Методические указания к лабораторной работе №2 Для студентов неинженерных специальностей
Вид материала | Методические указания |
- Методические указания к лабораторной работе по курсу «Информатика» для студентов всех, 254.72kb.
- Методические указания к лабораторной работе по органической химии для студентов специальностей, 227.51kb.
- Методические указания к лабораторной работе по курсу «Информатика» Основы алгоритмизации, 441.82kb.
- Методические указания к выполнению лабораторной работы №10 для студентов очной формы, 240.19kb.
- Методические указания к компьютерной лабораторной работе №005мтд, 275.63kb.
- Методические указания к выполнению лабораторной работы №12 для студентов очной и заочной, 222.24kb.
- Методические указания по выполнению лабораторной работы Уфа 2009, 528.08kb.
- Методические указания к лабораторной работе №3 по дисциплине «Периферийные устройства», 217.77kb.
- Методические указания к выполнению лабораторной работы №6 для студентов всех форм обучения, 197.64kb.
- Методические указания к лабораторной работе Составитель Т. Е. Дизендорф, 166.23kb.
Министерство сельского хозяйства
и продовольствия Республики Беларусь

департамент образования, науки и кадров

учреждение образования
"Белорусская государственная
сельскохозяйственная академия"

Кафедра технологии и организации механизированных
работ в растениеводстве
механизмы и системы
двигателей внутреннего сгорания
Методические указания
к лабораторной работе №2
Для студентов неинженерных специальностей
Горки 2004
Министерство сельского хозяйства
и продовольствия Республики Беларусь

департамент образования, науки и кадров

Учреждение образования
"белорусская государственная
сельскохозяйственная академия"

Кафедра технологии и организации механизированных
работ в растениеводстве
механизмы и системы
двигателей внутреннего
сгорания
Методические указания
к лабораторной работе №2
Для студентов неинженерных специальностей
Горки 2004
Одобрено методической комиссией факультета технического обеспечения процессов с.-х. производства 8.04.2003.
Составили кандидаты техн. наук Г.А. валюженич, а.е. улахович,
О.П. Лабурдов.
Компьютерный набор выполнила А.М. Валюженич.
УДК 631.3.004.5(075.8)
Механизмы и системы двигателей внутреннего сгорания: Методические указания / Белорусская государственная сельскохозяйственная академия; Сост. Г.А.Валюженич, А.Е.Улахович, О.П. Лабурдов. Горки, 2004. 32 с.
Рассмотрены вопросы назначения, общего устройства и принципа действия механизмов и систем двигателей внутреннего сгорания.
Для студентов неинженерных специальностей.
Таблиц 1. Рисунков 13.Библиогр 5. Приложений 1.
Рецензент канд.техн.наук, доцент А.А.РУДАШКО.
Составление. Г.А. Валюженич,
А.Е. Улахович, О.П. Лабурдов, 2004
Учреждение образования
«Белорусская государственная
сельскохозяйственная академия», 2004
Цель работы: 1. Изучить общее устройство и принцип действия кривошипно-шатунного и газораспределительного механизмов, расположение и взаимодействие их основных составных частей. 2. Усвоить назначение, общее устройство и принцип работы систем питания, охлаждения, смазки и пуска двигателей внутреннего сгорания.
- Кривошипно-шатунный механизм
К
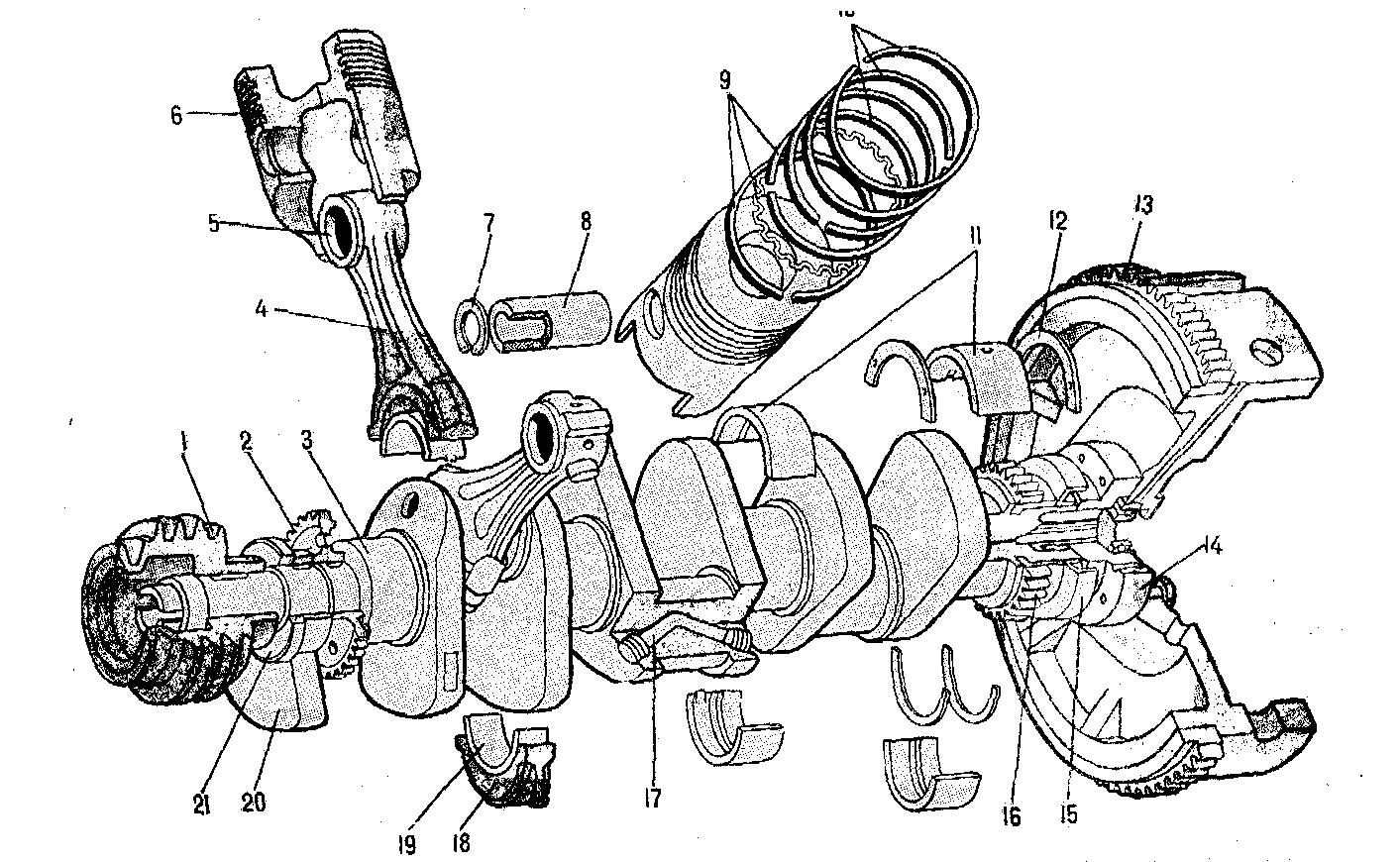
Рис. 1. Кривошипно-шатунный механизм дизеля СМД-60: 1 – шкив коленчатого вала; 2– зубчатое колесо привода масляного насоса;
3 – коленчатый вал; 4 – шатун; 5 – втулка верхней головки шатуна;
6 – поршень; 7 – стопорное кольцо; 8–поршневой палец; 9–поршневые маслосъемные кольца; 10–поршневые компрессионные кольца; 11– вкладыши коренных подшипников; 12– упорное полукольцо;
13–маховик; 14–фланец коленчатого вала; 15–задний маслоотражатель; 16– зубчатое колесо привода механизма газораспределения;
17–масляная полость шатунной шейки; 18– крышка шатуна;
19– вкладыш шатунного подшипника; 20– передний противовес;
21 – передний маслоотражатель.
ривошипно-шатунный механизмов (рис.1) на такте расширения (рабочий ход) преобразует прямолинейное поступательное движение
поршня во вращательное движение коленчатого вала, а на остальных тактах – вращательное движение коленчатого вала – в прямолинейное возвратно - поступательное движение поршня. Принцип этого преобразования станет понятен при подробном рассмотрении схемы сил, действующих на детали кривошипно-шатунного механизма.
В
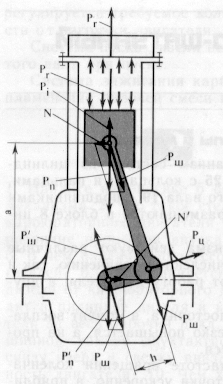
Рис.2. Силы и моменты, действующие на КШМ.
