Отчет о научно-исследовательской работе разработка модулей для производственных технологий
Вид материала | Отчет |
СодержаниеВзаимосвязь между электрическими характеристиками разряда (напряжением горения U) и параметрами магнитопровода определяется выра 3.2 Источник питания для опытно-промышленных образцов |
- Отчет о научно-исследовательской работе; пояснительная записка к опытно-конструкторской, 14.47kb.
- Реферат отчет о научно-исследовательской работе состоит, 61.67kb.
- Отчёт о научно-исследовательской работе за 2009 год, 851.3kb.
- Отчёт о научно-исследовательской работе за 2011 год, 1208.93kb.
- Отчет о научно-исследовательской работе контракт, 1195.26kb.
- Отчет о научно-исследовательской работе, 4231.21kb.
- Отчет о научно-исследовательской и опытно-конструктороской работе, 3288.39kb.
- Отчет о научно-исследовательской работе разработка концепции архитектуры программного, 551.78kb.
- Отчёт онаучно-исследовательской работе гу нии но ур за 2010 год, 997.69kb.
- Отчет о научно-исследовательской работе профессорско-преподавательского состава, 617.56kb.
Взаимосвязь между электрическими характеристиками разряда (напряжением горения U) и параметрами магнитопровода определяется выражением:

где f – частота тока, S – сечение магнитопровода, Bm – амплитудное значение индукции магнитного поля в магнитопроводе. Требуемое напряжение горения разряда U может быть достигнуто путем увеличения либо сечения сердечника S, либо параметра fxBm (при фиксированном сечении). Очевидно, что существенное увеличение сечения сердечника неприемлемо с практической точки зрения. Таким образом, для достижения требуемого напряжения горения разряда желательно максимально увеличить значение параметра fxBm, что может быть достигнуто только при использовании специальных сортов магнитных материалов.
Из широкого спектра ферромагнетиков (электротехнические стали, сплавы, ферриты) следует особо выделить две группы материалов, имеющих наименьшее значение объемных потерь при больших значениях частоты и индукции магнитного поля – аморфные магнитомягкие сплавы и специализированные сорта силовых ферритов.
Аморфные сплавы качественно отличаются от традиционных благодаря отсутствию кристаллической решетки. По сравнению с кристаллическими сплавами они обладают лучшими магнитными, механическими и химическими свойствами. Аморфные магнитомягкие сплавы в виде ленты характеризуются высокими значениями магнитной проницаемости, высоким удельным электрическим сопротивлением (ρ~108 Ом·см) и малыми потерями на гистерезис и вихревые токи (в 3–5 раз меньше, чем у лучших кристаллических сплавов). Основным недостатком «ленточных» тороидальных магнитопроводов является резкое возрастание потерь после разреза сердечника. В отличие от ленточных магнитопроводов ферритовые сердечники не имеют подобного недостатка, что позволяет изготавливать разборные конструкции магнитопроводов.
К числу недостатков ферритов можно отнести достаточно сильную зависимость магнитных свойств от температуры. Так, тепловые потери в ферритах существенным образом зависят от температуры материала; минимум потерь лежит в достаточно узком температурном диапазоне (для силовых ферритов ~80–120 0C). При перегреве феррита свыше 180–200 0С магнитная проницаемость уменьшается на несколько порядков и феррит теряет свои ферромагнитные свойства. Аморфные сплавы имеют гораздо более слабую зависимость магнитных свойств от температуры и способны эффективно работать вплоть до температур ~250–300 0C, что имеет принципиальное значение при разработке мощных безэлектродных источников света.
Для индукционных амальгамных УФ-ламп, как будет показано далее, рабочая температура стенки разрядной колбы не превышает ста градусов, что позволяет использовать как аморфные стали, так и ферриты. Конечный выбор магнитного материала определяется из условия достижения максимального значения величины Bm при требуемой частоте тока и заданном пороговом уровне удельных тепловых потерь.
На рисунке 3.1 приведена зависимость величины удельных тепловых потерь p’ от амплитудного значения магнитной индукции Bm и частоты f, для аморфного сплава 5БДср и лучших сортов силовых ферритов фирмы Philips. Как видно из рисунка, c увеличением индукции магнитного поля тепловые потери в ферритах возрастают быстрее, чем тепловые потери в аморфной стали вследствие меньшей индукции насыщения. Для частотной зависимости наблюдается обратная картина: при фиксированной индукции магнитного поля с ростом частоты тепловые потери в аморфных сплавах возрастают заметно быстрее, что обусловлено существенно большей проводимостью аморфных сплавов по сравнению с ферритами.
