Учебно-методический комплекс для дисциплины «Организация и планирование производства» для специальности атп
Вид материала | Учебно-методический комплекс |
- Внутрифирменное планирование учебно-методический комплекс для студентов специальности, 1405.1kb.
- Организация и планирование электронного бизнеса учебно-методический комплекс по циклу, 320.5kb.
- Учебно-методический комплекс по циклу дисциплин сд. 03 Для студентов очной и заочной, 466.36kb.
- Учебно-методический комплекс по дисциплине Сети ЭВМ и телекоммуникации (наименование, 743.2kb.
- А. Б. Тазаян Учебно-методический комплекс дисциплины "Философия права" (для студентов, 524.1kb.
- Учебно-методический комплекс дисциплины гендерология и феминология для студентов психологического, 670.76kb.
- Учебно-методический комплекс для студентов идпо специальности «Финансы и кредит», 1145.04kb.
- О. А. Миронова Учебно-методический комплекс дисциплины «международная торговля» Ростов-на-Дону, 727.71kb.
- Учебно-методический комплекс дисциплины «Разработка и технологии производства рекламного, 295.77kb.
- Учебно-методический комплекс для специальности 520400 «Философия» подготовки бакалавра, 724.75kb.
Комплексная подготовка производства представляет собой совокупность целенаправленных технических, экономических и организационных мероприятий по конструированию новых и модернизации выпускаемых машин, механизмов; проектированию технологии их изготовления; по организации производства и повышения технического уровня
Планирование в подсистеме управления подготовкой производства заключается в выработке управляющих воздействий и состоит из следующих видов работ:
а) определения объема работ по конструкторским и технологическим разработкам объектов производства;
б) определения затрат на подготовку производства;
в) разработки развернутых планов и графиков подготовки, а также периодической корректировки их по результатам анализа фактического выполнения работ.
Учет в подсистеме управления подготовкой производства состоит в сборе данных о фактическом ходе выполнения всех работ по подготовке за отчетный период времени и представлении их в виде, удобном для анализа (контроля) и корректировки планов и графиков, а также для использования данных в других функциональных подсистемах управления.
Контроль в подсистеме управления подготовкой производства заключается в выявлении на основе учетных данных состояния всех работ по отношению к плану и оценке общей тенденции по выполнению работ за отчетный период. При этом даются ответы, например, на такие вопросы:
а) как возросли или уменьшились объемы работ и затраты на подготовку;
б) на сколько дней уменьшился или увеличился период отставания (опережения) производства некоторых работ по сравнению с директивными сроками;
в) какие виды работ относятся к контролируемым.
Анализ позволяет разобраться в изменениях, происшедших за определенный период времени, и оценить их возможное влияние на будущий ход работ. Таким образом, цель анализа — прогнозирование будущего хода работ с выявлением в процессе его проведения «узких мест», которые подлежат ликвидации при корректировке.
Все рассмотренные выше фазы процесса управления подготовкой производства связаны между собой. Планирование подготовки производства является основным фактором подсистемы управления, воздействующим на объект. Для организации планирования необходимы следующие исходные данные:
- перспективный план экономического развития предприятия;
- плановые задания на изготовление опытных образцов изделий и их освоение в промышленном производстве;
- производственная программа предприятия на плановый период;
- нормативы для определения объема и трудоемкости работ по всем этапам технической подготовки производства;
- производственная мощность (или пропускная способность) цехов, опытного, экспериментального и инструментального производств и возможности технических служб предприятия.
Анализ исходных данных планирования позволяет сделать вывод о том, что информационно-замкнутая подсистема управления подготовкой производства связана на входе с подсистемой технико-экономического управления данного предприятия и с вышестоящими отраслевыми организациями (управление, министерство), если такие имеются. Она получает от последних задающие воздействия и нормативы.
Одна из важнейших особенностей подсистемы — формирование задающих воздействий непосредственно в подсистеме управления подготовкой производства. Что же касается взаимосвязи подсистемы управления подготовкой производства с другими подсистемами управления, то она осуществляется косвенным путем — через результаты выполненных работ по подготовке производства (например, установление нормативов труда, видов материалов в процессе разработки технологии). Эти результаты могут быть нормативами для подсистемы управления материально-техническим снабжением и оперативного управления основным производством. Характер связи подсистемы управления подготовкой производства с другими подсистемами, а также состав, содержание, периодичность и методы решения задач подсистемы зависят от типа производства.
