Методические указания к проведению лабораторно- практических занятий по дисциплине
Вид материала | Методические указания |
- Методические указания к проведению практических занятий по дисциплине "Финансовый менеджмент", 1157.87kb.
- Методические указания для студентов по выполнению практических занятий по дисциплине, 1393.58kb.
- Методические указания к проведению практических занятий по курсу «Архитектура гражданских, 272.14kb.
- Методические указания для выполнения практических занятий по дисциплине, 233.07kb.
- Методические указания к проведению практических занятий для студентов 3 курса педиатрического, 423.46kb.
- Методические указания для студентов по проведению практических занятий по дисциплине, 688.24kb.
- Методические указания Методические указания к проведению практических занятий по курсу, 71.22kb.
- Методические указания по самостоятельной подготовке к практическим занятиям и выполнению, 426.22kb.
- Рабочая программа и методические указания по проведению практических и самостоятельных, 380.19kb.
- В. И. Дихтяр Сетевые технологии в сксит учебно-методический комплекс, 318.51kb.
Министерство образования и науки Республики Казахстан
Павлодарский государственный университет
им. С. Торайгырова
Факультет металлургии, машиностроения и транспорта
Кафедра машиностроения и стандартизации
ПРОЕКТИРОВАНИЕ ТЕХНОЛОГИЧЕСКОЙ ОСНАСТКИ
методические указания к проведению лабораторно-
практических занятий по дисциплине
«Проектирование технологической оснастки»
для студентов машиностроительных специальностей
(для внутривузовского пользования)
Павлодар
УДК 621.002.54.001.63 (07)
ББК 34.4-я73
П79
Рекомендовано Учёным советом ПГУ им. С. Торайгырова
Рецензенты:
кандидат технических наук, профессор И.А. Шумейко
кандидат технических наук, профессор Н.С. Дудак
Составители: Р.О. Олжабаев
А.Ж. Касенов
П79 Проектирование технологической оснастки: методические указания к проведению лабораторно-практических занятий по дисциплине «Проектирование технологической оснастки» для студентов машиностроительных специальностей (для внутривузовского пользования)/ сост. Олжабаев Р.О., А.Ж. Касенов. – Павлодар, 2007. – 19с.
Методические указания составлены, с целью научить студентов проектировать технологическую оснастку. В процессе выполнения лабораторно-практической работы на конкретной детали студентам предлагается спроектировать приспособление из элементов УСП для механической обработки, также производится расчёт потребной силы зажима и экономическая эффективность применения приспособления.
Методические указания разработаны в помощь студентам машиностроительных специальностей при проектировании технологической оснастки для механической обработки деталей.
УДК 621.002.54.001.63(07)
ББК 34.4-я73
© Олжабаев Р.О., А.Ж. Касенов, 2007
© Павлодарский государственный университет им. С. Торайгырова, 2007
Введение
Технологическая оснастка является важной составляющей повышения эффективности и качества машиностроительного производства. Основную группу технологической оснастки составляют приспособления механосборочного производства. В промышленности эксплуатируются более 25 млн. специальных станочных приспособлений. Затраты на изготовление оснастки приблизились к затратам на производство станков. Значительные трудовые и материальные затраты связаны с тем, что технологическая оснастка оказывает влияние на производительность труда, качество и сокращение сроков освоения производства новых изделий.
Применение приспособлений позволяет устранить разметку заготовок перед обработкой, повысить точность обработки, снизить себестоимость продукции, расширить технологические возможности оборудования, сократить число станочников.
Частая смена объектов производства, требует создания конструкций и систем приспособлений, обеспечивающих сокращение сроков производства. В серийном производстве необходимо использовать специализированные быстропереналаживаемые и обратимые системы приспособлений. В мелкосерийном производстве широко применяются системы универсально-сборных приспособлений (УСП).
Применение технологической оснастки переналаживаемого типа позволяют расширять технологические возможности как универсальных, так и станков с ЧПУ, гибких производственных модулей (ГПМ) и робототехнических комплексов (РТК). Проводимая работа по унификации и стандартизации элементов приспособлений создала основу для автоматизированного проектирования приспособлений с использованием ЭВМ. При внедрении переналаживаемых станочных приспособлений в 2…3 раза уменьшается трудоёмкость проектирования и 3…4 раза сроки производства станочных приспособлений.
1 Цели и задачи работы
- Цель работы
Цель работы закрепление методики проектирования технологической оснастки из УСП и приобретения навыков сборки приспособления из элементов УСП.
- Основные задачи работы:
- общие принципы проектирования технологической оснастки станков;
- методику расчёта усилий зажима элементарных устройств;
- выбор и компоновка универсально-сборных приспособлений (УСП);
- расчёт потребной силы зажима;
- расчёт приспособления на точность;
- выбор и проектирование схем приспособлений;
- пользоваться нормативно-справочной литературой;
- пользоваться действующими стандартами при назначении параметров точности;
- технически грамотно оформлять чертежи и техническую документацию
Методическое указание состоит из двух взаимосязанных частей:
- для проведения практических занятий;
- для проведения лабораторных работ.
В первой части работы студенты выполняют расчётную часть проекта, а во второй части выполняют сборку приспособления из элементов УСП и производят обработку пробной заготовки.
2 Основные теоретические положения
2.1 Универсально-сборные и переналаживаемые приспособления
Переналаживаемые приспособления многократного применения позволяют быстро и многократно собирать их для различных видов механической обработки из набора стандартизованных деталей и сборочных единиц. Это обеспечивает повышение производительности труда, способствует внедрению высокопроизводительных методов обработки, снижает сроки подготовки технологической оснастки [1, 2, 3, 4].
Компоновки универсально-сборных приспособлений (УСП) собирают из готовых нормализованных взаимозаменяемых деталей и сборочных единиц.
