Ооо «Рябиновое» Декларация о намерениях по освоению месторождения «Рябиновое» (краткое содержание)
Вид материала | Краткое содержание |
- Оценка воздействия на окружающую среду (овос) намечаемой деятельности по строительству, 357.28kb.
- Краткое содержание информационного сайта муниципального образования, 693.73kb.
- Декларация о намерениях технического развития Филиала ОАО «Группа илим» в г. Братске, 714.21kb.
- Наименование и краткое содержание лекций № Тема лекций. Краткое содержание. Количество, 67.09kb.
- Наименование и краткое содержание лекций № лек. Тема лекции, краткое содержание Количество, 72.86kb.
- Наименование и краткое содержание лекций в соответствии с Рабочей программой Тема лекций,, 195.58kb.
- Nc-17 Жанр : romance Предупреждение : упоминания об инцесте. Краткое, 1403.64kb.
- Ооо «сму-94» Проектная декларация, 43.71kb.
- Ооо «сму-94» Проектная декларация, 46.27kb.
- Ооо «сму-94» Проектная декларация, 41.14kb.
ООО «Рябиновое»
Декларация о намерениях
по освоению месторождения «Рябиновое»
(краткое содержание)
Алдан
2011 г
1. ХАРАКТЕРИСТИКА ТИПА ОБОСНОВЫВАЮЩЕЙ ДОКУМЕНТАЦИИ
В качестве документации, обосновывающей намечаемую хозяйственную деятельность, приняты:
- Лицензия ЯКУ № 13728 БЭ на право пользования недрами;
- Технико-экономическое обоснование постоянных разведочных кондиций для золоторудного месторождения Рябиновое, Республики Саха (Якутия): ООО "АРДЖЕЙСИ КОНСАЛТИНГ" г. Санкт-Петербург, 2009 г;
- «Проведение лабораторных исследований на обогатимость руд месторождения «Рябиновое», представленных пробой, отобранной на участке «Мусковитовый» рудного тела №1, и тремя пробами, отобранными на участке «Новый». Проведение укрупнённых испытаний по извлечению золота из руд месторождения «Рябиновое» с разработкой рекомендаций по технологическому регламенту». Этап 3. «Разработка рекомендаций по технологическому регламенту, используемому при проектировании предприятия по добыче золота из руд месторождения «Рябиновое»: Отчет/ ООО «НПП «ГЕОТЭП» - Москва, 2009 г;
- Определение фоновых характеристик поверхностных вод, донных отложений, почв района месторождения «Рябиновое» (Алданский район)»: Отчет /ГУ РИАЦЭМ - Якутск, 2008 г.;
2. ЦЕЛЬ И ПОТРЕБНОСТЬ В РЕАЛИЗАЦИИ НАМЕЧАЕМОЙ ХОЗЯИСТВЕННОЙ ДЕЯТЕЛЬНОСТИ
2.1. Данные о предприятии - заказчике намечаемой деятельности
Полное наименование предприятия – Общество с ограниченной ответственностью «Рябиновое»
Сокращённое наименование предприятия – ООО «Рябиновое»
Сфера деятельности - Разведка и добыча полезных ископаемых и драгметаллов;
Юридический статус - Юридическое лицо на самостоятельном балансе.
Правовая форма - Общество с ограниченной ответственностью.
Юридический адрес – 678900, Россия, Республика Саха (Якутия), Алданский район, г. Алдан, 26 пикет, 12 .
тел. (факс) 35-6-25
Банковские реквизиты – Расчетный счет 40702810600000000271 в АБ «Алданзолотобанк» ЗАО г. Алдан, ИНН 14020000838, КПП 140201001, к/с 30101810800000000792, БИК 049853792, ОГРН 1041400016250
Хозяйственные отношения с деловыми партнёрами - Хоздоговорные.
2.2. Название инвестиционного объекта и планируемое место его реализации
Проектом рассматривается строительство рудника на месторождении Рябиновое, предназначенного для добычи и переработки руды месторождения Рябиновое с целью извлечения золота.
Месторождение рудного золота Рябиновое расположено в Центрально-Алданском золотоносном районе (ЦАЗР), являющимся одним из наиболее изученных и освоенных районов Якутии. Площадь промышленного освоения административно расположена в Алданском районе республики Саха (Якутия) в 50 км северо-восточнее г. Алдана. Географические координаты центра проявления: 125055/ восточной долготы и 58040/ северной широты и занимает бассейн руч. Рябиновый, являющийся правым притоком р. Якокит (рис. 2.1).
2.3. Данные на представителя
В качестве контактного лица по всем вопросам, связанным с осуществлением намечаемой хозяйственной деятельности предприятия, выступает генеральный директор ООО «Рябиновое» Татаринов Сергей Михайлович - р.т. (41145) 35-6-25.
