Учебное пособие для студентов нефтехимических колледжей и техникумов Специальность 1701 "Монтаж и техническая эксплуатация промышленного оборудования (по отраслям)"
Вид материала | Учебное пособие |
- Учебное пособие для студентов среднего профессионального образования Специальность, 3369.62kb.
- Программа и контрольные задания для студентов заочного отделения Специальность: 1701, 688.94kb.
- Методические указания и контрольные задания для студентов заочной формы обучения гоу, 2389.4kb.
- Методические указания и контрольные задания для студентов заочного отделения специальность:, 848.08kb.
- Федеральный государственный образовательный стандарт среднего профессионального образования, 1074.58kb.
- Государственный образовательный стандарт среднего профессионального образования государственные, 1346.06kb.
- «Материаловедение», 179.95kb.
- Формирование профессионально-значимых качеств личности в условиях личностно-ориентированного, 51.94kb.
- «Монтаж и техническая эксплуатация промышленного оборудования (в пищевой промышленности)», 1138.79kb.
- Курс 150411 «Монтаж и техническая эксплуатация промышленного оборудования», 58.89kb.
6.6 Типичные дефекты при резании металла, причины их появления
и способы предупреждения
Таблица 4
Дефект | Причина | Способ предупреждения |
Резание слесарной ножовкой | ||
Перекос реза | Слабо натянуто полотно. Резание производилось поперек полосы или полки угольника | Натянуть полотно таким образом, чтобы оно туго поддавалось нажатию пальцем сбоку |
Выкрошивание зубьев полотна | Неправильный подбор полотна. Дефект полотна – полотно перекалено | Полотно следует подбирать таким образом, чтобы шаг зубьев был не более половины толщины заготовки, т.е. чтобы в работе участвовало два-три зуба. Вязкие металлы (алюминий и его сплавы) резать полотнами с более мелким зубом, тонкий материал закреплять между деревянными брусками и разрезать вместе с ними |
Поломка полотна | Сильное нажатие на ножовку. Слабое натяжение полотна. Полотно перетянуто. Неравномерное движение ножовкой при резании | Ослабить вертикальное (поперечное) нажатие на ножовку, особенно при работе новым, а также сильно натянутым полотном. Ослаблять нажатие на ножовку в конце реза. Движения ножовкой производить плавно, без рывков. Не пытаться исправлять перекос реза перекосом ножовки. Если полотно тупое, то необходимо заменить его. |
Резание ручными ножницами | ||
При резании листового материла ножницы мнут его | Тупые ножницы. Ослаблен шарнир ножниц | Резание производить только острозаточен-ными ножницами. Перед началом резания проверить и, если необходимо, подтянуть шарнир ножниц так, чтобы раздвигание ручек производилось плавно, без заеданий и качки |
«Надрывы» при резании листового материала | Несоблюдение правил резания | Во время работы ножницами следить, чтобы лезвия ножниц не сходились полностью, так как это приводит к «надрывам» металла в конце реза |
Отступление от линии разметки при резании электровибрационными ножницами | Несоблюдение правил резания | При резании листового материала больших размеров (более 500 мм) лист задней кромкой упереть в какой-либо упор и разрезание производить перемещением (подачей) ножниц. При вырезании заготовок с криволинейными контурами (особенно при небольших размерах заготовок) подачу производить передвижением заготовки |
Ранение рук | Работа производилась без рукавиц | Работать ножницами следует только в брезентовых рукавицах (прежде всего на левой руке, поддерживающей разрезаемый лист) |
Резание труб труборезом | ||
Грубые задиры в местах закрепления трубы | Нарушение правил закрепления труб | Прочно закреплять трубу в трубном прижиме, чтобы она не проворачивалась в процессе резания. При закреплении трубы в тисках использовать деревянные прокладки |
| | |
Продолжение таблицы 4 | ||
«Рваный» торец отрезанной трубы | Несоблюдение правил резания труб | Точно устанавливать диски трубореза по разметочным меткам. Внимательно следить в процессе резания за перпендикулярностью рукоятки трубореза к оси трубы (при этом условии режущие диски трубореза не смещаются и линия реза не перекашивается). При каждом повороте трубореза поджимать его винт не более чем на половину оборота. Обильно смазывать оси режущих дисков и места реза |
Контрольные вопросы:
Почему при использовании ручной ножовкой необходимо следить за тем, чтобы в процессе резания участвовало не менее двух-трех зубьев?
- Почему при резании вибрационными ножницами больших листов подачу следует осуществлять за счет перемещения ножниц?
- Какую роль выполняет смазка, вносимая в зону резания, при разрезании труб труборезом?
- Чем вызвана необходимость использования рукавиц при резании металла ножницами?
- В чем преимущества раздвижного ножовочного станка перед цельным?
Тема 7 Правка и гибка
Студент должен:
знать:
- приемы правки и гибки металла;
- инструменты и приспособления, применяемые при гибке и правке металла;
- правила техники безопасности при гибке и правке металла.
уметь:
- выполнять правку и гибку металла вручную и приспособлениями;
- проводить контроль выполненных операций: правки и гибки.
Оснащение рабочего места: тиски слесарные, тиски ручные, угольники-нагубники к тискам; ножницы по металлу; молотки слесарные для правки массой 500…600 г; молотки из мягких металлов; молотки деревянные, киянки; линейки измерительные металлические, чертилки; кернеры; шаблоны разметочные; очки защитные.
7.1 Правка представляет собой первую операцию по подготовке заготовки или металла для ее последующей технологической обработки. Она предназначается для устранения искажений формы (вмятин, выпучиваний, волнистости, коробления, искривления и т.п.) путем пластического деформирования. Металл подвергается правке как в холодном, так и в нагретом состоянии. Правку можно выполнять ручным способом на стальной или чугунной плите или на наковальне, машинную правку производят на прессах и правильных вальцах.
Для правки применяют: молотки с круглым полированным бойком, так как молотки с квадратным бойком оставляют следы в виде забоин; молотки из мягких материалов (медные, свинцовые, деревянные); гладилки и поддержки (металлические или деревянные бруски) для правки тонкого листового и полосового металла; правильные бабки для закаленных деталей с цилиндрической, сферической и прочими фасонными поверхностями.
К
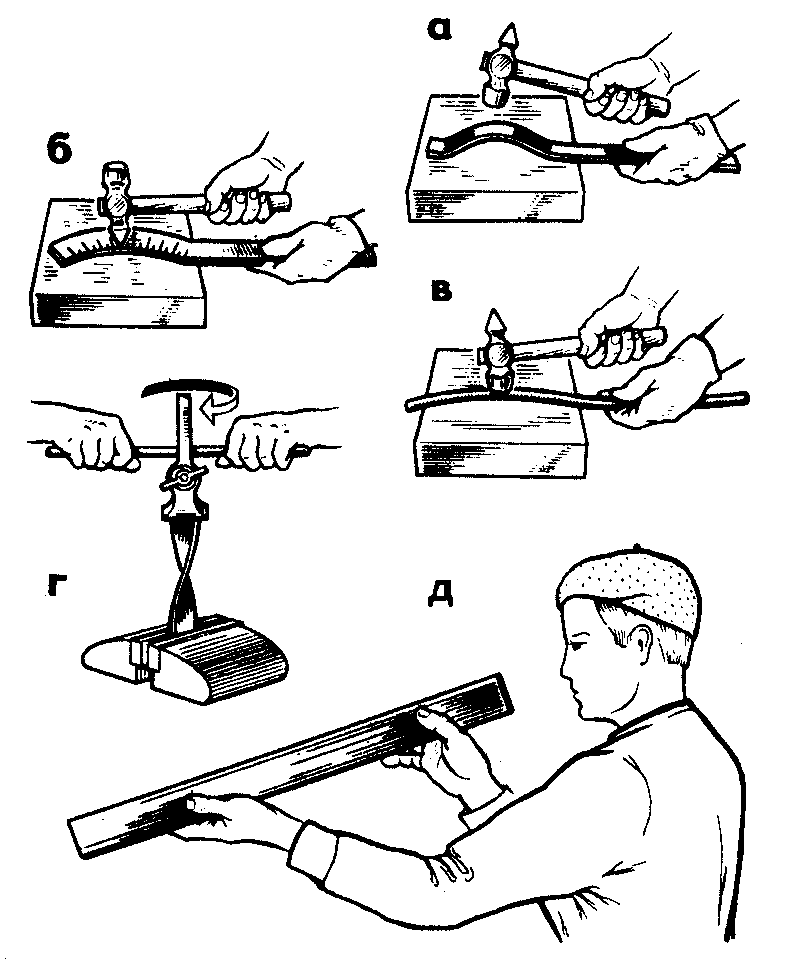
ривизну заготовок проверяют на глаз или по зазору между плитой и уложенной на нее заготовкой. Изогнутые места отмечают мелом. Правку производят на правильной плите или наковальне (рис. 7.1).
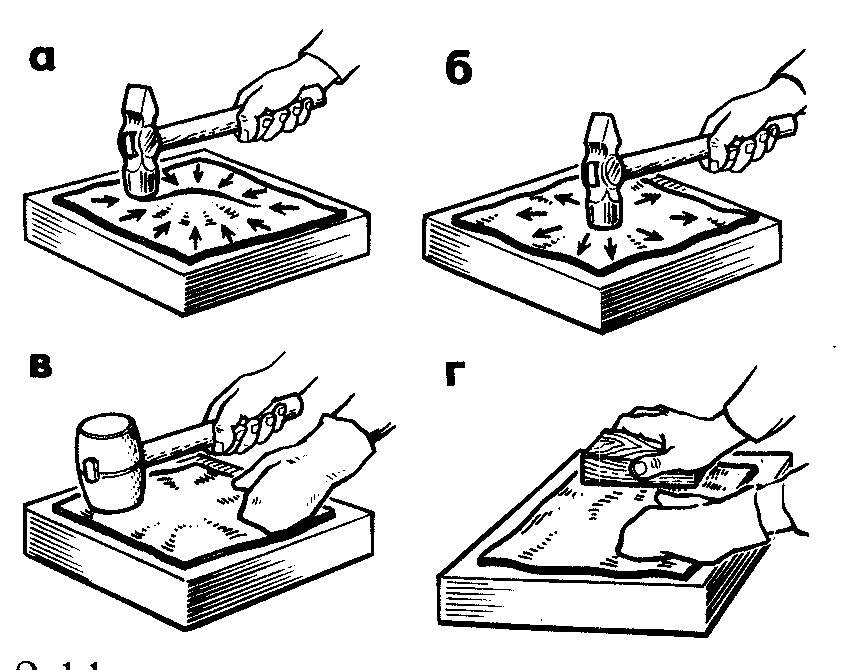
Рисунок 7.1 Приемы правки листового
материала
Рисунок 7.2 Приемы правки металла
полосового и круглого сечения
Простейшей является правка металла изогнутого по плоскости. В этом случае молотком или кувалдой наносят сильные удары по наиболее выпуклым местам полосы, уменьшая силу удара по мере выпрямления и поворачивая полосу с одной стороны на другую по мере необходимости (рис. 7.2 а, б). Сложней правка металла, изогнутого по ребру. Если в первом случае правка заключалась в простом выравнивании полосы, то здесь прибегают к деформированию растяжением части металла (рис. 7.2, в). Правку полос, имеющих скрученный (спиральный) изгиб (рис. 7.2, г), рекомендуется проводить методом раскручивания, для чего один конец заготовки зажимают в слесарные тиски, а на втором конце закрепляют ручные тисочки. Затем рычагом выправляют спиральную кривизну. При необходимости окончательную правку проводят на плите. Результаты правки (прямолинейность заготовки) проверяют на глаз (рис. 7.2, д), а для более точной проверки – на разметочной или контрольной плите по просвету, наложением линейки на полосу или щупом.
Правка листового материала – более сложная операция. Она зависит от вида деформирования, как, например, выпуклости или вмятины в середине листа или заготовки, более сложного деформирования, когда заготовка имеет одновременно выпуклость и волнистость кромок листа (рис. 7.1). Предварительно обводят мелом или карандашом волнистые участки на заготовке, затем кладут её на плиту выпуклостью вверх так, чтобы заготовка металла всей поверхностью была на плите. Придерживая лист левой рукой в рукавице, правой наносят молотком удары от края листа по направлению к выпуклости (рис. 7.1, а), по мере приближения к выпуклости удары наносят слабей и чаще. Во время правки заготовку поворачивают в горизонтальной плоскости так, чтобы удары равномерно распределялись кругом по всей площади заготовки. Если на листе имеется несколько выпуклостей, то удары наносят в промежутке между выпуклостями. В результате этого лист растягивается, и все выпуклости сводятся в одну общую, которую выправляют указанным выше способом.
Если лист имеет волнистость по краям, но ровную середину, то удары молотком наносят от середины листа к краям (рис. 7.1, б). От воздействия этих ударов лист в середине вытягивается, и волны по кромкам листа исчезают. После этого лист следует перевернуть и продолжать правку таким же способом до получения требуемых допусков прямолинейности и плоскостности.
Правку тонких листов производят деревянными молотками–киянками (рис. 7.1, в), а очень тонкие листы проглаживают деревянным или металлическим бруском – гладилкой, придерживая их на плите левой рукой (рис. 7.1, г). При правке лист периодически переворачивают.
