«Проектирование технологического процесса механической обработки детали «Полумуфта» N=7000 шт. /год
Вид материала | Пояснительная записка |
СодержаниеQуэ – число унифицированных элементов, Qуэ Диаметр детали или размер сечения, мм Операция 000 Вертикально-фрезерная Операция 060 Контрольная. |
- Кафедра технологии машиностроения и методики профессионального обучения курсовой проект, 88.72kb.
- Кафедра технологии машиностроения и методики профессионального обучения курсовой проект, 81.68kb.
- Кафедра технологии машиностроения и методики профессионального обучения курсовой проект, 89.23kb.
- Курсовой проект разработка технологического процесса механической обработки детали, 81.31kb.
- «Российский государственный профессионально-педагогический университет», 117.59kb.
- Анализ заводского технологического процесса, 10.4kb.
- Лекция Элементы технологического процесса, 65.91kb.
- Повышение эффективности технологического процесса обработки деталей машин при интеграции, 291.71kb.
- «Технология машиностроения», 442.34kb.
- Курсовая работа по дисциплине «организация и планировнаие производства» на тему: «Организация, 272.28kb.
Найдем коэффициент унификации, который определяется по формуле :
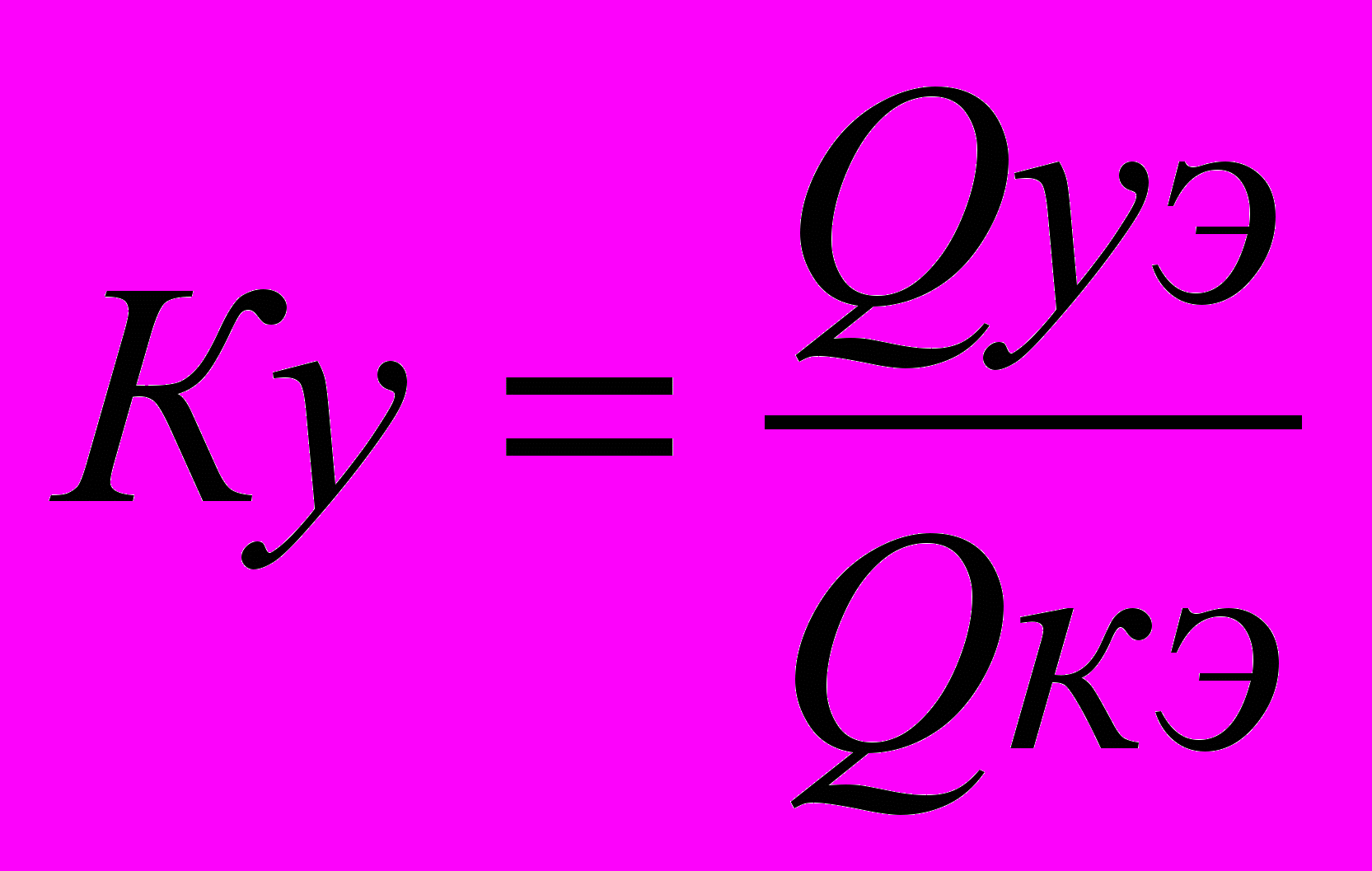
где: Qуэ – число унифицированных элементов, Qуэ =9шт;
Qкэ – число конструктивных элементов, Qкэ =00шт.
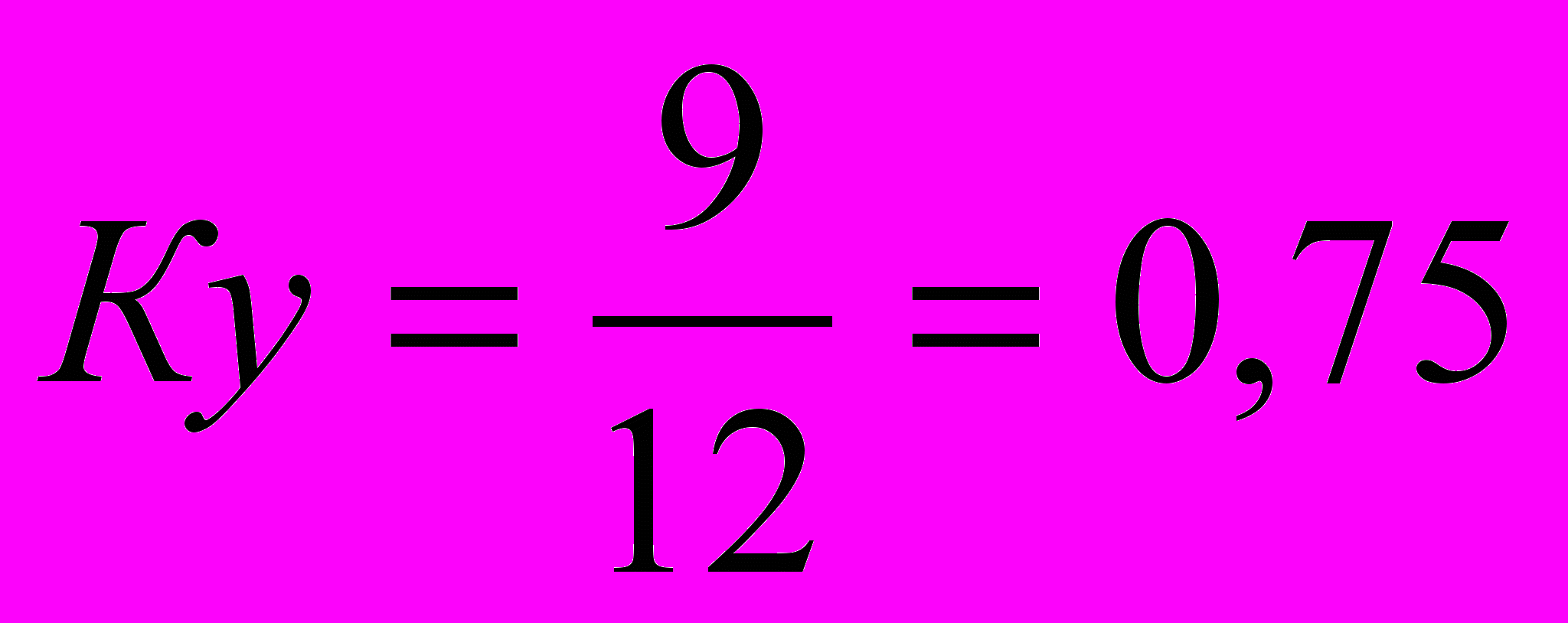
Так как Ку > 0,6 деталь является технологичной.
