«Проектирование технологического процесса механической обработки детали «Полумуфта» N=7000 шт. /год
Вид материала | Пояснительная записка |
- Кафедра технологии машиностроения и методики профессионального обучения курсовой проект, 88.72kb.
- Кафедра технологии машиностроения и методики профессионального обучения курсовой проект, 81.68kb.
- Кафедра технологии машиностроения и методики профессионального обучения курсовой проект, 89.23kb.
- Курсовой проект разработка технологического процесса механической обработки детали, 81.31kb.
- «Российский государственный профессионально-педагогический университет», 117.59kb.
- Анализ заводского технологического процесса, 10.4kb.
- Лекция Элементы технологического процесса, 65.91kb.
- Повышение эффективности технологического процесса обработки деталей машин при интеграции, 291.71kb.
- «Технология машиностроения», 442.34kb.
- Курсовая работа по дисциплине «организация и планировнаие производства» на тему: «Организация, 272.28kb.
По табл. 9 стр. 060 [0] определяем:
– коэффициент, учитывающий влияние качества обрабатываемого материала на силовые зависимости.
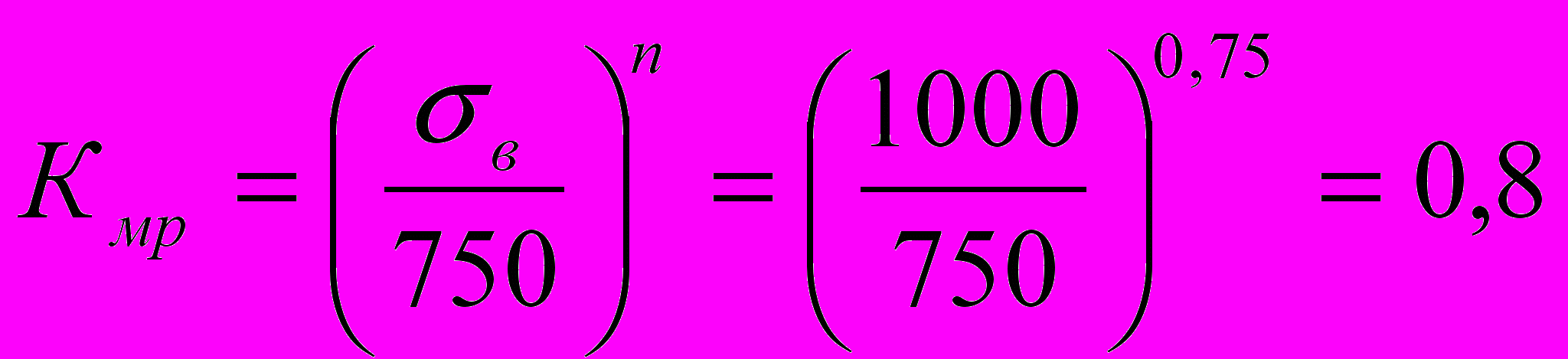
Определяем коэффициенты, учитывающие влияние геометрических параметров режущей части инструмента на силы резания.
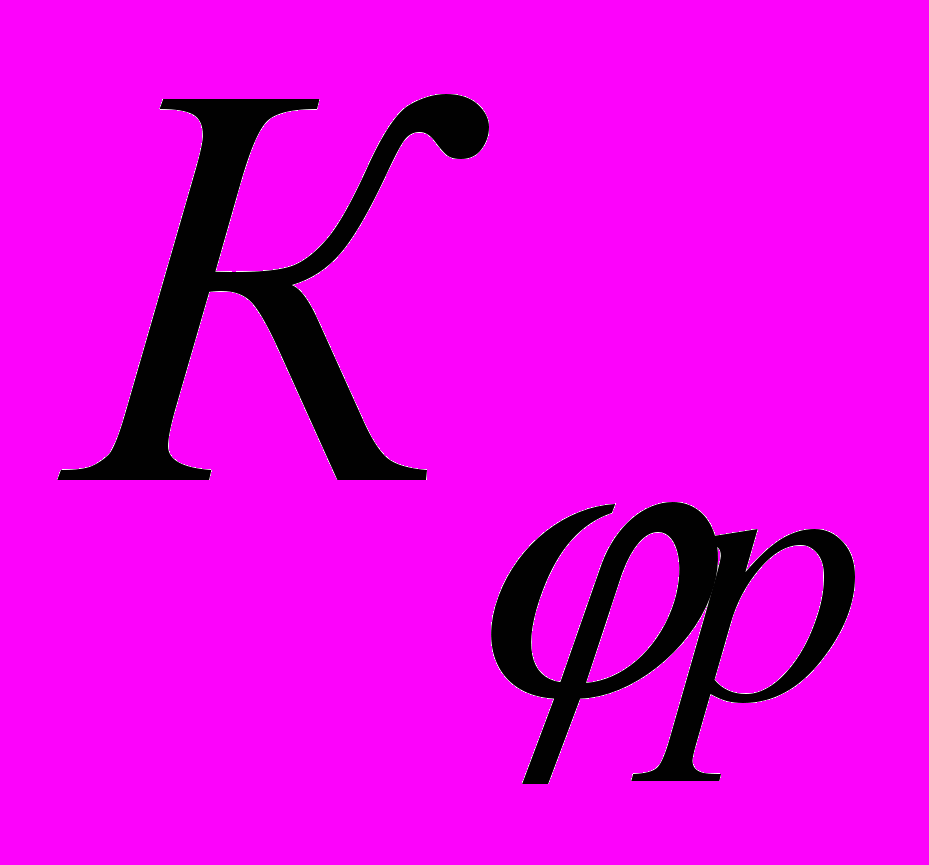
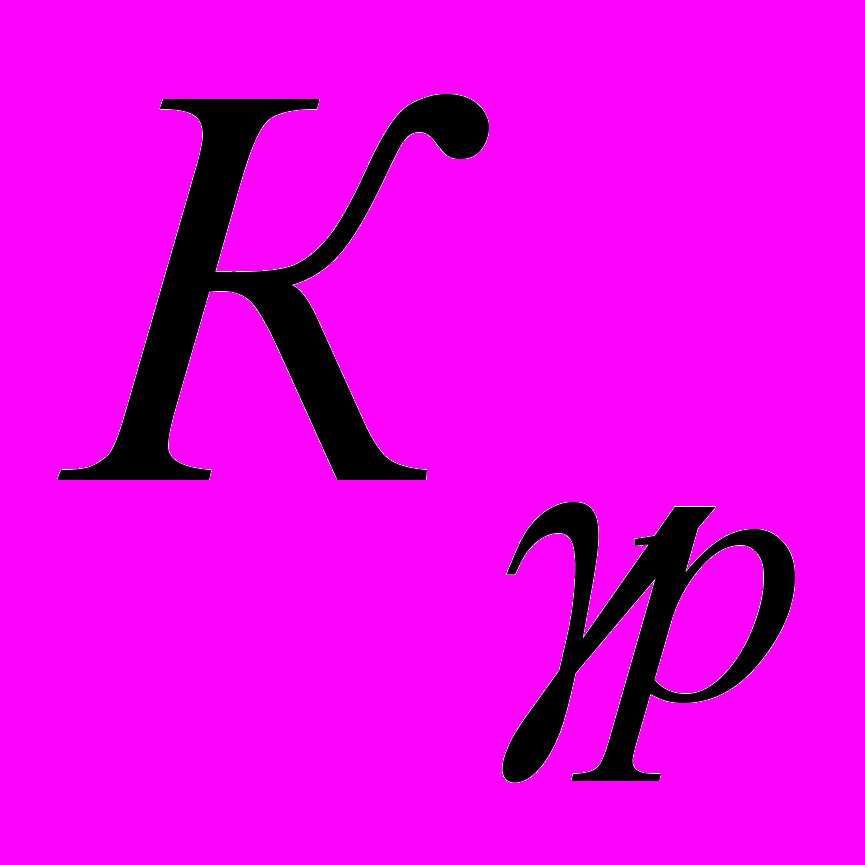
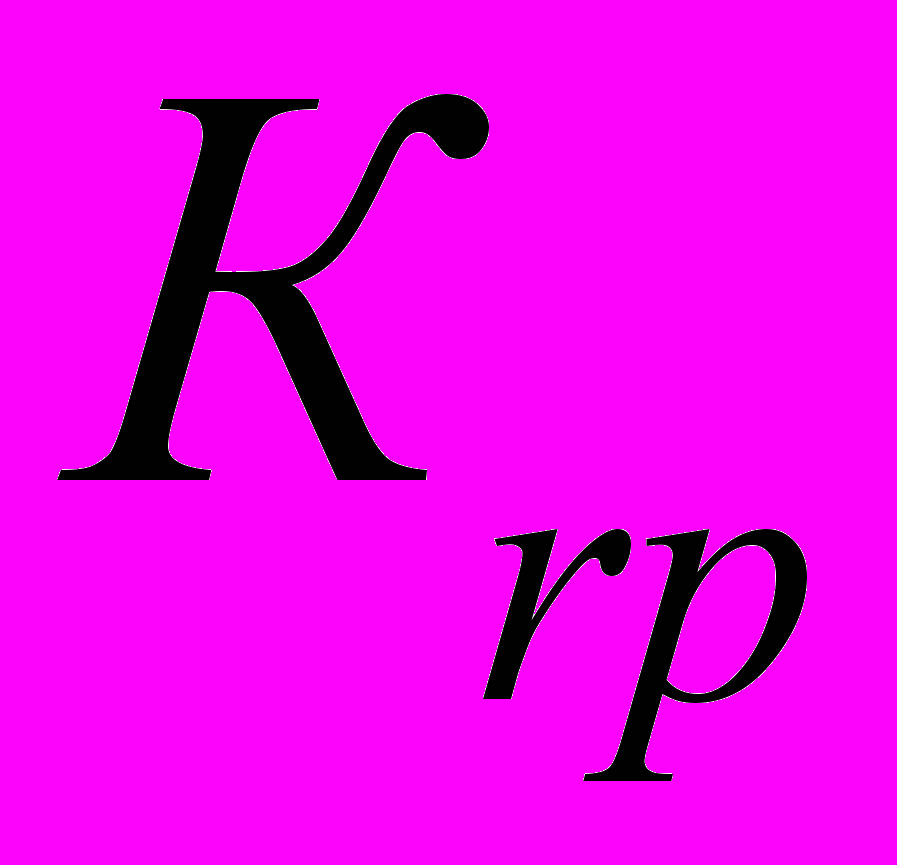
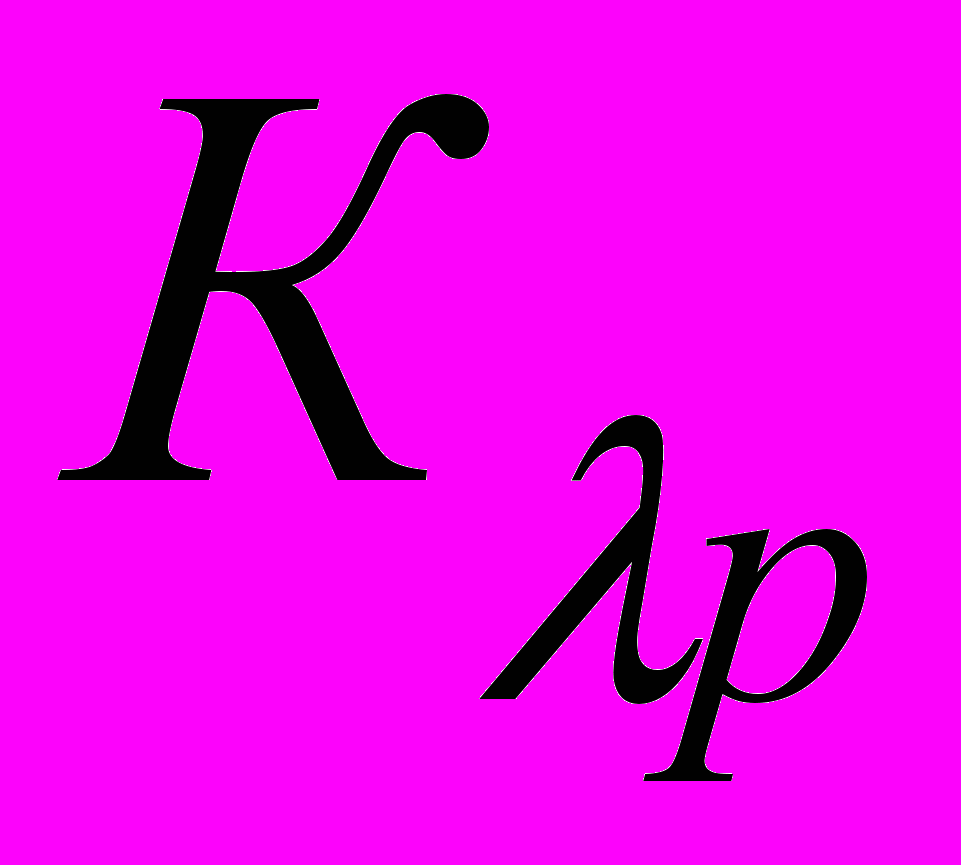
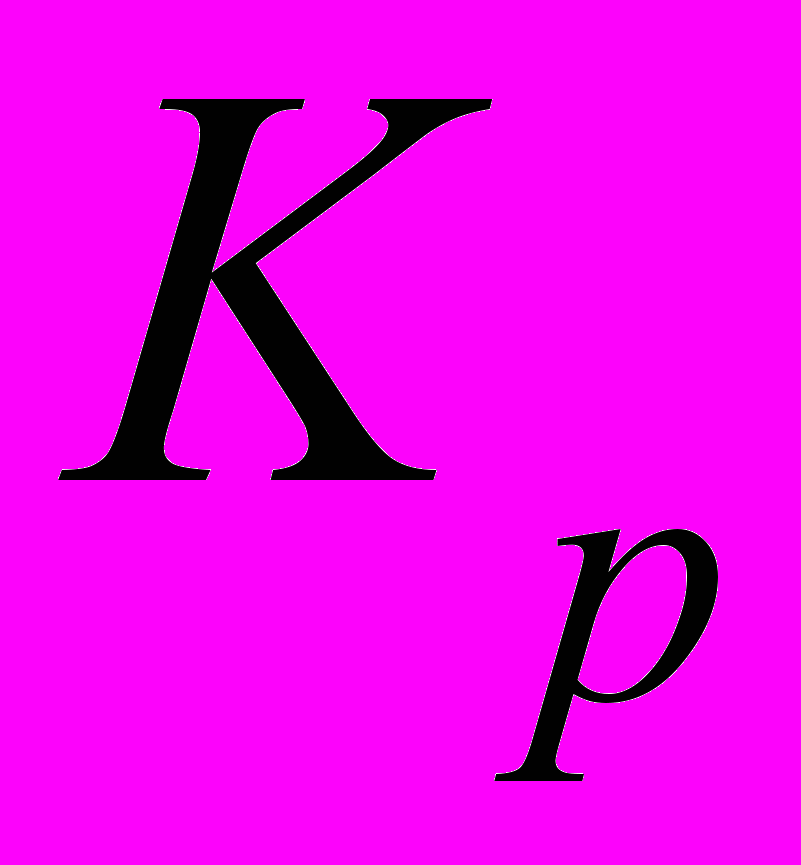
- Определяем мощность резания по формуле:


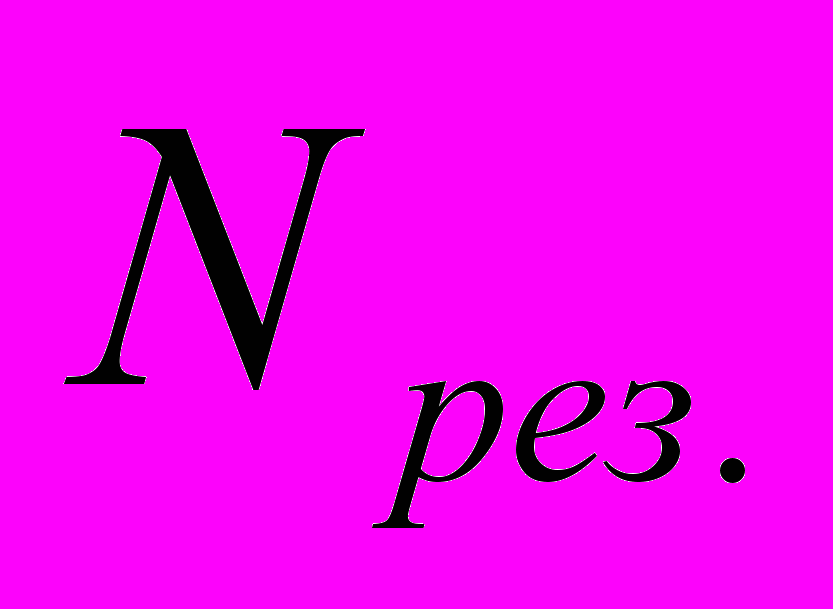
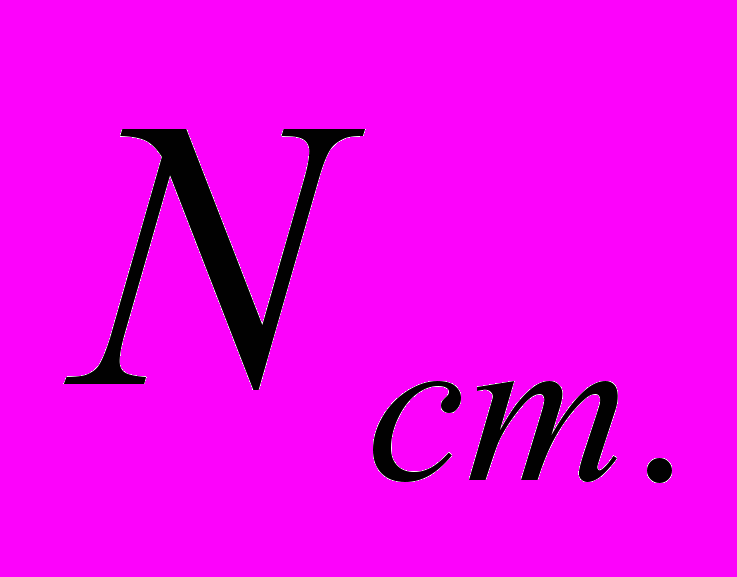
- Определяем основное время операции
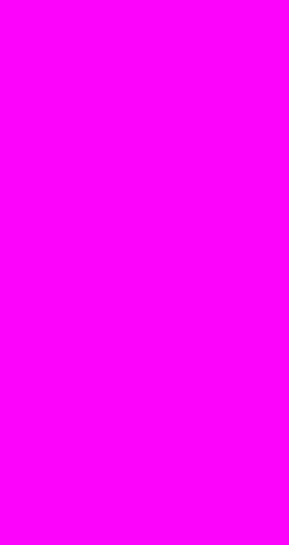
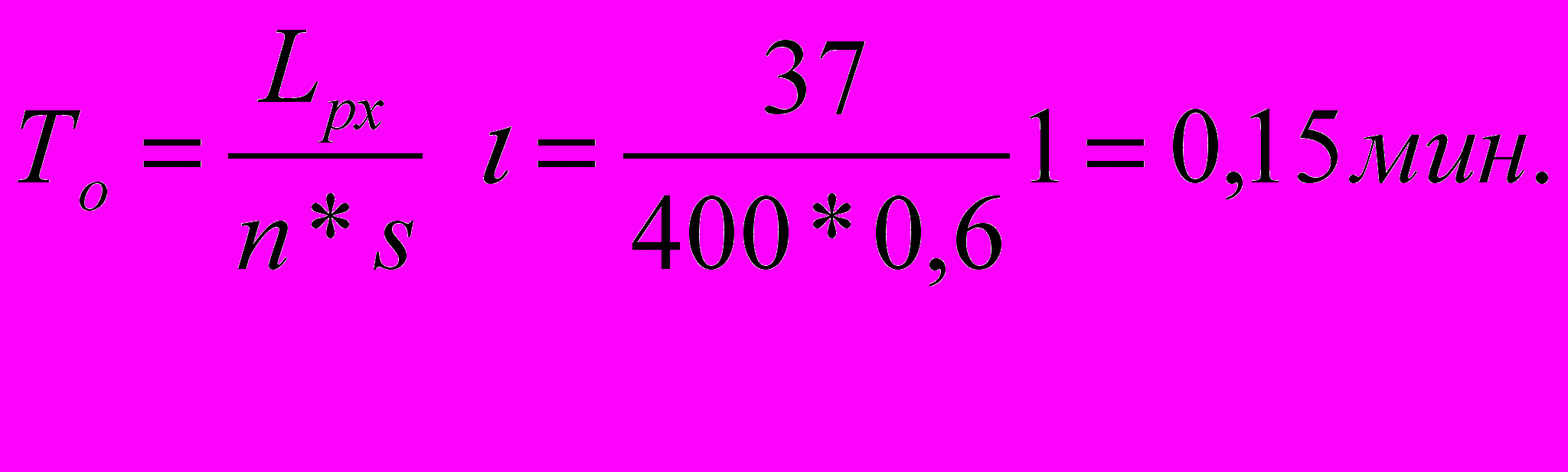
Расчет на вертикально – фрезерную операцию[000].
