Курс лекций для студентов по специальности I 37. 02. 03 «Техническая эксплуатация погрузочно-разгрузочных, путевых, дорожно-строительных машин и оборудования»
Вид материала | Курс лекций |
- Методика выполнения расчета гидропривода путевых машин конструкции путевых машин для, 865.62kb.
- 3. Требования к минимуму содержания основной профессиональной образовательной программы, 235.18kb.
- Учебный план на 2010 2011 учебный год специальность 190605. 51 «Техническая эксплуатация, 72.92kb.
- Конспект лекций по курсу: «Техническая эксплуатация силовых агрегатов и трансмиссий», 860.12kb.
- Прием и выпуск в учебное заведение, 806.72kb.
- Программа дисциплины по кафедре «Эксплуатация автомобильного транспорта» организация, 237.05kb.
- Перечень вступительных испытаний на заочное отделение, 25.4kb.
- Методические указания и контрольные задания для студентов заочной формы обучения гоу, 2389.4kb.
- «Техническая эксплуатация оборудования в торговле и общественном питании», 1185.85kb.
- Методические указания по выполнению контрольных работ для студентов заочного отделения, 299.59kb.
10 Методы снижения надежности в деталях и конструкции машины
Как уже отмечалось, различные виды внешних нагрузок (постоянные, переменные, циклические) вызывают в деталях, элементах и конструкциях машины напряжения, которые существенно влияют на их работоспособность (вплоть до разрушения).
Различают так называемые номинальные напряжения, оказывающие влияние на всю деталь или конструкцию, и местные напряжения, возникающие в зонах соединения деталей и в местах контакта сопряженных деталей. Местные напряжения обусловлены локальными причинами, включая концентрацию нагрузок в отдельных зонах деталей и сопряжений (в частности в зоне резкого изменения формы детали, в прессовой посадке), а также неоднородность структуры материала детали и др.
Соответственно различают и методы снижения внутренних напряжений, которые затрагивают целиком элемент конструкции или же отдельную локальную зону элемента или детали.
Кинетика накопления усталостных напряжений, приводящих, в конечном счете, к отказу, зависит как от величины, так и от равномерности распределения нагрузок. Из всех основных видов нагружения, действующих при различных видах внешних нагрузок на рабочие органы и узлы машины (растяжение, сжатие, сдвиг, изгиб, кручение), наибольшую неравномерность распределения номинальных внутренних напряжений (как по длине, так и по сечению детали) вызывают изгиб и кручение (рисунок 10.1).
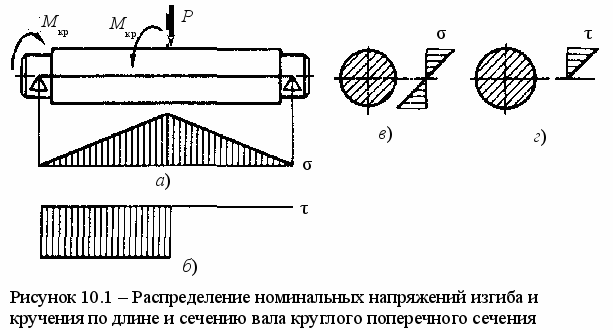
В настоящее время разработано и используется на практике ряд методов снижения или выравнивания номинальных внутренних напряжений, обусловленных стационарно действующими внешними нагрузками, к которым относятся:
1) замена элементов конструкций, работающих на изгиб, элементами, работающими на растяжение или сжатие; Это достигается применением предварительно напряженных элементов, например (рисунок 10.2), шпренгельных и предварительно напряженных балок, колонн с растяжками и др.;
2) оптимизация формы опасных сечений элементов, работающих на растяжение или сжатие; Это достигается за счет подбора сечения элементов с учетом показателя Wx/Q (в таблице 10.1 представлены величины этого показателя для различных форм сечения стандартных профилей, которые различаются между собой по эффективности использования при изгибе на порядок);
3) уменьшение внешней нагрузки за счет ее распределения на несколько элементов или за счет увеличения площади опасного сечения элемента; например, использование косозубого зацепления вместо прямозубого в зубчатых передачах, применение шлицевых соединений вместо шпоночных и др.;

3) уменьшение внешней нагрузки за счет ее распределения на несколько элементов или за счет увеличения площади опасного сечения элемента; например, использование косозубого зацепления вместо прямозубого в зубчатых передачах, применение шлицевых соединений вместо шпоночных и др.;
4) создание в элементах начальных напряжений обратного знака, компенсирующих напряжения от внешней нагрузки, например, создание в детали напряжений сжатия (при ее изготовлении) для эксплуатации в условиях растяжения;
5) обеспечение равнопрочности элементов по всей длине за счет подбора их формы, например, применение балок равного сопротивления с переменной высотой или с переменной шириной.
