1. Основные определения курса
Вид материала | Документы |
- Тема: Основные понятия и определения, 164.71kb.
- Краткое содержание курса, 84.97kb.
- Надежность в технике основные понятия. Термины и определения гост 27. 002-89 государственный, 583.36kb.
- № п./п. Темы; основные вопросы уроков, 330.51kb.
- Гост 60-2003 издания. Основные виды. Термины и определения, 62.99kb.
- Программа курса «Основы радиоэлектроники», 15.36kb.
- Методические указания и контрольные задания по физике для слушателей второго курса, 1404.08kb.
- Тема предмет курса. Основные определения. Классификация, 541.45kb.
- Расторгуев С. П. Информационная война, 5412.32kb.
- Сибид. Библиографическая деятельность. Основные термины и определения сибид. Библиографическое, 76.18kb.
Система УЗ «минимум-максимум»
В данной системе заказы производятся в фиксированные плановые моменты, но при условии, что текущий запас в этот момент <= установленного минимального уровня. Объем заказа определяется по принципу восполнения запаса до максимального уровня с учетом потребления за время поставки.
Входные параметры:
- ν – интенсивность, скорость потребления запаса (тов/д)
- S – затраты на хранение запаса (р/тов*д)
- k – затраты на осуществление заказа (р)
- tд – вредя доставки (д)
- tз – максимально возможная задержка (д)
Выходные параметры:
- τ – период поставки
- Hmin – минимальный (пороговый)уровень запаса
- Hmax – максимальный желательный запас
- Q – то что мы заказали
Пороговый уровень запаса в системе выполняет роль минимального уровня. Если в установленный момент этот уровень пройден, то заказ подается, иначе нет. Отслеживание порогового уровня, а также выдача заказа производится только через заданный интервал времени. Таким образом, данная система работает лишь с 2 уровнями запасов. Система мин-макс содержит элементы системы с фиксированным периодом и заказом. Система ориентирована на учет запасов и издержки на оформление заказа настолько значительны, что становятся соизмеримы с потерями от дефицита.
- Вытягивающие и выталкивающие логистические системы
Выталкивающая система (централизованная система) – это такая организация движения материального потока, при которой материальные ресурсы передаются с предыдущей операции на последующую в соответствии с графиком. Таким образом, материальные ресурсы выталкиваются с одного звена лог.цепи в другую под воздействием управляющей системы.
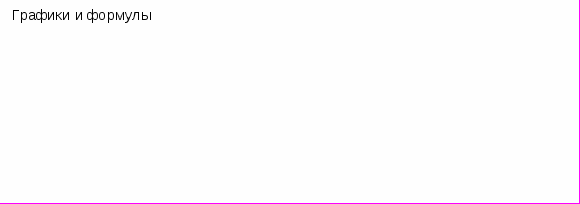
ЦОПП формирует производственное расписание для каждого подразделения. Выталкивающая система является традиционно используемой в ПП. Каждой операции в общей операции в общем расписании установлено время, к которому она должна быть завершена. Полученный продукт проталкивается дальше и становиться запасом незавершенного производства на входе след.операции. Такой способ организации игнорирует то, что в настоящее время делают следующие операции. В результате могут появляется задержки в работе и рост запасов незавершенного производства.
Вытягивающая система – это такая организация материального потока, при которой материальные ресурсы подаются (вытягиваются) на следующую технологическую операцию с предыдущей по мере необходимости. А поэтому жесткий график движения материального потока отсутствует. Размещение заказов на пополнение запасов материальных ресурсов или готовой продукции происходит, когда их количество достигает критического уровня.
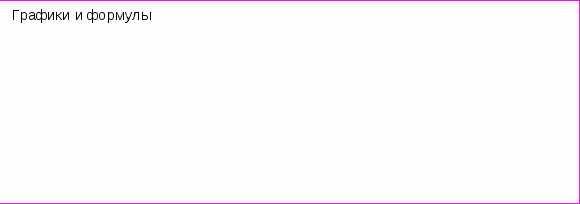
ЦОПП контролирует выпуск готовой продукции. Вытягивающая система основана на вытягивании продукта предыдущей операции с последующую в тот момент времени, когда последующая операция готова к работе. То есть когда в ходе i-ой операции заканчивается обработка одной единицы продукции, посылается сигнал, требующий на предыдущей операции, а она отправляет олбрабат.единицу дальше только тогда, когда получит на это запрос.
- Система планирования потребностей в материалах (MRP)
MRP- material requirement planning. – это система централизованного планирования выталкивающего типа
Основные задачи
- Удовлетворение потребностей в материалах, компонентах материалов и продукции для планирования производства и доставки потребителю
- Поддержание низкого уровня запасов материальных ресурсов, незавершенного производства, готовой продукции
- Планирование производственных операции, графиков закупки и доставки
Схема работы мрп:
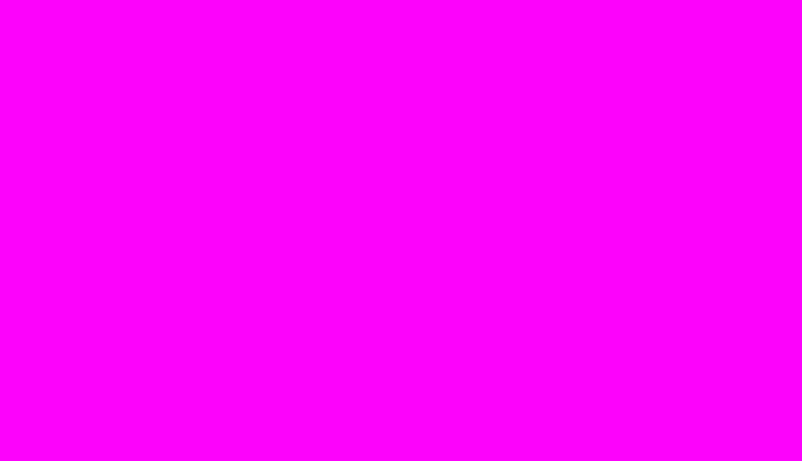
Данная система строится на основе заданного производственного расписания, сформированного по заказам потребителей и на прогнозе спроса, который определяет сроки и объемы производства конечного изделия.
Изделие | Недели планового периода | |||||||
A | 1 | … | 8 | 9 | 10 | 11 | 12 | 13 |
- | … | 50 | - | - | 50 | - | 100 |
Производственное расписание на изготовление изделия А.
Затем система последовательно определяет время и необходимое кол-во материальных ресурсов для выполнения производственного расписания. Для расчета необходимы следующие данные, хранящиеся в системе MRP:
- О материальных ресурсах и спецификации на изделия (состав изделия), содержащие всю информацию о номенклатуре и основных параметрах сырья, материалов, компонентов, полуфабрикатов и тд, которые необходимы для изготовления (сборки изделия)
- О нормативных сроках изготовления каждого элемента и компонента изделия
- О нормах расхода материальных ресурсов на единицу изготавливаемой детали, сборочного компонента или готового изделия
- О наличных запасах материальных ресурсов
Процесс создания конечного изделия (А) включает изготовление или закупку всех деталей, сборку всех сборочных единиц (узлов, агрегатов, механизмов), отладку и контроль готового изделия. При этом предполагается, что различные детали изготавливаются одновременно, а длительность совокупного производственного цикла определяется по ведущей детали. Тогда производственный цикл изделия рассчитывается по формуле:
Тц=Тцд+Тцс, где Тцд – производственный цикл изготовления ведущей детали, те детали, у которой производственный цикл наиболее продолжительный, Тцс – производственный цикл сборочных и испытательных работ.
Схема изготовления изделия (состав изделия) представляется в виде уровнего построения изделия.
А | ||||
В(1) | С(1) | |||
Д(2) | С(2) | E(1) | F(1) | |
E(1) | F(1) |
Расчет количества составных элементов для сборки изделия А в необходимом количестве представлен в таблице
Элемент | Кол-во | |
A | 50 | 100 |
B | 50 | 100 |
C | 150 | 300 |
D | 100 | 200 |
E | 150 | 300 |
F | 150 | 300 |
В соответствии с данными по наличному запасу ресурсов Zi на каждый элемент i (изделие, сборочная ед., деталь) необходимо в рачетах скорректировать истинную (чистую) производственную или закупочную потребность qir исходя из общей полной потребности qiп : qir= qiп-Zi
Заранее определенные нормативы времени изготовления деталей сборочных единиц и сборки готового изделия или времени поставки компонентов от поставщика ti влияет на общую продолжительность цикла изготовления изделия и определяет расчетное опережение срока запуска производства очередного компонента или момента заказа у поставщика необходимых материальных ресурсов.
| ti | Zi |
A | 1 | 10 |
B | 2 | 20 |
C | 3 | 0 |
D | 1 | 100 |
E | 1 | 10 |
F | 1 | 50 |
ti – время обработки, нед. Zi – в наличии.
Достионства MRP
- Уровень запасов низкий и повышается только перед выполнением заказа (экономия финансов, площади, персонала)
- MRP оперирует данными не о прошлом употреблении а о будущих потребностях
- Эффект автоматизации (экономия персонала и времени)
Недостатки
- Работы мрп не учитывают состав оборудования производственных цехов и участков (производственные мощности) – это один из основных недостатков, предполагающих максимальное запараллеливание работ
- Большой объем подробной и точной информации => высокая длительность внедрения
- Низкая гибкость не позволяет оперативно реагировать на внешние изменения
- Наличие очень сложных систем управления, большой размерности и загруженности
- Дорогостоящее и долговременное внедрение (≈105$, ≈10 мес)
- Системы планирования производственных ресурсов (MRP II) и планирования потребностей предприятия (ERP)
С
Управление запасами
Управление производством
Управление производственными мощностями
истема MRP не учитывает производственные мощности, их загрузки, стоимость рабочей силы и тд. Поэтому основным моментом в развитии систем данного класса было включение в новую систему MRP2 модуля планирования мощностей на уровне внутрицеховом и межцеховом.
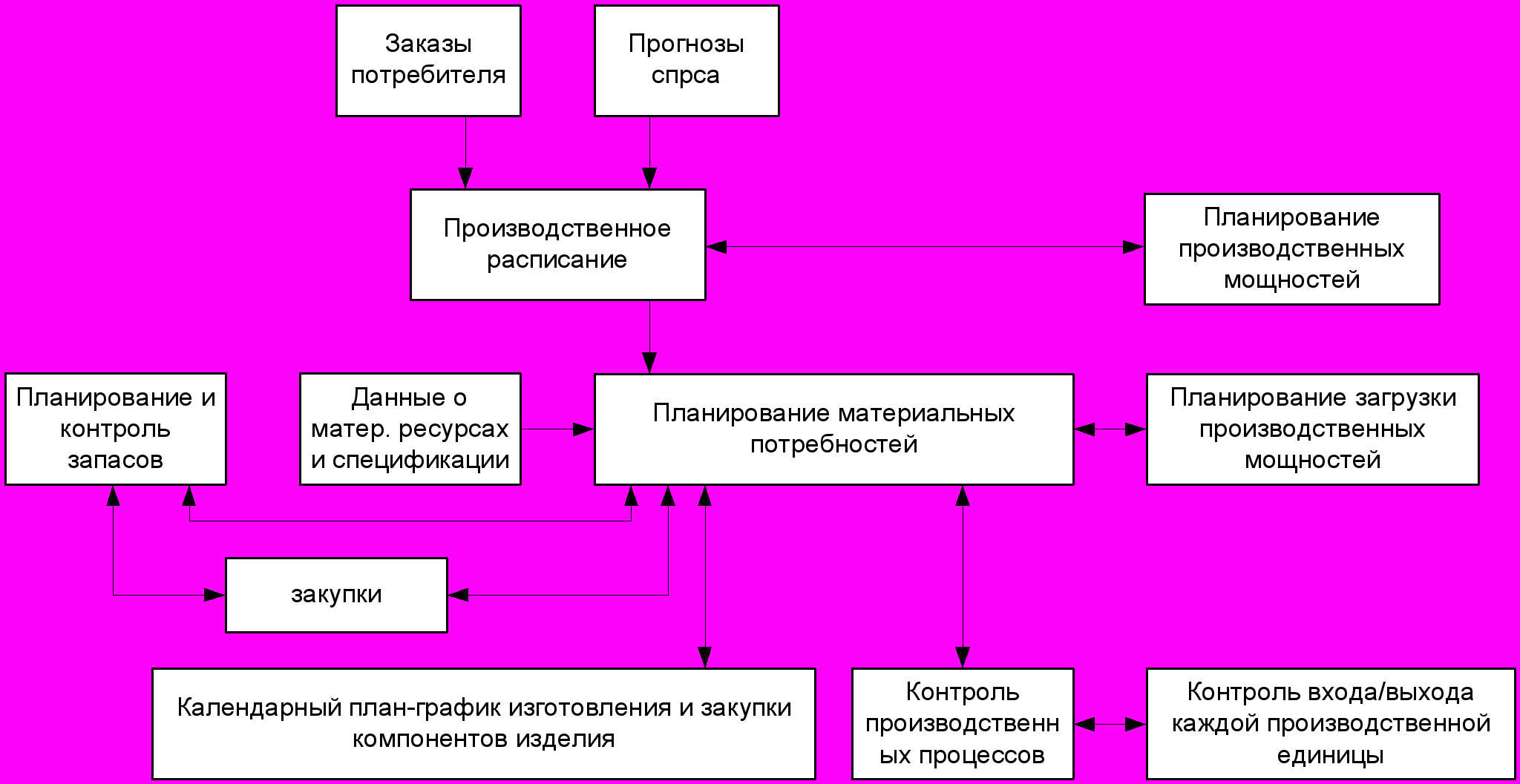
Последовательность работы системы MRP2
- По данным исследования рынка и прогноза спроса на продукцию составляется предварительное производственное расписание
