Курсовая работа по дисциплине «Технология приборостроения»
Вид материала | Курсовая |
- Курсовая работа Курс по дисциплине «Рекламное дело», 50.07kb.
- Московский Государственный Университет технологий и управления курсовая, 5.68kb.
- Курсовая работа по кафедре политической экономии, 105.07kb.
- Курсовая работа по дисциплине «История отечественного государства и права», 15.43kb.
- Методические указания к курсовой работе по дисциплине "Эксплуатация асоииУ", 1565.55kb.
- План введение стр 3 глава теоретическая часть сертификация и стандартизация в системе, 917.4kb.
- Методические рекомендации по написанию контрольной работы (реферата) по дисциплине, 270.13kb.
- «Проектирование и технология производства эа» мгту им. Н. Э. Баумана, 138.83kb.
- Курсовая работа по дисциплине, 9.38kb.
- Методические указания к выполнению курсовой работы для студентов специальности, 77.5kb.
санкт-петербургский государственный университет информационных технологий, механики и оптики |
Курсовая работа по дисциплине «Технология приборостроения» на тему |
«Анализ целесообразности применения КИМ в операции технического контроля» |
|
|
Выполнил студент группы 5659 Дроздков Андрей Николаевич |
Санкт-Петербург, 2010 год.
Оглавление
Оглавление 2
Введение 2
1.Анализ исходных данных и постановка задачи 4
1.1.Понятие геометрической точности 4
1.2. Информация об операции технического контроля 5
1.3.Анализ методов измерений и контроля геометрической точности на основе технологического процесса изготовления детали типа «корпус» 8
2.Анализ использования координатно-измерительной машины на ЗАО «Диаконт» 15
2.1.Общая информация о предприятии 15
2.2.Производственный процесс на ЗАО «Диаконт» 20
2.3.Использование координатно-измерительных машин в отделе ОТК на ЗАО «Диаконт» 23
3. Модернизированный технологический процесс изготовления детали типа «корпус» 28
3.1.Используемое ПО 28
3.2.План контроля детали 32
3.3.Преимущества и недостатки использования КИМ для контроля детали D70-03.10.03 35
3.4.Модернизированный технологический процесс изготовления корпусной детали D70-03.10.03 37
Заключение 39
Список использованной литературы 40
Введение
Современное состояние технологии – это постоянное, безостановочное движение вперед. В общем случае, новые технологии и способы обработки заготовок позволяют обеспечивать высочайшее качество и долговечность выпускаемого продукта, а жесточайшая конкуренция на рынке не оставляет технологам всего мира иного выбора, кроме как трудиться, трудиться и еще раз трудиться над обеспечением этих параметров.
Одной из важнейших характеристик качества большинства изделий в сфере приборостроения является точность. Она выступает критерием долгой безотказной работы прибора в различных условиях функционирования, что является даже не желательным, а, скорее, обязательным условием выпуска на рынок конкурентоспособного товара, обеспечивающего производителю не только неплохую прибыль, но и хороший имидж. Причем последний, в лучшем случае, должен быть международным.
В последние десятилетия произошла своеобразная революция в области приборо- и машиностроения. Повсеместное многообразное использование компьютеров и вычислительных систем, управление жизненным циклом изделий на всех этапах производства, технологии быстрого прототипирования, использование многокоординатных лезвийных и электроэрозионных станков с числовым программным управлением, - все это позволяет обеспечивать доселе недосягаемые параметры геометрической точности производимых изделий в диапазоне нескольких десятых долей микрометра. Однако достаточно ли этого?
Одним из элементов системы управления качеством на любом предприятии является организация технического контроля. И без его осуществления невозможно понять, соответствует ли изготовленная деталь или изделие требованиям, предъявленной ей конструктором, технологом и потребителем.
Повышение параметров точности обработки изделий обуславливают и повышение требований к измерительным приборам и системам, и уже далеко не всегда классические способы контроля могут обеспечить определение состояния изделия с требуемой точностью и погрешностью. Использование множества разнообразных инструментов для измерений и снятия показаний с изделия при необходимости контроля большого количества различных параметров всегда обеспечивает трудоемкость операции технического контроля, что зачастую означает высокие показатели норм времени и низкую производительность труда.
Цеховые координатно-измерительные машины решают эту проблему. Они достаточно компакты для размещения прямо в цеху, просты в освоении и использовании, для из обслуживания достаточно всего одного человека, а достигаемая точность выполняемых измерений варьируется в границах нескольких микрометров. Однако высокая стоимость, зависимость от наличия на предприятии лицензий CAD-систем, сложность и большие затраты времени на написание управляющих программ ограничивают применение координатно-измерительных машин на любых предприятиях.
В данной работе ставится вопрос о границах целесообразности использования КИМ в рамках предприятия ЗАО «Диаконт». Исследуется результативность модернизации технологического процесса изготовления детали типа «корпус» в результате замены классической операции контроля операцией контроля с использованием КИМ; изучаются принципы работы координатно-измерительной машины и принципы взаимодействия пользователя с ней.
-
Анализ исходных данных и постановка задачи
Понятие геометрической точности
Обеспечение заданной точности детали - основное требование к технологическому процессу. Точность детали можно охарактеризовать как степень соответствия ее требованиям чертежа и технических условий. Основными параметрами геометрической точности детали являются точность выполнения размеров, формы и относительного положения поверхностей. Под точностью формы поверхности понимают степень соответствия ее размеров в осевом и поперечном сечениях требуемой геометрической форме [2].
Существует три вида размеров:
- Номинальные – размеры на чертеже
- Предельные – границы «годности» изделия
- Действительные – размеры готового изделия, изготовленные с допустимой погрешностью.
Точность размеров определяется допуском на размер. Допуск - это разность между наибольшим и наименьшим предельными размерами, или разность между верхним и нижним предельными отклонениями:
- IT = Dнб – Dнм = ES – EI для обхватывающих размеров
- IT = dнб – dнм = es – ei для обхватываемых размеров
Размер поля допуска определяется квалитетом и величиной номинального размера. Влияние квалитета на допуск больше, чем влияние размера. В соответствии с ЕСКД, квалитет – это совокупность полей допусков всех номинальных размеров одной степени точности. Однако квалитет можно охарактеризовать и как степень точности. Чем выше квалитет, тем меньше поле допуска, тем меньше значения предельных отклонений от номинального размера и тем жестче требования к изготавливаемому изделию.
-
Информация об операции технического контроля
Операция контроля включает действия по проверке одного или нескольких контролируемых признаков у одного или нескольких объектов контроля. В зависимости от объектов контроля различают:
- контроль технологического процесса;
- контроль качества продукции;
- контроль средств технологического оснащения;
- контроль технической документации.
Организация технического контроля на предприятии является одним из элементов системы управления качеством. Под техническим контролем понимается проверка соблюдения требований, предъявляемых к качеству продукции на всех стадиях ее изготовления, и всех производственных условий, обеспечивающих его.
Основной задачей технического контроля является обеспечение выпуска высококачественной и комплектной продукции, соответствующей стандартам и техническим условиям.
По формам технический контроль может быть пассивным, когда просто фиксируются данные о качестве продукции (констатируется факт), и активным, когда не только оценивается качество, но и оказывается активное воздействие на технологический процесс с целью управления качеством.
По назначению технический контроль различают:
- входной, определяющий соответствие закупаемых для производства сырья, материалов, полуфабрикатов и комплектующих изделий требованиям научно-технической документации ;
- предварительный, осуществляется с целью предотвращения поступления в производство бракованных предметов труда и заключается в проверке качества сырья, материалов, полуфабрикатов и комплектующих изделий до начала их обработки (сборки);
- промежуточный, осуществляется в процессе изготовления какого-либо объекта по отдельным операциям. Он может быть пооперационным (проверка после каждой операции) и групповым - проверка после нескольких операций;
- окончательный, производится при приемке готовых изделий для выявления некачественной продукции.
