Машинознавство, обробка матеріалів у машинобудуванні
Вид материала | Документы |
- Зміни до Порядку проведення експертизи матеріалів на лікарські засоби, що подаються, 2751.76kb.
- Можна констатувати, що тривала криза в українській промисловості, що особливо зачепила, 17.29kb.
- Відповідно до постанови Кабінету Міністрів України від 26., 3656.85kb.
- Робоча навчальна програма предмет Методи дослідження властивостей матеріалів (Р-32), 48.64kb.
- Робоча навчальна програма кредитного модуля з дисципліни "Цифрова обробка сигналів", 410.54kb.
- Обробка сировини. Виробництво напівфабрикатів обробка овочів І грибів значення овочів, 196.83kb.
- Вимоги до оформлення матеріалів тез доповідей, 134.94kb.
- Діагностика сектору будівельних матеріалів, 235.87kb.
- Робоча навчальна програма предмет Фізика матеріалів (П-54) Спеціальність, 33.89kb.
- Міністерство освіти І науки україни наказ, 54.87kb.
^ ГЕОМЕТРИЧНИЙ ПІДХІД ДО МІНІМІЗАЦІЇ ЗАДИРОК
ПРИ ТОРЦЕВОМУ ФРЕЗЕРУВАННІ
Виклики сучасності, які стосуються якості виробів, невпинно зростають. Важливою складовою цієї якості є стан крайок обробленої деталі. Створені в системах автоматизованого проектування моделі майбутніх деталей мають абсолютно рівні в геометричному сенсі крайки. Але задирки, які з’явилися на завершальних стадіях обробки, значно спотворюють ідеальну геометрію моделі. В більшості випадків доводиться використовувати вартісну і тривалу процедуру позбавлення від задирок для забезпечення бажаної якості або функціональності деталей.
Сучасні дослідження демонструють важливість впливу формування задирок на процес обробки взагалі. Задирки не тільки приводять до необхідності економічно вартісної процедури видалення, але й у більшості випадків впливають на зношування різального інструменту. Навіть якщо задирки безпосередньо не впливають на функціональність деталі та їх видалення не передбачається, залишається, в усякому разі, дві проблеми. По-перше, задирки, як правило, дуже гострі й можуть травмувати складальників на етапі збирання готового виробу. По-друге, задирки, які спочатку досить міцно тримаються, можуть згодом відокремлюватися від деталі та ставати причиною порушення функціонування агрегату в цілому.
Дані з машинобудівних заводів Німеччини свідчать, що витрати, пов’язані з задирками, підвищують вартість готових виробів на 9 %.
Інша значна проблема стосовно задирок – це відсутність загальновизнаної стандартизації в описі та вимірюванні задирок. Хоча в контрактах на постачання машинобудівної продукції широко використовується термін «free of burrs» (без задирок).
Чистове фрезерування – одна з важливих фінішних операцій, які проходять деталі на останній стадії обробки. Формування задирок на цій стадії надзвичайно небажане. Експериментальні дослідження показують, що розмір задирок залежить від великої кількості параметрів, таких, як товщина шару, що зрізується, швидкість різання, подача, кут виходу леза інструмента з заготовки та властивостей матеріалу.
Відомо також, що виникають так звані первинні та вторинні задирки, які, в свою чергу, також залежать від умов різання, геометрії ножів, геометрії деталі та властивостей матеріалу. На практиці слід уникати саме первинної задирки.
Як правило, на фінішних стадіях обробки товщина шару, який зрізується, фіксована. З точки зору зменшення первинної задирки, існує деяке порогове значення кута виходу, яке забезпечує лише незначну вторинну задирку і як результат – прийнятну якість деталі.
Отже, природно, виникає завдання мінімізувати сумарну довжину крайок деталі, на яких кут виходу менший деякого порогового значення
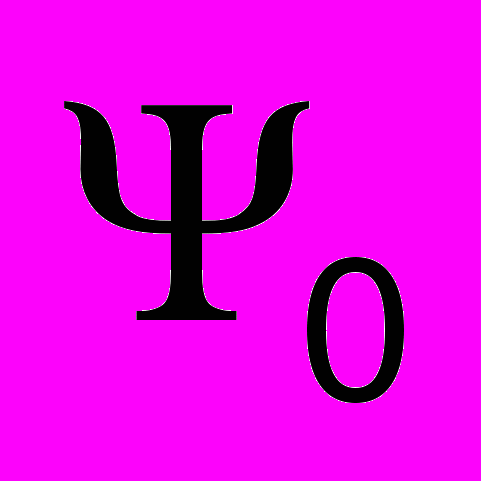
Опис траєкторії руху ножа здійснюється по трохоїді (рис. 1).
Параметричне представлення трохоїди має такий вигляд:
-
;
.
