Лекция Криволинейные детали
Вид материала | Лекция |
- 2 Назначение детали и её поверхностей, 231.92kb.
- Лекция 21 Точность обработки деталей Допуски и посадки, 160.03kb.
- Кафедра: тммси, 39.13kb.
- Гост замена, 1160.31kb.
- В чём состоит технологический анализ чертежа детали?, 389.41kb.
- Программа дисциплины по кафедре Детали машин детали машин и основы конструирования, 355.21kb.
- Трение, износ и стойкость инструмента. Охлаждение и смазка при бработке резанием. Качество, 115.44kb.
- Программа дисциплины по кафедре Детали машин теория механизмов и детали машин, 422.13kb.
- Методические указания к изучениюдисциплины «детали машин», 189.59kb.
- Примерное назначение углеродистой качественной конструкционной стали, 89.57kb.
Лекция
Криволинейные детали
Криволинейные детали в зависимости от способа изготовления подразделяются на гнутые, гнутоклееные, гнутопропильные и выпильные (по шаблону).
Гнутьё древесины – изгибание цельных или слоистых (склеиваемых) заготовок древесины и закрепление приданной им изогнутой формы. Гнутье древесины основано на пластических свойствах древесины. Древесина твёрдых лиственных пород — во много раз пластичнее, чем древесина хвойных и мягких лиственных пород (осина, ольха и др.), и наиболее пригодна для гнутья. Гнутье древесины применяют в вагоно- и судостроении, при изготовлении ферм, арок, рам, сводов, профилей, труб, мебели, лыж, бочек, ободьев колёс и пр. гнутых и гнуто-клеёных изделий из древесины. Различают горячее и холодное Г. д.
Гнутые детали изготовляют из цельной предварительно пропаренной древесины на специальных шаблонах или специализированных станках. В данном случае используют упругие свойства древесины некоторых твёрдых лиственных пород — дуба, ясеня и особенно бука, которые в пропаренном состоянии хорошо гнутся и при высыхании сохраняют заданную им криволинейную форму. Ясень, однако, может принять волнообразную форму. Конструкция гнутых деталей зависит от их назначения.
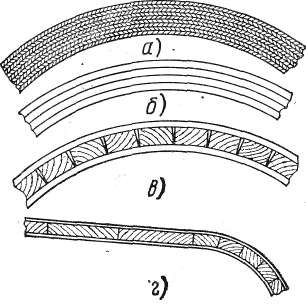
Рис. 1. Гнутоклееные детали: а — из шпона, б — из пластин древесины,
в, г — из брусков, оклеенных фанерой или твердой древесноволокнистой плитой
При конструировании нельзя допускать малых радиусов кривизны гнутых деталей во избежание их поломки при гнутье. Отношение толщины изгибаемой заготовки к радиусу изгиба на этих участках должно отвечать следующим условиям: h/R≤1/3, где h — толщина заготовки, мм; R — радиус изгиба, мм.
Гнутоклееные детали изготовляют следующим образом. Пласти делянок намазывают клеем, закладывают в шаблон и запрессовывают. После выдержки под прессом до полного схватывания клея деталь сохраняет заданную ей форму. Гнутоклееные детали изготовляют из шпона, пластин древесины, фанеры, из брусков хвойных пород, оклеенных фанерой или твердой древесноволокнистой плитой.
В гнутоклееных деталях из шпона (рис. 1а) направление волокон в слоях шпона может быть как взаимно перпендикулярным, так и одинаковым. Изгиб шпона, при котором волокна древесины остаются прямолинейными, называется изгибом поперек волокон, а при котором волокна изгибаются — изгибом вдоль волокон.
При конструировании гнутоклееных деталей из шпона, несущих при эксплуатации значительные нагрузки (ножки стульев, изделий), рациональны конструкции с изгибом вдоль волокон во всех слоях. Жесткость таких деталей значительно выше, чем деталей с взаимно перпендикулярным направлением волокон древесины.
С взаимно перпендикулярным направлением волокон в слоях шпона конструируют гнутоклееные детали толщиной до 10 мм, не несущие больших нагрузок при эксплуатации, например стенки ящиков. В этом случае они меньше подвержены формоизменяемости. Наружный слой таких деталей должен иметь долевое направление волокон (изгиб вдоль волокон), так как при изгибе поперек волокон в местах изгиба появляются мелкие долевые трещины, которые затрудняют отделку изделия.
При конструировании гнутоклееных деталей из шпона, несущих при эксплуатации значительные нагрузки, необходимо учитывать, что гнутоклееная деталь при эксплуатации лучше работает на сгиб, чем на разгиб. Предел прочности гнутоклееной детали при сгибе примерно в 2,5 раза больше, чем при разгибе. Поэтому, если в конструкции изделия гнутоклееная деталь работает на разгиб, ее деформация должна быть ограничена.
