Разработка и внедрение высокоэффективных технологических процессов изготовления отливок из алюминиевых и магниевых сплавов в авиастроении
Вид материала | Автореферат |
Режим закалки. Режим старения. |
- «производство отливок из сплавов цветных металлов», 38.25kb.
- Технология плавки и разливки магниевых сплавов, 160.13kb.
- Реферат Тема: Технология плавки и разливки магниевых сплавов, 154.86kb.
- Тема: сварка алюминия и его сплавов, 56.75kb.
- Цена дипломной работы с чертежом 500 рублей содержание, 51.27kb.
- Пояснительная записка к курсовому проекту по курсу: «Процессы и аппараты химической, 52.08kb.
- Батышев Константин Александрович исследование, 709.6kb.
- Флюсы и рециклинг алюминия, 130.43kb.
- «технология литейного производства», 45.75kb.
- Внастоящей работе проведен анализ зависимостей затухающих акустических колебаний отливок, 47.5kb.
Для приготовления сплавов использовалась лабораторная печь сопротивления собственного изготовления. Для вакуумирования расплава спроектированы и изготовлены специальный чугунный тигель с водоохлаждаемым буртиком и водоохлаждаемая крышка. Для приготовления магниевых сплавов использовался стальной тигель. Приведены технические характеристики печи. Создание вакуума над расплавом осуществлялось одноступенчатым форвакуумным насосом типа РВН-200. Контроль температуры расплав осуществлялся потенциометром типа КСП, гр. Х.А. Для преобразования переменного тока в постоянный применялся выпрямитель на диодах В-200 с тиристорной цепью управления, позволяющей осуществлять плавную регулировку тока в пределах 10…100 А. Для качественной оценки качества алюминиевого сплава по ходу плавки брали вакуумные пробы, которые разрезались по вертикальной оси и изготавливались макрошлифы. Для получения вакуумных проб использовалась установка собственного изготовления. Для гидростатического взвешивания образцов применялись весы ВК-500, точность измерения 0,001 г. Газосодержания в алюминиевых и магниевых расплавах определяли на установке Гудченко. Для сравнительного газосодержания алюминиевого сплава определялась плотность проб гидростатическим методом. Наряду с анализом на газосодержание приготовляемые алюминиевые сплавы проверялись на наличие твердых неметаллических включений по технологическим пробам Добаткина.
Для дегазации расплава металлом-геттером изготовлено устройство для введения рафинирующих средств в расплав. Для проведения процесса дегазации расплава внутренним вакуумированием использовался фильтр, состоящий из титанового корпуса и пористой графитовой вставки толщиной 10 мм. Посадку фильтра осуществляли на огнеупорный цемент.
Для рафинирования алюминиевых сплавов газофлюсовой смесью спроектировано и изготовлено специальное устройство.
Для обработки расплава постоянным током спроектирован и изготовлен электрод, состоящий из титанового стержня и герметично электроизолированного от него фланца.
Электрорафинирование магниевого расплава, приготовленного под слоем флюса, проводилось посредством двух электродов, изготовленных из титанового сплава марки ОТ4. При бесфлюсовом приготовлении для процесса рафинирования и модифицирования использовалось газораспределительное устройство для подачи газов в расплав.
Для проведения процесса рафинирования и модифицирования с одновременной обработкой расплава током при бесфлюсовом приготовлении было спроектировано и изготовлено устройство, состоящее из двух электродов – газораспределительного и титанового стержня с электроизолированным фланцем.
Для проверки отливок на герметичность пузырьковым методом был спроектирован и изготовлен пневмостенд модели К1876-0000.
Структурный анализ проводился на микроскопе «Neofot - 22».
Для определения механических свойств сплава использовалась разрывная машина модели Р-10.
Для обработки расплавов наносекундными электромагнитными импульсами (НЭМИ) использовали генераторы НЭМИ модели ГНИ-01-1-6 и ГНИ-15-1 с регулируемой амплитудой импульсов напряжения.
Для измерения теплопроводности применялся метод сравнения прохождения теплового потока через эталонный (12Х18Н10Т) и исследуемый образцы. Ддля уменьшения погрешности определения размера образцов применялся измерительный инструмент с ценой деления 0,01 мм и проводились многократные измерения линейных размеров, δ1 ≤ ±0,2 %. Для снижения погрешности определения перепада температур применялись градуированные термопары, δ ∆Т ≤ 1,5 %.
Исследования коррозионостойкости проводили «объемным» методом. Методика заключается в том, что в случае протекания процесса коррозии с водородной деполяризацией количество растворенного металла пропорционально количеству выделившегося водорода, что позволяет определить скорость коррозии по количеству выделившегося водорода. Параллельно определялась потеря массы образца по стандартной методике.
Кинетические исследования выполнены на дериватографе Q-1000 фирмы МОП при атмосферном давлении в среде воздуха при скорости нагрева 10 град/мин до температуры ~1000 оС. Ошибка измерения температуры не превышала ± 1 оС. Эталоном сравнения служил порошок аллунда Al2O3. Величина навесок составляла 0,2 г. Образец для испытания имел цилиндрическую форму диаметром 0,005 м и высотой 0,01 м.
