«Актуальные проблемы развития нефтегазового комплекса России»
Вид материала | Тезисы |
- Актуальные проблемы развития нефтегазового комплекса России, 64.7kb.
- Актуальные проблемы развития нефтегазового комплекса России, 34.44kb.
- Конференции, в которой планируется участие с докладом, 96.22kb.
- Программа V донского нефтегазового конгресса «xxi век. Современное состояние и перспективы, 30.13kb.
- Стратегия развития нефтегазового комплекса в механизме обеспечения экономической безопасности, 319.48kb.
- Программа дисциплины «Современные тенденции развития медиасистемы» Специальность: Журналистика, 281.97kb.
- «Нефть России» Нефтесервис и нефтегазовое машиностроение России: Нужен “либеральный, 23.58kb.
- Стратегические направления развития конкурентоспособного нефтегазового комплекса Республики, 743.56kb.
- Ов исполнительной власти, субъектов Российской Федерации, организаций строительного, 177.17kb.
- «актуальные проблемы обеспечения развития рынка драгоценных металлов и драгоценных, 199.53kb.
СОВРЕМЕННЫЙ Классификатор оборудования нефтегазопереработки и нефтехиМИи
Захарова М.В., Жедяевский Д.Н., Лукьянов В.А.
(РГУ нефти и газа имени И.М. Губкина)
Под классификатором, или классификационной схемой, понимается систематизированный свод (перечень) наименований классифицируемых групп, объектов, признаков классификации и их кодовые обозначения. На сегодняшний день не существует единого классификатора оборудования, который отвечает современному уровню техники и обладает достаточной полнотой и емкостью.
Целью работы является создание основы для систематизации существующих информационно-методических ресурсов в области нефтегазопереработки и нефтехимии за счет разработки классификатора оборудования нефтегазопереработки и нефтехимии. Для достижения поставленной цели в настоящее время проводится сравнительный анализ методов классификации, выявляются достоинства и недостатки известных классификаторов (УДК, МПК, ГРНТИ, ОКП и т.д.).
На основании проведенных исследований планируется выбрать метод классификации (или совокупность методов), позволяющий наиболее полно представить весь спектр оборудования нефтегазопереработки и нефтехимии с оправданной глубиной и полнотой, которая гарантирует охват всех объектов классификации в заданных границах, обеспечивает возможности решения комплекса задач различного уровня, возможность расширения множества классифицируемых объектов и внесения необходимых изменений в структуры классификации.
Планируется разработать: новый емкий и гибкий классификатор оборудования для предметной области нефтегазопереработки и нефтехимии, допускающий включение новых объектов и классификационных групп; информационно-методическое обеспечение формирования и актуализации классификатора; информационно-методическое обеспечение технологий применения классификатора. Направления применения классификатора: индексирование информационно-методических ресурсов нефтегазопереработки и нефтехимии, индексирование оборудования предприятий нефтегазопереработки и нефтехимии, формирование компетенций для работы с оборудованием нефтегазопереработки и нефтехимии на различных этапах жизненного цикла (от проектирования до утилизации), сопряжение различных имеющихся классификаторов.
Создание информационной системы на основе такого классификатора позволит решать ряд важных научных и практических задач в области нефтегазопереработки и нефтехимии.
ОПЫТ ЭКСПЛУАТАЦИИ ГЕЛИЕВОГО ЗАВОДА ООО «ГАЗПРОМ ДОБЫЧА ОРЕНБУРГ» – КАК СТРАТЕГИЧЕСКАЯ ОСНОВА ДЛЯ ПЕРСПЕКТИВЫ ПРОИЗВОДСТВА И РЕАЛИЗАЦИИ ГЕЛИЯ В РОССИИ
Хабибуллин Р.Р.
(Гелиевый завод ООО «Газпром добыча Оренбург»)
К 2030 году ожидается прогнозный дефицит мирового рынка гелия. По экспертным оценкам к этому сроку вероятно удвоение мирового потребления гелия при одновременном снижении его производства, что неизбежно приведет к его дефициту.
Дефицит гелия в мире может достичь к 2030 году от 122,2 до 166 млн. нм3. Надежды на улучшение ситуации с нехваткой гелия связаны с новыми проектами, в т.ч. с газовыми месторождениями в Восточной Сибири и Дальнего Востока, которые содержат до 40-50 % всего российского гелия. Особенностью этих месторождений является сложный компонентный состав, включающий значительные количества гелия и углеводородов С2+выше, которые могут рассматриваться в качестве сырья для дальнейшего развития нефтегазохимической подотрасли.
В целях развития газохимической промышленности была разработана «Программа создания в Восточной Сибири и на Дальнем Востоке единой системы добычи, транспортировки газа и газоснабжения с учетом возможного экспорта газа на рынки Китая и других стран Азиатско-Тихоокеанского региона», утвержденная приказом Минпромэнерго России № 340 от 03 сентября 2007 г.
В соответствии с данной Программой на базе крупнейших системообразующих месторождений (Ковыктинское ГКМ, Чаяндинское НГКМ, месторождения Красноярского края) предусматривается создание крупных добывающих мощностей Восточной Сибири и Дальнего Востока и формирование, таким образом, нового центра газовой промышленности РФ.
Освоение этих месторождений позволит России к 2030 году стать одним из крупнейших производителей и поставщиков гелия и продукции на его основе на мировой рынок и удовлетворять более половины мировых потребностей в этом сырье.
И все-таки это вопрос отдаленного будущего, а в настоящее время производство гелия в России не превышает 6 млн. куб. м., поскольку на сегодняшний день в России функционирует единственный производитель и поставщик гелия для потребителей РФ и стран СНГ - гелиевый завод ООО «Газпром добыча Оренбург».
И пока месторождения Восточной Сибири вступят в стадию разработки, ООО «Газпром добыча Оренбург» останется единственным производителем гелия на протяжении ближайших десяти лет.
«Газпром добыча Оренбург» ведет работы со специализированными организациями по разработке новых технологий и решений в производстве и транспортировке:
- В 2010 году планируется выполнить опытно-конструкторскую работу по созданию турбодетандерного агрегата нового поколения на электромагнитных подшипниках для охлаждения природного газа в криогенном цикле установок выделения этана и ШФЛУ производительностью 3 млрд. куб. м в год по сырьевому газу.
- В рамках проекта «Техперевооружение I,II,III очереди гелиевого завода» планируется полностью реконструировать систему тонкой очистки гелиевого концентрата с использованием технологии «на низком давлении» - до 3,0 МПа, что обеспечит снижение потребления энергоресурсов и технологических потерь гелия.
В перспективе гелиевый завод может стать важным звеном в обеспечении транспортировки восточносибирского гелия на рынки Европы. А гелиевый центр, созданный на базе ОГХК, может быть использован в качестве полигона по отработке новых технологий для объектов гелиевых производств Восточной Сибири.
Совершенствование методики оценки опасности коррозионно-эрозионных повреждений аппаратов и сосудов давления установок очистки природного газа
Велес-Пивоваров А.Р.
