Технологии повышения долговечности деталей машин восстановлением и упрочнением рабочих поверхностей комбинированными методами
Вид материала | Автореферат |
- Повышение несущей способности деталей машин упрочнением и отделкой, 509.34kb.
- Программа вступительного экзамена в аспирантуру по специальной дисциплине 05. 02., 266.3kb.
- Моделирование и динамическая стабилизация нановыглаживания прецизионных поверхностей, 151.88kb.
- Мальным режимам позволила увеличить предел выносливости стали 45 в 2,1 раза по сравнению, 29.85kb.
- Д. М. Медведев одноступенчатое технологическое обеспечение износостойкости цилиндрических, 106.33kb.
- Технологичность деталей машин, 94.77kb.
- 1. в номинации «Энергоэффективные и ресурсосберегающие технологии, оборудование и материалы, 23.2kb.
- Теория управления эксплуатационной надежностью и долговечностью деталей машин технологическими, 56.78kb.
- Вопросы вступительных испытаний в магистратуру по направлению, 395.66kb.
- Тема: обработка конструкционных материалов лекция 16 Обработка конструкционных материалов, 82.83kb.
1 2
На правах рукописи
Коломейченко Александр Викторович
ТЕХНОЛОГИИ ПОВЫШЕНИЯ ДОЛГОВЕЧНОСТИ ДЕТАЛЕЙ МАШИН ВОССТАНОВЛЕНИЕМ И УПРОЧНЕНИЕМ РАБОЧИХ ПОВЕРХНОСТЕЙ КОМБИНИРОВАННЫМИ МЕТОДАМИ
Специальность 05.20.03 – Технологии и средства технического обслуживания в сельском хозяйстве
АВТОРЕФЕРАТ
диссертации на соискание учёной степени
доктора технических наук
Москва, 2011
Работа выполнена в Федеральном государственном образовательном учреждении высшего профессионального образования «Орловский государственный аграрный университет».
Официальные оппоненты: доктор технических наук, профессор
Пучин Евгений Александрович,
доктор технических наук, профессор
Серебровский Владимир Исаевич
доктор технических наук, профессор
Эпельфельд Андрей Валериевич
Ведущая организация – Федеральное государственное образовательное учреждение высшего профессионального образования «Мичуринский государственный аграрный университет»
Защита диссертации состоится «9» июня 2011 года в 10 часов на заседании диссертационного совета ДМ 006.034.01 при Государственном научном учреждении Всероссийский научно-исследовательский технологический институт ремонта и эксплуатации машинно-тракторного парка Российской академии сельскохозяйственных наук (ГНУ ГОСНИТИ Россельхозакадемии) по адресу: 109428, г. Москва, 1-й Институтский проезд, д.1.
С диссертацией можно ознакомиться в библиотеке ГНУ ГОСНИТИ Россельхозакадемии.
Автореферат разослан «___»__________2011 г. и размещен на сайте ВАК ссылка скрыта (referat vak@ministri.ru) «___»__________2011 г.
Ученый секретарь
диссертационного совета Р.Ю. Соловьев
ОБЩАЯ ХАРАКТИРИСТИКА РАБОТЫ
Актуальность проблемы. В Доктрине продовольственной безопасности Российской Федерации, которую утвердил Президент России 30января 2010 года указано на необходимость устойчивого развития отечественного производства продовольствия и сырья для обеспечения продовольственной независимости страны. Государственная программа развития сельского хозяйства и регулирования рынков сельскохозяйственной продукции, сырья и продовольствия на 2008-2012 годы (утверждена постановлением Правительства Российской Федерации от 14 июля 2007 г. № 446) предусматривает инновационное развитие отрасли, ускоренный переход к использованию новых высокопроизводительных и ресурсосберегающих технологий. В условиях старения машинно-тракторного парка, многократного удорожания машин и запасных частей, нехватки финансовых средств проблема технического оснащения сельскохозяйственного производства не может быть решена только за счет увеличения поступления новой техники. Большая роль в этом отводится эффективному использованию имеющегося парка машин, постоянному поддержанию его готовности за счет технического обслуживания, а также развитию и совершенствованию технологических процессов их ремонта. При эксплуатации техники 85…90% машин выходит из строя не из-за поломок деталей, а вследствие изнашивания их рабочих поверхностей. Для повышения их долговечности необходимо на изнашивающихся поверхностях создавать упрочненные слои с высокими физико-механическими свойствами. При этом для наружных поверхностей такие технологические методы разработаны более полно. А для внутренних, на долю которых приходится до 60% всех изнашивающихся поверхностей, в связи с их труднодоступностью, упрочняющих технологий, обеспечивающих длительную безизносную работу изделий, разработано недостаточно. В сельскохозяйственном машиностроении за последние 10 лет применение алюминиевых сплавов увеличилось более чем в 3 раза. В то же время ужесточение условий эксплуатации современной техники и агрессивности применяемых технологических сред приводит к тому, что износостойкость и коррозионная стойкость рабочих поверхностей деталей из алюминиевых сплавов не позволяет обеспечить их требуемую долговечность.
Перспективным способом упрочнения рабочих поверхностей деталей, изготовленных из алюминиевых сплавов, в значительной мере лишённым многих недостатков и получающим в последнее время всё более широкое распространение, является микродуговое оксидирование (МДО). Однако, в условиях граничной смазки или взаимодействия без смазочного материала, которые возникают в периоды приработки, начала или окончания работы машины, а также при аварийных ситуациях, у покрытий, сформированных МДО, проявляются повышенные фрикционные свойства. Это приводит к тому, что деталь с покрытием вызывает значительный износ сопрягаемой с ней детали типа «вал» при их взаимодействии, за счёт чего происходит снижение износостойкости подвижного соединения. Механизм формирования покрытий способом МДО предопределяет наличие у них сквозной пористости, которая зависит от режимов оксидирования, концентрации компонентов и температуры электролита. В связи с тем, что упрочнённые слои химически инертны, именно сквозная пористость будет определять защитные свойства покрытия при работе деталей в агрессивных средах.
Однако, в научной литературе применительно к рабочим поверхностям деталей, упрочненным МДО, практически отсутствуют теоретические основы и технологические рекомендации по этим вопросам. Поэтому их разработка позволит существенно повысить износостойкость подвижных соединений и коррозионную стойкость рабочих поверхностей деталей машин с такими покрытиями. В связи с этим снижение изнашивания и, как следствие, повышение долговечности деталей машин является одной из важных и актуальных научных проблем как для предприятий изготавливающих, так и эксплуатирующих сельскохозяйственную технику.
Цель работы заключается в разработке технологий восстановления с упрочнением и повышения износостойкости рабочих поверхностей деталей машин за счёт нанесения медного слоя на покрытие, сформированное МДО, или наполнения его маслом и коррозионной стойкости, путем снижения сквозной пористости упрочнённого слоя.
Объектом исследования являются комбинированные технологии, включающие в себя восстановление рабочих поверхностей, МДО, как упрочняющую обработку, и технологические приемы, позволяющие повысить долговечность подвижных соединений и деталей машин с оксидными покрытиями.
Предметом исследования являются эксплуатационные свойства восстанавливаемых и упрочненных МДО подвижных соединений и деталей машин с модифицированными и коррозионостойкими оксидными покрытиями. В частности, восстанавливаемые рабочие поверхности деталей, изготовленные из алюминиевых сплавов и чугунов: поджимные и подшипниковые обоймы, втулки и корпуса шестеренных насосов, крышки распределительных шестерен двигателей, опоры граблин жаток для уборки трав кормоуборочных комбайнов и другие.
Методы исследования. Экспериментальные исследования проводили с использованием известных, отработанных методов и современных приборов и оборудования, теории вероятности и математической статистики.
Научная новизна работы состоит:
- в установлении рациональных состава электролита и режимов МДО, позволяющих получать оптимальные физико-механические свойства, толщину и пористость упрочненного слоя для дальнейшего наполнения покрытия маслом, нанесения на него медного слоя или использования в качестве защиты от коррозии;
- в обосновании технологической схемы и режимов нанесения фрикционно-механическим способом медного слоя на покрытие, сформированное МДО;
- в выявлении связи между скоростью коррозии металлической основы и физико-механическими свойствами, толщиной и пористостью упрочненного слоя, позволяющей прогнозировать работу защитного покрытия до предельного состояния.
Практическая ценность работы заключается в разработке комбинированных технологий восстановления изношенных рабочих поверхностей деталей машин с последующим упрочнением МДО и нанесением на покрытие медного слоя или наполнением его маслом, а также получением упрочненного слоя с минимальной пористостью. Технологии апробированы на примере восстановления посадочных отверстий опор граблин жаток для уборки трав кормоуборочных комбайнов КСК-100 и КПКУ-75, поджимных и подшипниковых обойм шестерённых насосов НШ-50-2, втулок и корпусов шестерённых насосов НШ-32У-2, поверхностей под крыльчатку водяного насоса крышек распределительных шестерён двигателей ЗМЗ-53.
Реализация результатов исследований. Результаты работы реализованы в пяти руководящих документах, подготовленных совместно с ГОСНИТИ, и утвержденных Минсельхозом РФ. Разработанные технологические процессы восстановления, упрочнения и модифицирования поджимных подшипниковых обойм шестеренных насосов НШ-50-2, втулок и корпусов шестеренных насосов НШ-32У-2, поверхностей под крыльчатку водяного насоса крышек распределительных шестерен двигателей ЗМЗ-53, посадочных отверстий опор граблин жаток для уборки трав кормоуборочных комбайнов КСК-100 и КПКУ-75 и ряда других деталей, обработанных по предлагаемым технологиям, приняты к внедрению на шести предприятиях г. Орла и Орловской области. Результаты исследований используются в учебном процессе ФГОУ ВПО Орел ГАУ при переподготовке руководящих и инженерных кадров АПК в Орловской области. Они отражены в учебном пособии для вузов, допущенным Министерством сельского хозяйства РФ, и двух монографиях.
Апробация работы. Основные результаты исследований докладывались на:
- международных научно-технических и научно-практических конференциях (Орел, ОрелГАУ, 2000, 2002, 2008, 2009, 2010; Новополоцк, ПГУ, 2001, 2003; Ялта, АТМ Украины, 2002, 2003; Кишинев, Молдавский агроуниверситет, 2002, 2003; Тула, ТГУ, 2002; Пенза, ПГУ, 2003; Брянск, БГСХА, 2003-2005; Гагры, 2004, 2005; Одесса, ОНМУ, 2010; С.-Петербург, С.-П.ГАУ, 2005; Москва, МГАУ, 2000, 2004; ГОСНИТИ, 2009,2010);
- Всероссийских научно-практических конференциях (Пенза, ПГУ, 2000, 2001);
- межвузовских конференциях (Москва, РГАЗУ, 2000, 2001, 2007);
- семинаре по восстановлению и упрочнению деталей (Москва, ВНИИТУВИД «Ремдеталь», 2003);
- заседаниях кафедры надежности и ремонта машин им. И.С. Левитского ФГОУ ВПО РГАЗУ в 2009, 2010 г.г.
Публикации. Основное содержание выполненных исследований отражено в 92 печатных работах, в том числе 14 патентах на изобретение и свыше 20 статей в центральных научных журналах, рекомендованных ВАК РФ.