(1)
Поверхня моделюється так. Проекція плоскої поверхні, яка обробляється торцевим фрезеруванням, на паралельну їй площину в загальному випадку має вигляд неопуклої множини точок. Межа цієї множини з будь-якою наперед заданою точністю може бути апроксимована ламаною, яка обмежує деякий неопуклий багатокутник
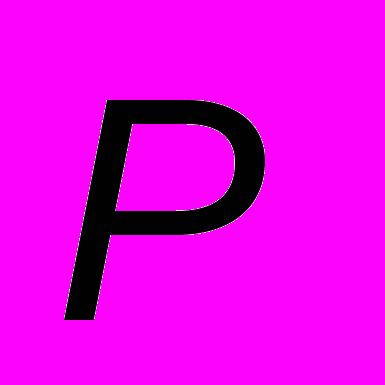
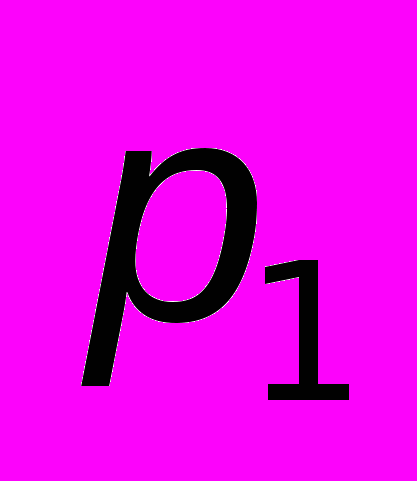
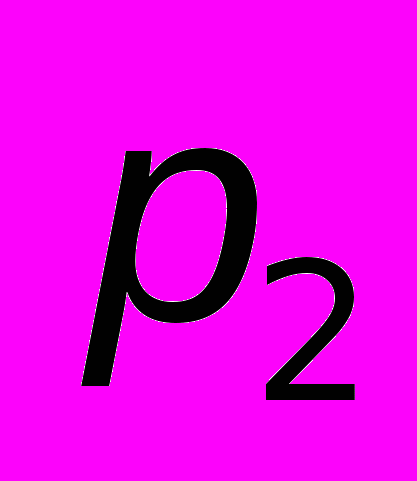
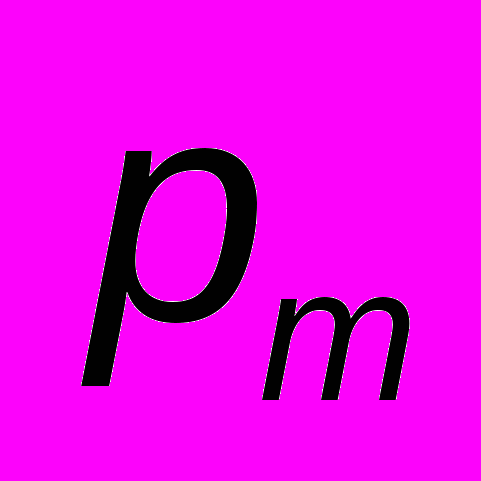
Координати точок
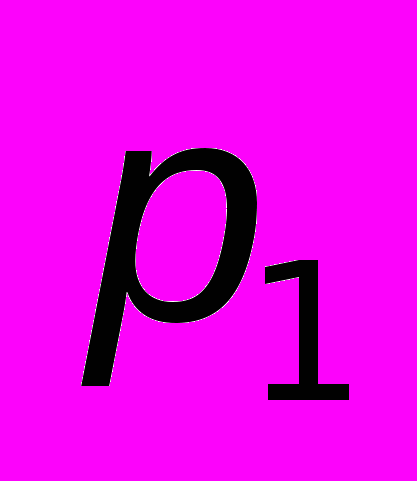
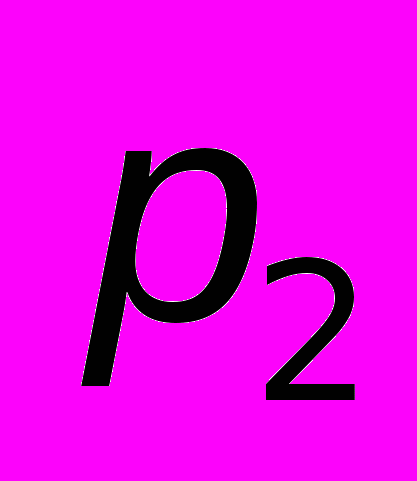
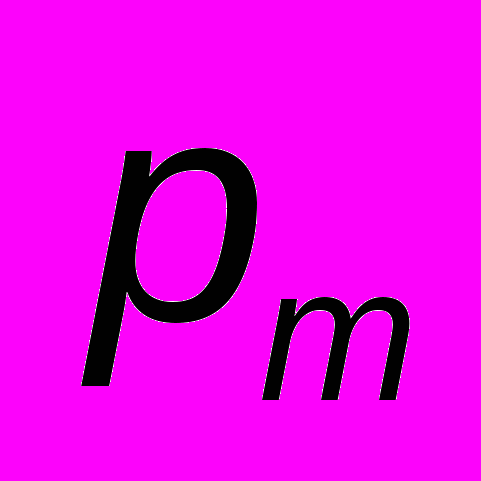
© В.Б. Крижанівський, 2011
-
.
