Машинознавство, обробка матеріалів у машинобудуванні
Вид материала | Документы |
- Зміни до Порядку проведення експертизи матеріалів на лікарські засоби, що подаються, 2751.76kb.
- Можна констатувати, що тривала криза в українській промисловості, що особливо зачепила, 17.29kb.
- Відповідно до постанови Кабінету Міністрів України від 26., 3656.85kb.
- Робоча навчальна програма предмет Методи дослідження властивостей матеріалів (Р-32), 48.64kb.
- Робоча навчальна програма кредитного модуля з дисципліни "Цифрова обробка сигналів", 410.54kb.
- Обробка сировини. Виробництво напівфабрикатів обробка овочів І грибів значення овочів, 196.83kb.
- Вимоги до оформлення матеріалів тез доповідей, 134.94kb.
- Діагностика сектору будівельних матеріалів, 235.87kb.
- Робоча навчальна програма предмет Фізика матеріалів (П-54) Спеціальність, 33.89kb.
- Міністерство освіти І науки україни наказ, 54.87kb.
Житомирський державний технологічний університет
СУЧАСНІ ТЕХНОЛОГІЇЇАВТОМАТИЗАЦІЇЇПРОЕКТУВАННЯ ВИРОБІВ
НА ПІДПРИЄМСТВІ
Швидкий розвиток машинобудування, авіа- й автомобілебудування вимагає активного впровадження на підприємствах сучасних систем управління життєвим циклом виробу (Product Lifecycle Management (PLM)). PLM-системи поєднують в єдиний комплекс всі засоби створення, зберігання, обробки та обміну інформацією про вироби підприємства. Таким чином, PLM-системи інтегрують у собі засоби проектування (Computer Aided Design (CAD)), інженерного аналізу (Computer Aided Engineering (CAE)), виробництва (Computer Aided Manufacturing (CAM)), а також управління документообігом (Product Data Management (PDM)). PLM-технології забезпечують глобальне середовище управління цифровою інформацією про продукцію. Це дає можливість віртуально проектувати і візуалізувати вироби, а також моделювати відповідні виробничі процеси. Відмова від виготовлення дослідних зразків і проведення дорогих випробувань дозволяє заощаджувати значні кошти. Крім того, віртуальне виробництво дозволяє підвищити конкурентоспроможність і поліпшити ергономічні характеристики продукції.
Провідні світові компанії, серед яких Lockheed Martin, Bell/Agusta, Boeing, McDonnell Douglas, ОАО “Сухой”, ОАО “Мотор Сич”, ДП Запорізьке машинобудівне конструкторське бюро “Прогрес”, BMW, Porsche, Daimler AG та інші, використовують на підприємствах PLM-системи від компаній Siemens PLM Software, Dassault Systèmes, Parametric Technology Corporation (PTC).
NX – PLM-система від компанії Siemens PLM Software. Засоби промислового дизайну в NX призначені для: моделювання поверхонь складної просторової форми, візуалізації, автомобільного дизайну, вирішення завдань зворотного інжинірингу, інтеграції з CAD, засобами інженерного аналізу CAE і технологічними CAM. До складу конструкторських програм NX входять інструменти для проектування деталей, роботи зі зборками, створення конструктивних елементів, креслень. Пакет засобів інженерного аналізу NX Digital Lifecycle Simulation – основа системи аналізу в NX. NX Nastran – інструмент для проведення комп'ютерного інженерного аналізу (CAE) проектованих виробів. NX CAM – інтегроване рішення для верстатів з ЧПУ. NX широко використовується в машинобудуванні, особливо в галузях, у яких випускаються вироби з високою щільністю компонування і великою кількістю деталей та виготовляють вироби зі складними формами (авіаційна, автомобільна тощо).
CATIA – PLM-система французької фірми Dassault Systemes. PLM-система CATIA містить модулі CATIA для автоматизації проектування, ENOVIA – для управління інженерними даними та колективної роботи, SIMULIA – для інженерного аналізу і DELMIA – для цифрового виробництва. Dassault Systеmes пропонує розвиток PLM-технологій з використанням глобальної комп'ютерної мережі Internet, який дає можливість тривимірного моделювання 3D і колективної роботи в реальному часі. Користувачам Internet пропонується оперувати одночасно віртуальними і реальними об'єктами.
