Машинознавство, обробка матеріалів у машинобудуванні
Вид материала | Документы |
- Зміни до Порядку проведення експертизи матеріалів на лікарські засоби, що подаються, 2751.76kb.
- Можна констатувати, що тривала криза в українській промисловості, що особливо зачепила, 17.29kb.
- Відповідно до постанови Кабінету Міністрів України від 26., 3656.85kb.
- Робоча навчальна програма предмет Методи дослідження властивостей матеріалів (Р-32), 48.64kb.
- Робоча навчальна програма кредитного модуля з дисципліни "Цифрова обробка сигналів", 410.54kb.
- Обробка сировини. Виробництво напівфабрикатів обробка овочів І грибів значення овочів, 196.83kb.
- Вимоги до оформлення матеріалів тез доповідей, 134.94kb.
- Діагностика сектору будівельних матеріалів, 235.87kb.
- Робоча навчальна програма предмет Фізика матеріалів (П-54) Спеціальність, 33.89kb.
- Міністерство освіти І науки україни наказ, 54.87kb.
Житомирський державний технологічний університет
СУЧАСНІ ІНСТРУМЕНТАЛЬНІ МАТЕРІАЛИ ДЛЯ ОБРОБКИ ПЛОСКИХ ПОВЕРХОНЬ ДЕТАЛЕЙ З ВАЖКООБРОБЛЮВАНИХ МАТЕРІАЛІВ ТОРЦЕВИМ ФРЕЗЕРУВАННЯМ
Для чорнової, напівчистової, чистової обробки плоских поверхонь деталей із чавунів і загартованих сталей використовують торцеві фрези, оснащені полікристалічними надтвердими матеріалами (ПНТМ). Основні форми різальних пластин з композитів, що випускаються країнами пострадянського простору: змінні непереточувані круглої форми з композита 01, 05, 10; змінні непереточувані двошарові круглої форми з композита 10Д; змінні непереточувані ромбічної форми з композита 10Д; змінні непереточувані квадратної форми з композита 05; змінні непереточувані тригранної форми з композита 05; змінні непереточувані двошарові ромбічної форми з композита 10Д, двошарові пластини з белбора (композит 02) діаметром 8 мм, з кіборита діаметром 7 мм.
Використання сучасних надтвердих матеріалів як різальної частини ножів ступінчастих торцевих фрез дає можливість суттєво збільшити максимально допустимий припуск на один ступінь фрези. Марка ПНТМ, форма й розміри різальної пластини обираються з врахуванням: 1) властивостей оброблюваного матеріалу; 2) виду обробки (чистова, напівчистова, чорнова); 3) схеми різання (послідовна або ступінчаста); 4) способу кріплення пластини в корпусі фрези; 5) технологічних особливостей оброблюваної (закритої чи відкритої) поверхні (існування пазів, отворів). Провідні світові фірми також інтенсивно розвивають виробництво та впроваджують інструментальні матеріали для обробки плоских поверхонь деталей з важкооброблюваних матеріалів.
Аналіз інструментальних рішень для обробки торцевим фрезеруванням деталей з високоміцних чавунів (ВЧ), представлений фірмами Kyocera, Tungaloy, Sumitomo Electric, Hitachi і Mitsubishi Materials, SECO Carboloy, Becker Diamantwerkzeuge, показує наступне.
Основні проблеми обробки цих чавунів пов'язані з їхньою підвищеною міцністю (до 1200 Н/мм2), що приводить до підвищеного зношування інструментів. Тому для фрезерування ВЧ рекомендуються фрези з обертальними пластинами. Зазначено, що оптимальним різальним матеріалом при торцевому фрезеруванні ВЧ є твердий сплав з покриттям (швидкість різання 100–200 м/хв.), кераміка (400–600 м/хв.) і ПНТМ. Фрезерування вимагає збільшення крутних моментів на шпинделі верстатів і збільшення кількості різальних кромок в інструментах.
