М. И. Юликов, # Б. И. Горбунов, Н. В. Колесов Проектирование и производство режущего инструмента москва «машиностроение» 1987 ббк 34. 6 Ю34
Вид материала | Документы |
- Методические указания к курсовому проекту "Расчет и проектирование режущего инструмента", 243.14kb.
- Рекомендации для расчета режущего инструмента при выполнении дипломного и курсового, 204.72kb.
- Физические свойства вакуумно-плазменных покрытий для режущего инструмента, 338.06kb.
- Физический факультет, 286.54kb.
- Методические указания к выполнению курсового проекта по дисциплине "Проектирование, 233.41kb.
- Тема: «Повышение эксплуатационных свойств режущего инструмента из твердого сплава Т15К6, 102.82kb.
- Работы режущего инструмента, основная нагрузка приходится на его рабочую поверхность,, 335.67kb.
- Вестник Брянского государственного технического университета. 2010. №1(25), 124.33kb.
- Курс лекций содержит принципиальные положения и основные исходные сведения для подготовки, 10.16kb.
- Автоматизация выбора режущего инструмента для процесса точения на многофункциональном, 267.6kb.
^ 4.4. АВТОМАТИЗАЦИЯ ТЕХНОЛОГИЧЕСКОЙ ПОДГОТОВКИ ПРОИЗВОДСТВА РИ
В функциональной схеме САПР технолологической подготовки инструмента (САПР ТПИ) укрупненно можно выделить четыре основных этапа (рис. 4.6).
Подготовка исходных данных (1-й этап) заключается в описании характеристик и размеров изготовляемого РИ в виде условных обозначений или чисел по принятой форме. Основой для этого служат рабочий чертеж инструмента и технические требования на
^ 1. Подготовка исходных данных
2. Определение структуры технологического процесса
3. Определение параметров технологического процесса
него (твердость, допуски и др.). Минимальное количество исходных данных достигается в том случае,если проектирование осуществляется на базе типовых техпроцессов для унифицированных РИ различных размеров или исполнений. При этом в исходных данных указываются условное обозначение (код) данного вида РИ и только те его параметры, которые меняются в различных исполнениях.
Формирование выходных документов
Рис. 4.6. Основные этапы САПР ТПИ
Например, в САПР ТПИ Оршанского инструментального завода (ОИЗ) (Д. М. Жихар и др.) обозначение 2321 — 4003.000А—02 соответствует 238
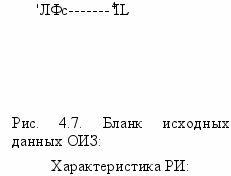
о | ВО | HO | Ш1 |
й | BO | HO | H |
кпо * | a, | ШЗ | |
L | BO | HO | |
1 | BO | HO | |
1, | BO | HO | |
| BO | HO | |
| BO | HO | |
h | Ш4 | HO | |
t | | | |
| | |
KM * | Ш2 | |
ко * | D | |
| | |
ПРТ * | ни | |
РБЛ • | | а |
РБК * | < | |
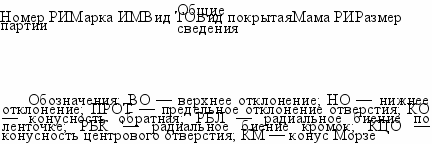
зенкеру из быстрорежущей стали, трехзубому, с коническим хвостовиком и размерами: D — 10,1 мм; d = 9,5 мм; йг = 1,0 мм; L = 160 мм и т. д. (рис. 4.7).
Выбор условных обозначений исходных данных, основанный на классификации и кодировании РИ и оснастки, является весьма ответственной задачей. В настоящее время на различных предприятиях используются разные системы классификации и кодирования технологической оснастки (СККТО). Они основываются
на общесоюзных классификаторах (ОКП, класс 39), общесоюзных нормалях машиностроения (МН74—59 и др.), на множестве имеющихся отраслевых СККТО, либо, наконец, на специальной для данного предприятия СККТО. По мере внедрения и усовершенствования САПРИ, САПР ТПИ, а также АСУП часто возникает необходимость перекодирования, что при большой номенклатуре РИ может превысить реальные возможности предприятий.