В массовом производстве подготовка включает весь комплекс работ конструкторского и технологического этапов, приведенных выше. В серийном производстве, как правило, отсутствует, как самостоятельный элемент, эскизное проектирование. Оно совмещается с техническим проектированием. В мелкосерийном и единичном производстве нет эскизного проектирования (вместо опытных образцов изготовляются отдельные узлы), а также рабочего проектирования по опытному образцу (опытные партии изделий не выпускаются).
Содержание и степень детализации расчетных и конструктивно-технологических процессов комплекса работ по подготовке зависят от типа производства. Так, в единичном и мелкосерийном производствах при разработке технологических процессов обычно ограничиваются составлением маршрутной технологии, т.е. установлением последовательности выполнения основных операций и использования ведущих групп оборудования.
Маршрутная технология определяет также движение предметов труда по рабочим местам, участкам, цехам, основные операции, оборудование, виды технологической оснастки, вес и размер заготовок, марку материала, разряды работ и нормы времени. В серийном же производстве проектирование технологических процессов ведется на каждую операцию, а в массовом и крупносерийном производствах разрабатывается подробная пооперационная технология, включающая перечень переходов, вид и номер оборудования, перечень и шифр оснастки, режим работы и расчетное время на каждый переход, марку материала, размер и вес заготовки. Таким образом, сама организация воздействия на объект управления, объемы выполняемых работ по подготовке, длительность цикла подготовки, величина затрат и т.д. зависят от особенностей характера производства.
Расчетную основу для задач управления подготовкой производства составляют нормативы трудоемкости и длительности цикла. Они разрабатываются применительно к особенностям выпускаемой продукции и этапам подготовки производства, а также с учетом конструкторской и технологической сложности изделия, количества оригинальных деталей, типа производства, характера технологических процессов, вида оснастки и степени ее сложности. Применение нормативов дает возможность правильно определять загрузку, устанавливать равномерность работы конструкторских и технологических отделов, потребность в кадрах, сроки разработок и рассчитывать затраты на организацию производства и освоение новых изделий.
В настоящее время еще не существует единой методики разработки нормативов планирования подготовки производства, однако некоторые проектные организации и заводы сами разрабатывают укрупненные нормативы.
С развитием технического прогресса увеличивается объем работ научно-исследовательских организаций на стадии технической подготовки производства. Стирается грань между научными исследованиями, проводимыми заводскими лабораториями, научно-исследовательскими организациями, и технической подготовкой, проводимой конструкторами и технологами завода, так как при проектировании и освоении производства нового изделия научные исследования лабораторий и институтов включаются в проектно-конструкторские и технологические работы. При техническом прогрессе, с одной стороны, происходит быстрейшая смена устаревших изделий новыми, более современными, с другой — на подготовку производства нового изделия затрачивается больше времени и труда, чем на изготовление изделия.
Комплексное планирование всех этапов подготовки производства нового изделия должно начинаться с конструкторских работ и заканчиваться выпуском и отработкой его первых опытных образцов. При этом устанавливаются сроки выпуска чертежей изделия, разработки и оснащения техпроцессов, окончательные сроки внедрения и затраты труда на отдельные этапы в процессе подготовки. Опытные образцы новых изделий должны изготавливаться в условиях, близких к условиям будущего массового их производства. Это даст конструкторам большой материал по надежности (работоспособности) нового изделия и позволит технологам разработать более экономичные технологические процессы с наименьшим количеством переделок в процессе ведения подготовки.
Постоянно растущие требования по сокращению сроков и повышению качества подготовки производства, а также увеличению количества вновь осваиваемых конструкций машин вызывают необходимость непрерывного совершенствования организации и методов технической подготовки производства новых изделий.
Организацию работ по технической подготовке производства (созданию) нового изделия можно подразделить на три вида.
Первый вид — организация работ по созданию нового изделия несколькими научно-исследовательскими, проектными организациями, опытными и промышленными предприятиями. Научно-исследовательские организации проводят научные исследования по определению новых технических решений и выдаче рекомендаций по составлению технического задания на модернизацию выпускаемого изделия или разработку нового; проектные организации ведут конструкторскую разработку; опытные заводы — изготовление опытных образцов; промышленные предприятия — изготовление отдельных узлов (агрегатов) и в целом нового изделия.
