Курс лекций для студентов по специальности I 37. 02. 03 «Техническая эксплуатация погрузочно-разгрузочных, путевых, дорожно-строительных машин и оборудования»
Вид материала | Курс лекций |
- Методика выполнения расчета гидропривода путевых машин конструкции путевых машин для, 865.62kb.
- 3. Требования к минимуму содержания основной профессиональной образовательной программы, 235.18kb.
- Учебный план на 2010 2011 учебный год специальность 190605. 51 «Техническая эксплуатация, 72.92kb.
- Конспект лекций по курсу: «Техническая эксплуатация силовых агрегатов и трансмиссий», 860.12kb.
- Прием и выпуск в учебное заведение, 806.72kb.
- Программа дисциплины по кафедре «Эксплуатация автомобильного транспорта» организация, 237.05kb.
- Перечень вступительных испытаний на заочное отделение, 25.4kb.
- Методические указания и контрольные задания для студентов заочной формы обучения гоу, 2389.4kb.
- «Техническая эксплуатация оборудования в торговле и общественном питании», 1185.85kb.
- Методические указания по выполнению контрольных работ для студентов заочного отделения, 299.59kb.
11.2 Дефектация деталей
Оценка технического состояния деталей машин, поступившей в ремонт, называется дефектацией.
Эта операция влияет на качество отремонтированной машины, ее ресурс, расход запасных частей и стоимость ремонта.
Цели дефектации достаточно обширны:
- определение технического состояния детали;
- сортировка на три группы (годные для дальнейшего использования, подлежащие восстановлению, негодные)
- сортировка деталей по маршрутам восстановления;
- систематизация данных о результатах дефектации и сортировки, необходимых для совершенствования ремонтного производства.
При дефектации руководствуются техническими требованиями на дефектацию машины (или агрегата). Они составляются в виде карт, где указаны:
- общие сведения по каждой детали;
- перечень ее возможных дефектов;
- способы обнаружения дефектов;
- допустимые без ремонта размеры детали;
- рекомендуемые способы устранения дефектов.
1)Общие сведения о детали включают эскиз с указанием мест расположения возможных дефектов, основные размеры, материал и др;
2) Возможные дефекты и способы их обнаружения базируются на НИИР и опыте ремонта подобных машин;
3) Рекомендованные способы восстановления также базируются на НИИР по оптимизации процессов восстановления деталей и опыте.
Способы выявления дефектов делятся на две группы: визуальные и измерительные.
Часть дефектов можно обнаружить простым осмотром (визуально), не производя измерений или не разрушая детали. К ним относятся: видимые трещины, пробоины, коррозия, обрыв, вмятины, деформация, нарушение герметичности, уплотнение и т.д.
Измерительный контроль применяют для получения количественной оценки отклонения параметров формы и относительного положения поверхностей детали, скрытых дефектов и физических (физико-механических) свойств материала деталей.
Контроль состояния деталей выполняют в порядке сложности дефектов и трудности их обнаружения и устранения.
- Сначала визуально определяют наличие крупных трещин, деформаций, изломов, коррозии, пробоин. Если обнаружены неустранимые дефекты, деталь непригодна.
- Далее пригодную (на первом этапе) деталь проверяют на наличие нарушения взаимного расположения рабочих поверхностей и существенного (недопустимого) изменения физико-механических свойств материала детали. Если обнаружен неустранимый дефект, деталь бракуется.
- Далее пригодную (уже на этом этапе) деталь контролируют на наличие скрытых дефектов.
- Если эти дефекты не обнаружены, то приступают к определению износа и геометрических форм рабочих поверхностей детали.
Для выявления дефектов используют различные методы и средства, которые зависят от параметров и формы проявления дефектов, а также конструктивных особенностей детали.
Например: радиаторы и баки, трубопроводы испытывают сжатым воздухом, затем их погружают в воду.
Блоки цилиндров испытывают на стендах (закачивают воду под давлением 0,3…0,4 МПа) и выявляют подтеки воды.
Для выявления скрытых дефектов на поверхности и в объёме детали используют различные методы. Для обнаружения скрытых поверхностных дефектов (трещин, волосовин, пористости) используют капиллярный, магнитный, ультразвуковой, люминесцентный, рентгеновский методы.
