Схемы возможного импортозамещения контроллеров в системах асу тп компрессорных станций газопроводов
Вид материала | Исследование |
- Оптимизация режимов работы синхронных двигателей в узлах нагрузки систем электроснабжения, 305.03kb.
- Правила устройства и безопасной эксплуатации стационарных компрессорных установок,, 236.53kb.
- Правила устройства и безопасной эксплуатации стационарных компрессорных установок,, 254.12kb.
- Правила устройства и безопасной эксплуатации стационарных компрессорных установок,, 320.09kb.
- Х обвязок насосных и компрессорных станций, а также других объектов нефтяной и газовой, 34.46kb.
- Разработка и анализ требований к проектируемой интегрированной асу. Проектирование, 43.72kb.
- Государственная программа, 596.17kb.
- Лекция 4 Обеспечивающие подсистемы асу. Математическое, программное, лингвистическое,, 59.3kb.
- Правила устройства и безопасной эксплуатации стационарных компрессорных установок,, 365.13kb.
- Управления, 35.34kb.
Высокая надежность контроллера обеспечена элементной базой индустриального применения ведущих фирм мира, использованием SMD-технологии при изготовлении плат и встроенными средствами самоконтроля. |
Архитектура контроллера.
В контроллере осуществлено 3 уровня управления: нижний, средний и верхний.
Нижний уровень реализован на однокристальном 8 битном микропроцессоре с RISC архитектурой, обеспечивает управление модулем УСО и отвечает за сбор данных с объекта с одновременной полномасштабной диагностикой работоспособности модуля УСО; а также предоставляет возможность самостоятельного выполнения отдельных задач управления и регулирования.
Средний уровень реализован на 8 битном процессоре, совместимом по командам с 8051. На него возложены задачи Ж по вводу данных в верхний уровень с модулей УСО и вывода данных управления в модули УСО с предварительной обработкой информации и обработкой диагностики нижнего уровня.
Средний уровень является самодостаточным для решения большого круга задач по автоматизации объектов, так как включает в себя возможности логической обработки данных.
Верхний уровень реализован на кристалле высокой степени интеграции, так называемой «SOC» (Sistem on chip), совместимой с РС486, и, по сути, является центральным процессором контроллера (ЦП). ЦП решает задачи связанные со сложной обработкой данных, а также коммуникационные задачи.
Связь между уровнями реализована на технологии перепрограммируемых (без демонтажа) логических схем высокой степени интеграции. Такая технология позволяет повысить надежность как при изготовлении, так и при эксплуатации контроллера.
Функциональные возможности.
Основная функция ЭЛПК-2 заключается в непосредственном управлении технологическим оборудованием: сбор сигналов аналоговых и дискретных датчиков, обработка собранной информации по заданным алгоритмам, выдача управляющих воздействий на исполнительные механизмы, обеспечение обмена управляющей и технологической информацией между контроллером и пультом оператора или с центральным диспетчерским пультом.
В состав контроллера входят интеллектуальные модули УСО, управление каждым из которых осуществляет их собственный микропроцессор. Такое решение позволяет создавать на базе универсального модуля УСО целый ряд функциональных узлов: АЦП, ЦАП, частотомеров, узлов дискретных входов/выходов и т.п. Кроме того, наличие собственного микропроцессора позволяет при использовании пары дискретных модулей ввода и вывода реализовывать функцию интеллектуального мультиплексирования входных данных. Все модули УСО имеют гальваническую развязку входных/выходных сигналов (2500В).
Операционная система контроллера позволяет загружать пользовательские программы, создаваемые на технологическом языке высокого уровня.
Встроенные интерфейсы ЭЛПК-2 позволяют объединять контроллеры в локальную промышленную сеть ETHERNET.
Технические данные.
Центральный процессор: Процессор ввода вывода:
ALAN 400 (совместимый с РС486) DS5002FP( совместимый с 8051);
8 мбайт ОЗУ ,2 мбайта флэш диск, ДОС 6.22, Память программ 64 кбайт,
RS232 -3 канала, часы реального времени, память данных 64 кбайт; два
2-х направленный параллельный порт, гальванически изолированных
порт ETHERNET, видеоконтроллер канала
RS-232, часы реального времени.
Дискретные входы: Дискретные выходы с защитой:
=24В / I = Зmа до 256 каналов =40В / I = 2а до 256 каналов,
(с мултиплексированием - до 740). =220В / I = 0,7а до 128 каналов.
= и ~ от 5В до 20В/1 = Зmа -до 128 каналов ~220В / I = 2а до 128 каналов.
