Лабораторно-практическая работа №1
Вид материала | Практическая работа |
- Урок лабораторно-практическая работа "Изготовление накладных карманов с использованием, 181.27kb.
- Методичні рекомендації 2008р. Кишкан Л. Б. Гудак Е. П. Інформатика. Лабораторно практичні, 733.15kb.
- Практическая работа по курсу «Рынок ценных бумаг». Фундаментальный анализ (практическая, 28.71kb.
- Практическая работа по географии в 6 классе безногова, 371.26kb.
- Тематический план лабораторно-практических занятий дисциплины «физическая и коллоидная, 129.77kb.
- Первая Всероссийская конференция Лабораторно-техническое и методическое обеспечение, 68.61kb.
- Методические указания к лабораторно-практическим занятиям для студентов очного и заочного, 620.25kb.
- Коркачёва Дина Александровна, учитель информатики высшей категории Апатиты 2010 Оглавление, 221.69kb.
- План- конспект урока по биологии в 9 классе Корнилова Наталья Павловна, 47.82kb.
- Анализировать и сравнивать, 157.08kb.
ЛАБОРАТОРНО-ПРАКТИЧЕСКАЯ РАБОТА № 1
ВЫБОР ГЛАВНОЙ ОПЕРАЦИОННОЙ БАЗЫ ПРИ БАЗИРОВАНИИ ВТУЛКО И ДИСКООБРАЗНЫХ ЗАГОТОВОК КОМПЛЕКТОМ БАЗ, СОСТОЯЩИМ ИЗ ОТВЕРСТИЯ И ТОРЦА
Цель работы
Выявить экспериментальным путем на моделях граничную длину оправки, определяющую условия перехода с одного комплекта баз на другой комплект с целью обеспечения заданной точности расположения обработанных поверхностей. В теоретической части вводится понятие «главная операционная база» и кратко излагается процедура назначения допусков на размеры в технологической операции.
I. Теоретическая часть
Комплект баз – это совокупность баз, используемых на данной операции для достижения требуемой точности размеров и расположения обрабатываемых поверхностей, заданных в технических требованиях на операцию. Для какой-то определенной операции значимость каждой базы из комплекта неодинакова. В комплекте баз можно выделить главную базу. Главная база обеспечивает положение обрабатываемых поверхностей и лишает заготовку трех или четырех степеней свободы. Для ограничения остальных степеней свободы по мере надобности для решения технической задачи на операции используют дополнительные базы. Главную базу необходимо выделять в первую очередь потому, что она обеспечивает выполнение технических требований по взаимному положению поверхностей, что обычно является самой сложной технической задачей на операции. Для различных заготовок может быть использован один и тот же способ базирования главной базой, если в качестве нее принять одинаковые по форме поверхности.
Рис. 1. Базирование деталей на оправках (без зазора): а) – дискообразных; б) - втулкообразных |
Главную базу из комплекта баз выбирает конструктор приспособления. Иногда это делает технолог при разработке технологического процесса, проставляя на операционном эскизе значками тип опорного элемента и число опорных точек. За главную базу предпочтительно брать поверхность, которая обеспечивает заготовке устойчивое положение в приспособлении даже при базировании только одной этой базой.
На выбор главной базы влияет также точность исходных размеров и допускаемых отклонений расположения обрабатываемой поверхности. За главную следует принимать базу, от которой заданы наиболее точные размеры и наименьшие отклонения расположения.
Базирование втулко- и дискообразных заготовок в приспособлении, как правило, достигается двумя или тремя базами (комплектом) и сводится оно к последовательному базированию отдельными базами (рис. 1).
Назначение допусков на размеры в технологических операциях неразрывно связано с выбором главной операционной базы. Поясним на примере (рис. 2). Обрабатывается участок цилиндрической поверхности (конечное положение инструмента изображено контуром режущей пластины). Необходимо назначить допуск на размеры А, Б или сделать заключение о сравнительной их точности. Предположим, что зазор между отверстием заготовки и центрирующим пальцем (оправкой) остается постоянным на всей длине контакта, тогда можно выделить два предельных случая. Для дискообразных деталей (см. рис. 2, а), имеющих опорную торцевую поверхность значительных размеров и ограниченной протяженности контакт центрирующей внутренней поверхности, т.е. при отношении внешнего диаметра заготовки к длине внутреннего центрирующего отверстия
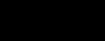
Рис. 2. Схема для определения операционных допусков с учетом выбора главной операционной базы |
Для лишения всех шести степеней свободы применяется комплект, состоящий не менее, чем из трех баз. Одна из них – главная, а остальные дополнительные. Дополнительная не должна дублировать функций, выполняемых элементами для базирования главной базой.
Для рассматриваемых предельных случаев при базировании заготовки по отверстию и торцу втулко- и дискообразных деталей, для которых однозначно устанавливается главная операционная база, можно выявить границу ее смены с одной поверхности на другую. Поясним на примере.
Предположим, что заготовка (рис. 3) имеет две базы: плоскость торца Б и поверхность цилиндрического отверстия А диаметром

