Повышение несущей способности деталей машин упрочнением и отделкой
Вид материала | Документы |
- Программа вступительного экзамена в аспирантуру по специальной дисциплине 05. 02., 266.3kb.
- Технологии повышения долговечности деталей машин восстановлением и упрочнением рабочих, 553.23kb.
- Касьянов Константин Геннадьевич оценка несущей способности и ресурса конструкционных, 452kb.
- Технологичность деталей машин, 94.77kb.
- Якість поверхонь деталей машин, 156.84kb.
- Повышение эффективности технологического процесса обработки деталей машин при интеграции, 291.71kb.
- Название курса: Детали машин, 59.22kb.
- Программа дисциплины по кафедре Детали машин детали машин и механизмов, 575.22kb.
- Рабочей программы дисциплины Теория механизмов и машин по направлению подготовки 190600, 39.8kb.
- Рабочей программы дисциплины Детали машин и основы конструирования по направлению подготовки, 37.93kb.
Область рационального применения шаровых устройств – обкатка маложестких и неравножестких деталей, в том числе деталей с высокой поверхностной твердостью.
Особенности шаровых устройств:
а) использование стандартных шаров, обеспечивающих высокую точность обкатки и качество поверхности;
б) отсутствие материальной оси шаров и самоустанавливаемость их относительно обрабатываемой поверхности под действием сил обкатывания и трения;
в) отсутствие или незначительность проскальзывания шаров;
г) незначительные силы обработки, связанные с точным (условно) контактом инструмента и обрабатываемой поверхности;
д) меньшие подачи и производительность обработки, чем при использовании роликовых устройств.
Сила трения между деформирующим шаром и опорой должна быть меньше силы трения между шаром и обрабатываемой поверхностью. В качестве опоры для шара в таком случае применяют один или большее число стандартных шарикоподшипника (рис. 34 а, г; 35; 36; 37 стр. 8); опорные шайбы из фторопласта или другого антифрикционного материала (рис. 34 б, в); возможно применение режущей пластины из твердого сплава или высококачественной закаленной стали в виде хорошо отполированной лунки.
Малый коэффициент трения фторопласта и его высокая износостойкость обеспечивают надежную работу фторопластовых опор шаров диаметров более 10 мм при обкатывании и вибронакатывании.
Общим недостатком шаровых державок с сепараторами, предотвращающими выпадение шара и ограничивающими его движение относительно корпуса державки в направлении подачи, является увеличение зазора между шаром и стенками рабочего отверстия сепаратора вследствие изнашивания его и опоры шара, что ухудшает условие протекания процесса, а при вибронакатывании искажает профиль выдавливаемой синусоидальной канавки.
В качестве оборудования для накатывания поверхностей шаровым инструментом могут быть любые металлорежущие станки. Применяют также специальные станки, например, станок для бесцентрового обкатывания цилиндрических деталей, работающий в автоматическом режиме.
Повышение несущей способности деталей машин
алмазным выглаживанием
По сравнению с другими методами ППД алмазное выглаживание обладает существенными преимуществами, обусловленными физико-механическими свойствами алмаза. Алмаз – самое твердое вещество в природе, его поверхность может быть отполирована до RZ = 0,025 – 0,063 мкм, он имеет высокую теплопроводность и низкий коэффициент трения по металлу. Применение алмаза в качестве выглаживающего инструмента позволяет эффективно обрабатывать заготовки из высокопрочных материалов с поверхностной твердостью более 58 HRC. Эти материалы практически не поддаются обработке такими методами поверхностного пластического деформирования, как обкатывание и раскатывание шариковым или роликовым инструментом, поверхностное дорнование и др., причем изначальные силы давления на инструмент (50-300 Н) позволяют обрабатывать маложесткие и неравножесткие детали. При обработке заготовок выглаживанием уменьшается в несколько раз шероховатость поверхности и улучшаются физико-механические свойства поверхностного слоя (микротвердость, микроструктура, напряженное состояние), поэтому данный метод можно успешно применять вместо трудоемких финишных операций (полирование, доводка), а также для улучшения качества поверхности и эксплуатационных свойств деталей. Износостойкость деталей может повышаться на 20-40, сопротивление усталости на 30-70, сопротивление контактной усталости на 20-40.
