План-конспект лекций по курсу: " Проектирование механосборочных цехов и заводов для студентов спец. 1201 "Технология машиностроения" Составители: Панчишин В. И., доц. Клепиков В. В., проф
Вид материала | План-конспект |
- Квалификационные тесты по дерматовенерологии Москва, 2267.11kb.
- Конспект лекций по теме: «Материаловедение» для специальности 120100 "Технология, 5022.76kb.
- Конспект лекций по теме: «Материаловедение» для специальности 120100 "Технология, 104.18kb.
- Программа курса " история мировой культуры" для студентов исторического отделения, 150.41kb.
- План подготовки электронной учебно-методической литературы на 2008 год план мф по подготовке, 285.38kb.
- Конспект лекций по курсу технология лекаственных форм и галеновых препаратов для студентов, 1506.84kb.
- Составители: доц., к м. н. Т. В. Моторкина, проф., д м. н. Св. Дмитриенко, проф.,, 646.33kb.
- Дополнительная программа кандидатского экзамена по специальности 08. 00. 13 «Математические, 276.2kb.
- Методические указания к лабораторной работе по курсу "Металорежущие станки" для студентов, 275.32kb.
- Конспект лекций бурлачков в. К., д э. н., проф. Москва, 1213.67kb.
ТЕМА 4. ОПРЕДЕЛЕНИЕ СОСТАВА И ЧИСЛА РАБОТАЮЩИХ
1. Цели и задачи изучения темы:
- знание состава работающих механосборочных цехов и выполняемых ими функций;
- знание основных путей уменьшения численности работающих в механосборочном производстве;
- умение определять состав и число работающих при проектировании производственных участков и линий механосборочных цехов для различных форм их организации;
2. Перечень основных вопросов темы
2.1. Определение числа производственных рабочих.
2.2. Многостаночное обслуживание.
2.3. Определение числа вспомогательных рабочих.
2.4. Определение числа ИТР, служащих и младшего обслуживающего персонала.
3. Краткое содержание основных вопросов темы
Состав и число работающих механических и сборочных цехов определяются характером производственного процесса, степенью его автоматизации, уровнем кооперации вспомогательных служб, структурой и степенью автоматизации системы управления производством.
Широкое использование автоматических линий в крупносерийном и массовом 'производстве, увеличение удельного веса станков с ЧПУ и ГПС в серийном производстве приводят к уменьшению удельного веса производственных рабочих в составе работающих механосборочных цехов. Вместе с этим возрастает удельный вес инженерно-технических работников и вспомогательных рабочих в связи с усложнением оборудования. Однако широкое использование средств вычислительной техники и автоматизированных систем управления, призванных повысить производительность инженерного труда, и внедрение автоматизированных систем технической диагностики современного оборудования, облегчающего его обслуживание, обеспечивают сокращение численности всех работающих.
Создание специализированных складов, централизованных ремонтных и инструментальных служб способствует уменьшению численности вспомогательных рабочих. Численность служащих (счетно-конторского персонала) уменьшают благодаря внедрению автоматизированных систем учета продукции на всех этапах ее создания и выполнения расчета заработной платы работающих на ЭВМ.
3.1. Определение числа производственных рабочих (наименование вопроса)
К производственным рабочим механических и сборочных цехов относят станочников и наладчиков оборудования, слесарей для выполнения ручных и механизированных операций обработки, пригонки и сборки, мойщиков деталей и других рабочих, непосредственно занятых выполнением операций технологического процесса обработки деталей и сборки машин.
Число производственных рабочих, непосредственно занятых выполнением операций технологического процесса, определяется по стан-коемкости или трудоемкости выполняемого объема работ.
Число станочников при укрупненных расчетах определяется по станкоемкости годового объема работ или по принятому числу станков цеха (участка). В первом случае:
Рст=Т∑/(Фр*Км),
где: Т∑- суммарная станкоемкость годового объема работ изготовления деталей на станках данного типа, на участке или в цехе в станко-часах;
Км - коэффициент многостаночного обслуживания - среднее число
станков, обслуживаемых одним рабочим.
Численность слесарей на операциях разметки, шабрения, ручного удаления заусенцев и острых кромок, а также сборщиков определяется по формуле;
Р=Т/Фр,
где:Т - трудоемкость соответствующего вида работ в человеко-часах;
Фр- эффективный годовой фонд времени рабочего.