Вышеописанные различия между магнитными свойствами ферритов и аморфных сплавов наиболее наглядно иллюстрируются рисунком 3.2, где показана зависимость величины fxBm от частоты f при фиксированном уровне удельных тепловых потерь в магнитопроводе (0.5 Вт/см3) для аморфной стали марки 5БДср и различных сортов силовых ферритов, производимых фирмой Philips. Как видно из рисунка, существует оптимальное значение частоты тока, при которой достигается максимальное значение параметра fxBm, причем максимально достижимое значение fxBm существенным образом зависит от качества магнитного материала. В области низких частот тока (менее 20–30 кГц) магнитопроводы на основе аморфных сплавов имеют явное преимущество перед лучшими сортами ферритовых материалов вследствие большей амплитуды магнитного потока в сердечнике. При частотах тока свыше 100 кГц оптимальным вариантом является использование ферритов, и
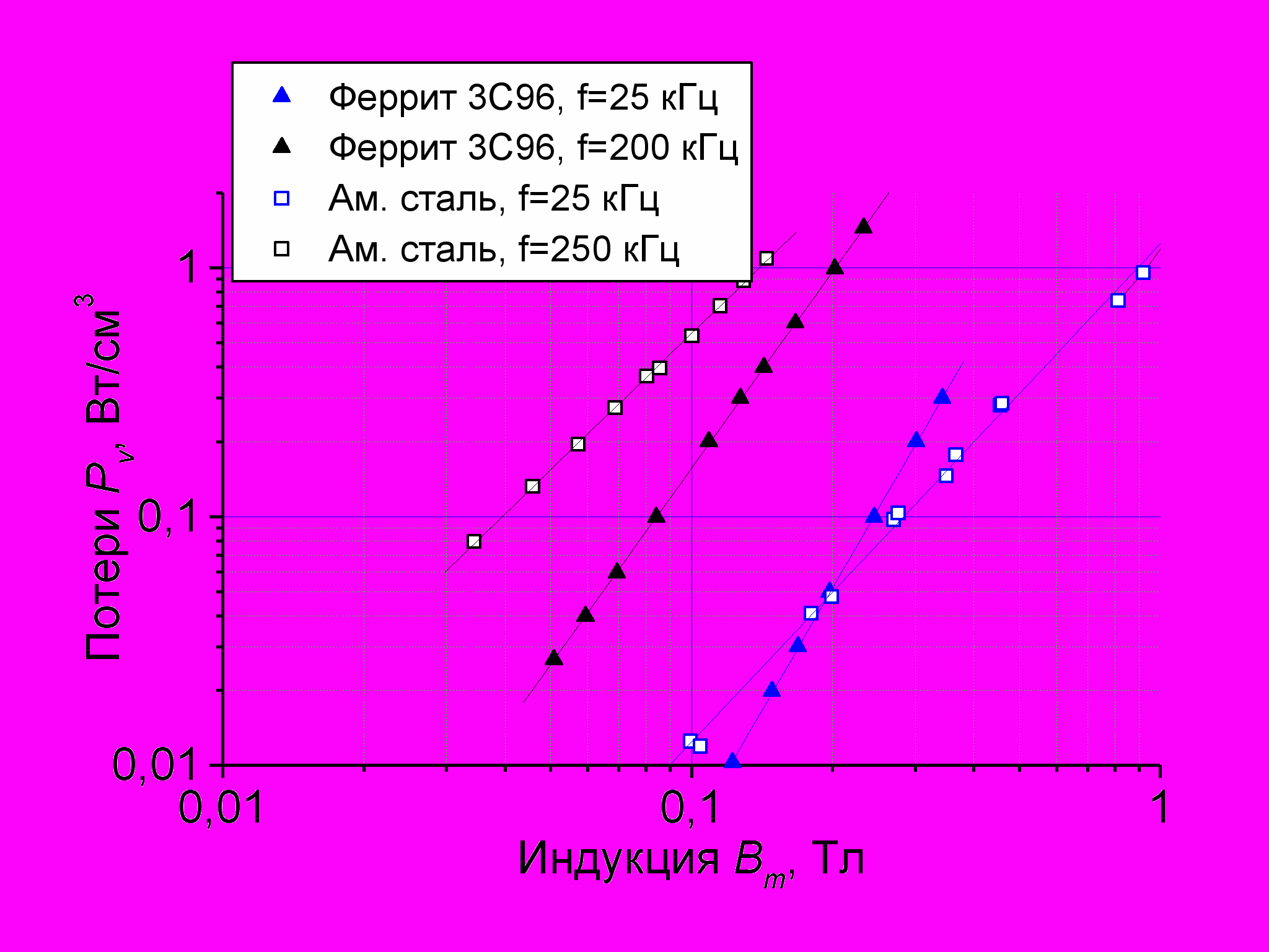
меющих более слабую зависимость магнитных свойств от частоты.