Таблица 10.1 – Сравнение различных форм сечений по показателю Wx/Q
Вид сечения | Wx | Q | Wx/Q |
Круг диаметром 60 мм Квадрат 52×52 Уголок равнобокий № 12,5 (125×125×12) Уголок неравнобокий № 18/11 (180×110×10) Двутавр № 20 а Швеллер № 22 а Двутавр широкополочный №24 Б Швеллер облегченный №30 Двутавр облегченный № 30 | 21,6 24,8 47,2 78,6 203 212 233 204 215 | 22,19 22,05 22,7 22,2 22,7 22,6 22,1 17,6 18,2 | 0,97 1,13 2,08 3,54 8,96 9,37 10,50 11,60 11,80 |
Местные напряжения также могут стать причиной разрушения деталей и элементов конструкций машины, поскольку усталостные трещины возникают и накапливаются именно в местах концентрации напряжений. Причины концентрации местных напряжений могут быть самыми различными, в том числе неоднородность материала детали, резкое изменение формы, концентрация нагрузки в локальной зоне и др.
Наиболее опасными местами деталей и сопряжений являются впадины зубьев и резьб, галтелей, шпоночных пазов, шлицев, поверхностей с острыми углами и др. Кроме того, опасными являются граничные зоны деталей в прессовых посадках, что связано с деформациями деталей в местах посадки и напряжениями растяжения и сжатия в этих зонах.
Концентрация нагрузки, вызывающая местные напряжения, связана, как правило, с технологическими дефектами, возникающими при изготовлении детали, и эксплуатационными причинами (упругие деформации и переносы при нагружении, неравномерное изнашивание сопряженных поверхностей и др.). В частности, при сжатии концентрация нагрузки имеет место в местах зацепления зубчатых передач различного типа, в местах контакта различных опорных элементов с основой (колес, роликов, катков и др.), в подшипниках качения и др. При растяжении она возникает в различных соединениях (сварных, заклепочных, резьбовых). При изгибе она, как правило, обусловлена деформацией деталей и наблюдается в зацеплениях зубчатых колес при их износах, а также в зонах контакта деформированных элементов (валов, валиков и др.) с сопрягаемыми деталями.
Как уже отмечалось, причиной концентрации местных напряжений могут быть неоднородности состава и структуры материала деталей, что особенно характерно для сварных соединений. Здесь концентраторами местных напряжений могут быть как дефекты сварки и неоднородность состава за счет выгорания легирующих добавок в зоне шва, так и структурные изменения в металле околошовной зоны, в частности на границе закаленной и незакаленной областей сварных соединений.
Для снижения местных напряжений используют ряд методов, к которым можно отнести следующие:
- замене элементов, являющихся концентраторами напряжений;
- изменение формы деталей за счет оптимизации конфигурации опасных сечений;
- устранение острых углов в деталях и конструкциях (в частности, за счет скругления впадин зубьев в зубчатых и других передачах;
- устранение резких переходов и изменение конфигурации переходных зон в деталях:
а) за счет сближения размеров различных элементов деталей;
б) за счет увеличения размеров галтелей;
5) смещения места концентрации нагрузки из зоны опасного сечения детали в другую зону.
11 Повышение надёжности и долговечности деталей машин
при их эксплуатации
Надежность, заложенная на стадии проектирования и изготовления, должна обеспечиваться и в период эксплуатации машин. В процессе эксплуатации нарушается взаимосвязь между отдельными деталями вследствие их износа, нарушаются первоначальные посадки и зазоры в сопряжениях, ослабляются крепления деталей в сборочных единицах и агрегатах. Все это приводит к увеличению динамических нагрузок и ухудшению условий смазки, росту скорости изнашивания, снижению эксплуатационных показателей машины и, наконец, к полному отказу машины.
Как отмечалось, к деталям рабочих органов ДСМ, подверженных интенсивному абразивному износу (т.е. механическому изнашиванию) относятся:
– зубья и передние стенки ковшей одноковшовых экскаваторов;
– детали ходовых частей машин;
– дробящие плиты дробильных машин и другие части ДСМ, имеющие непосредственное соприкосновение (контакт) с разрабатываемым грунтом или обрабатываемыми (перерабатываемыми) материалами.
Например, в суглинистых грунтах средний износ крайних ножей по ширине у мощных бульдозеров достигает 50 мм за 20 часов работы (при скорости изнашивания до 260 мкм/ч). Установлено, что при износе ножа уже на 15 мм общее сопротивление грунта резания увеличивается на 50 %, т.е. растет время на выполнение рабочих операций, падает производительность и увеличивается энергоемкость резания.