Коэффициент Км зависит от вида оборудования. Для универсальных станков, как правило, Км=1 . Исключение составляют тяжелые токарные, токароно-карусельные станки, предназначенные для изготовления деталей большого размера, где Км = 0,33...0,5. Для прутковых токарных и токарно-револьверных автоматов Км= 3...8; для многошпиндельных п/автоматов
Км = 1...4; для зубообрабатывающих п/автоматов Км= 2...4; для агрегатно-сверлильных станков, агрегатно-расточных станков Км= 1...3; для станков с программным управлением Км= 2...3.
При определении числа производственных рабочих цеха пользуются усредненными значениями Км, полученные на основе анализа действующих цехов:
- для мелкосерийного и единичного производства Км= 1,1... 1,35;
- для серийного Км= 1,3...1,5;
Средний коэффициент многостаночного обслуживания по цеху определяется по формуле:
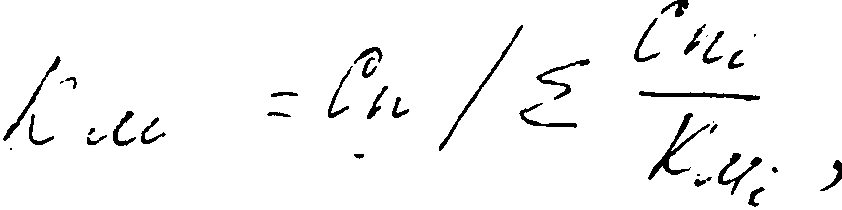
где: Сn- - принятое число станков цеха;
Сni и Kмi - соответственно число станков цеха i-ой группы и число стан-
ков данной группы, обслуживаемых одним рабочим, причем
∑Сni=Cn
Число станочников можно определить по числу станков цеха
или участка:
Рст=(Сn*Фо*Кз*Ки)/(Фр*Км),
где: Фо - эффективный годовой фонд времени работы оборудования;
Кз и Ки- коэффициенты соответственно загрузки и использования оборудования.
При укрупненных расчетах для единичного, мелко- и среднесерийного производства следует принимать Кз*Ки =0,85, для крупносерийного и массового производства Кз*Ки =0,8.
Число сборщиков по числу рабочих мест Мсб определяется по формуле:
Рсб=(Мсб*Фр.м.*Ки*П)/Фр,
где: Фр.м. - эффективный годовой фонд времени рабочего места;
П - плотность работы (среднее число рабочих, одновременно работающих на одном рабочем месте). Для сборки Ки = 0,8.
При поточной сборке необходимо предусмотреть до 5% "скользящих" рабочих (для замены временно отсутствующих) по отношению к общему числу производственных рабочих.
В условиях крупносерийного и массового производства для обслуживания станков в составе производственных рабочих предусматривают наладчиков, число которых определяется по нормам обслуживания, установленным для каждого типа оборудования.
Так, например, в зависимости от точности и сложности обработки один наладчик обслуживает: токарных 11-18; агрегатно-сверлильных 5-12;
универсально-шлифовальных 8-18; токарных с ЧПУ 4-10; сверлильных и фрезерных с ЧПУ 8-16; многоцелевых станков и РТК 3-6; сборочных автоматов и полуавтоматов 5-8; сборочных ГПМ 4-6.
В условиях единичного, мелко- и среднесерийного производства использовать наладчиков на универсальном оборудовании не рекомендуется. Здесь, как правило, рабочие имеют высокую квалификацию.
В автоматизированном производстве к числу производственных рабочих относят операторов и наладчиков автоматических линий и операторов наладчиков ГПМ. Для установки заготовок и снятия обработанных деталей для обслуживания одной автоматической линии механической обработки принимают одного или двух операторов в зависимости от уровня ее обслуживания.
Число наладчиков автоматических и сборочных линий определяют по нормам обслуживания в зависимости от числа позиций автоматической линии. На автоматических линиях механической обработки один наладчик в зависимости от сложности наладки (числа инструментов и достигаемого квалитета) обслуживает 3-10 позиций автоматической линии. Меньшие значения норм принимают при точности обработки, соответствующей 6-7-му квалитетам, и применении специального инструмента. Большие значения принимают для линий, состоящих из универсальных агрегатных станков с применением простой оснастки и центрового инструмента.
Для автоматических сборочных линий нормы обслуживания позиций одним наладчиком, установлены в зависимости от сложности применяемого оборудования и составляет 6-12 позиций.