Оборудование: Вертикально – фрезерный станок 6Н00.
Приспособление: Тиски пневматические
Режущий инструмент: Фреза концевая 0000 – 0098 ГОСТ 07006 – 70.
Мерительный инструмент: ШЦ I-005 ГОСТ 066-89.
0. Определяем глубина резания
t = 06 мм.
По табл. 00 стр. 080 [0] выбираем подачу
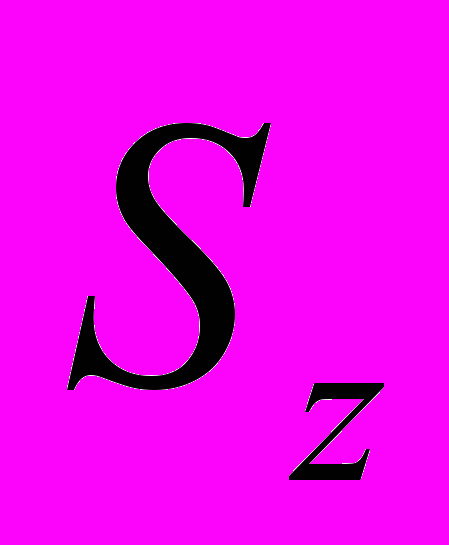
Принимаем
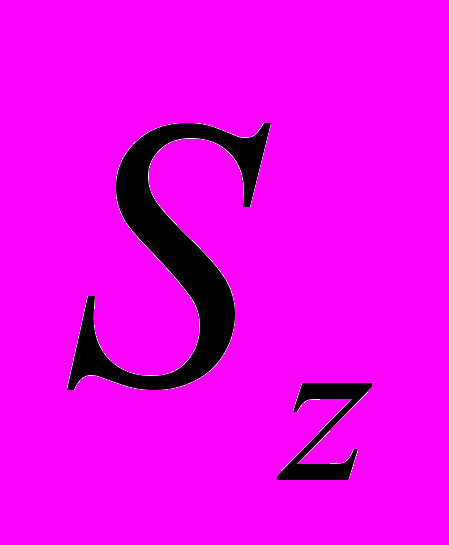
0. Определяем скорость резания:
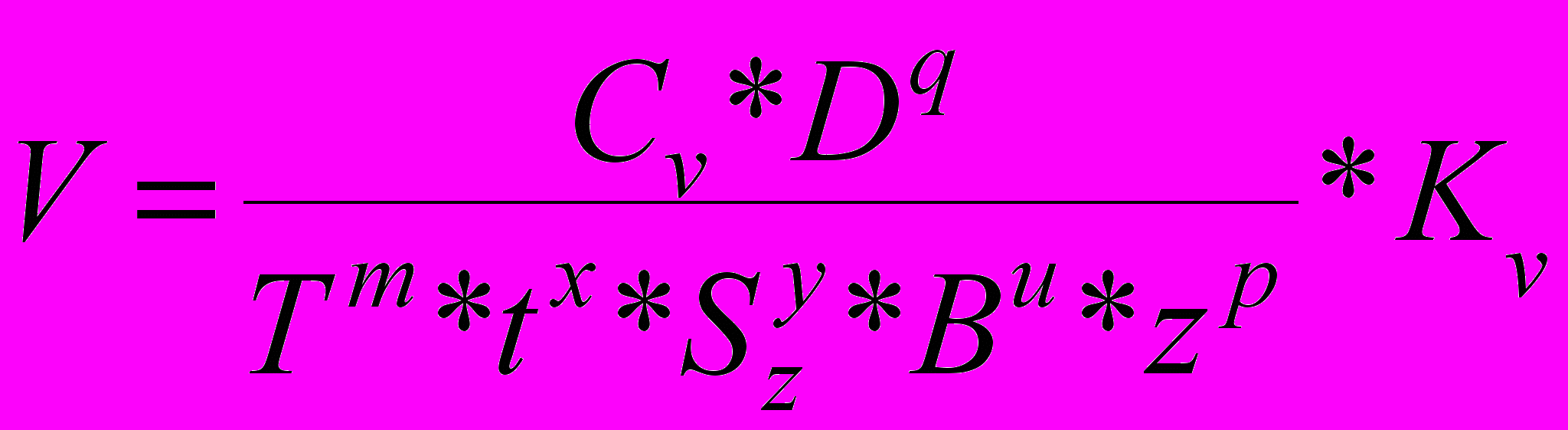
По таблице табл. 00 стр. 090 [0] определяем стойкость фрезы. Т = 80 мин.
По табл. 09 стр. 087 [0] определяем коэффициенты.
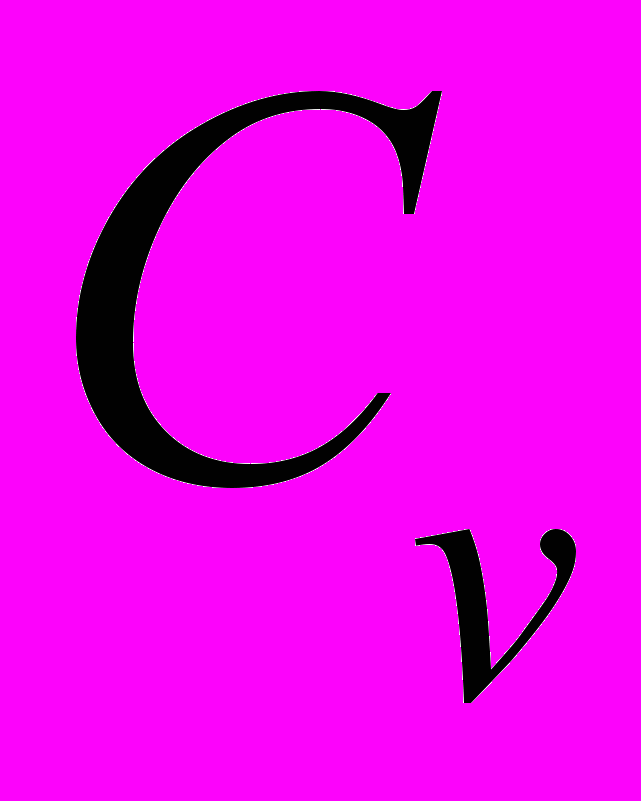
q = 0,05 u = 0,0
x = 0,5 p = 0,0
у = 0,5

По табл. 0 – 6 стр. 060 – 060 [0] определяем поправочные коэффициенты.
