Программа и контрольные задания для учащихся-заочников по специальности 2-36 01 01 «Технология машиностроения» Гомель, 2006
Вид материала | Программа |
- Программа и контрольные задания для учащихся-заочников по специальности 2-36, 1138.26kb.
- Методические указания и контрольные задания для студентов-заочников по специальности, 536.35kb.
- Программа преддипломной практики студентов специальности 1-36 01 01 «Технология машиностроения», 336.91kb.
- Методические указания и контрольные задания для студентов-заочников по специальности, 315.66kb.
- Программа, методические указания и контрольные задания для студентов 5 курса заочного, 2134.85kb.
- Программа, методические указания и контрольные задания для студентов 5 курса заочного, 439.54kb.
- Н. К. Джемилев технология конструкционных материалов методические указания, 89.05kb.
- Методические указания и контрольные задания для студентов заочников по специальности, 425.06kb.
- Рабочая программа и контрольные задания для студентов заочного обучения по специальности, 211.3kb.
- Программа учебной дисциплины "Материаловедение" предназначена для реализации, 400.85kb.
УКАЗАНИЯ ПО ВЫПОЛНЕНИЮ ПОЯСНИТЕЛЬНОЙ ЗАПИСКИ
КАЧЕСТВЕННЫЙ И КОЛИЧЕСТВЕННЫЙ АНАЛИЗ КОНСТРУКЦИИ ДЕТАЛИ НА ТЕХНОЛОГИЧНОСТЬ
Перед выполнением раздела необходимо составить технический эскиз детали.
Технический эскиз – документ, регламентированный стандартом Учреждения образования «Гомельский государственный машиностроительный техникум» специальности 2-36 01 01, разрабатывается с целью облегчения описания детали в отдельных главах пояснительной записки домашней контрольной работы, курсового и дипломного проекта.
Технический эскиз выполняется в пояснительную записку на листе бумаги необходимого формата (не менее А3) в соответствии со стандартами ЕСКД и содержит:
1 − чертеж детали в необходимом количестве проекций, видов, разрезов, сечений с указанием всех размеров и их точности в квалитетах в соответствии с ГОСТ 25347-82; допусков отклонений от геометрической формы поверхностей, допусков отклонений от взаимного расположения поверхностей и осей условными обозначениями по ГОСТ 2.308-79; шероховатости поверхностей по параметру Ra предпочтительного применения по ГОСТ 2789-73 условными обозначениями по ГОСТ 2.309-73 с учетом изменений, внесенных в него ИУС РБ № 3 2003;
2 − технические требования, предъявленные к детали;
3 − массу и материал детали с указанием стандарта в соответствующих графах основной надписи;
4 − номера всех обрабатываемых конструктивных элементов, проставленные в кружочках на концах выносных линий от соответствующих элементов.
Конструктивным элементом является поверхность или совокупность поверхностей, представляющих собой единый элемент: ступень в отверстии или на наружной поверхности; самостоятельно оформленный торец; резьбовая, зубчатая, шлицевая, шпоночная, и др. поверхность; паз, фаска, канавка для выхода шлифовального круга или сбега резьбы; отверстие под крепёж и т.д.
Выполнить качественный анализ детали на технологичность в соответствии с методикой: [9, c.10…18]; [10, c.11….19]; [15, c.21…23]; [21, c.26…28].
Количественный анализ детали на технологичность заключается в расчете коэффициентов унификации (Ку) и использования материала (КИМ).
Для расчета коэффициента унификации необходимо выполнить отработку элементов детали на соответствие стандартам, заполняя таблицу.
Таблица 1 – Отработка элементов детали на унифицированность
Номер элемента | Выдерживаемые размеры | Стандарт на элемент |
1 | 2 | 3 |
Первые две графы заполняются по техническому эскизу.
В третью графу необходимо заносить данные, показывающие выполнен ли конструктивный элемент по требованиям соответствующего стандарта (с указанием номера стандарта). Проверку степени унифицированности проводить по стандарту на соответствующие конструктивные элементы детали или по справочникам [7], [2].
