План-конспект лекций по курсу: " Проектирование механосборочных цехов и заводов для студентов спец. 1201 "Технология машиностроения" Составители: Панчишин В. И., доц. Клепиков В. В., проф
Вид материала | План-конспект |
- Квалификационные тесты по дерматовенерологии Москва, 2267.11kb.
- Конспект лекций по теме: «Материаловедение» для специальности 120100 "Технология, 5022.76kb.
- Конспект лекций по теме: «Материаловедение» для специальности 120100 "Технология, 104.18kb.
- Программа курса " история мировой культуры" для студентов исторического отделения, 150.41kb.
- План подготовки электронной учебно-методической литературы на 2008 год план мф по подготовке, 285.38kb.
- Конспект лекций по курсу технология лекаственных форм и галеновых препаратов для студентов, 1506.84kb.
- Составители: доц., к м. н. Т. В. Моторкина, проф., д м. н. Св. Дмитриенко, проф.,, 646.33kb.
- Дополнительная программа кандидатского экзамена по специальности 08. 00. 13 «Математические, 276.2kb.
- Методические указания к лабораторной работе по курсу "Металорежущие станки" для студентов, 275.32kb.
- Конспект лекций бурлачков в. К., д э. н., проф. Москва, 1213.67kb.
ГОСУДАРСТВЕННЫЙ КОМИТЕТ РОССИЙСКОЙ ФЕДЕРАЦИИ ПО ВЫСШЕМУ ОБРАЗОВАНИЮ
МОСКОВСКИЙ ГОСУДАРСТВЕННЫЙ ИНДУСТРИАЛЬНЫЙ УНИВЕРСИТЕТ (МГИУ)
ПЛАН-КОНСПЕКТ
лекций по курсу: " Проектирование механосборочных цехов и заводов для студентов спец. 1201 "Технология машиностроения"
Составители: Панчишин В.И., доц. Клепиков В.В., проф.
МОСКВА 1996
Содержание:
Часть 1
страница
Тема 1. Общие сведения по проектированию механосборочного производства
1. Цели и задачи изучения темы............................................................. 5
2. Перечень основных вопросов темы....................................................5
3. Краткое содержание основных вопросов темы.................................5
3.1. Основные понятия и определения................................................5
3.2. Основные задачи проектирования...............................................12
3.3. Последовательность проектирования.........................................13
Тема 2. Состав и количество основного технологического оборудования
1. Цели и задачи изучения темы............................................................ ..16
2. Перечень основных вопросов темы.................................................... 16
3. Краткое содержание основных вопросов темы................................. 16
3.1. Основные положения по выбору состава технологического оборудования..............................................................................………………………16
3.2. Производственная программа выпуска изделий и методы проектирования цеха................................................................…………………………..22
3.3. Методы определения трудоемкости и станкоемкости обработки и сборки...................................................................…………………………..26
3.4. Режим работы и фонд времени................................................... …28
3.5. Расчет количества основного технологического оборудования и рабочих мест для поточного производства...........................……………………29
3.6. Расчет количества основного технологического оборудования и рабочих мест при непоточного производства........................…………………..34
Тема 3. Принципы и структура построения основных производственных процессов
1. Цели и задачи изучения темы............................................................. …..37
2. Перечень основных вопросов темы...................................................…...37
3. Краткое содержание основных вопросов темы...............................……37
3.1. Основные принципы выбора структуры цеха...........................…...37
3.2. Методика выбора структуры цеха и организационных форм его основных подразделений....................................................... ………40
3.3. Расположение производственных участков цеха.....................……44
3.4. Предварительное определение площади цеха и основных параметров производственного здания.................................…...…………..47
3.5. Выбор варианта расположения оборудования на участках механической обработки...........................................................…………….49
3.6. Особенности расположения оборудования и рабочих мест на участках сборки..........................................................................………..54
3.7. Планировка оборудования и рабочих мест............................... …..55
Тема 4. Определение состава и числа работающих
1. Цели и задачи изучения темы........................................................... …..63
2. Перечень основных вопросов темы.................................................. ….63
3. Краткое содержание основных вопросов темы............................... ….63
3.1. Определение числа производственных рабочих....................... …64
3.2. Многостаночное обслуживание..............................................…….66
3.3. Определение числа вспомогательных рабочих.......................……68
3.4. Определение числа ИТР, служащих и младшего обслуживающего персонала.........................................................................………………………….69
Тема 5. Компоновка механосборочных цехов
1. Цели и задачи изучения темы.........................................................……...72
2. Перечень основных вопросов темы.................................................. ……72
3. Краткое содержание основных вопросов темы.............................……...72
3.1. Выбор параметров здания.......................................................………72
3.2. Компоновочный план............................................................………..75
3.3. Расчет площадей цеха............................................................……….76
3.4. Основные принципы компоновочных решений....................……...78
Литература..................................................................................................………...81
ТЕМА 1. ОБЩИЕ СВЕДЕНИЯ ПО ПРОЕКТИРОВАНИЮ МЕХАНОСБОРОЧНОГО ПРОИЗВОДСТВА
1. Цели и задачи изучения темы:
-знание задач, особенностей и основных направлений развития технологического проектирования механосборочного производства;
-знание применяемых в науке, технике и производстве терминов, определений и условных обозначений, относящихся к технологическому проектированию механосборочного производства;
-знание этапов и последовательности проектирования механосборочных цехов.
2. Перечень основных вопросов темы
2.1 Основные понятия и определения.
2.2 Основные задачи проектирования.
2.3 Последовательность проектирования.
3. Краткое содержание основных вопросов темы
З.1 Основные понятия и определния (наименование вопроса)
Механосборочное производство, состоящее из комплекса производственных участков и вспомогательных подразделений, в котором протекают производственные процессы изготовления изделий, представляет собой сложную систему, структура и параметры которой находятся в непосредственной зависимости от сложности конструкции, номенклатуры выпускаемой продукции и характеристик производственного процесса ее изготовления.
Понятие производственный процесс в машиностроении определяется как совокупность всех действий людей и орудий производства, необходимых на данном предприятии для изготовления выпускаемых изделий.
Следовательно, производственный процесс включает в себя не только обработку деталей, их контроль, сборку и испытания, но и межоперационную транспортировку обрабатываемых деталей, передачу деталей с участка на участок внутри цеха, хранение деталей на участках обработки и сборки, на складах, обслуживание рабочих мест, заточку инструмента, ремонт оборудования и оснастки, снабжение материалами и всеми видами энергии, планирование, учет, управление производством и т.д.
Основной составляющей производственного процесса является технологический процесс, содержащий действия, непосредственно связанные с изменением формы, размеров или физико-механических свойств обрабатываемых заготовок, полуфабрикатов или деталей и их сборкой в сборочные, а также контролем соответствия их заданным техническим требованиям.
Прочие вспомогательные процессы, протекающие в цехе, должны обеспечивать бесперебойное выполнение основного технологического процесса.
Различают две формы организации производственных процессов - поточную и непоточную.