Правку закаленных заготовок, иногда называемую рихтовкой, вызванную короблением при термической обработке, проводят различными молотками с закаленным бойком или специальным молотком с закругленной узкой стороной бойка. Удары наносят не по выпуклой, а по вогнутой стороне заготовки. Таким образом достигается растяжение волокон металла на вогнутой стороне заготовки и её выпрямление. Правку заготовок более сложной формы, например угольника, у которого после закалки изменился угол между измерительными сторонами, производят следующими способами: если угол стал меньше 900, то удары молотком наносят у вершины внутреннего угла (рис.7.3, а), если угол стал больше 900, то удары наносят у вершины наружного угла (рис. 7.3, б).
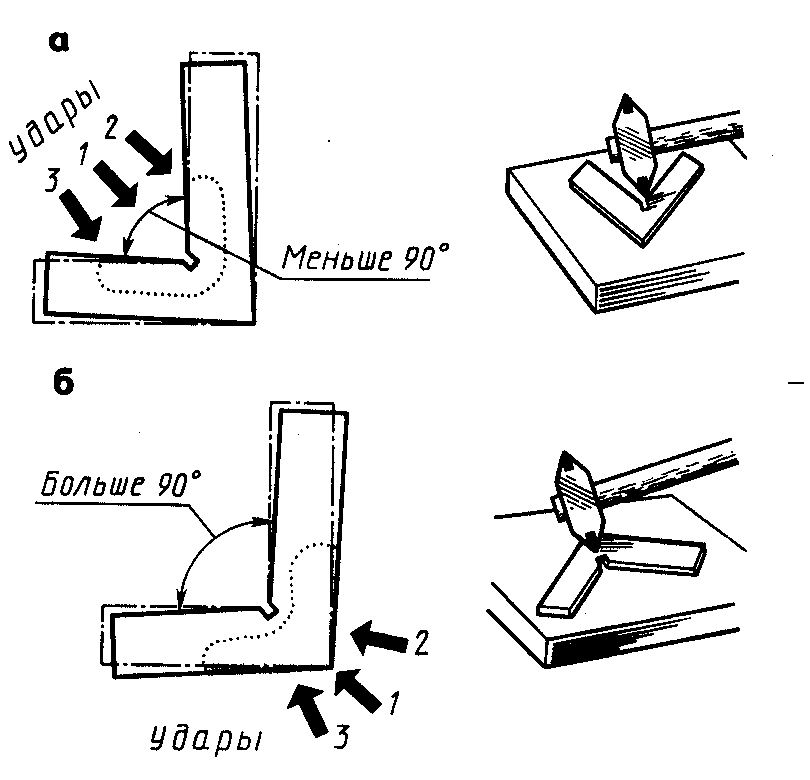
Рисунок 7.3 Правка закаленных деталей
и места нанесения ударов
7.2 Типичные дефекты при правке, причины их появления
и способы предупреждения
Таблица 5
Дефект | Причина | Способ предупреждения |
После правки обработанной детали в ней имеются вмятины | Правка производилась ударами молотка или кувалды непосредственно по детали | Правку производить через прокладку или наставку из мягкого металла, при правке обработанные цилиндрические детали устанавливать на призмы |
После правки листового материала киянкой или молотком через деревянную наставку лист значительно деформирован | Применялись недостаточно эффективные способы правки | Применять способ правки путем растяжения металла по краям выпуклости, чередуя этот способ с правкой прямыми ударами |
После рихтовки полоса непрямолинейна по ребру | Процесс правки не окончен | Правку заканчивать ударами по ребрам полосы, переворачивая ее в процессе правки на 1800 |
Контрольные вопросы:
Почему при правке металлов рекомендуют применять молоток с круглым, а не с квадратным бойком?
- Почему при правке мягких материалов и тонких листов рекомендуется использовать прокладки?
- Чем вызвана необходимость использования молотков с вставками из твердых материалов при рихтовке заготовок?
- С какой целью при правке валов с предварительно обработанными поверхностями применяют для их установки призмы?
- В чем состоят особенности правки деталей, подвергшихся термической обработке?
7.3 Гибка – одна из наиболее распространенных слесарных операций. Её применяют для придания заготовке изогнутой формы по заданному контуру. В процессе гибки металл подвергается одновременному воздействию растягивающих и сжимающих сил, поэтому при гибки необходимо учитывать механические свойства металла, его упругость, степень деформирования, толщину, форму и размеры сечения заготовки, углы и радиусы изгиба детали. Радиус изгиба не следует принимать близким к минимально допустимому, если это не диктуется конструктивными требованиями. Целесообразно не допускать радиус изгиба меньше толщины заготовки, так как уменьшение радиуса приводит к появлению трещин и других дефектов. В холодном состоянии рекомендуется изгибать детали из листовой стали толщиной до 5 мм, из полосовой стали толщиной до 7 мм, из круглой стали диаметром до 10 мм.
Гибку полосы из листовой стали выполняют в следующем порядке: наносят риску загиба, зажимают заготовку в тисках между угольниками-нагубниками так, чтобы разметочная риска была обращена к неподвижной губке тисков и выступала над ней 0,5мм (рис. 7.4, а), и ударами молотка, направленными к неподвижной губке, загибают конец полосы (рис. 7.4, б). Для гибки скобы заготовку зажимают в тисках между угольником и бруском–оправкой загибают первый конец (рис. 7.4, в), затем, вложив внутрь скобы брусок–оправку требуемого размера, зажимают скобы в тиски на уровне рисок и сжимают вторую лапку (рис. 7.4, г). Гибка полосы под острым углом с применением специальной оправки показана на рис.7.4, д.
Гибку хомутика из тонкой полосовой стали выполняют в следующем порядке: зажимают в тисках оправку 1 требуемого диаметра (рис. 7.5, а), загибают заготовку 2 на оправке двумя плоскогубцами 3 и обрабатывают хомутик окончательно с помощью молотка на оправке в тисках (рис. 7.5, б, в).
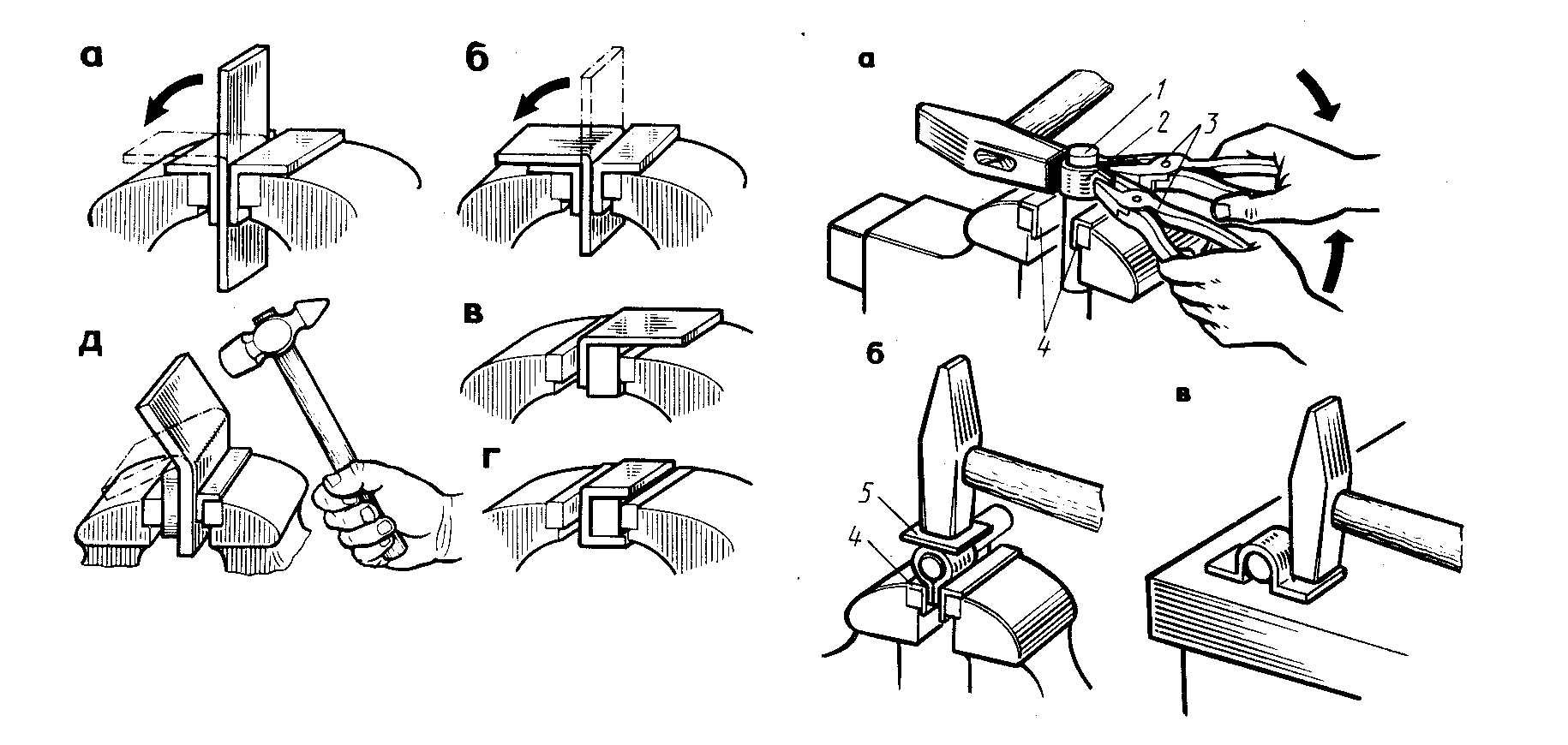
Рисунок 7.4 Приемы гибки полос
1-оправка; 2 - заготовка; 3 - плоскогубцы; 4 - нагубники; 5 - медная пластина
Рисунок 7.5 Приемы гибки хомутика
7.4 Типичные дефекты при гибке, причины их появления
и способы предупреждения
Таблица 6
ДЕФЕКТ | ПРИЧИНЫ | СПОСОБ ПРЕДУПРЕЖДЕНИЯ |
При изгибании уголка из полосы он получился перекошенным | Неправильное закрепление заготовки в тисках | Закреплять полосу так, чтобы риска разметки точно располагалась по уровню гибок тисков проверять угольником |
Размеры изогнутой детали не соответствуют заданным | Неточный расчет развертки, неправильно выбрана оправка | Расчет развертки детали производить с учетом припуска на загиб и последующую обработку. Точно производить разметку мест изгиба. Применять оправки, точно соответствующие заданным размерам детали |
Вмятины (трещины) при изгибании трубы с наполнителем | Труба недостаточно плотно набита наполнителем | Трубу при заполнении наполнителем (сухим песком) располагать вертикально. Постукивать по трубе со всех сторон молотком. |
Контрольные вопросы:
Почему расчет длины заготовки для последующей гибки производят по нейтральной линии?
- Почему при использовании наполнителя при гибке труб не происходят деформации?
- В каких случаях и почему при гибке используют молотки с мягкими вставками?
- Что учитывается при выборе ударного инструмента при гибке?
- Почему при использовании специальных гибочных приспособлений при гибке труб не требуется применение наполнителя?
7.5 Механизация работ при правке и гибке металла
Для механизации работ при правке используют различные правильные машины. Простейшим устройством для механизации правки является ручной пресс (рис. 7.6), с помощью которого производят правку профильного проката и пруткового материала.
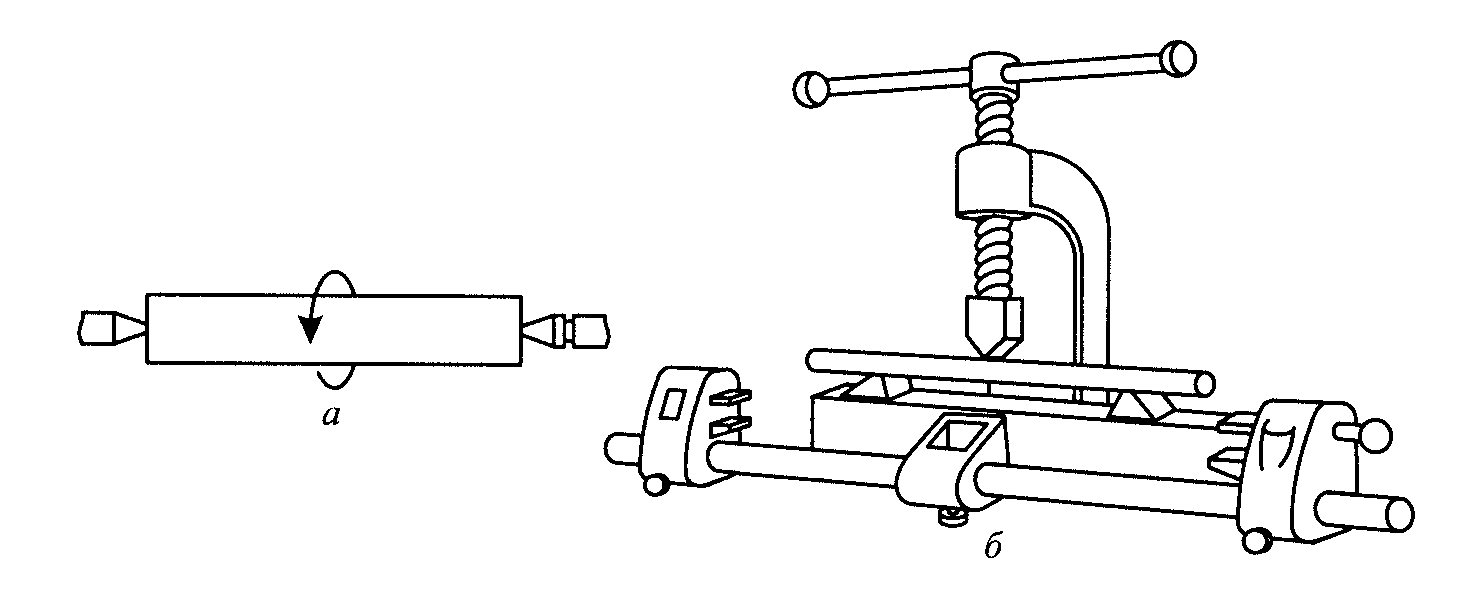
а - правка в центрах; б - правка на призмах
Рисунок 7.6 Ручной пресс
В большинстве случаев для правки листового и профильного проката используют специальные правильные машины (рис. 7.7, а), в которых основными рабочими органами являются вальцы (рис. 7.7, б). При правке лист подается в валки и благодаря силе трения втягивается между ними. Проходя между валками, лист перегибается то в одну, то в другую сторону и его волокна выравниваются. Для исправления лист пропускают через валки многократно. Кроме того, в правильных машинах можно править и профильный прокат, при этом правильные вальцы должны иметь профиль, соответствующий профилю материала.