- Запускается процедура предпроизводственного планирования мощностей для быстрой проверки выполнимости составленного расписания. С точки зрения производственных мощностей и существующих технологий.
- Если предварительное производственное расписание выпуска конечных изделий признается реально осуществимым, то оно становиться утвержденным производственным расписанием. В противном случае в предварительное производственное расписание вносятся изменения, и оно подвергается повторному тестированию с помощью процедуры планирования мощностей.
- Далее запускается процедура MRP, формирующая календарный план-график составления компонентов изделия. Закупки компонентов изделия с учетом запасов не складе.
- Запускается процедура планирования загрузки производственных мощностей, которая формирует расписание производственных работ, описывающих в дальнейшую производственную деятельность.
- По этим двум документам оценивается потребность в других средствах для осуществления производственной деятельности, то есть рассчитываются операционные расходы на закупки материалов производственной природы, зарплата и др. Далее в соответствии со сформированным расписанием начинается реальная производственная деятельность. При этом MRP2 осуществляет оперативное управление производственным процессом, контролирует выполнение плановых заданий и при необходимости вносит коррективы в действующие планы.
Система на основе сравнения фактических и нормативных показателей анализирует протекание производственного процесса. Например, для контроля выполнения работ система MRP2 в течение всего планового периода отслеживает величину производительности каждой производственной единицы. Аналогично система отслеживает потребление производственными единицами материалов и комплектующих и регистрирует отклонение фактических показателей потребления по каждой производственной единице. Это позволяет быстро диагностировать ситуацию, когда производственная единица не развивает плановую производительность из-за недостаточного снабжения материалом. Анализируя ход производственного процесса, MRP2 ежедневно формирует сменные задания, которые отсылаются руководителям. Сменные задания отражают последовательность проведения рабочих операций над сырьем и комплектующими на каждой единице производственных мощностей и длительность этих операций. Точно также формируются ежедневные задания на закупку/поставку сырья и комплектующих. MRP2 регулирует работу снабженческих, сбытовых и складских структур предприятий.