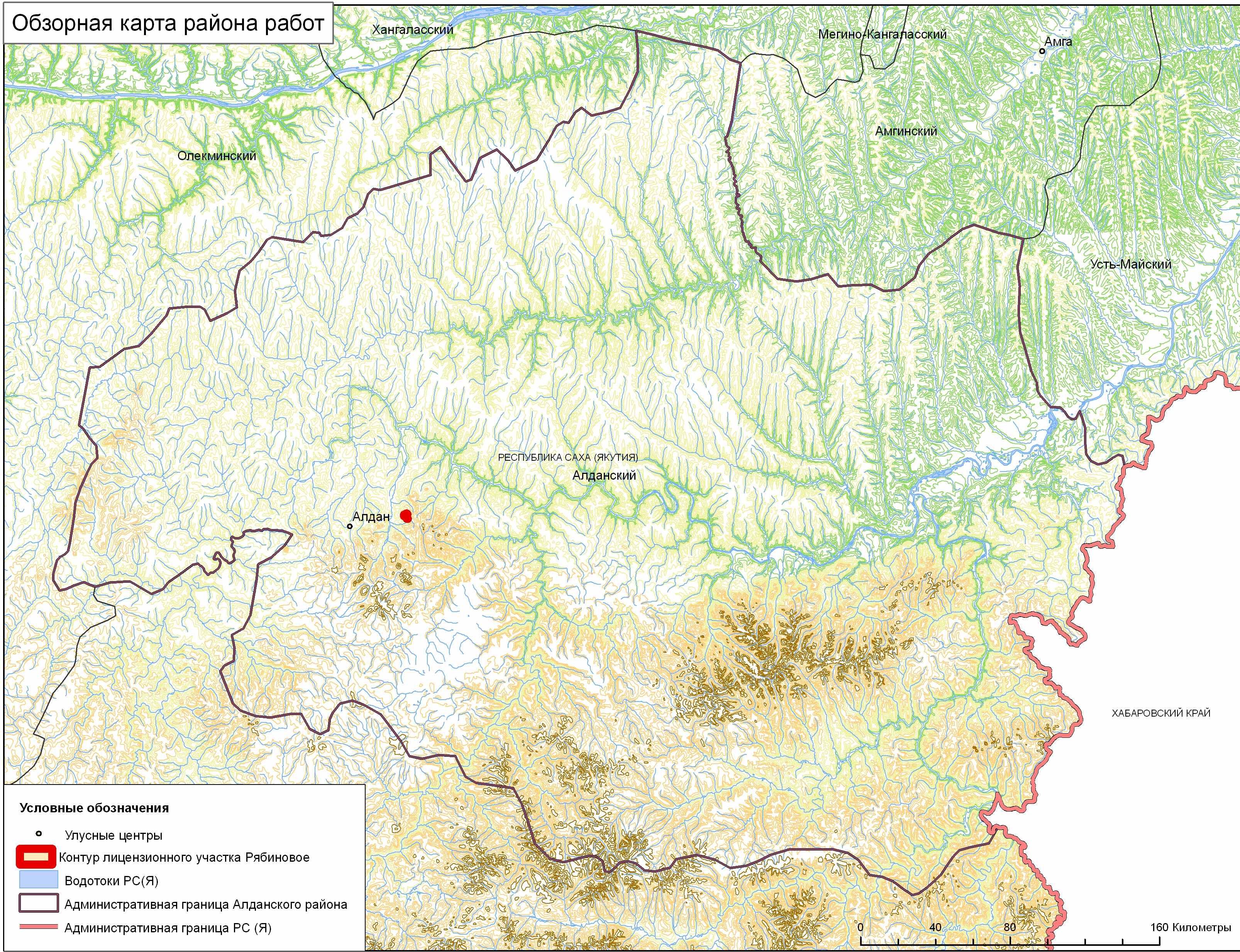
Рис. 2.1. Обзорная карта района работ
ООО «Рябиновое» планирует строительство обогатительного комплекса по добыче и переработке золотосодержащих руд на золоторудном месторождении «Рябиновое» производительностью 1,0 млн. т. в год. Цель строительства - разведка и добыча золотосодержащих руд с получением лигатурного золота (сплав Доре).
При реализации данного проекта ежегодно будет добываться до 1,8 т золота и до 2,8 т серебра.
С выбранной производительностью, с учетом строительства, увеличения производительности и затухания срок отработки месторождения составит 12 лет.
При реализации предлагаемого вида деятельности будут созданы дополнительные рабочие места непосредственно на производстве (280-450 чел.), а также в населенных пунктах Алданского района за счет отчислений в районный и республиканский бюджеты.
Учитывая сложности с занятостью трудоспособного населения в регионе, необходимость пополнения бюджета финансовыми отчислениями, реализация намечаемого производства положительно повлияет на социально-экономическую обстановку региона.
2.4. Предполагаемые сроки реализации проекта
Строительные и пусковые работы на месторождении «Рябиновое» планируется выполнить в течение 2 лет. Общий срок существования предприятия 12 лет.
3. Геологическое строение района
Площадь работ в региональном плане является частью Центрально-Алданского района. В схеме структурного районирования Республики Саха (Якутия) район принадлежит к обширной области автономной активизации Алданского щита. Особенности геологического строения района заключаются в сочетании выходов архейского фундамента, сложенного гранитизированными гнейсами и кристаллосланцами иенгрской серии, венд-нижнекембрийского карбонатного осадочного чехла, нижнеюрских терригенных образований, а также разнообразных по составу интрузивно-вулканических комплексов мезозойского магматического цикла и повсеместно распространенных рыхлых четвертичных образований.
4. Технологические свойства руд
С целью изучения технологических свойств и разработки оптимальной схемы переработки различных типов руд Рябинового месторождения в процессе поисково-разведочных работ 1990–1993 гг. изучены 4 технологические пробы.
Технологические исследования руд проводились по схеме гравитационного обогащения руды с цианированием хвостов гравитации, с моделированием процессов фабрики АК «Алданзолото» в лаборатории Куранахской ЗИФ.
В результате технологических исследований установлено, что руды в пробах содержат 10% золота, упорного к цианированию. Гравитационное обогащение обеспечивает возможность извлечения 20-30% золота при его выходе в концентрат 2-2,5%. Извлечение свободного золота в концентрат 55-60%.
В 1997 г. и 2000 г. АООТ «ИРГИРЕДМЕТ» были проведены работы по разработке технологии обогащения руды Рябинового месторождения, направленные на изучение методов кучного выщелачивания.
По данным технологических исследований золото в рудах присутствует в свободном состоянии, тонкое, ассоциирует с пиритом, лимонитом, глинисто-песчаными фракциями. Данные рационального анализа показывают, что основная массовая доля золота находится в форме, легко доступной для его цианистого выщелачивания, и составляет 61,9% и 85,7% соответственно для золота участка Мусковитового и участка Нового. Извлечение золота из руды месторождения Рябиновое методом кучного выщелачивания составило 72%.
Между тем, от 55 до 87% свободного золота и значительная часть металла, упорного к цианированию, может эффективно извлекаться гравитационными методами.
В 2008 г. ООО «НПП «ГЕОТЭП» выполнены работы по проведению лабораторных исследований на обогатимость руд месторождения Рябиновое.