Характерным признаком поточного производства является - непрерывность перемещения заготовок, полуфабрикатов или собираемых изделий в процессе их изготовления с операции на операцию в порядке последовательности их выполнения, причем это движение осуществляется с постоянным тактом в рассматриваемый промежуток времени. Время проле-живания полуфабрикатов между операциями в таких случаях равно или кратно такту.
При непоточном производстве в процессе их изготовления находятся в движении с различной продолжительностью операций и пролеживания между ними.
Для каждого производства устанавливают программу выпуска, под которой понимают совокупность изделий установленной номенклатуры, выпускаемых в заданном объеме в год. Число изделий, выпускаемых в единицу времени (год, квартал, месяц) называют объемом выпуска.
Каждое механосборочное производство обладает определенной производственной мощностью, под которой понимают максимально возможный выпуск продукции установленной номенклатуры и количества, который может быть осуществлен за определенный период времени при установленном режиме работы. Различают действительную и проектную мощность.
Проектная мощность - это установленная в проекте строительства или реконструкции производства производственная мощность, которая должна быть достигнута при условии обеспечения производства принятыми в проекте средствами производства, кадрами и организацией производства.
Производственная мощность действующего производства не является постоянной и зависит от технического уровня работающих, уровня использования основных и оборотных фондов, сменности работы, уровня механизации и автоматизации производства и других фактов.
Изготовление изделий занимает определенное время. Календарное время изготовления изделий от начала производственного процесса до его окончания называют производственным циклом.
Движение заготовок, полуфабрикатов или изделий может осуществляться поштучно или партиями. Партией принято называть определенное число заготовок, полуфабрикатов или изделий, одновременно поступающих на рабочую позицию (место).
Для выполнения производственного процесса рабочие позиции (места) должны быть оснащены соответствующим образом. В зависимости от содержания операции и организации ее проведения на рабочей позиции (месте) могут быть расположены: технологическое оборудование, накопители с полуфабрикатами, один рабочий или группа рабочих, средства автоматической загрузки и разгрузки оборудования (роботы, манипуляторы, автоматические агрегаты загрузки), режущий и контрольно-измерительный инструмент, оснастка, средства технического обслуживания и охраны труда, элементы системы управления и др.
Исходя из организационных соображений несколько рабочих позиций (мест) объединяют, образуя производственный участок. Производственным участком называют часть объема цеха, в котором расположены рабочие позиции (места), объединенные транспортно-накопительными устройствами, средствами технического, инструментального и метрологического обслуживания, средствами управления участком и охраны труда, на котором осуществляются технологические процессы изготовления изделий определенного назначения.
Более крупной организационной единицей является производственный цех, который представляет собой производственное административно-хозяйственное обособленное подразделение. Цех включает в себя производственные участки, вспомогательные подразделения, служебные и бытовые помещения, а также помещения общественных организаций.
Вспомогательные подразделения создают для обслуживания и обеспечения беспрерывной работы производственных участков. К ним относятся: отделение по восстановлению режущего инструмента, контрольное и ремонтное отделения, отделения для приготовления и раздачи СОЖ и др.
Состав производственных участков и вспомогательных подразделений определяется конструкцией изготавливаемых изделий, технологическим процессом, программой выпуска и организацией производства.
За общую площадь цеха в технологических расчетах принимают сумму производственной и вспомогательной площадей (без служебно-бытовой площади).
В состав производственной площади включают площади, занимаемые рабочими позициями (местами), вспомогательным оборудованием, находящимся на производственных участках, проходами и проездами между оборудованием внутри производственных участков (кроме магистрального проезда).
На вспомогательных площадях размещают все оборудование и устройства вспомогательных систем, не расположенных на производственных участках, а также магистральные и пожарные проезды.
Для движения автопогрузчиков, грузовых автомобилей в цехе создают магистральные проезды шириной не менее 4 м, которые выбирают по нормам технологического проектирования.
На служебно-бытовой площади цеха размещают конторские и бытовые помещения. К конторским относят площадь, занятую административно-хозяйственными службами цеха. В ту же площадь включают и площадь конструкторских бюро, размещаемых в цехе.
Для осуществления производственных процессов в механосборочном производстве предусмотрен определенный штат работающих, которых делят на следующие категории: производственные (основные) и вспомогательные рабочие, инженерно-технические работники (ИТР), служащие, младший обслуживающий персонал (МОП).
Производственные рабочие - это работники механосборочного производства, непосредственно выполняющие операции технологического процесса по изготовлению продукции.
Вспомогательные рабочие в механосборочном производстве - это работники, не принимающие непосредственного участия в выполнении операций по изготовлению производственной программы выпуска продукции, а занятые обслуживанием технологических процессов.
Инженерно-техническими работниками называют работников, выполняющих обязанности по управлению, организации и подготовке производства, занимающих должности, для которых требуется квалификация инженера или техника.
К служащим относят работников, выполняющих в соответствии с занимаемой должностью административно-хозяйственные функции, ведущих финансирование, учет, решающие социально-бытовые и подобные вопросы.
Младший обслуживающий персонал составляют сторожа, гардеробщики, уборщики бытовых и конторских помещений.
Одним из этапов проектирования является компоновка цеха. Под компоновкой цеха понимают взаимное расположение площадей производственных участков, вспомогательных отделений, магистральных проездов и служебно-бытовых помещений на площади цеха. После проведения компоновки цеха осуществляют планировку оборудования на нем. Под планировкой цеха понимают взаимное расположение технологического и вспомогательного оборудования, а также других производственных средств и устройств на площади цеха.
Механосборочное производство обычно располагают в зданиях, имеющих один или несколько пролетов. Пролетом называют часть здания, ограниченную в продольном направлении двумя параллельными рядами колонн. Расстояние между осями колонн в продольном направлении называют шагом колонн, а в поперечном - шириной пролета. Расстояние между осями колонн в продольном и поперечном направлениях образует сетку колонн. Под высотой пролета понимают расстояние от уровня пола до нижней части несущих конструкций покрытия здания.
После разработки производственного процесса приступают к этапу планировки, во время которого производят увязку расположения рабочих позиций (мест) и вспомогательного оборудования в выбранном масштабе.
Планировку оборудования в техническом проекте выполняют в масштабе 1: 100 для малых и средних цехов, 1: 200 для больших цехов.
На планировке изображают и указывают: сечение колонн с фундаментами; магистральные проезды; наружные и внутренние стены; окна, ворота и двери, как наружные так и внутренние; месторасположение работающих; подвалы, каналы, шахты и антресоли; верстаки, рабочие столы, подставки; места для хранения инструмента; места для складывания заготовок и готовой продукции; транспортные устройства, площадки для контроля; ширину пролетов; шаг колонн; общую ширину цеха; ширину продольных и поперечных проездов; расстояние от станков до колонн, между станками и рабочими местами; нумерацию оборудования с ее расшифровкой в спецификации; название всех производственных отделений и участков.
Ввиду большого количества строительных элементов и производственного оборудования, изображаемых на планах производственных помещений, целесообразно пользоваться принятыми условными обозначениями (табл. 1.1).