Дериватограф использовался в Q-режиме, что позволило получить кривые потери (привеса) массы в так называемом квази-изотермическом (квази-изобарном) режиме. Образцы помещались в тигли из керамики, в одном было инертное вещество Al2O3, а в другом – исследуемый образец. Пространство печи ограничивалось кварцевым стаканом, в котором свободно поступал воздух (окислительная среда) во время нагрева. Нагрев осуществлялся линейно в течение 120 мин с последующей 6-и часовой выдержкой. При этом автоматически проводилась запись дифференциальных кривых зависимостей температуры ∆Тобр = f(Тэтал) [ДТА], массы ∆m = f(Т,τ) и скорости окисления ∆m = f(Т,τ) [ДТГ и ТГ соответственно]. На основании этих зависимостей определяли прирост массы образца в процессе окисления, причем привес массы относился к единичной его площади поверхности S
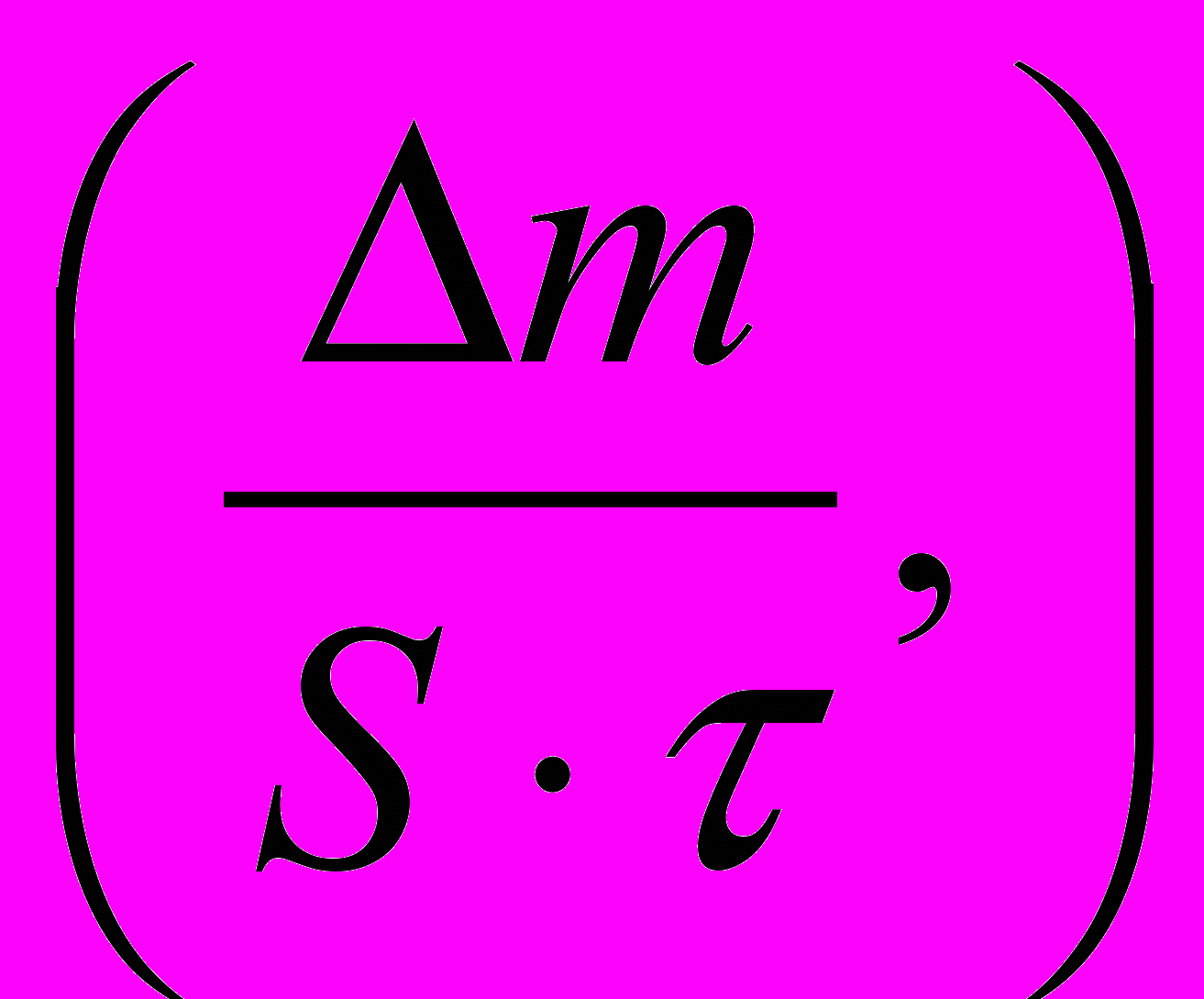
Износостойкость определялась по ГОСТ 23.2079 «Метод испытания материалов на износостойкость о нежестко закрепленные абразивные частицы».
Элементно-фазовый анализ выполнялся на установке LXA 8600 SUPEROB (Япония), электронно-микроскопическое исследование проводили на сканирующем электронном микроскопе EVO-50XP (фирма «Карл Цейс»).
В третьей главе для создания единого метода рафинирования применительно к соответствующему оборудованию, составу сплава и требованиям к сплавам исследовали влияние способов рафинирования на свойства литейных алюминиевых сплавов.
С этой целью исследовали и отрабатывали технологические параметры процесса рафинирования алюминиевых сплавов следующими методами: металлом-геттером, газофлюсовой смесью, электровакуумом, внутренним вакуумом с одновременной обработкой электрическим током, дегазирующей таблеткой «Эвтектика».
В данной главе приведены также результаты исследования по влиянию НЭМИ на процессы кристаллизации и структурообразования, физико-механические свойства алюминиевых сплавов, технологии литья и термической обработки высокопрочных алюминиевых сплавов на качество отливок, структуры и химической однородности производственного спектрального эталона из алюминиевых сплавов.