Рис.3. Схема для установления границы смены главной операционной базы |
Этот предельный случай напоминает двоевластие, выражающееся в наличии двух главных баз – отверстие и торец одновременно. Но такого быть не может, так как такие две главные базы должны были бы лишить деталь семи степеней свободы. Длину оправки lr назовем граничной длиной, которая разделяет их на длинные и короткие. При большой длине оправка будет поворачивать деталь, контакт по плоскости торца превратится в точечный, а ось отверстия будет стремиться совпасть с положением оси оправки (рис. 3, в). Неточность взаимного положения оси отверстия и оправки определяется величиной зазора и расстоянием между их контактными точками. Точность базирования в этом случае должна рассматриваться по явной базе с учетом величины зазора и длины оправки. Чем больше длина оправки и меньше зазор, тем базирование по отверстию точнее. Существует такая длина оправки, не превышающая длины отверстия, при которой можно обеспечить отклонение от параллельности оси базы и оправки в пределах требуемой точности. Точное базирование по главной базе «отверстие» может быть обеспечено только при контакте с оправкой без зазора, а именно на разжимной оправке или жесткой, но посаженной с натягом. В этом случае появляется скрытая база – «ось отверстия заготовки», что позволяет обеспечивать концентричность обрабатываемой поверхности по отношению к ней, как к главной базе (рис. 3, г). в случае применения оправки с гарантированным зазором и заготовки с ошибкой расположения торца к отверстию : 100 мм граничную длину lr оправки можно определить по формуле:

Вернемся к случаям базирования детали, показанным на
рис. 2. Допуск на размер А можно назначить по таблицам среднеэкономической (средне-статистической) точности для токарных работ из справочника. Эти таблицы составлены для случаев, когда технологическая база выбрана правильно, имеет минимальные погрешности формы, совпадает с измерительной. Любое отклонение от этих случаев вносит погрешность, которую следует прибавлять к допускам взятым из таблиц.
Для случая, изображенного на рис. 2, а, можно назначить

Поэтому допуск на размер Б включает две составляющие
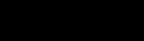
В случае, показанном на рис. 2, б, главная база – отверстие обеспечивает возможность получать размер Б с большей точностью и при отсутствии зазора между отверстием и оправкой можно назначить