Creo Elements/Pro – PLM-система від компанії Parametric Technology Corporation. Попередня назва системи – Pro/Engineer. Це найповніший у своїй галузі пакет для розробки виробів, призначений для оптимізації процесів проектування. Система містить передові інструменти 3D конструювання, систему MathCad для виконання інженерного аналізу і його документації, пакет Mechanica для вирішення основних завдань моделювання й оптимізації, Windchill – для управління даними, Product View Standard – модуль розширеного моделювання і візуалізації та ін.
А
© О.А. Громовий, С.В. Савицький, С.В. Завертайло, 2011
наліз наведених вище систем показує, що вони не лише вирішують завдання інформаційної підтримки життєвого циклу виробів, а й створюють концепцію організації єдиного інформаційного простору розробки виробів, що об'єднує розробників, виробництво, замовників та ін. З використанням Internet-технологій це дозволяє організувати реальну взаємодію різних підрозділів і компаній, незалежно від їх територіального розташування і глибини участі в рамках єдиного проекту.
УДК 681.5:620.1
О.А. Гутніченко, к.т.н., доц.
Житомирський державний технологічний університет
^ ВПЛИВ ПАРАМЕТРІВ УЛЬТРАЗВУКОВОЇ ОБРОБКИ НА ХАРАКТЕРИСТИКИ
ОТРИМАНИХ НАНОПЛАСТИНОК ГРАФІТУ
Нанокомпозити на основі полімерів з неорганічними наповнювачами, надзвичайно популярні в останнє десятиріччя, показали можливість значного покращання властивостей полімерних матеріалів, а в деяких випадках продемонстрували принципово нові властивості. Досягнення вказаного стало можливим завдяки тому, що, по-перше, на відміну від традиційних композитів, розміри наповнювача мають масштаб одного порядку з розмірами структурних складових матеріалу матриці (діапазон нанометрів) і, по-друге, частинки наповнювача внаслідок високої поверхневої енергії беруть активну участь у формуванні структури композиційних матеріалів. Прикладом таких матеріалів можуть бути системи «полімер–силікат», у яких значно покращуються механічні та теплопровідні характеристики при введенні в полімерну матрицю або інтеркальованих, або деламінованих силікатів, які мають шарувату структуру. Однак електричні властивості нанокомпозитів на основі силікатів значно поступаються графітовмісним композитам.
Подібно до шаруватих силікатів, частинки графіту також є представниками шаруватих матеріалів. Гратка кристала графіту складається із шарів графену, що сформовані за допомогою sp2-гібридизації атомів вуглецю, які пов’язані між собою дуже слабкими ван-дер-ваальсовими силами. Також відомо, що графіт – добрий провідник, питома провідність якого може сягати 104 (Ом м)-1 при кімнатній температурі, й, таким чином, він є чудовим кандидатом для виробництва полімерних електропровідних нанокомпозитів. Однак, на відміну від шаруватих силікатів, розшарування яких можна виконати за допомогою обмінних реакцій, розшарування графіту вказаним способом неможливе, що приводить до необхідності використання таких методів, як ультразвукова обробка сполук інтеркалювання графіту (СІГ) або терморозширеного графіту (ТРГ). Звідси випливає необхідність детального вивчення технології отримання графітових нанопластинок за допомогою використання ультразвукового випромінювання та дослідження структурних характеристик і властивостей отриманого матеріалу, а також його вплив на формування структури та властивостей полімерних електропровідних нанокомпозитів.
Як вихідну сировину використовували природний графіт Завалівського родовища з розмірами 50–75 мкм (залишок на ситі 05). Окислення графіту проводилося двома способами: за допомогою суміші сірчана кислота–дихромат калію та суміші азотної та сірчаної кислот (1:4). Після завершення процесу окислення СІГ промивався дистильованою водою до рН 6–7, частина якого використовувалася для ультразвукової обробки, інша частина – для виготовлення ТРГ: піддавалася термоудару при температурі 1000 С протягом 15 с.
Ультразвукова обробка матеріалів (СІГ та ТРГ) проводилася за допомогою ультразвукового диспергатора УЗД-500 з потужностями випромінювання 100, 250 та 320 Вт. Тривалість УЗ обробки складала 4, 8 та 16 год.
Вивчення властивостей отриманих матеріалів проводилося за допомогою седиментографа Shimadzu SA-CP3 (centrifugal particle size analyzer), растрової електронної мікроскопії та атомної силової мікроскопії.
Результати седиментації частинок показали нелінійну залежність зміни розмірів частинок графіту від тривалості та потужності ультразвукової обробки. Взагалі, при збільшенні тривалості обробки спостерігається більш поступове зміщення максимуму гранулометричного складу в область менших ефективних діаметрів, ніж при підвищенні потужності, де спостерігається швидке подрібнення часток графіту, особливо в діапазоні 25–315 Вт. Більший вплив має спосіб окислення, і це зрозуміло, тому що при обробці сумішшю сірчаної кислоти та дихромату калію відбувається процес інтеркалювання, внаслідок чого значно зростає відстань між шарами графіту.
Електронна мікроскопія показала достатню якість проходження процесу розшарування СІГ. Діаметр отриманих пластинок складає 1–5 мкм, товщина коливається у межах 10–70 мкм.
© О.А. Гутніченко, 2011
УДК 621.914:621.7.06
С.В. Завертайло, магістрант
Науковий керівник – к.т.н., проф. Лоєв В.Ю.
Житомирський державний технологічний університет
^ ОПТИМІЗАЦІЯ КОНСТРУКТИВНИХ ПАРАМЕТРІВ ВИСОКООБЕРТОВИХ ШПИНДЕЛЬНИХ ВУЗЛІВ ВЕРТИКАЛЬНО-ФРЕЗЕРНИХ ВЕРСТАТІВ
Потреба у високообертальних шпиндельних вузлах виникла поступово, в процесі підвищення продуктивності, що є одним з головних завдань виробництва. Шпиндельні вузли (ШВ) знайшли своє практичне застосування у верстатобудуванні, оскільки мали перевагу – підвищення продуктивності. Підвищення продуктивності обробки здійснюється за рахунок скорочення основного часу. Високообертові ШВ в сучасному машинобудуванні мають більше 25 тис. об./хв. Найбільш поширені – ШВ з частотою обертання 30–35 тис. об./хв. Такі ШВ використовують для обробки як “звичайних” деталей, так і прес-форм, штампів і маленьких точних деталей. Навіть проголошена конструкція високообертового ШВ з частотою обертання 500 тис. об./хв.
Класифікація шпиндельних вузлів:
1) залежно від просторового розміщення шпинделя на верстаті:
- вертикальні;
- горизонтальні;
2) за характером виконуваних робіт – на групи:
- свердлильна;
- розточувальна;
- фрезерна;
- токарна;
- інша;
3) за умовами роботи:
- шпинделі, на які діють крутні та згинні навантаження (токарні, фрезерні, шліфувальні та інші);
- шпинделі, на які діють переважно крутні навантаження (свердлильні, різьбонарізні);
4) за відношенням між потужністю і максимальною частотою обертання:
- силовий шпиндель: до 15 тис. об./хв. і потужність 50 кВт і більше, максимальний крутний момент 50 нм і більше;
- середній шпиндель: 15–50 тис. об./хв., потужність 4–50 кВт (пікова потужність до 107 кВт), крутний момент 0,4–50 нм;
- швидкісний шпиндель: 50–140 тис. об./хв., потужність до 4 кВт, момент до 0,4 нм;
5) за найбільшою частотою обертання:
- 8 000 об./хв., стандартний шпиндель загального застосування;
- 15 000 об./хв., широкодіапазонний шпиндель для обробки алюмінієвих і легких сплавів;
- 25–35 тис. об./хв., високообертовий шпиндель для обробки прес-форм, штампів і маленьких точних деталей.
ШВ призначений для здійснення точного обертання інструмента або деталі. Він входить у несучу систему верстата і значною мірою впливає на жорсткість і вібростійкість. ШВ верстата складається зі шпинделя, його опор, привідного механізму. До основних характеристик ШВ, від яких безпосередньо залежить його якість і технологічні можливості, відносять: точність, швидкохідність, надійність. Крім того, є додаткові характеристики працездатності ШВ: жорсткість, динамічні й теплові характеристики. До шпиндельних вузлів верстатів висувають такі вимоги:
1) Навантажувальна здатність – визначає допустимий крутний момент або потужність на шпинделі, який залежить від: навантажувальної здатності опор і силових можливостей приводу. Зручним показником для оцінки навантажувальної здатності ШВ є відношення N/D, де N – потужність приводу; D – діаметр передньої шийки шпинделя.