(РГУ нефти и газа имени И.М. Губкина)
Длительные наблюдения за техническим состоянием абсорберов установок очистки газа высокого давления от сероводорода и диоксида углерода позволили установить, что внутренняя поверхность аппаратов от второй тарелки до поверхности раздела газ-жидкость (кубовой части) подвержена усиленному эрозионно-коррозионному износу. Коррозионные поражения представляют собой язвы с размытыми нижними краями и пятна с переменной глубиной.
С целью снижения интенсивности износа внутренние устройства абсорберов покрывают полимерными и металлическими материалами, а также вносят изменения в их конструкцию. Наиболее эффективным оказалось нанесение металлического антикоррозионного покрытия, которое снижает скорость развития коррозионных процессов, но создает другие опасные виды коррозионного поражения – контактную коррозию между покрытием и незащищенной поверхностью металла (дефектные участки). При этом виде коррозии дефекты в основном металле образовываются, как правило, в виде язв или полос.
Исходя из однотипности дефектов, представляется интересным разработка простой и доступной методики оценки опасности дефектов для оперативного определения остаточного ресурса аппарата с учетом количества, размеров и месторасположения коррозионных поражений.
Существующие стандартные методики для определения опасности локальных дефектов и предельного ресурса эксплуатации базируются на субъективном подходе к схематизаций дефектов, не позволяют учесть конструктивные особенности аппарата и местонахождение дефектов.
Разработка упрощенной методики оценки опасности дефектов с использованием современных программных комплексов, базирующихся на методе конечных элементов, позволит:
- обеспечить безопасность эксплуатации оборудования;
- оценивать опасность коррозионно-эрозионных повреждений аппаратов и сосудов давления установок отчистки природного газа;
- прогнозировать предельный срок эксплуатации;
- планировать график проведения ремонтных работ для восстановления технического состояния оборудования;
- экономить на проведении дорогостоящих процедур экспертиз по оценке состояния оборудования, проводимых специализированными организациями.
Проблемы оценки технического состояния трубопроводных обвязок скважин Уренгойского НГКМ
Архипов М.Г., Лукьянов В.А., Урванцев А.В.
(РГУ нефти и газа имени И.М. Губкина, OOO «Газпромэнергодиагностика»)
Основная часть фонда газовых скважин Уренгойского НГКМ, составляющего более 1300 единиц, была введена в эксплуатацию при освоении Сеноманской залежи в 80-х годах. В течение длительного времени обеспечение безопасности и надежности эксплуатации газопроводов обвязок скважин базировалось на проведении планово-предупредительных и общих капитальных ремонтов, как правило, с заменой трубопроводов. В условиях старения трубопроводных систем и недостатка ресурсов для их обновления такой подход становится все менее эффективным. С развитием технического диагностирования основной стратегией безопасности газопроводов становится эксплуатация по техническому состоянию.
В 2007-2008 годах специалисты ООО «Газпромэнергодиагностика» провели оценку технического состояния 398 трубопроводных обвязок скважин, состоящую из стандартных методов технического диагностирования и расчета напряжено-деформированного состояния (НДС) трубопроводов с помощью программных комплексов, реализующих метод конечных элементов. Анализ НДС являлся неотъемлемым и основным этапом оценки технического состояния, определяющим реальное состояние трубопроводной конструкции.
При расчете НДС были выявлены следующие проблемы: отсутствие документации и информации о проектном положении трубопровода; сложность определения граничных условий (взаимодействие трубопровод-грунт, опора-трубопровод); способ задания внешних нагрузок.
В расчетной модели переход «земля-воздух» моделировался в виде жесткой заделки, сдвинутой по длине трубы, опорные конструкции – наложением ограничений по степеням свободы, а внешние нагрузки – заданием перемещений сечений трубопровода в контрольных точках.
Расчеты показали, что 29% обвязок скважин имели напряжения, превышающие допустимы значения по СП-34-116-97 и СНиП 2.05.06-85, причем 68 % превышений зафиксированы на опусках основных шлейфов и факельных линий в грунт. Эксплуатирующей организации ООО «Газпром добыча Уренгой» было рекомендовано произвести работы по разгрузке напряженного состояния. С другой стороны, прямые измерения НДС обвязок скважин методом магнитной памяти металла на данных участках не показали аномальных значений.
Данные факты говорят о необходимости разработки комплексной методики оценки технического состояния трубопроводной обвязки скважины при одновременном учете непроектного положения трубопровода и наличия возможных локальных дефектов стенок.
Подход к формированию парка технических средств реагирования на разливы нефти на акваториях нефтяных промыслов
Мерициди И.А., Шлапаков А. В.
(РГУ нефти и газа имени И.М. Губкина)
Информация по существующим технологиям локализации разливов нефти и нефтепродуктов носит явный рекламный характер, поэтому сложно оценить их реальную эффективность. Каждая из предлагаемых на рынке технологий, а также сопутствующие технические средства имеют ограниченную область применения.
В работе предложен алгоритм выбора технологии и формирования состава парка технических средств реагирования на разливы нефти на акваториях промыслов, с учетом факторов, влияющих на их эффективность.
Предлагаемый алгоритм выбора наиболее эффективных технологий реагирования на разливы нефти на акваториях промыслов состоит из двух этапов:
- на первом этапе определяются технологии, применимые в характерных условиях промысла, здесь учитываются такие факторы как тип акватории, тип нефтепродукта и условия окружающей среды (в первую очередь наличие ледового покрова, скорость течения, волнение воды и температура воздуха). Учитываются, также, индивидуальные особенности применения таких методов как потопление, диспергирование и сжигание нефти;
- на втором этапе учитывается эффективность методов, вследствие влияния процессов трансформации нефти после разлива.
Для определения относительной эффективности методов реагирования использованы такие параметры разлива как вязкость нефти и толщина нефтяного пятна.
Алгоритм адаптирован для реализации в качестве автоматизированного комплекса выбора технологии и технических средств локализации разливов нефти и нефтепродуктов на акваториях по исходным параметрам, с возможностью оценки динамики изменения их относительной эффективности.
К ВОПРОСУ ОПРЕДЕЛЕНИЯ РЕАЛЬНЫХ ТЕХНИЧЕСКИХ ПОКАЗАТЕЛЕЙ СКИММЕРНЫХ УСТРОЙСТВ
Слышенков В.А., Каравенкин Д.В.
(РГУ нефти и газа имени И.М. Губкина)
Для сбора нефтяных загрязнений с поверхности воды применяются специальные установки – скиммеры.
Следует отметить, что промышленное производство данного оборудования наиболее развито за рубежом.
Скиммерные установки (СУ) классифицируются по следующим признакам: принцип действия (пороговые, сорбционные, адгезионные и др.) и конструктивные особенности (ленточный, барабанный и др.).
Основными техническими показателями, характеризующим работу СУ, принято считать производительность и сепарационную способность.
Характерно, что паспортная производительность различных СУ может быть одинакова. Очевидно, технические показатели СУ не могут оставаться одними и теми же при изменении внешних условий, изменяясь от номинальных значений до нулевых. Причём у различных СУ интенсивность изменения будет разная.
