Пояснительная записка к курсовому проекту по дисциплине 'Основы конструирования механизмов и машин' содержит: 34 страницы, 2 таблицы, 3 рисунка, 6 источников. Объект исследования: привод к общего назначения
Вид материала | Пояснительная записка |
Содержание5.2Расчет червячной передачи(3-4) 5.3Проверочный расчет валов 5.4 Расчет подшипников на долговечность 5.5 Расчет соединений, передающих крутящий момент 6Технические условия на эксплуатацию |
- Пояснительная записка к курсовому проекту по дисциплине 'Основы конструирования механизмов, 375.77kb.
- Расчётно-пояснительная записка к курсовому проекту по дисциплине: "Теория механизмов, 22.29kb.
- Пояснительная записка к курсовому проекту на тему : Привод с цилиндрическим двухступенчатым, 145.44kb.
- Н. П. Огарёва факультет светотехнический Кафедра экономики и управления на предприятии, 529.21kb.
- Программа дисциплины по кафедре Детали машин детали машин и механизмов, 575.22kb.
- Пояснительная записка к курсовому проекту на тему №13: «Цех по ремонту строительных, 141.43kb.
- Пояснительная записка к курсовому проекту по дисциплине: «Объектно-ориентированное, 43.57kb.
- Государственная Академия Управления имени С. Орджоникидзе Институт национальной и мировой, 399.35kb.
- Пояснительная записка к курсовому проекту по дисциплине «методы оптимизации», 29.18kb.
- Пояснительная записка к курсовому проекту по дисциплине " системный анализ", 565.1kb.
5.2Расчет червячной передачи(3-4)
2 Проверочный расчет
2.1 Проверка на контактную выносливость передачи
Основная цель – определение контактных напряжений при окончательно принятых параметрах передачи. Эти напряжения не должны превышать напряжений допускаемых.



где


Уточняем исходные данные
Фактическая скорость скольжения

Коэффициент полезного действия передачи


где


Мощность на колесе
= = = 175,53 Н·м;
= = = 4,99 об/мин;
= = 2,53 кВт
Назначаем коэффициенты



где


Определяем контактные напряжения

197

2.2 Проверка на изгибную выносливость зубьев колеса
Основная цель – определение расчетных изгибных напряжений в зубьях колеса. Эти напряжения не должны превышать напряжений допускаемых.




где

Назначаем коэффициенты

= = = 46;

Определяем изгибные напряжения

26

2.3 Проверка на статическую изгибную прочность зубьев колеса при максимально возможной перегрузке
Основная цель – определение расчетных изгибных напряжений в зубьях колеса при действии на передачу наибольших кратковременных (статических) перегрузок. Эти напряжения не должны превышать напряжений допускаемых.
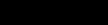


где


Максимальное изгибное напряжение

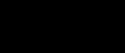

Допускаемое изгибное напряжение


68 < 132 – изгибная прочность при действии максимальных перегрузок обеспечена.
2.4 Проверка на теплостойкость передачи
Основная цель – определение расчетной температуры нагрева в процессе эксплуатации передачи. Эта температура не должна превышать температуры, допустимой для выбранного сорта масла.
=+


где - температура окружающего воздуха, =20°С;
- поверхность теплоотдачи, понимается как внешняя часть корпуса, которая омывается или обрызгивается изнутри маслом;
- коэффициент теплопередачи;
- отношение, которое представляет собой поправку на переменность режима нагружения.
При постоянной частоте вращения
= = = 0,6;
=15 (охлаждение естественное, хорошая циркуляция окружающего воздуха, чистая поверхность корпуса, отсутствие внутренних перегородок, ребер);
Поверхность теплопередачи определяем приближенно как сумму площадей шести граней прямоугольного параллелепипеда (см. рис. 2).
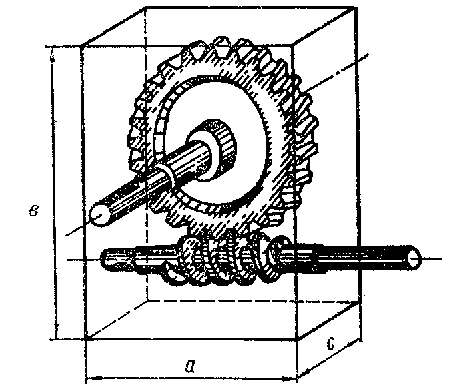
Рисунок 2 – К определению площади поверхности корпуса редуктора для теплового расчета
а ≈ +100 = 200+100 = 300 мм;
b ≈ ++2m+50 = 470+160+2·10+50= 700 мм;
c ≈ +80 = 125+80 = 205 мм;
= 2(ab+ac+bc)=2(0,3·0,7+0,3·0,205+0,7·0,205)=0,83 м2.
= += 20+ = 101°C.
Принимаем авиационное масло, при этом <