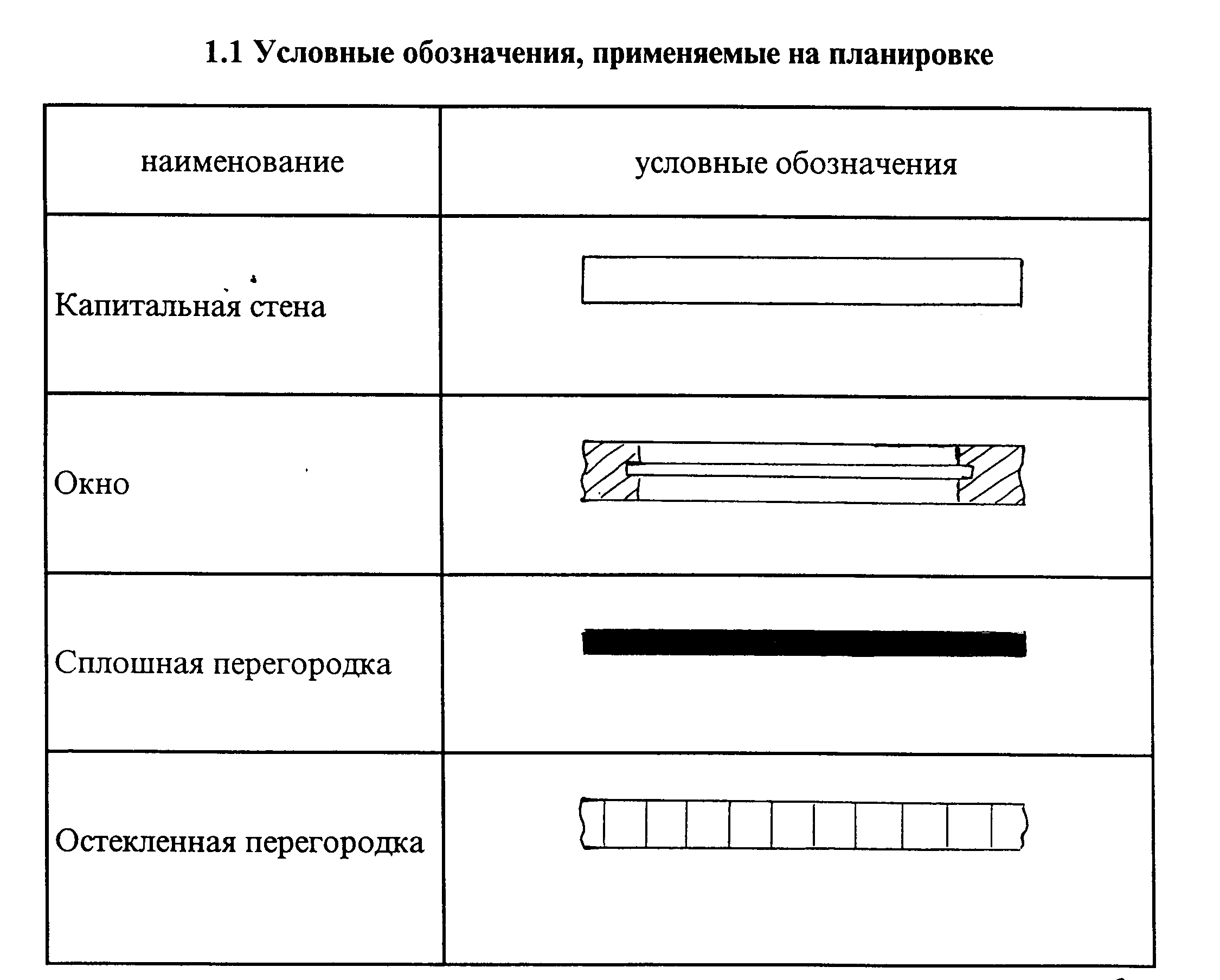
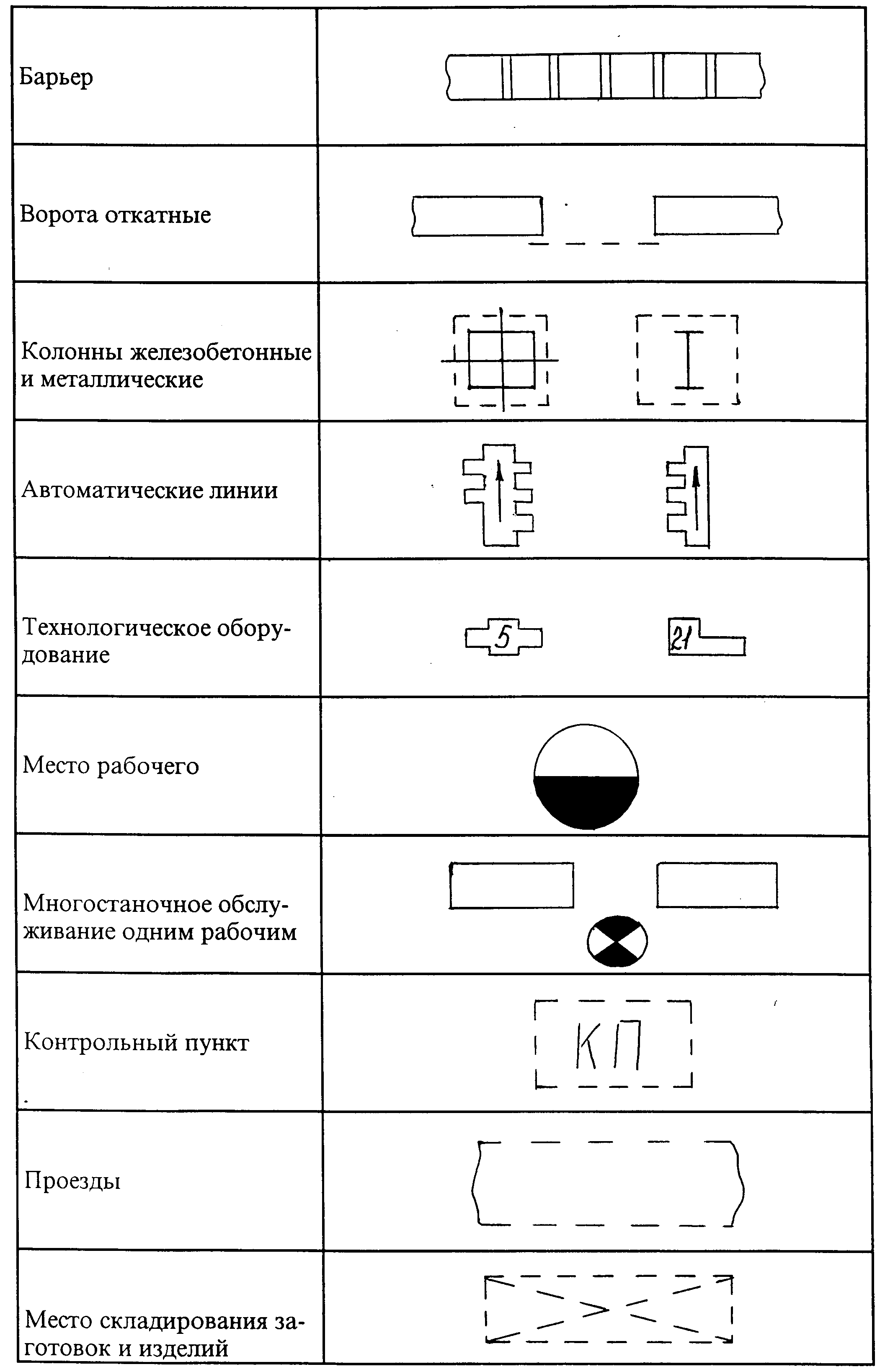
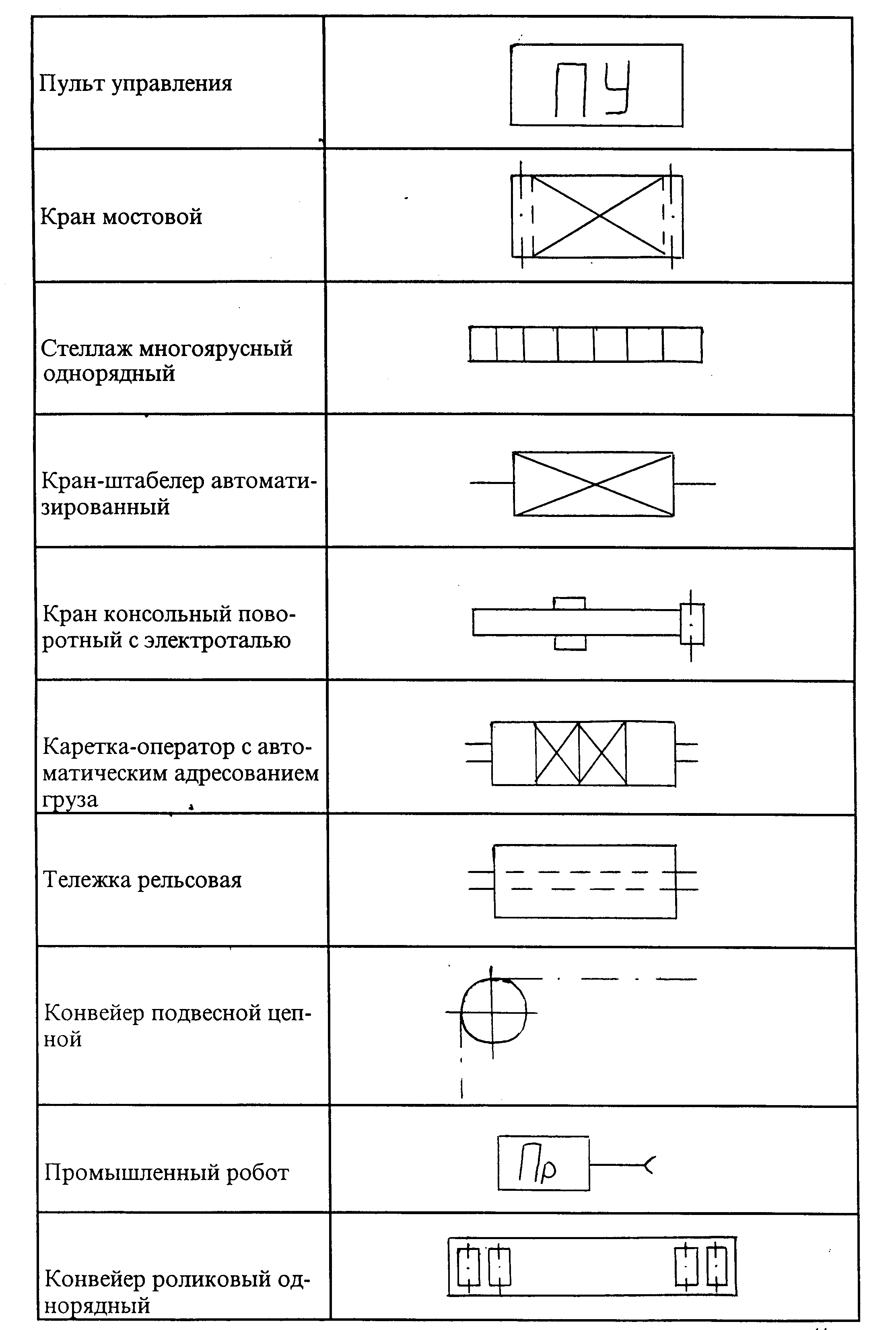
3
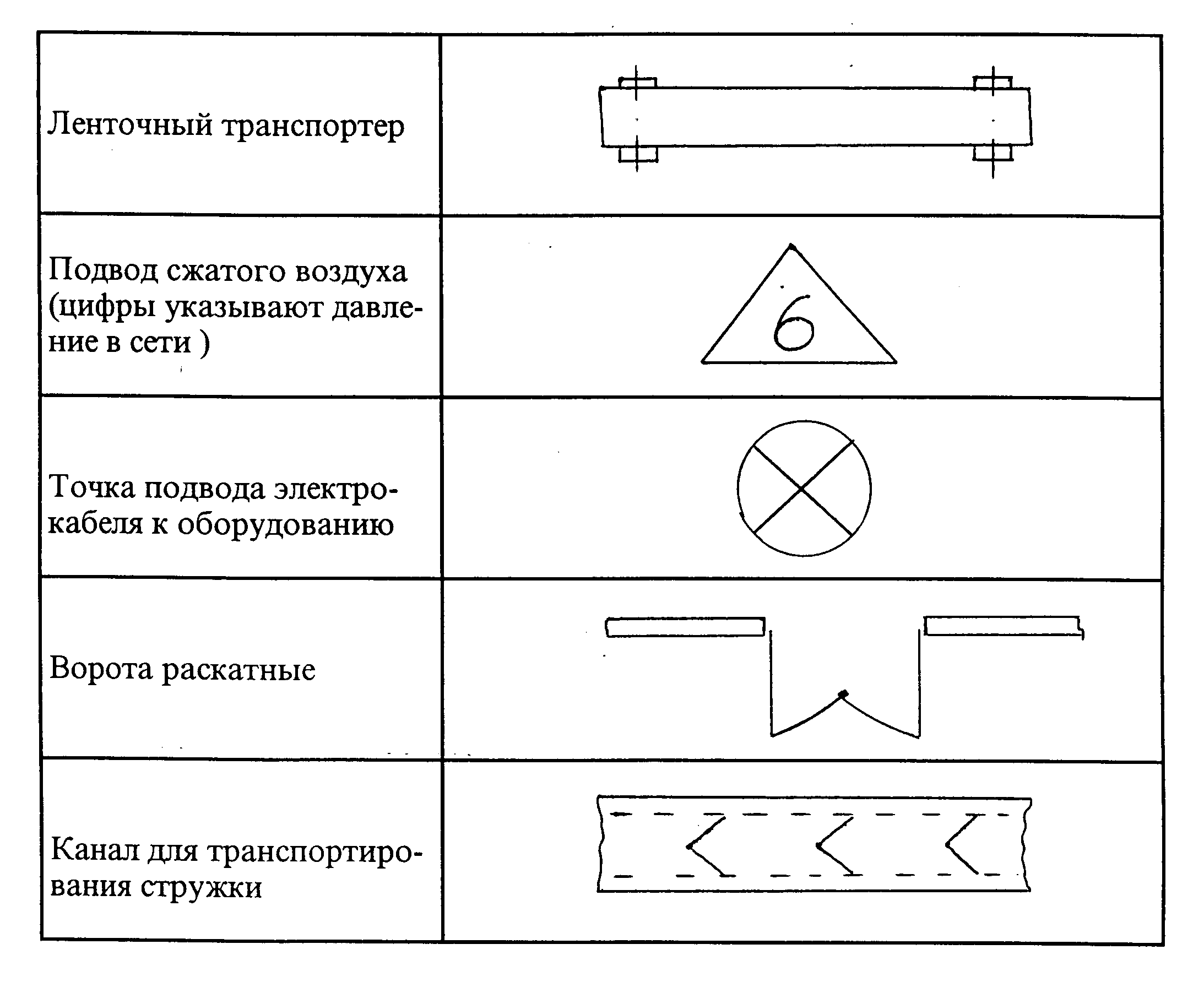
.2. Основные задачи проектировния (наименование вопроса)
Важнейшим показателем проекта является его технико-экономическая эффективность, определяемая более высоким уровнем производительности труда, которую он обеспечивает по сравнению с производительностью труда на действующих аналогичных производствах, минимальными относительными капитальными вложениями (на единицу продукции), короткими сроками их окупаемости и рентабельности производства при его эксплуатации. Для обеспечения высокой технико-экономической эффективности в проекте должен рационально быть решен ряд сложных, тесно связанных между собой технологических, экономических и организационных задач.
