Физико-химические и технологические основы повышения эффективности комплексной переработки нефелинсодержащего сырья кислотными методами
Вид материала | Автореферат |
- Ериментальные каскады разделительных центрифуг позволяют не только вести технологические, 353.87kb.
- Программа вступительных испытаний в магистратуру по направление 260100. 62 «Продукты, 46.1kb.
- 2. 2 Использование пектинсодержащего сырья при откорме молодняка крупного рогатого, 158.15kb.
- Практикум по химии Анкудимова И. А., Гладышева, 2202.13kb.
- Программа ХII международной конференции Физико-химические основы ионообменных процессов, 465.27kb.
- Научные основы субхлоридной комплексной переработки нещелочного сырья на примере титаномагнетитовых, 503.93kb.
- И товарных нефтепродуктов лежат физико-химические процессы и управление этими процессами, 133.38kb.
- И товарных нефтепродуктов лежат физико-химические процессы и управление этими процессами, 124.23kb.
- И товарных нефтепродуктов лежат физико-химические процессы и управление этими процессами, 151.03kb.
- Физико-химические свойства и технологические основы получения пирротинов из пирита, 328.59kb.
и удельную поверхность получаемого продукта
№ п/п | Условия старения | Показатели | |||
рН | τ, ч | t, оС | S, м2/г | фазовый состав* | |
1 | 7.0 | 0.5 | 75 | 2.1 | А |
2 | - | 2.0 | - | 3.0 | А |
3 | - | 4.0 | - | 9.4 | А |
4 | - | 6.0 | - | 10.9 | А |
5 | 9.0 | 0.5 | 75 | 76.4 | А+ПБ |
6 | - | 2.0 | - | 94.8 | А+ПБ |
7 | - | 4.0 | - | 165.0 | А+ПБ |
8 | - | 6.0 | - | 202.4 | А+ПБ |
9 | 10.0 | 0.5 | 75 | 215.6 | А+ПБ |
10 | - | 2.0 | - | 276.0 | ПБ |
11 | - | 4.0 | - | 293.7 | ПБ |
12 | - | 6.0 | - | 321.3 | ПБ |
13 | 11.0 | 0.5 | 75 | 246.6 | ПБ |
14 | - | 2.0 | - | 285.9 | ПБ |
15 | - | 4.0 | - | 303.9 | ПБ |
16 | - | 6.0 | - | 336.1 | ПБ |
17 | 10.0 | 0.5 | 60 | 203.1 | А+ПБ |
18 | - | 2.0 | - | 218.5 | А+ПБ |
19 | - | 4.0 | - | 238.8 | ПБ |
20 | - | 6.0 | - | 267.9 | ПБ |
21 | 9.0 | 0.5 | 105 | 82.9 | А+ПБ |
22 | - | 2.0 | - | 119.6 | А+ПБ |
23 | - | 4.0 | - | 181.8 | А+ПБ |
24 | - | 6.0 | - | 244.3 | ПБ |
*А – аморфный гидроксид алюминия; ПБ – псевдобемит.
Полученные данные хорошо согласуются с результатами ИКС (рис. 6). Максимумы поглощения 3060 см-1 и 1080 см-1, соответствующие псевдобемиту, наиболее отчетливо зафиксированы на спектре образца 4 (рис. 6).
Облик частиц при увеличении в 5000 раз, полученный с помощью цифрового сканирующего электронного микроскопа SEM LEO-420, представлен на рис. 7. На микрофотографиях отчетливо видно, как по мере увеличения рН старения от 7 до 11 во все большем количестве появляются кристаллические образования и образец 4 полностью состоит из конгломератов кристаллитов, имеющих преимущественно округлую форму.
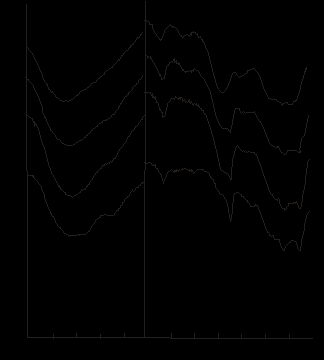
Рисунок 6 – ИК-спектры продуктов старения:
-
1 – рН = 7, t = 75оС, τ = 4 ч;
3 – рН = 10, t = 75оС, τ = 2 ч;
2 – рН = 9, t = 75оС, τ = 4 ч;
4 – рН = 11,t = 75оС, τ = 1 ч
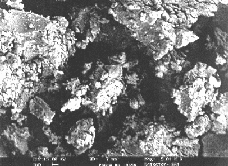
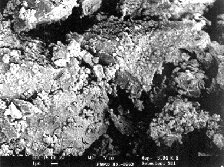
1 2
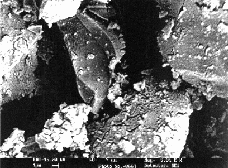
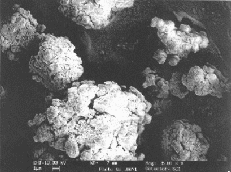
3 4
Рисунок 7 – Морфология продуктов старения:
1-4 – то же, что на рис. 6
По данным кристаллооптического анализа подавляющее количество (95% по объему) вещества в образце 4 оптически изотропно и имеет показатель преломления в пределах 1.556-1.564.