Планирование потребностей предприятий
Основной принцип - создание единого хранилища данных, которое содержит всю корпоративную информацию. Производственные данные, данные по персоналу и тд. Идея и интерпретация всех информационных систем используемых на предприятии в единую систему. Наличие таких возможностей устраняет необходимость передачи данных от одной системы к другой, а тк же обеспечивает одновременно доступность информации любого числа сотрудников предприятия, обладающих соответствующими правами доступа.
Следующим направлением развития системы MRP2, нашедшим сове отражение в концепции ERP явилась необходимость распространения MRP2 на предприятия логистической цепи. Если система ERP определила требуемый объем поставок материала, то электронный обмен данными может связать ERP с системой поставщика. Тогда поставщик, зная когда и сколько он сможет доставить материала может начать составлять расписание для своих операций, чтобы успеть к сроку. Если поставщики второго уровня связаны с системой ERP поставщиков первого уровня, то они так же могут начать свои приготовления. Т.о. информация перемещается по цепи поставок, обеспечивая интегрированное планирование в пределах всей логистической цепи.
- Концепция «точно в срок» (JIT)
Концепция была разработана в 70-е компанией тайота. Внедрение системы занято около 15 лет, что является рекордом среди логистич.с-м.
Основная идея выталкивающей системы JIT заключается в следующем: если производственное расписание задано, абстрагируясь от спроса и заказов, то можно так организовать движение МП, что все материалы, компоненты и полуфабрикаты будут поступать в необходимом количестве в нужное место на сборочной линии к точно назначенному сроку для производства или сборки готовой продукции. При этом заказы, замораживающие денежные средства предприятия ему не нужны.
Закупка самого современного оборудования, модернизация площадей, повышение квалификации персонала.
Логистическая концепция «точно в срок» характеризуется следующими основными чертами:
- Минимальные запасы материальных ресурсов незавершенного производства готовой продукции
- Короткий производственный цикл
- Небольшие объемы производства готовой продукции и пополнение запаса
- Взаимоотношением по закупочным материалам ресурсов с небольшим числом надежных поставщиков и перевозчиков
- Эффективной информационной поддержкой
- высоким качеством готовой продукции вплоть до остановки производства любым рабочим предприятия, если он не сможет исправить брак своими силами
- Качество продукции контролируется самим рабочим, а не отделом ОТК как при традиционном производстве.
- Может существовать только в непрерывном развитии и совершенствовании
Достоинства JIT
- На некоторых предприятиях с жит произошло сокращение запасов на 90%, площади до 40%, затраты на снабжение до 15%
- Сокращение времени производства продукции
- Повышение производительности
- более высокая загрузка оборудования
- Повышается качество материалов и готовой продукции
- Формирование более ответственного отношения к работе сотрудников
- Улучшение отношения с поставщиками
Недостатки
- Высокие первоначальные инвестиции и затраты на реализацию JIT : Покупка качественного совершенного дорогостоящего современного оборудования, затраты на подготовку специалистов и заработная плата, повышение затрат на производство, в следствие небольшие партии выпуска.
- Неспособность справляться с непредвиденными обстоятельствами (забастовки, поломка оборудования, задержки поставок)
- Зависимость от высокого качества поставленных материалов
- Необходимость работать в стабильном производстве, не смотря на часто колеблющийся спрос
- Снижение гибкости в удовлетворении часто меняющихся запросов потребителей.
- Неспособность отдельных поставщиков работать в режиме JIT
- Проблема привязки JIT к другим информационным системам партнеров
- Необходимость изменения планируемых сооружений
- Работа сотрудников в обстановке повышенного стресса
- Отсутствие духа сотрудничества и доверия между ними
- Неспособность отдельных сотрудников взять на себя б’ольшую ответственность
- Необходимость применения самых современных методов, технологий производства и промышленного оборудования
- Необходимость найма высококвалифицированных сотрудников