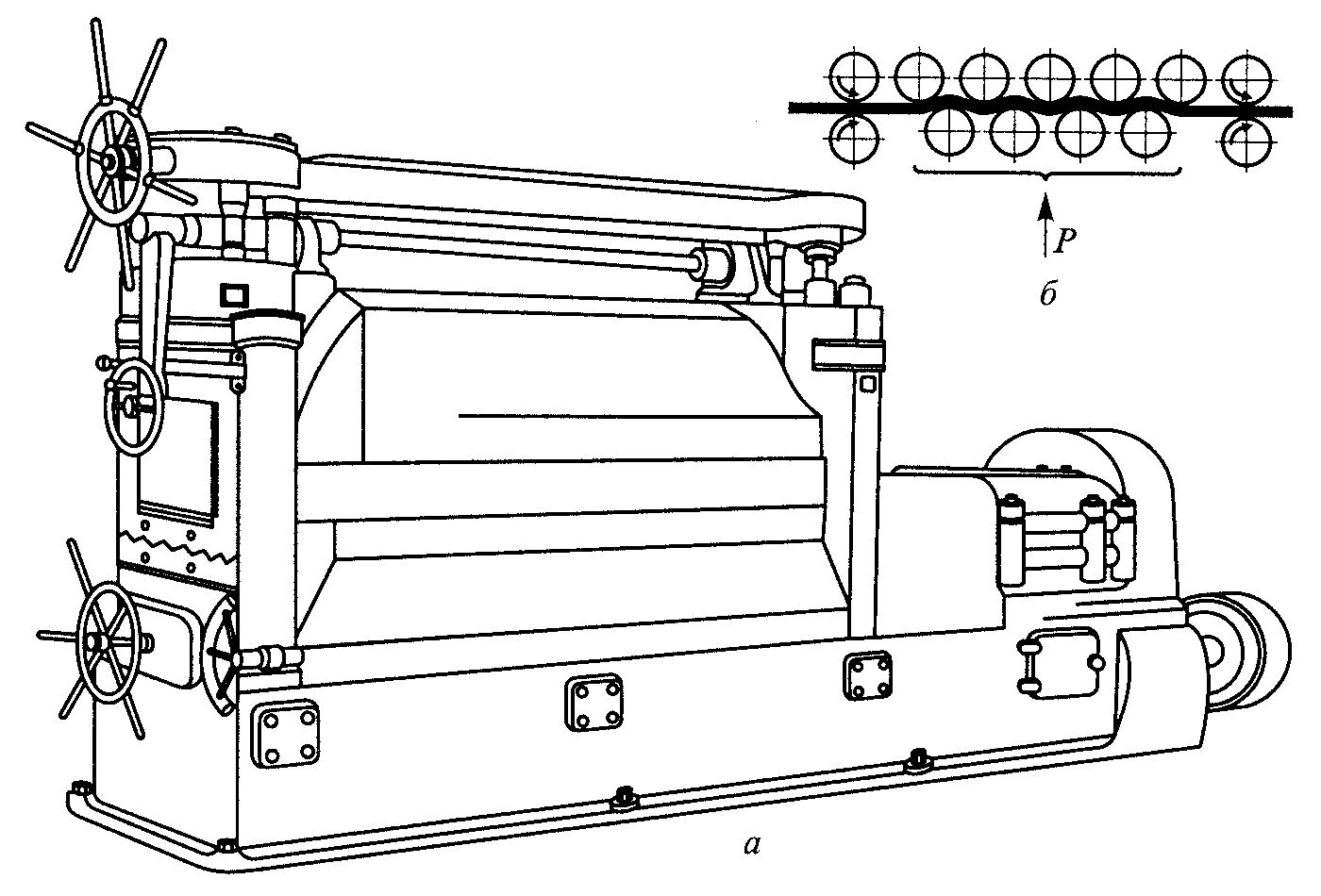
а - общий вид; б - схема правки; Р - усилие правки
Рисунок 7.7 Правильная машина
Для механизации работ при гибке используют гибочные машины. Некоторые из них представлены на рисунках. Листогибочные вальцы (рис. 7.8).
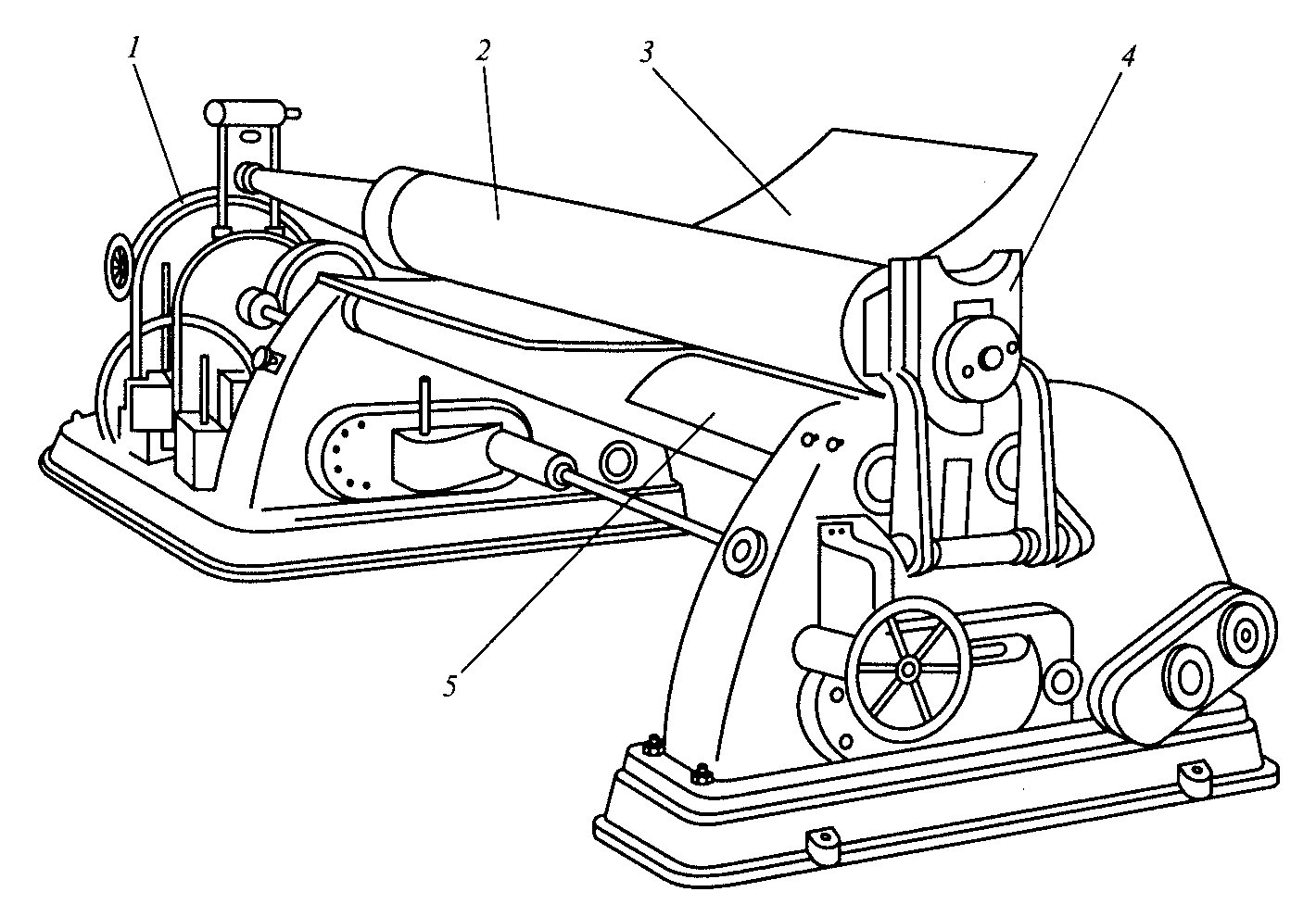
1 - механизм привода; 2 - верхний валок;
3 - изгибаемый лист; 4 - плита; 5 - нижний валок
Рисунок 7.8 Листогибочные вальцы
Верхний валок 2 имеет возможность перемещаться по высоте для придания листу заданного радиуса при гибке. Для получения конической формы изгибаемой детали верхнему валку придают наклон, равный углу наклона образующей конуса.
Роликовый гибочный станок (рис. 7.9, а, б).
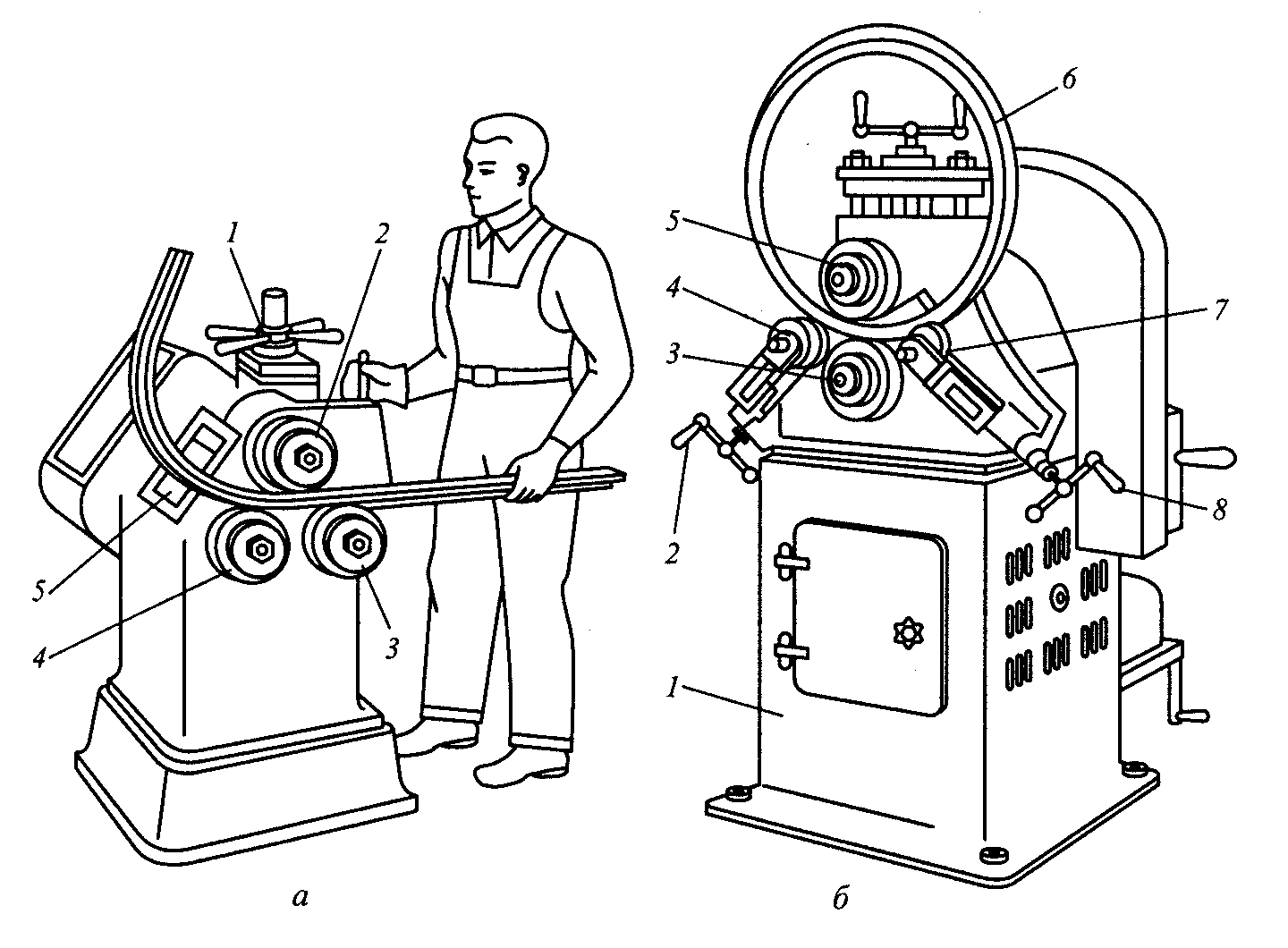
а - трехроликовый: 1 - рукоятка; 2 - верхний ролик; 3,4 - нажимные ролики;
5 - прижимы; б - четырехроликовый: 1 - станина; 2,8 - рукоятки; 3,5 - ведущие
ролики; 4,7 - нажимные ролики; 6 - заготовка
Рисунок 7.9 Роликовый гибочный станок
Листогибочные прессы (рис. 7.10, а, б, в) применяют для выполнения самых разнообразных работ – от гибки кромок до гибки профилей в одной или нескольких плоскостях.
