Машинознавство, обробка матеріалів у машинобудуванні
Вид материала | Документы |
СодержаниеМодель формування залишкових напружень у поверхневому шарі деталей із загартованих сталей при торцевому фрезеруванні Шорсткість поверхні після растрового фрезерування |
- Зміни до Порядку проведення експертизи матеріалів на лікарські засоби, що подаються, 2751.76kb.
- Можна констатувати, що тривала криза в українській промисловості, що особливо зачепила, 17.29kb.
- Відповідно до постанови Кабінету Міністрів України від 26., 3656.85kb.
- Робоча навчальна програма предмет Методи дослідження властивостей матеріалів (Р-32), 48.64kb.
- Робоча навчальна програма кредитного модуля з дисципліни "Цифрова обробка сигналів", 410.54kb.
- Обробка сировини. Виробництво напівфабрикатів обробка овочів І грибів значення овочів, 196.83kb.
- Вимоги до оформлення матеріалів тез доповідей, 134.94kb.
- Діагностика сектору будівельних матеріалів, 235.87kb.
- Робоча навчальна програма предмет Фізика матеріалів (П-54) Спеціальність, 33.89kb.
- Міністерство освіти І науки україни наказ, 54.87kb.
^ МОДЕЛЬ ФОРМУВАННЯ ЗАЛИШКОВИХ НАПРУЖЕНЬ У ПОВЕРХНЕВОМУ ШАРІ ДЕТАЛЕЙ ІЗ ЗАГАРТОВАНИХ СТАЛЕЙ ПРИ ТОРЦЕВОМУ ФРЕЗЕРУВАННІ
Розвиток сучасного машинобудування тісно пов’язаний з постійним підвищенням вимог до якості виготовленої продукції. Одним з основних показників якості механічно оброблених деталей є параметри стану поверхневого шару. Саме від властивостей поверхневого шару безпосередньо залежать майбутні експлуатаційні характеристики деталей.
Проблема, пов’язана з необхідністю керування процесом механічної обробки для отримання необхідних якісних характеристик деталей, завжди залишається актуальною для будь-якого машинобудівного підприємства. При керуванні процесом механічної обробки необхідно вирішувати складне завдання оптимізації, що враховує суперечливі вимоги: необхідно співставляти економічну ефективність з фізичними процесами, що виникають у зоні різання.
У даній роботі пропонується структурна модель керування процесом торцевого фрезерування, що дає можливість отримати необхідні зв’язки між параметрами стану поверхневого шару та вхідними і функціональними параметрами процесу обробки. На базі структурної моделі пропонується розроблена математична модель формування залишкових напружень від дії силового, температурного факторів та структурно-фазових перетворень у поверхневому шарі деталі при торцевому фрезеруванні.
Актуальність розробки методів аналітичного розрахунку залишкових напружень пов’язана з великими труднощами та великою вартістю обладнання при вимірюванні внутрішніх напружень у виробничих умовах. Розробка методик аналітичного визначення технологічних залишкових напружень дозволить підвищити якість параметрів стану поверхневого шару відповідальних деталей та створення комп’ютерних моделей на їх основі.
Фізика твердого тіла розглядає залишкові напруження в деталі як наслідок викривлення кристалічної решітки. Величина макронапружень визначається насамперед щільністю однорідних дислокацій. Знак макронапружень залежить від характеру розміщення однорідних дислокацій відносно поверхні деталі. За наявності в поверхневому шарі більшої кількості від’ємних дислокацій виникають напруження розтягу. А за наявності більшої кількості позитивних дислокацій – напруження стиску.
Дійсні залишкові напруження в поверхневому шарі можливо вирахувати алгебраїчно, склавши суми величин початкових залишкових напружень та напружень від дії силового, температурного факторів і структурно-фазових перетворень:
-
.
(1)
Значення початкових залишкових напружень у поверхневому шарі деталі безпосередньо залежать від попередніх механічних, термічних та інших операцій.
