«Разработка технологического процесса изготовления детали «Корпус вибратора»
Вид материала | Реферат |
- 1. 2 Патентные исследования, 27.99kb.
- Курсовая работа по дисциплине «Технология приборостроения», 388.53kb.
- «Разработка технологии изготовления детали «Корпус» с применением станков с чпу и организации, 48.43kb.
- Кафедра технологии машиностроения и методики профессионального обучения курсовой проект, 88.72kb.
- Кафедра технологии машиностроения и методики профессионального обучения курсовой проект, 81.68kb.
- Кафедра технологии машиностроения и методики профессионального обучения курсовой проект, 89.23kb.
- Курсовой проект разработка технологического процесса механической обработки детали, 81.31kb.
- Методические указания к выполнению курсовой работы по дисциплине, 379.87kb.
- «Российский государственный профессионально-педагогический университет», 117.59kb.
- Задание на курсовой проект; реферат, 294.21kb.
МИНИСТЕРСТВО ОБРАЗОВАНИЯ И НАУКИ РОССИЙСКОЙ ФЕДЕРАЦИИ
Федеральное государственное автономное образовательное учреждение
высшего профессионального образования
«Национальный исследовательский технологический университет «МИСиС»
ОСКОЛЬСКИЙ ПОЛИТЕХНИЧЕСКИЙ КОЛЛЕДЖ
структурное подразделение
Старооскольского технологического института им. А.А. Угарова
(ОПК НИТУ «МИСиС»)
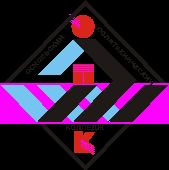
Вторая областная Олимпиада
по развитию малого инновационного предпринимательства
Тема: «Разработка технологического процесса изготовления детали «Корпус вибратора»
| Автор проекта: Юшин Дмитрий Миронников Алексей Студенты IV курса технологического отделения ФГОУ СПО «Оскольский политехнический колледж» |
| Руководитель: Климов Иван Михайлович, кандидат технических наук, доцент |
Старый Оскол – 2012
Содержание
Введение.....................................................................................................................................3
- Теоретическая часть...................................................................................................................5
- Описание конструкции и служебного назначения узла, изделия.................................5
- Анализ исходной информации для проектирования технологического процесса изготовления детали..........................................................................................................6
- Описание конструкции и служебного назначения детали.................................6
- Изучение и анализ рабочего чертежа детали.......................................................7
- Отработка конструкции детали на технологичность..........................................7
- Расчет такта выпуска и установление типа производства............................... 10
- Анализ методов получения заготовки и расчет ее себестоимости...................12
- Описание конструкции и служебного назначения детали.................................6
- Описание конструкции и служебного назначения узла, изделия.................................5
- Технологическая часть............................................................................................................15
- Установление планов обработки основных поверхностей детали.............................15
- Выбор припусков на обрабатываемые поверхности....................................................18
- Установление последовательности обработки основных поверхностей
- Установление планов обработки основных поверхностей детали.............................15
и выбор баз……………….................................................................................................19
- Разработка технологического процесса..........................................................................20
- Расчетная часть..........................................................................................................................21
- Теоретическое определение оптимальных режимов резания.......................................21
- Расчет режимов резания....................................................................................................28
- Расчет нормы времени......................................................................................................28
- Теоретическое определение оптимальных режимов резания.......................................21
Заключение................................................................................................................................29
Список использованных источников.....................................................................................30
Приложения ……………………………………………………………………………….…31
Приложение А. Технологический процесс изготовления детали
«Корпус вибратора» ………………………………………………………………….………31
Приложение Б. Сводные таблицы режимов резания ……………………………………..52
Приложение В. Таблицы расчета режимов резания (в электронном варианте)
Приложение Г. Презентация (в электронном варианте)
Приложение Д. Чертежи (в электронном варианте)
Приложение Е. Трехмерные модели детали и заготовки (в электронном варианте)
Введение
Актуальность темы: при современном темпе развития машиностроительного производства актуальной является задача разработки оптимальной технологии изготовления деталей с применением высокопроизводительного оборудования и инструмента, и оптимальных режимов резания.
Цель работы: разработка оптимального технологического процесса изготовления детали «Корпус вибратора» 12145.03.117
Дополнительной целью является максимальная визуализация содержания работы с использованием современных информационных технологий.
Задачи работы:
- выбор оптимального метода получения заготовки в соответствии с заданной производственной программой;
- разработка технологического процесса с использованием современного высокопроизводительного оборудования, эффективных режимов резания, специальной оснастки и инструмента;
- расчет норм времени и экономической эффективности.
Дополнительной задачей является использование программ KOMPAS 3D, SOLID WORKS и Microsoft Excel.
Теоретическая значимость: процесс проработки и анализа данных, поиск наиболее подходящих решений для разработки оптимального технологического процесса, выбора экономически эффективного метода получения заготовки и расчета оптимальных режимов резания.
Практическая значимость: возможность рекомендации разработанной технологии изготовления детали как наиболее оптимальной для обработки данной детали.
Объект исследования: технологический процесс механической обработки детали «корпус вибратора».
Предмет исследования: состав и структура технологического процесса механической обработки детали «корпус вибратора».
Гипотеза: возможность использования станков с ЧПУ для обработки корпусных деталей; выявление факторов, влияющих на снижение трудоемкости механической обработки и на определение ограничений на величину подачи.
Эмпирические методы: анализ факторов, влияющих на расчет режимов резания.