Исследованные технологические пробы по составу горнорудной массы сопоставимы между собой и относятся к алюмосиликатным. Преобладающими элементами являются кремний, алюминий и калий. Пробы незначительно отличаются друг от друга, как по химическому, так и по минеральному составу, что свидетельствует о едином технологическом типе руд на всех изученных участках месторождения Рябиновое.
Главным ценным компонентом является золото. К попутным компонентам относится серебро. Вредных примесей, осложняющих извлечение золота, не обнаружено. Количество сульфидов от 1% до 3-5%. По данным фазового анализа основная масса золота находится в амальгамируемой и цианируемой форме.
Золото представлено самородной формой в срастании с сульфидами, так же образует самостоятельные включения. Минералов серебра не обнаружено. Оно присутствует в качестве примесей в самородном золоте (10-15%). Крупность золотин колеблется в очень широких пределах: от первых мкм до 1,5 мм.
Поскольку достигнутые показатели по обогатимости руды на стадии тестовых испытаний свидетельствовали о едином технологическом типе руд на всех участках месторождения, укрупненные испытания проводились на шихте рудного материала из всех проб. В результате укрупненных испытаний переработано 364 кг шихты с содержанием золота 1,9 г/т, серебра - 9,4 г/т.
На основании проведенных исследовательских работ принята гравитационно-гидрометаллургическая технология. Схема переработки руды включает выделение на первой стадии «золотой головки» гравитационным методом на центробежных концентраторах с последующей доводкой ее на концентрационных столах и последующее гидрометаллургическое обогащение измельченных до крупности 95% класса -0,074 мм хвостов гравитации.
Суммарное сквозное извлечение золота из руды с содержанием 2,1 г/т золота в конечный продукт (лигатурное золото) составило 85,7% при содержании золота в хвостах 0,3 г/т.
5. Переработка руд месторождения Рябиновое
На основании проведенных лабораторных и полупромышленных исследований ООО «НПП «ГЕОТЭП» были разработаны 3 варианта технологии переработки руд месторождения Рябиновое:
- гравитационно-флотационно-гидрометаллургическая;
- гравитационно-гидрометаллургическая;
- гидрометаллургическая.
Технологический регламент разработан ООО «НПП «ГЕОТЭП» для гравитационно-гидрометаллургической схемы переработки руд.
Производительность предприятия определяется календарным графиком отработки месторождения и рассчитывается для четырех вариантов бортового содержания:
- бортовое содержание 1,2 г/т при годовой производительности по руде 700 тыс. т;
- бортовое содержание 1,0 г/т при годовой производительности по руде 800 тыс. т;
- бортовое содержание 0,8 г/т при годовой производительности по руде 1 000 тыс. т;
- бортовое содержание 0,6 г/т при годовой производительности по руде 1 200 тыс. т.
5.1 Обоснование рекомендуемой схемы извлечения золота из руд месторождения Рябиновое
Результаты исследовательских работ, выполненных на рудах отдельных участков месторождения Рябиновое и их шихте показали, что оптимальным вариантом технологической схемы переработки этих руд является схема прямого сорбционного цианирования. Расчетное извлечение золота из шихты руд со средним содержанием золота 2,1 г/т составит 85,7-90,5 %.
По фазовому анализу уровень извлечения цианируемого золота из различных типов руд составил 66,7-87,5% при содержании золота в хвостах 0,2-0,3 г/т.
Выявленное в результате минералогических исследований наличие в пробах руд месторождения Рябиновое наряду с крупным и средним мелкодисперсного золота тонковкрапленного в минералах, вызывает необходимость более тонкого измельчения рудного материала до 95-97% по классу -0,074 мм перед процессом цианидного выщелачивания с целью вскрытия тонковкрапленного золота.
Сам процесс цианидного растворения золота в пульпе происходит в диффузионной области и лимитируется вторичными процессами, такими, как: образование на поверхности золотин различных пленок, сорбция растворенного золота рудными остатками, соосаждение.
Введение в цианидную пульпу сорбента (активированного угля) приводит в процессе сорбционного выщелачивания к предотвращению протекания вторичных процессов, улучшению кинетики за счет активированного воздействия сорбента при выводе растворенного золота из зоны реакции. Во всех случаях это приводит к существенному увеличению степени извлечения золота.
Введение сорбента (активированного угля) уже в начальный период цианидного выщелачивания устраняет так же возможность сорбции (поглощения) растворенного золота природными углеродистыми веществами, наличие которых в пробах золотосодержащих руд месторождения Рябиновое отмечено по результатам минералогического анализа (содержание органического углерода Сорг=0,4%).
Предполагая, что при промышленном освоении месторождения в переработку будет поступать как шихта руд, в различном соотношении, так и, возможно, руды отдельных участков, отличающиеся как по петрографическому составу, так и по основным физико-механическим свойствам, стабильно выдерживать очень тонкий помол (95-98% класса -0,074 мм) будет весьма сложно. Для обеспечения требуемых условий по крупности измельченного продукта рекомендована развитая трехстадиальная схема классификации. Регулировка работы такой схемы имеет определенные сложности и не гарантирует «проскока» крупных классов в слив контрольных гидроциклонов (III стадия классификации) при возможных нарушениях технологического режима по различным причинам (нарушение отношения Ж:Т при колебании нагрузки по твердому, снижение давления на входе в гидроциклон при износе рабочего колеса насоса, переход с одного аппарата на другой и т.п). Такой «проскок» разумеется, будет носить временный характер, однако при его наличии неизбежны потери золота с хвостами цианирования, связанные с появлением относительно крупного золота в конечном продукте цикла рудоподготовки (в сливе контрольных гидроциклонов).
Исключить, или существенно понизить, влияние «проскока» на конечные показатели процесса извлечения золота из руд, можно включив в схему рудоподготовки операцию гравитационного обогащения на центробежных концентраторах (типа Knelson или Falcon) для улавливания относительно крупного свободного золота (крупность золотин свободного золота по данным минералогического анализа может достигать 1,5 мм). Концентраторы рекомендуется установить на разгрузке мельниц второй стадии.