о время работы на детали механизма действуют различные силы и моменты, изменяющиеся как по численному значению, так и направлению. Одни из них обеспечивают работу двигателя, а другие вызывают изнашивание его деталей.
Сила давления газов Рг (рис.2) непостоянна: в момент воспламенения (взрыва) рабочей смеси она резко повышается, а на протяжении рабочего хода плавно снижается. Давление газов зависит, в первую очередь, от количества топлива, сжигаемого за цикл, и некоторых других причин.
Силы инерции. При равномерной частоте вращения коленчатого вала поршень отходит от мертвой точки ускоренно, а приближается к ней замедленно. Поступательно движущиеся детали (поршень, палец и верхняя часть шатуна), получив разгон и стремясь сохранить свою скорость, сопротивляются ее изменению.
В результате неравномерного движения деталей кривошипно-шатунного механизма в нем действуют силы инерции. Они тоже непостоянны: когда скорость движения поршня уменьшается, силы инерции направлены в сторону движения, а когда скорость увеличивается, то в сторону, противоположную движению. Сила инерции зависит от массы поступательно движущихся деталей, колебаний частоты вращения вала, радиуса кривошипа и тоже изменяется по мере перемещения поршня. В мертвых точках сила инерции Рi достигает наибольшего значения. В в. м. т. она направлена вверх, а в н. м. т. – вниз. Поэтому в начале рабочего хода поршня Рi всегда противодействует силе Рг. Примерно в середине пути поршня его скорость наибольшая, а сила инерции доходит до нуля.
С
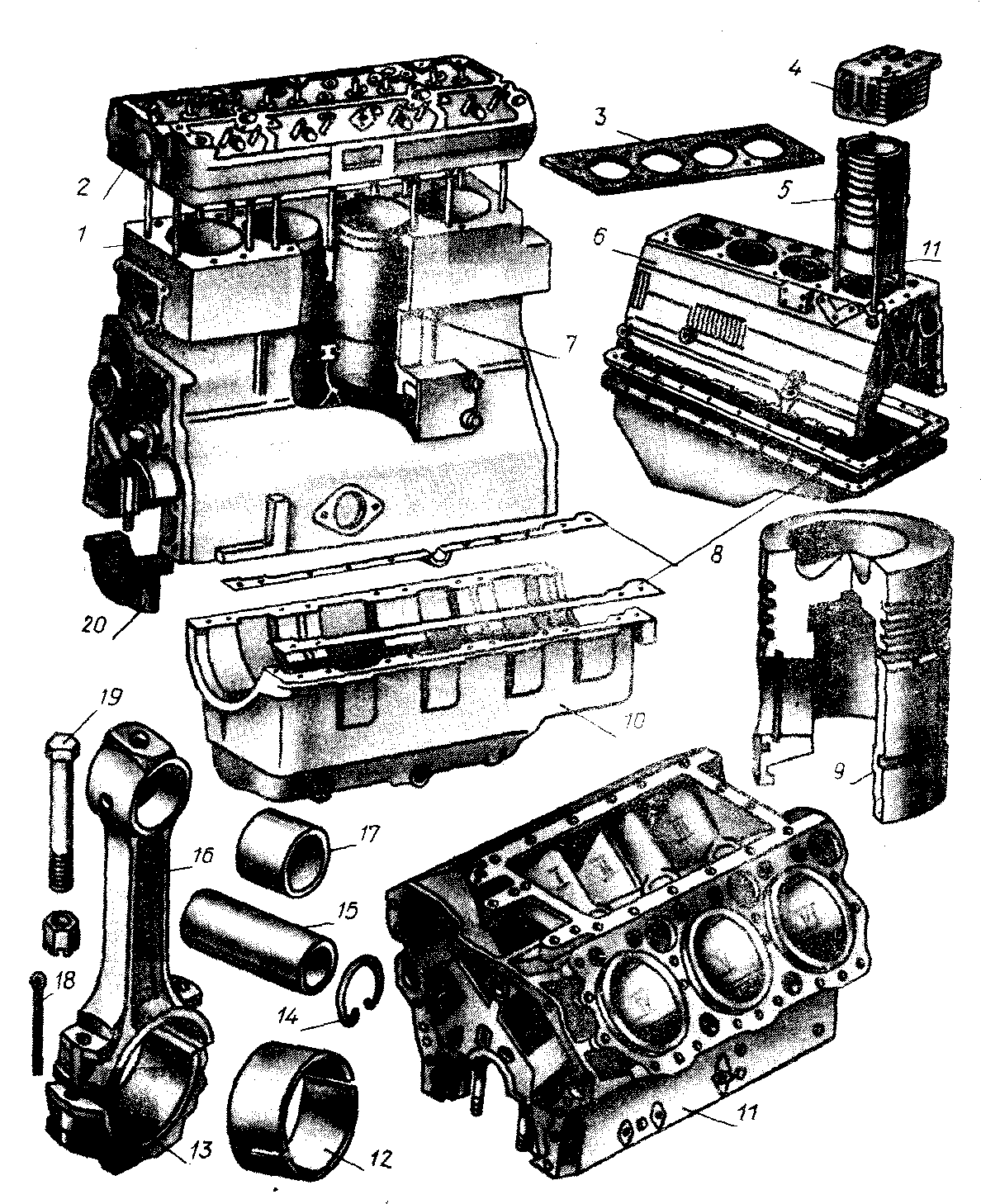
Рис 3. Детали двигателя: 1,11 – блок-картеры; 2, 4 – головки цилиндров; 3, 8 – прокладки; 5 – цилиндр; 6 – картер; 7 – гильза; 9 – поршень; 10 – поддон; 12 – вкладыши; 13 – крышка шатуна; 14 – стопорное кольцо; 15 – поршневой палец; 16 – шатун; 17 – втулка; 18 – шплинт, 19 – болт, 20 – коренной подшипник.
оставляющие сил инерции и давления газов (рис. 3). Обе силы, слагаясь вместе или вычитаясь одна из другой, дают равнодействующую силу Рп (большую или меньшую, чем сила Рг). Эта сила раскладывается на две: силу Рш, направленную вдоль шатуна, и силу N, направленную перпендикулярно стенке цилиндра.
Сила N прижимает поршень к цилиндру, а сила Рш, воспринимаемая шатунной шейкой коленчатого вала, умноженная на плечо h, создает кру тящий момент, под действием которого вращается коленчатый вал.
При вращении вала в нижней части шатуна возникает центробежная сила Рц, которая прямо зависит от массы вращающихся частей, частоты вращения и радиуса кривошипа. От ее действия увеличивается изнашивание подшипников и шеек вала. Центробежная сила может быть уравновешена противовесами коленчатого вала.
Сила Рш, приложенная к коренным шейкам вала, передается его подшипникам и корпусу двигателя. Эту силу можно разложить на две составляющие: N' и Рп.
Сила N' равна N, но направлена в противоположную сторону. Обе силы на плече а создают момент, называемый обратным, так как он стремится вращать двигатель в сторону, противоположную вращению коленчатого вала. Под действием этого момента ослабляются крепления опор двигателя на остове машины.
Сила Рп' передается через коренные подшипники вала корпусу двигателя.
Маховик под действием сил инерции получает разгон и при этом накапливает энергию вращательного движения. Когда силы давления Рг перестают действовать на поршень, его поступательное движение обеспечивается за счет накопленной маховиком энергии, а направление сил изменяется на противоположное.
Назначение деталей КШМ состоит в следующем.
Цилиндр 5– основная часть двигателя, внутри которой сгорает топливо. Цилиндр изготавливают в виде отдельной отливки, укрепляемой на чугунной коробке – картере 6, или в виде сменной гильзы 7, вставляемой в блок цилиндров. Материалом для изготовления цилиндров и гильз служит чугун. Внутреннюю поверхность цилиндров и гильз, называемую зеркалом цилиндра, делают строго цилиндрической формы и подвергают шлифовке и полировке. Число цилиндров или гильз у одного двигателя может быть различно: один, два, три, четыре, шесть и больше.
Блок цилиндров может быть изготовлен так, что цилиндры будут расположены в один или в два ряда под углом в 90°. Блок цилиндров и картер снизу закрыты поддоном 10 и уплотнены прокладками 8. Цилиндры сверху закрыты головкой 2 или 4 (в зависимости от конструкции двигателя), уплотняемой металлоасбестовой прокладкой.
Поршень 9, устанавливаемый внутри цилиндра, сжимает свежий заряд воздуха и воспринимает давление расширяющихся газов во время горения топлива и передает это давление через палец и шатун на коленчатый вал, заставляя его вращаться. Поршень отливается из алюминиевого сплава. На боковых стенках поршня делают два прилива – бобышки с отверстиями, в которые вставляется поршневой палец 15, соединяющий поршень с шатуном 16. В днище поршня сделана специальная камера, способствующая лучшему перемешиванию топлива с воздухом.
