X. переработка сырого бензола
Вид материала | Лекция |
- Viii. Переработка фракций сырого бензола, 431.56kb.
- Vii переработка химических продуктов термической переработки твердых горючих ископаемых, 256.07kb.
- Vii улавливание и получение сырого бензола, 353.99kb.
- Ароматические углеводороды. Бензол представитель аренов. Строение молекулы и физические, 54.51kb.
- Анализа состояния конкуренции на рынке сырого молока. I. Общие положения Анализ проводился, 348.46kb.
- Термохимия растворения ccl 4, бензола и его производных в индивидуальных и смешанных, 298.7kb.
- Зао «Куйбышевазот» Строительство производства бензола с сырьевым складом, 1760.62kb.
- Федеральный государственный образовательный стандарт среднего профессионального образования, 931.07kb.
- Методические указания и контрольные задания для студентов-заочников по специальности, 1294.44kb.
- Справочник работ и профессий рабочих Выпуск 27 Разделы: "Производство синтетических, 8171.37kb.
ЛЕКЦИЯ 7
X. ПЕРЕРАБОТКА СЫРОГО БЕНЗОЛА
10.1. Состав сырого бензола и характеристика основных
его компонентов
Сырой бензол представляет собой многокомпонентную систему, основными составляющими которой являются одноядерные ароматические соединения – бензольные углеводороды и различные примеси. Основная масса сырого бензола выкипает до 180°С. Выше этой температуры кипят содержащиеся в сыром бензоле легкокипящие погоны поглотительного масла, а также непредельные соединения.
Все входящие в сырой бензол (отгон до 180°С) соединения условно делят на пять групп, содержание и состав которых приведены в табл. 2.
Число различных химических соединений, содержащихся в сыром бензоле, весьма велико. Большинство из них содержатся в крайне незначительных количествах, в чистом виде практического значения не имеют.
Свойства сырого бензола определяются в основном содержанием бензольных углеводородов, а также непредельных и сернистых соединений, количество которых зависит от свойств коксуемой шихты и условий коксования. Основными компонентами сырого бензола являются бензол и его гомологи.
Бензол (С6Н6) – первый член гомологического ряда бензольных углеводородов (СnН2n–6) является основным компонентом сырого бензола, содержание которого достигает 55–80%. Температура кипения бензола 80,1°С. Ценность бензола определяется тем, что он является основным исходным материалом для органического синтеза пластических масс и других высококачественных продуктов.
Таблица 2. Состав сырого бензола
Группа | Основные соединения, входящие в группу | Содержание,% |
Бензольные углеводороды | Бензол, толуол, диметилбензолы (ксилолы), этилбензол, триметилбензолы, этилтолуолы | 80–95 |
Непредельные соединения | Циклопентадиен, стирол, кумарон, инден с гомологами, циклогексен, ме-тилциклогексен | 5–15 |
Сернистые соединения | Сероводород, сероуглерод, тиофен, ме-тилтиофен, диметилтиофены, триметил-тиофены | 0,2–2,0 (считая на серу) |
Насыщенные углеводороды жирного и гидроароматического ряда | Циклопентан, метилциклопентаны, циклогексан, метилциклогексаны, гептан, гексан | 0,3–2,0 |
Прочие | Фенол, азотистые соединения, нафталин | менее 1,0 |
Толуол (С6Н5СН3) – следующий за бензолом по своему содержанию компонент сырого бензола. Температура кипения толуола 110,6°С. Содержание толуола в сыром бензоле зависит от условий коксования и составляет 10–15%.
Ксилол, производимый в ректификационных цехах, является смесью трех изомеров орто-, мета- и пара-ксилола (С6Н4(СН3)2) и этилбензола (С6Н5С2Н5). Температура кипения о-ксилола 144,4°С; м-ксилола 139,1°С и п-ксилола 138,4°С. Содержание ксилолов в сыром бензоле составляет 4–7%.
Триметилбензолы (С6Н3(СН3)3) кипят в интервале температур 164–180°С и обычно выходят из ректификационных цехов в смеси с ксилолами, этилтолуолами, пропилбензолом под названием сольвентов. Триметилбензолы в сыром бензоле представлены – псевдокумолом, с температурой кипения 169,35°, мезитиленом с температурой кипения 164,7°С и гемимелитолом с темпе;-ратурой кипения 176,08°С. Содержание триметилбензолов в сыром бензоле незначительно (0,3–0,7%).
Все бензольные углеводороды в чистом виде представляют собой легкокипящие, бесцветные, прозрачные жидкости, легче воды (плотность при 20°С равна 0,86–0,880 г/см3), не смешиваются с водой и хорошо от нее отстаиваются.
Все бензольные углеводороды чрезвычайно горючи, легко воспламеняются, а их пары с воздухом образуют взрывоопасные смеси. Это требует большой осторожности и определенных мер безопасности при работе с ними.
На переработку сырого бензола больше всего влияет температура кипения. Благодаря значительному различию температуры кипения бензола, толуола, ксилолов и триметилбензолов, разделение их процессом ректификации не представляет особой сложности.
Разность температур кипения соседних пар при давлении 101,3 кПа (760 мм рт. ст.) составляет,°С:
-
Сероуглерод–бензол
33,6
Бензол–толуол
30,5
Толуол–ксилол
27,0
Ксилол–сольвент
25,0
Разность температур кипения изомеров ксилола очень невелика и разделение их посредством ректификации сложно. Поэтому изомеры ксилола выпускаются только в виде смеси.
Непредельные соединения, содержащиеся в сыром бензоле, являются в основном циклическими углеводородами с боковой цепью и без нее, с одной или двумя двойными связями. Для них характерны процессы полимеризации и осмоления, в противоположность весьма устойчивым бензольным углеводородам. Полимеризуясь, непредельные углеводороды образуют смолистые вещества, растворяющиеся в бензольных углеводородах и придающие им желтую окраску различной интенсивности и снижают качество чистых продуктов. Содержание непредельных соединений в сыром бензоле зависит, главным образом, от температуры коксования. С повышением температуры коксования содержание непредельных углеводородов снижается, их состав изменяется в сторону увеличения выхода низкокипящих соединений.