З
© Г.М. Виговський, О.А. Громовий, В.В. Сєров, О.С. Волков, 2011
окрема, SECO Carboloy пропонує багатогранні різальні пластини нового покоління Triple Zero. Пластини ТК2000 з покриттям призначені для важкої чорнової обробки, нестабільних умов переривчастого різання. Фірма Becker Diamantwerkzeuge випускає двосторонні пластини з різальною частиною з надтвердих матеріалів, які збільшують ресурс стійкості інструментів. Пластини зі змішаної кераміки з покриттям, розроблені фірмою Tungaloy, призначені для чорнового й чистового фрезерування чавуну зі швидкістю до 2000 м/хв. Iscar випущена серія торцевих фрез F45NMD-R08 з діаметрами 80–200 мм, оснащених твердими сплавами і придатних для чорнової та напівчистової обробки із глибиною різання до 5,5 мм. У більшості випадків фрезерування виконують на верстатах підвищеної жорсткості інструментом з кількістю різальних ножів від 2 (при діаметрі фрези до 12 мм) до 8 (при діаметрі фрези до 130 мм). Одне з провідних місць у виробництві пластин з ПНТМ та інструментів на основі даних пластин посідає корпорація STELLRAM. Вона займається випуском двошарових пластин з ПНТМ класів CVD (Chemical vapor deposition – хімічно нанесені покриття) та PVD (Physical vapor deposition – фізично нанесені покриття). Zinner GmbН випускає двошарові пластини, різальна частина яких виконується з кубічного нітриду бору, твердосплавна пластина має товщину 2,3 мм. Така двошарова різальна пластина припаюється до опорної пластини, виготовленої з інструментальної сталі. Спеціальна конструкція кріплення збірної (багатошарової) пластини в корпусах торцевих фрез дозволяє регулювати значення кутів у плані. Фірмою Nippon Oil організований промисловий випуск надтвердого матеріалу під торговельною назвою «вюрцин». Полікристали вюрцину виготовляють на твердосплавній основі. Крім того, фірма випускає стандартні багатогранні твердосплавні пластини із впаяними у вершини полікристалами вюрцину. Sandvik Coromant на основі кубічного нітриду бору BNк випускає двошарові пластини з товщиною робочого шару з полікристалічного кубічного нітриду бору до 0,7 мм.
УДК 621.83
О.С. Волков, магістрант
Науковий керівник – к.т.н., проф. Лоєв В.Ю.
Житомирський державний технологічний університет
^ ВПЛИВ КУЛЬКОВИХ ГВИНТОВИХ ПЕРЕДАЧ НА ТОЧНІСТЬ ПОЗИЦІЮВАННЯ РОБОЧИХ ОРГАНІВ ВЕРСТАТІВ З ЧПУ
Найбільш ефективним пристроєм для перетворення обертального руху на поступальний у виконавчих механізмах відповідального призначення є кулькові гвинтові передачі (КГП). Кулькові гвинтові передачі стають одним з найбільш широко вживаних компонентів механічних передач.
В даний час КГП широко застосовують у виконавчих механізмах, системах відслідковування і відповідальних силових передачах (верстатобудування, робототехніка, авіаційна і космічна техніка, залізничний транспорт, виробництво дорожніх машин, атомна енергетика тощо). Висока кінематична точність, плавність ходу, малий момент тертя, високий ККД — усе це визначило значну потребу машинобудування в таких передачах. Завдяки компактним розмірам і простоті конструкції КГП можуть бути вільно інтегровані в різноманітні машини і механізми, зокрема з гідравлічним і пневматичним приводами. У верстатах з ЧПУ кулькові гвинтові передачі допомагають забезпечити точність позиціювання.
Головні переваги кулькових гвинтових передач:
– низькі втрати на тертя і, як наслідок, можливість використання менш потужного двигуна і меншої кількості мастила;
– майже повна незалежність сили тертя від швидкості й дуже мале тертя спокою, що сприяє забезпеченню рівномірності (плавності) руху;
– ККД передач досягає значення 0,95, порівняно з ККД передач гвинт–гайка ковзання (для цих передач ККД становить від 0,2 до 0,4);
– можливість повного усунення зазорів і створення натягу, що забезпечує високу осьову жорсткість, що, в свою чергу, підвищує навантажуваність передачі при малих габаритах;
– невеликий нагрів у процесі роботи, висока швидкодія і точність позиціювання, великий експлуатаційний ресурс.