В тех случаях, когда изготовляется инструмент, на который на данном заводе отсутствует типовая технология, в исходные данные включаются параметры изготавливаемого режущего инструмента. В САПР ТП «ОИЗ» такие данные вводятся для инструментов, изготавливаемых по чертежам заказчика (см. рис. 4.7). Возможность проектирования техпроцесса изготовления не только унифицированного, но и специального инструмента, предусмотренная в некоторых системах, делает их более универсальными, хотя усложняет алгоритм и программу.
Определение структуры и параметров техпроцесса (2-й и 3-й этапы) осуществляется в большинстве систем сначала для маршрутной, а затем для операционной технологии.
В САПР ТПИ для изготовления круглых и шлицевых протяжек (рис. 4.8), разработанной в ИТК АН БССР, получение маршрутной технологии осуществляется путем выбора операций из комплексного типового технологического процесса (КТТП). Под КТТП понимается набор операций, с помощью которых можно обработать любую данного типа протяжку (круглую, шлицевую) или прошивку. Для получения КТТП базовый ТП, после соответствующего анализа изготовляемых конструкций РИ и технологических возможностей предприятия, дополняется необходимыми операциями и переходами. Комплексный маршрут представляет набор операций Qt (Лй; k = 1, .... т), i = 1, .... /, где Qi — t-я операция; Пк — k-й переход. Поиск технологического маршрута для конкретного инструмента осуществляется методом логического пересечения. На основе таблиц соответствий [таблиц принятия решений (ТПР)], учитывающих конструктивные, технологические и организационные факторы (г/, j = 1, л), в результате логического пересечения заданных условий с ТПР комплексного маршрута (КТПП) определяется совокупность операций Qt и переходов I7h, необходимых для изготовления данного инструмента.
Особенностью системы САПР ТПИ «ОИЗ» является применение различных методов проектирования ТП для унифицированных РИ, изготавливаемых по чертежам «ОИЗ», и для тех же типов РИ, но изготавливаемых по чертежам заказчика (рис. 4.9). В первом случае проектирование осуществляется на основе типовых технологических процессов. При этом по условному обозначению РИ, приведенному в исходных данных, с носителя памяти ЭВМ считывается соответствующий типовой техпроцесс. Его доработка
Действующие
на заводах технологи ческие процессы (ТП) определенной классификационной группировки
^ Анализ структур Wi и ТПМ
Синтез КТТП
i
Формирование ПВД
КТТП с ПВД
^ Анализ структур КТЩиКТТПк+7
Формирование ПВД
Варианты обработки с ПВД
L-
Входные данные
Лтехнико-экономической / оценки вариантов обработки
^ Выполнение техника -экономической оценки
Результаты технако-экономической оценки
Дополнительная нормативная информация
входные данные
этапа проектирования
Модуль проектирования ТП
Конкретные ТП
Рис. 4.8. Схема САПР ТП протяжки (КТТП — комплексный типовой технологический процесс; ПВД —перечень входных данных)
^ САПР ТПИ «ОИЗ»
Обслуживающие подсистемы
Проектирующие подсистемы
^ Подсистема «Диспетчер»
Информационно-поисковая система «Архив»
Подсистемы проектирования техпроцессов унифицированных РИ
на базе типовых ТП
^ Подсистема проектирования техпроцессов специальных РИ на основе индивидуального проектирования
Сверл
Подсистема «Документ»
Зенкеров
Сверл
Зенкеров
Подсистема стыковки с АСУП
—I Разверток
Разверток
Зенковок
Зенковок
— Метчиков
Метчиков
Резцов
Резцов
Рис. 4.9. Структурная схема САПР ТПИ «ОИЗ»
для конкретного размера данного унифицированного инструмента заключается в основном в уточнении технологических переходов в операциях и определении типоразмеров, марок и кодов оборудования и оснастки, режимов обработки и норм времени.
Во втором случае, т. е. для изготовления специальных РИ, для которых на заводе-изготовителе нет маршрута, используется метод индивидуального проектирования ТП. При этом алгоритм проектирования предусматривает наличие формул для определения структуры и параметров техпроцесса с учетом переменных параметров РИ. Основными документами, которые выдаются в результате автоматизированного проектирования (4-й этап), являются маршрутные и операционные карты, выполняемые в соответ
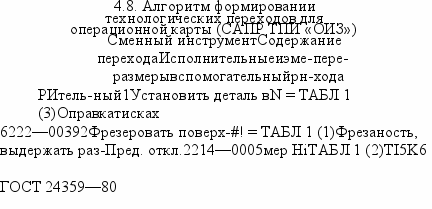
ствии с требованиями ЕСТД. Кроме того, выдаются нормативы трудоемкости и заработной платы, ведомости оснастки и инструмента и др.