Выглаживание заключается в пластическом деформировании обрабатываемой поверхности скользящим по ней инструментом – выглаживателем. При этом неровности поверхности оставшиеся от предшествующей обработки, сглаживаются частично или полностью, поверхность приобретает зеркальный блеск, повышается твердость поверхностного слоя, в нем образуются сжимающие остаточные напряжения, изменяется микроструктура и создается направленная структура (текстура). После выглаживания поверхность остается чистой, не шаржированной осколками абразивных зерен, что обычно происходит при процессах абразивной обработки.
Сферический индентор (выглаживатель) выдавливает канавку, раздвигая металл деформированных поверхностей в стороны. По сторонам и впереди инструмента образуются валики из пластически деформированного металла. Значительнее деформируется дно канавки, в меньшей степени - ее края. При этом создаются три вида очагов деформирования в зависимости от соотношения глубин внедрения инструмента и исходных параметров шероховатости. Контур контакта выглаживателя с деталью достаточно точно изображен на рис……
Схема формирования микронеровностей в направлении вектора скорости и подачи при выглаживании показана на рис….. Под действием силы Ру инструмент внедряется в поверхностный слой на глубину hд. В направлении скорости впереди инструмента образуется валик высотой hв. После рабочего хода инструмента происходит упругое восстановление металла на величину упр. В направлении подачи процесс формирования микронеровностей носит несколько иной характер. Помимо упругого восстановления на величину упр имеет место пластическое течение металла, выдавливаемого из-под выглаживателя в сторону выглаженной поверхности. Максимальная толщина выдавливаемого слоя А в сочетании с ∆упр определяет результирующую высоту микронеровностей после выглаживания. Представленная схема деформации, на наш взгляд, нуждается в уточнении. Параметр шероховатости исходной поверхности Rz исх. одинаков и в направлении скорости, и в направлении подачи. Учитывая, что предшествующей алмазному выглаживанию обработкой может быть или точение, или шлифование, необходимо отметить, что формирование шероховатостей в направлении и S для этих видов обработки различно. При точении на величину шероховатости в направлении скорости резания влияют особенности стружкообразования (сливная или элементная стружка). На параметры шероховатости существенно влияют геометрия инструмента, подача и глубина резания. При образовании шероховатости вдоль вектора скорости (рис. 104) тонкий поверхностный слой должен был бы иметь несплошную структуру (трещины, ориентированные вдоль вектора скорости), но ее не наблюдается при исследовании на электронном микроскопе. Кроме этого, повышение характеристик усталости выглаженных деталей также свидетельствует об отсутствии концентраторов напряжений в поверхностном слое.
Различные подачи на предшествующей обработке и при алмазном выглаживании способствуют периодическому контакту выглаживателя с различными по высоте исходными микронеровностями. Это способствует образованию микронеровностей с относительно большим шагом, т. е. волнистости поверхности в направление скорости выглаживания. Периодическое увеличение силы выглаживания в определённых условиях может вызвать автоколебания выглаживателя.
Образование шероховатости в направлении подачи определяется шагом исходных микронеровностей в этом направлении, подачей при выглаживании и радиусом сферы алмазного выглаживателя. Пластическое течение металла в сторону обрабатываемой поверхности при небольшой подаче возможно только в том случае, если при последующих обработках деформация обработанной поверхности будет больше величины ∆упр, что практически невозможно. Периодическое чередование закругленных выступов и впадин, получаемое при алмазном выглаживании, можно объяснить следующим. Величина силы при алмазном выглаживании не является постоянной, так как при движении по впадинам и выступам исходных микронеровностей припуск под выглаживание периодически меняется. Траектория движения вершины алмазного наконечника не является прямой линией, как видно из рис. , а имеет волнообразный характер (рис. 8). Существенным фактором в образовании микро-неровностей при выглаживании является копирование исходных микронеровностей.
На кромках деталей процесс выглаживания протекает следующим образом. В начальный момент выглаживания происходит пластическая деформация металла, в результате которой часть металла вспучивается перед инструментом в виде валика, а часть заваливается на краю детали, создавая наплыв на торце. Образованию наплыва способствует обратное течение металла. После выбора заданного натяга на участке 1-2 (рис. 104, д) сила выглаживания стабилизируется.