Капиллярный метод – специальная проникающая жидкость проникает в невидимую глазом трещину. После очистки поверхности и нанесения проявляющего вещества дефект обнаруживается визуально по следу жидкости. Жидкость – керосин, вещество – мел (трещины шириной не менее 20 мкм).
Метод магнитной порошковой дефектоскопии – нанесение на поверхность ферромагнетика, ферромагнитный порошок концентрируется по краям трещины, обозначая ее расположение.
Порошок наносят в виде суспензии в керосине, солярке, мыльной воде. Намагничивание детали осуществляют электрополем (постоянного или переменного тока) большой силы.
Намагничивание:
- циркулярное – ток через деталь или через стержень внутри полой детали (гильзы, цилиндры);
- полюсовое – полем соленоида или электромагнита.
Серийно выпускают магнитные дефектоскопы МЭД – 2 (диаметром < 90 мм и длиной < 900 мм) и УМД – 900 – для более крупных деталей.
Ультразвуковой метод (акустический) используют для анализа дефектов в объёме. Контроль дефектов (трещин, раковин, шлаковых включений) осуществляют путём распространения в металле ультразвуковых колебаний (частотой более
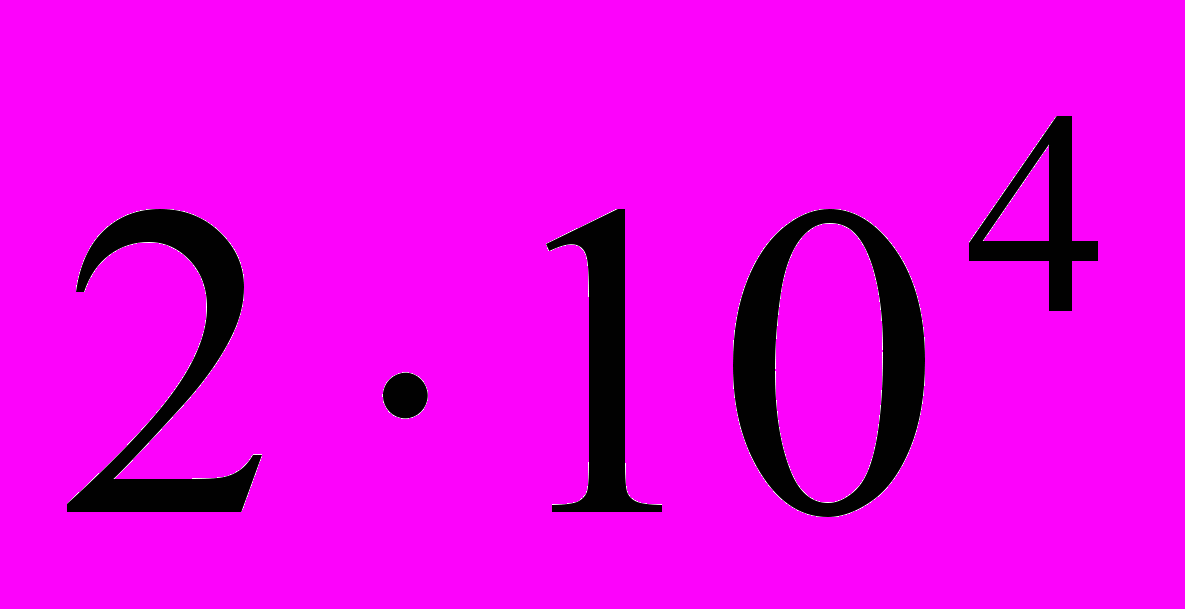
Теневой метод (просвечивание) – деталь помещают между излучателем и приемником.
Импульсный метод – отражение ультразвуковых волн от дефектов.
Люминесцентный метод – свечение неметаллических материалов и цветных металлов в ультрафиолетовых лучах.
Как отмечалось, после определения технического состояния деталей на участке контроля их сортируют.
Детали, которые будут восстанавливать, сортируют:
– по дефектам;
– по маршрутам.
Сортировка по дефектам базируется на однородности дефектов.
Сортировка по маршрутам основывается на однотипности (однородности) технологии восстановления деталей, имеющих комплекс дефектов.
Например: при восстановлении деталей типа вал оказываются дефектными:
Гладкие поверхности – 50 %;
Шлицевые и гладкие поверхности со шпоночными канавками – 23 %;
Зубчатые поверхности – 5 %;
Резьбовые и прочие поверхности – 22 %.