Поршень во время работы сильно нагревается (до 350 °С) и при этом расширяется. Во избежание заклинивания поршня в цилиндре его делают несколько меньшего диаметра, чем цилиндр, создавая тем самым между ними зазор 0,25...0,40 мм.
Поршневые кольца. Поскольку между поршнем и цилиндром имеется зазор, то через него могут проходить из камеры сжатия в картер газы. Из картера в камеру сжатия попадает и там сгорает смазочное масло, при этом увеличивается его расход.
Для устранения подобных явлений на поршень в специальные канавки надевают пружинные чугунные кольца. Диаметр колец делают немного больше диаметра цилиндра, в котором они будут работать. Чтобы такое кольцо можно было вставить в цилиндр, в нем сделан вырез (или, как его еще называют, замок), позволяющий сжать кольцо перед постановкой в цилиндр. Такое кольцо, будучи вставленным в цилиндр, стремится занять первоначальное положение и поэтому плотно прилегает к стенкам цилиндра, закрывая при этом своим телом зазор между поршнем и цилиндром.
Во время работы двигателя кольца, кроме уплотнения, обеспечивают распределение смазки по цилиндру, предотвращают попадание масла в камеру сгорания, уменьшая тем самым расход его, а также отводят теплоту от сильно нагретого поршня к стенкам цилиндра.
По назначению кольца бывают двух типов: компрессионные – уплотняющие (их обычно ставят по три-четыре) и маслосъемные (одно-два).
Компрессионные кольца воспринимают силы давления газов, причем наибольшую нагрузку до 75 % давления несет первое кольцо. Чтобы предохранить поршень от повышенного износа, у некоторых двигателей в первую канавку поршня устанавливают стальную вставку, а для уменьшения износа кольца его цилиндрическую поверхность покрывают пористым хромом. Остальные кольца, воспринимающие меньшую нагрузку – 20 и 5 % сил давления, хромом не покрывают.
Маслосъемные кольца чаще всего делаю коробчатого сечения с прорезями. Благодаря этому усилие прижатия кольца к стенке цилиндра передается через два узких пояска, что увеличивает удельное давление кольца. Кроме того, узкие пояски кольца лучше снимают излишнее масло со стенок цилиндра или гильзы при движении поршня вниз.
На дне канавки маслосъемного кольца сделаны отверстия в поршне, через которые отводится масло, собранное со стенок цилиндра.
для того чтобы увеличить упругость маслосъемных колец, у некоторых двигателей в зазор между кольцом и канавкой устанавливают стальной расширитель.
Шатун 16 соединяет поршень с коленчатым валом. Его штампуют из стали. Он состоит из верхней и нижней головок и стержня. Верхняя, неразъемная головка служит для соединения с поршнем, в нее вставляется поршневой палец. Для уменьшения трения между пальцем и шатуном в верхнюю головку запрессовывают бронзовую втулку 17. Нижняя, разъемная головка имеет крышку 13 и охватывает шейку коленчатого вала. Чтобы уменьшить трение шатуна о шейку вала, в нижнюю головку и крышку устанавливают вкладыши 12 – стальные пластины, у которых поверхность, прилегающая к шейке вала, покрыта тонким слоем свинцовистой бронзы или специальным алюминиевым сплавом.
Нижнюю головку шатуна и ее крышку соединяют шатунными болтами 19, гайки которых после затяжки шплинтуют.
Поршневой палец 15, соединяющий шатун с поршнем, изготовляют из стали, а наружную поверхность подвергают термической (цементации и закалке) и механической (шлифовке) обработке.
Палец во время работы двигателя может перемещаться в верхней головке шатуна и бобышках поршня в небольших пределах, поэтому его называют плавающим. Для того чтобы палец во время работы не вышел из поршня и не поцарапал зеркало цилиндра, ограничивают перемещение пальца в осевом направлении, устанавливая в бобышках (приливах) поршня стопорные пружинные кольца 14, которые не препятствуя пальцу поворачиваться в бобышках и головке шатуна, не позволяют ему перемещаться за пределы поршня.
Коленчатый вал воспринимает через шатуны силы расширяющихся газов, действующих на поршни, и превращает эти силы во вращательное движение, которое затем передается трансмиссии трактора. От коленчатого вала также приводятся в движение другие устройства и механизмы двигателя (газораспределительный, топливный и масляный насосы и др.). Коленчатый вал штампуют из стали или отливают из специального чугуна. Коленчатый вал состоит из следующих частей: коренных, или опорных шеек, на которых он вращается в коренных подшипниках 20, шатунных шеек, которые охватывают нижние головки шатунов, щек, соединяющих шейки между собой, и фланца, предназначенного для крепления маховика.
Чтобы продлить срок службы коленчатого вала, поверхности шеек подвергают термической обработке – закалке.
Маховик представляет собой массивный диск, отлитый из чугуна, он укрепляется на фланце заднего конца коленчатого вала.
Маховик во время работы двигателя накапливает кинетическую энергию, уменьшает неравномерность частоты вращения коленчатого вала, выводит поршни из мертвых точек и облегчает работу двигателя при разгоне машинно-тракторного агрегата и преодолении кратковременных перегрузок.
На маховике укрепляется зубчатый венец, через который специальными устройствами вращают коленчатый вал при пуске двигателя.
2. Газораспределительный механизм
В
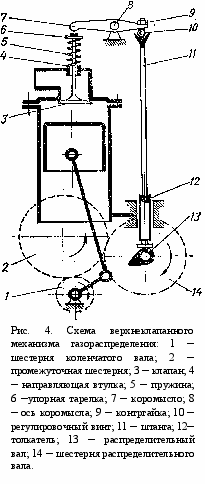
В пусковых двухтактных двигателях П-10УД и П-350 газораспределение золотниковое. Оно осуществляется поршнем.
Механизм газораспределения с подвесными клапанами. Коленчатый вал приводит во вращение через зубчатые колеса распределительный вал 13 (рис.4). При повороте распределительного вала выступ кулачка поднимает толкатель 12, а вместе с ним и штангу 11. Нижний конец ее упирается в пяту толкателя, а верхний – в регулировочный винт 10 коромысла 7, установленного на оси 8. Коромысло, поворачиваясь вокруг оси, бойком отжимает клапан 3 вниз. При этом открывается канал головки цилиндров, а предварительно сжатые пружины 5 (чтобы удержать клапан в закрытом положении) еще больше сжимаются. Стержень клапана движется в направляющей втулке 4. Клапан открыт полностью, когда толкатель находится на вершине кулачка.
При дальнейшем повороте распределительного вала толкатель начинает постепенно опускаться, а клапан под действием пружин движется вверх. Когда выступ кулачка выходит из-под толкателя, давление на клапан прекращается и он под действием пружин плотно закрывает отверстие канала (гнездо) в головке цилиндров.
При обратном движении клапана коромысло, штанга и толкатель перемещаются в первоначальное положение.
3. Система питания
3.1. Общие понятия, виды топлива
Преобразование химической энергии топлива, вводимого в цилиндры двигателя внутреннего сгорания, в тепловую энергию осуществляется путем его сжигания – окисления. Для того чтобы этот процесс протекал наиболее совершенно и чтобы теплоту, заключенную в топливе, можно было использовать для работы двигателя, необходимо обеспечить быстрое и возможно полное сгорание топлива. А для этого жидкое топливо, на котором работают двигатели, следует предварительно соответствующим образом подготовить. Подготовка заключается в том, что топливо вначале тщательно распыливают при помощи специальных устройств, затем испаряют и наконец испаренное топливо перемешивают с воздухом, содержащим в себе кислород. Полученная смесь испаренных паров топлива и воздуха называется топливовоздушной смесью, в цилиндрах двигателя она обеспечивает быстрое и полное сгорание топлива.
Рассмотрим составные части топливовоздушной смеси.
Топливо. Для дизелей в качестве основного топлива применяется дизельное и как дополнительное – керосин для работы трактора при низких температурах окружающего воздуха.
Дизельное топливо представляет собой слегка маслянистую жидкость желтоватого цвета плотностью 830... 860 кг/м3, полученную из нефти путем прямой перегонки или более сложных, вторичных процессов переработки нефти.
Дизельное топливо выпускается промышленностью трех марок: Л (летнее) для применения выше 0°С, 3 (зимнее) – от -20 до 0°С и А (арктическое) – от -50 до -20 °С. Каждое из перечисленных топлив, кроме того, выпускается двух видов в зависимости от содержания в нем примесей серы: первый вид – 0,2 % серы, второй – 0,4 % серы (арктическое 0,5 %).