При выходе инструмента на кромку большую роль играет валик металла, перемещающийся перед инструментом. На некотором расстоянии от кромки детали часть этого валика начинает выходить на кромку, выглаживающий наконечник заглубляется больше, чем на основной поверхности. В результате перераспределения объёмов металла крайних участков на торце образуется наплыв металла. Для цветных сплавов величина наплыва 10-40 мкм, для сталей с HRC 60 – не более 5 мкм.
Рассмотрим взаимодействие поверхностей инструмента и детали при обработке. Выглаживание можно представить как процесс трения, протекающий в условиях упругопластической деформации одной из поверхностей. Так как твёрдость инструмента значительно превышает твёрдость обрабатываемой поверхности, микронеровности алмазного наконечника как бы “впрессовываются” в обрабатываемую поверхность, вызывая дополнительную пластическую деформацию приконтактных слоёв металла. При относительном приращении поверхностей характер разрушения фрикционных связей является пластическим, и для объяснения механизма взаимодействия могут быть использованы основные положения теории трения.
Во-первых, плотный контакт поверхностей и высокое давление в очаге деформации благоприятствуют проявлению сил адгезии, которые приводят к микросхватыванию поверхностей. При относительном смещении поверхностей будет происходить разрушение мостиков схватывания с одновременным образованием новых. Очевидно, разрушение мостиков схватывания происходит по обрабатываемой поверхности с налипанием частичек металла на инструмент. Однако природные и синтетические алмазы как инструментальные материалы обладают положительными физико-механическими свойствами, исключающими налипание большинства материалов обрабатываемых деталей.
Во-вторых, при взаимодействии контактирующих поверхностей происходит процарапывание обрабатываемой поверхности внедрившимися в неё микровыступами поверхности инструмента. Перемещение каждого микровыступа инструмента сопровождается пластическим оттеснением близлежащих частиц металла. Чем больше высота микронеровностей инструмента, тем глубже они внедряются в обрабатываемую поверхность.
На формирование шероховатости обрабатываемой поверхности оказывают влияние и другие факторы, например, смазка и различные промежуточные вещества, которые образуют разделительный слой, экранирующий поверхности контакта; высокая температура, обуславливающая интенсивное окисление поверхностей в зоне трения и т. д.
Решающее значение в формировании качества поверхности детали имеет шероховатость поверхности инструмента (рис. 3 или 105).
Анализируя полученные зависимости, можно отметить следующее. При выглаживании недоведенными наконечниками, имеющими шероховатость Rz=0,2÷0,4 мкм, происходит смятие неровностей исходного микропрофиля и образуется новый микрорельеф, шероховатость которого существенно меньше исходной. С увеличением шероховатости наконечника процесс сглаживания вытесняется срезанием микронеровностей образца отдельными выступами микропрофиля наконечника. При шероховатости наконечника грубее Rz=0,4 мкм процесс выглаживания почти полностью заменяется микрорезанием, что сопровождается резким возрастанием шероховатости обработанной поверхности и значительным нагревом инструмента.
При работе доведенными наконечниками, имеющими высоту
микронеровностей менее 0,2 мкм, достигается наилучшее качество обработки. Процесс выглаживания доведенными наконечниками более стабилен по сравнению с обработкой недоведенными. Коэффициенты трения зависят от наиболее существенных факторов — силы выглаживания и твердости материала обрабатываемой заготовки [21, 25*]. С увеличением силы
выглаживания до оптимального значения коэффициент трения увеличивается, а с возрастанием твердости материала обрабатываемой заготовки – уменьшается. Максимальное значение коэффициента трения не превышает значения 0,1, обычно оно составляет 0,05-0,08.
При. рассмотрении силовых и температурных долей в очаге деформации был сделан вывод [11], что температура в очаге деформации на глубине не более 0,1 мм не превышает 200— 400° С при скорости выглаживания менее 100 м/мин. При увеличении скорости выглаживания до 400—500 м/мин температура возрастает в 2—2,5 раза.