(2)
Введемо нерухому систему координат
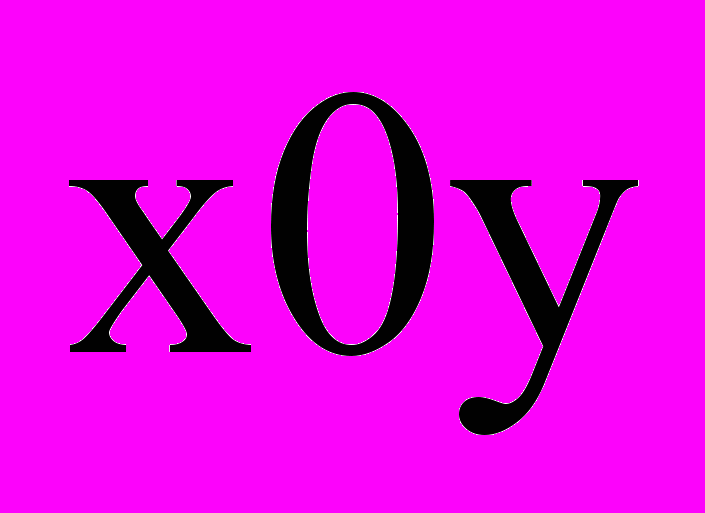
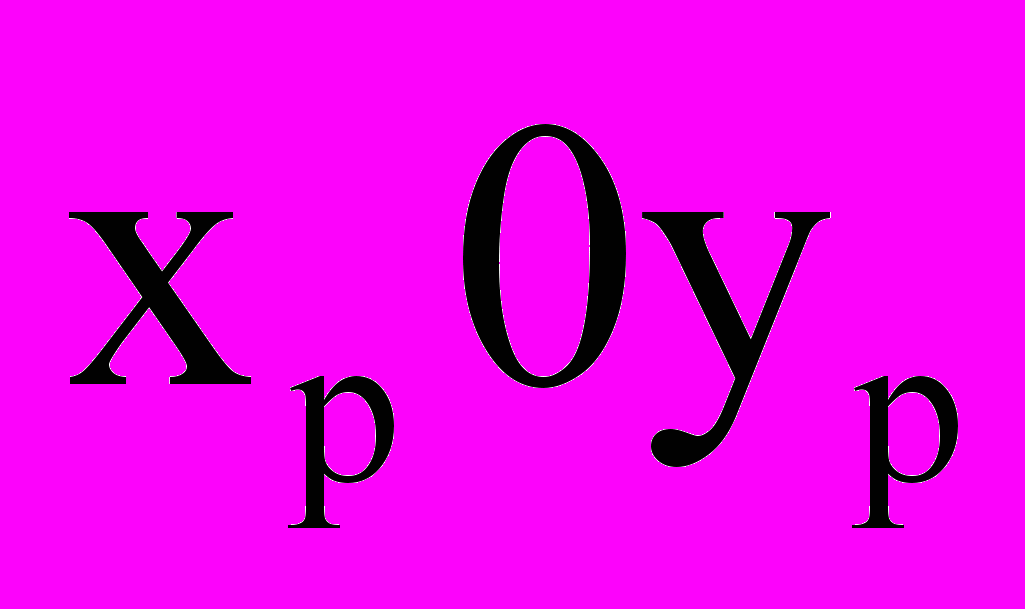
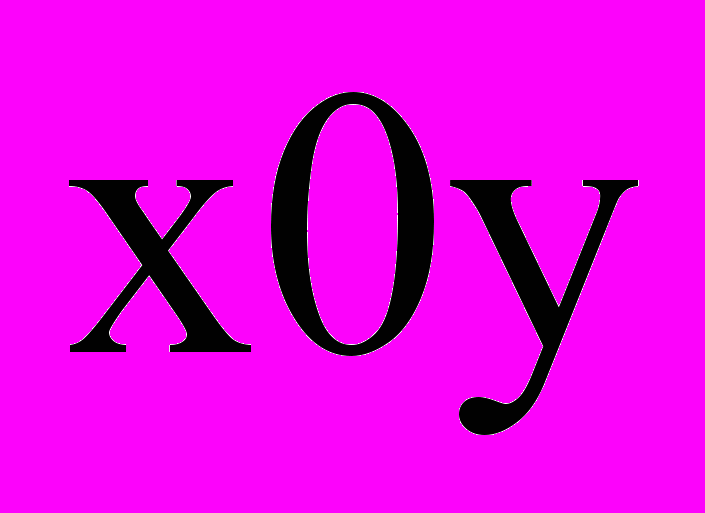
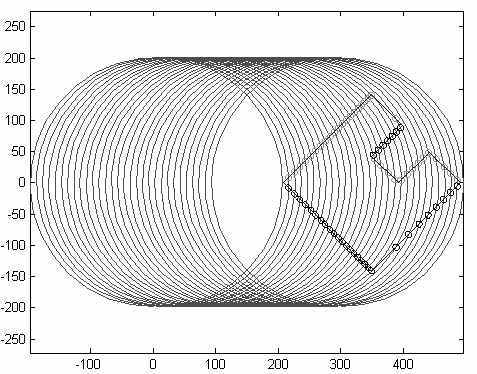
^ Рис. 1. Траєкторія ножа фрези та його точки входу
й виходу на межах деталі
Ці положення визначаються як композиція двох перетворень: трансляції та повороту. При переході до однорідних координат трансляція і поворот в обчислювальному сенсі реалізуються за рахунок матричного множення. Матриці трансляції та повороту в однорідних координатах:
-
;
(3)
(4)
де
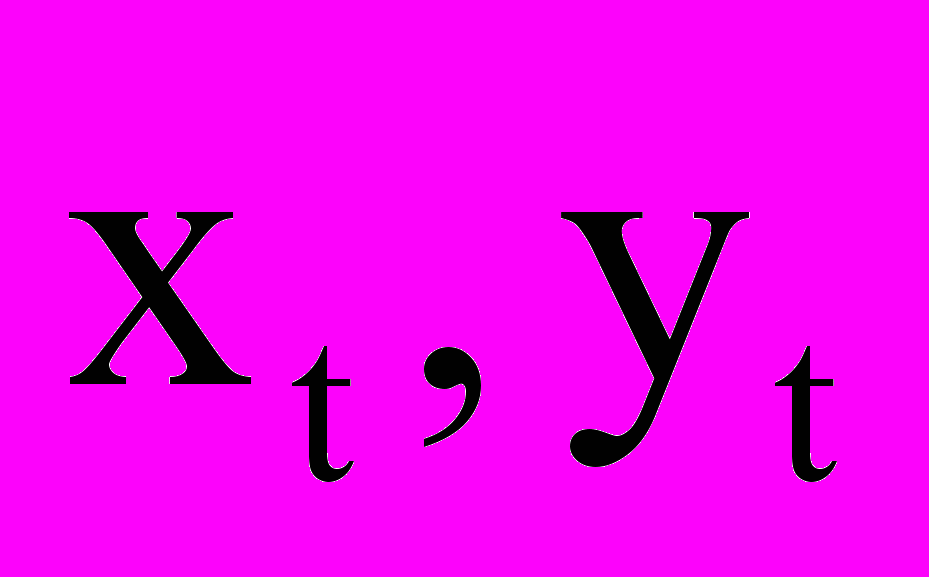
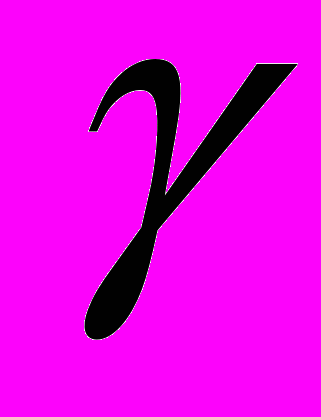
За рахунок цього відносного положення трохоїди та деталі й здійснюється мінімізація сумарної довжини ділянок ребер, на яких утворюється первинна задирка.
Першим кроком алгоритму мінімізації задирок є визначення ділянок ребер, через які ніж фрези входить у деталь і виходить з неї. Для цього слід обчислити точки перетину трохоїди та сторін багатокутника