Рисунок 3.1 – Зависимость удельных тепловых потерь от индукции магнитного поля
при фиксированной частоте тока
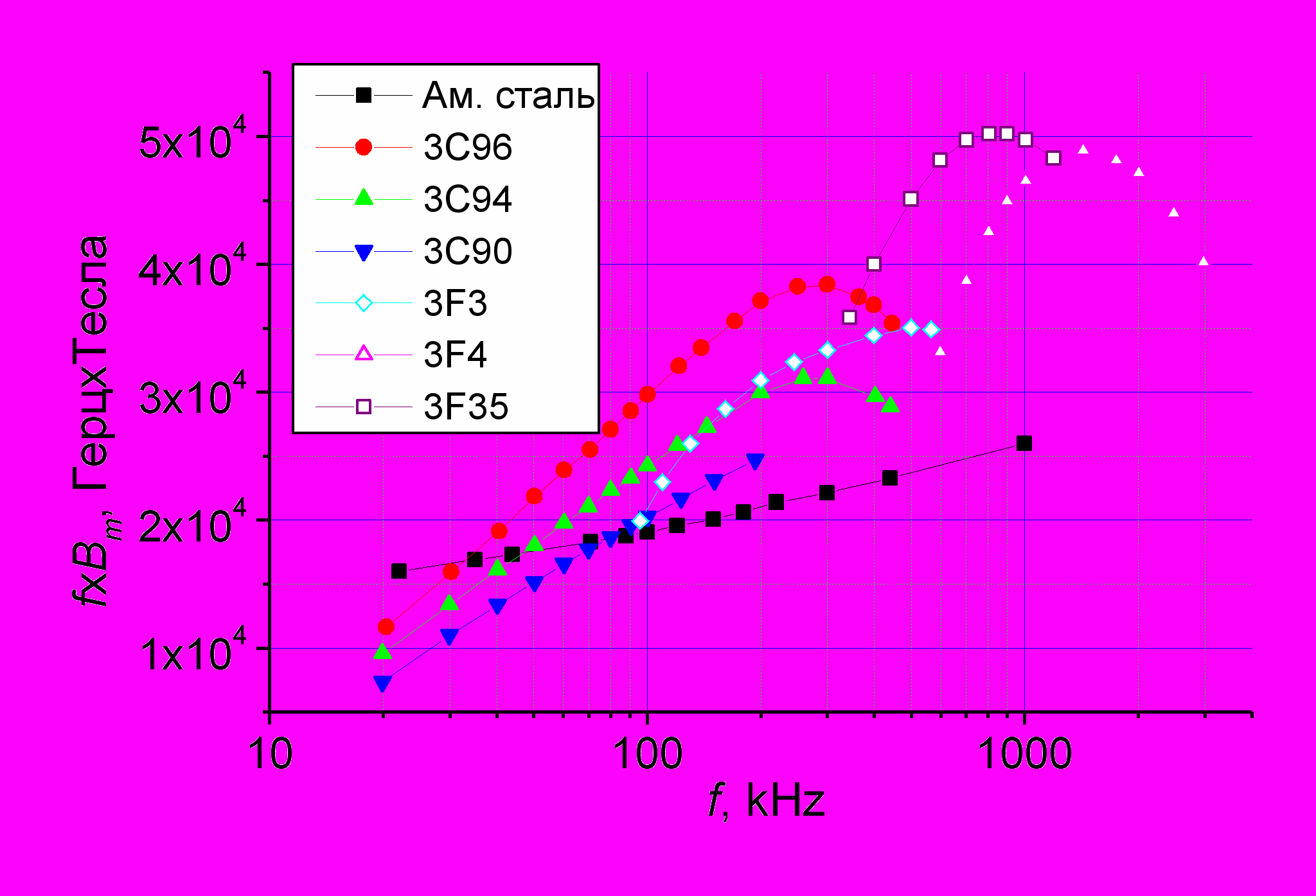
Рисунок 3.2 – Зависимость параметра fxBm от частоты тока
при фиксированном уровне тепловых потерь
Анализируя представленные на рисунке 3.1 данные и учитывая специфику работы магнитопроводов индукционных УФ ламп (оптимальный тепловой режим работы лампы соответствует минимуму потерь в ферритовых сердечниках), можно сделать следующий вывод: оптимальным вариантом является использование специализированных сортов силовых ферритов и «работа» на частотах тока свыше 100 кГц. Верхняя граница частотного диапазона определяется из требований, предъявляемых к источнику питания (простота конструкции, надежность работы). Проведенные опытно-конструкторские работы и испытания экспериментальных образцов источников питания показали, что верхняя граница частотного диапазона соответствует ~200–250 кГц. Дальнейшее повышение частоты источника питания нецелесообразно.
В настоящее время ввиду отсутствия магнитопроводов фирмы Philips на российском рынке используются магнитопроводы фирмы EPCOS марки N87. По своим свойствам данные ферриты являются аналогом ферритов 3F3.
Стандартные габаритные размеры используемых ферритовых колец марки N87:
644018 мм.