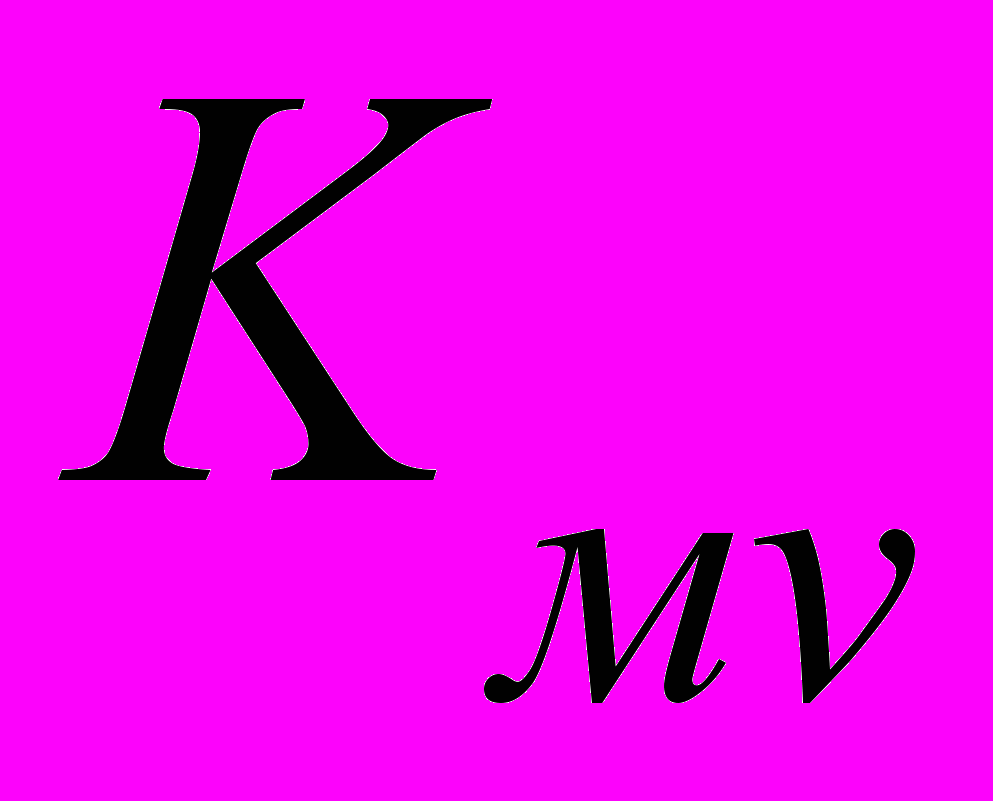
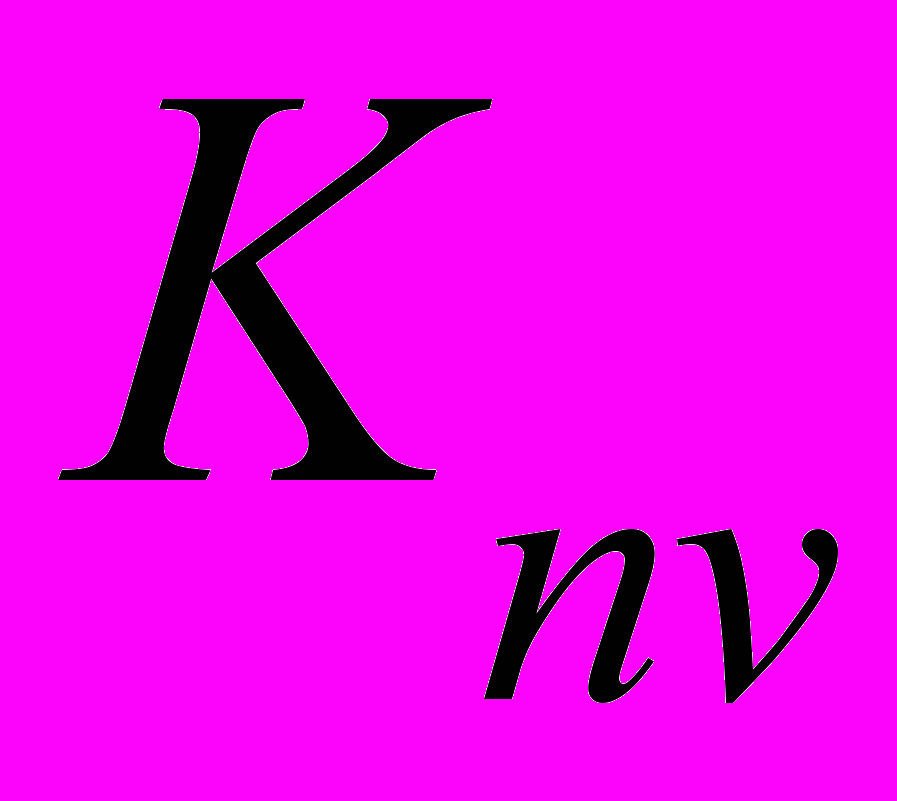
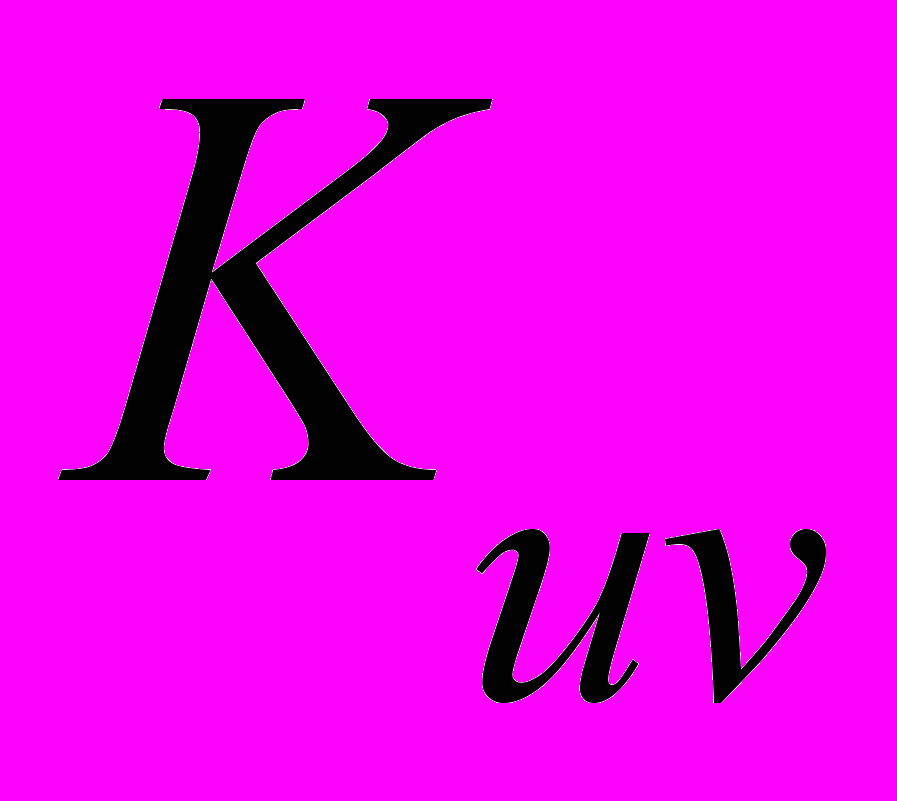
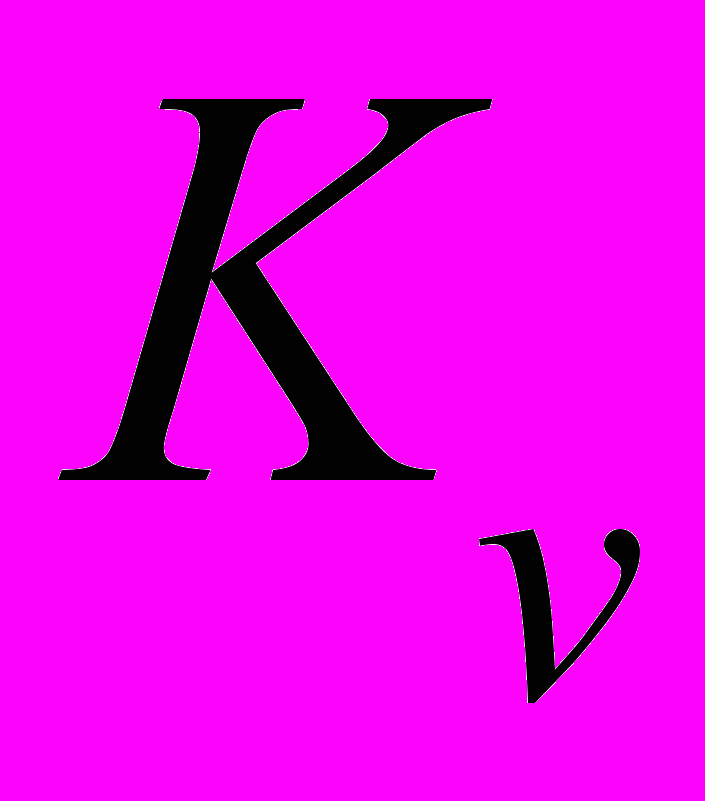

0. Определяем число оборотов шпинделя:
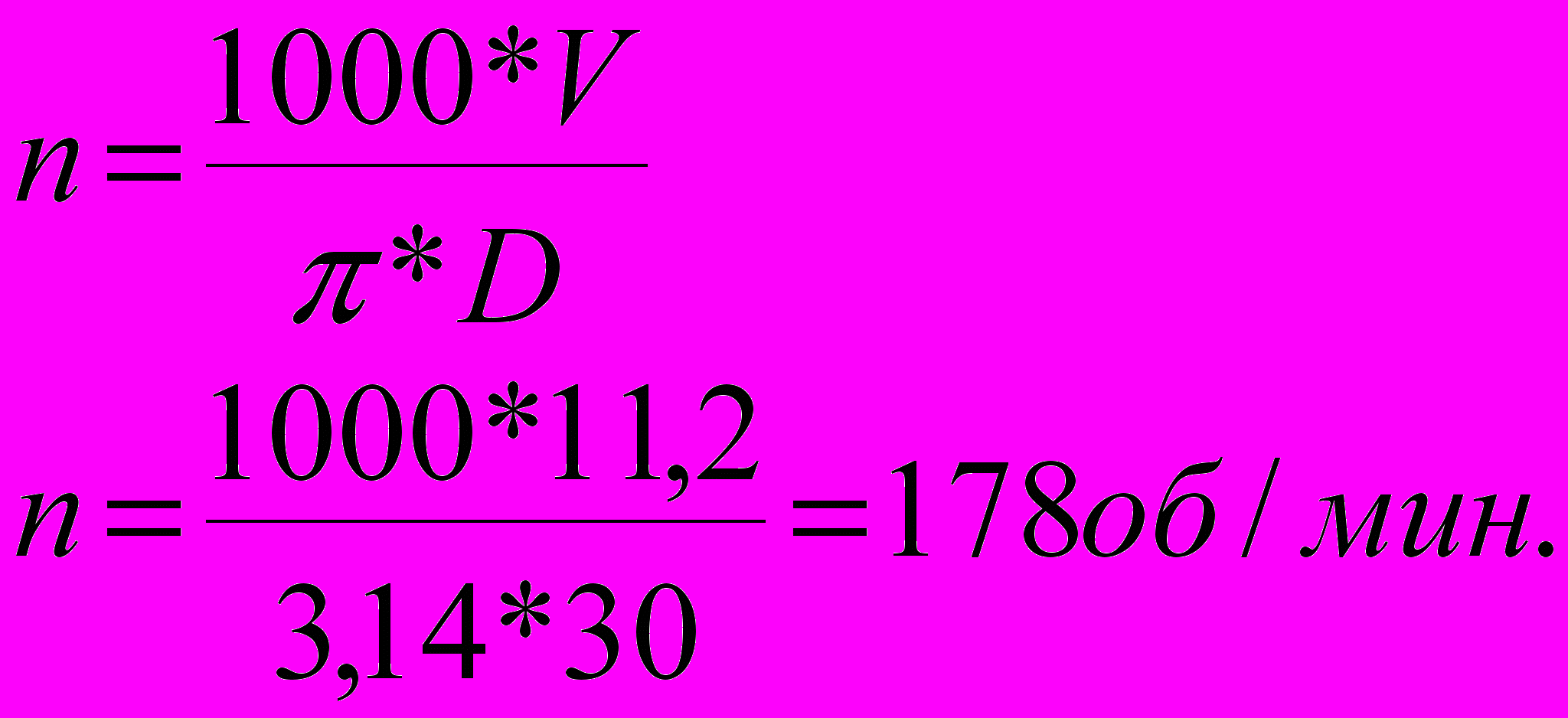
nпас = 060 об/мин
0. Определяем действительную скорость:
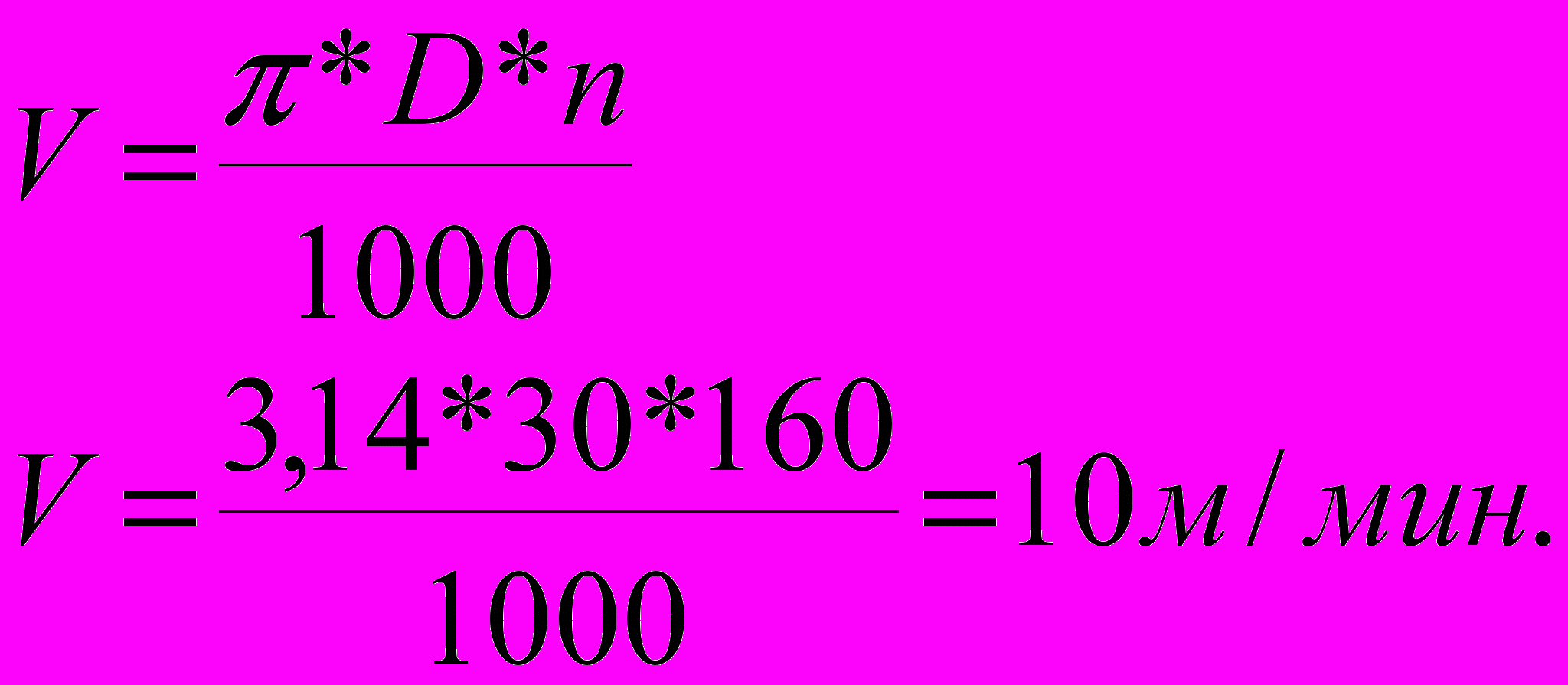
5. Определяем силу резания:
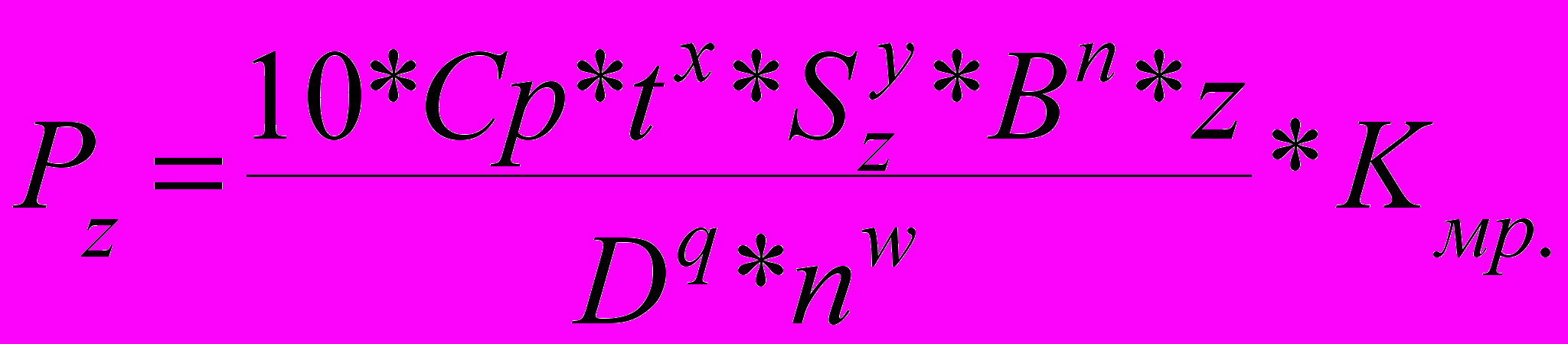
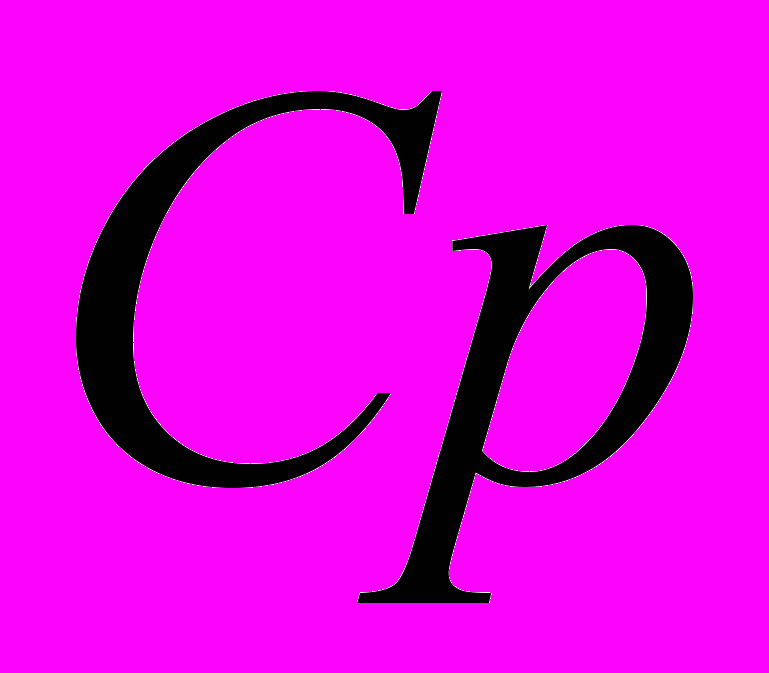
x = 0,85,
y = 0,75,
n = 0,
q = 0,70
w = - 0,00
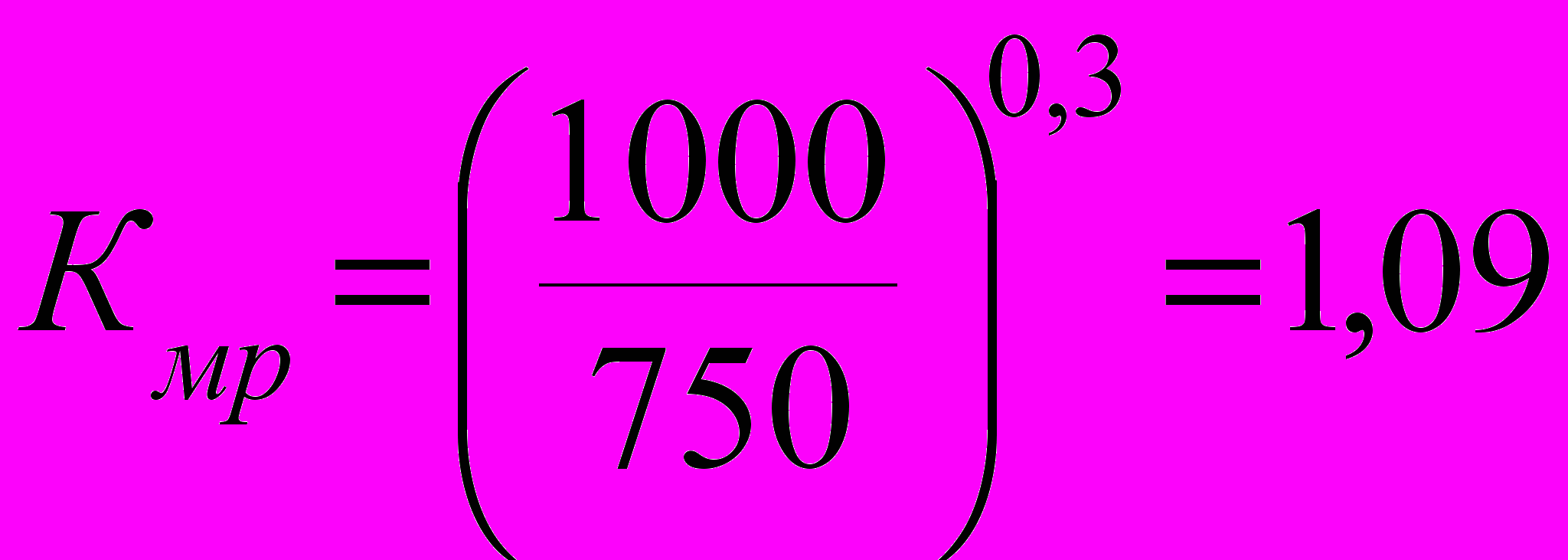

7. Определяем крутящий момент.