Наличие в схеме операции гравитационного обогащения позволит также выделять в отдельный продукт золотины, покрытые окисными пленками и связанные с сульфидами, количество которых колеблется от 4,2% до 20,83% в рудах различных участков месторождения. Прямое цианирование подобных форм золота затруднено, а вывод их в отдельный продукт, направляемый сразу на плавку, минуя цианирование, может несколько повысить общее извлечение золота в конечный продукт.
Учитывая вышесказанное, все расчеты сделаны для варианта гравитационно-сорбционной схемы, обеспечивающей более надежное получения достигнутых высоких показателей обогащения.
6. Описание технологического процесса
6.1 Рудоподготовка и гравитация
Исходная руда номинальной крупностью 500 мм подается на приемный бункер рудоперерабатывающего комплекса, оборудованный колосниковым грохотом с размерами щели между колосниками 250 мм.
Надрешетный продукт грохота крупностью -500+250 мм подается на крупное дробление, осуществляемое в щековой дробилке ЩС-6×9 при ширине щели 165 мм.
Разгрузка дробилки расчетной крупностью 248мм совместно с подрешетным продуктом грохота крупностью -250+0 мм подается в аккумулирующие бункера главного корпуса фабрики. Главный корпус фабрики разбит на две автономные параллельно работающие секции, укомплектованные однотипным оборудованием и работающие по одинаковым технологическим схемам.
Руда, номинальной крупностью 250 мм из аккумулирующего бункера ленточным питателем подается на сборный конвейер, оснащенный конвейерными весами, и далее в мельницу мокрого полусамоизмельчения MZ 55-18. Мельница работает с догрузкой шаров диаметром 100-120 мм в количестве до 16 тонн и оснащается навесной возвратной бутарой с размерами отверстий сита 10-12 мм.
Разгрузка мельницы полусамоизмельчения (подрешетный продукт возвратной бутары) номинальной крупностью -7(-10) мм подвергается поверочной классификации (Классификация-1) в гидроциклонах ГЦ-360 (2–в работе, 2–в резерве). Пески Классификации-1 возвращаются в мельницу I стадии на доизмельчение, то есть являются циркулирующей нагрузкой I стадии измельчения.
Слив гидроциклонов I-ой стадии (поверочной классификации) крупностью 45% класса -0,074 мм поступает на вторую стадию измельчения на предварительную и поверочную классификацию (Классификация-2), также проводимую на гидроциклонах ГЦ-360 (4 – в работе, 4 – в резерве). Слив Классификации-1, пройдя операцию щепоулавливания, проводимую на самобалансном грохоте ГСТ-31 с размерами отверстий сита -2 мм, поступает на обогащение (Гравитация-1) в центробежном концентраторе KC-CVD42. Хвосты концентратора подвергаются контрольной классификации (Классификация-3) в аналогичных гидроциклонах ГЦ-360 (3 – в работе, 3 – в резерве). Слив гидроциклонов контрольной классификации крупностью 95% класса -0,074 мм, являющийся конечным продуктом рудоподготовки, поступает на сорбционное цианирование.
Пески гидроциклонов совмещенной предварительной и поверочной классификации
(Классификация-2) и контрольной классификации (Классификация-3) поступают на вторую стадию измельчения, проводимую в шаровой мельнице типа МШР-40×50. Разгрузка мельницы проходит контрольное грохочение на двух параллельно работающих самобалансных грохотах ГСТ-31 с размером отверстий сита 0,7 мм для предохранения от повреждений рабочего конуса центробежного концентратора KC-CVD42, установленного на разгрузке мельницы II-ой стадии (Гравитация-2). Хвосты центробежной концентрации совместно с надрешетным продуктом контрольного грохочения подаются в голову II-ой стадии измельчения – в питание предварительной и поверочной классификации (Классификация-2).
Черновые гравитационные концентраты обоих центробежных концентраторов (Гравитация-1 и Гравитация-2) поступают на операцию «Доводка» для выделения «золотой головки». Доводочная операция проводится на 4-х тонко-шламовых концентрационных столах типа СКО-7,5ШС, работающих параллельно. Концентрат доводочных столов («золотая головка») поступают на плавку, а хвосты, пройдя интенсивное цианирование, возвращаются в голову II-ой стадии измельчения для доизмельчения.
Слив контрольных гидроциклонов (Классификация-3) перед сорбционным цианированием сгущается до 35-40% твердого в двух параллельно работающих сгустителях пластинчатого типа СП-12А. Слив сгустителей используется в качестве оборотной воды в операциях рудоподготовки.
6.2 Комплекс гидрометаллургической переработки
Рекомендуемая схема гидрометаллургической переработки хвостов гравитационного обогащения руды месторождения Рябиновое включает в себя следующие основные операции:
- предварительное грохочение исходной сгущенной пульпы хвостов гравитации от щепы и песков;
- предварительное цианидное выщелачивание;
- сорбционное выщелачивание цианидной пульпы с активированным углем;
- отмывка насыщенного угля от пульпы и илов;
- десорбция золота и серебра с насыщенного угля;
- отмывка угля после десорбции водой;
- кислотная обработка отмытого угля после десорбции;
- электролиз десорбционных золотосодержащих растворов с выделением золота и серебра на катод из стальной «ваты»;
- регенерация (реактивация) отмытого угля после кислотной обработки;
- контрольное грохочение хвостовой пульпы после сорбционного выщелачивания с целью улавливания мелкого угля (проскок активированного угля в хвосты);
- обезвреживание хвостовой пульпы раствором гипохлорита кальция и складирование ее в хвостохранилище.
В цех гидрометаллургического извлечения золота и серебра поступает сгущенная пульпа хвостов гравитационного обогащения руды крупностью измельчения 95–97 % класса -0,074 мм и плотностью 40–42% твердого (или 1,35–1,40 т/м3). Производительность цеха по твердой массе – 2950 т/сут (или 123 т/ч), а по пульпе – 230 м3/ч. Содержание благородных металлов в твердом исходного продукта (хвостов гравитации) составит 1,4 г/т золота и 8,5 г/т серебра.