Показателем самовоспламеняемости дизельного топлива служит цетановое число, численно равное содержанию цетана (в объемных процентах) в смеси с альфаметилнафталином, при котором самовоспламеняемость этой смеси и сравниваемого с ней испытуемого топлива одинакова. Цетановое число определяют на специальной одноцилиндровой установке. Установлено, что с повышением цетанового числа до 60...65 процесс сгорания топлива протекает более плавно, двигатель работает экономичнее и не так жестко, как на низкоцетановом топливе. При повышении цетанового числа улучшаются пуск дизеля при пониженной температуре окружающего воздуха. Дальнейшее увеличение цетанового числа ухудшает работу дизеля.
Для карбюраторных двигателей применяется бензин – бесцветная жидкость плотностью 700... 780 кг/м3, легко испаряющаяся и самовоспламеняющаяся при температуре 510 °С. При определенных условиях способна к взрывному сгоранию – детонации, вызывающей разрушение деталей двигателя.
Склонность данного бензина к детонации оценивается октановым числом — условной величиной, определяемой долей (в процентах) изооктана в эталонном топливе, которое по своим антидетонационным свойствам равнозначно бензину. Это число входит в марку бензина.
Воздух. Чистый атмосферный воздух представляет собой смесь различных газов: азота, кислорода, водорода и других, причем кислорода в нем содержится около 23 % по массе.
В результате механического воздействия на почву при движении тракторов почва размельчается в порошок, образуя дорожную пыль. Наибольшее ее количество может достигать в сухую погоду 2,5 г/м3, а в условиях пустынь – 6 г/м3. Основная составная часть пыли – окись кремния 5102 (кварц), содержание его в песчаных почвах 92...98%, в сероземах – 74, в черноземах – 68 и красноземах – 41 %. Поверхностная твердость пылинок окиси кремния значительно превышает твердость металлов, из которых сделаны детали двигателя.
Если учесть, что трактор средней мощности пропускает через свои цилиндры до 200 м3 воздуха в час, то количество пыли, которое может попасть в двигатель даже при ее содержании в воздухе до 2 г/м3, будет составлять 400 г в час, или 4 кг за 10-часовой рабочий день. Поэтому работа трактора без очистки воздуха, поступающего в цилиндры, недопустима. Чем чище воздух, тем дольше без ремонта работает двигатель трактора.
3.2. Устройство и действие системы питания
С
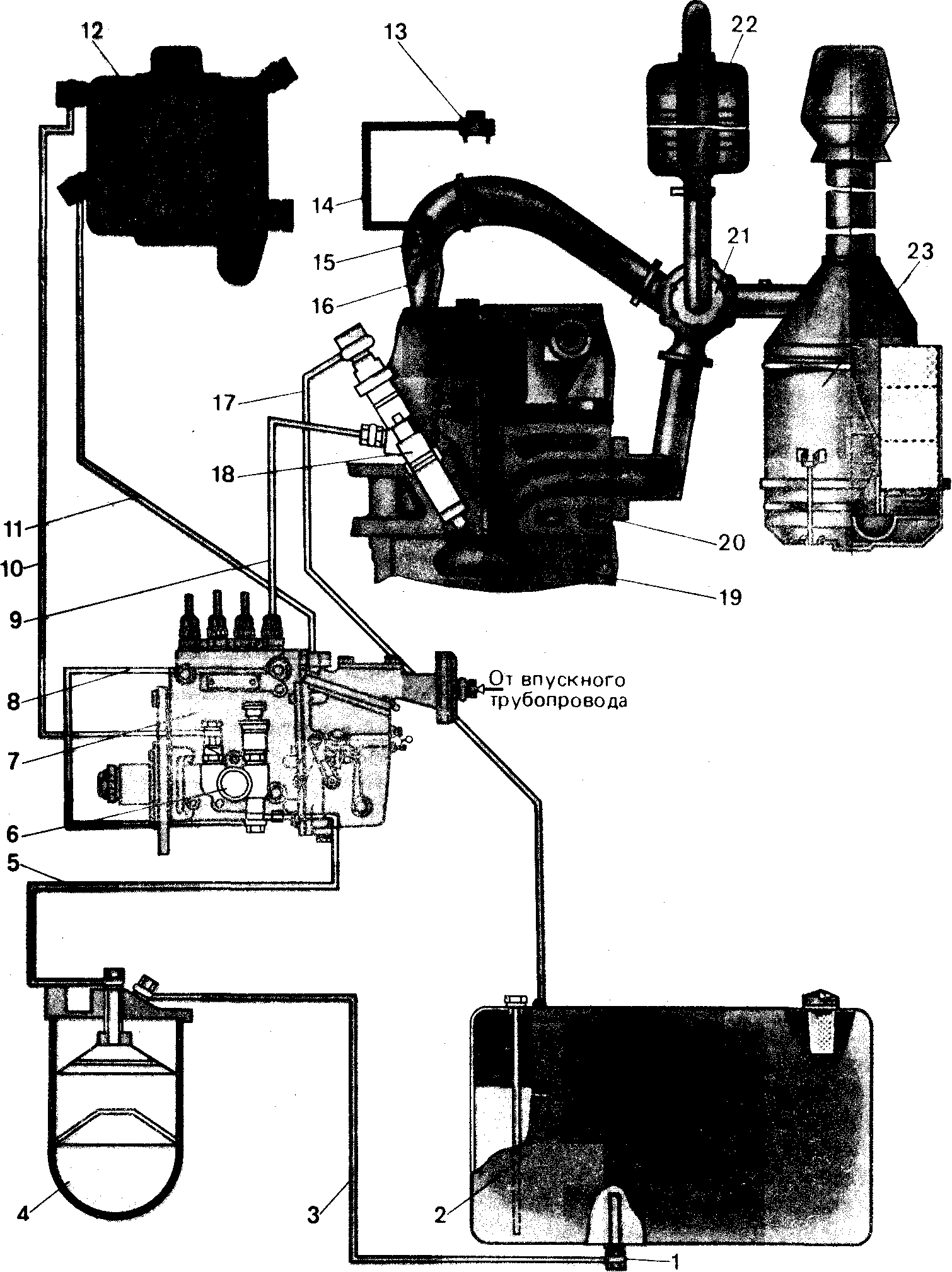
Рис. 5. Схема системы питания дизеля Д-245: 1 – кран; 2 – топливный бак; 3, 5, 8, 10, 11 и 17 – топливопроводы низкого давления;
4 – фильтр грубой очистки топлива; 6 – топливоподкачивающий насос; 7 – топливный насос высокого давления (ТНВД); 9 – топливопровод высокого давления; 12 – фильтр тонкой очистки топлива; 13 – бачок: 14 – топливопровод к факельному подогревателю;
15 – факельный подогреватель; 16 – впускной трубопровод;
18 – форсунка; 19 – камера сгорания; 20 – головка цилиндров;
21 – турбокомпрессор; 22 – глушитель; 23 – воздухоочиститель.
истемы питания дизельного и карбюраторного двигателей различаются. В качестве примера рассмотрим схему системы питания дизеля Д-245 (рис.5).
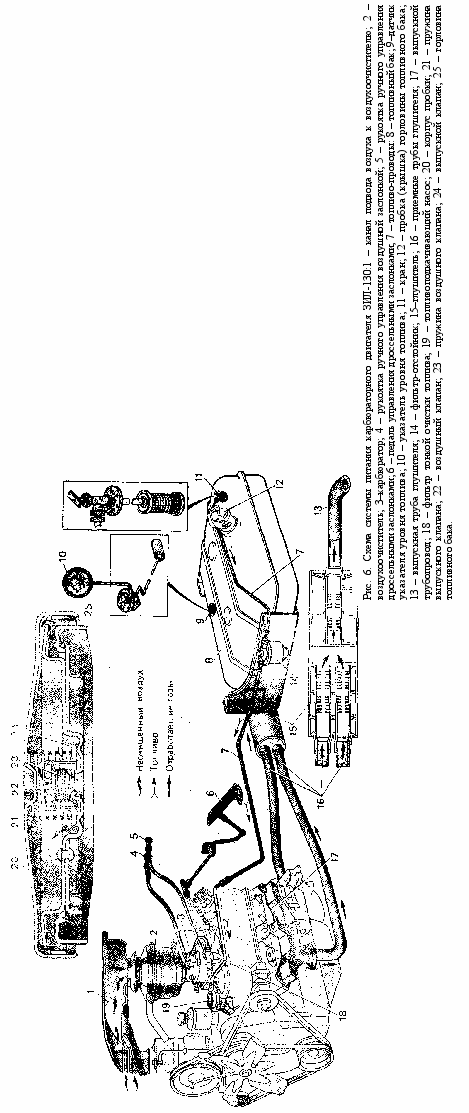
Топливо, заливаемое в бак 2 через фильтр его горловины, при открытом кране 1 засасывается подкачивающим насосом 6 через топливопровод 3, фильтр 4 грубой очистки, топливопровод 5 и подается под давлением по топливопроводу 10 к фильтру 12 тонкой очистки. В фильтре 4 топливо очищается от крупных механических частиц и воды, а в фильтре 12 – от оставшихся мелких частиц и воды, незначительное количество которой присутствует в топливе. По топливопроводу 11 оно поступает в топливный насос 7 высокого давления (ТНВД), из которого под большим давлением подается по топливопроводам 9 к форсункам 18. Через форсунки топливо впрыскивается в камеры 19 сгорания. ТНВД снабжен специальным всережимным регулятором, автоматически обеспечивающим различную подачу топлива к форсункам в зависимости от нагрузочных режимов двигателя
Топливо, просачивающееся через зазоры сопрягаемых деталей форсунок, по сливному топливопроводу 17 отводится в бак 2. Излишки топлива из насоса 7 по топливопроводу 8 возвращаются в топливоподкачивающий насос 6.