Аналоговые входы: Аналоговые выходы:
Разрешение 16 разрядов, Разрешение 16 разрядов:
точность преобразования ±0,05% I = О..5та до 128 каналов.
I = О..20mа до 128 каналов. I = 4..20та до 128 каналов.
V = 0..±10B до 128 каналов V = 0..+ 5В до 1 28 каналов.
Общие характеристики.
Питание.
Питание контроллера осуществляется постоянным напряжением 12В или 24В.
Возможно подключение резервного питания напряжением 12В или 24В.
Потребляемая мощность не более 15Вт.
Условия эксплуатации.
Диапазон рабочих температур: от -20°С до +60°С
Относительная влажность воздуха от 40% до 95% при Т=30°С
Вибрации частотой до 25Гц амплитудой < 0.1мм.
Конструктивное исполнение
Конструкция контроллера позволяет встраивать его в монтажные боксы или шкафы. Имеются три модификации ЭЛПК-2: на 4, 8 и 16 модулей УСО.
Габаритные размеры:
ЭЛПК-2-4 220x130x90 мм (макс, кол-во входов: дискр. 64 (185 с мудьтипликсированием)) или аналоговых 32
ЭЛ ПК-2-8 345x130x90 мм (макс, кол-во входов: дискр. 128 (370 с мульт.)) или аналог. 64
ЭЛПК-2-16 345x260x90 мм. (макс.кол-во входов: дискр. 256 (740 с мульт.)) или аналог. 128
Наиболее показательным является опыт импортозамещения контроллеров в распределенных САУ нефтеперекачивающих станций (НПС) в системе ОАО «Транснефть».
Функциональные задачи САУ НПС очень близки к задачам АСУ ТП газокомпрессорных станций:
- управление технологическим оборудованием (магистральные и подпорные насосные агрегаты, станционные задвижки, системы вентиляции и т.д.);
- регулирование давления на входе/выходе НПС;
- управление и контроль вспомогательных систем и вспомогательных сооружений;
- контроль и сигнализация пожара, автоматическое пожаротушение;
- отображение информации и документирование;
- прием и передача информации в систему телемеханики.
Некоторые российские фирмы уже имеют опыт в области проектирования, изготовления и наладки распределенных САУ нефтеперекачивающих станций (НПС).
Рассмотрим состав, функции, структуру и функционирование типовой системы автоматизации на базе отечественных микропроцессорных контроллеров с открытой внутренней архитектурой (на примере ЗАО «Эмикон» с производимыми им отечественными контроллерами) с точки зрения совпадения задач и «адаптации» к требованиям АСУ ТП газоперекачивающих станций.
Ниже приведена концепция построения распределенных систем автоматизации нефтеперекачивающих станций на базе центральных контроллеров с открытой внутренней архитектурой и контроллеров ввода/вывода на базе модулей ЭМИКОН сер. DCS-2000.
Микропроцессорные системы автоматизации нефтеперекачивающих станций (СА НПС) предназначены для управления технологическим оборудованием (магистральные и подпорные агрегаты, задвижки, системы вентиляции и т.д.), а также для обеспечения различных защит при отклонении параметров ТП или режима работы технологического оборудования от нормы (например, загазованность, повышение вибрации подшипников и т.п.)
СА НПС выполняет следующие функции:
- анализ режимов технологического оборудования;
- контроль технологических параметров, режимов перекачки, готовности магистральных и подпорных насосных агрегатов к запуску;
- обработка предельных значений параметров по агрегату;
- управление (открытие, закрытие, стоп) и контроль станционных и агрегатных задвижек;
- управление (программный и кнопочный пуск, программное и кнопочное отключение) и контроль магистральных и подпорных насосных агрегатов;
- задание установок регулирования;
- регулирование давления на входе/выходе НПС;
- управление вспомогательными системами;
- управление (пуск, отключение) и контроль агрегатов вспомогательной системы и вспомогательных сооружений;
- контроль исправности РП-2 (напряжения на вводах 6 кВ);
- контроль и сигнализация пожара;
- автоматическое пожаротушение;
- обработка измерений и контроль достоверности измеряемых параметров;
- отображение информации и документирование, формирование кадров отображения ТП, табличных форм представления информации, форм печати оперативных сообщений, архивных данных, отчетных документов;
- прием и передача сигналов в систему телемеханики.
Состав системы.
Нижний уровень включает датчики и вторичные преобразователи, а также показывающие приборы и органы управления, устанавливаемые на приборных щитах и отдельно по месту.