На стадии предварительного грохочения исходной пульпы используются вибрационные грохоты с размером ячеек сетки 0,60 мм для удаления древесной щепы и крупной песковой фракции, вызывающих большие осложнения в последующих циклах цианирования, сорбционного выщелачивания и десорбции.
После грохочения исходная пульпа самотеком поступает в цикл предварительного цианидного выщелачивания, который состоит из каскада трех аппаратов объемом 460м3 каждый с механическими перемешивателями, установленных с перепадом высот 0,3–0,5м. Цианид натрия и известковое молоко добавляют в первый аппарат цианирования. Концентрация цианида натрия в процессе 0,5 г/л; рН 10,5-11,0. Продолжительность выщелачивания в каждом аппарате – 2 ч при общем времени цианирования – 6 ч. Поток пульпы из аппарата в аппарат поступает самотеком. Концентрация золота в растворах на выходе из цикла цианирования составляет 0,7-0,73 мг/л.
Адсорбционный цикл сорбционного выщелачивания золота из цианидных пульп состоит из 9 (девяти) аппаратов с механическими перемешивателями, объемом 460 м3 каждый. Поток пульпы из аппарата в аппарат поступает самотеком с перепадом высот между аппаратами 0,3-0,5 м. Внутри каждого аппарата находится разделительный внутренний дренаж хордового типа с размером ячеек 0,85 мм для удерживания частиц угля в аппарате при переливе пульпы в пульповый желоб. Пульпа и уголь находятся в противотоке. Транспортировка угля между аппаратами сорбции осуществляется гидравлическим способом – насосами импеллерного типа. В межстадиальных грохотах для отделения угля от пульпы используются дренажи с сеткой, размер ячеек которой 0,85 мм. Содержание (концентрация) угля в пульпе в каждом аппарате составляет 10-15 г/л.
В качестве сорбента золота (серебра) используют активированный уголь (на основе скорлупы кокосового ореха) с размером частиц - 3,0 + 1,0 мм.
Насыщение угля в первом (головном) аппарате сорбции – 3-4 кг/т по золоту. Концентрация золота в хвостовой пульпе сорбции (в жидкой фазе) – 0,01-0,03 мг/л. Хвостовая пульпа из цикла сорбционного выщелачивания хвостов гравитации проходит через вибрационный грохот с сеткой 0,6 мм для улавливания тонкоизмельченного (за счет истирания) угля с целью снижения потерь золота с ним.
Десорбционный цикл включает на первой стадии отмывку насыщенного угля от пульпы и илов на вибрационном грохоте с размером ячеек сита 0,6 мм. Непосредственно десорбция золота (серебра) с насыщенного отмытого активированного угля проводится горячим (93–95°С) раствором состава 10 г/л NaOH и 2 г/л NaCN. После достижения остаточного содержания золота в угле после десорбции на уровне 0,1 кг/т растворы цианида натрия дренируются из десорбционных колонн, и активированный уголь промывается сначала горячей, а затем холодной водой. Насыщенный по золоту (серебру) раствор из десорбционных колонн протекает через электролизные ячейки, где золото и серебро осаждаются на катодах из стальной «ваты». Растворы при этом циркулируют в замкнутом цикле с оборотом непрерывно между десорбционной колонной и электролитической ячейкой, а после накопления примесей их выводят из процесса десорбции и используют в цикле предварительного цианирования исходной пульпы. Отработанный электролит из электролизной ячейки содержит остаточную концентрацию золота на уровне 5–10 мг/л. Он возвращается в теплообменники, повторно нагревается и используется в последующих циклах в качестве десорбирующего раствора.
Возможно рассмотрение в качестве варианта автоклавного способа десорбции золота, использующего чисто щелочные десорбирующие растворы NaOH и обеспечивающего сокращение общего времени десорбции и электролиза до 15 часов.
Кислотная обработка отмытого угля после десорбции проводится 3%-ным (30 г/л) раствором соляной кислоты HCl для удаления карбоната кальция CaCO3 и тонких взвесей из пористой структуры активированного угля. Возможна обработка при обычной температуре 18–20°С, но эффективнее процесс протекает при температуре 80–90°С. После кислотной обработки проводится промывка угля водой и затем разбавленным 4% (40 г/л) раствором едкого натрия NaOH для нейтрализации остаточной кислоты и удаления хлоридов.
Реактивация угля, проводимая для восстановления сорбционных свойств и удаления нежелательных примесей, происходит после обезвоживания его на грохоте (ячейки 0,85 мм) до влажности 40–50% и последующей прокалки во вращающейся горизонтальной (наклонной) трубчатой печи при температуре 640–650°С в течение 30 мин без доступа воздуха.
Реактивированный уголь после гашения водой поступает на грохочения по классу 0,85 мм, после чего крупная фракция (надрешетный продукт) возвращается в адсорбционный цикл для загрузки в последний (хвостовой) аппарат сорбции. Угольная мелочь по мере накопления выводится на складирование.
Катоды из стального «волокна» с нагрузкой осажденного золота из цикла электролиза цеха гидрометаллургической переработки хвостов гравитации по технологии «уголь-в-пульпе» отправляют на плавку с флюсами (бура, кварц, селитра) с получением слитков сплава золота лигатурного, соответствующего по составу требованиям ТУ 117-2-7-75.Суммарная массовая доля золота и серебра составит не менее 70%, примесей не более 30%, в том числе углерода не более 5%, железа, меди и цинка не более 10%, оксидов кальция, кремнезёма и глинозёма не более 15%.
7. РАССМОТРЕНИЕ АЛЬТЕРНАТИВНЫХ ВАРИАНТОВ
7.1. Обоснование целесообразности и методов отработки месторождения, альтернативные варианты
При оценке воздействия на окружающую среду первоочередным вопросом является целесообразность осуществления намечаемой деятельности с определением достигаемых положительных результатов, в основном экономических и социальных, и сравнением их с возможными экологическими и экономическими рисками, сопутствующими проведению горно-добычных работ и гидрометаллургической переработке добытого сырья.