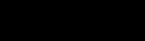
Погрешности взаимного расположения баз можно не учитывать только при выборе способа базирования по главной операционной базе, т.к. ее ориентирование осуществляется первой из группы баз. Способ базирования дополнительными базами должен выбираться с учетом погрешностей взаимного расположения баз. В размеры, получаемые от дополнительных баз, необходимо добавлять погрешности, связанные с расположением баз.
Таким образом, предложенная лабораторная учебная установка, рассматриваемая в экспериментальной части работы, показывает каким путем выполняется разработка способа базирования на данной операции комплектом баз:
Выбирается главная база из комплекта.
Определяется способ базирования главной базой данной формы, устанавливается, каких степеней лишится заготовка.
Устанавливается, какие степени свободы у заготовки останутся.
Выбирается способ базирования дополнительной базой, при этом не допускается дублирование функций, выполняемых главной базой.
Контрольные вопросы для защиты работы
Что такое комплект баз?
Охарактеризуйте понятия «главная операционная база» и «дополнительная база».
Как выбирается главная операционная база?
Охарактеризуйте комплект баз для базирования втулко- и дискообразных деталей на оправках цилиндрических жестких с зазором и без зазора, конических и разжимных. Изобразите теоретические схемы базирования для каждого варианта.
Как назначается допуск на размеры при проектировании технологической операции?
Что вкладывается в понятие средняя экономическая точность обработки? Объясните, откуда берется эта величина.
Какие условия установки должны быть выполнены, чтобы при назначении операционного допуска можно было ограничиться величинами таблиц средней экономической точности для соответствующего вида работ?
В какой последовательности разрабатывается способ базирования на конкретной операции комплектом баз?
Что такое граничная длина оправки, и каким образом ее можно определить?
II. Экспериментальная часть
Выявить экспериментальным путем на плоских моделях граничную длину оправки с целью выбора главной операционной базы для обработки детали с заданной точностью расположения баз и точностью размеров. Работа выполняется на учебной установке (рис. 4). Установка моделирует сечение в диаметральной плоскости консольно-расположенной жесткой цилиндрической оправки с буртом. Величина вылета консоли оправки может быть настроена в широком диапазоне размеров перемещением ее по направляющим вдоль оси симметрии. Модель детали составная, позволяет настраивать с желаемой точностью относительное расположение ее баз (отверстие и торец) и величину зазора между отверстием и оправкой с большим масштабом увеличения.
Рис. 4. Установка для моделирования схемы базирования деталей на оправках: а – учебная установка; б – модель детали |
Порядок выполнения экспериментальной части
Смоделировать величину зазора между оправкой и отверстием. Для этого установить модель детали на установку, прижать неподвижной направляющей отверстия к образующей оправки. Вставить щуп в зазор перемещением подвижной направляющей планки и зафиксировать настроенный размер стопорными винтами.
Настроить величину отклонения от перпендикулярности баз (торца и отверстия). Для этого повернуть на определенную величину основание модели детали с фланцем по отношению к направляющей части отверстия и зафиксировать винтом достигнутое положение. Эта настройка выполняется вне установки.
Настроить минимальный вылет оправки.
Установить настроенную модель детали в рабочую зону установки.
Медленно увеличивать вылет оправки, вводя ее в отверстие детали до того момента, когда нарушится линейный контакт ее фланца с опорой в бурт оправки. Это положение оправки является границей смены главной операционной базы.
Измерить величину вылета. Сравнить экспериментальные данные с расчетными для принятых величин погрешностей.
Смоделировать последовательно несколько вариантов модели-детали с различной величиной погрешности расположения баз при постоянной величине зазора. Для каждого варианта определить вылет оправки, соответствующий границе смены главной базы.
Аналогично п.7 повторить серию экспериментов по определению границы смены баз для фиксированной ошибки расположения баз и при изменяющемся зазоре.
Проанализировать самостоятельно варианты базирования втулко- и дискообразных деталей на разжимных и конических оправках. Выполнить эскизы схем базирования для этих вариантов установок.
Литература
ГОСТ 21495-76. Базирование и базы в машиностроении.
Кошеленко А.С. Методические рекомендации к выполнению лабораторных работ по курсу "Технология машиностроения". – М.: Изд-во УДН, 1991. – 48 с., ил.
Лабораторно-практическая работа № 2
Исследование точности базирования деталей по плоскости и двум отверстиям
Цель работы
Выявить экспериментальным путем на лабораторной учебной установке погрешность базирования деталей, ориентированных по плоскости и двум отверстиям с осями, перпендикулярными этой плоскости. Оценить влияние указанных погрешностей на точность взаимного расположения поверхностей, обработанных на различных операциях для различных вариантов относительной точности номинальных размеров базовых отверстий модели-детали и установочных элементов приспособления.
I. Теоретическая часть
Установка по двум отверстиям и плоскости, перпендикулярной осям отверстий, используется очень широко при обработке деталей малых и средних размеров типа корпусов, плит и др. Базирование приспособлений-спутников на позициях автоматических линий осуществляется по этой схеме.
Реализуется такая схема базирования опорными планками (плитами) и двумя пальцами (рис.1), при этом длина пальцев зависит от того, какая база принимается за главную. Предположим, что плоскость В принята за главную базу (рис. 1, б), которая в этом случае является установочной (реализуется планками 1, 3), лишает деталь трех степеней свободы - одного перемещения и двух вращений вокруг координатных осей. Тогда базирование дополнительными базами (отверстиями А, Б) реализуется короткими пальцами 2, 4.