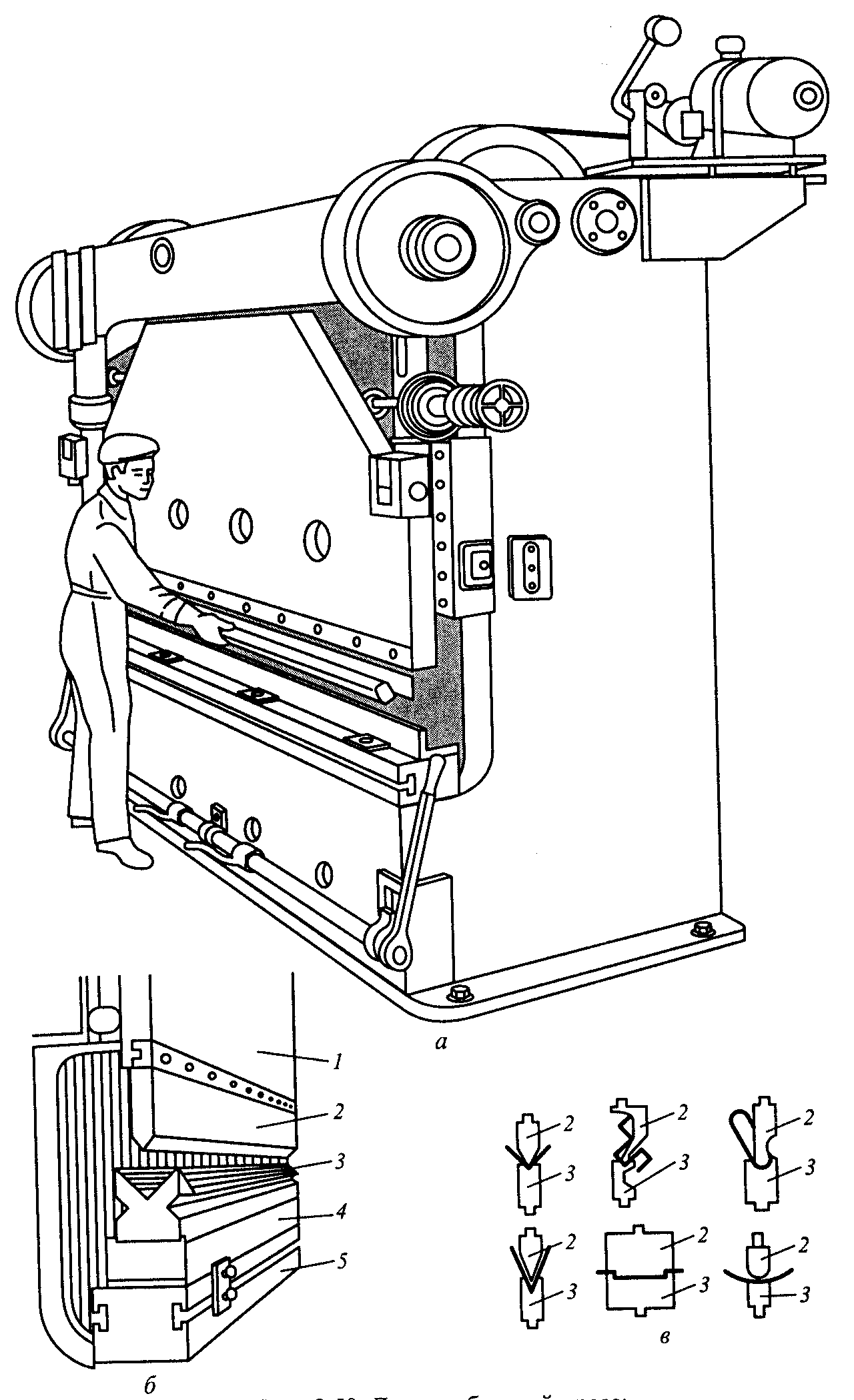
а - общий вид; б - конструктивная схема;
в - формы изгибаемого профиля;
1 - рама ползуна; 2 - пуансон;
3 - матрица; 4 - подкладка; 5 - плита
Рисунок 7.10 Листогибочный пресс
Размерная слесарная обработка
Под размерной обработкой понимается обработка заготовки (детали) для придания ей заданных форм, размеров и шероховатости обработанных поверхностей. В результате обработки получается готовое изделие, которое может иметь самостоятельное применение (например: молоток, зубило, угольник и т.п.) или деталь, пригодная к монтажу в собираемое изделие (например: рукоятки и рычаги различных конструкций). К операциям размерной слесарной обработки относятся: опиливание, обработка отверстий (сверление, зенкерование, зенкование, цекование, развертывание) и нарезание наружных, и внутренних резьб.
Тема 8 Опиливание
Студент должен:
знать:
- назначение напильников и их разновидности;
- приемы опиливания различных поверхностей деталей;
- приспособления, применяемые в процессе опиливания;
- правила техники безопасности при опиливании;
уметь:
- применять инструмент при опиливании поверхностей по назначению;
- подбирать инструмент в соответствии с поверхностью обрабатываемой
поверхности.
Оснащение рабочего места: верстак, тиски слесарные, набор напильников различных профилей поперечного сечения, длин и насечек, набор надфилей, лекальные линейки с двухсторонним скосом, угольники плоские 900 и 1200, штангенциркули с ценой деления по нониусу 0,1 и 0,05 мм, губки накладные; щетки металлические, щетка-сметка.
Опиливанием называют слесарную операцию по удалению с поверхности заготовки слоя металла (припуск) с помощью режущего инструмента – напильника, целью которой является придание заготовке заданных форм и размеров, а также обеспечение заданной шероховатости поверхности. Опиливание производят после рубки и резания металла ножовкой, а также при сборочных работах для пригонки детали по месту.
Напильниками обрабатывают плоские, криволинейные, фасонные сложного профиля поверхности, пазы, канавки, отверстия любой формы, поверхности, расположенные под любыми углами.
В зависимости от требуемой шероховатости поверхности опиливание выполняют напильниками с различной насечкой. Чем больше насечек на определенной длине напильника, тем мельче зуб. Опиливание подразделяется на предварительное (черновое) и окончательное (чистовое и отделочное). Припуски на опиливание предусматриваются в пределах 0,5–0,025 мм. Погрешность размеров детали может составлять 0,2-0,05 мм.
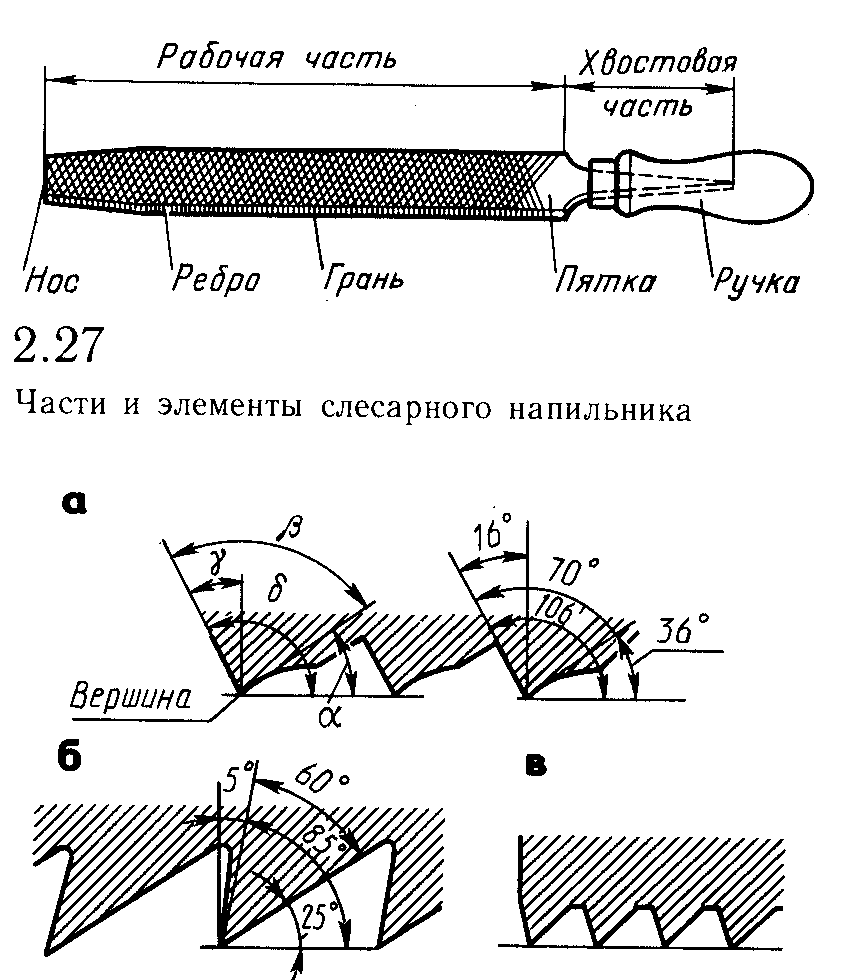
Рисунок 8.1 Части и элементы
слесарного напильника
Напильник представляет собой режущий инструмент в виде стального закаленного бруска определенного профиля и длиной 100-400 мм с большим количеством насечек или нарезок, образующих мелкие и острые зубья (резцы), которыми напильник срезает небольшой слой металла в виде стружки.
Основные части и элементы напильника показаны на рис.8.1. Зубья напильника могут быть образованы насеканием (рис.8.2, а), фрезерованием (рис. 8.2, б), протягиванием (рис.8.2, в) и другими способами. Наиболее распространенным способом образования зубьев является насекание их на специальных пилонасекательных станках с помощью зубила. Каждый зуб напильника имеет задний угол α, угол заострения β, передний угол γ.
Р
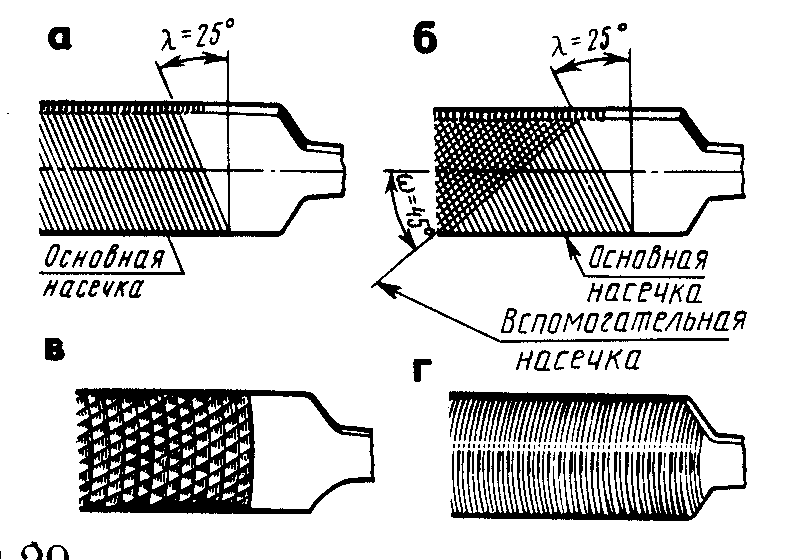
азличают напильники с одинарной или простой (рис.8.3, а), двойной или перекрестной (рис.8.3, б), рашпильной (точечной) (рис. 8.3, в), и дуговой (рис. 8.3, г) насечками.
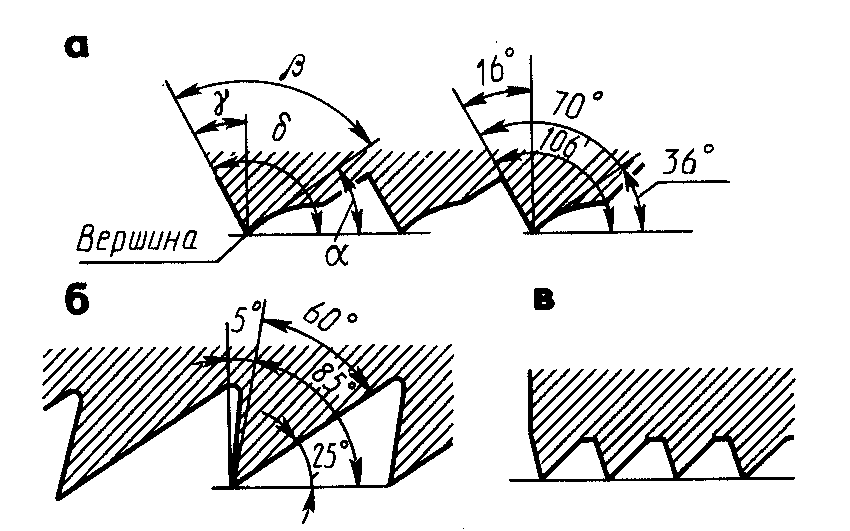
Рисунок 8.3 Виды насечек напильников
Рисунок 8.2 Геометрические элементы
напильников
Для обработки стали, чугуна и других твердых материалов, применяют напильники с двойной насечкой. Напильники классифицируются в зависимости от числа насечек на 10 мм длины напильника на 6 классов и предназначаются для определенных работ.
Таблица 7
Номер насечки | 0 | 1 | 2 | 3 | 4 | 5 |
Количество основных насечек на 10 мм длины | 5-13 | 8,5-14 | 12-20 | 17-28 | 24-40 | 34-56 |
Длина рабочей части напильника, мм | 350-400 | 100-400 | 100-300 |
Для грубого чернового опиливания (шероховатость Rz=160-80, точность 0,2-0,3 мм) применяются напильники 0 и 1 класса (драчевые), когда требуется удалить большой слой металла до 1 мм.
Для выполнения чистовой обработки (шероховатость Rz=40-20, точность 0,05-0,1 мм) используются напильники 2-3 класса (личные), снимаемый слой не превышает 0,3 мм.
Для пригоночных, отделочных и доводочных работ (шероховатость поверхности Rа 2,5-1,25, точность 0,02-0,05 мм) применяются напильники 4 и 5 класса (бархатные), снимаемый слой металла не более 0,05 мм.
По форме поперечного сечения напильники делятся на плоские (рис.8.4), квадратные, трехгранные, круглые, полукруглые, ромбические, ножовочные и др.
Надфили – небольшие напильники (длиной 80, 120 и 160 мм) различной формы поперечного сечения (рис. 8.5). В зависимости от количества насечек надфили делятся на пять типов №1,2,3,4,5 с количеством насечек 22-112 на 10 мм длины. Их применяют для опиливания и распиливания небольших поверхностей, недоступных для обработки слесарными напильниками; отверстий, углов, прорезей, пазов, радиусов, коротких участков фасонных профилей, шаблонов (лекал) и где требуется низкая шероховатость поверхности.
Наибольшее распространение надфили получили в инструментальных цехах при выполнении лекальных, граверных и ювелирных работ. При слесарной обработке применяют и другие типы напильников: со специальной державкой, тарированные, алмазные, рашпили, вращающиеся борнапильники и др.
Положение корпуса работающего напильником считается удобным и правильным, если стоять перед тисками прямо и устойчиво (рис 8.6, а) или вполоборота под углом 450 к оси тисков. Ступни ног должны стоять под углом 40-600, расстояние между пятками ног более 200-300 мм (рис. 8.6).
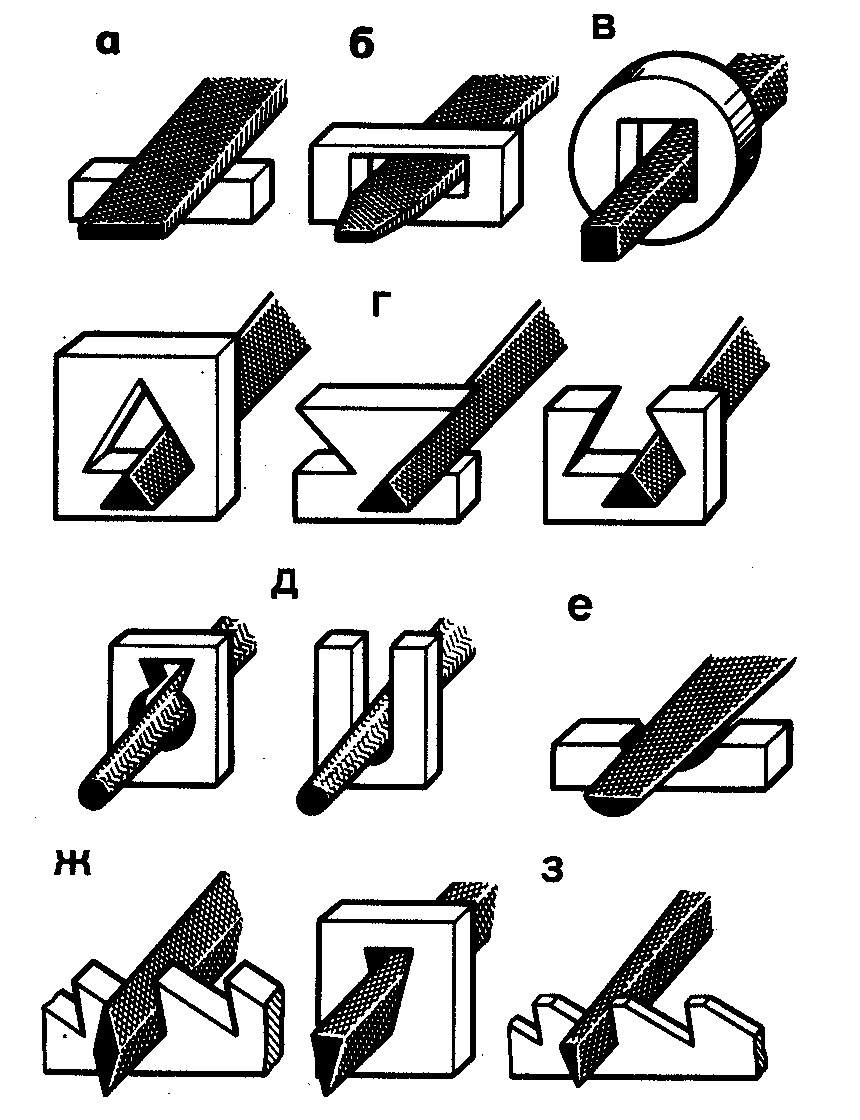
Рисунок 8.4 Формы сечения напильников и
примеры их применения
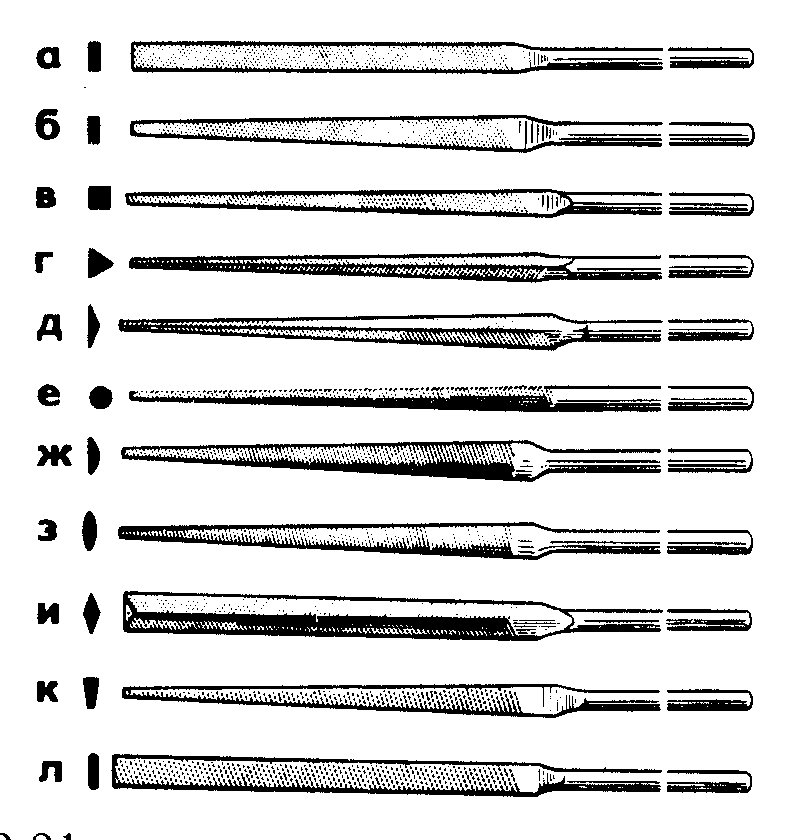
а - плоский тупоносый; б - плоский остроносый; в - квадратный; г - трехгранный односторонний; е - круглый; ж - полукруглый; з - овальный; и - ромбический; к - ножовочный; л - пазовый
Рисунок 8.5 Надфили
Правая рука с напильником, лежащая на губках тисков, согнутая в локте, образует прямой угол между плечевой и локтевой частью руки. Конец рукоятки напильника должен упираться в середину ладони правой руки, четырьмя пальцами охватывается снизу и большим вдоль оси рукоятки, сверху (рис. 8.7, а) ладонь левой руки располагается поперек напильника на расстоянии 20-30 мм от его носка; пальцы слегка согнуть, но не свешивать.
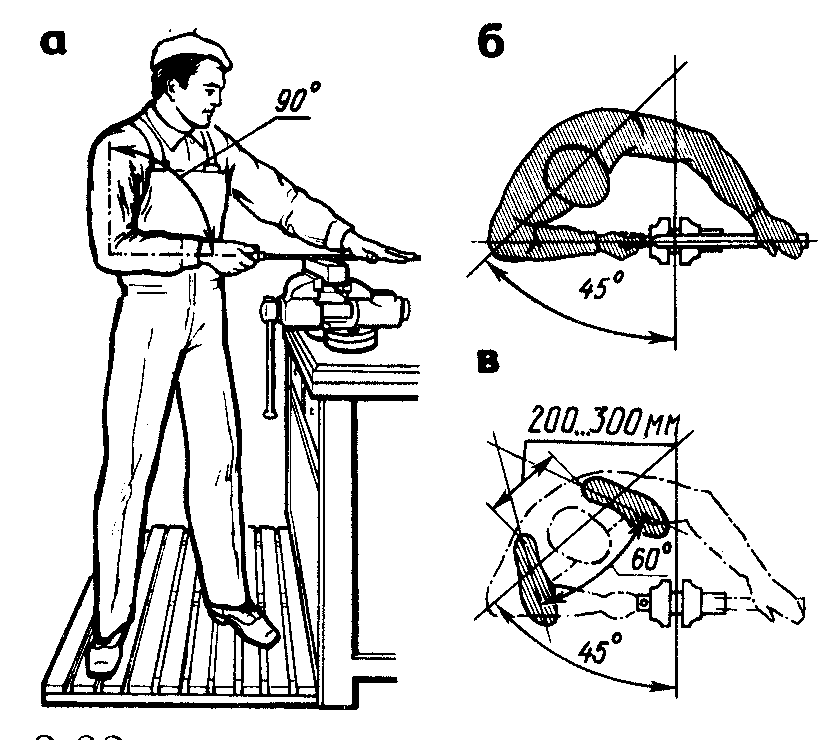
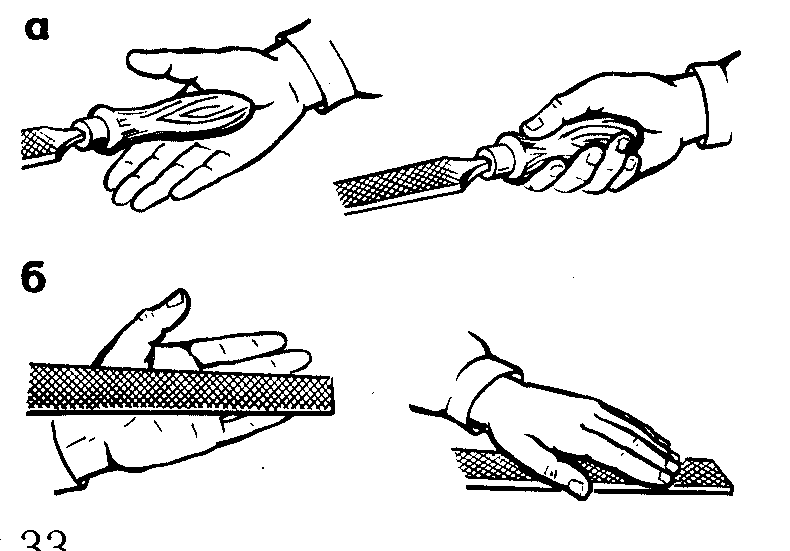
Рисунок 8.6 Положение при опиливании
Рисунок 8.7 Положение пальцев рук
при опиливании
8.1 Приемы опиливания деталей
При опиливании напильник перемещают строго горизонтально вперед (рабочий ход) плавно, производя 40-60 двойных ходов в минуту. Напильник должен касаться обрабатываемой плоскости всей своей поверхностью. Нажимать на напильник только при движении вперед, строго соблюдая распределение усилий, как показано на рис.8.8.
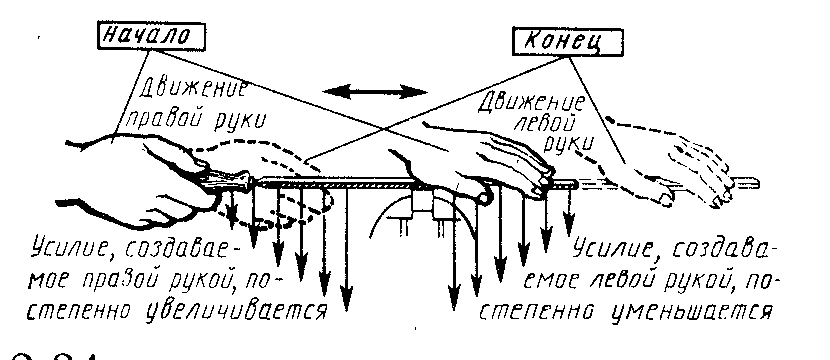
Рисунок 8.8 Распределение усилий нажима при опиливании
Обрабатываемая поверхность должна выступать над губками тисков на 8-10 мм. Опиливание плоскостей является сложным и трудоемким процессом. Чаще всего дефектом при опиливании плоскостей является неплоскостность. Работая напильником в одном направлении, трудно получить правильную и чистую поверхность.