Якість обробки на верстатах залежить від точності позиціювання робочих органів (РО). У верстатах з ЧПУ переміщення РО виконується механізмами відслідковування. Привід із КГП має мінімальний (або нульовий) люфт, і, отже, його точність значно вища, що дозволяє використовувати такі приводи в механізмах, у яких дуже важливі точність і повторюваність позиціювання.
Точність верстата залежить, у першу чергу, від його здатності витримувати швидкозмінні умови експлуатації. Перехід від чорнової обробки до чистової тягне за собою зміну механічних та термічних навантажень на верстат, які впливають на точність. Особливу роль при цьому відіграють приводи подач. Вони активно використовуються при великих швидкостях обробки і високих прискореннях і виділяють багато тепла, яке призводить до нагрівання частин верстата. За відсутності відповідних засобів позиціювання (наприклад, лінійних датчиків зворотного зв'язку за положенням для КГП) за короткий час це тепло викликає похибки позиціювання до 100 мкм. Залежно від швидкості переміщення і сили подачі різниця температур у КГП може дуже швидко змінюватися. Термічні розширення, що виникають при цьому (зазвичай до 100 мкм/м протягом 20 хв.) на верстатах без датчиків зворотного зв'язку, можуть призвести до суттєвих похибок. У зв'язку з цим використовують датчики лінійних переміщень. Вони визначають положення рухомих органів без додаткових механічних передаточних елементів. Якщо визначення положення виконується за допомогою датчика лінійного переміщення, то контур регулювання охоплює механіку приводів. Даний спосіб допомагає виключити цілий ряд джерел похибок:
- похибка позиціювання, викликана нагріванням кулькової гвинтової пари;
- похибка, викликана наявністю зазорів у КГП;
- кінематична похибка, викликана позиційною похибкою КГП.
З
© О.С. Волков, 2011
метою регулювання зазорів розроблені КГП із двома гайками, змінюючи взаємне розташування яких, можна управляти величиною осьового зазору аж до внутрішнього натягу різної інтенсивності. В основному, одержали поширення такі два способи усунення осьового зазору й створення натягу: регулюється відносне розташування гайок в осьовому напрямку при незмінному кутовому їх розташуванні; регулюється відносне розташування гайок у кутовому положенні при їх незмінному осьовому взаємному розташуванні. Другий спосіб дозволяє створювати великий натяг і, отже, забезпечує більш високу жорсткість.
При конструюванні КГП особливу увагу приділяють осьовій жорсткості гвинта. Відомі такі напрямки її підвищення: гвинт встановлюють на двох опорах; в конструкцію передачі вводять додатково тіла кочення; корпус КГП виготовляють у вигляді котушки, у фланцях якої закріплені підшипники. Проте КГП з підвищеною жорсткістю гвинта мають, як правило, великі габарити. Для їх зменшення і підвищення навантаженості вводять додаткові тіла кочення меншого діаметра або замінюють їх роликами з конічною поверхнею, зменшують габаритні розміри пристрою для регулювання натягу, використовують додаткові елементи з антифрикційних матеріалів. Також для збільшення жорсткості КГП їх часто обладнують нерухомими опорами на обох кінцях.
Для попередження явищ, що впливають на точність, швидкість переміщення та інші характеристики КГП, застосовується комплекс захисних заходів, у тому числі змащування і захист гвинта та рухомих елементів від пилу, вологи і механічних частинок. Одним з найбільш ефективних заходів є спеціальна фізико-хімічна обробка компонентів КГП, що забезпечує збільшення твердості поверхневого шару і збереження точнісних характеристик (азотування, обробка СВЧ та ін.).
Широке застосування КГП обумовлює необхідність постійного підвищення їхньої зносостійкості, довговічності, коефіцієнта корисної дії, жорсткості та здатності до навантаження. Проте навіть створення якісно нових КГП не вирішило остаточно питання їх зношування і довговічності. Постають нові завдання, які пов'язані з осьовою жорсткістю гвинта і навантаженістю КГП, чутливістю гайки до дії радіальних сил, а також з вирішенням протиріччя “навантаження–точність”. Зазначене призводить до необхідності пошуку принципово нових технічних рішень при створенні КГП.