Качество поверхности, получаемое при выглаживании,
и выбор параметров выглаживания
Качество поверхности деталей характеризуется геометрическими (микрогеометрия, волнистость) и физико-механическими параметрами (микротвердость, микроструктура, напряженное состояние). Волнистость при выглаживании несколько (несущественно) уменьшается, а микрогеометрия приобретает совершенно иной характер: резко уменьшается высота микронеровностей, а сами микронеровности имеют сглаженную, округлую форму с большим радиусом скругления вершин и с большой опорной поверхностью.
Параметрами процесса, выглаживания, влияющими на шероховатость, являются сила выглаживания, подача и радиус рабочей части инструмента. Зависимость шероховатости поверхности от силы выглаживания качественно одинакова для деталей из различных материалов. При увеличении силы выглаживания шероховатость уменьшается, а для определённой её величины изменение шероховатости прекращается. Это можно объяснить тем, что при малых нагрузках инструмент контактирует с обрабатываемой поверхностью по вершинам неровностей, опорная площадь которых мала. Вследствие этого на поверхности контакта развиваются значительные давления, превышающие предел текучести материала и вызывающие интенсивную пластическую деформацию неровностей. По мере роста силы выглаживания увеличивается глубина внедрения и растёт площадь контакта инструмента с обрабатываемой поверхностью.