Проведенные тестовые испытания данных ферритовых колец на частоте тока 250 кГц показали: оптимальное значение напряжения на вторичном витке ферритового сердечника составляет ~10 В. При этом потери в одном ферритовом сердечнике составляют ~3 Вт. Таким образом, требуемое количество ферритовых сердечников определяется по эмпирической формуле N~U/10, где U – напряжение горения разряда.
3.2 Источник питания для опытно-промышленных образцов
индукционных ультрафиолетовых ламп резонансного типа мощностью до 200 Вт
Эффективность работы источников вторичного электропитания в значительной мере определяется показателями используемых в них преобразователей напряжения. Улучшение удельных показателей преобразователей напряжения тесно связано с повышением частоты коммутации при одновременном повышении надежности и уменьшении энергетических потерь.
В традиционных схемах преобразователей форма тока, протекающего через силовые ключи, близка к треугольной или прямоугольной. При этом в силовых транзисторах возникают потери на переключение, которые растут пропорционально частоте. Особенно это касается IGBT-транзисторов, потери на переключение в которых велики по сравнению с MOSFET. В последнее время становятся популярны резонансные преобразователи напряжения, отличительной особенностью которых является переключение силовых транзисторов при нулевом токе или нулевом напряжении. Такой метод переключения позволяет существенно расширить частотный диапазон работы силовых транзисторов.
Методы, используемые при анализе таких схем, могут быть достаточно просты. Независимо от схемотехнического решения их объединяет одно общее свойство – реализация переходных процессов, близких к синусоидальным, достигается использованием резонансных свойств LC-цепи, при этом анализ схемы практически сводится к расчету последовательного или параллельного RLC-контуров.
3.2.1 Анализ ситуации на рынке подобной продукции
В настоящее время производится большой ассортимент электронных пускорегулирующих аппаратов, второе название которых – электронные балласты для питания трубчатых люминесцентных ламп.
Современные электронные балласты обеспечивают:
- мгновенное (без мерцаний и шума) зажигание ламп;
- комфортное освещение (приятный немерцающий свет без стробоскопических эффектов и отсутствие шума) благодаря работе в высокочастотном диапазоне;
- стабильность освещения независимо от колебаний сетевого напряжения;
- отсутствие миганий и вспышек неисправных ламп, отключаемых электронной системой контроля неисправностей;
- высокое качество потребляемой электроэнергии – близкий к единице коэффициент мощности благодаря потреблению синусоидального тока с нулевым фазовым сдвигом.
Электронные балласты являются достаточно дорогими устройствами, однако начальные затраты компенсируются их высокой экономичностью, которая характеризуется:
- уменьшенным на 20 % потреблением электроэнергии (при сохранении светового потока) за счет повышения светоотдачи лампы на повышенной частоте и более высокого КПД электронного балласта по сравнению с электромагнитным пускорегулирующим аппаратом;
- увеличенным на 50 % сроком службы ламп благодаря щадящему режиму работы и пуска;
- снижением эксплуатационных расходов за счёт сокращения числа заменяемых ламп и отсутствия необходимости замены стартеров;
- дополнительным энергосбережением до 80 % при работе в системах управления светом.
Электронные балласты производятся в массовом количестве и имеют высокий спрос на Западе, где интенсивно внедряются энергосберегающие технологии. В настоящее время электронные балласты находят растущее применение в изделиях ведущих электротехнических и светотехнических фирм Osram, Philips, General Electric, Sylvania, Tridonic, Motorola Lighting и др.
Современный этап развития техники характеризуется интенсивной разработкой и внедрением микропроцессоров и специализированных контроллеров для управления техническими средствами. Ведущие позиции в создании специализированных микросхем для электронных балластов занимают фирмы Motorola, International Rectifier, ST-Electronics. Разработанные устройства являются преобразователями тока сетевой частоты в ток повышенной частоты и содержат необходимые узлы для поддержания оптимального режима зажигания и работы лампы, а также устройства контроля работоспособности ламп и средства защиты от аномальных режимов.
На рынке электронных компонентов имеется достаточный ассортимент продукции, дающий основу для разработки источников питания для трубчатых люминесцентных ламп.
Был проведен подробный анализ технических характеристик и схемных решений на основе специализированных микросхем и микроконтроллеров таких производителей, как Motorola, International Rectifier, ST-Electronics.
Результат технического анализа показал невозможность применения данных электронных компонентов для создания источника питания безэлектродных индукционных ультрафиолетовых ламп. Невозможность применения обуславливает следующее техническое требование – рабочую частоту. Все изделия, использующие данные электронные компоненты, оптимизированы на рабочий диапазон частот от 40 до 75 кГц. Предельная рабочая частота, заявляемая производителями на некоторые электронные компоненты, равна 100 кГц, что как минимум в 2 раза ниже требуемой.