На рис. 2, а показана схема гнутоклееного стула. Недостаточно прочным в такой конструкции стула является криволинейный участок на границе перехода спинки к сиденью, работающий на разгиб.
Наиболее прочны конструкции гнутоклееных стульев, у которых все гнутоклееные детали при эксплуатации работают на сгиб (рис. 2, б, в). В схемах гнутоклееных кресел (рис. 2, г, д) показан конструктивный прием, ограничивающий деформацию разгиба с помощью подлокотников.
Применяемые в конструкциях мебели гнутоклееные детали унифицированы. Толщина унифицированных гнутоклееных деталей 3. . .30мм, угол изгиба 90. . .135°, радиус кривизны не менее 15мм.
Гнутоклееные заготовки из шпона, предназначенные для изготовления деталей мебели, должны отвечать требованиям ГОСТ 21178—75.
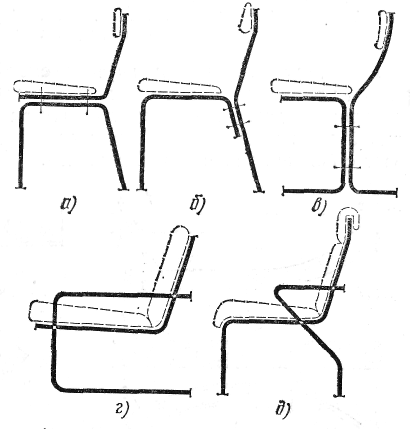
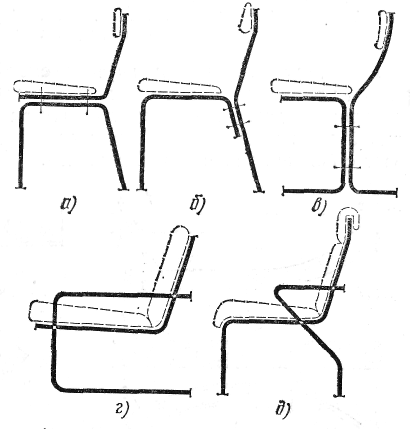
Рис. 2. Схемы гнутоклееных стульев:
а — с гнутоклееной деталью сиденье — спинка, работающей на разгиб, б, в — с гнутоклееными деталями, работающими на сгиб, г, д — с ограничением деформации разгиба гнутоклееных деталей с помощью подлокотников.
При конструировании гнутоклееных деталей из пластин древесины (см. рис. 1, б) допустимые соотношения H/R (где H —толщина изгибаемой пластины, R — внутренний радиус) при гнутье в жестких пресс-формах составляют не более: для березы — 1/50. . . . . .1/60; ели — 1/46. . .1/57; бука — 1/46; вяза — 1/31.
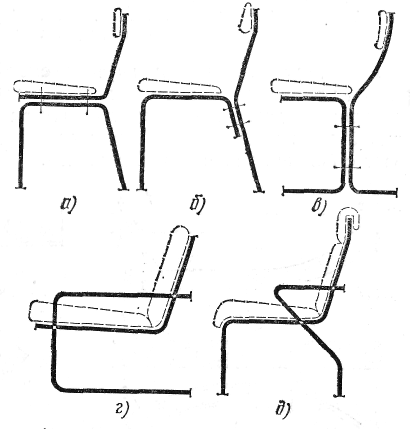
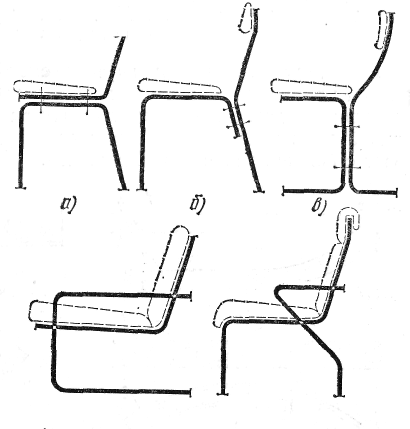
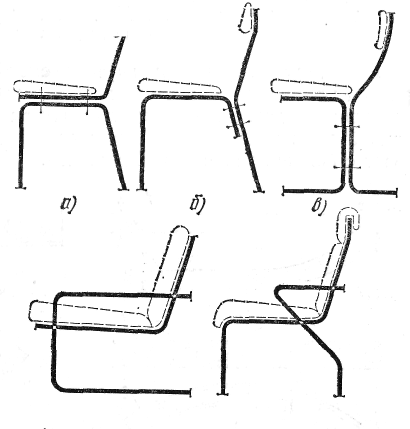
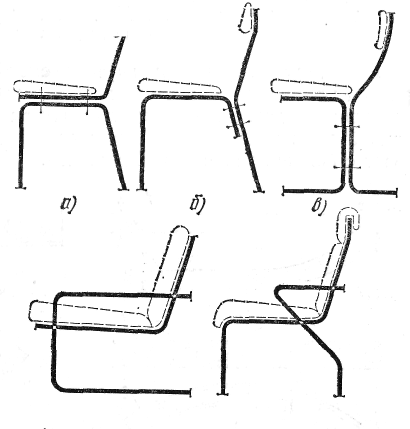
Гнутье фанеры возможно до небольших радиусов кривизны (по Б. М. Буглаю):
Толщина фанеры, мм 1 1,5 2 2,5 3 4
Допустимый радиус кривизны, мм .. 9 17 23 30 37 50
При конструировании гнутоклееных деталей с одинаковой и разной кривизной по ширине между двумя облицовками из фанеры или твердой древесноволокнистой плиты (см. рис. 1, в, г) располагают бруски из древесины хвойных пород. Такие плиты конструируют с большим радиусом кривизны.
