Разработка и внедрение высокоэффективных технологических процессов изготовления отливок из алюминиевых и магниевых сплавов в авиастроении
Вид материала | Автореферат |
- «производство отливок из сплавов цветных металлов», 38.25kb.
- Технология плавки и разливки магниевых сплавов, 160.13kb.
- Реферат Тема: Технология плавки и разливки магниевых сплавов, 154.86kb.
- Тема: сварка алюминия и его сплавов, 56.75kb.
- Цена дипломной работы с чертежом 500 рублей содержание, 51.27kb.
- Пояснительная записка к курсовому проекту по курсу: «Процессы и аппараты химической, 52.08kb.
- Батышев Константин Александрович исследование, 709.6kb.
- Флюсы и рециклинг алюминия, 130.43kb.
- «технология литейного производства», 45.75kb.
- Внастоящей работе проведен анализ зависимостей затухающих акустических колебаний отливок, 47.5kb.
отходов кузнечно-штамповочного производства. Качество сплава оценивали по газосодержанию, механическим испытаниям образцов, вакуумным пробам, микро-, макро– и химическому анализам образцов (рис. 11). Размеры и форму литой
заготовки, имеющей форму близкую к форме штамповки с размерами, обеспечивающими требуемую степень деформации, определяли следующим образом. Высоту заготовки находили, исходя из величины деформации z в направлении оси Z деформирования:
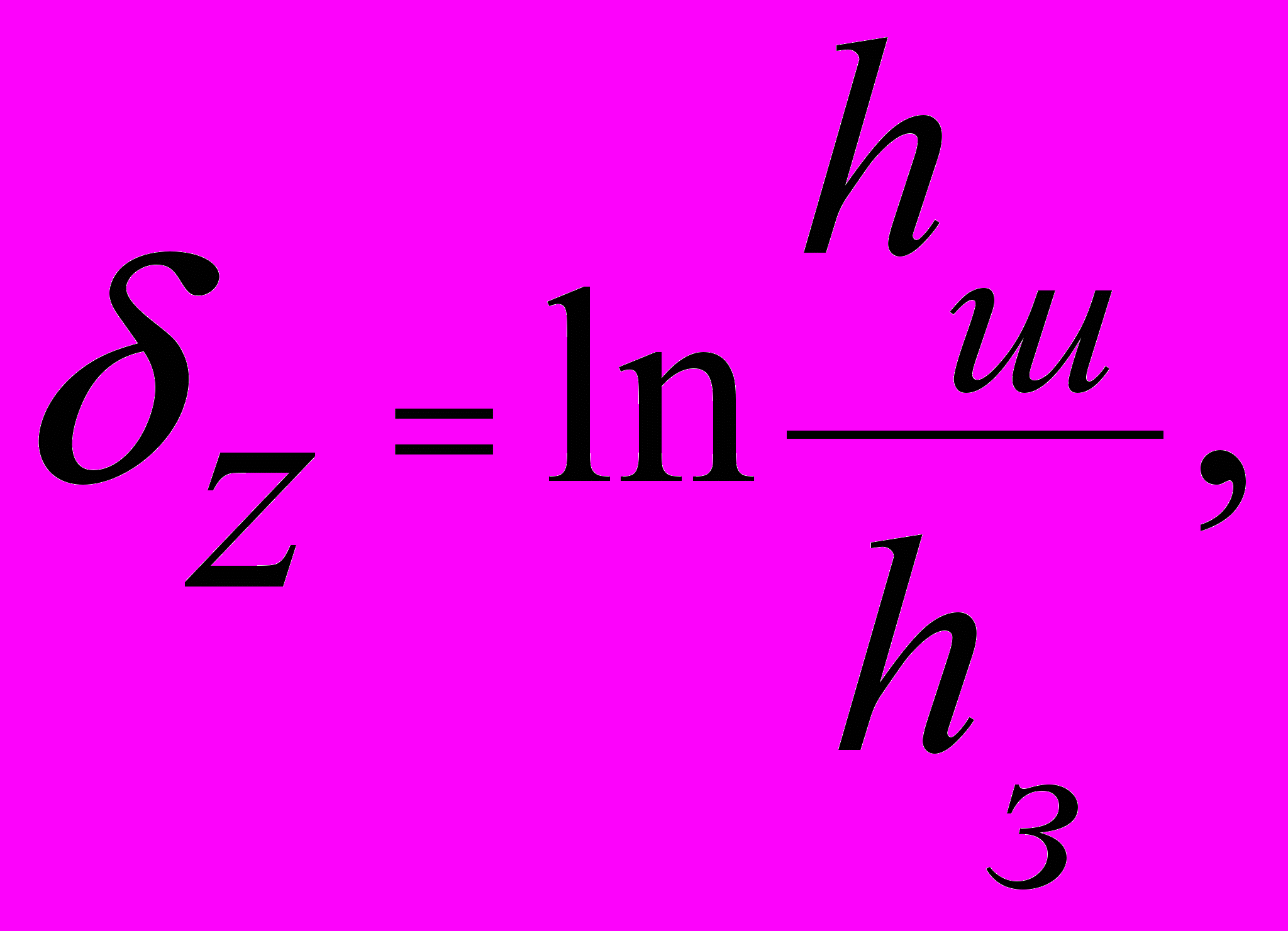
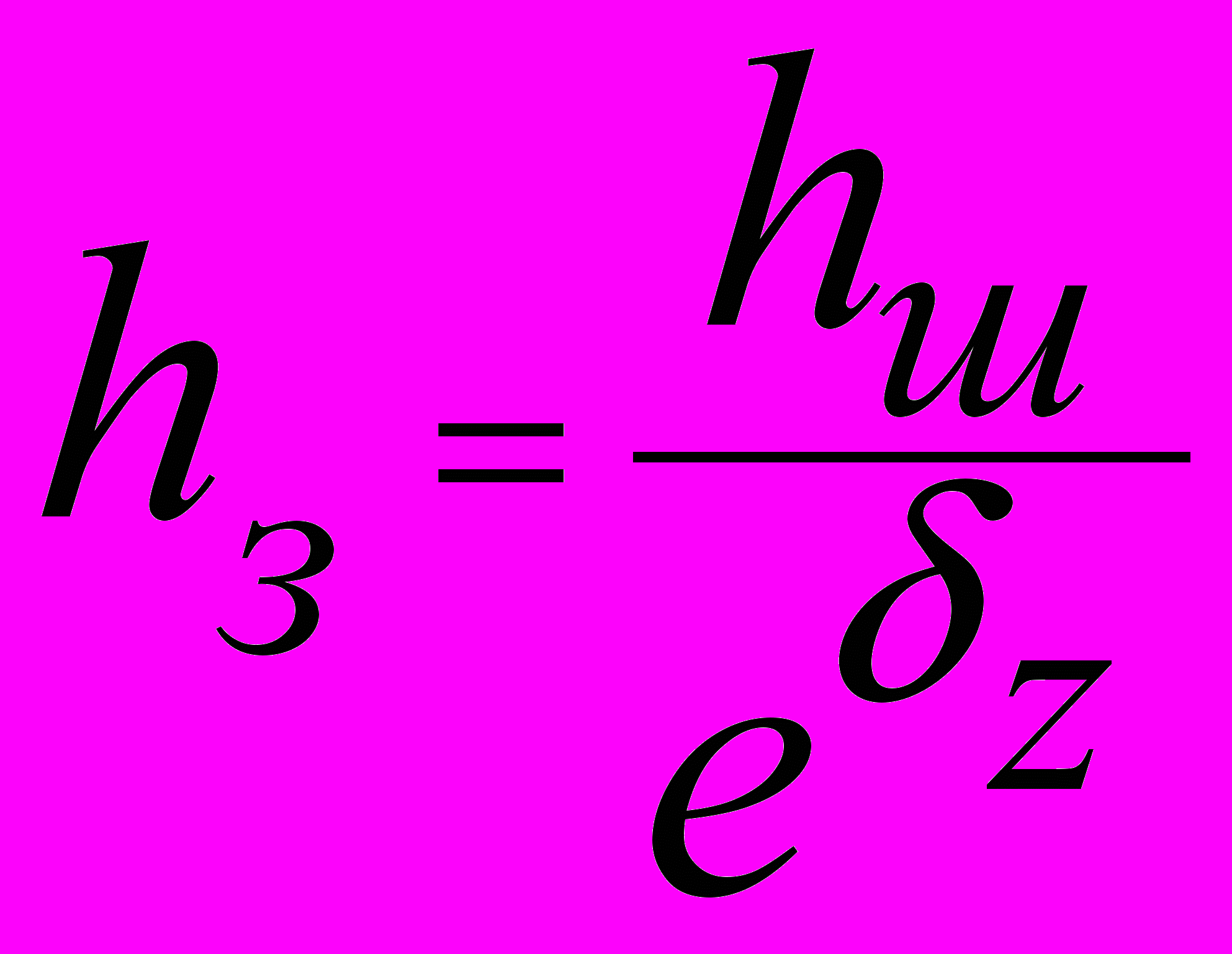
где hш – высота штамповки; hз – высота литой заготовки.
Состояние литой заготовки принималось плоско-деформированным, т.е. х = – z .
Широтные размеры заготовки определялись из величины х .
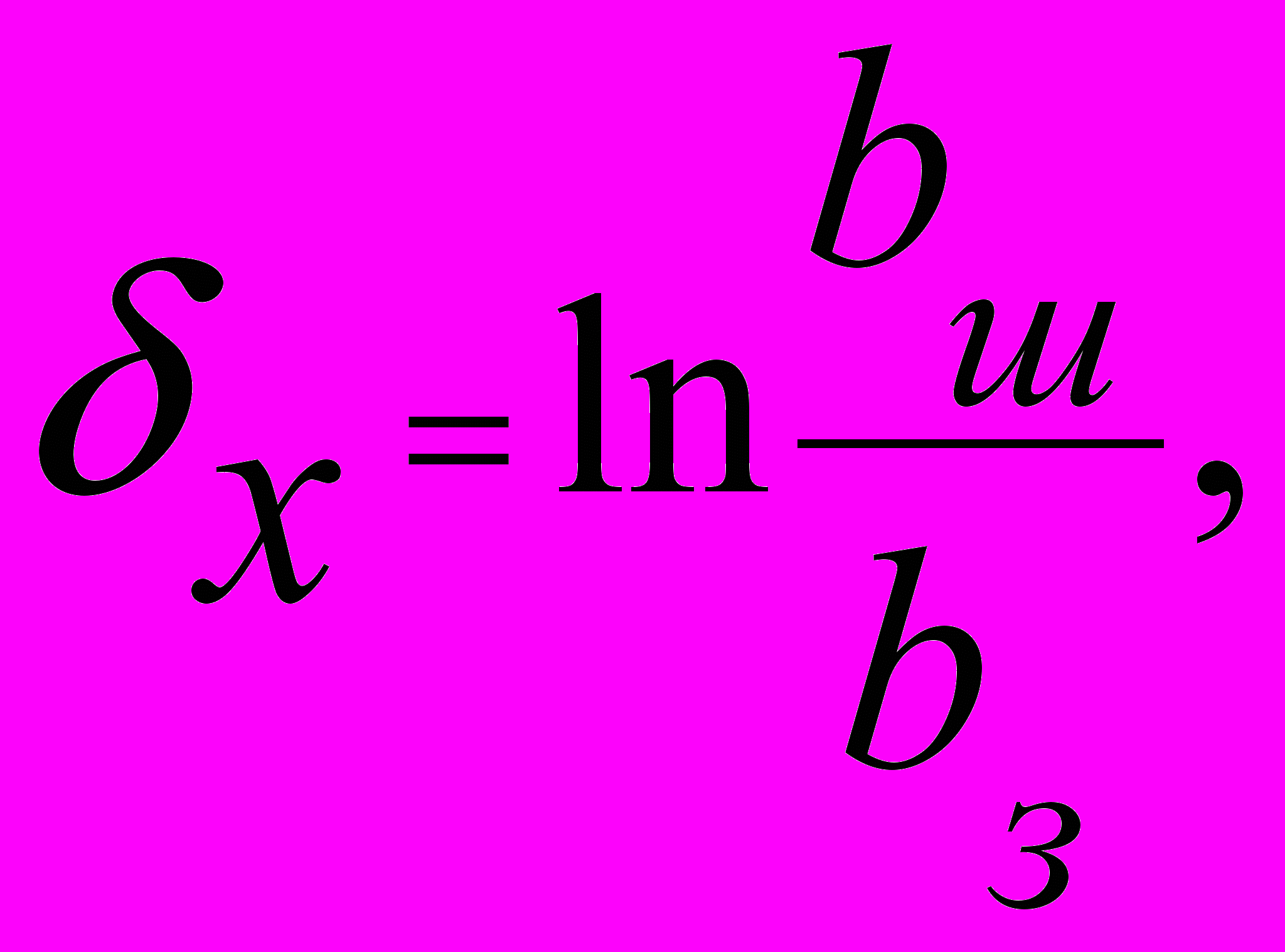
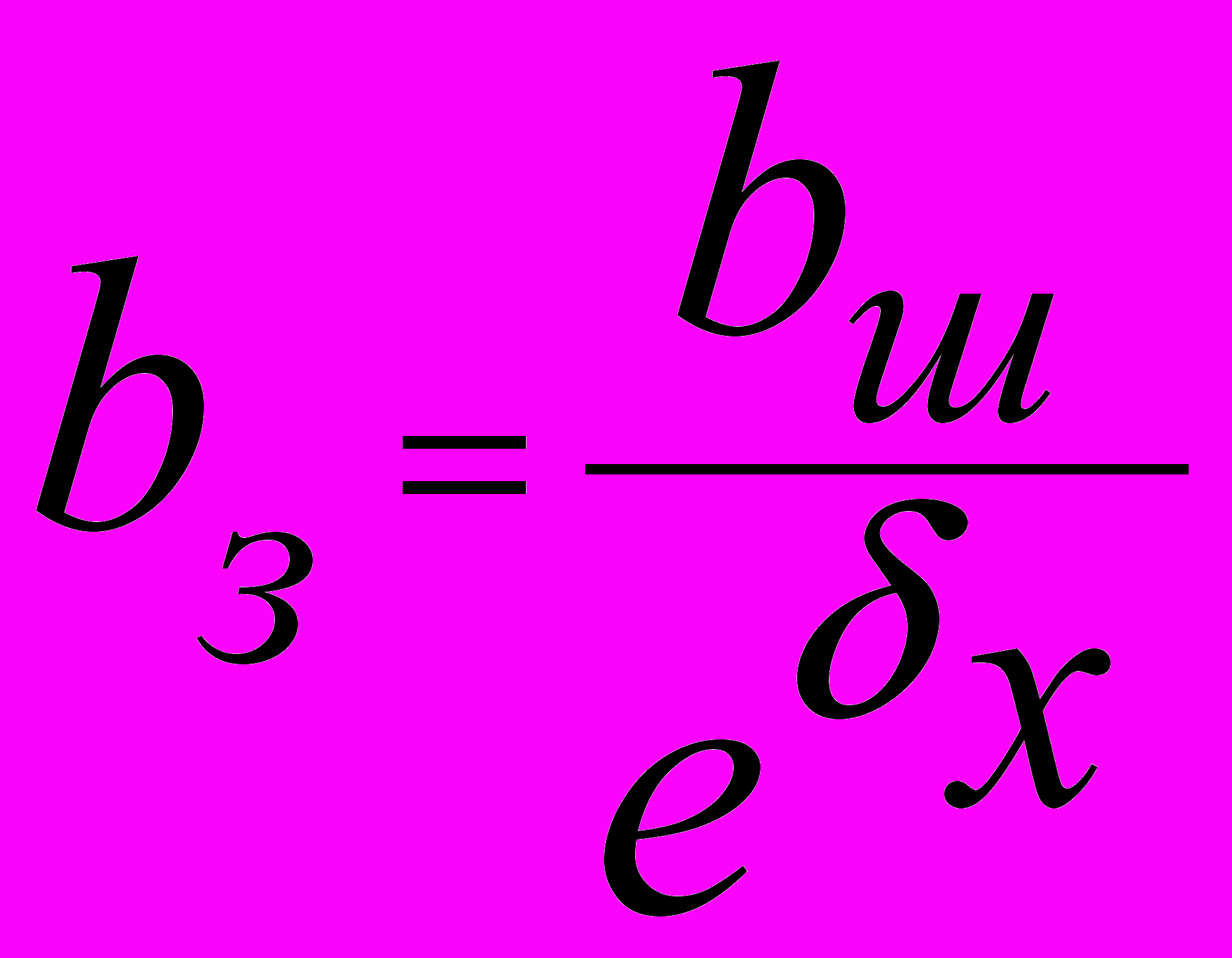
где bш – ширина штамповки; bз – ширина литой заготовки.