В основе работы имеющихся САПР ТПИ лежит использование алгоритмов в форме таблиц принятия решений (ТПР) и решение с их помощью задачи типа «поиск».
Например, алгоритмы формирования технологических переходов в САПР ТПИ «ОИЗ» содержат конкретные значения структуры и параметров операций или формулы (табл. 4.8). «Формула» Ях = ТАБЛ 1 (1) означает, что величина Нг находится в табл. 1 в 1-й графе.
Структурные схемы САПР ТПИ включают обслуживающие и проектирующие подсистемы. Первые предназначены для реализации процесса проектирования с использованием ЭВМ. В САПР ТПИ «ОИЗ» (см. рис. 4.9) обслуживающая подсистема «Диспетчер» дополняет и корректирует базовые данные: добавляет или устраняет операции в типовых процессах, добавляет новые исполнения инструментов и т. п. Информационно-поисковая система «Архив» позволяет производить обработку информации, представленной в форме ТПР: ввод в оперативную память, запись на диск, считывание из информационного фонда, корректировка. Подсистема «Документ» обеспечивает печатание выходной документации: карт техпроцессов, ведомостей и др. Подсистема стыковки САПР ТПИ с АСУП осуществляет формирование информации, используемой в АСУП.
Проектирующие подсистемы обеспечивают получение информации, необходимой и достаточной для формирования всей выходной технологической документации. В САПР ТПИ «ОИЗ» эти подсистемы соответствуют унифицированным или специальным РИ различных типов (см. рис. 4.9).
Информационная база системы «ОИЗ» включает базовые, вспомогательные данные, таблицы параметров, общие и специальные таблицы. Базовые данные отражают все сведения, одинаковые для всех РИ, охватываемых типовым техпроцессом. Например, если все РИ данного типа изготовляются из одного материала или режимы резания (глубина, скорость) рассчитываются по одной формуле, то они являются одинаковыми сведениями для всех РИ. Элементы базовых данных записываются сначала для всей технологической подготовки производства (из заголовка маршрутной карты), затем отдельно по каждой операции. В зависимости от вида технологической операции базовые данные на операцию представляются различным количеством массивов. Например, для операции механической обработки т = 16. В частности, первый массив Мх содержит сведения операции, печатаемые в маршрутной карте: 1 — количество переходов в операции; 2 — номер цеха; 3 — номер участка; 4 — номер операции; 5 — код наименования операции; 6 — количество предложений, описывающих содержание операций; 7 — код модели оборудования; 8 — коэффициент штучного времени; 9 — код профессии; 10 — количество рабочих операций; 11—разряд работы;...; 17 — подготовительно-заключительное время; 18 — штучное время.
Любой массив ^ Mk характеризуется номером k и количеством элементов aki, входящих в массив; каждый элемент aki характеризуется номером k массива и порядковым номером i элемента внутри массива. Для приведенного выше первого массива k = 1; i — = 1-18.
На месте каждого элемента в базовых данных находится число. В зависимости от его значения оно либо соответствует численному значению элемента, либо является его кодом, либо указывает, содержится ли значение данного элемента в таблице параметров или вычисляется по формуле. Для организации вычислений по формуле служат вспомогательные данные, указывающие номер формулы и исходных данных для вычислений.
В общих таблицах собраны все сведения о типовых техпроцессах, имеющие текстовый характер. Каждому типу текста, например, названиям операций, наименованию оборудования или инструмента, соответствуют разные таблицы, например, таблица названия операций:
^ Код Навмевованне операции
1 Токарная
2 Специальная токарная (ЧПУ)
3 Токарио-винторезная
80 Координатно-расточная
Язык общения САПР ТПИ имеет важное значение с точки зрения простоты эксплуатации системы технологом и возможности ее корректировки. В системе «ОИЗ» задания, которые должна выполнить система, описываются в форме утверждений, отражающих содержание этого задания. Такое построение языка делает его достаточно наглядным.