Распределение опорных точек между поверхностями, входящими в комплект баз, может быть изменено, если глубина хотя бы одного из отверстий больше его диаметра, как это имеет место на рис. 1, а. В отверстии А расположены четыре опорные точки, реализуемые длинным пальцем 1. Отверстие А – главная
Рис.1. Примеры базирования детали плоскостью и двумя отверстиями: |
база, двойная направляющая. Тогда в отверстии Б располагается одна точка (опорная база), которая реализуется коротким пальцем 2. На плоскости В располагается одна точка (опорная база), которая реализуется малой площадью контакта с опорой пальца 1. Между плоскостью В и опорой пальца 2 должен быть зазор S.
Рассмотрим теоретическую схему базирования для примера аналогичного варианту, представленному на рис. 1, б.
Изображение такой теоретической схемы базирования детали на координатные плоскости Х'Y'Z' декартовой системы координат представлено на рис. 2. Корпусная деталь, выполненная в объемном изображении, базируется комплектом баз, состоящим из плоскости Б и двух отверстий N и M. Плоскость Б является главной базой, лишает деталь трех степеней свободы - одного перемещения вдоль оси Z (т. 1) и двух вращений вокруг оси Y (т. 2) и оси X (т. 3). Реализуется эта явная установочная (главная) база опорами (штырями) 1, 2, 3. Вид в плане на координатную плоскость Х'О'Y' изображает эту базу символом опорной точки
( ) с соответствующими номерами. В проекции на плоскость Х'О'Z' главная база Б символизируется теми же опорными точками, но уже как вид сбоку ( ). И аналогичная символика изображения главной базы как вид сбоку ( ) имеет место в проекции на плоскость Y'O'Z'. На эту плоскость проектируются виды в сечении АСР и ВВ. Отверстие N принято за первую дополнительную базу и лишает деталь двух степеней свободы, а именно перемещений вдоль двух координатных осей Х (т. 5), Y
(т. 4). Это двойная опорная явная база символизируется опорными точками в проекции на плоскость Х'О'Y' как вид сбоку. Реализуется эта база коротким цилиндрическим пальцем. В проекции на плоскость Х'О'Z' эта двойная опорная база обозначается также опорными точками 4, 5, но символ опорной точки 4 представлен как вид в плане ( ), а для точки 5 как вид сбоку. В проекции на плоскость Z'O'Y' (сечение АСР) символика этой базы зеркально поменялась, а именно точка 4 представлена как вид сбоку, а точка 5 - вид в плане. Отверстие М принято за вторую дополнительную базу и лишает деталь последней шестой степени свободы - вращения вокруг вертикальной оси Z (т. 6), реализуется срезанным пальцем. Символизируется эта опорная явная база на плоскости Х'О'Y' как вид сбоку ( ). На плоскость Z'O'Y' в сечении ВВ (диаметральная плоскость отверстия М) также представлен вид сбоку - точка 6. А на плоскость Х'О'Z' эта точка 6 изображается как вид в плане. Принято изображать столько проекций видов схем базирования, сколько необходимо для полного представления о наложенных связях на перемещение детали.
Эта схема базирования часто используется, что объясняется следующими ее достоинствами: лишая деталь всех шести степеней свободы, она обеспечивает свободный доступ инструментов для обработки заготовки с разных сторон; позволяет реализовать принцип единства баз и тем самым получать размеры и относительные повороты поверхностей детали координатным методом; позволяет достаточно просто фиксировать заготовки и приспособления-спутники на поточных и автоматических линиях.
Плоскость и два отверстия - всегда чистовые базы. Плоскость обрабатывают начисто на одной из первых операций, отверстия, как правило, развертывают по 7 квалитету. В качестве установочных элементов, как уже отмечалось выше, применяют опорные пластинки и два неподвижных или выдвижных пальца. Выдвижные пальцы применяют при установке крупных и тяжелых заготовок, когда они задвигаются в приспособление сбоку по направляющим, а также для фиксированного положения приспособлений-спутников на позициях автоматических линий.
Конструктивно различают установку на два цилиндрических пальца или на один цилиндрический и один срезанный пальцы. Граница применимости этих сочетаний определяется точностью диаметров и взаимного расположения базовых отверстий и требуемой точностью выдерживаемых на операции относительных расстояний и поворотов обрабатываемых поверхностей.
Рис. 2. Теоретическая схема базирования по плоскости и двум коротким отверстиям |
При проектировании приспособлений с двумя пальцами перед конструктором всегда стоит задача определения диаметров пальцев, допусков на их изготовление и износ, допуска на межцентровое расстояние пальцев. Исходными условиями, которыми должен руководствоваться конструктор при решении этой задачи, являются:
1) обеспечение установки на два пальца любой заготовки с межцентровым расстоянием и диаметром отверстий в пределах заданного допуска;
2) обеспечение требуемой точности получаемых на операции размеров и взаимного положения поверхностей.
Диаметр одного из пальцев обычно задают равным номинальному размеру диаметра базового отверстия, а допуск назначают по f6, е9 в зависимости от точности отверстия. Диаметр второго пальца определяют, исходя из первого условия.
Существуют определенные условия, определяющие возможность установки деталей на два цилиндрических пальца. На рис. 3, а показано положение базовых отверстий 1 и 2 и пальцев 3 и 4 при номинальном размере межцентрового расстояния между ними L. Для вывода условия установки рассмотрим наихудший случай (рис. 3, б), когда межцентровое расстояние отверстий выполнено на наибольшему предельному размеру











Рис. 3. Установка детали на два пальца |
Если необходимо выбирать минимальный зазор между пальцем и вторым отверстием так же, как и для первого отверстия по f6 – e9 то, как видно из условия (1), допуски на межцентровые расстояния должны быть очень малы. Это делает обработку базовых отверстий дороже. Обычно допуски на межцентровые расстояния пальцев и отверстий значительно шире допусков на их диаметры. Поэтому чтобы выдержать условие установки детали на два цилиндрических пальца диаметр второго пальца приходится значительно уменьшить. Определим диаметр второго пальца исходя из условия, что расстояние S2min равно разности между минимальным диаметром отверстия dо2 и максимальным диаметром пальца dп2; т.е. S2min = do2 – dп2. Подставив это выражение в уравнение (1), получим S1min + do2 – dп2 = м.о + м.п, отсюда

где п2 – допуск на диаметр второго пальца, который выбирают так же, как и для первого.
Следовательно, чтобы сохранить возможность установки на два цилиндрических пальца, необходимо увеличить минимальные зазоры в сопряжениях пальцев и отверстий, а это чаще всего приводит к недопустимому снижению точности установки. Значительно повысить эту точность, при сохранении возможности гарантированной установки любой детали из партии с межцентровым расстоянием базовых отверстий в пределах заданного допуска, удается, если второй палец будет срезанным, а не цилиндрическим. Конструктивные элементы пальцев (кроме исполнительного диаметра) должны выполняться в соответствии с ГОСТом (рис. 4).
Рис. 4. Пальцы установочные постоянные |
Схема установки заготовок на один цилиндрический и один срезанный палец показана на рис. 3, в. Как видно, срез пальца увеличивает зазор х в направлении общей оси двух базовых отверстий О1О2, что позволяет установить заготовки с более широким допуском. Поэтому при расчете диаметра срезанного пальца следует выбирать стандартную величину цилиндрической ленточки b. Условие установки можно записать аналогично формуле (1), заменив S2min на х:
S1min + x м.о + м.п. ( 3 )
Величину х определим, рассмотрев два секторных треугольника О2КМ и