На защиту выносятся следующие основные положения:
- теоретическое обоснование технологической схемы и результаты экспериментальных исследований влияния режимов фрикционно-механического нанесения медного слоя на его толщину, шероховатость и прочность сцепления;
- теоретическое определение и экспериментальное подтверждение времени начала разрушения покрытия под давлением продуктов коррозии металлической основы, возникающей в результате воздействия на неё агрессивной среды, которая проникает через сквозные поры покрытия;
- результаты экспериментальных исследований изменения эксплуатационных свойств: нагрузочной способности и износостойкости подвижных соединений с покрытиями, сформированными МДО, различной пористости с нанесённым медным слоем и наполненных маслом, а также коррозионной стойкости деталей;
- новые способы восстановления с упрочнением МДО и модифицированием упрочняющих покрытий рабочих поверхностей деталей, а также устройства для их осуществления, защищенные патентами Российской Федерации на изобретения;
- разработанные комбинированные технологии восстановления с последующим упрочнением МДО и нанесением медного слоя или наполнением покрытий маслом, обеспечивающие повышение износостойкости подвижных соединений деталей машин, а также позволяющие получать высокую коррозионную стойкость изделий, и результаты их апробации;
- практические рекомендации по применению предлагаемых технологий и разработок в ремонтном производстве и их технико-экономическая оценка.
Объем и структура диссертации. Работа состоит из введения, пяти глав, общих выводов, библиографии и приложений. Диссертация изложена на 364 страницах машинописного текста и содержит 106 рисунков, 21 таблицу, список литературы из 311 наименований и 36 приложений.
Автор выражает признательность своим ученикам Титову Н.В., Чернышову Н.С. и Логачёву В.Н. за совместную научную работу над этой проблемой, а также Басинюку В.Л., Кукареко В.А. и Мардосевич Е.И. за помощь в проведении исследований. Отдельная благодарность профессорам Лялякину В.П., Юдину В.М. и Батищеву А.Н. за оказание консультаций при выполнении данной работы.
КРАТКОЕ СОДЕРЖАНИЕ РАБОТЫ
Во введении обоснована актуальность научной проблемы; определена цель работы; выбраны объект, предмет и методы исследований; раскрыты научная новизна и практическая ценность работы; приведены научные положения и результаты, выносимые на защиту, и структура диссертации.
Первая глава посвящена анализу современного состояния вопроса, определению цели и задач исследования.
Непрерывно повышающиеся требования к эксплуатационным свойствам сельскохозяйственной техники все чаще не могут быть удовлетворены с помощью применения известных конструкционных материалов и способов изготовления, восстановления и упрочнения поверхностей подверженных изнашиванию, а так же существующих методов модификации смазочных материалов. Всё это заставляет изыскивать новые более совершенные методы борьбы с изнашиванием для повышения долговечности машин и механизмов. Сопрягаемые внутренние цилиндрические поверхности подвижных соединений и плоские поверхности деталей машин являются часто изнашиваемыми при эксплуатации сельскохозяйственной техники. Для изготовления изделий, содержащих данные поверхности, используются алюминиевые сплавы и чугуны. Максимальный износ рабочих поверхностей деталей, выбранных в качестве предмета исследования, колеблется от 0,3 до 3,6 мм. От 70 до 100% продефектованных внутренних цилиндрических и плоских поверхностей деталей требуют своего восстановления. Большой вклад в развитие восстановления рабочих поверхностей деталей внесли Батищев А.Н., Бурумкулов Ф.Х., Голубев И.Г., Катц Н.В., Курчаткин В.В., Ли Р.И., Лялякин В.П., Патон Б.Е., Пучин Е.А., Серебровский В.И., Черноиванов В.И., Юдин В.М. и многие другие ученые.
Для повышения износостойкости и коррозионной стойкости внутренних цилиндрических и плоских поверхностей целесообразно использовать упрочняющие покрытия на основе оксида алюминия Al2O3. Данные покрытия обладают высокими служебными свойствами. Они стойки к изнашиванию и окислению. Одним из перспективных и стремительно развивающихся способов упрочнения оксидными покрытиями изделий сельскохозяйственного машиностроения из алюминиевых сплавов или из чугунов и сталей, с нанесёнными на изношенные поверхности алюмосодержащими материалами, является МДО. Большой вклад в развитие и совершенствование МДО внесли Басинюк В.Л., Батищев А.Н., Гордиенко П.С., Кузнецов Ю.А., Людин Б.Л., Малышев В.Н., Марков Г.А., Новиков А.Н., Снежко Л.А., Суминов И.В., Фёдоров В.А., Черненко В.И., Эпельфельд А.В. и ряд других учёных.
По сравнению с анодированием МДО ведется при напряжениях, которые выше примерно на порядок. Используются в основном переменный и импульсный токи, а не постоянный. Для МДО применяются различные электролиты. Наибольшее распространение вследствие современных экологических требований получил силикатно-щелочной электролит. В отличии от анодных оксидных пленок покрытия, сформированные МДО, характеризуются большими толщиной и твердостью.
Упрочнение можно осуществлять как при изготовлении, так и при восстановлении изношенных рабочих поверхностей деталей машин. Причем применение МДО в комбинации со способами восстановления рабочих поверхностей позволит не только компенсировать любой износ, но и упрочнить восстановленные внутренние цилиндрические и плоские поверхности. Вместе с тем, при граничной смазке или взаимодействии без смазочного материала у покрытий, сформированных МДО, проявляются высокие фрикционные свойства, что отрицательно сказывается на износостойкости подвижного соединения в целом. А наличие в упрочненном слое сквозных пор, предопределенных механизмом МДО, будет определять защитные свойства деталей при их эксплуатации в агрессивных средах.
Анализ литературных источников показал, что проблемы, возникающие при упрочнении деталей МДО, требуют дополнительного изучения, в соответствии с чем, и были сформулированы задачи научного исследования:
- Обосновать технологическую схему и режимы фрикционно-механического нанесения медного слоя на покрытие, сформированное МДО.
- Установить влияние сквозной пористости покрытия на защитные свойства упрочненного слоя от коррозии.
- Определить рациональные режимы МДО, состав, стабильность и температуру электролита для получения оптимальных твердости, толщины и сквозной пористости покрытия под нанесение на него медного слоя или наполнения его маслом, обеспечивающих высокую износостойкость подвижных соединений, а также надёжную защиту деталей от воздействия внешних факторов.
- Установить влияние качественных характеристик покрытия на толщину, шероховатость и прочность сцепления медного слоя.
- Оценить нагрузочную способность и износостойкость подвижных соединений с покрытиями, сформированными МДО, различной пористости с нанесённым медным слоем или наполненных маслом, а также коррозионную стойкость упрочненных рабочих поверхностей деталей.
- Разработать комбинированные технологии восстановления и упрочнения рабочих поверхностей деталей, провести стендовые и производственные испытания, рассчитать технико-экономическую эффективность результатов научного исследования.
Во второй главе представлены теоретические исследования по обоснованию технологической схемы нанесения медного слоя на поверхность покрытия и определения времени начала разрушения покрытия от давления, создаваемого продуктами коррозии металлической основы.
В основу технологии положен способ фрикционно-механического нанесения антифрикционных слоёв, разработанный группой российских специалистов под руководством Д.Н. Гаркунова и И.В. Крагельского, характеризующийся отсутствием ударного взаимодействия инструмента с поверхностью обрабатываемой детали. Однако при его использовании в зоне контакта инструмента и детали создаётся контактное давление до 150 МПа, которое приводит к разрушению покрытия за счет деформации металлической основы. Предварительные исследования показали, что при уменьшении контактного давления до уровня, исключающего разрушение покрытия, на его поверхности образуются лишь отдельные фрагментарные участки меди, а сплошной слой отсутствует.
Б
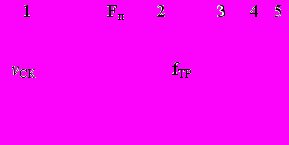
Рис. 1 – Схема взаимодействия натирающей пластины с покрытием, сформированным МДО, при фрикционно-механическом нанесении медного слоя: 1 – натирающая пластина из меди; 2 – теплоизолирующее оксидное покрытие, сформированное МДО; 3 – нажимной элемент устройства для натирания; 4 – покрытие, сформированное МДО; 5 – деталь
ыло выдвинуто предположение о том, что получение качественного медного слоя на поверхности покрытия, сформированного МДО, при контактном давлении исключающем его разрушение возможно если использовать в качестве инструмента тонкую медную натирающую пластину, закреплённую на нажимном элементе устройства для натирания и теплоизолированную от него таким же покрытием. При взаимодействии с покрытием на детали, натирающая пластина оказывается теплоизо-лированной с обеих сторон (рис. 1). В этом случае происходит локали-зованный нагрев зоны фрикционного контакта между покрытием и натирающей пластиной из меди до температуры, при которой происходит её рекристаллизация и перенесение на поверхность покрытия с образованием сплошного медного слоя.