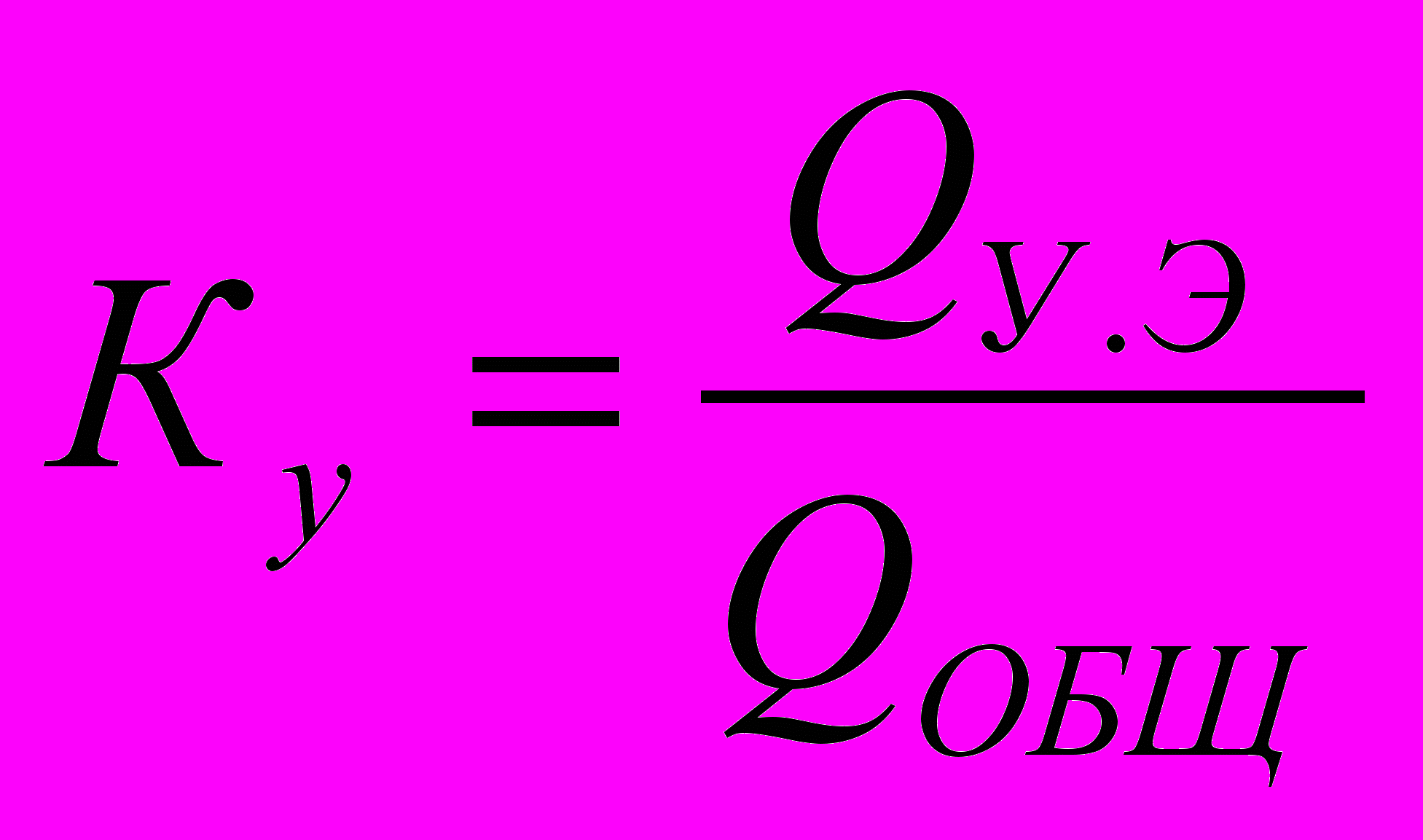
где Qу.э. – число конструктивных элементов детали, которые выполнены по
стандартам: резьбовые, зубчатые, шлицевые поверхности, шпоночные пазы, фаски, радиусы скругления, отверстия под крепеж, отверстия центровые, канавки для сбега резьб, резьбовые недорезы, сбеги, проточки и фаски, канавки для установки уплотнений на деталях пневмо-и-гидроаппаратуры, канавки для выхода резцов при тонком точении и растачивании или для выхода шлифовальных кругов, поверхности опорные под винты, болты, гайки, заклепки, шайбы, шурупы и т.д.; или в соответствии с нормальными рядами размеров и конусов: диаметральные размеры ступеней в отверстиях и на наружных поверхностях, конические поверхности.
Qобщ. –число всех конструктивных элементов детали.
Деталь считается технологичной, если КУ>0,6.
Коэффициент использования материала будет рассчитан в разделе 4.
АНАЛИЗ ТЕХНИЧЕСКИХ ТРЕБОВАНИЙ, ПРЕДЪЯВЛЕННЫХ К ДЕТАЛИ, НАЗНАЧЕНИЕ МЕТОДОВ ИХ ОБЕСПЕЧЕНИЯ И КОНТРОЛЯ
Этот раздел выполняется в виде таблицы.
Таблица 2 – Анализ технических требований
Номер конструктивного элемента | Размеры и требования к их размерной и геометрической точности | Требования к шероховатости поверхности | Требования к точности взаимного расположения поверхностей и осей | Методы достижения точности: способы базирования и виды обработки | Методы контроля и средства измерения |
1 | 2 | 3 | 4 | 5 | 6 |
Первые четыре графы заполняются по техническому эскизу.
