Повышение несущей способности деталей машин упрочнением и отделкой
Вид материала | Документы |
СодержаниеНоминальная площадь контакта |
- Программа вступительного экзамена в аспирантуру по специальной дисциплине 05. 02., 266.3kb.
- Технологии повышения долговечности деталей машин восстановлением и упрочнением рабочих, 553.23kb.
- Касьянов Константин Геннадьевич оценка несущей способности и ресурса конструкционных, 452kb.
- Технологичность деталей машин, 94.77kb.
- Якість поверхонь деталей машин, 156.84kb.
- Повышение эффективности технологического процесса обработки деталей машин при интеграции, 291.71kb.
- Название курса: Детали машин, 59.22kb.
- Программа дисциплины по кафедре Детали машин детали машин и механизмов, 575.22kb.
- Рабочей программы дисциплины Теория механизмов и машин по направлению подготовки 190600, 39.8kb.
- Рабочей программы дисциплины Детали машин и основы конструирования по направлению подготовки, 37.93kb.
Повышение несущей способности деталей машин упрочнением и отделкой
Надёжность работы машин непосредственно связана с качеством поверхностного слоя деталей, которое характеризуется геометрическими и физико-механическими параметрами.
При эксплуатации детали машин контактируют друг с другом или с окружающей средой. От качества поверхностного слоя зависят эксплуатационные свойства – сопротивление усталости, износостойкость, коррозионная стойкость, сопротивление контактной усталости и др. В связи с интенсификацией эксплуатационных процессов, увеличением скоростей перемещения рабочих органов, повышением температур и давлений роль качества поверхностного слоя значительно возрастает. Связь характеристик качества поверхностного слоя с эксплуатационными свойствами деталей свидетельствует о том, что оптимальная поверхность должна быть достаточно твёрдой, должна иметь сжимающие остаточные напряжения, мелкодисперсную структуру, сглаженную форму микронеровностей с большой площадью опорной поверхности.
С помощью широко применяемых методов окончательной обработки (шлифование, хонингование, доводка) создаётся необходимая форма деталей с заданной точностью, но часто не обеспечивается оптимальное качество поверхностного слоя. Оно достигается поверхностным пластическим деформированием (ППД), при котором стружка не образуется, а происходит тонкое пластическое деформирование поверхностного слоя. Во многих случаях применением ППД удаётся повысить запасы прочности деталей, работающих при переменных нагрузках в 1,5-3 раза и увеличить срок службы деталей в десятки раз.
Почти по каждому методу ППД имеются отдельные монографии, брошюры, и т. д. Сведения по методам ППД рассеяны в многочисленных статьях, сборниках. В этих работах методы ППД рассматриваются обособленно, без связи с другими методами поверхностного деформирования.
В учебной литературе информация по этим методам весьма ограничена. В настоящем курсе СпТМ делается попытка с единых позиций рассмотреть подавляющее большинство методов ППД, оценить их эффективность для различных условий применения.
В цикле лабораторных работ будет предоставлена возможность на практике ознакомиться с результатами влияния различных методов ППД на параметры состояния поверхностного слоя, дать им сравнительную оценку, область применения.
Понятие о поверхностном слое
Слой металла, имеющий отличающиеся от основной массы детали структуру, фазовый и химический состав, называют поверхностным.
В условиях эксплуатации поверхностный слой детали подвергается наиболее сильному физико-химическому воздействию: механическому, тепловому, магнитоэлектрическому, световому, химическому и др. В большинстве случаев у детали начинают ухудшаться служебные свойства поверхности, например, износ, эрозия, кавитация, коррозия, усталостные трещины и другие разрушения развиваются вначале на поверхности. Поэтому к поверхностному слою предъявляются обычно более высокие требования, чем к основной массе детали.