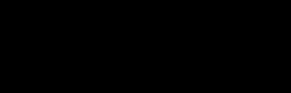
отсюда
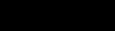
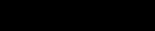
Тогда условие (3) можно записать

и диаметр срезанного пальца

При установке на два пальца возможны два случая:
когда обеспечивается контакт базовых отверстий с пальцами по определенным образующим;
когда такого контакта нет.
На рис. 5 приведена схема установки в первом случае, когда сила Q обеспечивает контакт базовых отверстий с пальцами по образующим в точках К и М. При такой установке могут возникать погрешности размеров А, Б, В, Г, Д и взаимного смещения . Погрешности указанных размеров вызваны несовмещением технологической и измерительной баз. Технологическая база – это непосредственно реальный контур базовых отверстий, а измерительная принадлежит скрытой точке оси этих базовых отверстий.
Погрешности базирования А, Б, В

В направлении размеров Г и Д не действуют силы, которые обеспечивали бы постоянный контакт базовых отверстий и пальцев по определенным образующим, поэтому погрешности базирования размеров Г и Д
Г = о1 + S1min + п1 ; Д = о2 + S2min = п2. ( 6 )
Рис. 5. Образование погрешностей размеров при установке на два пальца |
В случае установки детали на срезанный палец изменение положения оси центрового отверстия относительно оси срезанного пальца в направлении межцентрового расстояния может происходить в пределах х, поэтому

Во втором случае, при отсутствии сил, обеспечивающих контакт базовых отверстий с пальцами по определенным образующим, погрешности всех размеров будут больше, чем по первому варианту.
Контрольные вопросы для защиты работы
Дайте характеристику комплекту баз, состоящему из плоскости и перпендикулярными ей осями двух отверстий.
Какие элементы станочного приспособления реализуют эту схему базирования?
На какой параметр точности обрабатываемой детали оказывает относительная точность выполнения дополнительных баз и установочных элементов приспособления, реализующих эту схему базирования?
Объясните, почему один из двух установочных пальцев имеет ромбическую форму, и каким образом он ориентируется в станочном приспособлении?
Как определить величину погрешности базирования и как влияет относительное расположение обрабатываемой поверхности и дополнительных баз на ее величину?
Какой комплекс мероприятий можно рекомендовать при проектировании станочных приспособлений с целью снижения ошибок базирования?
Существуют ли производственные условия (и если да, то какие?) для снижения ошибок базирования на эксплуатируемых приспособлениях техпроцесса?
II. Экспериментальная часть
Описание конструкции экспериментальной установки
Измерение ошибок базирования выполняется на учебной лабораторной установке (рис. 6), где представлена конструкция и фото общего вида установки с исследуемой моделью детали. Конструкция установки реализует схему базирования, описанную ранее (см. рис. 1, б или рис. 2).
Корпус 1 имитирует установочную поверхность нижней плиты приспособления, а пластина 4 является моделью обрабатываемой детали. Для создания различных вариантов базирования в корпусе 1 и модели 4 выполнено по четыре отверстия, которые сверлились и развертывались совместно, чтобы обеспечить их попарную соосность. Втулки 5 с коническими отверстиями позволяют точно устанавливать комплекты сменных пальцев – цилиндрического 2 и ромбического 3 или двух цилиндрических. Индикаторы 6, 7 и 8 обеспечивают фиксацию ошибки базирования.
Рис.6 Учебная лабораторная установка |
Порядок выполнения работы
В отверстия конического профиля поочередно вставляется первая пара пальцев. На пальцы надевается модель детали.
Цилиндрический палец вставляется в крайнее левое отверстие корпуса, а ромбический палец последовательно переустанавливается в оставшиеся три отверстия. Это обеспечивает моделирование размера L между отверстиями. Для смены положения ромбического пальца модель детали необходимо снять. При каждой установке оценивается точность базирования. Для этого покачивают модель сначала по часовой стрелке, выбирая зазоры между отверстиями и пальцами, а затем против и снимают показания стрелок индикаторов 6, 7, 8. Результаты заносят в таблицу. Все переходы эксперимента повторяются аналогично и для второй пары пальцев.
По полученным данным следует произвести расчеты, позволяющие оценить, как влияет на точность взаимного расположения поверхностей, обработанных на различных операциях, погрешность базирования дополнительными базами для различных вариантов относительной точности номинальных размеров базовых отверстий модели детали и установочных элементов приспособления.
Расчет погрешности базирования при обработке сложной детали на агрегатном станке1
Рассмотрим влияние смещения детали (при установке) на координаты осей обрабатываемых в ней отверстий. Для точек, расположенных в пределах