Гнутопропильные детали — разновидность гнутоклееных. Их изготовляют из брусков лиственных и хвойных пород, в которых предварительно сделаны продольные пропилы (рис. 3, а), а также из древесностружечных и столярных плит, имеющих пропилы (рис. 3, 6) или специально выбранные пазы (рис. 3, в, г), в которые вставляют на клею конструктивные элементы из шпона, массивной древесины или других материалов.
Гнутопропильные детали из брусков с продольными пропилами делают в том случае, когда необходимо получить кривизну одного конца бруска. Для этого в пропилы закладывают промазанный клеем шпон, который должен быть на 0,1. . .0,2 мм тоньше пропила. Зазор 0,1 . . .0,2 мм необходим для того, чтобы шпон входил в пропил свободно и клей с его плоскости не сгонялся. Затем пропиленную часть бруска с вложенным шпоном подвергают гнутью в шаблоне. После схватывания клея заготовка сохраняет заданную ей форму.
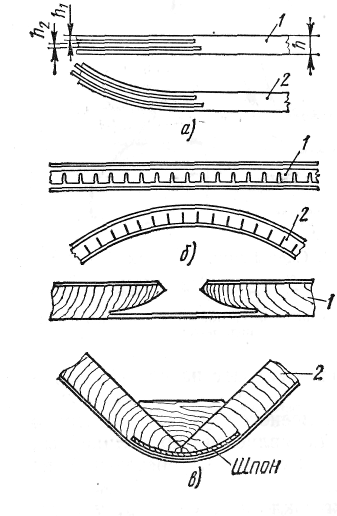
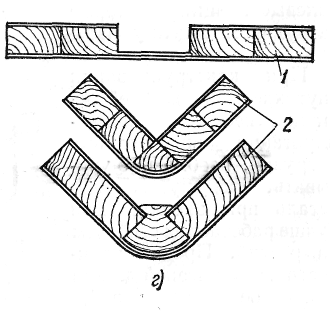
Рис. 3. Гнутопропильные детали:а — с продольными пропилами на концах деталей, б — с пропилами в плитах, в, г — с пазами в плитах; 1 — заготовки до склеивания, 2 — заготовки после склеивания
При конструировании гнутопропильных деталей с продольными пропилами необходимо толщину h1 крайних элементов, толщину h2 промежуточных элементов и число пропилов выбирать в зависимости от радиуса кривизны и толщины h изгибаемых заготовок (табл. 1 и 2).
Например, буковую заготовку толщиной h=22 мм требуется изогнуть радиусом 30 мм. По табл. 1 толщина крайних элементов h1 =1,5 мм, промежуточных — 2,5 мм. По табл. 2 в заготовке должны быть четыре пропила.
Таблица 1
Зависимость толщины изгибаемых элементов, от породы древесины и радиуса изгибаемых заготовок
Порода древесины и положение элементов в заготовке | Толщина элементов при радиусе кривизны, мм | |||
10 | 20 | 30 | 50 | |
Бук, сосна, береза: | | | | |
толщина крайних элементов h1 | 1,5 | 1,5 | 1,5 | 1,5 |
толщина промежуточных элементов h2 | 1,5 | 2 | 2,5 | 3 |
Дуб: | | | | |
толщина крайних элементов h1 | — | 1,5 | 1,5 | 1,5 |
толщина промежуточных элементов h2 | — | 1,5 | 2 | 2,5 |
Таблица 2
Оптимальное количество пропилов в изгибаемых заготовках шириной до 80 мм при толщине крайних элементов h1 =1,5 мм
Толщина заготовки, мм | Количество пропилов при толщине промежуточных элементов h2 , мм | |||
1,5 | 2 | 2,5 | 3 | |
19, 22 | 6 | 5 | 4 | 4 |
25, 28 | 7 | 6 | 5 | 5 |
33 | 10 | 9 | 7 | 7 |
38 | 12 | 10 | 9 | 8 |
43 | 14 | 12 | 11 | 10 |
48 | 15 | 13 | 12 | 11 |
52 | 17 | 14 | 13 | 12 |
Таким образом, сумма крайних и промежуточных элементов составит 2∙1,5+3∙2,5= 10,5 мм, следовательно, толщина пропила должна быть
(22-10,5):4≈3 мм. Минимальное расстояние между пропилами, которое можно получить, составляет 1,5 мм.