Изношенные зубья заменяют на новые или же восстанавливают износостойкой наплавкой или наваркой с последующей наплавкой.
Износ рабочих органов ДСМ связан с абразивностью грунтов, которая растет с увеличением содержания частиц SiO2, их размеров и закрепленности. Так в талом и мерзлом грунте износ деталей растет в 2 раза с уменьшением содержания глинистых частиц. С ростом плотности грунтов износ увеличивается в 5 раз (при малом содержании глинистых частиц). С уменьшением влажности (ниже 20 %) увеличивается абразивность глинистых грунтов. Наиболее высока абразивность мерзлых грунтов. Кроме того, абразивному изнашиванию подвержены и многие детали машин, образующие пары трения, в том числе подшипники, оси и валы, опорные катки, зубчатые передачи, а также другие сборочные единицы и сопряжения, плохо защищенные от пылевидного абразива (песок и т.д.). Наиболее интенсивно изнашиваются шейки валов в местах подвижного соединения с подшипниками. Износ шейки вала составляет
I = 0,02 – 0,2 мм для подшипников качения;
I = 0,15 –2,0 мм для подшипники скольжения.
В состав пыли входят двуокись кремния SiO2 – 65…95 %; окись железа Fe2O3 – 5…30 %; остальное соединения кальция, магния, натрия. Она же загрязняет масла. К моменту их замены содержание абразивных частиц в маслах достигает 3…5 масс. %.
В строительных машинах часто разрушаются металлоконструкции рам, стрел, рукоятей, ковшей, отвалов и др. Наиболее частой причиной разрушения сварных швов с последующим распространением трещин на основной металл являются внутренние напряжения или дефекты самого шва.
Практически любое сопряжение в процессе эксплуатации теряет свои первоначальные (исходные) показатели, в том числе крепежные соединения, шлицевые и шпоночные соединения, муфты, силовые передаточные механизмы (зубчатые передачи, червячные передачи, цепные передачи, ременные передачи), муфты сцепления, дисковые, конические и ленточные муфты, бортовые фрикционы, ходовое устройство, грузовые гибкие элементы и т.д.).
С учетом всего перечисленного очень важно поддерживать в период эксплуатации запланированный уровень надежности. Такая задача может быть выполнена при соответствующей организации системы технического обслуживания и ремонта. Эта система включает совокупность средств, объектов обслуживания и исполнителей, обеспечивающих заданные показатели надежности машин при минимальных затратах. В общем случае в состав работ по поддержанию машин в работоспособном состоянии входят: техническое обслуживание; технические осмотры; текущий ремонт; капитальный ремонт.
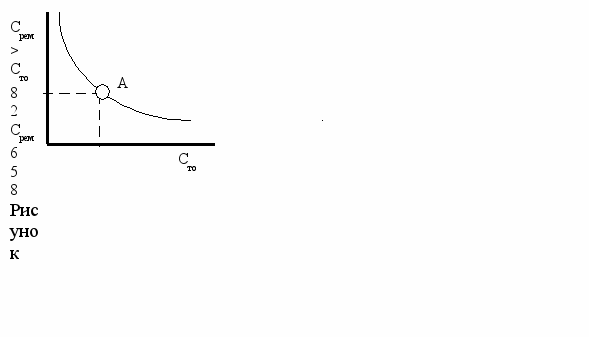
Рисунок 11.1 – Зависимость стоимости техобслуживания от стоимости
ремонта машин
Существует функциональная зависимость (рисунок 11.1) между стоимостью технического обслуживания и осмотров и стоимостью ремонтов и убытков от простоев (при высоком уровне организации снабжения запасными частями и резервирования).
На практике наблюдается тенденция увеличения затрат на техническое обслуживание и простои. Их целесообразно увеличивать до размеров, соизмеримых с затратами на ремонт (т.е. точка А): Сто ≈ Срем.
11.1 Ремонт машин. Классификация и основные положения
Любая машина в процессе эксплуатации утрачивает свои функциональные свойства и качественные показатели. Поэтому бессмысленно пытаться достичь абсолютной надёжности её элементов (и машины в целом). Гораздо более экономичным является принцип оптимальной надёжности.
Принцип оптимальной надёжности достигается нужным сочетанием однократного (разового) резервирования материальной структуры машины и периодического восстановления стареющих структурных элементов машины (т.е. ее ремонтом). Как известно, ремонт осуществляется при одновременном функционировании машины. Он включает операции по замене и восстановлению отказавших или пришедших в предельное состояние элементов машины. Поэтому ремонт можно рассматривать как особый вид динамического резервирования без изменения материальной структуры машины.
Одноразовое резервирование (т.е. обеспечение заданной надёжности машины путём подбора необходимых элементов, обладающих необходимыми величинами надёжности) материальной структуры осуществляется на стадиях проектирования и изготовления машины.