Для решения технологических задач необходимо: проработать вопросы технологичности изделий, спроектировать технологические процессы обработки и сборки, определить трудоемкость и станкоемкость операций, установить типаж и количество основного и вспомогательного оборудования, состав и количество работающих, нормы расхода материалов, определить площади и размеры участков и цеха, планировку оборудования и др.
Для решения экономических задач необходимо: рассчитать себестоимость и рентабельность выпуска изделий, определить удельные приведенные затраты, составить калькуляции и др.
Для решения организационных задач необходимо: выбрать принципы формирования производственных .подразделений, разработать структуру управления, научную организацию труда, документооборот, систему контроля за ходом производства и др.
При разработке нескольких вариантов проекта механосборочного производства или его частей, необходимо выбрать оптимальный.
3.3. Последовательность проектировния (наименования вопроса)
Проектирование механосборочного производства, которое представляет собой сложную динамическую систему, включает следующие последовательные этапы: структурно-функциональный, алгоритмический, параметрический и планировочный.
Структурно-функциональный этап может быть представлен в виде структурной модели цеха (участка), которая отражает состав, тип и взаимодействие элементов и функциональной модели, учитывающей свойства элементов и системы, необходимы для выполнения своего служебного назначения .
Алгоритмический этап проектирования включает в себя составление алгоритмической модели, содержащей взаимные связи между элементами в процессе производства изделий.
На параметрическом этапе проектирования производится определение количественных значений взаимосвязей между отдельными физическими параметрами системы.
На планировочном этапе решается задача размерных связей между отдельными элементами системы. Модели этого этапа аналогичны структурным, но отношения между элементами оцениваются в трехмерном пространстве.
На основании исходных данных, которые определяют из условий работы механосборочного производства и разработанных технологических процессов изготовления изделий, проектируют основные и вспомогательные системы, а затем производят пространственную увязку всего оборудования, формируя тем самым механосборочное производство изделий.
В исходных данных для проектирования должны быть указаны:
• номенклатура изделий, сборочных единиц и деталей, подлежащих изготовлению и сборке;
• годовая программа выпуска по каждому наименованию изделий и деталей;
• габаритные размеры, масса и материал изделий;
• трудоемкость и станкоемкость операций;
• типаж оборудования;
• режим работы цеха.
При проектировании цеха подлежат разработке и решению технологические, экономические и организационные задачи. Эти три типа задач должны решаться одновременно, т.к. каждое принимаемое в проекте техническое решение должно быть экономически обоснованно и осуществлено в определенных организационных формах. Решение перечисленных выше задач при проектировании ведется в определенной последовательности, вытекающей из взаимосвязанности решаемых вопросов.
В практике проектирования основные задачи решаются в последовательности указанной ниже.
Последовательность проектирования основной системы (производственных участков):
• определение количества основного, (технологического) оборудования на участках основного производства по принятому технологическому процессу ;
• выбор состава производственных участков;
• определение состава и количества оборудования на участке;
• определение алгоритма работы оборудования на участке;
• расчет производственной площади;
• разработка требований к условиям работы оборудования;
• составление заданий на проектирование нестандартного оборудования;
• компоновка производственных участков;
• планировка основного оборудования, предварительное определение числа работающих.
Проектирование каждой вспомогательной системы - складской, транспортной, инструментообеспечения, ремонтного и технического обслуживания, контроля качества изделий, а также системы охраны труда осуществляют в той же последовательности, что и основной системы.
На этапе синтезирования производственной системы производится:
• определение обшей площади цеха и его габаритов;
• уточнение компоновки цеха;
• уточнение планировки оборудования;
• уточнение состава и количества работающих;
• определение технико-экономических показателей;
• выбор оптимального варианта проекта.
Блок-схема последовательности проектирования представлена на рис. 1.1.




Исходные
данные
Основная
система
Вспомога-
тельные
системы
Производ-
ственная
система



Рис. 1.1 Последовательность проектирования
Контрольные вопросы:
1.Назовите основные этапы производственного процесса.
2.Назовите формы организации производственных процессов и дайте им краткую характеристику.
3. Дайте определения действительной и проектной мощностей механосборочного цеха.
4. Что называется рабочей позицией, производственным участком, цехом?
5. Чем отличается компоновка цеха от планировки?
6. Назовите состав и содержание задач, решаемых при проектировании механосборочного цеха.
7. Назовите основные этапы процесса проектирования механосборочного цеха.
ТЕМА 2. СОСТАВ И КОЛИЧЕСТВО ОСНОВНОГО ТЕХНОЛОГИЧЕСКОГО ОБОРУДОВАНИЯ
1. Цели и задачи изучения темы:
- значение технологических характеристик типов машиностроительного производства и методов их организации;
- знание основных требований к технологическому оборудованию и принципов выбора состава основного технологического оборудования для современного механосборочного производства;
- знание методов проектирования механосборочных цехов;
- умение определять количество основного технологического оборудования при проектировании производственных участков и линий механосборочных цехов для различных форм их организации.
2. Перечень основных вопросов темы
2.1 Основные положения по выбору состава технологического оборудования.
2.2 Производственная программа и методы проектирования цеха.
2.3 Методы определения трудоемкости и станкоемкости обработки и сборки.