5.3Проверочный расчет валов
Основные критерии работоспособности валов - прочность и жесткость. Прочность валов определяют размером и характером напряжений, возникающих под влиянием сил, действующих со стороны установленных на них деталей машин. В общем случае в валах возникает напряжение изгиба (от поперечных сил), нормальные напряжения растяжения-сжатия (от осевых сил) и касательные напряжения кручения (от вращающего момента), т.е. вал находится в условиях сложного напряженно состояния. Нормальные напряжения, а иногда и касательные, изменяются циклически, поэтому основной причиной разрушения валов является усталость материалов.
Для валов различают усталостную прочность при номинальных нагрузках (выносливость) и статическую прочность при пиковых нагрузках. Из-за опасности усталостного разрушения валы рассчитывают на усталостную прочность. Валы, работающие с перегрузками, рассчитывают не только на сопротивление усталости, но и на статическую прочность.
Для расчета валов составляем расчетную схему (см. рис. ). При этом принимаем, что детали передают валу силы и моменты посередине своей ширины. Собственную массу вала и массу установленных на нем деталей, а также силы трения, возникающие в опорах, не учитываем.
входной вал
1 Назначаем материал вала
К материалам машинных валов предъявляются требования достаточной прочности, жесткости, ударной вязкости при минимальной чувствительности к концентрации напряжения. Этим требованиям отвечают малоуглеродистые стали марок Ст. 5, Ст. 6 (ГОСТ 380-88), среднеуглеродистые стали - Сталь 35, Сталь 45 (ГОСТ 1050-88), легированные стали - 40Х, 40ХН, 20Х, 12ХНЗА, 18ХГТ, 30ХГТ (ГОСТ 4543-88).
Для изготовления вала назначаем материал Сталь 45 ГОСТ 1050-88:
- предел прочности по нормальным напряжениям =600 МПа;
- предел текучести по нормальным напряжениям =340 МПа;
- предел текучести по касательным напряжениям =220 МПа;
- предел выносливости по нормальным напряжениям
при симметричном цикле для образца =250 МПа;
- предел выносливости по касательным напряжениям
при симметричном цикле для образца =150 МПа.
2 Определяем силы, действующие на вал
К этим силам относятся силы, возникающие в деталях передач и от веса этих деталей, внешние силы на валу от действия шкивов, звездочек, муфт