Меньшие значения принимают для линий, состоящих из полуавтоматов с применением ПР, большие - для линий с применением механизированного сборочного инструмента.
Число операторов-наладчиков ГПС рассчитывают по нормам обслуживания в зависимости от числа ГПМ в их составе. Один оператор-наладчик обслуживает следующее число ГПМ: токарных 3-4, сверлильно-фрезерно-расточных 2-3, шлифовальных 2-3, зубообрабатывающих 3-4, сборочных 2-3. Меньшие значения даны при пяти ГШПМ в составе ГПС, большие - при ГПМ более пяти.
3.2. Многостаночное обслуживание (наименование вопроса)
При детальных расчетах число производственных рабочих-станочников уточняют с учетом размещения оборудования и анализа условий многостаночного обслуживания. Такой анализ проводят на основе разработанных планировок.
Основное условие для использования многостаночного обслуживания заключается в том, чтобы за время автоматической работы одного станка рабочий смог выполнить работу по обслуживанию других станков,
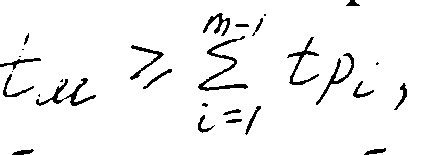
где tм- время работы станка без участия рабочего, когда рабочий свободен от обслуживания станка и активного наблюдения за его работой;
∑ti - суммарное время обслуживания и активного наблюдения за работой других станков с учетом времени на переход рабочего
от одного станка к другому.
бслуживании станков-дублеров, выполняющих одинаковую операцию, число станков, обслуживаемых одним рабочим, /тг = / У. В этом случае несколько станков, обслуживаемых одним рабочим, составляют зону обслуживания.
Циклограмма работы станочника при обслуживании станков-дублеров показана на рис.4.1.
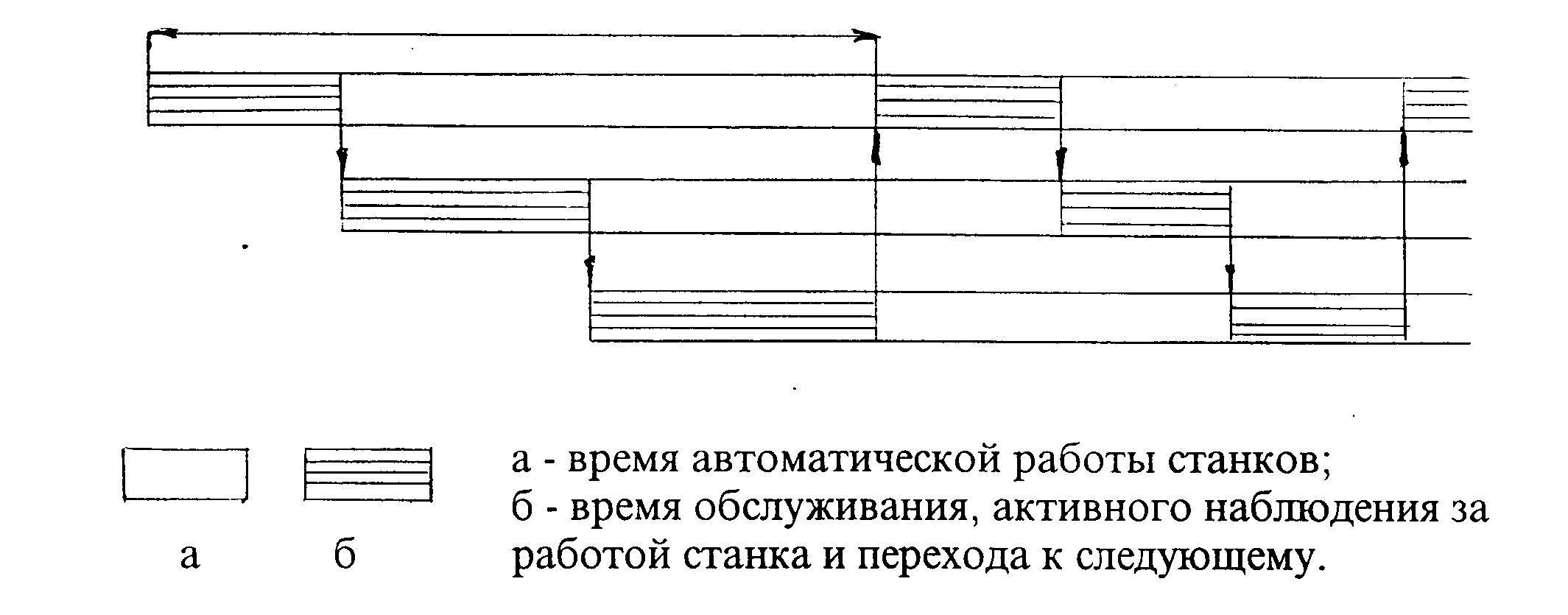
1. Цели и задачи изучения темы:
- знание состава работающих механосборочных цехов и выполняемых ими функций;
- знание основных путей уменьшения численности работающих в механосборочном производстве;
- умение определять состав и число работающих при проектировании производственных участков и линий механосборочных цехов для различных форм их организации;
2. Перечень основных вопросов темы
2.1. Определение числа производственных рабочих.
2.2. Многостаночное обслуживание.
2.3. Определение числа вспомогательных рабочих.
2.4. Определение числа ИТР, служащих и младшего обслуживающего персонала.
3. Краткое содержание основных вопросов темы
Состав и число работающих механических и сборочных цехов определяются характером производственного процесса, степенью его автоматизации, уровнем кооперации вспомогательных служб, структурой и степенью автоматизации системы управления производством.
Широкое использование автоматических линий в крупносерийном и массовом 'производстве, увеличение удельного веса станков с ЧПУ и ГПС в серийном производстве приводят к уменьшению удельного веса производственных рабочих в составе работающих механосборочных цехов. Вместе с этим возрастает удельный вес инженерно-технических работников и вспомогательных рабочих в связи с усложнением оборудования. Однако широкое использование средств вычислительной техники и автоматизированных систем управления, призванных повысить производительность инженерного труда, и внедрение автоматизированных систем технической диагностики современного оборудования, облегчающего его обслуживание, обеспечивают сокращение численности всех работающих.
Создание специализированных складов, централизованных ремонтных и инструментальных служб способствует уменьшению численности вспомогательных рабочих. Численность служащих (счетно-конторского персонала) уменьшают благодаря внедрению автоматизированных систем учета продукции на всех этапах ее создания и выполнения расчета заработной платы работающих на ЭВМ.
3.1. Определение числа производственных рабочих (наименование вопроса)
К производственным рабочим механических и сборочных цехов относят станочников и наладчиков оборудования, слесарей для выполнения ручных и механизированных операций обработки, пригонки и сборки, мойщиков деталей и других рабочих, непосредственно занятых выполнением операций технологического процесса обработки деталей и сборки машин.
Число производственных рабочих, непосредственно занятых выполнением операций технологического процесса, определяется по стан-коемкости или трудоемкости выполняемого объема работ.
Число станочников при укрупненных расчетах определяется по станкоемкости годового объема работ или по принятому числу станков цеха (участка). В первом случае:
Рст=Т∑/(Фр*Км),
где: Т∑- суммарная станкоемкость годового объема работ изготовления деталей на станках данного типа, на участке или в цехе в станко-часах;
Км - коэффициент многостаночного обслуживания - среднее число
станков, обслуживаемых одним рабочим.
Численность слесарей на операциях разметки, шабрения, ручного удаления заусенцев и острых кромок, а также сборщиков определяется по формуле;
Р=Т/Фр,
где:Т - трудоемкость соответствующего вида работ в человеко-часах;
Фр- эффективный годовой фонд времени рабочего.
Коэффициент Км зависит от вида оборудования. Для универсальных станков, как правило, Км=1 . Исключение составляют тяжелые токарные, токароно-карусельные станки, предназначенные для изготовления деталей большого размера, где Км = 0,33...0,5. Для прутковых токарных и токарно-револьверных автоматов Км= 3...8; для многошпиндельных п/автоматов
Км = 1...4; для зубообрабатывающих п/автоматов Км= 2...4; для агрегатно-сверлильных станков, агрегатно-расточных станков Км= 1...3; для станков с программным управлением Км= 2...3.
При определении числа производственных рабочих цеха пользуются усредненными значениями Км, полученные на основе анализа действующих цехов:
- для мелкосерийного и единичного производства Км= 1,1... 1,35;
- для серийного Км= 1,3...1,5;
- для крупносерийного и массового Км= 1,9...2,2.
Средний коэффициент многостаночного обслуживания по цеху определяется по формуле:
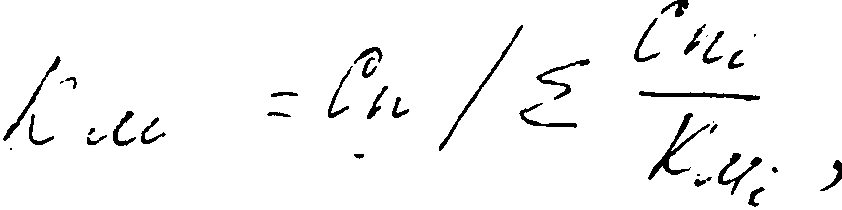
где: Сn- - принятое число станков цеха;
Сni и Kмi - соответственно число станков цеха i-ой группы и число стан-
ков данной группы, обслуживаемых одним рабочим, причем
∑Сni=Cn
Число станочников можно определить по числу станков цеха
или участка:
Рст=(Сn*Фо*Кз*Ки)/(Фр*Км),
где: Фо - эффективный годовой фонд времени работы оборудования;
Кз и Ки- коэффициенты соответственно загрузки и использования оборудования.
При укрупненных расчетах для единичного, мелко- и среднесерийного производства следует принимать Кз*Ки =0,85, для крупносерийного и массового производства Кз*Ки =0,8.
Число сборщиков по числу рабочих мест Мсб определяется по формуле:
Рсб=(Мсб*Фр.м.*Ки*П)/Фр,
где: Фр.м. - эффективный годовой фонд времени рабочего места;
П - плотность работы (среднее число рабочих, одновременно работающих на одном рабочем месте). Для сборки Ки = 0,8.
При поточной сборке необходимо предусмотреть до 5% "скользящих" рабочих (для замены временно отсутствующих) по отношению к общему числу производственных рабочих.
В условиях крупносерийного и массового производства для обслуживания станков в составе производственных рабочих предусматривают наладчиков, число которых определяется по нормам обслуживания, установленным для каждого типа оборудования.
Так, например, в зависимости от точности и сложности обработки один наладчик обслуживает: токарных 11-18; агрегатно-сверлильных 5-12;
универсально-шлифовальных 8-18; токарных с ЧПУ 4-10; сверлильных и фрезерных с ЧПУ 8-16; многоцелевых станков и РТК 3-6; сборочных автоматов и полуавтоматов 5-8; сборочных ГПМ 4-6.
В условиях единичного, мелко- и среднесерийного производства использовать наладчиков на универсальном оборудовании не рекомендуется. Здесь, как правило, рабочие имеют высокую квалификацию.
В автоматизированном производстве к числу производственных рабочих относят операторов и наладчиков автоматических линий и операторов наладчиков ГПМ. Для установки заготовок и снятия обработанных деталей для обслуживания одной автоматической линии механической обработки принимают одного или двух операторов в зависимости от уровня ее обслуживания.
Число наладчиков автоматических и сборочных линий определяют по нормам обслуживания в зависимости от числа позиций автоматической линии. На автоматических линиях механической обработки один наладчик в зависимости от сложности наладки (числа инструментов и достигаемого квалитета) обслуживает 3-10 позиций автоматической линии. Меньшие значения норм принимают при точности обработки, соответствующей 6-7-му квалитетам, и применении специального инструмента. Большие значения принимают для линий, состоящих из универсальных агрегатных станков с применением простой оснастки и центрового инструмента.
Для автоматических сборочных линий нормы обслуживания позиций одним наладчиком, установлены в зависимости от сложности применяемого оборудования и составляет 6-12 позиций.
Меньшие значения принимают для линий, состоящих из полуавтоматов с применением ПР, большие - для линий с применением механизированного сборочного инструмента.
Число операторов-наладчиков ГПС рассчитывают по нормам обслуживания в зависимости от числа ГПМ в их составе. Один оператор-наладчик обслуживает следующее число ГПМ: токарных 3-4, сверлильно-фрезерно-расточных 2-3, шлифовальных 2-3, зубообрабатывающих 3-4, сборочных 2-3. Меньшие значения даны при пяти ГШПМ в составе ГПС, большие - при ГПМ более пяти.
3.2. Многостаночное обслуживание (наименование вопроса)
При детальных расчетах число производственных рабочих-станочников уточняют с учетом размещения оборудования и анализа условий многостаночного обслуживания. Такой анализ проводят на основе разработанных планировок.