Средний уровень обеспечивает сбор информации от датчиков и вторичных преобразователей, ее передачу в центральный контроллер верхнего уровня, а также получение выходной информации от центрального контроллера и формирование управляющих воздействий на ИМ СА НПС. В качестве устройств среднего уровня используются контроллеры ввода/вывода на базе микропроцессорных модулей ЭМИКОН семейства DCS-2000, имеющих в своем составе встроенные барьеры искрозащиты и блоки питания первичных датчиков.
Семейство модулей DCS-2000 предназначено для использования в рассредоточенных системах автоматизации общего назначения, а также для автоматизации объектов, находящихся во взрывоопасных зонах.
Отличительной особенностью модулей DCS-2000 является наличие встроенных барьеров искробезопасности, а также искрозащищенных блоков питания. Это позволяет подключать непосредственно к модулям такие устройства, как датчики давления, термосопротивления, пассивные дискретные датчики (например, реле давления, напора, датчики уровня и
ДР)
В связи с тем, что в контроллере не требуется использование дополнительных устройств в виде внешних барьеров и источников питания, схема подключения датчиков существенно упрощается и фактически может быть представлена в виде таблицы сигналов.
Все МСО семейства DCS-2000 имеют гальванически развязанный интерфейс RS-485 (протокол ModbusRTU), скорость передачи до 115,2 Кбит/с.
В составе DCS-2000 имеется модуль CPU-11, который имеет ОС-188 (на базе RMX 86) и тестовый язык программирования CONT.
Связь между модулем центрального процессора и модулями связи с объектом (МСО) контроллера ввода/вывода осуществляется по последовательному интерфейсу (RS-485, протокол ModbusRTU, скорость передачи до 115,2 Кбит/с). К одному модулю центрального процессора может быть подключено до 64 МСО.
Связь между контроллерами ввода/вывода среднего уровня и центральным контроллером верхнего уровня осуществляется по резервированному последовательному интерфейсу (RS-485, протокол ModbusRTU, скорость передачи до 921,6 Кбит/с).
Модуль центрального процессора, а также источники питания контроллера ввода/вывода, как правило, выполняются по схеме с "горячим" резервированием, что существенно увеличивает надежность контроллера и всей системы в целом.
МСО, совмещенные с объектовыми клеммниками, образуют блоки информационные (БИ), предназначенные только для сбора информации и блоки информационно-управляющие (БИУ), предназначенные как для сбора информации, так и для формирования управляющих воздействий. БИ и БИУ могут располагаться как в одном электрошкафу с модулем центрального процессора контроллера ввода/вывода, так и в других электрошкафах и даже в других помещениях.
Максимальное удаление МСО от модуля центрального процессора - до 5 км. Использование малоканальных МСО (4... 8 каналов в одном модуле) позволяет существенно облегчить обслуживание системы, осуществлять поиск и замену неисправных модулей (в режиме "горячей" замены - hot swap) без остановки НПС.
Верхний уровень обеспечивает:
- логическую обработку входной информации, поступающей от среднего уровня, в соответствии с заданным алгоритмом управления;
- формирование управляющих команд для контроллеров ввода/вывода;
- мониторинг ТП на PC-совместимых станциях оператора;
- архивацию событий, поступающих с объекта и действий оператора.
При разработке микропроцессорной СА НПС основным критерием являлся выбор центрального контроллера с открытой внутренней архитектурой. Для таких типов контроллеров характерно: удобство программирования, наличие большого количества средств разработки прикладных программ от различных производителей и производителей аппаратных средств, которые полностью конструктивно и функционально совместимы друг с другом.
Аппаратно верхний уровень был реализован на базе PC-совместимого контроллера, включенного по схеме с "горячим" резервированием. В составе центрального контроллера, кроме модуля центрального процессора, были установлены сетевые модули, поддерживающие интерфейс RS-485, протокол ModbusRTU, скорость передачи до 921,6 Кбит/с, а также интерфейс Ethernet (протокол Modbus); тип ОС - QNX. Система программирования контроллера - ISaGRAF.
Центральный контроллер, как правило, располагается в операторной магистральных насосных агрегатов (МНА). Там же располагается одна или две операторские станции, подключенные к центральному контроллеру по интерфейсу Ethernet (протокол Modbus). В случае, когда одна из операторских станций располагается в местном ДП (МДП), связь между этой станцией и центральным контроллером осуществляется по интерфейсу RS-485. Двухканальные сетевые модули с интерфейсом RS-485 поддерживают две или более зарезервированные полевые шины.
К первой полевой шине (протокол Modbus) подключены контроллеры ввода/вывода, расположенные в операторной МНА.
Ко второй полевой шине подключены контроллеры ввода/вывода, расположенные в других помещениях, например, в операторной подпорной насосной станции (ПНС). При большом территориальном разбросе СА НПС могут быть организованы дополнительные полевые шины.
Данная конфигурация обеспечивает высокую надежность и живучесть всей системы автоматики НПС и существенно упрощает поиск и устранение неисправностей.
На базе модулей DCS-2000 были разработаны и сданы в промышленную эксплуатацию более 10 систем автоматизации НПС на трубопроводах АК "Транснефть".
Приведенная структурная схема СА в полной мере была использована и при автоматизации ПС на нефтепродуктопроводах.
Для сравнения с зарубежными аналогами приведем краткие характеристики модулей серии DCS-2000
Семейство модулей DCS-2000 содержит: CPU-11 - модуль центрального процессора; С1-01 - модуль преобразования интерфейсов; А1-11 - модуль аналогового ввода (сопряжения с термосопротивлениями); А1-12 - модуль аналогового ввода (токовые сигналы 4...20 или 0..,5 мА); CTF-11 - модуль сопряжения с тензодатчиками; D1-11 - модуль дискретного ввода; DIO -11 - модуль дискретного ввода/вывода; АО-11 -модуль аналогового вывода (токовые сигналы 0...20 мА).
Все модули ввода аналоговых и дискретных сигналов имеют входные цепи искрозащищенного исполнения (Exib11c). Модули выполнены в виде многослойных печатных плат размером 77x85 мм, установленных в пластмассовых корпусах с габаритными размерами 114x102x25 мм. Масса - не более 0,15 кг. Модули имеют элементы крепления на стандартный DIN-рельстипа DIN3 (TS35/F6) или DIN (TS32/F6). Питание осуществляется от стабилизированного источника напряжением 24 В.
Рабочие условия эксплуатации модулей.
Температура окружающего воздуха
(без конденсации влаги), °С ........................................ -25-85
Относительная влажность воздуха
(при температуре 25 °С), % ............................................ 85
Атмосферное давление, кПа ..................................... 84-107
Все модули УСО семейства DCO-2000 имеют идентичные системную и интерфейсную части и цоколевку системного разъема ХТ1.
Интерфейсная часть выполнена на основе микросхемы AD485, имеет свой источник питания и гальванически изолирована от других схем модуля. Напряжение изоляции составляет не менее 500 В.
В качестве управляющего устройства используется микропроцессор AT90S8535, в состав которого входят: память программ - 8 Кбайт; ОЗУ - 512 байт; энергонезависимая память - 512 байт; 8-канальный 10-разрядный АЦП; последовательный порт; 3 таймера.
Все цепи модулей семейства DCS-2000 гальванически изолированы от внешнего источника питания 24 В. Напряжение изоляции составляет не менее 500 В. Поскольку модули одной подсистемы связаны только по локальной сети конструктивно, они могут располагаться как в одном электрошкафу, так и в разных электрошкафах, в том числе и в разных помещениях.
Модуль центрального процессорного устройства CPU-11 является основным функциональным узлом контроллера и предназначен для работы в семействе DCS-2000.
Основные технические характеристики модуля CPU-11.
Тип процессора ...........................................N80C188EB20
Тактовая частота процессора, МГц ............................... 20
Объем Flash-памяти, Кбайт .......................................... 512
Объем оперативной памяти, Кбайт ............................. 128
Количество уровней прерывания .................................... 7
Количество 16-разрядных таймеров ............................... 3
Количество низкоскоростных последовательных каналов.............................................................…… 1 -RS-232
(протокол Modbus, скорость до 1 15200 бод).....… 1 -TTL
Количество высокоскоростных последовательных
каналов (протокол SDLC, скорость до 576000 бод),
TTL.........................................……………………………. 2
Ток потребления от системного источника 24 В,
не более, мА ....................................…………………. 100
На переднем торце пластмассового корпуса модуля расположены 8 светодиодов индикации режимов работы и состояния последовательных интерфейсов. Кроме того, модуль имеет:
- выходной дискретный сигнал индикации исправности -24 В, 50 мА, изоляция 2500 В;
- выходной дискретный сигнал общего назначения -24 В, 50 мА, изоляция 2500 В;
- входной сигнал блокировки -24 В, 5 мА, изоляция 2500 В.
Модуль С1-01 предназначен для преобразования последовательных данных модуля CPU-11 в виде сигналов TTL-уровня в сигналы интерфейса RS-485 с гальванической развязкой цепей. На переднем торце пластмассового корпуса модуля расположены 4 светодиода индикации состояния последовательных интерфейсов.