2.1 Рассчитываем силы в зацеплении цилиндрической косозубой передачи
- окружная сила Ft21= = = 2095,92 Н;
- радиальная сила Fr21= = = 794,64 Н;
- осевая сила Fa21= Ft21tg b= 2095,92·0,2917= 611,3 Н;
где a - угол зацепления в нормальном сечении, a=20°;
b - угол наклона зуба, b=16,26°.
2.4 Рассчитываем силу, действующую со стороны шкива
Со стороны шкива на вал действует изгибающая сила от натяжения ременной передачи
Qшк2 = 2717 Н (см. расчет ременной передачи)
3 Расчет опорных реакций и изгибающих моментов
Расчетная схема вала приведена на рисунке.
3.1 Вертикальная плоскость
составляем ур-е равновесия относительно опоры 1:
=-Fr21·40-Fa21·38,5415+R2z·70=0
откуда
R2z=(+Fr21·40+Fa21·38,5415)/70;
R2z=(+794,64·40+611,3·38,5415)/70=790,66 Н;
составляем ур-е равновесия относительно опоры 2:
=+Fr21·30-Fa21·38,5415-R1z·70=0
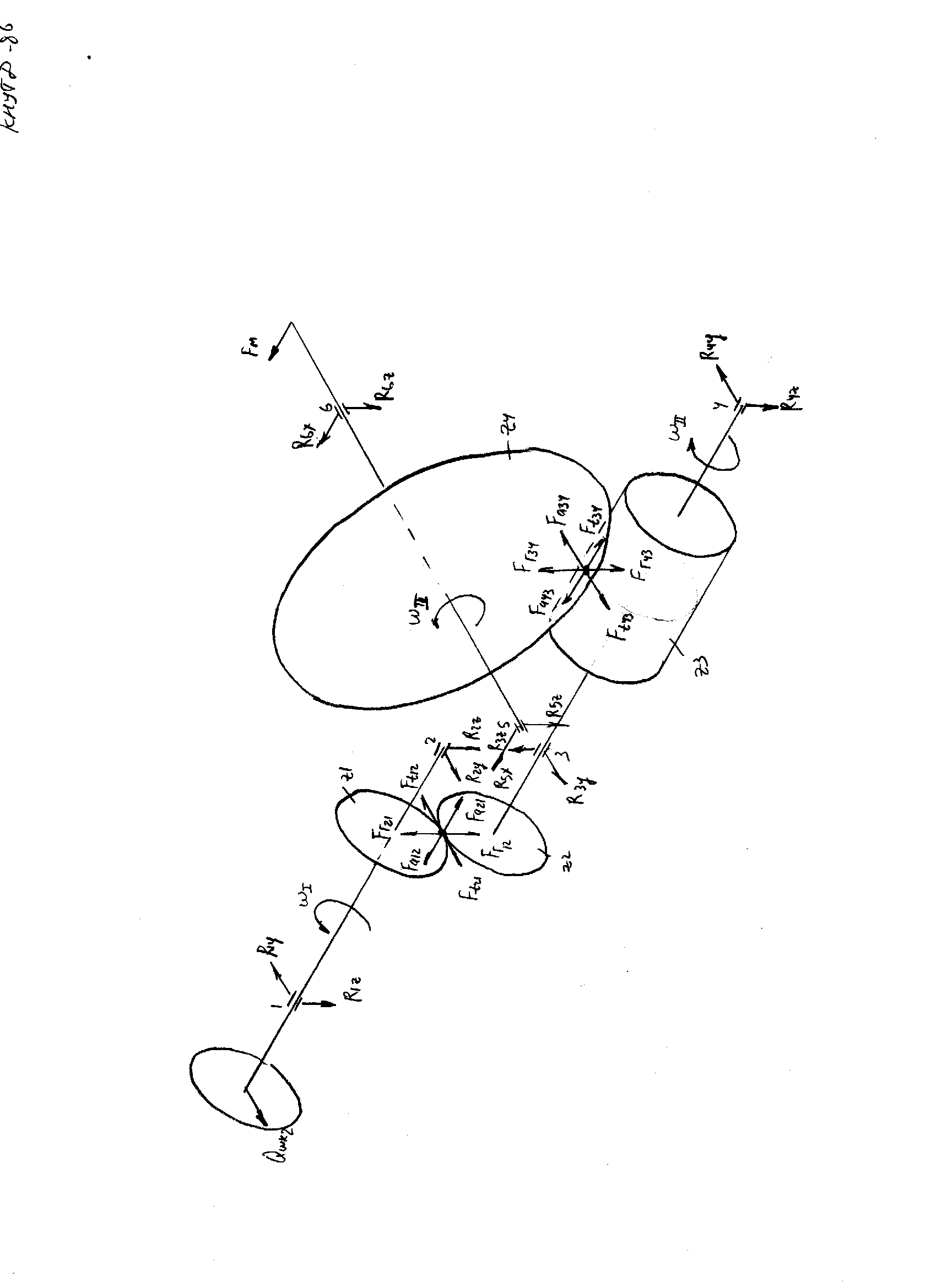
Рисунок - Расчетная схема
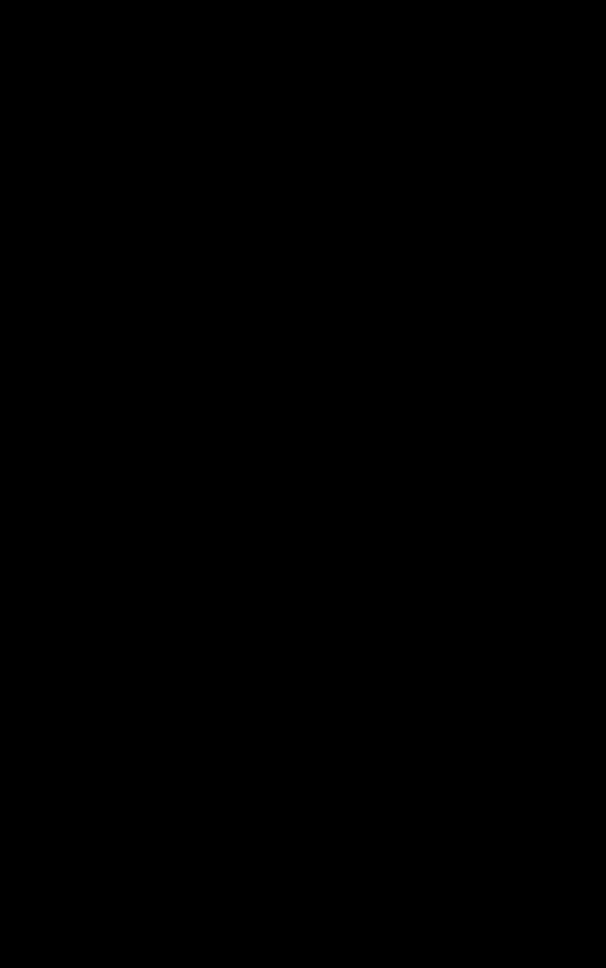
откуда
R1z=(+Fr21·30-Fa21·38,5415)/70;
R1z=(+794,64·30-611,3·38,5415)/70=3,98 Н;
проверка: SZ=+Fr21-R1z-R2z=+794,64-3,98-790,66=0,
следовательно расчет выполнен правильно.
рассчитываем изгибающие моменты в сечениях:
=0 Н·м;
=0 Н·м;
=-R1z·0,04=-3,98·0,04=-0,16 Н·м;
'=-Fa21·0,0385415-R1z·0,04=-611,3·0,0385415-3,98·0,04=-23,72 Н·м;
=+Fr21·0,03-Fa21·0,0385415-R1z·0,07=
=+794,64·0,03-611,3·0,0385415-3,98·0,07=0 Н·м;
3.2 Горизонтальная плоскость
составляем ур-е равновесия относительно опоры 1:
=+Ft21·40+R2y·70-Qшк2·82=0
откуда
R2y=(-Ft21·40+Qшк2·82)/70;
R2y=(-2095,92·40+2717·82)/70=1985,1 Н;
составляем ур-е равновесия относительно опоры 2:
=-Ft21·30+R1y·70-Qшк2·152=0
откуда
R1y=(+Ft21·30+Qшк2·152)/70;
R1y=(+2095,92·30+2717·152)/70=6798,02 Н;
проверка: SY=-Ft21+R1y-R2y-Qшк2=-2095,92+6798,02-1985,1-2717=0,
следовательно расчет выполнен правильно.
рассчитываем изгибающие моменты в сечениях:
=0 Н·м;
=-Qшк2·0,082=-2717·0,082=-222,79 Н·м;
=+R1y·0,04-Qшк2·0,122=+6798,02·0,04-2717·0,122=-59,55 Н·м;
=-Ft21·0,03+R1y·0,07-Qшк2·0,152=-2095,92·0,03+6798,02·0,07-2717·0,152=0 Н·м;
4 Определяем опасные сечения
………….
5.4 Расчет подшипников на долговечность
Расчетное условие:
где - долговечность, которую может выработать подшипник;