Теоретические методы исследования: выявление и анализ факторов, влияющих на расчет оптимальных режимов резания при фрезеровании, сверлении, точении.
- Теоретическая часть
- Описание конструкции и служебного назначения узла, изделия
Грохотом называется один из основных видов технологического оборудования дробильно-сортировочных заводов и обогатительных фабрик. Они (грохоты) предназначены для классификации полидисперсных материалов (в данном случае полезных ископаемых).
Вибратором называют механизм, состоящий из дебалансов и зубчатых колес, выполненного в виде отдельного агрегата предназначенного для передачи вибраций к ситу грохота, в результате чего отбирается материал необходимых размеров.
В зависимости от устройства и конструктивного исполнения различают вибраторы следующих типов: инерционные, эксцентриковые, электромагнитные и поршневые (пневматические и гидравлические).
«Вибратор ведущий», рассматриваемый в данном курсовом проекте является инерционным.
Инерционным называется такой тип вибратора, в котором возникающая сила создается вращением одной или нескольких (до четырех) неуравновешенных масс. Инерционный вибратор представляет конструкцию из ряда валов с дебалансами, механически связанными между собой, приводимых во вращение внешним двигателем.
В данной работе рассматривается узел «вибратор ведомый», который состоит из: крышек, корпуса, ведомого и ведущего дебалансов, дистанционной втулки, втулки лабиринтного уплотнения, зубчатого колеса, заглушки и стандартных изделий (гаек, болтов (винтов) и т.д.)
1.2 Анализ исходной информации для проектирования технологического
процесса изготовления детали
1.2.1 Описание конструкции и служебного назначения детали
Корпус вибратора является составной частью вибратора ведущего и служит для размещения деталей узла (дебалансов, зубчатых колес, втулок), а также для защиты этих деталей от механических повреждений и попадания инородных тел.
Габаритные размеры детали: длина 1460 мм, ширина 782 мм, высота 760 мм.
По периметру плоскости разъема 1240х602 мм расположены 30 отверстий М16-7Н для соединения с крышкой корпуса. Отверстия по плоскости разъема выполняются глухими глубиной 35 мм, и длиной резьбы 25 мм. По периметру плоскости основания 910х450 мм - десять отверстий Ø45 мм с шероховатостью Ra 12,5 мкм для крепления к плите.
С 2-х сторон корпуса находится по 2 фланца.
В выступах имеются сквозные ступенчатые отверстия, где диаметры 1-й ступени Ø350Н7 с шероховатостью Ra 1,6мкм и 2-й ступени - Ø330Н7мм с шероховатостью Ra 1,6мкм.
По окружности Ø420 мм фланцев радиально расположены по 6 глухих резьбовых отверстий М20-7Н. Они расположены друг к другу под углом 60°.
В нижней части детали с 2-х сторон имеются трубки (фланцевого типа). А в верхней части - уши размером 160мм. В трубках имеются сквозные отверстия Ø80 мм.
На фланцах трубок по окружности Ø420 мм радиально расположены 4 сквозных отверстия Ø16 мм.
В нижней части детали также имеются ребра толщиной 24 мм в количестве 12 шт.
Сама деталь «корпус вибратора» имеет коробчатую форму и является полой. Размеры полости: 1020х482х595 мм.
По плоскости разъема расположены 4 ступенчатых сквозных отверстия Ø16мм для подачи масла в подшипники.
В отверстиях фланцев имеются по 3 выточки R25мм по Ø340 мм и одна выточка R16мм по Ø350 мм.
1.2.2 Изучение и анализ рабочего чертежа детали
Чертеж детали «корпус вибратора» представлен на чертеже в масштабе 1:5 и выполнен на листе формата А1.
Деталь изображена в 3-х видах с достаточным количеством разрезов и сечений.
Габаритные размеры детали: длина 1460мм, ширина 782мм, высота 760мм.
Поверхность основания имеет размеры 450±0,8х910±0,5 мм и шероховатость Ra 6,3 мкм, высота основания 35±0,3 мм.
В основании имеются 10 отверстий Ø45±0,3 мм для крепления детали к плите болтами. Вдоль основания отверстия расположены на расстоянии 200±0,6 мм и 175±0,5 мм по ширине начиная от оси.
С двух сторон детали расположены трубки (по одной с каждой стороны) фланцевого типа для подвода и отвода масла. Диаметр трубок Ø90±0,4 мм; сквозное отверстия в трубках Ø80±0,35 мм.
Фланцы на трубках Ø185±0,6 мм и толщиной 18±0,2 мм, служат для присоединения со шлангами для подвода и отвода масла. Во фланцах расположено по 4 отверстия Ø18 мм радиально по окружности Ø150 мм. Отверстия служат для соединения фланцев со шлангами.
В фланцах имеются ступенчатые отверстия Ø350Н7мм, Ø330±0,7 мм. Технологические ограничения к механической обработке этих отверстий по 7-му квалитету предъявлено правильно, так как в них устанавливаются подшипники. В отверстиях имеются 3 выточки R25 мм служащие для извлечения подшипников. Они расположены друг к другу по окружности Ø340 мм под углом 120°. На торце выступов имеются по 6 отверстий М20-7Н служащие для крепления крышек.
Уши размерами 200±0,6х30±0,25 мм со сквозными отверстиями Ø40±3 мм для перемещения детали.
Полость в детали размерами 1120±0,8х482±1,5х595 мм служит для размещения деталей узла.
1.2.3 Отработка конструкции детали на технологичность
Анализ конструкции детали на технологичность обеспечивает улучшение разрабатываемого технологического процесса. Основные цели анализа конструкции детали на технологичность: выявление недостатков конструкции детали по сведениям, содержащимся в чертежах и технических требованиях, возможное уменьшение трудоемкости и металлоемкости детали высокопроизводительными методами обработки. Таким образом, улучшение технологичности конструкции позволяет снизить себестоимость ее изготовления без ущерба для служебного назначения. Анализ конструкции детали на технологичность проводится на основе качественной и количественной оценки.
Деталь «корпус вибратора» - представляет собой отливку коробчатой формы из углеродистой стали марки 40Л. Отливка довольно сложна по конфигурации и требует применения стержневой формовки для образования внутренних полостей, а также применения отъемных частей формы ввиду наличия у детали выступов и бобышек на боковой поверхности. Исходя из конструктивных соображений и необходимой прочности, толщина стенок принята 25 мм. Следовательно, условию минимальной металлоемкости данная деталь удовлетворяет.
С точки зрения механической обработки нетехнологичным является образование и обработка проточек R25 мм и R15 мм в отверстиях фланцев.
Также нетехнологичным является обработка цековок в основании, так как она требует применение специального инструмента.
С точки зрения подвода инструмента к обрабатываемым поверхностям все поверхности доступны.
В остальном деталь достаточно технологична, допускаем применение высокопроизводительных режимов обработки, имеет хорошие базовые поверхности для первоначальных операций.
Количественная оценка детали на технологичность:
Количественный анализ детали определяется нахождением коэффициентов: коэффициент унификации конструктивных элементов, коэффициент точности обработки, коэффициент шероховатости поверхности.
Коэффициент унификации конструктивных элементов определяется по формуле:

где:


Определяем унифицированные размеры:
- 1460, 530, 265, 60, 60, 200, 40x4, 360, 45, 45, Ø80, Ø90, Ø185, 1,5х2, 15, 420, 910, 35, 470, 1240, 560, 620, 560, 265, 265, 60, 30х2, 170х2, 40, 120, 30, 30, 25, 35, 15, 130, 60, 150, 45, 35, 140, 340, 10,130, 140, 115, 35, 360,615, 200х4, 175,2, Ø45х10, Ø 10, R250, М20х24, 120х10, 560, R15, R25, 110.
Не унифицированные размеры:
- 18, Ø128, Ø134, 32х2, М16х30, 602, 112, Ø16х4, 782, 391, 482, 2, R1x4, 8, Ø18х8
Унифицированные шероховатости:
Ra12,5х4, Ra25х164
Неунифицированные шероховатости:
Ra6,3x2, Ra3,2, Ra1,6x2
Количество унифицированных размеров

Количество всех размеров

Рассчитываем коэффициент унификации конструктивных элементов
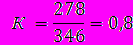
Коэффициент точности обработки определяется по формуле:

где:


где: n- число размеров соответствующего квалитета;
Значения квалитетов: Н7х3, Н10х2, Н11, Н12, Н15, Н14х130.
Всего квалитетов: n=173

Тогда:
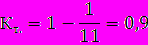
Коэффициент шероховатости поверхностей рассчитывается по формуле:

где: Бср. - среднеарифметическое числовое значение шероховатости, которое рассчитывается по формуле:

где: n - число поверхностей, соответствующей шероховатости;
Значение параметров шероховатости: 1,6х2, 3,2, 6,3х2, 12,5х4, 100х164.
Отсюда:

Тогда:
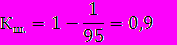
Коэффициент использования материала рассчитывается по формуле:

где: m- масса готовой детали, 1110 кг;
М - масса заготовки, 1245 кг;
Отсюда:
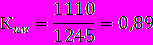
Проведя количественный анализ детали на технологичность можно сделать вывод, что она достаточно технологична, так как все коэффициенты стремятся к единице.
1.2.4 Расчет такта выпуска и установление типа производства
Определение типа производства необходимо с технологической точки зрения для того, чтобы в дальнейшем выбрать правильный метод получения заготовки, составить маршрут обработки, выгодный с экономической точки зрения, правильно выбрать инструмент, оборудование, технологическую оснастку и сделать все практические расчёты. Тип производства играет значительную роль при построении технологического процесса, поэтому прежде, чем приступить к проектированию технологического процесса, из заданной производственной программы и характера подлежащей обработке детали определяем тип производства
Определяем такт выпуска, который рассчитывается по формуле:

где:

N- годовая производственная программа, шт.; N=60 шт.;

Определяем среднюю длительность выполнения одной операции, исходя из норм времени по всем операциям технологического процесса по формуле:

где: Т шт.к - штучное время выполнения одной операции, мин;
n- количество операций;
Операция 005: Расточная, Тшт.=152,7 мин.;
Операция 010: Расточная, Тшт.=276,00 мин.;

Определяем коэффициент серийности, который рассчитывается по формуле:

где:

Тшт.ср. - среднее штучное время, мин;
Высчитываем Кс:
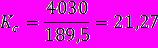
Так как коэффициент серийности 20<Кс<30, следовательно, данный тип производства относится к мелкосерийному.
1.2.5 Анализ методов получения заготовки и расчет ее себестоимости
Метод получения заготовок для деталей машин определяется назначением и конструкцией самой детали, материалом, техническими требованиями, масштабом и серийностью выпуска, а так же экономичностью изготовления. Выбрать заготовку - значит установить способ её получения, наметить припуски на механическую обработку каждой поверхности, рассчитать размеры и указать допуски на неточность изготовления.
Литьё - один из наиболее распространённых способов получения заготовок. Сущность литейного производства в получении заготовок путём заливки расплавленного металла в литейную форму, при охлаждении которой металл затвердевает, скопировав конфигурацию формы. Заготовка, получаемая литьём, называется отливкой.
Наиболее распространённым способом изготовления отливок является литьё в песчано-глинистые формы. Данным методом получают заготовки любой массы, конфигурации и любых габаритов. Отливки имеют невысокую точность размеров 16-17 квалитет, кроме того имеют большие припуски на механическую обработку. Метод отличается технологической универсальностью и дешевизной. Отливка получается в результате заполнения расплавленным металлом литейной формы, изготавливаемой из кварцевого песка, глины, цемента, жидкого стекла, битума и т.д. От способа формовки зависит точность и качество поверхностного слоя отливки. Формовка - это процесс изготовления песчано-глинистых литейных форм. Различают два вида формовки: ручную и машинную. Ручная формовка применяется в основном в условиях единичного и мелкосерийного производства отливок, а также при получении крупных отливок. Машинную формовку используют в условиях массового и крупносерийного производства, она осуществляется на специальных формовочных машинах, которые производят уплотнение формовочных смесей и извлечение модели из формы.
Проанализируем два способа получения заготовки литьём в песчано-глинистые формы: при ручной и машинной формовке.
Расчёт себестоимости заготовки получаемой литьём в песчаные формы ручной формовки производится по формуле:

где:


Q - масса заготовки, кг; Q= 1245 кг;
q - масса готовой детали, кг; q = 1110 кг;













Расчёт себестоимости заготовки получаемой литьём в песчаные формы ручной формовки:

Расчёт себестоимости заготовки получаемой литьём в песчаные формы машинной формовки:

Способ получения заготовки принимается получаемой литьём в песчаные формы ручной формовки, так как себестоимость получения заготовки данным методом меньше, чем себестоимость заготовки, получаемой литьем в песчаные формы машинной формовки (33729>32195 руб.). Для полученной заготовки принимаем класс размерной точности - 12, размерный ряд - 4.
Спроектированная форма состоит из двух опок с вертикальной плоскостью разъема (рис. 1, а), четырех керамических стержней диаметром 325 мм (рис. 1, б), двух керамических стержней диаметром 75 мм (рис. 1, в), верхней вставки (рис. 1, г) и нижней вставки (рис. 1, д).
![]() | ![]() | ![]() |
![]() | ![]() |
Рисунок 1 – Составные части литейной формы: