Н. Г. Забродская организация и экономика предприятий автосервиса учебно-методический комплекс
Вид материала | Учебно-методический комплекс |
Производственная неделя Основные фонды Остаточная стоимость Арендные отношения |
- Учебно-методический комплекс по дисциплине «организация производства на предприятиях, 1298.86kb.
- Вавилова Елена Васильевна, к с/х н., профессор учебно-методический комплекс, 907.06kb.
- Онсфоктор Елена Леонидовна Тимирьянова Венера Маратовна Экономика и организация оптово-посреднических, 589.99kb.
- Учебно-методический комплекс Для специальности 080502 Экономика и управление на предприятии, 1031.78kb.
- Учебно-методический комплекс по дисциплине «Экономика и управление в акционерных обществах», 610.54kb.
- Учебно-методический комплекс обсужден на заседании кафедры «Экономика труда», 947.18kb.
- Полякова Офелия Робертовна, кандидат педагогических наук, доцент учебно-методический, 389.78kb.
- Учебно-методический комплекс Для специальностей: 080102 Мировая экономика; 080301 Коммерция, 3186.12kb.
- Зимин Александр Федорович Ефимов Олег Николаевич Экономика предприятия (название дисциплины), 676.17kb.
- О. А. Миронова Учебно-методический комплекс дисциплины «международная торговля» Ростов-на-Дону, 727.71kb.
Промежуток времени от запуска сырья в производство до выхода готовой продукции называется производственным циклом.
Производственный цикл характеризует продолжительность и структура.
Под продолжительностью производственного цикла понимают время, в течение которого предмет труда, подвергается обработке с момента запуска его в производство до момента выпуска готовой продукции.
Под структурой производственного цикла понимают состав цикла по видам операций и соотношение затрат времени на их выполнение, включая все перерывы.
Продолжительность производственного цикла измеряется в календарных единицах времени:
– в месяцах;
– в днях;
– в часах;
– в минутах.
Продолжительность цикла состоит из:
– рабочего периода;
– и времени перерывов в производстве.
Продолжительность цикла включает время необходимое для выполнения технологических, транспортных, контрольно-учетных операций, а также время перерывов в производстве.
В общем виде продолжительность производственного цикла Тц можно представить формулой:
Тц = tопер + tпер
или
Тц = tос + tвс + tсуш + tтех + tреж + tмеж + tорг,,
где
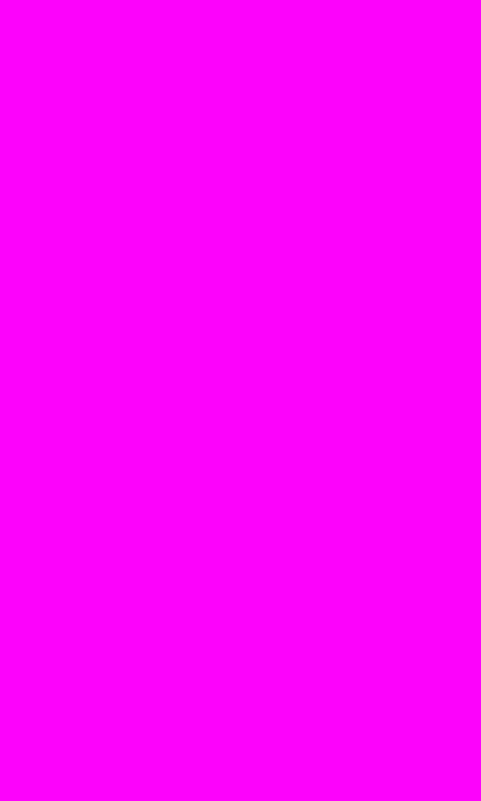
рабочий период
tос - время выполнения основных (технологических) операций;
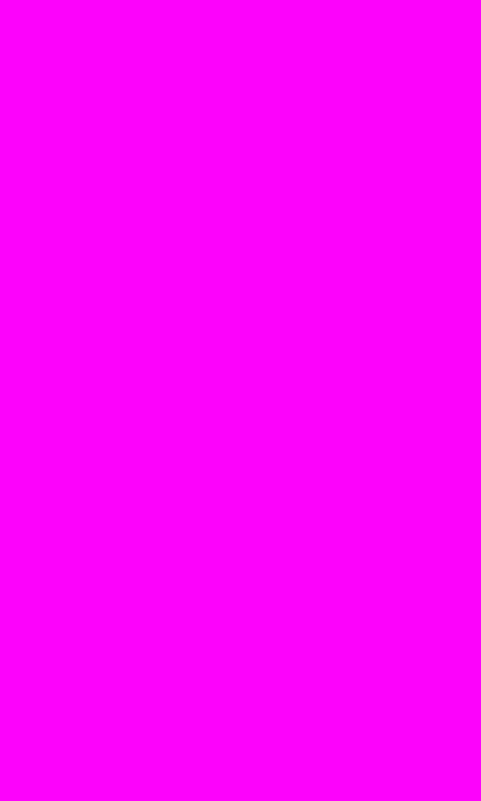
tвс - время выполнения вспомогательных операций;
tсуш - время искусственной сушки;
время перерывов
tтех - технологические перерывы, связанные с процессами не требующими применения труда (выдержка деталей после склеивания, прессования отделки);
tреж - перерывы обусловленные режимом рабочего времени (нерабочие смены, обеденные и другие регламентированные перерывы);
tмеж - межоперационные перерывы;
tорг - перерывы по организационным причинам (из-за недостатка инструмента, электроэнергии и др.)
Рабочий период складывается из времени выполнения:
– основных tос;
– вспомогательных операций tвс;
– и времени сушки tсуш;
К перерывам относятся:
– технологические перерывы tтех;
– организационные, т.е.
а) перерывы обусловленные режимом рабочего времени tреж;
б) межоперационные перерывы tмеж;
в) перерывы по организационным причинам tорг;
Можно отдельно рассматривать продолжительность производственного цикла, одной детали, партии деталей, изделия.
Продолжительность производственного цикла одной детали соответствует сумме продолжительности всех операций и перерывов, т.к. деталь проходит все операции только последовательно:
Тдет = t1 + t2 + … +tn.
Продолжительность технологического цикла партии деталей по всем операциям технологического процесса зависит от вида движения деталей, которое может быть:
– последовательным;
– параллельным;
– параллельно-последовательным (смешанным).
При последовательном движении партии деталей в механическом процессе каждая последующая операция начинается только после того, как выполнена предыдущая операция. При этом с операции на операцию все детали партии передаются одновременно, после окончания их обработки.
Продолжительность технологического цикла при последовательном движении определяется по формуле:
Т посц = nq∑tq,
где nq - число деталей в партии;
∑tq - сумма продолжительности всех операций, которую проходит обрабатываемая деталь.
Последовательное движение партии деталей в технологическом процессе является наименее эффективным, т.к. детали задерживаются у рабочего места до окончания обработки всей партии, в результате увеличивается незавершенное производство.
При параллельном движении партии деталей в технологическом процессе каждую деталь после выполнения одной операции сразу, без перерыва во времени, передают на другую, не ожидая окончания обработки всей партии.
Определяющее влияние на продолжительность технологического цикла оказывает tq – время, необходимое для выполнения наиболее трудоемкой, длительной (главной) операции:
Т парц = ∑tq = (nq – 1) tгл ,
где ∑tq - сумма продолжительности всех операций одной детали;
nq - количество деталей в партии;
tгл - продолжительность выполнения наиболее трудоемкой операции.
Параллельное движение партии деталей в технологическом процессе наиболее эффективно, т.к. оно характеризуется самым коротким технологическим циклом, наименьшим объемом незавершенного производства, наиболее быстрой оборачиваемостью средств.
При параллельно–последовательном движении партии деталей их обработка на каждой последующей операции начинается раньше, чем заканчивается обработка всей партии на предыдущей операции.
После определения продолжительности технологических операций устанавливают время на выполнение вспомогательных операций и перерывы и определяют общую продолжительность цикла.
Время выполнения вспомогательных операций и перерывов зависит от:
– размера партии деталей;
– транспортных средств;
– других производственных условий.
Обычно контрольно-учетно-сортировочные операции стараются выполнять параллельно с обработкой деталей.
Время выполнения вспомогательных операций и перерывов устанавливается путем замеров, методом технического нормирования.
От длительности производственного цикла зависит выпуск продукции, потребность предприятия в оборотных средствах, производительность труда и себестоимость продукции.
Поэтому сокращение продолжительности производственного цикла является одной из важных задач организации и планирования производства.
Основные пути сокращения производственного цикла:
- Сокращение времени технологических операций путем увеличения скоростей, повышения уровня механизации и автоматизации производства, уменьшение холостого хода, увеличение фронта работ, сокращение времени перерывов.
- Сокращение времени транспортных операций за счет уменьшения расстояний между рабочими местами.
- Совмещение контрольно-учетных операций с технологическими операциями.
- Режим работы предприятия
Режим работы предприятия – это организация рабочего времени в течение которого осуществляется процесс труда.
Основными элементами являются:
1) система производственной недели;
2) сменность;
3) продолжительность смены.
Эти элементы надо рассматривать отдельно применительно к оборудованию и к рабочим.
Производственная неделя – это дни работы предприятия в течение календарной недели. Она устанавливается, исходя из характера производства, и может быть семидневной с двумя выходными (суббота, воскресенье), пять дней рабочих. В непрерывном производстве выходные устанавливаются по скользящему графику.
Сменностью называют повторяемость рабочих смен в течение суток. В отдельных цехах и службах как периодического, так и непрерывного производства на предприятиях имеет место одно- двух- и трехсменная работа.
Для характеристики использования оборудования по времени определяют коэффициент сменности как отношение фактически отработанных машино-смен (аппарат-смен) к общему числу станков (аппаратов), закрепленных за участком (цехом, предприятием):
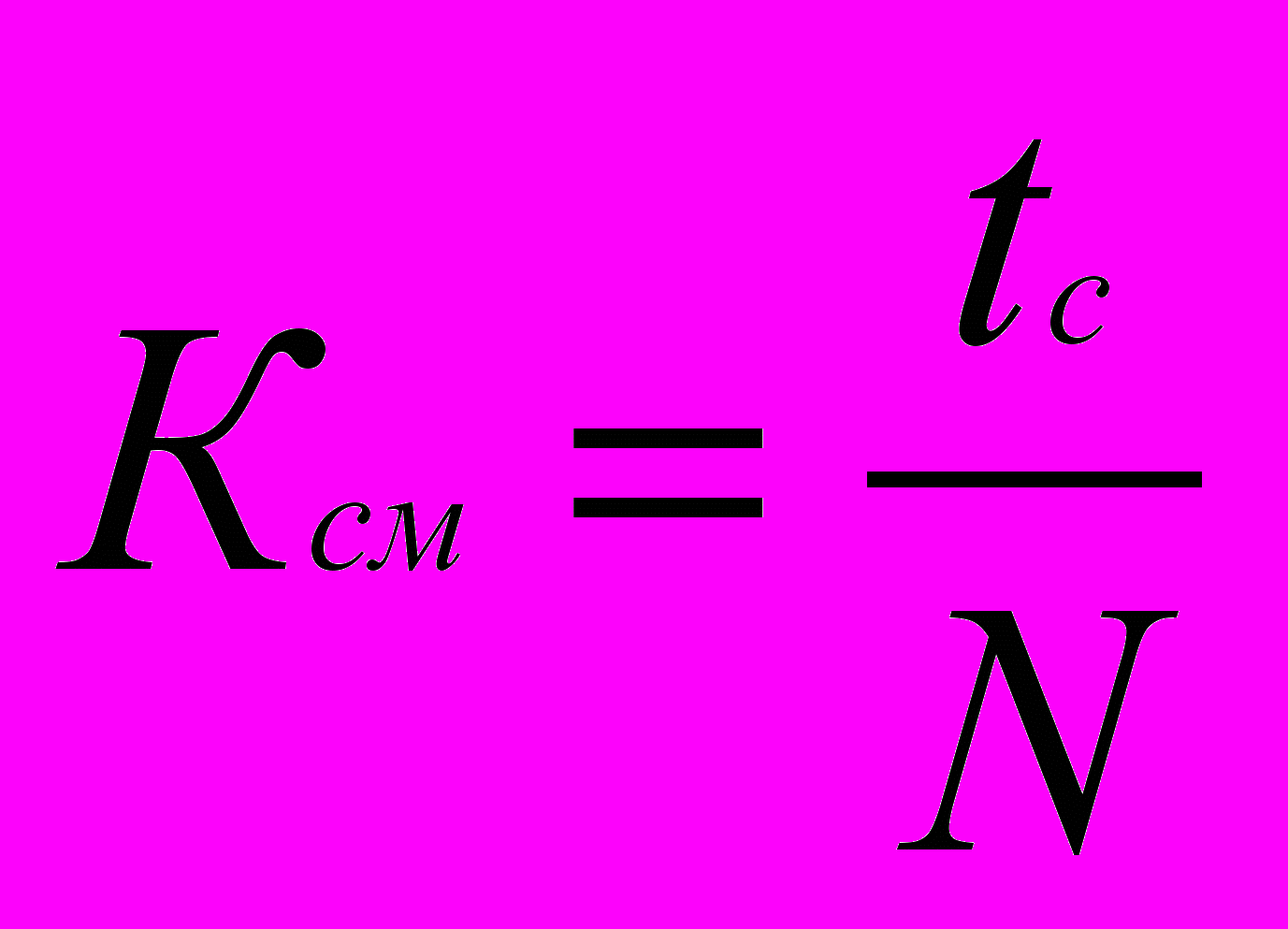
где tc - фактически отработанное число машино-смен (станко-смен) в сутки;
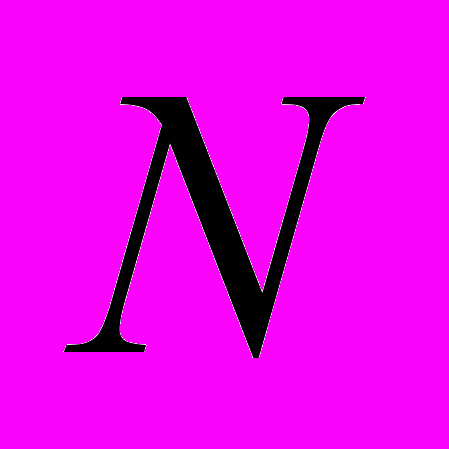
Например. Всего установлено 20 станков:
в 1-ю смену работали все 20;
во 2-ю смену – 18;
в 3-ю смену – 12.
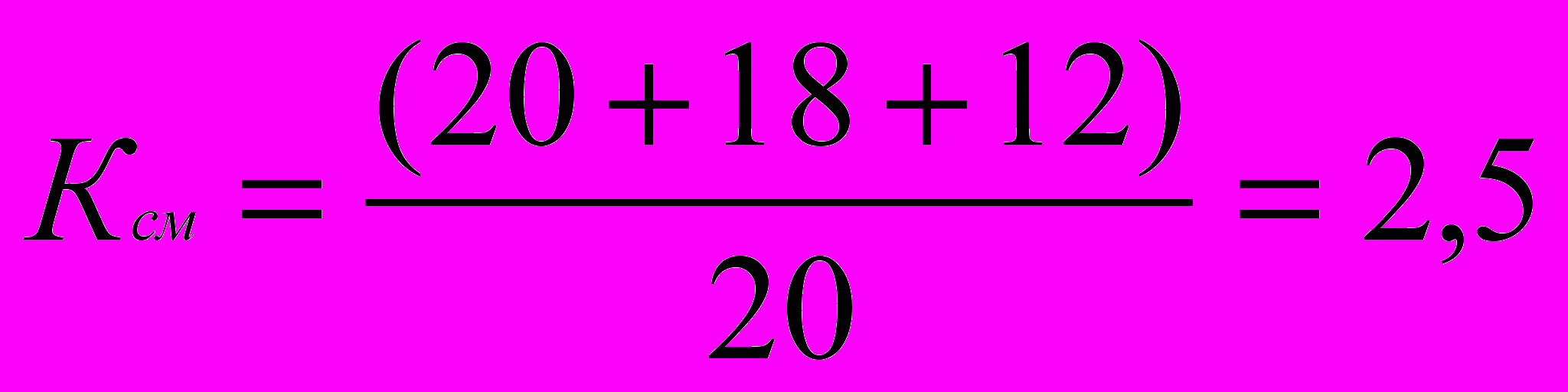
т.е. из 24 часов суточного времени оборудование работало 20 часов (8+8+4).
Продолжительность смены – это число часов работы в течение смены. Государством установлено 40 и 36 часовая рабочая неделя.
С учетом условий производства и труда установлена 8, 7,6 часовая продолжительность смены.
В условиях непрерывного производства труд организован обычно по 4-х бригадному графику с работой в 3 смены, т.е. три бригады работают, а четвертая отдыхает.
- Основы организации поточного и автоматизированного производства
Поточное производство – передовой метод организации производства, при котором оборудование располагается в соответствии с последовательностью выполнения технологических операций.
Наиболее прогрессивно непрерывное поточное производство.
Для его организации необходимо:
- разделение процесса производства на равные по трудоемкости операции и закрепление за рабочим местом определенной операции;
- расположение рабочих мест по ходу технологического процесса при минимальном расстоянии между рабочими местами;
- одновременное выполнение технологических операций для обеспечения непрерывности процесса производства.
Поточная линия может быть простой, если каждая операция выполняется на одном рабочем месте, и сложной, если одна операция выполняется одновременно на нескольких рабочих местах.
Наиболее распространенный вид поточной линии – конвейер. Конвейер может быть рабочим и распределительным.
Распределительный конвейер применяется только для транспортировки, а изделия для обработки снимаются с конвейера.
Рабочий конвейер служит одновременно средством транспорта и рабочим местом.
Прогрессивной формой организации производства является полуавтоматические и автоматические линии.
Поточные линии характеризуются ритмом. Различают средний, операционный и рабочий ритм.
Средний ритм – это средний промежуток времени между выпуском с поточной линии двух следующих друг за другом изделий.
Операционный ритм – это продолжительность операции на данном рабочем месте. Это понятие применимо к каждой операции поточной линии. Обычно берется среднее время выполнения операции.
Рабочий ритм – это промежуток времени между выпуском с поточной линии двух очередных изделий или партий, если изделия передаются с одной операции на другую не поштучно, а партиями в несколько штук.
Созданию поточной линии предшествуют расчеты, проводимые на стадии ее проектирования. Рассчитываются следующие параметры:
1) средний и рабочий ритм;
2) количество рабочих мест;
3) выбирается тип конвейера или средства межоперационной транспортировки;
4) рассчитывается длина поточной линии;
5) определяется скорость движения конвейера.
Средний ритм Rср определяется как отношение фонда рабочего времени к плану выпуска деталей:
Rср
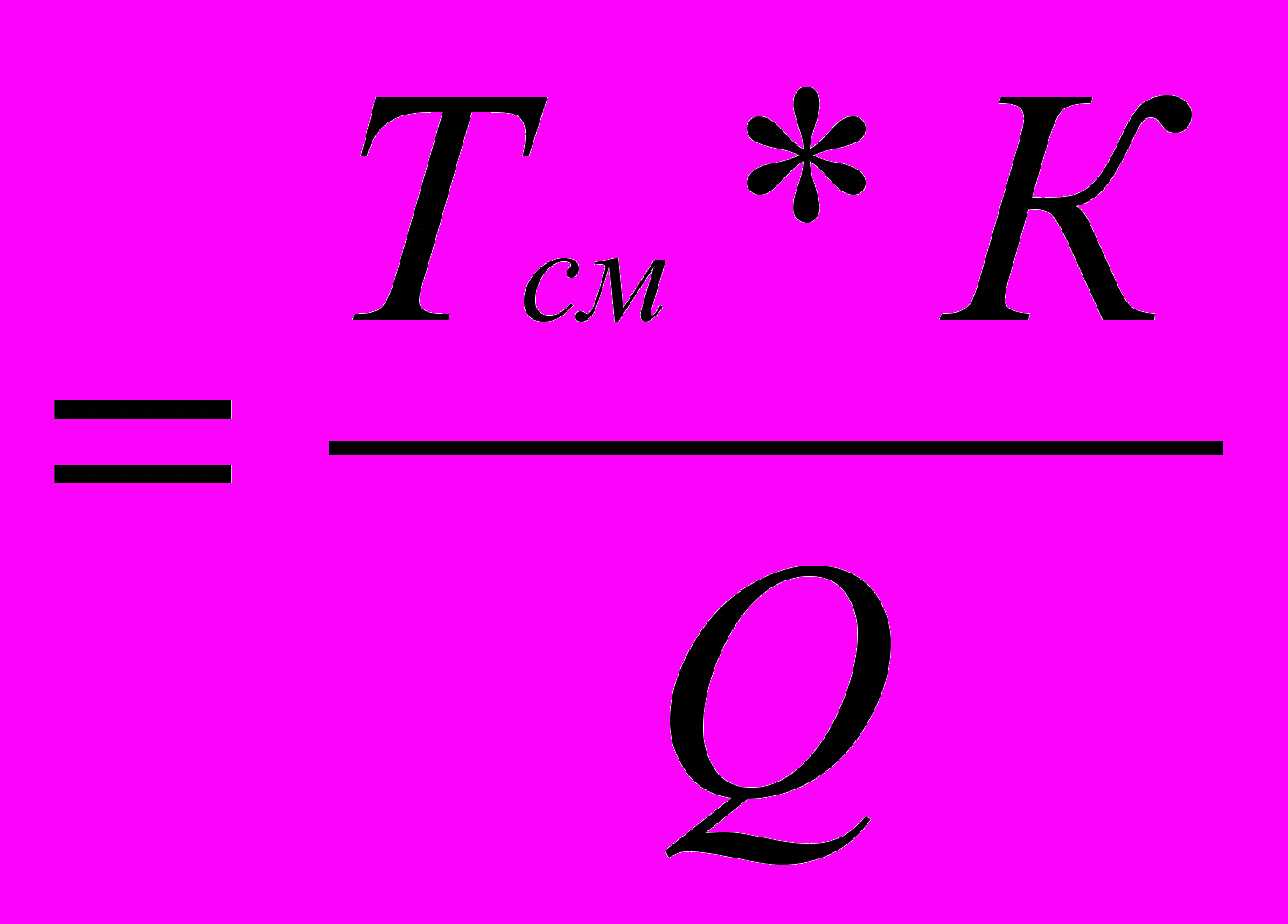
где Rср - средний ритм;
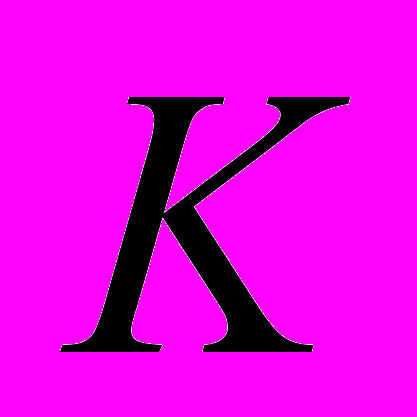
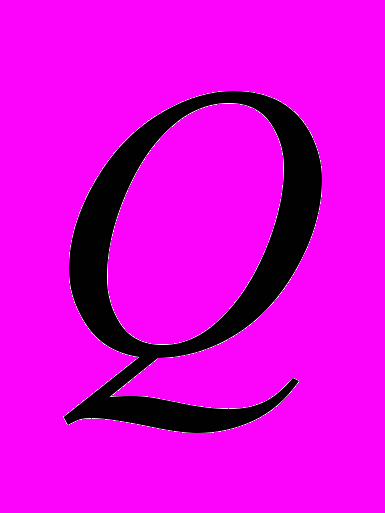
Например: Тсм = 480 минут, перерывы для отдыха и замены инструмента Тпер составляет 30 минут. Сменное задание для поточной линии Q =200 изделий.