Основное условие для использования многостаночного обслуживания заключается в том, чтобы за время автоматической работы одного станка рабочий смог выполнить работу по обслуживанию других станков,
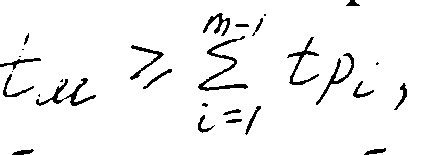
где tм- время работы станка без участия рабочего, когда рабочий свободен от обслуживания станка и активного наблюдения за его работой;
∑ti - суммарное время обслуживания и активного наблюдения за работой других станков с учетом времени на переход рабочего
от одного станка к другому.
бслуживании станков-дублеров, выполняющих одинаковую операцию, число станков, обслуживаемых одним рабочим, /тг = / У. В этом случае несколько станков, обслуживаемых одним рабочим, составляют зону обслуживания.
Циклограмма работы станочника при обслуживании станков-дублеров показана на рис.4.1.
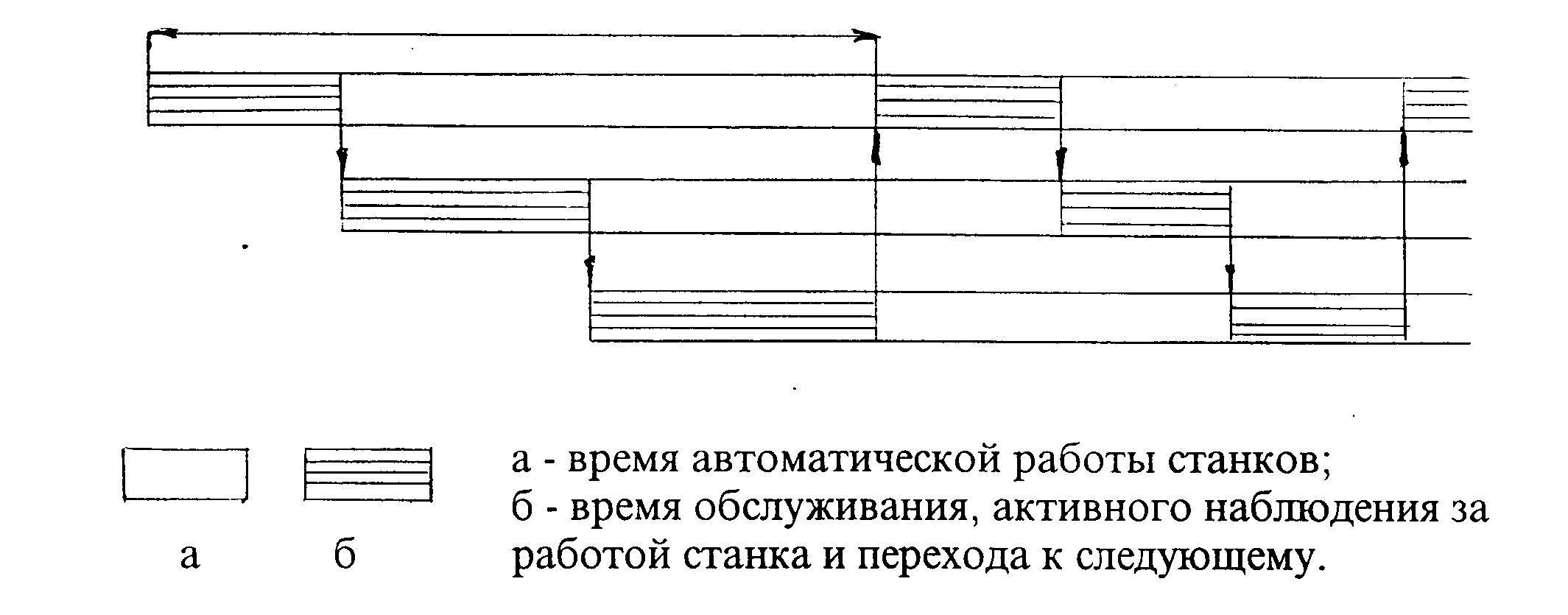
Рис.4.1. Циклограмма работы станочника при обслуживании станков-дублеров
Длительность цикла многостаночного обслуживания - промежуток времени, в течение которого рабочий обслуживает все станки, входящие в зону обслуживания. Длительность цикла при обслуживании, станков-дублеров, когда у рабочего нет свободного времени, равна оперативному времени tоп, т.е.