При разработке технологической схемы взаимодействия натирающей пластины с покрытием, сформированным МДО, были приняты следующие допущения:
- при малой толщине натирающей пластины, имеющей относительно небольшую, по сравнению с контактирующей поверхностью, площадь (не более 0,2% от площади контакта) потерями теплоты на ее боковых гранях можно пренебречь;
- потери теплоты через верхнюю и нижнюю части натирающей пластины должны быть небольшими, так как теплопроводность
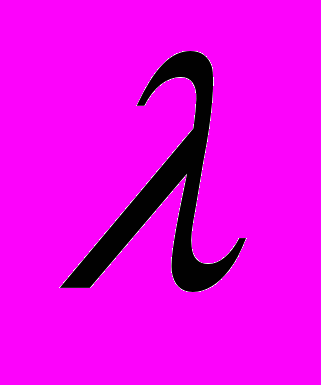
- в результате соприкосновения натирающей пластины с новым участком поверхности покрытия происходят потери, выделяющейся при трении в зоне фрикционного контакта теплоты, которые зависят от соотношения длин натирающей пластины и обрабатываемой поверхности;
- теплопроводность
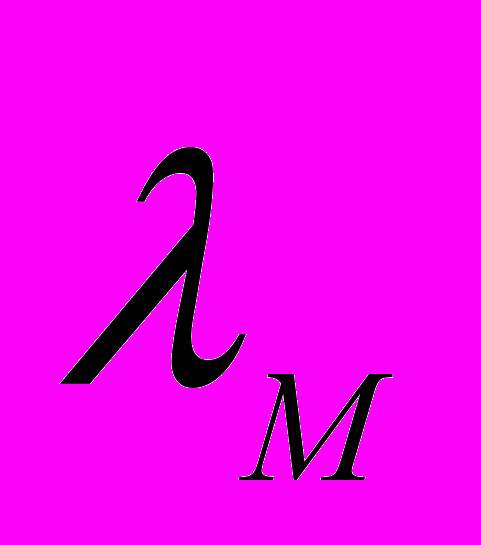
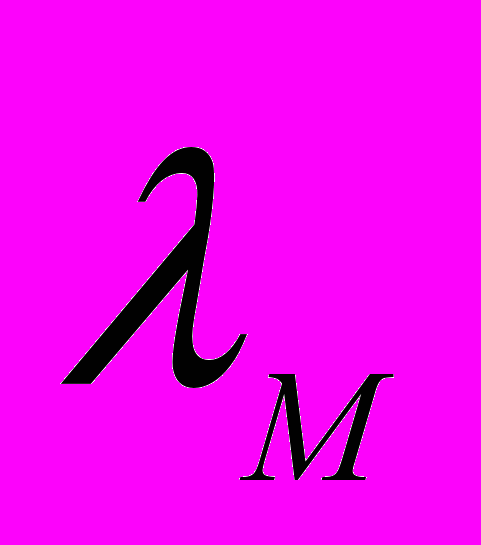
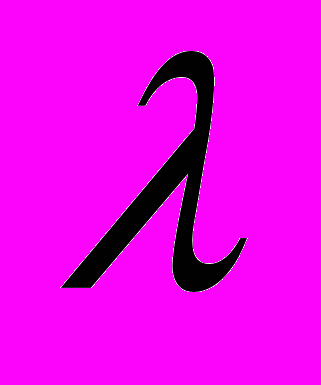
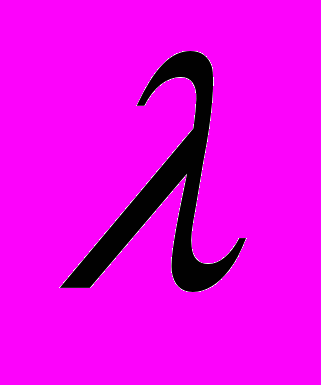
Количество теплоты, выделяющееся и концентрирующееся в натирающей пластине при ее трении по покрытию, до момента, при котором на его поверхности начинает образовываться медный слой, с учетом приведенных выше потерь теплоты, может быть определено следующим образом:

где
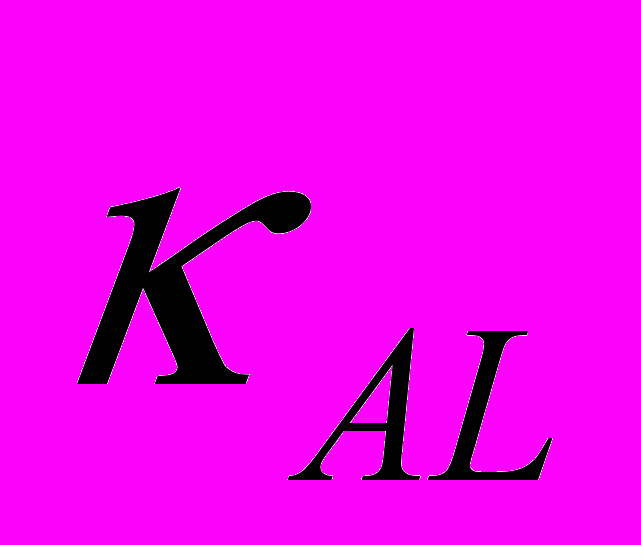
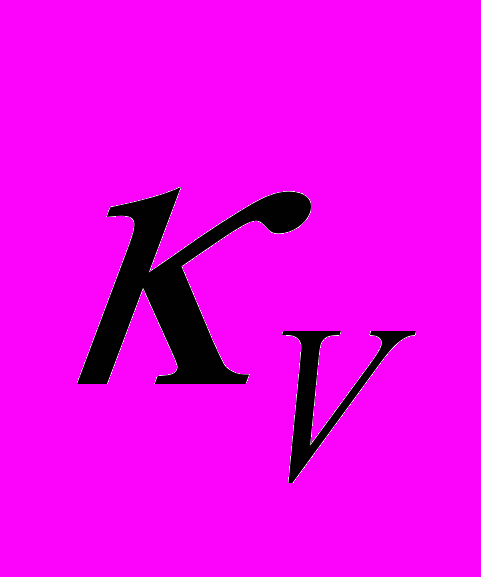
FП – сила прижатия натирающей пластины к покрытию, Н;
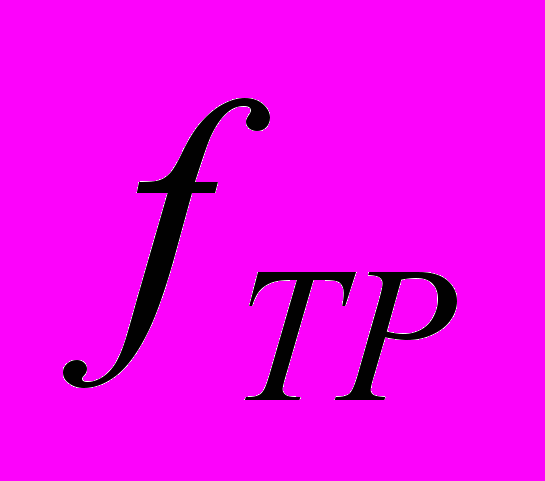
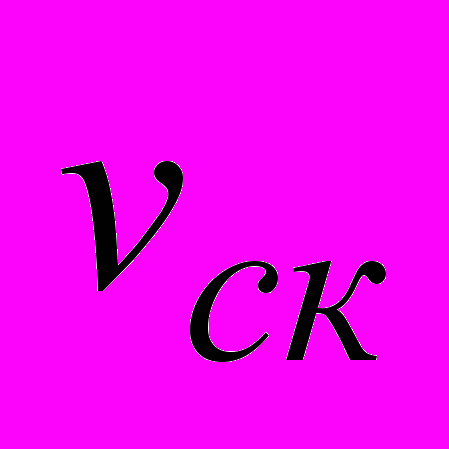
Т – продолжительность нагрева натирающей пластины до температуры, при которой на поверхности покрытия начинает образовываться медный слой, с.
Ориентировочное значение температуры натирающей пластины, при которой на поверхности покрытия, сформированного МДО, начинает образовываться медный слой, может быть определено по формуле:

где
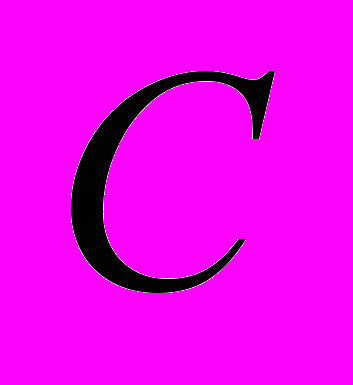
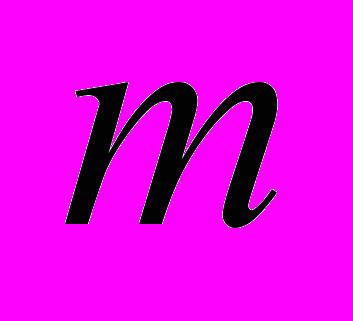
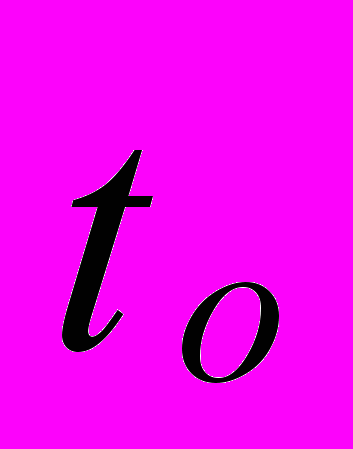
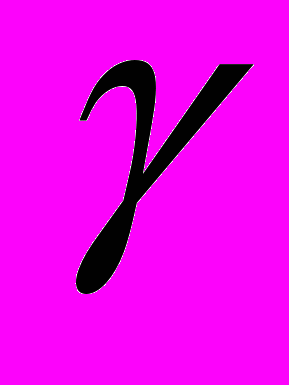
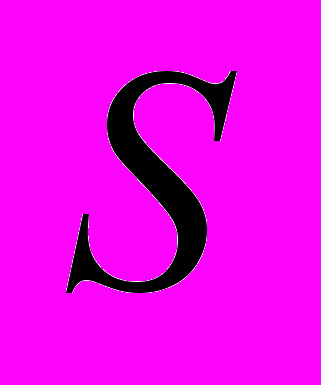
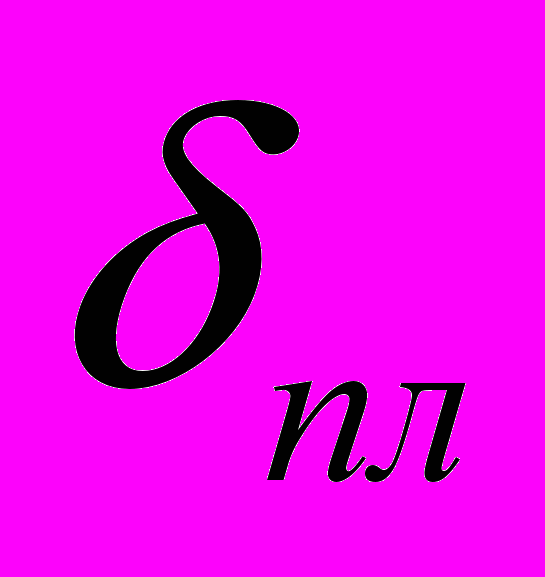
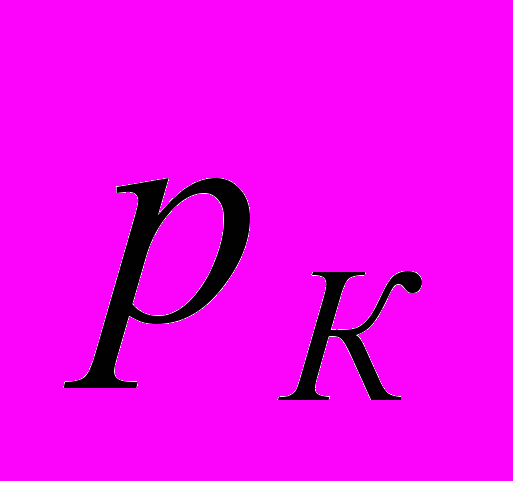
Обозначим отношение температуры натирающей пластины t к температуре плавления tМ материала, из которого она изготовлена, коэффициентом КМР, тогда
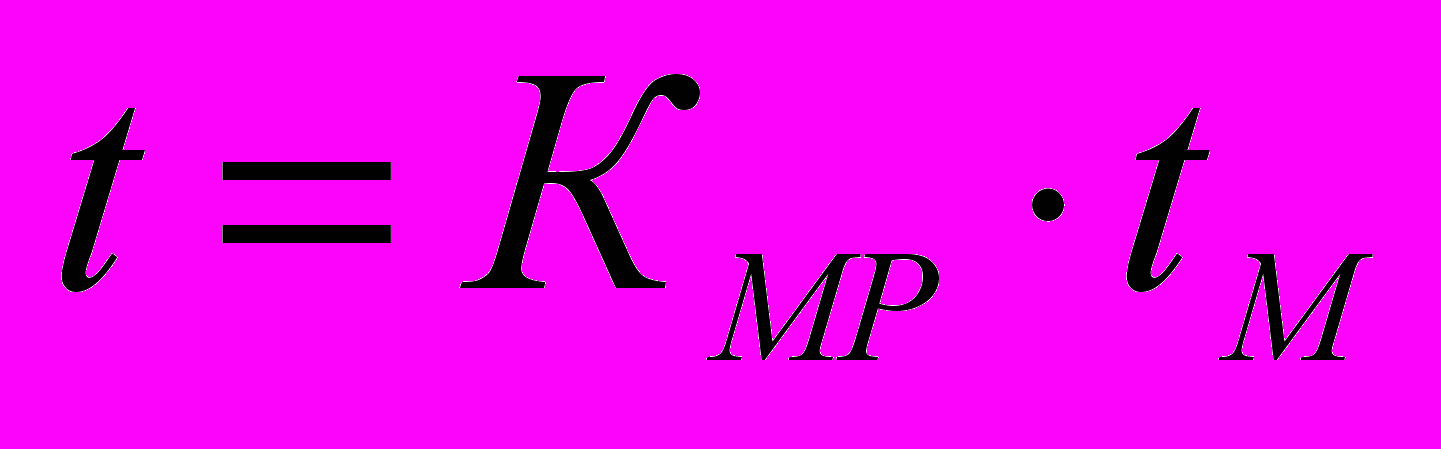
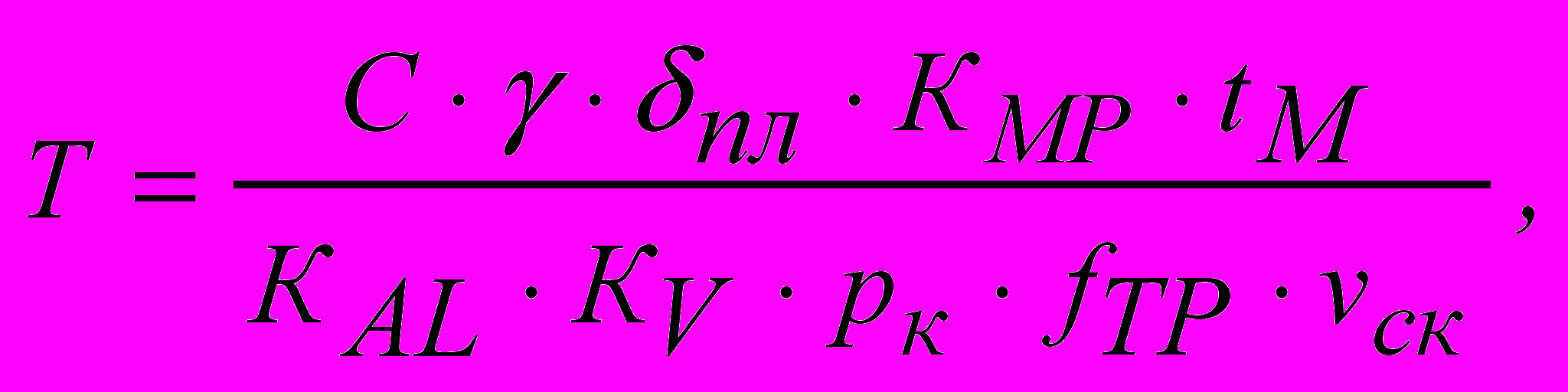
Предварительно проведённые исследования позволили установить, что значение
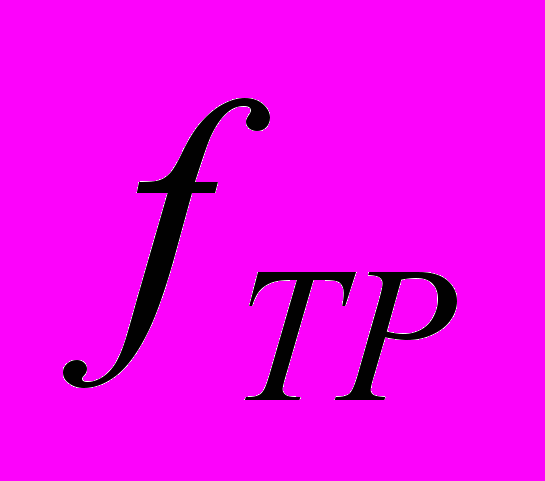
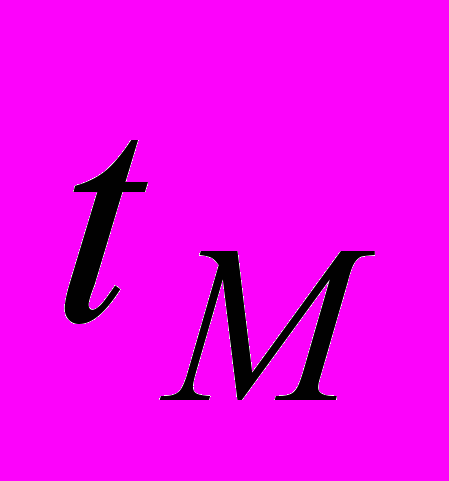
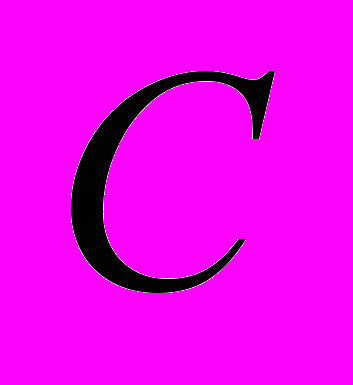
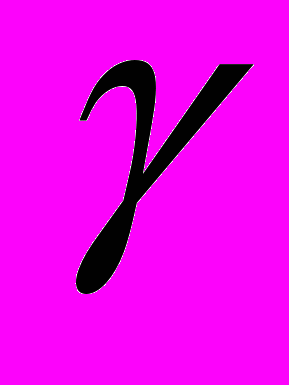


где
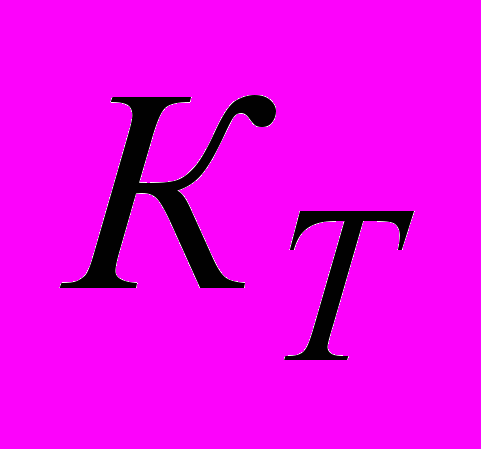
П

Одним из методов борьбы с коррозией является защита металлической поверхности не поддающимся воздействию агрессивной среды материалом. Оксидные покрытия, сформированные на алюминиевых сплавах МДО, являются химически инертными и не проводят электрический ток. В этом случае коррозионному разрушению, вследствие проникновения агрессивной среды через сквозные поры оксидного покрытия, будет подвергаться металлическая основа.
На основании проведенных исследований можно сделать допущение, что сквозная пора, через которую агрессивная среда проникает к металлической основе, имеет форму близкую к окружности радиуса r (рис. 2). Анализ разрушений деталей показал, что изношенная поверхность в первом приближении может быть аппроксимирована частью поверхности сферы со стрелой сегмента h (глубина коррозионной раковины).
В соответствии с химической реакцией процесса коррозии имеется определенное соответствие между массами прокорродированного металла и продуктами коррозии. Введем коэффициент изменения массы:
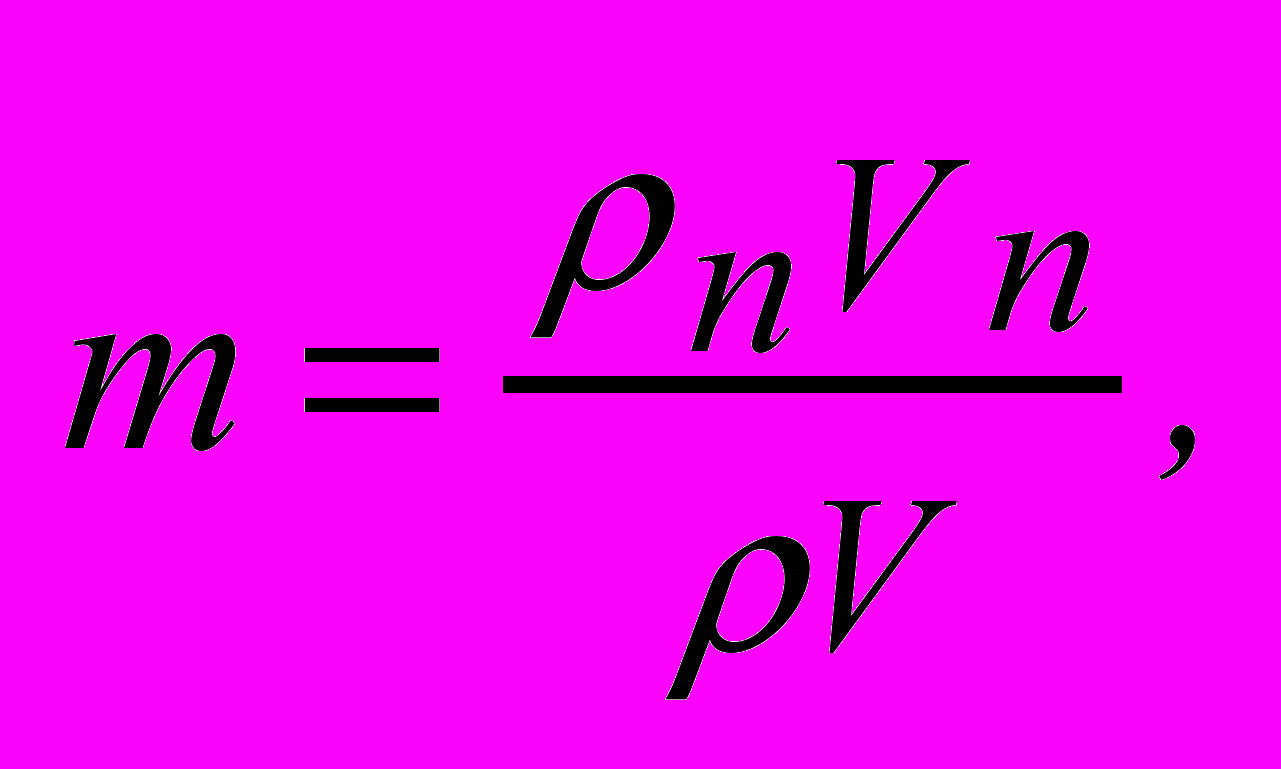
где ρп и ρ– плотность продуктов коррозии и металлической основы, кг/м3;
Vп и V – объемы продуктов коррозии и прокорродировавшего металла, м3.