Для Рябинового месторождения существует несколько альтернативных вариантов действий:
- «нулевой» вариант с отказом от разработки месторождения в пользу альтернативной хозяйственной деятельности;
- варианты добычи горной массы открытым или подземным способом;
- варианты технологии переработки добытой руды по фабричной схеме или методом кучного выщелачивания;
- варианты технологии складирования отходов;
- варианты организации противофильтрационного экрана для защиты подземных вод от техногенного воздействия хвостохранилища;
- варианты обезвреживания сточных вод, сбрасываемых в окружающую среду.
«Нулевой» вариант с отказом от разработки месторождения в пользу развития альтернативных видов хозяйственной деятельности нецелесообразен, в первую очередь, по экономическим и социальным соображениям – организация в районе любого вида деятельности, кроме горнодобывающей, малоперспективна из-за требующихся значительных финансовых вложений и низкой отдачи.
Почвы районов в своем большинстве характеризуются низкой продуктивностью. Отсутствие инфраструктуры - дорожной сети, не позволяют развивать здесь достаточно интенсивную сельскохозяйственную деятельность, связанную с овощеводством и животноводством. По этой же причине малоперспективна организация масштабного сбора дикоросов.
Развитие лесохозяйственной деятельности на территории Алданского района осложнено низкой или отрицательной рентабельностью, по этим причинам закрылось большое количество леспромхозов. Запасы деловой древесины невелики, а для возобновления лесодобычи необходимы значительные инвестиции, прежде всего в развитие инфраструктуры (строительство дорог). Вывоз дровяной древесины из районов, прилегающих к месторождению, нереален из-за отсутствия пригодных дорог и высоких транспортных затрат.
Развитие туризма также проблематично из-за отсутствия уникальных или вызывающих интерес природных образований и рекреационных объектов, в районе расположены обычные маловыразительные ландшафты.
Видовой состав охотничьих животных значительно обеднен. Прибыль от охоты на территории, занимаемой проектируемым рудником, не идет ни в какое сравнение с экономической выгодой, которую может получить Алданский район в целом от реализации намечаемой деятельности. Испрашиваемая для осуществления горно-добычных работ и перерабатывающего комплекса площадь, включая зону шумового влияния, является незначительной частью существующих охотугодий и мало повлияет на условия охоты. При переориентации на работу в проектируемом производстве у экономически активного местного населения появится возможность получения регулярных и существенно больших доходов по сравнению с доходами от охоты.
Нулевой вариант лишает район дополнительной улучшенной дороги, которая может использоваться сразу после строительства лесной службой для нужд лесников, охотниками, сборщиками дикоросов и т.п. В перспективе наличие такой дороги несомненно повысит экономический потенциал района за счет открытия доступа к значительным по площадям территориям.
Списочная численность обслуживающего персонала проектируемого рудника равна 500 человек, явочная численность - 250 человека. Кроме того, как показывает практика, каждое рабочее место промышленного предприятия может способствовать образованию как минимум 2 рабочих мест на других предприятиях, связанных с проектируемым объектом прямым или косвенным образом. В случае отказа от реализации проекта регион лишится до 1000 дополнительных рабочих мест как в период строительства, так и при эксплуатации предприятия. Планируемый период отработки разведанных запасов месторождения – до 12 лет. В период эксплуатации будет вестись доразведка как месторождения, так и прилегающих районов и, наиболее вероятно, период эксплуатации будет увеличен. Улучшение ситуации с занятостью населения в регионе предусматривается на длительный срок.
Отказ от освоения Рябинового месторождения не позволит ежегодно добывать порядка 2,5 т золота, лишит налоговых отчислений все уровни бюджетов и не даст возможности значительного укрепления экономики не только Алданского района, но и РС(Я).
Изложенное выше свидетельствует о том, что «нулевой» вариант неперспективен, для экономического и социального развития района реализация проекта освоения Рябинового месторождения принесет несомненную пользу.
Варианты добычи горной массы - открытым или подземным способом, выбираются в основном из экономических соображений, определяемых условиями залегания рудных тел и содержания в них извлекаемых металлов. Подземный способ отработки шахтами является наиболее дорогим, требует повышенных материальных и финансовых затрат и применяется для добычи богатых руд из глубоко залегающих месторождений. Открытый способ отработки карьерами более дешевый и применяется для отработки месторождений, залегающих относительно близко к земной поверхности.
На проектируемом предприятии предусматривается добыча и переработка руды рудных тел уч. Мусковитый и Новый месторождения Рябиновое. Рудные тела выходят к поверхности под слой крупноглыбового делювия мощностью 2-5 м. Большая мощность рудных тел, выход его на дневную поверхность и низкое содержание золота и серебра в руде предопределяют открытый способ разработки месторождения.
Ниже покровного слоя крупноглыбового делювия вскрышные породы и руды имеют коэффициент крепости по шкале проф. М.М. Протодьяконова 1618. Такая крепость вызывает необходимость применения буровзрывных работ при подготовке горнорудной массы к выемке.
Варианты технологии переработки добытой руды.
Добыча благородных металлов из руд возможна по принципиально различным технологиям: фабричной с переработкой руды на специально построенных золотоизвлекательных (обогатительных) фабриках и кучного выщелачивания с обработкой руды в рудных штабелях, расположенных на открытых площадках.
Процесс кучного выщелачивания может быть организован при относительно низких капитальных и эксплуатационных затратах, однако извлечение золота из руд месторождения Рябиновое при этом не превышает 50-60 %. Эта технология может иметь перспективы при переработке забалансовых руд с низким содержанием золота, для которых фабричная технология становится нерентабельной.
У фабричной технологии применительно к рудам месторождения Рябиновое, в свою очередь, имеются свои имеющие практическую значимость варианты:
- обработка всей массы руды методом цианирования с осаждением золота и серебра металлический цинк (фильтрационная технология);
- обработка всей массы руды методом цианирования с извлечением золота и серебра на ионообменную смолу или активированный уголь (бесфильтрационная технология);
- получение концентратов методами гравитационного и/или флотационного обогащения с последующей переработкой их на месте методом цианирования.