Реальная поверхность физического тела несовершенна. Различают следующие геометрические отклонения поверхности в зависимости от отношения шага S к высоте микронеровностей Rz: при S/Rz <50 – шероховатость поверхности, при S/Rz = 50…1000 – волнистость поверхности и при S/Rz >1000 – макроскопические отклонения или отклонения от правильной геометрической формы (конусность, овальность, вогнутость и др.). Дефекты поверхности – это отдельные неровности, совокупность неровностей или участки, размеры которых существенно отличаются от параметров шероховатости и волнистости. К дефектам поверхности относят риски, царапины, вмятины, раковины, поры, сколы, выкрашивания, трещины, задиры, заусенцы и др.
Шероховатость, волнистость и макроотклонения на контактирующих поверхностях деталей машин приводят к дискретности их контакта и дифференциации площадей контакта на фактическую Ar, контурную Ac, и номинальную Aa (рис 1.)
Максимально возможную площадь контакта идеальных поверхностей деталей машин без шероховатости, волнистости и макроотклонения будем называть геометрической площадью контакта А. Геометрическая площадь контакта, как это можно увидеть на рис. 1, определяется наименьшими размерами поверхностей А=Lпоп min · Lпр min.
Номинальная площадь контакта, обусловленная наличием макроотклонения на поверхностях деталей, будет равна сумме отдельных номинальных площадок

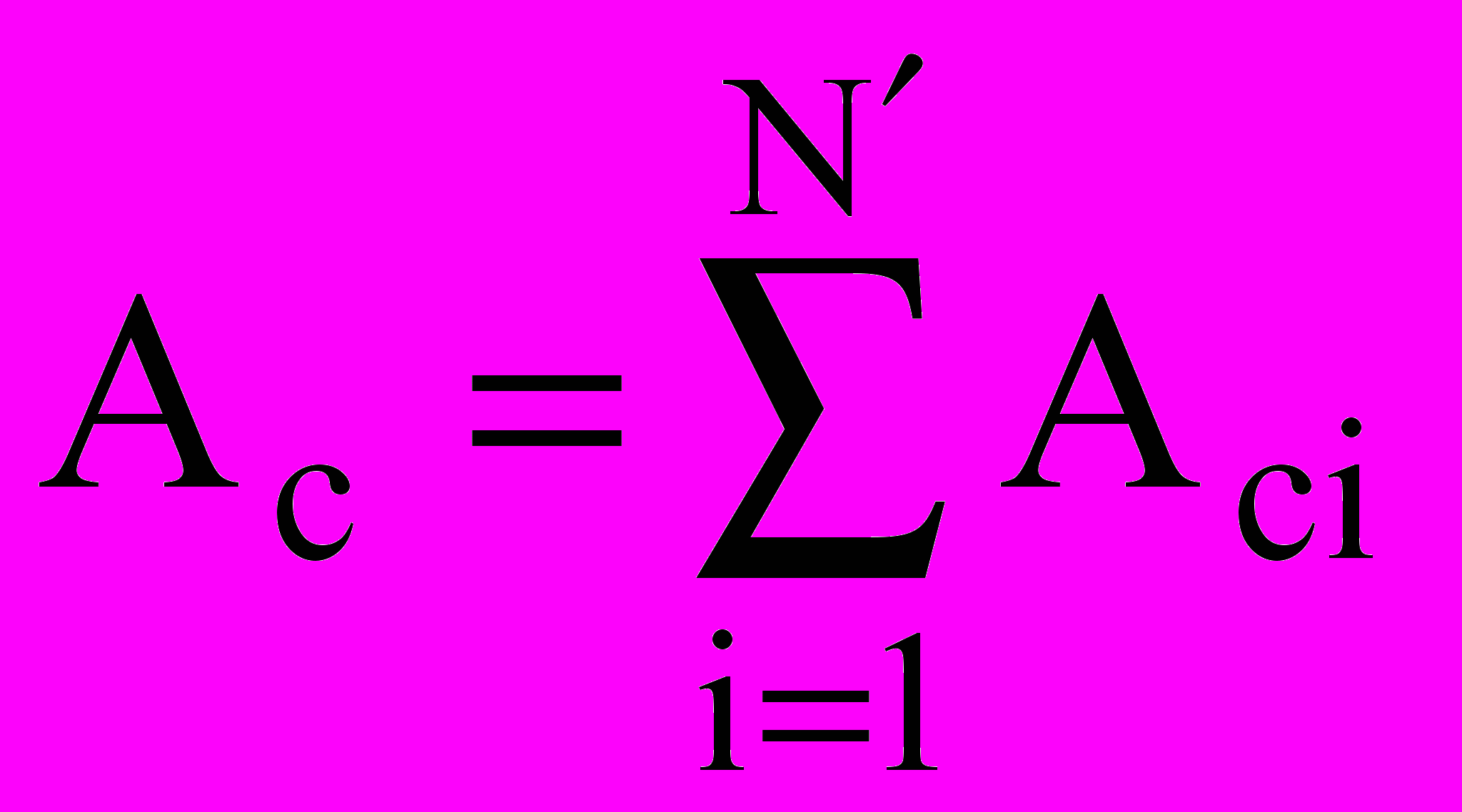
Контакт деталей машин происходит по фактическим площадкам контакта Ari, обусловленным наличием на поверхностях деталей машин шероховатости, которые в сумме создают фактическую площадь контакта
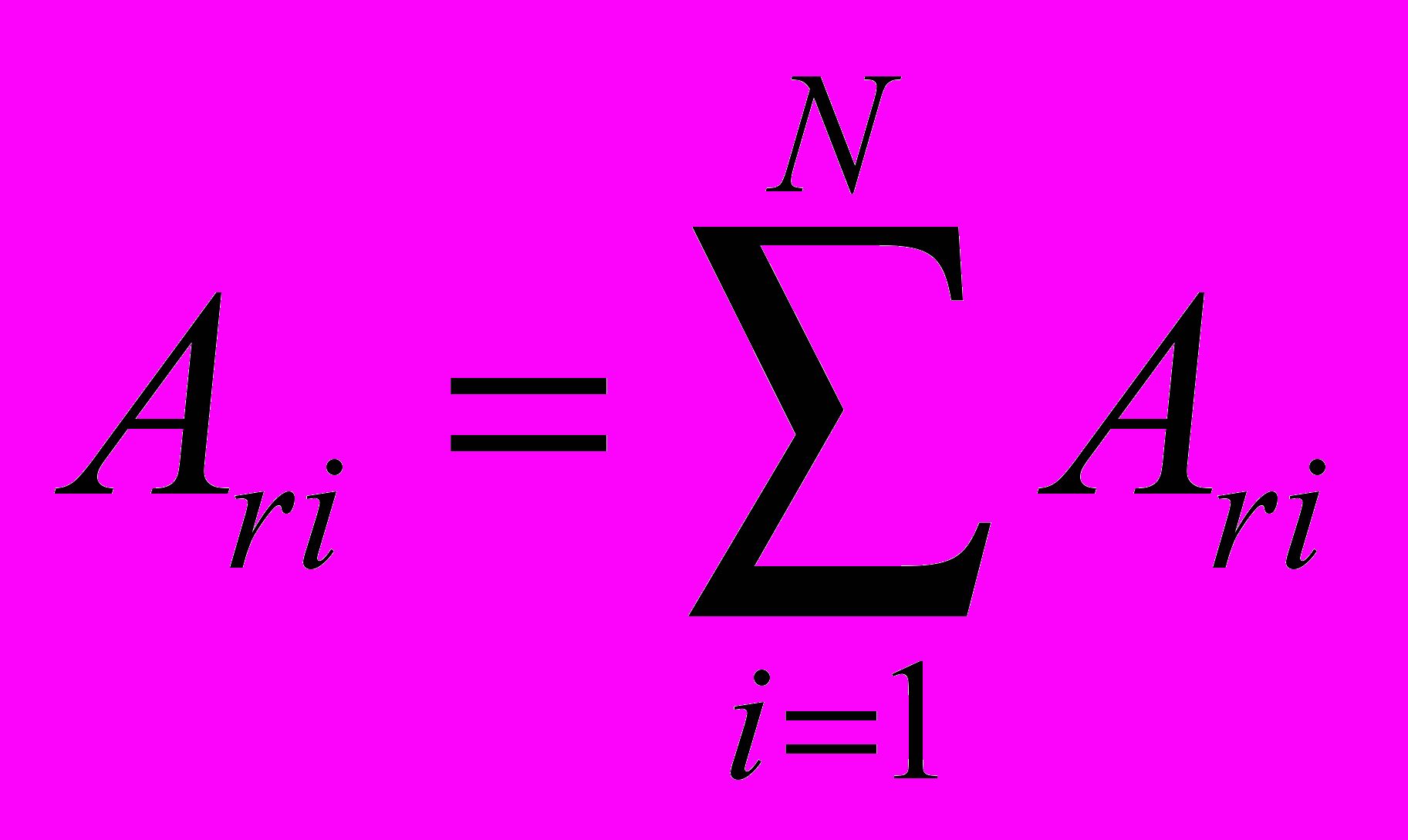
Шероховатость поверхности оценивается следующими показателями: Ra – среднее арифметическое отклонение профиля; Rz – высота неровностей по десяти точкам; Rmax – максимальная высота профиля; Sm – средний шаг неровностей; S – средний шаг неровностей по вершинам локальных выступов; tp – относительная опорная длинна профиля на уровне р.
В настоящее время широкое применение для оценки несущей способности шероховатости получили: кривая опорной поверхности, построенная в относительных координатах tp = bεν, параметры её начального участка ν и b, средние радиусы локальных выступов ρ и выступов ρm, радиус впадин ρ'm, безразмерный комплекс ∆.
По расположению опорных кривых и по значению их параметров проводят сравнение несущей способности шероховатостей, обработанных различными методами и с разной величиной Ra. Однако экспериментальные исследования часто опровергают такие необоснованные выводы. Это объясняется тем, что одинаковые относительные расстояния ε(р) при различной высоте шероховатости Rmax характеризуют разные уровни по своим абсолютным значениям y, поэтому при построении опорных кривых в относительных координатах одни из них как бы искусственно сжимаются, а другие растягиваются.
Так, на рис. 2 построены кривые для разных Rmax в относительных и абсолютных значениях по высоте ординат профиля.
Как видно из рис. 2, а, опорная кривая для Rmax=3мкм хуже, чем для Rmax=8мкм. При построении этих кривых по высоте ординат профиля в абсолютных значениях картина изменяется (рис. 2, б).
Проведённые исследования показывают, что с изменением шероховатости не всегда существует закономерность в изменении параметров b и ν. Всё это говорит о том, что по взаимному расположению опорных кривых, построенных в относительных координатах, и по значению их параметров b и ν затруднительно проводить сравнение несущей способности шероховатости поверхностей, обработанных различными технологическими методами и с разной величиной Rmax. Поэтому для сравнительной оценки несущей способности шероховатости поверхностей опорные кривые целесообразно строить в абсолютном значении по оси ординат профиля y (рис. 2, б).
Построение этих кривых возможно на профилографе-профилометре мод 252, который имеется на кафедре.
Анализ различных профилей (рис. 3) показывает, что несущая способность шероховатости при неизменной их высоте Rmax (Rz) и величине Ra тем больше, чем меньше высота сглаживания Rp (расстояние от линии выступов до средней линии). При одинаковых величинах Rp и Rmax (Rz) несущая способность шероховатости тем выше, чем больше (Ra). С уменьшением высоты шероховатости Rmax параметры Ra и Rp уменьшаются, а её несущая способность увеличивается. Таким образом, из анализа различных профилей установлено, что несущая способность шероховатости зависит от её высоты Rmax (Rz), высоты сглаживания Rp и от Ra.