Силова взаємодія різального інструменту та деталі супроводжує виникнення пружних та пластичних деформацій металу, що викликає утворення залишкових напружень.
Сумарні залишкові напруження від дії силового фактора можливо знайти як суму напружень стиску та розтягу, спричинених силовим контактом леза різального інструменту з поверхневим шаром деталі.
При стиску залежність між напруженнями та деформацією описується кривою, що складається з трьох ділянок:
- ділянка пружної деформації
-
, при 0 <
<
;
(2)
- ділянка малих пластичних деформацій
-
, при
<
<
;
(3)
-
© А.М. Снитко, 2011
ділянка різкого зростання величини умовних напружень при відносно невеликому зростанні пластичної деформації
-
, при
<
<
.
(4)
При розтяганні пружна деформація описується аналогічно виразу (2), а пластична деформація в діапазоні
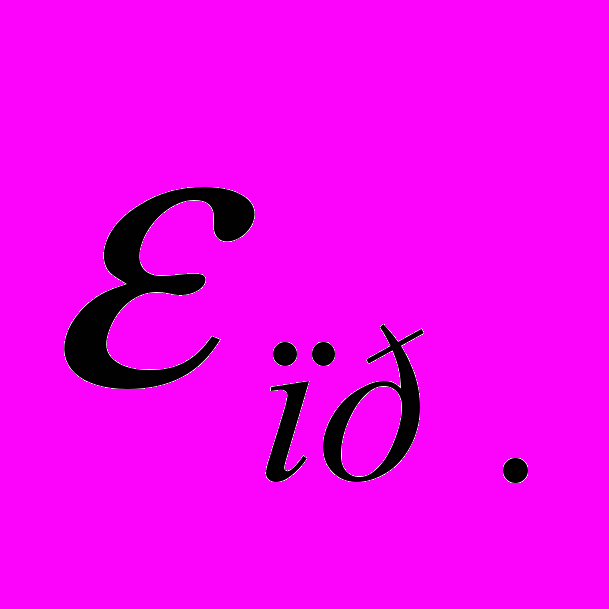
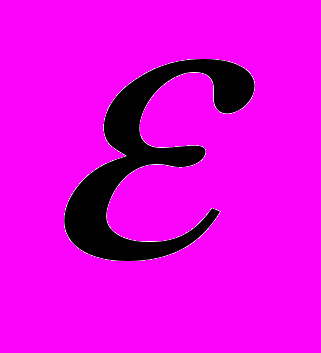
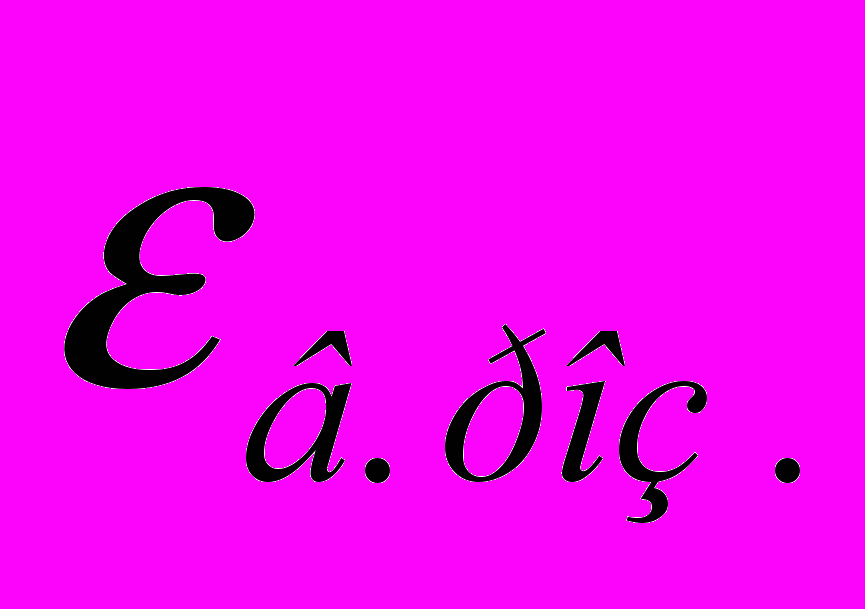
Якщо врахувати, що робота навантаження дорівнює роботі розвантаження контактної ділянки, то можна отримати величини залишкових напружень з формул:
- при стиску
-
;
(5)
- при розтяганні
-
.