УДК 621.9.02
М.А. Гайценредер, магістрант
Науковий керівник – к.т.н., проф. Лоєв В.Ю.
Житомирський державний технологічний університет
^ АНАЛІЗ І ОПТИМІЗАЦІЯ КОНСТРУКЦІЙ МЕХАНІЗМІВ ЗАКРІПЛЕННЯ ЗМІННИХ ПЛАСТИН ЛЕЗОВИХ ІНСТРУМЕНТІВ
Закріплення пластин з полікристалічного кубічного нітриду бору через ряд властивостей матеріалу (хімічна стійкість, незмочуваність розплавами металів, висока твердість тощо) викликає необхідність застосовувати такі способи: гаряче пресування в суміші порошків кольорових металів; заливка розплавленим металом; завальцювання і зачеканення в сталеві втулки. Ці способи базуються на тому, що метал і залишкові пружні зусилля через сили тертя утримують пластини. Крім того, розрізняють способи вакуумної пайки на основі адгезійно активних припоїв (використання молекулярної взаємодії). За інформацією д.т.н., проф. С.А. Климента, при цих способах не вдається уникнути браку, який може складати до 30 %. Другим суттєвим недоліком таких способів закріплення є можливість повторного використання інструменту (в результаті зношування) тільки після перезаточування, кількість якого обмежена малими розмірами пластинок.
Експериментами і дослідженнями було доведено, що найбільш перспективним способом закріплення шліфованих пластинок є механічний. Згідно зі стандартом ISO5608 передбачені різноманітні способи закріплення різальних пластин, а саме: прихоплювачем зверху (спосіб С); через центральний отвір (спосіб Р); через отвір і прихоплювачем (спосіб М); центральним гвинтом (спосіб S); без отворів за бокові поверхні (спосіб D); нерознімним методом (спосіб В). Найбільшого розповсюдження набули способи С, Р і В.
Вітчизняними інструментальними підприємствами інструменти з механічним закріпленням різальних пластин (різці, фрези) практично не виготовляються, тобто використовується виключно спосіб В. Це викликано, в першу чергу, необхідними занадто високими вимогами до точності виготовлення всіх без винятку деталей інструменту, а саме корпусу з ложементом під установлювання і закріплення різальних пластин із забезпеченням їх точного базування і надійного довготривалого утримання. Взаємне точне розташування різальних елементів у багатолезовому інструменті має визначальний вплив не тільки на працездатність конструкції, але й на точнісні параметри й якість оброблених поверхонь. Мова йде про мікрометричні відхилення розмірів і відповідну якість поверхонь (шорсткість, залишкові напруження тощо), що можливо забезпечити обробкою виключно на високоточному обладнанні з застосуванням сучасних технологічних процесів.
Перевагою механічних способів закріплення пластинок з НТМ є, перш за все, можливість використання декількох різальних кромок, а для круглих – практично всієї її колової довжини. Також у даній роботі використовується та досліджується конструкція, яку розробили на кафедрі технології машинобудування і конструювання технічних систем ЖДТУ. Це нова конструкція механізму затискання круглих пластинок з НТМ. Особливістю конструкції є застосування матеріалу з відповідною термообробкою і високопружними характеристиками для виготовлення корпусу. При цьому використовується спосіб закріплення D. Особливістю такого методу закріплення є відсутність прихоплювачів та притискачів, які погіршують сходження стружки. Крім точнісних проблем, про які вже йшлося, суттєва складність виникає в забезпеченні надійності й безпечності роботи, особливо при швидкісному і надшвидкісному різанні фрезами різноманітних конструкцій. При використанні існуючих конструкцій механізмів затискання пластин в інструментах для токарної обробки після певного часу експлуатації в результаті вібрацій і релаксаційних процесів відбувається ослаблення затягнутих стиків, але це не впливає суттєво на безпечність процесу через відносну нерухомість різців. Зовсім інші обставини виникають у разі застосування швидкообертального інструменту, коли кожна відокремлена від інструменту частинка може мати швидкість кулі. Небезпечними є не тільки самі пластинки з НТМ в разі застосування способу кріплення Р і D, але й елементи кріплення (прихоплювачі тощо) при використанні способів кріплення С і М. Всі способи закріплення пластинок, крім нерознімного В, налічують різьові з’єднання, що знаходяться під навантаженням зусилля затиску і змінних, переривчасто діючих сил різання при фрезеруванні. В новій конструкції передбачено встановлення під різальну пластину твердосплавної пластини, що забезпечує досягнення відомих переваг.