2
© С.В. Завертайло, 2011
) Точність – в першу чергу, визначає технологічні можливості ШВ, залежить від типу опор. Точність обертання вимірюють на передньому кінці шпинделя в радіальному й осьовому напрямках. Найбільш повно і достовірно оцінюють за параметрами траєкторії руху опорних точок шпинделя, які розміщені на передньому кінці шпинделя (на установлювальних базах шпинделя, які визначають положення пристрою з заготовкою або інструментом).
3) Швидкохідність – визначає технологічні можливості ВСО і продуктивність. За показник швидкохідності ШВ прийнято добуток діаметра D передньої шийки шпинделя на найбільшу частоту обертання n.
4) Надійність. Для ШВ потрібно забезпечення високої параметричної надійності, тобто збереження початкової точності протягом певного часу. Головна причина зниження параметричної надійності – теплові процеси, швидкість яких залежить від часу роботи верстата. Надійність можна розглядати з двох позицій: як надійність машини, коли оцінюються всі види відмов, і як надійність технологічної системи, коли беруться до уваги лише ті відмови, які пов’язані з випуском неякісної продукції.
5) Жорсткість. Статична жорсткість ШВ
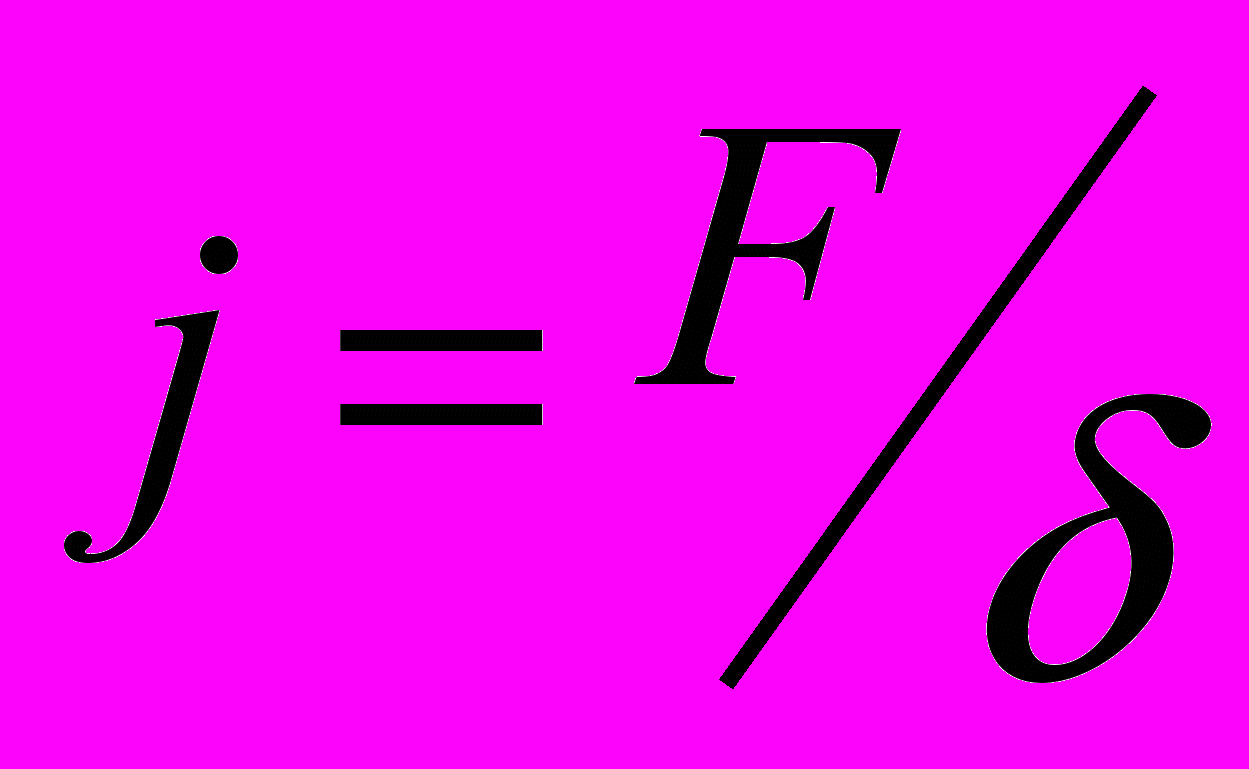
6) Динамічні характеристики. ШВ повинен мати високу вібростійкість для забезпечення якості, продуктивності обробки і стійкості інструменту. Динамічні характеристики для оцінки якості ШВ містять: частоти власних коливань, АЧХ (амплітудно-частотну характеристику), ФЧХ (фазочастотну характеристику), АФЧХ (амплітудно-фазову частотну характеристику), динамічну жорсткість, форми коливань на власних частотах, коефіцієнт демпфування.