Как уже отмечалось, на стадии эксплуатации обеспечение заданной надёжности машин осуществляется за счёт ряда мероприятий, связанных с поддержанием и восстановлением работоспособности машин за счёт выполнения работ по техническому обслуживанию и ремонту машин.
Напомню, что (ГОСТ 18322 – 76) под термином Техническое Обслуживание имеется в виду комплекс работ для поддержания исправности или только работоспособности машины.
Ремонтом называют комплекс работ для поддержания и восстановления исправности или работоспособности машин.
Ремонт можно выполнять для:
- поддержания исправности (работоспособности) – такой ремонт является составной частью Технического Обслуживания и называется текущим;
- восстановление исправности (работоспособности) и поддержание ресурса машины – такой ремонт называют капитальным.
В первом случае Техническое Обслуживание и ремонт являются составными частями единой системы поддержания и восстановления работоспособности машин. Основные принципы этой системы – плановость и предупредительность, т.е. все мероприятия, планируются заранее, в том числе и ремонт. Понятие ремонта многогранно. Это и события, и величина, и процесс. По ГОСТу 18322 – 78 ремонт – это комплекс технологических операций по восстановлению исправности или работоспособности машины и ее ресурса (или ее составных частей).
Событие – при определении частоты их появления или интервала времени между ними.
Величина (в выражении трудоёмкости, стоимости или времени) – при описании сложности (или продолжительности) устранения отказа машины.
Для анализа многообразия ремонта как комплекса операции его целесообразно классифицировать по ряду признаков:
- По степени восстановления – выделяют текущий, средний и капитальный ремонт;
- По состоянию машины – на работающей и остановленной;
- По характеру – выделяют ремонт с обновлением и без обновления;
- По планированию проведения выделяют предупредительный ремонт (плановый) и неплановый (аварийный, случайный, заявочный);
- По организации выполнения – выделяют агрегатный, поточный ремонт, ремонт организацией-потребителем, ремонт предприятием-изготовителем.
Ремонт восстанавливает свойства, утраченные машиной при эксплуатации. По существу ремонт – это одна из стадий (или видов деятельности), направленных на обеспечение необходимого качества и надёжности машины. В ряду: исследование, проектирование, изготовление, ремонт – каждый вид значим и необходим.
Следует уже на этапе конструирования машины определить оптимальное распределение финансов между стадиями проектирования и изготовления – с одной стороны и создание, и функционирование системы ремонта готовых машин – с другой.
Пример: Если стоимость машины мала по отношению к расходам на ремонт, то целесообразно выпустить большее количество новых машин, что снизит эксплуатационные расходы. Если же ремонт стоит дешевле хранения запасных машин, то следует больше средств выделять на ремонт.
Любая машина характеризуется (в общем случае) по крайней мере, с двух сторон: технической и экономической.
В процессе эксплуатации ее технические характеристики теряются, она приходит в предельное состояние и становится непригодной для эксплуатации. Одновременно уменьшается ее экономическая стоимость, так как она переносится на вырабатываемую продукцию, снижается качество работ, уменьшается эксплуатационная производительность. В процессе ремонта вкладываются и расходуются дополнительные экономические ресурсы – на выполнение ремонта. В графическом виде это будет выглядеть так (рисунок 11.2).
Проблема эффективности ремонта требует решения двух основных, взаимосвязанных задач.
Во-первых, определение общего срока службы машины.
Во-вторых, определение режима профилактики (т.е. оптимальной структуры мероприятий по ремонту) в течение общего срока ее службы.
При определении рационального срока эксплуатации (до списания) в качестве критерия эффективности обычно используют величину предвиденных затрат, т.е. расход ресурсов на единицу времени работы (или единицу продукции).
При этом при эксплуатации идут два процесса (как отмечалось): физическое старение и экономическое обесценивание (снашивание).
Старение вызывает два эффекта:
- увеличение стоимости эксплуатации;
- снижение эксплуатационных характеристик (производительности и т.п.).