© М.А. Гайценредер, 2011
УДК 620.172.251.12, 536.2
В.П. Гонтаровський, к.т.н., доц.
Житомирський державний технологічний університет
О.В. Горобець, асист.
Житомирський національний агроекологічний університет
^ ЗАХИСТ ТРУБ ВІД КОРОЗІЇ ДВОШАРОВИМИ ТЕРМОУСАДКОВИМИ СТРІЧКАМИ
ТА ЕКСТРУЗИВНИМИ МЕТОДАМИ
Трубопроводи експлуатуються в досить складних умовах. Ними транспортують різноманітні, в тому числі й агресивні, продукти, їх вкладають у ґрунт, який часто має високу корозійну активність, вони контактують з промисловою атмосферою, перебувають під дією високого тиску продукту і змінного температурного режиму. Тому й антикорозійні покриття повинні мати цілий комплекс властивостей, які б забезпечували надійний захист трубопроводу від корозії. Це достатня механічна міцність та еластичність, хімічна й біологічна стійкість, низька вологопроникність, стабільність техніко-експлуатаційних якостей у часі впродовж терміну експлуатації, простота технології виробництва й нанесення в заводських і польових умовах. Крім того, матеріали, що входять до складу покриття, повинні бути недефіцитними, а саме покриття – недорогим і довговічним.
Це завдання може бути вирішене розгорненням виробництва термоусадкових матеріалів, головною особливістю яких є відновлення початкової форми після нагріву, а також високі техніко-експлуатаційні параметри. Найбільш оптимальним є двошаровий варіант ізоляційного покриття труби. Тому для антикорозійного захисту трубопроводів використовуються двошарові термоусадкові стрічки (ДТС). Вони складаються з клеючого легкоплавкого шару (як правило, використовується севілен), який безпосередньо контактує з металом і шаром основного захисного матеріалу (поліетилену з різними добавками).
Формування ізоляційного покриття здійснюється так: на очищену нагріту трубу намотують стрічку. При цьому клеєний шар (адгезив) плавиться, заповнюючи нерівності на поверхні металу. При охолодженні поліетиленова основа термоусаджується і щільно притискає адгезив, завдяки чому утворюється суцільне покриття.
Нами були проведені дослідження на розтягання з метою отримання характеристик міцності та пластичності, визначення модулів Юнга й коефіцієнтів Пуассона та адгезивної міцності для різних ДТС. Випробування проводилося на зразках, товщина яких відповідала товщині досліджуваних матеріалів, шириною 10 мм, вирізаних під кутами через кожні 30°, які відраховувалися від поздовжньої осі стрічки.
Результати досліджень показали, що матеріал має ортогональну анізотропію, причому головні осі пружної симетрії збігаються з поздовжньою і поперечною геометричними осями стрічки.
Проведені дослідження дозволили зробити висновок, що ДТС відповідають усім вимогам до ізоляційних покриттів трубопроводів.
Іншою перспективною технологією захисту труб від корозії є екструзивний метод нанесення покриття, технологія розроблена на науково-технічному підприємстві «Ікар», розрахована на ізоляцію труб діаметром 57, 89, 108, 133, 159 мм. Попередньо труби проходять водяну або дробоструминну очистку, після чого їх нагрівають в індукційному нагрівачі до температури 105–110 °С. Потім на трубу наноситься адгезійний шар севілену товщиною 0,2 мм і захисний шар поліетилену високого тиску (ПВТ) товщиною 2,5 мм, які видавлюються «панчохою» під вакуумом із суміщеної екструзивної головки при температурі 150–180 °С. Севілен та поліетилен подаються в головку з екструдерів ЧП-32 та ЧП-63 відповідно. Далі проводиться водяне охолодження труб у ваннах до температури 50 °С, в процесі чого відбувається термоусадка й затвердіння ізоляції.