А также разработаны рекомендации по внедрению электровакуумного рафинирования алюминиевых сплавов на предприятиях авиационной промышленности, в частности на «КнААПО».
Эффективность дегазации металлом-геттером исследовали на сплаве АК8л (АЛ34). Качество сплава оценивали по вакуумным пробам, микро- и макроанализам шлифов, химическому анализу, по результатам испытаний образцов на газосодержание и механические свойства.
Исследовали зависимость газосодержания в сплаве и механических свойств от времени обработки металлом – геттером при расходе последнего 0,2% от массы расплава. По средним значениям газосодержания и механических свойств построены кривые зависимости от времени обработки (рис. 1). Как видно, обработку расплава металлом-геттером эффективно проводить в течение 6…7 мин. Металл плавился в печи сопротивления мод. САТ-0,15 емкостью тигля 150 кг. После расплавления металла и достижения температуры 740 0С вводили фторцирконат калия (0,2 мас.%) с помощью колокольчика, изготовленного из титанового прутка в виде спирали (шаг витков 4…5 мм) с коническим хвостовиком,
п
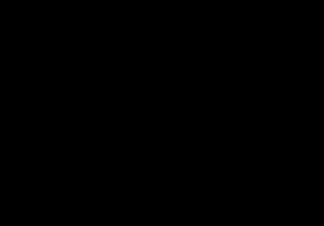
К
Рис. 1. Зависимость газосодержания в расплаве от времени обработки металлом-геттером (кривая 1) и фторцирконатом калия (кривая 2)
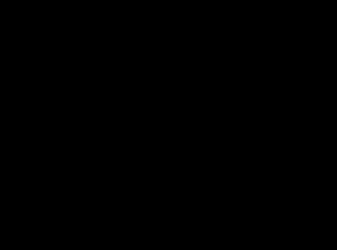
Отливки, полученные из сплава, рафинированного металлом – геттером, соответствуют требованиям производства.
П
Рис. 2. Зависимость временного сопротивления разрыву (кривая 1, 4), относительного удлинения (кривая 2, 5) и твердости (кривая 3, 6) от времени обработки металлом-геттером и фторцирконатом калия
ри исследовании технологических параметров процесса рафинирования алюминиевых расплавов газофлюсовой смесью для выявления влияния расхода и давления продуваемого газа на характер и скорость подъема пузырьков из расплава исследовали моделированием алюминиевого расплава водой, нагретой до температуры 70…800С. Установлено, что при внутреннем диаметре трубки 10 мм, давлении 0,01…0,02 МПа и расходе газа 1,5 л/мин обеспечивается невысокая скорость подъема пузырьков и создаются оптимальные условия рафинирования. Результаты исследований подтверждены опытными плавками алюминиевых сплавов АК7ч, АК8 с продувкой их флюсом (мас.%: NaCl – 33; KCl – 47; Na3AlF6 - 20) в струе аргона.
Д
Рис. 3. Зависимость газосодержания расплава от времени продувки газофлюсовой смесью
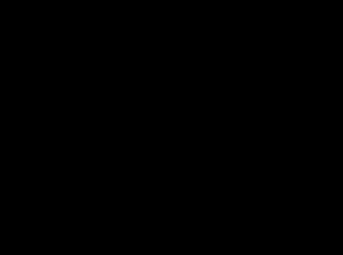










Макроструктура вакуумных проб соответствует первому баллу пористости по шкале ВИАМ. Получены следующие средние значения механических свойств:
для АК7ч (АЛ9) – σв=205 МПа;
δ=5%;
для АК8 (АЛ34) – σв =360 МПа;
δ=7%. Отливки соответствовали требованиям производства.
При исследовании и отработке параметров технологического процесса электровакуумного рафинирования расплава АЛ9 (АК7ч) на первом этапе установлено содержание газов в расплаве после вакуумирования при остаточном давлении 1,33×103 Па в течение 15 мин., которое составило 0,143…0,165 см3/100г.
На втором этапе исследований установлена зависимость газосодержания в расплаве от плотности пропускаемого через него постоянного тока (0,015…0,08 А/см2) при одновременном вакуумировании (рис. 4). Оптимальная плотность тока на аноде соответствует 0,04 А/см2.
Третьим этапом исследований было выявление оптимального времени (от 3 до20 мин.) электровакуумного рафинирования при постоянной плотности тока (0,04 А/см2). Как видно из рис. 5, оптимальное время электровакуумирования – 15 мин.
Э
Рис. 4. Зависимость газосодержания в расплаве от плотности тока
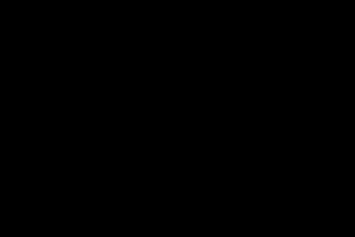






У
Рис. 5. Зависимость газосодержания в расплаве от времени обработки электрическим током
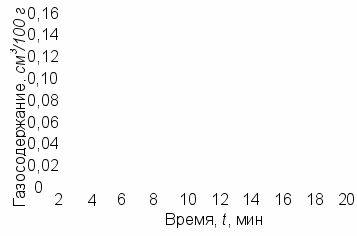








Исследовали влияние дегазирую-щих таблеток (ТУ РБ 1474/229004-98) производства НПП «Эвтектика» (г.
Минск) на эффективность очистки алюминиевых сплавов АК8л (АЛ34, АК7ч (АЛ9), АМ4,5Кд (ВАЛ10) от оксидов, шлаков и газовых включений.