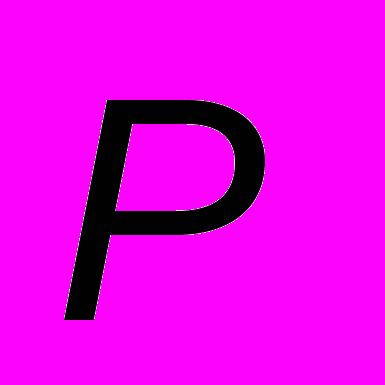
Потім у кожній точці виходу визначається величина кута виходу ножа фрези. В результаті отримуємо ділянки ребер, на яких значення кута виходу перевищує задане порогове значення. У програмному додатку сумарна довжина цих ділянок розглядається як функція від вектора трансляції
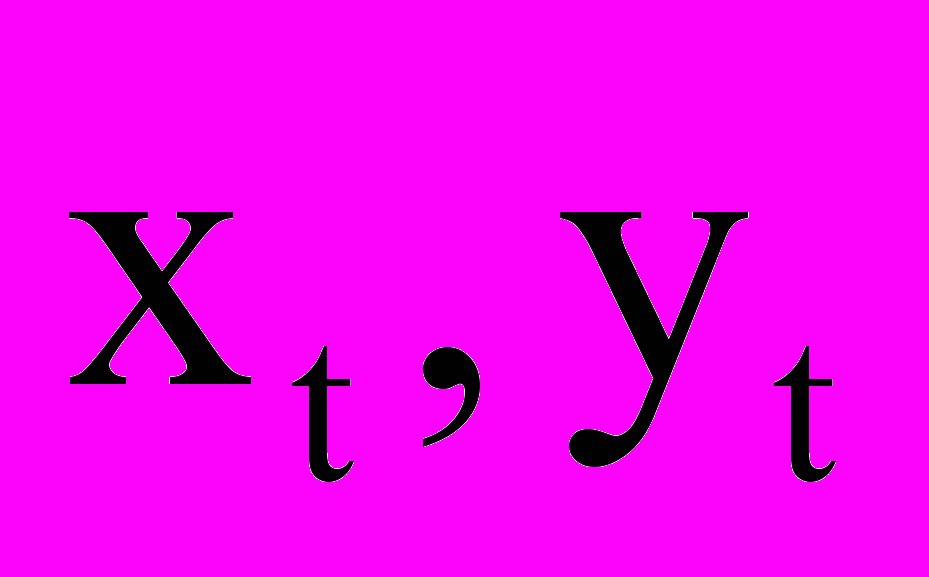
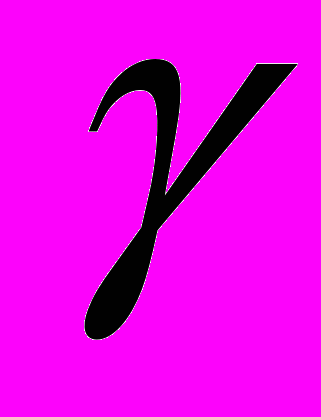
У розробленому в даній роботі програмному додатку розв’язується оптимізаційна задача обчислення параметрів розміщення багатокутника
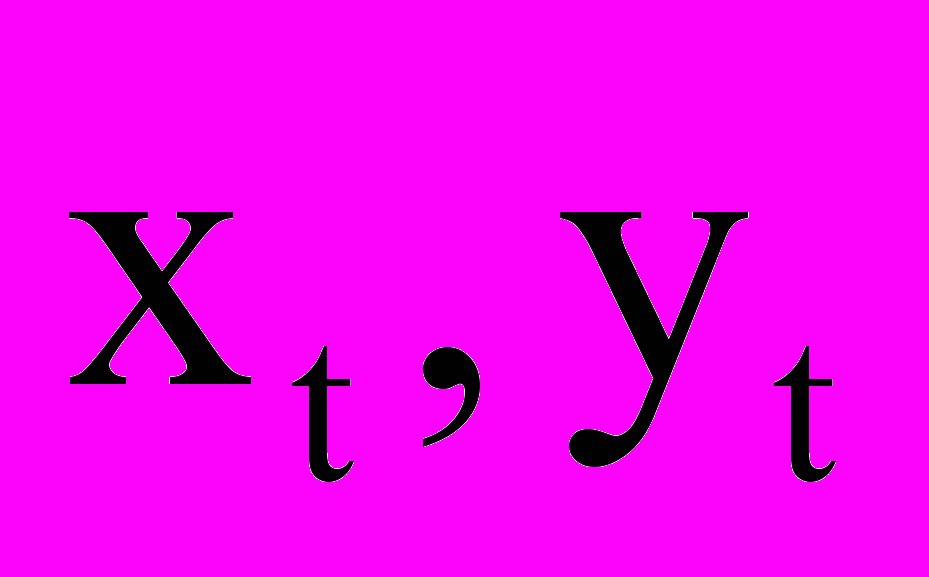
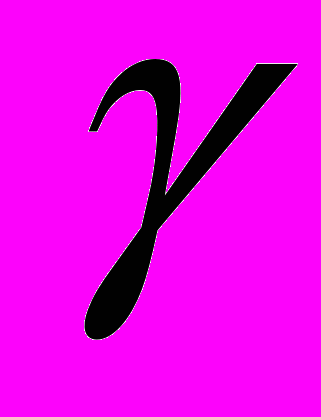
УДК 621.914; 621.9.015
В.Ю. Лоєв, к.т.н., проф.
О.В. Головатенко, асист.
Є.В. Салогуб, асист.
Житомирський державний технологічний університет
^ НОВІ СПОСОБИ ФІНІШНОЇ ОБРОБКИ ПЛОСКИХ ПОВЕРХОНЬ ДЕТАЛЕЙ ТОРЦЕВИМ ЛЕЗОВИМ ІНСТРУМЕНТОМ З КІНЕМАТИЧНО ПЕРЕТВОРЕНИМ РУХОМ ФОРМОУТВОРЮЮЧИХ ЕЛЕМЕНТІВ
Традиційні методи механічної обробки деталей машин і механізмів з видаленням припуску досягли певної межі розвитку в забезпеченні якісних показників і продуктивності праці.
Враховуючи високу питому вагу механічної обробки у виготовленні продукції машинобудівної галузі, одним з подальших напрямків суттєвого підвищення продуктивності обробки і скорочення енерговитрат є широке впровадження комбінованих і комплексних способів механічної обробки деталей. За прогнозами вчених, уже в найближчі роки доля технологічних процесів із застосуванням комбінованих способів обробки зросте до 15–40 % зі зниженням енерговитрат у 1,5–2 рази.
На кафедрі технології машинобудування і конструювання технічних систем ЖДТУ були розроблені нові способи фінішної обробки деталей, які дозволяють отримати суттєве підвищення якості обробленої поверхні, стійкості різального інструмента та високу продуктивність процесу обробки.
Нами розроблена конструкція інструмента для обробки плоских поверхонь на основі торцевої фрези з обертовими різальними елементами.