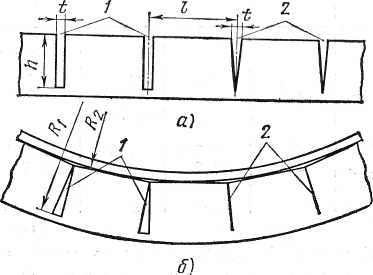
Рис. 4. Прямоугольные и конические пропилы в плитах: а — до изгиба, б — после изгиба; 1 — пропилы прямоугольной формы, 2 — пропилы конической формы
Пропилы в плите делают прямоугольной 1 (рис. 4) или конической 2 формы. Прямоугольные пропилы в изогнутой плите составляют зазоры, которые понижают прочность изделия. Конические пропилы при изгибе плиты плотно смыкаются, отчего соединение получается прочным и малозаметным. Для обеспечения необходимой прочности плит их с обеих сторон до гнутья облицовывают шпоном, фанерой или твердой древесноволокнистой плитой. Глубина пропилов h зависит от толщины плиты и радиуса ее изгиба. Обычно глубина пропилов составляет 2/3. . .3/4 толщины плиты. Расстояние l между пропилами определяют опытным путем в зависимости от назначения плиты, радиуса изгиба и ширины пропила. Для плит, облицованных шпоном, оно должно быть наименьшим, не более 10. . .15 мм. В противном случае на отделанной поверхности в местах изгиба впоследствии будут заметны ребра.
Ширина пропила t зависит от радиуса изгиба плиты и количества пропилов. Эта зависимость может быть выражена следующей формулой:
t = 2πR1/z —2πR2/z = 2π (R1—R2)/z,
где t — ширина пропила; R1 и R2 — радиусы изгиба плиты, мм; z — количество пропилов.
Для получения закругленных деталей в плите после ее облицовывания и шлифования выбирают паз в том месте, где будет изгиб. Паз может быть прямоугольным (см. рис. 3, г) или типа «ласточкин хвост» (см. рис. 3, в). Толщина оставшейся перемычки (дна паза) должна быть равна толщине облицовочного шпона с припуском 1. . .1,5 мм.
В прямоугольный паз вставляют на клею закругленный брусок, а в паз «ласточкин хвост» — полосу шпона. Затем плиту изгибают и выдерживают в шаблоне до схватывания клея.
Для придания изогнутой детали большей прочности в угол с внутренней стороны можно поставить деревянный угольник.
Выпильные детали различных форм изготовляют выпиливанием из предварительно размеченных по шаблону заготовок из древесностружечных и столярных плит, из массива древесины. Эти детали отличаются простотой конструкций, но имеют ряд существенных недостатков по сравнению с гнутыми, гнутоклееными и гнутопропильными.
Прочность выпильных криволинейных деталей, изготовленных из древесины хвойных и лиственных пород, значительно ниже прочности прямолинейных деталей из-за перерезания волокон древесины. Потеря прочности криволинейной детали вследствие изменения угла между действующей силой и направлением волокон значительна. В связи с этим должны быть снижены и допускаемые на деталь напряжения при сжатии вдоль волокон. Например, при угле наклона волокон 45° допускаемые напряжения на деталь должны быть снижены на 50 %. Учитывая это, при конструировании выпильных деталей необходимо стремиться, чтобы кривизна их была наименьшей.
Недостаток выпильных деталей — худшие условия обработки и отделки их криволинейных кромок. В этом случае древесностружечным плитам, имеющим изотропную структуру и не требующим заделки торцов перед облицовыванием кромок, следует отдать предпочтение перед столярными. Кроме того, при изготовлении выпильных деталей получаются значительные отходы.
Технология гнутья. Технологический процесс гнутья древесины состоит из гидродинамической обработки, гнутья и сушки изогнутых деталей для стабилизации приданной формы. В общем, технологическом процессе изготовления изделий место гнутья непостоянно. Чаще всего оно следует непосредственно за раскроем. Технологический процесс происходит так: раскрой на заготовки, гидротермическая обработка заготовок, гнутье, сушка и механическая обработка гнутых заготовок. В некоторых случаях гнутью подвергают уже частично обработанные детали. Например, задние ножки гнутого стула изгибают обычно после обработки на круглопалочных копировальных станках, а после гнутья только шлифуют.