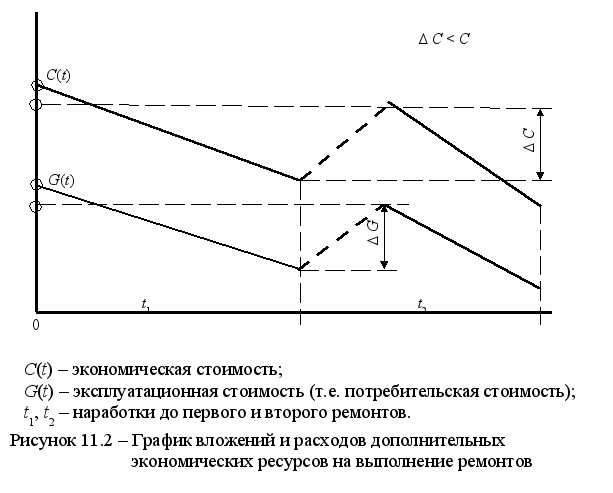
Суммарные затраты ресурсов на эксплуатацию машины включают отчисления на восстановление первоначальной стоимости (амортизация на возобновление машины); дополнительные затраты на доставку и монтаж машины; стоимости сменных элементов (деталей, сборочных единиц); затраты обусловленные старением и износом машины; отчисления на погашение кредита (процентной ставки) за сумму средств, необходимых на приобретение новой машины.
Полагают, что замена машин равносильна ее восстановлению до первоначального состояния (т.е. считают, что изменения технических параметров равны нулю).
11.1.1 Определение общего срока службы машины
Итак, суммарные затраты составляют

где С – цена новой машины с учётом ее доставки и монтажа, рублей;
Δ С – стоимость годных для использования и восстановления деталей
машины в момент ее списания, рублей;
δ – ликвидационная цена старой машины (негодных деталей),
рублей;
t – срок службы машины, в единицах времени (год, час) или едини-
цами работы (километры пробега, мото-часы, циклы, метры ку-
бические и др.);
К – приращение расхода ресурсов на поддержание машины в работо-
способном состоянии (рублей/год2, рублей/мотто-час2 и др.);
i – процентная ставка в долях рубля на 1 руб. за кредит (или ссуду),
1/год.
Анализ выражения (1) показывает, что первое слагаемое с ростом t уменьшается, а второе – растет (чем больше t, тем больше расходы К). Поэтому машину целесообразно эксплуатировать до тех пор, пока (1) не примет минимального значения, то есть

Тогда экономически оправданный срок службы машины равен
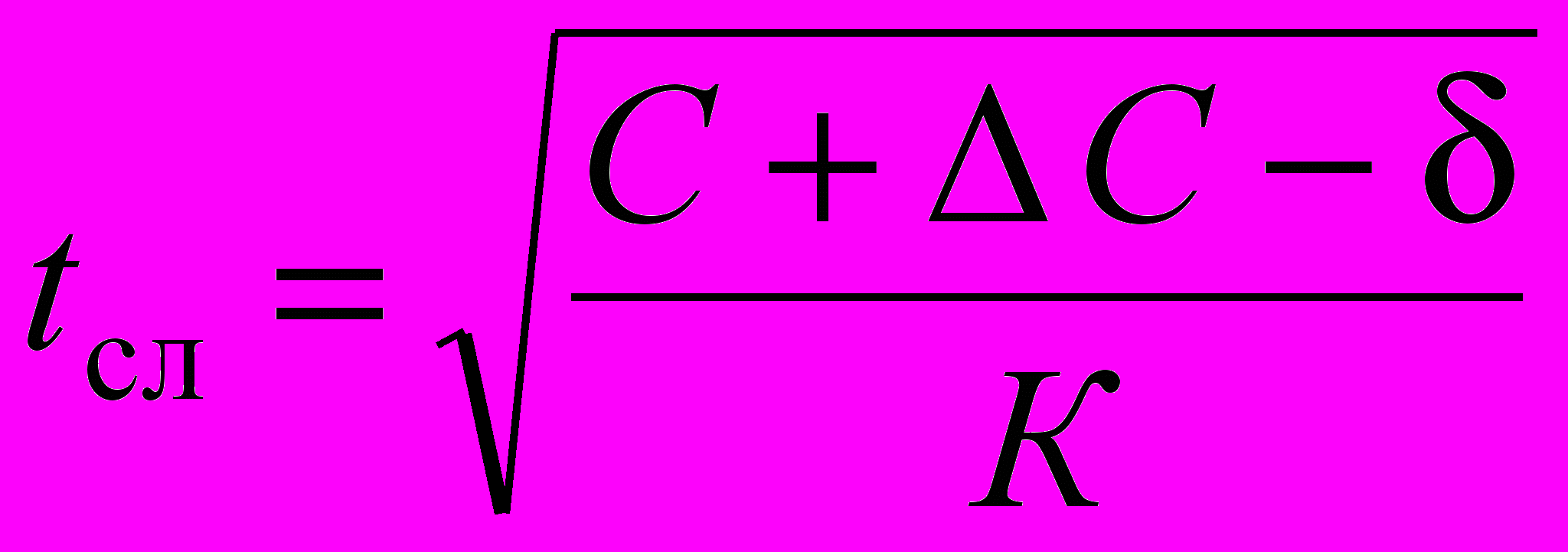
. (2)
Значения С определяют по прейскурантам цен на машину и ее перевозку потребителю, а стоимость Δ С (годных и подлежащих восстановлению деталей списываемой машины) определяют по формуле

где
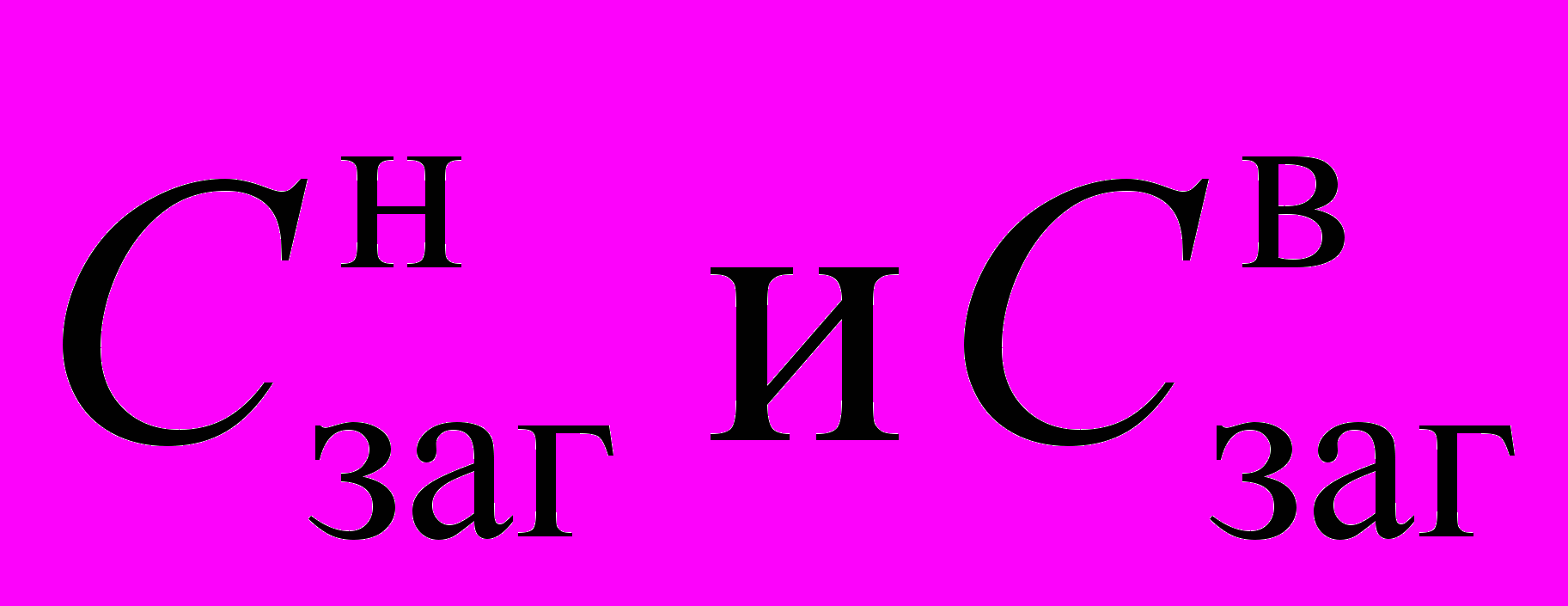
становленных до кондиции), рублей;
Сгодн – стоимость годных для повторного использования деталей
машины, подлежащей списанию;
β – коэффициент учёта утраты годности детали к восстанов-
лению по сравнению с заготовкой новой детали.
Анализ затрат на единичный ремонт показывает, что в общей стоимости капитального ремонта издержки на приобретение дефицитных, но поддающихся восстановлению деталей составляют до 50 %, что в среднем соответствует 25…35 % стоимости единичного капитального ремонта машины. В этом случае ликвидационная цена списываемой машины – не более 10 % цены новой машины. Приращении затрат К зависит от многих факторов (качества ремонта, условий эксплуатации типа машин и др.).
Например: для бульдозера Т – 130
50 ≤ К ≤ 80 руб/год2
для самосвала МАЗ – 5549
0,08 ≤ К ≤ 0,12 руб/тыс. км2
По формуле (2) определяют плановый срок службы машины, но действительные сроки могут значительно отличаться от плановых (особенно при эксплуатации в тяжелых условиях).
11.1.2 Структура ремонта
Технологический процесс ремонта машины является частью производственного процесса. Он включает ряд операций и видов работ, которые связаны между собой различным образом. В зависимости от способа соединения структурных элементов (операций, видов работ) структура ремонта может быть трех видов: последовательной, параллельной и комбинированной.
Процесс ремонта значительно сложнее, чем процесс изготовления машины, так как при изготовлении машины исходной заготовкой является материал, а при ремонте – исходной заготовкой и продукцией процесса ремонта является машина.
Более того, процесс ремонта представляет динамическую технологическую систему, которая реализует как совокупность операций анализа (разборка машины на элементы), так и синтеза (сборка машины из элементов).
Процесс ремонта, структура которого образована последовательным соединением элементов, когда операции технологического процесса (контроль состояния машины; разборка на агрегаты и детали; мойка и очистка машины и ее частей и др.) выполняются одна за одной в определенной последовательности, применяется в индивидуальном производстве.
Особенности: относительно низкий уровень эффективности, большой простой машины в ремонте, ограниченные возможности применения высокооперационного оборудования.
Процесс ремонта, структура которого образована параллельным соединением элементов, когда все технологические операции выполняются одновременно, т.е. применяется только в массовом производстве.
Особенности: число рабочих постов, число объектов ремонта должно соответствовать числу технологических операций; при этом длительность различных операций должна быть одинаковой.
При ремонте ДСМ практически невозможно использовать эту схему.
Комбинированная структура является наиболее предпочтительной при ремонте ДСМ. Она включает и параллельное, и последовательное расположение элементов (рисунок 11.2). Здесь представлена структура ремонта, которая образована из обобщенных элементов (их можно разбить на мелкие).
Итак: 1 – подготовка к ремонту ;
2 – разборка, мойка, очистка;
3 – контроль, комплектование, восстановление, изготовление деталей,
сборка узлов;
4 – сборка машины из узлов и агрегатов;
5 – обкатка, испытание, окраска и контроль машины.

Структуру эту можно изменять, дробя элементы на более мелкие и меняя их расположение на оси времени. Это влияет на параметры процесса. К параметрам относятся цикл и такт.
Цикл – интервал от начала первой до конца последней операции (независимо от числа одновременно ремонтируемых машин).
Такт – интервал времени, через который периодически производится выпуск отремонтированной машины определенного наименования.
Время цикла определяет эффективность использования оборудования и производственных площадей. Время можно уменьшить, изменяя структуру ремонта и деля ремонтные операции на более мелкие. При выборе процесса ремонта сопоставляют время цикла и коэффициент параллельности. В частности, элемент 1 – подготовка к ремонту – можно разделить на следующие элементы:
- Приемка машины в ремонт;
- Хранение принятой в ремонт машины;
- Снятие с машины некоторых деталей;
- Внешняя мойка машины.
Элемент 2 – разборка машины также можно разбить на подэлементы:
2.1 Разборка машины на агрегаты, узлы и детали;
2.2 Мойка и очистка деталей;
2.3 Контроль состояния деталей и их сортировка на годные, требующие
ремонта и брак;
2.4 Комплектование деталей и т.д.
Для системы с последовательным соединением элементов время цикла равно
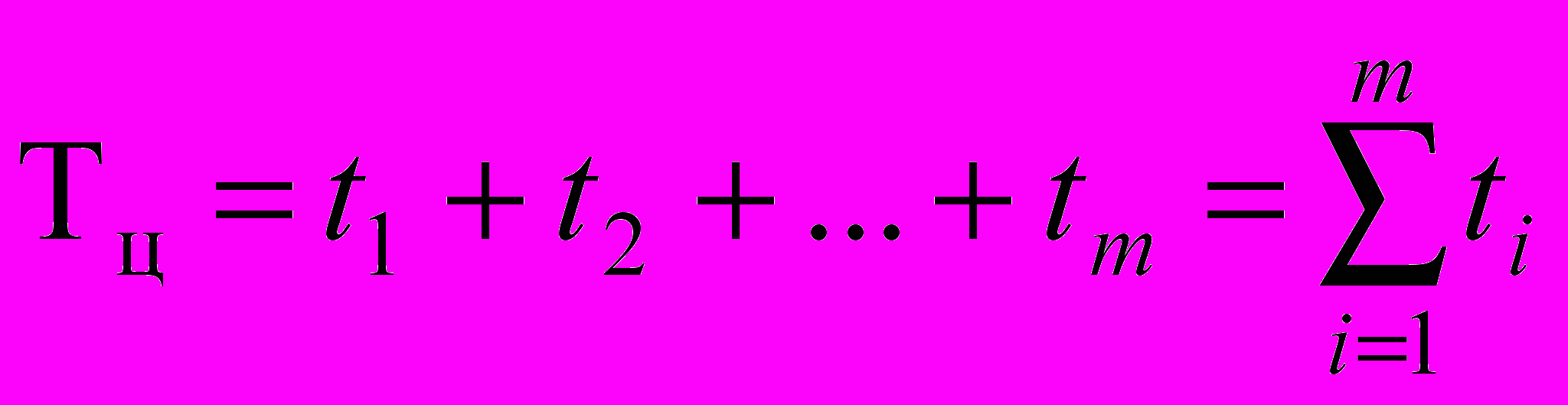
где ti – время технологической операции;
i – число операций.