Определение оптимального режима эксплуатации СУ осуществляется методом проб и ошибок. Следовательно, определяющими факторами являются внешние условия: масштаб разлива, физико-химические характеристики собираемых жидкостей и условия окружающей среды.
Предлагается дополнить существующую классификацию информацией по влиянию внешних факторов на основные технические показатели.
Аналитическими методами определена эффективность работы различных СУ с одинаковой паспортной производительностью в широком диапазоне изменения внешних факторов.
Установлены области предпочтительного использования СУ порогового и адгезионного принципов действия.
Приведены рекомендации, позволяющие избежать негативных эффектов при эксплуатации СУ.
Результаты позволяют определить тип СУ и его производительность, исходя из требуемой сепарационной способности и внешних условий.
Выводы позволяют скорректировать характеристики оборудования при разработке планов ликвидации аварийных разливов нефти (ПЛАРНов).
УСТАНОВКА ПО ОЧИСТКЕ ГРУНТА (ПОЧВЫ, ШЛАМА) ОТ НЕФТЕПРОДУКТОВ И ИССЛЕДОВАНИЕ РЕЖИМОВ ЕЕ РАБОТЫ
Ефимченко С.И., Агеев А.В., Пыльнов А.С.
(РГУ нефти и газа имени И.М. Губкина)
Объектом исследования является опытно-промышленный образец установки по очистке грунта (почвы, шлама) от нефти и нефтепродуктов, изготовленный в соответствии с технологической и компоновочной схемами, разработанными коллективом.
Технологическая схема включает следующее специальное оборудование: смеситель одновальный, грохот, оседиагональный и шламовые насосы, песко- и илоотделители, струйный аппарат и гравитационно-динамический сепаратор жидкости, емкостное оборудование, запорная арматура, электрические шкафы управления и автоматика.
Принцип работы установки заключается в предварительной подготовке загрязненного грунта (почвы, шлама); очистке грунта, на первом этапе которой происходит подача шламовым насосом нагретой до 60-80ºС воды в струйный аппарат, в турбулентном потоке которого происходит смешивание и отмывание частичек загрязненного грунта (почвы, шлама) от нефти и нефтепродуктов. Полученная смесь далее подается с помощью другого шламового насоса в песко- и далее в илоотделитель, где осуществляется отделение частичек загрязненного грунта (почвы, шлама) от жидкой фазы. В финальной стадии процесса очистки жидкая фаза попадает в гравитационно-динамический сепаратор жидкости, где происходит отделение нефти и нефтепродуктов от воды. Вода при этом возвращается в цикл очистки грунта.
В ходе проведения опытно-промышленных работ по очистке амбара с нефтешламом в августе 2009 года в г. Саратове подтверждена правильность концепции очистки грунта (почвы, шлама) от нефти и нефтепродуктов по принятой схеме. Установка очистки грунта от нефти и нефтепродуктов выведена на рабочий режим, подготовлен регламент работ на установке.
По результатам опытно-промышленных работ проведены лабораторные исследования образцов загрязненного и очищенного грунта и воды, получены экспертные заключения.
Краткие характеристики установки по очистке грунта (почвы, шлама) от нефти и нефтепродуктов: производительность, м3/час – 5-15; возможность работы с твердыми и жидкими нефтешламами; ограничения по химическому составу углеводородов, выступающих в качестве загрязнителя отсутствуют; остаточная степень загрязнения, г/кг, не более – 1; применение ПАВ, химических реагентов для организации очистки не требуется; потребляемая мощность, кВт, не более – 150.
УСТАНОВКА ПО ОБЕЗВРЕЖИВАНИЮ НЕФТЕШЛАМОВ, НЕФТЕЗАГРЯЗНЕННОГО ГРУНТА И ИЛОВЫХ ОСАДКОВ
Воробьева С.Ю., Мерициди И.А.
(РГУ нефти и газа имени И.М.Губкина, ООО «ГеоЛайнПроект»)
В настоящее время на предприятиях нефтедобывающей, нефтеперерабатывающей и нефтехимической промышленности накоплено несколько десятков миллионов тонн нефтешламов, представляющих серьезную экологическую угрозу окружающей среде. Одним из наиболее перспективных методов обезвреживания нефтешламов является метод химического капсулирования. Сущность метода заключается в химико-механическом преобразовании загрязняющего материала в порошкообразный материал, каждая частица которого покрыта гидрофобной оболочкой.
Технология химического, или реагентного, капсулирования успешно применяется в Европе, в частности в Греции компанией Actor S.A. Совместно с компанией Actor S.A. проводятся испытания опытной установки по переработке иловых осадков в Подмосковье, по результатам которых будут определены направления модернизации установки.
Установка по обезвреживанию нефтешламов, нефтезагрязненного грунта, иловых осадков данным методом состоит из следующих блоков: приемный блок (после загрузки шлама здесь осуществляется выделение крупных включений, подготовка пульпы); блок химического капсулирования (обработка известью с образованием капсул); блок очистки воды; блок утилизации крупных включений (сжигание); энергетический блок (требуемая мощность – не более 65кВт). Расчетная производительность установки – 15м3 шлама в час. Оборудование монтируется в специальном ангаре, возможно также мобильное исполнение установки.
Шламы с исходным содержанием нефтепродуктов до 75% превращаются в нейтральный для внешней среды материал, используемый в дорожном строительстве и рекультивации земель. Одно из главных преимуществ такой технологии – отсутствие необходимости определения химических параметров обезвреженного продукта на выходе и, соответственно, проведения повторных циклов обработки, как, например, при отмыве грунта. Данные лабораторных анализов переработанного продукта показали его соответствие всем экологическим требованиям российского законодательства.
ИССЛЕДОВАНИЕ УНОСА ЖИДКОСТИ НА ПРЯМОТОЧНОЙ КЛАПАННО-СИТЧАТОЙ ТАРЕЛКЕ
Ларькин А.В., Щелкунов В.А.
(РГУ нефти и газа имени И.М. Губкина)
Исследуемая тарелка содержит в отверстиях полотна клапаны, выполненные в виде пластин с просечками, под которыми размещены козырьки. В крайнем верхнем положении клапанов козырьки располагаются вертикально.
В настоящей работе унос жидкости на прямоточной клапанно-ситчатой тарелке исследовался фотоколориметрическим методом. Данный метод не нарушает режим работы тарелки. В качестве красителя был выбран метиленовый голубой индикатор. Определение концентраций красителя в растворах осуществлялось на фотометре «Эксперт–003».
В работе исследовалось влияние на унос жидкости с тарелки следующих факторов:
- скорости воздуха в рабочем сечении колонны WK [1,6-3,5 м/с];
- расстояния между тарелками HT [300-500 мм];
- нагрузки по жидкости LV [11,4-40,0 м3/(м·ч)];
- высоты переливной планки hW [40-80 мм].