Элементы системы УСП формируют в комплекты номенклатурный и качественный состав, которых зависит от характера объёма выпускаемой предприятием продукции, и колеблется от 4 до 50 тысяч элементов. Применяют комплекты УСП с шириной паза 8, 12, 16мм. Ширину паза используют для обозначения серии комплекта. Техническая характеристика комплектов УСП приведена в таблице 1.
Таблица 1 – Техническая характеристика комплектов УСП
№ п/п | Характеристика | Серия комплекта | ||
УСП-8 | УСП-12 | УСП-16 | ||
1 | Ширина шпоночного паза и его допустимое отклонение | 8Н7 | 12Н7 | 16Н7 |
2 | Допустимое отклонение шпонки | h6 | h6 | h6 |
3 | Диаметр основной крепёжной резьбы, мм | М8 | М12×1,5 | М16 |
4 | Шаг между пазами, мм | 30 | 60 | 90 |
5 | Среднее время сборки одного приспособления | 1,5 | 3,0 | 6,0 |
6 | Габаритные размеры обрабатываемых заготовок, мм: длина ширина высота | 220 120 100 | 700 400 500 | 2500 2500 1000 |
7 | Наибольшая масса обрабатываемых заготовок, кг | 3 | 60 | 3000 |
8 | Наибольший диаметр обрабатываемых заготовок, мм | 12 | 38 | 50 |
Используя комплекты всех серий можно собирать УСП для различных типов станков. Элементы УСП по функциональному назначению разделяют на шесть группы:
а) базовые (плиты, угольники, оправки и др.);
б) корпусные (опоры, призмы и др.);
в) установочно-направляющие (шпонки, пальцы, кондукторные втулки и др.);
г) крепёжно-прижимные (прихваты, планки, болты, гайки и др.);
д) разные (вилки, оси и др.);
е) сборочные единицы (поворотные головки, зажимные устройства и др.).
На сопрягаемых (рабочих) плоскостях основных элементов УСП имеется сетка из взаимно перпендикулярных П или Т-образных пазов. По способу «шпонка-паз» с минимально гарантированным зазором осуществляется взаимная ориентация элементов. К точности элементов УСП предъявляют высокие требования.
Базовые и корпусные детали УСП изготавливают из стали 12ХН3А с последующей цементацией и закалкой до твёрдости HRC 58…62, установочные из стали У8А с закалкой до твёрдости HRC 38…42.
Для обеспечения эффективного использования оснастки УСП созданы конструкторские службы в составе конструктора и слесаря-сборщика. Конструктор разрабатывает компоновочные схемы сложных УСП и производит расчёт настроечных размеров, а также конструирует специальные детали.
Монтаж УСП начинают с выбора основания, которое может состоять из одной или нескольких базовых плит, соединённых с помощью планок и угольников. С помощью шпонок и крепёжных деталей корпусные элементы крепят на основании или столе станка.
В УСП для сверлильных и расточных работ, в него вводят детали для направления режущего инструмента. При сборке вращающихся приспособлений для токарных, шлифовальных и др. станков предусматривается место для установки корректирующего элемента, массу и положение которого определяют при балансировке приспособления (допустимый дисбаланс – не менее 0,01…0,05 Н×м.).
Заключительным этапом компоновки приспособления является установка деталей, обеспечивающих точное положение УСП на станке.
На рисунке 1 приведен пример УСП для сверления двух отверстий в валике. Основанием служит прямоугольная плита 1, на которой установлены две колонки из опор 2 кондукторными планками 3. Заготовка 7 базируется на две ступенчатые планки 9 и винтом 6 поджимается к планке 8. Зажим производится прихватом 4, а сверление отверстия производится через кондукторную втулку 5.
К недостатком УСП следует отнести пониженную жёсткость элементов и компоновки в целом, высокую податливость крепёжных элементов, недостаточную жёсткость фиксации, невысокий уровень механизации и высокую стоимость комплекта.
Разработаны и широко применяются ряд специализированных систем УСП.
Универсально-сборные механизированные приспособления (УСПМ) предназначены для обработки заготовок (400×400×260) на универсальных станках и станках с ЧПУ фрезерной и сверлильной группы. УСПМ выпускают двух видов: с пазом 12мм (УСПМ-12ЧПУ) и 16мм (УСПМ-16ЧПУ). Применяемые средства механизации обеспечивают их использование с элементами стандартных комплектов УСП соответствующего размера. Точность обработки в УСПМ соответствует IT6…IT8.
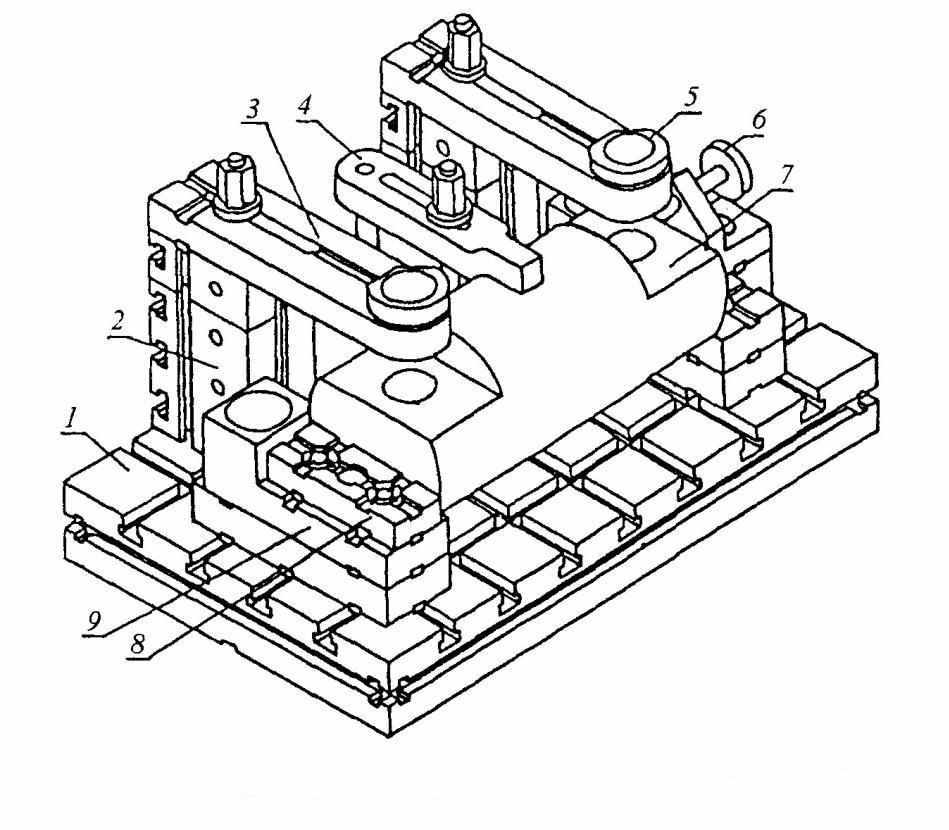
Рисунок 1 – УСП для сверления двух отверстий
На рисунке 2 показано УСПМ-ЧПУ для фрезерования пазов. Заготовку 3 устанавливают по плоскости и двум отверстиям на планки 2 5 и два пальца. Закрепление осуществляется прихватами 1 от гидроцилиндров 4.