- По возможности использования продукции контроль может быть разрушающий и неразрушающий
- По месту выполнения контрольных операций различают:
- стационарный контроль - производится на специально оборудованном постоянном рабочем месте контролера, куда поставляются объекты контроля;
- подвижной контроль - осуществляется на том рабочем месте, где выполняются операции.
По степени охвата контроль может быть сплошным (проверке подвергаются все без исключения объекты контроля одного наименования) и выборочным (проверке подвергается часть партии однородных объектов с использованием статистических методов контроля) [2].
Забегая вперед, отмечу, что на ЗАО «Диаконт» операция контроля занимает одно из важнейших мест в структуре любого технологического процесса. В силу своей профессиональной ориентации, предприятие вынужденно работать в условиях потенциально нулевого брака, так как любой отказ выпускаемого оборудования может привести к страшным последствиям, от потери заказчиков с одновременным падением имиджем компании до серьезных аварий на атомных ЭС, в результате которых могут пострадать и даже погибнуть люди.
Все это вынуждает ужесточать требования к качеству изделий и производить промежуточный технический контроль выполнения каждой технологической операции, связанной с процессом механообработки и нанесения покрытий. Помимо этого, в конце технологического процесса всегда назначается операция общего окончательного технического контроля.
Эти факторы заставляют задуматься о потребности использования для данных нужд последних достижений науки и техники и автоматизации процесса контроля и измерений.
-
Анализ методов измерений и контроля геометрической точности на основе технологического процесса изготовления детали типа «корпус»
Выбор способа и средств измерения геометрических размеров зависит от ряда факторов, основными из которых являются:
- допуски на размеры и точность изготовления измеряемой детали;
- метод контроля (пассивный или активный) и его точность;
- объем выпуска деталей;
- конструктивные особенности детали и экономические показатели назначаемых средств измерения (стоимость прибора, его производительность, время настройки, требуемая квалификация контролера).
Выбор измерительного средства по точности осуществляется сравнением предельной суммарной погрешности измерения и допуска на размер детали.
Необходимо выбрать такое измерительное средство, при котором искажение полученных результатов измерения настолько мало, что эти результаты измерения можно было бы принять за действительный размер. Величины допустимых предельных погрешностей измерения деталей, как правило, не должны превышать 30% от размера допуска.
В соответствии с чертежом корпусной детали, являющейся частью объектива видеокамеры, можно сделать следующие выводы:
- Деталь представляет собой корпус типа «Тело вращения»
- Габариты детали 26х25х25 мм.
- Имеется две наружных цилиндрических поверхности, выполняемых по 6-ому квалитету.
- Имеется одна внутренняя цилиндрическая поверхность, выполняемая по 7-ому квалитету
- Имеется несколько резьбовых элементов высокой точности.
- Шероховатость отдельно взятых внутренних и наружных цилиндрических поверхностей составляет 1.6 мкм по параметру Rа.
Анализируя технологический процесс выполнения детали, следует отметить, что для ее выполнения, в основном используются станки, снабженные стойкой ЧПУ, что говорит о достаточно сложной конфигурации детали и трудностях ее изготовления на универсальном оборудовании даже рабочими высокой квалификации. Не считая заготовительной операции, для изготовления детали используется один токарно-винторезный станок, один токарный станок с ЧПУ и один фрезерный станок с числовым программным управлением. В качестве работ по кооперации производится анодное оксидирование в операции электрохимического окисления. После выполнения каждой операции прямо на рабочем месте производится промежуточный контроль состояния детали.
В исходном технологическом процессе используется следующая оснастка:
- Для контроля линейных размеров по h12, Н12, IT12/2 и позиционных допусков
- Штангенциркуль ШЦ-1-125-0.1 ГОСТ 166-89
- Набор плоско-параллельных концевых мер длинны 2 класс (0.3 – 0.9) ГОСТ 9038-73
- Набор плоско-параллельных концевых мер длинны 3 класс (0.5 – 100) ГОСТ 9038-73
- Для контроля внутренних диаметров
- Калибр-пробка гладкая 15Н7 ГОСТ 14810-69
- Калибр-пробка гладкая 14Н7 ГОСТ 14810-69
- Для контроля наружных диаметров
- Микрометр МК-25-2 ГОСТ 6507-90
- Скоба СР 25 ГОСТ 11098-75
- Для контроля резьбы
- Калибр кольцо резьбовое М19х0.75-6g ПР ГОСТ 17763-72
- Калибр кольцо резьбовое М19х0.75-6g НЕ ГОСТ 17764-72
- Калибр пробка резьбовая М16х0.5-6Н ПР ГОСТ 17758-72
- Калибр пробка резьбовая М1,4 -6Н ПР ГОСТ 17756-72
- Калибр пробка резьбовая М1,6 -6Н ПР ГОСТ 17756-72
- Для контроля шероховатости поверхности
- Образцы шероховатости поверхности ГОСТ 9378-75
Всего в технологическом процессе 4 операции контроля. На одной из них контролируется только качество покрытия после анодного оксидирования, поэтому норма штучного времени на нее составляет всего 2 минуты. Сумма норм штучного времени для оставшихся трех операций контроля составляет 40 минут. Однако стоит учитывать, что на ЗАО «Диаконт» отсутствует какая-либо система или свод правил для нормирования технологических операций. При написании любого технологического процесса технолог ЗАО «Диаконт» руководствуется только интуицией и своими знаниями производственных процессов и их специфики на данном предприятии. Изначально нормы времени назначаются «с потолка», и, в случае ошибки технолога, позже корректируются с выпуском извещения об изменении. Учитывая, что технологический процесс был разработан 21 января 2010 года, и получен мной в качестве исходных данных моего задания спустя всего несколько дней, можно сделать вывод, что нормы штучного времени на операцию немного отличаются от реального затрачиваемого времени. Но с этого самого момента примем за аксиому и будем считать, что в общей сложности на операции контроля моей детали типа «корпус» тратится порядка 45 минут. И это без учета промежуточного контроля на рабочих местах операторов станков.
Также не стоит забывать, что, независимо от используемых инструментов, способов и продолжительности, в процессе измерений всегда имеет место человеческий фактор.
Ко всему прочему, такие представители средств измерений, как штангенциркули и микрометры, хотя и я остаются по сей день самыми распространенными и используемыми инструментами определения геометрии деталей и заготовок, являются динозаврами этой области. Подобными средствами пользовались и два поколения назад, это становится очевидным, если взглянуть на ГОСТы этих изделий. А предназначенные для контроля качества микроскопы, с одновременным обеспечением точности измерений добавляют трудности в виде долгой настройки оборудования и жесткой зависимости от механических вибраций.
Любой технический прогресс связан с частичным исключением человека из процесса производства и заменой его машиной, выполняющей его работу быстрее и качественнее. С этой целью не так давно на ЗАО «Диаконт» были закуплены две координатно-измерительные машины фирмы Zeiss. Одна из них, Zeiss DuraMax, была куплена совместно с НИУ ИТМО, и именно с ней связана эта работа. Изображение машины представлено на рис.1.