Уравнение для определения относительных опорных длин профиля шероховатости до средней линии будет иметь вид
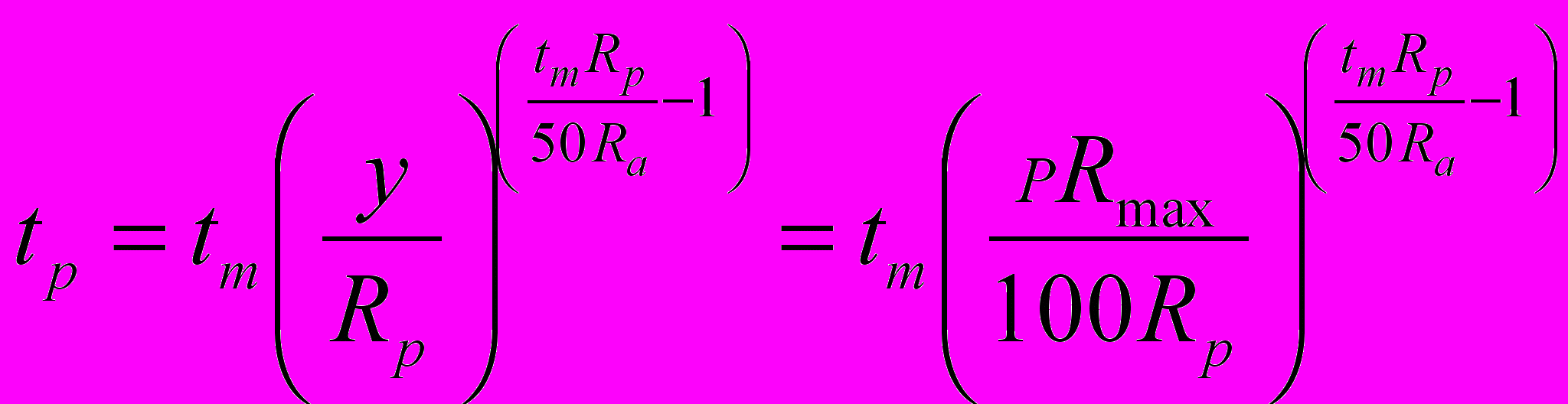
tm – относительная опорная длина профиля на средней линии.
Существующие в настоящее время теоретические зависимости расчёта контактного взаимодействия твёрдых тел основаны на моделировании выступов шероховатости. Так, в теории трения одной из важнейших характеристик является радиус скругления локальных выступов, а при расчёте контактной жёсткости – радиусы скругления выступов. Моделируя локальные выступы и выступы шероховатости телами двоякой кривизны так, чтобы их площадь в поперечном и продольном сечениях были соответственно равны площадям этих выступов, можно определить их поперечные и продольные радиусы (рис. 5).
Далее приведём зависимости для определения параметров шероховатости поверхностей деталей, используемые в расчётах контактного взаимодействия и усталостной прочности твёрдых тел.
Средний радиус выступов:
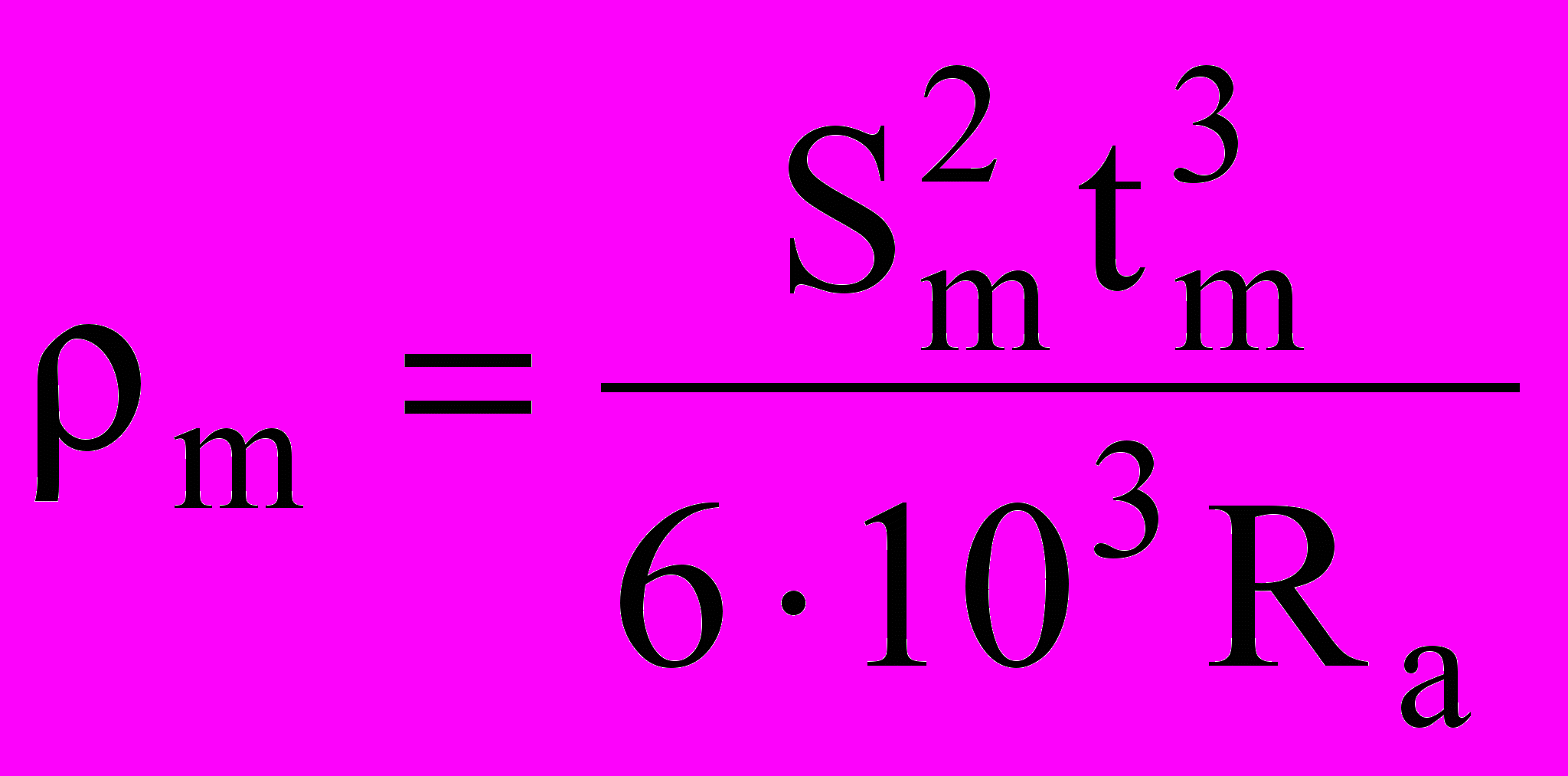
локальных выступов:
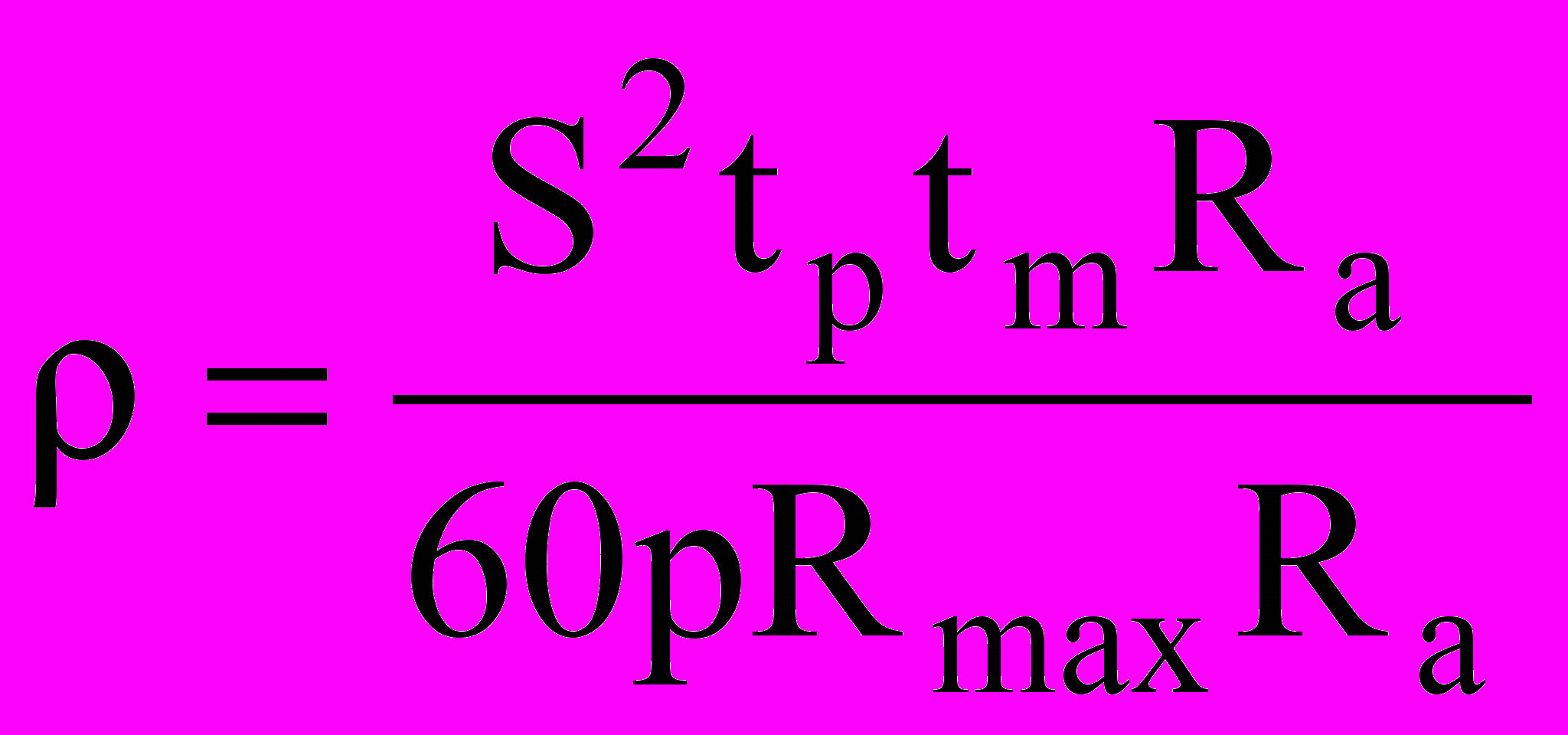
Радиус наибольшей впадины шероховатости, определяющей предел выносливости:
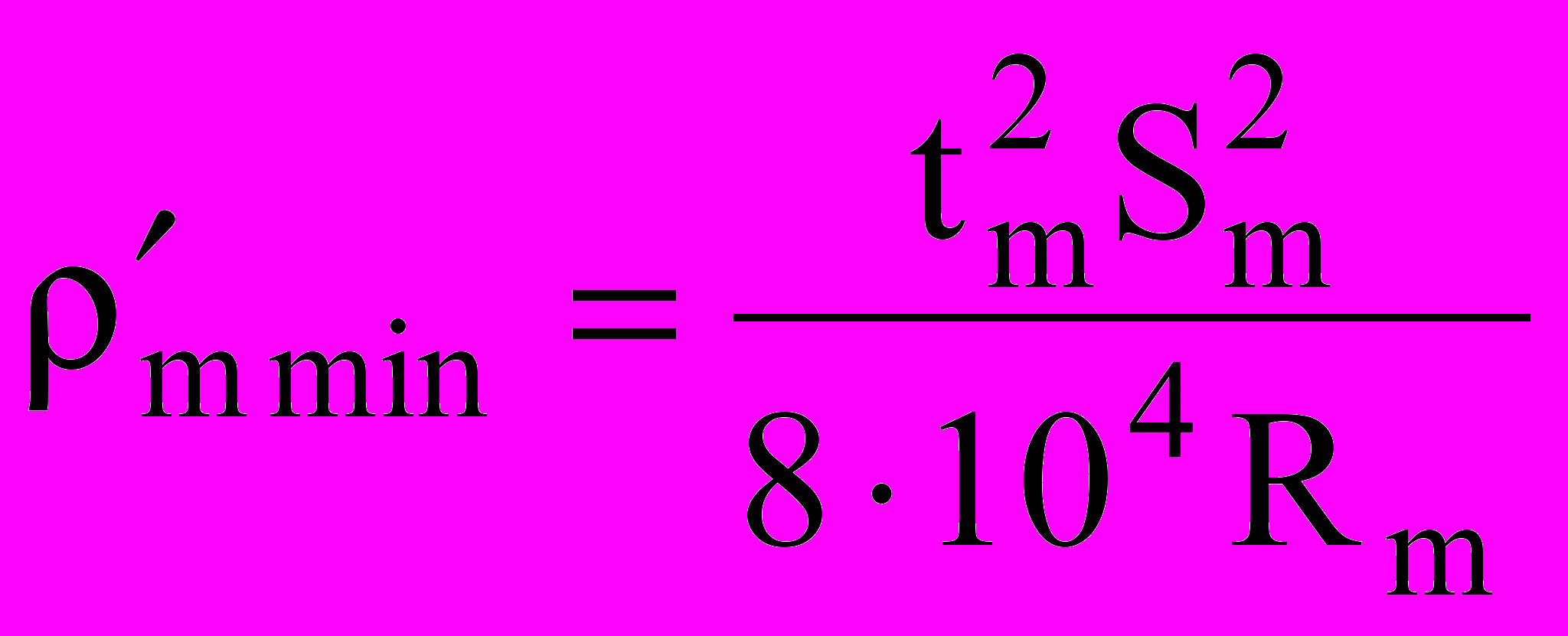
где Rm – глубина сглаживания (расстояние от средней линии до линии впадин).
Зависимость для определения безразмерного комплекса:
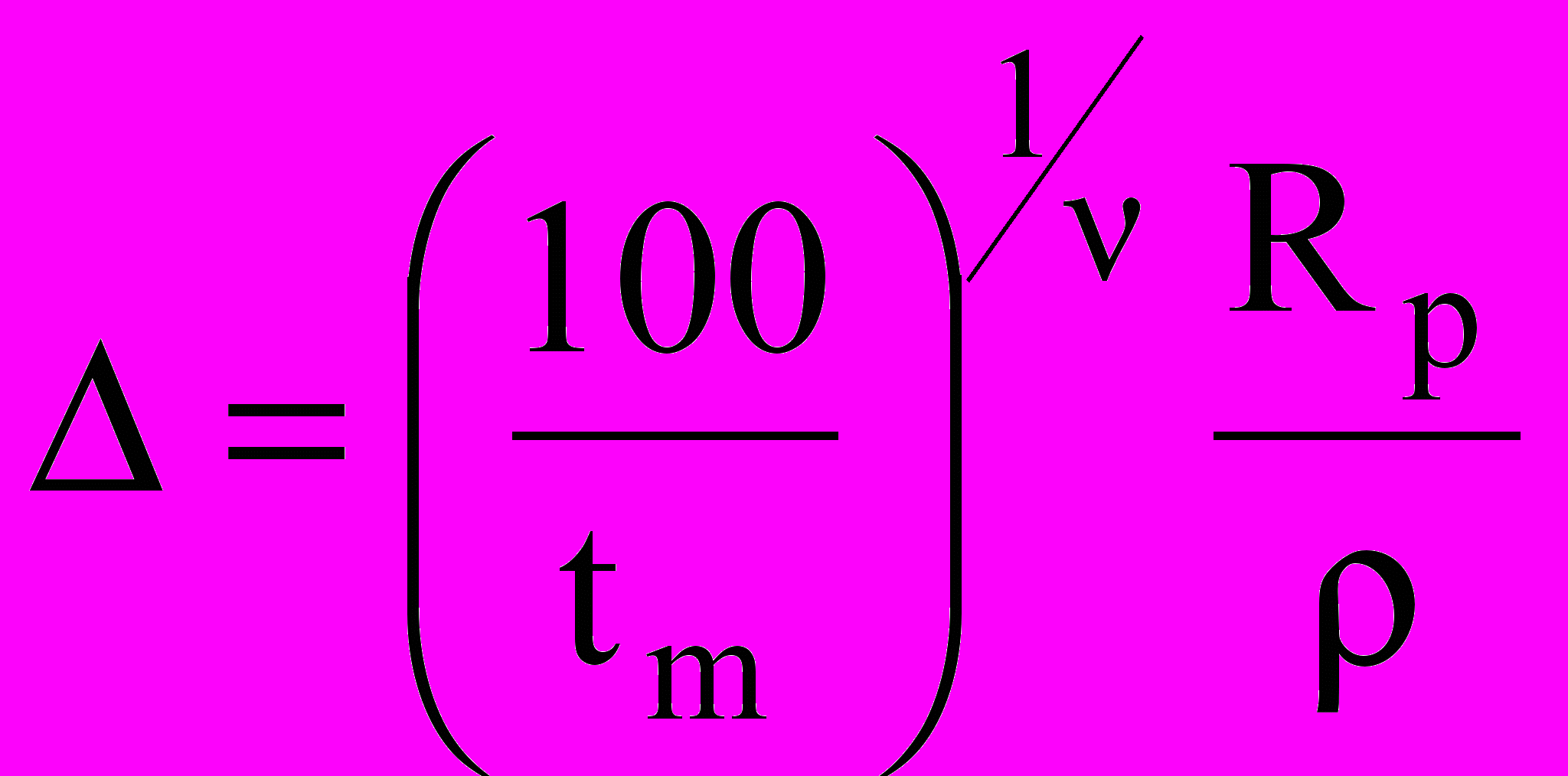
Таким образом, результаты теоретических исследований показывают, что для оценки шероховатости поверхностей деталей машин достаточно иметь следующую систему параметров: Ra, Rp, Rmax, tm, Sm и S, через которые могут быть определены все остальные параметры: ν, b, tp, ρm, ρ,
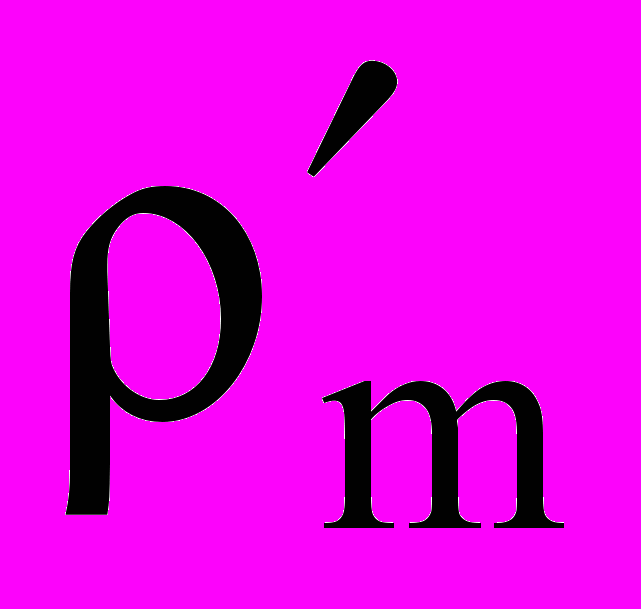
В последнее время для предотвращения процесса схватывания всё более широкое применение получают поверхности трения с искусственными масляными карманами, оценка которых требует особого подхода. Такие поверхности могут быть получены при отделочно-упрочняющей обработке (ОУО) и электромеханической обработке (ЭМО) на сглаживающих режимах, магнито-абразивной обработке (МАО), полировании, вибронакатывании, а также при трении скольжения (рис. 6).
Все эти поверхности имеют масляные карманы с большим шагом и с большой высотой, а также расположенную между ними шероховатость с малым шагом и меньшей высотой. Масляные карманы представляют собой впадины от