Лабораторно-практическая работа №1
Вид материала | Практическая работа |
Последовательность выполнения экспериментальной части Содержание отчета Цель работы Влияние приспособления на погрешность обработки Погрешность базирования Погрешность установки |
- Урок лабораторно-практическая работа "Изготовление накладных карманов с использованием, 181.27kb.
- Методичні рекомендації 2008р. Кишкан Л. Б. Гудак Е. П. Інформатика. Лабораторно практичні, 733.15kb.
- Практическая работа по курсу «Рынок ценных бумаг». Фундаментальный анализ (практическая, 28.71kb.
- Практическая работа по географии в 6 классе безногова, 371.26kb.
- Тематический план лабораторно-практических занятий дисциплины «физическая и коллоидная, 129.77kb.
- Первая Всероссийская конференция Лабораторно-техническое и методическое обеспечение, 68.61kb.
- Методические указания к лабораторно-практическим занятиям для студентов очного и заочного, 620.25kb.
- Коркачёва Дина Александровна, учитель информатики высшей категории Апатиты 2010 Оглавление, 221.69kb.
- План- конспект урока по биологии в 9 классе Корнилова Наталья Павловна, 47.82kb.
- Анализировать и сравнивать, 157.08kb.
Последовательность выполнения экспериментальной части
Модель № 1 с минимальной глубиной центровых отверстий устанавливаем между центрами. Контур Б обращен к передней бабке. Предварительно центры установки находятся в крайнем правом положении. Передний центр 1 зафиксирован гайкой 2. Замыкаем двусторонние связи модели по центровым отверстиям, перемещением заднего центра 6 влево и стопорим его гайкой 8. Настраиваем инструментальную оснастку на обработку контура «С», совместив режущую кромку пластины Р1 с торцем 2/ детали, что соответствует ее конечному положению в цикле обработки при перемещении суппорта на рабочей подаче. Это крайнее левое положение суппорта обеспечивается каждый раз при повторных циклах моделируемой траектории перемещения режущих кромок инструментов настройкой винтового упора, который не показан на рис. 4. Далее последует ускоренный отвод резца Р1 в исходное положение на начало нового цикла обработки. Конечное положение режущей кромки постоянно повторяется при обработке следующих деталей. Затем последовательно устанавливаются модели № 2, № 3, у которых глубина центровых отверстий больше, чем у модели № 1, что является причиной смещения всего контура модели с торцем 1 (измерительная база) влево, в сторону шпинделя. Положение торца 2 в результате обработки определяется конечным положением режущей кромки резца Р1. Переместим верхнюю подвижную часть модели (контур С) до соприкосновения с режущей кромкой Р1. В результате появляется модель контура детали после обработки на данной операции с фиксированным положением относительно смещения торцев 1max и 1min. Величина этого смещения бп и есть ошибка базирования при выполнении размера А на операции как следствие неточности выполнения технологической базы. Таким образом, величина ошибки базирования определяется величиной предельных положений измерительной базы в направлении измеряемого размера. Величину ошибки базирования измеряем штангенциркулем и сравниваем с расчетной
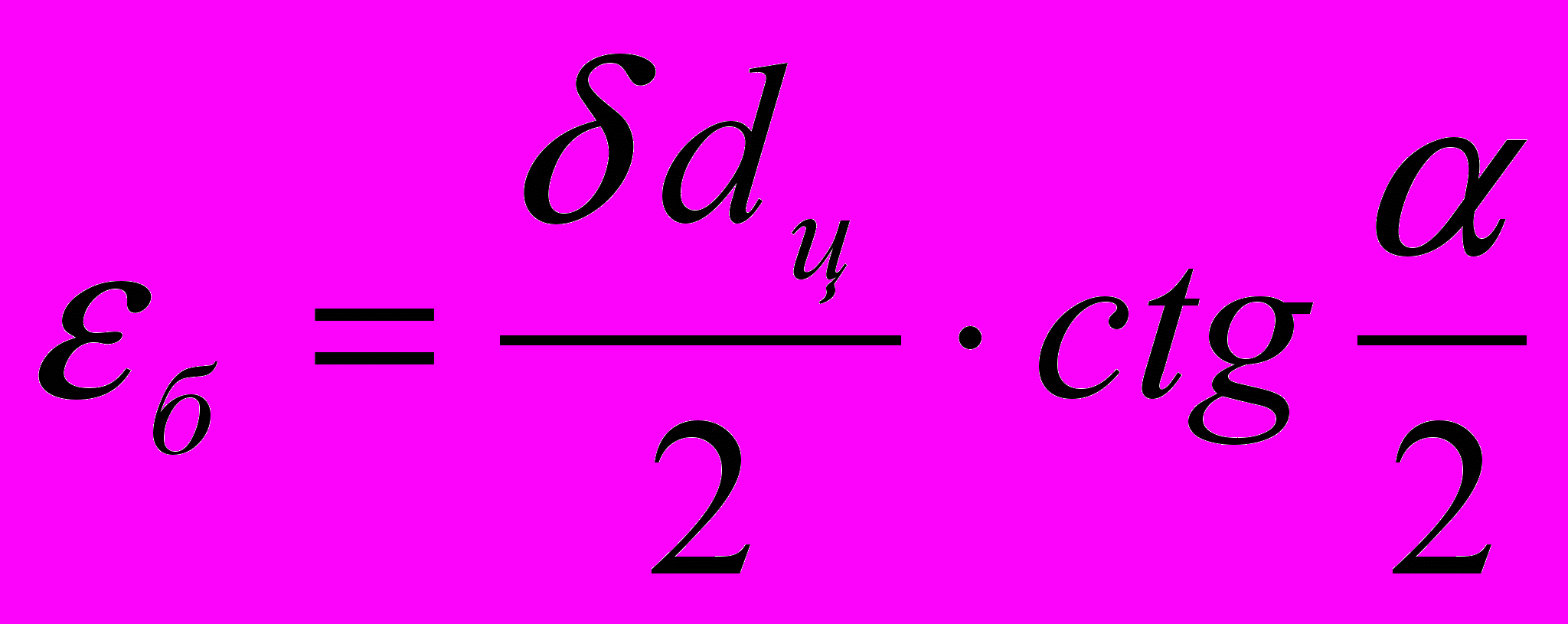
где
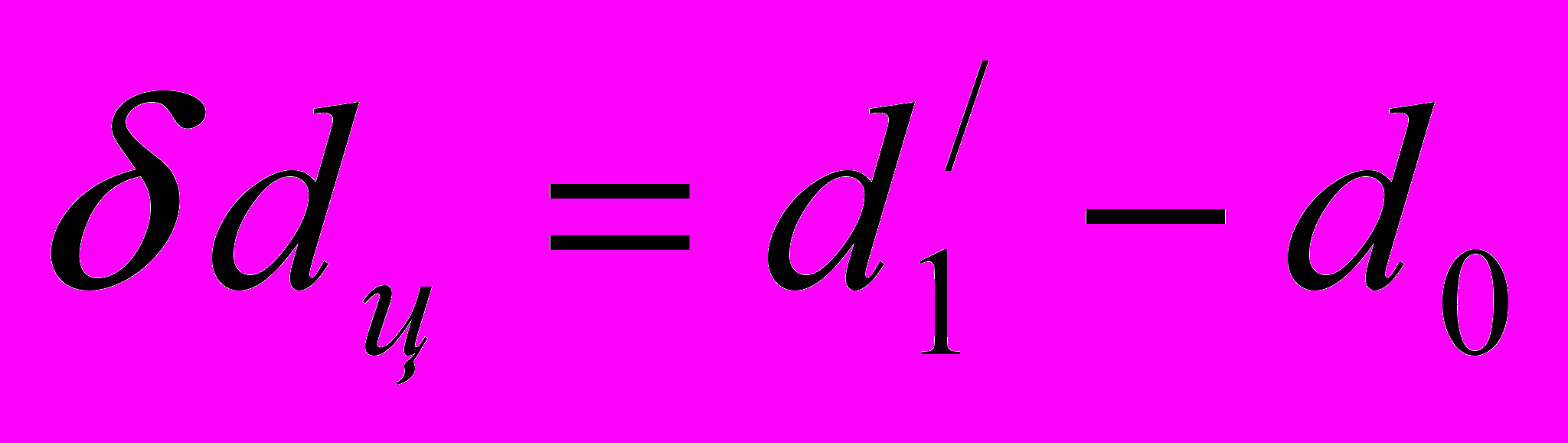
- угол конуса центрового отверстия.