Інструмент налічує корпус, в якому змонтовано 6 шпинделів. Кожен шпиндель через шестерні з’єднаний з нерухомим зубчастим колесом, яке жорстко закріплене на пінолі шпиндельної бабки верстата. В кожному шпинделі закріплена чотиризуба пальцева фреза, оснащена пластинами з НТМ або твердого сплаву. При обертанні корпусу інструмента жорстко закріпленого на шпинделі верстата обертання передається на кожен зі шпинделів.
Розроблений інструмент дозволяє розміщувати в собі різноманітні різальні інструменти, такі, як кінцеві, торцеві або спеціальні фрези. Рух будь-якої різальної крайки кожної фрези як матеріальної точки є кривою, утвореною в результаті трьох рухів: обертального руху фрези відносно власної осі й, разом з корпусом інструмента, поступального (подача) та обертального (головний рух) рухів корпусу. Отримане перетворення траєкторії руху формоутворюючих елементів дозволяє забезпечити рівномірність процесу фрезерування незалежно від форми переривчастої поверхні за рахунок скорочення довжини та товщини шару матеріалу, що зрізується.
Нами була розроблена конструкція інструмента з кінематичним перетворенням колового руху чорнових і чистових формоутворюючих елементів на прямолінійний, перпендикулярний до вектора подач.
На шпинделі верстата зцентрований і закріплений гвинтами корпус, в якому з мінімально можливим зазором рухаються 8 повзунів, в кожному з яких закріплені клиновими затискачами з можливістю регулювання вильоту диференційними гвинтами формоутворюючі елементи, один з яких є чистовим (зачисним).
Повзуни попарно між собою підпружинені пружинами через плунжери й восьмигранний елемент. У кожному повзуні закріплені стійки з роликами (підшипниками), які базуються на ексцентричних шийках стійок. Зміна положення стійок відносно повзунів забезпечує регулювання відстані від осі обертання інструмента (вісь шпинделя) до формоутворюючого елемента. Така конструкція разом з регулюванням диференційними гвинтами вильотів ножів забезпечує можливість здійснення ступінчастого стругання з останнім чистовим проходом.
Ролики (підшипники) опираються на поверхню копіра, який жорстко закріплений на пінолі шпинделя і рухається разом зі шпинделем та корпусом в осьовому (встановлювальному) напрямку.
К
© В.Ю. Лоєв, О.В. Головатенко, Є.В. Салогуб, 2011
опір має ділянку перетворення колового руху шпинделя на прямолінійний рух формоутворюючих елементів, забезпечуючи постійну відстань між протилежно розташованими різальними кромками елементів.
Передбачається проведення комплексу експериментальних досліджень розробленого інструмента, а саме підтвердження зазначених переваг стругання перед торцевим фрезеруванням.
Розроблено також конструкцію торцевої фрези з внутрішньою та зовнішньою обоймами, в яких закріплені різальні елементи при їх взаємопротилежному русі. В основу винаходу поставлено завдання вдосконалення конструкції торцевої ступінчастої фрези шляхом додаткового введення блока шестерень, закріпленого в корпусі з можливістю обертання, причому перше зубчасте колесо зчеплене з другим зубчастим колесом за допомогою шестерні та блока шестерень, а внутрішні та зовнішні різальні елементи, кількість яких однакова, встановлені з можливістю регулювання їх осьових вильотів, що забезпечить значне підвищення якості й точності обробки та збільшення продуктивності праці.
Поставлене завдання вирішується тим, що завдяки додатково введеному блоку шестерень передача крутного моменту від внутрішньої обойми, яка закріплена на шпинделі верстата, до зовнішньої обойми є триступеневою. Це робить кутову швидкість внутрішньої та зовнішньої обойм однаковою, але взаємопротилежною. В результаті цього сили, які діють на оброблювану деталь у процесі різання, урівноважуються, а також частково знімається навантаження з напрямних верстата. Все це суттєво підвищує якість і точність обробленої поверхні.
Крім того, встановлення внутрішніх та зовнішніх різальних елементів з можливістю регулювання їх осьових вильотів дозволяє виконувати це в закріпленому на шпинделі верстата інструменті без його розбирання, що значно збільшує продуктивність праці.
Нами було розроблено і запатентовано спосіб плоского фрезерування торцевими фрезами, який містить зняття припуску чорновими та чистовими різальними елементами з наступним поверхневим деформуванням деформуючими елементами. Суть винаходу: перед видаленням чистового припуску чорновий припуск видаляють також чорновими різальними елементами, які рухаються за прямолінійною траєкторією перпендикулярно до вектора поздовжньої подачі й розташовані в радіальному напрямку на меншій відстані від осі фрези з більшим вильотом відносно нерухомо закріплених у корпусі фрези чорнових різальних елементів та на більшій відстані від осі фрези з меншим вильотом відносно чистових різальних елементів. Перед кінцевим формуванням виконують легування поверхневого шару оброблюваної плоскої поверхні за допомогою легуючих елементів, які рухаються за прямолінійною траєкторією перпендикулярно до вектора поздовжньої подачі та пружно закріплені в корпусі фрези на меншій відстані від осі фрези в радіальному напрямку з більшим вильотом відносно чистових різальних елементів. Технічний результат: значне підвищення якості та зносостійкості оброблюваної поверхні.
