Схемы возможного импортозамещения контроллеров в системах асу тп компрессорных станций газопроводов
Вид материала | Исследование |
1. Анализ действующих схем использования контроллеров в системах АСУ ТП компрессорных станций газопроводов. Диспетчерский комплекс управления КС Программное обеспечение (ПО) системы автоматизации |
- Оптимизация режимов работы синхронных двигателей в узлах нагрузки систем электроснабжения, 305.03kb.
- Правила устройства и безопасной эксплуатации стационарных компрессорных установок,, 236.53kb.
- Правила устройства и безопасной эксплуатации стационарных компрессорных установок,, 254.12kb.
- Правила устройства и безопасной эксплуатации стационарных компрессорных установок,, 320.09kb.
- Х обвязок насосных и компрессорных станций, а также других объектов нефтяной и газовой, 34.46kb.
- Разработка и анализ требований к проектируемой интегрированной асу. Проектирование, 43.72kb.
- Государственная программа, 596.17kb.
- Лекция 4 Обеспечивающие подсистемы асу. Математическое, программное, лингвистическое,, 59.3kb.
- Правила устройства и безопасной эксплуатации стационарных компрессорных установок,, 365.13kb.
- Управления, 35.34kb.
1. Анализ действующих схем использования контроллеров в системах АСУ ТП компрессорных станций
газопроводов.
1.1. Компрессорная станция газопровода, как объект автоматизации.
Компрессорная станция (КС) - это сложный комплекс технологических объектов.
Основные объекты автоматизации:
- компрессорный цех, включая 3-10 газоперекачивающих агрегата (ГПА);
- общестанционные краны узла подключения;
- охранные краны компрессорной станции;
- система электроснабжения (ЗРУ);
- агрегаты охлаждения газа (АВО);
- установки очистки газа;
- установка подготовки импульсного газа;
- склад горюче-смазочных материалов (ГСМ).
Функциональными задачами АСУ ТП газокомпрессорных станций являются:
- управление технологическим оборудованием (магистральные и подпорные насосные агрегаты, станционные задвижки, системы вентиляции и т.д.);
- регулирование давления на входе/выходе перекачивающих систем;
- управление и контроль вспомогательных систем и вспомогательных сооружений;
- контроль и сигнализация пожара, автоматическое пожаротушение;
- отображение информации и документирование;
- прием и передача информации в систему телемеханики.
Автоматизированная система управления компрессорной станции строится как централизованная система управления с децентрализацией управления отдельными технологическими объектами на уровне Станций Локальных Технологических (СЛТ). Система состоит из следующих функциональных компонентов:
- диспетчерский комплекс;
- локальные станции технологические;
- коммуникационные средства, каналы связи и локальная вычислительная сеть.
Система обеспечивает выполнение следующих задач:
1) подача установленного объема газа в магистральный газопровод (бесперебойность и производительность);
2) поддержание требуемых параметров газа (давление, температура), подаваемого в газопровод;
3) обеспечение высокой эксплуатационной надежности КС в нормальных и аварийных ситуациях;
4) контроль и управление технологическим оборудованием;
5) сбор и передача технологической информации на верхний уровень управления и дистанционное управление отдельными технологическими системами с верхнего уровня.
Диспетчерский комплекс управления КС
На диспетчерский комплекс возлагается выполнение следующих задач:
- сбор параметров технологического процесса;
- визуальная информация и сопровождение ее звуковыми сигналами;
- привязка технологических событий к реальному времени;
- дистанционное управление охранными кранами, пуском и остановом агрегатов;
- ведение баз данных;
- сбор данных по учету газо- и энергопотребления;
- подготовка справочных и учетных документов;
- ведение и обслуживание архива ретроспективных данных о ходе процесса;
- печать сводок и рапортов;
- выполнение расчетов объемной производительности агрегатов, удаленности от зоны помпажа и оптимизационных расчетов.
Состав диспетчерского комплекса:
- пульт диспетчера (ДП);
- пульт инженера (ИП).
ДП является автоматизированным рабочим местом (АРМ) диспетчера компрессорного цеха компрессорной станции. Он содержит комплекс технических средств, в который входят:
- три ПЭВМ специального исполнения, используемые в качестве рабочих мест диспетчера;
- микро-ЭВМ промышленного исполнения, используемая в качестве коммуникационного сервера, который обеспечивает связь с СЛТ;
- коммуникационные устройства:
- многоканальные разделители интерфейса; |
- модемы и преобразователи интерфейса;
- концентратор локальной сети Ethernet-HUB;
- коммутационная панель
- источники бесперебойного питания (ИБП).