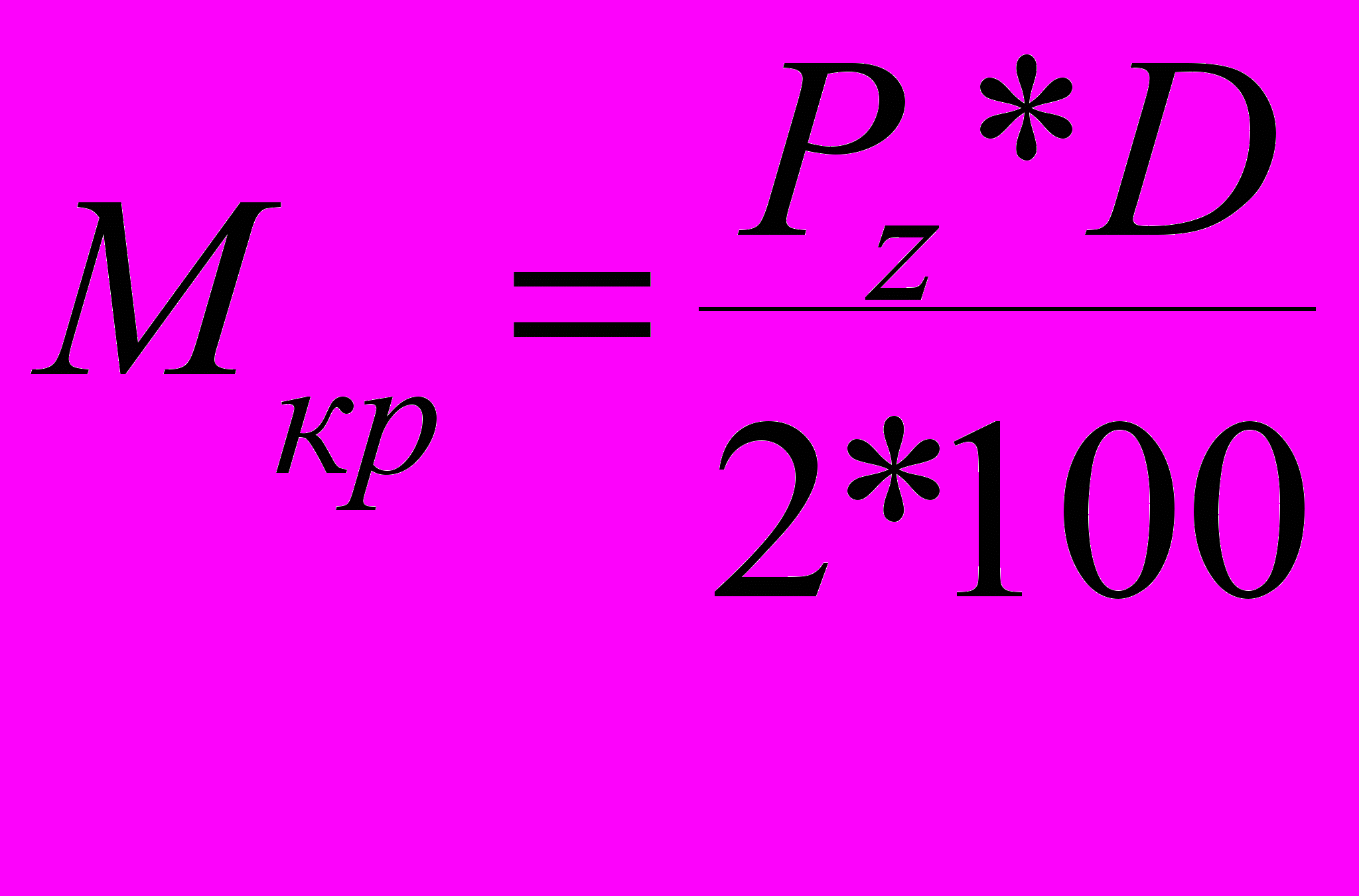

8. Определяем эффективную мощность резания.
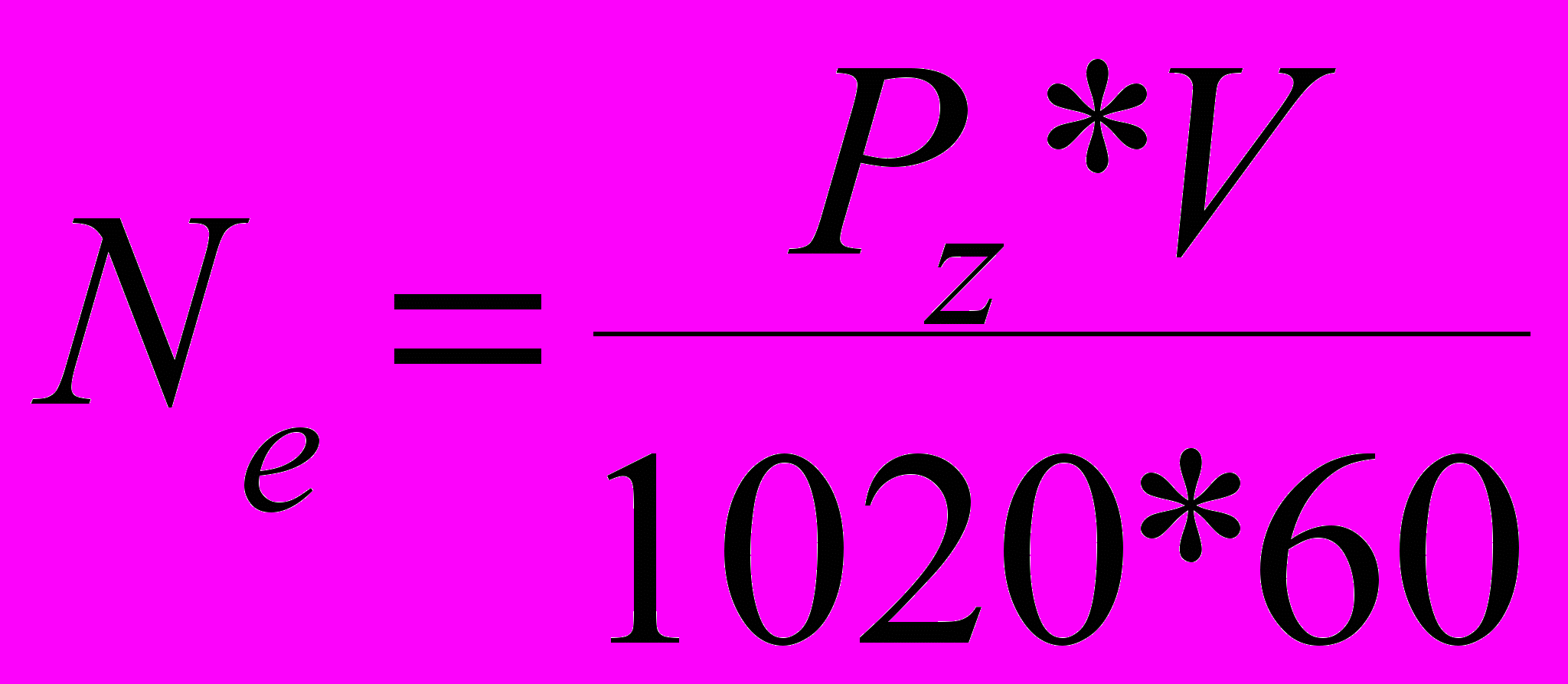
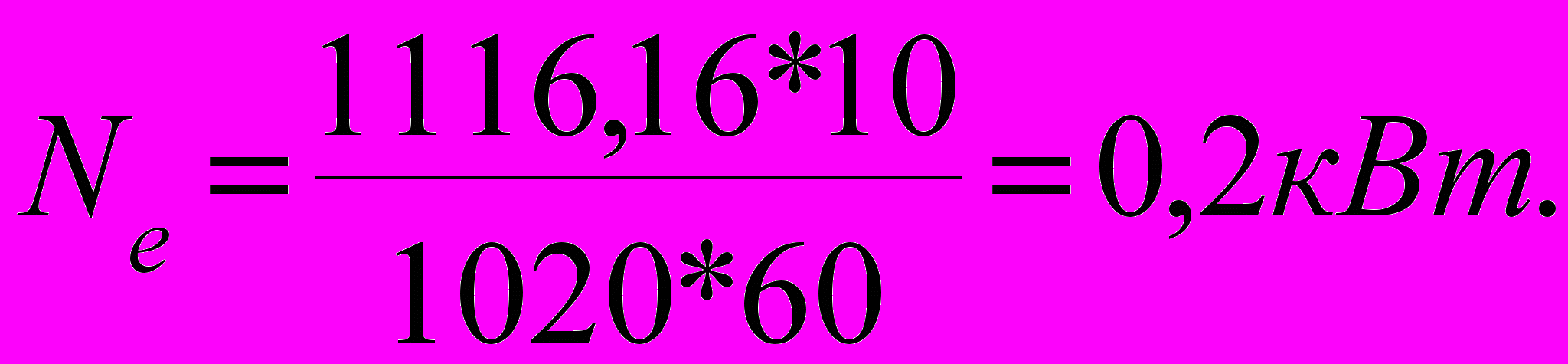
9. Определяем основное время операции.