В процессе пластической деформации поверхностный слой металла значительно упрочняется, что увеличивает сопротивление поверхности пластической деформации, поэтому уменьшение шероховатости с увеличением давления замедляется (рис. 5).
При определённых значениях силы выглаживания исходные неровности полностью сглаживаются и образуется шероховатость, обусловленная самим процессом выглаживания (величиной подачи). Дальнейшее увеличение силы выглаживания увеличивает величину пластических искажений, высота неровностей возрастает по сравнению с наименьшей, поверхностные слои разрушаются, и появляются трещины.
Оптимальная величина силы выглаживания для деталей из:
закаленных сталей
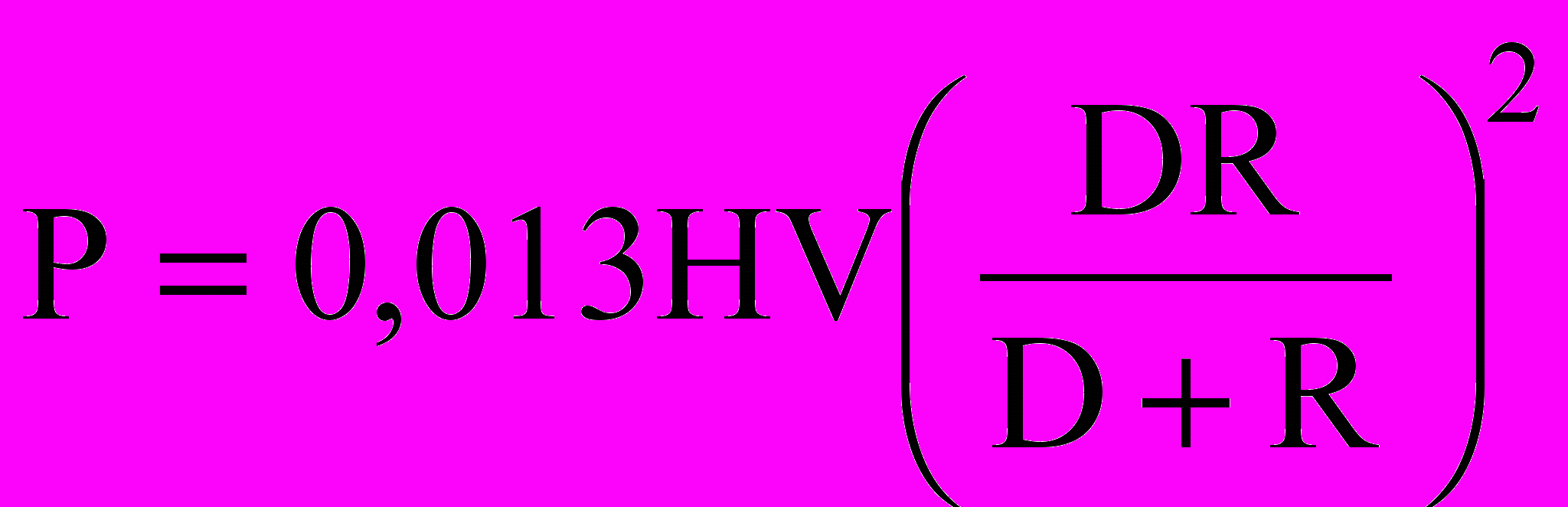
материалов невысокой и средней твердости
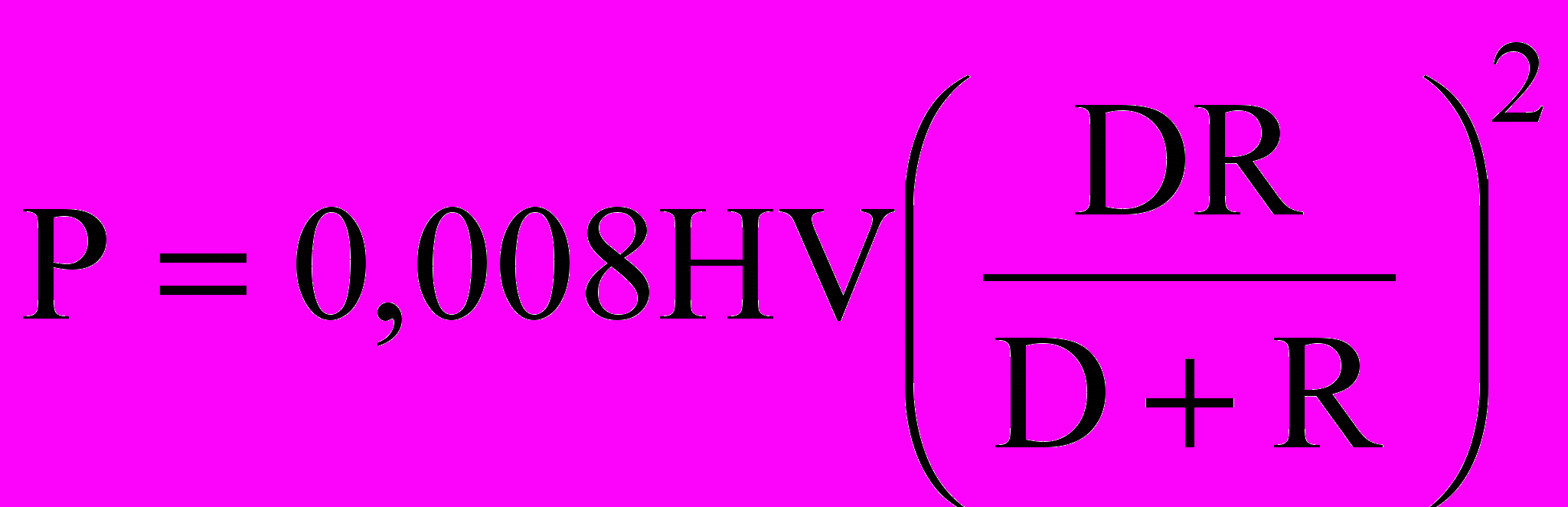
где Р - оптимальная сила .выглаживания, Н; HV – твердость обрабатываемой поверхности по Виккерсу, Н/м2107 (при измерении твердости по Бринеллю или Роквеллу эти числа твердости легко переводятся в твердость по Виккерсу по справочным таблицам); D – диаметр обрабатываемой поверхности, мм; R – радиус рабочей части алмаза, .мм.
Назначение силы выглаживания более 200—250 Н для деталёй из высокопрочных материалов и более 100—150 Н для материалов средней твердости, как правило, нецелесообразно, так как это ухудшает протекание процесса, снижает стойкость инструмента и может привести к перенаклепу поверхности.