Известно, что компания ST-Electronics производит специализированный микроконтроллер для построения источника питания безэлектродных индукционных ламп. Данный микроконтроллер создан по заказу одного из немногочисленных производителей безэлектродных индукционных ламп – Osram. Техническая информация по нему полностью закрыта. На рынке продаж электронных компонентов он не представлен.
3.2.2 Постановка задачи, принципиальная схема
и описание работы источника питания
Основные требования к устройству:
1. Схема источника питания должна быть резонансного типа с рабочей частотой генерации 200–250 кГц.
2. Должна обеспечиваться возможность регулировки выходной мощности лампы путем регулировки входного питающего сетевого напряжения с помощью ЛАТРа в широком диапазоне напряжений (для импульсного источника питания – нетривиальная задача).
3. Должна обеспечиваться регулировка рабочей частоты возбуждения индуктора лампы.
4. Устройство должно обладать достаточной надежностью и иметь непрерывный режим работы.
Упрощенная блок-схема источника питания представлена на рисунке 3.3.
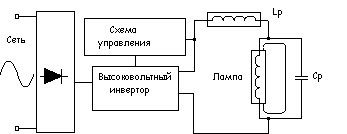
Рисунок 3.3 – Блок-схема источника питания индукционной лампы
Сетевое напряжение выпрямляется, фильтруется. Схема управления задает работу высоковольтного инвертора, который переключает выпрямленное сетевое напряжение с частотой
200 кГц. Нагрузкой инвертора служит резонансный контур, в состав которого входят силовые элементы Lр, Cр и обмотка индуктора лампы, включенная параллельно конденсатору.
В
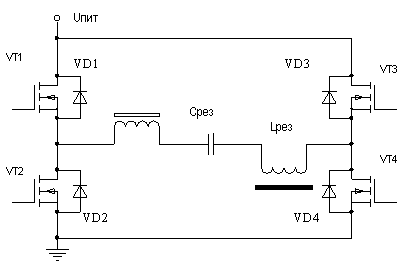
ариант схемы выходного каскада источника питания представлен на рисунке 3.4.
Рисунок 3.4 – Мостовой резонансный преобразователь
График зависимости тока через резонансный контур от времени показан на рисунке 3.5, где Тр – период собственных колебаний контура, Тпр – период преобразования, Тп – время паузы.
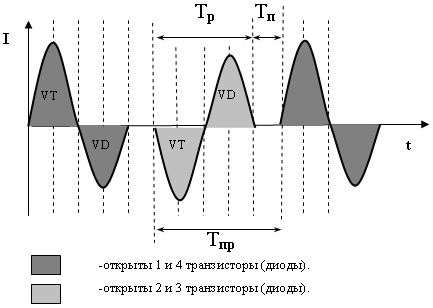
Рисунок 3.5– Ток через резонансный контур
Нагрузка с последовательным LC-контуром периодически подключается полупроводниковыми ключами к входному источнику питания Uпит. На интервале открытого состояния транзисторов происходят резонансный процесс накопления энергии в конденсаторе Срез и передача части энергии в нагрузку. На интервале закрытого состояния транзисторов энергия, накопленная в конденсаторе, через возвратные диоды передается в нагрузку и частично возвращается в источник питания. Потери в транзисторах при выключении равны нулю, так как фронт напряжения на стоке начинается после прохождения тока стока через нуль. Потери на включение определяются углом задержки включения транзисторов; с увеличением нагрузки угол задержки уменьшается, а переключение транзисторов происходит при меньшем значении тока. Это обеспечивает незначительные потери мощности. Форма тока через силовые ключи близка к синусоидальной, транзисторы переключаются при нулевом токе, потери на переключение минимальны.
Применение мостовой схемы преобразователя позволяет создавать источники питания большой мощности. При потреблении нагрузкой мощности менее 300 Вт использование мостовой схемы нецелесообразно. В данной конструкции в качестве выходного каскада использована полумостовая схема. Принципиальная электрическая схема источника питания безэлектродных индукционных ультрафиолетовых ламп представлена на рисунке 3.6. Сетевое напряжение 220 В промышленной частоты поступает на входной фильтр, выполненный на элементах С1, L1, С2, С3 через узел защиты от перенапряжений, включающий в себя варистор Ru1 и предохранитель F1. Соединенный последовательно с предохранителем терморезистор Rt1 с отрицательным коэффициентом сопротивления ограничивает бросок входного тока, обусловленный зарядом емкостного фильтра C4, С5, включенного на выходе выпрямительного диодного моста D1. Выпрямленное сетевое напряжение питает высокочастотный полумостовой инвертор, выполненный на полевых транзисторах V1,V2 (2SK1531).