Непредельные соединения распределены между фракциями сырого бензола неравномерно. Наиболее богаты непредельными углеводородами низкокипящие компоненты (до 79°С), называемые головной или сероуглеродной фракцией. Высококипящая фракция (выше 145°С) называется тяжелым бензолом.
В головной фракции содержится около 50% (до 25% от ресурсов в сыром бензоле) низкокипящих непредельных соединений. Основными компонентами являются весьма реакционный углеводород циклопентадиен (температура кипения 42,5°С), а также амилены – непредельные углеводороды жирного ряда с пятью углеродными атомами, кипящие в пределах 25–42°С и др. В тяжелый (второй) бензол переходят высококипящие непредельные соединения (до 35% от ресурсов) – стирол, кумарон и инден, кипящие соответственно при 145,3, 173,5 и 181,5°С. Во фракции БТК (бензол, толуол, ксилол) содержатся циклогексан и метилциклогексан, кипящие при температурах 83 и 120,3°С, а также другие непредельные соединения, но в крайне незначительных количествах. При переработке двух бензолов во фракцию БТК почти полностью переходит стирол.
Наибольшую ценность представляют высококипящие непредельные соединения, содержащиеся в тяжелом бензоле. Эти соединения служат сырьем для получения ценных полимерных смол. Для производства полимерных смол непредельные соединения головной фракции непригодны.
Температуры кипения некоторых непредельных соединений очень мало отличаются от температур кипения отдельных бензольных углеводородов, например, в непосредственной близости кипят: бензол (80,1°С) и циклогексан (80,4°С); толуол (110,6°С) и метилциклогексан (108–110°С) и т.д.
Отделение бензольных продуктов от этих примесей ректификацией очень затруднительно.
Основными представителями сернистых соединений в сыром бензоле являются сероуглерод (CS2), тиофен (C4H4S) и его гомологи. В зависимости от сернистости шихты, идущей для коксования, содержание этих примесей в сыром бензоле колеблется от 0,2 до 2%. С повышением температуры коксования их содержание в сыром бензоле увеличивается.
В сыром бензоле заводов Юга содержится до 1% сероуглерода и около 1% тиофена с гомологами. Остальные серусодержащие соединения в сумме около 0,3% состоят из сероводорода (около 0,15%), элементарной серы (0,03%) и незначительных количеств меркаптанов, сульфидов и дисульфидов (в сумме менее 0,12%). Сероводород чаще всего можно обнаружить в свежем сыром бензоле. В процессе ректификации он выделяется с неконденсирующими газами через воздушник.
В сыром бензоле, получаемом при коксовании низкосернистых углей Кузнецкого бассейна, содержится меньше сероуглерода (до 0,3%), тиофена и его гомологов.
При тщательной ректификации сероуглерод почти полностью сосредоточивается в головной фракции. Что касается тиофеновой серы, то она распределяется довольно равномерно по фракциям сырого бензола. При этом в бензольной фракции сосредоточен тиофен, в толуольной фракции – - и -метилтиофены, в ксилольной – диметилтиофены. Такое распределение объясняется близостью температур кипения соединений тиофенового ряда и углеводородов бензольного ряда.
Тиофен образует с бензолом твердый раствор, не вызывающий понижения температуры кристаллизации бензола.
Из всех сернистых соединений, содержащихся в сыром бензоле, применяется лишь сероуглерод. К температуре кипения бензола, толуола и ксилолов очень близки температуры кипения следующих сернистых соединений: тиофена (84,1), метилтиофена (112–114), диметилтиофена (134–144°С), что затрудняет выделение этих веществ из сырого бензола путем ректификации.
Из насыщенных углеводородов в сыром бензоле содержатся пентан (0,4–0,1%), гексан (0,2–0,4%), гептан (0,2–0,4%), метилциклопентадиен (0,75%) и др. Эти соединения также распределены по фракциям сырого бензола неравномерно.
Близость температур кипения насыщенных углеводородов к температурам кипения бензольных продуктов, свойство образовывать азеотропные смеси с последними, инертность к действию различных химических реактивов затрудняет их выделение из сырого бензола. Насыщенные углеводороды снижают плотность и показатель преломления чистых продуктов, снижают температуру их кристаллизации. Это особенно нежелательно при производстве бензола для синтеза, так как температура кристаллизации является одним из показателей качества продукта.
Содержание прочих примесей в сыром бензоле невелико и составляет: пиридина и его гомологов до 0,1%, фенолов 0,1–0,3%. Эти соединения удаляются из сырого бензола при его очистке и не используются. Присутствие пиридиновых оснований в сыром бензоле отрицательно влияет при его очистке от тиофена, увеличивает потери чистого продукта. Содержащийся в сыром бензоле нафталин (0,5–2%) в процессе его переработки переходит в сольвент-нафту.
Наличие в сыром бензоле непредельных и сернистых соединений исключает возможность непосредственного получения из него чистых продуктов без предварительной очистки его от этих нежелательных примесей. Объясняется это тем, что даже незначительные примеси серы в бензоле и толуоле, применяемых для некоторых органических синтезов, вызывают быстрое отравление катализатора, а смолистые вещества, образующиеся в результате полимеризации непредельных соединений, обволакивают поверхность катализатора, дезактивируют ее. В связи с этим переработка сырого бензола должна осуществляться таким образом, чтобы получающиеся бензольные продукты не содержали непредельных и сернистых соединений или же содержали их в очень незначительных количествах, при которых исключено их вредное влияние в процессе производства синтетических продуктов.
В промышленности для переработки сырого бензола используют два процесса:
1) ректификации – разделение смеси вследствие разности температур кипения ее компонентов;
2) очистки – выделение непредельных и сернистых соединений.
Поэтому в любую технологическую схему переработки сырого бензола обязательно включается предварительная стадия, назначение которой – удалить примеси непредельных и сернистых соединений, а затем переходить к ректификации очищенного сырья и получению товарных продуктов.