Воздух, необходимый для сгорания топлива, поступает в цилиндры через воздушный фильтр (воздухоочиститель 23) и впускной трубопровод 16, в котором установлен электрофакельный подогреватель 15.
Количество поступающего в цилиндр воздуха увеличивает турбокомпрессор 21. Его турбину приводят в действие отработавшие газы, уходящие затем через глушитель 22 в окружающую среду.
Системы питания карбюраторных двигателей незначительно отличаются от рассматриваемой ниже системы питания двигателя ЗИЛ-130.
Топливо из бака 8 (рис. 6) при открытом кране 11 через фильтр - отстойник 14, топливопровод 7 засасывается подкачивающим насосом 19, подается в фильтр 18 тонкой очистки и далее в карбюратор 3. При такте впуска воздух, очищенный от посторонних примесей в воздухоочистителе 2, поступает в карбюратор. В нем топливо распыливается, смешивается с воздухом и начинает испаряться. Приготовление горючей смеси продолжается во впускном трубопроводе, двигаясь по которому топливо испаряется и перемешивается с воздухом. Этот процесс заканчивается в цилиндрах двигателя во время тактов впуска и сжатия.
В зависимости от режима нагрузки на двигатель для его работы требуется топливовоздушная смесь различного качественного состава.
Для выполнения требования к горючей смеси по составу в карбюраторе имеются специальные системы, механизмы и устройства. после сгорания рабочей смеси отработавшие газы через выпускной трубопровод 17, трубы 16 и глушитель 15 выбрасываются в окружающую среду. Топливо заливают в бак 8 через горловину, закрываемую пробкой 12.
4. Система смазки
4.1. Общие сведения, применяемые масла
Масло, подаваемое насосом в смазочную систему, призвано надежно разделять трущиеся поверхности и отводить избыточную теплоту. В зависимости от условий работы сопряжений трение делят на следующие три вида:
1) трение без разделяющего смазочного слоя – сухое трение. Сухое трение вызывает повышенный нагрев деталей, молекулярное схватывание поверхностей и ускоряет износ деталей;
2) граничное трение – это трение при неполном разделении трущихся поверхностей слоем смазки;
3) жидкостное трение – трение между трущимися поверхностями, надежно разделенными слоем масла. Слой масла между трущимися поверхностями уменьшает силу трения и одновременно охлаждает детали. При жидкостном трении износ деталей во много раз меньше, чем при сухом и полужидкостном.
Итак, смазочная система необходима для непрерывной подачи масла к трущимся поверхностям деталей, отвода от них теплоты и защиты их от коррозии. Масло к трущимся деталям подводится несколькими способами: под давлением, разбрызгиванием и самотеком.
Под давлением масло подается к коренным и шатунным подшипникам коленчатого вала, подшипникам распределительного вала, в ряде случаев – к верхней головке шатуна для смазки поршневого пальца, втулкам коромысел и т. д.
Разбрызгиванием или самотеком обычно смазываются малонагруженные детали, а также цилиндры и поршни.
Моторные масла и требования, предъявляемые к ним. Наиболее широкое распространение для смазки двигателей получили минеральные масла, изготовляемые из тяжелых фракций нефти. Масло должно покрывать трущиеся поверхности прочной пленкой, не разрушающейся и не стирающейся при достаточно больших температурах, нагрузках и скоростях перемещения трущихся поверхностей. Масло не должно слишком быстро вытекать из зазора между трущимися поверхностями и создавать чрезмерно большое сопротивление в каналах и зазорах. Вязкость масла не должна резко изменяться в диапазоне от температуры окружающей среды до 110…120°С.
В зависимости от назначения двигателей и условий их эксплуатации моторные масла подразделяют на шесть групп (табл. 1).
Основным эксплуатационным показателем масла является его кинематическая вязкость, значение которой (сСт – «сантистокс») при 100°С входит в маркировку масла.
Таблица 1. Группы моторных масел
Типы двигателей | Группа масла |
Нефорсированные бензиновые | А |
Форсированные и двухтактные бензиновые | Б |
Высокофорсированные бензиновые и дизели | В |
Форсированные дизели и особо нагруженные бензиновые двигатели | Г |
Высокофорсированные дизели при использовании топлива с содержанием серы до 1% | Д |
Высокофорсированные судовые дизели при использовании топлива с содержанием серы до 3% | Е |
Для двигателей сельскохозяйственных тракторов и автомобилей применяют масла групп Б, В и Г. При маркировке масел, например, М-8Б1, М-10Г2, приняты следующие обозначения: М – моторное; 8,10 – кинематическая вязкость при 100°С, сСт; Б, Г – принадлежность к группе масла; индекс 1 – для карбюраторных двигателей, 2 – для дизелей.
Летом обычно применяют масло с кинематической вязкостью 10 сСт, а зимой – 8 сСт.
4.2. Устройство и действие смазочной системы
Смазочная система двигателя – это совокупность взаимодействующих устройств, обеспечивающих непрерывную подачу к поверхностям трения очищенного, смазочного материала (масла) в необходимом количестве при определенной температуре под определенным давлением и возврат его в поддон картера. Смазочная система большинства автотракторных двигателей комбинированная. В ней сочетаются способы подачи масла разбрызгиванием и под давлением. При комбинированной смазочной системе к наиболее нагруженным поверхностям трения сборочных единиц масло подается под давлением, а остальные поверхности смазываются маслом, разбрызгиваемым во внутренних полостях двигателя при его работе.
Комбинированная смазочная система включает в себя устройства для очистки и охлаждения масла. Это уменьшает расход масла и изнашивание деталей двигателя. Некоторые сборочные единицы многих двигателей имеют самостоятельные устройства для смазывания трущихся поверхностей деталей.
Смазочная система дизеля Д-240. Резервуар для масла – поддон 1 (рис. 7) картера. Масло в него заливают через горловину с сетчатым фильтром до уровня верхней метки на масломерной линейке (щупе). Нижняя метка показывает минимально допустимое количество масла. Если его уровень не достигает этой метки, запускать двигатель нельзя. Из поддона через сетчатый маслоприемник 5 масло засасывается н
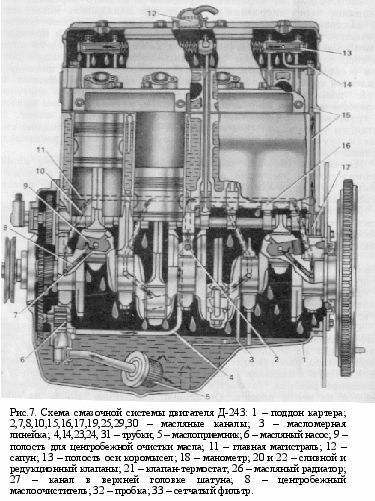
Очищенное масло по трубке 24 поступает в радиатор 26, где охлаждается, а далее по трубке 23 через сетчатый фильтр 33 нагнетается в канал 2 средней перегородки блок-картера. Здесь поток масла разветвляется. Часть его по наклонному каналу 30 поступает для смазывания среднего коренного подшипника, а основной поток направляется в продольный канал 11, называемый главной магистралью.
Из этой магистрали по каналам, просверленным в перегородках и стенках блок-картера, масло поступает к остальным коренным подшипникам. Из кольцевых проточек в верхних вкладышах коренных подшипников через сверления 7 в коренных шейках сверления 8 в щеках коленчатого вала масло поступает в полости 9 шатунных шеек, откуда после повторной центробежной очистки по трубкам 31 идет на смазывание шатунных подшипников.