Изменение давления p в коррозионной раковине в результате приращения объема продуктов коррозии под оксидным покрытием:
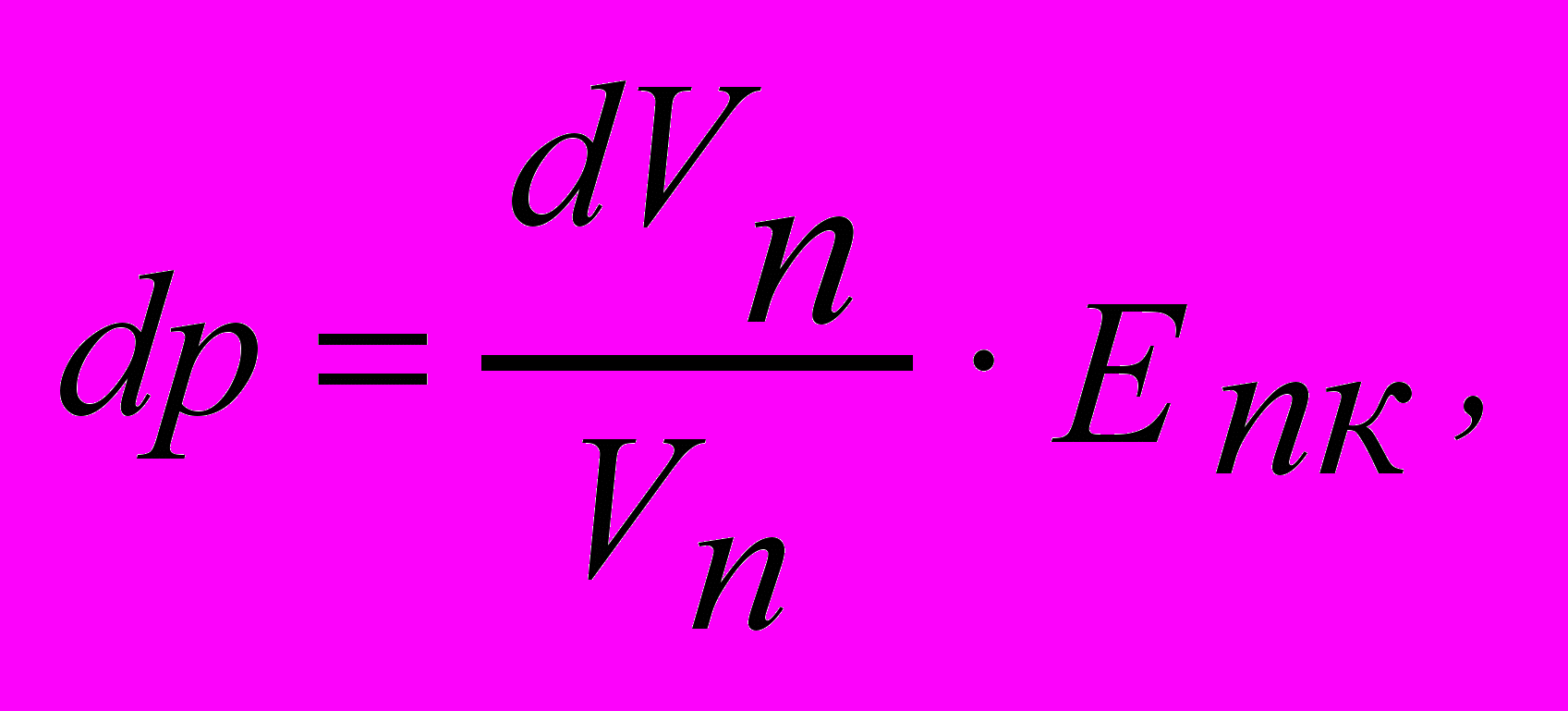
где Епк – модуль деформации продуктов коррозии, Па.
Началу образования продуктов коррозии под покрытием в зоне поры предшествует инкубационный промежуток времени τu, в течение которого начинается коррозия металла. Начальная размеры полости xм=r, h=h0. Избыточное давление p равно нулю.
При данных принятых начальных условиях интегрирование уравнения (6) дает выражение для определения избыточного давления продуктов коррозии под покрытием:
, Па, (7)
где относительное время отрыва покрытия:
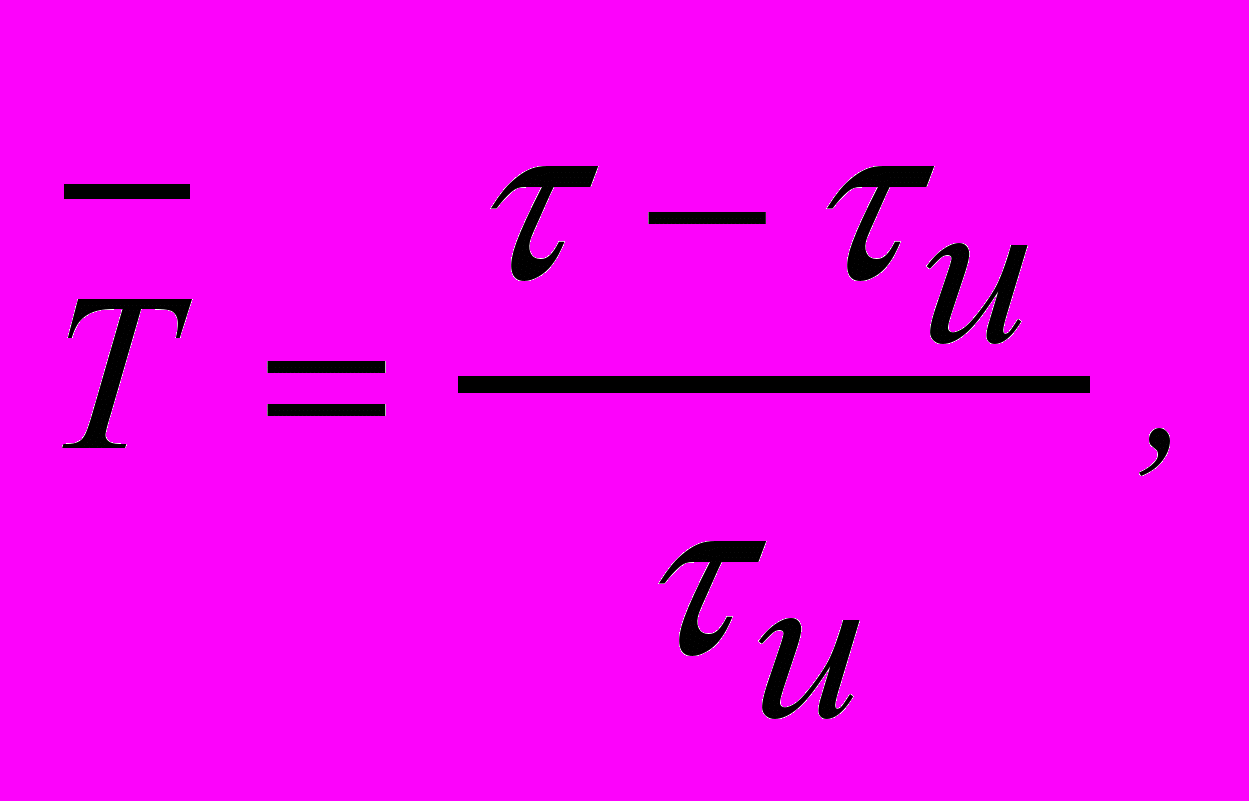
а
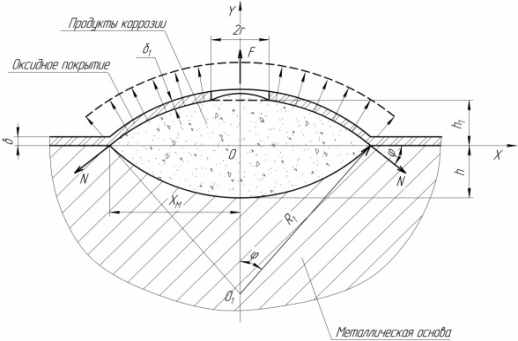
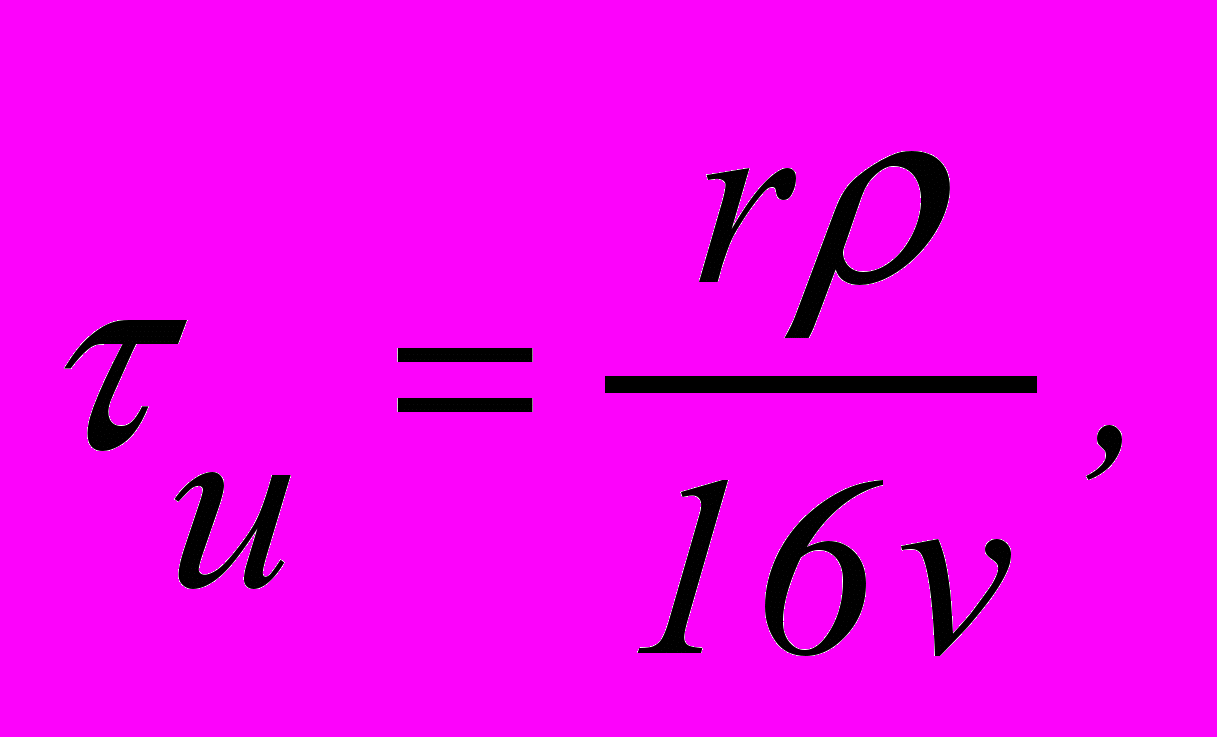
где v – скорость коррозии (масса прокорродировавшего металла с единицы поверхности в единицу времени), принимается постоянной;
r – радиус поры в покрытии, м.
О
Рис. 3 - Схема образования выпуклости на оксидном покрытии под воздействием давления продуктов коррозии металлической основы
бразование и увеличение количества нерастворимых продуктов коррозии под покрытием приводит к возникновению растягивающих напряжений в стенках образующейся выпуклости (рис. 3).
