Повышение несущей способности деталей машин упрочнением и отделкой
Вид материала | Документы |
- Программа вступительного экзамена в аспирантуру по специальной дисциплине 05. 02., 266.3kb.
- Технологии повышения долговечности деталей машин восстановлением и упрочнением рабочих, 553.23kb.
- Касьянов Константин Геннадьевич оценка несущей способности и ресурса конструкционных, 452kb.
- Технологичность деталей машин, 94.77kb.
- Якість поверхонь деталей машин, 156.84kb.
- Повышение эффективности технологического процесса обработки деталей машин при интеграции, 291.71kb.
- Название курса: Детали машин, 59.22kb.
- Программа дисциплины по кафедре Детали машин детали машин и механизмов, 575.22kb.
- Рабочей программы дисциплины Теория механизмов и машин по направлению подготовки 190600, 39.8kb.
- Рабочей программы дисциплины Детали машин и основы конструирования по направлению подготовки, 37.93kb.
применения различных методов ППД
Обрабатывают ППД детали от работоспособности, которых зависят надёжность и долговечность изделий в целом.
На рис. 14 и 15 показаны типовые детали автомобиля, упрочняемые методами ППД. Из тысяч наименований деталей в машине обычно незначительное количество их упрочняют этими методами, которые можно сгруппировать следующим образом:
- детали, работающие в условиях знакопеременных нагрузок, вызывающие усталостные разрушения (торсионы, силовые болты, балансиры, вилки, лопатки, к/в, кулачковые валы, крыльчатки, шатуны, шестерни, лонжероны, лопасти, пружины, полуоси, диски);
- детали, работающие в условиях высоких скоростей относительно перемещения и больших давлений с минимальными зазорами при обеднённом смазочном материале, что приводит к схватыванию металла (распределители, поршни, шатуны со сферическими головками, поршневые кольца, золотники, плунжеры, шпиндели);
- детали, работающие в условиях абразивного изнашивания (пальцы трака, диффузоры, крыльчатки, тормозные диски и барабаны, колеса, опорные ролики и т.п.);
- детали, работающие в условиях окислительного изнашивания (щетки коленчатых валов, цилиндры, подшипники скольжения);
- детали манжетных уплотнений, к герметичности и износостойкости которых предъявляются высокие требования (валы, втулки, оси, штоки, шкивы)
- детали, контактирующие с газовым потоком, имеющим высокую скорость температуру и давление (трубы, раструбы, лопатки и диски турбин, камеры);
- детали, работающие в условиях контактно-усталостных напряжений (беговые дорожки подшипников, цапфы шестерен, опорные шейки, крестовины, поворотные кулаки);
- детали инструментального производства, работающие в тяжелых условиях трения скольжения (валки холодной прокатки, пуансоны, матрицы, протяжки). Кроме того, методами ППД эффективно упрочняют детали, подвергаемые коррозионно-усталостному воздействию, фреттинг-коррозии, ударным нагрузкам, кавитационному воздействию и многим другим видам и условиям нагружения.
Цилиндрические, конические и другие наружные и внутренние поверхности правильной геометрической формы твердостью HRC< 45…50 эффективно обрабатывать накатыванием роликовым или шариковым инструментом, а поверхности твердостью HRC>50 методом алмазного выглаживания. Алмазное выглаживание по сравнению с накатыванием имеет существенно меньшую производительность, однако обладает большей универсальностью и позволяет обрабатывать маложесткие и неравножесткие детали, т.к. прикладываемое усилие при алмазном выглаживании составляет 100-200 Н, а при накатывании 10…100 кН.
Для осуществления накатывания и алмазного выглаживания сложных поверхностей необходимо дополнительно решить ряд технологических и конструктивных задач, связанных с созданием деформирующего инструмента специального профиля.
Детали более сложной конфигурации (пружины, рессоры, шатуны, лопатки) целесообразно упрочнять виброударным методом или обработкой дробью.
Для повышения долговечности деталей, подвергаемых изнашиванию, а также схватыванию металла на их поверхности создают регулярный микрорельеф путем вибрационного накатывания, выглаживания.
Эффективность упрочнения зависит от материала, структуры, виды напряженного состояния, формы и т. д. Большую роль играет выбор метода и режима упрочнения. Поэтому при внедрении методов ППД в производство обычно предварительно проводят исследования и испытания.