Второй вид — процесс разработки ведется несколькими организациями, а серийное изготовление — на промышленном предприятии. Научно-исследовательские институты ведут исследования новых направлений и поиск новых технических решений, дают рекомендации по составлению технического задания на модернизацию или разработку нового изделия; проектные организации разрабатывают техническую документацию и испытывают опытный образец. На основе результатов испытания опытного образца корректируется техническая документация и передается заводу для освоения производства. После получения документации службы предприятия ведут техническую подготовку по организации соответствующего типа производства (серийного, массового) нового изделия.
Третий вид — часть процесса создания нового изделия от научных исследований до испытания опытного образца осуществляется в научно-исследовательской или конструкторско-технологической организации, а серийное изготовление созданных образцов — на промышленном предприятии. Следует признать, что такая практика организации работ по созданию нового изделия с участием ряда самостоятельных организаций и предприятий усложняет управление разработками; на этапах разработки не учитываются технологические возможности предприятия, осваивающего промышленное производство, что снижает эффективность, а согласование и передача технической документации от этапа к этапу затягивает сроки создания новых изделий.
РАЗДЕЛ III. ОРГАНИЗАЦИЯ ПРОИЗВОДСТВЕННОГО ПРОЦЕССА ВО ВРЕМЕНИ
Тема 1. Производственный процесс.
Производственный процесс представляет собой совокупность процессов труда и естественных процессов, направленных на изготовление продукции. Основой производственного процесса является технологический процесс. Основой технологического процесса является операция.
Производственные процессы классифицируются по степени механизации и по назначению. По степени механизации выделяют ручные, машинно-ручные, машинные, автоматизированные и аппаратурные процессы. По назначению различают основные, вспомогательные и обслуживающие процессы.
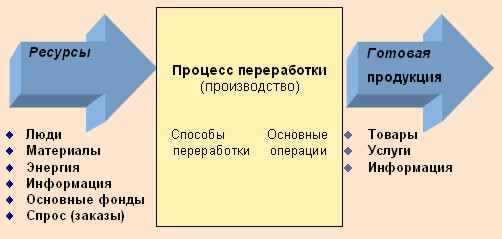
Рисунок 5. Содержание производственной деятельности
Принципы рациональной организации производственных процессов.
1. Принцип специализации означает разделение производственного процесса на составляющие и закрепление каждой из них за соответствующим подразделением или исполнителем.
2. Принцип пропорциональности означает соотношение производственных мощностей цехов, участков, рабочих мест. Нарушение принципа пропорциональности приводит к возникновению узких мест в производстве, то есть перегрузки оборудования и рабочих мест на 1 участке и недозагрузке на другом.
3. Принцип параллельности означает одновременное выполнение операций на всех или некоторых рабочих местах. Соблюдение этого принципа способствует сокращению длительности производственного процесса. Параллельность реализуется на всех уровнях организации. Например, параллельное выполнение основных процессов можно реализовать путем обработки детали и одновременном выполнении сборочно-монтажных работ. А параллельности в выполнении основных и вспомогательных операций можно достигнуть путем совмещения времени машинной обработки со временем установки и съема деталей, контрольных промеров, загрузки и разгрузки оборудования и т.д.
Усложнение продукции в настоящее время, а также использование автоматического оборудования и разделения труда увеличивают число параллельно проводимых процессов, что позволяет оптимально сократить длительность производственного процесса и соответственно повысить эффективность производства.
4. Принцип непрерывности означает сокращение до минимума перерывов в производственном процессе. На рабочем месте непрерывность достигается путем сокращения вспомогательного времени (внутриоперационных перерывов) в процессе выполнения каждой операции, на участке и в цехе - при передаче полуфабриката с одного рабочего места на другое (межоперационных перерывов) и т.д.
Непрерывность работ обеспечивается, прежде всего, совершенствованием производства, а также рациональным сочетанием и согласованием различных производственных процессов во времени.
5. Принцип прямоточности означает прямолинейное движение предметов труда в процессе изготовления изделия. В соответствии с этим требованием взаимное расположение зданий и сооружений на территории предприятия, а также размещение в них основных цехов должны соответствовать требованиям производственного процесса. Поток материалов, полуфабрикатов и изделий должен быть кратчайшим, без встречных и возвратных движений. Вспомогательные цехи и склады должны размещаться как можно ближе к обслуживаемым ими основным цехам.
6. Принцип ритмичности означает выпуск равного количества продукции в равные промежутки времени. При ритмичной работе обеспечиваются полная загрузка оборудования, нормальная его эксплуатация, улучшается использование материально-энергетических ресурсов и рабочего времени. Неритмичная работа каждого участка приводит к нарушению нормального хода производства.
Ритмичность производства может быть обеспечена рациональной организацией работы во всех подразделениях предприятия, а также его своевременной подготовкой и комплексным обслуживанием.
7. Принцип комплексности. Современные процессы изготовления продукции характеризуются постоянным взаимодействием и "сращиванием" основных, вспомогательных и обслуживающих процессов. Поэтому в связи с известным отставанием автоматизации обслуживающего производства по сравнению с оснащенностью основного необходимо концентрировать внимание на рациональной организации выполнения не только основных, но и вспомогательных и обслуживающих процессов производства.
Тема 2. Производственный цикл.
Производственным циклом называется календарный период времени, в течение которого предмет труда проходит все стадии производственного процесса - от первой производственной операции до сдачи (приемки) готового продукта включительно. Структура производственного цикла представлена на рисунке 6.
Производственный цикл состоит из двух частей: из рабочего периода, т.е. периода, в течение которого предмет труда находится непосредственно в процессе изготовления, и из времени перерывов в этом процессе.
Рабочий период состоит из времени выполнения технологических и нетехнологических операций; к числу последних относятся все контрольные и транспортные операции с момента выполнения первой производственной операции и до момента сдачи законченной продукции.
Практика успешного бизнеса показывает, что сокращение производственного цикла дает возможность предприятию ускорить оборачиваемость оборотных средств, выполнить установленный план с меньшими затратами этих средств, высвободить часть оборотных средств. Большое влияние на длительность производственного цикла оказывают методы организации производственных процессов.
Различают три основных метода организации производственных процессов:
- последовательный,
- параллельный,
- параллельно-последовательный.
При последовательном методе деталь в процессе производства переходит на каждую последующую операцию только после окончания обработки всех деталей данной партии на предыдущей операции. В этом случае с операции на операцию транспортируется вся партия деталей одновременно. При этом каждая деталь пролеживает на каждой операции сначала в ожидании своей очереди обработки, а затем в ожидании окончания обработки всех деталей по этой операции.
При параллельном методе обработка каждой детали на каждой последующей операции начинается немедленно после окончания предыдущей операции независимо от того, закончена обработка других деталей на данной операции или еще нет. При таком методе несколько единиц одной и той же партии могут одновременно находиться в обработке на разных операциях. Общая продолжительность процесса обработки партии деталей значительно уменьшается по сравнению с тем же процессом, выполняемым последовательно. В этом заключается существенное преимущество параллельного метода, позволяющего значительно сократить продолжительность производственного процесса.
Главной называется операция, которая имеет наибольшую продолжительность.
Параллельно-последовательный метод характеризуется тем, что процесс обработки деталей данной партии на каждой последующей операции начинается раньше, чем полностью заканчивается обработка всей партии деталей на каждой предыдущей операции. Детали передаются с одной операции на другую частями. Накопление некоторого количества деталей на предыдущих операциях перед началом обработки партии на последующих операциях (производственный задел) позволяет избежать возникновения простоев. При этом если продолжительность предыдущей операции меньше, чем последующей, передача деталей с операции на операцию осуществляется как при параллельном методе. Если продолжительность предыдущей операции больше, чем последующей, то необходимо определить время совмещения двух операций.
Параллельно-последовательный метод позволяет значительно уменьшить продолжительность производственного процесса обработки по сравнению с последовательным методом.
Тема 3. Организация инструментального обслуживания
производства
Назначение инструментального хозяйства предприятия заключается в своевременном и в полном объеме удовлетворении потребностей производственных подразделений предприятия в технологической оснастке с минимальными затратами.
На каждом производстве используется технологическая оснастка, от качества которой и своевременности оснащения рабочих мест зависят результаты производства и деятельности предприятия в целом. Затраты на инструмент и другую технологическую оснастку составляют от 5 до 30% стоимости оборудования, их удельный вес в себестоимости выпускаемой продукции — от 1,5 до 15%, причем эти затраты тем выше, чем выше серийность производства.
Рациональная организация инструментального обслуживания производства способствует повышению производительности, улучшению качества выпускаемой продукции и снижению ее себестоимости.
Основными задачами инструментального хозяйства предприятия являются:
- определение потребности и планирование обеспечения предприятия оснасткой;
- нормирование расхода оснастки и поддержание ее запасов на требуемом уровне;
- обеспечение предприятия покупной оснасткой;
- организация собственного производства оснастки;
- организация учета, хранения и обеспечения рабочих мест оснасткой;
- организация рациональной эксплуатации оснастки и технический надзор;
- организация восстановления оснастки;
- контроль внедрения учет и анализ эффективности использования оснастки.
Также инструментальное хозяйство предприятия осуществляет закупки, проектирование и изготовление, хранение, доставку, эксплуатацию, восстановление и утилизацию оснастки.
Управление инструментальным хозяйством предприятия осуществляет главный технолог или непосредственно главный инженер. Для определения потребности в инструменте на какой-либо период времени необходимо установить номенклатуру потребляемого инструмента, расход инструмента, запасы и оборотный фонд инструмента.
Количество инструмента, которое полностью потребляется в производстве за определенный период, называется расходом инструмента. Количество инструмента, которое необходимо иметь в эксплуатации и в запасе для обеспечения бесперебойного хода производства, называется оборотным фондом.
Потребность в инструменте на планируемый период времени складывается из расхода инструмента и разницы между необходимым оборотным фондом и его фактической величиной на начало периода.
Расход инструмента можно рассчитать тремя способами.
1. Статистический метод расчета. Здесь по отчетным данным бухгалтерского учета за прошлый период определяется фактический расход инструмента. Затем полученный результат корректируется с учетом мероприятий по сокращению расхода инструмента, намеченных в плановом периоде, и получается плановый расход. Этот метод может дать значительную погрешность, поэтому рекомендуется применять его лишь в проектном и позаказном производствах либо производстве мелкими партиями.
2. Метод расчета по нормам оснастки. Под нормой оснастки понимается количество инструмента, которое должно одновременно находиться на соответствующем рабочем месте в течение всего планового периода. Расход инструмента здесь определяется как произведение нормы оснастки и числа рабочих, одновременно применяющих данный инструмент, деленное на срок службы данного инструмента до полного износа.
3. Метод расчета по нормам расхода. Под нормой расхода понимается количество инструмента, расходуемого при обработке одной детали или изделия. Расход инструмента определяется как произведение нормы расхода и количества единиц продукции, подлежащих выпуску в планируемом периоде.
Чтобы обеспечить эффективную работу инструментального хозяйства на производстве, необходимо сделать следующее.
- Организовать работу инструментального склада. Функциями склада являются приемка, учет и выдача инструмента цехам. При этом инструмент, поступающий со стороны, принимается по сопроводительным документам (счетам-фактурам, накладным и т.п.), причем его количество его проверяется работниками склада, а качество — контрольным пунктом ОТК. Инструмент, поступающий из собственного производства, принимается по накладным и качественной приемке на складе не подвергается, поскольку его приемка осуществляется в цехах. На каждый инструмент заводится учетная карта, и выдача цехам производится в соответствии с потребностью согласно нормам расхода и планам производства.
- Организовать работу инструментально-раздаточных кладовых в цехах. Их функциями является получение инструмента со склада, его хранение и учет, выдача на рабочие места и приемка с рабочих мест, отправка в ремонт, проверку и последующая приемка, списание изношенного инструмента и отправка на восстановительную базу или в утиль.
- Организовать ремонт и восстановление инструмента. Ремонтировать частично изношенный или сломанный инструмент целесообразно в том случае, когда расходы на его ремонт меньше или равны остаточной части стоимости инструмента с учетом его износа. Под восстановлением инструмента понимается ремонт полностью изношенного или пришедшего в негодность и списанного (снятого с эксплуатации) инструмента для придания ему первоначального или другого вида, свойств и размеров.
- Организовать работу инструментального цеха.
Инструментальный цех должен изготавливать специальный инструмент для основных цехов (для выпускаемых и вновь осваиваемых заводом изделий), вспомогательных цехов и служб завода, (в т.ч. инструмент для изготовления инструмента), а также производить ремонт и восстановление инструмента.
Мероприятия по совершенствованию организации и планирования инструментального хозяйства:
- расширение области применения инструмента;
- более широкое использование типовых технологических процессов;
- концентрация производства однотипной специальной оснастки,
- расширение объемов восстановления инструмента;
- комплексная механизация и автоматизация инструментального хозяйства;
- внедрение прогрессивных форм обеспечения рабочих мест инструментом с усилением технического надзора за его состоянием;
- совершенствование нормативной базы, планирования и учета в инструментальном хозяйстве на основе современных информационных технологий;
- стандартизация и сертификация.