Заготовка материала для гнутья. Раскрой пиломатериалов на заготовки для гнутья возможен различными способами. В некоторых случаях заготовку для гнутья получают путем раскалывания коротких отрезков кряжей (чураков). Получаемая при этом колотая заготовка, как правило, не имеет перерезанных волокон, поэтому при изгибании дает наименьший процент брака. Недостаток такого способа — низкий выход заготовок из кряжа (приблизительно на 20—25 % ниже, чем при выпиливании) и большая трудоемкость этой операции, которую выполняют вручную. На индустриальных предприятиях в большинстве случаев пользуются обычными методами выкраивания заготовок из досок на круглопильных станках.
К качеству древесины заготовок для гнутья предъявляют повышенные требования: рационально раскраивать древесину по предварительной разметке, не допускать в заготовках дефектов, вызывающих брак гнутья. Заготовки необходимо вырезать только из здоровой древесины. Отклонение направления волокон от оси бруска (косослой) не должно превышать 5—10°. При раскрое следует добиваться, чтобы продольные резы шли по возможности вдоль волокон обреза доски.
При обычных методах гнутья в заготовках совершенно не допускаются сучки, в том числе и здоровые, вполне сросшиеся с древесиной. При гнутье с одновременным прессованием сучки допускаются в довольно больших пределах, что резко увеличивает выход заготовок. Нормы допускаемых пороков указываются в технических условиях на изделия. Выкраивать заготовку следует с учетом припусков на последующую обработку. Для гнутья с одновременным прессованием, кроме припуска на механическую обработку, должен учитываться припуск на упрессовку поперек волокон.
Величина упрессовки зависит от породы древесины и в среднем составляет 30—35% для сосны и ели, 50% для пихты, 20 % для лиственницы, 25 % для березы от первоначального размера. Кроме того, следует давать повышенный припуск по длине заготовки.
Гидротермическая подготовка. Гидротермическая подготовка перед гнутьем необходима для того, чтобы повысить пластичность древесины. Под пластичностью понимают свойство древесины изменять свою форму без разрушения под влиянием внешних сил и сохранять эту форму после прекращения действия этих сил.
Пластичность древесины при производственной влажности (6—10%) и комнатной температуре незначительна. В таком состоянии древесина требует для изгибания больших усилий и не допускает больших деформаций. Деформации получаются в основном упругими, т. е. исчезающими после прекращения действия вызвавших их сил.
Пластичность древесины значительно повышается при нагреве во влажном состоянии. Это объясняется тем, что часть веществ, входящих в состав клеток древесины, при нагревании переходит в состояние коллоидного раствора, в результате чего снижается жесткость клеток, а следовательно, и всей массы древесины. Если влажную древесину высушить в деформированном состоянии, то находившиеся в растворенном состоянии коллоидные вещества затвердеют и сохранят приданную заготовке форму.
Опыт показывает, что наилучшие результаты получаются при гнутье древесины влажностью 25—30 %, т. е. близкой к точке насыщения волокна. Как более низкая, так и более высокая влажность неблагоприятны. При меньшей влажности древесина менее пластична. Влажность сверх 25—30 %, не улучшая условий гнутья, удлиняет сроки сушки изогнутых деталей и экономически невыгодна. Излишняя влажность вредна потому, что при изгибе и сжатии древесных клеток находящаяся в них вода может местами разрывать стенки клеток, делая поверхность ворсистой.
Гидротермическая подготовка перед гнутьем чаще всего заключается в пропаривании или проваривании древесины в горячей воде. Недостаток проварки в горячей воде состоит в том, что она ведет к неравномерному увлажнению древесины и перенасыщению водой наружных волокон. Получить путем проваривания равномерную влажность и температуру нагрева всего бруска очень трудно. Поэтому проварка в горячей воде может быть рекомендована только в некоторых случаях, если пропаривание технически затруднено, например при необходимости обработать не всю деталь, а только ее часть (случай загиба носков у лыжных заготовок и т. д.), или если требуется значительное повышение начальной влажности сухих заготовок
.
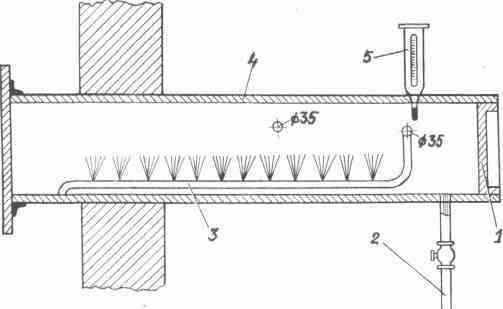
Рис. 63 Разрез пропарочного котла: 1- крышка, 2- спускная труба, 3 - паровая труба, 4- котел, 5 - термометр и манометр
Для проварки пользуются деревянными чанами или металлическими ваннами и баками (лучше с лужеными внутренними поверхностями). Проварочные баки и чаны обычно обогревают паром, пропускаемым по змеевику, уложенному у дна. Температуру воды поддерживают в пределе 90-95 градусов С, не доводя ее до кипения во избежание большого парообразования. Продолжительность проварки при такой температуре колеблется в зависимости от начальной влажности, размеров и породы древесины. Так для буковых заготовок толщиной 40 мм при начальной влажности 15-25 % чивания в воде) и затем на проварку требуется около 1,5 часа.