Это позволяет в условиях серийного ремонтного производства разработать маршрутную технологию восстановления деталей машин (профессора К. Т. Кошкина).
Состав операций определяется по сочетанию дефектов деталей.
11.3 Типичные дефекты деталей, подлежащих восстановлению
Типизация дефектов деталей, которые подлежат восстановлению, позволяет увеличить серийность технологических операций восстановления.
Мы уже отмечали, при дефектации деталей их сортируют по дефектам или по маршрутам.
Но прежде чем разрабатывать проект технологического процесса восстановления деталей, следует классифицировать дефекты, определить их параметры, сходство и повторяемость, разделить по сходным признакам на типы.
Следует отметить, что типизация дефектов и неисправностей деталей позволяет обнаруживать ненадежные элементы деталей, повысить долговечность и ремонтопригодность машин. Следует отметить понятия: дефект, неисправность и отказ. По ГОСТ 15467 – 79:
Дефект – это каждое отдельное несоответствие изделия (детали) требованиям, установленным нормативной документацией.
Примеры: выход размера детали за пределы допуска, недопустимое изменение формы поверхности, нарушение целостности тела детали.
Неисправность – это состояние объекта (детали), при котором он не соответствует хотя бы одному из требований установленных нормативно-технической документацией.
Находясь в неисправном состоянии, деталь может иметь один или несколько дефектов. При этом при наличии дефекта деталь либо восстанавливается, либо направляется в утиль.
Отказ – это понятие надежности.
Дефекты классифицируют по нескольким признакам. Во-первых, дефекты подразделяют по причинам их появления:
- ошибки конструирования;
- ошибки изготовления;
- старение и износ;
- нарушение правил эксплуатации.
Во-вторых, дефекты подразделяют по форме их проявления в виде изменений:
- линейных и объемных размеров форм поверхностей;
- относительного положения поверхностей;
- посадок и сопряжений;
- свойств материала поверхностных слоев детали;
- целостности тела детали;
- функциональных свойств материала;
- внешнего вида.
Однако для разработки технологии восстановления мало выявить формы проявления дефектов, необходимо также установить виды и количественные параметры дефектных элементов деталей.
11.3.1 Виды изнашивающихся и повреждаемых элементов деталей
Как правило, восстановление дефектной детали (на конечном этапе восстановления) сводится к обработке поверхностей на металлорежущих станках. Поэтому дефектные поверхности разных деталей группируют сначала по конструктивно-технологическим признакам, затем по видам.
Это делается для определения операционного маршрута восстановления за счет комбинации технологических операций восстановления типовых поверхностей.
Типовая поверхность – это поверхность, конструктивно-технологические характеристики и параметры дефекта которой присущи поверхностям множества различных деталей.
То есть цель типизации – установление конструктивно-технологической общности и сходства параметров дефектов поверхностей детали. Итак, по конструктивно-технологическому признаку поверхности восстанавливаемых деталей разделяют на:
- наружные поверхности, имеющие форму тел вращения (шейки, ступицы, опоры валов и осей);
- внутренние поверхности, имеющие форму тел вращения;
- поверхности других форм (эллиптические, зубчатые, плоские, поверхности со шпоночными и шлицевыми канавками, резьбой и т.д.).
Общим признаком всех трех типов поверхностей являются одинаковые требования к их обработке. Поэтому в типовой маршрут восстановления деталей включают и детали, имеющие одновременно дефекты всех трех типов поверхностей.
Для оценки необходимости включения восстановления дефектной детали в типовой маршрут используют следующие показатели поверхности:
L – длина поверхности;
T – точность обработки;
i – вид причины перехода поверхности в непригодное состояние;
δ – линейные изменения формы поверхности;
D – диаметр;
R – вид резьбы;
K – конусность;
H – твердость;
σ – материал.
Итак, в этом списке L, T, D, R, H, σ – это характеристики детали (точнее ее поверхностей); i, δ, K – это дефекты.
Пользуясь показателями характеристик поверхности и ее дефектов, составляют комплексную поверхность, для которой разрабатывают технологические операции восстановления. Итак, этот этап – типизация поверхностей по дефектам и технологическим процессам их восстановления – первый уровень специализации.
Второй уровень – это типизация технологических процессов восстановления однородных (однотипных) деталей. Для этого выбирают комплексную деталь, охватывающую параметры всех деталей, включенных в заданную группу. Как и при изготовлении новых деталей, комплексная деталь может не совпадать по параметрам с реальными деталями (точно), но разработанный для нее технологический процесс восстановления должен быть пригодным для ремонта любой детали, включенной в данную группу.
