Viii. Переработка фракций сырого бензола
Вид материала | Лекция |
9.2. Технология разделения смол |
- X. переработка сырого бензола, 321.46kb.
- Vii переработка химических продуктов термической переработки твердых горючих ископаемых, 256.07kb.
- Vii улавливание и получение сырого бензола, 353.99kb.
- Ароматические углеводороды. Бензол представитель аренов. Строение молекулы и физические, 54.51kb.
- Анализа состояния конкуренции на рынке сырого молока. I. Общие положения Анализ проводился, 348.46kb.
- Термохимия растворения ccl 4, бензола и его производных в индивидуальных и смешанных, 298.7kb.
- Viii переработка жидкого топлива, 647.45kb.
- Зао «Куйбышевазот» Строительство производства бензола с сырьевым складом, 1760.62kb.
- Примерный план Восточные славяне в древности. Общественный строй и культура древних, 11219.83kb.
- Изучение особенностей реакций гидродесульфирования и гидрирования компонентов дизельных, 426.94kb.
9.2. Технология разделения смол
Для разделения смолы можно использовать два приема (рис. 6.7) – фракционное испарение (а) и однократное испарение с последующей фракционной конденсацией паров фракций (б).
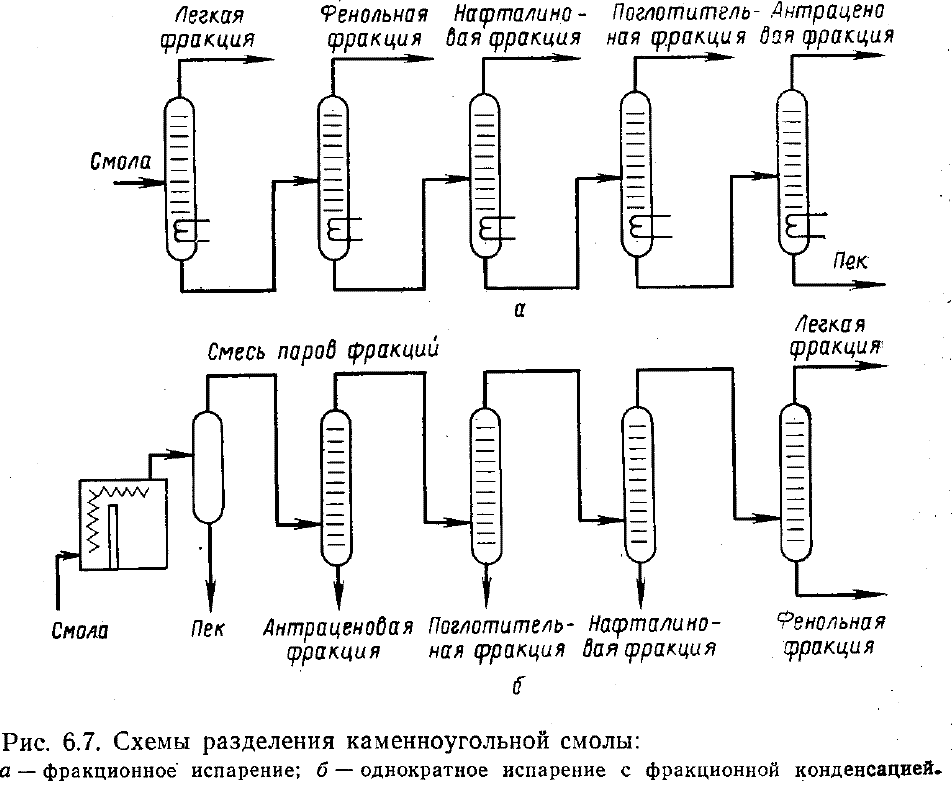
Рис. 6.7. Схемы разделения каменноугольной смолы:
а – фракционное испарение; б – однократное испарение с фракционной конденсацией
При использовании фракционного испарения в серии ректификационных агрегатов последовательно отбираются легкая фракция (до 170°С), фенольная (170–200°С), нафталиновая (200–230°С), поглотительная (230–300°С), антраценовая (300–360°С); в качестве донного продукта из последнего по ходу агрегата отводится высококипящий остаток – пек. Такие периодические схемы переработки смолы, в основе которых было фракционное испарение, существовали еще в 50-е годы. Единственным достоинством процесса фракционного испарения (естественно, при использовании колонн достаточно высокой эффективности) была возможность тщательного извлечения низкокипящих компонентов из высококипящих. Так, при подобном разделении было гарантировано, например, отсутствие компонентов легкого масла в нафталиновой фракции.