2.4 Режим работы и фонды времени.
2.5 Расчет количества основного технологического оборудования для поточного производства.
2.6 Расчет количества основного технологического оборудования и рабочих мест при непоточном производстве.
3. Краткое содержание основных вопросов темы
3.1 Основные положения по выбору состава технологического оборудования
(наименование вопроса)
Для современного механосборочного производства характерен высокий уровень автоматизации производственных процессов, поэтому технологическое оборудование должно обеспечивать не только автоматизацию обработки или сборки, но и стыковаться с оборудованием и технологическими средствами, объединяющими отдельные виды технологического оборудования в единый автоматизированный производственный процесс.
Так, например, станки с ЧПУ для встраивания в состав ГПС должны стыковаться с промышленными роботами для их автоматической загрузки, системы ЧПУ должны иметь вход для стыковки с ЭВМ высшего уровня и для передачи в их запоминающее устройство заранее разработанных управляющих программ, иметь системы диагностики и т.д.
Характер и состав технологического оборудования во многом определяется типом производства. Тип производства является классификационной категорией в зависимости от широты номенклатуры, регулярности, стабильности и объема выпуска изделий. Различают три типа производства: единичное, серийное и массовое.
Единичное производство характеризуется широкой номенклатурой изготавливаемых изделий и малым объемом выпуска. Это, как правило, опытное производство изделий, изготовление уникальных машин.
Серийное производство характеризуется ограниченной номенклатурой изделий, изготавливаемых периодически повторяющимися партиями и сравнительно большим объемом выпуска. В условиях серийного производства выпускают 75-80% изделий. Характерна тенденция увеличения относительной доли серийного производства. Серийное производство в зависимости от числа изделий в партии или серии и их повторяемости условно делят на мелко-, средне- и крупносерийное. Продукцией серийного производства являются станки, компрессоры, специальные машины- и другие изделия, выпускаемые, как правило, в различных модификациях на общей базе.
Массовое производство характеризуется узкой номенклатурой и большим объемом выпуска изделий, непрерывно изготавливаемых в течении продолжительного времени. Продукцией массового производства в машиностроении являются автомобили, тракторы, холодильники и другие изделия, выпускаемые в больших количествах.
Для определения типа производства пользуются коэффициентом закрепления операций:
Кз.о.= nоп/М
где –nоп число различных технологических операций, выполняемых или подлежащих выполнению на участке, линии или цехе в течении месяца, М - число мест рабочих соответственно участка, линии или цеха.
ГОСТ 3.1108-74 рекомендует следующие значения коэффициентов закрепления операций в зависимости от типа производства: для единичного производства - свыше 40; для мелкосерийного производства - свыше 20 до 40 включительно; для среднесерийного производства - свыше 10 до 20 включительно; для крупносерийного производства - свыше 1 до 10 включительно; для массового производства - 1.
Таким образом, тип производства с технологической точки зрения характеризуется средним числом операций, выполняемым на одном рабочем месте, а это в свою очередь определяет степень специализации и особенности используемого оборудования . В пределах одного цеха на разных участках могут быть различные типы производства. Это во многом зависит от продолжительности операций технологического процесса деталей или изделий изготовляемых на участке. Так, например, изготовление базовых деталей станка может быть организовано по принципу крупносерийного производства, в то время как на участках для изготовления деталей типа тел вращения (валов, зубчатых колес и др.) может быть среднесерийное или даже мелкосерийное производство. Это связано с тем, что трудоемкость обработки базовых деталей в десятки раз выше трудоемкости изготовления деталей типа тел вращения.
Необходимо иметь в виду то, что деление на типы производства условно, а также то, что при широком развитии ГПС будут постепенно стираться существенные различия в оборудовании производства различного типа. Даже массовое производство в настоящее время становится быстросменным, что требует высокопроизводительного оборудования, которое может быстро переналаживаться на изготовлении других изделий.
При выборе состава технологического оборудования современных цехов механосборочного производства необходимо учитывать следующие основные тенденции в технологии производства машин; интенсификацию технологических процессов; повышение качества обработки деталей и сборки машин; комплексную автоматизацию производственных процессов; повышение производительности труда и рентабельности производства.
Интенсификация производственных процессов заключается в использовании параллельных и параллельно-последовательных схем обработки и сборки, в создании и применении оборудования, реализующего многоинструментальную обработку в одной или нескольких позициях одновременно. Наиболее широкое применение интенсивные технологии нашли в массовом и крупносерийном производстве, где широко используют агрегатные станки и автоматические линии, скомпонованные из них. Так как современное массовое производство характеризуется быстросменностью, агрегатные станки и автоматические линии должны обладать гибкостью к изменению определенных конструктивных параметров изделий.
Традиционные одно- и многошпиндельные автоматы, существенным недостатком которых была сложность и высокая трудоемкость переналадки, в настоящее время оснащают системой ЧПУ, что делает эффективным их применение в условиях не только гибкого массового, но и серийного производства. При этом в токарных станках с ЧПУ предусматривают инструментальные шпиндели для обработки пазов, внецентренных отверстий, лысок и других поверхностей. Это позволяет практически полностью изготавливать деталь на одном станке.
Эффективность обработки повышают интенсификацией режимов резания за счет применения высокопроизводительных режущих материалов. Повышение точности обработки обеспечивают применением чистового точения, фрезерования и растачивания инструментами из сверх твердых материалов.
В условиях серийного производства возможности использования интенсивных технологий на основе параллельной или параллельно-последовательной концентрации технологических переходов были ограничены значительными потерями на переналадку. Широкое использование современных станков с ЧПУ, оснащенных инструментальными магазинами, обеспечивает значительную интенсификацию процесса обработки благодаря резкому сокращению вспомогательного времени (до 3-4 раз).
Создание многоинструментальных станков с ЧПУ для параллельной обработки, например, токарных станков, оснащенных головками, позволяет вести обработку валов, фланцев и других изделий с пазами, лысками, поперечными и внецентренными отверстиями. Широкие технологические возможности подобных станков обеспечивают их эффективность в мелко-, средне- и крупносерийном производстве. Многошпиндельную обработку на специализированных агрегатных станках с успехов применяют в массовом и крупносерийном производстве. При этом ведут одновременную обработку нескольких заготовок (параллельная схема), либо последовательную обработку нескольких поверхностей одной заготовки.
Основным критерием при выборе состава оборудования цеха являются минимальные приведенные затраты на годовой выпуск:
З=С+Ен*К,
где: С - себестоимость годового выпуска; Ен - нормативный коэффициент эффективности капитальных вложений; К - капитальные вложения, рассчитанные на годовой объем продукции, которые включают стоимость оборудования, инструмента, знаний, затраты на незавершенное производство, жилищное и культурно-бытовое строительство.
Развитие автоматизации производства, а также современные тенденции в машиностроении, характеризующиеся увеличением удельного веса многономенклатурного производства и сокращением продолжительности выпуска изделий в условиях массового производства, обусловили создание и широкое внедрение гибких производственных систем (ГПС).