В ходе исследований было установлено, что:
- с увеличением скорости газа в колонне увеличивается величина относительного уноса. Причем во всем диапазоне изменения скорости газа наблюдается линейная зависимость между логарифмом скорости и логарифмом величины уноса жидкости;
- с увеличением расстояния между тарелками наблюдается значительное уменьшение величины уноса жидкости;
- с увеличением нагрузки по жидкости или высоты переливной планки наблюдается незначительное увеличение уноса жидкости.
В результате для исследуемой тарелки была получена двухфакторная модель уравнения относительного уноса жидкости:
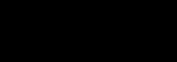
где HC – высота сепарационного пространства, м:

Из данного уравнения получена зависимость скорости газа, соответствующая 10%-ому уносу, от высоты сепарационного пространства:

ЭКСПЕРИМЕНТАЛЬНЫЕ ИССЛЕДОВАНИЯ ПРОЧНОСТИ МЕТАЛЛИЧЕСКИХ ОБРАЗЦОВ С ВНУТРЕННИМИ ДЕФЕКТАМИ
Булатова А.З., Захаров М.Н.
(РГУ нефти и газа имени И.М. Губкина)
В практике диагностических обследований оборудования и конструкций широко используются приборы неразрушающего контроля металла – дефектоскопы, позволяющее выявлять несплошности и трещиноподобные дефекты, появившиеся на стадии эксплуатации или изначально присутствующее в металле конструкции и незамеченные при входном контроле. Оценка возможности дальнейшей эксплуатации конструкции с подобными дефектами в полной постановке является достаточно сложной и не стандартной инженерной задачей. Поэтому актуальными становятся экспериментальные исследования процессов разрушения образцов металла с реальными технологическими дефектами изготовления проката и последующая оценка их несущей способности с помощью инженерных подходов механики разрушения.
В рамках обозначенной проблемы были проведены следующие эксперименты. Из отбракованного на машиностроительном заводе листа стального проката (сталь 09Г2С) было вырезано 27 образцов дефектного металла. Дефекты прокатного листа, обнаруженные методом ультразвуковой дефектоскопии, были идентифицированы как многочисленные расслоения, расположенные строго в срединной плоскости прокатного листа. Далее были проведены испытания на растяжение для определения разрушающего брутто-напряжения в образцах, содержащих реальные дефекты – расслоения.
По разрушающим нагрузкам и измеренным на изломах размерам дефектов вычислены пределы трещиностойкости и построена диаграмма трещиностойкости. Определен порядок использования диаграммы трещиностойкости для расчета допустимых длин трещин при назначенных коэффициентах запаса. Проведено сопоставление диаграммы трещиностойкости и аналогичной диаграммы, следующей из критерия R6.
Показана возможность использования предела трещиностойкости как для выбора и оценки материала и технологий, так и для проведения расчетов прочности конструктивных элементов оборудования с трещинами.
ЕМКОСТЬ ДЛЯ РАЗДЕЛЕНИЯ МНОГОФАЗНЫХ ЖИДКОСТЕЙ
Ефимченко С.И., Рожков В.О., Агеев А.В.
(РГУ нефти и газа имени И. М. Губкина)
В работе спроектирован сепаратор гравидинамического типа для разделения несмешивающейся водонефтяной эмульсии на воду и нефтепродукты и удаление их из аппарата, который имеет форму прямоугольной емкости с общим объемом порядка 20 м3.
Принцип действия основан на специальным образом организованном движении эмульсии, при котором достигается ускоренная коалесценция (слияние и укрупнение) мелких капель нефтепродуктов, а затем их выделение из водной среды, в том числе, под действием сил естественной гравитации.
Сепаратор состоит из отсеков, в которых реализуется принцип гидродинамического разделения фаз.
Основные области применения:
- сбор и обезвоживание нефтепродуктов при очистке емкостей, ликвидации розливов, переработке шламовых амбаров;
- очистка сточных вод от масел и нефтепродуктов;
- очистка и регенерация моющих и технологических жидкостей на машиностроительных и ремонтных предприятиях.
Номинальные параметры емкости:
- на вход жидкость подается самотеком или под давлением от насоса;
- на выходе продукты разделения движутся самотеком;
- расчетная производительность 40 м3/час;
- содержание нефтепродуктов на входе – любое.
Предусмотрены системы аэрации и подогрева для интенсификации процессов разделения и увеличения производительности емкости.
В ходе испытаний было установлено, что при содержании углеводородов порядка 10-15% по объему производительность емкости без ухудшения степени разделения ниже 98% составляет 150 м3/час.
Цель дальнейшей работы:
- оптимизация параметров емкости;
- оптимизация аэрации;
- выявление влияния температуры нагрева на разделение фаз и оптимизация соответствующего объема теплоносителя.
РАЗРАБОТКА ФИЛЬТРУЮЩИХ ЭЛЕМЕНТОВ БЛОКА ОЧИСТКИ БУРОВЫХ РАСТВОРОВ
Виноградова С.М., Ефимченко С.И.
(РГУ нефти и газа имени И.М. Губкина)
Из практики бурения скважин известно, что от качества очистки бурового раствора – степени его очистки от песка и в целом от выбуренной породы зависит скорость бурения, проходка на долото, долговечность долот и надежность оборудования насосного комплекса и циркуляционной системы.
Как правило, в практике бурения применяют многоступенчатые схемы очистки бурового раствора. Первая – ступень грубой очистки виброситами и сито-конвейерами позволяет выделить из раствора частицы от 76 и более мкм. Уменьшение ячеек сит снижает пропускную способность вибросита и снижает долговечность сеток-кассет до 100 часов и менее.
Недостатком гидроциклонов и илоотделителей, позволяющих отделять частицы размером от 40мкм и 20 мкм соответственно и применяемых в 2-х и 3-х ступенчатых схемах очистки, является большая потеря раствора в циклах очистки (5% и более).
Данная работа посвящена обобщению и продолжению работ выпускников кафедры МОНиГП, а именно – разработке щелевых фильтров, находящихся под воздействием ультразвука. Особенность работы щелевого фильтра состоит в том, что ячейка (щель) с возросшей в 100-150 раз пропускной способностью, находящаяся в ультразвуковом поле, снижает вязкость раствора (разрушается структура), а находящиеся в растворе твердые частицы отталкиваются от щели поперечной бегущей волной, проходящей вдоль по сетке.
Для дальнейших исследований разработана экспериментальная установка, которая позволит проверить возможность реализации идей в целом, оптимизировать тип и параметры волноводов, оптимизировать параметры фильтрующих элементов: толщин подложки и ее материал, тип сеток и размеры их ячеек.
Данные экспериментов будут основой для создания опытного образца полномасштабной промышленной установки по очистке буровых растворов.
ИССЛЕДОВАНИЕ РЕЖИМОВ РАБОТЫ УСТАНОВКИ ПНЕВМАТИЧЕСКОГО БАРЬЕРА С ОДНОВРЕМЕННОЙ ПОДАЧЕЙ СОРБЕНТА В ПРОГРАММНОЙ СРЕДЕ MATHCAD
Дубинова И.С., Мерициди И.А.