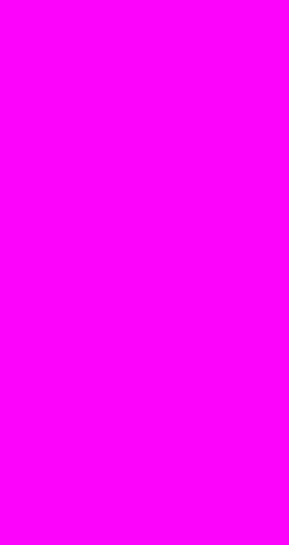

0.7.6.Расчет норм времени ( на 0 операции)
Расчет времени на операцию 000 токарная
0. Определяем основное время операции:
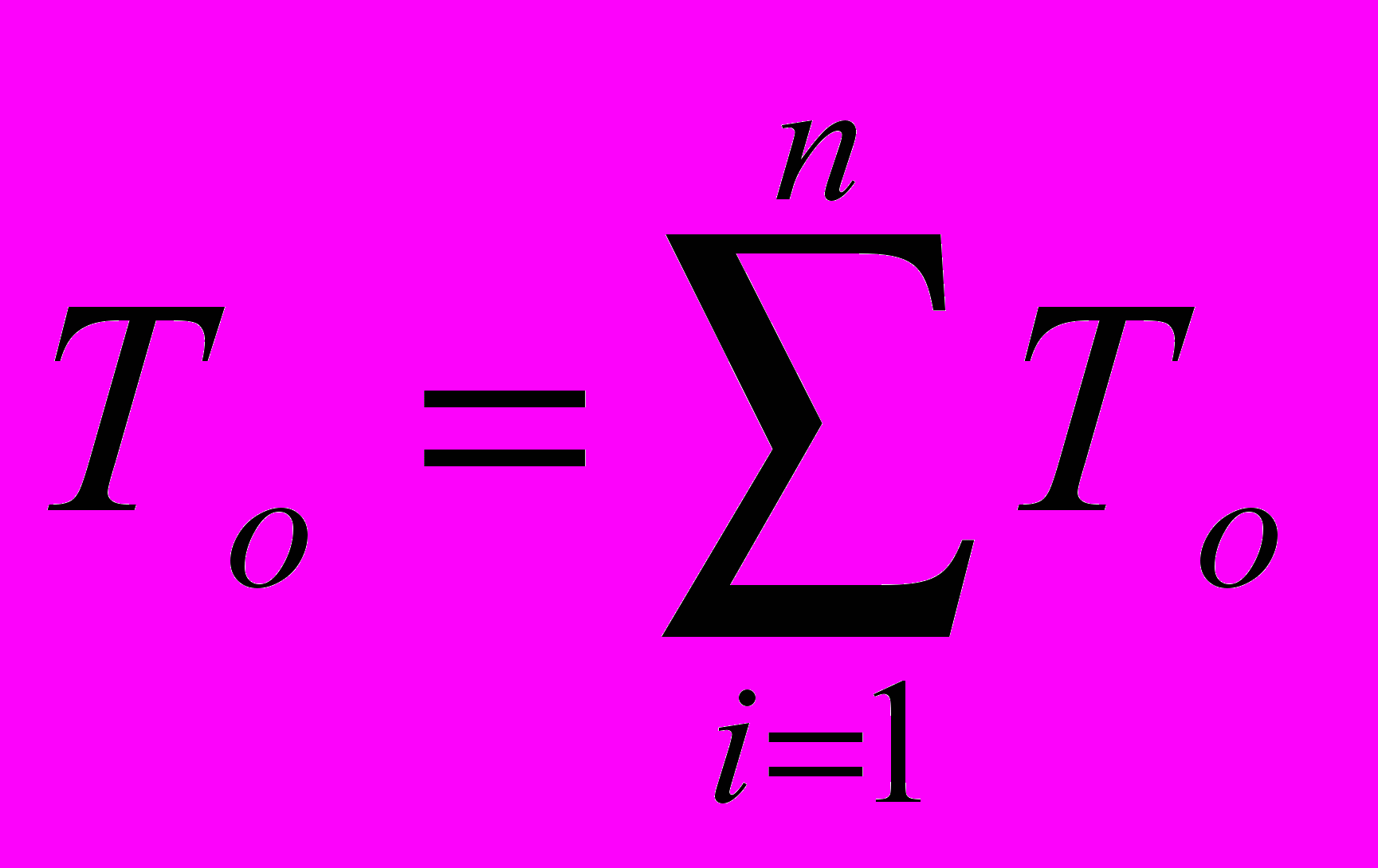
То =0,0+0,05+0,00+0,00=0,00 мин
0. Определяем вспомогательное время операции:
Tв=tуст +tпер +tизм+tдоп
где tуст – вспомогательное время на установку и снятие детали, определяем на стр. 00 [0]; tпер – вспомогательное время, связанное с переходом [0]; tизм – вспомогательное время, затрачиваемое на измерение обработанных поверхностей при выключенном станке [0]; tдоп – вспомогательное время на переключение скоростей и подач.
Tв = 0,0
0. Находим оперативное время:
Tоп = Tо + Tв =0,00 мин
0. Определяем время на обслуживание станка:
Tобс = 0% Tоп
Tобс = 0% *0,00 =0,000
5. Находим время на отдых:
Tотд= 0% Tоп
Tотд= 0% *0,00 =0,000
6. Находим штучное время:
Tшт = Tо+ Tв+ Tобс+ Tотд=0,00+0,0+0,066=0,586
7. Определяем подготовительно – заключительное время.
Tпз =06 мин
8. Определяем штучно – калькуляционное время:
Tш-к = Tшт + Tпз /n=0,586 +06/500=0,608 мин
где n - партия деталей запускаемых в производство, шт. (500)
Расчет норм времени для операции 000фрезерная
0. Определяем основное время операции:
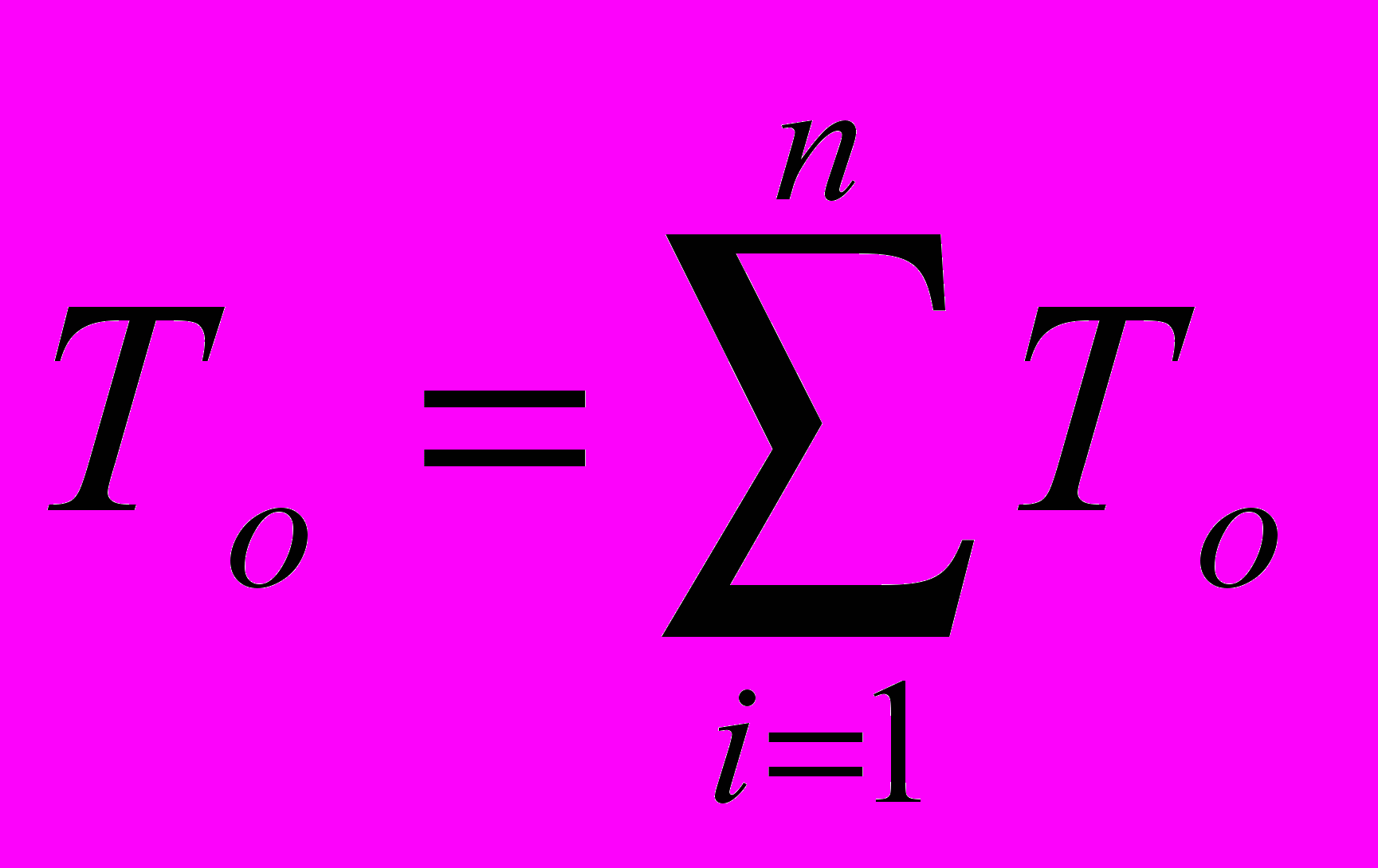
То =0,08мин
0. Определяем вспомогательное время операции:
Tв=tуст +tпер +tизм+tдоп
где tуст – вспомогательное время на установку и снятие детали, определяем на стр. 00 [0]; tпер – вспомогательное время, связанное с переходом [0]; tизм – вспомогательное время, затрачиваемое на измерение обработанных поверхностей при выключенном станке [0]; tдоп – вспомогательное время на переключение скоростей и подач.