Эти два уровня отражены в различных вариантах восстановления деталей. Первый вариант – восстановление по дефектной технологии, т.е. разрабатывается технологический процесс восстановления на каждый дефект детали. Второй (более эффективный) вариант – восстановление по маршрутной технологии, т.е. разрабатывается технологический процесс восстановления на все возможные дефекты детали.
Формирование технологического маршрута включает выполнение нескольких, последовательно выполняемых этапов.
Во-первых, массив дефектных деталей разбивают на классы в соответствии с их геометрической конфигурацией.
Во-вторых, в рамках каждого класса детали разделяют на группы по следующим признакам:
- габаритные размеры;
- количество (частота) дефектов;
- связь между дефектами различных поверхностей деталей;
- тип поверхностей, подлежащих восстановлению;
- вид сопряжений и их точность;
- возможные методы восстановления деталей;
- серийность деталей.
В-третьих, в каждой группе выбирается комплексная деталь.
В-четвертых, разработка для каждой комплексной детали маршрута или маршрутов группового технологического процесса восстановления.
В-пятых, оценка экономической эффективности различных маршрутов и выбор наиболее экономичного маршрута.
В-шестых, составление маршрутно-операционных карт технологических процессов восстановления деталей и их использование на местах (на постах дефектации и в цехах по восстановлению деталей).
12 Восстановление деталей. Классификация основных методов
Изготовление новых деталей, а также восстановление изношенных и поврежденных составляет значительную часть расходов ресурсов при ремонте машин. Так даже на специализированных заводах они доходят до 50 % стоимости и 40 % трудоемкости ремонта машин.
Поэтому сокращение расходов – важная задача, одним из путей ее решения является восстановление дефектных деталей. Как уже отмечалось, типичные дефекты деталей и сборочных единиц:
- нарушение посадки между сопряженными поверхностями;
- нарушение размеров, геометрической формы и относительного положения в пространстве поверхностей деталей;
- ухудшение свойств материала;
- ухудшение внешнего вида.
Задача восстановления дефектных сопряжений и деталей состоит в возврате утраченных свойств: посадки, формы, относительного положения в пространстве поверхностей, свойств материала и внешнего вида детали.
Восстановить посадку между сопряженными поверхностями деталей можно следующими методами:
- обработкой изношенной поверхности одной детали и заменой сопряженной детали (способ ремонтных размеров);
- применение дополнительной ремонтной детали (компенсатора износа);
- восстановлением первоначальных размеров сопряженных поверхностей деталей.
Восстановить деталь или ее отдельные поверхности можно следующими методами:
- наращиванием на дефектную поверхность детали другого материала;
- перемещением посредством пластической деформации материала детали с одного участка к другому (изношенному);
- восстановлением целостности тела детали;
- снятием (удалением) материала с поверхности детали;
- восстановлением относительного положения поверхностей детали в пространстве.
- Способ наращивания материалов на изношенные поверхности деталей осуществляют наплавкой металлических и полимерных материалов, напылением, электролитическим и химическим осаждением и др.
- Способ пластических деформаций осуществляют осадкой, раздачей, обжатием, вытяжкой и накаткой;
- Способы восстановления целостности тела детали включают сварку, пайку и склеивание;
- Способы удаления материала с поверхности детали включают обточку, шлифование и фрезерование;
- Способы восстановления относительного положения поверхностей деталей в пространстве включают статическое нагружение, чеканку, местный нагрев.
13 Способы восстановления посадки между сопряженными
поверхностями деталей
I) Как отмечалось, наиболее распространен способ ремонтных размеров, по которому восстанавливают посадку путем механической обработки наиболее сложной детали и замены сопряженной с ней детали новой.
Размеры обрабатываемой детали регламентируются системой ремонтных размеров. Это делается для того, чтобы иметь достаточное число запасных частей, а также технологическую оснастку. Ремонтные размеры для каждого сопряжения, а также их количество рассчитывают на основе величин ремонтного интервала и предельной толщины слоя металла, который может быть снят с детали при сохранении достаточной работоспособности.
Ремонтный интервал (γ) – это сумма величин уменьшения тела детали в результате изнашивания и обработки. Обработку выполняют для восстановления ее геометрической формы и положения в пространстве, а также обеспечения необходимой шероховатости поверхности.