(РГУ нефти и газа имени И.М. Губкина)
В настоящее время методы локализации разливов нефти и нефтепродуктов в условиях сплошного льда, используемые на промыслах, не удовлетворяют требованиям оперативности, дистанционности и экологичности.
Авторами проведен подробный анализ средств и методов локализации и ликвидации разливов нефти и нефтепродуктов в ледовых условиях.
В качестве прототипа выбран общий пневматический метод локализации разливов нефти и нефтепродуктов. На основании анализа сведений, связанных с применением данного метода, сделан вывод о необходимости создания общедоступной методики подбора оборудования для его осуществления.
Авторами была разработана и обоснована методика подбора оборудования для реализации пневматического метода с одновременной подачей сорбента для совмещения операций по локализации и ликвидации разлива нефти/нефтепродуктов в ледовых условиях в зависимости от исходных данных.
Следующим шагом было составление расчетной схемы и разработка алгоритма математической модели для графического метода выбора оптимальных режимов устройств для ликвидации разливов нефти и нефтепродуктов в ледовых условиях с использованием терморасщепленного графитового сорбента.
На основе алгоритма была построена математическая модель движения смеси воздух-сорбент по трубопроводу с последующим выходом ее из отверстий трубопровода и образованием поверхностного течения. Моделирование проведено для максимально возможной скорости производимого течения 0,1; 0,3 и 0,5 м/с, также при скорости 0,1 м/с для разных диаметров перфорированного трубопровода в составе установки пневматического барьера. В ходе математического моделирования исследовалось и влияние глубины укладки перфорированного трубопровода на эффективность проведения операции ликвидации.
ТРИБОТЕХНИЧЕСКАЯ ЭФФЕКТИВНОСТЬ АЛЮМИНИЙСОДЕРЖАЩЕЙ СМАЗОЧНОЙ КОМПОЗИЦИИ
Пичугин В.Ф., Додонова Д.А.
(РГУ нефти и газа имени И.М. Губкина, ООО «Лоран»)
Повышение срока службы подвижных сопряжений нефтегазового оборудования, экономия горюче-смазочных материалов и защита окружающей среды является важной технической задачей. Одним из основных факторов при этом является износостойкость трибосопряжений, зависящая не только от металлофизических характеристик поверхностей трения, но и от свойств смазочного материала.
В условиях физико-химического взаимодействия смазочного материала с поверхностями трения одним из направлений повышения износостойкости является трибомодификация их зоны трения формированием металлсодержащих антифрикционных и противоизносных пленок.
Анализ литературы по использованию новых технологий в триботехнике с целью повышения срока службы подвижных сопряжений показал, что разработка составов смазочных материалов, процессов финишной антифрикционной безабразивной обработки, безразборного восстановления технических характеристик машин и оборудования, в основном, проводятся с применением меди и ее соединений, а также олова.
Учитывая, что содержание алюминия в природе, в количественном отношении, значительно превосходит наличие таких элементов, как медь и олово, а также тот факт, что стоимость алюминия значительно ниже вышеуказанных металлов, целью данной работы явилась разработка маслорастворимой алюминийсодержащей смазочной композиции и исследование ее триботехнической эффективности.
Представлены результаты экспериментальных исследований по влиянию смазочных материалов на процессы трения и изнашивания металлических пар. Проведена оценка изменений микрогеометрии зоны трения образцов, изношенных как в режиме трения скольжения, так и качения.
С привлечением рентгеноспектрального и рентгенофотоэлектронного анализов установлены элементный состав, строение и толщина, формирующихся на поверхности трения, защитных пленок
ПОВЫШЕНИЕ ЭФФЕКТИВНОСТИ РАБОТЫ ТОРМОЗНЫХ УСТРОЙСТВ
Томский К.О.
(РГУ нефти и газа имени И.М.Губкина)
Тормозные устройства являются высокоответственным узлом в любом механизме, и от надежности их работы напрямую зависит безотказность эксплуатации механизма в целом. Они широко применятся в машинах и оборудованиях различных отраслей промышленности, включая нефтяную и газовую отрасль. Основным фактором, определяющим эффективность и долговечность тормозного устройства, является сила трения, возникающая между колодкой и диском и представляющего собой источник интенсивного теплообразования. Активный разогрев приводит к разупрочнению поверхностного слоя материала тормозной колодки и диска, потере им фрикционных характеристик, и, в конечном итоге, к интенсификации процессов изнашивания.
Энергия, выделяющаяся в процессе трения, преимущественно превращается в механическую и тепловую энергии. В работе был произведен анализ энергетического баланса при трении, в котором было рассмотрено долевое соотношение тепловой и деформационной составляющей энергетического баланса. Была разработана новая расчетная методика, позволяющая определить долю тепловой составляющей энергетического баланса при трении, с помощью которой можно определить тепловую мощность, выделяющуюся в процессе трения.
Предложен принципиально новый подход к конструированию узлов трения тормозных устройств: с целью усиления теплоотвода с поверхности тормозного диска предложено использовать биметаллические материалы. Биметаллический тормозной диск состоит из стальной контактной поверхности трения и расположенную под ней вставку из сплавов на основе цветных металлов. Такой подход обеспечивает высокий уровень прочностных свойств контактной поверхности в сочетании с повышенной теплопроводностью по объему детали.
Для обоснования эффективности предложенного подхода в работе были проведены экспериментальные исследования по определению температур нагрева поверхности стальных и биметаллических образцов, а также исследования по определению весового износа образцов. Исследования показали, что применение биметаллических материалов существенно снижает температуру разогрева поверхности трения, тем самым повышая износостойкость в 1,5-2 раза.
Также в работе разработана новая расчетная методика по определению температуры по сечению биметаллического материала, которая дает возможность определить оптимальные параметры тормозного устройства.
ЗАЩИТНЫЕ ПЛЕНКИ НА ПОВЕРХНОСТЯХ ТРЕНИЯ ПАРЫ АНТИФРИКЦИОННЫЙ СПЛАВ–СТАЛЬ В ГЛИЦЕРИНЕ
Щербинин В.М., Пичугин В.Ф.
(ООО «ГАЗНАДЗОР», РГУ нефти и газа имени И.М. Губкина)
Внешнее трение двух тел без промежуточной прослойки – пленки, обеспечивающей положительный градиент механических свойств по глубине – невозможно. Эти защитные пленки различной природы и свойств формируются в результате механо-физико-химических процессов на контакте путем искусственного нанесения, а также за счет воздействия окружающей среды.
В результате исследований, проведенных в области физико-химии контактных взаимодействий, проф. Гаркуновым Д.Н. и проф. Крагельским И.В. установлено явление избирательного переноса меди с одной поверхности на другую при трении медных сплавов по стали в условиях граничной смазки (например, глицерин, спиртоглицериновая смесь), исключающих окисление меди. Избирательный перенос меди из твердого раствора медного сплава на сталь и обратного ее переноса сопровождается уменьшением коэффициента трения до значения соответствующего жидкостному, а износ, практически, отсутствует.