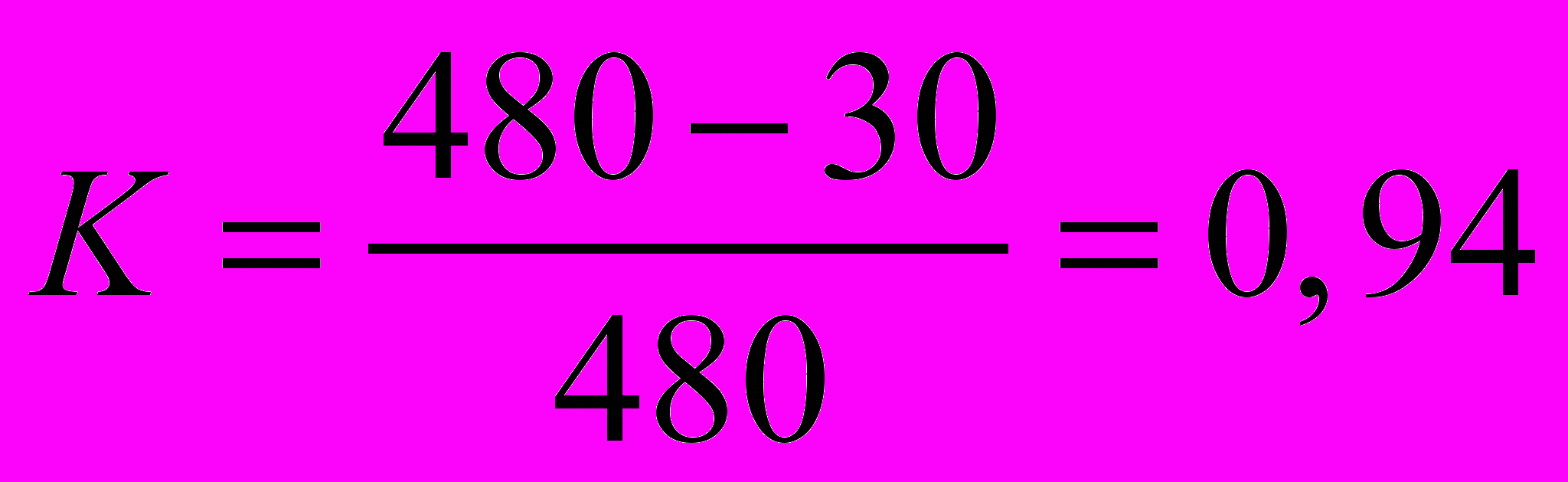
Rср
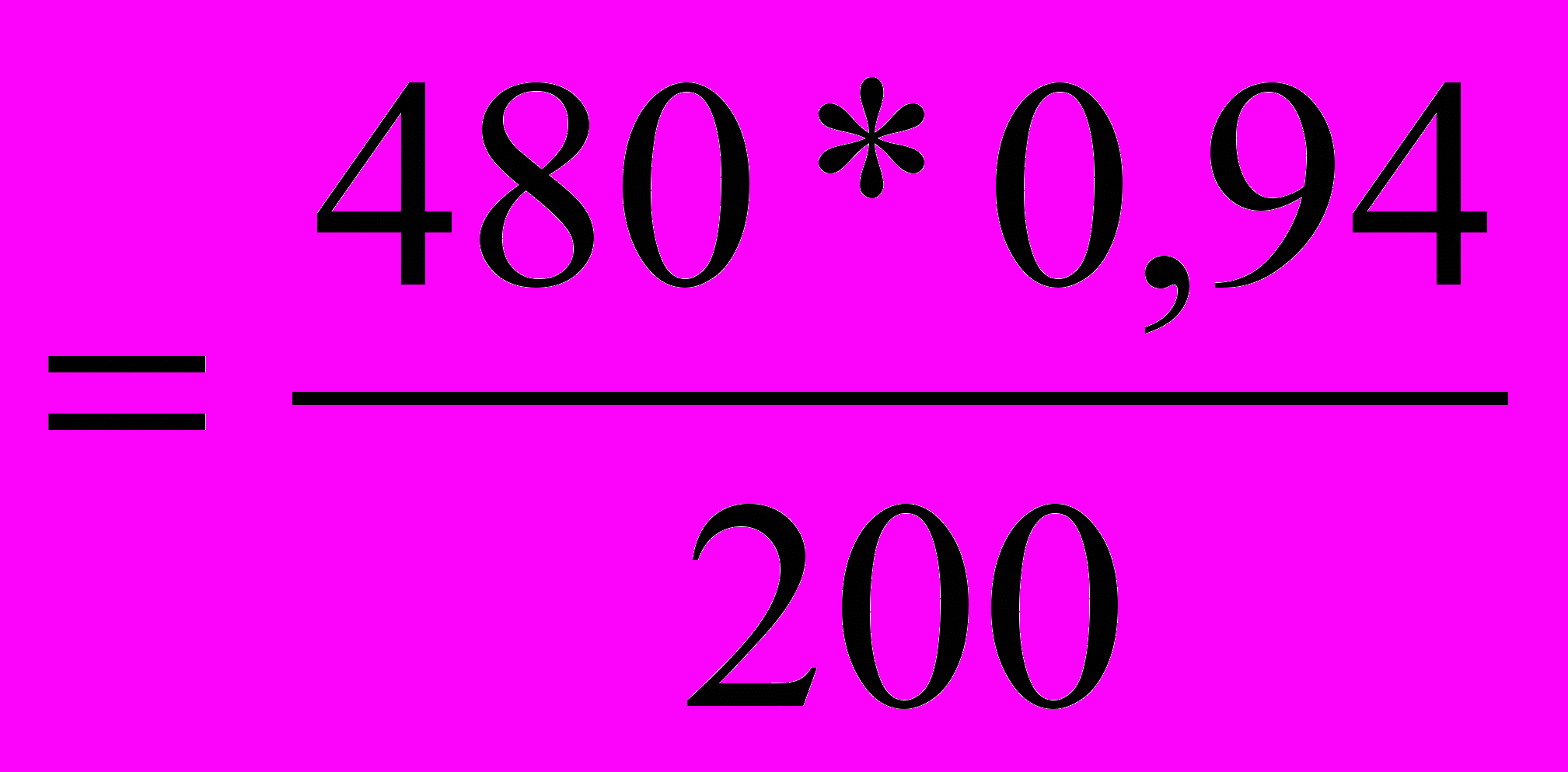
В средний ритм поточной линии входит время выполнения операций и время перемещения деталей (изделия) от одного рабочего места к другому.
На конвейерах периодического действия средний ритм Rср складывается из времени выполнения операции (tоп) и времени передвижения конвейера (tк) :
Rср = tоп + tк
На конвейере непрерывного действия время выполнения операции tоп и время передвижения конвейера tк совпадают, поэтому средний ритм равен времени операции:
Rср = tоп
Для обеспечения ритмичной работы поточной линии необходимо равенство продолжительности выполнения каждой операции среднему ритму, т.е. синхронизация операций.
На линиях с преобладанием ручных процессов сравнительно легко добиться синхронизации операций. На механизированных линиях синхронизация операций достигается разнообразными техническими и организационными мероприятиями:
а) переводом некоторых операций с одних станков на другие, более производительные;
б) освобождением основных рабочих от выполнения обязанностей по обслуживанию рабочих мест.
Эффективность поточного производства во многом зависит от правильности выбора типа конвейера. Рабочий конвейер применим, если конструкция изделия позволяет его обрабатывать без снятия с конвейера. Если при обработке изделия участвует специальное оборудование, то устанавливают распределительный конвейер.
На операциях сборки обычно применяют конвейер периодического действия. Количество рабочих мест рассчитывается по каждой операции в отдельности. Кроме рабочих мест для выполнения технологических и контрольных операций организуются резервные рабочие места, они необходимы в случае возможных отклонений от первоначального технологического процесса.