Пример: Максимальная толщина слоя (рисунок 13.1), который можно снять (в процессе изнашивания и обработки) определяется условиями прочности или износостойкости (если поверхность упрочнена на ограниченную глубину).
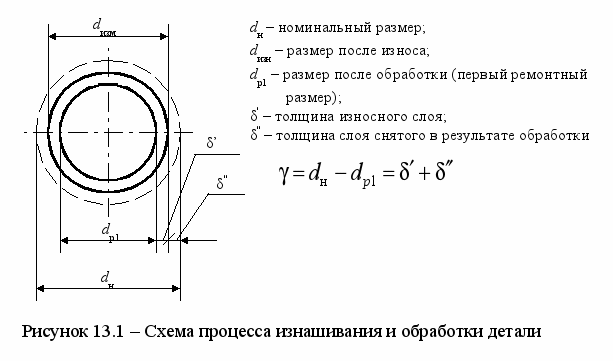
Для валов в большинстве случаев допускают уменьшение диаметра шейки до 5 % их номинального размера (исходя из условия прочности). Дальнейшее уменьшение диаметра шейки разрешают только при наличии расчета доказывающего допустимость намечаемого уменьшения.
Количество ремонтных размеров определяют по следующим формулам:
- Для охватывающей детали
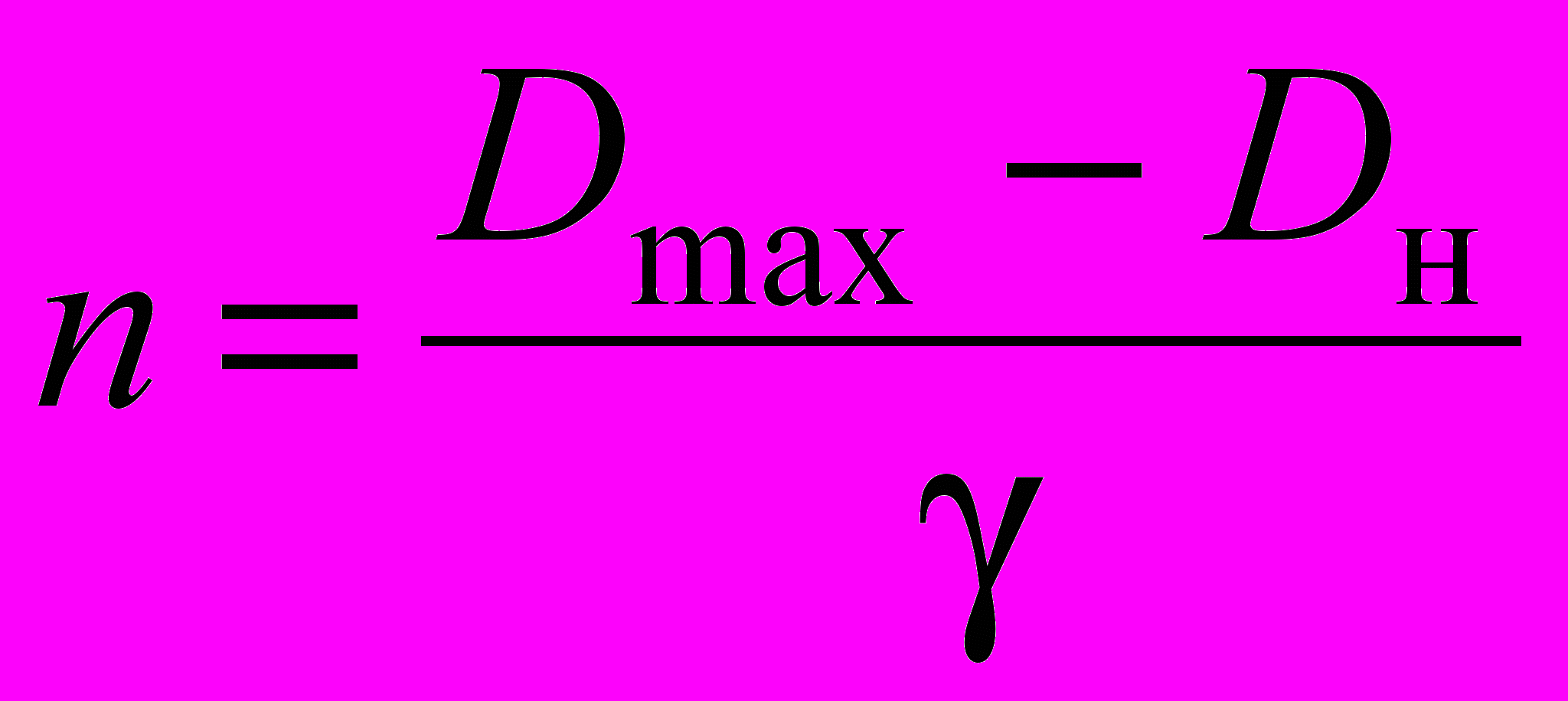
- Для охватываемой детали
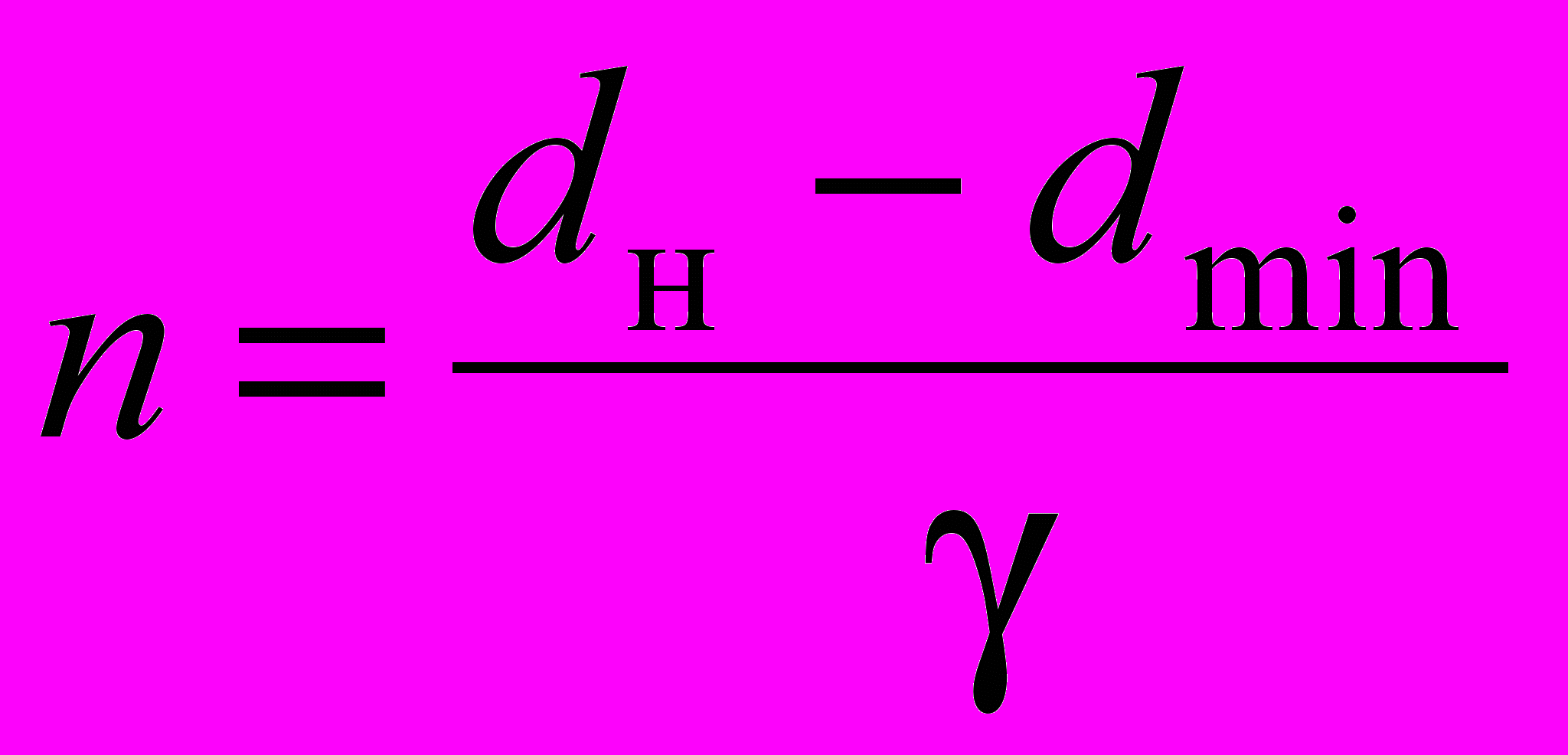
где Dmax, dmin – предельно допустимые размеры, соответственно охваты-
вающей и охватываемой детали;
Dн, dн – их номинальные размеры;
γ – ремонтный интервал.