Выполнив трансформацию моделей № 2 и № 3 смещением контура «С», переходим к моделированию профиля деталей при обработке контура «Б» на следующей, то есть текущей операции. Настраивается конечное положение инструмента (резец Р2) по модели № 1, а на моделях № 2 и № 3 смещается подвижная часть «Б». Относительное положение торцев 2/max, 2/min и 2 обусловлено ошибкой базирования на данной операции из-за ошибок в изготовлении технологических баз, использованных на текущей и предшествовавшей операциях. На точность выполнения размера «С» не оказывает влияние схема базирования, так как имеет место компенсирующаяся погрешность. При выполнении экспериментальной части копировать контур эталонной и трансформирующейся моделей на лист миллиметровой бумаги, установленный на платформе под моделями. Рекомендуется обводить контуры исследуемых моделей разным цветом для удобства при сопоставлении результатов экспериментов. Результаты измерения и расчета представить в табличной форме. Таблицу выполнить в произвольной форме. Сравнить расчетные величины ошибок базирования с экспериментальными.
Содержание отчета
В отчете в произвольной форме представить ответы на контрольные вопросы и результаты эксперимента.
Литература
- ГОСТ 21495 – 76. Базирование и базы в машиностроении.
- Матвеев В.В. и др. Размерный анализ технологических процессов. М.: Машиностроение, 1982.
- Терликова Т.Ф. и др. Основы конструирования приспособлений: Учебное пособие для машиностроительных вузов. – М.: Машиностроение, 1980. – 119 с., ил.
- Кошеленко А.С. Методические рекомендации к выполнению лабораторных работ по курсу "Технология машиностроения". – М.: Изд-во УДН, 1991. – 48 с., ил.
ЛАБОРАТОРНО-ПРАКТИЧЕСКАЯ работа № 4
ИССЛЕДОВАНИЕ ТОЧНОСТИ обработки партии деталей НА ФРЕЗЕРНОМ СТАНКЕ с учетом погрешности базирования
Цель работы
Изучить влияние приспособления на погрешность обработки. Ознакомиться с методами достижения точности и методами настройки металлорежущего оборудования на выполнение технологической операции. Выполнить анализ теоретической схемы базирования при установке деталей типа «ось» на неподвижной призме. Определить размеры настройки станка по любой детали из партии с целью обработки всей партии деталей с учетом погрешности базирования.
I. Теоретическая часть.
Влияние приспособления на погрешность обработки
Технологическая система состоит из отдельных элементов и подсистем, каждая из которых влияет на погрешность обработки. Для определения требований к точности составляющих элементов и подсистем технологической системы необходимо четко представлять механизм их влияния на общую погрешность обработки и уметь количественно оценить это влияние.
Приспособление должно обеспечить требуемое положение заготовки относительно инструмента. Для партии заготовок по ряду причин это положение не является идентичным, а получает рассеяние в некоторых пределах. Величину поля рассеяния положений измерительной базы заготовки для данного выдерживаемого размера относительно инструмента называют погрешностью установки у.
Погрешность установки у входит составной частью в общую погрешность обработки:

где: о – суммарная погрешность обработки на заданной операции;
у – погрешность выполняемого размера, вызываемая упругими отжатиями элементов технологической системы под влиянием нестабильности сил резания;
н – погрешность настройки станка;
у – погрешность установки;
и – погрешность, вызываемая размерным износом режущего инструмента;
т – погрешность, вызванная тепловыми деформациями технологической системы;
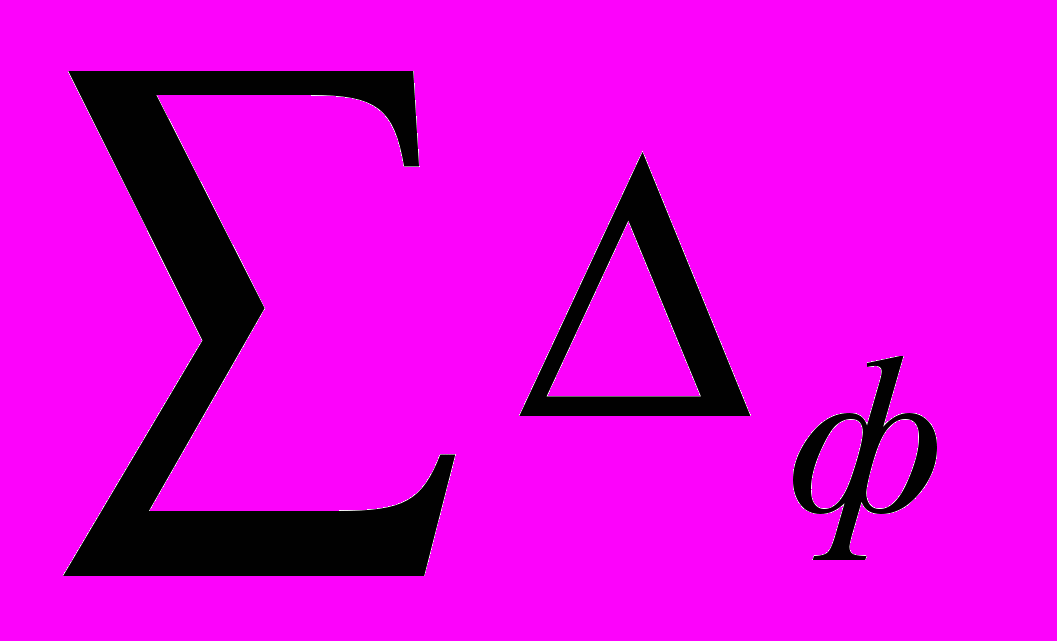