где
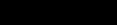
Smax, max – зазоры в сопряжениях обрабатываемая деталь – установочные пальцы и фиксаторы – направляющие втулки соответственно. На учебной лабораторной установке
(рис. 6) вторая составляющая равна 0, так как реализуется случай установки на жесткие пальцы. Определим слагаемые погрешности в направлении осей Х и Y, приняв дугу МС1, в связи с ее малостью, в качестве прямой. В полученном треугольнике катеты Х и Y определяют величины смещения точки в направлении соответствующих осей:

При этом
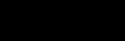
Подставив в (8) значения , заменив R1 в формуле (7), получим
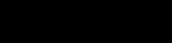
Рис. 7. Схема иллюстрирующая влияние погрешностей на расположение осей обрабатываемых отверстий (1 – 5 – номера шпинделей) |
В общем случае при обработке большого количества заготовок, кроме поворота в обе стороны от среднего положения, возможно смещение заготовки на тех же зазорах в направлении осей координат на величину

Тогда точка М расположится в некоторой области F, ограниченной по осям X и Y величиной

С1М + С2М = С1С2.
Соотношение величин, составляющих погрешности базирования по осям координат, можно изменить в желаемом направлении путем иного расположения пальцев и базовых отверстий.
Если перенести центр ромбического пальца из точки О2 в точку О3, что повлечет перемещение центра поворота заготовки в точку О1, то смещение точки М определится отрезком Ml1 вместо МС1. В этом случае величина



При установке корпусных деталей в рабочих позициях их базовые поверхности могут занимать нижнее, боковое или верхнее положение. При верхнем расположении установочные элементы меньше загрязняются, изнашиваются и подвергаются воздействию горячей стружки. Характер образования погрешности базирования аналогичен нижнему расположению. При реализации баз на вертикальных элементах корпуса приспособления зазоры в сопряжениях палец – отверстие всегда смещаются вниз и погрешность базирования, таким образом, будет однозначной, не превышающей половины зазора. Однонаправленность погрешности при такой установке позволяет учесть ее при настройке технологического процесса. Однако эффект уменьшения погрешности базирования может быть достигнут лишь в случае неизменной ориентации заготовки на всех этапах технологического процесса. В случае поворота заготовки вокруг продольной оси зазоры сместятся в противоположную сторону и погрешность базирования по отношению к ранее обработанным поверхностям будет равной полной величине зазора в сопряжениях «базовые отверстия – установочные пальцы».
Литература
Корсаков В.С. Основы конструирования приспособлений. Учебник для вузов. М.: Машиностроение, 1983.
Косилова А.Г. Точность обработки деталей на автоматических линиях. М.: Машиностроение, 1976.
ГОСТ 21495 – 76. Базирование и базы в машиностроении.
Терликова Т.Ф. и др. Основы конструирования приспособлений: Учебное пособие для машиностроительных вузов. – М.: Машиностроение, 1980. – 119 с., ил.
Уткин Н.Ф. Приспособления для механической обработки. – 2-е изд., перераб. и доп. – Л.: Лениздат, 1983. – 175 с., ил.
Кошеленко А.С. Методические рекомендации к выполнению лабораторных работ по курсу "Технология машиностроения". – М.: Изд-во УДН, 1991. – 48 с., ил.
ЛАБОРАТОРНО-ПРАКТИЧЕСКАЯ РАБОТА № 3
ИЗМЕРЕНИЕ ОШИБОК БАЗИРОВАНИЯ ДЕТАЛЕЙ ПРИ УСТАНОВКЕ НА ЦЕНТРОВЫЕ ОТВЕРСТИЯ