Необходимая величина радиуса зависит от твердости обрабатываемого материала заготовки и допустимой величины силы. Основным критерием вы6opa величины радиуса является твердость материала обрабатываемой заготовки. Для деталей из мягких сталей и цветных сплавов радиус сферы инструмента должен составлять - 2,5-3 мм; для деталей из материалов средней твердости - 1,5-2,5 мм; для деталей из высокопрочных сталей (HRС
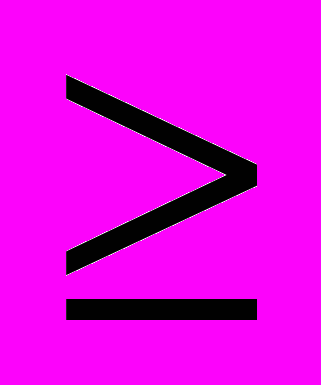
Не менее значительное влияние на качество шероховатости оказывает подача. При изменении подачи от 0,02 до 0,10 мм/об шероховатость возрастает, при этом величина остаточной пластической деформации уменьшается. Наименьшая шероховатость достигается при подаче 0,02-0,04 мм/об. При подаче ниже 0,02 мм/об шероховатость не изменяется или возрастает по сравнению с оптимальной, что можно объяснить перенаклёпом поверхностного слоя. Уменьшение исходной шероховатости при выглаживании с подачами, большими 0,08—0,10 мм/об, не существенно, поэтому процесс выглаживания становится малоэффективным (см. рис. 5, в).
Шероховатость зависит от числа рабочих ходов t выглаживающего инструмента. В основном шероховатость уменьшается во время первого рабочего хода. С увеличением числа t до двух-трёх шероховатость уменьшается, но в меньшей степени, так как повторные рабочие ходы проводятся уже по сглаженной и упрочненной поверхности. При числе t больше четырех возможен перенаклеп поверхностного слоя; шероховатость при этом несколько увеличивается, поэтому при выглаживании целесообразно назначать один рабочий ход.
Скорость выглаживания мало влияет на величину шероховатости. При изменении скорости от 16 до 120 м/мин величина шероховатости практически не изменяется. Рост скорости выглаживания от 120 до 200 м/мин приводит к небольшому увеличению шероховатости. При больших скоростях (200 м/мин и более) алмаз из-за перегрева сильно изнашивается. В этом случае необходимо обильное охлаждение зоны контакта алмаза с обрабатываемой поверхностью. На качество выглаживания существенно влияет также процесс охлаждения. Действие СОЖ проявляется в создании местных легко деформируемых зон охлаждений контактной поверхности, создании на поверхности алмаза пленки, предохраняющей от износа и уменьшающей коэффициент трения, и др. При выглаживании заготовок из черных металлов и сплавов рекомендуется применять индустриальное масло И-20А, а из цветных металлов и сплавов – керосин. Применяют также специальные составы СОЖ и поверхностно-активных веществ (ПАВ).
Шероховатость выглаженной поверхности зависит от исходной шероховатости. Заготовки из закаленных сталей эффективно выглаживать при исходной шероховатости не более Ra= 1,25 мкм. Выглаживание с оптимальными режимами при Ra = 0,08-l,25 мкм дает стабильное уменьшение шероховатости в 4—5 раз. При выглаживании заготовок из закаленных сталей с исходной шероховатостью Rа ≥1,25 мкм из-за неполного сглаживания неровностей шероховатость уменьшается только в 1,5—2 раза, т. е. применение алмазного выглаживания неэффективно. При выглаживании заготовок из незакаленных сталей, бронзы, алюминия и других аналогичных металлов установлено, что можно эффективно выглаживать поверхности с исходной шероховатостью Ra≈2,0мкм. При снижении исходной шероховатости степень ее сглаживания уменьшается. Большая степень сглаживания получается при выглаживании точёных или шлифованных поверхностей, имеющих остроконечный профиль микронеровностей. Меньшая степень сглаживания будет при выглаживании поверхностей, имеющих неровности притупленной формы, например хонингованных, полированных обкатанных роликом.
В результате алмазного выглаживания размер детали может изменяться на 3-5 микрон. Для большинства деталей это находится в пределах допуска на размер. При выглаживании более точных деталей следует учитывать изменение размера. Важнейшие характеристики микрогеометрии поверхности – относительная опорная длина профиля tp, относительная опорная часть площади tf и радиус скругления микронеровностей при алмазном выглаживании — более благоприятные, чем при других финишных методах обработки (табл. 1).
В процессе алмазного выглаживания, как и при обработке деталей другими методами ППД, в тонком поверхностном слое происходят сложные физические процессы, обусловленные пластической деформацией, нагревом. В частности, увеличивается число дефектов кристаллической решетки, происходят некоторые структурные превращения, например, для закаленных сталей - распад остаточного аустенита и превращение его в мартенсит. Вследствие этого увеличивается удельный объём деформированного металла, который стремиться расшириться, но лежащие ниже слои препятствуют этому. Так возникают сжимающие остаточные напряжения, повышающие эксплуатационные свойства деталей.