Пропаривание древесины в атмосфере насыщенного пара получило значительно большее применение, чем проварка. Преимущество пропаривания в том, что оно незначительно изменяет влажность древесины, причем древесина с начальной влажностью ниже точки насыщения волокна повышает свою влажность, а древесина влажностью 50-60 % и выше даже немного подсушивается. Таким образом, пропаривание позволяет нагревать древесину до нужной температуры, мало изменяя ее влажность. Путем предварительного подсушивания или увлажнения (вымачивания в воде) и затем пропаривания можно регулировать влажность древесины и получать ее всегда близкой к оптимальной для гнутья, т. е. около 25—30 %.
Для пропаривания чаще всего пользуются насыщенным паром невысокого давления, около 0,02—0,05 МПа, что соответствует температуре пара 102—105°. Применение пара более высоких давлений сокращает сроки пропаривания, но усложняет оборудование и повышает опасность.
Заготовки цельной древесины пропаривают чаще всего в специальных пропарочных котлах, представляющих собой стальные, горизонтально установленные барабаны небольшой емкости (рис. 63), Длина барабана на несколько сантиметров больше длины пропариваемых деталей. Барабан по диаметру невелик (0,3—0,4 м) и рассчитан на небольшую закладку брусков, которая может быть переработана за 30—40 мин. Увеличение емкости удлиняет время от момента открытия котла до выемки из него последних брусков; это ведет к значительному охлаждению брусков и ухудшает условия гнутья. Выгоднее иметь несколько малых котлов, чем один большой емкости.
Продолжительность пропаривания заготовок зависит от размеров и влажности древесины. При влажности заготовок 7— 10 % значительное влияние оказывает также порода древесины. При влажности, близкой к точке насыщения волокна, необходимые сроки пропаривания почти одинаковы для всех пород,
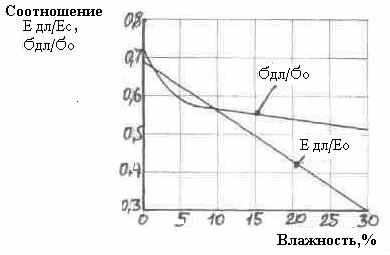
Рис. 64. Зависимость соотношения прочностных показателей древесины от ее влажности
На рис. 64 показано снижение соотношения модуля упругости и предела прочности древесины в зависимости от ее влажности. Соотношение ЕКЛ/Е0 характеризует жесткость древесины. Укладывать бруски в пропарочную камеру рекомендуется с учетом положения бруска при гнутье, т. е. так, чтобы стороны бруска, примыкающие к шине и шаблону, хорошо охватывались паром; боковые же поверхности брусков могут примыкать одна к другой.
Бруски перед гнутьем можно нагревать в течение нескольких минут при помощи электрического тока высокой частоты. Физическая сущность такого нагрева описана ниже. Для повышения пластичности древесину можно пропитывать растворами аммиака, дубильных веществ, фенолов и альдегидами. Растворы алюминиевых и железных квасцов, хлористого магния и другие также повышают ее гигроскопичность. При необходимости гнуть бруски при значительном отношении H/R>1/6 их предварительно пропитывают 40 %-ным раствором мочевины и сушат до влажности 15 %, после чего гнут при температуре 100 °С с последующим охлаждением в изогнутом состоянии до 25 °С для фиксирования формы. Полученные таким образом криволинейные летали при температуре 60—70 °С размягчаются и теряют свою форму. Для устранения этого недостатка пропитывают древесину перед гнутьем в смеси растворов мочевины, формалина, едкого натра и буры. При гнутье пропитанную древесину нагревают также до 100 °С. При этом компоненты раствора в стенках клеток древесины образуют мочевиноформальдегидную смолу, которая в период нагрева и гнутья отверждается окончательно, фиксируя приданную заготовке форму. Недостатком такой подготовки древесины к гнутью является длительность пропитки (3 ч на 1 мм толщины) и необходимость последующей сушки перед гнутьем в мягком режиме, исключающем отверждение образующейся в клетках мочевиноформальдегидной смолы.