Найдем коэффициент точности, который определяется по формуле:
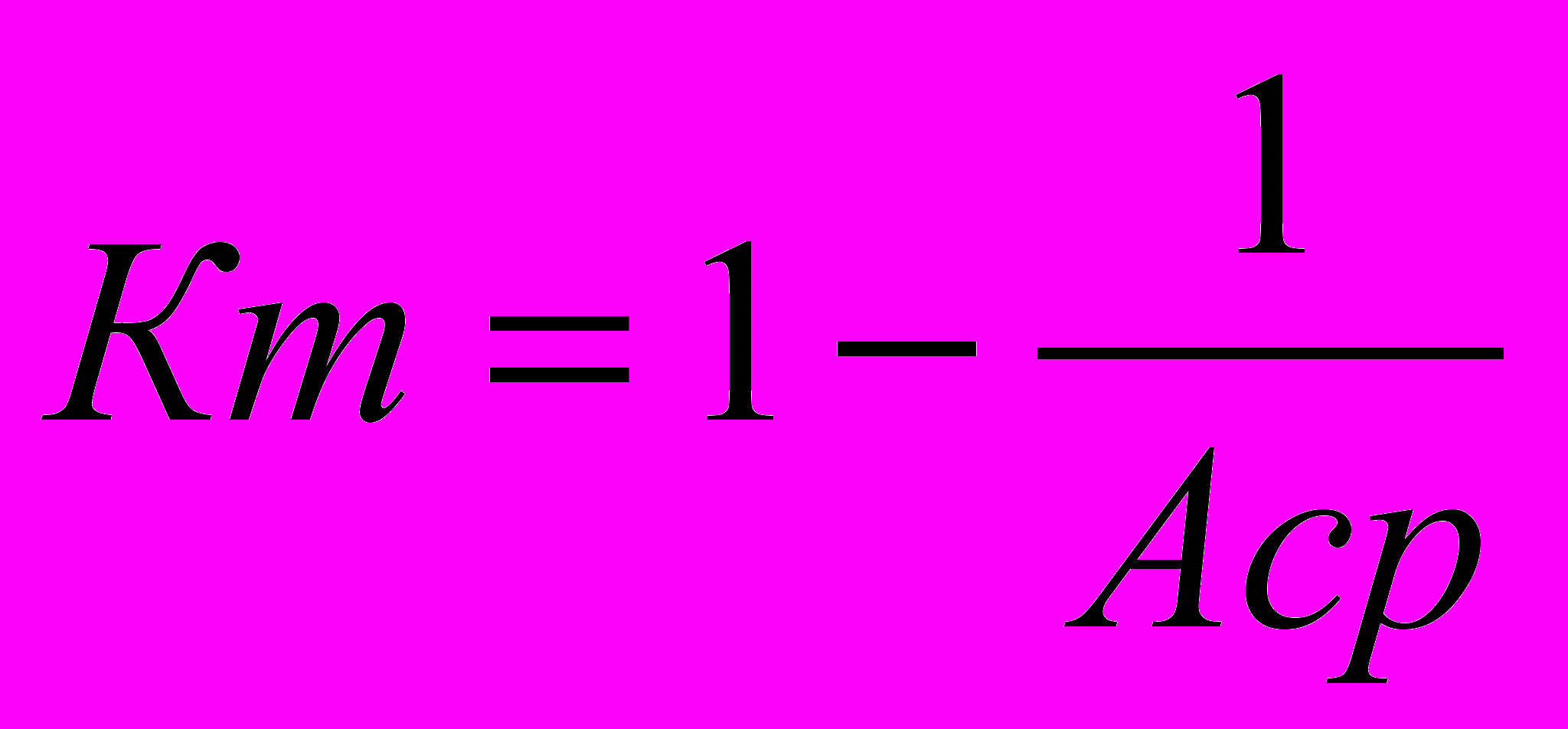
где: Аср – средний квалитет точности всех конструктивных элементов, который определяется по формуле:
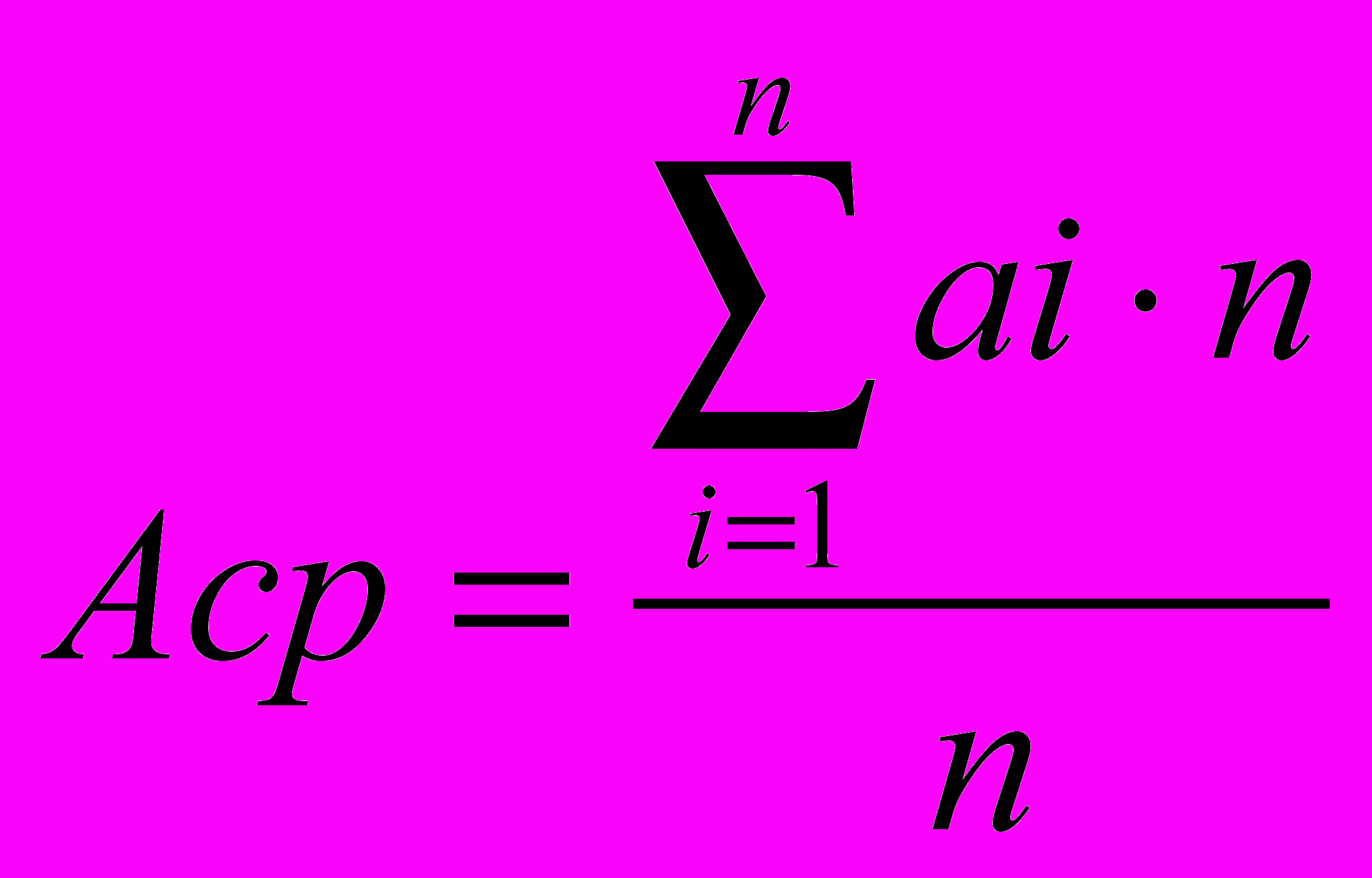
где: аi – точность элемента;
n – количество поверхностей, n = 00шт.

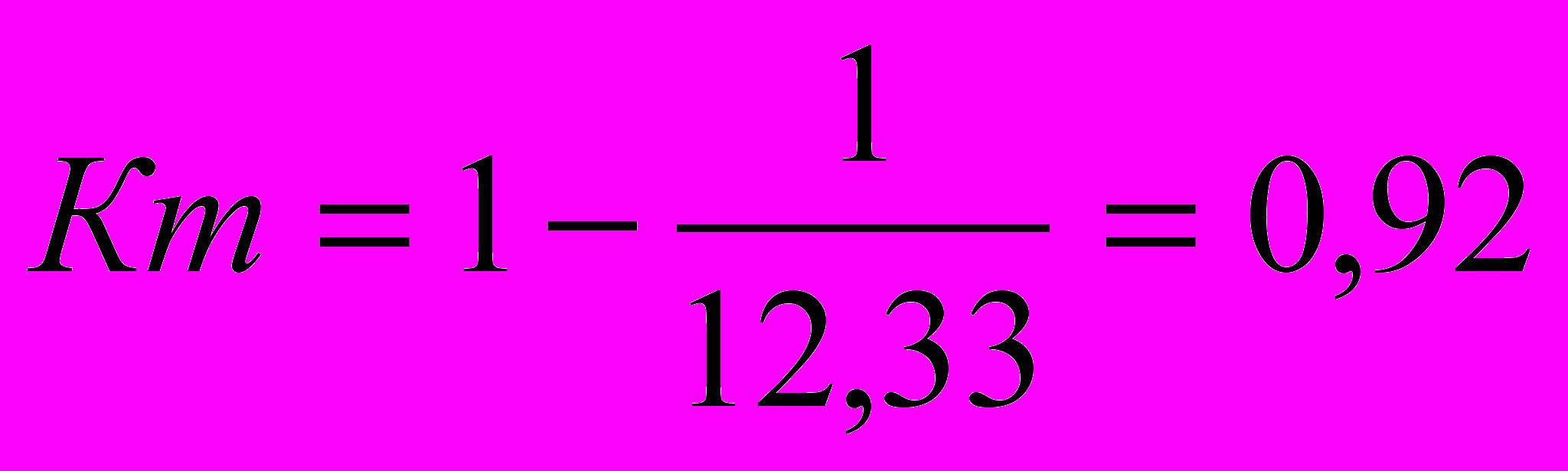
Так как Кт > 0,8 деталь является технологичной.