В
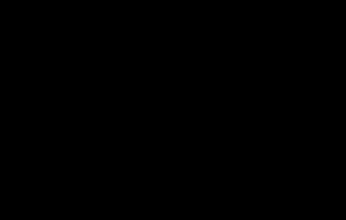
- н
а поверхности расплава образуется более «сухой» шлак и в гораздо большем количестве. Поверхность расплава после снятия шлака имеет зеркальный вид. Хорошая скатываемость образующего порошкообразного шлака с зеркала расплавленного сплава при рафинировании приводит к минимальным потерям металла, уносимого со шлаком;
- з
Рис. 6. Зависимость газосодержания в расплаве от времени обработки внутренним вакуумированием
начительно увеличилась жидкотекучесть. Образцы для определения физико-механических свойств сплава методом акустической эмиссии, имеющие размеры в сечении 3×3 мм и длину 70 мм, заливались при температуре 700…710 °С (после рафинирования расплава К2ZrF6 при такой температуре образцы не заливались – брак – 100 %).
В
Рис. 7. Зависимость газосодержания в расплаве от времени обработки внутренним вакуумированием и постоянным электрическим током




газовой пористости при заполнении формы расплавом, приготовленным по заводской технологии. После заливки партии форм расплавом, приготовленным с применением дегазирующих таблеток «Эвтектика», были получены отливки со 100 % выходом годного, не имеющие ни газовой пористости (прошли рентгенконтроль), ни незаливов.
Заливались также отливки двух видов типа «корпус» (сплав АК8л), также имеющие стабильный высокий брак по газовым раковинам. После заливки форм расплавом, обработанным дегазирующей таблеткой «Эвтектика», отливки также имели 100 % выход годного. Но отливки «Катушка», «Пушка», полученные с использованием расплава АМ4,5Кд (ВАЛ10), имели подкорковую пористость и газовые раковины.
Таким образом, дегазирующая таблетка «Эвтектика» более предпочтительна для сплавов АК8л (АЛ34) и АК7ч (АЛ9), а для сплава АМ4,5Кд необходимо провести дополнительные исследования, в результате которых было установлено:
– при обработке расплава АМ4,5Кд хлористым марганцем (MnCl2) и гексафторцирконатом калия (K2ZrF6) наблюдался брак по подкорковой пористости, газовым раковинам, по отдельным позициям до 90 %, и микротрещинам;
– при обработке расплава дегазирующей таблеткой «Эвтектика» и гексафторцирконатом калия наблюдалось снижение брака отливок по подкорковой пористости и газовым раковинам, а по микротрещинам брак находился на том же уровне. Это вызвано тем, что K2ZrF6 имеет большой удельный вес и мелкодисперсный. Вследствие чего он (K2ZrF6) не успевает прореагировать и раствориться в расплаве и выпадает в осадок (в донном осадке содержание циркония до 1,38 %). Из-за обедненности сплава цирконием уменьшается количество центров кристаллизации, увеличиваются межкристаллитные напряжения и склонность к трещинообразованию, что приводит к окончательному браку отливок после механической обработки по микротрещинам. Кроме того, после обработки расплава таблеткой «Эвтектика» присутствовал неприятный запах серы;
– при обработке расплава смесью рафинирующих (MnCl2, таблетка «Эвтектика») и модифицирующих (K2ZrF6) солей, заложенных в колокольчик послойно, сначала MnCl2 затем K2ZrF6 и таблетка «Эвтектика» в соотношении 1 : 1 - 2 : 0,5 - 0,75, брак отливок по подкорковой пористости и газовым раковинам снизился до 5 – 10 %, а брак по микротрещинам исключился. Кроме того, исчез запах серы. Использование комбинированной смеси рафинирующих солей в заданной последовательности обеспечивает оптимальное использование рафинирующих средств.
Исследовалось влияние температуры разливки металла, скорости охлаждения и влажности песчаных форм на отдельно отлитых образцах из сплава АМ4,5Кд. Часть образцов после отливки подвергалась обезводораживающему отжигу при температуре 280 °С в течение 8 часов. Все образцы термически обрабатывались по режиму Т5. Существенное влияние на механические свойства, макро- и микроструктуру сплава АМ4,5Кд (ВАЛ10) оказывают температура разливки металла и влажность песчаных форм. Высокая температура разливки металла приводит к росту зерна, газонасыщению и образованию микрорыхлоты, а это вызывает снижение прочности и пластичности. Анализ фрактограмм излома разрывных образцов показал хрупкое разрушение (камневидный излом) при температуре разливки 730 °С и вязкое разрушение (чашечный излом) при температуре 690 °С. В табл. 1 приведены результаты исследований влияния температуры разливки сплава на механические свойства, балл зерна и максимальную величину очага газоусадочной рыхлоты.
Отжиг позволяет повысить пластичность в этом случае в 2…3 раза, прочность почти не изменяется. Изменение свойств сплава АМ4,5Кд (ВАЛ10) объясняется образованием в отливках большого количества газоусадочной рыхлоты. Причём после закалки в зоне газоусадочной рыхлоты в образцах без предварительного отжига появляются микротрещины, и даже вторичная пористость. Образование микротрещин вызывает резкое снижение пластических свойств.