7) Швидке і надійне закріплення інструментів, пристроїв або заготовки, забезпечення точного центрування і точного обертання.
8) Обмеження тепловиділення і температурних деформацій шпиндельного вузла. ШВ повинен мати мінімальне тепловиділення, оскільки теплові деформації прямо впливають на точність, викликаючи теплові зміщення.
На даний час існує велика кількість варіантів конструкцій високообертових ШВ. Усі вони відрізняються за багатьма параметрами: за кількістю підшипників, типом змащування, розташуванням, сприйняттям різних видів навантажень, вартістю виготовлення і обслуговування, необхідними режимами роботи і т. д. ШВ різняться за своїми технічними характеристиками. Сучасні ШВ мають електронні системи активного контролю за параметрами роботи, складну будову і значну кількість допоміжних обслуговуючих систем.
В даній роботі оптимізується конструкція високообертового ШВ з метою розроблення нової конструкції ШВ, яка відповідає певним характеристикам. Оптимізація – це знаходження найкращого (із множини можливих) варіанта вирішення завдання при заданих вимогах і обмеженнях. Розробляється конструкція ШВ для вертикально-фрезерного верстата, який має: максимальну частоту обертання 30–35 тис. об./хв., систему закріплення інструментів
HSK–A50, електронні системи активного контролю, систему центральної затискної тяги і змінний гідравлічний натяг підшипників. Максимальну частоту обертання забезпечують кулькові гібридні радіально-упорні підшипники прецизійної точності, які змащуються масляно-повітряною сумішшю імпульсним методом. Система закріплення інструментів здійснюється за допомогою центральної затискної тяги, яка створює зусилля за допомогою пакета тарільчастих пружин до 13 кН (залежно від типорозміру ШВ). Електронні системи активного контролю слідкують за: зміною температури підшипників передньої групи, осьовим рухом шпиндельного вала, параметрами віброактивності всієї конструкції ШВ, вимірюванням частоти обертання шпиндельного вузла, системою зміни і закріплення інструментів. Система змінного гідравлічного натягу підшипників дозволяє керувати значенням жорсткості підшипників залежно від частоти обертання і режиму обробки деталей. Значення жорсткості може змінюватися в 3 рази. Також ця система компенсує теплові деформації.
УДК 621.793.71
М.П. Кравченко, аспір.
Л.Г. Полонський, д.т.н., проф.
Житомирський державний технологічний університет
^ ЗМІНА ЯКОСТІ ОБРОБЛЕНИХ ПОВЕРХОНЬ
газотермічних покриттів ПРИ ПОШАРОВОМУ ТОЧІННІ
Процес газотермічного напилення покриття – це поетапне нашарування часток порошку, що нагріваються до відповідної температури і розганяються струменем газу, прохід за проходом. При нанесенні покриття теплота, що виділяється при горінні, розплавляє або пластифікує частки напилюваного матеріалу. Крім того, вона дає можливість підігрівати поверхню основи в зоні напилення. Отже, при напиленні ГТП частина теплоти, що утворюється при спалюванні горючого газу, передається і на деталь. Полум’я викликає послідовне рівномірне підвищення температури поверхні за рахунок теплообмінних процесів. Нагрівання напилюваним матеріалом відбувається внаслідок контакту великої кількості часток, що ударяються, розтікаються, твердіють і віддають своє тепло деталі й одна одній.