- долговечность, заданная в техническом задании.
Расчет подшипников входного вала
Тип подшипников, на которых установлен вал:
опора 1: 7307 - роликоподшипники радиально-упорные конические однорядные ГОСТ 333-79 C=48100 Н; C0=35300 Н;
опора 2: 7307 - роликоподшипники радиально-упорные конические однорядные ГОСТ 333-79 C=48100 Н; C0=35300 Н;
Рассчитываем нагрузки, действующие в опорах
= = = 6798,02 Н;
= = = 2136,77 Н;
Опора 1 является более нагруженной, по ней и ведем дальнейший расчет.
Рассчитываем долговечность подшипника в млн.об.
= 6798,02·1·1,5·1=10197,03 Н;
где - суммарная нагрузка на подшипник;
=1, так как вращается внутреннее кольцо подшипника;
- коэффициент, учитывающий рабочую температуру нагрева подшипника, =1 (до 100°С);
- коэффициент безопасности, =1,5.
= =114,41 млн.об
где - динамическая грузоподъемность подшипника;
…………..
5.5 Расчет соединений, передающих крутящий момент
Выполним расчет основных соединений, передающих крутящий момент между валом и посаженной на нем деталью
Соединения на входном валу
- расчет шпоночного соединения (I - шк2)
Исходные данные: T=81,52 Н·м; d=30 мм; Lст=50 мм.
Назначаем материал шпонки: Сталь 6, =330 МПа.
По ГОСТ 23360-78 устанавливаем размеры призматической шпонки: b´h=8´7; L=45 мм.
Рассчитываем смятие на рабочей грани шпонки
= =52,46 МПа,
где K=0,4h=0,4·7=2,8 мм;
Lр=L-b=45-8=37 мм;
Рассчитываем допускаемое напряжение смятия
= = 165 МПа,
где [S] - принятый коэффициент запаса прочности, [S]=2;
- предел текучести для материала шпонки, =330 МПа.
< = 165 МПа, следовательно, шпоночное соединение работоспособно.
Соединения на промежуточном валу
- расчет шпоночного соединения (II - z2)
Исходные данные: T=177,2 Н·м; d=35 мм; Lст=50 мм.
Назначаем материал шпонки: Сталь 6, =330 МПа.
По ГОСТ 23360-78 устанавливаем размеры призматической шпонки: b´h=10´8; L=45 мм.
Рассчитываем смятие на рабочей грани шпонки
= =90,41 МПа,
< = 165 МПа, следовательно, шпоночное соединение работоспособно.
Соединения на выходном валу
- расчет шпоночного соединения (III - z4)
Исходные данные: T=5692,55 Н·м; d=140 мм; Lст=460 мм.
Назначаем материал шпонки: Сталь 6, =330 МПа.
По ГОСТ 23360-78 устанавливаем размеры призматической шпонки: b´h=36´20; L=400 мм.