Таблица 1
№ плавки | Заливка металла с 730 °С | Заливка металла с 690 °С | ||||||
Механ. св-ва. | Балл зерна | Максимальная величина очага рыхлоты | Механ. св-ва. | Балл зерна | Максимальная величина очага рыхлоты, мм | |||
σв, МПа | δ, % | σв, МПа | δ, % | |||||
201 | 340,0 | 4,0 | 3 | 1,62 | 400,0 | 8,0 | 9 | 0,23 |
202 | 330,0 | 3,3 | 3 | 1,44 | 425,0 | 12,0 | 11 | 0,00 |
203 | 310,0 | 4,0 | 4 | 1,08 | 450,0 | 8,0 | 12 | 0,00 |
204 | 330,0 | 4,5 | 3 | 1,36 | 415,0 | 7,0 | 7 | 0,63 |
Повышенная влажность песчаных форм оказывает влияние в основном на газонасыщение и образование газоусадочной микрорыхлоты.
Условия изготовления титановой лигатуры оказывают существенное влияние на прочность и пластичность сплава АМ4,5Кд (ВАЛ10). Заниженная температура расплава алюминия при растворении титана приводит к образованию грубых включений TiAl3, что подтверждается пластинчатой формой выделения включений и изменением светло-серой окраски в светло-коричневую при травлении в щелочном реактиве. Грубые включения TiAl3 в отливках приводят к снижению пластичности и к хрупкому разрушению по границам этих включений.
Режим закалки. Сплав АМ4,5Кд (ВАЛ10) относится к термически упрочняемым алюминиевым сплавам. Для сплавов этой группы при нагреве под закалку необходимо получить твёрдый раствор с максимальной концентрацией упрочняющих элементов. Оптимальная температура 545 ± 3 °С для сплава АМ4,5Кд (ВАЛ10). Нагрев свыше этой температуры будет вызывать пережёг металла, т.е. в этом случае образуется каркас непластичной эвтектики по границам зёрен. Это может привести не только к снижению пластичности, но и к снижению прочности (табл. 2).
Таблица 2
Условия закалки | № плавки | Механические свойства | Балл зерна | Максимальная величина очага микрорыхлоты, мм | |
σв, МПа | δ, % | ||||
Недогрев | 178 195 199 180 170 171 162 | 280,0 355,0 391,0 370,0 235,0 214,0 380,0 | 3,00 1,33 10,00 6,35 9,70 6,30 7,00 | 6 1 5 12 8 8 7 | 0,27 1,26 0,72 0,18 0,90 0,18 0,72 |
Перегрев Пережог | 93 94 96 | 475,0 470,0 260,0 | 1,00 1,50 2,00 | 8 10 11 | 1,26 0,72 0,63 |
Удовлетворительный нагрев | 200 183 169 20 29 | 460,0 455,0 445,0 448,0 417,0 | 11,50 12,00 9,20 8,10 10,10 | 12 12 12 12 8 | 0,36 - 0,36 - 0,54 |
Охлаждение при закалке должно обеспечивать фиксацию твёрдого раствора, образованного при высокой температуре. Максимальные прочностные свойства достигаются после закалки с высокими скоростями охлаждения, но при этом возрастают как поводки, так и остаточные напряжения. Это особенно необходимо учитывать при изготовлении сложных по конфигурации и крупногабаритных деталей. С целью уменьшения закалочных напряжений исследовали влияние на прочностные свойства сплава АМ4,5Кд (ВАЛ10) закалочной среды (в горячей воде, в водной суспензии (20 %) окиси алюминия и в кипящем слое кварцевого песка). Величину остаточных напряжений оценивали по изменению размеров кольца «Френча». Результаты исследований приведены в табл. 3.
Таблица 3
Охлаждающая среда при закалке | Механические свойства | Балл зерна | ∆ S, мкм | |
σв, МПа | δ, % | |||
Вода 80 °С | 400,0 | 6,0 | 12 | -6 |
Вода 15 °С | 460,0 | 10,0 | 12 | -124 |
Кипящий слой кварцевого песка | 430,0 | 7,5 | 12 | -16 |
Водная суспензия | 480,0 | 12,0 | 12 | -26 |
Примечание - Образцы перед термообработкой подвергались отжигу при 280 °С в течении 8 часов. |
Из данных табл. 3 видно, что скорость охлаждения оказывает существенное влияние на механические свойства и остаточные напряжения. Закалка на горячую воду вызывает минимальные напряжения, но при этом наблюдается и минимальные механические свойства. Наилучшие механические свойства и малые значения остаточных напряжений получаются при закалке в водную суспензию окиси алюминия.
Режим старения. Поскольку сплав АМ4,5Кд (ВАЛ10) относится к сплавам системы Al-Cu-Mn, то он подвержен старению. В процессе старения в сплавах происходят сложные структурные изменения: сначала образуются зоны Гинье-Престона, которые затем переходят в частицы метастабильных и стабильных фаз; параллельно изменяются внутренние напряжения и мозаичная структура, концентрация дислокаций и других дефектов решётки. Во время старения может изменяться плотность и расположение дефектов, а также их характер. Исследовали влияние на механические свойства сплава АМ4,5Кд (ВАЛ10) температуры и времени выдержки при искусственном старении. Результаты исследований сведены в табл.4.
Таблица 4
Режим старения | Механические свойства | Электропроводность, м/Ом×мм2 | ||
Температура, °С | Выдержка, ч | σв, МПа | δ, % | |
150 | 4 8 | 360,0 380,0 | 14,0 12,5 | 18,7 18,6 |
160 | 1 2 4 8 12 | 340,0 360,5 415,0 430,0 450,5 | 15,5 13,6 14,2 8,0 7,1 | 18,5 18,5 18,5 18,5 18,5 |
170 | 4 8 | 450,0 450,0 | 7,5 4,3 | 18,4 18,5 |
180 | 4 8 | 425,0 435,0 | 3,0 3,7 | 19,2 19,6 |
Как видно температура и время выдержки при искусственном старении оказывают существенное влияние на механические свойства сплава АМ4,5Кд (ВАЛ10). Изменение температуры всего на 10 0С приводит к изменению пластичности почти в два раза. Оптимальными температурами искусственного старения являются 160 0С (время выдержки 12 ч) – 170 0С (время выдержки 4ч) для достижения хорошего сочетания прочностных и пластических свойств (σв = 450 МПа, δ = 7,1…7,5 %).