Рабочую длину конвейера (
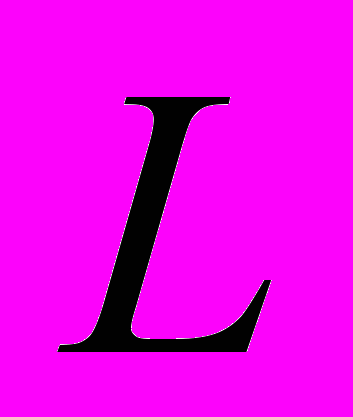
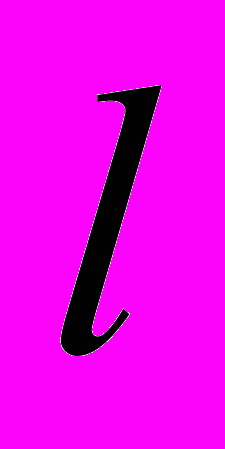
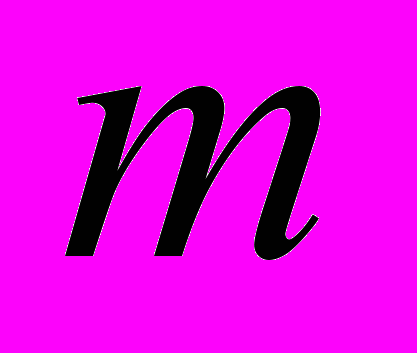
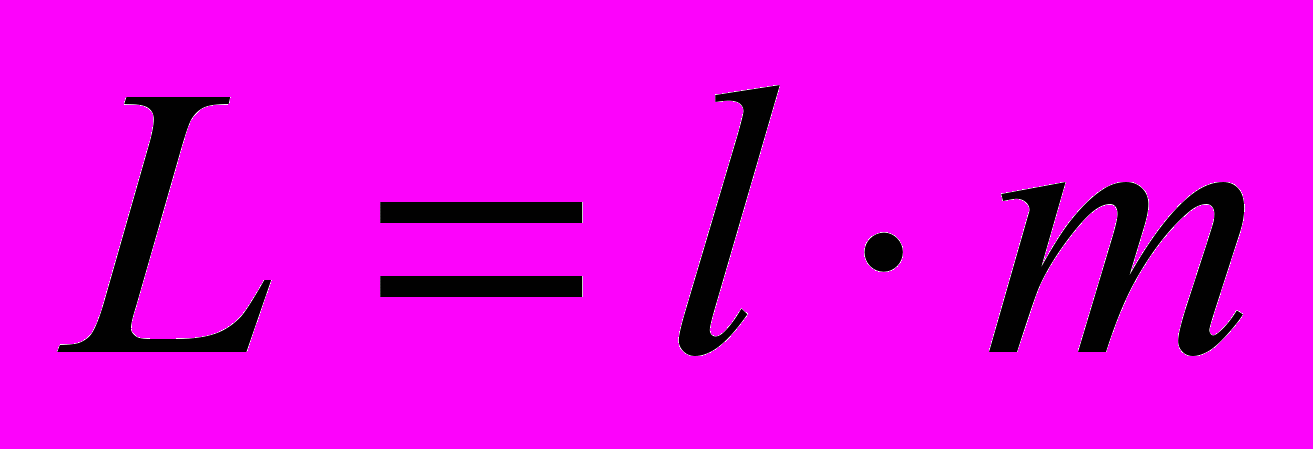
Шаг конвейера – это расстояние между двумя рабочими местами.
Скорость движения непрерывно действующего конвейера определяется как отношение шага конвейера к среднему ритму:
υ = l .
Rср
Например. Шаг конвейера l равен 1м, средний ритм Rср составляет 2,5мин. На поточной линии 10 рабочих мест. Определить длину и скорость конвейера.
Длина конвейера:
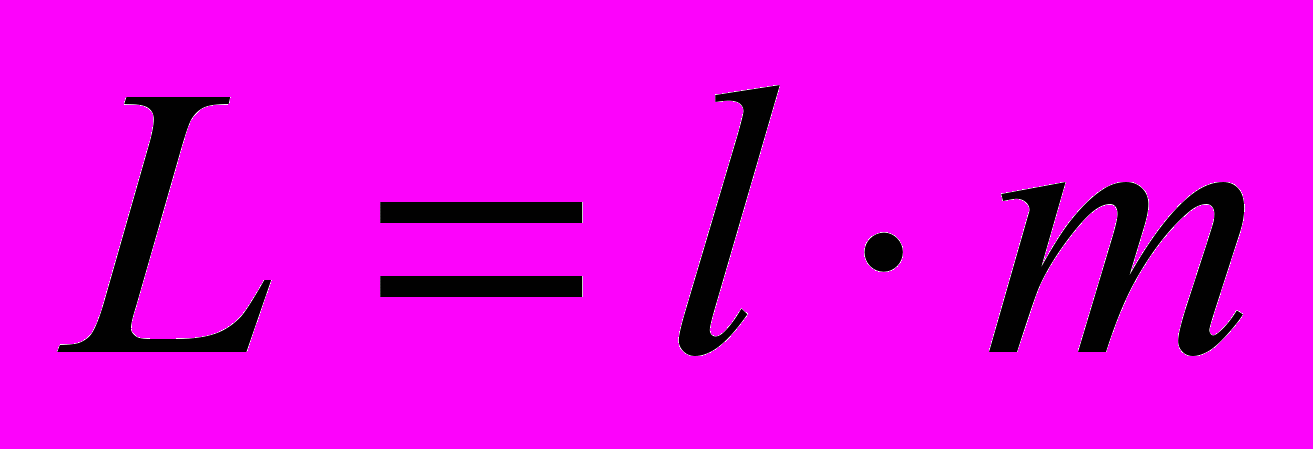
Скорость движения υ = l , υ =1 : 2,5 = 0,4м/мин.
Rср
Вопросы для самопроверки знаний
Какова структура производственного процесса?
- Что относится к основному и вспомогательному производству?
- Что понимают под операцией, какие их виды?
- Охарактеризуйте типы производств?
- Как определить длительность производственного цикла?
Тема 6. Организация подготовки производства на предприятии автосервиса
- Содержание и задачи подготовки производства
Подготовка производства включает организацию и планирование работ по внедрению новых видов изделий, услуг, достижений научно-технического прогресса в производство.
От подготовки производства зависит рентабельность и ритмичность работы предприятия. Объем подготовки зависит от структуры производственного процесса, вида услуг, работ, характера выпускаемой продукции.
Мероприятия по подготовке производства выполняются по календарному плану, который составляется на основании заданий по освоению новой техники, внедрению новых видов продукции и услуг.
Подготовка производства осуществляется в отделах, лабораториях и цехах предприятия.
Основные работы по подготовке производства ведут инженеры и специалисты предприятий автосервиса. На крупных предприятиях подготовку производства осуществляют конструкторский, технический отделы, отделы главного механика, энергетика, заводские лаборатории, инструментальный цех предприятия.
Задачи, стоящие перед подготовкой производства:
1) обеспечение технического прогресса путем ускорения выпуска продукции, внедрения новых видов услуг, улучшение качества и увеличения ассортимента продукции и освоения высокопроизводительного оборудования;
2) обеспечение снижения трудоемкости и себестоимости продукции и услуг, улучшение экономических показателей производственной деятельности предприятия;
3) сокращение длительности научно-исследовательских, конструкторских, технологических, экспериментальных и других работ, входящих в комплекс подготовки производства.
Подготовка производства включает следующие виды работ:
- разработка планов научно-исследовательских и опытно-конструкторских работ;
- изучение и освоение новых видов сырья и материалов, работ и услуг;
- проектирование новой и совершенствование выпускаемой продукции;
- проектирование новых и совершенствование действующих технологических процессов;
- разработка ресурсосберегающих и энергосберегающих производств, прогрессивных норм расходов сырья и материалов;
- проектирование и изготовление технологической оснастки;
- наладка и внедрение запроектированных оборудования и технологических процессов в производство.
- Виды подготовки производства
Подготовка производства включает следующие виды:
- техническую подготовку производства, состоящую из конструкторской и технологической подготовки;
- материальную подготовку;
- организационную подготовку.
Техническая подготовка – это мероприятия по созданию и освоению производства новых видов продукций, услуг, оборудования, технологических процессов, а также их совершенствование.
Эти работы ведутся на предприятиях, в отраслевых научно-исследовательских институтах, конструкторских бюро, в лабораториях, в технопарках.
Техническая подготовка включает два вида работ: конструкторские и технологические.
В ходе конструкторской подготовки производства осуществляется конструирование новых и совершенствование действующих видов оборудования и изделий.
Конструкторская подготовка должна обеспечивать:
- увеличение единичной мощности машин и агрегатов с учетом их экономичности и целесообразности;
- создание принципиально новых орудий труда;
- повышение надежности и долговечности изделий и снижение их веса;
- уменьшение трудоемкости изготовления, их материалоемкости и энергоемкости.
В современных условиях меняются методы конструкторской подготовки. Раньше обычно проектировалось одно изделие (агрегат), однако целесообразней проектировать совокупность изделий аналогичных по технологическому процессу и назначению. Каждый ряд изделий имеет базовую модель и от нее получается производные.
Такой метод проектирования позволяет:
- проектировать изделия и оборудование в более короткие сроки;
- стандартизировать узлы и детали машин, что особенно актуально, в связи с усложнением конструкции машин и агрегатов;
- возможность использования унифицированных методов проектирования оборудования, которые базируются на соответствующих научных исследованиях.
Конструкторская подготовка производства включает:
– разработка заданий на проектирование;
– эскизное проектирование;
– техническое проектирование;
– изготовление экспериментального образца, испытание его и внедрение.
В задании на проектирование определяются назначение нового изделия, важнейшие эксплуатационные показатели.
Заказчик (потребитель) изделия указывает в задании на проектирование:
1) конфигурацию изделия;
2) условия эксплуатации;
3) техническую характеристику изделия, включающую следующие параметры:
– прочность;
– диэлектрические свойства;
– водо- и газопоглощение;
– герметичность;
– термостойкость;
– теплопроводность;
– внешний вид и др.