Сборно-разборные приспособления (СРП) являются разновидностью системы УСП. Основное отличие СРП от УСП заключается в том, что СРП собирают из деталей и сборочных единиц с применением сменных наладок на весь период производства изделия. Точность обработки в СРП соответствует IT6…IT7. СРП переналаживают путём перекомпоновки, регулирования или замены сменных наладок. Фиксацию элементов в СРП осуществляют способом «палец – точное отверстие», для чего на элементах выполнены система точно координированных цилиндрических отверстий. Для закрепления сменных наладок и других элементов предусмотрены продольные Т-образные пазы. Закрепление заготовок обеспечивают встроенные в плиты гидроцилиндры, а также гидравлические зажимные устройства.
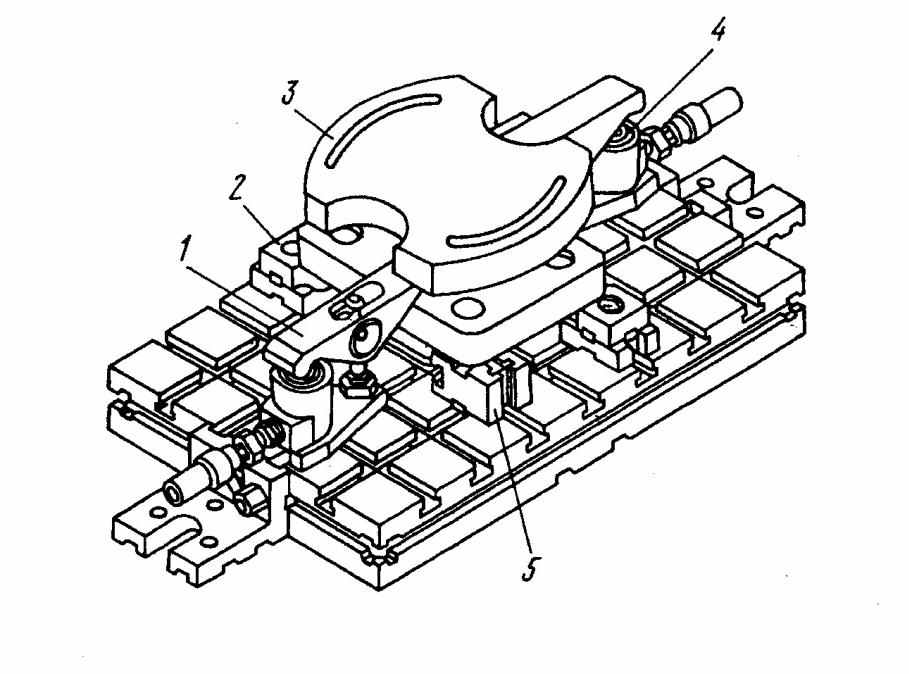
Рисунок 2 – УСПМ-ЧПУ для фрезерования пазов
Так как плиты СРП выполнены не с поперечными пазами и отверстиями, их жёсткость в 2 раза выше, чем жёсткость аналогичных плит УСП. В комплекте СРП предусмотрены переходники, позволяющие собирать комбинированные приспособления из УСП и СРП, что расширяет их технологические возможности. К недостаткам СРП относят меньшую универсальность, более трудоёмкую и дорогую наладку, отсутствие деталей для направления режущего инструмента.
Комплекс универсально-сборной и переналаживаемой оснастки (УСПО) является новой системой переналаживаемого типа. УСПО предназначена для сборки приспособлений в серийном производстве деталей мелких и средних размеров на станках фрезерно-сверлильно-расточной групп.
В УСПО применяют беззазорное соединение элементов способом «цилиндрическое отверстие – пружинящее разрезное коническое кольцо – жёсткий штифт с двумя конусами», которое обеспечивает высокую жёсткость и точность сборки элементов и сохранение этой точности в течение всего периода работы УСПО [2, 3].
Для комплекта УСПО характерен высокий уровень механизации вследствие применения механизированных сборочных единиц (гидрофицированные базовые плиты) и автономных средств механизации (гидроцилиндры, гидроприжимы и др.) все гидравлические устройства рассчитаны на рабочее давление 20 МПа вместо 10 МПа как УСПМ. Увеличены габариты базовых плит до 800×630 мм, что позволяет собирать приспособления для многоместной обработки крупных заготовок.
Увеличение жёсткости элементов УСПО в 1,3 раза вследствие перехода от П и Т-образных пазов к цилиндрическим и резьбовым отверстиям, повышение точности и стабильности положения элементов приспособления в 2…3 раза, что позволяют в 1,7 раза увеличить режимы резания и в 2 раза точность обработки заготовок по сравнению с УСП.