На микросхеме U1 (TL494) выполнен задающий генератор тактовых импульсов. Он формирует сигналы управления полумостового инвертора. Частота генерации определяется номиналами элементов С5 и R5+ R6. Частота генерации устанавливается на 10 % выше резонансной частоты выходного контура (Fрез = 200 кГц). На выводах 9, 10 микросхемы U1 получаем последовательность прямоугольных импульсов амплитудой 15 В со скважностью, равной двум. Сигналы на выводах 9, 10 находятся в противофазе. С выхода задающего генератора сигналы управления поступают на входы мощных высокочастотных драйверов U2, U3 (MAX4420). Данный тип драйвера позволяет осуществлять работу на нагрузку при пиковом токе до 6 А с фронтом сигнала 20 нс, с максимальной рабочей частотой 300 кГц. С выходов драйверов U2,U3 через разделительные емкости С6, С7 сформированные сигналы поступают на первичные обмотки согласующих трансформаторов Т1, Т2.
Как показала практика макетирования, использование импульсных трансформаторов для управления затворами транзисторов инвертора является самым простым и надежным схемотехническим решением.
Вначале отрабатывался вариант схемы с использованием интегрального высоковольтного драйвера производства International Rectifier IR2110.
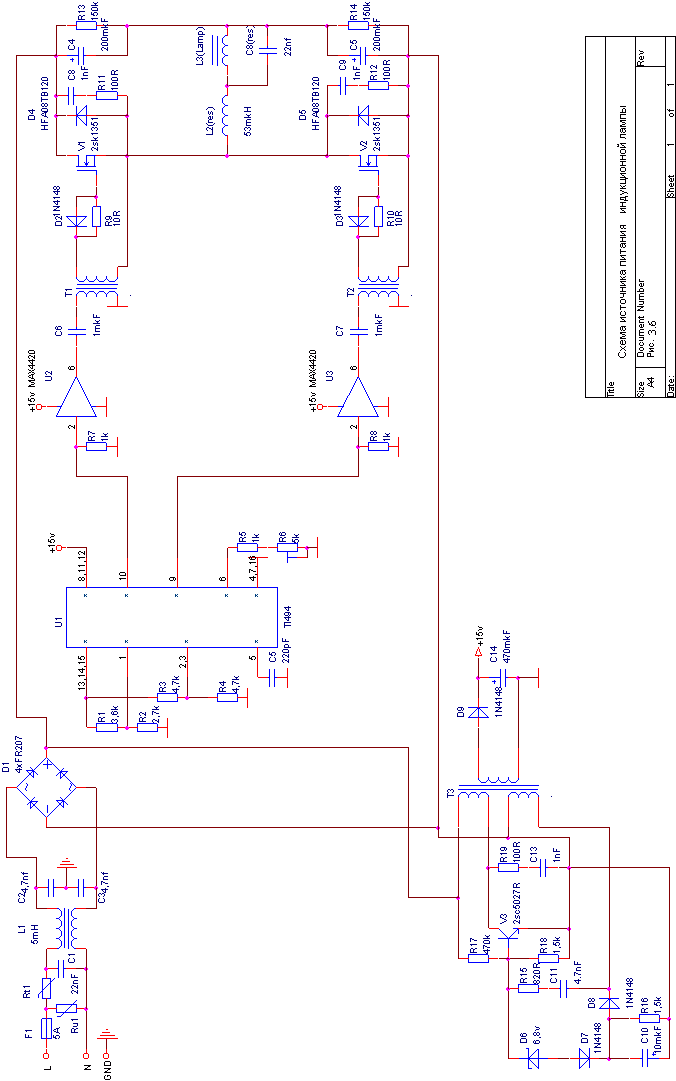
Таблица 3.1 – Список элементов, используемых в схеме блока питания
Обозначение на схеме | Тип элемента | Обозначение на схеме | Тип элемента |
R1 | 3,6 k 0.25w | C9 | 1 nF 1000v |