Основные технические характеристики модуля С1-01:
Количество низкоскоростных преобразователей
последовательных каналов (TTL/RS-485, скорость
до 1 15200 бод, изоляция 2500В) ...................……………….. 2
Количество высокоскоростных преобразователей последовательных каналов (TTL/RS -485, скорость
до 2500000 бод, изоляция 2500 В).................................……. 2
Ток потребления от системного источника
24 В мА, не более........................................…………………… 50
Модуль А1-11 предназначен для подключения к нему по трехпроводной схеме термометров сопротивления типа ТСМ (ТСП)-50 или ТСМ (ТСП)-ЮО и преобразования полученного с них входного напряжения в десятиразрядный цифровой код. Искробезопасность цепей модуля достигается за счет ограничения тока защитными резисторами и соответствующей конструкцией модуля. Эти резисторы конструктивно выделены в отдельную зону и для исключения их повреждения залиты специальным компаундом.
Технические характеристики и параметры модуля
Количество каналов ввода .............................................…….. 4
Диапазон измеряемого сопротивления, Ом 40...90 или 80... 180
(выбирается джампером на плате)
Время коммутации канала мкс, не более ................……. …1000
Время преобразования мкс, не более ........................…. ….180
Разрядность аналого-цифрового
преобразования, бит.....................................................….. …..10
Основная погрешность
преобразования, %, не более .......................................…….. 0,3
Дополнительная температурная
погрешность, %/°С ....................................................……… 0,01
Величина тока встроенного источника, мА .......……… 2 или 4
Диапазон измеряемых модулем температур составляет -45...185 °С при использовании медных термометров сопротивлений и -50...210 °С для платиновых.
Модуль имеет 2 постоянные времени фильтра входного сигнала (выбирается джампером на плате) - одну стандартную, вторая предназначена при использовании датчика в условиях высокого уровня помех, например, когда термометр сопротивления установлен внутри мощного электродвигателя для измерения температуры обмотки.
ПО модуля обеспечивает тестирование узлов модуля, аналого-цифровое преобразование входного сигнала, фильтрацию результата измерения, индикацию работоспособности модуля и информационный обмен с устройствами верхнего уровня.
Модуль А1-12 предназначен для подключения к нему датчиков с токовым выходом и преобразования измеренного тока в десятиразрядный цифровой код.
Датчики могут быть как активными (имеющие собственный источник питания), так и пассивными, использующими встроенный в модуль источник питания. По виду взрывозащиты, уровню искробезопасной электрической цепи и подгруппе взрывозащищенного электрооборудования модуль полностью идентичен А1-11.
Технические характеристики и параметры модуля:
Число каналов ввода .......................................................…….4
Диапазон измерения тока, мА ...............…………..4...20 или 0...5
Время, мкс, не более коммутации канала............………… 1000
преобразования .......................................................…………180
Разрядность аналого-цифрового преобразования, бит...... 10
Основная погрешность преобразования, %, не более.........0,3
Дополнительная температурная погрешность, %/°С ……..0,01
Величина входного сопротивления, Ом ....................…….. 100
Для сохранения свойств полностью дифференциального входа каждый канал имеет свой изолированный источник питания (DC/DC конвертер) пассивного датчика.
Модуль сопряжения с тензодатчиками CTF-11 предназначен для работы в составе распределенных систем управления для подключения к нему по шестипроводной схеме тензодатчиков мостового типа, например, тензорезисторных датчиков силы типа Т2 и преобразования полученного входного напряжения в 10-, 12- или 16-разрядный цифровой код. При десятиразрядном коде на выходе обеспечивается минимальное время преобразования, при 16 -максимальная точность преобразования.
Основные технические характеристики модуля CTF-11:
Диапазон измеряемого напряжения, мВ ................. 0...20
Защита от подачи напряжения питания обратной
полярности ..........................................……………..Имеется
Количество каналов ввода ................................................ 1
Номинальное напряжение питания датчиков, В ........……..10
Время преобразования, мс, не более:
10-разрядный код.......................................................... ………8
12-разрядный код ......................................................………..35
16-разрядный код ....................................................………….350
Основная погрешность
преобразования, %, не более ......................................….……0,1
Дополнительная температурная
погрешность, %/°С ..................................................………….0,005
Гальваническая развязка между внешним
стабилизированным источником питания
24 В и питанием модуля. В, не менее ..................................500 Интерфейс..............................................................……….RS-485
Протокол...............................................................………..Modbus
Скорость передачи, бод ...................................………До 1 15200
Модуль DI-11 предназначен для ввода дискретных сигналов с напряжением 24 В постоянного тока. На переднем торце пластмассового корпуса модуля расположены десять светодиодов. Светодиоды INI...IN8 индицируют состояние входных сигналов. Светодиоды светятся, когда на входе модуля устанавливается низкий активный уровень сигнала (состояние "Включено").