Каждому сечению bш с координатой Z соответствует bз с координатой
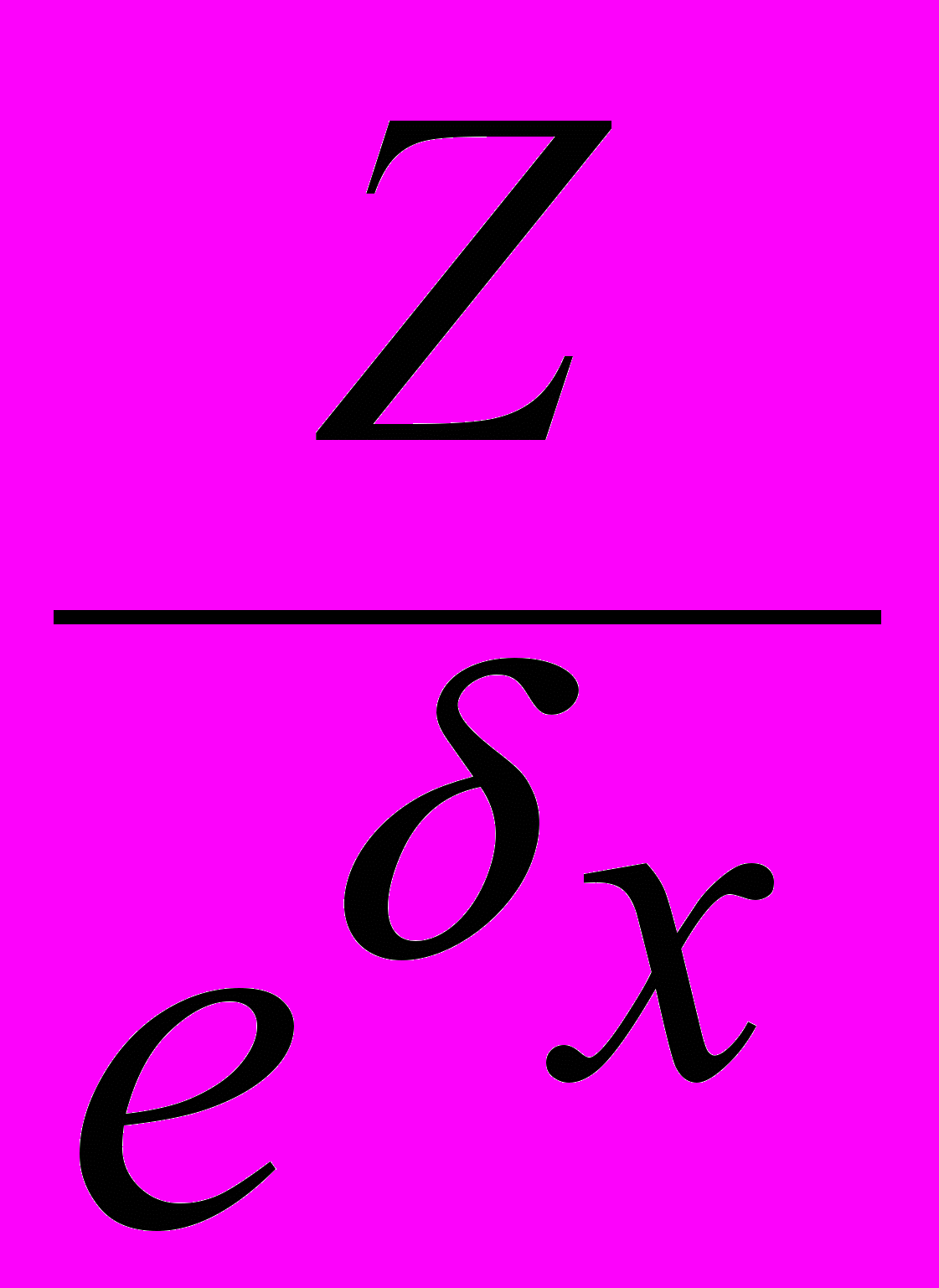
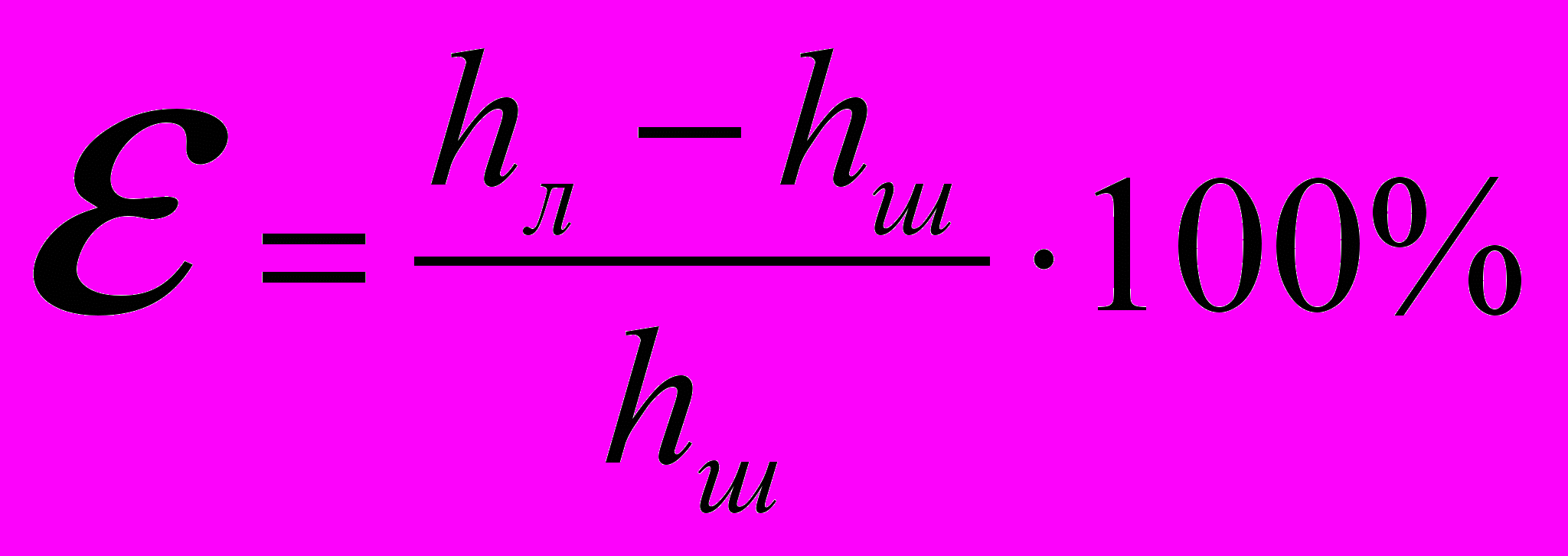
где hл – высота литой заготовки; hш – высота штамповки.