Например, задание, заключающееся в том, чтобы ввести в общие таблицы обозначение режущих инструментов по ГОСТ 24359—80 вместо обозначений по ГОСТ 8529—69, записывается так:
^ КОРРЕКТИРОВКА ОБЩИХ ТАБЛИЦ ЗАМЕНИТЬ СИМВОЛЫ ГОСТ 8529—69 В ТАБЛ ГОСТ 24359—80 КОНЕЦ ЗАДАНИЯ.
Представляет интерес определенный опыт, накопленный в ПНР. Институт обработки резанием ПНР (г. Краков) разработал систему проектирования технологических процессов изготовления концевого инструмента (рнс. 4.10).
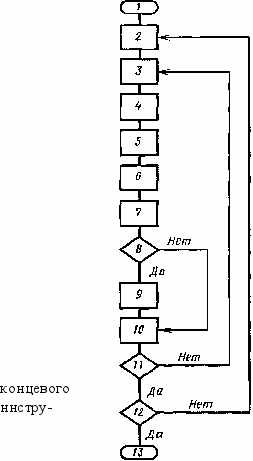
^ 4.5. ОСНОВНЫЕ НАПРАВЛЕНИЯ РАЗВИТИЯ ТЕХНОЛОГИИ ИЗГОТОВЛЕНИЯ РИ
Краткое содержание основных направлений развития технологии изготовления РИ изложено ниже по схеме, представленной на рис. 4.11.
Рис. 4.10. Схема САПР ТПИ мента:
/ — начало проектирования; 2 — выбор операции; 3 — выбор перехода; 4 — выбор рабочего места; 5 — выбор инструмента; 6 — выбор крепления; 7 — выбор измерительных устройств; В — операция формообразования; 9 — выбор параметров резания; 10 — выбор времени обработки; // — верно ли выбраны переходы? 12 — верно ли выбраны операции?; 13 — конец проектирования
Основные направления развития технологии РИ
^ Совершенствование процессов изготовления РИ
Механизация и автоматизация технологии изготовления РИ
^ Заготовительные операции (включая изготовление биметаллического РИ)
Механические операции
Термические операции
Операции шлифования
и затачивания
Операции облагораживания и упаковки РИ
^ Рис. 4.11. Направления развития технологии производства режущего инструмента
Заготовительные операции (включая изготовление биметаллического РИ). Основное направление совершенствования этих операций — изготовление заготовок, приближающихся по форме и размерам к готовым РИ. Это обеспечивает не только снижение расхода дорогостоящих и дефицитных инструментальных материалов и увеличение производительности труда, но и улучшает качество инструмента за счет повышения его прочности и стойкости.
Например, в случае производства сверл используется продольно-винтовой прокат. Внедрение горячего прессования сверл 0 45—80 мм и концевых фрез 0 18—36 мм обеспечивает экономию быстрорежущей стали до 50 % по сравнению с фрезерованием и до 20 % по сравнению с секторной прокаткой сверл. Горячее прессование позволит также более производительно осуществить изготовление спиральных сверл с внутренним подводом СОЖ.
Радиальная штамповка заготовок метчиков (до 75 %) и безоб-лойная штамповка заготовок резцов и насадного РИ (торцовых фрез, долбяков и др.) вместо свободной ковки обеспечивают экономию металла на 25—50 % и снижают трудоемкость последующих токарных операций примерно на 20 %, улучшая структуру металла.
Эффективным направлением экономии быстрорежущей стали является использование технологических процессов изготовления биметаллического режущего инструмента. В этом направлении необходимо и дальше совершенствовать операции сварки и напайки; получать точные сварные заготовки (в том числе с помощью диффузионной сварки); осваивать производство конструкций с клееной режущей частью (развертки, зенкеры, расточные резцовые вставки, мелкомодульные червячные фрезы с твердосплавными 246 пластинами и др.)." осваивать электроконтактную наплавку режущей части таких инструментов, как дисковые отрезные и прорезные фрезы, сегменты отрезных пил, развертки, метчики и др.
Анализ промышленного внедрения технологии склеивания РИ, проведенный во ВНИИ, показал, что возможно сокращение расхода дефицитных инструментальных материалов на 50—80 %, исключение трещинообразования, снижение себестоимости изготовления инструмента на 15—25 % за счет исключения операций отжига, удаления грата и наплывов припоя и др. При переводе паяных и сварных конструкций (там, где это целесообразно) на клееную иногда увеличивается стойкость РИ в 1,3—1,5 раза по сравнению с паяным и сварным за счет сохранения исходных режущих свойств инструментальных материалов.
Использование технологического процесса изготовления биметаллического РИ на основе электроконтактной наплавки. Отличительной особенностью этого процесса является нагрев присадочного материала и приконтактного объема металла заготовки импульсами электрического тока и их совместная пластическая деформация. По данным ВНИИ, суммарное повышение трудоемкости изготовления биметаллического инструмента с использованием данного метода по сравнению с производством цельного РИ не превышает 20 %, а экономия быстрорежущей стали составляет 80—85 %.
В перспективе возможно получение биметаллического РИ из стружки и кусковых отходов быстрорежущей стали. Существующая схема утилизации отходов, включающая два металлургических передела в электродуговых печах (выплавка шихтовых заготовок и выплавка марочного металла), приводит к потере в виде окислов и пыли более 20 % металла, а выход годного составляет 50 %. При переработке каждой тонны стружки (по данным ВНИИ) теряется около 30 кг вольфрама, 30 кг молибдена и 20 кг ванадия. Поэтому желательно использовать электрошлаковую технологию, т. е. непрерывное плавление исходного металла в перегретом шлаке с одновременным наращиванием получаемого слитка. Возможен и другой путь — производство РИ из стружки, исключающий металлургический передел — технология порошковой металлургии. В области совершенствования операции «пайка—закалка» предполагается использование высокопрочных порошковых припоев.
Затачивание РИ алмазными и эльборовыми кругами. Повышение производительности и качества при затачивании РИ связано с использованием кругов из синтетических алмазов и эльбора. Электроалмазное затачивание твердосплавного инструмента обеспечивает повышение производительности в 8—10 раз с одновременным повышением качества обработанной поверхности и повышением стойкости РИ. При шлифовании и затачивании быстрорежущего инструмента удалось обеспечить низкую шероховатость (ниже Ra = 0,32 мкм) в бесприжоговом режиме.
Применение скоростного и глубинного шлифования алмазными и эльборовым кругами позволяет повысить производительность труда при бесцентровом шлифовании и резьбошлифовании на 15—20%, при абразивной отрезке — на 30—45 %, при затачивании сверл из быстрорежущих сталей в 3,—3,5 раза, а при вышлифовке стружечных канавок заменить операцию фрезерования и повысить производительность труда в 4 раза.
Для расширения области применения скоростного и глубинного шлифования необходимы дальнейшие исследования в области использования СОЖ и систем их подачи в зону резания, улучшения качества шлифовальных кругов и станков.
Химико-термическая обработка и нанесение износостойких покрытий. При изготовлении быстрорежущего РИ получили применение различные способы химико-термической обработки.
^ Азотирование, нитрирование — диффузионное насыщение поверхностного слоя (0,2—0,8 мм) изделия в среде аммиака или в расплаве солей на основе карбамида (жидкостное азотирование) при температуре 500—650 °С. В результате азотирования повышаются твердость, износостойкость, коррозионная стойкость и сопротивление усталости.
Борирование — насыщение поверхности изделия из стали бором для повышения твердости (до 1400HV), теплостойкости, износостойкости и коррозионной стойкости.
Алитирование (алюминирование) — насыщение поверхностного слоя изделия алюминием на глубину 0,02—1,2 мм для повышения теплостойкости (красностойкости).
Сульфидирование—поверхностное насыщение стальных деталей серой для повышения износостойкости и предупреждения задиров.
Фосфатирование — химический процесс образования на поверхности стальных изделий тонкого слоя фосфатов (солей фосфатных кислот), предохраняющего от коррозии.
^ Электрофизические методы нанесения покрытий» Поверхность инструмента (режущие пластины) покрывается износостойкими пленками высокопрочных материалов (карбидов или нитридов титана, карбидов молибдена и др.) методом конденсации вещества из плазменной фазы в условиях ионной бомбардировки или газофазным методом (применяется для покрытия твердосплавных пластин).
^ В последние годы получили распространение ионные методы нанесения износостойких покрытий; реактивный электронно-плазменный (РЭП), катодного расплавления, метод конденсации с ионной бомбардировкой (КИБ).
^ В нашей стране проводятся широкие исследования, направленные на создание установок и совершенствование метода КИБ.