Тц=tоп,
Для станков с различной продолжительностью операций при определении длительности цикла сопоставляют время ручного обслуживания каждого станка с наибольшим оперативным временем обработки на станке, входящем в предполагаемую зону обслуживания. Если суммарное время обслуживания станков больше максимального оперативного времени работы данного станка, т.е.
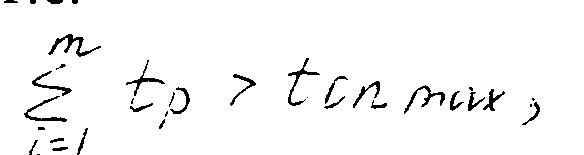
то время цикла принимают равным суммарному времени обслуживания
с
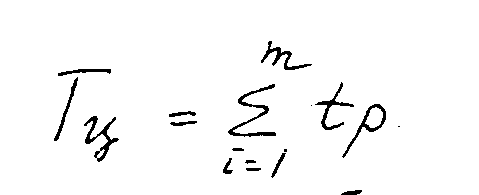
танков:
Если суммарное время обслуживания станков меньше максимального оперативного времени станка, т.е.
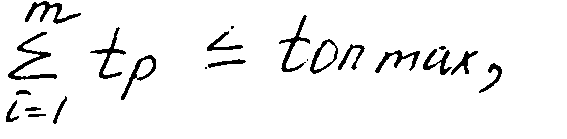
то длительность цикла принимают равной максимальному оперативному времени
Тц=tоп max,
Если обработку ведут на непрерывно-поточной линии, длительность цикла обслуживания должна быть равна или кратна действительному такту выпуска. Действительный такт выпуска определяется по номинальному такту:
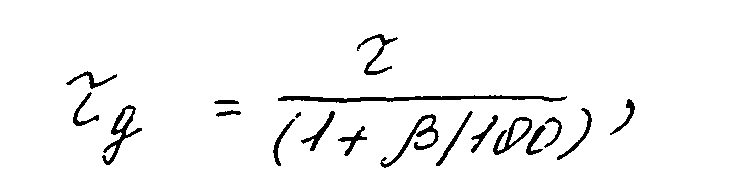
где β - потери времени, % оперативного времени, на организационное и техническое обслуживание рабочего места и регламентированные перерывы;
β = 6 ... 8 %
Для оценки занятости рабочего обслуживанием каждого станка используют коэффициент занятости ;
Кзi=tpi/Тц,
О
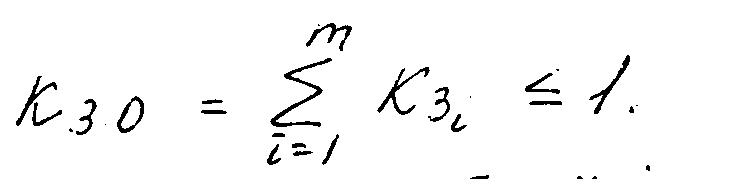
бщий коэффициент занятости рабочего по всем станкам не должен превышать единицы:
В практике проектирования общий коэффициент занятости принимают не выше 0,7 - 0,8 , оставляя резерв на случай возможного совпадения времени обслуживания станков с длительностью выполнения операций.
В настоящее время при двухсменном режиме работы численность производственных рабочих в первой смене (% общего числа производственных рабочих) рекомендуется принимать: в единичном и мелкосерийном производстве 60%, в серийном 55, в крупносерийном и массовом производстве 50.
При укрупненных расчетах численность операторов-наладчиков, обслуживающих ГПМ и ГПС по сменам (% общего числа рабочих) следует распределять следующим образом: в первую смену 50, во вторую 30 и в третью смену 20.
3.3. Определение числа вспомогательных рабочих (наименование вопроса)
К вспомогательным относятся рабочие, выполняющие техническое обслуживание производственных участков и линий: рабочие ремонтных и инструментальных служб, транспортные и подсобные рабочие, уборщики производственных помещений, рабочие складов и кладовок и др.
Численность вспомогательных рабочих при укрупненном проектировании определяют общим числом в зависимости от числа производственных рабочих. При детальном проектировании вспомогательных служб число вспомогательных рабочих определяют либо по нормам обслуживания, либо в зависимости от трудоемкости выполняемого объема работ.
В табл.4.1 приведены данные о соотношении (%) числа вспомогательных рабочих в зависимости от числа производственных рабочих цеха. Указанные соотношения даны с учетом централизации всех вспомогательных служб и являются ориентировочными, так как состав и число вспомогательных рабочих существенно зависит от уровня автоматизации производственных процессов.