Штамповали заготовки на паровоздушном штамповочном молоте. Нагрев заготовок под штамповку производили со скоростью 1,5 °С мм/мин до 430°С. Допустимая температура нагрева заготовок под штамповку 500 °С. Полученные штампованные заготовки подвергали термической обработке (закалка и искусственное старение).
Качество заготовок, изготовленных комбинированным методом литье-штамповка, оценивали по результатам химического анализа, макро- и микроанализов шлифов и испытаний на механические свойства образцов, вырезанных из штамповки. Химический состав литых штампованных заготовок соответствовал марке алюминиевого сплава АК4–1. Контроль структуры макрошлифов показал отсутствие расслоений, трещин, пористости и неметаллических включений.
Деформация литых заготовок способствует измельчению дендритов, более равномерному распределению структурных составляющих по объему металла и ликвидации пористости.
Штамповка литой заготовки значительно повышает ее механические свойства. Временное сопротивление разрыву в увеличивается в среднем с 205 до 400 МПа. Относительное удлинение - с 4,0 до 7,5%. Средние значения в у штамповок, полученных из прессованных и литых заготовок, примерно одинаковы и составляют 400 МПа. Относительное удлинение (=7,5%) для литейно-штампованной заготовки оказалось несколько выше, чем у штамповки из прессованной заготовки ( = 6,0%).
Для выявления возможности широкого применения в производстве деталей, полученных методом литье-штамповка, проведены повторностатические испытания образцов, деталей и прочностные испытания деталей на статические нагрузки до разрушения. Цель испытаний на повторно-статические нагрузки – сравнительное определение усталостного разрушения образцов, изготовленных штамповкой из литых и прессованных заготовок.
Исследования на малоцикловую усталость проводились на гладких образцах круглого сечения 12 мм, длиной рабочей части 60 мм до полного разрушения на испытательной машине «LOSENCHAUSEN» с частотою 520 циклов в минуту. Нагружение осуществлялось по асимметричному знакопостоянному циклу. Для построения кривых усталости по результатам испытаний образцы были разбиты на три серии, с разным для каждой серии среднем напряжением m. В каждой серии три уровня. Количество образцов на одном уровне не менее трех.
Для проведения повторно-статических и прочностных испытаний деталей на статические нагрузки до разрушения была изготовлена партия «качалок». Цель испытаний на повторно-статические нагрузки – определение усталостной прочности деталей до базового числа циклов. Нагружали «качалку» по циклограмме. Расчетная нагрузка 6300 МПа (630кг). Детали, прошедшие испытания, выдерживали без разрушения 10000 циклов нагружения.
Испытания деталей на повторно-статические нагрузки показали, что детали, изготовленные методом литье-штамповка, удовлетворяют эксплуатационным требованиям.
Цель испытаний на статистические нагрузки до разрушения – определение фактической прочности экспериментальных «качалок».
Результаты испытаний считаются положительными если «качалка» выдержавшая испытания в полном объеме и последовательности, указанной в программе, и разрушалась при воздействии нагрузок выше 125% от расчетной. Расчетная нагрузка РР = 10600 МПа (1060 кг).
Запас прочности деталей, изготовленных по серийной технологии, составлял 262…294 %, а запас прочности деталей, изготовленных по предлагаемой технологии – 302…311 %.
На основании проведенных исследований была проанализирована номенклатура деталей, перевод которых на процесс литье–штамповка из прессованной заготовки наиболее эффективен. Номенклатуру подобранных заготовок составляют в основном качалки, кронштейны, вилки, фланцы массой до 5 килограмм из алюминиевого сплава марки АК4–1 для деталей «наземного» оборудования.
Пятая глава посвящена исследованиям, разработке и внедрению технологических процессов рафинирования магниевых сплавов как при приготовлении расплава под слоем флюса, так и при бесфлюсовом приготовлении. Это – электрорафинирование при приготовлении под слоем флюса, продувка газами при бесфлюсовом приготовлении, совместная обработка электрическим током и продувка газами, электрорафинирование с внутренним вакуумированием, фильтрация через фильтрирующую камеру. Все исследования проводились на сплавах Мл5 и Мл5пч.
Влияние постоянного тока на газосодержание и свойства сплава, приготовляемого под слоем флюса. На первом этапе, при приготовлении сплава Мл5 под слоем флюса, установили вид применяемых электродов, схемы их расположения и направление электрического поля – совпадающее с направлением силы тяжести расплава. Электрообработке подвергалась постоянная масса металла – 12 кг. На втором этапе исследовано влияние постоянного тока на газосодержание расплава. Установлено, что наименьшее газосодержание в расплаве наблюдается после обработки его током 50… 65 А в течение 5…7 мин (рис. 12): катод, выполненный из пластины в форме круга, был расположен в нижнем слое расплава ( в «техническом остатке»), а анод в в виде стержня – в верхнем слое жидкой ванны. Водород, в жидких магниевых расплавах, как и в алюминиевых, находится и в ионизированном состоянии. В результате электрорафинирования, ионизированный водород собирается у катода, в «техническом остатке», который не выбирается во время разливки готового сплава. При таком расположении электродов направление электрического поля совпадает с направлением силы тяжести расплава. Дальнейшее увеличение тока способствует ассоциации водорода в молекулы и возвращению их в расплав.