Каждая серия УСПО включает комплекты Е – для единичного и мелкосерийного производства с пониженным уровнем механизации и С – для серийного производства (таблица 2).
Таблица 2 – Основные данные комплекта УСПО
Показатель | УСПО-8Е | УСПО-8С | УСПО-12Е | УСПО-12С | УСПО-16Е | УСПО-16С |
Число деталей и сборочных единиц всего базовых | 4100 40 | 1600 32 | 4000 40 | 1700 32 | 4900 40 | 1700 32 |
Число собираемых приспособлений одновременно в течении года | 40 2540 | 32 2100 | 40 2600 | 32 2100 | 40 1740 | 32 2100 |
Габариты базовых плит, мм длина ширина высота | 200-400 140-400 30 | 240-630 180-480 45 | 220-980 220-700 45-60 | |||
Максимальная масса устанавливаемых заготовок, кг | 5 | 50 | 500 |
По функциональному назначению элементы комплекса УСПО подразделяют на следующие группы: базовые, корпусные, установочные, направляющие, зажимные, крепежные, средства механизации зажима заготовок.
К группе базовых деталей относятся квадратные, прямоугольные и круглые плиты, угольники тумбы; к группе корпусных – элементы комплекта, предназначенные для создания корпусов приспособлений. Основой построения конструкции всех элементов группы корпусных деталей является модуль – квадрат со сторонами для каждой серии 8, 12, 16 соответственно 30, 45, 60 мм. В углах квадратов расположены четыре отверстия диаметром соответственно 8, 12, 16 мм с межцентровым расстоянием 20, 30 и 40 мм и центральным отверстием с зенковкой 10/16, 14/23, 18/28.
Установочные детали в виде колпачковых опор, дисков, пальцев, упоров и т.д. используются в приспособлениях УСПО в качестве баз. К направляющим элементам относятся различные шпонки, штифты, втулки, валики, колонки др. детали, используемые при компоновке приспособлений. К зажимным деталям относятся различные прихваты, прижимы, зажимы, качалки, быстросъёмные шайбы, предназначенные для закрепления заготовок.
Для компоновки механизированных приспособлений может использоваться гидроплита, на верхней плоскости которой выполнена сетка координатно-фиксирующих и резьбовых отверстий, предназначенных для установки и закрепления сменных наладок для установочных и зажимных единиц комплекта УСПО. В корпусе плиты встроены гидроцилиндры.
3 Последовательность выполнения работы по сборке приспособления из элементов УСП
3.1 Изучение чертежа детали. Выбор установочных элементов. Эскизная компоновка приспособления из УСП
Для выполнения лабораторной работы студенту выдаются чертёжи деталей и детали с ТУ на изготовление. Детали представлены в виде ступенчатого валика (1 вариант) для фрезерования шпоночного паза и деталь в виде плиты для сверления отверстия (2 вариант).
В зависимости от конструктивных форм обрабатываемой заготовки выбирается тип установочных элементов (призмы, установочные пластины и т.п.).
3.2 Разработка кинематической схемы зажимного устройства. Определение потребной силы зажима
В наборе УСП имеется винтовой зажим, поэтому необходимо использовать схемы зажимного устройства с винтовым зажимом. Потребная сила зажима определяется из условия равновесия сил действующих при обработке [1, 2].
Расчёт винтовых зажимных устройств производится в следующей последовательности:
3.2.1 Определяется номинальный диаметр резьбы винта d по формуле
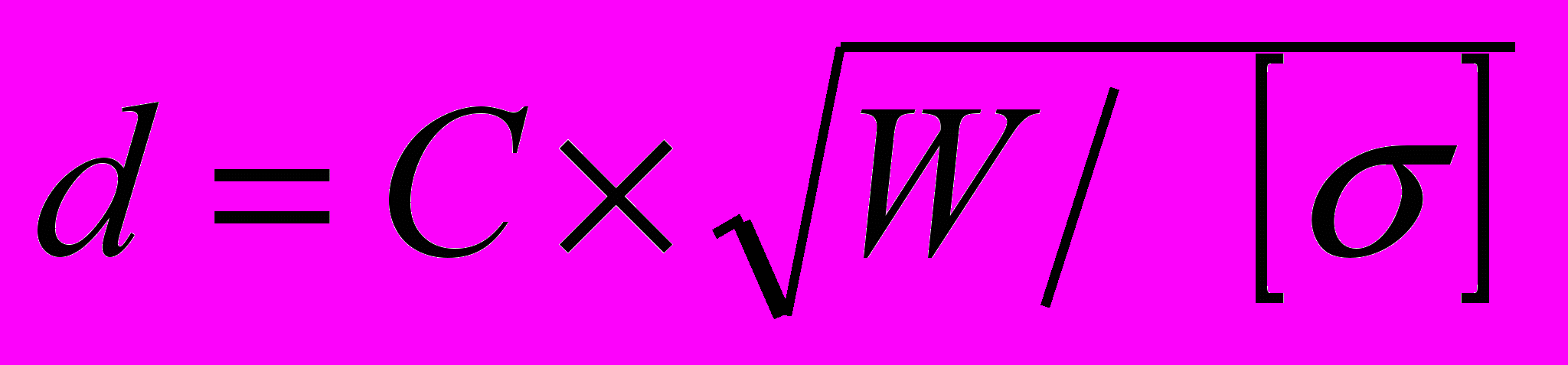
где С – коэффициент, для основной резьбы С=1,4;
W – потребная сила зажима, Н;
[σ] –допускаемое напряжение растяжения (сжатия), для винтов из стали 45 с учётом износа резьбы можно принимать [σ]=80…100 МПа.
Значения d округляют до ближайшего большего стандартного значения. Обычно в приспособлениях применяются резьбы от М6 до М52.
