«Разработка технологического процесса изготовления детали «Корпус вибратора»
Вид материала | Реферат |
- 1. 2 Патентные исследования, 27.99kb.
- Курсовая работа по дисциплине «Технология приборостроения», 388.53kb.
- «Разработка технологии изготовления детали «Корпус» с применением станков с чпу и организации, 48.43kb.
- Кафедра технологии машиностроения и методики профессионального обучения курсовой проект, 88.72kb.
- Кафедра технологии машиностроения и методики профессионального обучения курсовой проект, 81.68kb.
- Кафедра технологии машиностроения и методики профессионального обучения курсовой проект, 89.23kb.
- Курсовой проект разработка технологического процесса механической обработки детали, 81.31kb.
- Методические указания к выполнению курсовой работы по дисциплине, 379.87kb.
- «Российский государственный профессионально-педагогический университет», 117.59kb.
- Задание на курсовой проект; реферат, 294.21kb.
2 Технологическая часть
2.1 Установление планов обработки основных поверхностей детали
Для установления планов обработки детали необходимо произвести анализ поверхностей детали для определения наиболее эффективных методов их обработки. Выбираемые методы обработки также зависят от точности обработки поверхности, шероховатости, материала обрабатываемой заготовки и т.п.
Таблица 1 - Маршрут обработки детали.
![]() | ||||||
![]() | ||||||
№ перехода № перехода | Наименование поверхности | Квалитет | Шероховатость, мкм | Индекс | Метод получения | Припуск, (на сторону), мм |
1 | 2 | 3 | 4 | 5 | 6 | 7 |
1 | 910х450 (750х140) | js14 js12 js12 js10 js8 | Ra100 Ra12,5 Ra6,3 Ra3,2 Ra1,6 | 0 1 2 3 4 | Заготовка Фрезерование Фрезерование Фрезерование Фрезерование | 5,5 2,15 1,6 0,45 0,3 |
2 | Ø45 | Н12 Н12 Н10 Н8 | Ra12,5 Ra12,5 Ra6,3 Ra3,2 | 1 2 3 4 | Центрование Сверление Зенкерование Развертывание | 4 21,5 0,75 0,25 |
3 | Ø65 | Н12 | Ra12,5 | 1 | Цекование | 10 |
4 | Ø160х18 | js14 js12 | Ra100 Ra12,5 | 0 1 | Заготовка Фрезерование | 5 5 |
5 | Ø160х15 | js12 | Ra12,5 | 1 | Фрезерование | 3 |
6 | Ø70 | H14 H12 | Ra100 Ra12,5 | 0 1 | Заготовка Зенкерование | 5 2,5 |
7 | Ø16 | H12 H12 | Ra12,5 Ra12,5 | 1 2 | Центрование Сверление | 4 8 |
8 | 1240х602 (1120х482) | js14 js12 js12 js12 | Ra100 Ra12,5 Ra6,3 Ra3,2 | 0 1 2 3 | Заготовка Фрезерование Фрезерование Фрезерование | 8,5 5 2,9 0,6 |
9 | М16-7Н | Н12 Н12 7Н | Ra12,5 Ra12,5 | 1 2 3 | Центрование Сверление Нарезание резьбы | 0,4 6,9 - |
10 | Ø10 | Н12 Н12 | Ra12,5 Ra12,5 | 1 2 | Центрование Сверление | 4 5 |
11 | Ø16 | Н12 | Ra12,5 | 1 | Рассверливание | 3 |
12 | Ø466 (Ø325) | js14 js12 js12 js10 js8 | Ra100 Ra12,5 Ra12,5 Ra6,3 Ra3,2 | 0 1 2 3 4 | Заготовка Фрезерование Фрезерование Фрезерование Фрезерование | - 4 1,1 0,23 0,15 |
13 | М20-7Н | H12 H12 7H | Ra12,5 Ra12,5 | 1 2 3 | Центрование Сверление Нарезание резьбы | 4 8,65 - |
14 | Ø350 | H14 H12 H12 H12 H10 H8 H8 | Ra100 Ra12,5 Ra12,5 Ra12,5 Ra6,3 Ra3,2 Ra1,6 | 0 1 2 3 4 5 6 | Заготовка Растачивание Растачивание Растачивание Растачивание Растачивание Растачивание | 26,2 2,5 5 4,4 0,6 0,3 0,3 |
15 | R25 | js12 | Ra12,5 | 1 | Фрезерование | 25 |
16 | R16 | js12 | Ra12,5 | 1 | Фрезерование | 7 |
2.2 Выбор припусков на обрабатываемые поверхности
В машиностроении величину припуска для элементарной поверхности детали определяют 2-мя методами: расчетно-аналитическим и опытно- статистическим (табличным).
Расчетно-аналитический метод определения припусков был разработан профессором В.М.Кованом. По данному методу припуск рассчитывается по определенным формулам.
При использовании опытно - статистического (табличного) метода, припуски на обработку поверхностей назначаются по таблицам соответствующим данным технических справочников.
В данном случае основные припуски на механическую обработку определяются опытно - статистическим методом.
Сначала необходимо определить класс точности и ряд припусков в зависимости от способа литья, габаритных размеров и материала отливки [таблица 3.1 страница 9] .
Затем определяются допуски на размеры, которые зависят от самого размера и класса точности [таблица 3.51 страница 18].
Основные припуски на механическую обработку отливок ГОСТ26645-85 определяются [таблица 3.50 страница 18] в зависимости от допусков на размеры и ряда припуска.
Например, для плоскости разъема 1240х782мм выполняемой по 14 квалитету точности с шероховатостью поверхности Ra6,3 мкм, необходимо провести 2 перехода обработки. Припуски назначаются на 2 черновые обработки. Исходя из того, что отливка имеет 12 класс точности размеров [таблица 3.1 страница 10], ряд припусков 4-й [таблица 3.1 страница10], допуск на размеры составляет 11 мм [таблица 3.51 страница 18]. Следовательно, основной припуск на сторону находится в диапазоне 11.0-14.0 мм. Отсюда припуск на 1-й черновой переход будет равен 6,5 мм.
Для отверстия Ø350 мм выполняемого по 7 квалитету точности с шероховатостью поверхности Ra 1,6 мкм, необходимо провести 4 перехода обработки: 2 перехода чернового растачивания и 2 перехода чистового растачивания. Отливка имеет 11 класс точности размеров и ряд припусков 4-й [таблица 3.1 страница 10]. Исходя из этого, допуск на размер Ø350 мм равен 6,4 мм [таблица 3.51 страница 18]. Отсюда общий припуск в диапазоне от 7,5 мм до 11,0 мм. Следовательно, припуск на черновое растачивание равен - 3,2 мм и на чистовое - 1,6 мм (припуски выбраны на сторону).
2.3 Установление последовательности обработки основных поверхностей и выбор баз
На первой операции установка заготовки осуществляется на необработанные поверхности. Поэтому большое значение имеет правильный выбор баз на данной операции, что не мало важно для последующего обеспечения чистовых баз для последующей обработки.
При выборе черновых баз руководствуются следующими рекомендациями:
1. Черновая базовая поверхность должна обеспечивать устойчивое положение заготовки в приспособлении.
2. Если у детали имеются необрабатываемые поверхности, то эти поверхности могут быть использованы в качестве черновых баз.
3. Если все поверхности заготовки подлежат обработке, то в качестве черновых баз используются поверхности с минимальными припусками.
При выборе чистовых баз руководствуются следующими рекомендациями:
1. Использовать по возможности принцип баз, т.е. в качестве технологических баз использовать поверхности, являющиеся измерительными и конструкторскими.
2. Использовать по возможности принцип постоянства технологических баз, т.е. в ходе обработки на большинстве операций в качестве технологических баз использовать одни и те же поверхности.
3. Выбранная чистовая база должна обеспечивать простую и надежную конструкцию приспособления.
Исходя из перечисленных рекомендаций, в качестве черновой базы для первой операции выбираем торцы конусообразных выступов Ø466 мм и отверстий в этих выступах Ø 325 мм, так как они являются самыми точными в заготовке и обеспечивают надежное закрепление в приспособлении.
В качестве чистовой технологической базы служит плоскость основания 910х450 мм и 2 отверстия Ø45Н8 мм под пальцы, полученные на первой операции.
Операция 005.
Многоинструментальная. Деталь базируется в специальном приспособлении. Установка производится на 2 необработанных отверстия Ø325 мм. На данной операции заготовка меняет 4 позиции, на которых обрабатываются различные поверхности: фрезерованием, сверлением, зенкерованием, развертыванием.
Операция 010.
Многоинструментальная. Деталь базируется по плоскости и двум отверстиям. В отверстия вставляют установочные пальцы: цилиндрический ГОСТ12209-66 и срезанный ГОСТ122-66. На данной операции производится обработка: торцов конусообразных выступов, находящихся в них отверстий и отверстий Ø350 мм и Ø330 мм.
2.4 Разработка технологического процесса
Технологический процесс обработки детали «Корпус вибратора» представлен в приложении А.
3 Расчетная часть
3.1 Теоретическое определение оптимальных режимов резания
Для оптимизации режимов резания критериями оптимальности являются следующие технико-экономические показатели:
- период стойкости инструмента Т – время непосредственной работы инструмента (исключая время перерывов) от переточки до переточки.
Для каждого вида обработки период стойкости инструмента рассчитывается по определенной формуле. Так, например, для токарной обработки:
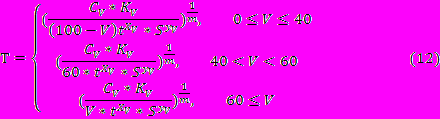
для сверлильной обработки:

для фрезерной обработки:

- штучное время (Тшт) – норма времени на изготовление единицы продукции (изделия) или выполнения единицы работы (операции), установленная без подготовительно-заключительного времени (так как подготовительно-заключительное время устанавливается на отдельную серию изделий). Оно определяется по формуле:

- часовая производительность Nшт – определяется по формуле:

- затраты на режущий инструмент Q:
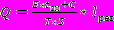
- стоимость операции З:
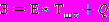
Для различных видов обработки существуют различные технологические ограничения.
* Для процесса точения существуют следующие технологические ограничения:
- точность обработки –

Она зависит от погрешности деформации узлов станка, погрешности деформации обрабатываемой детали, погрешности деформации вершины резца.
- шероховатость поверхности –

- прочность державки резца –
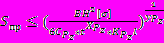
Зависит от момента сопротивления сечения державки, силы резания, допустимого напряжения на изгиб материала державки.
- прочность пластинки твердого сплава –
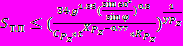
Она зависит от предельной нагрузки для пластинки из твердого сплава и силы резания.
- мощность станка –
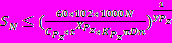
Зависит от эффективной мощности станка Nэф , при условии, что NэфN, где N – мощность станка
- прочность механизма подач –
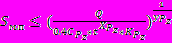
Зависит от силы резания и усилия, предельно допустимого прочностью механизма подач.
- Технологические ограничения для процесса фрезерования
- жесткость оправки –
а) цилиндрическое фрезерование –
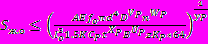
б) торцовое фрезерование –

Зависит от осевой силы, силы резания и величины прогиба детали
- шероховатость поверхности –

Зависит от требуемой шероховатости
- размещаемость стружки –

Зависит от размеров фрезы (количества зубьев и диаметра).
- прочность зуба фрезы –
а) фрезы с пластинками из твердого сплава -

б) фрезы из быстрорежущей стали, кроме прорезных –
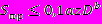
в) прорезные фрезы (D75 мм, t6мм)-
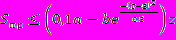
г) прорезные фрезы (D75 мм, t6мм ) -

- мощность станка –
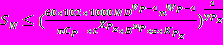
Зависит от эффективной мощности станка Nэф , при условии, что NэфN, где N – мощность станка
- прочность механизма подач -
а) торцовое фрезерование -

б) прочие виды фрезерования –
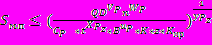
Зависит от усилия механизма подач, силы резания и осевой силы.
- Технологические ограничения на сверлильную обработку
- жесткость сверла –
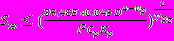
Она зависит от критической по жесткости сверла силы и осевой силы.
- жесткость детали –
а) для прямоугольной детали
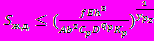
б) для круглой детали
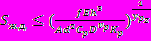
Зависит от прогиба детали под действием осевой силы и величины осевой силы.
- шероховатость поверхности –
а) обработка сталей
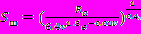
б) обработка чугуна и цветных металлов
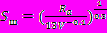
- условия вывода стружки –

- прочность сверла –
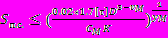
Зависит от величины крутящего момента, момента сопротивления сечения сверла и величины касательного напряжения, допустимого материалом сверла.
- мощность станка –
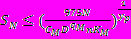
Она зависит от мощности затрачиваемой на сверление и крутящего момента при сверлении.
- прочность механизма подач –
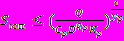
Зависит от осевой силы и подачи, допускаемой предельной силой механизма подач станка.
Рассмотрим расчет режимов резания и основного времени для обработки отверстия 45Н10 с шероховатостью Ra6,3, глубина которого 35 мм (на первый - черновой - переход).
На черновом (выбранном) переходе сверлится отверстие 43Н12 мм с шероховатостью Ra12,5 мкм, длина отверстия - 35 мм.
В качестве режущего инструмента выбираем сверло спиральное Ø43 мм цельное, с усиленным коническим хвостовиком, изготовленного из быстрорежущей стали Р6М5. Геометрические параметры сверла: 2φ =118° , ω=30° , γ=10° , α=10° , ψ=50°, L=359 мм, l=210 мм.
Рассмотрим несколько вариантов технико-экономических показателей для сверления отверстия под зенкерование Ø43 мм. Деталь - корпус вибратора - изготовлена из конструкционной стали 40Л. Обработка ведется на многофункциональном станке ИР1600МФ4, сверлом спиральным Ø43 мм изготовленного из быстрорежущей стали Р6М5. Заготовка - отливка.
Определяем режимы резания сверлильной обработки.
С учетом всех ограничений для сверлильной обработки определяем подачу. При сверлении отверстия в детали из конструкционной стали подача S находится в пределах от 0,6 мм/об до 0,85 мм/об. В соответствии с паспортными данными станка ИР1600МФ4 принимаем подачу S равную 0,6 мм/об.
Глубина резания в данном случае равна половине получаемого размера, таким образом
t = 43/2 = 21,5 мм.
Для определения оптимальной частоты вращения инструмента рассмотрим три варианта расчетов, исходя из критериев оптимальности для сверлильной обработки.
Вариант 1.
Обороты шпинделя - 125 об/мин
Максимально допустимая подача – Smax =0,85 мм/об
Скорректированная подача - S=0,6 мм/об
Технико-экономические показатели:
Стойкость - Т=122 мин
Затраты на инструмент - Q=95 руб
Стоимость операции - З=585 руб
Штучное время – Тшт =98 мин
Производительность – Nшт =0,61 шт/час
Увеличим число оборотов шпинделя до 200 об/мин и сравним с 1-м вариантом.
Вариант 2
Обороты шпинделя - 200 об/мин
Максимально допустимая подача - Smax =0,85 мм/об
Скорректированая подача - S=0,6 мм/об
Технико-экономические показатели:
Стойкость - Т=12 мин
Затраты на инструмент - Q=960 руб
Стоимость операции - З=1575 руб
Штучное время - Тшт =123 мин
Производительность - Nшт =0,48 шт/час
Как видно стойкость инструмента значительно уменьшилась, также уменьшилась производительность и увеличились затраты.
Рассмотрим еще один вариант, увеличив число обротов шпинделя до 250 об/мин.
Вариант 3.
Обороты шпинделя - 250 об/мин
Максимально допустимая подача - Smax =0,85 мм/об
Скорректированая подача - S=0,6 мм/об
Технико-экономические показатели:
Стойкость - Т=4 мин
Затраты на инструмент - Q=2880 руб
Стоимость операции - З=4089 руб
Штучное время - Тшт =7603 мин
Производительность - Nшт =0,008 шт/час
Сравнив все варианты видно, что при увеличении числа оборотов шпинделя сильно ухудшаются технико-экономические показатели. Следовательно, наиболее оптимальным является вариант 1, и принимается число оборотов шпинделя равное 125 об/мин.
Исходя из определенного оптимального значения частоты вращения шпинделя (125 об/мин), определяем остальные режимы резания.
Скорость резания в данном случае определяется по формуле:

где n – частота вращения шпинделя;
D – диаметр инструмента (43 мм).
Рассчитываем скорость резания:

Крутящий момент при сверлении определяется по формуле:

где

D - диаметр инструмента - 43 мм;
S - подача; S=0,6 мм/об

y, q - показатели степени.
При обработке стали конструкционной (σв =75 кгс) инструментом, режущая часть которого из быстрорежущей стали марки Р6М5, получим:
C = 0,0345; y=0,8; q=2
Исходя из полученных данных , рассчитываем крутящий момент при сверлении равен:
М = 0,0345*432 *1*0,60,8 = 42,39 кгс/м.
Рассчитываем мощность по формуле:

где М - крутящий момент - равен 42,39 кгс/м;
п - частота вращения инструмента - 125 об/мин.
Рассчитываем:
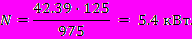
Основное время при сверлении определяется по формуле:

где L= lобр. +lвр. +lп. , (45)
lобр. - длина обрабатываемой поверхности;
lвр. - длина врезания;
lп - длина перебега.
Длина обрабатываемой поверхности lобр.= 35 мм.
Длина врезания lвр при глубине резания 21,5 мм и главном углу в плане φ =59° равна 2 мм ([3], табл. 16,8, стр. 1132), а длина перебега при диаметре инструмента Ø43 мм lп = 2,5 мм.
Исходя из полученных данных L=35+2+2,5=39,5 мм.
Также в формуле для расчета основного времени присутствует:
n- частота вращения инструмента - 125 об/мин;
S - подача - она равна 0,6 мм/об.
Определяем основное время на данный переход:
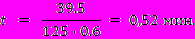