СЛТ - станция локальная технологическая
СЛТ обеспечивает выполнение задач сбора и предварительной обработки данных, логического управления, передачу данных на ДП, а также прием командных сообщений от ДП и управление исполнительными механизмами.
СЛТ выполняются на базе универсальных программируемых контроллеров, размещаемых в типовых конструктивах - шкафах. В одном шкафу может быть размещено до шести контроллеров.
Контроллер реализован как проектно-компонуемый программно-технический комплекс, позволяющий создавать простые (одноуровневые) и сложные (многоуровневые) системы автоматизации.
Проектная компоновка контроллера состоит в создании базы данных объекта автоматизации на основе описания таблицы подключения входных и выходных сигналов, составляемой при пpoектировании системы автоматизации технологического процесса.
Таблица подключения является основой для выбора состава модулей связи с объектом автоматизации, их числа и компонент Контроллера.
Алгоритмы контроля и управления технологического процесса служат основой для программного обеспечения (ПО) контроллера в конкретной выбранной компоновке. ПО создается с помощью Системы прикладного Технологического Программирования (СПТП).
Программное обеспечение (ПО) системы автоматизации
Специальное ПО строится на основе комплекса программных средств диспетчерского управления и обработки данных. Комплекс построен на основе единых принципов и технологий MS WINDOWS с использованием возможностей средств Открытой архитектуры (WOSA) и пользовательских интерфейсов WINDOWS.
Комплекс представляет собой взаимоувязанный набор приложений и библиотек WINDOWS, обеспечивающий решение круга задач диспетчерского управления и информационного обслуживания.
Приложения, входящие в комплекс, могут размещаться на одной ЭВМ или быть распределены в сети компьютеров. Приложения могут выполняться в среде операционных систем семейства Windows.
Компоненты комплекса ПО функционируют на ЭВМ архитектуры IBM PC.
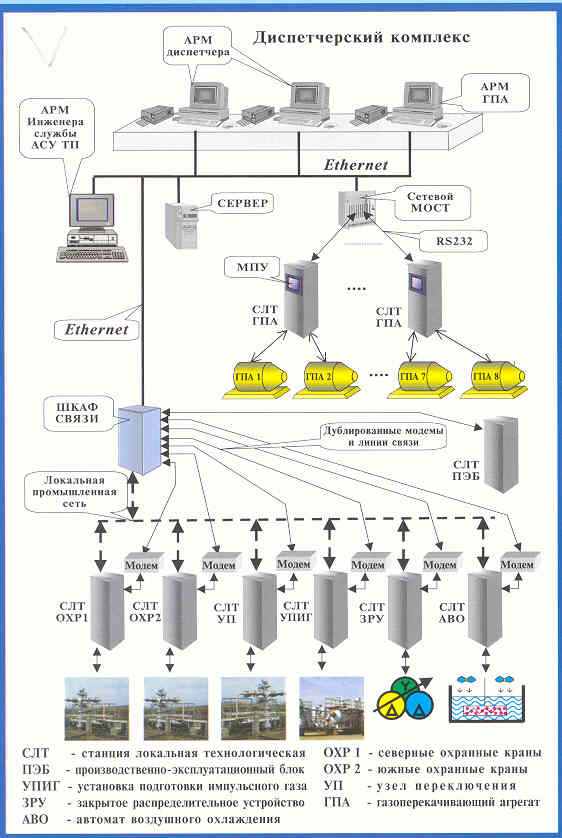
Рис. №1
Газоперекачивающий агрегат (ГПА), повышающий давление газа путем его сжатия, является основным элементом магистральных газопроводов. Он состоит из центробежного компрессора и двигателя (газотурбинного или электроприводного от 4 до 25 МВт), который приводит его во вращение.
Для обеспечения нужной степени сжатия и объемной производительности в компрессорном цехе обычно работают сразу несколько ГПА (от 3-х до 10-ти) на общую нагрузку.
Система автоматизированного управления (САУ) ГПА предназначена для автоматизации функций контроля и управления электроприводными газоперекачивающими агрегатами компрессорных станций.