Аналогичные триботехнические характеристики подвижных сопряжений отмечаются не только в паре медный сплав–сталь, но и в паре алюминиевый сплав–сталь при изнашивании в глицерине, а также в других смазочных материалах.
Изучение элементного состава, строения и толщины защитных металлсодержащих пленок на поверхностях трения пар медный, алюминиевый сплав–сталь, работавших в глицерине, имеет большое практическое значение, а также позволит приблизиться к механизму их формирования.
Экспериментальные исследования процессов трения и изнашивания металлических пар выполняли на машине трения СМЦ-2 по схеме колодка–ролик и на установке возвратно-поступательного движения при нагрузках и скоростях скольжения, обеспечивающих наибольшее снижение триботехнических характеристик.
Представлены результаты рентгеноструктурного, электронографического анализов, рентеноспектральных исследований зоны трения металлических пар на растровом электронном микроскопе с рентгеноспектральной приставкой «Камека», а также метода Оже-спектроскопии и рентенофотоэлектронного анализа.
На основании выполненных исследований предложена схема строения и состава защитных пленок на поверхности трения пар медный, алюминиевый сплав–сталь толщиной 0,6÷0,8 мкм.
МЕТОДИКА ПРОЕКТИРОВАНИЯ МАРШРУТНЫХ ТЕХНОЛОГИЧЕСКИХ ПРОЦЕССОВ МЕХАНИЧЕСКОЙ ОБРАБОТКИ ДЕТАЛЕЙ
Байбаков С.В.
(РГУ нефти и газа имени И.М.Губкина)
Производство любой продукции невозможно без проведения технологической подготовки производства, центральное место в которой занимает проектирование технологических процессов (ТП) изготовления изделий и их элементов. Именно правильность и обоснованность принятых решений на этапе проектирования ТП в наибольшей степени определяет качество изготавливаемой продукции.
Разработка ТП механической обработки деталей изделия (в первую очередь маршрутного) является наиболее сложным видом технологических проектных работ, требующих значительных затрат времени и средств. Объясняется это тем, что большинство решаемых в процессе проектирования задач носят эвристический характер, т.е. в их решении используются различные рекомендации, прошлый опыт, отраженный в различной справочной литературе, и опыт технолога, решающего эти задачи.
В рамках работы на основе анализа и обобщения различной справочно-нормативной и научной литературы по вопросам технологического проектирования, а также на основе опыта проектирования ТП, была разработана методика проектирования маршрутных ТП механической обработки деталей, включающая:
· методику формализованного описания (декомпозиции) машиностроительной детали, позволяющую на основе ее рабочего чертежа осуществить классификацию ее элементов и связей между ними, т.е. осуществить подготовку исходных данных для решения задачи проектирования ТП;
· методику целенаправленного выбора комплектов технологических баз и обрабатываемых от этих баз элементов детали по критерию наивысшей точности внешних связей между этими элементами;
· методику назначения планов обработки элементов детали с подбором оборудования, оснастки и инструмента.
Применение разработанной методики позволяет существенно повысить эффективность работ в технологической подготовке машиностроительного производства. Ожидаемое повышение производительности проектных работ составляет 2-3 раз на фоне общего повышения качества выполняемых работ.
Кроме того, особенностью данной методики является ее пригодность для применения в автоматизированном проектировании благодаря формализации каждого этапа проектных работ.
ПРОБЛЕМЫ ФОРМИРОВАНИЯ ПЛАНОВ И МАРШРУТОВ МЕХАНИЧЕСКОЙ ОБРАБОТКИ ПОВЕРХНОСТЕЙ ДЕТАЛЕЙ ПРИ ПРОЕКТИРОВАНИИ ТЕХНОЛОГИЧЕСКИХ ПРОЦЕССОВ
Тюлина Н.В.
(РГУ нефти и газа имени И.М. Губкина)
Постоянно повышающаяся сложность изделий, а, следовательно, рост трудоемкости проектирования технологических процессов в рыночных условиях требуют ускорения технологической подготовки производства. Основу для выполнения проектных работ технологической подготовки производства составляют планы обработки поверхностей деталей.
Нами рассмотрена последовательность формирования планов и маршрутов обработки поверхностей (предварительный выбор маршрута обработки поверхности, число этапов обработки, окончательный выбор, назначение промежуточных и общих припусков на механическую обработку, а также промежуточных размеров заготовки по технологическим переходам обработки), процесс формирования планов и маршрутов обработки на примерах наружных и внутренних цилиндрических поверхностей вращения, плоских поверхностей, выполнена классификация справочных данных по составлению планов и маршрутов обработки поверхностей деталей, рассмотрено использование САПР в проектных работах при составлении планов и маршрутов обработки поверхностей деталей.
По составлению планов и маршрутов обработки в технологической литературе приводятся различные, иногда противоречивые, рекомендации, что позволяет назвать данный этап технологического проектирования неформализованным. При этом необходимость использования на данном этапе целого комплекса справочных и нормативных документов свидетельствует о возможности автоматизации.
Общий вывод: существующие подходы не совершенны, ведь для составления маршрута обработки поверхности детали технолог использует несколько таблиц справочных данных (технологические допуски в зависимости от способа обработки, припуски на механическую обработку, и др.), собственные знания, опыт, навыки и интуицию. Отсутствие автоматизированных решений приводит к тому, что проектные решения субъективны, затратные по времени и зачастую далеки от оптимальных, что, в частности, может привести к назначению некорректных припусков на обработку.
Отсутствие в настоящее время обобщенной методики составления планов и маршрутов механической обработки поверхностей деталей различных классов, использование эвристических методов решения проектных задач при составлении планов и маршрутов обработки поверхностей деталей – проблемные места для применения САПР.
Оценка надежности монтажных сварных соединений запорной арматуры
Елагина О.Ю., Вышегородцева Г.И.
(РГУ нефти и газа имени И.М. Губкина)
При монтаже запорной арматуры предъявляются повышенные требования механической и промышленной безопасности к используемым технологическим процессам. Элементом, определяющим надежность при установке запорной арматуры, является сварное соединение, поскольку процесс сварки существенным образом изменяет структуру и свойства металла сварного соединения по сравнению с его исходным состоянием. Обеспечение нормативного срока службы газопроводов (40 лет) требует учета как технологических факторов при проведении сварочных работ, так и эксплуатационных параметров.
Наибольшую опасность для работоспособности сварного соединения представляет охрупчивание металла зоны термического влияния (ЗТВ) и, в частности, ее околошовного участка (ОШУ), в процессе эксплуатации. Поэтому в качестве критерия работоспособности сварных соединений может быть принято значение ударной вязкости. Значительная часть монтажных сварных соединений запорной арматуры, используемой на магистральных газопроводах, выполняется на сталях категории прочности К42 – К52. В работе были определены рациональные скорости охлаждения металла ОШУ ЗТВ сварного соединения, обеспечивающие нормативный уровень механических свойств.
