости?
- В чем причина высокой восприимчивости сталей к термической обработке?
- Назовите основные фазовые превращения при термической обработке стали.
- В чем заключаются принципиальные отличия в условиях охлаждения при получении равновесных и неравновесных микроструктур?
Список рекомендуемой литературы
- Арзамасов, Б.М. Материаловедение: учеб. для вузов / Б.Н. Арзамасов, В.Н. Макарова, Г.Г. Мухин [и др.]: под общ. ред. Б.Н. Арзамасова, Г.Г. Мухина. – 5-е изд., стер. – М.: Изд-во МГТУ им. Н.Э. Баумана, 2003. – 648 с.
- Лахтин, Ю.Н. Металловедение и термическая обработка металлов: учеб. для вузов / Ю.М.Лахтин. – 4-е изд. – М.: Металлургия, 1993.- 448с.
- Лахтин, Ю.М. Материаловедение / Ю.М.Лахтин. – М.: Машиностроение, 1990. - 528 с.
- Мельников, В.П. Материаловедение. Термическая и химико-термическая обработки: сб. инд. заданий /В.П.Мельников – Брянск: БГТУ,1996.– 11с.
- Мельников, В.П. Материаловедение. Термическая обработка: индивидуальные задания /В.П.Мельников. – Брянск: БИТМ, 1989. – 9 с.
Приложение
Справочные данные
Таблица 1
Критические температуры сталей
Марка стали | Критические точки, оС | Марка стали | Критические точки, оС | |||
АС1 | АС3 | АС1 | АС3 | АСсm | ||
20 25 30 35 40 45 50 55 | 735 735 730 730 730 730 725 725 | 850 835 820 810 790 755 760 755 | 60 У7 У8 У9 У10 У12 | 725 730 730 740 730 730 | 750 770 765 - - - | - - - 760 800 820 |
Таблица 2
Интенсивность охлаждения изделий в охлаждающих средах
Охлаждающая среда | Скорость охлаждения в интервале температур ( о/сек) | |
500…600оС | 200…300оС | |
Вода при + 18о + 26о + 50о + 74о Масло (20…200оС) Раствор NaCl в воде при + 18оС Спокойный воздух | 600 500 100 30 150 1100 3 | 270 270 270 200 30 300 1 |
Таблица 3
Твердость и микроструктура некоторых сталей в зависимости
от термообработки
Марка стали | Термообработка | Микроструктура | Твердость | Примечание | |
НВ | HRC | ||||
45 | Отжиг Нормализация Закалка Закалка и отпуск 200оС Закалка и отпуск 400оС Закалка и отпуск 600оС | Феррит и перлит Феррит и перлит Мартенсит закалки Мартенсит отпуска Троостит отпуска Сорбит отпуска | ~179 ~197 - - - | - - ~56 ~52 ~42 ~27 | Диаметр образца 10 мм. Охлаждение при закалке в воде |
У8 | Отжиг Нормализация Закалка Закалка и отпуск 200оС Закалка и отпуск 600оС | Перлит пластинчатый Перлит пластинчатый сорбитизированный Мартенсит закалки Мартенсит отпуска Сорбит отпуска | ~230 ~270 - - - | - - ~63 ~60 ~30 | Ø =10мм. Охлаждение при закалке в воде. После закалки кроме мартенсита имеется остаточный аустенит, который обнаруживается только спецметодами исследования |
Материаловедение. Материаловедение и технология конструкционных материалов и другие совмещенные дисциплины. Исследование влияния термической обработки на микроструктуру и механические свойства некоторых углеродистых конструкционных и инструментальных сталей: методические указания к выполнению лабораторной работы № 6 для студентов всех форм обучения всех специальностей.
Мельников Валентин Павлович
Научный редактор С.В. Давыдов
Редактор издательства Л.И. Афонина
Компьютерный набор А.И. Жуков
Иллюстрации В.П.Мельников
Темплан 2008 г., п 165
Подписано в печать . Формат 60х84 1/16. Бумага офсетная. Офсетная печать. Усл. печ.л. 0,93. Уч.-изд.л. 0,93. Тираж 50 экз. Заказ . Бесплатно.
Брянский государственный технический университет.
241035, Брянск, бульвар 50-летия Октября, 7, БГТУ. 58-82-49.
Лаборатория оперативной полиграфии БГТУ, ул. Институтская, 16.