Наименьшее содержание газа в расплаве было получено после электрорафинирования в течении 5…7 минут независимо от величины тока, причем чем больше величина тока, тем интенсивнее удаляется газ из расплава (рис. 12, Б). В опытных плавках (рис. 12, В) в условиях производства (масса обрабатываемого расплава 180 кг) наименьшее газосодержание было достигнуто после обработки расплава током 600…750 А (время обработки током – 5 минут). Сравнительный анализ механических свойств 10 плавок показал, что в образцов, полученных из металла, обработанного током, увеличилось на 15 МПа, а – на 1,7 % по сравнению со сплавом, необработанным током. При этом содержание газа снизилось в 1,5 раза.
А
Б
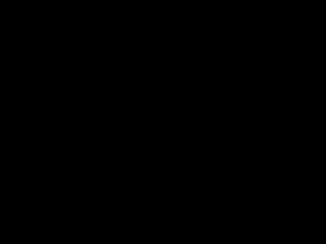
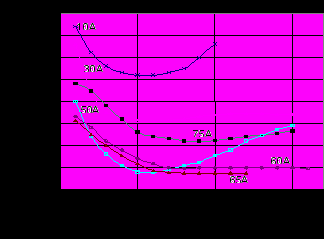
Рис. 12. Кривая зависимости газосодержания в расплаве МЛ5 от:
А – силы тока (масса сплава – 12 кг);
Б – времени обработки электрическим током (от 10 А до 75 А);
В – силы тока (масса сплава – 180 кг).
В
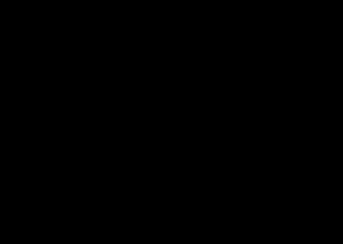
Влияние постоянного тока на газосодержание и свойства сплава при бесфлюсовом приготовлении. При исследовании и отработке технологических параметров рафинирования и модифицирования при бесфлюсовом приготовлении магниевых сплавов на первом этапе выбиралась оптимальная защитная атмосфера из различных газовых сред, содержащих активные и инертные газы и их смеси (СО2, SF6, Ar, N2). На основании проведенных исследований была выбрана защитная атмосфера из смеси SF6 и СО2. Из рис. 13 следует, что относительное изменение массы расплава от концентрации элегаза – SF6 носит экстремальный характер: с повышением его концентрации в смесях увеличивается герметичность пленки, состоящей из химических соединений MgO, MgF2, MgS, Mg3N2.
![]() ![]() | Рис. 13 Зависимость относитель-ного изменения массы расплава от времени выдержки в защитной среде Газовая среда: 1 - 0,01 % SF6 + CO2 (остальное); 2 - 0,1 % SF6 + CO2 (остальное); 3 - 0,2 % SF6 + CO2 (остальное); 4 - 1,0 % SF6 + CO2 (остальное); 5 - 2,0 % SF6 + CO2 (остальное); 6 - 5,0 % SF6 + CO2 (остальное); 7 - 10 % SF6 + CO2 (остальное); 8 - 0,5 % SF6 + CO2 (остальное) |
Время выдержки, ч. |
На следующем этапе исследовано влияние тока на качество получаемого магниевого сплава при бесфлюсовом приготовлении. Сплав Мл5 приготавливался следующим образом. В тигель загружалась шихта, при достижении температуры 400 °С тигель накрывали крышкой и через отверстие в крышке подавали защитный газ. При достижении расплавом температуры 720…740 °С через специальное окно в центре крышки колокольчиком проводилось модифицирование гексохлорэтаном. После чего в отверстие крышки вставлялся электрод, подключенный к отрицательному полюсу источника постоянного тока. Положительный полюс подключался к корпусу печи и, соответственно, к тиглю. В качестве защитного газа использовался аргон, углекислый газ и азот. Наиболее удовлетворительно зарекомендовала защитная среда из смеси углекислого газа (50 %) и азота (50 %). В остальных случаях наблюдалось значительное испарение магния, достигающее 3 %. Расход газа на плавку 20 кг сплава составлял 5…6 литров. Установлено, что обработка расплава постоянным током в процессе бесфлюсового приготовления позволяет снизить газосодержание на 4…5 см3/100 г, что весьма существенно при литье деталей, работающих в условиях герметичности.
При исследовании в производственных условиях влияния постоянного тока на качество магниевого сплава при бесфлюсовом приготовлении была использована установка собственного изготовления РПБМ-0,3, созданная на базе РПБМ-0,25. За основу взят технологический процесс приготовления магниевых сплавов, включающий плавление шихты в инертной среде, рафинирование и модифицирование сплава продувкой гелием и углекислым газом и выстаивание. Для обработки электрическим током создавалось электрическое поле между двумя электродами, один из которых располагался в верхнем слое расплава, второй – газораспределительное устройство для подачи рафинирующих и модифицирующих газов, располагался у дна тигля.
Исследования проводились на сплаве Мл5, расплавленном в среде инертного газа. Процесс рафинирования и модифицирования проводился с различным соотношением рафинирующего ( гелия - Н2) и модифицирующего (углекислого газа - СО2) газов в смеси с различным количеством электричества (1,0 – 3,0 Кулона), пропускаемого через расплав.