Результаты исследований и испытаний различных технологий извлечения благородных металлов из руд месторождения Рябиновое показали, что наиболее перспективным для реализации является процесс предварительного гравитационного обогащения и далее цианирование хвостов гравитации с извлечением золота из пульп активированным углем /1, 2/, а гравиоконцентрат подвергается интенсивному цианированию в аппаратах типа Акация отдельной веткой с возвратом хвостов цианирования в отделения измельчения. Хотя экономические и технологические показатели этой технологии сравнимы с показателями других перечисленных выше фабричных вариантов, она является наиболее простой в аппаратурном исполнении и управлении, следовательно, экологически более безопасной, обеспечивает высокое извлечение золота - 89,0.
Варианты складирования отходов.
В соответствии с технологиями горнодобывающего и перерабатывающего переделов в процессе отработки месторождения образуются отходы горного и гидрометаллургического производств.
Отходы горного производства – вскрышные породы и забалансовая руда, представляют собой твердую крупнокусковую массу и складируются в виде отвалов на специально выделенных местах.
Отходы гидрометаллургического производства – хвостовая пульпа, содержащая в жидкой фазе остаточные количества токсичного цианида и продукты реагирования цианида с рудными минералами. Следует отметить, что твердая фаза хвостовой пульпы (мелкоизмельченная отработанная руда) содержит ценные вещества – недоизвлеченное золото и серебро. В настоящее время их извлечение экономически невыгодно. Однако, в будущем, с разработкой более совершенных и экономичных технологий, а также с изменением цен на металлы, добыча перечисленных ценных веществ с большой долей вероятности будет целесообразна. В связи с этим процесс складирования отходов гидрометаллургии должен предусматривать возможность их повторной отработки.
Складирование хвостовых пульп золотоизвлекательных фабрик возможно по перечисленным ниже технологиям:
1. Подача хвостовой пульпы в хвостохранилище наливного типа с распределением её через раструбы с целью формирования намывного пляжа («мокрое» складирование).
2. Складирование сгущенной хвостовой пульпы («пасты») на пляж хвостохранилища с фильтрацией жидкой фазы через фильтрующую дамбу и сбором фильтрата в специально оборудованном прудке («полусухое» складирование).
3. Складирование кека фильтрации на огражденную дамбой площадку-отвал («сухое» складирование).
Практика работы российских и зарубежных золотоизвлекательных фабрик показывает, что эксплуатация перечисленных способов складирования вполне приемлема с технической точки зрения.
Как показывает опыт работы золотоизвлекательных фабрик, наиболее простым является способ складирования пульпы в хвостохранилище наливного типа. Однако, этот способ одновременно является и наиболее экологически опасным - прорыв дамбы наливного хвостохранилища, находящейся под напорным воздействием хвостов, может привести к существенному экологическому ущербу за счет попадания в поверхностные водотоки значительной массы жидкой фазы и иловой фракции мелкоизмельченной руды.
Два других рассматриваемых способа складирования не имеют напорных дамб, хвосты в хвостохранилище находятся в компактном виде, не способном к миграции, растворы собираются в прудке, выполненном в виде выемки в грунте, обвалованной устойчивыми бермами. Разрушение ограждающей дамбы при сейсмических ударах или диверсиях не приведет к попаданию твердых и жидких хвостов в окружающую среду. Именно эти способы рассмотрены более подробно для определения целесообразности их применения на проектируемом золотодобывающем предприятии и выбора проектного варианта.
Оба рассматриваемых способа складирования являются относительно новыми. В России «полусухое» складирование применяется только на одном объекте – золотоизвлекательной фабрике месторождения Кубака (Магаданская область). Сложность его применения заключается в правильном выборе материала фильтрующей дамбы, представляющего собой специально подготовленную шихту с достаточно строгим соотношением гальки и песка раз личного гранулометрического состава. При отклонениях состава материала дамбы либо ухудшается фильтрация жидкой фазы, либо через дамбу начинает просачиваться замутненныйслив, что приводит к нарушению работы гидротехнического сооружения.
«Сухое» складирование в России более распространено – по этой технологии работает несколько предприятий - золотоизвлекательные фабрики на месторождениях «Рябиновое» и «Тас-Юрях» артели старателей Амур, Хабаровский край, золотоизвлекательная фабрика на месторождениях «Валунистое», Чукотка (артель старателей «Чукотка»), ЗИФ месторождения Березитовое, Амурская область. За рубежом этот метод также распространен, в частности, большинство золотоизвлекательных фабрик КНР практикуют складирование хвостов цианирования в виде кеков. Достоинством «сухого» складирования является относительная простота и надежность. По сравнению с «полусухим» складированием не требуется подбора и точного дозирования флокулянтов на операцию сгущения, подготовки галечно-песчаных фракций определенного состава и составления шихты для фильтрующих дамб, постоянно наращиваемых по мере заполнения хвостохранилища.
С экологической точки зрения метод «сухого» складирования более безопасен, нагрузка на хвостохранилище по жидкой фазе и содержащимся в ней техногенным веществам минимальна, последствия аварийных ситуаций наименьшие из всех известных способов складирования. Предварительные расчеты показывают, что стоимость строительства, оборудования и эксплуатационные затраты по обоим рассматриваемым методам близки.
Изложенное выше, позволяет рекомендовать для проектируемого предприятия метод «сухого» складирования хвостов цианирования, как наиболее экологически безопасный.
Организация хранения отработанных хвостов при любом варианте складирования предполагает защиту поверхностных и подземных вод от неорганизованных сбросов. Для организации такой защиты рекомендуется хвостохранилище оборудовать сплошным противофильтрационным экраном из полимерных материалов, организовать забор осветленной жидкой фазы для повторного использования на золотоизвлекательной фабрике и регулируемый сброс излишков воды в случае их образования за счет выпадения атмосферных осадков (превышения осадков над испарениями) через узел обезвреживания.
Варианты организации противофильтрационного экрана. Для сооружения противофильтрационного полимерного экрана необходима организация выровненной и утрамбованной поверхности ложа хвостохранилища - отвала. Наиболее оптимальным является строительство основания экрана из мелкой песчаной фракции.