3.2.2 Определяют момент М, который нужно развить на винте (гайке) для обеспечения заданной зажимной силы W:

где rср – средний радиус резьбы (для практических расчётов rср=0,45
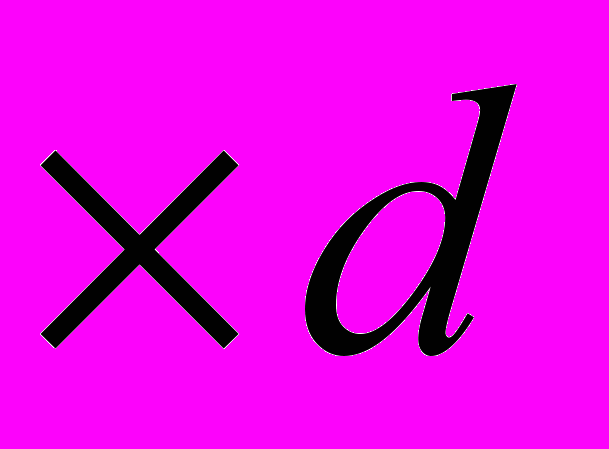
α – угол подъёма резьбы (α=3010'…1050')
φ – угол трения в резьбе;
Мтр – момент трения на опорном терце гайки
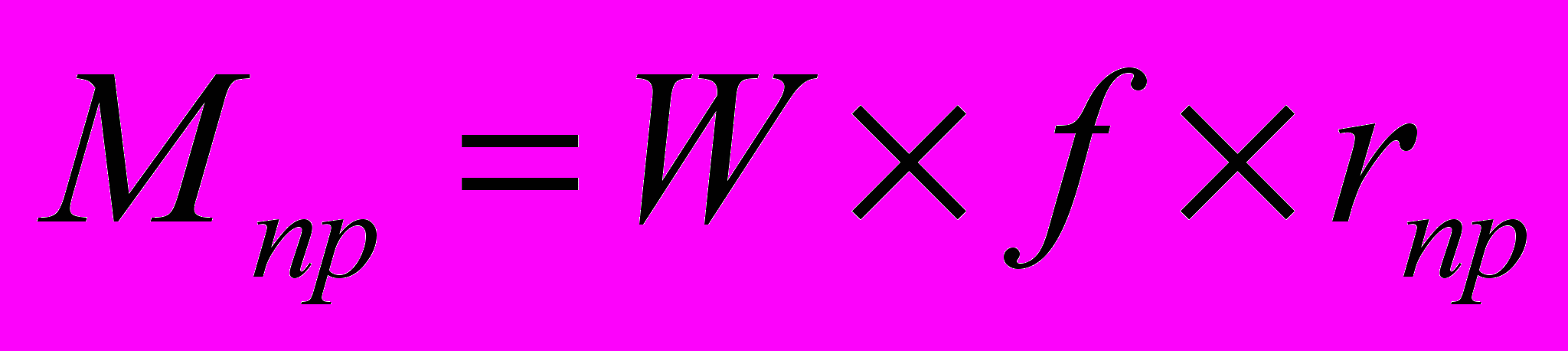
где rпр – приведённый радиус кольцевого торца
для гаек
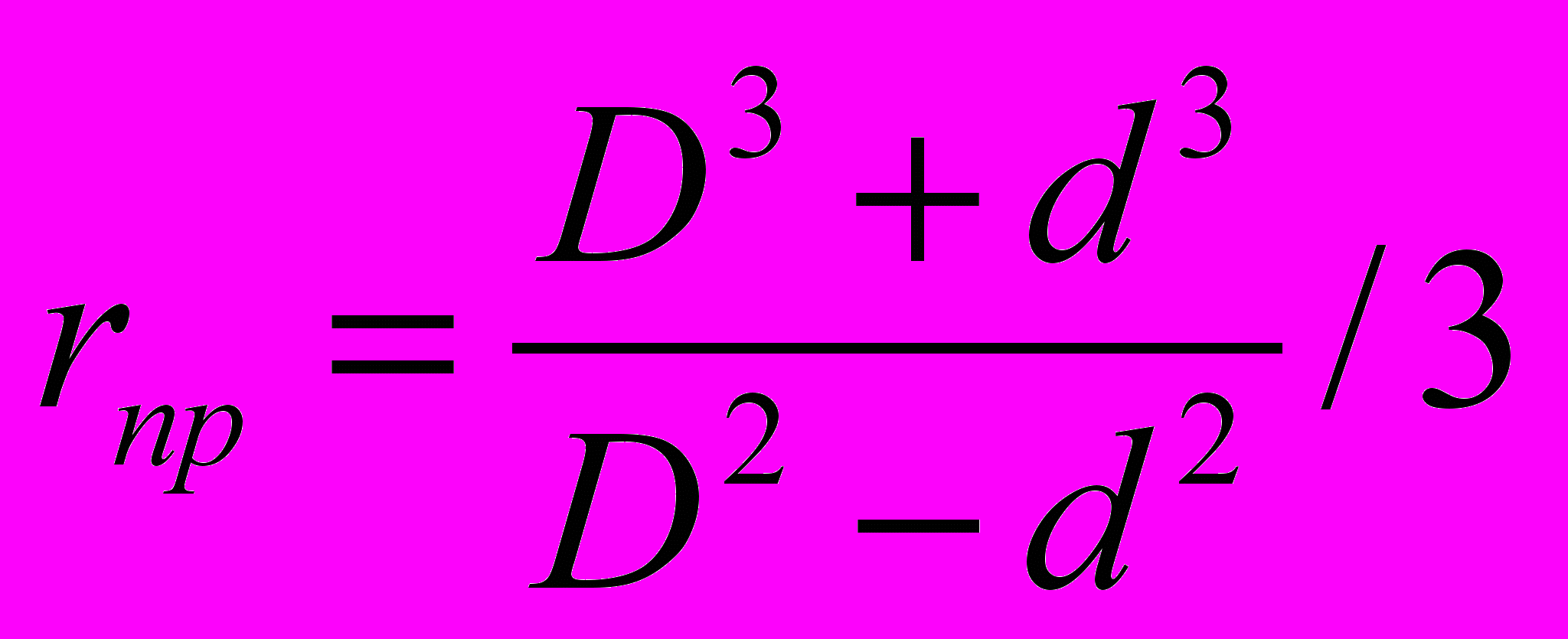
где D – наружный диаметр кольцевого торца гайки.