Главным недостатком такой схемы является высокая температура в нагревателях колонн. Содержание пека в исходной смоле составляет около 60%, поэтому именно температуры кипения компонентов пека решающим образом влияют на температуру в нагревателях даже при отборе низкокипящих фракций. При этом возникают трудности с подбором греющего агента, температура которого должна быть всегда на 15–20°С выше самой высокой температуры низа колонны (условие создания необходимого теплового напора). Кроме того, при использовании фракционного испарения самому длительному нагреву подвергают наиболее высококипящие соединения, которые в наибольшей степени подвержены термическим превращениям при нагревании. В связи с этим при современной переработке смолы, как и при переработке нефти, преимущественно используют сочетание однократного испарения с фракционной конденсацией.
Как видно из рис. 6.7 (б), при нагревании в змеевике образуется паровая фаза, находящаяся в равновесии с жидкой фазой. В паровую фазу в соотношениях, определяемых давлением насыщенных паров при заданных температурах, переходят все компоненты смолы. Одновременно в остатке в соотношениях, определяемых также условиями равновесия, находятся все компоненты смолы. Таким образом, в пеке может оставаться какое-то незначительное количество компонентов легкой фракции. Глубина отгона, т.е. степень перехода компонента в паровую фазу при однократном испарении, при тех же температурах больше, чем при фракционном испарении.
На рис. 6.8 приведены кривая истинных температур кипения, полученная при четком фракционировании смолы на лабораторной колонне периодического действия, и кривая однократного испарения, характеризующие влияние температуры на глубину отгона.
Паровая и жидкая фазы после змеевика трубчатой печи разделяются в сепараторе (испарителе), где происходит дополнительное испарение жидкой фазы за счет снятия тепла перегревав (в змеевике создается повышенное давление паров, а при входе парожидкостной смеси в испаритель происходит дросселирование – снижение давления до атмосферного).
Оптимальная температура в испарителе 370–390°С, что соответствует температуре 390–405°С на выходе из змеевика. Уменьшение температуры, необходимой для достижения определенной полноты отбора, при использовании однократного испарения по сравнению с применением фракционного испарение объясняется тем, что пары низкокипящих фракций снижают давление паров высококипящих фракций, необходимое для переходу их в паровую фазу (аналогия с перегонкой при подаче водяного пара.