Равнодействующая сила F давления Р уравновешивается реакцией N в контуре общей зоны контакта радиуса xм. Когда усилия N создадут напряжения, превышающие предел прочности материала покрытия, происходит его разрушение. Как показано в работе, условие разрушения покрытия можно записать в виде:
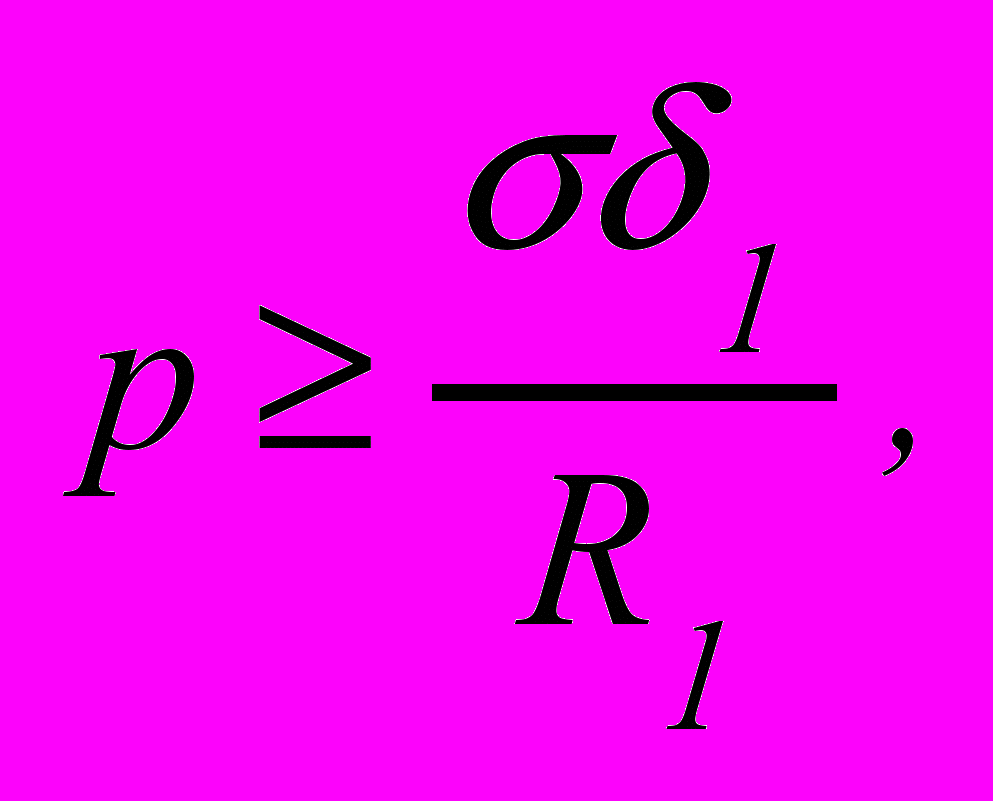
где - предел прочности покрытия, Па;
δ1 – толщина стенки образовавшейся выпуклости, м;
R1 – радиус выпуклости, м.
После преобразования условия (10) получаем зависимость для определения времени начала разрушения покрытия:
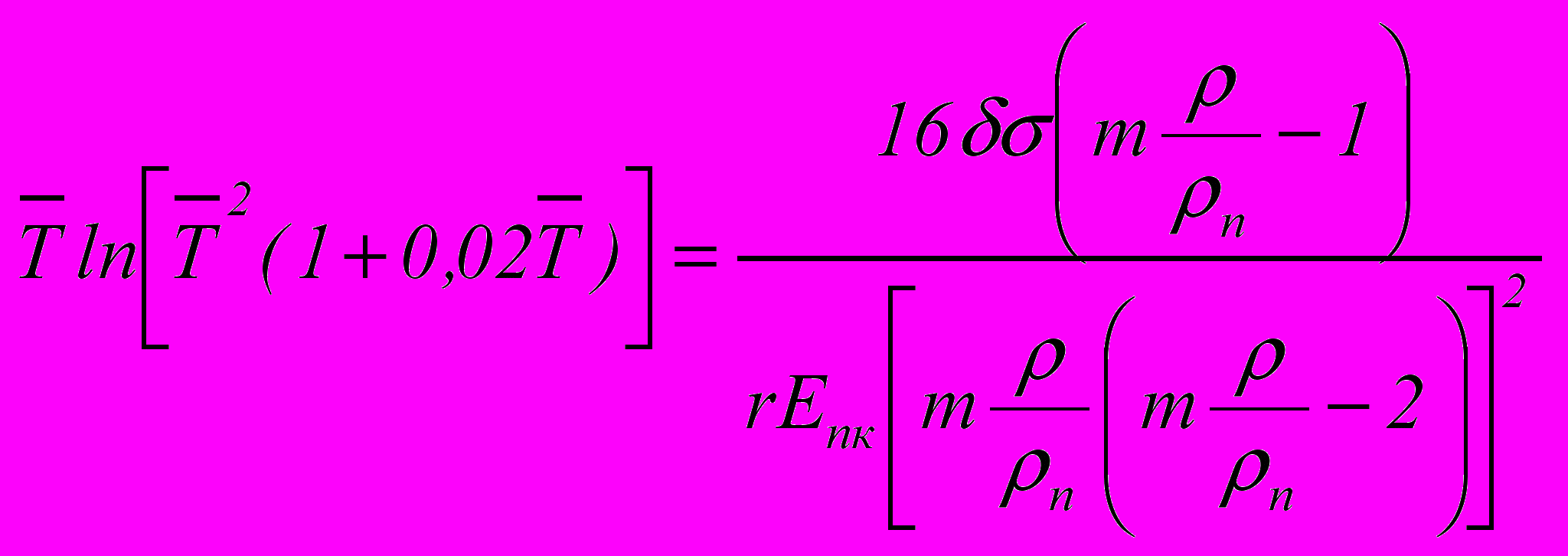
В работе приведено графическое решение этого уравнения, которое позволяет прогнозировать продолжительность работы покрытия в агрессивных средах до его разрушения под воздействием давления продуктов коррозии, зная толщину и физико-механические свойства покрытия, размеры сквозной поры, а так же скорость коррозии металлической основы.
В третьей главе приведены программа, оборудование и методики экспериментальных исследований. Программой исследований предусматривалось: разработать научные и технологические основы повышения долговечности деталей машин восстановленных и упрочненных МДО; провести теоретические и экспериментальные исследования физико-механических и эксплуатационных свойств восстановленных рабочих поверхностей деталей; разработать практические рекомендации и внедрить предлагаемые технологии в производство; выполнить технико-экономическую оценку разработанных технологий.
Для проведения исследований использовали:
- алюминиевые сплавы Д16, АК7ч, АК9ч, АО3-7, АК9М2. При выборе материала исходили из того, что данные сплавы широко применяются при изготовлении – труб, корпусных деталей, втулок шестеренных насосов и прочих изделий в сельскохозяйственном машиностроении;
- припой алюминиевый марки ПА12, который используется для пайки деталей из алюминиевых сплавов, эксплуатирующихся в коррозионно-жестких условиях;
- флюс ФА-40, предназначенный для высокотемпературной пайки алюминиевыми припоями;
- сварочные проволоки свАК5 и свАМr6, а также прутки из сплава АК9М2, которые используются для аргонодуговой наплавки и электродуговой металлизации;
- в качестве материала натирающей пластины применяли технически чистую медь марки М2 с содержанием меди не менее 99,7%;
- наполнение пор покрытия жидким смазочным материалом производили маслом веретенным АУ с кинематической вязкостью 4,910-5 м2/с при температуре 200С;
- в качестве смазки при нанесении слоя меди использовали технический глицерин.
Для пайки использовали установку сварочную водородно-кислородную Энергия 1,5. Наплавку производили на установке УДГ-301. Электродуговую металлизацию осуществляли металлизатором ЭМ-12М.
Оксидирование проводили на экспериментальной установке, работающей от трёхфазной сети частотой 50Гц напряжением 380В, позволяющей осуществлять МДО в анодно-катодном режиме при соотношении катодного и анодного токов IК/IА=1,0. Электролит для МДО готовили путём растворения в дистиллированной воде необходимого количества следующих химических реактивов: КОН ГОСТ9285 с квалификацией ЧДА и Na2SiO3 ГОСТ130078 с модулем 3,0 и плотностью 1,47х103 кг/м3.
Нанесение медного слоя осуществляли на экспериментальной установке в которой диск с натирающей пластиной вращался относительно неподвижного образца с покрытием, сформированным МДО. При этом определяли максимальную силу сопротивления скольжению натирающей пластины по поверхности покрытия. После её снижения в 1,5....1,8 раза и стабилизации на этом уровне нанесение медного слоя прекращали из-за уменьшения тепловыделения в зоне контакта. Требуемое контактное давление создавали образцовым динамометром.
Кислотность электролита контролировали с помощью рН-метра-миливольтметра модели рН-121. Толщину покрытия измеряли неразрушающим методом по ГОСТ 9.302 вихретоковым толщиномером ВТ-201. Твердость покрытий определяли на приборах ПМТ-3М и КМТ-1. Для изготовления поперечных шлифов и исследования топографии покрытий использовали оборудование научно-исследовательского центра по нанотехнологиям и наноматериалам в АПК ГНУ ГОСНИТИ Россельхозакадемии: высокоточный отрезной станок Minitom “Struerus”, автоматический электрогидравлический пресс CitoPress-1 “Struerus”, шлифовально-полировальный станок LaboPol-5 “Struerus”, сканирующий зондовый микроскоп Solver Next.
Сквозную пористость покрытий определяли по ГОСТ 9.302 взаимодействием металлической основы с реагентом с образованием в местах пор пятен выделившейся меди. Для окрашивания пор образцы выдерживали в водном растворе, содержащем 20 г/л сернокислой меди и 20 мл/л соляной кислоты.
Толщину нанесенного медного слоя определяли неразрушающим методом при помощи микротвердомера ПМТ-3М с усовершенствованным барабанчиком микрометрического движения тубуса, цена деления которого составляла 0,5 мкм.
Шероховатость оксидного покрытия и медного слоя определяли профилометром модели 171621. Измеряемым параметром шероховатости являлось среднее арифметическое отклонение профиля микронеровностей – Rа.
Прочность сцепления медного слоя с поверхностью оксидного покрытия определяли на разрывной машине Р1,5 клеевым методом, основанным на отрыве склеенных дисков, на один из которых был нанесён медный слой. Её определяли, как частное от деления усилия отрыва на площадь сечения склеенных образцов.
Определение маслоемкости покрытий проводили в соответствии с требованиями ГОСТ 9.302. Количество масла, проникающего в поры, определяли на аналитических весах АДВ-200М.
Исследования нагрузочной способности подвижных соединений проводили на установке МТУ-01. Схема контакта: торцы вращающихся трёх образцов по неподвижному контробразцу. Испытанием подвергались следующие соединения: сталь - покрытие пористостью 3....4% (эталон сравнения); сталь – покрытие пористостью 14....15%; сталь – покрытие пористостью 3....4% с медным слоем; сталь – покрытие пористостью 14....15% наполненное маслом. В качестве материала для изготовления контробразцов использовали сталь 45, закаленную до HRC 40....45 с шероховатостью Rа=0,63 мкм. После приработки испытуемых соединений (20…200Н) контактное давление ступенчато повышали до скачкообразного (в 1,5....2,0 раза) увеличения коэффициента трения между взаимодействующими поверхностями. Скорость скольжения составляла 1 м/с.
Испытания на изнашивание подвижных соединений проводили в соответствии с требованиями ГОСТ 23.224 на машине трения СМТ-1М по группе А. Схема контакта: вращение контртела в виде втулки относительно неподвижного образца в виде кольца. В качестве смазки использовали масло индустриальное – 20 ГОСТ 20779, в которое для ускорения изнашивания добавили кварцевый песок дисперсностью 5 мкм в количестве 3±0,5% по массе масла, соответствующий требованиям ГОСТ 2138. Исследовались подвижные соединения аналогичные исследованиям нагрузочной способности. Приработку осуществляли при нагрузке от 20 до 200Н. Соединения испытывались при максимально допустимом контактном давлении, не приводящем к схватыванию рабочих поверхностей, и скорости скольжения 1 м/с. Износ определяли на аналитических весах АДВ-200М.