R2 | 2,7 k 0.25w | C10 | 10 mkF 63v |
R3 | 4,7 k 0.25w | C11 | 4,7 nF 160v |
R4 | 4,7 k 0.25w | C12 | 22 nF 1000v |
R5 | 1 k 0.25w | C13 | 1 nF 1000v |
R6 | 5 k 0.25w | C14 | 470 mkF 35v |
R7 | 1 k 0.25w | D1 | FR207 |
R8 | 1 k 0.25w | D2 | 1N4148 |
R9 | 10R 0.5w | D3 | 1N4148 |
R10 | 10R 0.5w | D4 | HFA08TB120 |
R11 | 100R 0.5w | D5 | HFA08TB120 |
R12 | 100R 0.5w | D6 | BZX6V8 |
R13 | 150 k 0.5w | D7 | 1N4148 |
R14 | 150 k 0.5w | D8 | 1N4148 |
R15 | 820R 0.25w | D9 | 1N4148 |
R16 | 1,5 k 0.25w | U1 | TL494CN |
R17 | 470 k 0.25w | U2 | MAX4420CPA |
R18 | 1,5 k 0.25w | U3 | MAX4420CPA |
R19 | 100R 0.5w | V1 | 2SK1531 |
Ru1 | NVS 5R | V2 | 2SK1531 |
Rt1 | Var 430v | V3 | 2SC5027R |
C1 | 22 nF 630v | T1 | M2000 20w/20w |
C2 | 4,7 nF 1000v | T2 | M2000 20w/20w |
C3 | 4,7 nF 1000v | T3 | M2000 200w/20w/18w |
C4 | 200 mkF 250v | L1 | M2000 5mH |
C5 | 200 mkF 250v | L2 | M2000 36w 53mkH |
C6 | 1 mkF 63v | | |
C7 | 1 mkF 63v | | |
C8 | 1 nF 1000v | | |
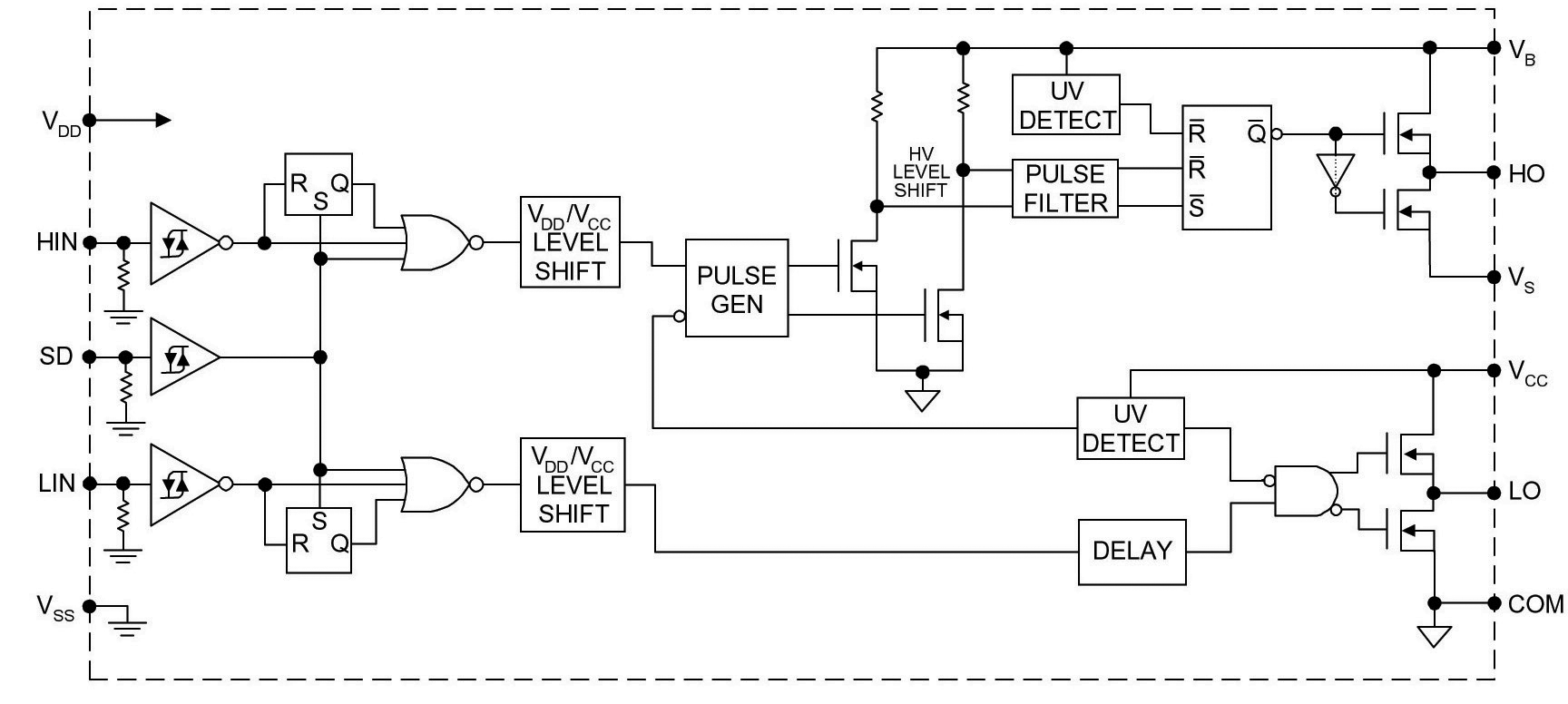
Рисунок 3.7 – Структурная схема драйвера IR2110
Приведенная на рисунке 3.7 схема полумостового драйвера IR2110 иллюстрирует основные схемные решения, заложенные в микросхеме. Драйвер содержит каскады, предназначенные для нормирования входных логических сигналов, каскад сдвига уровня, выходные каскады управления изолированными затворами и устройство контроля напряжения управления. Входы драйвера совместимы с уровнями сигналов TTL – CMOS.