исходной шероховатости при трении скольжения, ОУО, ЭМО, полировании, МАО или канавки, полученные при вибронакатывании. Шероховатость между масляными карманами образуется при окончательной обработке и трении скольжения или является исходной при нанесении системы канавок вибронакатыванием.
Опубликованные в последние 10-15 лет исследовательские работы по аналитическому определению относительных опорных площадей поверхностей с масляными карманами позволяют наметить подход к оценке их состояния. Анализ зависимостей, полученных авторами этих исследований, показал, что несущая способность таких поверхностей будет определяться как характеристиками масляных карманов, так и параметрами шероховатости поверхности, расположенной между этими карманами. Для оценки масляных карманов рекомендуется использовать ряд характеристик таких как относительную площадь, занимаемую масляными карманами, высота масляных карманов
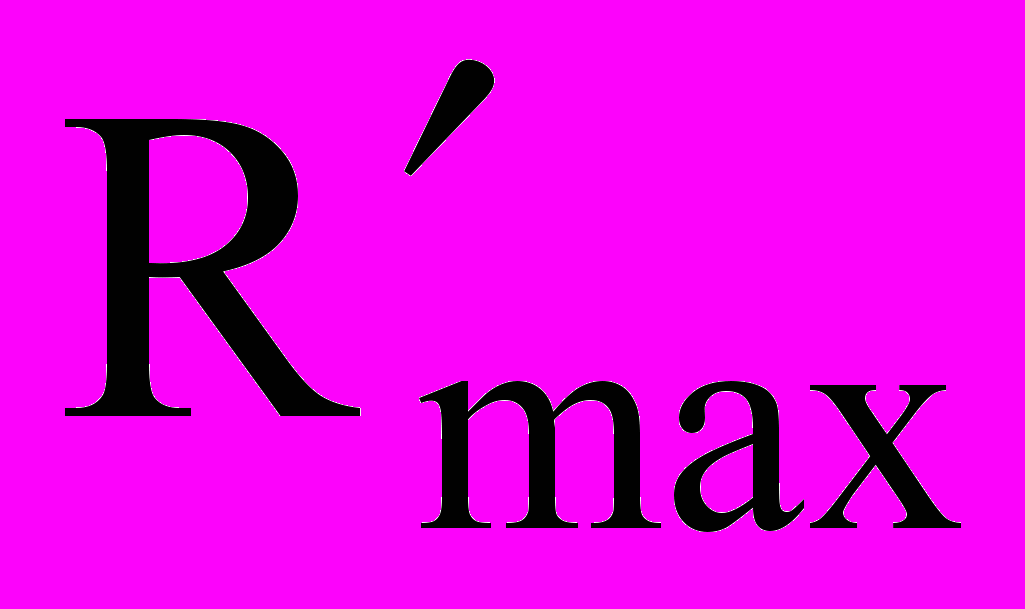
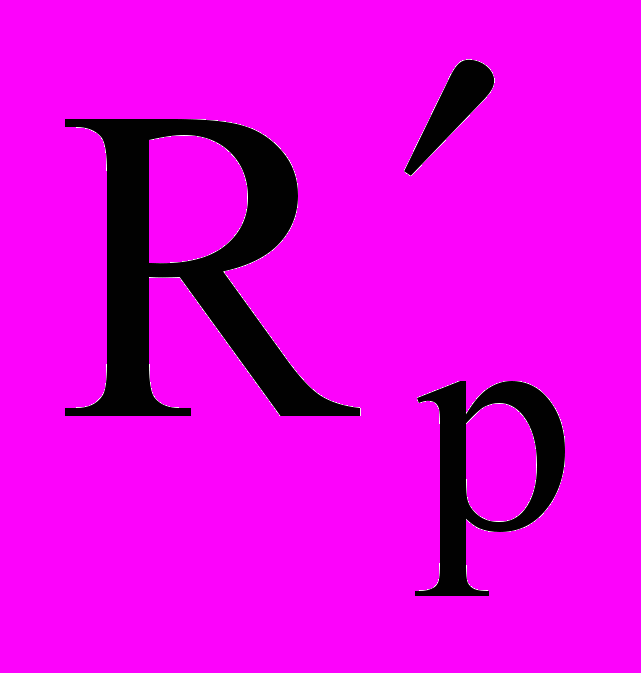
Физико-механические свойства поверхностного слоя изменяются при изготовлении деталей, а затем во время эксплуатации под действием силовых, температурных и других факторов.
Поверхность твёрдого тела по сравнению с его внутренней частью имеет ряд особенностей. Любой атом, расположенный внутри твёрдого тела с идеальной кристаллической решёткой находится в состоянии подвижного устойчивого равновесия, поскольку для него по всем направлениям интенсивность силового поля одинакова. В ином положении оказываются атомы, которые находятся на поверхности: они имеют только односторонние связи с металлом, поэтому их состояние неуравновешенное, неустойчивое; они более активны, обладают избыточной или свободной энергией по сравнению с атомами, находящимися внутри. Поверхность металла в реальных условиях адсорбирует атомы элементов окружающей среды, покрываясь слоями адсорбционных газов, паров воды, жиров и образуя различные окислы.
В результате диффузии в поверхностном слое возникают химические и иные соединения основного металла с проникающими извне веществами. Диффузионная подвижность атомов может привести к перераспределению концентрации легирующих элементов (обезуглероживание поверхностного слоя в сталях и снижение количества хрома и алюминия в жаропрочных никелевых сплавах при высоких температурах нагрева и др.). Диффузия через поверхность оказывает сильное влияние на свойства металлов, особенно их поверхностных слоёв. Это особенно характерно в тех случаях, когда температура в зоне обработки деталей высока (шлифование, скоростное точение, цементация, азотирование и др.).
Остаточными напряжениями называют такие напряжения, которые существуют и уравновешиваются внутри твёрдого тела после устранения причин, вызвавших их появление.
По протяжённости силового поля различают следующие остаточные напряжения:
- напряжение первого рода, или макронапряжения, охватывающие области, размеры которых соизмеримы с размерами детали; они имеют ориентацию, связанную с формой детали, возникают от неоднородности силового, температурного поля внутри детали;
- напряжения второго рода, или микронапряжения, распространяющиеся на отдельные зёрна или на группу зёрен;
- напряжения третьего рода (субмикроскопические), относящиеся к искажениям атомной кристаллической решётки.
Напряжения второго и третьего рода дезориентированы и не проявляются в виде коробления при разрезании детали на части.
Основными причинами возникновения макронапряжений являются неоднородность пластической деформации и локальный неоднородный нагрев металла поверхностного слоя, а при наличии превращений – разность объёмов возникающих структур. Микронапряжения – местные остаточные напряжения в микрозонах. Они являются следствием фазовых превращений, изменения температуры, анизотропии механических свойств отдельных зёрен, границ зёрен и распада зёрен на блоки при пластической деформации.
Причиной образования искажений кристаллической решётки являются, главным образом, дислокация и внедрение атомов.
Степень и глубина наклёпа обусловлены пластической деформацией поверхностного слоя и непосредственно связаны с увеличением дислокаций, вакансий и других дефектов кристаллической решётки металла.
Классификация и особенности применения методов ППД
Методы ППД подразделяют на статические и ударные. При статических методах обработки инструмент, рабочие тела или среда воздействуют на обрабатываемую поверхность с определённой постоянной силой Р, происходит плавное перемещение очагов воздействия, которые последовательно проходят всю поверхность, подлежащую обработке. При этом инерционные силы не оказывают существенного влияния на ППД.
При ударных методах инструмент, рабочие тела или среда многократно воздействуют на всю обрабатываемую поверхность или на её часть, при этом сила воздействия Р в каждом цикле изменяется от нуля или от некоторого значения Р1 до максимума.
Статические методы ППД обеспечивают меньшую шероховатость поверхности с благоприятной формой микронеровностей; с помощью ударных методов можно достичь большой степени упрочнения. Однако обработка некоторыми ударными методами уступает по степени упрочнения обработке статическими методами, например, при виброударной обработке степень упрочнения бывает обычно меньше, чем при накатывании.
Обработка ППД имеет по сравнению с точением, шлифованием и полированием ряд преимуществ:
- сохраняется целостность волокон металла и образуется мелкозернистая структура-текстура в поверхностном солее;
- отсутствует шаржирование обрабатываемой поверхности частичками шлифовальных кругов, полировочных паст;
- отсутствуют термические дефекты;
- стабильны процессы обработки, обеспечивающие стабильное качество поверхности;
- можно достигать минимального параметра шероховатости Ra=0,1…0,05 мкм и менее как на сырых сталях, чугунах, цветных сплавах, так и на высокопрочных закалённых материалах, сохраняя исходную форму заготовок;
- можно уменьшить шероховатость поверхности в несколько раз за один рабочий ход;
- создаётся благоприятная форма микронеровностей с большей долей опорной площади;
- можно образовывать применением некоторых методов регулярные микрорельефы с заданной площадью углублений для задержания смазочного материала;
- создаются благоприятные сжимающие остаточные напряжения в поверхностном слое;
- плавно и стабильно повышается микротвёрдость исходной поверхности.
Явления, происходящие в поверхностном слое при обработке деталей ППД. Механизм упрочнения.
Поверхностный слой при обработке ППД формируется в результате пластических деформаций, изменения прочностных и пластических свойств деформируемого материала, трения и тепловых процессов, изменения микро и макроструктуры и др.
При обработке методами ППД происходит пластическая деформация поверхностного слоя детали в процессе которой большую роль играют искажения кристаллической решётки. Искажения (дефекты) кристаллической решётки являются причиной значительного расхождения между величинами теоретического и реального сопротивлений сдвигу. В искажениях кристаллической решётки возникает пластическая деформация, которая распространяется по кристаллическим плоскостям. Внутри зёрен происходит интенсивное образование и движение дислокаций. Движущиеся дислокации, встречаясь с препятствиями, например, с дислокациями, расположенными в другой плоскости, блокируются, т. е. закрепляются. При пластической деформации происходит дробление кристаллов на фрагменты и блоки с большими искажениями кристаллической решётки на их границах. Это ведёт к увеличению числа границ, около которых задерживаются дислокации, что в свою очередь увеличивает сопротивление деформированию. Это обстоятельство и является причиной упрочнения металлов при пластическом деформировании. В процессе обкатывания величина деформирующих напряжений снижается по мере удаления от контактной поверхности и приводит к их затуханию. Наиболее упрочнённой оказывается верхняя часть пластически деформированного слоя. Физические свойства металла в поверхностном слое изменяются: повышаются твёрдость, предел прочности и предел текучести.
Упрочнение при пластическом деформировании зависит от удельных напряжений и размеров контактной площади между шаровым инструментом и обрабатываемой поверхностью.
Увеличение скорости при обкатывании приводит к изменению степени и градиента наклёпа. Поверхностный слой получает более сильное упрочнение, хотя глубина его снижается.
Основные параметры ППД следующие: упругая и пластическая деформации в очаге деформирования, площадь контакта инструмента с обрабатываемой поверхностью, сила воздействия на инструмент, напряжения, возникающие под действием этой силы, и кратность приложения силы.
Как при статическом, так и при ударном воздействии на обрабатываемой поверхности в первоначальный момент образуется отпечаток от инструмента, который затем превращается в примыкающие друг к другу следы или в серию отпечатков.
При нагружении твёрдого шара статической или ударной силой Р (рис. 3, а) он вдавливается в обрабатываемый материал: по мере увеличения силы Р вначале происходит упругая деформация поверхности, а затем пластическая (линия ОАВ, рис. 3, б). Вследствие возникших пластических деформаций обратный процесс идёт по линии ВС. Остаточная пластическая деформация выражается в размере отпечатка d, соответствующего ОС. Пластическое деформирование под отпечатком распространяется равномерно и как бы копирует с некоторым искажением поверхность (рис. 4).
Глубина наклёпа h пропорциональна глубине отпечатка h1, т. е. h=mh1. Для различных условий обработки коэффициент m=2…20.