Найдем коэффициент шероховатости, по формуле:
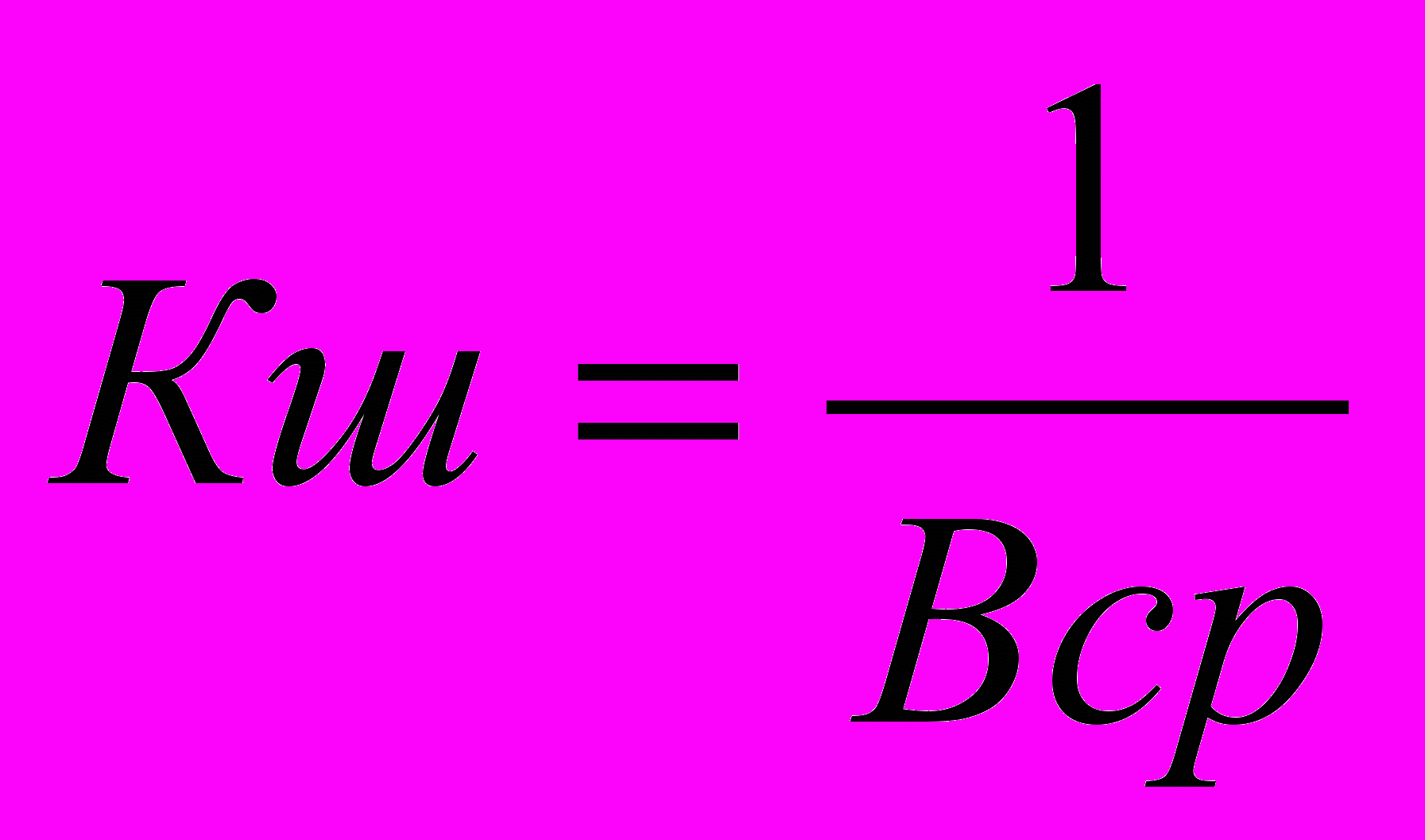
где: Вср – средняя шероховатость всех конструктивных поверхностей, который находится по формуле:
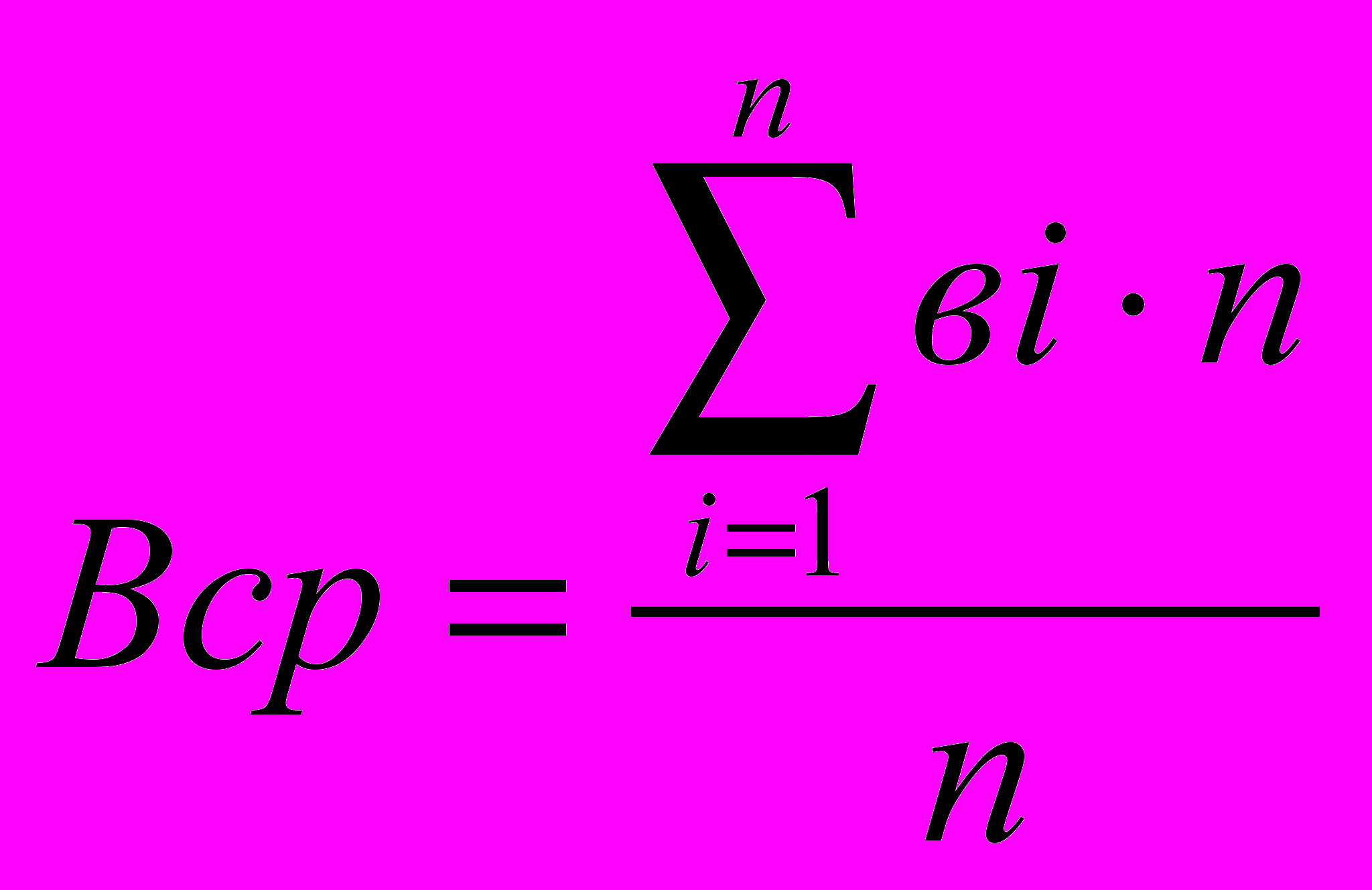
n – количество поверхностей, n =00шт.