Зона термического влияния сварного соединения, также как и основной металл тела трубы, работает в условиях динамических нагрузок. В связи с этим представляет интерес оценка влияния деформационного старения этого участка сварного соединения при эксплуатации на характеристики его ударной вязкости, которая была проведена на примере стали 17ГС.
Оценка степени деформационного старения основного металла и ОШУ ЗТВ показывала, что сварные соединения в процессе эксплуатации охрупчиваются более интенсивно, чем основной металл. Вместе с тем, на склонность к деформационному старению можно повлиять изменением структурно-фазового состава ЗТВ. В частности, в рассматриваемом случае наибольшим сопротивлением деформационному старению обладает металл ОШУ ЗТВ с преимущественно бейнитной структурой. Сталь с преимущественно бейнитной структурой характеризуется минимальным уменьшением ударной вязкости и наименьшим значением коэффициента деформационного старения, которое на 40 % ниже соответствующего показателя металла с ферритно-перлитной структурой.
Для увеличения продолжительности межремонтного цикла необходимо повысить уровень ударной вязкости металла ОШУ ЗТВ сварных соединений запорной арматуры, изготовленных из стали категории прочности К42 - К56. Достичь такого повышения можно путем регулирования термического цикла сварки за счет оптимизации режимов и температуры подогрева в процессе сварки, обеспечивающих охлаждение металла ОШУ ЗТВ в интервале 15-20 ºС/с.
Как показали расчеты, для обеспечения заданного диапазона скоростей охлаждения необходимо при выполнении корневого прохода на режимах указанных в нормативных документах повысить температуру предварительного подогрева до 150+30 0С, при выполнении заполняющих проходов увеличить погонную энергию сварки до 1,1-1,2 кДж/мм, при выполнении облицовочных проходов повысить погонную энергию сварки до 1,5-1,6 кДж/мм и увеличить минимальную межслойную температуру до 150+30 0С.
Применение указанных режимов сварки позволит обеспечить ударную вязкость ОШУ ЗТВ при температуре испытаний –40 ºС на уровне 60-62 Дж/см2, что в свою очередь позволит увеличить продолжительность межремонтного цикла для сварных соединений запорной арматуры до 27-28 лет.
ПРИМЕНЕНИЕ ЦИНКОНАПОЛНЕННЫХ ПОЛИМЕРНЫХ ПОКРЫТИЙ ДЛЯ ЗАЩИТЫ ОТ КОРРОЗИИ РЕЗЕРВУАРОВ ДЛЯ ХРАНЕНИЯ НЕФТИ
Прыгаев А.К., Медведева М.Л., Бакаева Р.Д., Васильев А.А.
(РГУ нефти и газа имени И.М.Губкина)
К противокоррозионным покрытиям для защиты внутренних поверхностей средств хранения и транспортировки нефти и нефтепродуктов предъявляют жесткие требования.
Цинковое металлизационное покрытие, которое не только тормозит коррозионное разрушение за счет своих протекторных свойств, но и обеспечивает кондиционную сохранность перевозимых продуктов, обладает нефтемаслостойкостью и паростойкостью, обеспечивает электростатическую безопасность. Однако сам процесс цинковой металлизации отличается весьма трудоемкой технологией нанесения, токсичностью и взрывоопасностью; потери цинка достигают 50%.
Применение метода «холодного цинкования», который формирует цинконаполненные полимерные покрытия (ЦНП) с помощью композиций, состоящих из высокодисперсного цинкового порошка и полимерной матрицы, позволяет существенно повысить производительность проведения работ, т.к. эти композиции наносятся как обычные лакокрасочные. ЦНП способно защищать сталь катодно, реализуя свою протекторную функцию, подобно цинковым металлическим покрытиям.
Вместе с тем, ЦНП присущ и типичный для лакокрасочных покрытий барьерный механизм защиты: накопление в микропорах покрытия нерастворимых продуктов коррозии цинка, которые тормозят электрохимический коррозионный процесс. Таким образом, ЦНП сочетают достоинства металлических и лакокрасочных покрытий, обеспечивая их конкурентоспособность.
В работе показано, что композиция формируется на уровне наноразмеров, и для выбора композиции необходимо оценивать не только технологические, коррозионно-защитные и механические свойства ЦНК, но прежде всего влияние на электрохимические свойства пленкообразующей основы.
ЦНП с успехом могут заменить цинковую металлизацию, как в чистом виде, так и с последующим покрывным лакокрасочным материалом для повышения коррозионно-механических характеристик покрытия.
Методологические основы разработки нормативной базы, определяющей требуемое качество внутреннего полимерного покрытия НКТ
Макаренко А.В.
(РГУ нефти и газа им. И.М.Губкина)
Накопленный опыт работы НКТ в осложненных условиях эксплуатации показывает, что одним из перспективных направлений повышения их надежности является нанесение полимерных покрытий на внутреннюю поверхность НКТ.
Наряду с этим имеется достаточно много примеров низкой эффективности и ограниченного срока службы используемых покрытий, необоснованных значительных материальных затрат на их применение. Сложившаяся ситуация объясняется отсутствием нормативной базы, определяющей качество внутреннего покрытия НКТ в соответствии с его назначением, методики разработки подобной нормативной базы, методики выбора оптимальной конструкции покрытия для конкретных условий эксплуатации. Поэтому решение указанных вопросов является актуальной проблемой.
Создана методика разработки нормативной базы, определяющей требуемое качество внутреннего полимерного покрытия НКТ в соответствии с его назначением и базирующейся на установленных взаимосвязях между функциями, выполняемыми покрытием, и комплексом свойств покрытия, показателей свойств и норм, обеспечивающих выполнение покрытием этих функций при разных видах внешнего воздействия на него в разнообразных условиях эксплуатации НКТ в течение регламентированного срока службы.
Разработана методика формулирования требуемого качества внутреннего полимерного покрытия НКТ конкретного назначения на основе разработанной нормативной базы.
УПРАВЛЕНИЕ СИСТЕМНым ИНЖИНИРИНГом ОБЪЕКТОВ НЕФТЕГАЗОВОЙ ПРОМЫШЛЕННОСТИ
Безкоровайный В.П., Дроздов С.В., Седов А.В.
(РГУ нефти и газа имени И.М.Губкина)
Современные условия реализации крупных международных проектов по добыче и транспортировке газа требуют вовлечения тысяч организаций, рассчитаны на десятки лет эксплуатации, учитывают требования конкурентоспособности и международные нормы в отношении окружающей среды. Отсюда следует необходимость рассмотрения всего процесса реализации в целом и деятельности каждого субъекта на конкретном этапе жизненного цикла через призму подходов международных стандартов системного инжиниринга и стандартов интеграции данных.
Системный инжиниринг и методы интеграции данных позволяют ответить на вопрос «межъязыкового» взаимодействия различных контракторов, имеющих устоявшиеся информационные инфраструктуры и сложившиеся традиции и подходы к информационного обмену с внешними субъектами, учитывая стоимостной критерий минимизации подобных интеграционных решений.