Исходя из того, что погрешность обработки не должна превышать величину технологического допуска т, проектируемая схема установки заготовки должна обеспечить допустимую погрешность установки у доп:

Необходимое положение заготовки в приспособлении достигается после ее базирования и закрепления. Базирование – это придание заготовке требуемого положения относительно выбранной системы координат. Закрепление – приложение сил к заготовке для обеспечения постоянства ее положения, достигнутого при базировании. Погрешность установки у включает погрешности, сопутствующие обоим процессам.
Рис. 1. Схема для определения погрешности базирования прямоугольной заготовки | Рис. 2. Схема для определения погрешности базирования заготовки по центральному отверстию на цилиндрический палец |
Погрешность базирования – есть отклонение фактически достигнутого положения заготовки при базировании от требуемого положения.
Погрешность базирования – величина геометрическая. Для данной схемы базирования она определяется проекцией расстояния между предельными положениями измерительной базы заготовки на направление получаемого при обработке размера. Для одного и той же схемы базирования она может быть различной. При совмещении измерительной и технологической (установочной) баз погрешность базирования равна нулю.
На рис. 1 показана схема базирования прямоугольной заготовки для фрезерования в ней паза. При обработке партии заготовок погрешность базирования относительно размера А равна нулю, так как измерительная и технологическая базы совмещены в плоскости 1 заготовки. Погрешность базирования относительно размера В равна допуску на размер С заготовки. В этом случае технологическая база (плоскость 1) не совмещена с измерительной базой (плоскость 2). Погрешность базирования относительно размера Е будет равна нулю, так как плоскость заготовки 3 является одновременно направляющей технологической и измерительной базой.
Схема базирования заготовки по центральному отверстию на цилиндрический палец приспособления приведена на рис. 2. При посадке без зазора (разжимной палец) погрешность базирования для размера А равна половине допуска на диаметр заготовки. При наличии зазора погрешность базирования для того же размера возрастает на величину предельного изменения зазора. Во всех случаях отклонения размеров элементов формы (деталей), полученных мерным инструментом, не зависят от погрешности базирования. Так, для размеров В и С (рис. 2) погрешность базирования равна нулю. Для размера С поверхность 1 является настроечной технологической базой. Имеет место компенсирующаяся погрешность.
Погрешность закрепления з – это разность предельных смещений измерительной базы в направлении получаемого размера под действием силы зажима заготовки. Заготовка смещается в результате упругих деформаций отдельных звеньев цепи, в которой происходит силовое замыкание заготовки: заготовка – установочные элементы – корпус приспособления. При достаточной жесткости корпуса приспособления и заготовки погрешности закрепления зависят в основном от перемещений в стыке «заготовка – установочные элементы». Одновременно с измерительной смещается также и технологическая база.
Если величина смещения измерительной и технологической баз (как бы велика она ни была) постоянна для партии заготовок, то погрешность закрепления равна нулю, так как это смещение может быть учтено в настроечном размере.
Величина смещения технологической базы при закреплении не постоянна для партии заготовок. Это объясняется изменениями силы зажима, микрогеометрии и физико-механических свойств поверхностного слоя технологических баз заготовок.