Фанеру в случае гнутья на малые радиусы кривизны также можно гидротермически обрабатывать. Фанеру, полученную при склеивании водоупорными клеями, можно проваривать. Фанеру, полученную при склеиваниии белковыми клеями, можно только пропаривать, причем только наружную сторону, подвергающуюся растяжению. Если изгибают только часть заготовки, при выгибании углов, пропаривать следует только ту часть, в которой будет сделан загиб. Для этого пользуются устройством из двух гладких паровых труб, между которыми зажимается заготовка фанеры. Одна из труб имеет ряд очень мелких отверстий для выхода пара на стороне, обращенной к фанере. Таким путем заложенная между трубами фанера прогревается .и одновременно с одной стороны увлажняется. Необходимое время такой обработки перед гнутьем составляет от 5 до 10 мин.
Способы и оборудование для гнутья древесных материалов разнообразны. Однако во всех случаях необходим шаблон, вокруг которого изгибается заготовка и профиль которого определяет форму ее изгиба. Только при использовании точного шаблона можно получить гнутые детали заданной формы.
Применяемые для гнутья массивных брусков гнутарные станки можно разделить на два типа: станки для гнутья на неполную окружность и станки для гнутья на полную окружность.
В станках первого типа бруски с наложенной на наружную сторону стальной шиной изгибают вокруг неподвижного шаблона приложенными усилиями к обоим концам бруска или к одному из концов при неподвижно закрепленном другом конце. Станки такого типа встречаются со съемными и с неподвижно укрепленными обогреваемыми шаблонами. В первом случае после огибания бруска шиной вокруг шаблона концы тины закрепляют на шаблоне при помощи скобы. Шаблон с закрепленным на нем бруском снимают со станка и отправляют в сушильную камеру. Во втором случае брусок также закрепляют на горячем шаблоне при помощи шины и оставляют на нем для подсушивания до закрепления приданной ему формы. В отличие от станков со съемными шаблонами такие станки получили название гнутарно-сушильных. Гнутарно-сушильные станки могут быть двустороннего и одностороннего обогрева. При двустороннем обогреве они имеют вид пресса с обогреваемыми профильными плитами, между которыми зажимают бруски. Станки с односторонним обогревом имеют пустотелый шаблон, обогреваемый паром. Изогнутую и закрепленную на шаблоне заготовку подсушивают на нем.
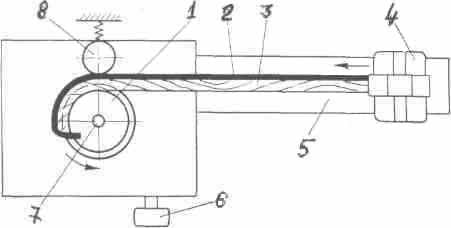
Рис. 65. Гнутье заготовок по замкнутому контуру на гнутарном станке
Недостаток гнутарно-сушильных станков — неравномерность сушки и выдерживание в них заготовок в течение нескольких часов для высушивания до состояния, при котором фиксируется соответствующая форма зоготовок. Это резко снижает производительность станков. Для увеличения производительности гнутарно-сушильных станков целесобразно заготовку перед гнутьем предварительно подсушивать до 20 %, высушивать в станке до 12—15 %, а окончательно досушивать освобожденные из станка заготовки в сушильных камерах.
В станках для гнутья на замкнутый контур бруски изгибают вокруг съемного необогреваемого шаблона. В механизированных станках шаблоны вращающиеся (рис. 65). Съемный шаблон / с прикрепленной к нему шиной 2 надевают на вертикальный вал 7, приводимый в движение от электродвигателя через редуктор 6. Конец шины крепят к каретке 4, скользящей по направляющим 5. После закрепления бруска 3 в шине включают электродвигатель, который, поворачивая вал 7 с надетым шаблоном, как бы навивает на шаблон брусок с шиной. В месте изгиба поставлен ролик 8, плотно прижимающий брусок к шаблону. По окончании гнутья задний конец шины прикрепляют к шаблону при помощи скобы, шаблон с бруском и шиной снимают со станка и отправляют в сушилку, а на станок надевают новый шаблон. На гнутарных станках есть обжимной ролик, прессующий брусок в момент наворачивания его на шаблон, и устройство, регулирующее отход заднего упора шины в процессе гнутья. Оптимальная угловая скорость гнутья станках составляет около 40—50° в секунду.
Во всех случаях гнутья, независимо от используемого этой цели оборудования, необходимо, чтобы вынутые из пропарочного котла или варочного бака бруски подвергались гнутью немедленно. Задержка в гнутье недопустима, потому что остывают в первую очередь наружные слои древесины, которые испытывают наибольшие напряжения.
При гнутье желательно, чтобы в брусках твердых лиственных пород (дуба, ясеня, граба, ильма) расположение годичных слоев совпадало с плоскостью изгиба, т. е. тангентальный распил приходился на боковые стороны бруска или отклонялся лишь на 45—50°.