(6)
Сумарні залишкові напруження від дії силового фактора визначаються за формулою:
-
.
(7)
При зміні температури залишкові напруження виникають внаслідок наявності в матеріалі різних фаз, що мають різні коефіцієнти лінійного розширення
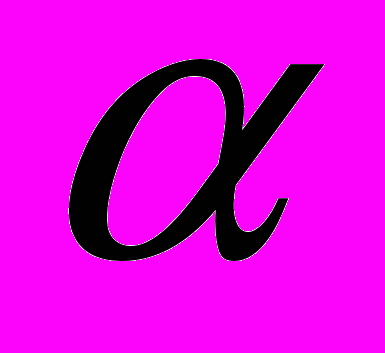
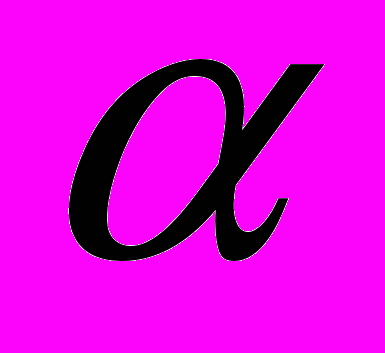
Дію температурного фактора на величину залишкових напружень описує формула:
-
,
(8)
де
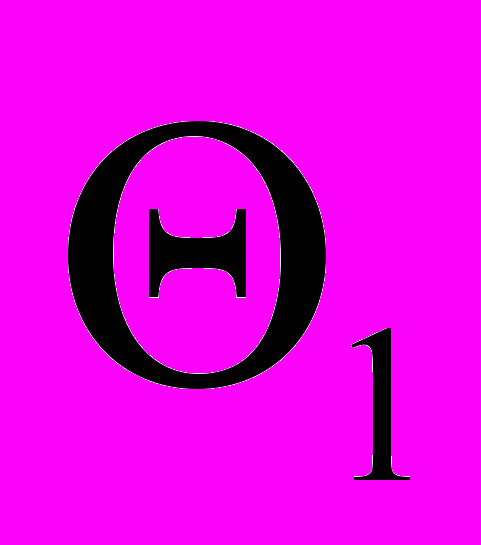
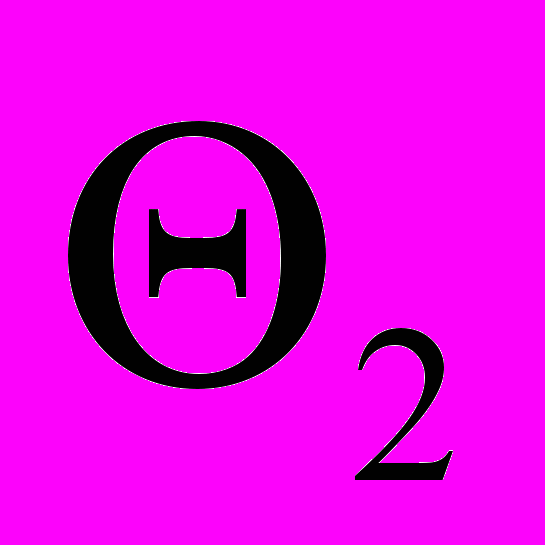
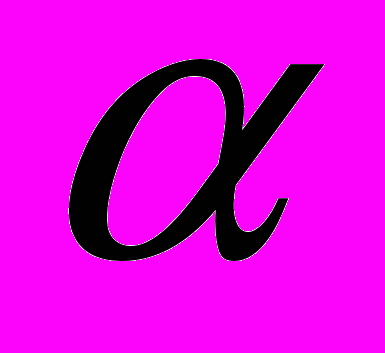
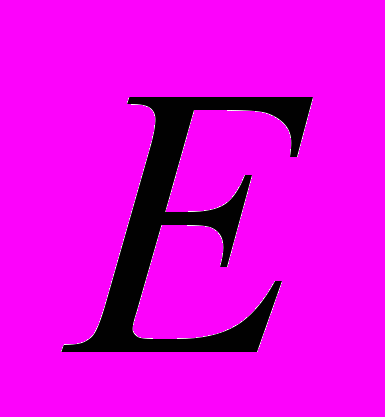
Високий поверхневий нагрів загартованої сталі може викликати розпад залишкового аустеніту, а також перехід тетрагонального мартенситу в кубічний або навіть утворення ферито-карбідної механічної суміші. Через нерівномірну зміну температури в поверхневому шарі деталі, на різних глибинах металу виникають шари металу різної структури і відповідно різної густини. Наявність зон металу з різною структурою призводить до виникнення в цих зонах