Часть масла от переднего, среднего и заднего коренных подшипников через сверления в их верхних вкладышах нагнетается по наклонным каналам блока-картера для смазывания соответствующих опорных шеек распределительного вала. При вращении этого вала в моменты совмещения сверления 17 в его задней шейке со сверлениями во втулке масло нагнетается пульсирующим потоком в совмещенные каналы 15 блок-картера и головки цилиндров. Далее по трубке 14 оно поступает в полость 13 оси коромысел. Из этой полости через радиальные сверления оси масло поступает в зазоры между осью и коромыслами. По каналам 25 оно выходит к трущимся поверхностям регулировочных винтов и штанг. По штангам через канал 16 в толкателях масло стекает в поддон, смазывая трущиеся поверхности толкателей и кулачков распределительного вала.
Из канала 10 часть масла направляется в сверление пальца промежуточной шестерни для смазывания ее втулки, а также в каналы 29 для смазывания топливного насоса. Давление в магистрали контролируют по манометру 18.
Масло, выдавливаемое из зазоров, разбрызгивается движущимися деталями; образуется масляный туман, который оседает на поверхностях цилиндров, поршней, толкателей и других деталей и таким образом смазывает их.
К поршневым пальцам масло подводится через сверления в верхних головках шатунов. Стекающее с деталей масло собирается в поддоне картера.
Для предотвращения выдавливания масла через уплотнения газами, проникающими из цилиндров, полость картера сообщена с атмосферой через сапун 12.
Смазочная системы V-образных дизелей (СМД-60 (62)) в основном подобна рассмотренным, но имеют более сложную сеть каналов и трубопроводов. Для заполнения этих каналов после пуска требуется определенное время, поэтому в системе имеется насос предпусковой прокачки, благодаря чему обеспечивается нормальная подача масла к трущимся деталям сразу же после пуска двигателя.
Такая смазочная система работает следующим образом. Основная секция 2 масляного насоса по каналам блок-картера нагнетает масло в центробежный маслоочиститель 14. Часть очищенного масла сливается в поддон, а остальное по каналам 6 нагнетается в магистраль 5 (продольное сверление в правой стенке блок-картера). Из магистрали
п
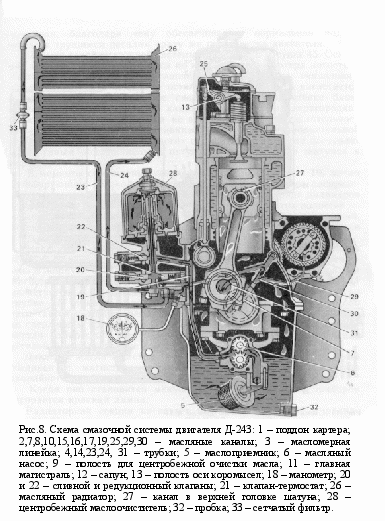
о каналам в поперечных перегородках блок-картера масло подается ко всем шейкам распределительного вала и к коренным подшипникам (рис.8).
Далее после дополнительной центробежной очистки в полостях шатунных шеек масло поступает к шатунным подшипникам и оттуда, по сверлениям в шатунах, – к поршневым пальцам.
В моменты совмещения сверлении 7 с каналами 12 и 19 масло пульсирующим потоком нагнетается от передней шейки распределительного вала в полость 18 оси коромысел левого ряда цилиндров и от задней шейки в полость 13 правого ряда, а из этих полостей – к деталям распределительного механизма. Цилиндры, поршни, поршневые кольца и распределительные шестерни смазываются разбрызгиванием.
Часть масла из канала 19 по трубке 16 поступает в полость корпуса водяного насоса, смазывает его подшипники и по сверлению в корпусе сливается под переднюю крышку блок-картера. Из магистрали через дополнительный фильтр 10 масло по трубке 11 нагнетается к подшипнику вала турбокомпрессора, а затем по трубке 15 стекает в поддон. По шлангу 4 из магистрали оно нагнетается к торцу коленчатого вала воздушного компрессора и по сверлениям проходит к его шатунным подшипникам. Остальные детали компрессора смазываются разбрызгиванием. Стекающее с деталей масло по трубке 3 отводится в двигатель.
Давление масла в системе контролируют по манометру, который соединен с магистралью. Кроме того, имеется сигнализатор аварийного давления. Когда оно становится меньше 0,1 МПа, на щитке приборов загорается красная лампа.
Радиаторная секция нагнетает масло по трубке 22 в радиатор 21. На некоторых двигателях СМД-62 установлен односекционный масляный насос, со стороны нагнетательной полости которого прикреплены две трубки: по одной масло нагнетается в систему, а по другой через калиброванное отверстие, ограничивающее поток, – к масляному радиатору. Охлажденное масло по трубкам 23 и 24 возвращается в поддон.
По трубке 24 масло подводится к насосу 28 предпусковой прокачки, который вступает в работу вместе с пусковым двигателем и нагнетает масло по трубке через обратный клапан 29 в каналы смазочной системы. Спустя 1...2 мин в системе устанавливается давление 0,05...0,1 МПа. После пуска дизеля под действием пружины и увеличившегося в системе давления клапан 29 закрывается, предотвращая утечку масла из системы через насос.
5. Система охлаждения
5.1. Принципы работы и классификация систем
охлаждения, охлаждающие жидкости
Работа двигателя внутреннего сгорания сопровождается выделением большого количества теплоты. Температура газов в момент вспышки достигает 2000°С, а средняя температура газов в течение рабочего цикла составляет 800...900 °С. Только 25...40% теплоты, выделяющейся при сгорании топлива в двигателях внутреннего сгорания, используется эффективно. Большая же часть теплоты теряется с отработавшими газами (до 40%) и отводится системой охлаждения (25...35%).
В результате контакта горячих газов с цилиндрами, камерами сгорания, поршнями, клапанами и другими деталями температура этих деталей повышается. Чрезмерный нагрев деталей двигателя приводит к уменьшению зазоров в подвижных соединениях, ухудшению смазки деталей и смазочных свойств масла, а также к нарушению процессов смесеобразования и сгорания (преждевременное воспламенение рабочей смеси, детонация и т. п.). Поэтому для обеспечения нормальной работы двигателя при различных скоростях и нагрузках его температурный режим должен быть вполне определенным и постоянным.
Переохлаждение двигателя или его работа при недостаточном прогреве также отрицательно сказывается на смесеобразовании и сгорании (дополнительные потери теплоты на прогрев двигателя или отвод в систему охлаждения, плохое испарение, конденсация топлива, неоднородная рабочая смесь, смыв масла топливом), а следовательно, снижает эффективность работы двигателя. Детали двигателя охлаждают путем отвода теплоты в атмосферу. В качестве теплоносителей в системах охлаждения двигателей используют жидкость или воздух. В зависимости от рода применяемого теплоносителя системы охлаждения подразделяют на жидкостные (водяные) и воздушные.
Жидкостные системы охлаждения могут быть с термосифонной и принудительной циркуляцией жидкости.
В термосифонной системе охлаждения жидкость циркулирует за счет разницы в плотности холодной и горячей жидкости. Термосифонная система охлаждения проста, но малоэффективна вследствие медленной циркуляции жидкости. Она применяется для охлаждения преимущественно пусковых двигателей.
Принудительная циркуляция жидкости осуществляется при помощи центробежного насоса. Вследствие интенсивной циркуляции жидкости отвод теплоты от деталей ускоряется. Если полость жидкостной системы охлаждения свободно сообщается с атмосферой, то такая система охлаждения называется открытой. Она применяется редко, так как требует большого расхода интенсивно испаряющейся жидкости.
Преимущественное применение нашли закрытые системы охлаждения, сообщающиеся с атмосферой периодически через паровоздушный клапан. Эти системы охлаждения отличаются малым расходом воды, простотой обслуживания и меньшим образованием накипи.
Система жидкостного охлаждения современных двигателей состоит из следующих элементов (рис. 9, а): водяной рубашки, образуемой полостями блока 9 и головки 7 цилиндров, радиатора 7, водяного насоса 10, вентилятора 13, термостата 6, водораспределительной трубы 8, шлангов 4 и 11.