Рассчитываем смятие на рабочей грани шпонки
= =27,93 МПа,
< = 165 МПа, следовательно, шпоночное соединение работоспособно.
- расчет шпоночного соединения (III - м)
Исходные данные: T=5636,37 Н·м; d=120 мм; Lст=140 мм.
Назначаем материал шпонки: Сталь 6, =330 МПа.
По ГОСТ 23360-78 устанавливаем размеры призматической шпонки: b´h=32´18; L=125 мм.
Рассчитываем смятие на рабочей грани шпонки
= =140,29 МПа,
< = 165 МПа, следовательно, шпоночное соединение работоспособно.
6Технические условия на эксплуатацию
Для уменьшения потерь мощности на трение и снижения интенсивности изнашивания трущихся поверхностей, а также для предохранения их от заедания, задиров, коррозии и для лучшего отвода теплоты трущиеся поверхности деталей должны иметь надежное смазывание
Смазывание передач
Для смазывания передач применяем картерную систему. В корпус заливают масло так, чтобы венцы колес были в него погружены. Колеса при вращении увлекают масло, разбрызгивая его внутри корпуса. Масло попадает на внутренние стенки корпуса, откуда стекает в нижнюю его часть. Внутри корпуса образуется взвесь частиц масла в воздухе, которая покрывает поверхность расположенных внутри корпуса деталей.
………………………...
Смазка подшипников качения
Смазка подшипников качения осуществляется тем же маслом что и деталей передач за счет разбрызгивания смазки этими деталями. На плоскости разъема корпуса выполнены специальные каналы, собирающие смазку, стекающую со стенок и направляющие ее в гнезда подшипников. Для свободного проникновения масла полость подшипника открыта внутрь корпуса.
Заключение
В процессе выполнения работы представлен полный порядок разработки конструкции привода общего назначения и связанной с ним документации.
На основе кинематической схемы привода разработаны элементы передач, несущих и опорных элементов и вспомогательных деталей. Разработка конструктивных особенностей привода выполнена с проведением проектировочных и проверочных расчетов деталей и узлов привода, передач (зубчатых зацеплений, муфты, подшипников и т.д.). Описаны технико-экономические и эксплуатационные параметры привода, что позволит наиболее рационально обеспечить его работу при заданных внешних условиях.