Глубина залегания сжимающих напряжений в зависимости от материала обрабатываемой заготовки и режимов выглаживания составляет 0,15—0,4 мм, величина напряжений – до 1,2 ГПа.
Пластическая деформация при алмазном выглаживании вызывает упрочнение поверхностного слоя металла: увеличиваются твердость, предел упругости и предел текучести, но уменьшается его пластичность. Упрочнение поверхностного слоя связано с изменением кристаллической структуры металла. Зерна металла дробятся, и образуется мелкозернистая структура. При этом увеличивается количество искажений кристаллической решетки — дислокаций. Дислокация препятствует перемещению отдельных частей кристаллов по плоскостям скольжения, а преодоление сопротивления дислокаций требует приложения больших напряжений, чем это необходимо в не упрочненном металле, поэтому возрастает прочность пластически деформированного металла. Величина силы выглаживания определяет степень пластической деформации и в наибольшей степени влияет на характеристики упрочнения поверхностного слоя.
Обычно максимальную микротвердость имеет непосредственно поверхность выглаженной детали. С увеличением глубины микротвердость убывает и на глубине 0,2—0,4 мм становится равной исходной. С увеличением силы выглаживания микротвердость достигает максимума при Р=160÷230Н. При чрезмерном увеличении силы выглаживания может произойти перенаклеп, что проявляется в появлении микротрещин и снижении микротвердости поверхности. Микротрещины также появляются при выглаживании с небольшими силами, но малыми подачами (менее 0,02 мм/об), и числом рабочих ходов, превышающими пять - восемь. При оптимальных режимах алмазного выглаживания вероятность разрушения поверхностного слоя исключается.
Температура при выглаживании по обычным режимам не превышает 150-300°С, причем она резко падает с увеличением глубины. На глубине 0,1-0,3 мм от поверхности температура снижается до исходной величины. Однако при выглаживании с большими силами, когда величина сил трения и выделение тепла возрастают, возможно значительное повышение температуры поверхностного слоя. При нормальных условиях выглаживания температура поверхностного слоя гораздо ниже температуры рекристаллизации и. нагрев не существенно влияет на микроструктуру поверхностного слоя.
Доминирующим фактором при алмазном выглаживании является деформационное упрочнение, однако тепловые процессы оказывают определенное влияние на формирование свойств поверхностного слоя и в основном ограничивают производительность обработки. При выглаживании на упрочняющих режимах с большими скоростями образуются термопластические деформации, которые меняют характер и уровень напряжений, образованных собственно пластической деформацией. Кроме того, контактная температура в значительной мере определяет стойкость инструмента. При среднеконтактных температурах, превышающих 400-500°С, наблюдается ухудшение качества поверхности и иногда появляются прижоги. При более высоких контактных температурах возможно ускоренное изнашивание алмаза вследствие графитизации его рабочей поверхности.
Назначение режимов выглаживания с учетом температурного фактора позволяет получить более благоприятные свойства поверхностного слоя и значительно повысить несущую способность деталей машин.
Тепловые процессы, происходящие при алмазном выглаживании, определяются трением и пластической деформацией в зоне контакта. Следовательно, упрочнение, формирование микрорельефа и нагрев поверхностного слоя зависят от температурно-силового фактора, определяемого режимами и условиями протекания процесса выглаживания.
Наибольшее влияние на температуру в зоне контакта оказывает скорость выглаживания и давление в зоне контакта. На рис. 16 показана зависимость максимальной температуры от скорости алмазного выглаживания. Уменьшение радиуса сферы действия алмаза и, следовательно, увеличение контактного давления ведет к повышению температуры.
Время действия теплового источника при алмазном выглаживании зависит от площади контакта и скорости выглаживания. При скорости = 1,67 м/с и радиусе сферы алмаза Rсф = 1,5 мм время действия теплового источника составляет τ = 0,910-3 с.
Кратковременность воздействия теплового источника и высокая скорость нагрева способствуют интенсивному нагреву тонких поверхностных слоев, которые под действием совместного температурно-силового фактора оказываются наиболее деформированными (рис. 17).