Стоит обратить внимание, что традиционный жизненный цикл систем, состоящий из определенных стадий, в рассматриваемом подходе определяется природой и свойствами самой системы, т.е. каждая рассматриваемая сущность имеет свой жизненный цикл с определенным набором стадий. Это позволяет более точно понимать, какие точки принятия решений (гейты, вехи) содержит каждый конкретный проект. Исходя из практики реализации проектов, мы понимаем, что каждый этап жизненного цикла не имеет четких границ, может начинаться раньше окончания предыдущего, возобновляться по мере необходимости. Такое понимание реальной картины реализации проекта учтено и отражено в международном стандарте системной инженерии ISO 15288.
Важным аспектом реализации современных подходов к автоматизации деятельности организации является внедрение единого информационного пространства проекта. В качестве центрального объекта автоматизации при реализации проектов проектирования, строительства и эксплуатации нефтегазовых объектов выступает 4D модель объекта.
Рассмотренные подходы позволяют вывести реализацию проектов нефтегазовой промышленности на качественного новый уровень, учитывающий требования конкурентоспособности отечественных организаций на международной арене.
ВЫБОР ОПТИМАЛЬНОГО РАСПОЛОЖЕНИЯ БУРОВОЙ ПЛАТФОРМЫ ДЛЯ СНИЖЕНИЯ ОБЩЕЙ СТОИМОСТИ ПРОЕКТА ОСВОЕНИЯ МОРСКОГО МЕСТОРОЖДЕНИЯ
Ананьев И.Б.
(РГУ нефти и газа имени И.М. Губкина)
Освоение морского нефтегазового месторождения – сложный процесс, требующий огромных капитальных вложений. Он состоит из множества задач, большинство из которых необходимо решать на стадии проектирования.
Основными задачами на стадии процесса проектирования обустройства месторождения, являются следующие: 1) выбор количества и типа МНГС (платформ, трубопроводов, манифольдов и т.д.); 2) расположение МНГС; 3) размер МНГС; 4) количество ПДК; 5) количество скважин (для добычи и нагнетательных); 6) расположение скважин (для добычи и нагнетательных).
Опыт обустройства морских месторождений показывает, что процесс оптимизации этих решений именно на начальных стадиях проектирования приводит к существенным уменьшениям общих капитальных затрат при дальнейшей реализации проекта.
Так, количество МНГС, используемых на одном месторождении, зависит от их типа и производительности (количества скважин, объема хранимой в основании платформы нефти и т.д.). Тип платформ зависит от глубины, характеристик дна, ледовых условий, возможности использования данного типа исходя из коммерческих, технологических, политических соображений и т.д. В свою очередь общая стоимость конструкции скважин, зависят от параметров залежи, места расположения МНГС, что говорит о необходимости принятия комплексных решений по системе платформа – скважины – трубопроводы.
В докладе показано влияние количества и типа платформ, а также их взаимного расположения на общую стоимость проекта обустройства морского месторождения.
Сложность процесса проектирования обустройства месторождения его систематическое описание не является тривиальной задачей. Предпринятые попытки найти способ формализации этого процесса, его стандартизации и универсализации, завершились множеством похожих предложений, отличающихся, однако, деталями.
В данной работе приводится анализ существующих подходов, моделей и алгоритмов решения задачи выбора оптимального расположения буровой платформы, их сравнение. Делаются выводы о возможных направлениях их развития и совершенствования.
информационная Модель инвестиционно-строительного проекта
Сафонова Е.Б.
(РГУ нефти и газа им. И.М. Губкина)
Необходимость обеспечения воспроизводства основных фондов предприятий нефтяной и газовой промышленности в условиях дефицита инвестиционных средств диктует высокие требования к обоснованию объемов капитальных вложений, повышению эффективности инвестиционных проектов за счет сокращения капитальных затрат и оптимизации операционных затрат, возникающих в процессе эксплуатации создаваемого объекта. Анализ мирового опыта показывает, что затраты на строительство в Российской Федерации превышают затраты на строительство в странах Западной Европы и США, несмотря на более низкую стоимость строительных ресурсов в РФ. Рассматривая полный жизненный цикл инвестиционного проекта, можно объяснить подобный дисбаланс недостаточной проработкой проекта на стадиях обоснования инвестиций и базового проектирования (FEED).
Для достижения высокой эффективности реализуемых инвестиционных проектов необходимо решить следующие задачи:
- Повышение качества проектирования за счет комплексной автоматизации процессов проектирования – инженерных расчетов, разработки технологических схем, генеральных планов, конструктивных решений и т.д.
- Создание единой информационной модели проекта, консолидирующей информацию о создаваемом объекте и его элементах – оборудовании, трубопроводах и т.д. При этом модель должна быть применима как на прединвестиционой и инвестиционной стадиях, так и на последующих стадиях жизненного цикла объекта.
- Формирование автоматизированной базы знаний проектов и проектных решений.
Для создания эффективной системы управления жизненным циклом проекта требуется адекватная информационная модель инвестиционного проекта, сформированная на основании:
- анализа состава документации, возникающей в процессе разработки инвестиционного проекта, и связей между документами;
- анализа документооборота в части, касающейся капитальных вложений;
- анализа инструментов автоматизации разработки и хранения проектной документации;
- выявления возможностей интеграции проектных процедур, разработки методики и инструментов проведения интеграции.
УПРАВЛЕНИЕ ПРОЕКТОМ ОСВОЕНИЯ МОРСКОГО МЕСТОРОЖДЕНИЯ В СОВРЕМЕННЫХ УСЛОВИЯХ С ПРИМЕНЕНИМ СИСТЕМЫ ЕДИНОГО ИНФОРМАЦИОННОГО ПРОСТРАНСТВА
Корнеев Д.В.
(РГУ нефти и газа имени И.М. Губкина)
Проекты освоения шельфовых месторождений являются крайне сложными как с технической, так и с управленческой стороны. В силу того, что на данный момент промышленность нашей страны не в состоянии полностью справиться с поставленной задачей, приходится прибегать к помощи иностранных специалистов. Различия в подходах, документации, стандартах и т.д. усложняет управление проектом. Большое количество ограничений, связанных с высокой стоимостью работ, сроками, экологическими ограничениями также актуализируют вопрос о качественной системе управления.
В сфере управления проектом можно выделить пять основных этапов его реализации:
- Организация проектных работ.
- Организация строительно-монтажных работ.
- Организация закупок материалов, оборудования, комплектующих и выбора субподрядных организаций.
- Ввод в месторождения в эксплуатацию.
- Организация взаимодействия между российскими и иностранными участниками проекта.
В докладе проводится сравнительный анализ проектных фаз, используемых западными компаниями и принципы организации проектных работ в России.
Предлагается структура проекта освоения морского месторождения, структура системы управления проектированием и строительством сооружений шельфовых месторождений.
На примере освоения типичного морского месторождения предлагаются оптимальные формы управления проектами. Рассматривается технология единого информационного пространства на примере программных продуктов AVEVA PDMS и REVIEW.
Также предлагается вариант совместного использования программ AVEVA PDMS и Primavera для улучшения процесса управления проектированием и строительством объекта.