Зависимость между диаметром отпечатка d и нагрузкой Р на шар при его внедрении в упругой и пластической областях описывается уравнениями Герца и Мейера:
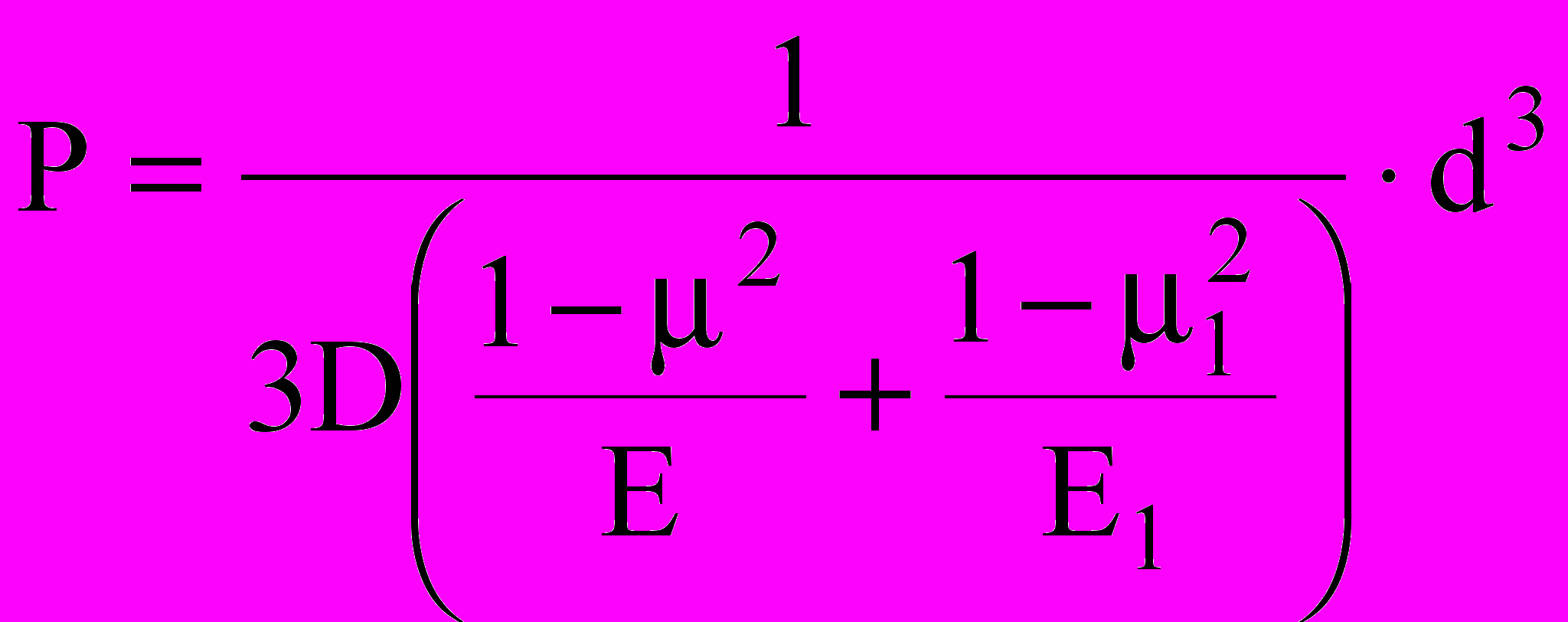
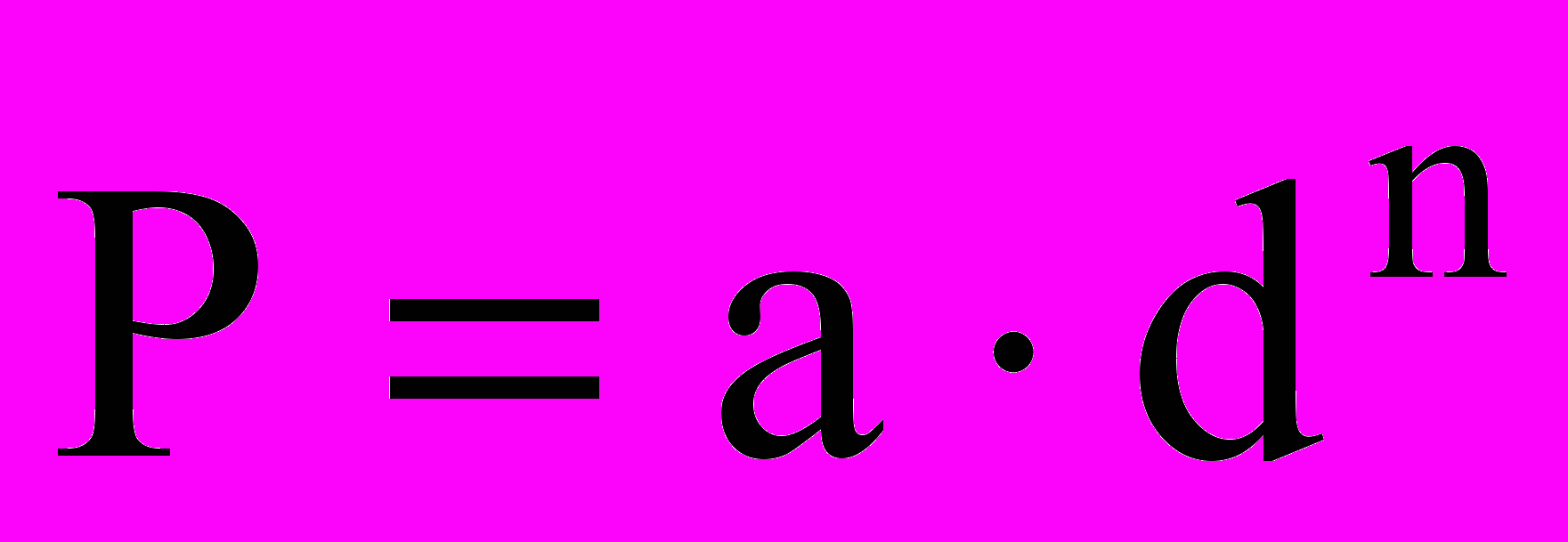
где D – диаметр шара; E, E1 – модули упругости шара и обрабатываемого материала; , 1 – коэффициенты Пуассона шара и материала; а, n = 2 – константы пластичности.
Эти формулы справедливы для условий деформирования без учёта трения, когда контактирующие тела изотропны, подчиняются закону Гука, площадь контура мала и нагрузки приложены перпендикулярно к обрабатываемой поверхности. Процессы ППД протекают в более сложных условиях, поэтому указанные формулы в данном виде имеют ограниченное применение, однако они показывают основные силовые зависимости при ППД.