Светодиод RXD индицирует прием информации из ЛВС;
светодиод - TXD передачу информации из модуля в ЛВС.
Технические характеристики и параметры модуля DI-11:
Число каналов ввода ......................................................... 8
Напряжение встроенного стабилизированного
источника питания постоянного тока, В .............……….. 24
Входной ток, мА:
номинальный, мА.......................................................…….. 5
максимальный, мА.....................................................…….. 6
Задержка входного сигнала, мс, не более ...................…20
Напряжение оптоэлектрической изоляции, В .......……1500
Модуль DIO-11 предназначен для ввода/вывода дискретных сигналов напряжением 24 В постоянного тока. Электрические цепи соединения модуля с датчиками дискретного ввода являются искробезопасными. Цепи дискретного вывода, не являющиеся искробезопасными, выведены на отдельный пользовательский клеммный соединитель ХТЗ.
На торце пластмассового корпуса модуля расположены 7 светодиодов. Светодиоды IN1...IN4 индицируют состояние входных сигналов. Свечение этих светодиодов означает, что на входе модуля установился низкий активный уровень сигнала. Светодиод RXD индицирует прием информации из ЛВС, светодиод TXD - передачу информации из модуля в ЛВС. Свечение светодиода RUN свидетельствует о том, что модуль находится во включенном, рабочем состоянии.
Технические характеристики и параметры модуля DIO-11:
Число каналов ввода ......................................................... 4
Напряжение встроенного стабилизированного
источника питания постоянного тока, UBC, В .............… 24
Входной ток, мА:
номинальный, мА.......................................................……. 6
максимальный, мА.....................................................……. 8
Задержка входного сигнала мс, не более ......................20
Количество каналов вывода:............................................. 4
Напряжение внешнего источника питания
постоянного тока для дискретных выходов,
UBH, В ..................................................……………….24±20%
Максимальный ток нагрузки одного выхода, А .......…. 0,1
Максимальный ток утечки выхода в
состоянии "Выключено",мА ..........................................….. 1
Напряжение опто-электрической изоляции выхода, В …1500
Модуль АО-11 предназначен для преобразования 12-ти разрядного цифрового кода в аналоговые токовые сигналы в диапазоне 0... 20 мА. На торце пластмассового корпуса модуля расположены 3 светодиода. Светодиод RXD индицирует прием информации из ЛВС, светодиод TXD - передачу информации, из модуля в ЛВС. Свечение светодиода RUN свидетельствует о том, что модуль находится во включенном, рабочем состоянии.
Технические характеристики и параметры модуля АО-11:
Число каналов вывода ....................................................…. 2
Шкала выходного тока, мА ....................................……. ..0...20
Время преобразования мкс, не более ........................….. 100
Разрядность цифро-аналогового
преобразования, бит.....................................................…… 12
Основная погрешность преобразования, %, не
более.........................................................................………. 0,2
Дополнительная температурная погрешность, %/ °С….0,005
Максимальная величина сопротивления
нагрузки, Ом................................................................…….. 400
Защита центробежного компрессора от помпажа
Если раньше предлагалось только антипомпажное регулирование с помощью байпасного клапана, то теперь реализуется двойная система, включающая в себя как антипомпажное регулирование (АПР), так и сигнализатор помпажа (СП).
СП работает в дежурном режиме и при отказе АПР, его отключении, изменении состава газа и т.п., реагирует на начинающийся помпаж и через несколько миллисекунд выдает сигнал на принудительное открытие байпасного клапана.
До недавнего времени сказывалось отсутствие надежных и быстродействующих электронных блоков. После получения доступа к современным зарубежным компонентам и технологиям, в ЗАО «Эмикон» был создан специализированный контроллер защиты от помпажа РОМРС1.
Контроллер помпажа РОМРС1 представляет собой современное микропроцессорное устройство, полностью выполненное на зарубежной элементной базе (например, процессор типа Т80С188ЕВ20 фирмы «Intel») и специально спроектированное для эффективного решения всего комплекса проблем, связанных с защитой от помпажа центробежных компрессоров.
Высокие эксплуатационные характеристики контроллера обеспечиваются также оригинальной архитектурой и применением новейших технологий при изготовлении печатных плат и монтаже.