Для повышения помехозащищённости высоковольтного драйвера IR2110 следует принять ряд дополнительных мер. Установка резисторов в цепи затвора силовых транзисторов, а также использование сглаживающей RC-цепи на выходе инвертора устраняет возможность срабатывания (защёлкивания) паразитного тиристора в структуре КМОП драйвера затвора за счёт снижения уровня паразитных емкостных токов, пропорциональных скорости изменения напряжения на силовых транзисторах в режимах переключения. Одновременно для защиты транзистора от самовключения параллельно резистору в цепи затвора рекомендуется подключить диод. Конденсатор сглаживающей RC-цепи должен быть рассчитан таким образом, чтобы его полный перезаряд обеспечивался выходным током инвертора за время паузы между отпирающими импульсами верхнего и нижнего транзисторов. Это время неизменно и составляет 1,2 мкс.
Однако и эти меры оказываются недостаточными, если в процессе работы электронного балласта возникает режим, при котором нагрузка имеет ёмкостный характер. Этот режим соответствует работе на частоте F, ниже резонансной Fрез, и возможен при неправильном расчёте частоты задающего генератора, параметров резонансного контура (индуктивности и ёмкости конденсатора силового контура) или сбоях в системе управления. Он проявляется на этапе зажигания лампы или при аварийном режиме, приводящем к возникновению на выходе инвертора контура с высокой добротностью. В отличие от благоприятного режима (при индуктивном характере нагрузки), когда во включённом состоянии транзистор замыкает на себя ток после его перехода с собственного диода, а заряд и разряд конденсатора сглаживающей RC-цепи осуществляется выходным током инвертора, при ёмкостном характере нагрузки транзистор включается на ток нагрузки, одновременно осуществляя через свою структуру разряд конденсатора сглаживающей RC-цепи и разряд собственной ёмкости сток – исток. Такой режим характеризуется ростом динамических потерь в силовых транзисторах, высокой скоростью изменения напряжения на транзисторах и, соответственно, высоким уровнем ёмкостных токов, что ведёт к снижению помехозащищённости управляющей микросхемы. Усугубляет положение аварийный режим, сопровождающийся многократным возрастанием тока нагрузки по отношению к номинальному и ростом напряжения на паразитных индуктивностях. Как правило, этот режим ведёт к выходу из строя управляющей микросхемы и силовых МОП-транзисторов. Изложенные выше негативные явления проявлялись и в данной конструкции источника питания. Положение усугублялось требованием работы источника в очень широком диапазоне питающих напряжений. Поэтому несмотря на кажущуюся простоту и изящество схемотехническое решение с использованием данного драйвера оказалось непригодным.
С выходов вторичных обмоток трансформаторов Т1, Т2 сформированные сигналы управления через цепочки D2,R9,D3,R10 поступают на затворы силовых транзисторов инвертора V1,V2 (2SK1531). Нагрузкой инвертора служит резонансный контур, в состав которого входят силовые элементы L2, C8 и обмотка индуктора лампы L3, включенная параллельно конденсатору С8.
Номиналы элементов выходного контура рассчитаны таким образом, что резонансная частота напряжения на индукторе лампы в момент ее горения равна 200 кГц.
На элементе V3 (2SC5027) выполнена схема питания (+15 В) задающего генератора U1 и драйверов U2,U3. Собственно схема представляет собой блокинг-генератор с самовозбуждением. Работа схемы построена таким образом, что выходное напряжение (+15 В) появляется при достижении входного сетевого напряжения на входе источника питания ~ 60 В. Этим обеспечивается защита силовой части источника питания от переходных процессов при питании его пониженным сетевым напряжением от ЛАТРа.
3.2.3 Результаты испытаний источника
Источник питания, схема которого представлена на рисунке 3.6, был изготовлен как законченная конструкция. Он успешно использовался на рабочем стенде в составе макета установки ультрафиолетового обеззараживания воды. При помощи данного источника исследовались различные рабочие характеристики безэлектродных индукционных ультрафиолетовых ламп мощностью до 200 Вт.
По результатам его эксплуатации можно сделать следующие выводы:
1. В процессе разработки, макетирования и отладки источника питания выявлены особенности поведения различных конструкций ламп. Получена ценная информация для возможной оптимизации принципиальных электрических схем и конструктива источников питания подобного типа.
2. Оптимизация схемотехники источника питания должна производиться под конкретные фиксированные технические характеристики лампы (заявленная мощность, параметры индуктора, напряжение зажигания лампы).
3. В качестве схемы управления целесообразно использовать микроконтроллер с собственным (созданным разработчиком источника питания) программным обеспечением. Это позволит гибко менять алгоритмы запуска лампы, отслеживать режим ее работы, организовывать защиту. Данный вариант надежно защищает изделие от реинжиниринга при массовом производстве.