4.1. Нормы для определения численности вспомогательных рабочих механических и сборочных цехов (% числа производственных рабочих)
Цеха и линии | Производство | |||
единичное и мелкосерийное | среднесерийное | крупносерийное | массовое | |
Механические цеха Автоматические линии Сборочные цеха | 20-25 - 20-25 | 20-25 - 20-25 | 20-25 - 20-25 | 20-25 30-40 20-25 |
3.4. Определение числа ИГР. служащих и младшего обслуживающего персонала
(наименование вопроса)
К категории инженерно-технических работников (ИТР) относятся лица, осуществляющие руководство цехом и его структурными подразделениями (начальник цеха, его заместители, начальники отделений, участков, лабораторий, мастера), а также инженеры, технологи, техники, экономисты, нормировщики, механики, энергетики и т.д.
При укрупненном проектировании численность ИТР механических цехов определяют по нормам в зависимости от числа основных станков цеха, а ИТР сборочных цехов - в зависимости от числа производственных рабочих. В табл.4.2 приведены нормы для расчета численности ИТР механических и сборочных цехов с учетом разработки технологических процессов, их нормирования и разработки управляющих программ на ЭВМ, а также проектирования приспособлений и инструментов.
4.2.Нормы для определения численности ИТР механических и сборочных цехов
Цеха | Число ИТР ( % числа основных стан ков механического цеха или числа производственных рабочих сборочного цеха) при производстве | |||
единичном и мелкосерийном | среднесерийном | крупносерийном | массовом | |
механические сборочные | 24-18 12-9 | 22-16 11-8 | 21-15 10-8 | 20-15 10-7 |
Большие значения норм соответствуют числу основных производственных станков механического цеха до 50 или числу производственных рабочих сборочного цеха до 75, меньшие значения - числу станков более 400 и числу производственных рабочих более 700.
При детальных расчетах численность ИТР уточняют в соответствии с разработанной структурой цеха и схемой его управления. Предполагается, что 70% общей численности ИТР работает в первую смену.
К категории служащих относится персонал, выполняющий работы по счету, отчетности, снабжению, оформлению: бухгалтеры, кассиры, копировщики, чертежники, секретари, учетчики, заведующие складов и кладовых.
Число служащих механических и сборочных цехов определяют по нормам в зависимости от числа производственных рабочих.
Для цехов единичного и мелкосерийного производства в зависимости от числа производственных рабочих число служащих составляет 1,2-2,2%, среднесерийного производства 0,9-1,9%, крупносерийного производства 0,6-1,6%, массового производства 0,1-1,4%. Меньшие значения соответствуют численности производственных рабочих более 700 человек, большие - численности производственных рабочих менее 75. Для первой смены численность служащих принимают равной 70% их общей численности.
К категории младшего обслуживающего персонала относят гардеробщиков, уборщиков бытовых и служебных помещений, курьеров и др. Их число принимают равным 2-3% от общего числа работающих.
Контрольные вопросы:
1. Как определяют число производственных рабочих при укрупненном и детальном проектировании?
2. Когда возможно многостаночное обслуживание?
3. Как определить число станков обслуживаемых одним рабочим?
4. Как определить численность вспомогательных рабочих, инженерно-технических и служащих цеха? Каковы их функции?
5. Каковы особенности определения численности работающих в ГПС?
6. Назовите пути уменьшения численности работающих в механосборочном производстве.
ТЕМА 5. КОМПОНОВКА МЕХАНОСБОРОЧНЫХ ЦЕХОВ
1. Цели и задачи изучения темы:
- умение решать задачи, связанные с разработкой компоновочных планов механосборочных цехов;
- знание основных факторов, влияющих на выбор компоновочной схемы производственного задания;
- знание основных принципов выбора принципиальных компоновочных схем механосборочных цехов;
2. Перечень основных вопросов темы
2.1. Выбор параметров задания.
2.2. Компоновочный план цеха;
2.3. Расчет площадей цеха.
2.4. Основные принципы выбора компоновочных решений механосборочного цеха.
3. Краткое содержание вопросов темы
Для разработки компоновочного плана цеха ( корпуса ), т. е. решения вопросов о размещении всех входящих в него подразделений, необходимо предварительно определить основные параметры здания, обеспечивающего наиболее рациональное взаимное расположение участков с учетом существующих между подразделениями технологических связей и требований строительной техники.