На основании проведенных исследований был разработан технологический процесс бесфлюсового приготовления магниевых сплавов. Сплав Мл5 расплавлялся в среде защитного газа, состоящей из смеси газов – элегаза и углекислого газа. После достижения температуры 750 – 760 °С расплав рафинировался в течение 5 минут газовой смесью, состоящей из гелия и углекислого газа в соотношении (1,0 – 2,0) : (0,1 – 0,2) с расходом гелия 24 литра, углекислого газа 2,5 литра и постоянным электрическим током с направлением электрического тока, совпадающим с гидростатическими силами пузырьков газовой смеси. При этом количество электричества, пропускаемое через 1 см3 расплава, составляло 1,70 – 1,75 Кулона. По окончании рафинирования при этой же температуре проводили модифицирование в течение 5 минут газовой смесью, состоящей из гелия и углекислого газов в соотношении (0,01 – 0,02) : (1,0 –2,0) с расходом гелия 0,4 литра, углекислого газа – 33,0 литра и постоянным электрическим током с направлением электрического поля противоположного направления чем при рафинировании. При этом, количество электричества, пропускаемого через 1 см3 расплава, оставалось прежним 1,70 – 1,75 Кулона. По окончании процессов рафинирования и модифицирования с поверхности расплава снимали шлак, после чего расплав выстаивался в течение 15 минут. Затем брались образцы для определения газосодержания, испытания на механические свойства, пробы на излом и заливались опытные партии деталей.
Получены следующие механические свойства: σв = 300 МПа; δ = 12 %. Газосодержание – 4,0…5,0 см3/100 г. Брак отливок – 5,0…7,0 %.
Излом нерафинированного сплава Мл5 имеет мелкозернистую структуру с волокнистым строением. Поверхность излома - светлая. В изломе наблюдаются крупные интерметаллические включения серого цвета и мелкие черные. В изломе образца из сплава, рафинированного флюсом, также имеются крупные и мелкие включения интерметалида, но в меньшей степени.
Излом образца из сплава, полученного при бесфлюсовом приготовлении и обработанного продувкой газами, имеет мелкозернистую, однородную, светлую структуру, мелкие интерметаллические включения черного цвета, расположенные ближе к поверхности образца.
Поверхность излома образца, полученного из сплава бесфлюсового приготовления и обработанного продувкой газами совместно с постоянным током, имеет мелкозернистую, однородную, светлую структуру. В изломе нет инородных включений и дефектов по макроструктуре. Микроструктура состоит из δ – твердого раствора алюминия и цинка в магнии с мелкозернистыми включениями Mg17Al12 (Mg4Al3).
Таким образом, обработка магниевых сплавов постоянным электрическим током при бесфлюсовом приготовлении способствует:
- понижению газосодержания в расплаве с 8 – 14 см3/100 г до 4 – 5 см3/100г;
- повышению механических свойств (временное сопротивление на разрыв с 255 до 300 МПа; относительное удлинение с 5,5 до 12 %);
- с
нижение брака отливок, особенно по герметичности с 50 – 60 % до 5 %.
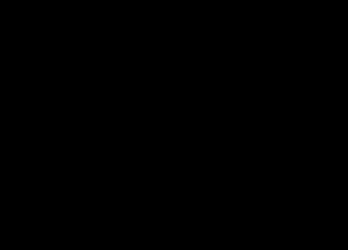
А | Б |
Рис. 14. Зависимость газосодержания в расплаве от: А - времени обработки электрическим током; Б - плотности тока на аноде |
Для оценки эффективности процесса дегазации внутренним вакуумированием, на первом этапе исследований была выявлена зависимость газосодержания в расплаве от времени обработки электрическим током и плотности тока на аноде.
Как видно из рис. 14 оптимальное время обработки соответствует 5 минутам, а плотность тока - 0,04…0,09 А/см2. При этом имеет место ионизация свободных атомов водорода и разрушение ионных связей водорода с окисью магния и гидридами, которые перемещаются к катоду и по мере накопления, образуют пузырьки, а затем всплывают на поверхность расплава. При плотности тока более 0,1 А/см2 происходит резкое увеличение газосодержания, т.е. происходит ассоциация водорода в молекулы, которые распространялись по всему объему расплава.
Совместное влияние внутреннего вакуумирования и электрического тока.
Исследовалось влияние только внутреннего вакуумирования и совместно с электрическим током на газосодержание в расплаве. Установлено, что обработка внутренним вакуумированием незначительно снижает газосодержание в расплаве (рис. 15, А). К резкому снижению газосодержания приводила совместная обработка расплава током с плотностью на аноде более 0,1 А/см2 и внутренним вакуумированием в течение 15 мин. (рис. 15, Б).
Фильтрация расплава. При исследовании эффективности обработки магниевых сплавов фильтрацией, была установлена зависимость влияния толщины и состава фильтрирующего слоя на эффект модифицирования и рафинирования. В качестве материалов фильтрирующего слоя использовали магнезит, электродный бой и магнезит + электродный бой. При фильтрации через один слой наблюдалось снижение включений до 0,2…0,3 мм2/см2 и газосодержания – до 10…11 см3/100 г, а через двухслойный фильтр – 0,05…0,10 мм2/см2 и 7…8 см3/100 г. При этом механические свойства соответствовали: σв = 280…300 МПа; δ = 7…12 % при значительном снижении защитного газа (с 800 до 500 л/плавку).
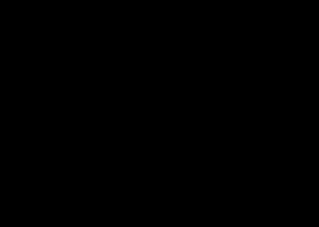
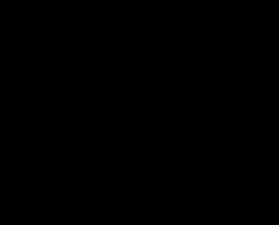
А | Б |
Рис. 15. Зависимость газосодержания от: А - времени обработки расплава внутренним вакуумированием; Б - времени обработки расплава внутренним вакуумированием и постоянным током |
При определении эффективности очистки расплава была выявлена зависимость относительного содержания включений от скорости фильтрации. При скорости фильтрации более 8 см/сек происходит значительное ухудшение очистки.