Нагретая в водяной рубашке двигателя вода под напором водяного насоса 10 проходит через открытый клапан термостата 6 и верхний соединительный шланг 4 в радиатор 1. Протекая по трубкам радиатора, которые подвергаются обдуву потоком воздуха, всасываемым в
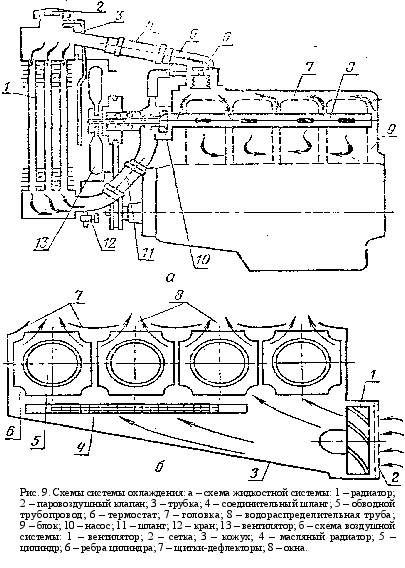
ентилятором 13, вода охлаждается.
Из нижнего бачка радиатора охлажденная вода подсасывается через нижний шланг 11 к насосу 10 и направляется далее по водораспределительной трубе 8 к наиболее нагревающимся частям двигателя.
При перегреве двигателя, когда давление в системе охлаждения повышается вследствие парообразования, часть пара отводится в атмосферу через паровоздушный клапан 2 и трубку 3. Быстрое охлаждение нагретого двигателя приводит к конденсации пара в системе охлаждения и образованию вакуума. В этом случае атмосферный воздух подсасывается в систему через трубку 3 и клапан 2.
Прогрев двигателя происходит при закрытом клапане термостата 6. В этом случае вода в верхний шланг 4 не поступает, а отводится по обводному трубопроводу 5 во всасывающую камеру водяного насоса. Вода циркулирует от водяного насоса 10 к водораспределительной трубе 8, попадает в водяную рубашку двигателя, затем по обводному трубопроводу снова идет к насосу 10. Радиатор 1 оказывается выключенным, вода циркулирует по малому кругу, прогрев воды интенсивный. Циркуляция воды по малому кругу замедляется по мере открытия клапана термостата 6: поток воды получает доступ в радиатор.
При нормальной работе двигателя под нагрузкой температура воды, поступающей в радиатор, составляет 85...90°С, и температура воды на входе в водяную рубашку – 70...75°С. В радиаторе вода снижает температуру на 10...15°С.
Система воздушного охлаждения (рис.9, б) состоит из вентилятора 1, кожуха 8 и щитков-дефлекторов 7. При работе двигателя вентилятор засасывает атмосферный воздух через сетку 2 и направляет его при помощи кожуха 3 к ребристым поверхностям цилиндров 5 и их головок. Поток воздуха обдувает цилиндры и головки и выходит через окна 8 между дефлекторами. Чем больше открыты окна 8, тем меньше сопротивление потоку воздуха и интенсивнее обдув цилиндров и их головок. Под кожухом 3 устанавливают масляный радиатор 4, который также охлаждается потоком воздуха.
По сравнению с водой воздух как теплоноситель имеет более низкие теплопроводность и теплоемкость. Поэтому в двигателях с воздушным охлаждением наиболее нагревающиеся детали (цилиндры, головки цилиндров) имеют увеличенную поверхность контакта с теплоносителем за счет оребрения, а вентилятор повышенной подачи обеспечивает интенсивный обдув двигателя.
Система воздушного охлаждения удобнее в эксплуатации, позволяет снизить массу и габариты двигателя, однако отличается повышенной шумностью и значительными затратами мощности на привод вентилятора (от 5 до 10 % мощности двигателя).
В качестве охлаждающей жидкости используют воду или жидкости с низкой температурой замерзания (антифризы).
Вода должна быть чистой, с небольшим содержанием солей кальция и магния (мягкой). Единица жесткости воды – миллимоль на килограмм (ммоль/кг). Воду считают мягкой, если в ней содержится солей до 1 ммоль/кг, средней жесткости – 1...2,5, жесткой – 2,5... 5 ммоль/кг.
Воду средней жесткости и жесткую без предварительного умягчения применять нельзя, так как при работе двигателя соли осаждаются на стенках деталей, омываемых водой, образуя накипь, которая снижает теплопроводность стенок и ухудшает циркуляцию воды. Это ведет к перегреву двигателя, снижению мощности, интенсивному изнашиванию деталей.
Простейший способ умягчения воды – кипячение в течение 30...40 мин с последующим отстаиванием и фильтрацией через матерчатый фильтр. Воду, которую сливают после работы из системы охлаждения, нужно накапливать, отстаивать и фильтровать для последующего использования.
Широко распространены химические способы умягчения воды три-натрийфосфатом, известью, кальцинированной содой.
Антифризы – это жидкости на основе этиленгликоля. Их марки: 40 и 65 (ГОСТ 159-52), ТОСОЛ-А40М и ТОСОЛ-А65М (ТУ 6-02-751-86). Антифриз 40 и ТОСОЛ-А40М можно применять при температурах воздуха, достигающих минус 40°С, а антифриз 65 и ТОСОЛ-А65М – до температуры минус 65 °С. Низкозамерзающие жидкости нужно заливать в систему охлаждения на 5...7 % (по объему) меньше, чем воды, так как они больше расширяются при нагревании.
5.2. Устройство основных узлов систем охлаждения
5.2.1. Водяные насосы
Н
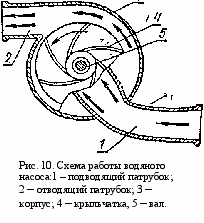
Отсюда она вытесняется в водяную рубашку двигателя по
отводящему патрубку 2, который расположен по касательной к камере насоса.
Привод водяного насоса может быть клиноременный или шестеренчатый, совместный с приводом вентилятора или отдельный.
5.2.2. Радиаторы и вентиляторы
Радиатор предназначен для снижения температуры циркулирующей в системе охлаждения жидкости путем передачи части его теплоты потоку воздуха. Он состоит (рис. 11, а) из верхнего 9 и нижнего 5 бачков, связанных трубчатой сердцевиной 7. Верхний бачок имеет заливную горловину, которая закрывается крышкой. В закрытых системах охлаждения в этой крышке устанавливают паровоздушный клапан.
Полость верхнего бачка сообщается с водяной рубашкой двигателя через патрубок 2, а с атмосферой через паровоздушный клапан и трубку 3. Нижний бачок связан с водяной рубашкой патрубком 4.
Сердцевина радиатора 7 может быть трубчато-пластинчатой (
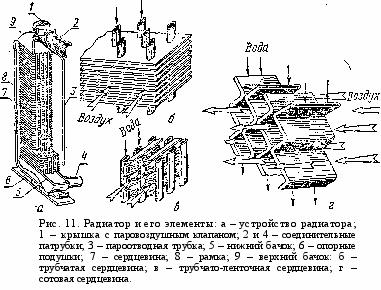
рис. 11, б), трубчато-ленточной (рис. 11, в) или сотовой (рис. 11, г). Ее изготовляют отдельно или совместно с бачками. В случае отдельного изготовления сердцевина крепится к бачкам болтами и имеет уплотнительные прокладки. При изготовлении сердцевины совместно с бачками концы трубок припаивают к бачкам или уплотняют резиновыми втулками – кольцами.
Радиатор монтируют в рамке 8 и крепят к специальным кронштейнам или раме трактора на резиновых подушках 6 или прокладках.
Детали радиатора, через которые осуществляется теплообмен, изготавливают из теплопроводных материалов – латуни, меди и т. п.
Паровоздушный клапан, устанавливаемый в крышке заливной горловины радиатора, изолирует систему охлаждения от атмосферы и поддерживает в ней давление, равное 0,14 МПа, что повышает температуру кипения, снижает парообразование и расход охлаждающей жидкости. В случае образования вакуума в системе охлаждения (при быстром охлаждении горячего двигателя) через воздушный клапан подсасывается атмосферный воздух, благодаря чему исключается деформация тонких латунных трубок сердцевины. Воздушный клапан открывается при разрежении 0,001...0,01 МПа.
Отвод теплоты от охлаждающей жидкости можно ограничивать путем уменьшения обдува сердцевины радиатора (выключением вентилятора, прикрытием радиатора шторкой или жалюзи), или изменения интенсивности циркуляции.
Вентиляторы, как правило, выполняются совместно с водяными насосами, в отдельных случаях как самостоятельные агрегаты (Д-108).
Крыльчатка вентилятора имеет четыре или шесть лопастей. Для уменьшения вибрации и шума лопасти располагают попарно под разными углами. Концы лопастей иногда несколько отгибаются для получения эффекта центробежной подачи воздуха.
Для повышения эффективности охлаждения вентилятор устанавливают в направляющем кожухе, который крепится на рамке радиатора.
Вентилятор системы воздушного охлаждения отличается большей подачей, так как в этой системе охлаждения он единственный источник циркуляции теплоносителя.