Ускоренные коррозионные испытания проводили с помощью лабораторного автоклава А-10 MINI согласно ГОСТ 9.308. Для проведения эксперимента использовали коррозионные растворы с различным содержанием хлористого натрия NaCl квалификации ЧДА с добавлением 0,5% концентрированной уксусной кислоты СН3СООН, остальное дистиллированная вода. Температуру агрессивной среды изменяли от 200С до 900С. Продолжительность испытаний составляла 600ч. Коррозионную стойкость образцов исследовали при помощи микроскопа МИМ-6. Изменение линейных размеров образцов контролировали рычажным микрометром МР-25 ГОСТ 4381 и вихретоковым толщиномером ВТ-201.
Ускоренные стендовые испытания шестерённых насосов НШ-32У-2 и НШ-50-2 проводили в соответствии с РД70.0009.006-85, разработанными ВНПО «Ремдеталь», на стенде КИ-4815М-03. Исследования подвергали насосы с втулками и обоймами, сопрягаемые внутренние цилиндрические поверхности которых имели покрытия наполненные маслом. Сравнение осуществляли с упрочненными деталями не наполненными маслом. Для ускорения испытаний в минеральное масло М10Г2 добавляли абразивный материал, изготовленный из кварцевого песка дисперсностью 5....20 мкм - 70% и 30....40 мкм - 30%. Концентрация засорителя составляла 1 г/л масла. Износ внутренних цилиндрических поверхностей поджимных и подшипниковых обойм под цапфы шестерен, а также аналогичных поверхностей поджимных обойм, сопряженных с головками зубьев шестерен определяли глубиномером микрометрическим ГМ-100 кл. 1 ГОСТ 7470. Износ внутренних цилиндрических поверхностей втулок под цапфы шестерен определяли нутромером индикаторным НИ-50-0,002, а колодцев корпуса – НИ-100-0,002 ГОСТ 4381. Износ цапф и венцов шестерен - соответственно микрометрами рычажными МР50 и МР75 ГОСТ 4381.
Эксплуатационные испытания экспериментальных изделий проводили на предприятиях г. Орла и Орловской области.
В четвертой главе представлены результаты экспериментальных исследований и анализ изменения эксплуатационных свойств: нагрузочной способности и износостойкости подвижных соединений покрытиями, сформированными МДО, различной пористости с нанесённым медным слоем и наполненных маслом, а также коррозионной стойкости покрытий и их стойкости к нагреву и термоциклам.
Сформированные МДО оксидные покрытия химически инертны по отношению к большинству агрессивных сред. Однако в результате их проникновения через сквозные поры оксидного покрытия коррозионному разрушению подвергается металлическая основа - алюминиевый сплав. В связи с этим основной характеристикой покрытий, обеспечивающей их коррозионную стойкость, будет являться минимальная сквозная пористость упрочненного слоя. Кроме того, увеличение сквозной пористости интенсифицирует тепловые потери при нанесении медного слоя, что непременно отразится на его толщине и качестве. С другой стороны, наличие определенного процента пористости может благоприятно сказаться на изнашивании покрытия в смазочной среде. Поэтому были проведены исследования, позволившие установить влияние изменения режимов МДО, состава и температуры электролита на сквозную пористость покрытия.
Исследования показали, что изменение концентрации КОН в электролите, при постоянных остальных параметрах МДО, не оказывает значительного влияния на сквозную пористость покрытия. Это связано с тем, что химический состав оксидируемого сплава главным образом влияет на элементный и, соответственно, фазовый состав покрытия, а изменение КОН в электролите сказывается главным образом на растравливании поверхности образца и формировании внутреннего упрочненного слоя, а также на времени зажигания МДР. При исследовании влияния, которое оказывает на пористость покрытия содерджание Na2SiO3 в электролите, при постоянных остальных параметрах МДО, выявлено, что её минимальное значение практически не изменяется до концентрации 11 г/л (рис. 4). После этого значения наблюдается стремительный рост пористости упрочненного слоя. Это связано с возрастанием энергии микродуговых разрядов (МДР) и скорости формирования покрытия, что способствует увеличению количества и размера пор. В тоже время известно, что толщина упрочненного слоя при СNa2SiO3=6 г/л составляет всего 80....90 мкм, которой явно недостаточно для высокой твердости, которая обычно возрастает с увеличением толщины покрытия. Это обусловлено постоянно возрастающим термическим воздействием МДР на материал покрытия, при увеличении толщины которого уменьшается теплоотвод в металлическую основу и электролит и возрастает формовочное напряжение. В связи с этим для получения высокой твердости необходимо формировать покрытие не менее 120....150 мкм. Анализируя влияние, которое оказывает изменение плотности тока на сквозную пористость покрытия, при постоянных остальных параметрах МДО, можно отметить, что ее минимальные значения приходятся на интервал от 15 до 25 А/дм2 (рис. 5). Это связано с тем, что при низкой плотности тока энергии МДР недостаточно для сплавления границ кристаллов, образующих упрочненный слой. С другой стороны, чем выше энергия МДР, тем больше размеры кристаллов покрытия. При этом МДР возникают на большем расстоянии друг от друга, не успевая сплавлять границы образующихся кристаллов. Исследуя влияние продолжительность оксидирования на сквозную пористость покрытия, при постоянных остальных параметрах МДО, можно отметить, что ее минимальные значения наблюдаются в районе 2-х часов обработки (рис. 6). Это связано с тем, что формирование покрытия практически завершается. МДР начинают затухать и переходить в более мощные дуговые разряды (ДР), которые обладают большей энергией и увеличивают пористость упрочненного слоя. С увеличением температуры электролита, при постоянных остальных параметрах МДО, сквозная пористость покрытия возрастает (рис. 7). Это связано с тем, что с ростом температуры электролита увеличивается скорость растворения металлической основы и формируемого покрытия в диэлектрически слабых местах. Таким образом, оптимальной температурой для получения минимальной сквозной пористости покрытия является 200С, так как для ее дальнейшего снижения потребуется мощная система охлаждения электролитической ванны и дополнительные энергозатраты. Причем данная тенденция прослеживается как на деформируемых, так и на литейных сплавах, а также на поверхностях, полученных с использованием алюмосодержащих припоев и сварочных проволок.
![]() | ![]() |
Рис. 4 – Влияние концентрации Na2SiO3 на сквозную пористость покрытия П на сплаве Д16 при Дт =20А/Дм2; t=200С; Т = 2 ч; Скон = 3 г/л ![]() | Рис. 5 – Влияние плотности тока Дт на сквозную пористость П покрытия на сплаве Д16 при t=200С, Т = 2ч, СKOH = 3 г/л; СNa2SiO3=10 г/л ![]() |
![]() | ![]() ![]() |
Рис. 6 – Влияние продолжительности оксидирования T на сквозную пористость П покрытия на сплаве Д16 при Дт =20А/Дм2; t=200С;СKOH = 3 г/л; СNa2SiO3=10 г/л ![]() | Рис. 7 – Влияние температуры электролита t на сквозную пористость П покрытия при Дт =20А/Дм2; Т=2ч; СKOH = 3 г/л; СNa2SiO3=10 г/л ![]() |
Таким образом, для получения минимальной сквозной пористости покрытий, рекомендуются следующие параметры МДО: концентрация компонентов электролита, г/л: КОН -3, Na2SiO3 – 10, остальное – дистиллированная вода; режимы МДО: плотность тока - 20 А/дм2, температура электролита - 200С, продолжительность МДО - 2 часа. Долговечность электролита до его корректировки составит около 20 А·ч/л. При использовании вышеуказанных рациональных параметров МДО сквозная пористость покрытия составит 3…4%, что обеспечит возможность избежать тепловых потерь при нанесении медного слоя и надежную защиту деталей от коррозионного воздействия агрессивной среды.
При использовании силикатно-щелочного электролита: КОН – 3 г/л, Na2SiO3 – 10 г/л, остальное дистиллированная вода и режимов МДО: плотность тока – 20 А/дм2, соотношение катодного и анодного токов IК/IА=1,0 и продолжительность обработки - 120 мин. толщина покрытия (после удаления технического слоя) составит: на деформируемом сплаве Д16 – 150 мкм, на литейном сплаве АК9ч – 120 мкм, на литейном и антифрикционном сплавах АК7ч и АО3 -7 после обжатия – 120 мкм, на припое ПА12 – 120 мкм, на сварочных проволоках свАМr6 – 120, свАК5 и свАК9М2 мкм. Максимальное значение твердости покрытий: деформируемый сплав Д16 – 22 ГПА, литейный сплав АК9ч – 9 ГПА, литейный и антифрикционный сплавы после обжатия АК7ч – 10 ГПА, АО3-7 – 12 ГПА, припой ПА12 – 8 ГПА, сварочные проволоки свАМr6 – 11 ГПА, свАК5 – 10 ГПА, свАК9М2 – 9 ГПА.
Т
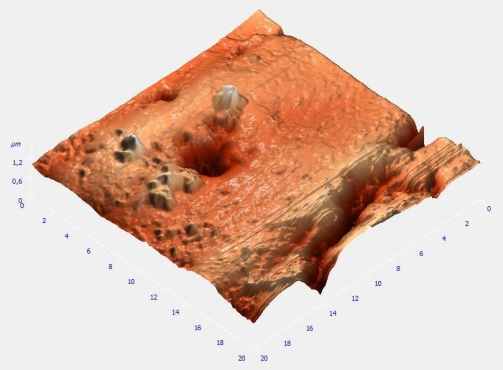
А
Рис. 8 - Топография поверхности покрытия с поперечного шлифа на плоскости 20 х 20 мкм
пробацию фрикционно-механического нанесения медного слоя на поверхность покрытия, сформированного МДО, осуществляли на экспериментальной установке при рк=5…15МПа, vск=0,1....0,5 м/с с использованием натирающих пластин различной толщины ПЛ = 0,05....0,45 мм. При этом контактирующие поверхности смазывали техническим глицерином, а также наносили медный слой без применения смазочного материала. Было установлено, что:
- продолжительность нагрева натирающей пластины существенно зависит от ее толщины, контактного давления в зоне обработки, скорости скольжения пластины по поверхности оксидного покрытия, потерь теплоты в зоне фрикционного контакта и особенностей материала натирающей пластины, определяющих температуру начала фрикционно-механического нанесения медного слоя на поверхность оксидного покрытия;
- с уменьшением толщины натирающей пластины время её нагрева до температуры, при которой на поверхности покрытия начинает образовываться медный слой, также уменьшается. Однако при этом необходимо учитывать, что минимальное значение толщины натирающей пластины определяется её прочностью на разрыв под действием сил трения и соотношением площадей пластины и обрабатываемой поверхности.