При средних значениях α=2030', φ=10030', D=1,7
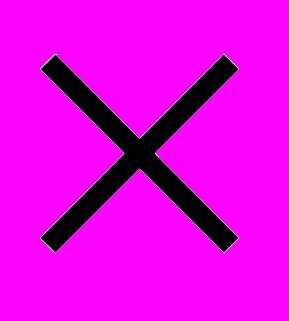

Для момента открепления

3.2.3 Определяется длина рукоятки (ключа) l по заданной силе воздействия (при ручном ) зажиме Рпр≤150 Н) из условия равновесия гайки (винта)
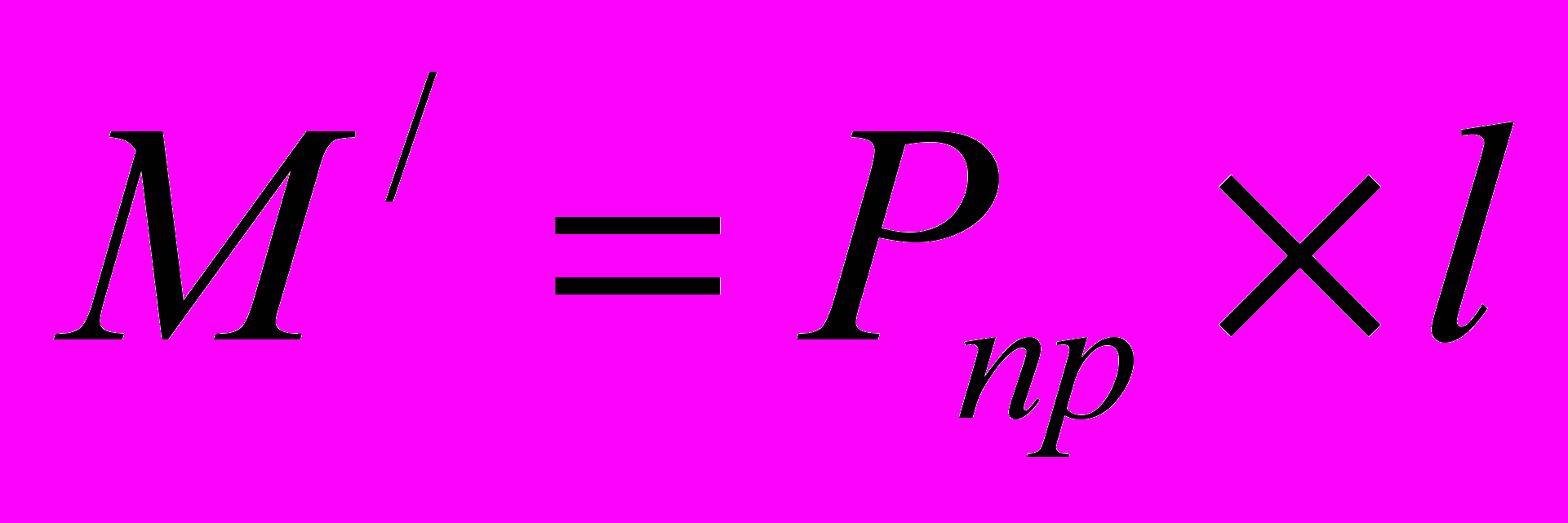
Откуда
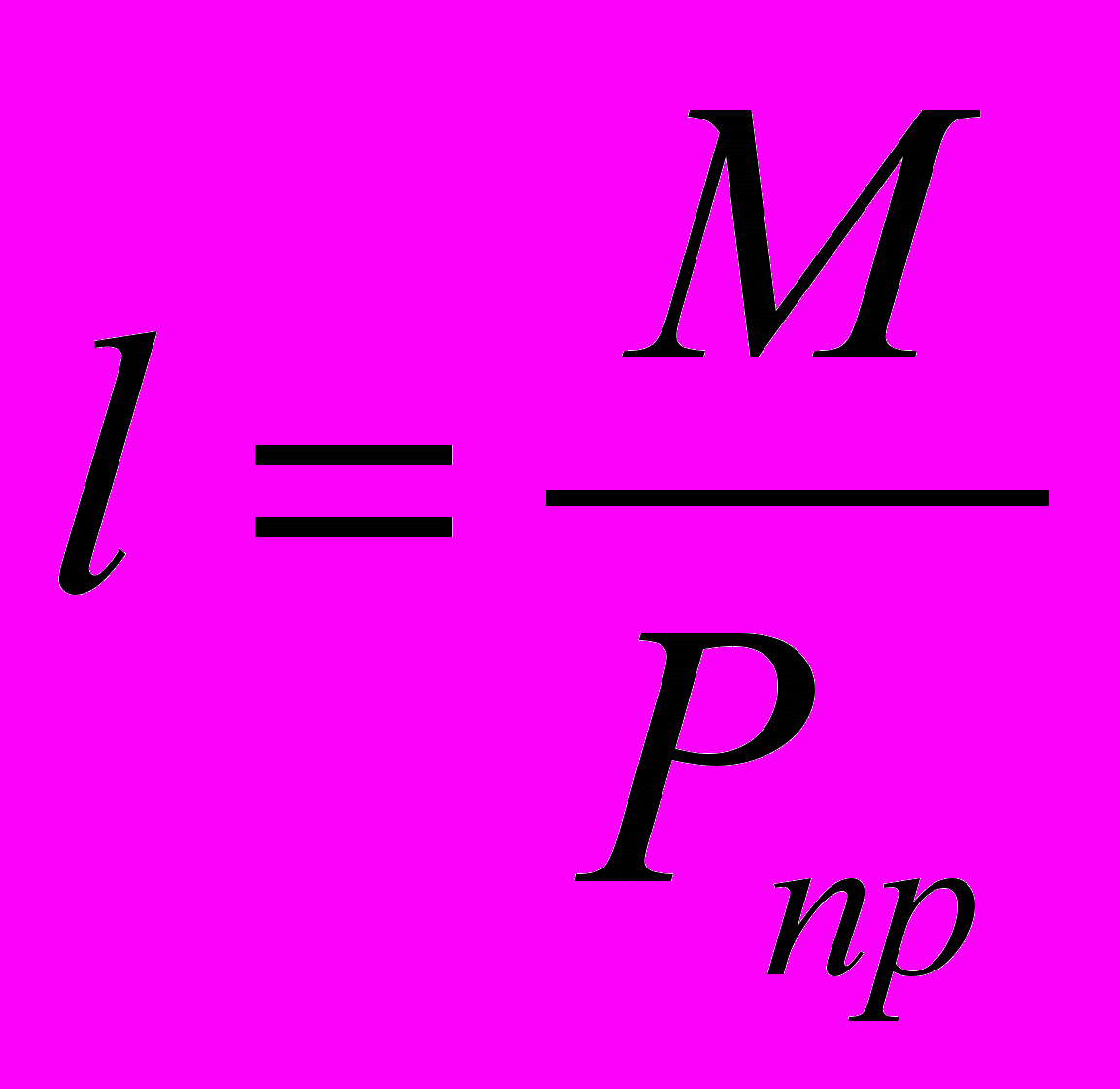
3.3 Оформление чертежа конструкции приспособления. Привязка приспособления к рабочей зоне станка. Определение технических требований к приспособлению
Порядок оформления общего вида приспособления:
3.3.1 Вычертить контуры обрабатываемой заготовки в зависимости от сложности конструкции приспособления в одной или двух (трёх) проекциях. Проекции должны быть вычерчены пунктирными линиями;
3.3.2 Вычертить установочные и базирующие элементы приспособлений в соответствии со схемой базирования;
3.3.3 Вычертить зажимные устройства приспособления в соответствии со схемой приложения сил зажима;
3.3.4 Вычертить устройства для направления и координирования инструмента;
3.3.5 Вычертить вспомогательные устройства (устройства для повышения жёсткости детали, делительные и поворотные устройства);
3.3.6 Вычертить рычажные устройства, соединяющие механизированный привод с зажимными устройствами;
3.3.7 Вычертить приводы механизированных зажимных устройств;
3.3.8 Вычертить корпус приспособления (при этом необходимо учитывать, что корпус приспособления должен быть достаточно жёстким и технологичным);
3.3.9 Вычертить элементы для базирования и ориентации приспособления на столе станка, такими элементами являются направляющие шпонки, пальцы и др.
3.3.10 Вычертить необходимые разрезы и сечения. Проставить размеры, на всех сопрягаемых поверхностях, проставить размеры с посадками. Диаметр отверстия с допустимыми отклонениями на кондукторных втулках, допуски на межцентровое расстояние. Габаритные размеры приспособления. Технические требования, определяющие точность положения базирующих элементов приспособления. Составляется спецификация.
3.4 Подбор элементов УСП и сборка приспособления
Монтаж УСП начинается с выбора основания, которое может состоять из одной или нескольких базовых плит, соединённых с помощью планок и угольников. С помощью шпонок и крепёжных деталей корпусные элементы крепят на основании или столе станка.