5.2.3. Термостаты
Термостат необходим для ускорения прогрева двигателя и поддержания наивыгоднейшего его теплового состояния за счет изменения количества воды, проходящей через радиатор. Для заполнения термосиловых элементов термостатов используют смесь церезина (нефтяного воска) с медным или алюминиевым порошком, которая сильно расширяется при нагревании.
Жидкостные термостаты на современных двигателях не устанавливают, так как их работа существенно влияет на изменение давления в закрытых системах охлаждения. На рис. 12, а и б показан термостат дизеля Д-240. Его детали изготовлены из латуни. На пустотелом цилиндре 4 расположены основной 5 и два перепускных 3 клапана, а внутри помещена эластичная резиновая вставка 6, нижний конец которой завальцован в цилиндре. Пространство вокруг вставки заполнено активной смесью 8.
Т
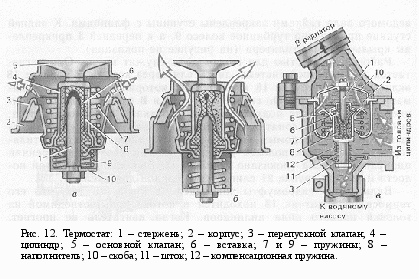
ермосиловой элемент надет на стержень 1, закрепленный гайкой в скобе 10, которая припаяна к корпусу 2 термостата. Пружина 7, нажимая на опорную шайбу, надетую на термосиловой элемент, удерживает его в нижнем положении (показано на рис.12). При этом основной клапан закрывает горловину корпуса 2 и таким образом не позволяет воде проходить в радиатор. Через боковые окна корпуса 2 неохлажденной она поступает к водяному насосу.
По мере нагрева расширяющаяся активная смесь сдавливает вставку 6, и когда температура воды достигнет 78...82°С, она начинает скользить вверх по конусному закругленному концу стержня, увлекая за собой термосиловой элемент вместе с клапанами. При температуре 95°С основной клапан полностью открыт, а боковые закрыты.
В термостатах дизелей СМД-62 и КамАЗ-740 (рис. 12, в) элемент, нагреваясь, скользит вместе с клапанами по стержню 1 вниз. При этом основной клапан 5 отходит от горловины корпуса 2, открывая путь воде в радиатор, а перепускной клапан закрывает канал патрубка, по которому вода отводится к водяному насосу (пока двигатель не прогрет). Клапан 3 не препятствует дальнейшему движению термосилового датчика и после того, как упрется в кромку отверстия, так как шток 11 свободно проходит в отверстии клапана, сжимая компенсационную пружину 12.
6. Системы пуска двигателей
Чтобы запустить двигатель внутреннего сгорания, вращение коленчатого вала необходимо довести до некоторой частоты, обеспечивающей смесеобразование, заполнение цилиндров свежим зарядом, сжатие и воспламенение смеси. Эта частота вращения при температуре воздуха выше 0°С для карбюраторных двигателей должна быть не менее 40…50 мин-1, а дизелей – не менее 150…250 мин-1.
Специальные механизмы и устройства, предназначенные для быстрого и надежного пуска, составляют систему пуска. Различают следующие способы пуска двигателей.
Пуск от руки применим для карбюраторных двигателей. При этом способе пуска коленчатый вал двигателя поворачивают пусковой рукояткой, палец которой сцепляется с храповиком на носке коленчатого вала, или шнуром, наматываемым на маховик (двигатель П-10УД).
П
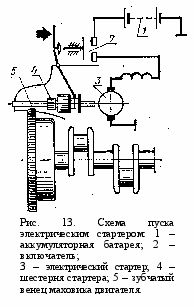
Для облегчения пуска дизеля водяные системы охлаждения пускового двигателя и дизеля связаны между собой, что обеспечивает прогрев двигателя.
Пуск электрическим стартером – наиболее распространенный способ, пригодный для автомобильных, тракторных и пусковых двигателей. Схема системы пуска электрическим стартером показана на рис.13. Электрический стартер 3 питается от аккумуляторной батареи 1 током низкого напряжения. В период пуска шестерня 4 стартера входит в зацепление с зубчатым венцом 5 маховика двигателя. Передаточное число между шестерней стартера и венцом маховика подбирают с таким расчетом, чтобы сообщить коленчатому валу двигателя необходимую для пуска частоту вращения. Стартер включается на период пуска и выключается специальным механизмом сразу после того, как двигатель начнет работать.
У многих моделей двигателей, оборудованных электрическим стартером, установлено устройство для пуска от руки, которым пользуются, когда разряжена аккумуляторная батарея или неисправен стартер.
Система пуска дизелей при помощи пускового двигателя надежна в любых температурных условиях, но ее обслуживание и операции при пуске сложнее, чем в случае пуска электрическим стартером. Кроме того, дополнительный пусковой двигатель и его силовая передача увеличивают вес всей двигательной установки в целом.
Система пуска стартером менее материалоемка, однако в условиях низких температур воздуха менее надежна
Система пуска от руки (ручной пуск) наиболее проста, однако мало надежна и небезопасна для механизатора.
Оформление отчета
Отчет по лабораторной работе оформляется в рабочей тетради и содержит в себе титульный лист (ф.1) и кратко изложенные следующие вопросы.
1.Назначение основных механизмов и систем двигателя внутреннего сгорания.
2.Устройство и принцип действия кривошипно-шатунного механизма ДВС.
3.Устройство и принцип действия газораспределительного механизма.
4.Назначение, общее устройство и принцип действия жидкостной системы охлаждения. Сравнение ее с воздушной системой охлаждения. Применяемые охлаждающие жидкости.
5.Назначение, общее устройство и принцип действия комбинированной системы смазки. Маркировка моторных масел.
6.Назначение, общее устройство и принцип действия системы питания дизельного двигателя.
7.Назначение, общее устройство и принцип действия системы питания карбюраторного двигателя.
8.Способы запуска ДВС, сравнение систем пуска от пускового двигателя и стартера.
Приложение
Форма 1 «Титульный лист»
Министерство сельского хозяйства
и продовольствия Республики Беларусь

департамент образования, науки и кадров

учреждение образования
"Белорусская государственная
сельскохозяйственная академия"

Кафедра технологии и организации механизированных
работ в растениеводстве
лабораторная работа №
_________________________________________________________________________________________________________________________________________________________________________________________________________________________________________________________________________________________________________________
(название работы)
_
Цель работы
_____________________________________________________________________________________________________________________________________________________________________________________________________________________________________________________________________________________________________________Работа зачтена______
(число)
___________________
(подпись преподавателя)
___________________
Выполнил студент_____ курса, _____группы_________
________________________
(наименование специальности)
_________________________
(Ф И О)
Горки 2004
Литература
1.Гуревич А.М. , Болотов А.К., Судницын В. И. Конструкция тракторов и автомобилей. – М.: Агропромиздат, 1989. – 368 с.
2.Белоконь А.Е., Окоча А.И., Кохановский С.П., Антоненко А.Ф. Тракторы. – К.: Урожай, 1989. – 384 с.
3.Семенов В.М., Власенко В.Н. Трактор. – М.: Агропромиздат, 1989. – 352 с.
4.Гельман Б.М., Москвин М.В. сельскохозяйственные тракторы и автомобили. Кн.1. Двигатели. – М.: Агропромиздат, 1987. – 287 с.
5.Родичев В.А., Родичева Г.И. тракторы и автомобили. – М.: Колос, 1996. – 336 с.
Содержание
1. Кривошипно-шатунный механизм…………………………………………………….3
2. Газораспределительный механизм…………………………………………………….9
3. Система питания………………………………………………………………………10
4. Система смазки…………………..……………………………………………………15
5. Система охлаждения………………..…………………………………………………20
6. Системы пуска двигателей……………………………………………………………28
Оформление отчета………………………………………………………………………29
Приложение………………………………………………………………….…………30
Литература………………………………………………………………………………31
У ч е б н о - м е т о д и ч е с к о е и з д а н и е
Геннадий Анатольевич Валюженич
Александр Егорович Улахович
Олег Петрович Лабурдов
механизмы и системы
двигателей внутреннего сгорания
Методические указания к лабораторной работе №2
Редактор Е. Г. Бутова
Техн. редактор Н. К. Шапрунова
Корректор Е. А. Юрченко
Подписано в печать 03.03.2004.
Формат 60х84 1/16. Бумага для множительных аппаратов.
Печать ризографическая. Гарнитура «Таймс».
Усл. печ. л.1,86. Уч. - изд.л. 1,72.
Тираж 100 экз. Заказ . Цена 2640 руб.

Редакционно-издательский отдел БГСХА
213410, г. Горки Могилевской обл., ул. Студенческая, 2
Отпечатано на ризографе копировально-множительного бюро БГСХА,
г. Горки, ул. Мичурина, 5