Непосредственными объектами контроля и управления ГПА являются подсистемы:
- нагнетатель с приводным электродвигателем и редуктором;
- крановая обвязка;
- электропитание двигателя.
САУ ГПА спроектирована на современных принципах и программно-технических средствах диспетчерского управления, включающих:
- программную систему контроля и управления SCADA;
- АРМ оператора;
- программируемые логические контроллеры - ПЛК.
САУ ГПА обеспечивает выполнение функций контроля и управления в следующих основных режимах работы ГПА:
ГПА остановлен - пуск ГПА - работа - нормальный останов - аварийный останов - экстренный останов – опробование.
САУ ГПА реализует следующие функции
- автоматическое управление пуском и остановом ГПА;
- автоматическая защита ГПА;
- оперативное отображение на дисплеях АРМ основных параметров процесса, а также аварийных и предупредительных сообщений;
- создание, обработка и хранение массивов оперативной и ретроспективной информации;
- взаимодействие оператора с САУ ГПА средствами человеко-машинного интерфейса;
- взаимосвязь со смежными подсистемами;
- проверка исправности и правильности функционирования основных узлов и механизмов, а также системы в целом (опробование) после проведения ремонтных работ или в ходе проведения регламентных мероприятий;
- выполнение вспомогательных действий, таких как:
- инициализация САУ ГПА;
- корректировка баз данных при изменениях в конфигурации системы и/или в структурах слайдов;
- самодиагностика САУ ГПА;
- резервирование функций контроля и аварийной защиты.
Верхний уровень САУ работает под управлением операционной системы Windows. Прикладное программное обеспечение разрабатывается на базе отечественной SCADA-системы TraceMode.
Система выполняет две основные задачи:
- сбор данных о контролируемом технологическом процессе;
- управление технологическим процессом на основе собранных данных и критериев, выполнение которых обеспечивает наибольшую эффективность и безотказность.
SCADA-система:
1) Основана на распределенной общей модели объектов - DCOM, лежащей в основе Windows.
2) Поддерживает языки визуального программирования, соответствующие международным стандартам I ЕС-1131/3.
3) Имеет открытый коммуникационный интерфейс - поэтому легко настраивается на любые контроллеры, как отечественного, так и зарубежного производства.
4) Позволяет создавать резервированные многоуровневые АСУ ТП масштаба предприятия на базе ведущих сетевых ОС с обменом по протоколу NetBios, NetBEUI, IPX/SPX, TCP/IP.
Подсистема виброконтроля ГПА
Входит в состав САУ ГПА и использует алгоритмы анализа изменений виброакустических сигналов, возникающих на поверхности оборудования при одновременном контроле технологических параметров установок: температуры, давления, расхода и т.д., что позволяет выявлять и идентифицировать аномалии в работе двигателя, компрессора ГПА и их составных частей на ранней стадии их развития, еще до того момента времени, когда произойдут необратимые изменения. Внедрение такой системы повышает безопасность работы оборудования ГПА, позволяет персоналу своевременно проводить регламентные работы, прогнозировать остаточный ресурс оборудования.
Блок спецзащит (БСЗ)
САУ ГПА имеет в своем составе микропроцессорный блок специальных защит электродвигателя. БСЗ отслеживает и частично архивирует основные параметры работы приводного электродвигателя, обеспечивая возможность просмотра на встроенном дисплее текущих параметров двигателя, запоминание статистики эксплуатации (количество пусков и отключений, количество срабатываний защит и т.д.), запоминание с последующим отображением информации о развитии трех последних аварийных остановов. БСЗ может передавать накопленную информацию в общую систему управления через стыки RS-232 или RS-485.
ВС БСЗ обеспечивает:
1. Опережающее отключение электродвигателя при потере устойчивости (асинхронный режим с возбуждением) при аварийных возмущениях в питающей сети (функция опережающего отключения).
2. Отключение электродвигателя при возникновении несимметрии тока фаз статора (повреждение или обрыв фаз питающей сети).
3. Защиту приводного электродвигателя от колебаний нагрузки на валу при помпаже агрегата.
Основой системы автоматического управления (САУ) для компрессорных станций (КС) является семейство программируемых контроллеров, объединенных в промышленную сеть.