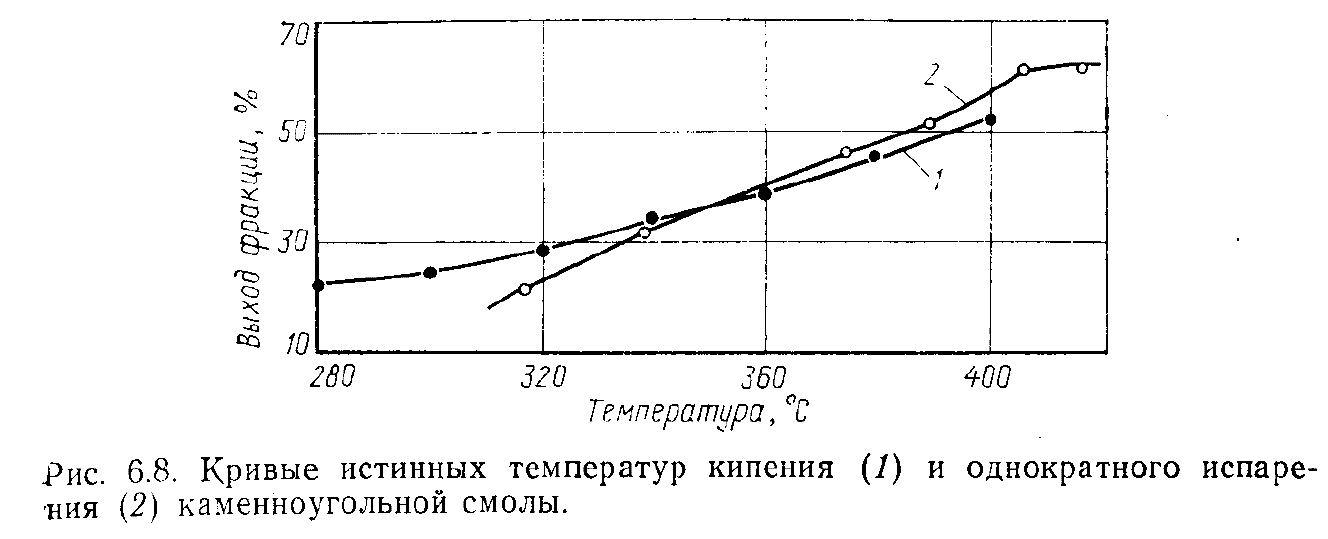
Рис. 6.8. Кривые истинных температур кипения (1) и однократного испарения (2) каменноугольной смолы
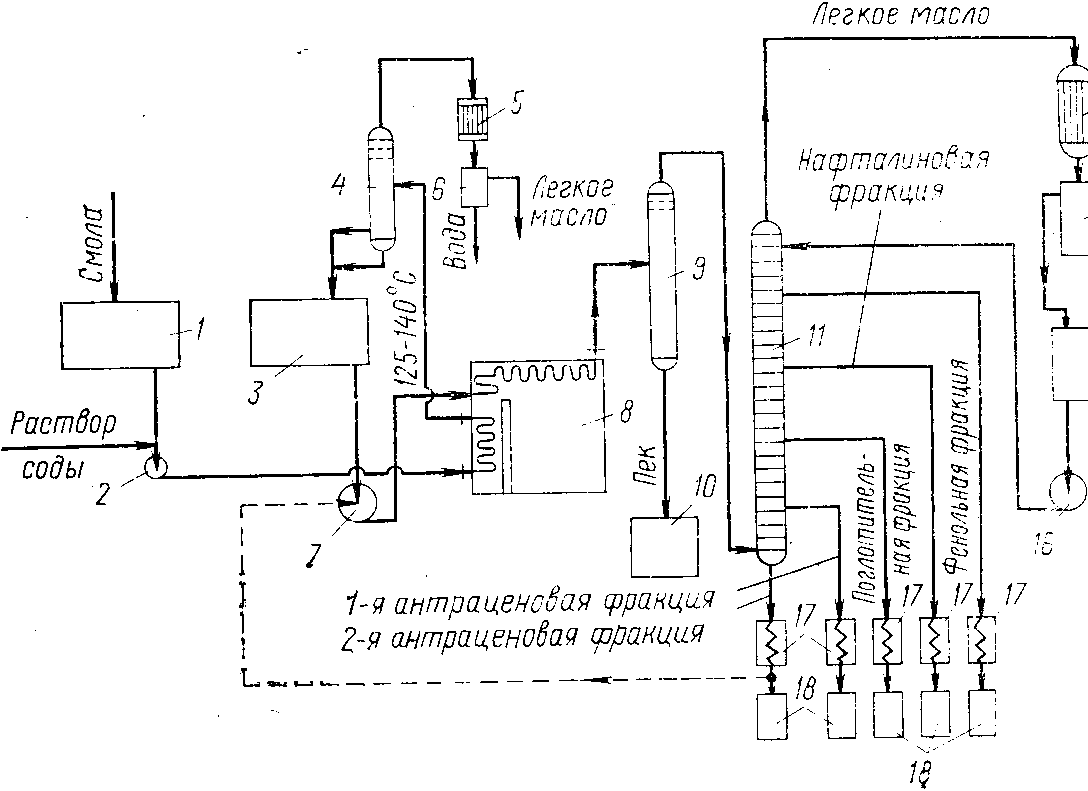
Рис. 6.9. Технологическая схема фракционирования каменноугольной смолы в одноколонном агрегате:
1 – хранилище смолы; 2, 7, 16 – насосы; 3 – хранилище обезвоженной смолы; 4 – испаритель 1 ступени; 5, 12 – конденсаторы; 6, 13 – сепараторы; 8 – трубчатая печь; 9 – испаритель II ступени; 10 – емкость пека; 11 – фракционная колонна; 14 – промежуточная емкость; 15, 18 – сборники; 17 – холодильники
На рис. 6.9 представлена наиболее распространенная в настоящее время технологическая схема обезвоживания и ректификации каменноугольной смолы.
Подобная технологическая схема используется и при переработке нефти и многих других смесей высококипящих продуктов. От канонических схем ректификации эта схема отличается следующим:
1) для нагревания многокомпонентной смеси используют трубчатую печь, в которой и осуществляется однократное испарение;
2) традиционные ректификационные схемы предполагают подачу питания на колонну в виде жидкой фазы на одну из средних тарелок колонны (тарелка питания, разделяющая ректификационную колонну на две секции–укрепляющую и исчерпывающую), тогда как в предлагаемой схеме питание подается в виде паровой фазы на нижнюю тарелку колонны;
3) во всех схемах ректификационная колонна орошается сверху, а избыточное тепло, необходимое для испарения этого орошения, подается снизу. При ректификации смол отсутствует специальный подвод избыточного тепла. Тепло, необходимое для проведения процесса ректификации, подводится лишь с каменноугольной смолой, которая поступает в колонну из трубчатой печи;
4) обычно при разделении методом ректификации любых смесей продукты отводятся либо в паровой фазе (сверху колонны), либо в жидкой фазе (снизу колонны), причем их качество можно регулировать, изменяя либо орошение, либо подачу тепла. При этом для разделения смеси из N компонентов необходимо использовать (N–1) колонн. Здесь же из одной колонны отбирают шесть различных продуктов, причем четыре наиболее представительные фракции отводятся в виде жидкой фазы путем бокового отбора.
При использовании однократного испарения из испарителя выходит смесь паров всех фракций при температуре 370–380°C. Между тем температура отбора фракций составляет: соответственно фенольной 170–180°С, нафталиновой 205–210°С, поглотительной 250–260°С, антраценовой 280–290°С. Таким образом, во фракционную колонну поступают перегретые пары фракций. Кроме того, проходя колонну, пары фракций последовательно конденсируются, выделяя тепло конденсации. Таким образом, дополнительным источником тепла, необходимого для испарения холодной флегмы, подаваемой на орошение и осуществление ректификации, служит тепло конденсации и тепло перегрева фракций.
В отличие от обычных схем все тепло, необходимое для осуществления процесса ректификации смолы, подается в колонну с питанием парами, нагретыми в трубчатой печи, и невозможно изменить его количество в заметных пределах. Увеличить резерв тепла можно лишь снижая теплопотери, т.е. увеличив термоизоляцию колонны, трубопроводов и других аппаратов.
По аналогии с подобными схемами в нефтепереработке существует возможность увеличения количества тепла, подводимого во фракционную колонну, путем циркуляции нижнего продукта через отдельную секцию трубчатой печи (так называемый «метод горячей струи»).
Подобная система разделения эффективна в тех случаях, когда содержание низкокипящих фракций невелико и по условиям фазового равновесия они легко отделяются от высококипящих. Тогда низкокипящие примеси во фракциях, отводимых путем бокового отбора, будут незначительными. Такая схема может быть использована, если требования к качеству фракций не очень жесткие, а примеси низкокипящих компонентов не представляют опасности и могут быть даже полезными. И, наконец, схема используется, если организация подвода дополнительного тепла связана с серьезными техническими трудностями, например, если нужно применить греющий агент с очень высокой температурой.
Таким образом, традиционное применение одноколонного агрегата с боковым отводом фракций при ректификации смолы объясняется тем, что ресурсы легкого масла и фенольной фракции невеликий они относительно легко отделяются от наиболее ценной нафталиновой фракции; требования к содержанию низкокипящих фракций в поглотительном масле не очень жесткие, а примеси нафталина (до 10–12%) даже снижают температуру застывания этого масла.
Использование многоколонной схемы фракционной конденсации связано с определенными трудностями, т.к. потребуется несколько подогревателей типа трубчатых печей.
В табл. 6.5 приведены сведения о фракциях, получаемых при использовании традиционной технологической схемы (суммарное число тарелок 48–52) на заводах СССР.
Таблица 6.5. Характеристика фракций каменноугольной смолы
Фракция | Пределы выкипания,°С | Выход, % | Содержание во фракции, % | Степень извлечения, % | |||
нафталин | фенолы | основания | нафталин | фенолы | |||
Легкая | до 170 | 0,6 | 2,0 | 0,5 | 0,8 | 0,12 | 0,17 |
Фенольная | 170–210 | 2,5 | 18,0 | 38,0 | 6,2 | 4,5 | 52,3 |
Нафталиновая | 210–230 | 10,0 | 82,0 | 6,0 | 3,8 | 82,2 | 33,0 |
Поглотительная | 230–300 | 9,5 | 8,0 | 1,5 | 4,5 | 7,6 | 7,8 |
Антраценовая I | 300–360 | 17,4 | 2,5 | 0,7 | 6,7 | 4,4 | 6,7 |
Антраценовая II | 310–440 | 8,0 | 1,5 | – | – | 1,2 | – |
Состав фракций, отводимых путем бокового отбора, можно регулировать, меняя тарелки, с которых они отбираются. Поэтому отбор фракций предусматривается с нескольких соседних тарелок. Однако возможности такого регулирования ограниченны. Более важно регулирование постоянства количества продукта, отведенного боковым отбором. Как известно, главное условие надежной работы аппарата непрерывного действия – стабильность состава и температур на каждой тарелке аппарата. Боковые отборы нарушают распределение потоков флегмы по высоте колонны, делают работу аппарата нестабильной. Поэтому использование регуляторов постоянства расхода фракций позволяет улучшить работу аппарата и качество фракций.
Принципиально улучшение качества фракций возможно при использовании отпарных колонн, в которых либо при подаче острого пара, либо при циркуляции продукта через трубчатую, печь достигается удаление низкокипящих компонентов. При этом содержание нафталина в нафталиновой фракции может быть увеличено до 85–89% при степени извлечения его до 87–90% от содержания в сырье, а переход нафталина в поглотительную фракцию уменьшается до 3–4%.