Во вторую графу, кроме посадки и точности размера в квалитетах, заносятся требования к геометрической точности поверхности.
В пятой графе должны быть отображены соображения по методам обеспечения заданных параметров. При этом следует помнить о том, что вид обработки обеспечит размерную точность и точность геометрической формы.
Для достижения точности взаимного расположения поверхностей и осей и размерной точности некоторых поверхностей необходимо правильно назначить базовые поверхности детали при обработке: либо одна из поверхностей должна быть обработана при базировании по другой, либо они должны быть обработаны без переустановки за одну операцию от единой базы.
ВЫБОР ОБЩИХ ПРИПУСКОВ И РАСЧЕТ РАЗМЕРОВ ЗАГОТОВКИ С ДОПУСКАМИ
1 Ознакомиться с рабочим чертежом детали и способом получения заготовки.
2 Уточнить основные характеристики заготовки.
2.1 Для поковки способ изготовления (штамповки), основное деформирующее оборудование – по ГОСТ 7505-89 (приложение 1);
2.2 Для отливки: технологический процесс литья, тип сплава в соответствии с таблицами приложений 1…5 ГОСТ 26645-85; класс размерной точности по таблице 9 приложения 1, степень коробления по таблице 10 приложения 2, степень точности поверхности по таблице 11приложения 3, класс точности массы по таблице 13 приложения 5, допуск смещения, конфигурацию поверхности разъёма формы и модели - по ГОСТ 26645-85 (раздел 5, с. 29…31);
3 Назначить общие припуски и допуски на заготовку:
3.1 Последовательность определения допусков, предельных отклонений и припусков на поковку по ГОСТ 7505-89;
3.1.1 рассчитать массу поковки, как произведение массы детали на расчётный коэффициент, определённый по таблице 20 приложения 3;
3.1.2 найти класс точности, пользуясь таблицей 19 приложения 1;
3.1.3 определить группу стали по таблице 1 на с.8;
3.1.4 определить степень сложности, используя методику приложения 2;
3.1.5 выбрать конфигурацию поверхности разъёма штампа (П - плоская, Ин - изогнутая несимметрично, Ис - изогнутая симметрично);
3.1.6 найти исходный индекс по таблице 2 на с.10;
3.1.7 вычертить и заполнить таблицу 3:
3.1.7.1 определить номера поверхностей, для которых необходимо назначить припуски на обработку (все наружные обрабатываемые поверхности, отверстия, прошиваемые или намечаемые в заготовке, обрабатываемые торцы), заполнить графу 1;
3.1.7.2 по чертежу детали заполнить графы 2 и 3. При этом следует помнить о том, что один размер может соединять две поверхности с разной шероховатостью. Особенно часто это бывает при обработке противоположных торцов, к которым предъявлены разные требования по качеству поверхности;
3.1.7.3 назначить допуски на размеры поковки в зависимости от исходного индекса, конкретных размеров детали и вида размера по таблице 8 на с 17…19, учитывая, что допускаемые отклонения внутренних размеров поковок устанавливаются с обратными знаками.
Виды размеров:
длина, ширина, диаметр, высота и глубина – размеры элементов поковки, получаемых в одной части штампа;
толщина – высотный размер элемента поковки, получаемый в обеих частях штампа.
Заполнить графу 4: указать величину допуска и (в скобках) – величины предельных отклонений;
3.1.7.4 определить основной припуск по таблице 3 на с 12…13 в зависимости от исходного индекса, конкретного размера детали, вида этого размера, а так же от шероховатости обрабатываемой поверхности и заполнить графу 5;
3.1.7.5 определить дополнительные припуски по таблицам 4; 5; 6 на те размеры, где могут появиться соответствующие искажения при изготовлении поковки:
смещение поверхности разъема штампа влияет на размеры, которые параллельны разъему, и заполняется в графу 6;
изогнутость и другие отклонения формы, как правило, возникают на поверхностях большой протяженности в одном направлении, но малой в перпендикулярном ему. Учитываются эти дополнительные припуски на размерах меньшей величины поверхности и заполняются в графу 7;
отклонение межосевого расстояния учитывается при наличии в детали двух прошиваемых или намечаемых отверстий, оси которых находятся на некотором расстоянии и параллельны друг другу, и заполняется в графу 8;
3.1.7.6 определить величину расчетного припуска путем сложения основного и необходимых дополнительных припусков, заполнить графу 9;
Примеры расчета допусков, припусков и размеров заготовок предоставлены в приложении 5 на с 33…51.
Назначение и расчет вести в табличной форме.
Таблица 3 – Назначение допусков и припусков на поковку
Номер поверхности | Номинальный размер детали с указанием посадки и квалитета точности | Шероховатость обрабатываемой поверхности детали, Ra,мкм | Допуск на заготовку с указанием предельных отклонений, мм | Основной припуск, мм | Дополнительные припуски, мм | Расчетный припуск на размер поковки, мм | ||
Смещение поверхности разъема штампов | Изогнутость и другие отклонения формы | Отклонение межосевого расстояния | ||||||
1 | 2 | 3 | 4 | 5 | 6 | 7 | 8 | 9 |
3.1.8 при необходимости найти по таблице 9…17 допускаемые отклонения отдельных элементов поковки для указания их в технических требованиях на чертеже заготовки.
3.1.9 Составить предварительно эскиз заготовки: линией «штрих, две точки» прочертить контур детали, наметить припуски на всех обрабатываемых поверхностях, проставить их величины, наметить поверхность разъема штампов;
3.2. Последовательность определения допуска и назначения припуска на отливку по ГОСТ 26645-85:
3.2.1 вычертить и заполнить таблицу 4:
3.2.1.1 определить номера поверхностей, для которых необходимо назначить припуски на обработку (все наружные обрабатываемые поверхности, отверстия, проливаемые в заготовке, обрабатываемые торцы), заполнить графу 1;
3.2.1.2 по чертежу детали заполнить графы 2 и 3. При этом следует помнить о том, что один размер может соединять две поверхности с разной шероховатостью. Особенно часто это бывает при обработке противоположных торцов, к которым предъявлены разные требования по качеству поверхности;
3.2.1.3 допуск на номинальные размеры отливки определяется по таблице 1 ГОСТ 26645-85 в зависимости от класса размерной точности и заносится в графу 4;
3.2.1.4 допуск формы и расположения элементов отливки на каждый номинальный размер определяется по таблице 2 в зависимости от степени коробления и заносится в графу 4;
3.2.1.5 общий допуск находится по таблице 16 в зависимости от допуска размера и допуска формы и расположения элементов поверхности, запись осуществляется в графе 6;
3.2.1.6 ряд припусков на обработку отливок определяется по таблице 14 в зависимости от степени точности поверхности: для размеров, расположенных при заливке сверху допускается увеличивать ряд припусков на 1-3 единицы (для разовых форм в единичном и мелкосерийном производстве). При определении ряда припусков следует внимательно прочитать примечание к таблице. Запись производится в графе 7;
3.2.1.7 минимальный литейный припуск определяется по таблице 5 в зависимости от ряда припусков и записывается в графу 8;
3.2.1.8 общий припуск на сторону для каждого номинального размера определяется по таблице 6 в зависимости от общего допуска, ряда припусков и вида окончательной механической обработки и записывается в графу 9.
При этом вид окончательной механической обработки (черновая, получистовая, чистовая, тонкая) определяется в зависимости от параметров шероховатости поверхности и размерной точности детали или по таблицам 7 и 8, или по ТП механообработки;
3.2.1.9 расчетный припуск определяется путем сложения минимального литейного припуска и общего припуска и записывается в графу 10.
Таблица 4 – Назначение допусков и припусков на отливку.
Номер поверхности | Номинальный размер детали с указанием посадки и квалитета точности | Шероховатость обрабатываемой поверхности детали, Ra,мкм | Допуск размера заготовки, мм | Допуск формы, мм | Общий допуск, мм | Ряд припусков | Минимальный припуск, мм | Общий припуск, мм | Расчетный припуск на размер отливки, мм |
1 | 2 | 3 | 4 | 5 | 6 | 7 | 8 | 9 | 10 |
3.2.2 При необходимости найти по таблицам 3;4;12;16 допускаемые отклонения и шероховатости отдельных элементов отливки для указания их в технических требованиях на чертеже заготовки.
3.2.3 Составить предварительно эскиз заготовки: тонкой сплошной линией прочертить контур детали, наметить припуски на всех обрабатываемых поверхностях, проставить их величины, наметить поверхность разъема форм и модели;
4. Рассчитать размеры заготовки предварительно. Полученные данные занести в таблицу 5:
Таблица 5 – Расчет размеров заготовки
Номер поверхности | Размер, выдерживаемый при обработке заданной поверхности детали, мм | Допуск на размер заготовки, мм | Расчетный припуск на размер заготовки, мм | Расчет размеров заготовки, мм | Исполнительный размер заготовки с указанием предельных отклонений, мм |
1 | 2 | 3 | 4 | 5 | 6 |
4.1 в графу 1 заносятся данные из граф 1 таблиц 3 или 4;
4.2 в графу 2 заносятся данные из граф 2 таблиц 3 или 4, но без указания посадки и квалитета точности;
4.3 в графу 3 заносятся данные из графы 3 таблицы 3 или из графы 4 таблицы 4;
4.4 в графу 4 заносятся данные из графы 9 таблицы 3 или из графы 10 таблицы 4;
4.5 в графе 5 рассчитываются размеры заготовки. Расчет проводится с учетом изменений конфигурации заготовки относительно контура детали
4.6 в графе 6 записывается значение, округлённое до десятых долей миллиметра или уточнённое по результатам аналитического и табличного расчёта припусков по переходам.
ОПРЕДЕЛЕНИЕ КОЭФФИЦИЕНТА ИСПОЛЬЗОВАНИЯ МАТЕРИАЛА
Коэффициент использования материала определяется по формуле:
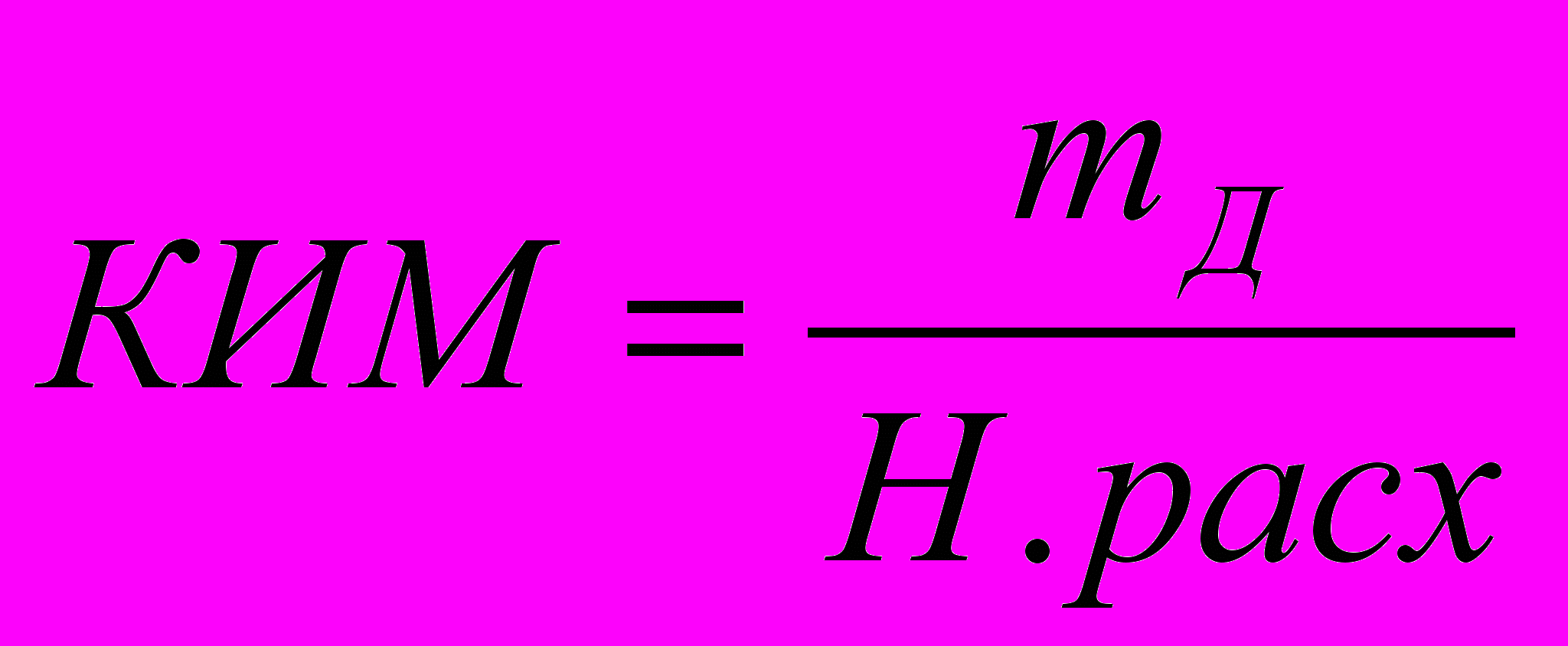
где тД - масса детали, кг;
Н.расх - норма расхода материала, кг.
Деталь считается технологичной, если КИМ:
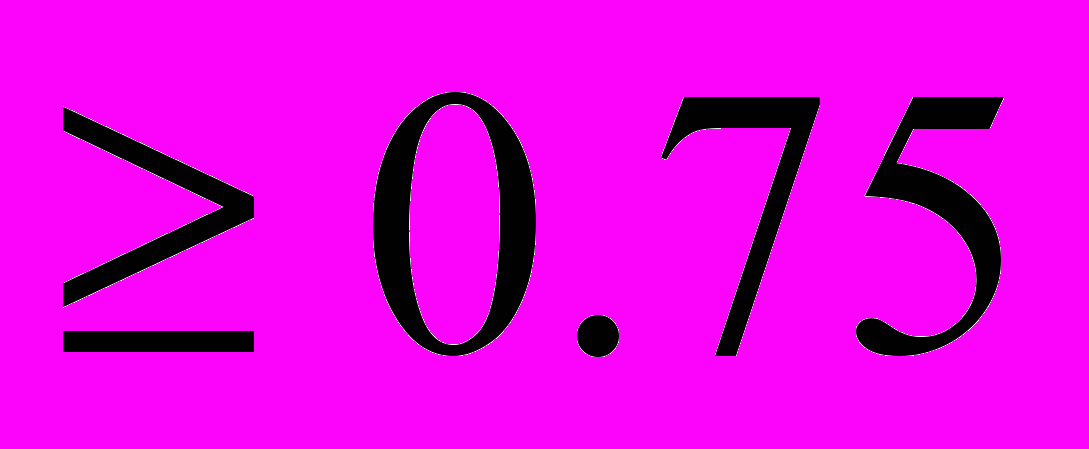
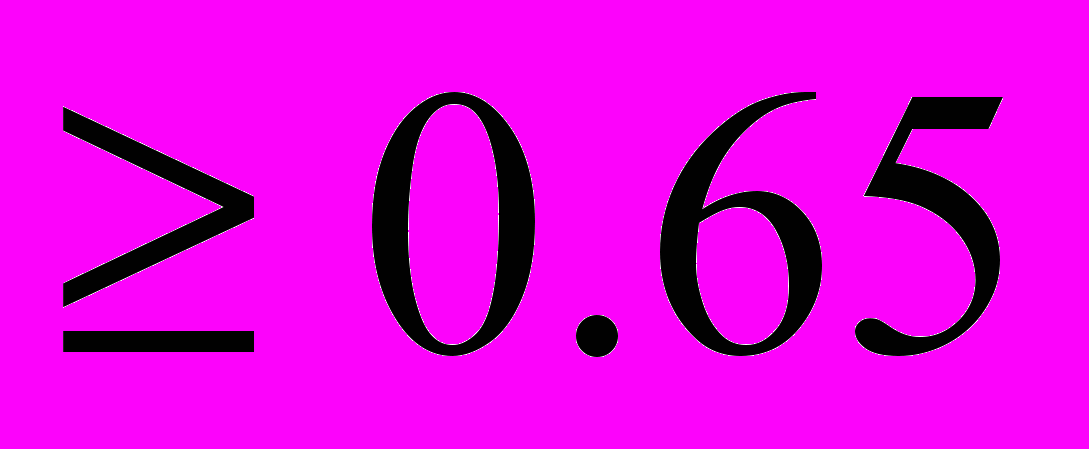
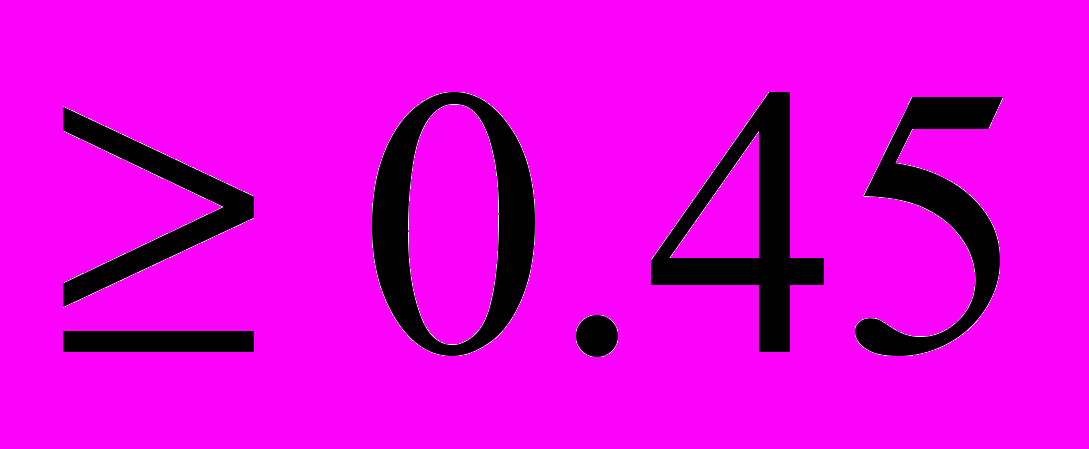
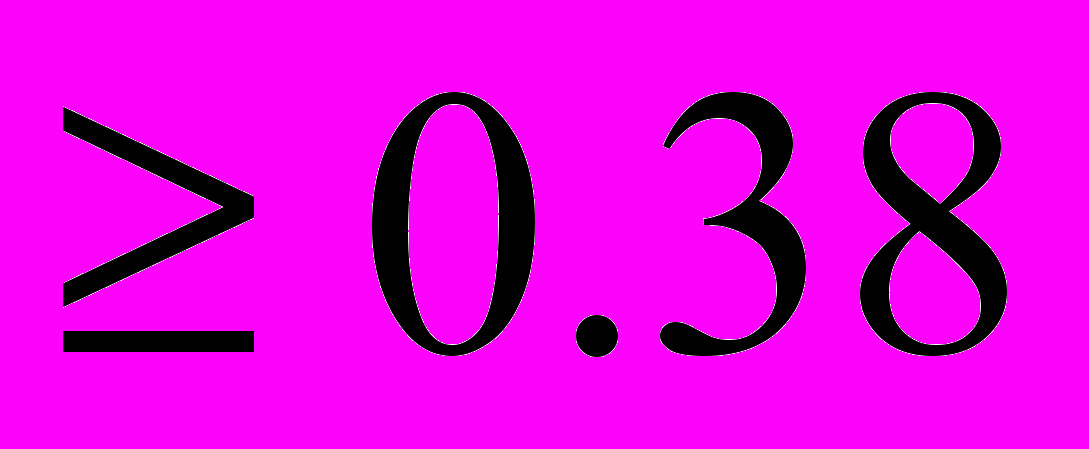
Н.расх можно рассчитать по формуле:
Н.расх=тЗ+тОТХ.З., кг
где тЗ - масса спроектированной заготовки:
mз=mд+mотх.м.о, кг
где mд - масса детали, кг (принимается по чертежу детали);
mотх.м.о- масса отходов механической обработки, кг;
mотх.мех.обр =Vотх.*ρ, кг
где Vотх.м.о. - суммарный объём удаляемого в процессе механической обработки
материала, т.е. объем припусков, мм3.