В УСП для сверлильных работ, в него водят детали для направления режущего инструмента. Заключительным этапом компоновки приспособления является установка деталей, обеспечивающих точное положение УСП на станке.
3.5 Контроль приспособления по точности положения и обработка пробной заготовки. Контроль точности обработки
Контроль приспособления по точности положения на станке. Технические требования, определяющие точность положения базирующих элементов на ступенчатом валике или отверстия на детали типа плиты (рисунок 3).
3.6 Разборка УСП
После окончания обработки пробных заготовок приспособления разбираются и протираются. Элементы УСП раскладываются по ячейкам шкафа-стеллажа хранения до следующей сборки.
4 Содержание отчета
4.1 Цель работы
4.2 Чертежи деталей
4.3 Кинематическая схема приспособления
4.3 Технические требования на приспособление
4.5 Выводы о проделанной работе
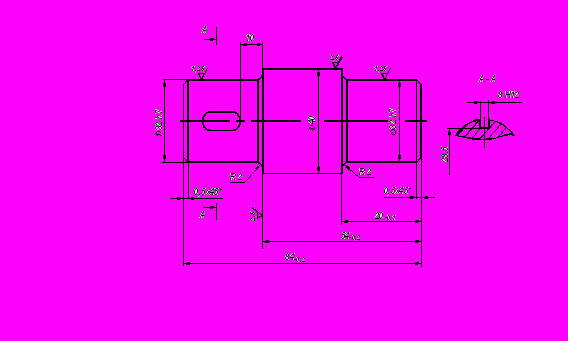
а) цилиндрическая деталь – типа «вал»
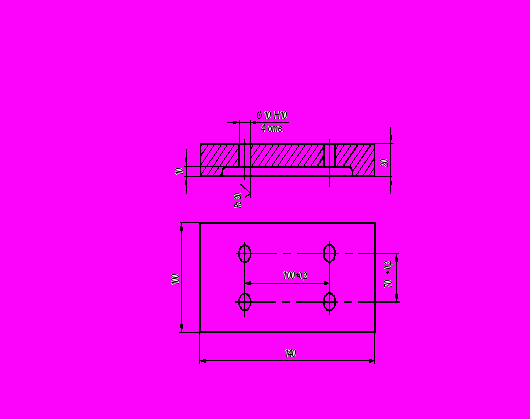
б) плоская деталь
Рисунок 3 – Чертежи деталей
5 Меры безопасности
5.1 При сборке приспособления из элементов УСП не следует применять неисправные ключи
5.2 При обработке пробной заготовки убедиться в прочности крепления заготовки и приспособления на станке
5.3 При работе на станке не пытаться останавливать шпиндель рукой. Деталь следует снимать и устанавливать после полной остановки шпинделя
5.4 Соблюдать правила электробезопасности
Контрольные вопросы
1 Исходные данные для конструирования приспособлений
2 Рабочая зона станка и связь её с приспособлением
3 Приспособление и его составные части
4 Типовые элементы, материализующие основные схемы базирования
5 Материалы, применяемые для изготовления опор
6 Для чего срезают боковые поверхности одного из пальцев при установке детали на два установочных пальца
7 Основные виды элементарных зажимных устройств
8 Классификация приспособлений
9 Последовательность конструирования приспособлений
10 Материалы, применяемые для корпусов
Литература
1 Корсаков В.С. Основы конструирования приспособлений. М.: Машиностроение, 1983 –277с.