При выглаживании величина подачи находится в пределах 0,07—0,1 мм/об и ее изменение в этом диапазоне не оказывает существенного влияния на температуру деформированного слоя. Однако с уменьшением подачи до 0,03 мм/об (упрочнение закаленных деталей по упрочняющему режиму) возрастает число повторных деформаций каждой точки, нагретой при предшествующих проходах, что вызывает рост температуры. При выглаживании с большими силами, т. е. при более мощных источниках теплоты, влияние подачи на изменение контактной температуры увеличивается.
Анализ эксплуатации деталей и узлов и взаимосвязь параметров качества поверхностного слоя с работоспособностью и надёжностью изделий
Типичными видами нагружения многих деталей и узлов являются: циклические, различные виды контактного статического и объёмного нагружения в широком диапазоне температур. Требуемое качество поверхности достигается на финишных операциях ТП, поэтому окончательная обработка оказывает решающее влияние на эксплуатационные свойства деталей. Поверхностный слой имеет наибольшее число дефектов, а условия работы деталей и узлов таковы, что наиболее нагруженными являются как раз поверхностные и подповерхностные слои. Такие процессы, как концентрация напряжений, развитие микротрещин, выгорание легирующих элементов, разупрочнение, изнашивание, окисление, перераспределение остаточных напряжений, фреттинг, наиболее интенсивно происходят в поверхностных слоях, что служит основной причиной снижения работоспособности деталей.
При ППД поверхностный слой претерпевает качественные изменения: сглаживаются микронеровности, повышается твердость и прочность, образуются остаточные напряжения сжатия, которые оказывают доминирующее влияние на повышение циклической прочности деталей, сдвигая критические напряжения в область более высоких значений и замедляя процесс развития микротрещин. Кроме того, они снижают чувствительность материала к концентрации напряжений от внешней нагрузки и вблизи конструктивных и технологических концентраторов.
Износостойкость поверхности определяется:
а) высотой неровностей,
б) кривизной их вершин,
в) параметрами опорной поверхности,
г) микротвердостью,
д) пределом текучести,
е) коэффициентом трения.
Фреттинг возникает в резьбовых, прессовых, фланцевых соединениях, штуцерах, уплотнениях, муфтах и т.п. С ростом вибронагруженности деталей особенно при повышенных температурах и недостатке смазочного материала, при наличии малых осциллирующих микросмещений в сопряжениях на передний план выдвигается проблема обеспечения фреттингостойкости контактных поверхностей.
Эффективным технологическим мероприятиям для повышения фреттингостойкости поверхности является нанесение регулярных микрорельефов, что достигается лучшим сохранением смазочных материалов на контакте, удалением продуктов фреттинга во впадины рельефа и локализацией коррозионно-механических разрушений.
Контрольные вопросы к разделу
Повышение несущей способности деталей машин упрочнением и отделкой
1. Какими параметрами характеризуется качество поверхностного слоя деталей машин?
2. На какие эксплуатационные свойства оказывает влияние качество поверхностного слоя деталей машин?
3. О чем свидетельствует связь характеристик качества поверхностного слоя с эксплуатационными свойствами деталей?
4. Какими технологическими методами возможно обеспечение оптимального качества поверхностного слоя?
5. Какими технологическими методами можно повысить запасы прочности деталей, работающих при переменных нагрузках?
6. Охарактеризуйте понятие «поверхностный слой» в сравнении с основной массой детали и его служебными свойствами.
7. Какими параметрами характеризуется геометрия поверхностного слоя?
8. Какие дефекты поверхности детали, не регламентированные ГОСТом Вам известны?
9. Охарактеризуйте контакт реальных поверхностей деталей машин.
10. Как сравнивают несущую способность шероховатости поверхностей, обработанных различными методами и с Rа = var?
11. Поверхности с масляными карманами (искусственными), область применения?
12. Характеристика физико-механических свойств поверхностного слоя.
13. Причина возникновения остаточных макронапряжений и микронапряжений?
14. Классификация методов ППД.
15. Преимущество методов ППД по сравнению с другими методами.
16. Явления, происходящие в поверхностном слое при обработке ППД, механизм упрочнения.
17. Сравнительный анализ и области рационального применения различных методов ППД.