Этот способ простой и надежный.
Недостатки: усложнение производства; удорожание ремонта из-за выбраковки одной из деталей, необходимость увеличения запасов сменных деталей и, соответственно, снижение оборачиваемости оборотных средств.
Кроме этого, эксплуатационные недостатки – ухудшение работы сочленений при большом изменении размеров (изменение скорости относительного перемещения, давления, инерционных нагрузок), что вызывает ускоренный износ.
При отсутствии регламентаций на ремонтные размеры деталь обрабатывается до устранения дефекта, а заменяемая деталь изготавливается с подгонкой к основной детали.
II) Способ постановки дополнительной ремонтной детали (рисунок 13.2) состоит в том, что в сопряжение для компенсации износа вводят дополнительную деталь (компенсатор износа).
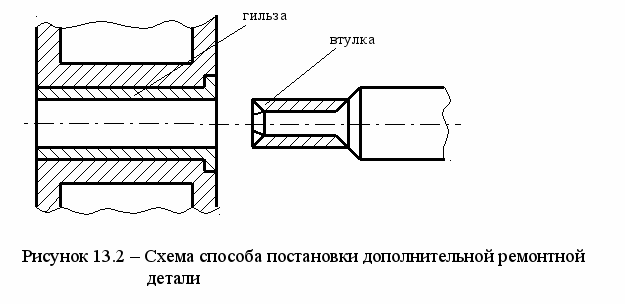
Надежность ее соединения с основной деталью достигается посадкой с гарантированным натягом, сваркой, с помощью винтов и штифтов, но снижается жесткость сопряжения, повышается теплонапряженность, что ускоряет износ. Наиболее эффективным является восстановление посадок сопряженных поверхностей с одновременным восстановлением первоначальных размеров деталей.
14 Методы восстановления деталей основанные на пластическом
деформировании материала
Централизованный ремонт деталей машин в ряде отраслей народного хозяйства стал эффективным путем удовлетворения потребности в запасных частях. Ремонтируемая деталь является удобной заготовкой , поскольку требует новых материальных и трудовых затрат. Ее размеры в максимальной степени соответствуют окончательным размерам, поэтому восстановление связано с минимальным объемом механической обработки. При этом количество повреждений поверхностей, как правило, невелико, а восстановительные работы имеют небольшой объем. Поэтому стоимость отремонтированных деталей даже в условиях несовершенного ремонтного производства оказывается в несколько раз ниже, чем стоимость новых. Применение эффективных методов упрочнения при ремонте позволяет повышать ресурсы деталей в сравнении с ресурсами новых деталей. Все это определяет высокую эффективность правильно организованного восстановительного ремонта. При огромном парке машин он обеспечивает крупную экономию материалов, энергии и трудозатрат.
В машиностроении возможности централизованного ремонта деталей машин используют в ограниченных объемах, что связано с рядом причин: децентрализацией ремонта, выполнением его силами каждого отдельного предприятия, большими возможностями изготовления запасных частей в собственных ремонтных и основных производственных цехах. Малая потребность в деталях одного наименования в этих условиях делает восстановление их не всегда выгодным.
В строительстве, на транспорте и в ряде отраслей промышленности, где централизация ремонта машин достигла больших масштабов, ремонтная техника получила значительное развитие и располагает обширным арсеналом способов восстановления деталей.
14.1 Ремонт обработкой давлением
Ремонт обработкой давлением основан на пластическом деформировании материала, перераспределении его и благоприятном изменении формы и размеров детали без изменения ее массы. Применяют следующие виды обработки давлением (рисунок 14.1): осадку, вдавливание, раздачу, обжатие, вытяжку, правку, накатку, обкатку роликом, дробеструйный наклеп и чеканку.
При осадке деталь деформируют в направлении, перпендикулярном усилию. Осадкой восстанавливают бронзовые втулки с износом по наружному и внутреннему диаметрам. При деформировании в холодном состоянии их высоту можно уменьшить до 15 %. Для сохранения отверстий во втулке их при осадке заполняют вставками. Диаметр пальца должен быть меньше, чем у отверстия втулки с учетом припуска на обработку.