На коксохимических заводах РФ наибольшее распространение получила технологическая схема переработки сырого бензола с получением чистых продуктов, которая включает следующие технологические операции: 1) получение фракции БТК (бензольно-толуольно-ксилольной) путем выделения сероуголеродной фракции из первого бензола или предварительной ректификации сырого бензола (с отгоном до 180°С); 2) сернокислотную очистку фракции БТК; 3) ректификацию очищенной фракции БТК.
На первой стадии происходит выделение сероуглерода и некоторой части непредельных соединений и насыщенных углеводородов, на второй – очистка от непредельных соединений и тиофена и на третьей – выделение бензола и иных продуктов из очищенной фракции БТК.
В некоторые технологические схемы включают ректификацию сероуглеродной фракции, редистилляцию второго бензола и получение бензола для синтеза.
10.2. Основы переработки сырого бензола
Основная цель переработки сырого бензола – выделение важнейших ароматических компонентов (бензола, толуола, изомеров ксилола и др.) в возможно более чистом виде с наименьшими потерями и получение наряду с этим полезных для народного хозяйства продуктов и ароматических примесей. Выделение чистых продуктов из сырого бензола осуществляется методом ректификации, являющимся одним из наиболее эффективных для разделения жидких смесей на отдельные компоненты. Для переработки сырого бензола и его фракций получили применение непрерывная и периодическая ректификация под атмосферным давлением и ректификация в вакууме для редистилляции второго бензола. Процесс ректификации сырого бензола осуществляется в колоннах барботажного типа, имеющих внутри колпачковые или ситчатые ректификационные тарелки, на которых достигается противоточное взаимодействие потоков пара и жидкости. В результате многократно чередующихся процессов частичного испарения остатка и частичной конденсации паров в колонне достигается практически полное выделение легкокипящего компонента в паровую фазу и отделение от него высококипящих компонентов – остатка, который выводится снизу колонны.
Основным условием достижения требуемой степени разделения компонентов в колонне является подвод тепла вниз колонны и подача холодного орошения на верх колонны.
Орошение ректификационных колонн может осуществляться двумя способами: флегмой – продуктом частичной конденсации паров, выходящих из колонны в аппарате, называемом дефлегматором, и рефлюксом – продуктом полной конденсации паров в конденсаторе-холодильнике. Интенсивность орошения колонны характеризуется отношением количества рефлюкса (флегмы) к количеству дистиллята, которое называется рефлюксным числом (или флегмовым). В практических условиях изменение рефлюксного (флегмового) числа достигается изменением количества отбираемого дистиллята.
При орошении колонны рефлюксом дозатором можно быстро и точно установить количество подаваемого на орошение рефлюкса, автоматизировать работу колонны.
Для нагрева сырья и испарения легкокипящего компонента, нагрева и испарения рефлюкса, в нижнюю часть колонны подается глухой пар в выносные подогреватели термосифонного типа. Предусмотрена подача острого пара. Степень разделения компонентов в колонне зависит от режима работы ректификационного агрегата и определяется температурами внизу и вверху колонны.
Температура внизу колонны характеризует полноту выделения легкокипящего компонента и должна соответствовать температуре кипения остатка, она регулируется количеством подаваемого в колонну глухого и острого пара. Чистота дистиллята регулируется изменением подачи рефлюкса на орошение и контролируется температурой верха колонны, которая должна соответствовать температуре кипения дистиллята.
В практике ректификации сырого бензола и его фракций для понижения температуры кипения получил распространение метод ректификации с острым паром.
Отбор головной (сероуглеродной) фракции и бензола производится без острого пара, так как необходимая температура может быть достигнута при обогреве колонн глухим паром. Толуол и все последующие продукты отбирают с применением острого пара. Для редистилляции второго бензола используют острый пар и вакуум.
XI. ОЧИСТКА СЫРОГО БЕНЗОЛА ОТ НЕПРЕДЕЛЬНЫХ
И СЕРНИСТЫХ СОЕДИНЕНИЙ
11.1. Сернокислотная очистка
Для очистки сырого бензола и его фракций от непредельных и сернистых соединений в промышленности получили применение: сернокислотная очистка и каталитическая гидроочистка.
Для глубокой очистки бензола от примесей насыщенных соединений большое значение приобретает процесс экстрактивной ректификации, который сочетается как с методом среднетемпературной гидроочистки, так и с методом сернокислотной очистки. Для глубокой очистки бензола также могут использоваться: очистка хлористым алюминием, хлором, гипохлоритом и фтористым водородом; электролитическая и парофазная очистка с различными активированными контактами; очистка солями ртути и др. Однако эти методы пока не получили промышленного применения.
Для очистки коксохимического сырого бензола широко используется метод сернокислотной очистки, обеспечивающий получение продукции высокого качества, отвечающей современным требованиям.
В настоящее время сернокислотный метод очистки применяется в двух вариантах – для очистки фракции БТК и при получении бензола для синтеза.
Очистка фракции БТК. Состав фракции БТК определяется главным образом условиями разделения сырого бензола, выкипающего до 180°С (на первый и второй), производимого в бензольных отделениях цеха улавливания.
В цехах ректификации, работающих по схеме полунепрерывной или непрерывной ректификации фракцию БТК получают в результате ректификации первого сырого бензола после отбора сероуглеродной фракции. К ней примешивают отгон до 145–150°С, полученный при редистилляции второго бензола, содержащего толуол, ксилол и высококипящие непредельные соединения – стирол, инден и др. Средний состав фракции БТК для заводов Юга (1) и Востока (2) примерно следующий, %:
-
1
2
Тиофен
1,18–1,35
0,20–0,25
Бензол
77,50–79,14
82,65–83,30
Толуол
13,10–14,12
10,9–11,20
Ксилол
4,12–4,90
3,75–3,90
Стирол
1,10–1,28
0,88–0,95
Инден
0,55–0,70
0,25–0,35
Прочие примеси
0,44–0,50
0,69–0,70
В незначительных количествах во фракции БТК содержатся насыщенные углеводороды, фенолы, пиридиновые основания и сероуглерод (не более 0,0002%). Насыщенные углеводороды проявляют инертность к действию химических реагентов, в частности к серной кислоте, поэтому их выделение затруднено.