Выполнение гидроизоляционных работ до сих пор регламентируется инструкцией от 1982г. СН 551-82 «Инструкция по проектированию и строительству противофильтрационных устройств из полиэтиленовой пленки для искусственных водоемов», в которой не рассматриваются новые материалы, разработанные и нашедшие применение в последнее время. В соответствии с рекомендациями этого документа для создания подстилающего слоя следует применять песчаные грунты с максимальной крупностью до 5 мм. Использование галечно-эфельных материалов старых дражных выработок не противоречат этим рекомендациям. Применение дробленого материала с крупнозернистыми частями не окатанной формы СН не рекомендуется. Однако, в последнее время промышленностью налажен выпуск специальных материалов, защищающих пленочные покрытия от механических повреждений. В частности, достаточно широкое применение получили нетканые геотекстильные материалы «Дорнит», позволяющие организовывать сооружение полимерных композиций на основаниях из дробленого материала.
В рассматриваемых условиях толщина пленки не превышает 1 мм и в принципе по расчетам вполне работоспособен однослойный экран. Однако, для повышения экологической надежности работы хвостохранилища кеков цианирования рекомендуется применить комбинированную четырехслойную конструкцию, состоящую из подложки - мягкого нетканого геотекстильного полотна "Дорнит" плотностью 350 – 550 г/м2, двойного слоя сваренного полиэтиленового листа толщиной 1 – 1,5 мм с прокладкой между слоями мягкого нетканого геотекстильного полотна "Дорнит" плотностью 350 – 550 г/м2.
Полимерные пленки для противофильтрационных экранов выпускаются как российскими, так и зарубежными производителями. На отечественных золотодобывающих предприятиях наибольшее распространение получили полиэтиленовые геомембраны фирмы «Техполимер» (г. Красноярск), применение которых на многих предприятиях для гидроизоляции хранилищ материалов и отходов, в том числе цианидсодержащих, до сих пор не вызывало нареканий. Достоинством фирмы «Техполимер» является самостоятельное выполнение работ по укладке и сварке экранов обученными и квалифицированными специалистами с использованием современного оборудования и приемов работы.
Варианты обезвреживания сточных вод. Сточные воды золотоизвлекательных фабрик, применяющих в качестве растворителя золота цианистые соединения, содержат цианиды, тиоцианаты, металлы в виде цианидных комплексов, являющиеся высокотоксичными веществами, подлежащими обезвреживанию.
Методов обезвреживания цианидсодержащих сточных вод известно достаточно много: хлорирование /86, 87/, обработка смесью диоксида серы и воздуха /88, 9/, обработка пероксидом водорода /90, обработка формальдегидом /90/, обработка железным купоросом /86/, озонирование /91/, окисление кислородом воздуха /92/, ионообменная очистка /93/, биологическая очистка /94/ и др. Многие из перечисленных выше методов хотя и обладают способностью удалять (разрушать) цианиды из жидкой фазы, однако имеют низкую эффективность или высокую стоимость и по этой причине в промышленных масштабах не применяются.
В настоящее время в мировой практике для обезвреживания цианидсодержащих техногенных отходов золотоизвлекательных фабрик в основном используются три технологии:
- хлорирование с использованием гипохлорита кальция;
- обработка смесью диоксида серы и воздуха (INCO-технология);
- обработка формальдегидом.
Процесс хлорирования позволяет обезвреживать практически все токсичные соединения, присутствующие в сточных водах – цианиды, тиоцианаты, цианидные комплексы металлов.
Хлорирование является достаточно простым процессом в технологическом и аппаратурном отношениях – процесс заключается во введении в обезвреживаемые хвосты приготовленного раствора гипохлорита кальция и известкового молока (либо раствора гидроксида натрия). Подача реагентов достаточно просто управляется в автоматическом режиме по окислительно-восстановительному потенциалу и рН.
INCO-технология, заключающаяся в обработки цианидсодержащих отходов смесью SO2 и воздуха, также основана на окислении цианидов. Химизм процесса достаточно сложен и состоит из нескольких стадий с участием катализатора. Суммарная реакция приведена ниже:
СN- + SO2 + O2 + H2O + катализатор = CNO- + H2SO4 + катализатор (6.1.5)
Катализатором традиционно является медь, либо присутствующая в обезвреживаемых хвостах, либо вводимая в виде CuSO4. В качестве донора SO2 наиболее часто используют метабисульфит натрия (Na2S2O5).
При обработке сточных вод по этой технологии происходит удаление части металлов с ферроцианидами. Тиоцианаты при обработке отходов смесью SO2/воздух практически не обезвреживаются.
Процесс протекает в щелочной среде (рН = 8 – 9), для подщелачивания обычно используют известь.
INCO-технология более сложна технологически и аппаратурно, чем хлорирование, однако отличается меньшими затратами на реагенты. Основным недостатком этой технологии является невозможность обезвреживания тиоцианатов, на которые в России установлены нормы ПДК (0,09 мг/л), сравнимые с ПДК на цианиды. Для обезвреживания отходов процесса цианирования руды месторождения Рябиновое данная технология не пригодна.
Технология обработки формальдегидом основана на реакции циангидрирования:
OH-CH2-CN + 2H2O = HOCH2COOH + NH3 (6.1.8)
Эта технология, разработанная ОАО «Иргиредмет», выгодно отличается простотой и низкими эксплуатационными затратами. Однако, она не способна обезвреживать тиоцианаты, цианидные комплексы меди, и применяется на предприятиях, перерабатывающих не сульфидные и мало сульфидные руды. Для обезвреживания отходов процесса цианирования руды месторождения Рябиновое данная технология не пригодна.
Таким образом, в настоящее время практически единственным процессом обезвреживания цианидсодержащих отходов, по эффективности соответствующим действующим в России экологическим требованиям по отношению к цианидам и тиоцианатам, является хлорирование. Именно эта технология рекомендуется к применению для обезвреживания цианидсодержащих отходов процесса гидрометаллургической переработки руд месторождения Рябиновое.