значних за величиною залишкових напружень різного знака. Також частково виникають структурно-фазові перетворення від дії силового фактора. Адже, як відомо, при пластичних деформаціях залишковий аустеніт може перетворюватися на мартенсит.
Формування залишкових напружень від дії структурно-фазових перетворень можливо розрахувати за формулою:
-
,
(9)
де Е – модуль пружності;
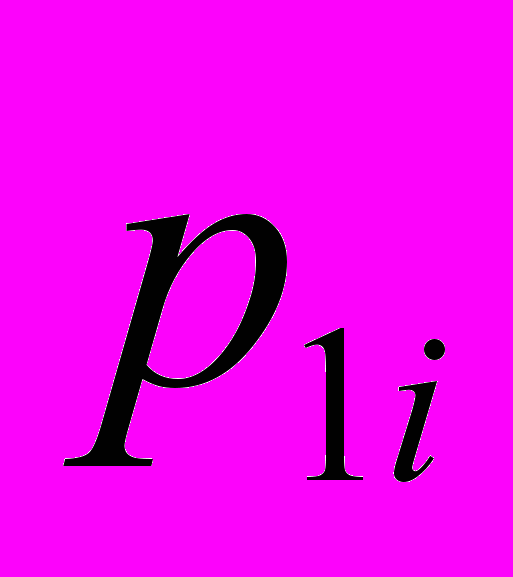
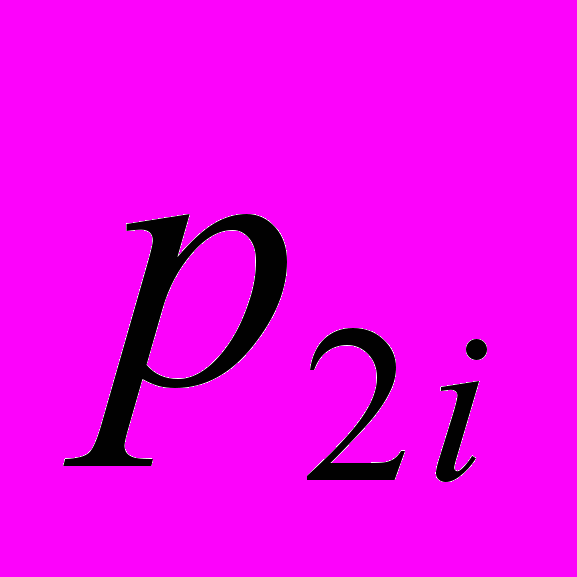
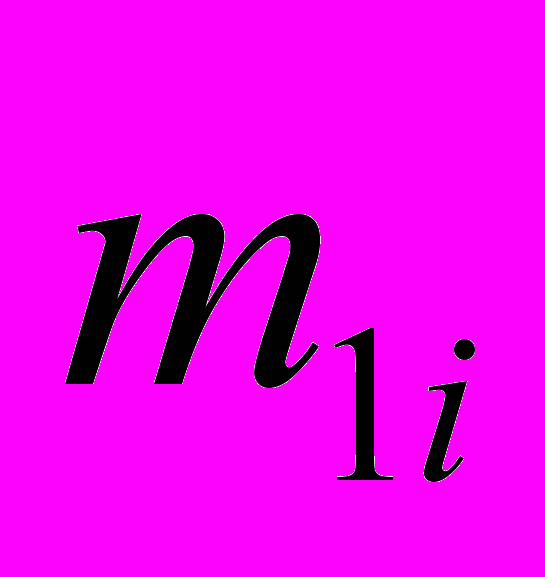
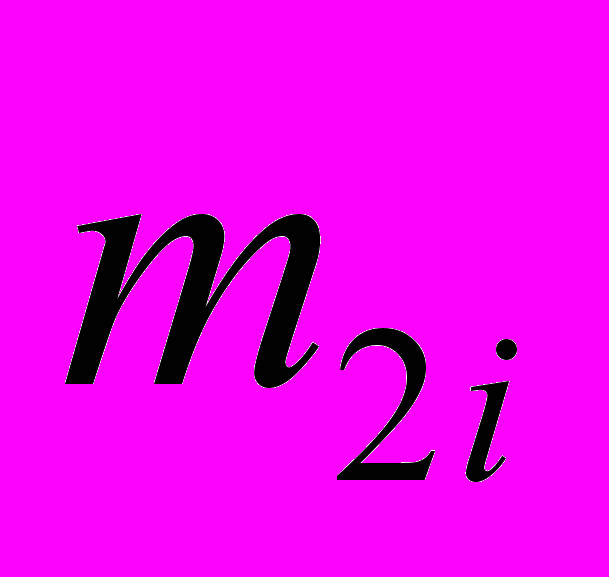
Запропонована методика розрахунку дозволить ще на етапі попередньої підготовки виробництва прогнозувати залишкові напруження в поверхневому шарі деталей. Формування поверхневого шару із заздалегідь заданими властивостями дозволить значно підвищити якість та довговічність продукції машинобудування.
УДК 612.914
В.Є. Юмашев, к.т.н., доц.
О.А. Степчин, інж.
Житомирський державний технологічний університет
^ ШОРСТКІСТЬ ПОВЕРХНІ ПІСЛЯ РАСТРОВОГО ФРЕЗЕРУВАННЯ
СФЕРИЧНИМИ ФРЕЗАМИ ПРОСТОРОВО-СКЛАДНИХ ПОВЕРХОНЬ
Обробка сферичними фрезами як метод отримання просторово-складних поверхонь з’явилася нещодавно, проте широко застосовується в різних галузях промислового виробництва. В сучасних технологічних процесах сферичне фрезерування застосовується при виготовленні моделей, пресових штампів, детонаційних інструментів, форм, відлитих під тиском. Цей метод використовують при 4,5-осьовій обробці деталей зі складним профілем з алюмінію та титану, з’єднувальних елементів зі скла, пластика або композита, виготовленні лопаті та турбіни літаків, газових та парових машин.
Обробка поверхонь сферичними фрезами може відбуватися у двох варіантах побудови траєкторії переміщення інструмента. Перший варіант – по січних лініях площин, що розміщені перпендикулярно осі обертання фрези (умовно – контурний). Другий – по лініях січних площин, що розміщені паралельно осі обертання фрези (умовно – растровий). При растровому фрезеруванні має значення напрямок подачі фрези: згори донизу чи знизу догори.