При восстановлении детали вдавливанием направления усилия и деформации также взаимно перпендикулярны, но преобладает местная деформация детали и ее общие размеры не меняются столь значительно, как при осадке. Вдавливанием восстанавливают изношенные боковые поверхности шлице на валах, зубья шестерен и др. Восстановление стальных деталей проводят с нагревом и без него.
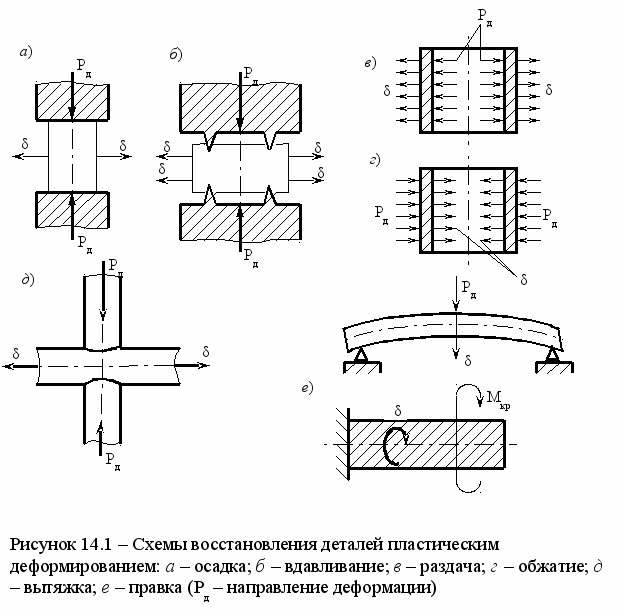
Восстановление раздачей применяют для увеличения наружного диаметра полых цилиндрических деталей без изменения высоты. Раздачу проводят под постоянный размер шариком или пуансоном или под любой размер – развальцовкой отверстия.
Обжатие применяют при решении задачи, обратной раздаче. Обжатие проводят проталкиванием детали через матрицу меньшего диаметра или деформированием металла в зоне отверстия. Стальные детали перед этим нагревают до температуры 800 – 950о С. Обжатием восстанавливают втулки, зубчатые муфты с внутренними изношенными зубьями, звенья гусениц, рычаги, шатуны и др.
Вытяжку применяют для увеличения длины детали путем местного уменьшения ее поперечного сечения. Вытяжку применяют для удлинения стержневых элементов (тяг) на небольшую длину.
Восстановление правкой обеспечивает исправление искривленных, скрученных и покоробленных деталей. Правкой восстанавливают валы, шатуны, рычаги, вилки, кронштейны, элементы металлоконструкций. При небольшой деформации (до 1,5 – 2 мм) правку проводят в холодном состоянии, а при большой – в нагретом. В обоих случаях после правки нужна термообработка детали для стабилизации правки, снятия остаточных напряжений и улучшения механических свойств материала. Правку выполняют на прессах, в специальных приспособлениях и вручную.
Накаткой восстанавливают шейки валов с нарушенными размерами в месте посадки. Ее проводят острозубчатым роликом, создающим рифления с вытеснением металла и увеличением диаметра вала в месте накатки. Нужный размер обеспечивают механической обработкой.
14.2 Восстановление деталей слесарно-механической обработкой
Восстановление деталей слесарно-механической обработкой включает следующие разновидности: опиловку, шабрение, притирку, постановку заплат, штифтование и склеивание. Опиловка, шабрение и притирка – составные части пригоночных работ, выполняемых для получения необходимой точности в сопряжениях. Постановку заплат и штифтование применяют при заделке пробоин, трещин и других повреждений, если нельзя применять сварку или пайку. Наложением заплат ремонтируют стенки картеров, корпусов и других емкостей. Штифтование состоит в последовательном ввинчивании медных штифтов диаметром 4 – 6 мм в отверстия с резьбой на месте короткой трещины. Склеивание применяют при ремонте треснувших и поломанных деталей из металла и пластмасс. С помощью карбинольного клея склеивают и герметизируют шланги, бензо- и газопроводы, приклеивают тормозные накладки к колодкам и др. Для заделки пробоин и трещин применяют эпоксидные клеевые составы, для заделки раковин в чугунных деталях – бакелитовую мастику. Склеиваемые поверхности нужно тщательно обезжиривать.