Vотх.м.о. = V1 + V2 + … + Vп , мм3
где п – множество удаляемых с поверхности заготовки припусков.
ρ - плотность материала заготовки, кг/мм3;
тОТХ..З. - масса отходов при производстве заготовки.
Для штамповок, полученных на молотах, тОТХ..З. составляет около 20% массы заготовки. Для штамповок, полученных на прессах, и для отливок – от 10% (для крупных
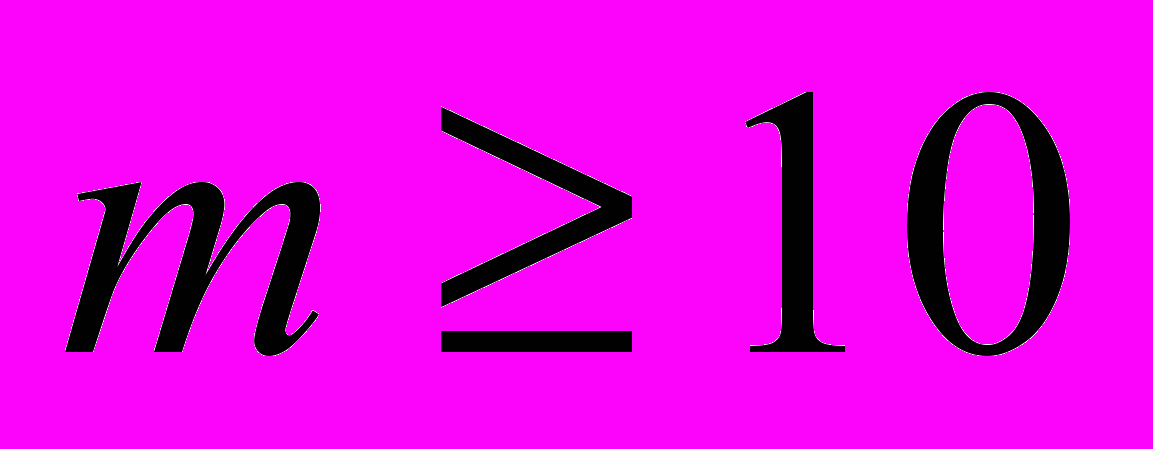
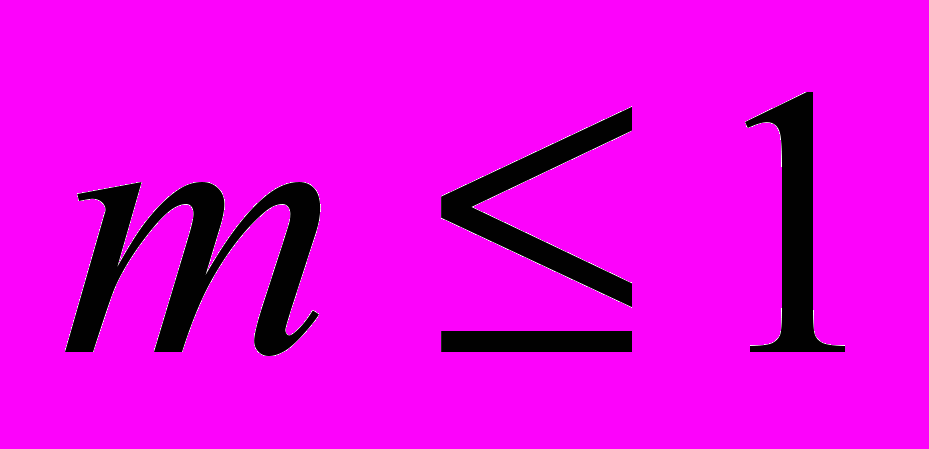
Для заготовок в виде проката тОТХ..З. состоит из ширины пропила или отрезки, длины концевого отхода, оставшегося в патроне или цанге, длины отхода на некратность.
