Методические указания к выполнению лабораторной работы №10 для студентов очной формы обучения всех специальностей Издание третье
Вид материала | Методические указания |
- Методические указания к выполнению лабораторной работы №12 для студентов очной и заочной, 222.24kb.
- Методические указания к выполнению лабораторной работы №6 для студентов всех форм обучения, 197.64kb.
- Методические указания к выполнению лабораторной работы №21 по физике для студентов, 119.29kb.
- Методические указания к выполнению лабораторной работы №9 для студентов очной и заочной, 251.35kb.
- Методические указания по выполнению лабораторной работы №6 для студентов 1-го курса, 124.2kb.
- Методические указания к выполнению курсовой работы для студентов эфф, автф всех специальностей, 1176.51kb.
- Методические указания к практическим занятиям и для самостоятельной работы студентов, 441.72kb.
- Методические указания к выполнению лабораторной работы №3 для студентов всех специальностей, 152.69kb.
- Методические указания к выполнению задания по черчению для студентов всех специальностей, 589.35kb.
- Методические указания к лекционным и практическим занятиям для студентов Iкурса очной, 331.48kb.
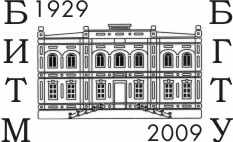
ФЕДЕРАЛЬНОЕ АГЕНТСТВО ПО ОБРАЗОВАНИЮ Брянский государственный технический университет |
Утверждаю
Ректор университета
____________ А.В.Лагерев
«_____»____________2009 г.
ТЕХНОЛОГИЯ КОНСТРУКЦИОННЫХ МАТЕРИАЛОВ
ОБРАБОТКА ЗАГОТОВОК
НА СВЕРЛИЛЬНЫХ СТАНКАХ
Методические указания
к выполнению лабораторной работы № 10
для студентов очной формы обучения
всех специальностей
Издание третье
переработанное и дополненное
Брянск 2009
УДК 621.946.025.7
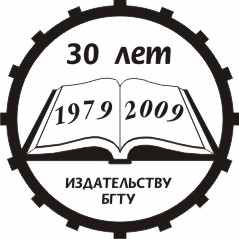
Технология конструкционных материалов. Обработка заготовок на сверлильных станках: методические указания к выполнению лабораторной работы № 10 для студентов
очной формы обучения всех специальностей - 3-е изд., испр. и доп. – Брянск: БГТУ, 2009г.- 14 с.
Разработал:
Е.В. Ковалева
канд.техн.наук, доц.
Рекомендовано кафедрой "Технология металлов и металловедение" БГТУ (протокол № 9 от 25.12.08 г.)
Печатается по изданию: Обработка заготовок на сверлильных станках: методические указания к выполнению лабораторной работы
№ 10 для студентов 1-го курса очной и 2-го курса очно-заочной (вечерней) форм обучения всех специальностей. - Брянск, 2001г.
1. ЦЕЛЬ РАБОТЫ
Цель работы - ознакомиться с применением станков сверлильной группы, инструментами и особенностями технологии обработки отверстий на вертикально-сверлильных станках.
Продолжительность работы - 2 часа.
2. КРАТКАЯ ХАРАКТЕРИСТИКА СВЕРЛИЛЬНЫХ СТАНКОВ
Сверлильные станки относятся ко второй группе станков. Эти станки предназначены для сверления и рассверливания отверстий, нарезания в них резьбы, зенкерования, зенкования, цекования, притирки отверстий и т. п.
Основные типы сверлильных станков:
- вертикально-сверлильные;
- одношпиндельные полуавтоматы;
- многошпиндельные полуавтоматы;
- радиально-сверлильные;
- горизонтально-сверлильные.
Наибольшее распространение получили вертикально-сверлильные и горизонтально-сверлильные станки.
Вертикально-сверлильные станки применяют для обработки отверстий в деталях сравнительно небольшого размера. При сверлении главным движением является вращательное движение инструмента, а движением подачи – поступательное движение инструмента вдоль оси.
На вертикально-сверлильных станках ось вращения шпинделя
расположена вертикально. Совмещение оси вращения инструмента с осью отверстия достигается путем перемещения заготовки на столе станка.
Общий вид вертикально-сверлильного станка представлен на рис. 1.