Работоспособность деталей повышают применением комбинированной обработки различными методами ППД, а также в сочетании с другими методами упрочнения. Например, обработка ППД под хромирование обеспечивает наиболее высокое качество и прочность хромового покрытия. Поверхности трения деталей из титана можно упрочнять комбинированным способом: вначале электроискровое микролегирование сверхтвердыми материалами, а затем жесткое обкатывание, что снижает вредное влияние микролегирования на сопротивление усталости и обеспечивает требуемую точность и шероховатость.
Обкатывание и раскатывание шаровым инструментом.
Схема процесса, давление и кратность приложения деформирующей силы
Шаровым инструментом можно обкатывать плоские, наружные и внутренние цилиндрические поверхности одним и несколькими шарами одновременно. По характеру создания деформирующей силы применяют «упругий» и «жесткий» контакт инструмента с обрабатываемой поверхностью. При упругом контакте деформирующая сила создается с помощью тарированной пружины, пневматическим или гидравлическим способом. При жестком контакте деформирующая сила обеспечивается натягом между инструментом и обрабатываемой поверхностью. Шаровым инструментом обрабатывают специальные и сложнопрофильные поверхности, например, сферы, галтельные переходы, желоба подшипников и т.п.
В обкатниках с жестким контактом нормальная сила (натяг) создается за счет поперечной подачи обкатника, осуществляемой винтом поперечной подачи станка, а иногда – при помощи груза. Такая схема не обеспечивает равномерного упрочнения всей обкатываемой поверхности из-за неточностей заготовки, погрешностей установки ее на станке, неравномерной жесткости детали по длине и как следствие различного прогиба от давления инструмента, неравномерные механические свойства в основном металле на различных участках ее поверхности. Поэтому обкатники с «жестким контактом» не нашли широкого применения, хотя более просты в изготовлении.
Обкатники с упругим контактом между инструментом и обрабатываемой поверхностью предпочтительнее, так как траектория перемещения деформирующего инструмента в процессе обработки определяется формой исходной заготовки.
Конструкция инструмента обеспечивает постоянство нормальной силы при обработке, что практически обеспечивает не изменяемость формы исходной заготовки.
При упругом контакте достигается более равномерный наклеп всей обработанной поверхности, хотя погрешности формы детали в этом случае не исправляются.
В процессе обработки деталь вращается, а деформирующий инструмент (шар), находящийся в контакте с обрабатываемой поверхностью, вместе с обкатным приспособлением имеет продольную подачу. Благодаря самоустанавливаемости шара во время обкатывания обеспечивается его свободное вращение при трении качения между шаром и деталью, что и создает благоприятные условия для пластической деформации, обеспечивающие меньшую шероховатость поверхности при небольшом давлении шара.
В зависимости от характера обрабатываемой поверхности образуется определенная форма пятна, чаще всего это правильная геометрическая фигура (эллипс или окружность), искаженная упругой и пластической деформациями металла.
Для наружной цилиндрической поверхности (рис. 24, а) необработанная поверхность находится слева от линии М1КК1К2М2, а обработанная справа. При статическом вдавливании формой контакта является эллипс с полуосями a, b. Во время обкатывания со скоростью V и подачей S перед шаром образуется стоячая волна деформированного металла, а за шаром остается пластически деформированная поверхность. Передняя часть пятна контакта ограничена линией КК1К2, близкой к дуге эллипса, но частично выходящей за нее из-за образования стоячей волны, которая охватывает сферическую поверхность шара.
Задняя часть пятна контакта ограничена линией КК3МК2, при этом участки КК3, К3М, МК2 являются кривыми, близкими к дугам соответствующих эллипсов. Поэтому суммарную площадь пятна контакта можно с достаточной точностью определить из геометрических соотношений, эта площадь на 30-50 % меньше площади эллипса с полуосями a,b. Площадь контакта более точно определяют по формуле:

где R – радиус шара;
Rd – радиус детали;
ω – местная упругая деформация детали и инструмента;
h1 – остаточная деформация;
Величину h1 определяют экспериментально, а ω рассчитывают по формулам теории упругости. Знак ± в знаменателе для обработки наружных цилиндрических поверхностей и отверстий соответственно.
Образование микропрофиля
При обкатывании деталей машин образуется новая поверхность с шероховатостью, зависящей от основных параметров обработки. Представление о микропрофиле как следе рабочего движения инструмента является не точным вследствие искажений, вызываемых пластическим течением металла от места контакта инструмента с деталью. Пластическое течение происходит как в направлении подачи с образованием волны, перемещающейся вместе с инструментом, так и в направлении, противоположном подаче, вызывая искажение образованного ранее соседнего микропрофиля. Схема последовательного образования микропрофиля (рис. 24, б) составлена по профилаграммам, снятым при обработке различных углеродистых сталей.
В начале обработки при первом обороте детали образуется канавка с волнами по обеим сторонам (рис. 24, б I). При втором обороте детали в связи с перемещением инструмента на величину подачи образуется вторая канавка (рис. 24, б II), глубина которой больше первой, так как вследствие контактной площади между инструментом и деталью увеличивается контактное давление. Образование последующих канавок производится таким же образом. Штриховой линией на схеме показан микропрофиль, полученный при предыдущем обороте, а сплошной линией – микропрофиль, образуемый в данный момент (при данном обороте). Величина искажения характеризуется зоной пластикового смещения металла (заштрихованные участки), являющейся своего рода волной, возникающей в направлении противоположном подаче инструмента. Таким образом при обработке с продольной подачей микропрофиль, образовавшийся при данном обороте детали (первичный микропрофиль) вследствие пластического течения металла, искажается при следующем обороте, образуя вторичный микропрофиль, который и характеризует обработанную поверхность. Пластическое течение происходит в области, ограниченной смежной впадиной. При обработке с большими давлениями и малыми подачами эта область может захватывать несколько соседних микронеровностей, вызывая повторное искажение. На профилограмме (рис. 50) сплошной линией изображен микропрофиль обкатанной поверхности, полученной в результате искажения (вторичный микропрофиль), а штриховой линией - первичный микропрофиль, который имела бы обкатанная поверхность при отсутствии искажения и который можно рассматривать как след рабочего движения инструмента. Величина искажения микропрофиля зависит от давления, пластических свойств материала детали и формы деформирующего элемента. С возрастанием давления и повышением пластичности увеличивается зона пластического смещения и в большей степени происходит искажение микропрофиля.
Определение высоты микронеровностей
Для расчета высоты микронеровностей рекомендуется выражение:
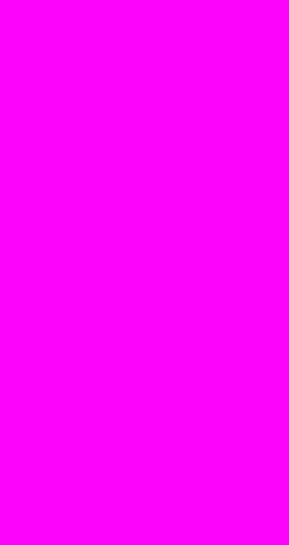
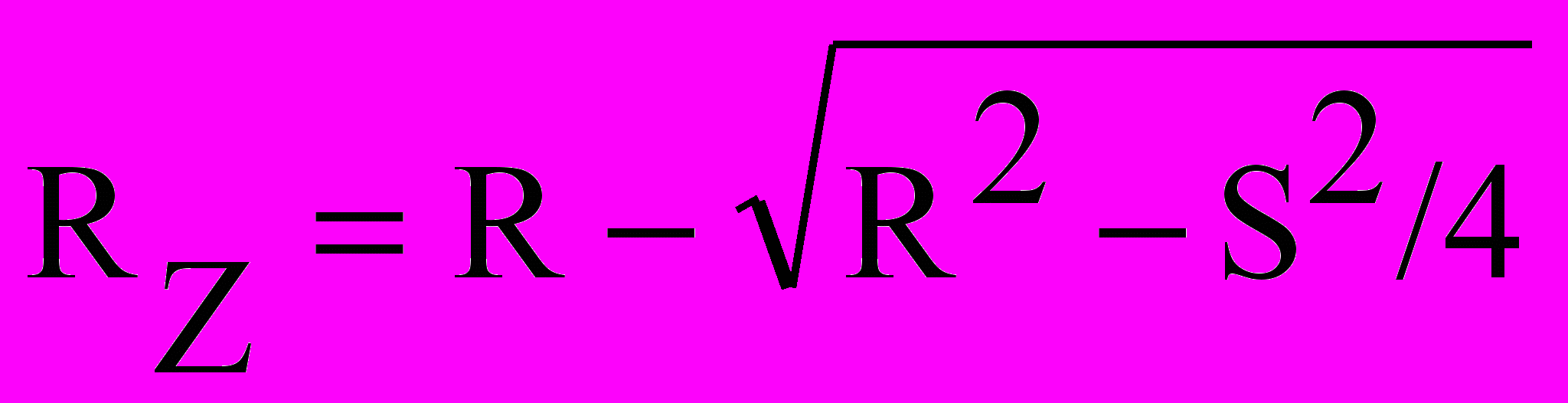
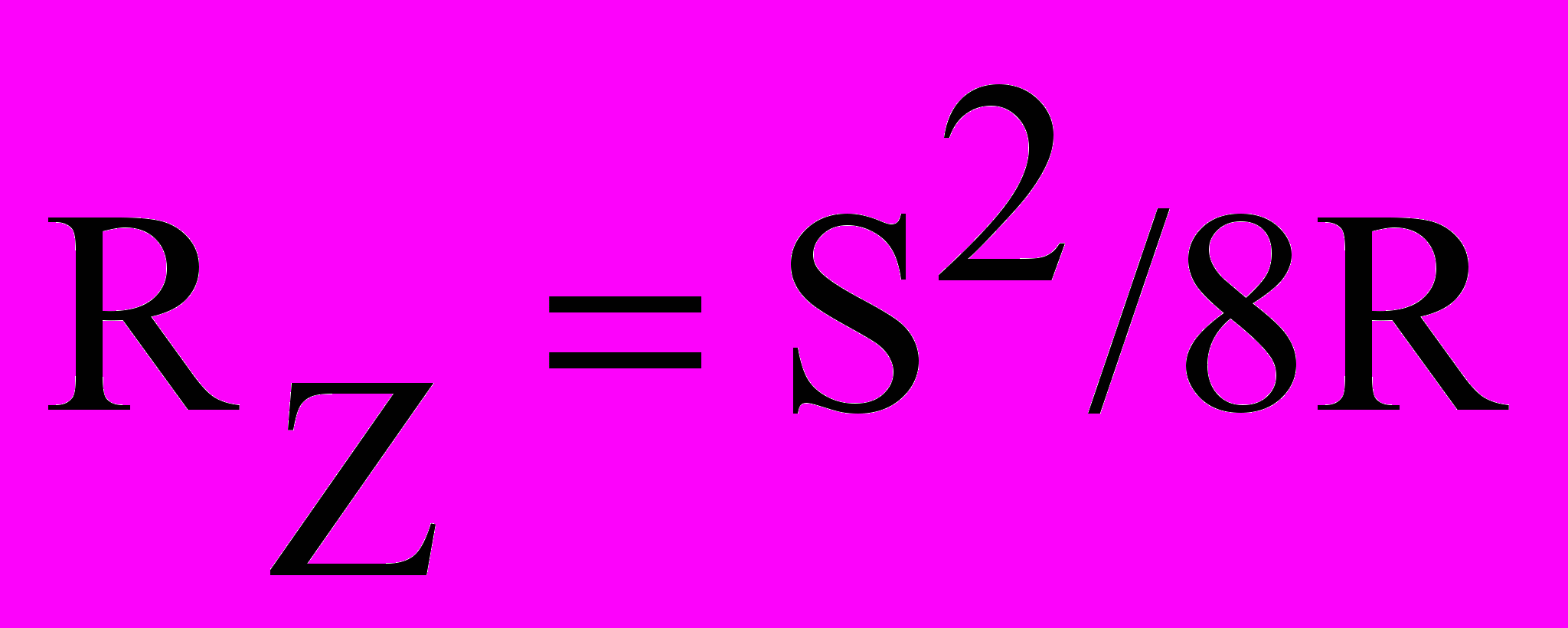
Обе формулы являются приближенными и справедливы только для случая полной деформации исходных шероховатостей. В процессе обработки происходит упругая деформация материала детали. Наибольшую деформацию металл имеет в точке С, т. е. в центре впадины. В точке В, находящейся на вершине неровности, деформация минимальна. Следовательно после упругого восстановления материала высота микронеровностей будет отличаться от значения RZ , определенное по приведенным выше выражениям. Это отличие должно быть равно разнице в величине упругой деформации материала в точках С и В. Упругую деформацию неровностей приближенно определяют с помощью формулы Герца. Из теории упругости известно, что при упругом контакте двух тел смещение (ω1 и ω2) от местной деформации точек первого и второго тела в направлении действия силы определяется следующим образом:
ω1 + ω2 = £ - х2 · β,
где £ - сближение обоих тел;
β – постоянная величина, зависящая от радиуса кривизны;
х – расстояние точек от оси (от центра).
При обработке одношаровым инструментом S = 0,06…0,4 мм/об, а размер пятна контакта в направлении подачи – 0,6…1,1 мм, следовательно, кратность приложения нагрузки N = 4…6. При таком значении достигается наиболее высокая производительность и обеспечивается достаточно высокое качество поверхностного слоя. Использование многошаровых устройств позволяет увеличить подачу при постоянном N.
На высоту неровностей, образующихся при обкатывании, большое влияние оказывает давление в контакте, продольная подача, размеры деформирующего инструмента, исходная шероховатость поверхности и физико-механические свойства материала детали. У незакаленных сталей и титановых сплавов вследствие обкатывания неровностей снижаются в 8 - 20 раз, а у высокопрочных (закаленных) в 3 -4 раз. Минимальные неровности образуются при оптимальном давлении, которое возрастает по мере перехода к более твердым и менее пластичным металлам. При обкатывании стали 20 оптимальное давление (140…175 кгс/мм2) достигается при нормальной силе 50 – 80 кгс, то при обкатывании стали У8 оно повышается до 180 – 220 кгс/мм2 и достигается при нормальной силе 100 – 170 кгс. Если давление выше оптимального то высота неровностей возрастает, т.к. происходит искажение микропрофиля из-за перенаклепа, приводящее к разрушению верхнего слоя.
Изменение подачи и размеров деформирующего инструмента можно в значительной степени управлять (изменять) шероховатостью обрабатываемой поверхности. Высота неровностей прямо пропорциональна величине подачи во второй степени и обратно пропорциональна радиусу шара.
При проектировании технологического процесса необходимо предусмотреть возможность получения неровностей в допустимых пределах. Важно установить их наибольшую допускаемую высоту под обкатывание, так как снижение шероховатости поверхности при обработке резанием удорожает стоимость изготовления деталей. При обкатывании незакаленных сталей с давлениями, близкими к оптимальным, исходные неровности до 15 -20 мкм практически не влияют на величину шероховатостей обкатанной поверхности. При таком условии обкатывание обеспечивает поверхность с Ra = 0,15…0,20 мкм. Закаленные стали, обладают пониженной пластичности и для них целесообразно, чтобы подлежащая обкатыванию поверхность имела шероховатость с Ra < 1,25, что обеспечит при обкатывании поверхность с Ra = 0,2…0,5 мкм. Перед обкатыванием обычно производят шлифование, которое обеспечивает требуемую точность. Обкатывание рекомендуется выполнять со скоростью 50…100 м/мин. При оптимальных давлениях обработку выполняют в один рабочий ход. Для нежестких – два, три хода.
Точность обработки при обкатывании
Обкатывание применяется при финишных операциях, поэтому большое значение имеет достигаемая точность. Обработка деформирующим инструментом упругого действия вследствие копирования погрешностей сохраняет форму детали, но ввиду остаточной деформации изменяет ее размер. Изменение размера определяется величиной остаточной деформации h и высотой неровностей, образующихся в результате обработки:δ0 = h- RZ. для цилиндрических поверхностей изменения диаметра:δD = 2 · (h- RZ). Если обозначить через D3 и D – соответственно диаметр до обработки и после нее, то получим D = D3 ± 2 · (h- RZ). В формулах (-) соответствует обработке вала, а (+) – отверстия.
Так как остаточная деформация и высота неровностей определяется параметрами обработки, при их назначении необходимо обеспечить требуемую точность и установить технически обоснованные припуски. При отсутствии данных для подсчета остаточной деформации изменение размера определяется экспериментально. Результаты исследований показывают, что изменение размера зависит от размера, материала детали, подачи, радиуса деформирующего инструмента и числа рабочих ходов. При обкатывании с силами, обеспечивающими полное смятие исходных неровностей получение минимальной шероховатости, повторные рабочие ходы практически не изменяют размера.
В некоторых случаях может наблюдаться увеличение диаметра на 1 – 2 мкм. Это явление возможно при обработке с режимами, вызывающими интенсивную деформацию тонкого верхнего слоя, в структуре которого содержалось более остаточного аустенита по сравнению с другими образцами. При интенсивной деформации верхнего слоя происходит более полное превращение остаточного аустенита в мартенсит, имеющего большой удельный объем, что и сказывается на изменение диаметра.
Обкатывание не приводит к образованию волнистости, а лишь снижает полученную на предшествующих операциях.
При обработке инструментом с жестким контактом точность может повышаться. Однако вследствие изменения давления из-за погрешностей геометрической формы детали, обработанная поверхность будет неоднородной по напряженности, наклепу и шероховатости. Поэтому использование деформирующего инструмента с жестким контактом не рекомендуется. При нежесткой СПИД вследствие появления вынужденных колебаний волнистость поверхности при обкатывании может увеличиваться.
Предварительная обработка должна обеспечить точность в пределах требуемого квалитета с необходимым припуском под обкатывание.
Для ориентировочных расчетов можно принять, что при оптимальных режимах припуск под обработку составляет Zd = K1·(Rz исх -Rz),
где Rz исх – высота исходных неровностей,
Rz - высота после обработки.
На основании экспериментальных данных можно рекомендовать К1 = 1,1…1,5. Меньшие значения К1 – для твердых сталей, а большие – для мягких, пластичных сталей.
Механизм формирования остаточных напряжений при ППД
Обработка поверхностным пластическим деформированием создаёт остаточные напряжения, которые являются результатом воздействия двух основных факторов – собственно деформации и протекающих при этом тепловых процессов.
![]() |
Рис. 43. Схема образования остаточных напряжений в остывшей детали с максимальным напряжением в глубине слоя а и в и на поверхности б: 1 — напряжения от пластической деформации; 2 — термические напряжения; 3 — суммарные напряжения |
Вследствие значительного роста плотности происходит некоторое увеличение удельного объёма деформированного слоя, чему препятствуют (в силу сплошности материала) слои, лежащие ниже. В результате такого взаимодействия в наружных слоях возникают напряжения сжатия, а во внутренних – уравновешивающие их растягивающие напряжения. При местном сжатии двух тел, например при внедрении сферического пуансона в плоскость, область максимальных касательных напряжений, в которой начинает зарождаться пластическая деформация, располагается на некоторой глубине от поверхности, то можно ожидать, что в лежащей выше области, непосредственно примыкающей к поверхности, пластическая деформация начнется позже и будет протекать менее интенсивно. Тогда максимум деформационных напряжений может сказаться смещенным в глубину слоя. Это остается справедливым, если рассматривать деформацию по линии действия сжимающей силы. По мере удаления от этой линии картина меняется. Поэтому в зависимости от конкретных условий обработки — нормальной силы, сил трения, подачи, размеров инструмента и детали, а также в зависимости от свойств материала деформационные напряжения могут формироваться с максимумом, как на поверхности, так и в глубине слоя (рис. 48, а и в). Поскольку увеличение объема происходит в пластически деформированной зоне, деформационные напряжения (до перемены знака) должны соответствовать толщине этой зоны. Следовательно, все параметры обработки, определяющие упрочнение слоя, оказывают влияние и на формирование остаточных напряжений.
Напряжения формируются и вследствие давления на пластически деформированный верхний слой со стороны лежащего ниже упруго деформированного слоя.