Було розроблено також спосіб обробки різанням нежорстких деталей, який дозволяє знизити металоємність і трудомісткість машин та механізмів, а також без застосування люнетів, підвідних опор та інших пристроїв здійснювати якісну обробку нежорстких деталей.
Розроблено також перспективний спосіб обробки плоских поверхонь торцевим фрезеруванням «без робочих подач» – спосіб обробки плоских поверхонь торцевим фрезеруванням, згідно з яким відносне переміщення заготовки і торцевої фрези відбувається без процесу різання за час обертання інструмента після виходу останнього різального елемента до врізання першого, який відрізняється тим, що в процесі різання робоча подача відсутня.
Переваги розробленого способу полягають у наступному:
1. В момент видалення припуску заготовка і шпиндель верстата жорстко закріплені відносно напрямних, що підвищує якість обробки, через збільшення жорсткості технологічної системи.
2. Траєкторія руху різального елемента колова, на відміну від традиційної трахоїдної при торцевому фрезеруванні, що підвищує якість обробки і стійкість інструмента через незмінність параметрів різання.
3. Суттєво знижено вібрації в системі «інструмент–заготовка», що сприяє зниженню шорсткості оброблюваної поверхні й підвищенню стійкості інструмента.
Нами ведеться подальша робота з розробки сучасних комбінованих методів обробки плоских поверхонь деталей машин.
УДК 681.5:620.1
^ О.Л. Мельник, аспір.
Житомирський державний технологічний університет
Я.Д. Ярош, к.т.н., доц.
Житомирський національний агроекологічний університет
^ ФОРМУВАННЯ СТРУКТУРИ І ВЛАСТИВОСТЕЙ ГРАФІТ-КЕРАМІЧНИХ КМ
ПРИ СПІКАННІ У ЗАКРИТІЙ СПЕЦФОРМІ
Основні напрямки використання графіт-керамічних композиційних матеріалів (ЕГККМ) у будівельній промисловості – це електронагрівальні елементи з рівномірно розподіленим тепловиділенням, широким діапазоном робочих температур (до 300 C), значним діапазоном зміни електричної провідності до 100 (Ом ∙ м)-1 і можливістю гнучкого варіювання потужності приладів для забезпечення необхідних температур.
У даній роботі описаний вплив параметрів пресування і спікання на структуру та властивості ЕГККМ, вплив деформацій на кінетику електричного опору матеріалу отриманих матеріалів, явище, що відоме в літературі як п’єзорезистивний ефект.
Для виготовлення ЕГККМ використовували терморозширений графіт (ТРГ), що виготовлений із природного графіту Завалівського родовища, та каолін Глухівецького гірничо-збагачувального комбінату марки П-2 сухого збагачення.
У процесі спікання спресованих напівсухим способом виробів ЕГККМ значно зростала їх пористість. При тиску пресування 150 МПа у зразках із 23 % (мас.) ТРГ пористість неспечених зразків складала близько 28 %. Після спікання таких зразків при максимальній температурі 900 C і витримуванні при цій температурі 1 год. пористість зросла до 58 %; при температурі спікання 1300 C та витримуванні протягом 1 год. – до 55 %.
Збільшення часу витримування при максимальній температурі призводить до збільшення пористості в середньому на 1 %, а температури спікання з 900 C до 1300 C – до зниження пористості, що пов’язано з тим, що в межах температур 1205–1240 C відбувається значна усадка через кристализацію кристобаліту з аморфного кремнезему. Взагалі, діапазон зміни пористості за даних умов експерименту складав 34–50 %.
Зростання пористості відбувалося за рахунок проходження таких процесів:
- Істотне збільшення об’єму зразка після спікання у "вільному" стані за рахунок пружної післядії ТРГ під впливом температури. Зокрема, це підтверджується тим, що залежність пористості графіт-кераміки від вмісту ТРГ має близький до лінійного характер і змінюється від спадної (до спікання) до зростаючої (після спікання). Взагалі, діапазон зміни пористості спечених матеріалів складає 30–60 %.
- Структурні термохімічні перетворення в матеріалі. Перетворення -кварц -кварц зі збільшенням об’єму на 2,4 %; -кварц α-тридиміт – збільшення об’єму на 16 %;
-кристобаліт β-кристобаліт – збільшення об’єму на 2,8 %.
- Дегідратація мінералів та вигорання органічних домішок, що призводить до зменшення ваги.
- Утворення мінералів з більшою густиною/питомою вагою. Густина вихідного каолініту 2,6 г/см3, кінцевого муліту 3,1 г/см3, що зменшує розрахунковий об’єм (об’єм абсолютно щільного матеріалу) при незмінному дійсному об’ємі.
Пори в керамічних матеріалах залежно від розмірів, форми, розташування й об’єднання в канали відіграють роль концентраторів напруги, знижуючи механічну міцність матеріалу. Близько 90 % всього об’єму пор припадає на макропори (розмір > 10 мкм за Дубліном).