Работа показала, что создание эффективно работающего привода возможно только с учетом последовательных проектировочных и проверочных расчетов, минимизацией затрат на изготовление, сборку и эксплуатацию привода.
Перечень ссылок
1 Расчеты деталей машин: Справ. пособие/А.В. Кузьмин, И.М. Чернин, Б.С. Козинцов. – 3-е изд., перераб. и доп. – Мн.: Выш. шк.., 1986. – 400 с.: ил.
2 Методические указании к курсовому и дипломному проектированию для студентов всех специальностей. Выбор электродвигателя и кинематический расчет привода / Сост. С.Г. Карнаух. – Краматорск: ДГМА, 2002. – 64 с.
3 Методические указания к курсовому и дипломному проектированию для студентов механических специальностей. Расчеты зубчатых передач в закрытом исполнении / Попов В.Л. – Краматорск: КИИ, 1981. – 113 с.
4 Методические указания к курсовому и дипломному проектированию по дисциплине «Расчет червячных цилиндрических передач с применением ЭВМ» (для всех студентов механических специальностей) / Сост. А.В. Чумаченко, А.И. Гребенюк. – Краматорск: КИИ, 1989. – 40 с.
5 Методические указания к курсовому и дипломному проектированию для студентов всех специальностей. Расчет передачи роликовой цепью / Сост. А.В. Чумаченко, С.С. Сервирог – Краматорск, ДГМА, 2000 – 18 с.
6 Методические указания к курсовому и дипломному проектированию для студентов механических специальностей. Расчеты ременных передач / Попов В.Л. – Краматорск: КИИ, 1981. – 39 с.
7 Методические указания к курсовому и дипломному проектированию для студентов механических специальностей. Расчет ременных передач на ЭВМ / Шишлоков П.В., Новицкая Л.Н. – Краматорск: ДГМА, 1997. – 19 с.
8 Методические указания к расчету валов и осей (для студентов всех специальностей вуза) / Сост. В.Л. Попов, А.В. Чумаченко. – Краматорск: КИИ, 1992. – 47 с.
9 Методические указания к выполнению курсового проекта по дисциплине «Детали машин». Расчет и конструирование сцепных кулачковых муфт (для студентов механических специальностей вуза) / Сост. В.Л. Попов, Л.П. Филимошкина. – Краматорск: КИИ, 1987. – 16 с.
10 Дунаев П.Ф., Леликов О.П. Детали машин. Курсовое проектирование: Учеб. пособие для машиностроит. спец. техникумов. – 2-е изд., перераб. и доп. – Высш. шк., 1990.-399 с., ил.