На рис. 3, а приведена схема появления погрешности закрепления детали при обработке углового паза шириной А. Под действием силы зажима Q контактная база смещается. При изменении силы зажима в пределах Qmin – Qmax контактная база будет смещаться от m’n’ до m’’n’’. В данном примере контактная технологическая база совпадает с измерительной, т.е. в результате изменения силы зажима измерительная база занимает те же положения, что и технологическая. Погрешность закрепления в случае равных жесткостей опор (частный случай) можно рассчитать по формуле
з = (ymax – ymin)cos, ( 3 )
где – угол между направлением получаемого размера и направлением приложения силы зажима.
Рис. 3. Схема появления погрешности закрепления |
Погрешность закрепления з – случайная величина, так как изменение силы зажима Q для партии заготовок случайно. Зависимость контактных деформаций стыка заготовка – установочный элемент приспособления от силы зажима показана на рис. 3, б. В этом виде зависимость выражается формулой
y = cQn,
где Q – сила зажима, приходящаяся на установочный элемент,
с – коэффициент, характеризующий вид контакта, материал заготовки, шероховатость и структуру ее поверхностного слоя.
Значения с и n для каждого конкретного случая определяют экспериментально.
Для уменьшения з необходимо стремиться к постоянству Q. Вот почему при выполнении точных работ при любом масштабе производства применение приспособления с ручным приводом нежелательно. К уменьшению з также приведет повышение жесткости стыка установочный элемент – базовая поверхность заготовки, однородность поверхностного слоя базовой поверхности, увеличение жесткости элементов приспособления, воспринимающих силу зажима Q.
В процессе закрепления происходит деформация нежестких деталей, таких, как тонкостенные кольца, длинные валы, корпусные детали и др. деформации в ряде случаев могут достигать значительных величин, поэтому при закреплении нежестких деталей их необходимо рассчитывать (по формулам, известным из курса «Сопротивление материалов») либо определять экспериментально. Погрешности могут привести как к изменению положения обрабатываемых поверхностей, так и к искажению их формы.
Погрешность положения заготовки п вызывается неточностью приспособления и зависит от ошибки изготовления и сборки установочных элементов, их прогрессирующим износом, ошибками установки приспособления на станке.
Для схемы базирования, данной на рис. 2, эта погрешность представляет собой увеличение зазора, вызванное износом оправки и зависящее от допуска на изготовление шейки оправки.
Погрешность установки заготовок в приспособлении у равна сумме погрешностей базирования б, закрепления з и положения п.
Учитывая, что эти погрешности являются случайными величинами, суммирование их производят по правилу квадратного корня:
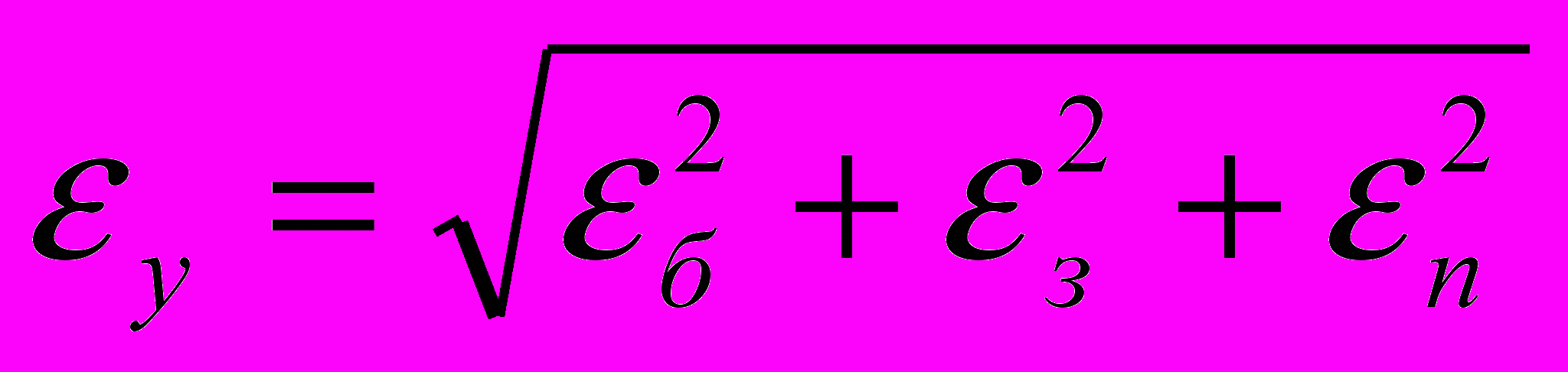