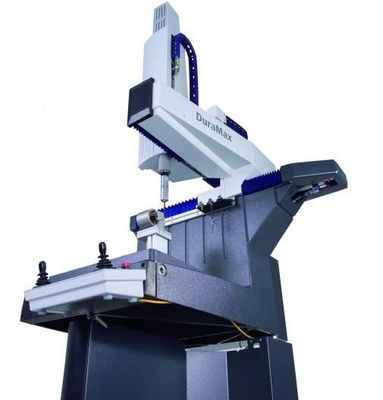
Рис.1. Общий вид КИМ “Duramax”
Основные характеристики:
- Zeiss DuraMax хорошо подходит для контроля производственного процесса непосредственно в цехе, для быстрого контроля между операциями для малогабаритных деталей, а также для контроля объемных партий в процессе производства
- Максимальные габариты измеряемого изделия 500х500х500 мм, что сравнительно много для машин этого класса
- Машина всегда готова к измерениям и после включения не требует дополнительных настроек и подстроек
- Пригодность для работы в «горячих» производственных условиях: защита от вибраций станков и оборудования, широкий диапазон рабочей температуры
- Высокая точность измерений: Значение максимально допустимой погрешности MPE лежит в пределах от 2,4 + L/300 мкм при +18°C...+22°C и 2,9 + L/200 мкм при +18°C...+30°C. Это инновационные показатели в данном классе машин
- Сканирование – это не опция, а стандартная характеристика DuraMax, наряду с возможностью и обычного одноточечного ощупывания
- Наличие CAD-ориентированного программного обеспечения CALYPSO, полностью переведенного на русский язык
- Планы контроля для Zeiss DuraMax создаются на основе трехмерных моделей контролируемых деталей [8].
Данная координатно-измерительная машина позволяет производить контроль деталей различных геометрических форм в диапазоне размеров до 500 мм. Контролировать можно любую деталь, даже ту, для которой отсутствует виртуальная 3D-модель. В программном обеспечении CALYPSO встроены алгоритмы контроля стандартных геометрических форм, а также имеется возможность собственноручного написания управляющих программ для измерений. Однако это чрезвычайно трудоемкий и долгий процесс. Так, для написания плана контроля детали сложной конфигурации или точной геометрии, даже профессионалу может понадобиться порядка трех рабочих смен.
Учитывая приведенную выше информацию, можно сказать, что наряду с процессом автоматизации операции контроля и обеспечением быстрых и качественных измерений с погрешностями, количественно сравнимыми с погрешностями таких точных измерительных приборов, как микрометр, компактности, универсальности и простоты в использовании, применение КИМ Zeiss DuraMax чревато существенными минусами, такими, как сложность программирования машины при неполной автоматизации процессов конструирования изделий и отсутствии требуемого программного CAD-ориентированного обеспечения, а также нецелесообразность использования КИМ в условиях единичного производства и при выпуске изделий очень малыми партиями в несколько штук. Также не стоит забывать, что, несмотря на простоту в освоении и использовании, для обслуживания и работы с машиной требуется либо специалист с профильными знаниями и навыками, либо время на ознакомление с измерительным комплексом, что влечет за собой дополнительные материальные затраты и простой оборудования.
Целью данной работы является анализ целесообразности применения конкретной координатно-измерительной машины в конкретных условиях на конкретном предприятии для контроля конкретной детали. На данном этапе было дано определение понятию точности изделий, раскрыта общая информация о операции технического контроля и ее специфике на ЗАО «Диаконт», были проанализированы исходные данные в виде конструкторской и технологической документации для конкретной детали типа «Корпус» и рассмотрены общие особенности применения координатно-измерительной машины Zeiss DuraMax в операции контроля качества изделия. Для анализа целесообразности применения ее на данном предприятии необходимо обработать информацию о выпускаемых на предприятии изделиях, серийности и объемам выпуска, используемом оборудовании и программном обеспечении. Необходимо рассмотреть структуру, понять специфику предприятия, собрать информацию о общем использовании координатно-измерительных машин в процессе производства деталей и приборов в целях контроля выполнения операций механообработки и собираемости изделий, сделать выводы о возможности ее использования в процессе селективной сборки. Нужно проанализировать полученную информацию, соотнести ее с условиями изготовления на группе станков детали типа «корпус» и сделать однозначный вывод о нежелательности, возможности или экономической предпочтительности модернизации технологического процесса изготовления детали путем замены классической операции технического контроля операции контроля качества с использованием координатно-измерительной машины Zeiss DuraMax.
-
Анализ использования координатно-измерительной машины на ЗАО «Диаконт»
Общая информация о предприятии
ЗАО "Диаконт" - это ведущее российское инженерно-производственное предприятие, предлагающее эффективные решения для повышения безопасности атомных станций в более чем 10-ти странах мира.
К числу заказчиков относятся атомные электростанции России, Европы, США и Японии, заводы по переработке радиоактивных отходов.
Лицензии Федеральной службы по экологическому, технологическому и атомному надзору СЕ-11-101-1341, СЕ-12-101-1342, СE-03-101-12-1038.
Предприятие производит радиационно-стойкую телевизионную аппаратуру; системы контроля герметичности оболочек тепловыделяющих сборок; системы управления дизель-генераторными установками атомных электростанций; манипуляторы для неразрушающего контроля оборудования АЭС, оказывает услуги по проведению количественного анализа безопасности транспортно-технологических процессов с ядерным топливом; проведению телевизионного контроля компонентов 1-го контура атомных электростанций; проведению внутритрубной диагностики трубопроводов газокомпрессорных станций открытого акционерного общества "Газпром".
Области специализации предприятия:
- Проектирование электрических схем
- Разработка программного обеспечения
- Конструирование
- Механическое производство
- Электрический и механический монтаж
- Управление проектами
- Контроль качества
Система качества на закрытом акционерном обществе «Диаконт» сертифицирована в соответствии со стандартом ISO 9001-2000.
Структура закрытого акционерного общества «Диаконт» представлена на рис. 2.
Управляющая компания разрабатывает цели предприятия и его структурных подразделений, планирует развитие предприятия, обеспечивает его инновационную деятельность, финансовую устойчивость и платежеспособность, всесторонне анализирует деятельность предприятия [4].
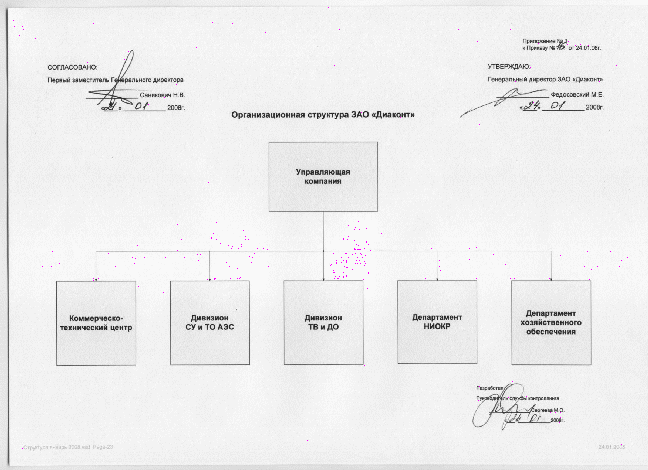
Рис. 2. Организационная структура закрытого акционерного общества «Диаконт»
Коммерческо-технический центр занимается продвижением и продажей продукции и услуг предприятия на российском и международных рынках в соответствии с целями предприятия, обеспечивает удовлетворенность заказчика за счет предложения ему комплексных организационно-технических решений, максимально отвечающих его требованиям.
Дивизион систем управления атомными электростанциями отвечает за создание конкурентоспособных систем управления перегрузочными машинами и дизель-генераторами атомных электростанций.
Дивизион телевизионного и диагностического оборудования отвечает за выпуск продукции и оказание услуг в соответствии с условиями договоров и с максимально эффективным использованием ресурсов, а так же за оптимизацию конструкции и технологии выпускаемых изделий, организации производства с целью снижения себестоимости.
Департамент научно-исследовательских и опытно-конструкторских работ обеспечивает повышение конкурентоспособности предприятия путем внедрения новых технических решений в существующую продукцию предприятия и разработкой принципиально новых продуктов.
Департамент хозяйственного обеспечения служит для удовлетворения всех хозяйственных потребностей предприятия.