2 Корсаков В.С., Олжабаев Р.О. и др. Технологические основы роботизированной сборки. Фрунзе, «Илим» Издательство АН Кирг. СССР, 1986. – 295с.
3 Олжабаев Р.О., Касенов А.Ж. Методические указания к курсовой работе по дисциплине «Проектирование технологической оснастки для студентов машиностроительных специальностей. Павлодар, 2007. – 33с.
4 Справочник технолога-машиностроителя/ Под. ред. А. Г. Косиловой, Р.К. Мещерякова. М.: Машиностроение, 1984, Т1 – 655с., Т2 – 496с.
5 Станочные приспособления: Справочник/ Под. ред. Б.Н. Варушкина и др. М.: Машиностроение, 1984 - Ч.1 –592с.
6 Технология машиностроения. В 2-х томах. Т.2 Производство машин: Учебник для вузов/ Под общ. ред. Г.Н. Мельникова М.: Издательство МГТУ им. Баумана, 1999. – 640с.
Содержание
-
Введение…………………………………………………..….
3
1
Цели и задачи лабораторной работы………………….……
4
1.1
Цель лабораторной работы…………………………….……
4
1.2
Задачи лабораторной работы…………………………..……
4
2
Общие теоретические положения…………………………..
4
2.1
Универсально-сборные и переналаживаемые приспособления………………………………………..…….
4
3
Последовательность выполнения работы по сборке приспособления из элементов УСП…………….…………..
10
3.1
Изучение чертежа детали.
Выбор установочных элементов.
Эскизная компоновка приспособления из УСП……..…….
10
3.2
Разработка кинематической схемы зажимного устройства. Определение потребной силы зажима………………………
11
3.3
Оформление чертежа конструкции приспособления.
Привязка приспособления к рабочей зоне станка.
Определение технических требований к приспособлению..
12
3.4
Подбор элементов УСП и сборка приспособления………..
13
3.5
Контроль приспособления по точности положения и обработка пробной заготовки. Контроль точности обработки……………………………………………………..
13
3.6
Разборка УСП………………………………………………….
13
4
Содержание отчета……….………………………………….
13
5
Меры безопасности….………………………….
15
Контрольные вопросы……….………………………………
16
Литература……………………………………………………
17
УТВЕРЖДАЮ
Проректор по УР
ПГУ им. С. Торайгырова
__________Н.Э. Пфейфер
(личная подпись)
«____»____________2007г.
Составители: к.т.н., профессор Р.О. Олжабаев ______________
старший преподаватель А.Ж. Касенов __________
Кафедра машиностроения и стандартизации
Утверждено на заседании кафедры «07» 09. 2007г. Протокол № 2
Заведующий кафедрой _________________ И.А. Шумейко
Одобрено методическим советом факультета металлургии, машиностроения и транспорта «10» 09. 2007г. Протокол № 2
Председатель МС _____________________Ж.Е. Ахметов
СОГЛАСОВАНО
Декан факультета _____________ Т.Т. Токтаганов «___»_______2007г.
Нормоконтролер ОМК _________ Г.С. Баяхметова «___»______2007г.
ОДОБРЕНО ОПиМО
Начальник ОПиМО ___________ Л.Т. Головерина «___»______2007г.
Рецензия
на методические указания к лабораторно-практической работе «Проектирование технологической оснастки» по дисциплине «Проектирование технологической оснастки».
В методических указаниях представлены устройства, назначение и применение УСП и его элементы, а также технические требования к ним. По приведённым теоретическим положениям студент приобретает навыки проектирования технологической оснастки.
Методические указания разработаны в соответствии с общими требованиями к оформлению и изданию в научно-издательском центре ПГУ им. С. Торайгырова согласно МИ ПГУ 4.02.1-05.
Методические указания разработаны в помощь студентам для полного и наглядного освоения лекционного материала на практике.
Учитывая практическую значимость данной лабораторно-практической работы «Проектирование технологической оснастки» для студентов машиностроительных специальностей, рекомендовать к изданию в НИЦ ПГУ им. С. Торайгырова.
Кандидат технических наук, профессор И.А. Шумейко
Рецензия
на методические указания к лабораторно-практической работе «Проектирование технологической оснастки» по дисциплине «Проектирование технологической оснастки».
Методические указания составлены, с целью научить студентов проектировать технологическую оснастку. В процессе выполнения лабораторно-практической работы на конкретной детали студентам предлагается спроектировать приспособление из элементов УСП на механическую обработку, а также производится расчёт потребной силы зажима и экономической эффективности применения приспособления.
Лабораторная работа предусмотрена для дальнейшего освоения теоретического материала по дисциплине «Проектирование технологической оснастки».
Учитывая практическую значимость данной лабораторной работы «Проектирование технологической оснастки» для студентов машиностроительных специальностей, рекомендовать к изданию в НИЦ ПГУ им. С. Торайгырова.
Кандидат технических наук, профессор Н.С. Дудак