Існують математичні методи підрахунку температури будь-якої точки деталі з покриттям. Також встановлено, що для міцного зчеплення часток цієї температури не завжди достатньо. Хоча навколо часток відбувається інтенсивне нагрівання і градієнти температури сягають 105 град./см, розрахунки показують, що глибина зони термічної дії під часткою в кінці стадії твердіння не перевищує всього декількох десятків мікрон. Тому процеси фізико-хімічної взаємодії при напиленні не зачіпають об’єму матеріалу деталі, а проходять, в основному, в шарі покриття, який має низку аномальних властивостей. Вивчення кінетики з’єднання між собою розплавлених і пластифікованих часток напилюваного матеріалу використовується для дослідження властивостей цього шару.
При ударі об поверхню напилюваної деталі сферичні частки порошку деформуються, твердіють і набувають форми тонкого диска. Висока швидкість деформації та розплавлення часток призводить до контакту матеріалів між собою і з деталлю на межі взаємодії. Але оскільки процес напилення від початку до кінця є непостійним (змінюється температура, товщина напиленого покриття і т. ін.), то, відповідно, буде непостійною структура ГТП.
Відомо, що газотермічні покриття за своєю природою є гетерогенними. За об’ємом і товщиною вони мають різні властивості. На рисунку 1 наведено мікроструктуру газополуменевого напиленого покриття, з якого чітко видно розподіл його на зони.
С
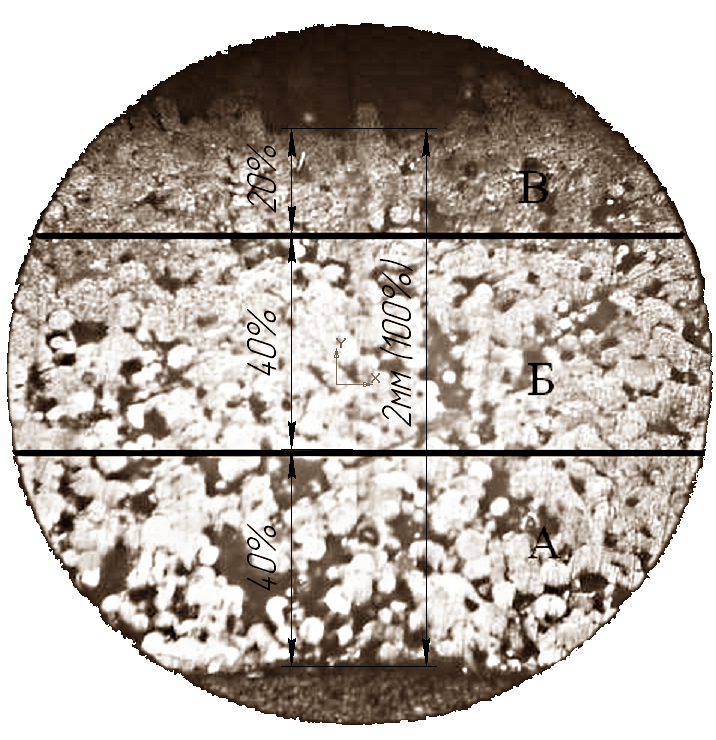
П
^ Рис. 1. Мікроструктура газополуменевого напиленого покриття з самофлюсівного порошку ПГ-12Н-01 товщиною 2 мм (х63)
оділ шару покриття на три зони широко відомий у техніці газотермічного напилення, але це явище практично не використовується при проектуванні технологічних процесів формування та механічної обробки деталей з покриттями.
Ц
© М.П. Кравченко, Л.Г. Полонський, 2011
е необхідно враховувати при їх кінцевій обробці, тому що в разі призначення різних припусків ми отримаємо на оброблені поверхні, що експлуатуватимуться, різну шорсткість і, очевидно, твердість, зносостійкість тощо.
У зв’язку з таким станом речей призначення оптимального припуску постає як проблемне при обробці (особливо кінцевій) покриттів різанням. Для вірного призначення припуску на обробку необхідно знати структуру покриття на різних глибинах, якісні та кількісні залежності фізико-механічних властивостей поверхонь, оброблених зняттям прошарків покриття різної сумарної товщини (зняттям різного припуску).