Оценка эффективности заливки форм в инертной среде, с точки зрения образования «вторичных» окислов, проводили путем изучения макрошлифов продольных разрезов участков литниковой системы с фильтрирующей сеткой. В качестве защитной среды использовалась смесь инертных газов тяжелее и легче воздуха. Причем перед разливкой в полость формы подавали один «тяжелый» газ, во время заливки – смесь «тяжелого» и «легкого» при соотношении 1:20 и после заливки тоже один «тяжелый». Давление газов поддерживали в пределах 0,02…0,03 МПа, расход 0,3 л/мин. При оценке макрошлифов было установлено, что при разливки форм без защитной среды площадь включений в литниковой системе составляла 750 мм2, а при заливке в инертной среде – 150 мм2. Испытания опытной партии деталей показали высокую герметичность отливок.
Влияние НЭМИ. При исследовании влияния ПОН расплава на процессы кристаллизации, структурообразования и некоторые свойства магниевого сплава МЛ5 плавку проводили двумя способами: в атмосфере чистого азота и под слоем флюса ВИ2. Перегрев расплава соответствовал 670 – 700 ºС, время выдержки – 5 минут, после чего расплав облучали НЭМИ в течение 5, 10, 15, 20 и 25 минут.
![]() Риc. 16. Влияние НЭМИ на кристаллизационные параметры магниевого сплава Мл5: А – плавка в атмосфере аргона; Б – плавка под слоем флюса ВИ 2 |
Продолжительность кристаллизации α-твердого раствора τл изменяется от времени облучения расплава НЭМИ по экстремальной зависимости в соответствии с расшире- нием температурного ин-тервала кристаллизации α-твердого раствора ∆t = tл–tс (рис. 16,А и Б, б). Продолжительность охлаждения сплава от tс до t1 (τс-1) имеет минимальное значение при 15-минутном облучении.
В соответствии с расширением температурного интервала кристаллизации α-твердого раствора увеличивается степень уплотнения расплава (-∆Jл) при кристаллизации. Аналогично изменяется степень уплотнения закристаллизовавшегося сплава в интервале температур tс–t1:
минимальная степень уплотнения -∆Jс-1 наблюдается при продолжительности облучения расплава НЭМИ, равной 15 минутам (рис. 16, А и Б, в). Таким образом, независимо от способа плавки наблюдается общая закономерность изменения кристаллизационных пара-метров от ПОН расплава. Плавка сплава МЛ5 под флюсом способствует меньшему изменению кристаллизационных параметров под воздействием облучения расплава НЭМИ.
С повышением ПОН расплава до 15-минутной обработки в атмосфере чистого аргона твердость сплава Мл5 возрастает почти на 10 НВ с последующим ее падением до 20-минутной обработки. В случае приготовления и кристаллизации магниевого сплава под слоем флюса твердость практически не изменяются. В обеих случаях наблюдается незначительное повышение плотности сплава Мл5.
Теплопроводность сплава МЛ5 также изменяется от ПОН по экстремальной зависимости с максимумом ее значения при 10-минтной обработке расплава НЭМИ независимо от способа приготовления сплава. Теплопроводность сплава МЛ5, закристаллизовавшегося в атмосфере чистого аргона по абсолютной величине (114 Вт/(м.к)) выше, чем у сплава закристаллизовавшегося под слоем флюса (97 Вт/(м.к)). В обеих случаях теплопроводность возрастала в 1,3…1,4 раза по сравнению с необлученным сплавом.
На основание проведенных исследований, были разработаны и внедрены технологические процессы и оборудование к его осуществлению, а именно для:
- электрорафинирования магниевых сплавов, приготовляемых под слоем флюса;
- бесфлюсового приготовления магниевых сплавов на установке РПБМ-0,3;
- электрорафинирования при бесфлюсовом приготовлении магниевых сплавов;
- РТМ (руководящий технический материал) для электрорафинирования магниевых сплавов.
Для приготовления магниевых сплавов с рафинированием постоянным током наиболее приемлемы тигельные печи сопротивления с тиглями различной вместимости и агрегаты выпрямительные типа ВАКГ.
Проведенные исследования показали, что геометрия и объем тигля не оказывают существенного влияния на режимы рафинирования постоянным током.
Для серийного внедрения была спроектирована и изготовлена печь раздаточная для магниевых сплавов РПБМ-0,3, предназначенная для бесфлюсового приготовления магниевых сплавов в среде защитного газа, который способствует образованию на поверхности расплава устойчивой газовой защитной пленки, предохраняющей расплав от воздействия с кислородом воздуха. В качестве защитной атмосферы использовался 1 – 2 % элегаз (ТУ6 – 02 – 1249 – 83) в смеси с осушенным углекислым газом (ГОСТ 8050 – 85).
Получены авторские свидетельства и патенты на технологии и оборудование, которые использованы на ОАО «КнААПО» при разработке и внедрении технологий получения отливок из магниевых сплавов.
Внедрение на ОАО «КнААПО» технологических процессов приготовления магниевых сплавов и электрорафинирования позволило снизить газосодержание в 1,5…3 раза, сократить брак отливок по негерметичности на 30…40 %, исключить брак отливок по флюсовой коррозии, увеличить долговечность и надежность литых заготовок на 5…10 %, увеличить производительность печей на 20 %, трудоемкость расплавления шихты на 15 % и получить экономический эффект в сумме 6655 тыс. руб в ценах 2004 года.
Кроме того, технологический процесс обеспечил снижение вредных газовых выделений в 50 раз, аэрозолей флюса в 10 раз, шлаков в 3 раза, что улучшило санитарно-гигиенические условия труда на участке магниевого литья.