Высокое системное быстродействие, позволяющее вести обсчет параметров процесса с периодом 10 мс в совокупности с высокоэффективными алгоритмами, разработанными на основе опыта проектирования и внедрения центробежных компрессоров, а также низкая стоимость по сравнению с зарубежными аналогами, делает контроллер РОМРС1 уникальным по эффективности и соотношению «цена/ качество» средством защиты от помпажа. Размеры блока: высота-205, ширина- 265, глубина -135.
Перед установкой контроллера помпажа проводятся предварительные работы, связанные с построением реальной линии помпажа и адаптируются алгоритмы работы контроллера с учетом всех особенностей компрессора и технологии. Работы проводились с применением специального комплекса оборудования по исследованию помпажа (с использованием компьютера типа «Notebook»).
Установка антипомпажного контроллера не требует больших дополнительных капиталовложений, потому что в большинстве случаев существующая система автоматизации компрессора уже имеет необходимые датчики с электрическим выходным сигналом и антипомпажный (регулирующий или отсечной) клапан.
Приведенные характеристики аппаратно-технических средств российских производителей позволяют констатировать, что отечественные средства автоматизации не уступают импортным.
Российские аппаратно-технические средства пригодны для замещения западного оборудования, а их технические характеристики отвечают самым строгим требованиям, предъявляемым к автоматизации в газовой отрасли, а в части взрыво-пожаробезопасности даже превосходят их.
По оценкам экспертов, проведенное импортозамещение систем автоматизации нефтеперекачивающих станций на объектах АК «Транснефть» привело к уменьшению стоимости систем автоматизации в 2,5 раза по сравнению с импортными аналогами.
Выбор контроллера
Наличие различных ПЛК ставит вопрос: как выбрать из этого обилия необходимый именно вам контроллер? Требуется не превосходство одной какой-то характеристики, а некая интегральная оценка, позволяющая сравнить ПЛК по совокупности характеристик и свойств.
При исследовании рынка выяснилось, что многие фирмы не приводят данные по надежности (MTBF и MTTR). Однако там, где эти параметры есть, разброс идет на порядки.
Один из самых важных параметров ПЛК – быстродействие - в каталогах фирм указывается в совершенно разных вариантах. Могут фигурировать время выполнения бинарных команд, время опроса 1К дискретных входов, время выполнения смешанных команд и т.д.
Цены - самый интригующий фактор. Кто-то приводит их в американских долларах, кто-то в немецких марках, при этом курс иностранной валюты очень разный и всегда завышенный. На это к тому же накладываются разные форматы цен: FOB, DDP и т.д.
Спектр продукции, предлагаемой сегодня, чрезвычайно широк (см. табл. №4).
Как видно из таблицы №4, контроллеры имеют равные функциональные возможности, близкие технические и эксплуатационные характеристики и даже почти одинаковые размеры. В такой ситуации необходимо определить критерии оценки и выбора ПЛК, удовлетворяющего поставленной задаче.
Учитывая специфику устройств, критерии оценки можно разделить на три группы (рис.№6):
- технические характеристики;
- эксплуатационные характеристики;
- потребительские свойства.
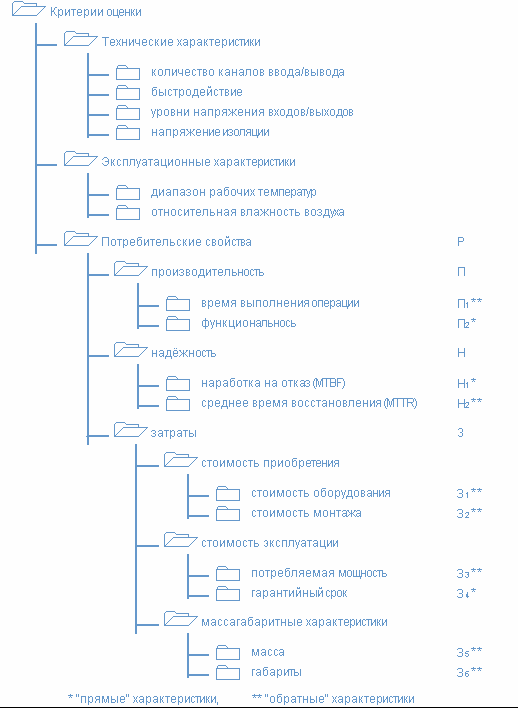
Рис. № 6
При этом критериями выбора следует считать потребительские свойства, т.е. соотношение показателей затраты/производительность/надежность, а технические и эксплуатационные характеристики ограничениями для процедуры выбора.