С
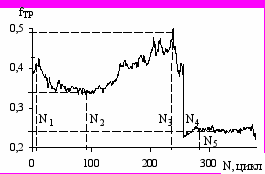
Рис. 9 – Изменение коэффициента трения при фрикционно-механическом нанесении медного слоя на поверхность покрытия, сформированного МДО, со смазыванием техническим глицерином
учетом этого при проведении экспериментов было выявлено, что оптимальные значения КТ=40....50. При отсутствии смазочного материала на поверхности оксидного покрытия образовывались фрагментарные участки меди, однако в целом сплошной слой получен не был. При смазывании контактирующих поверхностей техническим глицерином (рис. 9) коэффициент трения в начальный момент времени, в течение N1
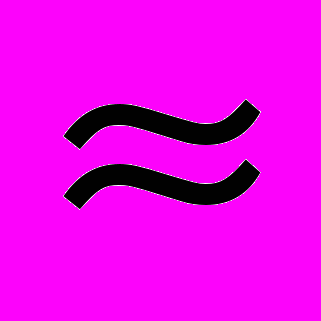
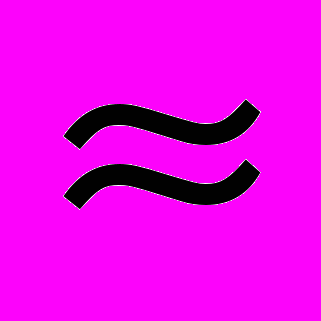
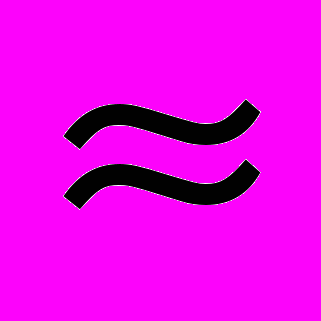
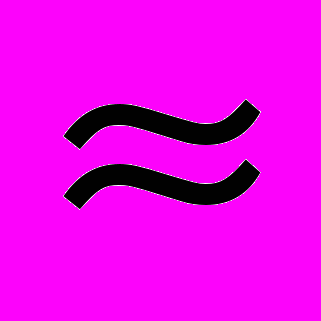
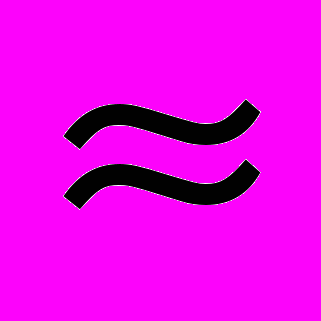
Исследования показали, что увеличение контактного давления с 5 до 15 МПа, скорости скольжения с 0,1 до 0,5 м/с и толщины покрытия с 0,09 до 0,15 мм интенсифицируют нагрев натирающей пластины при фрикционно-механической обработке, что приводит к увеличению толщины медного слоя. В то же время увеличение толщины натирающей пластины приводит к возрастанию тепловых потерь и уменьшению толщины медного слоя, а при пл=0,3 мм и более сплошной слой меди вообще не образуется. При выборе толщины пластины также необходимо учитывать её прочностные свойства и требуемый объем наносимого материала. Следует отметить, что с увеличением пористости оксидного покрытия толщина нанесённого медного слоя снижается и при пористости 15....20% сплошной слой не образуется. Это связано с тепловыми потерями. Кроме этого в сквозные поры уходит технический глицерин.
Наибольшая толщина медного слоя образуется на покрытии с шероховатостью Rа=1,20....1,25 мкм. После этого она начинает снижаться и при Rа=1,5 мкм сплошной медный слой не образуется.
Увеличение толщины натирающей пластины не оказывает влияния на шероховатость нанесённого медного слоя. В то же время увеличение контактного давления от 5 до 15 МПа при постоянной скорости скольжения 0,5 м/с приводит к уменьшению Rа с 0,93 до 0,63 мкм. Это связано с лучшим сглаживанием вершин микронеровностей при более высоких контактных давлениях. Увеличение скорости скольжения от 0,1 до 0,5 м/с при постоянном контактном давлении 15 МПа также способствует уменьшению Rа с 0,81 до 0,63 мкм. В этом случае увеличивается температура в зоне контакта поверхностей, что приводит к лучшему распределению материала натирающей пластины по обрабатываемой поверхности и её выравниванию.
Т
Рис. 10 – Нагрузочная способность для соединений: «сталь – покрытие, сформированное МДО, пористостью 3…4%» (1), «сталь – покрытие, сформированное МДО, пористостью 14…15%» (2), «сталь – покрытие, сформированное МДО, пористостью 14…15% наполненное маслом» (3), «сталь – покрытие, сформированное МДО, пористостью 3…4% с медным слоем» (4)
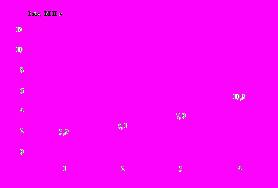
Прочность сцепления медного слоя с поверхностью покрытия, сформированного МДО, пористостью 3....4% и шероховатостью Rа=1,20....1,25 мкм составляет 21…22 МПа. Величина сцепления косвенно характеризует его физическую природу как механическое соединение слоя меди с покрытием, сопровождающееся заполнением его поверхностных пор и микронеровностей.
Маслоёмкость оксидного покрытия пористостью 14....15%, сформированного МДО, на рациональных режимах и составе электролита при его температуре 400С составляет 0,021 мг/мм2.
Анализ результатов исследования нагрузочной способности подвижных соединений показал следующее (рис. 10):
- повышение пористости покрытия до 14…15% увеличивает нагрузочную способность подвижного соединения за счёт того, что при понижении температуры после окончания приработки воздух, находящийся в порах, сжимаясь, увлекает остатки масла из зоны трения в поры упрочненного слоя. При возобновлении работы, масло, находящееся в порах, за счёт объёмного расширения воздуха, которое происходит при повышении температуры, вытесняется в зону трения и способствует повышению нагрузочной способности соединения в 1,3 раза;
- при испытаниях соединений с покрытиями с пористостью 14…15%, наполненных маслом, нагрузочная способность возрастает в 1,8 раза. Это связано с тем, что в порах покрытия находится большее чем в первом случае количество масла, что способствует приложению более значительного контактного давления к подвижному соединению до его схватывания;
- медный слой, нанесённый на поверхность покрытия, сформированного МДО, пористостью 3…4%, повышает нагрузочную способность соединения в 2,8 раза. Это происходит за счёт того, что медь переносится на ответную деталь соединения и, выступая в качестве твёрдого смазочного материала, обеспечивает возможность приложения к подвижному соединению гораздо большего контактного давления (чем в двух предыдущих случаях) до начала его схватывания.
Таким образом, нанесение медного слоя на поверхность покрытия, сформированного МДО, наиболее эффективно для повышения нагрузочной способности подвижных соединений, содержащих детали с покрытиями данного типа, работающих в условиях граничной смазки.
Сравнительные испытания на изнашивание показали, что:
-

- самая низкая скорость изнашивания после приработки наблюдалась у соединения «сталь – покрытие, сформированное МДО, пористостью 3…4% с медным слоем» (рис. 12). Она оказалась в 6,7 раза ниже, чем у соединения «сталь – покрытие, сформированное МДО, пористостью 3…4%». Наполнение покрытий пористостью 14…15% маслом снизило скорость их изнашивания в 1,6 раза. Наличие у покрытия пористости 14…15% по сравнению с пористостью 3…4% незначительно (на 10%) улучшило этот показатель. Это связано с тем, что для проведения измерений испытания периодически останавливали, и за счёт уменьшения температуры в зоне трения воздух в порах покрытия сжимался, в результате чего масло частично проникало в упрочненный слой. После возобновления испытаний происходил обратный эффект, вызывающий самосмазывание соединения в зоне трения.
Таким образом, наполнение пор оксидного покрытия маслом или нанесение на его поверхность фрикционно-механическим способом медного слоя оказывает благоприятное влияние на износостойкость подвижных соединений, а именно, увеличивает её, соответственно, в 1,7 раза и 4,5 раза по сравнению с обычным покрытием, сформированным МДО, пористостью 3…4%. В связи с этим данные технологические приёмы целесообразно применять в качестве финишных операций при восстановлении изношенных деталей с последующим упрочнением МДО, так как от них зависит не только приработочный износ, но и скорость изнашивания подвижного соединения при эксплуатации машины.
К
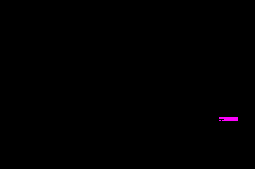
Рис. 13 - Сравнение расчетного и экспериментального (полученного в режиме 4) значений продолжительности разрушения покрытия
оррозионные испытания показали, что при воздействии агрессивной среды под покрытием в зонах сквозных пор развивается коррозия металлической основы. Под давлением, создаваемым продуктами коррозии, происходит увеличение действительных размеров образцов с образованием «мениска». Затем покрытие начинает отслаиваться. Конечной стадией воздействия агрессивной среды на покрытие является его разрушение, которое происходит при высоте «мениска» более 76…80 мкм в местах отрыва. Исследованиями была подтверждена правомерность уравнения (11) для определения времени начала разрушения покрытия от давления продуктов коррозии, возникшего в результате воздействия агрессивной среды на металлическую основу. Расхождение расчетных и экспериментальных данных составило не более 5% (рис. 13).
Ускоренные сравни-тельные стендовые испытания в течение 30 часов показали, что износостойкость подвижных сое-динений гидравлических шесте-ренных насосов НШ-32У-2 и НШ-50-2 с деталями, восстанов-ленными и упрочненными оксид-ными покрытиями пористостью 14…15% наполненными маслом, в 1,4…1,5 раза выше, чем у аналогичных с покрытиями пористостью 3…4% или 14…15% не наполненными маслом.
Таким образом за счет наполнения маслом внутренних цилиндрических рабочих поверхностей деталей упрочненных МДО обеспечивается как более качественная приработка подвижных соединений (насосы обеспечивают лучшую действительную подачу), так и больший ресурс до наступления предельного состояния.
На пяти предприятиях г. Орла и Орловской области были проведены эксплуатационные испытания экспериментальных деталей в условиях рядовой эксплуатации. В течение заданной наработки отказов испытуемых изделий выявлено не было и они были оставлены для дальнейшей эксплуатации. По каждой из рассматриваемых рабочих поверхностей деталей было отмечено существенное увеличение износостойкости или коррозионной стойкости.
В пятой главе даны практические рекомендации по применению, разработанных на основе теоретических и экспериментальных научных исследований, комбинированных технологий, позволяющих существенно повысить долговечность восстановленных и упрочнённых МДО рабочих поверхностей деталей машин. Определена их возможная экономическая эффективность.
В зависимости от износа, площади повреждения, размера и типа восстанавливаемых рабочих поверхностей, материала деталей, а так же наличия на конкретном предприятии ремонтно-технологического оборудования, восстановление или изготовление новых (ремонтных) изделий проводится по одному из маршрутов (рис. 14). После компенсации износа поверхности по любому из предложенных способов восстановления или изготовления новых (ремонтных) изделий производится упрочнение рабочих поверхностей МДО. Покрытия с пористостью 3…4% используются для повышения коррозионной стойкости рабочих поверхностей деталей или износостойкости подвижных соединений за счет нанесения на упрочненную поверхность медного слоя и реализации эффекта избирательного переноса при трении. Покрытия пористостью 14…15% применяются для повышения износостойкости подвижных соединений за счет наполнения упрочненного слоя маслом.
При выборе любой из предлагаемых технологий необходимо учитывать, что при эксплуатации восстановленных или изготовленных деталей с упрочняющим покрытием, сформированным МДО, контактные давления на него не должны превышать 15 МПа. В противном случае из-за возможной деформации металлической основы может произойти разрушение оксидного покрытия.
Выполненные исследования позволили разработать ряд организационных, технических и технологических рекомендаций по практическому осуществлению предложенных технологических процессов, а также конструкции устройств для их осуществления.
Расчетная экономическая эффективность от внедрения разработанных технологий повышения долговечности восстановленных и упрочнённых МДО рабочих поверхностей деталей машин при программе ремонта 300 шт. по каждому из рассмотренных изделий за счет увеличения их ресурса на предприятиях г. Орла и Орловской области составит свыше 1100 тыс. рублей.