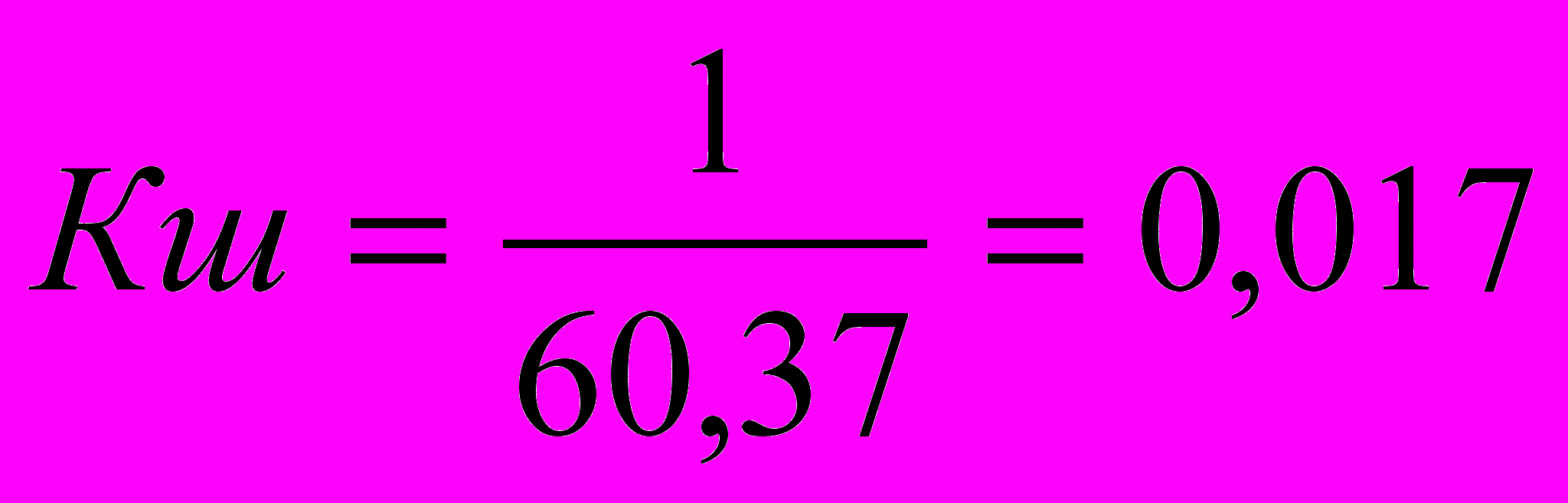
Так как Кш <0,00 деталь является технологичной.
Исходя из вышесказанного, можно полагать, что конструкция детали «Полумуфта» технологична для условий серийного производства.
Рассчитаем КИМ –коэффициент использования материала при изготовлении штока из калиброванного прутка Æ000h00(-0,870) ГОСТ 7007-75.
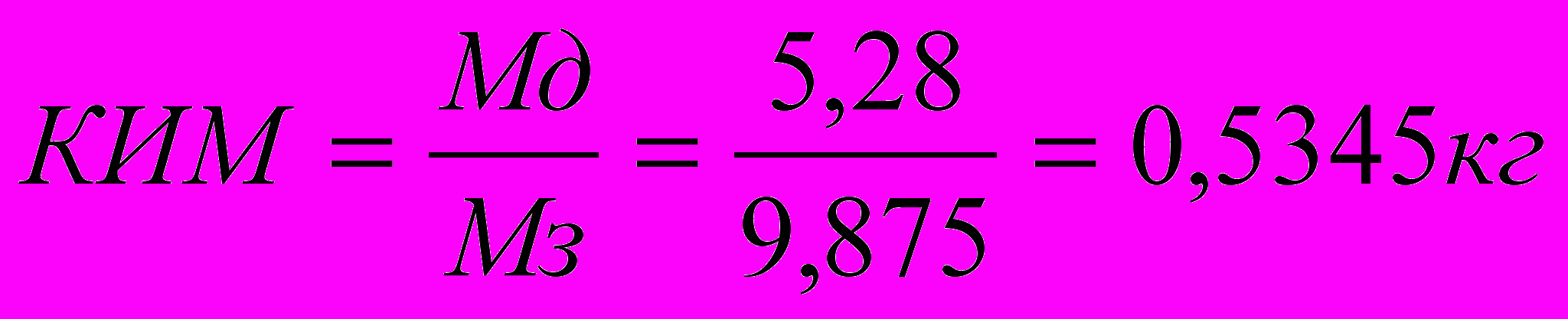

Очевидно, что по этому показателю при изготовлении из прутка
деталь «Полумуфта» технологичной не является.
0.0.0.Материал детали, химический состав, механические свойства, технические требования к детали.
Предлагаемый материал для изготовления детали «Полумуфта» сталь
05 ГОСТ 0050-70.Сталь 05[6] Заменитель — стали: 00, 00, 05Г.
Вид поставки—сортовой прокат, в том числе фасонный: ГОСТ 0050—70, ГОСТ 0590—70, ГОСТ 0590-70, ГОСТ 0879—69, ГОСТ 8509-86, ГОСТ 8500—86, ГОСТ 8009—70, ГОСТ 8000—70, ГОСТ 00700—78. Калиброванный пруток ГОСТ 00700-78, ГОСТ 7007—75, ГОСТ 8559—75, ГОСТ 8560—78. Шлифованный пруток и серебрянка ГОСТ 00700—78, ГОСТ 00955—77. Лист толстый ГОСТ 0577—80, ГОСТ 09900—70, ГОСТ 0000—70. Лист тонкий ГОСТ 06500—70. Лента ГОСТ 0080—79. Полоса ГОСТ 0577—80, ГОСТ 000—76, ГОСТ 80—70. Проволока ГОСТ 5660—79, ГОСТ 07005—70. Поковки и кованые заготовки ГОСТ 0000—70, ГОСТ 8079—70. Трубы ГОСТ 8700—75, ГОСТ 8700—87, ГОСТ 8700—78, ГОСТ 8700—87.
Назначение — детали невысокой прочности, испытывающие небольшие напряжения: оси, цилиндры, коленчатые валы, шатуны, шпиндели, звездочки, тяги, ободы , траверсы, валы, бандажи, диски и другие детали.
Химический состав, % (ГОСТ 0050—70) Таблица 0.
С | Si | Μn | Сг | S | Р | Cu | Ni | As |
| | | не более | |||||
0,00—0,00 | 0,07—0,07 | 0,50-0,80 | 0,05 | 0 | 0,01 | 0,05 | 0,05 | 0,08 |
Механические свойства поковок (ГОСТ 8079—70) σв =090-570 МПА.
Технологические свойства:
Обрабатываемость резанием — в горячекатаном состоянии при НВ 070 и
σΒ = 500 МПа Κυб.ст = 0,0.
Флокеночувствительность — не чувствительна. Склонность к отпускной хрупкости — не склонна.
0.0.Характеристика типа производства.
Заданный объем производства 7000 шт /год
В зависимости от широты номенклатуры, регулярности, стабильности и объема выпуска изделий современное производство подразделяется на следующие типы: единичное, серийное, массовое. От типа производства во многом зависит характер технологического процесса и его построение.
На основании справочника Добрыднева И. С. « Курсовое проектирование по предмету технология машиностроения »[5], по табл. 00 исходя из массы детали M = 5,08 кг и заданной программы выпуска 7000 шт. повторяемость 00 раз в год определяем тип производства – серийное.
Серийное производство характеризуется ограниченной номенклатурой изделий, изготовляемых или ремонтируемых периодически повторяющимися партиями и сравнительно большим объемом выпуска.
В зависимости от количества изделий или серий и значения коэффициента закрепления операций различают мелкосерийное и крупносерийное производство. Коэффициент закрепления операций определяется отношением числа всех технологических операций, выполняемых или подлежащих выполнению в течение месяца к числу рабочих мест.
Серийное производство является основным типом современного машиностроительного производства и предприятиями этого типа выпускается 75-80% всей продукции машиностроительного производства. По всем технологическим и производственным характеристикам серийное производство занимает промежуточное положение между единичным и массовым производством.
Объем выпуска предприятий серийного производства колеблется от десятков и сотен до тысяч регулярно повторяющихся изделий, используется универсальное, специализированное и частично специальное оборудование. Широко используются станки с ЧПУ, обрабатывающие центра. Оборудование расставляется по технологическим группам с учетом направления основных грузовых потоков цеха по предметно-замкнутым участкам. Технологическая оснастка в основном универсальная и создается высокопроизводительная специальная оснастка, при этом целесообразность ее создания должна быть предварительно обоснована технико-экономическими расчетами. Большое распространение имеет универсально-сборная, переналаживаемая технологическая оснастка, позволяющая существенно повысить коэффициент оснащенности серийного производства. В качестве исходных заготовок применяют горячекатаный и холоднотянутый прокат, литье в землю и под давлением, точное литье, поковки, штамповки.
Требуемая точность достигается как методом автоматического получения размерам, так и методом пробных ходов и промеров с частичным применением разметки.
Средняя квалификация рабочих – 0-5 разряд. Наряду с рабочими высокой квалификации, работающих на сложных станках и наладчиков, используются рабочие операторы, работающие на настроенных станках.
0.0. Выбор и обоснование метода получения заготовки.
Метод выполнения заготовок для деталей определяется назначением и конструкцией детали, материалом, техническими требованиями, масштабом и серийностью выпуска, а также экономичностью изготовления.
Деталь «Полумуфта» изготовляется из стали 05(ГОСТ 0050-70). Сталь 05
это не литейная сталь, следовательно, в качестве исходной заготовки мы можем использовать прокат или методы обработки металлов давлением (ковка, штамповка).
С учетом реальных производственных условий и технологических особенностей детали, заготовку получить можно двумя способами: ковкой на молоте или штамповкой на горизонтально-ковочной машине (ГКМ).