Для выявления влияния легирующих компонентов на качество сплава и свойства были выполнены промышленные плавки в количестве 170 штук подвергались испытанию механических свойств на отдельно-отлитых образцах, химическому и спектральному анализу. Химический состав оказывает существенное влияние на механические свойства АМ4,5Кд:
- увеличение содержания железа свыше 0,1…0,11 % приводит к резкому снижению не только пластичности, но и прочности сплава АМ4,5Кд (ВАЛ10). Для исключения попадания железа в сплав необходимо пользоваться инструментом только из титана, а также производить обновление возврата;
- медь, кадмий и титан при содержании свыше 4,6 %, 0,18 %, 0,21 % соответственно снижают пластичность сплава и увеличивают прочность.
Исследованиями установлено, что основной причиной брака тонкостенного кокильного литья являются включения, которые попадают в отливку с металлом при недостаточной степени рафинирования, а также образующиеся при контакте металла с атмосферой во время заливки «вторичные» окислы. Для исключения образования и попадания в отливку «вторичных» окислов создается защитная атмосфера из инертного газа вокруг струи заливаемого металла. Этот принцип был использован в данной разработке при проектировании устройства защиты струи алюминиевого сплава, заливаемого в кокиль, инертным газом. Для оценки эффективности заливки в инертной среде, с точки зрения образования «вторичных» окислов, заливку осуществляли в кокиль, в литниковой системе которого смонтирована фильтрующая сетка марки ССФ-4 для улавливания неметаллических включений в виде окислов. При заливке в инертной среде образование окислов происходит в значительно меньшей степени. Так при диаметре фильтрующей вставки с сеткой 50 мм, площадь сечения окисных включений в литниковой системе вокруг фильтрующей сетки составила более 750 мм2 при заливке без защитной атмосферы. При заливке кокиля сплавом в струе защитного газа площадь сечения включений в литниковой системе вокруг фильтрующей сетки составила 150 мм2. В процессе заливки кокилей создавали рабочее давление аргона в пределах 0,02…0,03 МПа, расход аргона 0,3 л/мин, что обеспечивает создание инертной среды вокруг струи расплава и сокращения брака кокильного литья на 10 %.
Одно из важных условий получения качественных отливок без рыхлот, включений и химической неоднородности – выбор кокиля для отливки эталонов для спектрального анализа сплавов и при соблюдении ряда необходимых условий: соответствия по форме и размерам как стандартным эталонам, так и размерам и формам рабочих образцов, отливаемых в двухрожковый кокиль. В производственных условиях для достоверности и точности определения химического состава сплава по ходу плавки спектральным анализом используются государственные стандартные образцы (ГСО) и «рабочие» эталоны - стандартные образцы предприятия (СОП). Однако ГСО и контрольные СОП имеют ряд существенных недостатков. Количество и номенклатура выпускаемых ГСО недостаточны. Изготовление СОП по ГОСТ 7727-81 и ГОСТ 7728-79 не обеспечивает производство стандартными образцами в достаточном количестве. В связи с этим необходимо обоснование выбора оптимальной формы для изготовления СОП и использования их в комплексе с ГСО для оперативного и качественного определения химического состава плавок алюминиевых сплавов. Первоначально исследования проводили на отливках «рабочих» эталонов в кокиля следующих форм: кокиль двухрожковый; кокиль «солнышко», предложенный инж Н.К. Тихомировой; кокиль, имеющий гравюру рабочей полости «гребешковой» формы.
Исследование рентгенограмм образцов из сплава АК8л (АЛ34) - самого многокомпонентного из алюминиево-кремнистых сплавов, отлитых в кокиля этих типов, показали большую структурную неоднородность эталонов. Спектральные исследования химического состава этих образцов также выявили большую химическую неоднородность, особенно в местах расположения рыхлот. Вследствие проведенной работы было выявлено, что для отливки «рабочих» эталонов из сплава АК8л эти кокиля использовать нельзя. Поэтому был разработан новый тип кокиля с восемью образцами эталонов и с дополнительным питателем у образцов для изучения структурной и химической однородности отливок образцов из сплава АК8л. Все образцы подвергались рентгеновскому просвечиванию на выявление структурных неоднородностей. Все образцы без исключения имели однородную структуру без каких – либо признаков рыхлот. Следовательно, они полностью удовлетворяют требованиям, предъявляемым к «рабочим» эталонам. Анализ кривых распределения всех элементов приводит к выводу, что все элементы распределяются по высоте эталона достаточно равномерно, о чем говорит средняя арифметическая ошибка однородности, просчитанная на этом образце: кремний – 2,75 %; железо – 4,42 %; бериллий – 4,43 %; титан – 4,99 %; магний – 7,49 %; марганец – 6,69 %. Внедрение СОП, отлитых в кокиль «гребешковой» формы, позволило уменьшить трудоемкость, повысить качество анализов и ускорить выдачу плавок.