На стадии эскизного проектирования разрабатывается принципиальная конструкция изделия, изготавливаются чертежи общего вида изделия, исследуется возможность использования действующего оборудования.
При разработке изделий широкого потребления большое значение приобретают эстетические требования: лаконичность и пропорциональность форм изделия, цветовое решение, внешнее оформление.
Техническое проектирование выполняется на основе эскизного проекта с учетом изменений, внесенных при его рассмотрении.
Технический проект содержит чертежи общего вида, разрезов изделия, комплектующих деталей.
При технологической подготовке выбираются оборудование и материалы, даются указания о порядке и последовательности обработки и сборки изделия.
Опытные образцы изготавливаются на основании технического проекта, их испытывают, вносят поправки в конструкцию и дают заключение о готовности нового изделия.
На сегодняшний день время освоения предприятиями Республики Беларусь структурно сложных образцов новой техники сопоставимо с периодом ее морального старения. Опыт промышленно развитых стран свидетельствует о том, что для решения объемных научно-технических проблем народнохозяйственного значения требуется разработка и проведение единой государственной политики в этих вопросах, координация исследований в рамках государственных научно-технических программ. Одним из важных направлений решения этой задачи является создание и внедрение технологий информационной поддержки жизненного цикла продукции (CALS - технологии). CALS – технология – информационная поддержка жизненного цикла: маркетинговые исследования, составление технического задания, проектирование, технологическая подготовка производства, изготовление, поставка, эксплуатация, ремонт, утилизация. Фактически – это полная компьютеризация и информатизация всей деятельности предприятия, направленная на повышение его эффективности, сокращение сроков освоения новых изделий, энерго- и ресурсосбережение. Особенно это касается полной автоматизации ключевого звена – проектной сферы, подготовки производства и перевода ее в компьютерную форму.
Вопросы для самопроверки знаний
- Охарактеризуйте порядок подготовки производства.
- Какие задачи решает подготовка производства?
- Какие существуют виды подготовки производства?
- Что включает технический проект?
Тема 7. Научная организация труда на предприятии автосервиса
- Организация труда
Под организацией труда на предприятии следует понимать совокупность мероприятий направленных на более полное, рациональное и планомерное использование трудовых ресурсов при данном уровне техники и технологии.
Организация труда включает следующие вопросы:
1. Разделение и кооперацию труда.
2. Организацию и обслуживание рабочих мест.
3. Организацию трудового процесса на рабочих местах.
4. Создание соответствующих условий труда и установление режимов труда и отдыха.
5. Нормирование труда.
6. Производственное обучение.
7. Дисциплина труда.
8. Материальное и моральное стимулирование труда.
Современное разделение труда требует коллективного труда, следовательно высокой его организации. Организация труда в каждом производстве должна соответствовать определенному уровню техники и технологии.
Непосредственно на предприятиях сложились следующие формы разделения труда:
– функциональное, включающее общее руководство, снабжение, техническое обслуживание;
– технологическое;
– квалификационное;
– пооперационное.
При технологическом разделении обособление работ зависит от характера их исполнения, оно может быть по стадиям производства.
- Основные направления научной организации труда
Работа по научной организации труда (НОТ) проводится в определенной последовательности и начинается с анализа использования рабочего времени.
Рабочее время складывается из времени фактической работы и регламентированных (установленных) перерывов. Существует еще один элемент, входящий в рабочее время – это простои.
Простои бывают по организационно-техническим причинам (плохая организация труда) и по причинам, зависящим от рабочего (низкая дисциплина).
Время смены рабочего включает время работы и время регламентированных и нерегламентированных перерывов.
Организуя процесс труда необходимо стремиться к тому, чтобы оперативное время в общей продолжительности времени работы возрастало за счет изменений времени других элементов работы и перерывов.
Отношение времени оперативной работы (Топ) ко всему рабочему времени (Тсм) называется коэффициентом использования рабочего времени рабочих (kвр), который определяется по формуле
kвр = Топ .

Коэффициент использования рабочего времени не характеризует, какой процент времени рабочий фактически работает, поэтому в дополнение к коэффициенту использования рабочего времени определяется коэффициент загрузки рабочего (kзаг), который определяется делением времени работы рабочего на продолжительность смены:
kзаг = Тр .

Для рабочих, работающих на станках и аппаратах, коэффициент использования рабочего времени и загрузки рабочего необходимо рассматривать во взаимодействии с использованием рабочего времени оборудования.
Рабочее время оборудования состоит из времени работы (Тр) и времени перерывов (Тп) или простоев. Время работы - это период, в течение которого оборудование работает независимо оттого, является эта работа производительной или нет.
Время работы включает работу по выполнению производственного задания (Трз) и работу, не предусмотренную выполнением производственного задания (Тнз).
Время работы (Тр) делится на:
– время рабочего хода (Трх);
– время холостого хода (Тхх).
Время рабочего хода – это время, затрачиваемое непосредственно на обработку предмета труда.
Во время холостого хода станок работает, а предмет труда не обрабатывается.
Холостой ход оборудования может быть вызван:
– конструкцией станка;
– несоответствием скорости подачи деталей, скорости их обработки;
– необходимостью ручных работ перед подачей деталей в станок.
Перерывы в работе оборудования могут быть регламентированными (Тпр) и нерегламентированными (Тнр).
Регламентированные перерывы включают:
– перерывы, связанные с подготовкой к работе и организационно-техническим обслуживанием (ремонт оборудования, смена инструмента) (Тпот);
– перерывы, предусмотренные установленной технологией (Тпт);
– перерывы, связанные с отдыхом и личными надобностями рабочего (Тол).
К нерегламентированным перерывам относятся перерывы, вызванные нарушением нормального течения производственного процесса (Тнп) (отсутствием сырья, материалов, выход из строя оборудования) и перерывы вызванные нарушением трудовой дисциплины (Тнд).
Коэффициент, характеризующий использование рабочего времени оборудования (Kвро) определяется как отношение времени его работы (Тр) к времени смены (Тсм)
Kвро = Трх + Тхх = Тр.


Время рабочего и холостого хода в сумме составляет оперативное время работы оборудования.
Оперативное время рабочего, работающего на том или ином станке, обычно совпадает с оперативным временем оборудования.
Коэффициент использования рабочего времени оборудования не характеризует, какую часть рабочего дня оборудование работает на выпуск продукции, поэтому в дополнение к нему определяется коэффициент машинного времени (Kм), который рассчитывается как отношение времени рабочего хода (Трх) к продолжительности смены (Тсм):
K

Тсм
Проектируя нормы затрат рабочего времени и нормы выработки, необходимо составить перечень организационно-технических мероприятий, обеспечивающих уменьшение излишних затрат времени.
На основании нового рационального баланса рабочего времени устанавливают коэффициенты использования рабочего времени и загрузки рабочего, которые кладут в основу норм времени и норм выработки.
Коэффициент уплотнения рабочего дня (Kуп) определяется по формуле:
Kуп = (Топпроект - Топфакт) * 100.
Т

Производительность труда зависит от производительности оборудования, поэтому необходимо изучать все факторы, определяющие производительность оборудования и увязывать нормы обслуживания и выработки с системой материального и морального стимулирования.
Повышение квалификации работников осуществляется путем обучения на курсах с отрывом и без отрыва от производства, бригадного и индивидуального обучения без отрыва от производства, когда на 3-6 месяцев молодой рабочий прикрепляется к высококвалифицированному рабочему.
Инженерно-техническим работником (ИТР) необходимо повышать свою квалификацию не реже 1 раза в 5 лет.
Непосредственно работа по управлению трудовой дисциплиной начинается с анализа причин ее нарушений, выявления недостатков (правил внутреннего распорядка, ответственности за результаты труда).
Укрепление дисциплины осуществляется по нескольким направлениям. Административные средства воздействия включают замечание, выговор, перевод на нижеоплачиваемую должность, увольнение за нарушение дисциплины, частичное или полное лишение премии. Важная роль в укреплении дисциплины принадлежит трудовому коллективу.
Вопросы для самопроверки знаний
- Какие вопросы включает организация труда?
- На какие элементы делится рабочее время?
- Какие показатели характеризует использование рабочего времени?
Тема 8. Производственные ресурсы предприятия автосервиса
Каждое предприятие обладает уставным капиталом, который состоит из основных фондов и оборотных средств.
