Пояснительная записка к курсовому проекту по дисциплине 'Основы конструирования механизмов и машин' содержит: 34 страницы, 2 таблицы, 3 рисунка, 6 источников. Объект исследования: привод к общего назначения
Вид материала | Пояснительная записка |
Содержание4.5Расчет валов 4.6Выбор подшипников 4.7Расчет основных размеров корпуса и крышки 4.7.2Конструирование вспомогательных элементов корпуса |
- Пояснительная записка к курсовому проекту по дисциплине 'Основы конструирования механизмов, 375.77kb.
- Расчётно-пояснительная записка к курсовому проекту по дисциплине: "Теория механизмов, 22.29kb.
- Пояснительная записка к курсовому проекту на тему : Привод с цилиндрическим двухступенчатым, 145.44kb.
- Н. П. Огарёва факультет светотехнический Кафедра экономики и управления на предприятии, 529.21kb.
- Программа дисциплины по кафедре Детали машин детали машин и механизмов, 575.22kb.
- Пояснительная записка к курсовому проекту на тему №13: «Цех по ремонту строительных, 141.43kb.
- Пояснительная записка к курсовому проекту по дисциплине: «Объектно-ориентированное, 43.57kb.
- Государственная Академия Управления имени С. Орджоникидзе Институт национальной и мировой, 399.35kb.
- Пояснительная записка к курсовому проекту по дисциплине «методы оптимизации», 29.18kb.
- Пояснительная записка к курсовому проекту по дисциплине " системный анализ", 565.1kb.
4.5Расчет валов
входной вал
d³ =27,3 мм;
Принимаем диаметр под подшипник dп=35 мм (с учетом действия на вал силы натяжения ременной передачи Q=2717 Н);
промежуточной вал
d³ =35,4 мм;
Принимаем диаметр под подшипник dп=40 мм;
выходной вал
d³ =112,5 мм;
Принимаем диаметр под подшипник dп=130 мм (с учетом размещения на валу муфты).
4.6Выбор подшипников
входной вал
Принимаем роликоподшипники радиально-упорные конические однорядные № 7307 ГОСТ 333-79
d=35 мм; D=80 мм; B=21 мм; C=48100 Н; =35300 Н;
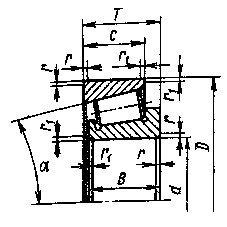
промежуточной вал
Принимаем роликоподшипники радиально-упорные конические однорядные № 7308 ГОСТ 333-79
d=40 мм; D=90 мм; B=23 мм; C=61000 Н; =46000 Н;
выходной вал
Принимаем роликоподшипники радиально-упорные конические однорядные № 7526 ГОСТ 333-79
d=130 мм; D=230 мм; B=64 мм; C=387000 Н; =429000 Н;
4.7Расчет основных размеров корпуса и крышки
4.7.1Конструирование основных элементов корпуса
Толщина стенки основания корпуса
= = 9,7 мм ,
где - максимальный вращающий момент на тихоходном валу.
Принимаем s=10 мм.
Толщина стенки крышки корпуса
= 0,9·10=9 мм.
Принимаем =9 мм.
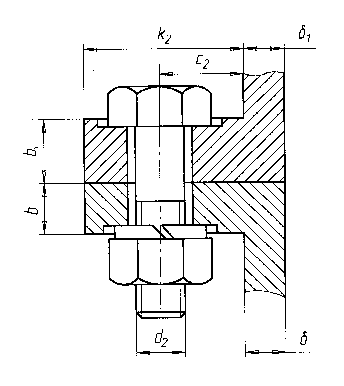
……………
4.7.2Конструирование вспомогательных элементов корпуса
Размеры проушин
- толщина проушины
S = 2s = 2·10 = 20 мм.
…….
5Проверочные расчеты
5.1Расчет цилиндрической косозубой передачи (1-2)
2 Проверочный расчет
2.1 Проверка на усталостную прочность
Расчетное условие:



Рассчитываем контактное напряжение в полюсе зацепления при номинальной нагрузке
,
где





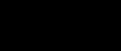



По известным параметрам передачи уточняем значения коэффициентов
при = = 0,39,






принимаем



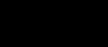










459<500 – контактная выносливость обеспечена.
2.2 Проверка на изгибную усталостную прочность
Расчетное условие:

Допускаемое изгибное напряжение определяем по формуле
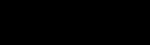
где




















где


m – показатель степени.
Принимаем:






Изгибная прочность зубьев шестерни и колеса в общем случае разная, поэтому для дальнейшего расчета необходимо установить «слабый» элемент, для чего и для шестерни и для колеса рассчитываем отношение

Допускаемое изгибное напряжение для шестерни:


m = 6 (для зубчатых колес с твердостью поверхности зубьев НВ=<350)
=
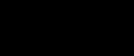








== 205 МПа.
Допускаемое изгибное напряжение для колеса:
Предел контактной выносливости при эквивалентном числе циклов нагружения


= = 45

m = 6 (для зубчатых колес с твердостью поверхности зубьев НВ=<350)







Допускаемое изгибное напряжение
== 196 МПа.
Определяем более «слабый» элемент

=3,94 (= = = =39) [3, табл. 4]
=3,62 (= = = =86) [3, табл. 4]
= = 52; = = 54.
Более «слабым» элементом является шестерня 1, по которой и ведется дальнейший расчет.
Расчетное изгибное напряжение при номинальной нагрузке определяем по формуле

где



Принимается: ==3,94 (см. выше);
== =0,88;
при = =0,39,


где n – степень точности по нормам контакта по ГОСТ 1643-72, n=9;





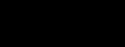

принимаем








Остальные данные см. проектировочный расчет.

145<205 – изгибная выносливость обеспечена.
2.3 Проверка на контактную прочность при действии максимальных перегрузок
Расчетное условие:
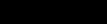
Максимальное контактное напряжение
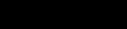
где



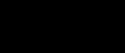

Допускаемое контактное напряжение

743 < 1540 – контактная прочность при действии максимальных перегрузок обеспечена.
2.4 Проверка на изгибную прочность при действии максимальных перегрузок
Расчетное условие:
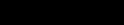
Максимальное изгибное напряжение
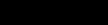
где



Допускаемое изгибное напряжение

380 < 688 – изгибная прочность при действии максимальных перегрузок обеспечена.
205>500>