Положение штрихов (следов зубьев напильника) на обрабатываемой поверхности зависит от направления движения напильника, которое может быть прямым (продольным) (8.9, а), косым (поперечным) (рис. 8.9, б) и перекрестным (рис.8.9, в).

Рисунок 8.9 Опиливание плоских поверхностей
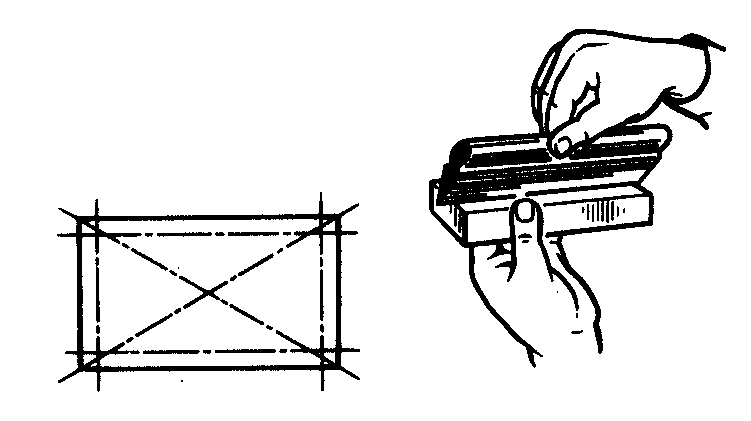
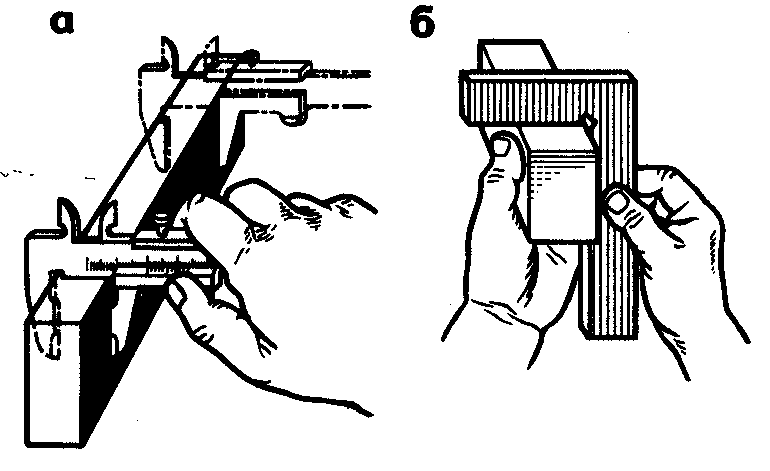
Рисунок 8.10 Проверка отклонения от
плоскостности опиленной
поверхности
а - от параллельности; б - от перпендикулярности
Рисунок 8.11 Примеры отклонения опиленных
поверхностей
Наименьшего отклонения от плоскости поверхности достигают при опиливании перекрестным штрихом. Опиливание всегда начинают напильником с насечкой №1 или №2, снимая основной слой металла не доходя до разметочной риски 0,8 – 1 мм, после чего напильником с насечкой №3 и 4 окончательно снимают оставшийся слой металла по риске, выдерживая заданный размер по чертежу. Контроль опиленной поверхности осуществляют поверочными линейками, штангенциркулями, угольниками и поверочными плитами.
Отклонение от плоскостности и прямолинейности проверяют лекальной линейкой. Отклонение от параллельности проверяют штангенциркулем, а плоскостей расположенных под прямым углом – угольником или универсальным угломером (рис.8.10, 8.11.).
Опиливание плоскопараллельных плоскостей заготовки начинают с наиболее широкой поверхности, которую принимают за основную измерительную базу. Эту поверхность опиливают окончательно, соблюдая все правила опиливания и проверки плоских поверхностей. Затем штангенциркулем предварительно проверяют толщину и параллельность сторон заготовки, замеры производят в 3-4 местах. Определив припуск, подлежащий удалению в различных местах второй широкой обрабатываемой поверхности, производят ее опиливание. Контроль отклонения от прямолинейности, плоскостности и параллельности производят периодически. Отклонение от параллельности сторон в процессе опиливания контролируют кронциркулем (рис. 8.12).
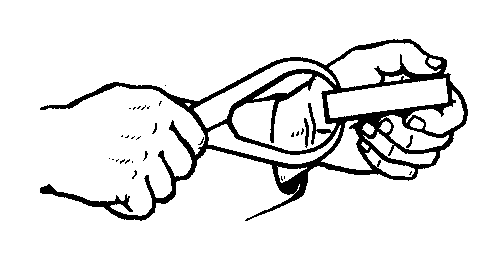
Рисунок 8.12 Определение отклонения от
параллельности сторон кронциркулем
На окончательно обработанной поверхности должны быть наведены продольные штрихи. Отклонение от параллельности, прямолинейности и плоскостности обработанных сторон и их толщина должны быть в пределах допусков, указанных на чертеже.
Опиливание сопряженных поверхностей – самый распространенный вид опиливания, так как предназначается для плоскостей, расположенных под углом 900 друг к другу или под иным углом, требуемым чертежом. Наружные углы обрабатывают плоскими напильниками, внутренние углы в зависимости от их размера, можно обрабатывать плоскими (с одним ребром без насечки), трехгранными, квадратными ножовочными и ромбическими напильниками. Обработку заготовки начинают с базовой, наиболее длинной или широкой плоскости.
Эту поверхность (или ребро) опиливают окончательно, соблюдая все правила опиливания и проверки плоских поверхностей. Затем угольником предварительно проверяют угол между обработанной (базовой) и необработанной поверхностями. Выступающие места на необработанной поверхности опиливают перекрестным штрихом, периодически проверяя угол угольником, а отклонение от прямолинейности и плоскостности – линейкой. Если при проверке линейкой и угольником наблюдается равномерный просвет между проверяемой поверхностью и линейкой, проверяемым углом и ребром угольника, то работа по обеспечению точности обработки считается выполненной, после чего на обработанной поверхности необходимо нанести равномерные продольные штрихи. Последовательность опиливания поверхностей, расположенных под внутренним углом, такая же, как и поверхностей, расположенных под внешним углом. Особое внимание обращать на тщательность обработки мест сопряжения внутренних плоскостей угла, пользуясь для этого ромбическим или трехгранным напильником.
При закреплении заготовки в тисках для предохранения уже обработанной базовой поверхности от повреждений обязательно пользоваться накладными губками. Размер напильника выбирают с таким расчетом, чтобы он был длинней опиливаемой поверхности не менее чем на 150 мм. Если параметр шероховатости поверхности на чертеже обрабатываемой детали не указан, опиливание производят только напильником с насечкой №1 или №2. Если требуется получить поверхность с более низкой шероховатостью, то опиливание заканчивают напильником с насечкой №3 или №4.
8.2 Опиливание криволинейных поверхностей, пазов и отверстий
Криволинейные поверхности разделяются на выпуклые и вогнутые, они могут находиться как на плоских деталях типа шаблонов, планок, так и на цилиндрических, многогранных и другой формы стержнях и валиках. Обычно опиливание таких поверхностей связано со снятием больших припусков. Прежде чем приступить к опиливанию следует разметить заготовку, удалить излишек металла путем вырезания ножовкой, срубания зубилом, или высверливанием с последующим вырубанием. Выпуклые поверхности опиливают плоскими напильниками вдоль и поперек выпуклости. Контроль опиленной заготовки производят шаблонами, угольником и штангенциркулем.
Приемы опиливания наружных криволинейных поверхностей и цилиндрических показаны на рис. 8.13, а…е. Опиливание вогнутых поверхностей начинают с разметки на заготовке контура детали. Большую часть металла (припуска) можно удалить выпиливанием ножовкой, придав впадине заготовки форму треугольника. Затем круглым или полукруглым напильниками спиливают излишний металл до нанесенной разметочной риски.
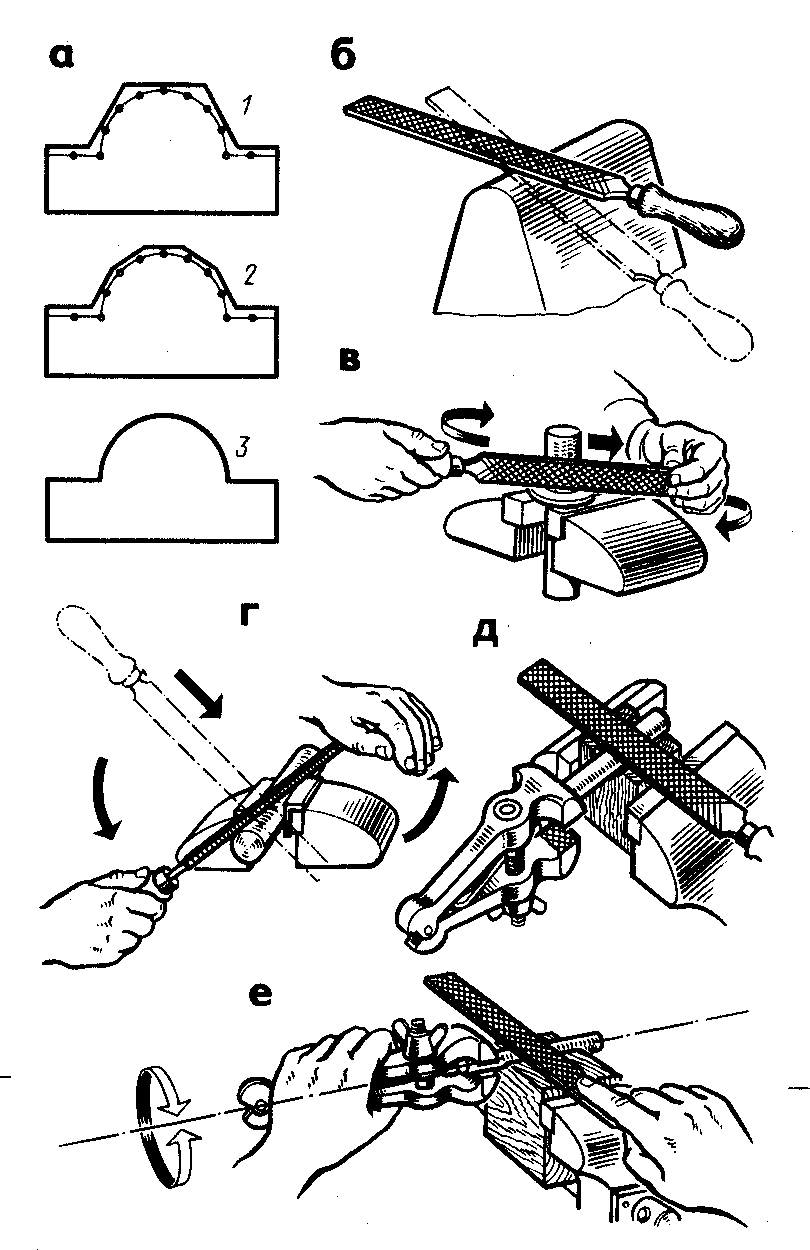
а - последовательность обработки:
1 - срезание излишнего металла ножовкой;
2 - опиливание черновое на многогранник;
3 - опиливание окончательное по шаблону;
б - опиливание выпуклой поверхности (носка молотка);
в - опиливание стержня, закрепленного вертикально;
г - опиливание стержня, закрепленного горизонтально;
д - опиливание цилиндрического стержня, закрепленного в ручных тисках; е - опиливание стержня на конус, закрепленного в ручных тисках
Рисунок 8.13 Приемы опиливания наружных
криволинейных поверхностей
Профиль сечения круглого или полукруглого напильника выбирают таким, чтобы его радиус был меньше, чем радиус опиливаемой поверхности. Правильность формы поверхности проверяют по шаблону на просвет, а перпендикулярность опиленной поверхности к торцу заготовки – угольником. При опиливании сочетаются два движения напильника – прямолинейное и вращательное, т.е. каждое движение напильника вперед сопровождается небольшим поворотом его правой рукой на ¼ оборота вправо или влево. Все приемы опиливания и проверки полученной поверхности аналогичны обработке выпуклых поверхностей.
Приемы опиливания вогнутых криволинейных поверхностей показаны на рис. 8.14, а…г.