Заміна в результаті технологічних операцій (наприклад, вібраційні методи) капілярної пористості (розмір > 1 мкм) на мікро- та макропори сприяє підвищенню міцності на 30–40 %. Дисперсія розмірів пор в об’ємі матеріалу повинна знаходитися в межах 2–5 %. Збільшена дисперсія визначає більшу різнотовщинність міжпорових перегородок. Останнє негативно впливає на механічну міцність та рівномірність теплопередачі. З іншого боку, пористість утрудняє створення адекватної математично-механічної моделі для прогнозування властивостей композита. Тому однією з найважливіших проблем при розробці ЕГККМ є керування пористістю зразків.
Н
© О.Л. Мельник, Я.Д. Ярош, 2011
айбільший вплив на пористість має перший чинник. У зв’язку з цим нами був запропонований і випробуваний спосіб спікання зразків у закритих формах, які забезпечують постійність геометричних розмірів виробів. Такий "формообмежуючий" чинник дозволив уникнути вказаних вище недоліків і отримати деякі переваги в структурі та властивостях матеріалу. Також було запропоновано використовувати промислові значення тисків пресування ЕГККМ в межах 5–30 МПа, що полегшить їх впровадження у виробництво.
У результаті зразки, що містять 23 % (мас.) ТРГ, спресовані з тиском 30 МПа після спікання протягом 3 год. при температурі 1150 C, мали пористість 57,15 %.
Наступний важливий аспект при створенні графіт-кераміки – це формування електропровідних властивостей і перколяційних характеристик. Питома електрична провідність "вільно" спечених ЕГККМ нелінійно зростає і досягає при максимальній концентрації 28,6 % (мас.) ТРГ значення 100 (Ом ∙ м) -1. При цьому варто зазначити незначний вплив спікання на зміну провідності матеріалу, що, швидше за все, пов’язано з різким зростанням його пористості. Зростання тиску пресування сприяє підвищенню провідності в напрямку вздовж осі пресування, а в напрямку поперек осі пресування провідність спадає при підвищенні зусилля пресування. Це можна пояснити специфікою формування провідних кластерів із частинок ТРГ у процесі пресування зразків. Зрозуміло, що при підвищенні тиску пресування частинки ТРГ (або їх агломерати) утворюють плоскі шаруваті структури, товщина яких зменшується при підвищенні тиску пресування. Таким чином, електричний опір таких шарів спадає, але тиски недостатні для утворення належної кількості "зв’язків" між такими шарами. У напрямку, перпендикулярному осі пресування, навпаки, в кожному умовно незалежному шарі при збільшенні площі пласких графітових структур підвищується ймовірність утворення провідного кластера з частинок ТРГ.
Графіт-кераміка за даних умов виготовлення, при вмісті ТРГ у межах 16–23 % (мас.) знаходиться якраз навколо порога протікання, про що свідчать, зокрема, перехід у провідний стан і висока чутливість електричного опору до механічних деформацій.
Електропровідність графіт-кераміки, спеченої у спецформах, істотно зменшується, і, крім того, присутня значна анізотропія електричних властивостей у напрямах паралельно й перпендикулярно осі пресування. Як приклад, електропровідність зразків з 23 % (мас.) ТРГ після спікання у "вільному" стані та спецформі складає відповідно до 80 (Ом ∙ м)-1 і 1 (Ом ∙ м)-1. Анізотропія електричних властивостей коливається в межах /|| = 15–20.
Аналіз отриманих результатів показав, що найбільше значення модуля Юнга мають зразки, сформовані при максимальному тиску 30 МПа та масовому вмісті ТРГ 9,1 %. При цьому максимальні напруження згину до початку руйнування зразків відрізняються несуттєво. Значна зміна значення модуля Юнга обумовлюється такими основними причинами:
- Збільшення тиску пресування сприяє зростанню щільності, зменшенню пористості та лінійних розмірів. Зменшення лінійних розмірів, у свою чергу, зменшує полярний момент опору, що знаходиться в обернено пропорційній залежності з модулем Юнга. Максимальний тиск відповідає мінімальному прогину балки зразка матеріалу.
- Збільшення вмісту ТРГ сприяє збільшенню лінійних розмірів, зменшенню щільності, збільшенню пористості, внаслідок чого зменшується жорсткість зразка, або, іншими словами, збільшується поперечний прогин зразка при навантаженні поперечною силою.
- При тиску р = 30 МПа та масовому вмісті ТРГ 9,1 % мало місце значне осьове прогинання досліджуваного зразка, максимальне значення якого до руйнування становило 0,45 мм, що свідчить про початок пластичного деформування матеріалу.
Таким чином, завдяки спіканню в спеціальній формі ми досягли однакової пористості, зменшивши тиск пресування в 3 рази. При цьому міцність матеріалу відповідає міцності будівельних матеріалів (модуль Юнга Е = 140 МПа, межа міцності на згин 3–3,5 МПа), забезпечивши задовільну провідність матеріалу. Структура отриманих матеріалів утворює кластер із провідних частинок з докритичною, але близькою до порога перколяції вагою, про що свідчить надзвичайна чутливість електричного опору до незначних змін напружено-деформованого стану, що потребує подальших досліджень.
УДК 621.9.015
^ А.М. Снитко, аспір.
Житомирський державний технологічний університет