ГПС - это совокупность в разных сочетаниях оборудования с ЧПУ, роботизированных технологических комплексов, гибких производственных модулей, отдельных единиц технологического оборудования и систем обеспечения их функционирования в автоматическом режиме в течении заданного промежутка времени, обладающая свойством автоматизированной переналадки при производстве изделий произвольной номенклатуры в установленных пределах знаний их характеристик.
По организационным признакам выделяют следующие ГПС; гибкая автоматизированная линия (ГАЛ), гибкий автоматизированный участок (ГАУ) и гибкий автоматизированный цех (ГАЦ).
Производственная структура ГПС включает в себя два основных комплекса: производственный и управляющий вычислительный комплекс. При построении комплексов и их составных частей используют системный подход; каждая составная часть рассматривается как система, состоящая
из технических средств автоматизации и механизации физического труда и управленческих функций с определенным порядком их взаимодействия.
В свою очередь производственный комплекс включает в себя производственную систему и систему обеспечивания функционирования производства. Система обеспечивания функционирования ГПС - это совокупность взаимосвязанных систем, обеспечивающих технологическую подготовку производства изделий, управление ГПС с помощью ЭВМ, хранение и автоматическое перемещение объектов производства и технологической оснастки.
В общем случае в состав системы обеспечения функционирования входят:
- автоматизированная транспортно-складская система;
- автоматизированная система инструментального обеспечения;
- автоматизированная система управления технологическими процессами;
- система автоматизированного контроля;
- автоматизированная система удаления отходов;
- автоматизированная система проектирования;
- автоматизированная система управления ГПС и др.
В соответствии с двумя формами специализации участков механообработки- технологической и предметной, возможны два направления создания ГПС.
Первое направление охватывает автоматизацию отдельных технологических операций и создание операционных ГПС (токарных, фрезерных, шлифовальных).
Второе направление характеризуется комплексной автоматизацией технологических процессов обработки деталей определенного класса, что в условиях быстрой переналадки обеспечивает значительно большую эффективность по сравнению с эффективностью операционных ГПС. Организационной основой ГПС является групповая технология, обеспечивающая минимальные простои оборудования из-за переналадки при целевой подетальной специализации участков и цехов. В этом случае на участке выполняются технологически однородные операции обработки одного изделия или нескольких различных изделий.
Для этого предварительно производят классификацию всех деталей по конструктивно-технологическим признакам. Затем детали объединяют в группы по признаку общности применяемого оборудования, наладок и инструментальной оснастки. После этого разрабатывают групповые технологические процессы, позволяющие выполнять обработку на участке любых деталей группы по общему технологическому процессу.
В соответствии с принципами групповой технологии создают ГПС для изготовления:
- деталей типа тел вращения (валы, фланцы, втулки, зубчатые колеса и др.);
- корпусных деталей и пространственных кронштейнов и рычагов;
- плоскостных деталей (планки, крышки, панели и др.)
- смешанной группы деталей, состоящих из деталей, входящих в перечисленные выше группы.
Преимущества ГПС наиболее полно реализуются, если на автоматизированном участке или линии осуществляется полное изготовление деталей. Однако ввиду отсутствия пока ГПМ для некоторых технологических операций, а также необходимости использования имеющегося оборудования, допускается в обоснованных случаях выполнять отдельные операции на других участках с более низким уровнем автоматизации.
В этом случае ГПС включается в качестве составной части участка, цеха имеющий менее высокий уровень автоматизации для обеспечения замкнутого цикла изготовления.
В настоящее время в механообработке применяют три типа решений ГПС:
1.создание гибких участков и линий из работающих на заводе и серийно выпускаемых станков с ЧПУ. При этом участки дополняют автоматизированными транспортными системами, складами. Станки оснащаются устройствами автоматической загрузки;
2.создание линий и участков на базе типовых решений, разработанных станкостроительными НИИ и КБ, и серийно выпускаемых ГПМ;
3.создание ГПС на базе специальных разработок с использованием новых прогрессивных решений и оборудования, спроектированного по агрегатному принципу (многопозиционных многоцелевых станков, ГПМ с многошпиндельными головками и др.).
ГПС занимает промежуточное положение между станками с ЧПУ, обладающими высокой гибкостью и относительно маленькой производительностью, и автоматическими линиями массового производства, высокопроизводительными, но значительно менее гибкими.
Основными источниками повышения эффективности ГПС являются, повышение машинного времени за счет автоматической смены заготовок и сокращения времени переналадки, повышение коэффициента сменности до 2,5-3, уменьшения вложений в оборотные средства путем сокращения партий запуска и производственного цикла.
По этому при выборе состава ГПС и степени автоматизации транспортной системы, системы инструментообеспечивания и контроля необходимо оценивать допустимое при этом возростание стоимости производственной системы по сравнению со стоимостью при использовании автономных станков с ЧПУ. Ориентировочно допустимое возростание стоимости ГПС по сравнению со стоимостью автономных станков К цв.ст-должно быть компенсировано увеличением машинного времени (К цв.м.в.), увеличением стоимости (К цв.см. ) и уменьшением вложений в оборотные средства (К ум.о.с.)
Кцв.ст.=(К цв. м.в.*К цв.см)/К ум.о.с.
При выборе состава основного оборудования сборочных цехов и сборочных отделений необходимо учитывать изложенные выше принципы, обеспечивая наименьшие приведенные затраты на годовой выпуск.
В состав основного сборочного оборудования включают оборудование для выполнения технологического процесса сборки: сборочные стенды, верстаки для сварки, столы сборщиков, металлорежущие станки для дополнительной обработки при сборке, прессы, моечные машины, испытательные и контрольные стенды, сборочные конвейеры, автоматические и автоматизированные сборочные установки и линии и т.д.
В массовом и крупносерийном производстве сборку выполняют с использованием автоматических и автоматизированных установок и линий, сборочных конвейеров, средств механизации и автоматизации технологических переходов сборки на отдельных позициях.
В условиях серийного, мелкосерийного и единичного производства используются сборочные стенды, верстаки, оснащенные приспособлениями и механизированным инструментом в соответствии с выполняемой работой,
Прогресс в области роботизации открывает реальные перспективы использования в условиях серийного производства автоматизированных сборочных мест, оборудованных одним или несколькими сборочными роботами с магазином сменных схватов и их автоматической сменой. На их основе создают ГПС сборки.
3.2. Производственная программа выпуска изделий и методы проектирования цеха
(наименование вопроса)
Производственную программу выпуска цеха определяют, исходя из производственной программы завода, с учетом установленного процента запасных частей.
В зависимости от типа производства и этапа проектирования производственная программа выпуска может быть точной, приведенной и условной. В соответствии со способом задания применяют методы проектирования по точной, приведенной и условной программе.
Производственная программа выпуска, обеспеченная всеми чертами и техническими условиями на изготовление изделий и составленная по определенной форме в виде ведомости, включающей полный перечень деталей и сборочных единиц, подлежащих обработке или сборке в данном цехе, с указанием их количества, массы, вида заготовки и материала - называется точной программой.