Для комбинированной системы время цикла меньше:
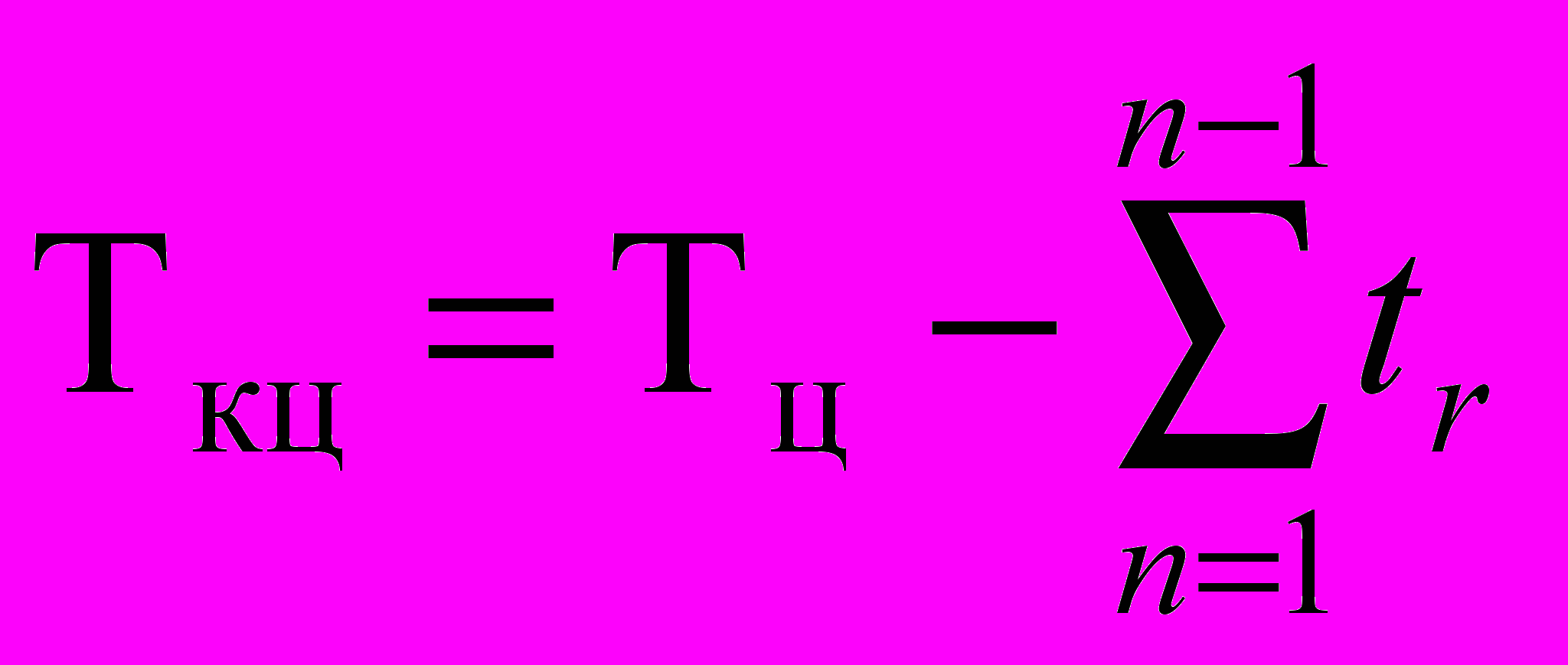
где Ткц – время цикла при комбинированной системе;
tr – время технологической операции выполняемой параллельно с
другими;
r – число параллельных операций.
Эффективность комбинированной системы оценивают коэффициентом параллельности

Эту структуру ремонта можно разделить на более мелкие элементы и (частично) пустить в параллельной системе.
Например: элемент 1 – подготовка машины – делится на: приемку машины в ремонт; хранение принятой машины; снятие некоторых частей; внешняя мойка.
Элемент 2 – разборка машины делится на: разборка на агрегаты, узлы и детали; мойка и очистка деталей; контроль состояния деталей и их сортировка на годные, требующие ремонта и брак; комплектование деталей и т.д.
Эти элементы отличаются различной технологической общностью. Отдельные (приемка, мойка, очистка, сборка и разборка) выполняют при ремонте разных машин и агрегатов. Отдельные (по восстановлению работоспособности агрегатов и узлов) являются специфическими и требуют специальных технологий и оборудования.