Основные фонды подразделяются на две группы: основные производственные и непроизводственные фонды.
Основные производственные фонды – это средства труда, участвующие в процессе производства длительное время, сохраняющие при этом свою натуральную форму, их стоимость переносится на готовую продукцию постепенно, частями, по мере использования. К производственным фондам относятся основные фонды промышленного, строительного, химического, основные фонды сельскохозяйственного назначения, связи, торговли, транспорта и других видов материального производства.
Непроизводственные фонды находятся на балансе предприятия, однако они не участвуют в процессе производства и не переносят своей стоимости на продукт. К ним относятся жилые здания, поликлиники, детские учреждения, клубы, то есть непроизводственные основные фонды, предназначенные для обслуживания нужд жилищно-коммунального хозяйства, здравоохранения, просвещения, культуры.
От эффективного использования основных фондов зависит финансовое состояние, конкурентоспособность предприятия, технический уровень и качество продукции.
8.1. Структура основных производственных фондов
В зависимости от назначения и выполняемых функций основные производственные фонды промышленности подразделяются на следующие группы:
- здания;
- сооружения;
- передаточные устройства;
- силовые машины и оборудование;
- рабочие машины и оборудование;
- транспортные средства;
- инструмент;
- производственный инвентарь.
Соотношение отдельных групп основных производственных фондов в их общем объеме представляют производственную структуру основных фондов, в которой выделяют активную и пассивную части.
Рабочие машины, оборудование, приборы, инструменты принимают непосредственное участие в процессе производства, прямо влияют на величину производственной мощности, объем выпускаемой продукции и поэтому относятся к активной части основных производственных фондов. Здания, сооружения оказывают косвенное влияние на величину производственной мощности, объем продукции и поэтому называются пассивными элементами основных производственных фондов. Под совершенствованием структуры основных фондов понимается процесс увеличения в общем объеме активной части за счет пассивной.
Основные производственные фонды предприятий совершают хозяйственный кругооборот, который состоит из следующих стадий: износ основных фондов, амортизация, накопление средств для их полного восстановления, замена фондов путем осуществления капитальных вложений (реальных вложений предприятий).
8.2. Оценка и учет основного капитала предприятия
Учет и планирование воспроизводства основных фондов осуществляется как в стоимостных, так и в натуральных показателях. Общий размер основного капитала может быть определен только в денежном выражении. Стоимостная (денежная) оценка необходима для анализа динамики основных фондов, установления величины износа, амортизационных начислений, расчета себестоимости продукции и рентабельности производства. Оценка основных фондов в натуральных показателях ведется для расчета производственной мощности, определения их технологического и возрастного состава, для планирования предупредительно ремонта и модернизации. Способы оценки основных средств зависят от времени приобретения и от их состояния. В зависимости от времени приобретения различают первоначальную и восстановительную стоимость. В зависимости от состояния – полную, остаточную и ликвидационную.
Первоначальная стоимость формируется в момент поступления объектов в эксплуатацию по фактическим и ценам и складывается из затрат на их приобретение, сооружение и изготовление, включая расходы по подготовке, монтажу и установке.
Восстановительная стоимость – это стоимость воспроизводства основных фондов в современных условиях, как правило, устанавливается в ценах, действовавшим в момент переоценки фондов.
Остаточная стоимость – это разница между первоначальной стоимостью и суммой износа, которому подвергаются основные фонды.
Ликвидационная стоимость – это стоимость реализации демонтированной техники, изношенной и снятой с производства, обычно цена металлолома.
Среднегодовая стоимость основных фондов определяется на основе первоначальной стоимости с учетом их ввода и ликвидации по следующей формуле:
Фср = Фнач +
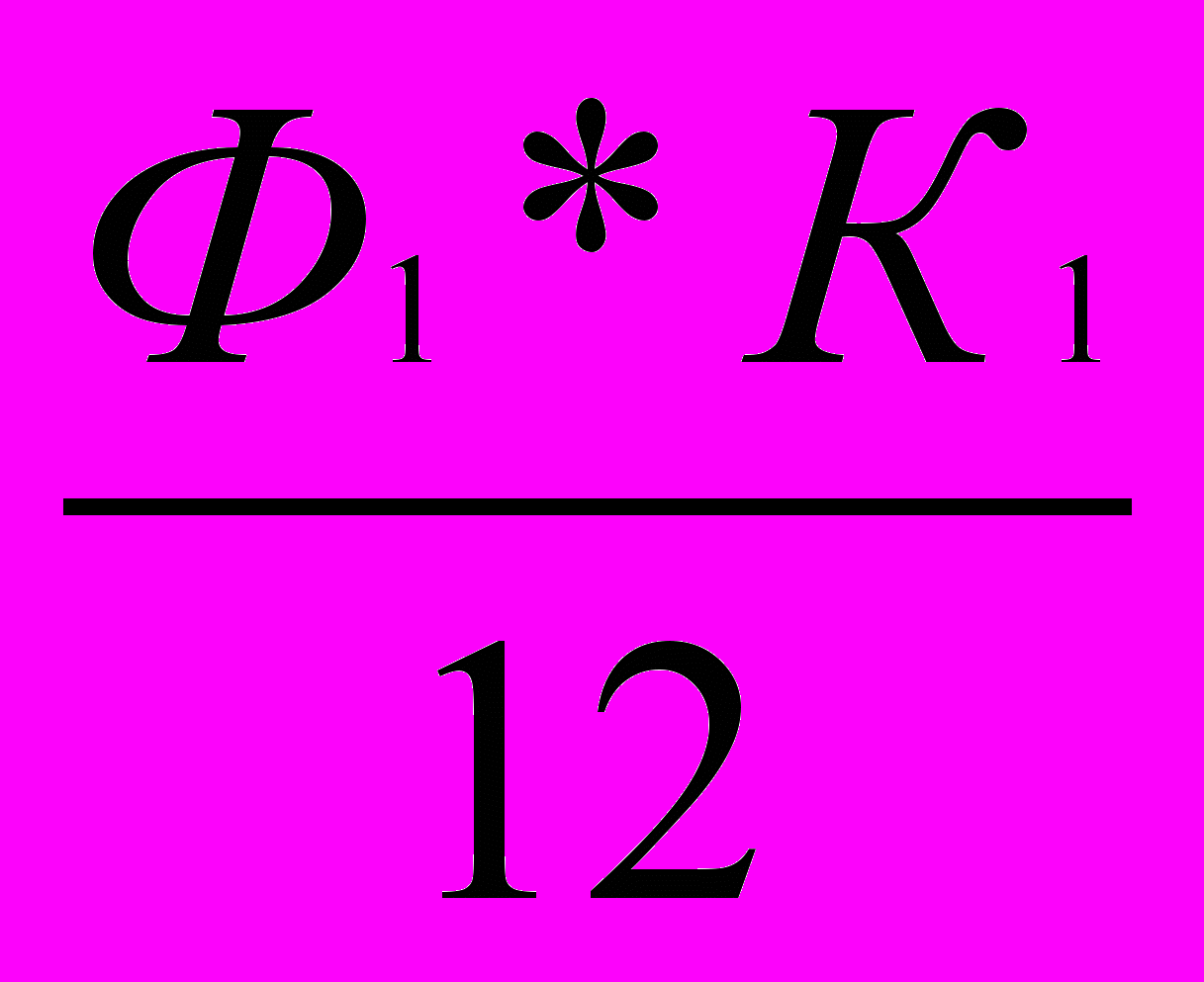
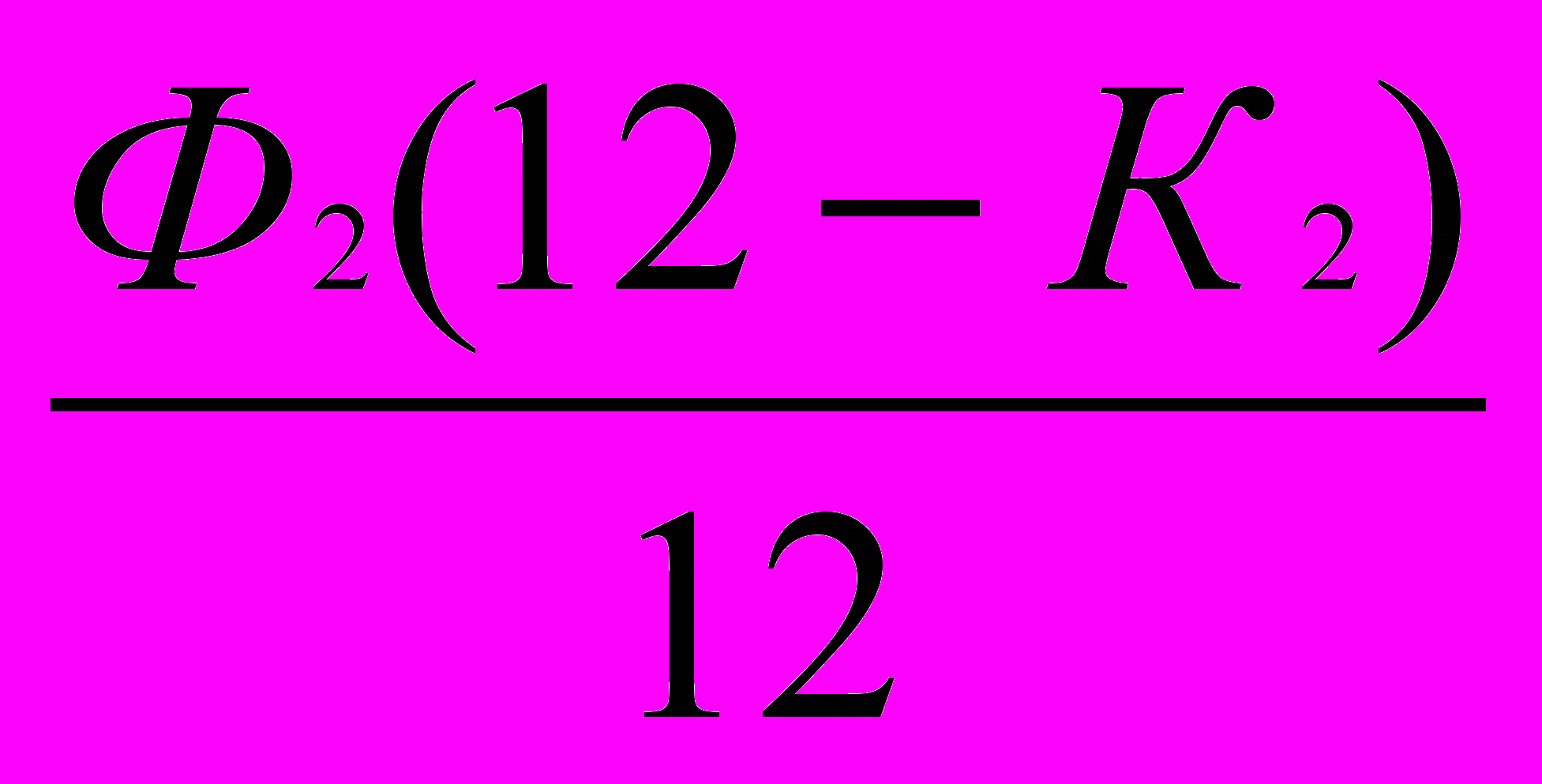
где Фср – среднегодовая стоимость основных фондов;
Ф нач – стоимость основных фондов на начало года;
Ф1 – стоимость введенных фондов;
Ф2 – стоимость выбывающих основных фондов;
К1 – число месяцев работы в год введенных основных фондов;
К2 – количество месяцев работы в год выбывших основных фондов.
Между переоценками основные фонды учитываются на предприятии по смешанной (балансовой) стоимости. Остаточная стоимость основных фондов используется при расчете эффективности их замены.
При переоценке основных средств устанавливается полная восстановительная стоимость на дату переоценки, т.е. полная стоимость новых основных средств, аналогичных оцениваемым.
Переоценка фондов требует значительных материальных и временных затрат и производится на основе специальных нормативных актов правительства Республики Беларусь.
Применяют следующие виды переоценки:
- по коэффициентам пересчета государственных статистических органов;