В настоящее время представляется возможным управление процессом формирования отливок с определенным комплексом свойств воздействием на расплав наносекундными электромагнитными импульсами (НЭМИ). В связи с этим представляет большой теоретический и практический интерес проведение целенаправленного исследования влияния продолжительности облучения жидкой фазы НЭМИ (ПОН) на кристаллизационные параметры, физико-механические (теплопроводность, плотность, твердость, микротвердость структурных составляющих) и эксплуатационных (жаростойкость, коррозионностойкость, износостойкость) свойства промышленных алюминиевых сплавов (АК7ч и АК7). Методика исследований заключалась в следующем.
Нагрев производили до температуры 900 °С, после 5-ти минутной выдержки при этой температуре обрабатывали расплав НЭМИ путем погружения излучателя печь, изолировав его от контакта с жидким металлом с помощью алундового наконечника, прозрачного для наносекундных электромагнитных волн. Плавку проводили в алундовом тигле ( 300 мм и высота 50 мм) на установке «ПАРОЛОИД-4» конструкции «ЦНИИТМАШа». В качестве излучателя использовался стальной стержень (сталь 3) диаметром 6 мм. Продолжительность обработки расплава НЭМИ соответствовала 5, 1,. 15, 20 и 25 минут. Затем после отключения генератора НЭМИ (ГНИ-01-1-6), определялась интенсивность (обратная величина плотности) гамма-проникающих излучений в процессе охлаждения со скорость 20 °С/мин до температуры 300 °С. Параллельно строилась термограмма кристаллизации.
В качестве примера на рис. 8, а-ж приведены результаты влияния ПОН расплава на кристаллизационные параметры и свойства алюминиевого сплава АК7ч. Установлено, что:
- увеличение продолжительности облучения расплава ПОН наносекундными электромагнитными импульсами (НЭМИ) способствует повышению температур начала кристаллизации α-твердого раствора (tл), начала (tнэ) и конца (tкэ) кристаллизации эвтектики; расширяется температурный интервал кристаллизации α-твердого раствора и время его кристаллизации возрастает; увеличивается также продолжительность кристаллизации эвтектики;
- степень уплотнения расплава (-∆Jж), гетерофазного (α + ж) - ∆Jл и эвтектического - ∆Jэ постоянно возрастает по мере увеличения ПОН; коэффициенты термического сжатия расплава ж и закристаллизовавшегося сплава тв увеличиваются с повышением ПОН; ж < тв, т.е жидкий сплав подвергается усадке в меньшей степени, чем твердый силумин; таким образом, под воздействием НЭМИ происходит существенное изменение строения расплава, о чем свидетельствует изменение параметров жидкого состояния -∆Jж и ж;
| а | | д | |
Температура (t, ºС) | ![]() | Теплопроводность, (λ, Вт/м·К) | ![]() Плотность (d, г/см3) | |
| б | | е | |
Продолжительность кристаллизации (τ, мин) | ![]() | Коэффициент износостойкости | ![]() Твердость (HB) | |
| в | | | |
Степень уплотнения расплава, (J·103, имп/с) | ![]() | Жаростойкость (удельный прирост массы образцов (Δm/S, г/м2) | ж | |
![]() | ||||
| г | |||
Коэффициент термического сжатия (α, имп/(с·°С)) | ![]() | |||
| Продолжительность облучения расплава НЭМИ, мин | | Продолжительность облучения расплава НЭМИ, мин | |
Рис. 8. Зависимость кристаллизационных параметров и физико-эксплуатационных свойств силумина АК7ч (АЛ9) от продолжительности обработки расплава НЭМИ | |
- износостойкость и твердость силуминаАК7ч также изменяется от ПОН по экстремальной зависимости с максимумом их значений при 15 – минутном облучении; в сплаве АК7 износостойкость монотонно возрастает до 25 – минутного облучения;
- обработка расплава НЭМИ отрицательно влияет на жаростойкость силуминов;
- увеличение ПОН расплава АК7ч и АК7 способствует измельчению структурных составляющих до 15 – минутного облучения с последующим их укрупнением при длительных облучениях расплава НЭМИ;
- увеличение и укрупнение количества кристаллов кремния приводит к снижению твердости силуминов.
Результаты микрорегеноспектрального анализа не – и облученных НЭМИ сплавов АК7ч показали, что:
- в необработанном НЭМИ сплаве в α-твердом растворе растворяются кремний (15,6 мас. %) и магний (0,49 мас. %). В кремнистой фазе содержание кремния колеблется от 82,36 до 92,34 мас. %, алюминия от 7,58 до 17,68 мас. % и магния от 0 до 0,08 мас %. Таким образом, в эвтектическом кремнии все-таки растворяются алюминий и магний;
- в светлом кристалле, кристаллизующемся в переплетенном виде с кремнистой эвтектикой, обнаружено повышенное содержание Fe (22,39 мас. %), Mn (7,38 мас. %), Cr (0,22 мас %), Si (9,15 мас. %) и Al (60,19 мас. %.). Следовательно, светлые кристаллы можно считать включениями железистой фазы AlxSiyFez с небольшими содержаниями Mg, Cr, Mn и др.;
- при облучении расплава НЭМИ в течение 5 – 10 минут кристаллы железистой фазы пластинчатой формы кристаллизуются в металлической основе в изолированном виде. При облучении расплава НЭМИ в течение 15 минут кристаллы железистой фазы пластинчатой формы в структуре исчезают и появляются включения этой фазы в виде компактной формы.
При дальнейшей обработке расплава НЭМИ вновь появляются кристаллы железистой фазы пластинчатой формы:
- увеличение продолжительности обработки до 10 мин способствует снижению растворимости кремния в α-твердом растворе. При этом содержание магния в нем доходит до уровня фона. При дальнейшем увеличении продолжительности облучения НЭМИ (ПОН) расплава растворимость магния и кремния в α-твердом растворе существенно возрастает. Растворимость Si и Mg изменяется по обратной зависимости от таковой алюминия при повышении ПОН расплава.