Поскольку основными единицами производства на ЗАО «Диаконт» являются радиационно-устойчивые камеры внутреннего наблюдения и различные устройства для неразрушающего контроля атомного и газового оборудования, дивизион ТВ и ДО выступает важнейшей структурной составляющей всего предприятия. Этот дивизион создан с целью получения максимальной прибыли в процессе производства оборудования в соответствии с требованиями внешних и внутренних заказчиков в сроки, определённые заключёнными договорами, с минимальными затратами. В него входит непосредственно механическое производство и все, что требуется для его обеспечения: начиная от конструкторских разработок и контроля качества и заканчивая упаковкой и хранением. Структура этого дивизиона представлена на рис.3.
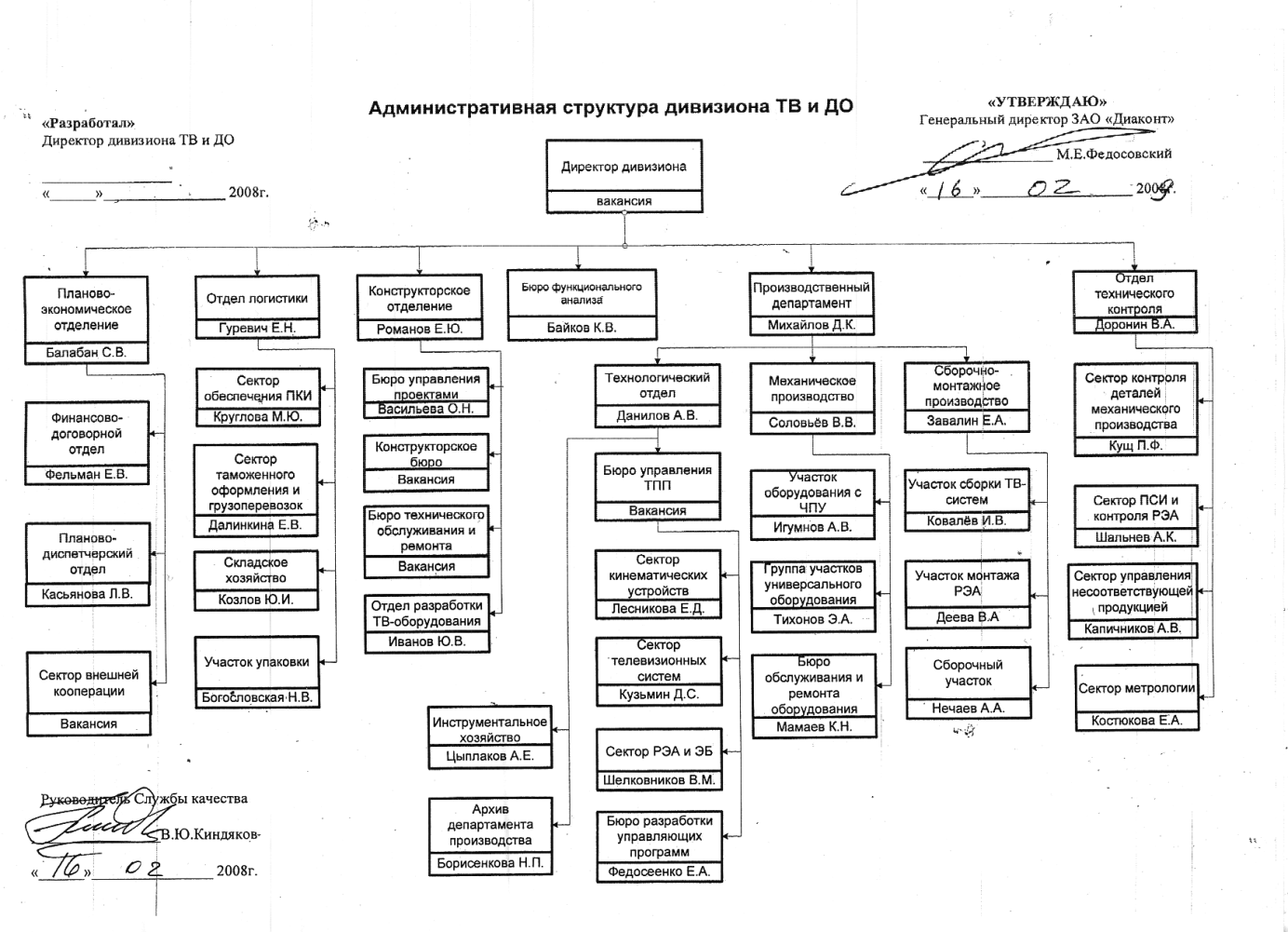
Рис. 3. Структура Дивизиона телевизионного и диагностического оборудования
Основной задачей дивизиона ТВ и ДО является осуществление его эффективной производственно-хозяйственной деятельности:
- выполнение внутренних и внешних договоров со структурными подразделениями ЗАО "Диаконт" и внешними заказчиками, согласно «Плана работ дивизиона» в установленные сроки, с требуемым качеством и минимальными затратами
- минимизация непроизводительных издержек дивизиона
- снижение косвенных расходов дивизиона
- создание системы мотивации персонала
- организационно-техническое развитие
В состав дивизиона ТВ и ДО в соответствии с утвержденной структурой и штатным расписанием входят
- конструкторское отделение
- планово-бюджетный отдел
- отдел логистики
- бюро анализа процессов управления производством
- производственный департамент
- отдел технического контроля
-
Производственный процесс на ЗАО «Диаконт»
В задачи коммерческо-технического центра предприятия, помимо продажи существующим заказчикам уже существующих товаров услуг, входит маркетинговое исследование рынка на выявление факта его потенциальной потребности в еще не производимых на предприятии изделиях или еще не реализуемых предприятием услугах. В случае обнаружения подобных изделий и услуг, а также в случае крупного заказа одного из клиентов предприятия, происходит быстрая и четкая формализация требований к продукту, и в работу включается дивизион НИОКР, а также конструкторский отдел дивизиона ТВ и ДО. На этом этапе реализуется конструкторская подготовка производства, первый элемент технической подготовки производства.
Результат работы этих двух дивизионов передается в технологический отдел производственного департамента дивизиона ТВ и ДО, где в кратчайшие сроки реализуется технологическая подготовка производства. В отделе совместно работают технологи и программисты станков с ЧПУ.
ЗАО «Диаконт» - предприятие с мелкосерийным типом производства. Партийность выпускаемых изделий колеблется от одной до восьмидесяти штук. В редких случаях количество изделий в партии превышает сто. При этом требования к качеству выпускаемых изделий жесточайшие. Плановые показатели заложенного в партию брака равны нулю не только для условия брака вне предприятия, но и для условия брака внутри во время производства. То есть, при наличии систематических погрешностей в виде погрешности закрепления и настройки оборудования, требуется свести к минимуму человеческий фактор. Поэтому в условиях выпуска деталей высокой точности или сложной пространственной конфигурации применение в производственном процессе станков с ЧПУ является предпочтительным.
Инженеры-технологи разрабатывают, используя средства автоматизированного проектирования, технологические процессы, обеспечивающие изготовление изделий требуемого качества с минимальными затратами производственных ресурсов. В качестве средств автоматизированного проектирования на предприятии «Диаконт» используется система автоматизированного проектирования «Интермех». Комплекс программ «Интермех» состоит из следующих функциональных модулей:
- Search (архивное хранение и управление документами);
- AVS (редактор спецификаций, перечней элементов и других документов ЕСКД);
- Imbase (база стандартных изделий, покупных изделий, сортамента, материалов и др.);
- Cadmech (разработка графической документации (чертежи, схемы));
- Techcard (разработка технологической документации).
Для разработки графической документации вместо модуля Cadmech используется система автоматизированного проектирования и черчения ZWCAD 2009.
При назначении операции на станке с ЧПУ инженер-технолог обязан сопроводить маршрутную карту требуемым количеством операционных эскизов, на основе которых программисты станков с ЧПУ строят твердотельные компьютерные модели, используемые для написания управляющих программ, текст которых впоследствии подкрепляется к маршрутной карте технологического процесса. Для создания 3D моделей изделий и написания управляющих программ на ЗАО «Диаконт» применяется CAD/CAM/CAE – система Unigraphics. В ней создание программы осуществляется путем назначения инструмента на переход и обозначения обрабатываемой поверхности на 3Д-модели изделия. Такой интерфейс гораздо больше адаптирован под пользователя, нежели написание программы с использованием Джи-кода. Поэтому написание управляющей программы фрезерования крыльчатки на пятикоординатном фрезерном станке возможно только с использованием CAD/CAM/CAE систем.
Из технологического отдела производственного департамента комплект технологической документации, включающий в себя маршрутную карту технологического процесса с подкрепленными к ней эскизами и текстами управляющих программ (в случае использования станков со стойкой ЧПУ) и чертеж изделия, переходит в отдел механического производства. Этот отдел включает в себя заготовительный участок с ленточно-пильными станками и гильотиной, участок оборудования с ЧПУ, представленный токарными станками фирмы Masturn, токарно-фрезерными Mazak, электроэрозионным станком Sodick и фрезерными обрабатывающими центрами, включающими новейший 5-ти координатный центр DMU 70eVO, а также группу участков универсального оборудования и бюро обслуживания и ремонта.
В отделе механического производства производится отрезка заготовок и последующая их механообработка с реализацией операции промежуточного контроля прямо на рабочем месте. Полученные изделия переходят в отдел ОТК для последующего контроля их качества.
-
Использование координатно-измерительных машин в отделе ОТК на ЗАО «Диаконт»
Измерительное оборудование Отдела ОТК на ЗАО «Диаконт» представлено во всем своем многообразии. Многочисленные шкафы с классическими измерительными приборами и разнообразными средствами измерений занимают добрые 30% площади отдела. Штангенциркули, представленные как старожилами со следами ржавчины на корпусе, так и высокотехнологичными собратьями с цифровым дисплеем, всевозможные скобы, микрометры, угломеры, калибры, наборы концевых мер длины на любой вкус. Для точных измерений размеров используются микроскопы, а для контроля шероховатости – профилометр. Однако наибольший интерес представляют новейшие мировые разработки в области технического контроля изделий – Координатно-измерительные машины марки «Zeiss», модели «Global» и «DuraMax».
Две эти модели абсолютно идентичны по техническим характеристикам, однако «Global» является машиной портального типа с качающимся щупом, а «DuraMax» - цеховой машиной с функцией сканирования.
Операции контроля с использованием координатно-измерительной машины при написании технологических процессов назначаются технологами все чаще. В основном, КИМ применяется для контроля деталей сложной пространственной конфигурации, размеры и параметры которой не просто долго, но и затруднительно контролировать с использованием стандартного измерительного инструмента.
Координатно-измерительные машины позволяют контролировать абсолютно все параметры детали, указанные на чертеже, за исключением:
- Резьбы
- Параметров шероховатости поверхности
- Маленьких фасок (меньше 2 мм)
Чаще всего с использованием КИМ контролируются первые детали в партии. И только в том случае, если они соответствуют всем требованиям чертежа, в производство запускаются остальные детали. Это позволяет избежать брака всей партии изделий с высокой вероятностью гарантируя их качество. А самое замечательное то, что план контроля для остальных деталей партии писать уже не придется.
КИМ используется как для окончательного контроля изделий, так и для промежуточного. В 70% случаев план контроля для машины пишется не для полного, а для пооперационного контроля изделия. Это позволяет контролировать выполнение отдельных операций и, в случае обнаружения брака, быстро и точно узнать, что послужило его причиной, и, как следствие, быстро эту причину устранить. Окончательный контроль изделий может быть выборочным и полным. Выборочный контроль предусматривает измерение параметров определенной выборки изделий партии, количественно составляющей около 20% их общего числа. При обнаружении недопустимого отклонения только у какого-то одного размера или параметра деталей выборки, остальные детали партии проверяются только по этому размеру или параметру, что позволяет быстро выявить бракованные детали и определить характер брака.
Во время измерений большое значение имеют условия окружающей среды. То, что современные КИМ компактны и предназначены для расположения прямо в рабочем цехе предприятия, не означает, что и изделие не зависит от внешних воздействий. Самый большой вред измерениям приносит тепловое расширение контролируемых деталей. Согласно статистике, каждое увеличение температуры окружающей среды всего на один градус цельсия приводит к увеличению детали длиной 1 м на целых 20 микрометров. Поэтому на ЗАО «Диаконт» координатно-измерительные машины стоят в отдельном помещении, где с помощью кондиционеров поддерживается наиболее благоприятный микроклимат. Погрешность измерений в таких условиях для детали размером 300 мм составляет 2 микрометра.
Использование КИМ возможно с помощью управляющей программы и в ручном режиме. Ручной режим характеризуется использованием стойки управления и имеет место при контроле каких-то единичных параметров детали, а также при быстром контроле детали простой конфигурации. Это лишает пользователя необходимости написания управляющей программы, что существенно упрощает и ускоряет процесс взаимодействия человека с КИМ.
Управляющие программы для КИМ пишутся с использованием КАД-ориентированных систем. На «Диаконте» в роли такой программы выступает «Unigraphics», однако это могут быть и «Cimatron», и «CATIA», и «Solid Works». В ней создается требуемая твердотельная модель изделия (причем это может быть как конечное состояние изделия, так и множество промежуточных состояний, например, по операциям), которая потом конвертируется в требуемый формат данных и загружается в специальную программу CALYPSO, поставляемую фирмой Zeiss вместе с КИМ. ПО «CALYPSO» не имеет встроенных средств для создания 3D моделей изделия, однако обладает функциями ограниченного редактирования моделей, такими, как сглаживание поверхности и удаление требуемых элементов модели. Хотя это все лишь условности, потому что, на мой взгляд, очевидно, что гораздо удобнее править модель в той программе, в которой она была создана.
После импортирования файла с моделью и, если требуется, его редактирования, задаются все элементы детали, которые будут использованы в процессе контроля: плоскости и точки. Затем вводятся параметры всех ходов и перемещений щупа. Иными словами, виртуально моделируется «процесс ощупывания» изделия. Стоит отметить, что при наличии 3D модели мы уже имеем в памяти компьютера все номинальные размеры изделия. Поэтому все, что нам остается сделать для завершения написания программы – это вручную задать допуск на каждый размер в соответствии с чертежом. После этого программа запускается и проходит процесс отладки.
Даже написание программы с уже имеющейся трехмерной компьютерной моделью детали занимает у программиста КИМ 4-8 часов в зависимости от сложности ее геометрической конфигурации. Написание же программы для контроля сложной детали вручную может занять несколько рабочих смен. Поэтому ручные измерения применяются только для элементарных и единичных параметров изделий. Но зато применяются довольно широко.
Несмотря на сложность процесса создания управляющей программы, процесс измерения с помощью КИМ может уменьшить время выполнения операции контроля со 180 до 20 минут максимум. Производительность работы и многократность использования одной программы для контроля всей партии изделий обусловливают оправданность применение КИМ уже при размере партии в 10 штук.
К тому же, КИМ «DuraMax», помимо щупа, оснащена VAST XXT сенсором для сканирования контролируемых заготовок. Несомненно, оптическое сканирование не подходит для сложных геометрических объектов типа крыльчаток, однако он повсеместно используется для исследования плоскостей, цилиндров, окружностей, конусов и прочих подобных объектов.
В частности, использование сенсора для сканирования объектов цилиндрической формы позволяет получить информацию о состоянии поверхности в каждой ее точке, в потом при помощи ПО «CALYPSO» вывести на экран диаграмму этого состояния. Далее можно получить информацию о максимальном и минимальном расстояниях между двумя противоположными точками поверхности, что соответствует реальным отклонениям формы и размеров от идеальных, узнать о участках поверхности, не попадающей в требуемое поле допуска. Использование оптического сенсора позволяет манипулировать полной информацией о состоянии поверхности изделия, а не довольствоваться данными полученными на основе ощупывания всего нескольких ее точек, что обеспечивает пользователя глобальной вооруженностью знаниями о причинах проблем, возникающих на этапах сборки в случае сопряжения особо точных и ответственных поверхностей.
-
Модернизированный технологический процесс изготовления детали типа «корпус»
Используемое ПО
Как уже было сказано в первой главе моей работы, для взаимодействия человека с КИМ DuraMax фирма-производитель Zeiss поставляет в комплекте с машиной программное обеспечение CALYPSO, которое позволяет решить весь необходимый спектр задач, возникаемых во время операции контроля, непосредственно в рамках производственного цеха.
Для более полного понимания принципов работы с машиной далее я приведу базовые понятия и определения.
Измеряемый элемент – непосредственно элемент, который необходимо контролировать или использовать в плане измерений. Он может быть реально существующим (плоскость, цилиндр) или сконструированным элементом, который физически не существует и необходим, к примеру, для описания сечения в виде прямой линии или оси цилиндра. При ручном ощупывании большинство геометрических элементов КАЛИПСО распознает автоматически. Процесс контроля размеров, формы и положения измеряемого элемента определяется контролируемыми параметрами. В общем случае, это параметры, указанные на конструкторском чертеже изделия. Совокупность контролируемых параметров, направлений и последовательности ощупывания различных измеряемых элементов составляют план контроля детали. В обычном понимании это так называемая управляющая программа для КИМ. В отличие от УП для станков с ЧПУ, номер плана контроля и факт его наличия никак не указываются в технологическом процессе изготовления детали.
Для точного определения положения детали в пространстве и надежного процесса измерений нельзя обойтись без точно определенных систем координат и возможности пересчета из одной системы координат в другую. В качестве основы команд перемещения и измерений КИМ служит система координат машины. Однако из-за непрактичности ее использования для проведения конкретных измерений, существует система координат детали, связанная непосредственно с деталью и ее положением и ориентацией на измерительном столе. Эта система координат вводится при начальном ощупывании и определении положения детали в пространстве. Для одного контролируемого изделия могут быть заданы несколько систем координат детали, но одна из них обязательно определяется для плана контроля в качестве базовой. Дополнительно для каждого измеряемого элемента можно использовать локальную систему координат, ориентация которой определена соответствующим образом через измеряемый элемент.
Запуск программы и ее интерфейс не являются новинкой для людей, имеющих опят работы в среде Windows. Двойной щелчок мыши по иконке CALYPSO открывает пользователю окно программы.
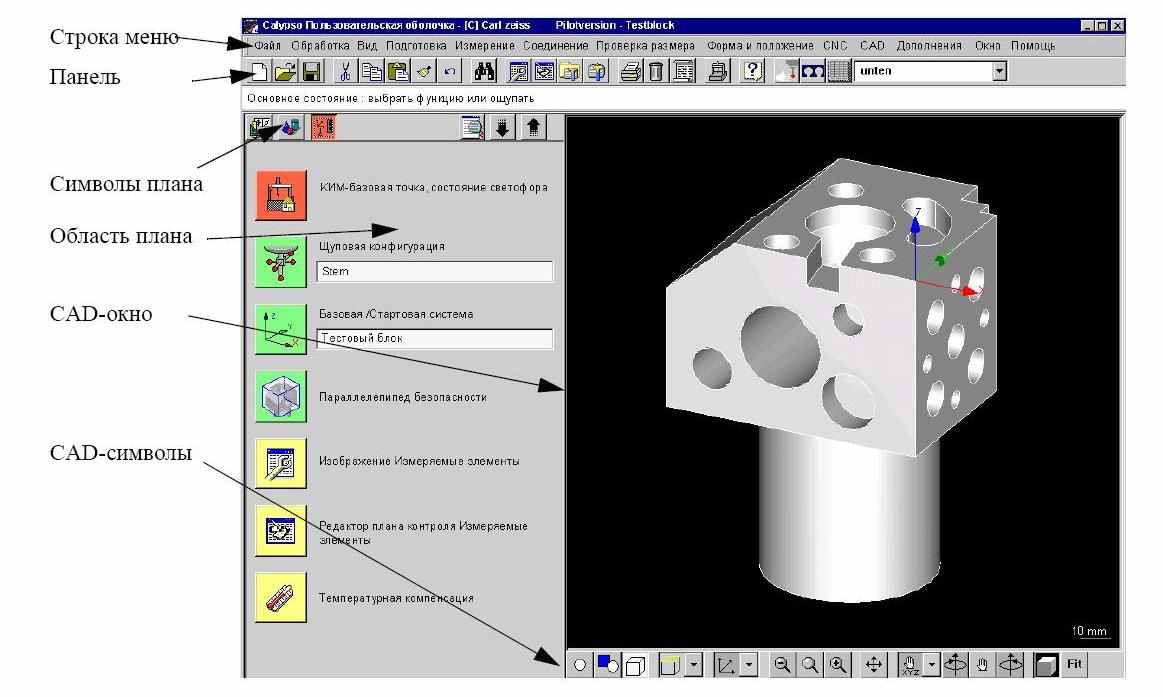
Рис. 4. Интерфейс ПО «Calypso»
CAD-окно служит для индикации CAD-файла, который содержит контролируемую деталь. Отображаемая деталь называется CAD-моделью. Эту модель в CAD-окне можно поворачивать, увеличивать или смещать – в зависимости от того, что необходимо пользователю для следующего действия. Однако изменение и редактирование модели в окне не представляется возможным.
CAD-окно призвано упростить работу пользователя. При наличии открытой модели измеряемой детали план контроля составляется без использования КИМ. Точки ощупывания и измеряемые элементы определяются обыкновенным щелчком мыши по необходимым элементам модели.
План контроля включает в себя любую последовательность контролируемых параметров, требуемых для их контроля измеряемых элементов, а также всю информации, необходимую для измерения: щуповую конфигурацию, систему координат детали, плоскость безопасности и так далее.
На предприятии «Диаконт» имеется набор разнообразных щуповых конфигураций, полностью удовлетворяющих требованиям ОТК, наименьший диаметр щупа, имеющегося на предприятии, составляет всего 0.5 мм. Перед работой необходимо калибровать установленную щуповую конфигурацию. Калибровка производится по сферическому эталону, поставляемому вместе с машиной. Погрешность его изготовления составляет порядка 0.5 микрометров, и сфера-эталон условно считается «идеальной». Назначение щуповой конфигурации и ее калибровка входят в этап «выполнение подготовительных операций».
Для повышения точности измерений в программе CALYPSO имеется функция температурной компенсации. Заданные значения точности, как правило, относятся к комнатной температуре 20º С, а различные материалы весьма по-разному реагируют на изменение температуры. Для учета температурной компенсации контролируемой детали необходимо ввести значение коэффициента теплового расширения для материала, из которого она изготовлена.
Генерирование путей ощупывания происходит автоматически, без участия пользователя, если введен параллелепипед безопасности. Если он не определен, пути ощупывания придется вводить вручную. Также стоит отметить, что написание плана контроля возможно и в полностью ручном режиме. Для этого КИМ оснащена пультом управления Dynalog P, который представляет собой комбинацию дисплея, компьютерной клавиатуры, мыши и пульта управления машиной.
После прогона плана контроля в CALYPSO создаются протоколы измерений. Они бывают трех видов: рабочий протокол, компактный протокол и презентационный протокол. Кроме того, имеется возможность экспорта данных в среду Microsoft Excel. По умолчанию создается рабочий протокол, однако в зависимости от желаний и потребностей пользователя, возможен выбор любого из вышеперечисленных вариантов. Результирующие отчеты просты в восприятии (особенно презентационный протокол) и удобны в использовании, а также обеспечивают документирование результатов контроля, что позволяет на основе имеющейся суммарной информации ввести какие-либо корректировки в производственный процесс для его оптимизации и улучшения качества изготавливаемой продукции.
Помимо CALYPSO, для КИМ DuraMax существует более новое и многофункциональное ПО HOLOS. Оно также выпускается фирмой-производителем ZEISS, но распространяется уже коммерческим путем. Основным его преимуществом перед базовой программой для КИМ является то, что она направлена на измерение не только геометрических элементов правильной формы, но и фасонных деталей с криволинейными поверхностями. Это стало возможно благодаря построению программы на основе принципа модульности. Модули HOLOS’а:
- HOLOS Geo: Измерение элементов правильной геометрической формы. Ориентировано на измерение кузовных деталей. Автоматическое управление действиями оператора.
- HOLOS Light: Измерение криволинейных поверхностей путем сравнения заданных и фактических значений.
Полное графическое изображение результатов измерения для надежной интерпретации измеренных значений.
- HOLOS Extended: Быстрое и высокоточное измерение сложных криволинейных поверхностей. Полная автоматизация процессов измерения. Возможность открытого обмена данными.
Идеально подходит для сравнения моделей за один рабочий цикл при определении объема.
- HOLOS Digitize: Оцифровка кривых и поверхностей.
Непосредственное преобразование в данные CAD для мгновенной оценки. Автоматический расчет линий сканирования.
Однако, к сожалению, ни на «Диаконте», ни на «ЛОМО», где установлены КИМ DuraMax, ПО HOLOS не применяется. Поэтому процесс измерения детали будет представлен в среде CALYPSO [9].
-
План контроля детали
Как уже было отмечено ранее, контролировать деталь на КИМ можно без использования компьютера, на основе взаимодействия с пультом Dynalog P. Однако это способствует наличию у пользователя некоторых ограничений действий и недостатков самого процесса, таких как:
- Необходимо указывать номинальный размер контролируемых параметров, который уже имеется при наличии CAD-модели.
- Выводимые на экран в процессе ощупывания элементы детали представляются пользователю, как разрозненный набор геометрических элементов, практически никак не связанных друг с другом, что достаточно сильно усложняет процесс восприятия.
- Из-за усложнения работы с векторами снижается точность операции контроля детали. Дело в том, что при отсутствии загружаемой CAD-модели машина не знает, какой частью шарика щупа происходит касание измеряемого элемента детали. Это приводит к появлению дополнительной погрешности, которая в некоторых случаях может быть очень и очень большой.
- Усложнение процесса задания системы координат детали. При наличии CAD-модели достаточно просто задать ощупываемые элементы мышкой, а потом коснуться их ручным методом. При отсутствии модели необходимо произвести ручное ощупывание всех элементов, а при низкой их точности многие из них могут определиться машиной неправильно, учитывая, что определение поверхности происходит всего по трем точкам.
- Сложность моделирования траектории ощупывания.
Создание плана контроля детали состоит из пяти основных этапов:
- Открытие и задание имени новому плану контроля.
- Выполнение подготовительных операций.
- Определение требуемых измеряемых элементов.
- Определение параметров, которые необходимо контролировать.
- Выполнение плана контроля.
Подготовительные операции включают в себя назначение щуповой конфигурации, назначение базовой системы координат детали, задание параллелепипеда безопасности и параметров температурной компенсации.
Задание измеряемых элементов происходит обыкновенным щелчком мыши по требуемой поверхности модели Пример этого действия показан на рис. 5.

Рис. 5. Задание измеряемых элементов в CALYPSO.
Ввод контролируемых параметров происходит вручную. Машина способна измерить все допуски размеров и форм, указанные на чертеже, поэтому происходит задание требуемых функций измерения и требуемых значений точности.
Круглость и цилиндричность измеренных поверхностей содержат графическое отображение поверхности для более наглядного представления ее профиля.
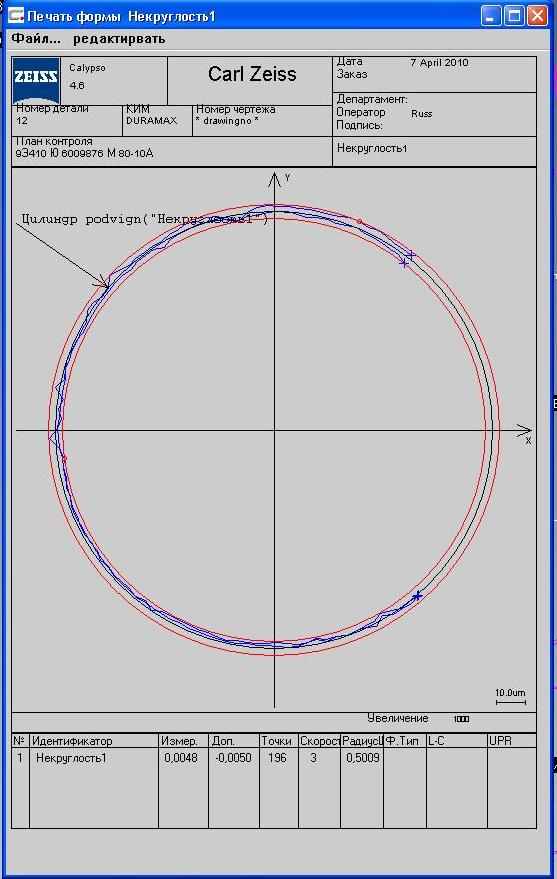
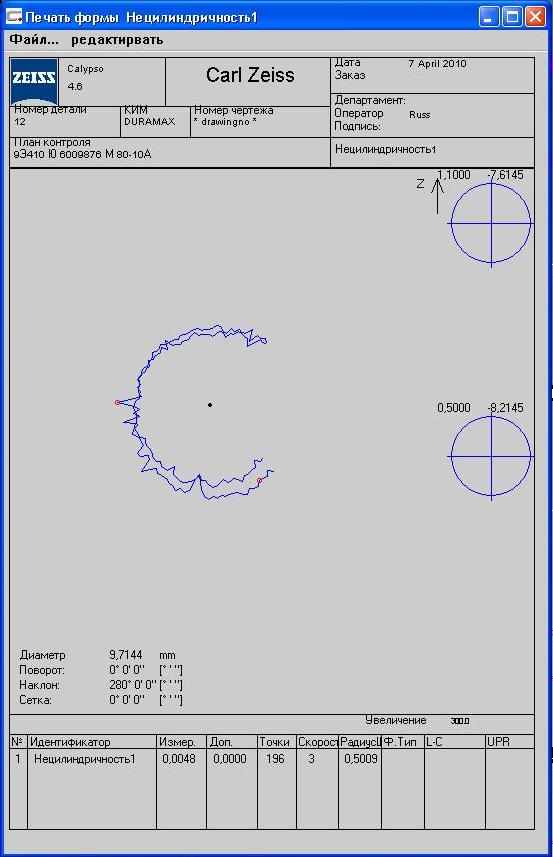
Рис. 6. Диаграмма поверхности при ощупывании
Таким же образом выводится диаграмма поверхности при сканировании VAST XXT – сенсором, позволяющая в максимально точной степени узнать отклонения реальной поверхности от идеальной в каждой ее точке [9].
Далее остается только запустить выполнение плана контроля. По возможности, необходимо выполнить прогон программы дважды, так как второй раз происходит с изменением базового выравнивания после первого ощупывания.
-
Преимущества и недостатки использования КИМ для контроля детали D70-03.10.03
Координатно-измерительная машина ЦЕЙСС DuraMax обеспечивает высокоточные автоматизированные измерения на одном рабочем месте при занятости всего одного человека – программиста КИМ. Она заменяет огромное количество измерительных инструментов, используемых для контроля расстояний и допусков точности, геометрической формы и взаимного расположения поверхностей. В частности, при использовании КИМ в операции контроля при производстве корпусной детали объектива D70-03.10.03 она позволяет исключить из технологического процесса такую оснастку, как штангенциркуль ШЦ-1-125-0.1 ГОСТ 166-89, набор плоско-параллельных концевых мер длинны 2 класс (0.3 – 0.9) ГОСТ 9038-73, набор плоско-параллельных концевых мер длинны 3 класс (0.5 – 100) ГОСТ 9038-73, калибр-пробка гладкая 15Н7 ГОСТ 14810-69, калибр-пробка гладкая 14Н7 ГОСТ 14810-69, микрометр МК-25-2 ГОСТ 6507-90 и скоба СР 25 ГОСТ 11098-75. Невозможность контроля параметров шероховатости компенсируется быстротой ее сравнения с эталонными образцами и временными затратами на это действие порядка нескольких секунд, если, конечно, требования чертежа не являются очень точными и не требуют использования в операции контроля профилометра. Использование резьбовых колец и калибров для контроля резьбы также не занимает много времени, а контроль фасок в любом случае осуществляется на микроскопе.
Из процесса измерений по большей части устраняется человек, уступая место более точному, безошибочному, быстрому, добросовестному и дешевому труду машины. Погрешность измерений лежит в пределах порядка двух микрометров, а такие функции, как учет вектора ощупывания и температурная компенсация теплового расширения превозносят точность получаемых измерений на новый уровень.
Контроль точности геометрических форм с использованием КИМ позволяет получать графические изображения профиля формы поверхностей, что дает возможность выявить любые отклонения на физическом, осязаемом человеком уровне, а использование сканирующей головки VAST XXT позволяет получить наиболее точную характеристику формы поверхности контролируемого элемента, что, при различных результатах измерений, является гарантией удачного или объяснением неудачного сопряжения ответственных поверхностей. Это актуально для наружных диаметров детали D70-03.10.03. В сборке объектива происходит сопряжение самых ответственных наружных цилиндрических поверхностей детали, выполненных по 6-ому квалитету, с поверхностями детали D70-03.10.02, выполненными по 7 квалитету.
Наличие CAD-модели детали и возможность контроля таких параметров, как радиальное и торцовое биение, которые имеют место в требованиях чертежа корпусной детали, обычным назначением соответствующей функции при создании плана контроля не только сокращают время создания самого плана, но и очень быстро реализуются машиной. Автоматическое определение геометрических элементов и функций для них, назначение траекторий перемещения щупа без участия человека – все это лишает человека лишних и ненужных действий, которые может наилучшим образом сделать машина. А возможность использования одной программы для контроля всех деталей партии значительно ускоряет и упрощает процесс самих измерений.
Не очень высокая сложность пространственной конфигурации детали D70-03.10.03 обусловливает не очень большие временные затраты программиста на написание плана контроля для всех необходимых операций контроля детали. А небольшое увеличение норм подготовительно-заключительного времени на операцию за счет калибровки щуповой конфигурации, выполнения подготовительных работ и определения базовой системы координат с лихвой компенсируются уменьшением норм штучного времени на операцию, что усугубляется размером партии детали порядка 20 штук.
Все эти факторы склоняют меня сделать вывод, что использование КИМ DuraMax в операциях контроля изготовления корпусной детали D70-03.10.03 является разумным и предпочтительным решением.
-
Модернизированный технологический процесс изготовления корпусной детали D70-03.10.03
В моем случае при использовании КИМ количество операций контроля не изменится, так как не изменятся операции лезвийной обработки детали. Контроль назначается для проверки выполнения операций точения, фрезерования и точения после операции электрохимического окисления. Контролируемые параметры на операциях останутся теми же, и сохранится оснастка для контроля резьбы и шероховатости. Однако изменятся нормы времени на операцию. С применением КИМ возрастает показатель нормы подготовительно-заключительного времени на операцию. И берется он без учета времени написания плана контроля детали. Однако экономия штучного времени одной операции контроля одной детали составляет порядка 7 минут. И эта цифра вырастает до 19 минут для всех операций общего технического контроля. А при размере партии хотя бы в десять штук экономия времени составляет уже 3 часа, что с лихвой компенсирует время, затраченное на написание плана контроля для КИМ.
К сожалению, в базе данных ЗАО «Диаконт» в папке «измерительное оборудование» отсутствует КИМ DuraМax. Поэтому я был вынужден модернизировать технологический процесс изготовления детали D70-03.10.03, назначив на операции контроля оборудование КИМ ZEISS GLOBAL. Не сочтите это за ошибку. В основном, на «Диаконте» применяется именно эта координатно-измерительная машина, наличие способности наклона щупа существенно увеличивает возможности КИМ и границы ее применения, а КИМ DuraMax является своего рода прикладной. Возможно, это частично объясняет ее отсутствие в базе данных и невозможность назначения как оборудования для выполнения операции контроля.
Заключение
В ходе данной работы произведен анализ специфики производства изделий на предприятии ЗАО «Диаконт», рассмотрены особенности операции технического контроля, оценены возможности применения в ней координатно-измерительной машины ZEISS DuraMax. Рассмотрены преимущества и недостатки операции контроля с применением КИМ на основе процесса изготовления корпусной детали D70-03.10.03 и сделан вывод о целесообразности применения КИМ в операции контроля. Текущий технологический процесс изготовления детали модернизирован путем замены классической операции контроля на столе ОТК операцией контроля с использованием КИМ. Изменены нормы времени на операцию и назначаемая оснастка. Полученный в результате модернизации технологический процесс завершен и может быть запущен в производство на ЗАО «Диаконт».
Список использованной литературы
- Валетов В.А., Бобцова С.В., Новые технологии в приборостроении. СПбГУ ИТМО, 2004. – 120 с.
- Валетов В.А., Кузьмин Ю.П., Орлова А.А., Третьяков С.Д., Технология приборостроения. Учебное пособие, – СПб: СПбГУ ИТМО, 2008 – 336 с.
- Валетов В.А., Мурашко В.А., Основы технологии приборостроения: Учебное пособие. - СПб.: СПбГУ ИТМО, 2006. - 180 с.
- Васильева И.А., Пилипенко Н.В., Подготовка и защита выпускных квалификационных работ. Учебное пособие по итоговой государственной аттестации. – СПб: СПб ГУ ИТМО, 2007. - 36 с.
- Положение «О дивизионе телевизионного и диагностического оборудования» от 28.08.2008. // СПб.: ЗАО «Диаконт». 2008.
- Приказ «О реорганизации ЗАО «Диаконт»» от 24.01.2008 №16.//СПб.: ЗАО «Диаконт». 2008.
- Видиконная камера D70: [Электронный ресурс] / СПб: ЗАО «Диаконт». 2009. – Режим доступа: ссылка скрыта, свободный. Дата последнего обращения 30.11.2010.
- DuraMax: [Электронный ресурс]/ «ZEISS». Режим доступа: ссылка скрыта, свободный. Дата последнего обращения 30.11.2010.
- «CALYPSO_38_ru_introduction»: руководство пользователя координатно-измерительной техники.