- на основе рыночной стоимости объекта. Как правило, это стоимость инвестиций, необходимых для технического перевооружения и модернизации объекта с целью освоения инновационных технологий и выпуска конкурентоспособной продукции.
В соответствии с Положением о порядке переоценки основных средств организации Национального статистического комитета Республики Беларусь стоимость основных средств можно определить следующими методами:
1. Определение восстановительной стоимости основных средств методом прямой оценки с использованием сведений о стоимости производства аналогичных видов основных средств от организаций-изготовителей (с учетом расходов по приобретению, доставке, монтажу и установке), торгующих организаций, оценщиков, используя сведения о ценах информационных бюллетеней без налога на добавленную стоимость.
2. Определение восстановительной стоимости основных средств индексным методом путем отнесения основных средств к определенным группам и видам шифров норм амортизации и умножая первоначальную стоимость объекта на коэффициент (индекс) пересчета стоимости каждого объекта основных средств. Для объектов лизинга их первоначальная стоимость умножается на коэффициент (индекс), соответствующий дате ввода в эксплуатацию. Если договор лизинга закончен, то вначале определяется их восстановительная стоимость согласно указанному Положению, а затем применяется коэффициент (индекс) пересчета.
3. Определение восстановительной стоимости основных средств методом пересчета их валютной стоимости осуществляется путем пересчета стоимости таможенных платежей, иных затрат по приобретению, доставке, монтажу и установке, которые уплачивались в белорусских рублях, в иностранную валюту по курсу Национального банка Республики Беларусь на момент их уплаты и прибавления этой стоимости к валютной стоимости объекта. Рассчитанная таким образом первоначальная стоимость объекта в иностранной валюте пересчитывается в белорусские рубли по курсу Национального банка Республики Беларусь.
4. Определение суммы износа и остаточной стоимости основных средств при переоценке осуществляется следующим образом. Сумма износа, по объектам, переоценку которых организация осуществляла самостоятельно, определяется, исходя из восстановительной стоимости, полученной в результате переоценки, и степени (процента) их износа по данным бухгалтерского учета до проведения переоценки.
Остаточная стоимость основных средств определяется как разность между восстановительной стоимостью и переоцененной суммой износа. Пропорциональное соотношение остаточной стоимости и суммы износа после переоценки должно сохраняться по каждому объекту таким же, как и до переоценки.
По объектам основных средств, переоценка которых осуществлялась с привлечением оценщиков, организация может по своему усмотрению: либо рассчитать самостоятельно сумму износа и остаточную стоимость каждого объекта, либо принять как результат переоценки сумму износа и остаточную стоимость, определенные оценщиком.
Результаты переоценки влияют на эффективность финансовой деятельности предприятий. Они отражаются при установлении налога на имущество, в размере амортизационных отчислений, следовательно, налогооблагаемой прибыли.
Многие предприятия не имеют денежных средств для приобретения основных фондов (оборудования, транспортных средств, зданий и др.), поэтому они вступают в арендные отношения с собственниками этих средств (арендодателями).
Арендные отношения – это передача и получение основных средств в аренду (имущественный наем) путем заключения договора, по которому одна сторона (арендодатель) обязуется предоставить другой стороне (арендатору) имущество во временное пользование за определенное вознаграждение.
Аренда может быть текущей и долгосрочной. В бухгалтерском учете объект аренды числится на балансе арендодателя, который продолжает начислять амортизацию (износ), платить налог на имущество.
Различают долгосрочную аренду без передачи права собственности и с передачей права собственности (лизинг).
8.3. Нематериальные активы: сущность, виды и способы формирования
К основному капиталу относятся нематериальные активы – долгосрочные инвестиции.
Нематериальные активы являются результатом интеллектуального труда. Как правило, они не обладают традиционным физическим содержанием, но принимают участие в хозяйственной деятельности предприятия и могут приносить ему доход.
В составе нематериальных активов включаются их следующие виды:
- расходы на учреждение и расширение предприятия;
- продукты научно-исследовательских и опытно конструкторских работ (НИОКР);
- права на объекты интеллектуальной и промышленной собственности, в том числе на изобретения, патенты, лицензии, фирменные наименования и товарные знаки (эмблема, рисунок или символы, зарегистрированные в установленном порядке);
- ноу-хау – совокупность технических, технологических, управленческих, коммерческих знаний, оформленных в виде технической документации; описания накопленного производственного опыта, являющиеся предметом инновации, но не запатентованные;
- авторские права;
- права на промышленные образцы и модели;
- права на использование компьютерных программных продуктов;
- приобретение предприятием права пользования отдельными ресурсами (природными, земельными и др.);
- деловая репутация.
Классификация нематериальных активов по способам формирования приведена в таблице 8.1.