Образующееся при обработке тепло производит мгновенный и неравномерный нагрев очага деформации. Неравномерность распределения температуры по деформированному слою вызывает неравномерные объёмные изменения, а следовательно, и появление внутренних термических напряжений. Так как лежащие ниже холодные слои препятствуют расширению верхнего нагретого слоя, то в нем возникают термические сжимающие напряжения. Они складываются с напряжениями от деформации и могут достигать высоких значений. Одновременно во внутренних слоях суммируются растягивающие напряжения. Если термические напряжения достигают предела текучести, то при одном только тепловом воздействии в поверхностном слое после охлаждения возникают остаточные растягивающие напряжения обусловленные уменьшением объема верхнего слоя и препятствующим этому влиянием слоев, расположенных на большой глубине. В рассматриваемых случаях в результате охлаждения будет снижена величина напряжений сжатия, образованных пластической деформацией. Уравновешивающие их растягивающие напряжения также несколько уменьшаются. При образовании деформационных напряжений с максимумом на поверхности в зависимости от величины и градиента деформационных и термических напряжений максимальное значение суммарных напряжений в охлажденной детали может быть или на поверхности, или сдвинуто в глубину (рис. 48, а и б). При деформационных напряжениях с максимумом в глубине слоя термические напряжения будут всегда снижать их, оставляя максимум в глубине слоя. Все рассматриваемые случаи являются характерными для обработки поверхностным пластическим деформированием.
Механизм формирования остаточных напряжений следует рассматривать как приближенную схему взаимодействия деформационных и тепловых процессов, происходящих при отделочно-упрочняющей обработке. При обкатывании и выглаживании каждый участок поверхностного слоя подвергается многократному деформированию, приводящему всякий раз к дополнительному упрочнению и повышению температуры. В результате этого величина и градиент деформационных и термических напряжений, возникающих в момент первичной деформации, претерпевают изменения. Соответственно меняются и суммарные напряжения. Поскольку при обработке с продольной подачей повторные деформации происходят главным образом за счет пластического течения металла в осевом направлении, то осевые остаточные напряжения вызванные собственно пластической деформацией, формируются с максимумом на поверхности. Его смещение в глубину слоя со снижением осевых напряжений у поверхности может происходить как вследствие высокого локального нагрева, так и вследствие перенаклёпа. Однако на осевые напряжения тепловой эффект влияет в меньшей степени, нежели на тангенциальные, чем и объясняются редкие случаи формирования суммарных осевых напряжений с максимумом в глубине слоя.
При обработке цилиндрических поверхностей текущий очаг деформации представляет собой часть эллипсоида с малой осью, расположенной в направлении движения инструмента. Следовательно, в этом направлении образующее тепло локализуется в меньшем объёме по сравнению с осевым направлением. Естественно, что и нагрев тонкого верхнего слоя в этом случае будет значительно выше. Эта разница возрастает и благодаря более высокой скорости деформации в направлении движения инструмента.
При одной и той же мощности теплового источника температурный градиент зависит от размеров (диаметра) детали и скорости перемещения источника, т. е. скорости обработки. С увеличением диаметра детали возрастает масса холодного металла сердцевины, воспринимающая тепло, что повышает температурный градиент.
При более высоких скоростях уменьшается время нагрева деформируемого участка поверхностного слоя, вследствие чего температурный градиент также увеличивается. Поэтому при обкатывании и выглаживании деталей большого диаметра, а также при повышенной скорости обкатки наиболее вероятным является сдвиг максимума остаточных напряжений в глубь охлажденной детали и резкое снижение сжимающих напряжений у поверхности и даже в некоторых случаях переход их в растягивающие напряжения. Необходимо отметить, что обязательным условием резкого снижения напряжений у поверхности является высокий градиент термических напряжений, что возможно при определенной тепловой мощности источника так как тепло образуется за счет деформации, то спад напряжений тем более вероятен, чем больше сила деформирования. Тепловой эффект усиливается с понижением теплопроводности материала.
Экспериментальные напряжения остаточных напряжений при обкатывании, выглаживании и центробежно-шариковом наклепе показывают, что спад напряжений всегда имеет место при режимах обкатки, вызывающих высокую мгновенную температуру.
При фазовых превращениях, связанных с объемными изменениями, в поверхностном слое появляются дополнительные напряжения растяжения или сжатия, которые в результате суммирования с рассмотренными выше напряжениями будут изменять их величину.
При обкатке закаленных сталей с мартенситно-аустенитной структурой остаточный аустенит распадается и превращается в мартенсит, что сопровождается увеличением удельного объема. Поэтому при обкатывании и выглаживании таких сталей возникают фазовые напряжения сжатия. Естественно, что они увеличивают значение суммарных напряжений. При деформировании титановых сплавов, наоборот, превращение -фазы в -фазу сопровождается уменьшением объема, следовательно оно связано с образованием растягивающих напряжений.