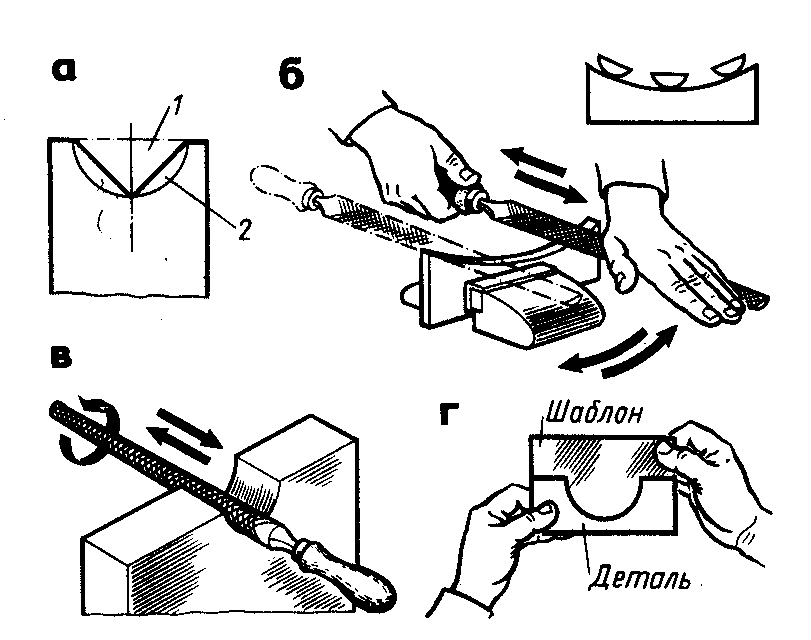
а - последовательность обработки:
1 - срезание излишнего металла ножовкой;
2 - опиливание круглым напильником;
б - опиливание вогнутой поверхности большого радиуса кривизны;
в - опиливание вогнутой поверхности малого радиуса кривизны;
г - проверка опиленной поверхности шаблоном
Рисунок 8.14 Приемы опиливания
вогнутых криволинейных
поверхностей
Распиливание отверстий и пазов в целях придания им нужной формы является одной из разновидностей обработки внутренних прямолинейных и криволинейных поверхностей. Распиливание выполняют напильниками соответствующей формы сечения, например, круглые отверстия, обрабатывают круглыми и полукруглыми напильниками; трехгранные отверстия – трехгранными, ножовочными и ромбическими напильниками и т.п.
Подготовка к распиливанию начинается с разметки и накернивания разметочных рисок, сверления по разметочным рискам отверстий и вырубки проймы (удаления излишнего металла из будущего отверстия). Все приемы опиливания и проверки аналогичны приемам, выполняющимся на предыдущем занятии.
При обработке отверстий и проемов малого сечения, где использование слесарных напильников невозможно, применяют надфили требуемого профиля. Приемы распиливания отверстий и пазов показаны на рис.8.15.
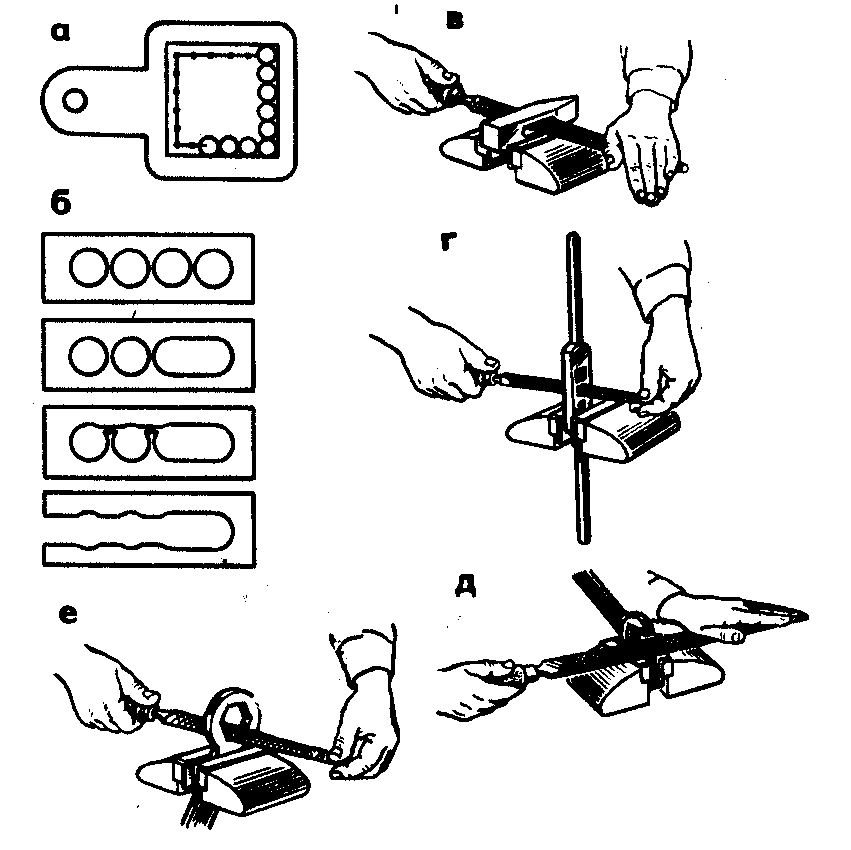
а - разметка и обсверливание контура;
б - сверление, вырубка и распиливание проема;
в - распиливание отверстия молотка;
г - распиливание квадратных отверстий воротка; д - распиливание зева гаечного ключа;
е - распиливание шестигранного отверстия ключа
Рисунок 8.15 Приемы распиливания пазов
и отверстий
8.3 Механизация работ при опиливании
Трудоемкое и утомительное ручное опиливание поверхностей имеет до сих пор значительный удельный вес в общем объеме слесарной обработки, поэтому повсеместно принимаются меры к механизации процесса опиловочных работ.
Механизация опиливания осуществляется двумя способами:
- заменой опиловочных работ станочной обработкой;
- использованием специальных опиловочных станков, электрических и пневматических инструментов, а также специальных приспособлений.
При использовании опиловочных станков и средств малой механизации необходимы специальные инструменты, которые можно применять с этим оборудованием.
Инструменты для механизации опиловочных работ
Эти инструменты подразделяются на две группы: инструменты для механизированных устройств возвратно-поступательного и вращательного действия.
К инструментам с возвратно-поступательным движением относятся машинные напильники, которые изготовляют из инструментальных углеродистых сталей марок У12 и У12А (рис. 8.16). Они, как и обычные напильники для ручного опиливания, имеют разную форму поперечного сечения, однако их номенклатура ограничена тремя типами (квадратные, плоские и треугольные). Поэтому машинные напильники применяются для обработки плоских поверхностей, а также поверхностей, расположенных под различными углами друг к другу, причем углы эти не должны быть менее 300.
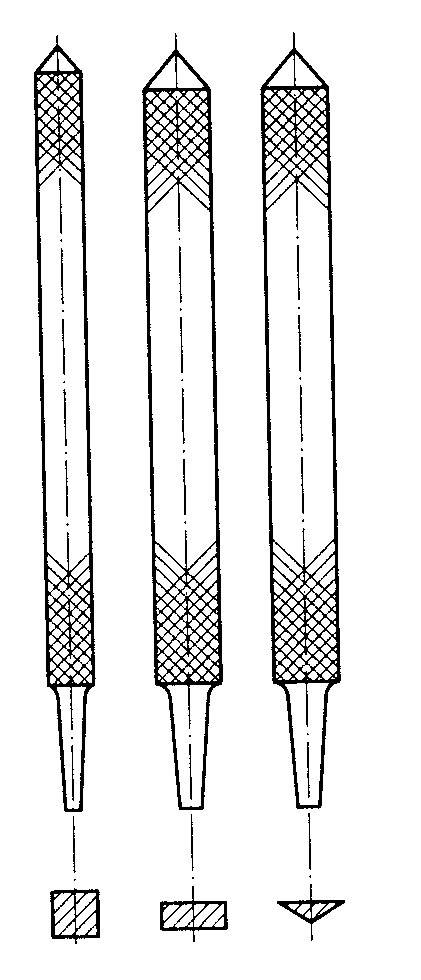
Рисунок 8.16 Машинные напильники
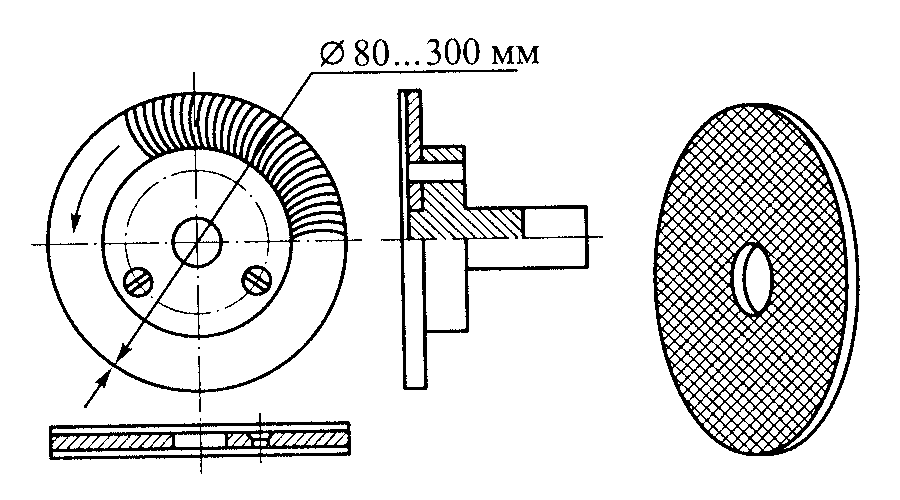
Рисунок 8.17 Опиловочные диски
К
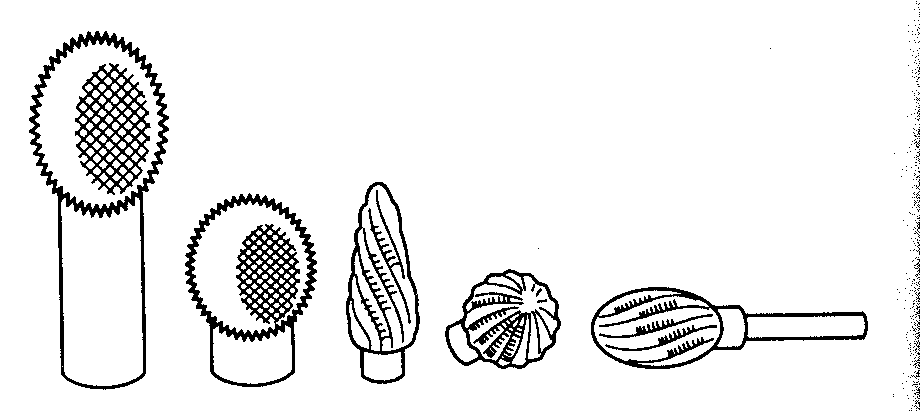
инструментам с вращательным движением относятся диски (рис. 8.17), фрезы, шарошки (фрезы с большим шагом зубьев), боры (рис. 8.18) (фрезы с малым шагом зубьев) и шлифовальные головки-насадки (рис. 8.19), которые применяются при отделочных операциях.
Рисунок 8.18 Боры
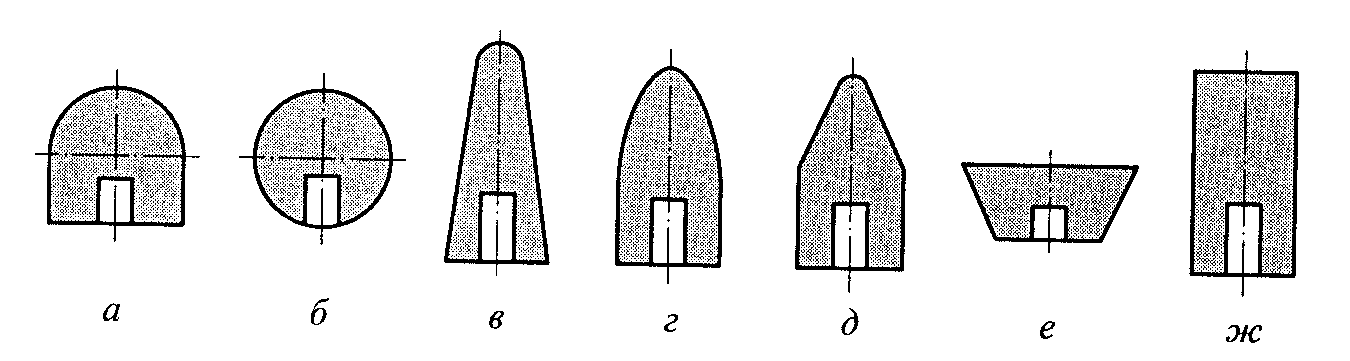
а - полукруглая; б - круглая; в, г, д - конические;
е - обратноконическая; ж - цилиндрическая
Рисунок 8.19 Шлифовальные головки
Ручные механизированные инструменты могут иметь как электрический, так и пневматический привод. Рабочее движение у этих инструментов может быть вращательным (при использовании дисков, боров, шлифовальных головок), так и возвратно-поступательным (при использовании машинных напильников).
Электрическая опиловочная машина с гибким валом, который может передавать вращательное движение от электрического привода к исполнительному механизму, изгибаясь при этом под различными углами, изображена на рис.8.20. Это значительно расширяет технологические возможности устройств подобного типа. Машины такого типа отличаются большим разнообразием конструкций.