В ближайшее время необходимо решать задачу повышения стойкости быстрорежущего инструмента (в том числе безвольфрамовых с доведением их по качеству до уровня вольфрамосодержа-щих материалов) в 3—4 раза за счет нанесения многослойных износостойких покрытий. Аналогичная задача существует для инструмента, оснащенного пластинами из минералокерамики и синтетического сверхтвердого материала на основе кубического нитрида, а в перспективе для РИ из углеродистых и легированных сталей.
Расширение области применения упрочнения режущих элементов инструмента поверхностным пластическим деформированием (ППД). Помимо упрочнения все способы ППД снижают шероховатость, улучшают микрорельефную структуру, в отдельных случаях используются для скругления режущих кромок. Одним из способов поверхностного деформирования твердосплавных пластин является виброабразивная и дробеструйная обработка.
Виброабразивная обработка повышает стойкость пластин при фрезеровании в 1,2—2 раза, при точении — в 1,5 раза. Дробеструйное упрочнение наиболее эффективно для крупных РИ, работающих с большими подачами.
Для быстрорежущего закаленного РИ упрочнение осуществляется с помощью алмазного выглаживания, обкатки шариком, ультразвука. Например, алмазное выглаживание протяжек повышает в 2—3 раза их стойкость по сравнению со шлифованными и на 20—40 % по сравнению с полированными зубьями.
Термомеханическое упрочнение используется в процессе изготовления РИ с использованием методов пластического деформирования, совмещения пластической деформации с закалкой (например, при изготовлении сверл методом секторного и продольно-винтового проката).
Механизация и автоматизация технологии изготовления режущего инструмента. Автоматизируются заготовительные операции, например, производится полная автоматизация на базе групповых агрегатов и автоматических линий на операциях сварки, правки и снятия сварочного грата (опыт завода им. Воскова с использованием машин мод. МИ-086 и СИ-049; обработка заготовок концевого РИ на автоматической линии АЛ-14). Автоматизируются не только загрузка и обработка, но и выгрузка и укладка (автоматические укладчики типа мод. СИ-050), используются прогрессивные виды оснастки (резинометаллические цанги и втулки, торцовые поводковые патроны с заклинивающимися ведущими элементами, автоматизированные приспособления с полиуретано-выми зажимными элементами, групповые магнитные сепараторы и кассеты для обработки многогранных пластин, приспособления-спутники для работ с точным позиционированием и т. д.).
Используются станки с ЧПУ, в том числе многоцелевые станки. Опыт внедрения станков с ЧПУ при изготовлении РИ показал, что производительность оборудования возрастает до 1,5 раз, а производительность труда—до 3 раз.
Основная область применения станков с ЧПУ — это обработка: а) державок сборных резцов на сверлильно-фрезерных станках мод. 6Р11МФЗ, ЛФ-260МФЗ; б) корпусов сборных инструментов (фрезы торцовые, головки резьбонарезные) на сверлильно-фрезеряых етанках мод. 2204МФ4; в) концевого инструмента (фрезы, зенкеры, развертки) на токарных станках мод. 16Б16ФЗ, 16К20ФЗ и шлифовальных станках мод. ВЗ-201ФЗ, ВЗ-212Ф2, ВЗ-213ФЗ; г) насадного инструмента (шеверы, долбяки, фрезы, зенкеры и развертки) на токарных станках мод. 16К20ФЗ и шлифовально-заточных мод. ЗБ662ВФ2, ВЗ-210Ф2 и др.; д) круглых и шлицевых протяжек и долбяков.
Для эффективного использования станков с ЧПУ необходимо провести научно-исследовательские работы в следующих направлениях: а) исследование статических и динамических погрешностей технологической системы при контурной токарной обработке в центрах деталей типа протяжек, при фрезеровании корпусов сборного концевого инструмента; б) исследование возможности компенсации погрешностей технологической системы и повышение производительности обработки РИ на станках с ЧПУ с использованием адаптивного управления; в) разработка новых технологических процессов изготовления РИ с учетом максимального использования возможностей станков с ЧПУ; г) разработка предложений по повышению технологичности конструкций режущего и вспомогательного инструментов применительно к обработке на станках с ЧПУ.
Автоматические линии и агрегаты для термической обработки РИ используются для закалки, отпуска, химического очищения. Для консервации и упаковки РИ необходимо расширить область применения автоматов, полуавтоматов и автоматических линий для консервации и упаковки всех видов РИ в крупносерийном и массовом производстве.