Выполненные исследования подтвердили справедливость вывода о специфичности структуры первичных частиц аморфного ГОА, формирующихся в процессе твердофазного гидролиза, и показали, что независимо от условий старения осадка аморфного ГОА в аммиачном растворе процесс кристаллизации идет исключительно по пути формирования структуры псевдобемита, причем наиболее быстро и полно в условиях, считающихся «байеритными».
В разделе 4.4 приводятся результаты исследований по выделению алюминия из азотнокислых растворов от разложения нефелинсодержащего сырья.
Изучение автоклавного гидролиза азотнокислого алюминия показало, что по мере повышения основности соли и уменьшения концентрации раствора степень гидролиза существенно возрастает, однако даже при обработке раствора двухосновной соли концентрацией 20 г/л Al2O3 при температуре 290оС степень гидролиза достигает лишь 72%. Выполненные исследования показали неприемлемость автоклавного гидролиза для выделения алюминия из азотнокислых растворов, поэтому он не может быть рекомендован для технологии.
Для выделения алюминия из азотнокислых растворов предпочтительны методы, включающие упаривание растворов и последующую термическую обработку смеси азотнокислых солей алюминия, натрия и калия. Необходимость глубокого упаривания азотнокислых растворов обусловлена тем, что существенная доля в общем балансе энергозатрат приходится на испарение и перегрев воды. Выполненные исследования показали, что при упаривании как растворов, так и плава нитрата алюминия до конечной температуры ∼150оС в парогазовую фазу отгоняется до 1/3 связанной кислоты, что позволяет получать конденсаты общей концентрации 5.4-28 и 47.5-52.85% HNO3 соответственно.
Возможны два варианта термической обработки азотнокислых солей. По первому из них обработку ведут при 300-400оС, когда разлагается только нитрат алюминия и железа. Продуктом реакции при этом является смесь гидроксида алюминия с примесью железа и нитратов натрия и калия. В этом случае часть затраченной кислоты будет выводиться из процесса в составе товарных продуктов. Если термическую обработку смеси нитратов вести при температуре 750-850оС, то твердым продуктом реакции является алюминатный спек, а вся азотная кислота удалится в парогазовую фазу, из которой она может быть регенерирована и возвращена на разложение нефелина. Осуществление низкотемпературной обработки имеет ряд недостатков, связанных с трудностью полного удаления азота, налипанием продукта реакции на стенки аппарата, а также тем, что 10-15% нитратного азота разлагается до оксидов. Поэтому предложено вести разложение при более низких температурах в области 250оС, когда нитрат алюминия разлагается не полностью, а продукт реакции представляет собой рассыпчатый продукт. При этом практически весь нитратный азот, связанный с алюминием, удаляется в виде паров азотной кислоты.
Изучена кинетика процессов при термической обработке азотнокислых солей. Разложение солей осуществлялось в условиях кипящего слоя. Исследование термического разложения азотнокислого алюминия в интервале температур 150-300оС показало, что процесс протекает, как минимум, в две стадии, имеющих величину энергии активации соответственно 42.06 и 67.56 кДж/моль. Исходя из полученных данных о степени денитрации и имеющихся представлений о механизме разложения Al(NO3)3∙9Н2О, обе стадии могут быть отнесены к формированию оксинитратов алюминия сначала низкой (1-я стадия) и затем высокой (2-я стадия) основности. Исследование высокотемпературной обработки (650-850оС) смеси нитратов натрия и калия при молярном отношении Na2O:К2О ∼3.2 на оксиде алюминия показало неизменность характера процесса во времени. Величина энергии активации составила 183.0 кДж/моль, что соответствует кинетической области протекания реакции. Рентгенофазовый анализ твердых продуктов показал наличие в них соединения, близкого по составу к (Na,К)AlO2. Следовательно, с большой вероятностью можно утверждать, что скорость денитрации азотнокислых натрия и калия на оксиде алюминия может быть интерпретирована как скорость образования алюминатов натрия и калия.
В пятой главе приведены результаты химико-технологических исследований, изучения и отработки отдельных технологических процессов и операций и их проверки в укрупненном масштабе.
Раздел 5.1 содержит данные по азотнокислотной переработке нефелина. С использованием статистического метода планирования и обработки эксперимента получена система уравнений, показывающих комплексное влияние условий азотнокислотного разложения нефелина на удельное сопротивление (Y1) и влажность (Y2) фильтр-остатков:
Y1р = 284.15 – 2.544t – 56.705 - 6.278С – 0.4m + 0.0632tC + 1.513C +
+ 0.553t - 0.0158tC, м-210-12, (8)
Y2р = 93.485 – 0.254t – 3.36 - 0.173C, %, (9)
где t температура разложения, оС; продолжительность дозирования нефелинового концентрата, ч; С концентрация HNO3, мас.%; m расход «затравки» аморфного кремнезема, г/100 г нефелинового концентрата.
Определены оптимальные параметры процесса азотнокислотного разложения нефелина: концентрация кислоты – 35%; ее расход 100% от стехиометрически необходимого количества; температура – 85оС; продолжительность дозирования нефелина – 3 часа с последующим перемешиванием суспензии в течение 30 минут; расход затравки – 20-25% от массы кислотонерастворимого остатка. Скорость фильтрования растворов при этом составляет 1.2-1.4 м3/м2∙ч, влажность осадков 51.0-53.5%. Извлечение компонентов в раствор составило, %: Al2O3 – 88.7-89.9; Na2O – 89.3-92.5; K2O – 70.5-71.5; Fe2O3 – 36.3-39.0.
В этих же условиях были выполнены эксперименты по разложению хвостов апатитовой флотации. Установлено, что 96-98% содержащегося в ХАФ апатита разлагается с переходом Р2О5 в раствор. Некоторым отличием является более низкая влажность осадков (46-49%), что обусловлено меньшим содержанием диоксида кремния за счет присутствия в большем количестве кислотонерастворимых минеральных примесей.
Проведены исследования по выделению аморфного кремнезема из кислотонерастворимого остатка, для чего осадок репульпировали в течение 15-30 минут в воде при температуре 40-60оС и соотношении Ж:Т = 46:1, выдерживали суспензию без перемешивания в течение 2-3 минут, декантировали осветленный слой на фильтр и затем сушили. Сгущенный продукт также обезвоживали на фильтре и сушили. Выход легкой фракции (аморфный кремнезем) составил 41-47% от массы кислотонерастворимого остатка при следующем содержании компонентов, мас.%: SiO2 90-92; Аl2О3 0.6-1.2; Fe2O3 0.5-0.8; Na2O 0.2-0.5; К2О 0.3-0.7; СаО 0.1-0.2; TiO2 0.1-0.2; Р2О5 0.01-0.03; п.п.п. 3-7.
Выведены эмпирические интерполяционные уравнения концентрационно-темпе-ратурной зависимости плотности () и вязкости () азотнокислых растворов:
= 1036.93 + 4.7794С (0.2658 + 0.0041С)t, кг/м3,
ln = -0.5239 + 0.0436С – (0.00819 + 0.000179С) t,
где динамическая вязкость, мПа·с; С – концентрация Аl2О3, г/л; t – температура, оС.
Плавный ход политерм показал возможность использования этих уравнений для получения в некоторых пределах оценочных значений плотности и вязкости путем экстраполяции, не прибегая к трудоемким и сложным в аппаратурном оформлении непосредственным измерениям, например в области повышенных температур.
Изучение процесса упаривания азотнокислых растворов показало целесообразность раздельного сбора конденсата. Крепкий конденсат с содержанием 30-36% HNO3 может быть непосредственно использован в голове процесса на стадии разложения нефелин содержащего сырья. Слабый конденсат частично может быть использован для промывки нерастворимого остатка от разложения нефелина, но основная его масса должна направляться в абсорбционное отделение регенерации кислоты. Осуществление этого процесса под разрежением способствует уменьшению перехода азотной кислоты в парогазовую фазу. Упаривание азотнокислых растворов при остаточном давлении 260 мм рт. ст. позволило почти вдвое снизить содержание HNO3 в конденсате. Поэтому 150-175 мл его (на каждые 500 мл упариваемого раствора) может быть использовано для первых промывок кислотонерастворимого остатка во избежание гидролиза азотнокислого железа, что приведет к загрязнению выделяемого аморфного кремнезема.
Дальнейшая переработка упаренных растворов осуществлялась в двух температурных режимах. При термической обработке в области температур 250-270оС практически вся удаляемая кислота регенерируется в виде конденсата при степени денитрации азотнокислого алюминия 75-80%, а получаемый твердый продукт представляет собой рассыпчатую сухую массу, которая не налипает на стенки аппарата. Продукт термической обработки, содержащий в своем составе некоторое количество нитратного азота, выщелачивался раствором аммиака с образованием легко расслаивающихся и хорошо фильтрующихся суспензий. Влажность промытых осадков, представляющих собой гидроксид алюминия с примесью железа, составляла всего 48-52%. Организация выщелачивания продукта термической обработки и промывки гидратного осадка в режиме противотока приводит к получению растворов с суммарным содержанием солей 600-700 г/л, что позволяет значительно сократить энергозатраты на его обезвоживание. При переработке 1000 кг нефелинового концентрата может быть получено 380-390 кг чернового гидроксида алюминия (64-66% Al2O3) и 700-720 кг смеси аммиачной, натриевой и калиевой селитр. Черновой гидроксид может быть рафинирован по упрощенной схеме Байера. Выход суммы солей составит приблизительно 3 тонны на одну тонну продукционного глинозема.
При термической обработке смеси солей в области температур 750-850оС происходит разложение не только азотнокислого алюминия и железа, но и нитратов щелочных металлов с образованием алюминатных спеков. Такая возможность обусловлена тем, что молярное отношение суммы оксидов натрия и калия к сумме оксидов алюминия и железа составляет примерно 1:1. Установлено, что при 850оС и продолжительности спекания 45 минут процесс алюминатообразования практически завершается: выщелачивание полученных спеков 5%-ным раствором натриевой щелочи при 90оС в течение 30 минут позволяет извлечь в раствор 95.7-96.8% Al2O3. Выполненные исследования показали, что спекание смеси азотнокислых солей целесообразно вести при подаче в зону реакции паров воды. При расходе пара 0.4 г на 1 грамм спекаемой смеси выход азотной кислоты в конденсат достигает почти 94% против 61% при спекании в отсутствие пара. Наличие водяных паров оказывает также положительное адсорбционно-каталитическое влияние и на собственно процесс алюминатообразования, ослабляя связи между ионами алюминия и кислорода в решетке оксида и облегчая тем самым ее перестройку в решетку новой фазы – алюмината.
Полученные спеки обрабатывали содо-щелочными растворами, содержавшими 42 г/л Na2Oк (каустического) и 20 г/л Na2Oу (углекислого), при 90-100оС в течение 30-40 минут. Во избежание самопроизвольного гидролиза алюминатов конечный каустический модуль αк (молярное отношение Na2Oк/Al2O3) растворов поддерживали на уровне 1.7. В алюминатный раствор извлекается до 96.4% Al2O3; до 97.5% Na2O и до 98% К2О. В полученных растворах содержание SiO2 составляло 0.15-0.18 г/л. С целью его снижения в раствор вводили известковое молоко в количестве 10 г СаО на 1 г SiO2 и вели перемешивание при 90-95оС в течение 1.5-2 часов. В результате образования малорастворимого гидроалюмосиликата кальция (гидрограната) состава 3СаОAl2O3∙m SiO2∙(6-2 m)Н2О, где m = 0.1-0.4, содержание SiO2 снижалось до 0.03-0.05 г/л, а кремневый модуль ((массовое отношение Al2O3/SiO2) повышался до 1800-3100. Потери алюминия со шламом обескремнивания составили 0.7-1%.
При выщелачивании алюминатных спеков, полученных при переработке хвостов апатитовой флотации, в раствор извлекается дополнительно 13-16% содержащегося в спеке Р2О5 в виде тринатрийфосфата, что вызвало необходимость очищать алюминатные растворы не только от SiO2, но и от Р2О5. С этой целью растворы, содержащие 85-89 г/л Al2O3, 2.4-2.9 г/л Р2О5 и 0.09-0.14 г/л SiO2, также обрабатывали известковым молоком, которое брали в количестве, необходимом для связывания не только кремнезема, но и фосфора в виде нерастворимого трикальцийфосфата 3СаО∙Р2О5. Условия обработки были аналогичны указанным выше. Содержание Р2О5 и SiO2 в растворе понижалось до 0.11-0.15 и до 0.02-0.04 г/л соответственно.
В ходе исследований было установлено, что основное количество фосфора, а также железо и кальций концентрируется в нерастворимом шламе от выщелачивания, где содержание Р2О5 составляет примерно 28-29%. Поэтому шлам необходимо рассматривать не как отход, а как весьма перспективное сырье для получения фосфорного удобрения. С этой целью предложено спекать шлам с частью получаемого поташа в присутствии аморфного кремнезема. Выполненные исследования показали, что наилучшие результаты достигаются при спекании шихты с молярным отношением Р2О5 : К2О = 1:11.5 при 1150оС в течение 40 минут в присутствии кремнезема при его расходе 10% от массы шихты. При соблюдении этих условий 79.6-91.8% Р2О5 переходит в цитратно-растворимую, а 98.4-99.1% в лимонно-растворимую форму.
Выделение гидроксида алюминия из очищенных алюминатных растворов осуществлялось карбонизацией с довыкручиванием. С этой целью через раствор при перемешивании барботировался диоксид углерода. Его подача велась до появления «молока», т.е. начала гидролиза алюминатов. Затем раствор, содержавший образовавшиеся частицы гидроксида алюминия в качестве затравки, перемешивали при 70оС до остаточного содержания Al2O3 в маточном растворе 2-3 г/л. Продолжительность выкручивания составляла 10-12 часов. Полученную суспензию разделяли фильтрованием. Гидратный осадок тщательно промывали горячей водой, сушили и прокаливали при 1150-1250оС. Выход глинозема составил 238-242 г на 1000 г нефелинового концентрата и 156-159 г на 1000 г хвостов апатитовой флотации, что соответствует товарному извлечению 83.6-85.0 и 75.4-76.8% соответственно.
Среднее содержание примесей в полученном глиноземе составило, мас.%: 0.02-0.035 SiO2; менее 0.01 Fe2O3; 0.28-0.31 Na2O; 0.02-0.03 К2О. Содержание Р2О5 в глиноземе, полученном при переработке ХАФ, не превышает 0.01%.
Укрупненные испытания по азотнокислотной переработке нефелинсодержащего сырья до получения глинозема проводились на опытно-заводской установке. Испытания показали возможность осуществления всех технологических операций и полностью подтвердили данные лабораторных исследований. Технологическая схема комплексной переработки ХАФ азотнокислотным методом приведена на рис. 8.
Одним из наиболее сложных вопросов азотнокислотной технологии переработки нефелина является аппаратурное оформление процесса термической обработки (спекания) смеси азотнокислых солей. Исследования, выполненные совместно с Государственным институтом азотной промышленности (ГИАП), позволили предложить и разработать принципиально новый высокоэффективный метод разложения азотнокислых солей в плазме, совмещая его с процессом плазмохимического получения азотной кислоты из атмосферного воздуха. Для отработки этого метода в составе опытной установки был смонтирован плазмохимический стенд. Упаренный раствор подавался в плазмохимический реактор (ПХР), где смешивался с потоком высокоионизированных газов, имевших температуру 3000-4500оС. Твердые продукты разложения осаждались в бункерах ПХР, пылеуловителя и фильтра, а нитрозные газы направлялись в систему регенерации азотной кислоты. Состав продуктов зависит от температуры отходящих газов, которую легко можно регулировать расходом раствора (плава) солей, вводимого в плазменную струю. Данный процесс характеризуется высокой производительностью, безынерционностью, обеспечивает снижение материалоемкости и уменьшение занимаемых производственных площадей. Около 40% затраченной энергии утилизируется в виде высокопотенциального (200оС) пара, который может быть использован для упаривания азотнокислых растворов. Применение плазмохимического метода позволяет осуществить процесс в замкнутом цикле, что обеспечивает высокую степень защиты окружающей среды от вредных газовых выбросов, а также рациональное решение вопросов аппаратурного оформления передела спекания азотнокислых солей и регенерации азотной кислоты. Выполненные работы показали, что продукты плазмохимического разложения азотнокислых солей по составу и физико-химическим свойствам аналогичны получаемым в обычных условиях и поэтому могут быть переработаны обычными методами, принятыми в глиноземной промышленности. В ходе испытаний было переработано свыше 50 тонн нефелинового концентрат (НК) и ХАФ.

ХАФ – 1111,11, в т.ч. H2O – 111,11
HNO3 – 30,81





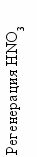


Разложение
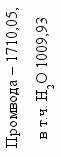

Вода на промывку – 472,67

Потери – 82,85



Фильтрование и промывка


Кремнеземный
остаток – 1090,96






Гидросепарация
H2O – 523,66
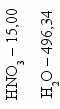





Минеральный остаток
(вл.) – 367,30
Сушка
Азотнокислый раствор 2868,73
HNO3 – 122,77
H2O – 590,07


Аморфный кремнезем – 200,00
Упаривание



Плав нитратов – 1644,55
HNO3 – 925,42
H2O – 292,75
Спекание



Алюминатный спек – 426,38

Выщелачивание
Оборотный раствор – 2970,41
Красный шлам – 106,07




Алюминатный раствор – 3290,72
Спекание
СО2 – 13,62








Фосфорно-калиевое удобрение – 135,17
Поташ – 65,96

Поташ – 23,24
Глинозем – 167,67
Сода – 167,72