Технология очистки фракции БТК серной кислотой предусматривает следующие операции: кислотная промывка фракции БТК и обработка фракции непредельными углеводородами («присадкой»); регенерация серной кислоты; выделение регенерированной кислоты и кислой смолки; нейтрализация мытого продукта щелочью и отделение от нее фракции.
Сернокислотный метод очистки фракции БТК состоит в обработке фракции концентрированной серной кислотой (93,0–93,5%) с последующей нейтрализацией мытого продукта раствором щелочи (12–15%). Серная кислота в этом процессе является катализатором. Процесс очистки осуществляется в аппаратах периодического или непрерывного действия. При этом удаляются также содержащиеся в сыром бензоле пиридиновые основания, которые связываются с серной кислотой в сульфат пиридина. При последующей нейтрализации мытого продукта щелочью из него удаляются также и фенолы в виде фенолятов натрия.
При взаимодействии фракций БТК с концентрированной серной кислотой протекают несколько параллельных процессов.
1. Катализируемая кислотой реакция полимеризации непредельных соединений. Под влиянием концентрированной серной кислоты многие непредельные углеводороды фракции БТК легко полимеризуются с образованием полимеров различной степени сложности (димеров, тримеров и т. п.). При этом серная кислота выделяется в свободном виде.
Продукты менее глубокой полимеризации (димеры, тримеры), растворяются в очищаемом продукте и выделяются при ректификации в виде кубовых остатков, а продукты более глубокой полимеризации образуют полимеры, которые выпадают в виде кислой смолки, состоящей из полимеров, серной кислоты и чистых продуктов.
Различные непредельные соединения полимеризуются по-разному. Легкокипящие непредельные соединения (циклопентадиен и др.) полимеризуются очень глубоко с большим выделением тепла. Продуктом их полимеризации являются густые и вязкие смолы очень сложного строения.
Высококипящие непредельные соединения (стирол, кумарон и инден) в процессе полимеризации не образуют кислой смолки. Образующиеся полимеры растворяются в чистых продуктах и выделяются в виде кубовых остатков в процессе ректификации; Эти полимеры достаточно устойчивы, и поэтому процесс ректификации обычно не сопровождается их разложением. Сополимериза-зия непредельных соединений с бензольными углеводородами протекает с образованием высококипящих соединений, большей частью растворимых в очищенном продукте и при повторной ректификации выделяющихся в виде кубовых остатков.
Эти реакции нежелательны и приводят к потерям чистых продуктов, что снижает их выход.
2. Реакции сульфирования тиофена и его гомологов с образованием сульфокислоты тиофена, растворимой в воде и кислоте. Реакция сульфирования тиофена протекает очень медленно и для ее ускорения требуется применение серной кислоты высокой концентрации. Метилтиофены сульфируются 93,5%-ной серной кислотой легче тиофена и удаляются из фракции БТК без затруднений.
Реакциям сульфирования подвергаются все бензольные углеводороды. Толуол и ксилол сульфируются легче бензола. С повышением температуры эти процессы усиливаются. За исключением реакции сульфирования тиофена, эти реакции являются нежелательными. Они приводят к образованию кислой смолки, снижают качество, уменьшают выход регенерированной серной кислоты, увеличивают потери чистых продуктов.
3. Катализируемое серной кислотой алкилирование тиофена непредельными соединениями. В присутствии 93-%ной серной кислоты тиофен с высокой скоростью может алкилироваться непредельными углеводородами разных классов, содержащихся во фракции ВТК или добавленных в последнюю при очистке. Механизм алкилирования тиофена протекает в две стадии: сначала непредельные углеводороды реагируют с серной кислотой с образованием чрезвычайно реакционноспособного промежуточного продукта – иона карбония (–СН–СН3), который реагирует с тиофеном с образованием сополимера, а кислота остается в неизменном виде. Алкилирование тиофена, а еще в большей степени метилтиофенов с непредельными соединениями, особенно высококипящими (стиролом, инденом и др.) под влиянием незначительного количества серной кислоты протекает быстро и полно, с незначительным образованием кислой смолки.
Таким образом, удаление тиофена является определяющим процессом сернокислотной очистки фракции БТК. Удаление тиофена алкилированием непредельными соединениями более выгодно, чем сульфированием.
В процессе очистки фракции БТК основная часть тиофена (60–70%) переходит в кубовые остатки в виде полимеров и сополимеров, часть распределяется в серной кислоте и кислой смолке. В незначительном количестве тиофен остается в чистом продукте.
Все эти реакции в процессе сернокислотной очистки протекают одновременно, но преимущественное развитие в начале процесса очистки получают реакции полимеризации непредельных соединений, а в конце реакции алкилирования тиофена непредельными соединениями.
Серная кислота с непредельными соединениями может образовывать кислые и средние эфиры. Кислые эфиры легко растворяются в серной кислоте и воде, в результате чего они выводятся из очищаемого продукта. Средние эфиры очень плохо растворимы в воде и в кислоте, но хорошо растворимы в бензольных продуктах, они термически неустойчивы и под влиянием температуры разлагаются с выделением сернистого газа, сероводорода, углекислого газа, меркаптанов, элементарной серы, углистого остатка и ненасыщенных углеводородов. Выделяющийся сернистый газ вызывает коррозию аппаратуры. Сероводород, меркаптаны и ненасыщенные углеводороды ухудшают качество чистых продуктов. Углистый остаток откладывается на поверхности труб паровых подогревателей и ухудшает процесс теплопередачи.
Из непредельных соединений, содержащихся в сыром бензоле, очень склонны к образованию термически неустойчивых полимеров и средних эфиров циклопентадиен и другие, сосредоточенные преимущественно в сероуглеродной фракции. Еще более склонен к этим процессам дициклопентадиен.