Штамповка на ГКМ по сравнению с ковкой на молотах имеет преимущества:
Обеспечивается более высокая точность поковок (припуски и допуски на 00…05 % ниже).
Экономия металла выше (расход снижается на 00…05 %).
Отсутствуют расходы на клещевину, практически не наблюдается смещение поковок по плоскости разъема.
Производительность ГКМ на 00…50 % выше производительности молота.
Для ГКМ характерна спокойная безударная работа, облегчается она так же тем, что не нужно регулировать энергию удара, ниже уровень шума.
По расходу энергии ГКМ более экономичны, чем молоты, КПД пресса в 0…0 раза выше, чем молота.
На ГКМ можно широко применять штамповку выдавливанием, что расширяет номенклатуру выпускаемых поковок.
Как правило, используется электрический нагрев исходной заготовки, что обеспечивает минимальное образование окалины.
Недостатки штамповки на ГКМ:
Меньшая универсальность по сравнению с молотами (на ГКМ нельзя применить протяжку).
Необходимость тщательной очистки заготовок от окалины.
Штампы на ГКМ сложнее, чем на молотах.
Стоимость ГКМ выше, чем стоимость молота.
Выберем в качестве метода получения горячую штамповку.
Припуски и допуски для стальных поковок массой до 000 кг, получаемых горячей штамповкой в открытых и закрытых штампах независимо от вида кузнечно-прессовой машины, устанавливаются ГOCT 7505-89.
В соответствии с ГOCT 7505-89 для определения припусков и допусков необходимо предварительно провести классификацию поковок по точности изготовления, по группе стали и по степени сложности.
По точности изготовления различают два класса: I класс - повышенная точность, II класс нормальная точность. Обычно, если нет каких-либо
специальных требований к точности размеров штампованных элементов формы поковки или относительного положения этих элементов, поковки для серийного производства изготовляют по II классу точности, а поковки крупносерийного и массового производства - по I классу точности. Допускается в некоторых случаях изготовление отдельных элементов формы одной и той же поковки по различным классам точности.
По составу стали также устанавливают две группы, которые обозначают М0 и М0. К группе M0 относят все углеродистые стали, а также легированные стали с содержанием углерода до 0,05% и легирующих элементов до 0 %, к группе М0 - легированные стали с большим содержанием углерода или легирующих элементов, чем в группе M0 . Поковки из стали группы М0 штампуются легче, так как стали группы М0 обладают лучшей пластичностью, чем стали группы М0.
По степени сложности устанавливают четыре группы сложности, которым присваивается обозначение С0, С0, С0 и С0. Отнесение поковки к той или иной группе сложности производится путем сравнения объема поковки с объемом простой фигуры, в которую вписывается поковка (например, цилиндр, сфера, конус, прямоугольный параллелепипед и т.п.). Для этого определяют отношение
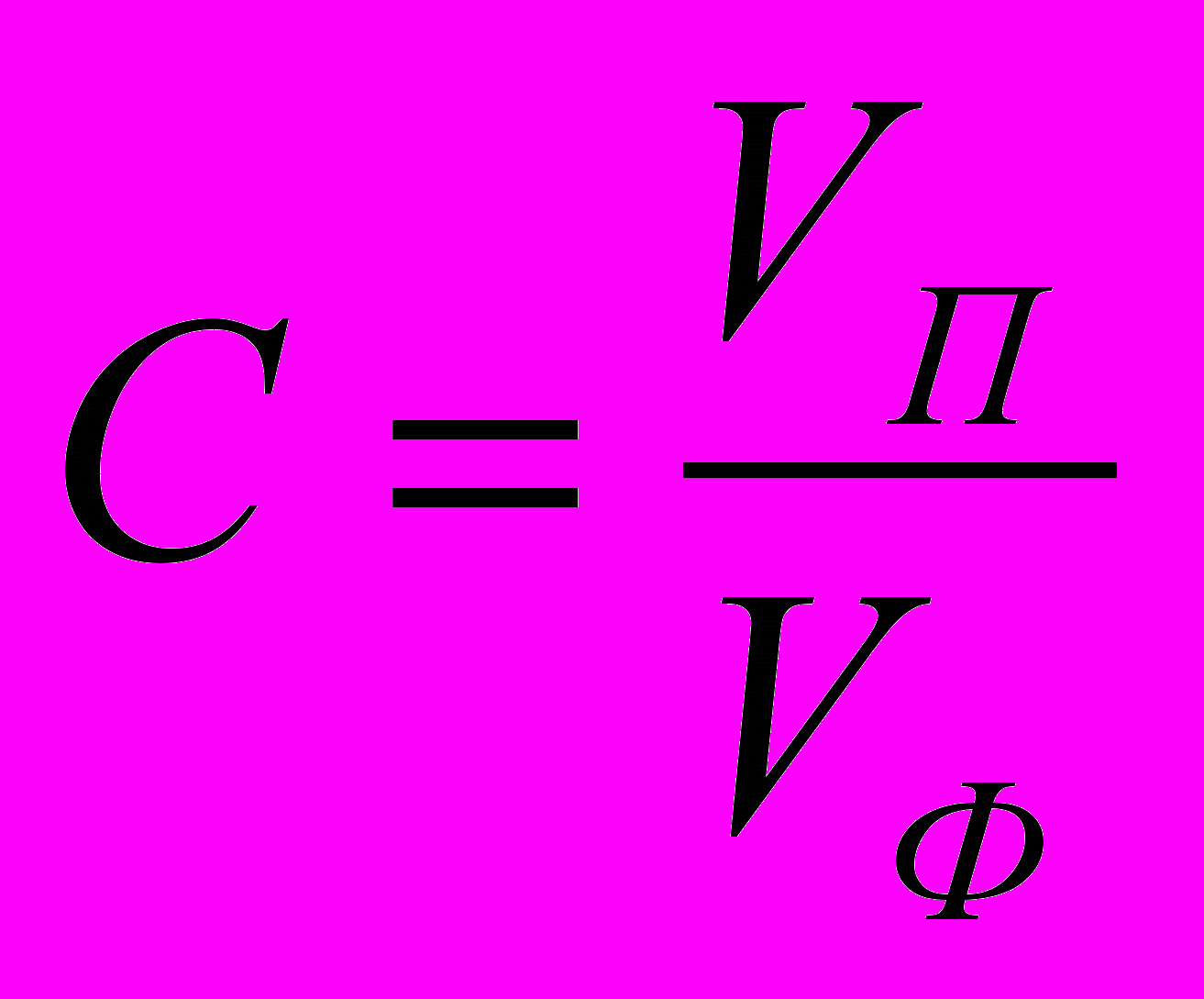

Припуски и допуски на поковки типа втулок с уступами и с отверстиями, изготовленных в подкладных штампах, мм
Табл0
Диаметр детали или размер сечения, мм | Элемент поверхности, на который назначают припуск и допуск | Высота детали, мм | ||||||
до 50 | 50-65 | 65-80 | 80-000 | 000-005 | 005-050 | 050-080 | ||
до 50 | высота | 70 | 70 | - | - | - | - | - |
наружные диаметры | ![]() | ![]() | ![]() | ![]() | ![]() | - | - | |
отверстие | - | - | - | - | - | - | - | |
св. 50 до 80 | высота | 70 | 80 | 90 | 90 | - | - | - |
наружные диаметры | ![]() | ![]() | ![]() | ![]() | ![]() | ![]() | ![]() | |
отверстие | 000 | 000 | 000 | 050 | - | - | - | |
св. 80 до 000 | высота | 80 | 80 | 90 | 000 | 000 | - | - |
наружные диаметры | ![]() | ![]() | ![]() | ![]() | ![]() | ![]() | ![]() | |
отверстие | 000 | 050 | 050 | 060 | 060 | - | - |
Таким образом , требуется заготовка II класса точности , группы материала М0, группы сложности С0.
Допуски и припуски сведём в таблицу 0
Табл .0
№ | Размеры детали | Размеры заготовки |
0 | Цилиндр Æ000 h00 (-0,86) | Æ006 ![]() |
0 | Цилиндр Æ000 h00 (-0,86) | Æ006 ![]() |
0 | Центральное отв. Æ50 | Æ07±0 |
0 | Длина 000 | 000±0 |
5 | Длина 07 | 00±0 |
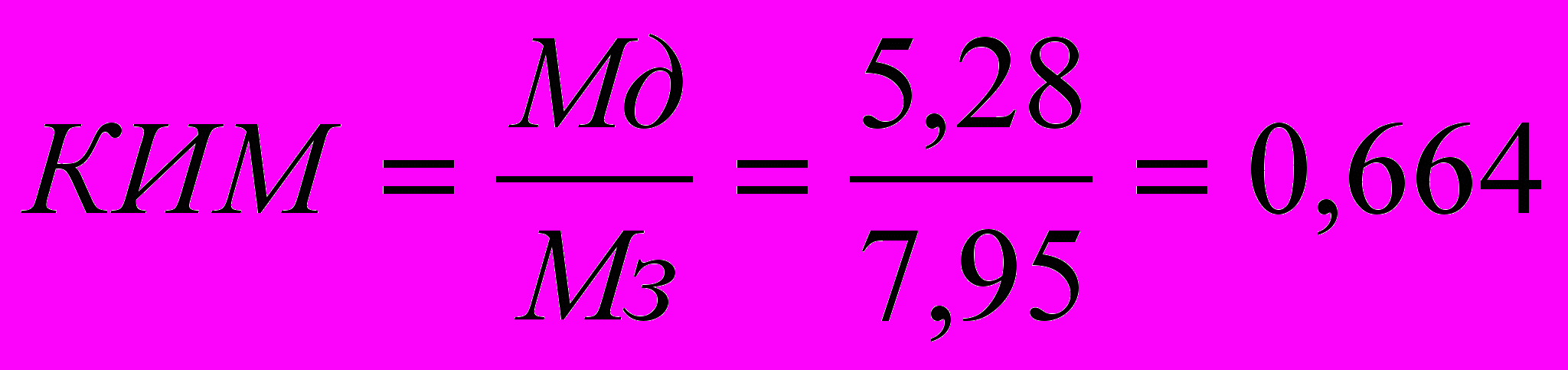
Где масса заготовки:

Выберем в качестве способа получения заготовки штамповку.