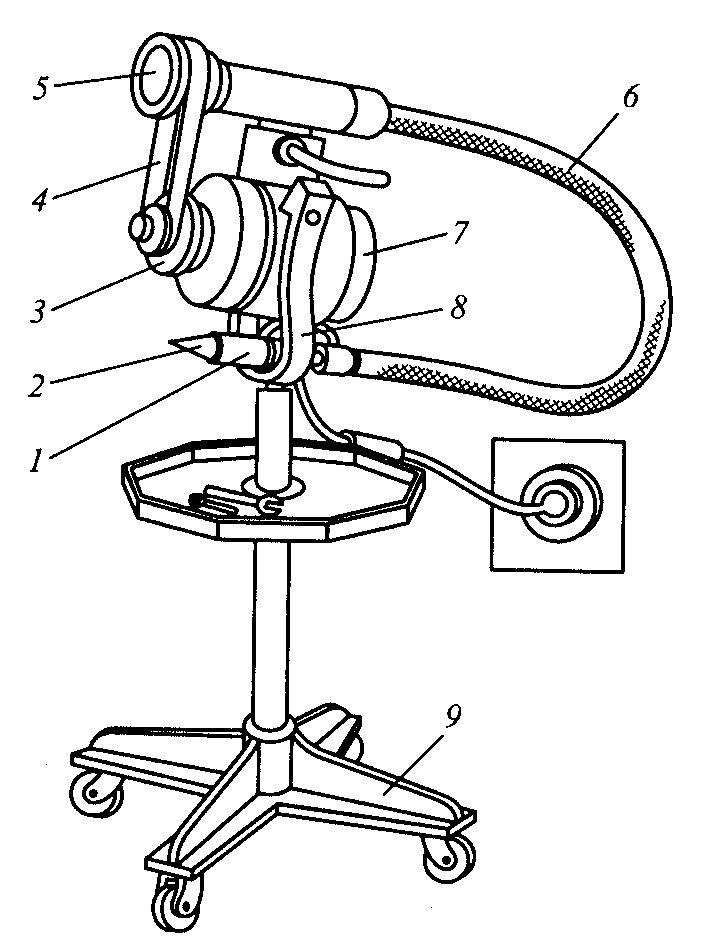
1 - патрон; 2 - инструмент; 3,5 - шкивы; 4- ремень; 6 - гибкий вал; 7 - электродвигатель; 8 - кронштейн; 9 - опора
Рисунок 8.20 Электрическая опиловочная
машина с гибким валом
Приведенная в качестве примера опиловочная машина смонтирована на опоре 9. Вращательное движение передается рабочему органу от электродвигателя 7 посредством ремня 4 и ступенчатых шкивов 5 и 3 гибкому валу 6. На гибком валу установлен патрон 1, в котором крепится инструмент – фреза, шарошка, шлифовальная головка 2. В нерабочем положении патрон с напильником устанавливают в кронштейн 8.
В электрических машинах возвратно-поступательного действия используются механизмы преобразования вращательного движения в возвратно-поступательное. Принципиальных конструктивных отличий от опиловочных устройства вращательного типа такие машины не имеют, за исключением установки механизма преобразования движения.
Пневматические опиловочные машины (рис. 8.21) не имеют индивидуального привода, их присоединяют либо к централизованной сети разводки воздуха высокого давления, либо к индивидуальному компрессору, производящему воздух высокого давления.
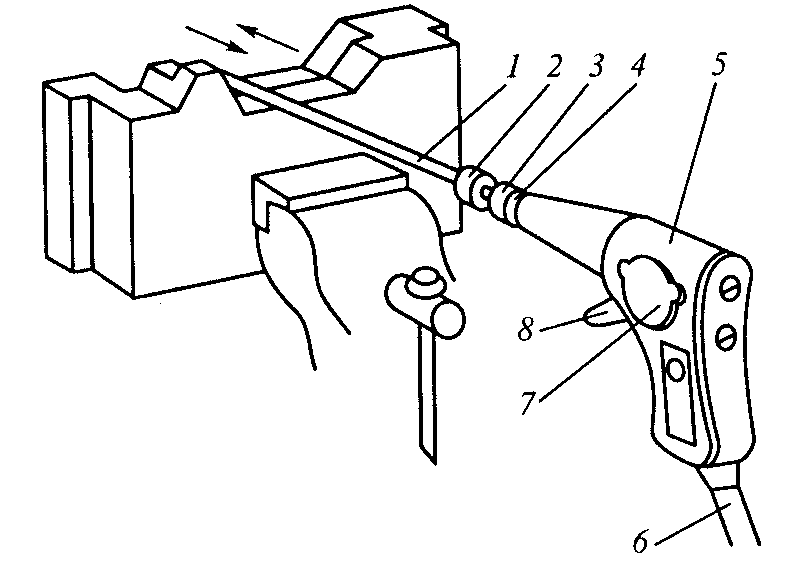
1 - инструмент; 2 - патрон; 3 - поршень;
4 - поворотная втулка; 5 - поршневая коробка;
6 - шланг; 7 - крышка; 8 - пусковой крючок
Рисунок 8.21 Пневматическая
опиловочная машина
Воздух высокого давления по воздухопроводящему шлангу 6 (независимо от источника сжатого воздуха) поступает в поршневую коробку 5, заставляя поршень 3 совершать возвратно-поступательные движения, которые через шток передаются инструменту 1. Инструмент 1 закрепляют в патроне 2, связанном с поршнем поворотной втулкой 4. Доступ воздуха в поршневую коробку 5 осуществляется нажатием на пусковой крючок 8. Доступ к поршневой группе для контроля за ее состоянием осуществляется при снятии крышки 7.
Стационарное опиловочное оборудование обеспечивает повышение производительности по сравнению с ручным опиливанием более чем в 15 раз, однако использование такого оборудования ограничено номенклатурой применяемого на нем инструмента. На этом оборудовании можно обрабатывать плоское поверхности наружного и внутреннего контура, расположенные, как правило, под углами более 300.
Опиловочный станок с абразивной лентой (рис. 8.22) предназначен для обработки наружных и внутренних поверхностей, в качестве рабочего инструмента в нем используется бесконечная абразивная лента. Станок монтируется на основании 5, на котором устанавливают кронштейн 1. Внутри кронштейна находится бесконечная абразивная лента 3, приводимая в движение от электродвигателя, расположенного в основании. На кронштейне смонтирован стол 4, на котором закрепляют заготовку. Для обеспечения комфортных условий работы на станке предусмотрено местное освещение лампой 2. Пуск станка осуществляется от кнопки включения 6.
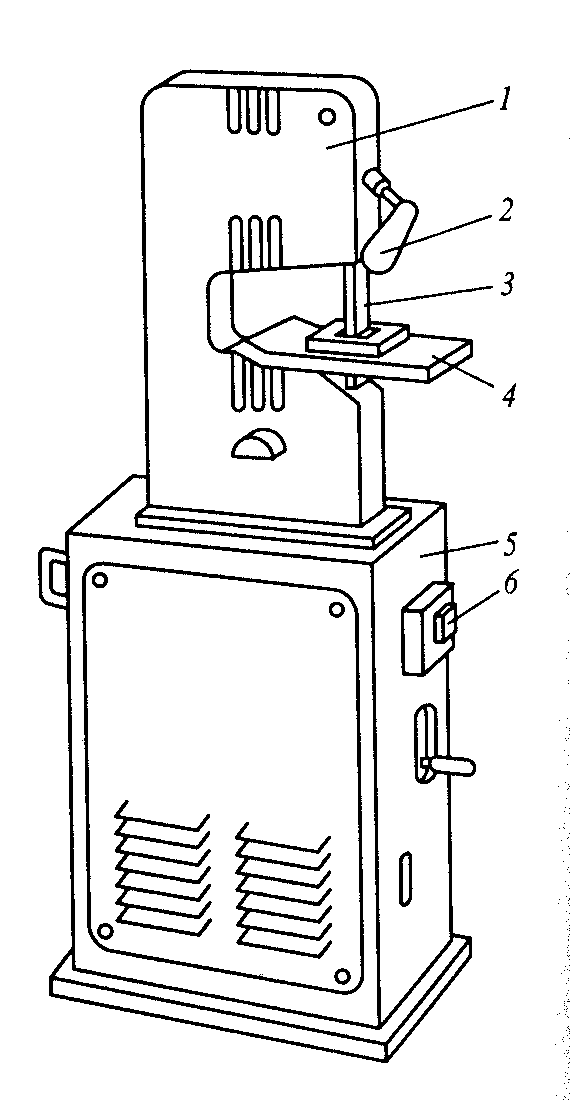
1 - кронштейн; 2 - лампа; 3 - бесконечная образивная лента; 4 - стол; 5 - основание; 6 - кнопка включения
Рисунок 8.22 Опиловочный станок с
абразивной лентой
Стационарный опиловочно-зачистной станок (рис.8.23) предназначен для обработки плоских поверхностей, как наружных, так и внутренних, расположенных под углом, не превышающим 300. Он состоит из станины 1, на которой установлена стойка 4. Все приводы расположены внутри станины и стойки, в стойку вмонтирован шток 6, на котором крепятся кронштейны 5 и 3. Напильник 7 закрепляют в кронштейнах 3 и 5 при помощи винтов 12. Заготовку 8 устанавливают на столе 9. Установка заготовки на заданный угол обработки производится за счет поворота стола при помощи винта 10. Шкивы привода защищены кожухом 2, а запуск станка в работу осуществляется при помощи нажатия на педаль 11.
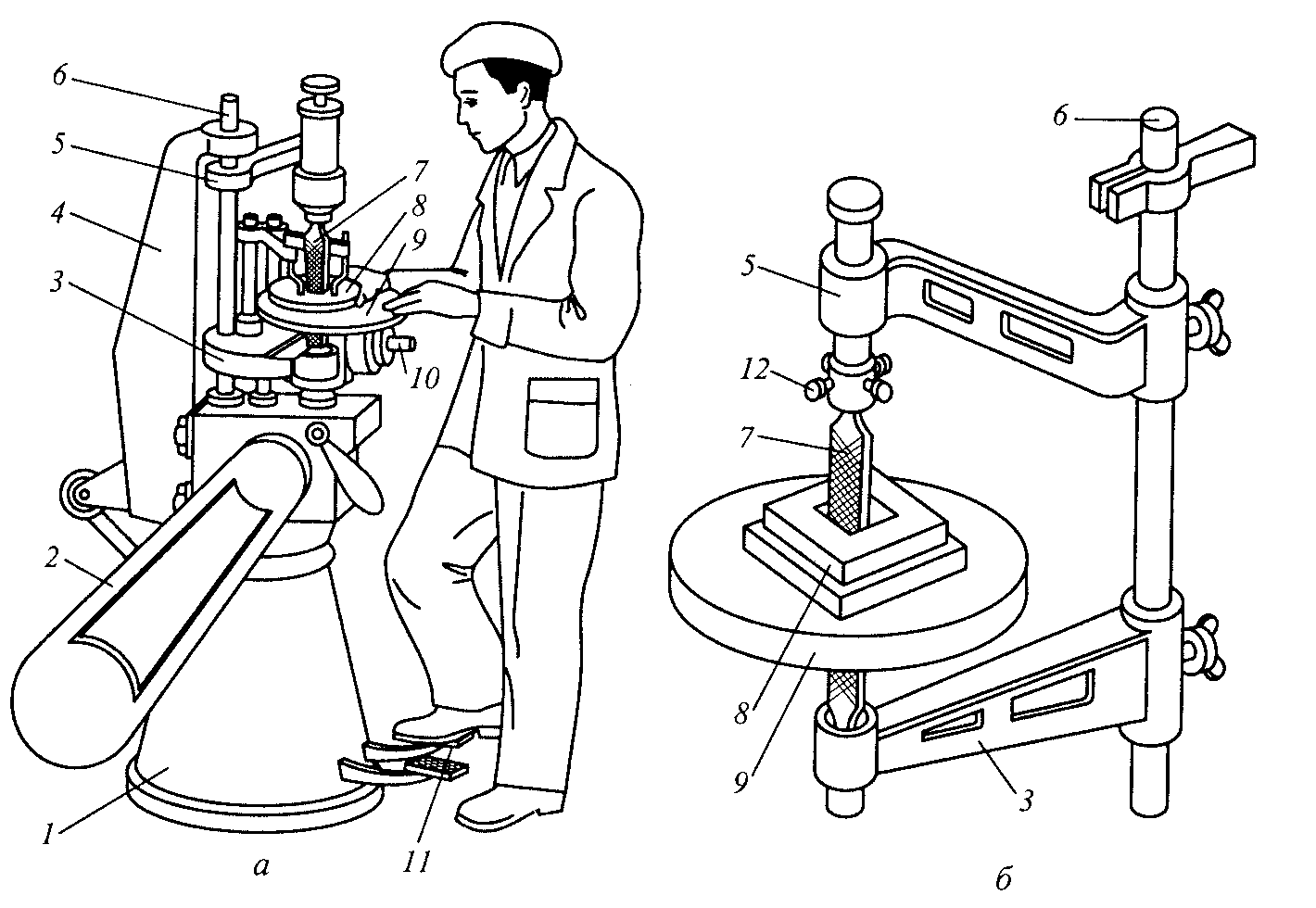
а - общий вид станка; б - исполнительный узел; 1 - станина; 2 - кожух; 3, 5 - кронштейны; 4 - стойка; 6 - шток; 7 - напильник; 8 - заготовка; 9 - стол; 10,12 - винты; 11 - пусковая педаль
Рисунок 8.23 Стационарный опиловочно-зачистной станок
8.4 Типичные дефекты при опиливании металла,