При переработке сырого бензола предварительно отделяют фракции, кипящие ниже 70 и выше 145°С, так как в них концентрируется большая часть непредельных и сернистых соединений. Химической очистке подвергают фракции, выкипающие в пределах 79–145°С. Это позволяет сократить расход на химическую очистку сырого бензола и квалифицированно использовать циклопентадиен и сероуглерод, выделенные в головную фракцию, и высококипящие непредельные соединения (инден, кумарон и стирол).
В результате сернокислотной очистки фракции БТК основным продуктом является очищенная фракция, содержащая высококипящие соединения, которые выделяются при последующей ректификации в виде кубовых остатков.
Степень очистки бензольных продуктов от непредельных и сернистых соединений характеризуется пробой с серной кислотой и определением бромного числа. Сернокислотная проба характерна для непредельных соединений и должна быть в пределах 0,15–0,30, бромное число (количество брома в граммах на 100 г пробы) характеризует содержание тиофеновой серы и составляет 0,20–0,30.
Для достижения достаточно полного выделения тиофена в процессе сернокислотной очистки фракции БТК в промышленности используют способ добавки непредельных соединений (присадки). В качестве присадки используют отходы производства бутадиена, пипериленовую фракцию (побочный продукт при производстве изопрена), дивинильную фракцию (отходы производства дивинила) и др. Некоторые из них характеризуются показателями:
| Отходы производства бутадиена | Пипериленовая фракция |
Плотность при 20°С, кг/м3 | 750 | 695 |
Температура,°С начала перегонки отгона 95% (объемн.) | 170–190 | 65–75 |
Бромное число, г/100 г | 140–180 | 195 |
Сумма непредельных углеводородов,% | 75–80 | 95 |
Использование присадок при сернокислотной очистке фракции БТК позволяет использовать их для алкилирования тиофена, снизить интенсивность протекания процессов сульфирования и сополимеризации бензольных углеводородов и уменьшить их потери. Непредельные соединения присадок реагируют с тиофеном с большей избирательностью и интенсивностью.
Очистка фракции БТК производится двухстадийным методом, по которому подача кислоты на промывку фракции осуществляется в две стадии, а присадки добавляются после того, как прореагировали непредельные соединения, содержащиеся во фракции БТК. Сущность стадийной подачи присадки заключается в том, чтобы исключить полимеризацию непредельных соединений в процессе очистки, подавить малоизбирательную реакцию сульфирования тиофена и продлить во времени реакцию алкилирования тиофена, т.е. провести процесс в желаемом направлении и рационально использовать непредельные соединения фракции БТК и присадки.
Этот метод позволяет снизить потери чистых продуктов, особенно метилированных, в результате снижения интенсивности реакций их сульфирования и сополимеризации, улучшить качество целевых продуктов, снизить расход серной кислоты. Введение присадки в две и несколько ступеней значительно улучшит показатели счистки, так как удаление тиофена достигается исключительно за счет его алкилирования, это также позволяет снизить расход присадки.
Для получения глубокоочищенных бензолов рекомендуется подвергать переработке не широкую фракцию БТК, а более узкую БТ (бензол–толуол). При этом из процесса очистки исключается содержащийся во фракции БТК стирол, склонный к взаимодействию с гомологами бензола.
Нейтрализация мытой фракции осуществляется 12–15%-ным раствором щелочи. Расход щелочи составляет: 3,5–4,5 кг 100%-ного едкого натра на 1 т фракции БТК или 3–4 кг на 1 т сырого бензола, отогнанного до 180°С.
Основными технологическими факторами, влияющими на эффективность сернокислотной очистки являются: качество исходной фракции БТК по содержанию тиофена; концентрация серной кислоты и ее качество; температура процесса; продолжительность процесса и эффективность массообмена, количество и качество присадки.
Подвергаемая очистке фракция БТК должна содержать все ресурсы бензола, толуола, большую часть ксилола и не содержать тяжелого бензола, минимальное количество сероуглерода и низкокипящих непредельных соединений.
Процесс сернокислотной очистки фракции БТК следует вести с минимально возможным количеством кислоты. В заводской практике расход серной кислоты 93,0–93,5%-ной концентрации составляет 4–7%. Использование метода стадийной подачи присадки позволило значительно снизить расход серной кислоты и довести ее на 1 т готового продукта до 54–75 кг, и ниже. Расход серной кислоты при очистке фракции БТК заводов Юга и Востока обусловливается содержанием в них сернистых соединений.
Расход присадки по данным заводов Юга составляет: пипериленовой фракции (содержащей 95% непредельных соединений) 1,5–1,8%; дивинильной около 1,6% (по массе). Оптимальная температура процесса очистки зависит от состава промываемой фракции и не должна быть выше 35–45°С. Температура загружаемой в аппарат фракции должна составлять 20–25°С.
Реакции, которым сопровождается процесс химической очистки, экзотермичны. Количество выделяющегося при этом тепла обусловлено составом фракции и в первую очередь содержанием непредельных соединений и их свойствами. При промывке фракции БТК оптимального состава подъем температуры при очистке составляет 15–20°С.
Достоинством очистки с присадками непредельных соединений является также малая чувствительность к температурным условиям, поэтому при ее проведении не требуется тщательного регулирования температуры.
На процесс сернокислотной очистки влияют условия контактирования кислоты и продукта. Протекающие при сернокислотной очистке реакции проходят в основном на поверхности кислоты; чем эта поверхность больше, тем полнее и быстрее они заканчиваются.
Усиленная турбулизация среды, помимо большой поверхности для протекания реакций, обеспечивает также непрерывный приток реагирующих веществ к этой поверхности и отвод от нее продуктов реакции. При достижении более высокой эффективности перемешивания уменьшается количество образующейся кислой смолки и расход кислоты, а при постоянном расходе кислоты улучшается степень очистки.
Оптимальная продолжительность перемешивания очищаемой фракции БТК с концентрированной кислотой в насосе-смесителе 2,5 с, в гидрошарах 30–40 с и в реакторе 4,5–5,0 мин.
Увеличение продолжительности перемешивания, существенно не влияет на степень очистки, приводит к увеличению количества кислой смолки, ухудшению ее консистенции (увеличивается вязкость) и связанному с этим росту потерь кислоты и продукта, а также нарастанию сульфирования ароматических углеводородов.