Метод проектирования по точной программе предусматривает разработку технологических процессов обработки и сборки, выбор оптимального оборудования и расчет технически обоснованных норм времени на все детали и сборочные единицы, входящие в производственную программу. На основании этих расчетов определяют количество потребного оборудования, загрузку его по времени, а также составляют заявочную спецификацию на оборудование.
Точная программа выпуска обязательна при проектировании цехов массового и крупносерийного производства, требующих большой точности всех технологических расчетов.
По приведенной программе проектируют цехи средне- и мелкосерийного производства. Это объясняется тем, что при большой номенклатуре изделий нецелесообразно разрабатывать подробные технологические процессы на каждое изделие, так как эта работа связана с очень большим объемом технологических разработок и расчетов, и для его сокращения реальную многономенклатурную программу заменяют приведенной, выраженной ограниченным числом представителей и эквивалентной по трудоемкости фактической многономенклатурной программе. Таким образом, основной задачей при проектировании по приведенной программе является определение с достаточной степенью точности трудоемкости годового объема выпуска без проведения подробных технологических расчетов по всей номенклатуре изделий.
С этой целью все изделия, подлежащие изготовлению, разбивают на группы по конструктивным и технологическим признакам, и в каждой группе выбирают изделие (деталь или сборочную единицу) - представитель, по которой далее ведут все расчеты. На указанные представители разрабатывают подробные пооперационные технологические процессы обработки или сборки и путем технологического нормирования определяют трудоемкость их изготовления.
В качестве представителей выбирают детали или сборочные единицы, наиболее характерные для данной группы. Рекомендуется, чтобы масса Мпр и годовой выпуск Ипр представителя удовлетворяли следующим неравенствам:
0,5m max
0,1N max< N пр< 10 N min,
где m max, m min, N max, N min - максимальные и минимальные массы и годовые объемы выпуска остальных изделий, входящих в данную группу.
Формирование групп и выбор из них представителей является сложным и ответственным этапом проектирования, так как точность дальнейших технологических расчетов по приведенному объему выпуска в значительной степени зависит от выбора представителя. В практике проектирования любой объект производства, входящий в группу, может быть приведен по трудоемкости к представителю с учетом различия в массе, программе выпуска, сложности обработки или сборки и других параметрах.
Общий коэффициент приведения;
Кпр=К1*К2*К3*…*Кn,
Где К1 - коэффициент приведения по массе ;
К2- коэффициент приведения по серийности ;
К3 - коэффициент приведения по сложности ;
Кn-коэффициент приведения, другие особенности объекта, напри мер, различие в точности изделий и изделия - представителя, наличие комплектующих поставок по кооперации узлов или агрегатов и др.
Коэффициент, учитывающий различия в массе для технологически однородных деталей:
К1=√(m i/m пр),
где : m i и m пр - соответственно масса рассматриваемой детали группы и масса детали - представителя.
Эта формула выражает соотношение площадей обрабатываемых поверхностей рассматриваемой детали группы и детали - представителя.
Коэффициент приведения, учитывающий различия в массе собираемых изделий, определяют по формулам:
К1=( m i / m пр) или К1=m i / m пр,
где : m i и m пр соответственно масса собираемого изделия группы и изделия - представителя.
Первая формула пригодна при большом объеме пригоночных работ, вторая - при малом.
Коэффициент приведения по серийности учитывает изменение трудоемкости обработки или сборки при изменении программы выпуска:
К2=( N пр / Ni),
где : N пр и Ni - программа выпуска соответственно изделия - представителя и "приводимого" изделия показатель степени; = 0,15 - для объектов легкого и среднего машиностроения и = 0,2 для объектов тяжелого машиностроения.
Коэффициент приведения по сложности К3 учитывает влияние технологичности конструкции на станкоемкость обработки или трудоемкость сборки. Так, например, увеличение точности обработки и повышение требований к шероховатости поверхности ведут к увеличению станкоемкости обработки. Трудоемкость сборки, например, существенно зависит от числа сопрягаемых элементов конструкции изделия, точности сопряжения и др.
В общем виде коэффициент приведения по сложности можно представить в виде произведения коэффициентов, учитывающих связи между конструктивными факторами и трудоемкостью приводимых изделий:
К3=Р1* Р2*…*Рn
где : Р1, Р2…Рn - коэффициенты, учитывающие различия соответствующих технических параметров в рассматриваемом изделии и изделии - представителя; ,,...- показатели, отражающие степень влияния соответствующих параметров на трудоемкость обработки или сборки.
Так, например, для однородных деталей группы наиболее существенными параметрами, определяющими сложность, а соответственно и трудоемкость изготовления, будут точность и параметр шероховатости поверхности обработки. Для этого случая:
К3=(Ктi / Кт пр)*(Rai / Ra пр),
где : Ктi, Кт пр - средние значения квалитета точности приводимой детали и детали-представителя; Rai , Ra пр - среднее значение параметра Ra-шероховатости приводимой детали - представителя.
Для определения значений рекомендуются следующие нормативы:
средний квалитет 6 7 8 11 12 13
(Кт)………......... 1,3 1,2 1,1 1,0 0,9 0,8
Значение ( Ra) при обработке резанием определяют по следующим нормативам:
R .............. 20 10 5 2,5 1,25 0,63
(Ra) ......... 0,95 0,95 1,0 1,1 1,2 1,4
Произведение всех коэффициентов приведения даст общее значение коэффициента приведения для рассматриваемой детали, сборочной единицы или изделия. Приведенная программа для каждого изделия определяется произведением заданной программы выпуска на общий коэффициент приведения. В результате этого вместо фактической многономенклатурной программы получают эквивалентную ей по трудоемкости приведенную программу, выраженную ограниченным числом изделий - представителей.
Проектирование по условной программе применяют, когда невозможно точно определить номенклатуру и технические характеристики будущих машин (опытное, единичное производство). В этом случае программу задают условным изделием, близким по характеристике к изделию, планируемому к изготовлению в данном цехе.
Метод проектирования по условной программе очень близок к методу проектирования по приведенной программе, с той лишь разницей, что изделие - представитель является условным. По условному изделию определяют трудоемкость обработки и сборки и выполняются все последующие расчеты.
3.3. Методы определения трудоемкости и станкоемкости обработки и сборки
(наименование вопроса)
При проектировании цеха, участка наряду с характеристикой и номенклатурой выпускаемых изделий необходимо иметь достоверные данные о трудоемкости изделия. Трудоемкость изделия называется время, затрачиваемое на его изготовление и выраженное в человеко-часах ( Т чел-час). Расчетная трудоемкость включает в себя все нормируемое по техпроцессу время обработки на станках и ручных операциях, причем при многостаночном обслуживании суммарное время обработки на станках, обслуживаемых одним рабочим, для определения трудоемкости делят на число обслуживаемых станков.
При расчете количества оборудования необходимо иметь данные о станкоемкости изделия, т.е. о времени, затраченном на изготовление изделия и выраженном в станко - часах работы оборудования (Тст.ч.).
Ориентировочно связь между трудоемкостью и станкоемкостью выражается через значение коэффициента многостаночного обслуживания:
2>