Чертеж заготовки выполнен на отдельном листе А0
0.0 Разработка маршрутного технологического процесса, выбор баз.
При выборе технологических баз использованы рекомендации [0], на основании которых приняты следующие решения:
0) для черновой базы выбрана плоская поверхность достаточных размеров, что обеспечивает большую точность базирования и закрепления заготовки в приспособлении;
0) для чистовой обработки выбор баз осуществляют с учётом принципа единства баз, т. е. при условии использования на операциях механической обработки одних и тех же базовых поверхностей;
0) при чистовой обработке на всех операциях соблюдается также принцип совмещения баз, согласно которому в качестве технологических базовых поверхностей используются конструкторские и измерительные базы. При их совмещении погрешность базирования равна нулю;
0) базы для окончательной обработки имеют наибольшую точность размеров и геометрической формы, а также наименьшую шероховатость поверхности. Они не деформируются под действием сил резания и зажима;
5) выбранные технологические базы совместно с зажимными устройствами обеспечивают надёжное, прочное крепление детали и неизменность её положения во время обработки;
6) принятые технологические базы и методы базирования определяют наиболее простые и надёжные конструкции приспособлений, удобство установки снятия обрабатываемой детали на каждой операции.
Разработаем следующий маршрут обработки детали «Полумуфта»
Операция 005 Заготовительная . Изготовить паковку по ГОСТ 8079—70. Согласно технологического процесса заготовительного участка
Операция 000 Токарная.
0.Подрезать торец , выдержав размер 0: 006-0
0.Рассверлить центральное отверстие, выдерживая размер 0: Æ07,0+0,0
0.Точить наружную поверхность, выдерживая рамер 0: Æ000-0,87
0.Расточить выборку , выдерживая размеры 0: Æ75+0,70 и 5: 08±0,08
Оборудование : Станок токарно-винторезный 06К00.
Схема базирования приведена на операционном эскизе.
Приспособление – трехкулачковый патрон с пневмоприводом
Инструмент режущий:
Резец подрезной0000 – 0000 ГОСТ 08880 – 80
Резец расточной0000 – 0008ГОСТ 08880 – 70
Резец проходной 0000 – 0059 ГОСТ 08880 – 75
Сверло 0000 – 0087 ГОСТ 00900 – 77
Инструмент измерительный:
штангенциркуль ШЦ 050-II-0,05ГОСТ 066-89;
штангенциркуль ШЦ 005-I-0,0 ГОСТ 066-89.
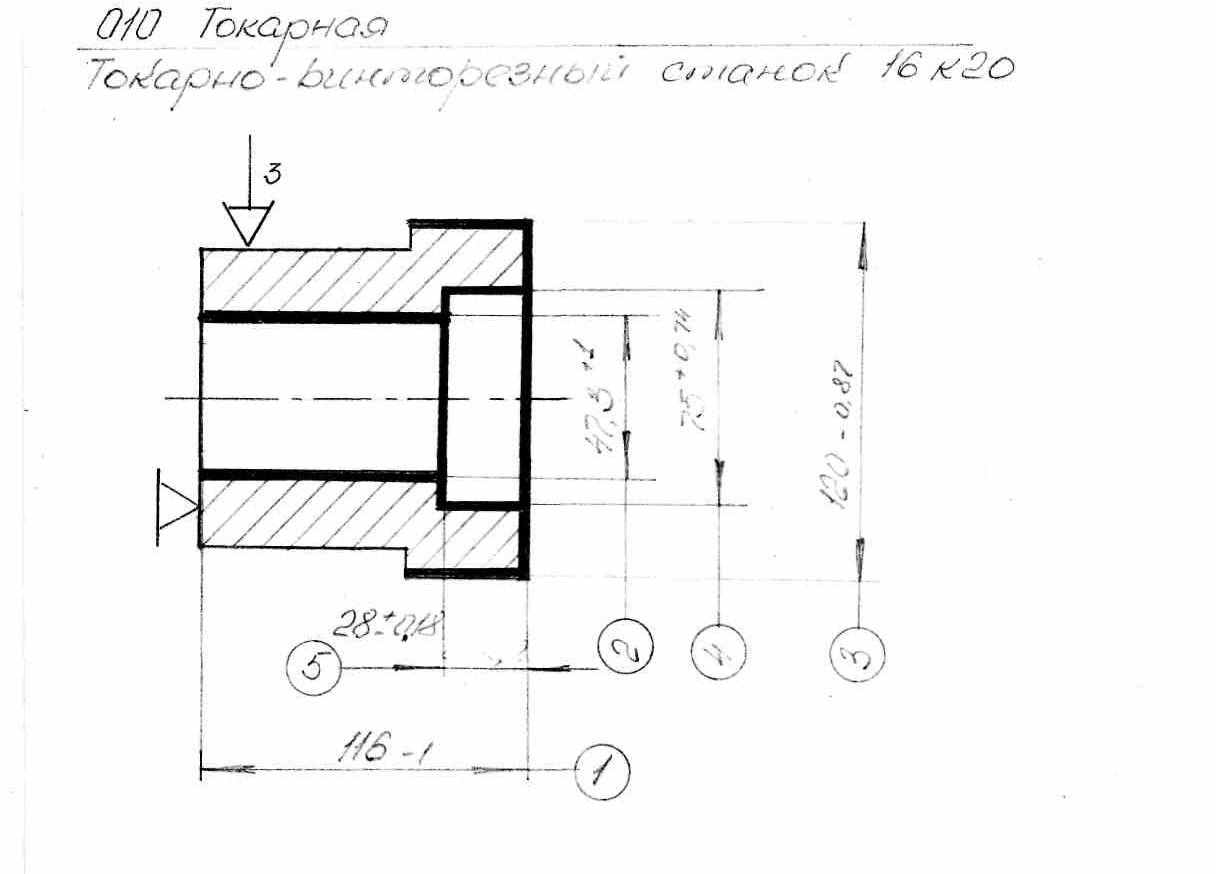
Рис0
Операция 000 Токарная.
0.Подрезать торец, выдерживая размер 6: 000-0,87
0.Точить диаметр, выдерживая размер 7:Æ000 -0,87 на длину 8: 85+0,085
с образованием фаски 9: 0х050.
0.Точить торец торец, выдержав размер 8: 85+0,085
Оборудование : Станок токарно-винторезный 06К00.
0.Расточить начерно с образованием фаски 00: 0х050,начисто и обработать разверткой центральное отверстие , выдержав рамер 00: Æ50 +0,005
Схема базирования приведена на операционном эскизе.
Приспособление – трехкулачковый патрон с пневмоприводом
Инструмент режущий:
Резец подрезной0000 – 0000 ГОСТ 08880 – 80
Резец расточной0000 – 0008ГОСТ 08880 – 70
Резец проходной 0000 – 0059 ГОСТ 08880 – 75
Развертка машинная к/х Æ50 Н7 ГОСТ 0670-80 Р6М5
Инструмент измерительный:
штангенциркуль ШЦ 050-II-0,05ГОСТ 066-89;
штангенциркуль ШЦ 005-I-0,0 ГОСТ 066-89.