Весьма важной технологической операцией процесса сернокислотной очистки является регенерация серной кислоты. Если не считать некоторых незначительных потерь серной кислоты, механически увлекаемой кислой смолкой, основная часть ее может быть выделена путем регенерации в смесителях, куда подается вода, которая уменьшает концентрацию серной кислоты и прерывает процессе полимеризации. Вода расходуется в количестве 1,8–2,0 объема на 1 объем кислоты. При недостатке воды снижается выход регенерированной кислоты и увеличивается выход кислой смолки. Регенерированная кислота плохо отделяется от смолки. Обычно концентрация регенерированной кислоты составляет 40–50%, а ее выход не менее 70–80%.
Образующаяся в процессе сернокислотной очистки кислая смолка, выход которой колеблется от 0,2–0,3 до 1–2%, используется для производства дорожного дегтя. Состав ее в зависимости от условий процесса и состава очищаемой фракции может заметно колебаться, что подтверждается следующими данными:
-
Плотность, г/см3
1,08–1,20
Содержание, %
кислоты
10–30
бензольных углеводородов
25–45
полимеров
40–60
Общие потери при очистке обычно составляют 3–5%. В практических условиях выход чистых продуктов составляет 91–93% от количества бензола, отогнанного до 180°С, что объясняется значительными потерями при переработке головной фракции.
Недостатками сернокислотной очистки являются несколько завышенные потери чистых продуктов, образование отходов производства в виде кислой смолки и получение отработанной (регенерируемой) кислоты, применение которой для производства сульфата аммония затруднительно. Однако такие достоинства сернокислотной очистки, как доступность и дешевизна реактива, гибкость процесса и простота управления им, небольшие удельные затраты и простота аппаратурного оформления, обеспечивают этому методу широкое применение и будущность.
На рис. 17 приведена принципиальная схема непрерывной сернокислотной очистки фракции БТК. Преимуществами непрерывной сернокислотной очистки являются: постоянство технологического режима, удобство обслуживания и возможность весьма интенсивного перемешивания, которое недостижимо в аппаратуре периодического действия большой емкости.
Фракция БТК поступает в смеситель 2, а затем в центробежный насос 1, являющийся также смесителем, сюда же подается концентрированная серная кислота. Здесь происходит процесс алкилирования тиофена с непредельными соединениями фракции. Перед второй группой смесителей 2 подается присадка для продолжения реакции выделения тиофена. Затем смесь поступает в следующую группу смесителей 2, куда подается вода для регенерации серной кислоты, отсюда смесь поступает в реактор 3. Во всех предыдущих аппаратах суммарная продолжительность контакта не превышает обычно 1 мин, в реакторе 4–6 мин. Вся последующая цепь аппаратов предназначена для отстоя кислоты и кислой смолки, нейтрализации фракции и отстоя отработанной щелочи.
Если для удаления тиофена необходимо добавить непредельные соединения, присадку последних подают непосредственно во фракцию перед поступлением ее в насос. Показатели очистки фракции БТК с использованием присадки примерно следующие: окраска с серной кислотой 0,15–0,4; бромное число 0,12–0,20, содержание тиофена не более 0,10%.
При очистке фракции БТК или БТ (бензол – толуол) не удается получить бензол для синтеза, в котором содержание тиофена не должно превышать 0,0002–0,0004%, а в некоторых случаях он должен быть свободным от тиофена. Поэтому бензол обычного качества, например, бензол для нитрации, перемывают серной кислотой вторично. При этом благодаря отсутствию в нем реакционноспособных гомологов бензола процесс удаления тиофена удается провести с незначительными потерями продукта. Повторная очистка бензола возможна в двух вариантах – с применением олеума или моногидрата, или с применением обычной 92–94%-ной серной кислоты и добавкой непредельных соединений.
Промышленное применение получил метод перемывки бензола 92–94%-ной серной кислотой с добавкой непредельных соединений. Подаваемые на очистку непредельные соединения полностью используются на алкилирование тиофена и сополимеризацию друг с другом. Ступенчатая подача присадки позволяет направить непредельные соединения в основном на целевую реакцию – взаимодействие с тиофеном.
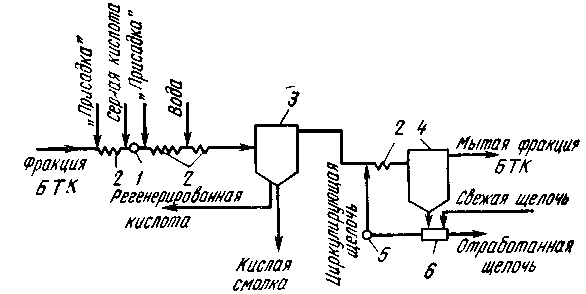
Рис. 17. Принципиальная схема сернокислотной очистки:
1 – насос-смеситель; 2 – смесители гидравлические; 3 – отстойник кислоты и кислой смолки; 4 – отстойник щелочи; 5 – насос для циркуляции щелочи; 6 – сборник щелочи
Перемытый бензол подвергают ректификации для отделения головных погонов и кубовых остатков с получением бензола для синтеза и нитрации.
Опыт промышленного производства бензола с применением различных алкилирующих присадок подтверждает его высокое качество, отвечающее требованиям стандартов.
При очистке бензольных продуктов серной кислотой невысокой концентрации (93,0–94,5%) в присутствии непредельных соединений почти не развиваются процессы сульфирования, поэтому в отработанной кислоте содержится мало органических примесей (не более 2,5–5,0%). Такая кислота направляется на очистку фракции БТК совместно со свежей кислотой, а затем после регенерации передается в производство сульфата аммония. Таким образом, общий расход кислоты на очистку сокращается. При ступенчатой подаче присадки схема усложняется, но расход реагентов может быть сокращен и степень очистки повышена.
Так, например, при одноступенчатой очистке бензола с исходным содержанием тиофена 0,02–0,03% до остаточного его содержания 0,00005% расходуется 1% пипериленовой фракции, а при двухступенчатой очистке ее расход можно снизить до 0,5–0,6%.
Основным аппаратом для осуществления сернокислотной очистки фракции БТК в установках периодического действия, является меланжер с механическими перемешивающими устройствами – пропеллерным или турбулентными мешалками. В установках непрерывного действия широкое применение получили аппараты с механическими устройствами (трехлопастных пропеллеров), гидравлические смесители – шаровые, змеевиковые, ребристые радиаторы, а также центробежные насосы-смесители.
11.2. Каталитическая гидроочистка
Наиболее перспективным методом очистки бензола является каталитическая гидрогенизация, позволяющая наряду с глубокой очисткой от сернистых и непредельных соединений достичь глубокого удаления насыщенных углеводородов.
Сущность процесса каталитической гидроочистки заключается в обработке паров очищаемого сырья (фракции сырого бензола) водородом или водородсодержащим газом над катализатором при соответствующих температуре, давлении и объемной скорости сырья с получением бензола и его гомологов и полного гидрирования содержащихся примесей.
Схема процесса каталитической гидроочистки состоит из четырех стадий: 1) подогрев и испарение сырья (фракции БТК); 2) каталитическая гидроочистка; 3) отделение газа и подготовка полученного рафината; 4) ректификация рафината с получением конечных продуктов.
В отличие от жидкофазной очистки фракций сырого бензола (БТК концентрированной серной кислотой, при гидрировании под давлением процесс осуществляется в газовой фазе над катализатором, поэтому необходимо полностью перевести очищаемые продукты в парообразное состояние и отделить их от неиспаряемого остатка. Полученные пары фракции смешиваются с чистым водородом или с коксовым газом (около 57–60% водорода) и подвергаются каталитической гидроочистке.
При прохождении смеси паров и водородсодержащего газа над катализатором под влиянием температуры и давления протекают различные реакции, к числу которых относят: реакции гидрообессеривания, гидрирование ненасыщенных соединений, гидрирование ароматических углеводородов, гидрокрекинг насыщенных углеводородов, деметилирование гомологов бензола.
Целевыми реакциями очистки являются гидрообессеривание и гидрирование ненасыщенных углеводородов. При получении бензола высокой степени чистоты определяющими являются реакции гидрообессеривания, особенно гидрогенолиз (разрушение) наиболее термически стабильного соединения – тиофена. Катализаторами гидрообессеривания могут быть сульфиды или оксиды молибдена, кобальта, вольфрама, никеля, ванадия. В промышленности широко распространен алюмокобальтмолибденовый катализатор.
Основными факторами, определяющими процесс, являются тип катализатора, температура, давление водорода и объемная скорость сырья. В зависимости от этих факторов методы гидрогенизации условно делят на: 1) низкотемпературное гидрирование – гидроочистка (350–380°С); 2) среднетемпературный гидрокрекинг (450–530°С); 3) высокотемпературный гидрокрекинг (530–650°С); 4) каталитическое и термическое гидродеалкилирование. Важной особенностью каталитических методов, в частности, гидрогенизационных, является исключение образования неутилизируемых отходов производства и, следовательно, повышение выходов и чистоты товарных продуктов.
Химизм процесса гидроочистки заключается в том, что серусодержащие примеси гидрируются с образованием соответствующих углеводородов и сероводорода:
-
Сероуглерод
CS2 + 4Н2 – 2H2S + СН4
Этилмеркаптан
C2H5SH + Н2 – H2S + С2Н6
Метилтиофен
C4H3SCH3 + 4H2 – H2S + С5Н12
Тиофен
C4H4S + 4Н2 – H2S + С4Н10
Из всех сернистых соединений, содержащихся в сыром бензоле, наиболее устойчивым при гидрировании, а также при термической обработке является тиофен, который не разлагается даже при 800°С. Однако в присутствии водорода и соответствующих катализаторов, при наличии необходимого давления разложение тиофена происходит сравнительно полно.
Азотсодержащие вещества при гидрировании дают аммиак и углеводороды, кислородсодержащие соединения – воду и углеводороды:
CH3CN + 3Н2 – С2Н6 + NH3,
C5H5N + 5H2 – С5Н12 + NH3,
6С6Н5ОН + 3Н2 – 5С6Н6 + 6Н2O
Гидродеалкилирование гомологов бензола протекает по реакциям:
С6Н5СН3 + Н2 = С6Н6 + СН4,
С6Н4(СН3)2 + Н2 = С6Н5СН3 + СН4.
Непредельные соединения насыщаются по реакции
C6H5CH=СН2 + Н2 = С6Н5СН2СН3.
Также осуществляются реакции гидрокрекинга насыщенных углеводородов (циклогексана, метилциклогексана) с образованием парафиновых углеводородов.
Процесс каталитической гидроочистки может осуществляться по среднетемпературной схеме и по схеме высокотемпературной очистки.
На рис. 18 приведена принципиальная схема среднетемпературной каталитической гидроочистки. Исходным сырьем чаще всего бывает БТКС, которая насосом высокого давления 14 подается на испарительную установку 1, представляющую собой систему каскадов, в которых последовательно происходит повышение температуры и испарение фракции. Испарение фракции производится непосредственно в поток циркуляционного газа при большой скорости последнего, чтобы предупредить отложение полимеров на поверхности греющей аппаратуры.
После последней секции каскада производится выпуск полимеров в виде 12–15%-ного раствора неиспарившейся фракции БТКС. Раствор полимеров перегоняется для получения дистиллята, который передается в исходную фракцию. Побочным продуктом является полимерная смола.
Температура парогазовой смеси после испарения 170–190°С и давление 4,0–4,5 МПа (40–45 ат). После каскада парогазовая смесь направляется в теплообменник 2, где нагревается циркуляционным газом до 200–230°С и поступает в форконтактный аппарат 3. В последнем в присутствии алюмомолибденокобальтового катализатора осуществляется гидростабилизация (форконтактная очистка), при которой протекают процессы насыщения нестабильных непредельных соединений (стирола, индена и др.) в устойчивые насыщенные соединения, гидрогенолиз сероуглерода с образованием метана и сероводорода. В форконтактном аппарате 3 происходит повышение температуры на 15–20°С за счет экзотермичных реакций гидрирования непредельных соединений.