При призначенні припуску на обробку покриттів та визначенні їх робочої товщини рекомендується застосовувати відповідні аналітичні залежності, наявні в технічній літературі. Але користуватися ними у більшості випадків неможливо через відсутність кількісних значень вихідних даних (глибини дефектного шару покриття, висоти мікронерівностей, просторових відхилень відносно базових поверхонь заготовки, похибки установки на операції механічної обробки). Проте навіть після розрахунку припуску існує велика ймовірність зняття тієї частини покриття, що має найприйнятніші експлуатаційні показники, у вигляді припуску, попадання робочої (обробленої) поверхні в зону з погіршеними змінними значеннями показників якості або того, що в товщу прошарку покриття на знос попадуть прошарки з цієї області.
Очевидно, при виборі припуску на обробку покриттів необхідно застосовувати інші підходи. Бажано призначати його таким, щоб робоча поверхня після обробки знаходилася в межах якісного (за певними критеріями) прошарку.
З метою виправлення такого становища нами проведено низку досліджень з призначення припусків на обробку ГТП системи Ni–Cr–B–S за критеріями шорсткості, мікротвердості, сили різання. А оскільки провідне значення в призначенні припусків на обробку покриттів має той факт, що вони гетерогенні, – виконано низку експериментів з метою визначення місця розташування прошарків з підвищеними експлуатаційними характеристиками.
За об’єкт дослідження в експериментах обрано циліндричний зразок Ø 36 мм із шаром покриття ПГ-12Н-01 товщиною 2 мм, обробка якого проводилася по черзі на різних глибинах шляхом зняття припусків певної величини.
За даними вимірювання шорсткості видно, що по всій товщині покриття прослідковується прошарок, в якому Ra має найменші значення. Він знаходиться на глибинах від 0,4 до 0,6 мм, займаючи при цьому проміжок у межах 20–30 % (в середньому – 25 %) від товщини покриття.
Найкращі показники Hµ по всій товщині покриття має прошарок, який знаходиться в межах 0,3–0,5 мм від поверхні.
При вимірюванні сили різання встановлено, що найбільші її значення спостерігаються при знятті прошарків покриття в діапазоні 0,5–0,6 мм від поверхні.
З результатів першого, другого і третього експериментів стає очевидним, що вони корелюються між собою. Глибини розташування прошарків з підвищеними механічними властивостями за трьома параметрами близькі між собою (для Ra – це 0,4–0,6 мм; для Hµ –0,3–0,5 мм; для Р – 0,5–0,6 мм).
На підставі викладеного вище матеріалу можна зробити висновок, що газотермічні покриття мають по своїй товщині прошарки, в яких показники якості Ra, Hµ і міцності та щільності за значеннями сили різання Р є найліпшими на відстані 0,3–0,6 мм (15–30 %) від поверхні. Прошарок, що має нижчі механічні показники і дефектні включення, становить ~ 15–20 % загальної товщини покриття від поверхні. При знятті цього прошарку як припуску на обробку експлуатаційні показники поверхні будуть найбільш прийнятними для подальшої роботи виробу. Структура газотермічних покриттів із самофлюсівних порошків системи Ni–Cr–B–Si є змінною за товщиною, чим пояснюється і зміна властивостей, відмічених у роботі прошарків. А зміна властивостей останніх пов’язана зі зміною градієнта температури протягом процесу напилення та специфікою поверхонь основи і покриття. Результати, отримані на основі проведених експериментів, які використані у даній роботі, дають змогу визначити розташування найприйнятніших прошарків покриття і, відповідно, призначити оптимальний припуск на механічну обробку, з точки зору довготермінової експлуатації робочої поверхні.
Виходячи з цього, можна також досліджувати показники якості ГТП за глибиною і за іншими параметрами якості. Знання глибин розташування шарів з найприйнятнішими показниками цих параметрів дають можливість рекомендувати оптимальні величини товщин напилюваного покриття і припуску для конкретних випадків обробки.
УДК 621.914
^ В.Б. Крижанівський, к.ф.-м.н., доц.
Житомирський державний технологічний університет