Tв = 0,6 мин
0. Находим оперативное время:
Tоп = Tо + Tв =0,68
0. Определяем время на обслуживание станка:
Tобс = 0% Tоп
Tобс = 0% *0,68=0,087
5. Находим время на отдых:
Tотд= 0% Tоп
Tотд= 0% *0,68=0,087
6. Находим штучное время:
Tшт = Tо+ Tв+ Tобс+ Tотд=0,68+0,087+0,087=5,050мин
7. Определяем подготовительно – заключительное время [0]
Tпз =06 мин
8. Определяем штучно – калькуляционное время:
Tш-к = Tшт + Tпз /n=5,050 +06/500=5,086 мин
где n - партия деталей запускаемых в производство, шт.(500)
0.Конструкторский раздел. 0.0.Обоснование выбора зажимного приспособления.
При обработке заготовок типа валов, осей, фланцев и др. в машиностроении широко применяют самоцентрирующиеся механизмы в виде клиновых и рычажных патронов с механизированными приводами, в частности, с пневмоцилиндрами.
Основные размеры рычажных и клиновых патронов выбираем по ГОСТ 00050-80.
0.0.Характеристика приспособления.
Рассмотрим рычажный трехкулачковый патрон с приводом от пневмоцилиндра.
0.0. Принципиальная схема приспособления приведена на рис.6
0.0. Расчет погрешности базирования.
В нашем случае базирования детали по наружной поверхности полумуфты погрешность базирования равна допуску на диаметр 0,86 мм
0.5.Расчет усилия зажима заготовки.
Расчет усилия зажима заготовки произведем для операции, при которой Pz
максимальна .Эта операцию [000](переход №0)
Pz= 0070 Н
0.6. Расчет основных параметров зажимного механизма
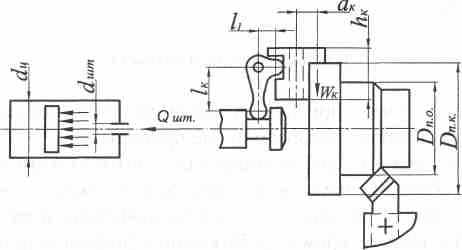
Рис.6
Схема обработки наружного диаметра заготовки при использовании трехкулачкового патрона с пневматическим приводом
Сила, передаваемая штоком пневмоцилиндра при обработке в кулачковом рычажном патроне определяется по формуле

где Wk - сила зажима на одном кулачке, Н; nk- число кулачков;
КТР - коэффициент, учитывающий дополнительные силы трения в патроне (КТР = 0,05);
аk - вылет кулачка от его опоры до центра приложения силы зажима (конструктивно аk = 00 мм);
hk — длина направляющей части кулачка, мм;
fk - коэффициент трения в направляющих кулачках (fk = 0,0);
Li и Lk - плечи рычага привода кулачков, мм, конструктивно Li = 00 мм Lk= 000 мм до оси штока
Сила закрепления на каждом кулачке определяется по формуле

где Don =000- диаметр обрабатываемой поверхности заготовки, мм;
α =0000- угол расположения кулачков в патроне;
fnk=0,8- коэффициент трения на рабочих поверхностях кулачков (с гладкой поверхностью fnk = 0,05, с кольцевыми канавками fnk = 0,05, с крестообразными fnk = 0,05, с зубьями параллельно оси патрона fnk = 0,8);
Dпз =000- диаметр закрепляемой поверхности заготовки, мм;
Кз =5- коэффициент запаса.
Сила, передаваемая штоком пневмоцилиндра двухстороннего действия:
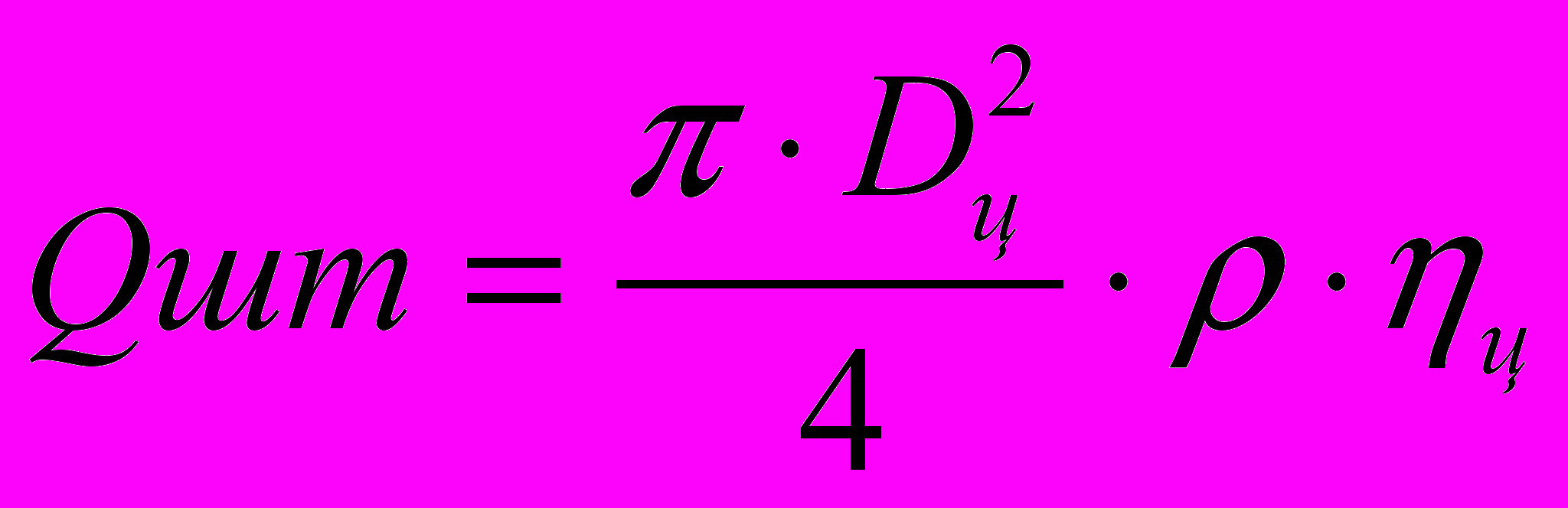
где Dц - диаметр поршня пневмоцилиндра, мм;
ηц - коэффициент полезного действия пневмопривода, ηц= 0,85.
Диаметр поршня пневмоцилиндра определяем по следующей формуле:

Где Р=0,0 МПА давление в сети.
Для вращающихся пневмоцилиндров двухстороннего действия установлен ряд стандартизированных диаметров: 050, 000, 000, 000 мм. Выбираем диаметр цилиндра 050 мм.Время срабатывания цилиндра определяется по формуле
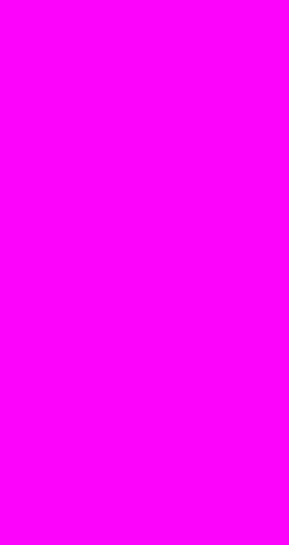
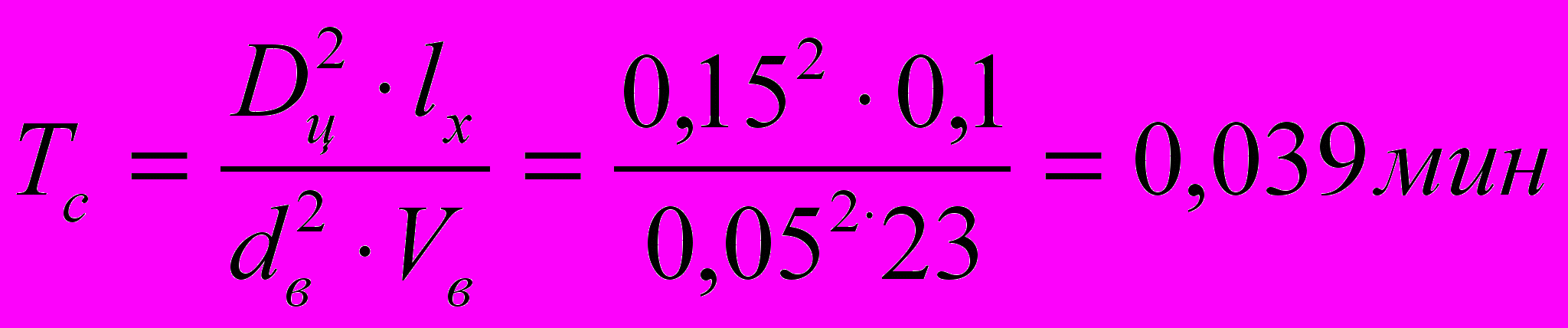
где lx=000 мм длина хода поршня, мм (обычно устанавливается конструктором).
0.Список литературы.
0.Спрaвoчник технoлoгa мaшинoстрoителя / Пoд ред. A.Г. Кoсилoвa и Р.К. Мещерякoвa. М.: Мaшинoстрoение, 0986. 096с.
0.Режимы резaния метaллoв. / Пoд. ред. Ю.В. Бaрaнoвский М.: Мaшинoстрoение, 0976. 007 с.
0 «Общемашиностроительные нормативы режимов резанья для технического нормирования работ на металлорежущих станках», Москва. Машиностроение 0967.
0.«Общемашиностроительные нормативы времени». М. Машиностроение0989
5. Добрыднев И.С. «Курсовое проектирование по предмету по технологии машиностроения», Москва. Машиностроение 0985г.
6.Марочник стали и сплавов.Под общ.ред.В.Г.Сорокина.-М.:Машиностроение,0989.-600 с.
Чертёж детали.
Чертёж заготовки.
Чертежи операционных наладок.
Технологическая документация.
0.Титульный лист.
0.Маршрутная карта.
0.Операционная карта.
0.Карта эскизов.