Гидрогенолиз тиофена, а также гидрирование ароматических углеводородов при температурах форгидрирования не происходит.
Из форконтактного аппарата 3 парогазовая смесь поступает в трубчатую печь 4, где нагревается до 340–360°С. Обогрев печи производят коксовым газом. Из печи парогазовая смесь поступает в реакторный блок 5, состоящий из двух реакторов (контактных аппаратов), имеющих алюмомолибденокобальтовый катализатор. В первом происходит гидрогенолиз (разрушение) основной массы тиофена и в незначительной степени гидрируются ароматические углеводороды. Температура повышается на 15°С. После первого реактора в систему вводится свежий коксовый газ с температурой 200–220°С, что позволяет на 15–20°С повысить температуру перед вторым реактором. Коксовый газ предварительно очищается от сероводорода, оксидов азота и осушается. Газ также освобождается от бензольных углеводородов и легких компонентов головной фракции.
Во втором реакторе 5 происходит гидрогенолиз оставшегося тиофена, в незначительной степени гидрирование бензольных углеводородов, а также гидрирование компонентов введенного коксового газа. Благодаря экзотермичности реакций температура поднимается на 15–20°С. Повышение температуры в пределах
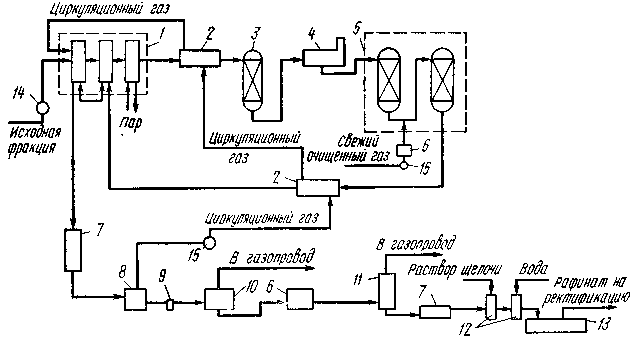
Рис. 18. Схема среднетемпературной каталитической гидроочистки:
I – исходная фракция; II – циркуляционный газ; III – свежий очищенный газ; IV – в газопровод; V – раствор щелочи; VI – рафинат на ректификацию
340–400°С приводит к более глубокому гидрогенолизу тиофена и одновременному росту содержания насыщенных соединений (циклогексана и метилциклогексана), в результате развития процессов гидрирования.
О снижении активности катализатора судят по содержанию тиофена в рафинате. При содержании водорода в коксовом газе 58–60% содержание его в циркулирующем газе обычно поддерживают на уровне 48–50%.
В первом реакторе гидрогенолизу обычно подвергается 97– 98% исходного тиофена, во втором достигается необходимая степень очистки.
При содержании тиофена в исходном сырье 1,0–1,4% после второго реактора оно составляет до 0,0004–0,0006%, содержание n-гептана сохраняется на том же уровне, что и в сырье, а содержание циклогексана и метилциклогексана возрастает.
После второго реактора парогазовая смесь с температурой 360–370°С поступает в теплообменник 2, отдает тепло циркулирующему газу и охлаждается до 240–250°С. С этой температурой она поступает в теплообменники каскадов испарителя 1, где охлаждается до 120–130°С, отдавая тепло фракции БТКС.
После теплообменников каскада испарения 1 парогазовая смесь поступает в холодильник 7, охлаждается до 25–35°С и поступает в сепаратор высокого давления 8. В последнем при давлении 3,3–3,6 МПа (33–83 ат) происходит выделение циркуляционного газа, а конденсат с растворенными газами поступает в сепаратор низкого давления [0,2–0,3 МПа (2–3 ат)] 10. Рафинат поступает в подогреватель 6 и стабилизационную колонну 11, в которой происходит выделение остаточного количества газов, а также сероводорода и аммиака.
Рафинат после стабилизационной (отпарной) колонны 11, холодильника 7 попадает в промыватели щелочи 12, а затем в хранилище 13, откуда направляется на ректификацию. Циркуляционный газ после сепаратора высокого давления 8 при помощи компрессора 15 подается в систему.
Энергетические затраты процесса гидроочистки на 1 т сырья (фракции БТКС) составляют: 90–120 кВт ч электроэнергии; 1,89–2,52 МДж (0,45–0,60 Мкал) – пара; 1,5 м3 воды. Выход рафината составляет 98% от исходного сырья.
Процесс гидроочистки отличается большим выходом и сравнительно высоким качеством продуктов, что позволяет компенсировать увеличенные капитальные затраты и расходы по переделу.
В результате среднетемпературного процесса достигается полное удаление непредельных соединений, глубокая очистка от тиофена, но не достигается очистка бензола от насыщенных углеводородов.
В установке высокотемпературной гидроочистки процесс проводят на алюмокобальтмолибденовом катализаторе под давлением 4 МПа (40 ат) и температуре выше 550°С, что дает возможность подвергнуть гидрокрекингу насыщенные углеводороды и этим улучшить качество бензола, увеличить его выход до 98%.
Схема гидроочистки сырого бензола, разработанная сотрудниками УНИХа, Гипрококса и Гипрогазтоппрома, предусматривает очистку лишь фракции БТК, что сохраняет ресурсы смолообразующих для производства полимерных смол и дает возможность использовать сероуглеродную фракцию для получения сероуглерода и циклопентадиена. Поэтому из первого бензола раньше всего выделяется сероуглеродная фракция. Полученная фракция БТК поступает на гидроочистку.
Продукт после очистки под давлением и отмывки от сероводорода и аммиака содержит значительное количество неароматических (насыщенных) углеводородов, образовавшихся в результате гидрирования непредельных углеводородов. Наличие неароматических примесей, многие из которых образуют с бензолом и другими ароматическими углеводородами азеотропные смеси, усложняет ректификацию рафината.
Для получения бензольных продуктов, не содержащих насыщенных углеводородов, предусматривается сочетание каталитической гидроочистки с экстрактивной ректификацией.