Таким образом, вследствие энергетического взаимодействия корпоткоимпульсных электромагнитных полей напряженностью 105…107 В/м с металлическим расплавом происходит локальное разрушение его кластерной структуры, приводящие к изменению физических характеристик расплава и кристаллизационных параметров, физико-механических и эксплуатационных свойств силуминов.
На следующем этапе исследовалось влияние мощности (амплитуды импульсов напряжения) генератора на кристаллизационные параметры и теплопроводность силумина АК7ч. Использовали генератор НЭМИ марки ГНИ-15-1 с регулируемой амплитудой импульсов напряжения до 15 кВ (5, 10 и 15 кВ). По заводской технологии силумин нагревали до температуры 740 °С, после 5-ти минутной выдержки облучали жидкую фазу в течение 15 минут, при котором была достигнута максимальная теплопроводность при использовании генератора НЭМИ ГНИ 01-1-16 с амплитудой импульсов напряжения 6 кВ.
Из рис. 9 следует, что увеличение амплитуды импульсов напряжения (АИН) способствует повышению температур начала кристаллизации α-твердого раствора tл и эвтектики tэ. Время их кристаллизации уменьшается (рис. 9,а и б). В соответствии с сокраще-
н
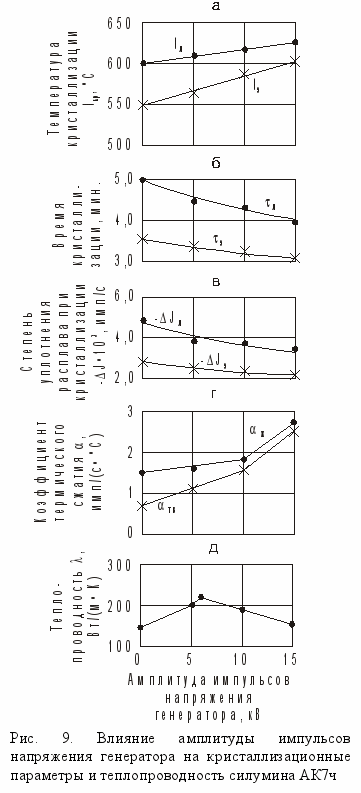
Вибрационная обработка расплава также существенно оказывает влияние на процессы кристаллизации и структурообразования силумина. Воздействие вибрацией на жидкую фазу осуществляли погружением в расплав стального переходника диаметром 10 мм. Применяли генератор звуковой частоты (400 Гц) марки Г3-12. температура расплава соответствовала 750 °С, а время обработки 2,5; 5,0; 7,5; и 10,0 минут.
Из рис. 10, а – б следует, что с увеличением продолжительности обработки расплава вибрацией (ПОВ) намечается тенденция снижения кристаллизационных параметров (τл, τэ). Степень уплотнения расплава при кристаллизации α-твердого расплава -Δ Jл незначительно уменьшается, а степень уплотнения расплава при эвтектическом превращении -Δ Jэ существенно снижается до 5-ти минутной продолжительности обработки расплава вибрацией с последующим ростом значения -Δ Jэ до 10 минут.
Средний размер кристаллов α-твердого раствора уменьшается по мере повышения ПОВ до 10 мин от 80 до 50мкм, а ширина эвтектического зерна, наоборот, увеличивается от 100 до 330 мкм при 10-ти минутной обработке расплава вибрацией. Следовательно, при вибрационной обработке происходит одновременное уменьшение размера α-твердого расплава и увеличение размера эвтектических зерен. Микротвердость α-твердого раствора и эвтектики приведены на рис. 10 г, д.
| г |
Микротвердость Н20, МПа | ![]() |
| д |
Микротвердость Н20, МПа | ![]() |
Время воздействия вибрации, с |
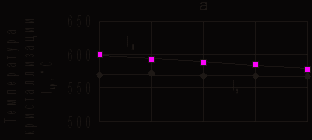
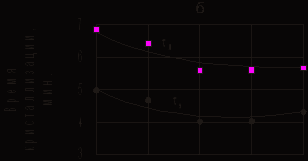
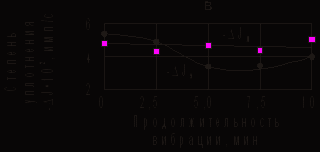
Рис. 10. Влияние продолжительности вибрации на кристаллизационные параметры и микротвердость структурных составляющих:
г – микротвердость α-твердого раствора;
д – микротвердость эвтектики
Теплопроводность силумина незначительно (до 163 – 171 Вт/(мК)) повышается при вибрационной обработке вследствие частичного удаления из расплава неметаллических включений и структурных изменений.
В работе подробно рассмотрены возможные механизмы влияния НЭМИ на вышеуказанные параметры с позиции современных представлений о жидкостном металле и его взаимодействия с электромагнитным полем высокой напряженности.
Н
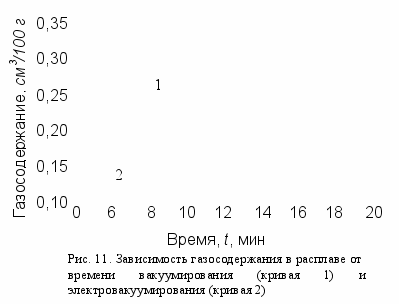
Для базового предприятия были разработаны чертежи и изготовлены установки модели ВЭР-200, которые были использованы при внедрении технологического процесса электровакуумного рафинирования.