Станина 3 имеет вертикальные направляющие, по которым перемещается стол 2 и шпиндельная бабка 5, несущая шпиндель 4. На шпиндельной бабке расположены электродвигатель 15, механизмы привода главного движения и подач, механизм включения и отключения вращения шпинделя и органы управления. Управление коробками скоростей и подач осуществляется рукоятками 7, 16; ручная подача – штурвалом 8. Глубину обработки контролируют по лимбу 10. Фундаментная плита 1 служит опорой станка. Стол 2 перемещают по направляющей станины 3.
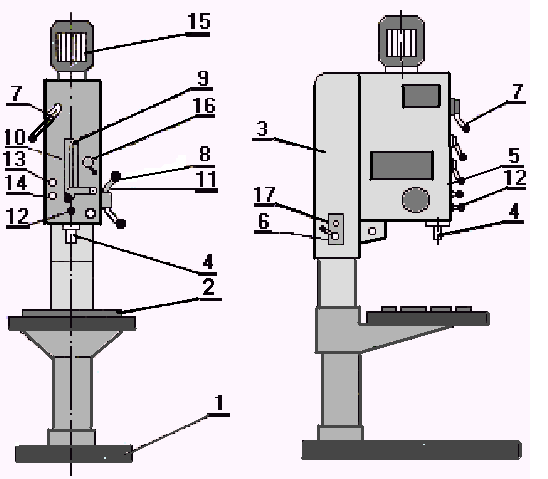
Рис. 1. Схема вертикально-сверлильного станка:
1 – плита; 2 – стол; 3 – станина; 4 – шпиндель; 5 – шпиндельная бабка; 6 – рукоятка включения двигателя; 7 – вариатор скоростей; 8 – штурвал; 9 – рукоятка установки глубины сверления; 10 – лимб глубины обработки; 11 – рукоятка включения самохода; 12 – рукоятка для выбивания инструмента; 13 – гнездо для подъема и опускания шпиндельной бабки; 14 – гнездо для закрепления шпиндельной бабки; 15 – электродвигатель; 16 – рукоятка скорости подачи;
17 – контрольная лампочка
Настройка и наладка станка на работу производится следующим образом: включение станка происходит путем поворота ручки 6 в положение «включено» (должна загореться контрольная лампочка 17). Рукояткой 7 устанавливают нужную частоту вращения шпинделя, поворачивая ее вправо или влево. Нужную величину подачи устанавливают рукояткой 15, вращая ее вправо или влево. На столе 2 устанавливают приспособление, в которое закрепляют деталь. При сверлении глухих отверстий глубину резания устанавливают рукояткой 9.
Радиально-сверлильные станки применяются для обработки заготовок с большим числом отверстий. Эти станки отличаются тем, что оси инструмента и обрабатываемых отверстий совмещаются поворотом и горизонтальным перемещением шпиндельной бабки станка без изменения положения заготовки.
3. ВИДЫ РАБОТ И РЕЖУЩИЕ ИНСТРУМЕНТЫ
Сверление (рис.3а) - процесс образования отверстий в сплошном материале с помощью сверл.
По конструкции и назначению сверла подразделяют на спиральные, центровочные и специальные. Наибольшее распространение получили сверла спиральные, имеющие два режущих лезвия и две спиральные канавки для выхода стружки.
Спиральное сверло с цилиндрическим или коническим хвостовиком состоит из четырех частей: рабочей 6, шейки 2, хвостовика 4 и лапки 3(рис. 2). В рабочей части 6 различают режущую 1 и направляющую части 5 с винтовыми канавками.
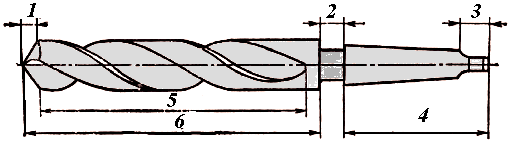
Рис.2. Основные части спирального сверла.
Шейка 2 соединяет рабочую часть сверла с хвостовиком. Хвостовик 4 служит для установки сверла в шпинделе станка. Лапка 3 является упором при выбивании сверла из отверстия шпинделя станка.
Спиральные сверла применяют для получения отверстий диаметром от 0,3 до 80 мм. Точность обработки отверстий после сверления невысокая и находится в пределах 12...13 квалитетов, шероховатость Rа = 5...20 мкм.
Зенкерование (рис. 3, в) – процесс обработки цилиндрических и конических необработанных отверстий в деталях, полученных литьем, штамповкой или ковкой, а также предварительно просверленных, с целью увеличения диаметра, улучшения качества их поверхности, повышения точности (уменьшения конусности, овальности, разбивки). Выполняется зенкерами, которые по внешнему виду напоминают сверло и состоят из тех же элементов, но имеют больше режущих кромок (3–4) и спиральных канавок.
Зенкеры диаметром до 30...40 мм выполняют с коническим хвостом, диаметром до 100 мм – насадные. Насадные зенкеры закрепляются на специальных отправках.
Точность и шероховатость обработки зенкерованием:
а) после сверления - 11 квалитет и Rа = 2,5...5 мкм;
б) литых и прошитых отверстий - 12 квалитет и Rа = 10...20 мкм.
Развертывание (рис. 3, г) – обработка отверстий после сверления, зенкерования или расточки для получения точных размеров и малой шероховатости поверхности. Основным инструментом является развертка, которая состоит из рабочей части, шейки и хвостовика. В зависимости от формы обрабатываемого отверстия применяют цилиндрические и конические развертки с 6–12 зубьями. Развертки различают машинные и ручные, по способу применения - с цилиндрическим хвостовиком диаметром до 10 мм, коническим хвостовиком диаметром до 32 мм и насадные диаметром до 50 мм. Для больших размеров отверстий применяют развертки сборной конструкции.
Для развертывания конических отверстий в заготовке отверстие сначала обрабатывают ступенчатым коническим зенкером (рис.3,м), а затем конической разверткой со стружкоразделительными канавками (рис.3,н). После этого окончательно обрабатывают конической разверткой с гладкими режущими кромками (рис. 3, о).
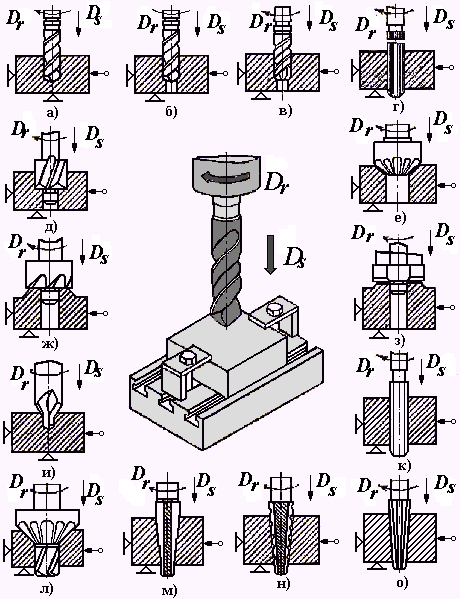
Рис.3. Схемы обработки поверхностей на сверлильных станках:
а – сверление; б – рассверливание; в – зенкерование;
г – развертывание; д – цилиндрический зенкер (зенковка);
е – конический зенкер (зенковка); ж – цековка; з – пластинчатый резец; и – центровочное сверло; к – метчик; л – комбинированный инструмент; м – конический зенкер; н, о– конические развертки
Точность и шероховатость обработки развертыванием:
а) нормальное (предварительное) - 9 и 10 квалитеты,
Rа = 1,25...2,5 мкм;
б) чистовое - 7 и 8 квалитеты, Rа = 0,32...1,25 мкм;
в) тонкое - 6 и 7 квалитеты, Rа = 0,16...0,32 мкм.
Зенкование – образование цилиндрических или конических углублений в предварительно просверленных отверстиях под головки болтов, винтов и заклепок. Применяют для этого цилиндрические (рис. 3, д) и конические (рис. 3, е) зенкеры (зенковки), имеющие 4–8 торцовых зубьев. Некоторые зенковки имеют направляющую часть (рис. 3, д), которая обеспечивает совпадение осей углубления и основного отверстия.
Цекование – обработка торцовых поверхностей под гайки, шайбы и кольца. Применяют торцовые зенкеры или ножи (пластины). Перпендикулярность торца основному отверстию достигается наличием направляющей части у цековки (рис. 3, ж) и у пластинчатого резца (рис. 3, з).
Нарезание резьбы в отверстиях заготовки производят метчиком (рис. 3, к).
Сложные поверхности получают комбинированным инструментом (рис. 3, л).
4. РЕЖИМЫ РЕЗАНИЯ ПРИ ОБРАБОТКЕ
НА СВЕРЛИЛЬНЫХ СТАНКАХ
К режимам резания при сверлении, рассверливании, зенкеровании, развертывании относятся скорость резания Dr, подача Ds, глубина резания t.
Скоростью резания при обработке на сверлильных станках является окружная скорость точки режущей кромки, наиболее удаленной от оси сверла. По скорости резания рассчитывается частота вращения инструмента n , мин:
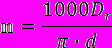
где Dr - скорость резания, м/мин;
d - диаметр инструмента, мм;
π = 3,14.
Выбор скорости резания зависит от механического свойства обрабатываемого материала и материала режущей части сверла, его диаметра, величины подачи, стойкости инструмента, охлаждения, глубины резания и других факторов и назначается по нормативам.
Так, сверла, изготовленные из быстрорежущей стали марки Р6М5, допускают скорость резания при обработке стали до 0,5 м/с
(30 м/мин), у твердосплавного инструмента – до 0,67 - 1,33 м/с
(40 - 80 м/мин).
При сверлении и зенкеровании инструментами из быстрорежущей стали с применением охлаждающих жидкостей рекомендуется скорость резания Dr , м/мин:
- сталь конструкционная средней точности - 21...30;
- чугун серый средней прочности - 30...40;
- алюминиевые сплавы - 60...90.
Из технологических соображений для обеспечения заданной точности и шероховатости при развертывании скорость резания уменьшается. При развертывании отверстий в стальных и чугунных деталях средней твердости и прочности рекомендуется принимать
Dr = 6...3 м/мин.
Подачей на сверлильных станках является осевое перемещение инструмента за время его полного оборота Ds, мм/об.
В зависимости от обрабатываемого материала, вида обработки, диаметра инструмента рекомендуемое значение подачи можно выбрать из табл.1.
Глубина резания t , мм - расстояние от обрабатываемой до обработанной поверхности. Иначе говоря, глубина резания – это слой металла, срезаемый за один рабочий ход сверла.
При сверлении t определяют как половину диаметра сверла
tс= 0,5dс , (4.2)
где dс - диаметр сверла, мм.
При зенкеровании и развертывании
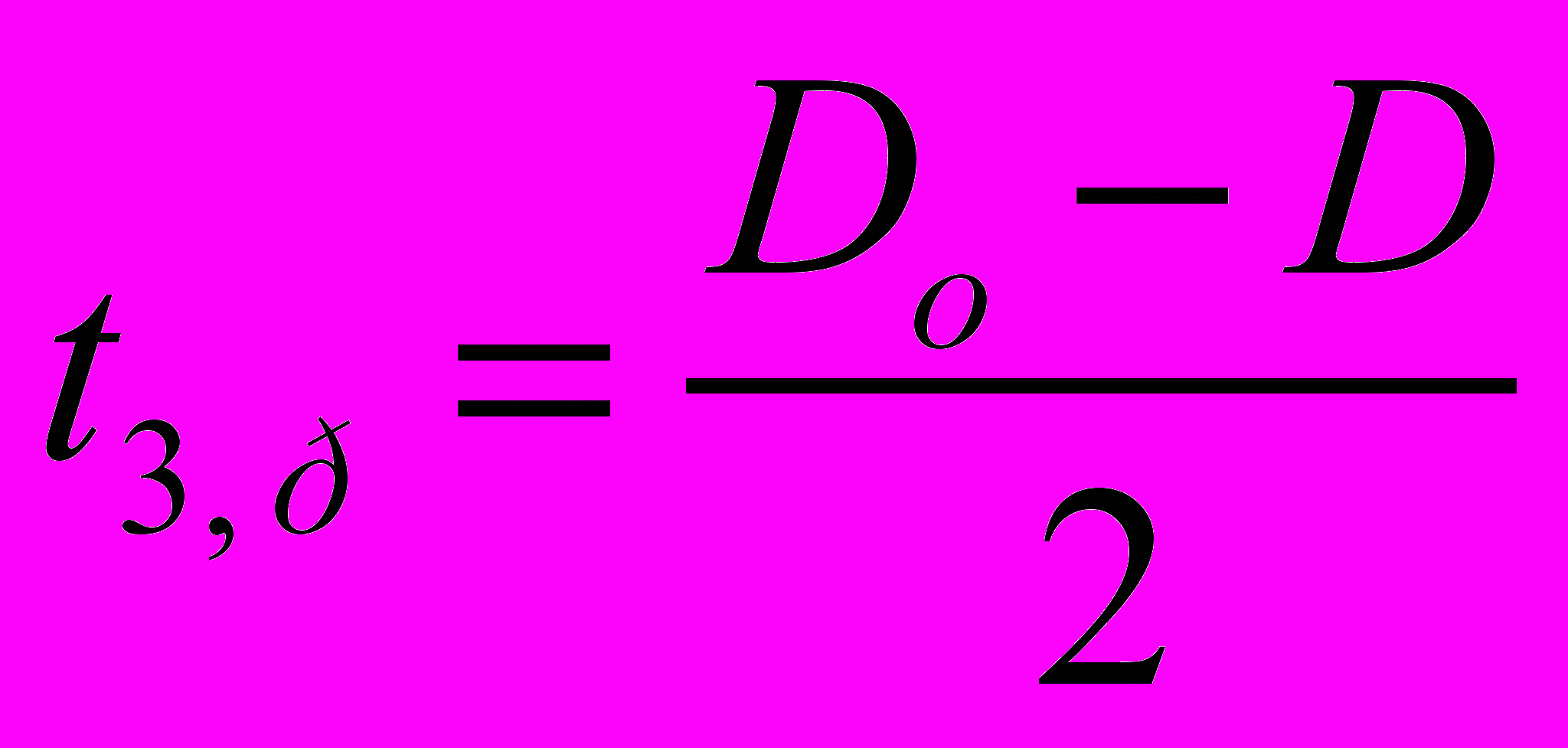
где Do и D - соответственно диаметры отверстия до и после обработки данным инструментом, мм.
При зенкеровании отверстий в отливках и поковках глубина резания назначается t3 = 3...5 мм и более.
При зенкеровании отверстия после сверления глубина резания ориентировочно принимается t3= 0,3.. .0,5 мм.
При развертывании глубина резания tр принимается следующая:
-при предварительном tр = 0,12…0,2 мм;
-при чистовом tр = 0,07...0,12 мм;
-при тонком tр = 0,05...0,08 мм
Таблица 1
Обрабатываемый материал | Вид обработки | Значение подачи при диаметрах инструмента Ds (мм/об) | |||
15-20 | 21-25 | 26-30 | 31-35 | ||
Сталь углеродистая конструкционная средней твердости | Сверление Зенкерование Развертывание предварительное Развертывание чистовое | 0,33-0,38 0,4-0,5 1,0 0,7 | 0,38-0,43 0,5-0,6 1,1 0,8 | 0,43-0,48 0,6-0,7 1,2 0,85 | 0,48-0,58 0,6-0,8 1,3 0,9 |
Серый чугун средней твердости | Сверление Зенкерование | 0,41-0,47 0,6-0,8 | 0,47-0,54 0,7-0,8 | 0,54-0,60 0,8-0,9 | 0,60-0,71 0,8-1,0 |
Цветные сплавы силумин, бронза (Ал, Бр) | Развертывание Развертывание точное | 2,6 1,8 | 2,7 1,9 | 3,1 2,1 | 3,2 2,2 |
5. ТЕХНОЛОГИЯ ОБРАБОТКИ ОТВЕРСТИЙ
НА СВЕРЛИЛЬНЫХ СТАНКАХ
Выбор технологии обработки отверстий зависит от вида заготовки, требований и точности, а также шероховатости.
Рекомендации для определения технологической последовательности обработки отверстия приведены в табл.2.
Таблица 2
Заготовка | Точность обработки отверстия | Последовательность технологических переходов |
Сплошной материал | 9...10 квалитет | сверление зенкование фаски зенкерование развертывание |
7...8 квалитет | сверление зенкование фаски зенкерование развертывание предварительное развертывание чистовое | |
Отверстие отлито или прошито | 9...10 квалитет | зенкерование предварительное зенкование фаски зенкерование развертывание |
6. ПОРЯДОК ВЫПОЛНЕНИЯ РАБОТЫ
1.Разработать технологический процесс обработки отверстия.
Варианты заданий:
1. d 20 - Н9 - в сплошном материале заготовки из стали Ст. 3.
2. d 20 - Н9 - в сплошном материале заготовки из чугуна СЧ 18.
3. d 20 - H7 - в сплошном материале заготовки из чугуна СЧ 18.
4. d 20 - Н8 - в поковке из стали 20 с прошитым отверстием.
2.Технологический процесс записать в табл.3.
Справочные данные:
1. Размеры сверл по ГОСТ 2092-77 от d 14 и выше через
0,25 мм.
2. Диаметр сверла, зенкера и развертки определять по зависимостям:
- диаметр развертки dp = D;
- диаметр зенкера d3 = dp- 2tp;
- диаметр сверла dc = d3- 2t3,
где tp и t3 - глубина резания соответственно при развертывании и зенкеровании, мм.
Таблица 3
№ п/п | Запись перехода | Эскиз перехода | Режущий инструмент и его размер | Режимы резания | |||
t, мм | Ds, мм/об | Dr, мм/мин | n, мин-1 | ||||
1 | | | | | | | |
2 | | | | | | | |
3 | | | | | | | |
4 | | | | | | | |
7. ТРЕБОВАНИЯ К ОФОРМЛЕНИЮ ОТЧЕТА
Отчет о выполненной лабораторной работе должен содержать:
1. Перечень основных типов сверлильных станков.
2. Перечень видов работ, выполняемых на сверлильных станках.
3. Название основных режущих инструментов, применяемых при выполнении работ на сверлильных станках.
4. Рисунок сверла с его основными элементами.
5. Технологический процесс, разработанный согласно варианту задания.
8. ТЕХНИКА БЕЗОПАСНОСТИ
Перед началом выполнения лабораторной работы студенты должны ознакомиться с правилами техники безопасности при работе на станках, одним из которых является наличие защитных устройств.
9. КОНТРОЛЬНЫЕ ВОПРОСЫ
1. Какие типы сверлильных станков вы знаете?
2. Назовите виды работ, выполняемых на сверлильных станках.
3. Какой режущий инструмент используется на сверлильных станках и в чем его особенность?
4. Какие виды движения сообщаются режущему инструменту при
сверлении, при нарезании резьбы метчиком?
5. По общему виду сверлильного станка расскажите об устройстве и назначении его основных элементов.
6. Расскажите об назначении основных частей сверла.
7. Исходя из чего назначаются режимы резания при обработке заготовок на сверлильных станках?
8. Какими характеристиками определяются режимы резания при
сверлении?
9. От чего зависит выбор скорости резания?
10.Что позволит обеспечить заданную точность и шероховатость при развертывании?
11. Что понимается под глубиной резания при сверлении?
12. Как выбирается глубина резания при зенкеровании и развертывании?
13. Приведите зависимости для определения величин t, Ds, Dr, n.
СПИСОК РЕКОМЕНДУЕМОЙ ЛИТЕРАТУРЫ
1. Технология конструкционных материалов /под ред. А.М. Дальского. - 5-изд., испр. - М.: Машиностроение, 2004. - 512с.
2. Справочник технолога-машиностроителя. в 2-х т. /под ред. А.М. Дальского, А.Г. Косиловой, Р.К. Мещерякова, А.Г. Суслова. – М.: Машиностроение, 2003. – Т.2. - 944с.
3. Справочник технолога-машиностроителя: в 2-х т./под ред. А.А. Малова. – М.: Машиностроение, 1972. – Т.2.
4. Материаловедение и технология металлов: учеб. для студентов вузов / Г.П. Фетисов [ и др.]. – М.: Высш. шк., 2001. – 637 с.
5. Обработка металлов резанием, металлорежущий инструмент и станки: учеб. для вузов / Б.И. Горбунов. – Киев: Машиностроение, 1981. – 287 с.
Технология конструкционных материалов. Обработка заготовок на сверлильных станках: методические указания к выполнению лабораторной работы № 10 для студентов очной формы обучения всех специальностей
ЕЛЕНА ВЛАДИМИРОВНА КОВАЛЕВА
Научный редактор С.В. Давыдов
Редактор издательства Л.И.Афонина
Компьютерный набор А.Г. Ковалев
Темплан 2009 г., п.172
Подписано в печать Формат 60х84 1/16. Бумага офсетная. Офсетная печать. Усл. печ.л. 0,81. Уч.-изд.л. 0,81. Тираж 40 экз. Заказ. Бесплатно.
Издательство Брянского государственного технического университета
241035, Брянск, бульвар 50-летия Октября, 7, БГТУ. 58-82-49.
Лаборатория оперативной полиграфии БГТУ, ул. Институтская, 16.