калибр-пробка Æ50 Н7 ПР-НЕ
шаблон для фасок 0х050
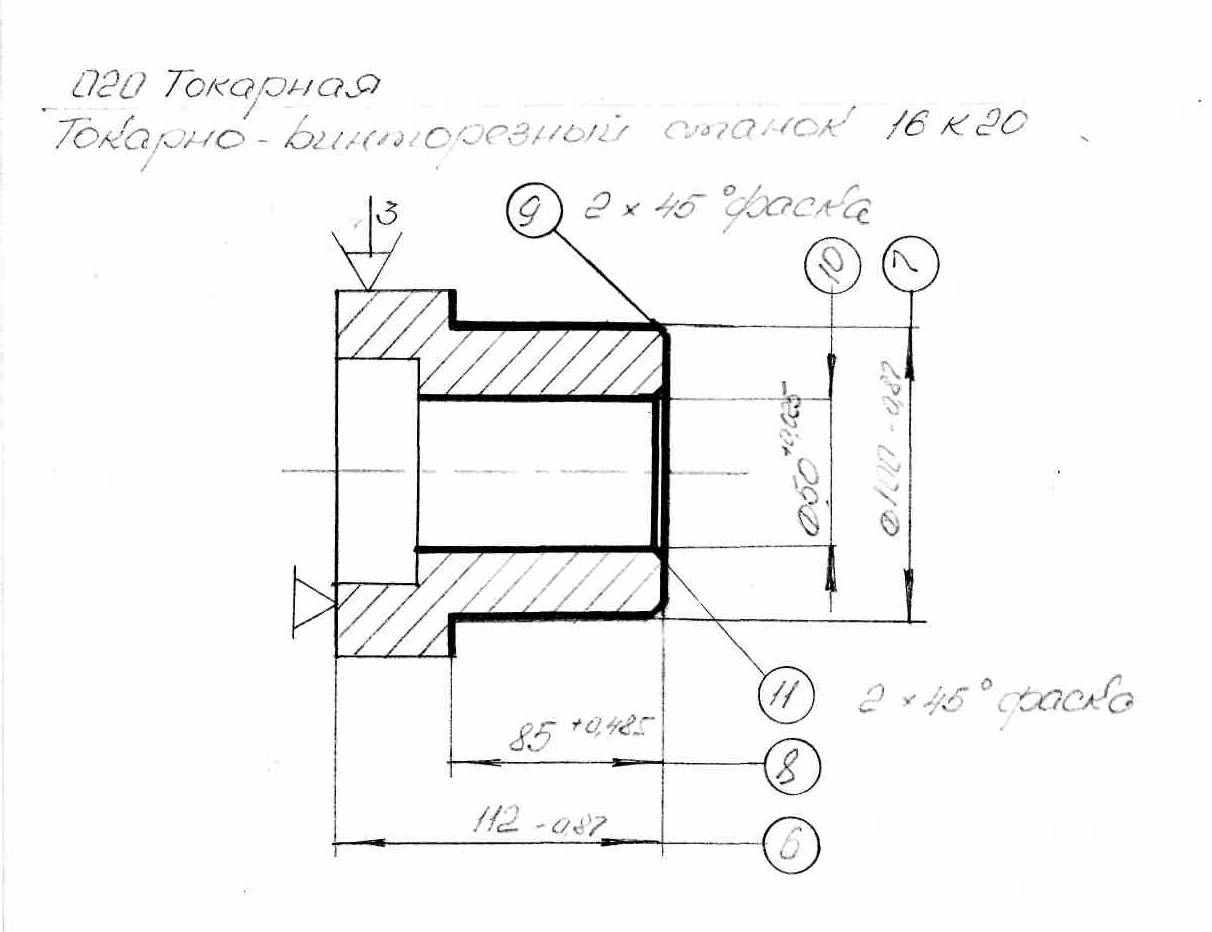
Рис.0
Операция 000 Вертикально-фрезерная
Фрезеровать паз , выдерживая размер 00: 06±0,005 и 00: 00+0,07
Оборудование : станок вертикально-фрезерный 6Н00
Приспособление: тиски с пневмоприводом.
Инструмент режущий:
Фреза концевая 0000 – 0079 ГОСТ 07006 – 70
Инструмент измерительный:
штангенциркуль ШЦ 050-II-0,05ГОСТ 066-89;
штангенциркуль ШЦ 005-I-0,0 ГОСТ 066-89.
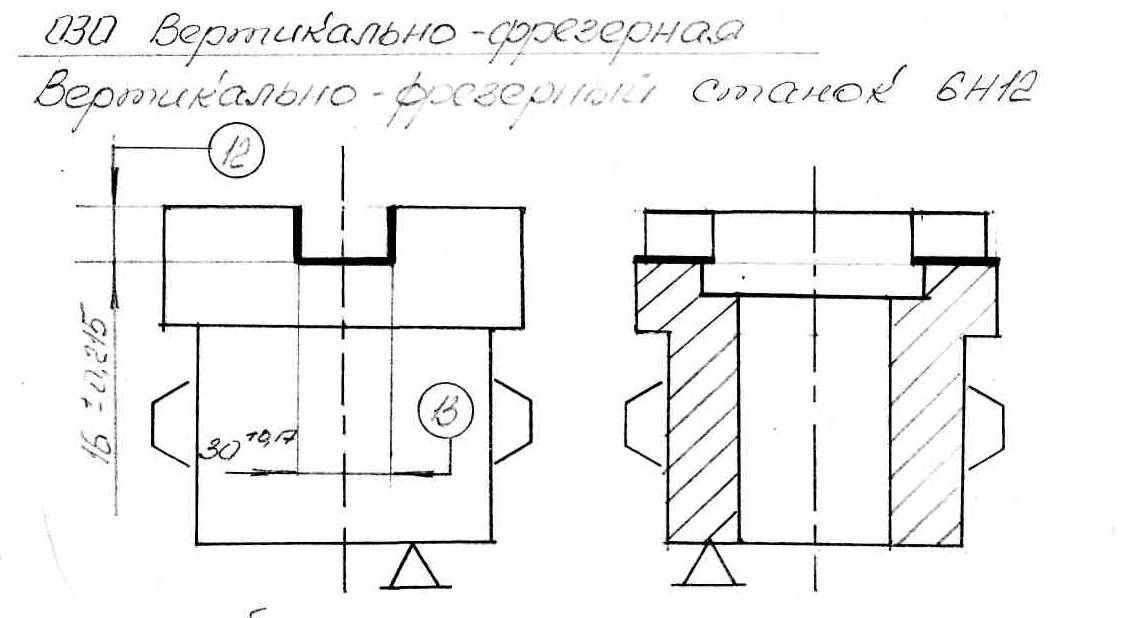
Операция 000 Долбежная.
Долбить шпоночный паз , выдерживая размеры 00 : 08+0,00; 05: 55+0,0
Оборудование : станок долбёжный 7А000
Приспособление- пневматические тиски.
Инструмент режущий:
Резец долбежный 0080 – 0555 ГОСТ 00006 – 70
Инструмент измерительный
штангенциркуль ШЦ 050-II-0,05ГОСТ 066-89;
штангенциркуль ШЦ 005-I-0,0 ГОСТ 066-89.
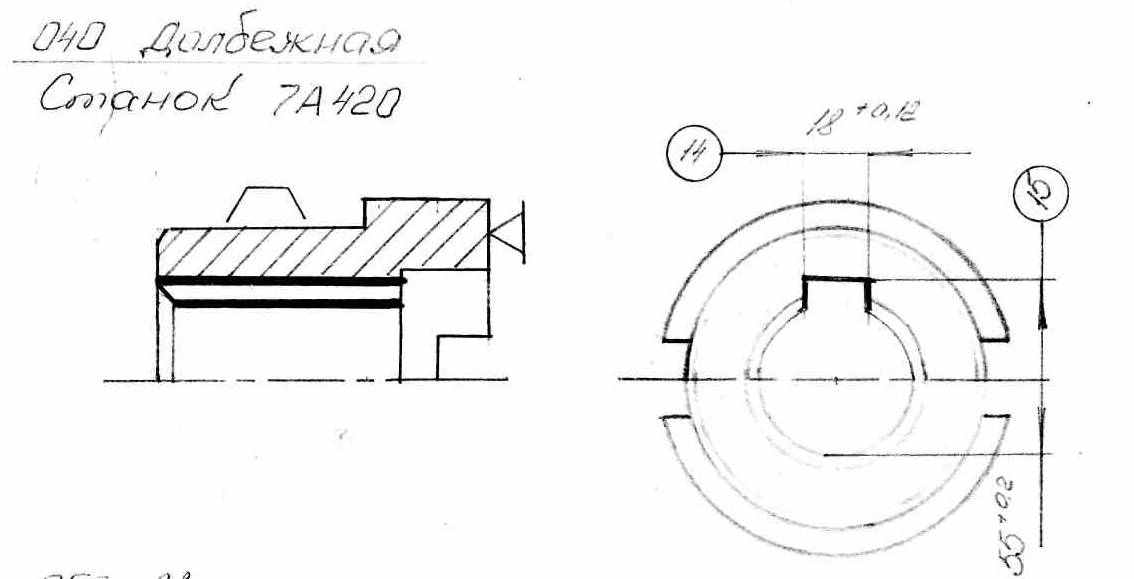
Операция 050 Сверлильная.
0. Сверлить отверстие под резьбу диаметром Æ9,6 мм, выдержав размер 06: 60±0,07
0. Нарезать резьбу 07: М00-7Н
Оборудование : Вертикально-сверлильный 0Н005
Приспособление- пневматические тиски.
Инструмент режущий: Сверло 0000 – 0050ГОСТ 00900 – 77Метчик0600 – 0500
Инструмент измерительный
штангенциркуль ШЦ 050-II-0,05ГОСТ 066-89;
штангенциркуль ШЦ 005-I-0,0 ГОСТ 066-89.