Кроме того, необходимо разделить характеристики на прямые (для которых положительным результатом является её увеличение) и обратные (для которых положительным результатом является её уменьшение).
Так как характеристики между собой конфликтны, т.е. улучшение одной характеристики почти всегда приводит к ухудшению другой, необходимо для каждой характеристики Ki определить весовой коэффициент ai, учитывающий степень влияния данной характеристики на полезность устройства.
(Терминология и состав критериев оценки ПЛК приведены в соответствии с основными положениями квалиметрии и стандартами качества (ГОСТ 15467-79).)
Выбор аппаратуры производился в четыре этапа:
- определение соответствия технических характеристик предъявленным требованиям;
- определение соответствия эксплуатационных характеристик предъявленным требованиям;
- оценка потребительских свойств выбираемой аппаратуры;
- ранжирование изделий.
На первом этапе каждая техническая характеристика анализируемого изделия сравнивалась с предъявленными к проектируемой системе требованиями, и если данная характеристика не удовлетворяет этим требованиям, изделие снимается с рассмотрения.
Такой же анализ проводится на втором этапе с эксплуатационными характеристиками, и только если технические и эксплуатационные характеристики соответствуют поставленной задаче и предъявленным требованиям, проводится оценка потребительских свойств ПЛК.
Для этого использовался аддитивный метод оценки, когда суммарная оценка каждого свойства вычисляется по следующей формуле:
г
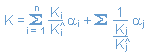
де:
- Ki, Kj, - прямая и обратная характеристики выбираемого изделия;
- Ki, Kj - соответствующие характеристики аналога;
- ai , aj - весовые коэффициенты характеристик;
- n, m - количество прямых и обратных характеристик.
Деление на характеристики аналога необходимо для приведения всех свойств к относительным величинам.
Определение весовых коэффициентов для характеристик ПЛК является одной из самых ответственных задач, т.к. именно от их правильной величины зависит достоверность результатов анализа. Для нахождения усредненной оценки каждого коэффициента была выбрана следующая методика экспертных оценок и программа их расчета.
Составлялась матрица эксперты-коэффициенты, в которой проставляются полученные от каждого эксперта оценки коэффициентов по шкале от 0 до 10 (см.табл. №7).
Т
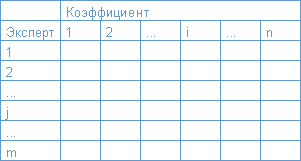
аблица №7
Рассчитывалась относительная значимость (Wij) всех коэффициентов в отдельности для каждого эксперта. С этой целью оценки, полученные от каждого эксперта, суммировались (по горизонтали), а затем нормируются:
п

ри j = const.
В

ычислялась усредненная оценка, данная всеми экспертами каждому коэффициенту. Для этого нормированные оценки, полученные в предыдущем шаге, суммировались (по вертикали), а затем рассчитывалось среднее арифметическое для каждого коэффициента:
при i = const.
Для расчетов использовалась программа расчета весовых коэффициентов написанная с использованием СУБД Microsoft Access 97.
Программа содержит 3 таблицы, 10 запросов, 7 форм и 3 отчета.
На рис.№ 7 приведен алгоритм этой программы.
- Требования к входным данным следующие:
каждый оцениваемый параметр идентифицируется наименованием (до 45 символов);
- оценки, выставляемые экспертами, представляются целыми числами от 1 до 10 включительно;
Р
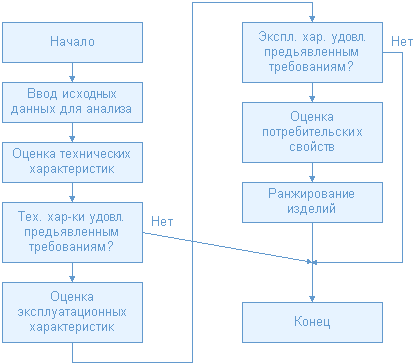
ис. №7
В результате анализа потребительских свойств аппаратуры составлялась матрица изделия-потребительские свойства, которая содержали исходные данные для выбора ПЛК.
Ранжирование изделий, т.е. расположение их в порядке возрастания (или убывания) соотношения показателей затраты/производительность/надежность проводилось по формуле:
Р = П+Н+З
Проведенный анализ не претендует на полноту охвата всех показателей в основном по субъективного причинам. Однако даже в таком виде можно сделать вывод о том, что данная методика позволила провести оценку и принять решение о выборе ПЛК с достаточно высокой степенью достоверности.
По результатам оценки был выбран ПЛК фирмы «Эмикон»