Важнейшими из многочисленных функций, которые они выполняют, являются:
- управление режимом работы ГПА;
- автоматическое управление исполнительными механизмами и кранами газовой обвязки ГПА по заданным алгоритмам;
- антипомпажное регулирование и антипомпажная защита ГПА при параллельно - последовательном подключении, автоматизированный съем помпажных характеристик;
- управление агрегатами двигателя; представление на экране мнемосхем агрегата с указанием значений измеряемых параметров и состояний исполнительных механизмов, отображением аварийной и предупредительной сигнализации;
- непрерывная самодиагностика оборудования САУ;
- обеспечение функций пожаробезопасности и контроля загазованности в защищаемых объектах.
Программное обеспечение САУ ГПА
Информационные функции в САУ ГПА обеспечивают выполнение широкого набора задач, необходимых для управления объектом, в том числе:
- формирование и передачу информации в систему отображения, регистрации и хранения;
- представление на экране измеренных значений технологических параметров, в том числе и в графической форме, с отображением значений установок аварийной и предупредительной сигнализации;
- представление на экране вычисленных значений результатов косвенных измерений;
- представление на экране мнемосхем агрегата с указанием значений измеренных параметров и состояний исполнительных механизмов;
- автоматическое обнаружение, отображение и звуковая сигнализация отклонений технологических параметров от аварийных и предупредительных значений;
- представление информации о невыполненных предпусковых условиях;
- представление информации об основных режимах работы агрегата.
При создании АРМа сменного инженера (СИ) используются персональные компьютеры платформы IBM в связи с простотой их приобретения, наличием у заказчиков специалистов, знакомых с системным программным обеспечением.
Пульт оператора обладает высокой отказоустойчивостью. Кроме того, он многотерминален в связи с тем, что на одном экране невозможно представить наглядно всю информацию по цеху. Кроме того, время от времени возникает необходимость использовать это АРМом у инженера КИПиА, начальника цеха.
Обычно ставятся несколько резервируемых компьютеров.
В состав АРМа включают также индикаторные панели с кнопками основных функций, заведенными на физические входы технологических контроллеров на случай общего отказа сети, связывающей контроллеры с АРМом.
Системы автоматического управления (САУ) газоперекачивающими агрегатами (ГПА), компрессорными цехами (КЦ) и другими технологическими объектами компрессорной станции строятся на единых аппаратно-программных средствах.
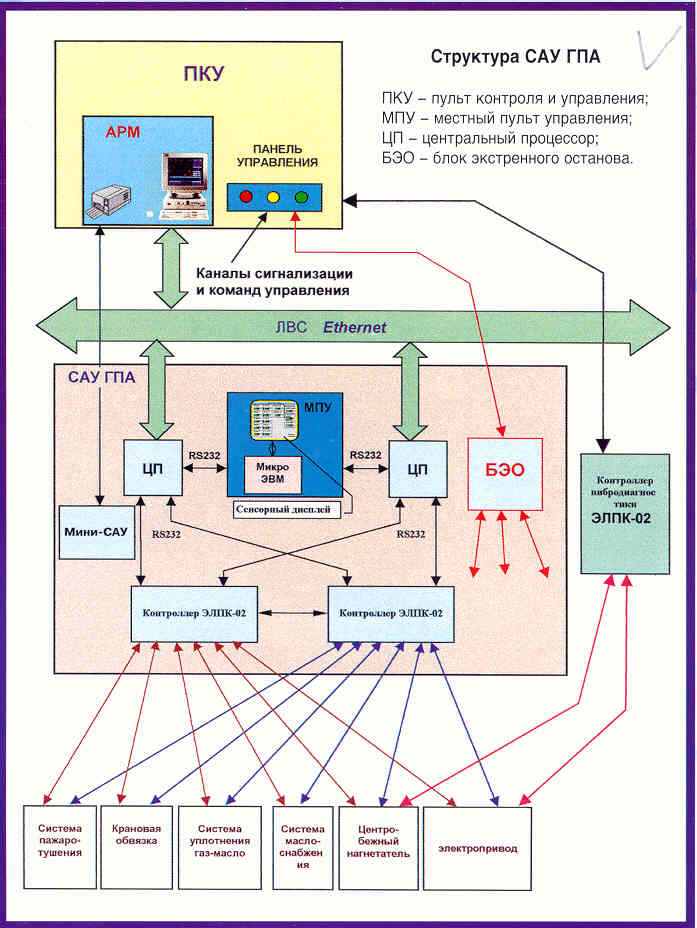