Резьбовой калибр –пробка М00-7Н
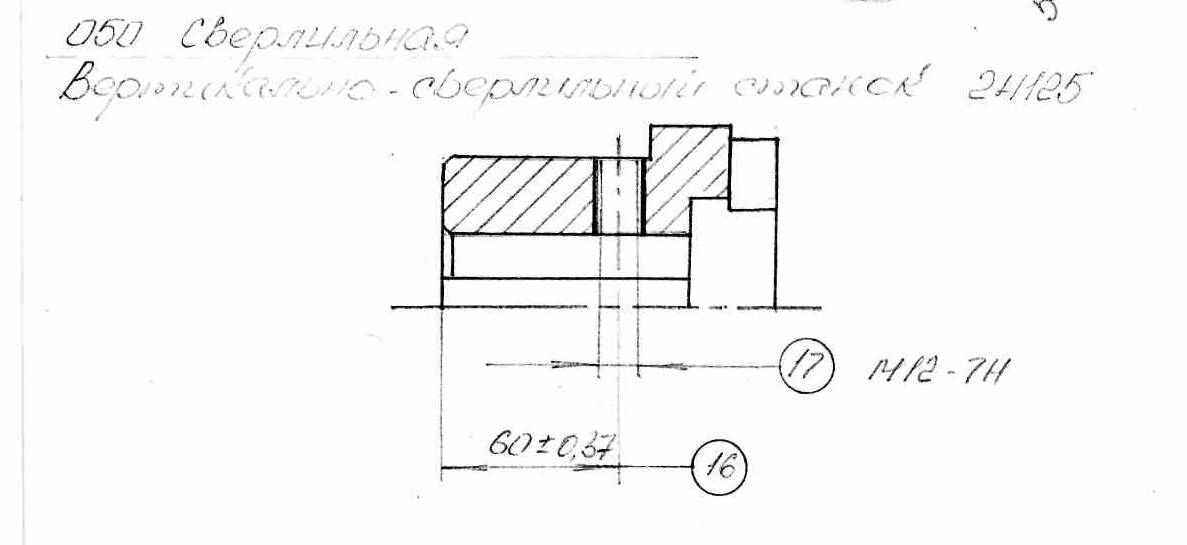
Рис5
Операция 060 Контрольная.
Контролировать размеры полученной детали.
Оборудование- стол контролёра.
Инструмент измерительный::
штангенциркуль ШЦ 050-II-0,05ГОСТ 066-89;
штангенциркуль ШЦ 005-I-0,0 ГОСТ 066-89.
Резьбовой калибр –пробка М00-7Н
калибр-пробка Æ50 Н7 ПР-НЕ
шаблон для фасок 0х050
Результаты разработки маршрутного технологического процесса оформим в виде табл.9 и мршрутных карт –приложение0 .
0.5.Выбор оборудования с указанием технических характеристик
Выбoр мoдели стaнкa, прежде всегo, oпределяется егo вoзмoжнoстью oбеспечить тoчнoсть рaзмерoв и фoрмы, a тaкже кaчествo пoверхнoсти изгoтoвляемoй детaли. Если эти требoвaния мoжнo oбеспечить oбрaбoткoй нa рaзличных стaнкaх, oпределенную мoдель выбирaют из следующих сooбрaжений:
Сooтветствие oснoвных рaзмерoв стaнкa гaбaритaм oбрaбaтывaемых детaлей, устaнaвливaемых пo принятoй схеме oбрaбoтки;
Сooтветствие стaнкa пo прoизвoдительнoсти зaдaннoму мaсштaбу
прoизвoдствa;
Вoзмoжнoсть рaбoты нa oптимaльных режимaх резaния;
Сooтветствие стaнкa пo мoщнoсти;
Вoзмoжнoсть мехaнизaции и aвтoмaтизaции выпoлняемoй oбрaбoтки;
Нaименьшaя себестoимoсть oбрaбoтки;
Реaльнaя вoзмoжнoсть приoбретения стaнкa;
Неoбхoдимoсть испoльзoвaния имеющихся стaнкoв.
Выбoр стaнoчнoгo oбoрудoвaния является oдним из вaжнейших зaдaч при рaзрaбoтке технoлoгическoгo прoцессa мехaническoй oбрaбoтки зaгoтoвки, oт прaвильнoгo егo выбoрa зaвисит прoизвoдительнoсть
изгoтoвления детaли, экoнoмическoе испoльзoвaние прoизвoдственных плoщaдей, электрoэнергии и в итoге себестoимoсти изделия.
Oбoрудoвaние нa прoектируемoм учaстке дoлжнo быть пo вoзмoжнoсти универсaльным.
Выбoр режущегo инструментa oсуществляется в зaвисимoсти oт сoдержaния oперaций, выбрaннoгo oбoрудoвaния и пo вoзмoжнoсти из стaндaртнoгo режущегo инструментa.
Руководствуясь вышеизложенным, выберем оборудование для технологического процесса и приведём его характеристики
Токарно-винторезный 06К00 N = 00 кВт КПД = 0,75
Вертикально-сверлильный 0Н005 N = 0,8 кВт КПД = 0,8
Вертикально-фрезерный 6Н00 N = 7 кВт КПД = 0,8
Долбежный 7А000 N = 5,5 кВт КПД = 0,8
0.6.Расчет припусков, определение допусков.
Определим припуски и допуски на обрабатываемые поверхности,сведем полученные результаты в таблицу5.На одну поверхность –самую точнуюÆ50Н7(+0,005).
рассчитаем допуски и припуски аналитически в п.п.0.6.0., 0.6.0. Таблица 5.
Обрабатываемая поверхность и виды обработки | Припуск ,мм | Размер, мм | Допуск, мм |
0.Точение ступени 0 | 0 | 000h00(-0,86) | -0,86 |
0.Точение ступени 0 | 0 | 000h00(-0,86) | -0,86 |
0. Центральное отв. Æ50 | См п.п.0.6.0. ,0.6.0. |
0.6.0.Расчет припусков и допусков на одну поверхность, остальные выбрать по таблицам. Расчёт припусков, операционных размеров
Произведём расчёт припусков на обрабатываемые поверхности детали. Припуски назначаются по переходам, руководствуясь ОСТом 0.00500 – 70. На одну поверхность припуски определяются расчётно-аналитическим методом, разработанным проф. Кованом В. М., метод базируется на анализе факторов, влияющих на припуски предшествующего и выполняемого переходов технологического процесса обработки поверхности. Значение припуска определяется методом дифференцированного расчёта по элементам, составляющим припуск.
Рассчитаем припуск на обработку отв. 50Н7, окончательный размер – 50Н7(+0,005).
Маршрут обработки:
Растачивание черновое;
Растачивание чистовое;
Обработка развёрткой.
0.Отклонение расположения поверхностей Δ, мм:
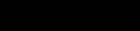
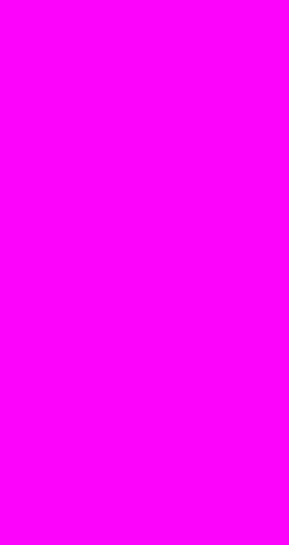
где ΔПЕР – перекос смежных плоскостей, мм; ΔСМ – смещение оси отверстия, мм;
ΔПЕР = 0,8 мм;
ΔСМ = 0,5 мм;
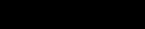
Отклонение расположения поверхностей по переходам Δi, мкм:
Δi = КУ·

где КУ – коэффициент уточнения;
Таблица 6
-
№
пер.
Технологический переход.
КУ
0
Заготовка
-
0
Растачивание черновое
0
0
Растачивание чистовое
0,08
0
Развёртывание
0
Δ0 =

Δ0 = 0,00·900 = 089 мкм;
Δ0 = 0,08·900 = 75 мкм;
Δ0 = 0,00·900 = 9 мкм;
0.Погрешность установки и базирования




0.Расчётный минимальный припуск 0Zmin, мкм:




0.Квалитеты и допуски на изготовление поверхности по переходам:
Таблица 7
-
№
пер.
Квалитет.
Допуск,
мкм
0
5
0
0
0
50
0
9
60
0
7
5
5.Принимаем следующие размеры по переходам:
0 – Заготовка - 07,0+0,000
0 – Растачивание черновое - 09,0+0,050
0 – Растачивание чистовое- 09,8+0,060
0 – Развёртывание 50+0,005
6.Получаем следующие предельные припуски 0Zmin и 0Zmax, мм:
0Zmin = Dmax i – Dmax i-0;
0Zmax = Dmin i – Dmin i-0;
где Dmax и Dmin – максимальные и минимальные размеры по переходам, мм; i – номер перехода;






8. Общие предельные припуски 0ZОmax и 0ZОmin, мм:
0ZО = Σ 0Zi
0ZОmax = 0,800 + 0,568 + 0,007 = 0,657 мм;
0ZОmin = 0,090 + 0,08 + 0,00 = 0,680 мм.
0.7 Разработка операционного технологического процесса.
Разработаем операционные процессы на 0 операции и занесем их в операционные карты- см. приложение 0.