Степень пластического деформирования ε = d/D, где d – диаметр отпечатка (лунки); D – диаметр вдавливаемой сферы. Для различных методов ППД и различных условиях обработки ε = 0,1...0,9; для конструкционных сталей ε = 0,1...0,7. Степень наклёпа различных структур, оцененная по относительному приращению твёрдости
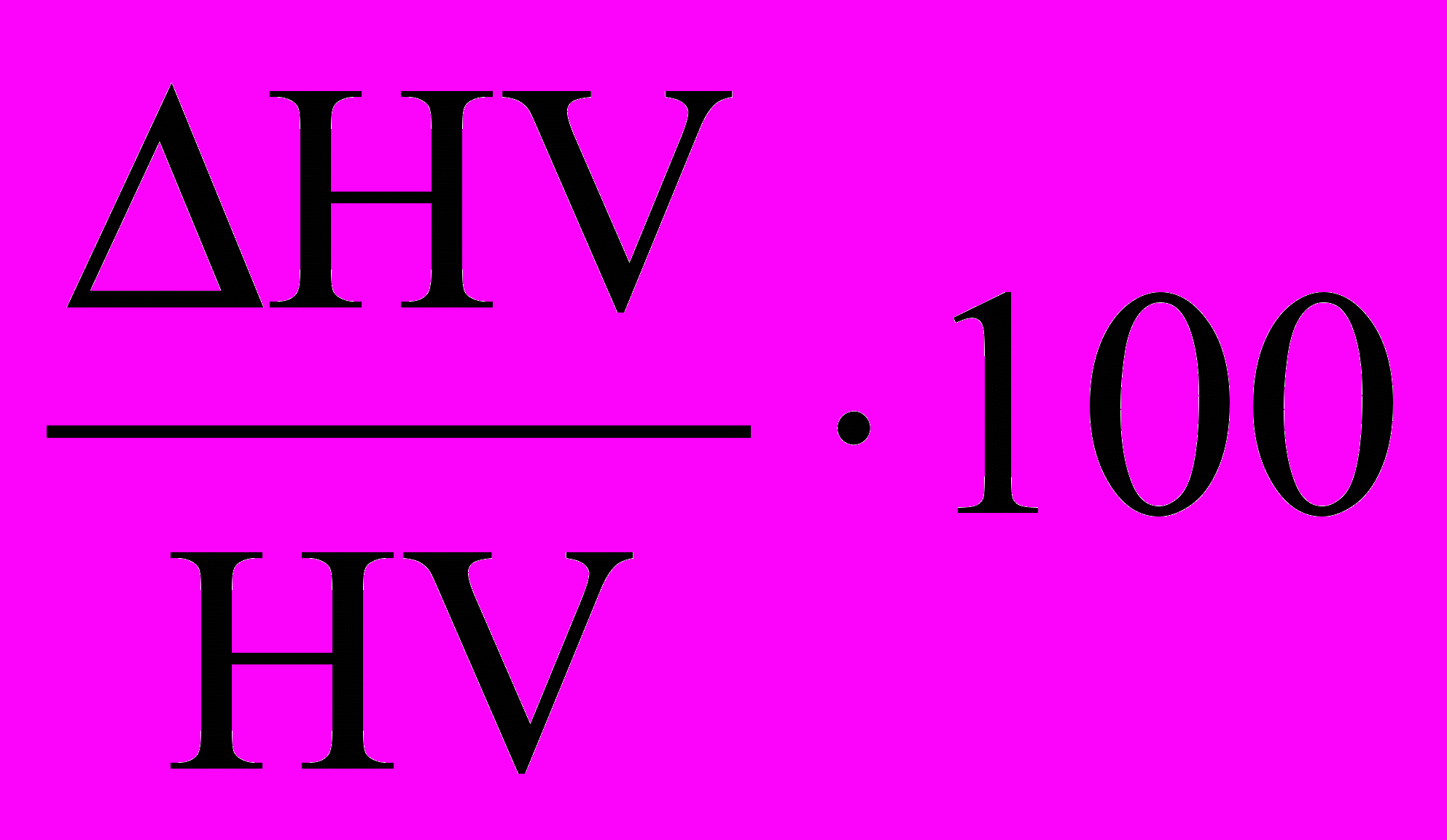
Глубина наклёпа h связана с силой деформирования Р соотношением
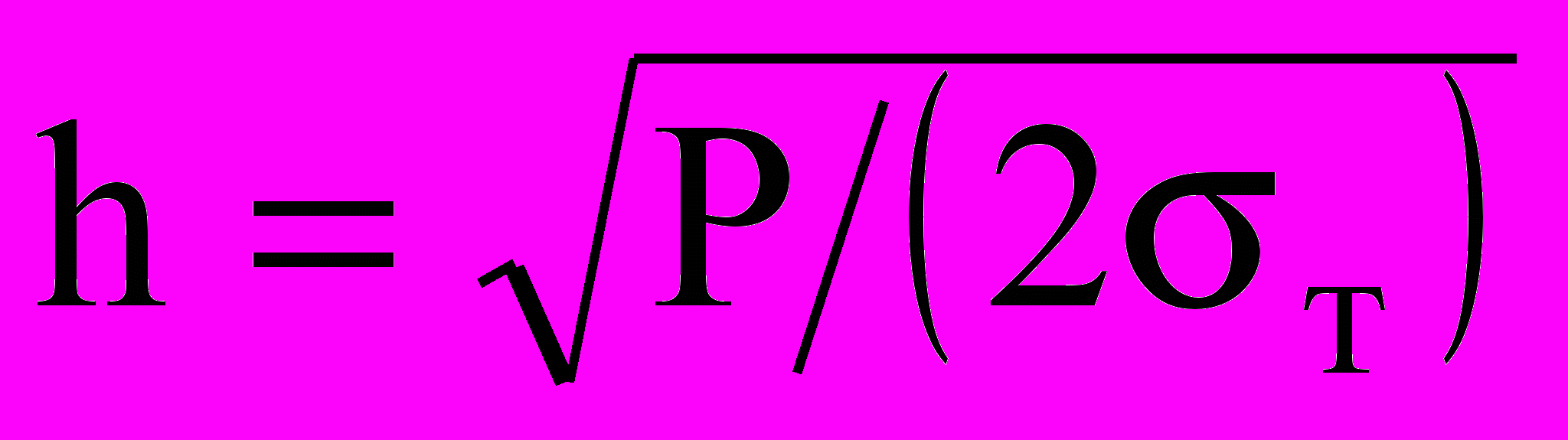
Для конструкционных сталей с погрешностью не более ±10% справедливо соотношение т = HB/3, поэтому h = 1,5d (рис. 7).
Многократное приложение одной и той же статической нагрузки при вдавливании шара в одно и то же место не приводит к заметному увеличению размеров пластического отпечатка. В отличие от статического, при ударном вдавливании шара с увеличением числа ударов до 15…20 размер отпечатка для различных условий обработки увеличивается в 1,25…1,55 раза (рис. 8).
Глубина наклепанной зоны, полученной при ударном вдавливании шара, практически равна глубине наклепанной зоны, полученной при статическом однократном вдавливании шара, при статическом однократном вдавливании шара, при условии равенства диаметров отпечатков. Поэтому зависимости параметров от глубины наклёпанного слоя для условий статического вдавливания могут быть применены для ударного нагружения. Ударное вдавливание по сравнению со статическим в зависимости от твёрдости обрабатываемого материала требует в 1,7…2,8 раза больше энергии.
Одна из причин этого заключается в том, что чем больше скорость нагружения, тем меньше время протекания пластического деформирования, а следовательно, выше напряжение, при котором происходит переход от упругого деформирования к пластическому. Зависимость напряжения от деформации для динамического нагружения расположена выше такой зависимости для статического нагружения (рис. 11).
Характер изменения механических свойств металла поверхностного слоя при обработке методами ППД показан на рис. 12.
При обработке ППД в результате деформирования поверхностного слоя металла и работы трения образуется теплота, которая нагревает обрабатываемую заготовку. Такой нагрев может вызвать термопластическое деформирование и другие явления, снижающие эффект упрочнения.
Термическое деформирование приводит к резкому спаду остаточных сжимающих напряжений на поверхности, а в некоторых случаях – к превращению их в растягивающие. Могут образовываться также вторичные структуры, снижающие эксплуатационные свойства поверхности. Стыки структур являются концентраторами напряжений, что приводит к зарождению усталостных трещин. Необходимо устанавливать такие давления и скорости обработки конкретных материалов, которые не вызывают повышения температуры поверхности более допустимой.
Если при обработке происходят структурные превращения, сопровождаемые увеличением удельного объёма (например, переход аустенита в мартенсит), то образуются остаточные сжимающие напряжения, при обратном процессе – растягивающие напряжения. Увеличение концентрации точечных и линейных дефектов кристаллического строения и образования субмикроскопических (не опасных и не вредных) трещин также увеличивает удельный объём металла. Суммарное максимальное увеличение удельного объёма для сталей достигает 1,1%.
Это обуславливает образование в наклёпанной зоне остаточных напряжений сжатия, которые в зависимости от материала и метода обработки достигают 1200-1500 МПа; глубина залегания напряжений обычно на 10-15% превышает глубину слоя с повышенной твёрдостью. Максимальное напряжение чаще всего непосредственно на поверхности или на некотором расстоянии от поверхности (что вызвано тепловыми явлениями).
При завышенных силовых параметрах обработки может происходить перенаклёп, в результате которого в поверхностном слое появляются опасные микротрещины, намечается образование частичек отслаивающегося металла, поверхностные зёрна сплющиваются так, что становятся почти неразличимыми. Резко увеличивается шероховатость поверхности. Наклёп металла можно частично или полностью снять путём отжига.
Перенаклёп – необратимый процесс, при котором нагрев не восстанавливает исходную структуру металла и его механические свойства.
50>