Расположение годичных слоев перпендикулярно плоскости изгиба может вызвать появление складок на вогнутой стороне. Заготовки из лиственных рассеянно-сосудистых пород (бука, березы ), а также из хвойной древесины, изгибаемые с одновременным прессованием, желательно располагать при гнутье так, чтобы годичные слои были перпендикулярны плоскости изгиба. Желательное расположение годичных слоев для условий гнутья не всегда может быть соблюдено по техническим условиям. Например, у лыж скользящая поверхность должна быть поверхностью радиального распила, иначе износ этой поверхности будет неравномерным.
При гнутье с одновременным прессованием положение деталей следует выбирать таким, чтобы пороки древесины расположились по возможности в растянутой и нейтральной части деталей. Наоборот, при гнутье без прессования, и особенно гнутье без шины, растягиваемая поверхность должна быть более чистой, потому что малейшие дефекты на ней могут стать причиной разрывов и отщепов волокон.
Гнутье фанеры часто осуществляют в шаблонах, состоя из двух частей, т. е. из матрицы и пуансона, между которыми закладывают и выгибают фанеру. Для вдавливания пуансо фанеры в матрицу можно пользоваться винтами, пневматическими и гидравлическими прессами. Если гнутью подлежат большие листы фанеры, то для облегчения веса матрицу и пуансон делают легкой каркасной конструкции, но достаточно жесткой, чтобы она не деформировалась в процессе гнутья.
При расположении волокон в наружном слое перпендикулярно оси шаблона (гнутье вдоль волокон) возможные радиусы загиба фанеры, склеенной белковыми клеями, почти не отличаются от минимальных радиусов загиба цельной древесины. При расположении волокон параллельно к оси шаблона фанера обладает меньшим сопротивлением и допускает изгиб до радиусов примерно в 2 раза меньше, чем при гнутье вдоль волокон. Однако, жесткость получаемой таким образом детали меньше, а на наружной стороне ее часто появляются мелкие долевые трещины, особенно если наружный слой состоит из шпона, имеющего скрытые трещины от недостаточного обжима при лущении. Появление таких трещин делает практически невозможной хорошую отделку, так как в период эксплуатации изделия сужаются или расширяются даже при незначительных изменениях влажности и вызывают растрескивание лежащего на них лакокрасочного покрытия. Поэтому предпочтительнее изгибать фанеру вдоль волокон или под некоторым углом к ним.
Гнутье тонкой фанеры (толщиной 1—4 мм) возможно до малых радиусов кривизны. Изгибание на малые радиусы толстой фанеры и плит (выше 5 мм) требует специальных приемов. Чаще всего делают ряд пропилов на внутренней стороне заготовки, если это допускается конструкцией изделия.
Изогнутые заготовки (вместо с шаблонами и охватывающими их шинами) сушат в сушильных камерах. Конечная влажность гнутоклееных заготовок соответствует производственной влажности, принятой на данном предприятии. Применяемые режимы сушки мало отличаются от режимов сушки пиленых заготовок из тех же пород, а конструкции и системы сушильных камер подобны тем, какие применяют для сушки пиломатериалов.
Высушенные до влажности (обычно ниже 12 %, стабилизирующей форму, заготовки поступают в остывочное отделение, где их охлаждают в течение нескольких часов, затем освобождают от шин и шаблонов и направляют в механическую обработку. Обработка гнутых заготовок, т. е. придание им окончательных размеров и требуемых поверхностей, принципиально не отличается от обработки прямолинейных заготовок.
Базирующим приспособлением, а иногда и столам станков, на которых обрабатывают гнутые заготовки, придают форму, соответствующую форме обрабатываемых заготовок. Последовательность обработки гнутых заготовок на станках аналогична обработке заготовок из пиломатериалов.
Рабочие места в гнутарном цехе включают гнутарный станок или приспособление для гнутья, устройства для гидротермической обработки заготовок, запас необработанных и обработанных заготовок, шин и шаблонов. Схема организации рабочих мест зависит от вида и размера изгибаемых заготовок и оборудования. Однако, во всех случаях рабочие места должны быть организованы так, чтобы пропаренные заготовки можно было подавать на гнутарный станок сразу после выемки их из пропарочного котла, не перенося на большие расстояния и не разворачивая. Пропарочные котлы должны иметь манометры, указывающие давление пара. В цехе должны быть стенные часы, хорошо видные с каждого рабочего места.
Литература.
1.Запрессовочные устройства для производства гнутоклееных деталей, Сахаров М. Д М., 1964
2.Основы гнутья древесины, Манкевич Л. А., Минск, 19613.Примеры и задачи по гидротермической обработке древесины: учеб. пособие. Тупицын В.П. Хабаровск, 1992. -117 c.: ил.
4.Производство гнутой мебели, Леонтьев И. И. и Абухов Л. Г., М. — Л., 1954