^ Автоматизация проектирования технологических процессов изготовления режущего инструмента. Исследованием проблемы автоматизации проектирования технологических процессов изготовления РИ, главным образом, занимается ИТК АН БССР (г. Минск). Здесь эта проблема была частью разрабатываемой автоматизированной системы инструментальной подготовки производства.
Первые публикации по автоматизации проектирования технологических процессов изготовления РИ были на примере протяжек, в которых была сделана попытка формализовать процесс анализа типовой технологии, производимой технологом.
При реализации наивысшего уровня автоматизации предполагается объединение в единое целое процессов конструирования, разработки технологии изготовления РИ и осуществление процесса изготовления в автоматизированном цикле. На этом уровне имеется возможность осуществления наиболее полной оптимизации принимаемых решений при разработке техпроцесса в связи с наиболее глубоким учетом всех факторов — от конструкции РИ до реальных условий его изготовления.
^ Совершенствование управления производством — важная народнохозяйственная задача. Технической основой ее решения в различных отраслях, в том числе в инструментальном производ-
стве, является использование ЭВМ вплоть до создания автоматизированных систем управления (АСУП). Такие системы позволяют получить оперативную, полную и достоверную информацию, что является объективной предпосылкой для улучшения показателей производственно-хозяйственной деятельности предприятия. Одним из первых предприятий страны, на котором в 1963 г. начали проводиться работы по созданию АСУП, является завод режущих инструментов им. М. И. Калинина «Фрезер». В 1975 г. на заводе была введена в эксплуатацию в полном объеме проекта третья очередь системы «АСУ—Фрезер».
По функциональной структуре она включает следующие подсистемы: 1) управления технической подготовкой производства (конструкторско-технологические расчеты); 2) технико-экономического планирования, в том числе мощности цехов, плановой численности рабочих, себестоимости продукции; 3) оперативного управления основным производством, включающую данные о наличии материалов на складе, о движении изделий на всех стадиях технологического процесса, о составе и размещении незавершенного производства; 4) управления материально-техническим снабжением, расчета потребности в материалах, контроля за уровнем материальных ресурсов по системе максимум—минимум; 5) управления сбытом готовой продукции, комплектации заказов, организации их доставки, финансового оформления заказов; 6) бухгалтерского учета по предприятию в целом и по отдельным цехам, включая учет труда и заработной платы, определение расходов на материалы, на собственный и покупной инструмент и др.
Каждая подсистема «АСУ—Фрезер» обеспечивает обработку информации, связанной с определенной функциональной службой предприятия. За основу оптимизации технико-экономического планирования производства принят критерий максимального использования технологического оборудования, что обеспечивает в условиях инструментального производства наибольшую производительность при минимальной себестоимости.
Эффективность АСУ зависит не только от ее структуры, стоимости и научно-технического уровня, но и от оптимальности решений, принимаемых на основе информации. Благодаря АСУ возможности для более оптимального решения задач управления значительно расширяются. На машиностроительных предприятиях автоматизация управления инструментальным хозяйством (ИНХ) может включать различный объем задач — от отдельных задач, входящих в подсистемы АСУП, до самостоятельных комплексных систем АСУ ИНХ. Опыт разработки АСУ ИНХ показал, что затраты на ее создание при минимальном количестве решаемых задач около 12—15 для среднего завода составляют 150— 200 тыс. руб. Поэтому создание АСУ ИНХ экономически целесообразно не для всех предприятий. Одним из основных показателей, характеризующих целесообразность внедрения АСУ ИНХ, является объем потребляемой оснастки, который должен составлять около 1 млн. руб. в год и более.
5. ПРИЛОЖЕНИЯ ^ ПРИЛОЖЕНИЕ I. КОДЫ ОБРАБАТЫВАЕМЫХ МАТЕРИАЛОВ (ОМ)
Наименование ОМ
Марки (примеры)
МПа, или НВ
Алюминий и его сплавы деформируемые мягкие Деформируемые средней прочности Деформируемые высокой прочности Литейные высококремнистые Литейные с содержанием Si «g: 5 % Бронза
^ Литейная оловянная Деформируемая оловянная
Безоловянная средней твердости Безоловянная твердая
Безоловянная высокой твердости Безоловянная высшей твердости Латунь
Деформируемая мягкая
Деформируемая средней твердости Деформируемая твердая
^ Литейная мягкая