Під час фрезерування під дією складових сил різання виникають вібрації. Шорсткість обробленої поверхні суттєво залежить від їх величини та напрямку. Для встановлення цієї залежності була розглянута розрахункова силова схема. Вона допомогла визначити нерівнозначний вплив складових вібрацій на висоту нерівностей поверхні. Так було припущено, що основний вплив на шорсткість справляють вібрації, напрямок яких має більший кут до твірної оброблюваної поверхні. Вони утворюють профіль мікронерівностей. Вібрації під малим кутом матимуть згладжувальний характер. За цим припущенням, з розрахункової схеми випливає, що у випадку, коли кут нахилу твірної оброблюваної поверхні до основи
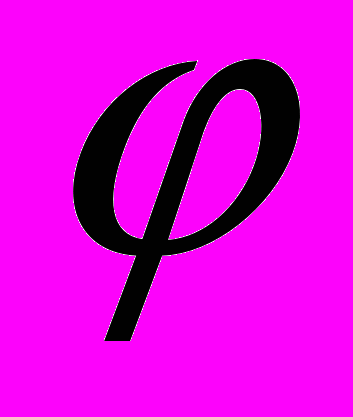
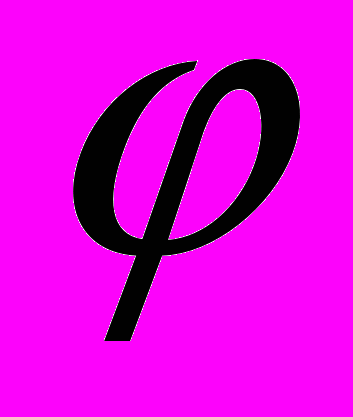
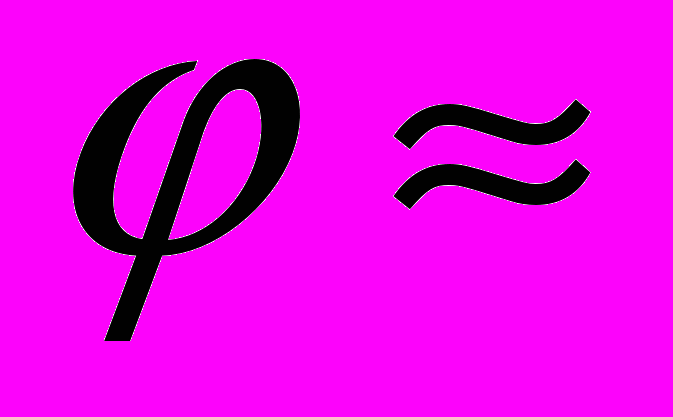
Для експериментального підтвердження наведеного вище припущення, було проведене фрезерування алюмінієвого сплаву Д16. Для обробки використовувався вертикальний, гравірувально-фрезерний верстат із системою керування Mach3Mill. Під час різання вимірювалися вібрації по осях верстата Z та Y (для наведеного вище позначення Po та Pr відповідно). Амплітуда вібрацій вимірювалася п’єзодатчиками ПД-4. Отримані дані записувалися та оброблялися за допомогою комп’ютерної програми LGraph2. На оброблених ділянках була виміряна шорсткість.
Результати експерименту, в цілому, підтверджують теоретичні припущення стосовно впливу кута нахилу твірної та напрямку руху фрези на шорсткість обробленої поверхні. Але треба зазначити необхідність додаткової перевірки теорії на сучасному промисловому обладнанні. Це обумовлено тим, що додатково проведені вимірювання жорсткості використаного верстата показали, що він має низьку та нерівномірну по різних осях жорсткість. Жорсткість по осі Z (вертикальній) виявилася в два рази меншою, ніж по осях X та Y (повздовжній та поперечній).
Цей факт вносить значну похибку в коректність експерименту, особливо за значеннями шорсткості обробленої поверхні. В масиві результатів вимірювань присутні дані, що ставлять під сумнів теоретичні припущення.
© В.Є. Юмашев, О.А. Степчин, 2011