Рекомендации: [15, с.38].
ВЫБОР ОПЕРАЦИОННЫХ ПРИПУСКОВ НА ОБРАБОТКУ ОДНОЙ ПОВЕРХНОСТИ
ТАБЛИЧНЫМ СПОСОБОМ
И УСТАНОВЛЕНИЕ ОПЕРАЦИОННЫХ РАЗМЕРОВ С ДОПУСКАМИ НА ОБРАБОТКУ.
- Установить маршрут обработки поверхности детали с указанием точности обработки и качества обрабатываемой поверхности на каждом переходе. Рекомендации по выбору параметров приведены в соответствующих графах таблицы 6.
- Назначить межоперационные припуски и рассчитать операционные размеры с допусками на обработку по таблицам. Величину припусков межоперационных выбирать в соответствии с рекомендациями, приведенными в пятой графе таблицы 6.
3 Расчёт выполнять заполняя таблицу 6.
Таблица 6 - Табличный расчёт припусков
Переходы механической обработки поверхности (указать размер с допуском по чертежу детали) | Точность обработки | Припуск табличный, Z, мм | Расчёт размеров заготовки d или D, мм | ||
Квалитет | Допуск, мм | Шероховатость, Rа, мкм | |||
1 | 2 | 3 | 4 | 5 | 6 |
Последний переход механической обработки (п.п.) | С чертежа детали | [4 с.72…88 т.33…43] [27 с.189…195 т.35…37] | d – для наружных поверхностей D – для внутренних поверхностей (с чертежа детали) | ||
Промежуточные переходы механической обработки (пр.п.) | [26 с.8…9 т. 4; с.11…12 т.5]; [15 с.63 т.3.21; с.67 т.3.25; с.69 т.3.27; с.70 т.3.28] | dПР.П. = dП.П. + ZП.П. DПР.П. = DП.П. + ZПП | |||
Заготовка (з) | - | ГОСТ на вид и способ получения заготовки | - | - | dЗ = dПР.П. + ZПР.П. DЗ = DПР.П. - ZПР.П. |
Под таблицей следует записать размер заготовки с указанием верхнего и нижнего предельных отклонений.
РАСЧЕТ ОПЕРАЦИОННЫХ ПРИПУСКОВ НА ОБРАБОТКУ ОДНОЙ ПОВЕРХНОСТИ
АНАЛИТИЧЕСКИМ СПОСОБОМ
И УСТАНОВЛЕНИЕ ОПЕРАЦИОННЫХ РАЗМЕРОВ С ДОПУСКАМИ НА ОБРАБОТКУ.
1 Установить маршрут обработки поверхности заданной для расчета. Заполнить графу 1 таблицы 7.
2 Определить точность обработки, технологические допуски и шероховатость обработки для каждого перехода механической обработки [3, с. 8…9, таблица 4; с. 11…12, таблица 5]. Заполнить графы 2 и 3 таблицы 7.
3 Описать способ базирования детали в приспособлении: по какой поверхности (размер и степень обработанности) и в какое приспособление устанавливается деталь на каждом переходе, - заполняя графу 4 таблицы 7.
4 Определить погрешность базирования, закрепления и установки для каждого перехода индивидуально, заполняя графу 5 таблицы 7: [1, с. 75…83].
Все расчеты выполнять в миллиметрах с точностью до трех знаков после запятой.
Таблица 7 - Определение последовательности обработки детали и погрешности установки
Последовательность механической обработки поверхности | Точность обработки | Способ базирования детали в приспособлении | Расчет погрешности установки, ![]() ![]() мм ![]() | |
Квалитет с допуском технологическим, мм | Шероховатость, Ra, мкм | |||
1 | 2 | 3 | 4 | 5 |