При розробці таких технологій потрібно знати розподіл температури по товщині труби й покриття по мірі охолодження, що дозволяє визначити час охолодження труб з поліетиленовим покриттям до необхідної температури та розраховувати напруження, які виникають у покритті.
В даній роботі наведені результати розв’язку нестаціонарної задачі теплопровідності методом кінцевих елементів.
Б
© В.П. Гонтаровський, О.В. Горобець, 2011
ули проведені розрахунки для двох типорозмірів стальних труб: з товщиною стінки 4 мм при товщині покриття 2 мм і з товщиною стінки 6 мм при товщині покриття 2,2 мм. Стальна труба, нагріта до температури 110 °С, покрита зовні ПВТ, нагрітим до температури 180 °С. Розрахунки проведені для охолодження труб на повітрі та при рівномірному омиванні водою при температурі 25 °С. Теплофізичні властивості стальної труби й поліетиленового покриття наведені в таблиці 1.
Таблиця 1
Теплофізичні властивості стальної труби й поліетиленового покриття
Теплофізична властивість | Розмірність | Стальна труба | Поліетиленове покриття |
Теплопровідність | Вт/(м К) | 47 | 0,345 |
Густина | кг/м3 | 7800 | 924 |
Теплоємність | Дж/(кг К) | 465 | 2164 |
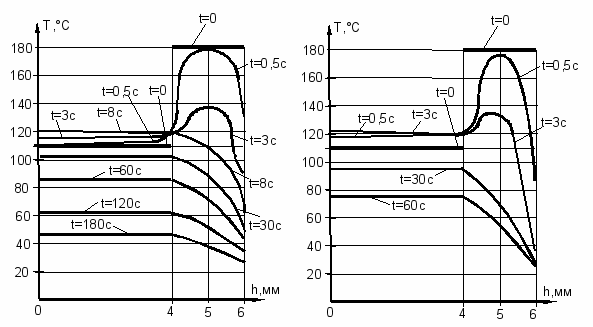
а) б)
^ Рис. 1. Розподіл температури по товщині труби з покриттям
при охолодженні на повітрі (а) та при омиванні водою (б) через певні проміжки часу
Як видно з рисунка 1, у перші моменти труба підігрівається, а поліетилен охолоджується в обидва боки, причому в бік сталі підвищення температури практично не залежить від інтенсивності зовнішнього охолодження і до 10 с температура труби піднімається на 7–8 °С. Після 10 с температура змінюється вже лише в один бік – назовні й інтенсивність охолодження залежить від інтенсивності теплообміну зовні. При охолодженні за допомогою омивання водою вже через 30 с зовнішній шар поліетилену має температуру, яка приблизно дорівнює температурі зовнішнього середовища, і більш інтенсивне охолодження нічого не змінить. Оскільки теплопровідність сталі на 2 порядки вища за теплопровідність поліетилену, температура в трубі встигає вирівнятися і майже не залежить від радіуса. Через 60 с після початку охолодження вона дорівнює 75 °С. Охолодження на повітрі займає більше часу: зовнішній шар поліетилену охолоджується до температури зовнішнього середовища (25 °С) за 180 с, але при цьому температура стальної труби складає 47 °С.
Для другого типорозміру труб з товщиною стінки 6 мм при товщині покриття 2,2 мм охолодження відбувається повільніше, хоча вид розподілу температур по товщині ідентичний наведеному на рисунку 1. Через 60 с після початку охолодження на повітрі температура стінки труби становить 95 °С, а зовнішнього шару ПВТ – 37 °С; при охолодженні водою ці температури – відповідно 87 °С і 27 °С.
Проведені дослідження та розрахунки дозволяють визначати необхідний час охолодження труби з покриттям за різних граничних умов теплового потоку (теплоізоляції), конвективного теплообміну, теплообміну тепловипромінюванням за законом Стефана–Больцмана в поєднанні з тепловим потоком і теплообміном.
УДК 621.914
^ О.А. Громовий, к.т.н., доц.
С.В. Савицький, магістр
С.В. Завертайло, магістр